汽车后桥壳开裂的分析与改进
道路桥梁施工中的裂缝原因及其改进措施探析

道路桥梁施工中的裂缝原因及其改进措施探析道路桥梁是人们出行的重要通道,对于城市的发展和交通的畅通起到了重要的作用。
但是,在道路桥梁的施工中,随着时间的推移,往往会出现裂缝等问题,影响了道路桥梁的使用寿命和安全性。
因此,本文将从道路桥梁施工中的裂缝原因及其改进措施进行探析。
一、裂缝的产生原因1、材料问题道路桥梁的施工使用的材料质量不佳,容易出现疏松、空鼓、开裂等问题。
2、施工工艺问题在道路桥梁的施工中,工人在处理混凝土时,可能会导致混凝土的水灰比例不均等,出现质量问题。
这些问题都在未来的使用过程中会逐渐显现出来。
3、环境因素道路桥梁在施工和使用过程中,难免会受到外部因素的影响,如气候、温度等变化。
这些因素容易导致道路桥梁的温度膨胀和收缩,从而导致桥墩的裂缝问题。
二、改进措施1、加强质量管理在道路桥梁的施工过程中,应该加强质量管理,确保所有材料的质量达到标准。
此外,应该对材料的制作和加工过程进行频繁的检测,确保混凝土的水灰比例均匀,避免出现质量问题。
2、选用合适材料道路桥梁的施工中,应该选择适合的材料,用于制造桥墩等重要构件。
这些材料应该有较高的抗压性和抗拉强度,能够承受外部环境的影响。
在道路桥梁的施工中,应该优化混凝土的施工工艺,保证混凝土内的空气被排泄,以避免疏松和空鼓的产生。
此外,在施工中还应该采取有效的加强措施,防止桥梁内部的温度过高,从而导致桥墩的裂缝问题。
4、加强维护在道路桥梁的使用过程中,应该定期进行检查,及时发现已经出现的裂缝,并采取相应的维护措施。
这些维护措施包括修复裂缝、更换疲劳的构件和加固桥体等。
综上所述,道路桥梁施工中裂缝的产生原因比较复杂,在施工中应该加强质量管理,选用合适的材料和改进施工工艺。
并且,在使用过程中要坚持定期检查,加强维护及时解决存在的问题,以保证道路桥梁的安全性和使用寿命。
桥壳后壳盖失效分析

图1㊀后壳盖开裂失效件分析测量故障件板厚为2.7~2.8mm,符合材料拉伸范围要求理论最小允许厚度1.98mm)㊂材料成分见表1,符合标准要P Cr Ni Cuɤ0.035ɤ0.1ɤ0.25ɤ0.0.010.01860.00340.002是焊接时焊渣飞溅到后壳盖表面,会在金属表面产生类似焊接的金相组织,并有一定深度的热影响区,降低后壳盖的强E-mail:576857534@㊂图2㊀球状颗粒附着壳盖表面沿断口试样横截面切取磨制金相试样,经3%硝酸酒精溶液腐蚀㊁清洗㊁干燥后,宏观照片如图3所示,焊缝㊁薄板的位置特征清晰可见㊂置于莱卡DMI5000M 金相显微镜下观察,断口处金相组织为铁素体+珠光体组织,裂纹两侧未见偏析㊁杂质㊁脱碳等现象㊂同时在金相试样上进行洛氏硬度测试,经沃博特洛氏硬度计检测,故障件的洛氏硬度为52HRB ,故障件金相组织和硬度均正常㊂图3㊀裂纹附近金相组织将断口试样经超声波清洗干燥后,置于TESCAN 扫描电子显微镜下观察,起裂区在内侧,为多点起裂,如图4所示㊂图4㊀断口14倍SEM 照片㊀㊀在起裂区未见明显的冶金缺陷,其形貌为准解理+撕裂,如图5所示㊂图5㊀起裂区800倍SEM 照片扩展区形貌为准解理+贝壳纹,如图6所示,为典型的疲劳断口特征㊂图6㊀扩展区1500倍SEM 照片从对故障件的分析结果可以看出,后壳盖属于疲劳断裂,但故障件本身除焊渣飞溅到表面之外,其他方面未见明显的质量缺陷,这就需要从后壳盖的设计及使用环境去判断引起本次失效的原因[2]㊂3 失效原因分析3.1㊀壳盖材料机械性能根据标准GB /T228.1 2010进行材料拉伸试验[3],如图7所示,试样厚度3mm ,宽度30mm ,材料下屈服强度为175MPa ,抗拉强度290MPa ,符合原材料供应商技术协议中定义的要求㊂图7㊀材料拉伸试样3.2㊀CAE 分析根据现在发布的行业标准‘QC /T533 1999㊀汽车驱动桥台架试验方法“中驱动桥桥壳垂直弯曲疲劳试验的加载方法,建立CAE 分析模型(图8),得到桥壳后壳盖开裂区域应力为38MPa (图9),壳盖材料屈服强度为175MPa ㊂整车道路试验是按标准负荷加载的,没有发生超载情况,同时桥壳垂直弯曲疲劳台架试验已通过验证[4],且没有出现后壳盖失效故障㊂因此从CAE 分析及台架试验结果判断,后壳盖不可能在只承受垂向力作用下发生疲劳断裂㊂图8㊀CAE分析图9㊀后壳盖应力图3.3㊀路谱采集及台架对标基于故障件㊁原材料机械性能及常用工况CAE 分析结果均未发现异常,有必要对样件的使用环境进行路谱采集,以便进一步查找失效原因㊂应变片贴在后壳盖失效位置(图10),90ʎ为整车X 方向,0ʎ为Y 方向,45ʎ为Z 方向,在试验场地测试开裂位置处的应力应变㊂实测结果表明90ʎ方向(即整车X向)应力应变最大,最大值达到244MPa ,95%道路工况开裂位置应力值为103MPa (图11)㊂图10㊀开裂位置贴应变片图11㊀道路测试应力值根据路谱采集结果,欲在台架上模拟道路试验受力来复制整车上的故障模式㊂将装配主减速器壳体的桥壳总成样件,按主减速器壳体朝上的状态安装在试验台架上(图12),同时在开裂位置贴应变片以监控台架试验工况后壳盖受力与道路试验基本一致㊂共测试3台样件,均出现桥壳后壳盖开裂,开裂位置与道路试验一致㊂对台架试验开裂件进行检测,金相组织㊁材料成分等均正常㊂图12㊀台架试验装置3.4㊀焊接对材料性能的影响文中提到故障件表面有附着焊接时,飞溅到后壳盖表面的焊渣㊂在供应商现场抽取后壳盖表面附着焊渣的样件进行硬度梯度检测,判断焊缝热影响区范围以及焊渣的影响[5]㊂将样件磨制成金相试样(图13),分别进行硬度检测:(1)焊缝热影响区分析:沿图13箭头1方向进行硬度梯度检测,每隔0.5mm 取一个检测点,硬度曲线如图14所示㊂在焊缝区域任取一个点为测试起点(坐标位置0点),距离起点1mm 位置处为焊缝区域,该区域硬度最大为188HB ㊂从位置1mm 点开始,硬度快速下降㊂距起点位置1~2mm 区域为焊接热影响最大的区域,最低硬度为116HB ;距起点位置2~6mm 区域硬度逐步上升,位置6mm 点硬度152HB ,接近母材硬度(ȡ150HB ),焊缝热影响区域在1~6mm 范围㊂本次故障件开裂区域距离焊缝10mm ,因此焊缝热影响区对本次失效基本关联㊂图13㊀抽检试样图14㊀焊缝热影响区硬度梯度(2)焊渣的影响:沿图13箭头2方向进行硬度梯度检测,每隔0.2mm 取一个检测点,硬度曲线如图15所示㊂在焊渣区域任取1点为测试起点(坐标位置0点),距离起点0.2mm 位置处为焊渣区域,该区域硬度最大321HB ㊂从位置0.2mm 点开始,硬度快速下降㊂距起点位置0.2~0.4mm 区域为焊渣热影响最大的区域,最低硬度为137HB ;距起点位置0.4~0.6mm 区域硬度逐步上升,位置0.6mm 点硬度152HB ,接近母材硬度(ȡ150HB ),焊渣热影响区域在0.2~0.6mm 范围㊂从故障件分析来看裂纹有沿焊渣扩展趋势,焊渣对本次故障可能会有一定的影响,但不是关键影响因素㊂图15㊀焊渣热影响区硬度梯度通过以上分析,导致失效的主要原因是道路试验工况整车X 方向作用力大,后壳盖承载能力不足,需要对壳盖的材料进行重新选型㊂4㊀解决措施及验证根据路谱采集的结果,后壳盖材料选择热轧板SAPH440,屈服强度不小于305MPa ,抗拉强度不小于440MPa ㊂按照图12方式进行台架验证,完成80万次循环后,检查后壳盖是否开裂㊂原状态试样在完成80万次台架循环,后壳盖出现开裂;新材料试样,完成80万次循环,后壳盖未开裂,继续进行台架试验至185次循环,试样无裂纹,试验停止㊂台架试验寿命至少提升1.3倍以上,新状态样件也顺利通过整车道路试验考核㊂5㊀结束语综上所述,后壳盖失效是在整车X 向作用力下,后壳盖强度不足引起的㊂在实际工作中,后壳盖通常与桥壳壳体一起组成总成件,按行业标准‘QC /T533 1999㊀汽车驱动桥台架试验方法“中驱动桥桥壳垂直弯曲疲劳试验进行验证,往往忽略了来自整车X 方向作用力的台架验证㊂本文阐述的后壳盖开裂是典型的失效案例,通过道路试验路谱采集和台架试验对标分析,可建立适用企业设计研发用的台架验证标准,为今后零部件开发提供理论依据,在设计初期就考虑到类似风险并规避,提高开发效率㊂参考文献:[1]刘惟信.汽车车桥设计[M].北京:清华大学出版社,2004.[2]李亚江.焊接冶金学[M].北京:机械工业出版社,2007.[3]刘春廷.材料力学性能[M].北京:化学工业出版社.2009.[4]邓开豪.汽车桥壳焊缝漏油原因分析及改进措施[J].装备制造技术,2008(4):131-132.[5]李晓丽,王俊杰,路强.汽车驱动桥后盖焊缝㊁渗油漏油原因分析及改进措施[J].汽车实用技术,2015(7):110-111,116.。
325M矿用汽车后桥壳体总成失效的潜在因素及修复分析

速器 总成拆 卸 出来 , 可 以用 相 似 的方 法 把 主 减 速 也 器及 差速 器总成 安 装 回到 汽车 后 桥 壳 中 , 样 就 大 这
大地 减少 了汽 车主 减速器 及差 速器 总成 的拆 装工 作
中抢 修汽 车 主减 速 器及差 速器 方面 的故 障时 提供 了
汽 车 2 1 年 第 3期 01
在 原 设计 中 , 因主 体 结 构庞 大 , 构 复杂 , 结 在设
・
2 ・ O
矿
用
★ 使 用 与 维修 ★
延续 后桥 壳体 的利 用率 。
3 后桥 壳体 修复分析建议
后桥 壳 体 的制 造 工 艺 复 杂 , 格 较 贵 , 货 期 价 购 长 。如果 按 着科 学规 范 的工 艺 标 准 修 复 后 , 为 企 可
附图
后桥 壳体 图
3 2 两端 A面 上各 3 - 1 . o-
. r
( 2牙/ ) 纹 通 孔 1 时 螺
以上修 复建议 仅 作为后 桥 壳体修 复参 考 。
参 考 文 献
若 有 损坏应 在原 位 置上 改扩 成 M4 纹孔 2 2螺 X 3 3 在上 述 改扩 之螺 孔 中 , . 拧入 预 先作 之螺 纹孔 套
( ) 代 的整 体结构 焊 接 完成 后 , 行 构 件 整 体 回火 处 进 理 , 进行 机加 工 , 完全 可 以消除 潜在 的结 构变形 再 就
后桥 壳体 总成 , 是安 装主 减速 器 ( 速器 )半 轴 差 、 套管 、 制动器 总成 、 边行 星减 速 器 总 成 、 动半 轴 轮 传 等 , 到支 撑与保 护作 用 的关键 大 型主体 单元 部件 , 起 它又是 行驶 系 中 的大型组 合件 之一 。 为 了在深层 上 分 析 后桥 壳 体 失 效 的潜 在 因 素 , 做到修 复后 达 到其装 配标 准 , 以保证 车辆 正 常运行 , 仅作 以下分 析 , 其 修复 中参 考 。 作
汽车后桥板簧的断裂分析

汽车后桥板簧的断裂分析摘要:整车可靠性耐久道路试验中,后桥板簧是重要试验验证对象,是影响整车性能的重要因素之一。
