重油催化裂化装置油浆系统结焦的原因及措施
催化裂化装置结焦原因分析及对策研究

催化裂化装置结焦原因分析及对策研究催化裂化装置在长期运行过程中,由于操作条件、催化剂质量、原料质量等因素的影响,很容易出现结焦现象,严重影响装置运行稳定性和经济效益。
本文从结焦原因和处理方案两个方面进行分析研究。
一、结焦原因分析1. 催化剂质量不佳催化剂质量不佳往往会导致催化剂中的焦炭生成速度变快,一旦催化剂中焦炭过多,就会对催化剂活性和选择性进行破坏,进而导致催化剂失活。
而失活的催化剂不仅容易出现结焦现象,更会对生产造成较大的经济损失。
2. 操作条件不当操作条件不当也是造成催化裂化装置结焦的主要原因之一。
比如炉温过高、压力过低、流量过大等,都容易导致原料在装置内过热、过量分解,从而增加结焦风险。
3. 原料质量不稳定催化裂化装置原料质量的稳定性很重要。
如果原料中存在杂质、异物等不良物质,就容易引起催化剂中焦炭的快速生成,导致结焦现象的出现。
同时,原料成分的波动也容易影响催化剂的活性,从而增加催化剂失效的风险。
二、对策研究1. 改进催化剂质量针对催化剂质量不佳的问题,应优化催化剂生产的技术、提高催化剂活性等手段,尽可能延长催化剂寿命,减少催化剂中焦炭的生成,从根本上防止结焦现象的出现。
2. 优化操作条件优化操作条件是解决结焦问题的重要途径。
比如合理控制装置温度、压力、流量等参数,减小原料在装置内的分解程度,减少催化剂中焦炭的生成率,有效地增加装置运行的稳定性。
结语催化裂化装置结焦问题是长期以来困扰生产工艺的难点之一,笔者在此分析了造成结焦的原因,并提出了相应的防治策略。
不过,避免催化裂化装置结焦问题的出现,仅仅通过以上几种手段还是不够的,需要生产人员和技术人员综合发力,从各个方面对催化裂化装置进行管理和运行,以确保装置平稳运行,为生产水平的提高提供有力支持。
催化裂化装置结焦原因分析及对策研究

催化裂化装置结焦原因分析及对策研究
催化裂化装置结焦是指在催化裂化过程中,由于反应过程中产生的碳积累在催化剂表面,导致催化剂活性降低,反应效率下降,甚至催化剂失活的现象。
结焦问题严重影响了
催化裂化装置的生产效率和经济效益。
本文将分析催化裂化装置结焦的原因,并提出相应
的对策。
催化裂化装置结焦的原因主要包括以下几个方面:
1. 高温:催化裂化反应需要在较高温度条件下进行,高温会加速碳积聚的过程,导
致催化剂结焦。
2. 高碳含量的原料:催化裂化装置处理高碳含量的原料,会使得产生的碳积聚更多,导致催化剂结焦。
3. 高流速:高流速会引起催化剂表面的碳积聚过程加剧,进而促使催化剂的结焦。
4. 催化剂质量:催化剂材料的选择和质量会影响结焦问题,较差质量的催化剂容易
结焦。
5. 动力不足:催化裂化反应需要消耗大量的热力,如果动力系统供应不足,反应温
度无法保持在适宜的范围内,会导致结焦现象。
针对以上的原因,我们可以采取如下对策来应对催化裂化装置结焦问题:
1. 优化温度控制:通过合理控制反应温度,使其在适宜的范围内,既不过高也不过低,可以减少碳积聚的速度,降低催化剂结焦的风险。
3. 调整流速:合理调整反应器的流速,减缓碳积聚的速度,降低催化剂结焦的风
险。
4. 优化催化剂质量:选择高质量的催化剂材料,并严格控制催化剂制备的过程,以
提高催化剂的抗结焦能力。
催化裂化装置结焦问题是一个复杂的工艺问题,需要从温度控制、原料选择、流速调整、催化剂质量和动力供应等多个方面综合考虑,通过优化工艺参数和采取相应的对策,
才能有效降低结焦的风险,提高催化裂化装置的生产效率和经济效益。
催化裂化油浆结焦原因及对策

催化裂化油浆结焦原因及对策标签:催化裂化;油浆结焦;解决对策在我国炼油厂的催化裂化过程当中,油浆系统当中产生的结焦结垢问题直接影响到了催化裂化设备的正常工作,主要是因为产生大量的结焦结垢物质,直接降低了热换器的热转化效率,同时提高了管道当中材料输送的阻力,进而造成了蜡油渣油的热转换效率降低。
系统内部产生的蒸汽量减少,同时整个反应设备在工作过程当中的能源消耗量加大,油浆当中多余的热量无法及时被排除,进而造成了整个反应系统内部的热平衡性下降,严重的情况下还直接造成油浆输送系统堵塞,进而影响到了整个生产过程的正常进行。
在最近几年发展过程当中,我国炼油厂的催化裂化原材料质量都不是非常理想,外加上在加油的催化裂化技术方面一直是难以攻克的难题。
因此,催化裂化油浆结焦和结垢的问题受到了各大化工企业的广泛关注,必须要采取相应的解决措施来解决这一问题。
1.催化裂化油浆结焦问题分析1.1温度问题的影响从催化裂化的整个反应过程中可以看出,该反应过程中会受到温度的影响,在相同的催化设备当中分馏塔的底部温度越高,那么出现的结焦现象就越明显。
针对己经产生结焦问题来讲,随着温度不断提高整个反应过程的结焦问题就更加明显,就在模拟FCC油浆的结焦单元当中所得出的结论非常明显。
1.2氧含量的影响通过模拟实验分析了FCC油浆当中产生结焦单元的具体原因,通过向试管当中通入一定量的空气或者是氧气,可以看出在不同量的空气和氧气掺入的情况下,对结焦问题的影响比较明显,其中如果空气或者氧气的参与量较大,那么结焦的问题就越严重。
由此可以看出氧气含量的多少对结焦问题的影响非常明显。
1.3固体和电效应影响通过实际的生产过程可以看出,在催化裂化反应过程当中,如果增加油浆内部的沉降器和过滤器设备之后,在产生结焦和结垢的问题上有着明显的缓解。
因此,这一现象也可以得到充分的证明,从中可以得出催化裂化反应过程中油浆当中,所存在的固体杂质对结焦问题的影响比较明显。
重油催化裂化结焦原因及改进措施

重油催化裂化结焦原因及改进措施重油催化裂化是润滑油加工工艺的一个重要环节,是提高润滑油的质量的关键技术。