本文通过对耐久性道路试验中的后板簧断裂现象,应用设计复核、宏观分析、微观分析、金相分析、硬度检测等技术手段开展分析判断,阐述了后桥板簧表面凹坑缺陷、后悬架无减振器是造成板簧早期断裂的关键及实施优化的设计方案,为后续车型开发提供必要的经验积累。
关键词:汽车后桥板簧断裂前言板簧是汽车悬架系统的弹性元件,具有可靠性好、结构简单、制造工艺流程短、成本低等优点。
车板簧一般是由若干片不等长的簧片组成,簧片按照一定的组合方式使得板簧呈现线性或非线性弹性特征,在悬架系统中起到缓冲作用。
汽车在非平整路面上行驶时,在交互冲击载荷作用下,各片板簧有相对的滑动而产生摩擦,产生一定的阻力,促使车身的振动衰减。
板簧结构在商用车及轻小型车辆上应用广泛,实际应用场景中,在交变应力下板簧可能发生疲劳和断裂,故板簧应具有较高的疲劳强度和耐蚀等性能。
一、后板簧断裂案例某汽车后悬架根据该车型的总质量、底盘布置等特点,采用板簧结构,用于连接车身与后桥,且不装后减振器。
主要由三片不等长的钢板弹簧组成,并用夹箍将三片板簧固定,防止各簧片横向错位,在弹簧回弹将力传递给其他片,减少主板簧片的应力。
后悬架采用板簧结构,开发阶段需在试验场进行道路耐久试验验证,试验场给汽车提供各种类型的路面试验条件,满足零件的耐久试验要求。
在可靠性耐久道路试验中,3台试验车均出现了后钢板弹簧断裂的情况,在第一片到第三片板簧均有发生断裂情况。
二、后板簧断裂原因探讨为确定后桥板簧断裂的根本原因,应用设计复核、金相分析、硬度检查等技术手段开展分析。
1、设计复核应用CAE软件对板簧设计进行复核,对板簧应力分析结果与已量产车型进行横向对比,根据分析结果并结合设计经验,板簧设计满足设计要求。
按汽车行业标准QC/T 29035-1991对板簧进行强度台架测试,测试结果均不低于试验标准(板簧的疲劳寿命不小于8万次)。
某轻卡桥壳制动气室支架底座焊接处撕裂分析及改进

某轻卡桥壳制动气室支架底座焊接处撕裂分析及改进作者:杨小见张硕猛耿广锐孙磊宁忠翼来源:《汽车科技》2019年第04期摘; 要:某轻卡在道路试验过程中出现后桥桥壳左侧制动气室支架焊接处撕裂拔起的危险情况,本文通过焊接失效分析得到焊接处撕裂原因,预测了撕裂起源位置,并通过有限元分析模拟轻卡后桥桥壳制动气室支架底座焊接处强度载荷工况,并对其气室支架底座结构及焊接方式进行改进设计,降低了各工况下桥壳的最大应力值,使其满足设计要求,规避风险。
关键词:轻卡;桥壳;撕裂;气室支架底座;CAE 分析中图分类号:U466; ; 文献标识码:A; ; 文章编号:1005-2550(2019)04-0082-04Abstract: During the road test of a light truck,the dangerous situation of tearing and pulling out at the welding place of the brake chamber bracket on the left side of the rear axle bridge shell.In this paper, the causes of tearing at welded joints are obtained by welding failure analysis, the origin of tearing is predicted, and the strength load condition of the brake chamber bracket is simulated by finite element