在重油催化裂化过程中,结焦是一个常见的问题,会严重降低催化裂化的效率。
重油催化裂化结焦的原因,主要有三个方面:首先,催化剂受污染。
催化剂通常是复合物,容易受到空气、产品成分和其他物质的侵蚀、混入或碳化,受到污染时,催化剂性能会受到严重影响,从而导致结焦。
其次,催化剂不可逆变化。
重油催化裂化温度高,使重油催化剂发生不可逆变化,催化剂的性能也下降,从而导致结焦等问题。
最后,温度控制不当。
重油催化裂化的温度控制是很重要的,太高或太低的温度都会影响催化剂的功能,导致结焦。
为了解决重油催化裂化结焦问题,应采取一些有效的措施。
首先,科学选用催化剂。
重油催化裂化中使用的催化剂一般是催化剂复合物,应根据实际需要科学选择恰当的催化剂,降低催化剂受污染的可能性。
其次,采用稳定性好的催化剂。
重油催化裂化时,要选择温度稳定性较好的催化剂,不变性的催化剂能有效降低结焦的可能性。
再次,做好温度控制。
重油催化裂化时,温度应稳定在一定范围内,太高或太低的温度都会影响催化剂的功能,因此应做好温度控制,以保证重油催化裂化效果。
最后,改善反应条件和催化裂化技术。
采用新型催化剂和剂的组合,改善反应条件,控制反应温度和反应压力,改进催化裂化技术,进一步提高重油催化裂化的效率。
综上所述,重油催化裂化结焦的主要原因是催化剂受污染、催化剂不可逆变化以及温度控制不当。
要改善这种情况,应采取有效的措施,如科学选用催化剂、采用稳定性好的催化剂、做好温度控制、改善反应条件和催化裂化技术等。
只有真正落实这些措施,才能有效防止重油催化裂化结焦,达到质量理想。
催化裂化装置结焦原因分析及对策研究
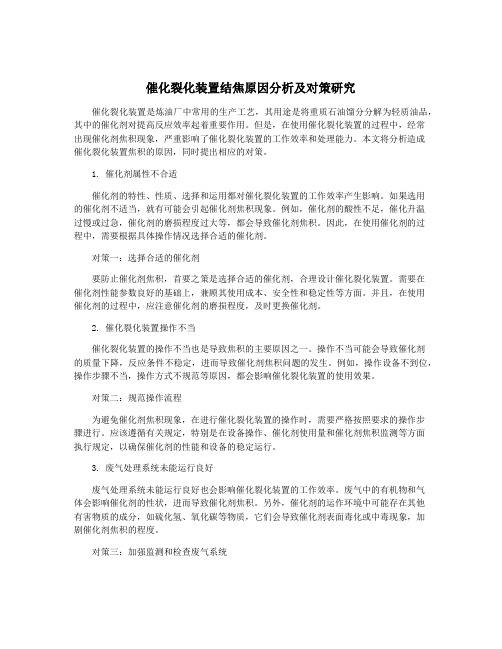
催化裂化装置结焦原因分析及对策研究催化裂化装置是炼油厂中常用的生产工艺,其用途是将重质石油馏分分解为轻质油品,其中的催化剂对提高反应效率起着重要作用。
但是,在使用催化裂化装置的过程中,经常出现催化剂焦积现象,严重影响了催化裂化装置的工作效率和处理能力。
本文将分析造成催化裂化装置焦积的原因,同时提出相应的对策。
1. 催化剂属性不合适催化剂的特性、性质、选择和运用都对催化裂化装置的工作效率产生影响。
如果选用的催化剂不适当,就有可能会引起催化剂焦积现象。
例如,催化剂的酸性不足,催化升温过慢或过急,催化剂的磨损程度过大等,都会导致催化剂焦积。
因此,在使用催化剂的过程中,需要根据具体操作情况选择合适的催化剂。
对策一:选择合适的催化剂要防止催化剂焦积,首要之策是选择合适的催化剂,合理设计催化裂化装置。
需要在催化剂性能参数良好的基础上,兼顾其使用成本、安全性和稳定性等方面。
并且,在使用催化剂的过程中,应注意催化剂的磨损程度,及时更换催化剂。
2. 催化裂化装置操作不当催化裂化装置的操作不当也是导致焦积的主要原因之一。
操作不当可能会导致催化剂的质量下降,反应条件不稳定,进而导致催化剂焦积问题的发生。
例如,操作设备不到位,操作步骤不当,操作方式不规范等原因,都会影响催化裂化装置的使用效果。
对策二:规范操作流程为避免催化剂焦积现象,在进行催化裂化装置的操作时,需要严格按照要求的操作步骤进行。
应该遵循有关规定,特别是在设备操作、催化剂使用量和催化剂焦积监测等方面执行规定,以确保催化剂的性能和设备的稳定运行。
3. 废气处理系统未能运行良好废气处理系统未能运行良好也会影响催化裂化装置的工作效率。
废气中的有机物和气体会影响催化剂的性状,进而导致催化剂焦积。
另外,催化剂的运作环境中可能存在其他有害物质的成分,如硫化氢、氧化碳等物质,它们会导致催化剂表面毒化或中毒现象,加剧催化剂焦积的程度。
对策三:加强监测和检查废气系统为避免催化剂焦积现象的发生,需要严格监测和检查废气系统,确保其正常运行。
催化裂化装置结焦原因分析及对策研究

催化裂化装置结焦原因分析及对策研究催化裂化装置是炼油厂的关键设备之一,其作用是将重质石油馏分分解成轻质产品,包括汽油、柴油和液化石油气等。
由于操作不当或设备故障等原因,催化裂化装置很容易出现结焦现象,严重影响生产效率和产品质量。
对催化裂化装置结焦原因进行分析,并制定相应的对策,对于炼油厂的稳定运行和产品质量具有重要意义。
1. 温度控制不当催化裂化装置工作温度的控制是避免结焦的关键因素之一。
如果温度过高,容易导致催化剂在装置中的积炭过多,从而引发结焦现象。
温度过低也会使催化剂在反应过程中不能充分活化,同样容易导致结焦。
保持合适的工作温度是避免结焦的重要手段。
2. 催化剂质量不良催化裂化装置中使用的催化剂质量的好坏直接影响装置的运行情况。
如果催化剂中存在杂质或者受到空气污染,会导致催化剂的活性降低,从而影响反应的进行,最终导致结焦。
3. 操作人员不当操作催化裂化装置是复杂的设备,需要操作人员具备一定的专业知识和技能。
如果操作人员不当操作,比如在设备运行时不按规定添加催化剂,或者不及时清理催化剂床中的积炭,都会加重结焦的程度。
4. 设备故障设备故障是导致催化裂化装置结焦的另一重要原因。
比如设备堵塞、管道泄漏等故障,都会导致催化剂无法正常流动或者反应不能顺利进行,最终导致结焦。
二、催化裂化装置结焦对策研究为了避免催化裂化装置结焦,首先需要严格控制工作温度。
可以通过安装温度传感器和控制系统,不断监测和调节催化裂化装置的工作温度,保证其在安全范围内稳定运行。
选择高质量的催化剂是避免催化裂化装置结焦的重要措施。
可以通过提高催化剂的制备工艺、严格控制原料质量和加强催化剂检测等手段,提高催化剂的活性和稳定性。
催化裂化装置的操作人员需要接受系统的培训,掌握装置的结构与工作原理,熟悉操作规程,了解可能影响反应的因素,提高操作技能,以减少因操作不当而导致的结焦情况。
4. 定期检查与维护为了预防催化裂化装置结焦,需要定期检查设备的运行情况,发现问题及时处理。
催化裂解装置反应系统结焦原因分析及应对措施
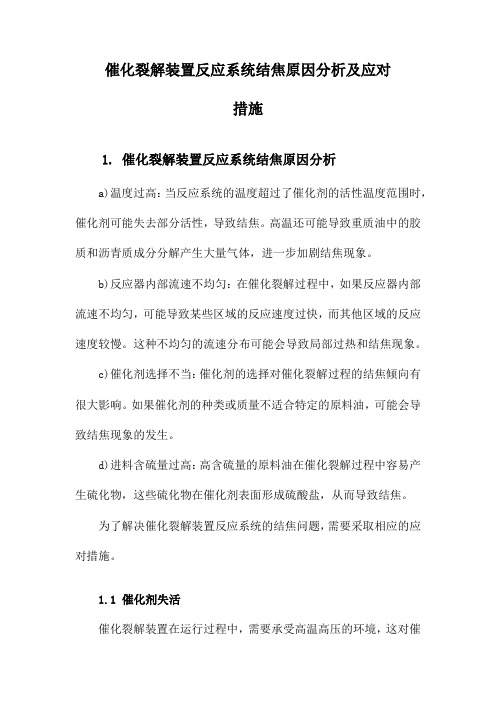
催化裂解装置反应系统结焦原因分析及应对措施1. 催化裂解装置反应系统结焦原因分析a)温度过高:当反应系统的温度超过了催化剂的活性温度范围时,催化剂可能失去部分活性,导致结焦。
高温还可能导致重质油中的胶质和沥青质成分分解产生大量气体,进一步加剧结焦现象。
b)反应器内部流速不均匀:在催化裂解过程中,如果反应器内部流速不均匀,可能导致某些区域的反应速度过快,而其他区域的反应速度较慢。
这种不均匀的流速分布可能会导致局部过热和结焦现象。
c)催化剂选择不当:催化剂的选择对催化裂解过程的结焦倾向有很大影响。
如果催化剂的种类或质量不适合特定的原料油,可能会导致结焦现象的发生。
d)进料含硫量过高:高含硫量的原料油在催化裂解过程中容易产生硫化物,这些硫化物在催化剂表面形成硫酸盐,从而导致结焦。
为了解决催化裂解装置反应系统的结焦问题,需要采取相应的应对措施。
1.1 催化剂失活催化裂解装置在运行过程中,需要承受高温高压的环境,这对催化剂的活性和稳定性提出了很高的要求。
在长时间的高温高压作用下,催化剂会发生热老化、碱腐蚀等现象,导致其活性降低甚至失活。
催化裂解装置的空速是影响催化剂活性的重要参数,如果空速过快,会导致催化剂表面的气体流速过大,从而使催化剂表面积炭速度加快,进而导致结焦现象的发生。
催化裂解装置所处理的原料油品质直接影响催化剂的使用寿命和活性。
如果原料油中杂质含量过高,如硫、磷等元素含量过高,会加速催化剂的失活过程,从而导致结焦现象的发生。
催化裂解装置的操作条件对催化剂的活性有很大影响,如温度、压力、进料量等参数设置不当,都可能导致催化剂失活,进而引发结焦现象。
选择适合催化裂解工艺条件的催化剂,并对其进行优化设计,以提高其抗高温、抗高压、抗污染等性能,从而降低催化剂失活的风险。
通过调整空速参数,使催化剂表面的气体流速保持在合适的范围内,减缓催化剂表面积炭的速度,降低结焦风险。
加强对原料油的质量监控和管理,严格控制原料油中硫、磷等有害元素的含量,降低催化剂失活的可能性。
石化企业催化裂化装置结焦原因及解决对策研究

第52卷第7期 辽 宁 化 工 Vol.52,No. 7 2023年7月 Liaoning Chemical Industry July,2023石化企业催化裂化装置结焦原因及解决对策研究李法军(山东京阳科技股份有限公司,山东滨州251800)摘要:催化裂化装置对我国石油产业而言非常重要,存在结焦现象,严重影响着安全生产活动。
通过对于焦块的整体形态以及其构成因素进行分析,催化剂不足、相关原料油处理不当、重组分冷凝等都是导致结焦的重要因素。
因此,为了有效对催化裂化装置结焦原因进行认知,就需要结合工程的实际情况,开展有效的讨论,阐述催化裂化装置的基本概述,分析结焦的危害以及形成原因,研究如何通过合理有效的方式,在实际使用中,降低催化裂化装置结焦所带来的安全危害。
关键词:石油化工;催化裂化装置;结焦原因;对策分析;研究分析中图分类号:TE624 文献标识码:A 文章编号:1004-0935(2023)07-1006-03催化裂化装置在炼油过程中,其需要保持长时间运行。
因此,其运行周期以及运行效率是我国炼油企业最关注的重点问题之一。
在催化装置运行当中,一般而言在发达国家,催化裂化装置在运行周期当中,通常可以保持3~5年。
而我国国内,因其技术原因,约有90%以上的催化裂化装置无法有效达成使用寿命,甚至部分催化裂化装置仅能维持1~2年左右。
在对出现损坏催化裂化装置原因分析中,可以得知其结焦是影响我国催化裂化装置运行的重要阻碍。
就大部分炼油企业进行分析,结焦问题是企业必须解决的重点问题。
延长催化裂化装置,并根据其生产周期进行设置,可以保障各炼油企业解决发展目标,完成催化裂化装置的有效增长。
根据实际过程,对出现结焦的具体部位、形态、相关组成等因素考量。
归纳结焦机理,提出相应的减缓措施,以避免在运转过程中,沉降器发生结焦,影响运转效率,干扰相关的运转效果。
1 催化裂化概述想保障对催化裂化装置出现结焦的原因进行有效的解决,就必须对催化裂化形成认知。
催化裂化装置结焦原因分析及对策研究

催化裂化装置结焦原因分析及对策研究1. 引言1.1 研究背景催化裂化装置是炼油厂中重要的设备之一,其主要功能是将重质烃分子通过催化剂的作用分解成轻质烃。
在装置长期运行过程中,往往会出现结焦现象,即催化剂表面会沉积焦炭,导致装置效率下降,产品质量下降,甚至影响整个装置的安全稳定运行。
结焦问题一直是炼油行业面临的重要挑战之一,其严重影响了装置的运行效率和经济效益。
目前对于催化裂化装置结焦问题的研究仍存在许多不足之处,需要进一步深入探讨。
本文旨在对催化裂化装置结焦原因进行分析,探讨结焦对装置运行、产品质量和能耗的影响,并提出可行的对策措施,以期提高装置运行效率,保证产品质量,降低能耗,为炼油企业的可持续发展提供有力支撑。
1.2 研究目的研究目的是为了深入分析催化裂化装置结焦的原因,探讨结焦对装置运行、产品质量和能耗的影响,并提出有效的对策研究,以减少结焦现象对装置生产的不利影响,提高装置运行效率和产品质量,降低能耗消耗。
通过研究,我们希望能够为催化裂化装置的优化运行和设备管理提供有益的参考,促进装置的稳定运行和经济效益的提升。
通过对结焦问题的深入探讨和对策研究,我们将为相关行业提供科学合理的解决方案,为我国石油化工行业的发展贡献力量。
【研究目的】是本文研究工作的核心内容,也是我们研究的出发点和目标所在。
2. 正文2.1 裂化装置结焦原因分析裂化装置结焦是由于多种因素共同作用而导致的问题。
主要包括以下几个方面:1. 原料质量不佳:原料中存在硫、氮等杂质或者含硫量、含金属杂质过高,会加剧结焦的风险。
2. 操作条件不当:操作温度、压力、流速等参数控制不严,会导致裂化反应不完全,产生焦碳。
3. 催化剂失活:催化剂在长时间的使用过程中会逐渐失活,失活的催化剂无法有效促进裂化反应,容易引起结焦问题。
4. 设备老化:设备长时间运行会导致管道、换热器等部件堵塞或老化,影响流体正常流动,从而促进结焦现象的发生。
要解决裂化装置结焦问题,需要从原料选取、操作控制、催化剂管理、设备维护等方面进行全面考虑和改进。
某重油催化裂化装置结焦原因分析及其预防应对策略

某重油催化裂化装置结焦原因分析及其预防应对策略本文以某石化公司1.2Mt/年重油催化装置为例,就其运行过程中出现的装置提升管、沉降器、分馏塔底和油浆循环系统结焦问题进行了原因分析,并提出了针对性的预防应对措施。
标签:重油催化裂化装置;结焦原因;预防应对措施1.装置结焦概况该装置开工运行两个月后由于分馏塔底结焦,油浆泵出现抽空,经反复调节无效后,装置被迫停工。
停工检查发现:(1)分馏塔底严重结焦,塔底几乎全部充满了焦碳,只有油气入口处和靠近分馏塔搅拌蒸汽入口处的塔壁有空隙。
分馏塔板一层焦厚300-400mm,二层200-300mm,多块塔板被压弯变形,还有两块板脱落。
(2)油浆循环下返塔、油浆回炼线、提升管喷嘴预热线及反应集合管处分馏塔底补油线被堵塞,堵塞物为黑色半固状体。
经做苯溶解和苯不溶物灼烧后,Al2O3含量分析结果为苯溶物49%,苯不溶物为51%,Al2O3含量为4.3%(m),推算结果约含催化剂15%左右。
(3)油浆/原料换热器堵塞严重,且油浆系统调节阀磨损严重。
(4)装置停工检修期间检查发现提升管喷嘴上方1m处有大量硬质焦块,该部位人孔全部堵死。
沉降器顶有大量焦块,防焦蒸汽环管大部分被埋死。
沉降器旋分器升气管外壁有大量硬质焦块。
2.结焦原因分析2.1分馏塔底与油浆系统结焦导致分馏塔底与油浆系统结焦的因素较多,其中油浆的化学组成、分馏塔底和油浆系统的操作条件(如:分馏塔底液面、温度、催化剂固体含量、工艺管线和换热器管束流速等)是主要原因,此外,还与事故状态下的应急处理方式、分馏塔底结构形式等有关。
为提高装置负荷将部分性质恶劣的原料油大量供给重催,为提高装置轻质油收率,采取油浆部分回炼,直接导致油浆性质恶化,油浆比重长期在 1.05~1.1g/cm3运行;操作上,分馏塔底温度控制过高,油浆泵单台运行,循环量只有350t/h,油浆循环系统流速只有不足1.0m/s;为降低能耗,大量限制反应系统各部蒸汽,低负荷运行时沉降器旋分器偏离允许运行工况,导致油浆固含长期超标,这都加剧了分馏塔底与油浆系统结焦的速度。
催化裂化装置结焦原因分析及对策研究
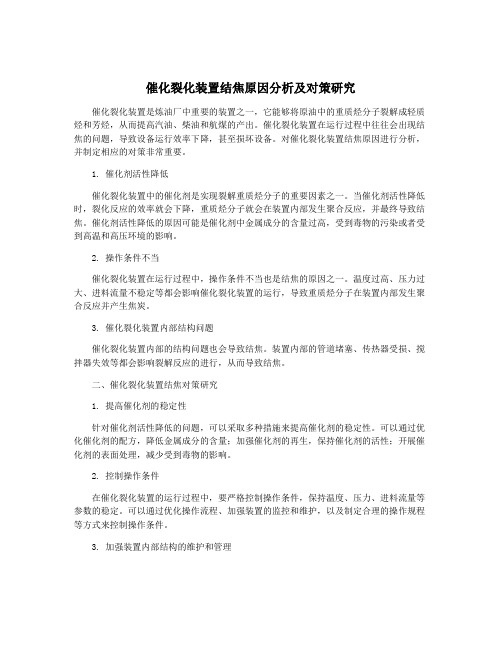
催化裂化装置结焦原因分析及对策研究催化裂化装置是炼油厂中重要的装置之一,它能够将原油中的重质烃分子裂解成轻质烃和芳烃,从而提高汽油、柴油和航煤的产出。
催化裂化装置在运行过程中往往会出现结焦的问题,导致设备运行效率下降,甚至损坏设备。
对催化裂化装置结焦原因进行分析,并制定相应的对策非常重要。
1. 催化剂活性降低催化裂化装置中的催化剂是实现裂解重质烃分子的重要因素之一。
当催化剂活性降低时,裂化反应的效率就会下降,重质烃分子就会在装置内部发生聚合反应,并最终导致结焦。
催化剂活性降低的原因可能是催化剂中金属成分的含量过高,受到毒物的污染或者受到高温和高压环境的影响。
2. 操作条件不当催化裂化装置在运行过程中,操作条件不当也是结焦的原因之一。
温度过高、压力过大、进料流量不稳定等都会影响催化裂化装置的运行,导致重质烃分子在装置内部发生聚合反应并产生焦炭。
3. 催化裂化装置内部结构问题催化裂化装置内部的结构问题也会导致结焦。
装置内部的管道堵塞、传热器受损、搅拌器失效等都会影响裂解反应的进行,从而导致结焦。
二、催化裂化装置结焦对策研究1. 提高催化剂的稳定性针对催化剂活性降低的问题,可以采取多种措施来提高催化剂的稳定性。
可以通过优化催化剂的配方,降低金属成分的含量;加强催化剂的再生,保持催化剂的活性;开展催化剂的表面处理,减少受到毒物的影响。
2. 控制操作条件在催化裂化装置的运行过程中,要严格控制操作条件,保持温度、压力、进料流量等参数的稳定。
可以通过优化操作流程、加强装置的监控和维护,以及制定合理的操作规程等方式来控制操作条件。
3. 加强装置内部结构的维护和管理为了避免装置内部结构问题导致结焦,需要加强装置的维护和管理。
定期清理管道和传热器、加强设备的检修和保养、进行装置内部结构的改进等,都可以有效减少结焦问题的发生。
催化裂化装置结焦是炼油生产中常见的问题,但通过对结焦原因的分析,并采取相应的对策,可以有效降低结焦的发生,保障装置的安全运行和生产效率。
催化裂化装置结焦原因分析及对策研究

催化裂化装置结焦原因分析及对策研究催化裂化装置作为炼油厂重要的催化反应器,在生产中经常发生结焦问题,给生产带来很大的影响,甚至导致设备损坏,因此对催化裂化装置结焦问题进行原因分析,并提出有效的对策十分必要。
1. 催化剂中杂质含量高由于催化剂生产和再生过程中无法完全除去常见的混合杂质和小颗粒杂质,会导致催化剂孔道堵塞,进而造成结焦问题。
2. 反应温度过高在高温条件下,不仅会加速化学反应过程,增加产品产量,同时也会增加碳代谢物生成的速度,导致催化剂的失活,反应产物中的重组物、聚合物和部分不饱和烃最终结焦生成焦炭,造成催化裂化装置的结焦问题。
3. 催化剂失活程度高催化剂的失活程度不仅与反应温度有关,还与催化剂寿命、催化剂产地、催化剂再生情况等因素有关。
催化剂失活对于催化裂化反应来说是十分严重的问题,因为失活催化剂难以发挥催化作用,反应会出现明显的减缓,产生结焦现象。
4. 再生效果不好在催化裂化反应中,催化剂在反应过程中会失活,在达到一定的失活程度后需要经过再生,再生后催化剂重新活化,恢复催化作用。
若再生效果不好,催化剂的失活仍没有得到很好的处理,则催化剂对重复使用无力,即使更换了新催化剂也会出现结焦现象,加剧催化裂化装置的结焦情况。
1. 增加催化剂的选择性和活性增加质量优良的催化剂,能够提高催化反应选择性,增加催化剂活性,减少结焦问题。
提高催化裂化装置的控制温度,尽可能减少炉内温度过高,能有效减少产生结焦现象的几率。
应该通过一定的方法来简化操作程序,降低操纵参数之间的变量,精度控制反应温度,以对避免产生大量结焦反应物及焦炭的生成。
3. 催化剂后续处理简单地减少现有催化剂中的杂质含量是不行的,需要加强催化剂的再生和处理过程,从催化剂再生,酸洗处理和干燥等方面入手,能够有效减少催化剂的失活程度,降低结焦发生的绝对值。
4. 悬浮固定床催化剂技术采用悬浮固定床催化剂技术,能有效提高孔道的通透性,获得更高的选率和活性,有选择性地促进催化裂化反应的进行,降低产生结焦现象的几率。
催化裂化装置结焦原因分析及对策研究
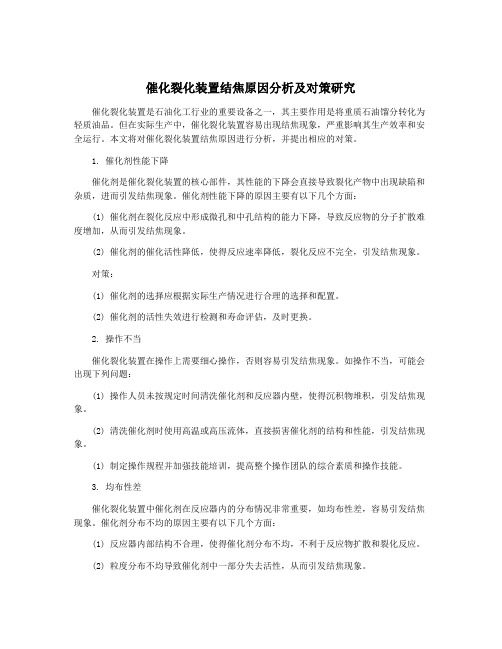
催化裂化装置结焦原因分析及对策研究催化裂化装置是石油化工行业的重要设备之一,其主要作用是将重质石油馏分转化为轻质油品。
但在实际生产中,催化裂化装置容易出现结焦现象,严重影响其生产效率和安全运行。
本文将对催化裂化装置结焦原因进行分析,并提出相应的对策。
1. 催化剂性能下降催化剂是催化裂化装置的核心部件,其性能的下降会直接导致裂化产物中出现缺陷和杂质,进而引发结焦现象。
催化剂性能下降的原因主要有以下几个方面:(1) 催化剂在裂化反应中形成微孔和中孔结构的能力下降,导致反应物的分子扩散难度增加,从而引发结焦现象。
(2) 催化剂的催化活性降低,使得反应速率降低,裂化反应不完全,引发结焦现象。
对策:(1) 催化剂的选择应根据实际生产情况进行合理的选择和配置。
(2) 催化剂的活性失效进行检测和寿命评估,及时更换。
2. 操作不当催化裂化装置在操作上需要细心操作,否则容易引发结焦现象。
如操作不当,可能会出现下列问题:(1) 操作人员未按规定时间清洗催化剂和反应器内壁,使得沉积物堆积,引发结焦现象。
(2) 清洗催化剂时使用高温或高压流体,直接损害催化剂的结构和性能,引发结焦现象。
(1) 制定操作规程并加强技能培训,提高整个操作团队的综合素质和操作技能。
3. 均布性差催化裂化装置中催化剂在反应器内的分布情况非常重要,如均布性差,容易引发结焦现象。
催化剂分布不均的原因主要有以下几个方面:(1) 反应器内部结构不合理,使得催化剂分布不均,不利于反应物扩散和裂化反应。
(2) 粒度分布不均导致催化剂中一部分失去活性,从而引发结焦现象。
(1) 反应器内部结构应尽可能合理,通过模拟进一步优化设计。
(2) 催化剂的粒度分布应做好分类,确保均布性,防止局部失活。
综上所述,针对催化裂化装置结焦问题,应该加强对催化剂的管理和维护,规范操作流程,优化反应器结构,并在操作过程中决不掉以轻心。
通过制定全面的管理和保养计划,以及严格操作规程,消除结焦隐患,提高催化裂化装置生产效率和安全运行水平。
重油催化裂化装置反应器结焦的原因及对策探索

重油催化裂化装置反应器结焦的原因及对策探索摘要:重油催化裂化装置反应器结焦是一个常见且严重的问题,影响着装置的稳定性和经济效益。
其主要原因包括重油中的杂质、不饱和化合物、反应温度和催化剂质量等。
为解决这一问题,相关企业可以采取一系列对策,包括提高重油预处理工艺、优化反应温度、改善催化剂质量等,这些对策的实施能够有效预防或减少反应器结焦现象的发生,提高装置的稳定运行和产能。
为此,本文主要对重油催化裂化装置反应器结焦的原因及对策进行探究,进而为提升重油催化裂化装置反应器的运用效果提供参考借鉴。
关键词:重油催化裂化装置;反应器结焦;原因及对策前言:重油催化裂化装置反应器结焦的根源可以追溯到重油中的杂质、不饱和化合物、反应温度和催化剂质量等多方面因素,这些因素相互作用,导致反应器内部出现积炭和结焦现象。
相关企业应创新应对措施,其能够有效预防或减少反应器结焦现象的发生,从而提高装置的稳定运行。
本文将对重油催化裂化装置反应器结焦的原因及对策进行详细介绍,进而为解决这一问题提供参考和指导。
一、重油催化裂化装置反应器结焦的原因1.重油中的杂质:重油中含有硫、氮、金属等杂质,它们在反应过程中会形成催化剂中毒物质,促使催化剂失活并导致结焦。
2.不饱和化合物:重油中的不饱和化合物在高温下容易发生聚合反应,形成高分子聚合物,这些聚合物会沉积在反应器内壁上,导致结焦。
3.反应温度和压力:反应温度过高或压力过低会导致重油分子裂解过程中的碳链断裂,生成的碳烯烃和芳烃会聚集在反应器内,形成积炭和结焦。
4.催化剂质量和活性:催化剂质量差、活性低或使用时间过长会导致催化剂失活,降低了重油分子的裂解效率,增加了结焦的风险[1]。
二、防止重油催化裂化装置反应器结焦的措施1.优化催化剂选择和管理一是选择高活性和稳定性催化剂:催化剂的选择是防止结焦的关键因素之一。
寻找具有高活性和稳定性的催化剂,可以提高重油的转化效率,并降低结焦的风险。
二是定期检查和更新催化剂:企业应定期检查催化剂的状态和性能,如颗粒大小、活性、金属含量等,并根据需要进行更新,老化或失活的催化剂容易导致结焦问题。
催化裂化装置结焦原因分析及对策研究
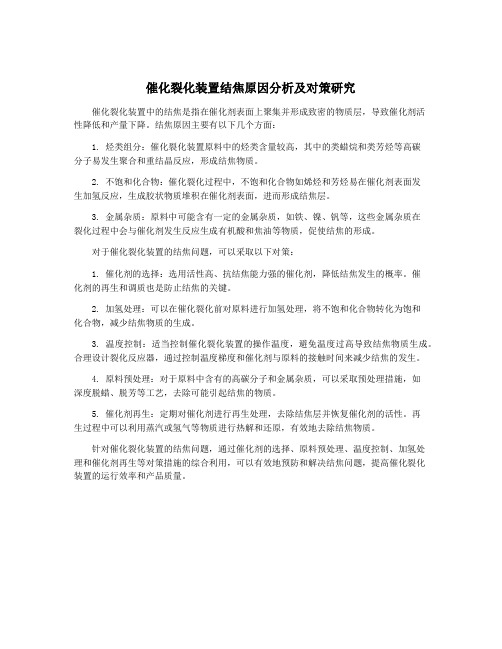
催化裂化装置结焦原因分析及对策研究催化裂化装置中的结焦是指在催化剂表面上聚集并形成致密的物质层,导致催化剂活性降低和产量下降。
结焦原因主要有以下几个方面:1. 烃类组分:催化裂化装置原料中的烃类含量较高,其中的类蜡烷和类芳烃等高碳分子易发生聚合和重结晶反应,形成结焦物质。
2. 不饱和化合物:催化裂化过程中,不饱和化合物如烯烃和芳烃易在催化剂表面发生加氢反应,生成胶状物质堆积在催化剂表面,进而形成结焦层。
3. 金属杂质:原料中可能含有一定的金属杂质,如铁、镍、钒等,这些金属杂质在裂化过程中会与催化剂发生反应生成有机酸和焦油等物质,促使结焦的形成。
对于催化裂化装置的结焦问题,可以采取以下对策:1. 催化剂的选择:选用活性高、抗结焦能力强的催化剂,降低结焦发生的概率。
催化剂的再生和调质也是防止结焦的关键。
2. 加氢处理:可以在催化裂化前对原料进行加氢处理,将不饱和化合物转化为饱和化合物,减少结焦物质的生成。
3. 温度控制:适当控制催化裂化装置的操作温度,避免温度过高导致结焦物质生成。
合理设计裂化反应器,通过控制温度梯度和催化剂与原料的接触时间来减少结焦的发生。
4. 原料预处理:对于原料中含有的高碳分子和金属杂质,可以采取预处理措施,如深度脱蜡、脱芳等工艺,去除可能引起结焦的物质。
5. 催化剂再生:定期对催化剂进行再生处理,去除结焦层并恢复催化剂的活性。
再生过程中可以利用蒸汽或氢气等物质进行热解和还原,有效地去除结焦物质。
针对催化裂化装置的结焦问题,通过催化剂的选择、原料预处理、温度控制、加氢处理和催化剂再生等对策措施的综合利用,可以有效地预防和解决结焦问题,提高催化裂化装置的运行效率和产品质量。
重油催化裂化装置结焦原因分析及抑制措施

重油催化裂化装置结焦原因分析及抑制措施摘要:随着重油催化裂化装置的不断改造,结焦问题已经成为制约该装置长周期、安全、稳定运行的重要因素之一。
对于重油催化裂化装置结焦问题的研究,为提高该装置的工艺水平、保证装置长周期运行具有重要的意义。
本文在介绍我国重油催化裂化装置结焦情况及对其原因分析基础上,对结焦抑制技术进行了阐述,并结合实际情况提出了一些建议。
希望能够在今后重油催化裂化装置结焦抑制工作中有所帮助。
关键词:重油催化裂化;沉降器;雾化蒸汽;结焦;原因引言某企业制造的一种新型的重油催化裂化设备,是近年来投入应用的一种新型的设备,其设备的结构采用了同轴向的布局,整个设备的整体高约57 m,并采用了器内再生烧焦的形式。
由于旋风分离机的出风口没有横向隔断,所以沉淀机的上方通常都设置了防焦气。
该管道的总长度约为44米,并配有适当数量的喷头。
现实中在装置正常生产的时候,所产生的焦量一般是近10%的给料量。
在一定的条件下,由于各种因素的影响,可能会产生凝块,对设备造成极大危害。
一、我国重油催化裂化装置结焦情况我国重油催化裂化装置大多是在70年代开始设计,经过多年的生产运行,目前已有很多重油催化裂化装置采用了重叠式两段再生、蒸汽吹扫和回炼油抽提等工艺技术,但操作中不可避免的会出现结焦问题,结焦严重时可导致催化剂活性降低、装置停工、产品收率降低、产品质量下降、甚至产生恶性事故等,因此也成为影响催化裂化装置长周期运行的一个重要因素。
结焦对催化裂化装置的危害主要有以下几方面:一是再生操作中大量焦炭燃烧引起再生器温度超高从而使催化剂床层温度升高;二是使催化剂床层温度分布不均;三是容易造成碳堆积,若烧炭量小于积碳量,再生剂含碳量过高进入反应器后,反应原料不能充分反应从而使油气附着在催化剂表面造成恶性循环引发恶性事故;四是引起催化剂再生器结垢和堵塞;五是引起催化剂床层密度降低、减压塔压力升高,当减压塔压力升高到一定程度时,会导致减压塔顶出现积蜡现象,从而降低减压塔顶循环液中的回流比。
催化裂化装置结焦原因分析及对策研究
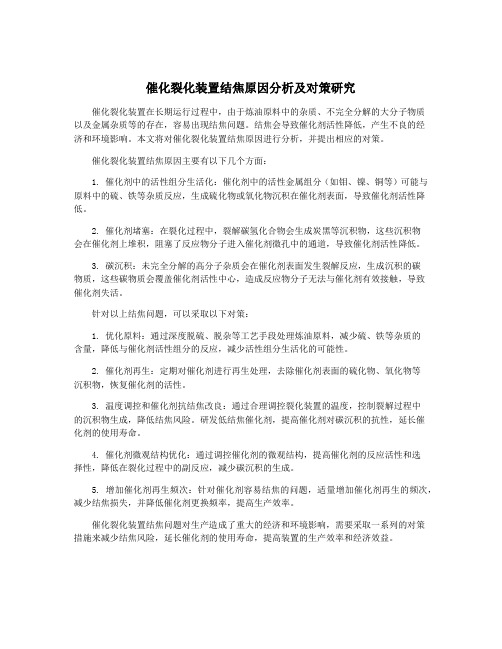
催化裂化装置结焦原因分析及对策研究催化裂化装置在长期运行过程中,由于炼油原料中的杂质、不完全分解的大分子物质以及金属杂质等的存在,容易出现结焦问题。
结焦会导致催化剂活性降低,产生不良的经济和环境影响。
本文将对催化裂化装置结焦原因进行分析,并提出相应的对策。
催化裂化装置结焦原因主要有以下几个方面:1. 催化剂中的活性组分生活化:催化剂中的活性金属组分(如钼、镍、铜等)可能与原料中的硫、铁等杂质反应,生成硫化物或氧化物沉积在催化剂表面,导致催化剂活性降低。
2. 催化剂堵塞:在裂化过程中,裂解碳氢化合物会生成炭黑等沉积物,这些沉积物会在催化剂上堆积,阻塞了反应物分子进入催化剂微孔中的通道,导致催化剂活性降低。
3. 碳沉积:未完全分解的高分子杂质会在催化剂表面发生裂解反应,生成沉积的碳物质,这些碳物质会覆盖催化剂活性中心,造成反应物分子无法与催化剂有效接触,导致催化剂失活。
针对以上结焦问题,可以采取以下对策:1. 优化原料:通过深度脱硫、脱杂等工艺手段处理炼油原料,减少硫、铁等杂质的含量,降低与催化剂活性组分的反应,减少活性组分生活化的可能性。
2. 催化剂再生:定期对催化剂进行再生处理,去除催化剂表面的硫化物、氧化物等沉积物,恢复催化剂的活性。
3. 温度调控和催化剂抗结焦改良:通过合理调控裂化装置的温度,控制裂解过程中的沉积物生成,降低结焦风险。
研发低结焦催化剂,提高催化剂对碳沉积的抗性,延长催化剂的使用寿命。
4. 催化剂微观结构优化:通过调控催化剂的微观结构,提高催化剂的反应活性和选择性,降低在裂化过程中的副反应,减少碳沉积的生成。
5. 增加催化剂再生频次:针对催化剂容易结焦的问题,适量增加催化剂再生的频次,减少结焦损失,并降低催化剂更换频率,提高生产效率。
催化裂化装置结焦问题对生产造成了重大的经济和环境影响,需要采取一系列的对策措施来减少结焦风险,延长催化剂的使用寿命,提高装置的生产效率和经济效益。
重油催化裂化结焦原因及改进措施

重油催化裂化结焦原因及改进措施重油催化裂化结焦,也被称为下游结焦,是指重油在催化裂化过程中的一种现象,它的出现会给裂化过程带来很多不便,使裂化效果受到一定的影响,因此重油催化裂化结焦的定量与质量是催化裂化产品质量的关键因素。
结焦的主要原因是催化剂不均匀的分布。
当反应催化剂在重油催化裂化剂中的分布不均匀时,部分反应区域的催化剂不足,从而导致反应产物积累,进而形成结焦物。
此外,反应条件不合理也是造成结焦的重要原因,包括反应温度过高或者反应温度不稳定,反应压力过高、反应压力不稳定,反应液体的层数、反应时间过长等等。
另外,重油催化裂化结焦还可能是由于原料重油中夹带的杂质或者水分、油类离子过高等原因造成的。
在重油中,各种杂质如烃、氧化物、含碳水等不易被催化裂化,如果温度和压力条件不合适,就可能形成结焦物。
另外,当重油中含碳水离子过高时,它们会结合形成结焦物,也会对裂化过程造成影响。
二、改进措施(1)优化催化剂的使用。
要想有效的解决重油催化裂化结焦的问题,首先要保证催化剂的分布均匀,可以采用多种方法,如加入悬浮剂等,以改善催化剂的可利用性,使催化剂均匀地分布在反应液中,从而提高反应效率。
(2)优化反应条件。
反应条件的优化是降低结焦率的重要措施。
反应温度和反应压力不能过高,应当根据重油类型和反应条件来选择合适的反应温度和反应压力,保证反应稳定。
另外,反应时间也不能过长,否则反应产物容易积累,形成结焦物。
(3)改善原料重油质量。
原料重油中存在的杂质和水分都会影响重油催化裂化的效果,要想获得较好的催化裂化效果,首先应该提高原料重油的质量,如选择质量较好的原料重油,做好原料重油的净化和精制等,以提高催化裂化效果。
三、结论重油催化裂化结焦是指重油在催化裂化过程中出现的现象,它的出现会给裂化过程带来一定的影响,常见的原因有:催化剂分布不均匀、反应条件不合理、原料重油中夹带的杂质或者水分、油类离子过高等。
改善重油催化裂化结焦的措施有:优化催化剂的使用、优化反应条件、改善原料重油质量等。
催化裂化装置结焦分析和防结焦措施

催化裂化装置结焦分析和防结焦措施摘要:随着原油价格上涨,原油重质化和劣质化是各炼油企业实现效益最大化的有效方法,由此带来了催化裂化装置结焦问题,目前重油催化裂化装置不可避免的存在结焦问题。
催化裂化结焦主要是由于原料性质变重后,原料喷嘴的雾化效果差,原料油在催化剂上不能完全汽化而产生湿催化剂,这些湿催化剂粘附结焦是引起提升管及沉降器内结焦的主要原因,而油气中重组分油气遇冷凝结,粘附在器壁上,长时间高温条件下发生缩合反应生成焦块,则是油气大管结焦的主要原因。
关键词:催化裂化;结焦;分析1前言催化裂化装置是炼油企业的核心装置,也是影响炼油企业效益的重要装置,如何减少催化裂化装置结焦延长装置运行周期,已成为各炼油企业实现效益最大化的重要手段。
湛江东兴1#催化裂化装置经过数次改造,由蜡油催化裂化改为重油催化裂化,2005年由洛阳设计院对催化装置进行扩能改造后,处理量提高至50万吨/年,设计减渣掺炼比例40%。
随着装置掺渣量的提高,结焦已成为影响装置长周期运行的重要因素,特别是沉降器的结焦长期威胁着装置的安全平稳运行。
1#催化裂化装置于05年3月16日一次性喷油成功后,由于掺渣量大,装置结焦较为严重,见表一。
2007年3月14日按计划进行检修,停工打开沉降器清焦时发现,装置结焦严重,清出的焦炭共约50吨,见图一。
目前1#催化装置沉降器内部结焦也较为严重,本周期运行过程中曾两次出现焦块脱落,造成催化剂循环困难现象。
本文通过分析结焦的原理及部位,结焦的原因,采取相应的防范措施,避免在生产过程中提升管、沉降器、油气大管、分馏塔底及油浆换热系统结焦,确保装置安稳长周期运行。
图一:2007年3月检修时,由沉降器清出的焦块表一:沉降器至气压机入口压力实测数据日期沉降器顶压力Mpa单旋出口压力Mpa油气入分馏塔压力MpaE201顶压力MpaF203压力Mpa气压机入口压力Mpa单旋压降kpa油气大管压降kpa分馏塔压降kpaE201顶至F203压降kpa沉降器至气压机压降kpa2005.6.7 0.245 0.228 0.209 0.194 0.152 0.151 17 19 15 42 94 2005.7.15 0.257 0.238 0.216 0.197 0.166 0.165 19 22 19 31 92 2005.8.1 0.26 0.234 0.199 0.181 0.155 0.154 26 35 18 26 106 2005.8.30 0.272 0.233 0.202 0.178 0.145 0.144 39 31 24 33 128 2005.9.30 0.272 0.234 0.208 0.184 0.142 0.137 38 26 24 42 1352006.1.19 0.266 0.228 0.197 0.174 0.158 0.138 38 31 23 16 128 2006.3.23 0.262 0.227 0.198 0.173 0.148 0.147 35 29 25 25 115 2006.8.28 0.263 0.232 0.206 0.186 0.153 0.152 31 26 20 33 111 2006.11.15 0.263 0.233 0.215 0.187 0.142 0.137 30 18 28 45 126 2007.3检修2007.5.23 0.261 0.252 0.244 0.229 0.209 0.198 9 8 15 20 63 2催化裂化装置结焦原理一般来说结焦的过程可以分为两种,一种为催化裂化反应结焦,催化裂化反应是一个重油脱碳的过程,由低氢碳比的重质油生产高氢碳比的轻质油的过程,因此必然生成一些焦炭,一些易生焦物(烯烃、芳烃、胶质、沥青质)在高温下具有很强的结焦倾向,通过脱氢缩合反应,以催化剂颗粒为结焦中心逐渐长大,最后生成焦。
- 1、下载文档前请自行甄别文档内容的完整性,平台不提供额外的编辑、内容补充、找答案等附加服务。
- 2、"仅部分预览"的文档,不可在线预览部分如存在完整性等问题,可反馈申请退款(可完整预览的文档不适用该条件!)。
- 3、如文档侵犯您的权益,请联系客服反馈,我们会尽快为您处理(人工客服工作时间:9:00-18:30)。
浅谈重油催化裂化装置油浆系统结焦的原因及措施
【摘要】分析了玉门油田炼油化工总厂催化裂化装置现有加工模式下,引起油浆系统结焦的主要原因,并提出相应的解决措施,确保了装置的长周期运行。
【关键词】油浆结焦原因措施
玉门炼化总厂80万吨/年催化裂化装置是2004年9月在原50万吨/年蜡油催化裂化装置的基础上扩建而成,改造后可掺炼减压渣油,作为全厂最重要的二次加工装置,承担着重质油轻质化的任务。
随着我厂“短流程燃料型”炼厂的转型,为维持我厂的重油平衡,装置提高了掺渣量,由于掺渣比的上升和原料油变重,油浆系统结焦问题变得日益突出。
本文通过对油浆系统结焦成因分析,有针对性地制定科学合理的对策,保证装置长周期、安全平稳运行。
1 油浆系统结焦的原因
1.1 分馏塔低温度
由于装置进入三年一修的开炼后期,油浆换热系统结焦严重,换热效率下降,导致分馏塔底部温度长期居高不下(348℃~355℃之间),该温度下塔底组分中的芳烃、烯烃等不饱和烃类进一步缩合成胶质、沥青质,造成结焦前反应物浓度的增加。
1.2 分馏塔低液位
由于分馏塔底始终保持着一定的液位,即油浆在分馏塔底有一定的停留时间,而分馏塔底是分馏塔内液相温度最高、催化剂含量最大的部位,在塔底的操作温度下极有可能发生热裂解反应,同时在
油浆的稠环芳烃等多种因素的作用下,更进一步趋于缩合脱氢形成焦质,使得塔底出现结焦。
1.3 油浆返塔温度
油浆自分馏塔底部抽出,通过换热后,其返塔温度降为250℃~280℃,温度的大幅度降低,使得油浆的粘度增加,流动性能变差,油浆在流动过程中对催化剂以及固体悬浮物的夹带作用减弱,导致催化剂颗粒、固体悬浮物和焦粒变得更易沉积,增加了结焦的几率。
1.4 油浆的停留时间
当油浆在某一高温下停留时间足够长时,油浆中将有焦炭生成。
1.5 油浆流速
油浆在管道中的流速过低,容易使缩合物沉积在管道表面而得以富集。
聚集的缩合物进一步反应,生成软焦。
1.4 油浆性质
玉门炼油厂调和原料和油浆中所含胶质、沥青质比重较高,胶质、沥青质使得结焦倾向增加。
因此,油浆系统结焦倾向与自身组成有十分重要的关系。
2 油浆系统防结焦措施
2.1 控制好调和原料性质
原料性质的改善,减少油浆中的胶质、沥青质等组分的生成,间接的改善了油浆的性质,使得油浆系统的结焦倾向减弱。
2.2 控制适当的反应深度
反应深度直接影响油浆的族组成和性质。
反应深度大时,反应油
气中的热裂化反应表现明显,产物的不饱和程度增加,导致油浆的粘度、密度也增大,流动性能变差,这样使得油浆更容易在温度低的区域挂壁结焦,堵塞过滤器、换热器。
2.3 控制油浆固体含量
要控制好油浆固含,一方面要控制好沉降器内旋风分离器线速和高速部位线速(如喷嘴)在工况范围内:vqs出口线速在16~20m/s;粗旋入口线速在15~18m/s;顶旋入口线速在18~22m/s。
另一方面监控好新鲜催化剂的性质,如新鲜催化剂的粒径组成、比表面积、孔体积以及活性等,从源头上控制油浆固含值。
2.4 优化分馏塔及设备操作条件
(1)控制较低的分馏塔底温.控制分馏塔底液相温度≯346℃。
气相温度≯380℃。
避免因分馏塔底温高造成油浆在塔底的结焦(2)保持浆循环量不小于327t/h,在分馏塔底不超温的情况下,尽量保证油浆上返塔流量。
使催化剂粉末完全洗涤下来.保证了分馏塔盘不被催化剂粉末堵塞,从而确保分馏塔的分离效率控制(3)确保适宜的油浆外甩量及回炼量,控制油浆固含量≯6.0 g/l,保证设备的长周期运转。
(4)执行油浆泵“一月一切换”制度.防止备用油浆泵由于长期不运行.油浆中的催化剂粉末和焦炭沉积在泵体及管线中。
致使启泵后油浆循环量达不到使用要求的情况发生。
(5)对换热效果较差的盘管切出用柴油浸泡,提高其换热效率。
2.6 其他措施
针对油浆结焦原因,采用24小时不间断加注油浆阻垢剂至油浆泵入口,通过油浆循环至整个油浆系统。
由于油浆阻垢剂具有清净分散性、抗氧化性、阻聚合性、钝化金属表面性和抗腐蚀性。
使用后,换热器的换热效果得到了改善,油浆返塔温度从290℃降至270℃。
3 结束语
(1)油浆系统结焦加重,主要是由外部操作条件造成的,操作中可以采取精细操作、优化工艺参数来实现。
比如降低分馏塔底温度、提高搅拌蒸汽量、适当增加油浆循环量等措施来解决。
(2)面对原料较重,芳烃、稠环芳烃等结焦因子较多时,依靠改进操作条件已不能有效地避免结焦、结垢现象的发生,这就需要采取加阻垢剂、柴油冲洗、浸泡和优化操作条件等措施来共同实现减少结焦的目的。
随着调和原料的变重,油浆系统结焦问题越来越普遍,只有结合装置实际,针对本装置生产特点,找出结焦原因并制定出相应的解决方案,才能更好的减少油浆系统结焦,达到催化裂化装置长周期运行。
参考文献
[1] 刘怀元.催化裂化油浆系统运行中的问题及对策[j].石油炼制与化工,2001,32 (4):65-67
[2] 马伯文.催化裂化装置技术问答[m].第二版.北京:中国石化出版社,2003:236-238
[3] 周康.重油催化裂化装置分馏系统结焦的控制对策[j].炼油设计,2002,32 (11):11-l5
[4] 孙庆.催化裂化装置油浆系统长周期运行影响因素及对策[j].化学工业,2012,30(10):53-54。