analysis.The structure and welding method of the brake chamber bracket are improved and designed to reduce the maximum of the axle bridge shell each working condition stress value, and to meet the design requirements and avoid risks.某轻型载货车在坏路试验中行驶4282km时,后桥桥壳左侧制动气室支架焊接处撕裂拔起,如图1所示。
微型汽车后桥半轴力学分析及断裂分析

轴的头部商径很大,另一端花键处到 轴承安装处直径相对很小,如果采用整体 锻造在头部镦出巾124直径是很困难的成
本也较高。所以采用摩擦对焊的工艺对截 面选在弯曲力矩很小的地方。另外在图l所 示的区域进行中频表面淬火,表面硬度 HRC50一60心部硬度HRC25—32,这样可以 提高疲劳强度。半轴材料采用45号钢。
万方数据
科技创业家TECHNOLOGICAL P10NEERs
1 49
有纵向力和侧向力作用,所以半轴只受垂 向弯矩:
垂向力F,,最大,纵向力F。,=O,侧向力 F,,=0:此时垂直力最大值F,:为:
F:2L=F:2R=K(G 2/2一g。)=807l(N) 其中K为动载系数K=1.8,
而魄r=足ב2£×6=282.49(N’m)
该半轴按照工艺规范生产并检验合格 后装车。在试车过程中发生断裂,对断裂件 的原材料成分进行了光谱分析,其结果符 合有关技术标准,为弄清楚该半轴早期断 裂的原因,本文对其硬度、显微组织、宏观 及微观端【J进行了研究。 3.1试验方法
首先l记录并分析断口宏观形貌,然后 用酒精等将端口表面清洗干净.用扫描电 子显微镜做断u微观形貌分析,用光学显 微镜对半轴表层和心部显微组织进行研 究,|一l时测定了其硬度。
4结论 45#汽车后桥半轴中存在较多的铁素
体是造成半轴疲劳断裂的原因。应该在生 产中找出造成调质淬火工艺温度不正确的 原因,并予以改正,使后桥半轴的调质组织 和硬度符合技术要求。
(a)纵向 (a)Lห้องสมุดไป่ตู้ngthwise section
(b)纵向 (b)Transverse section
某驱动桥半轴套管断裂分析和优化设计

某驱动桥半轴套管断裂分析和优化设计发表时间:2018-10-29T10:11:01.057Z 来源:《知识-力量》2018年11月上作者:张瑞华穆玉峰[导读] 后桥是汽车的关键零部件,起着承受载荷和扭矩的作用,一旦出现断裂,将严重影响乘客的生命安全,故对其失效模式分析尤为重要。
本文对一款新型后桥在道路试验过程中发生半轴套管断裂的失效模式进行分析,通(精诚工科汽车系统有限公司,河北保定 071000)摘要:后桥是汽车的关键零部件,起着承受载荷和扭矩的作用,一旦出现断裂,将严重影响乘客的生命安全,故对其失效模式分析尤为重要。
本文对一款新型后桥在道路试验过程中发生半轴套管断裂的失效模式进行分析,通过材质检测及理论计算,对失效因素进行排查。
最终找到失效原因,并提出改进措施,避免再次失效,对提高汽车的安全性意义重大。
关键词:驱动桥;半轴套管;断裂引言驱动桥壳起着支撑汽车载荷的作用,同时还要承受制动载荷、静载荷所引起的较大弯矩和扭矩。
一旦桥壳出现断裂,将会影响整车安全,故对桥壳断裂失效模式分析意义重大。
现某公司有一款新设计后桥在搭配汽车进行道路试验可靠性试验过程中,行驶至强化路的石坏路时,左后驱动桥半轴套管发生断裂,需立刻分析原因并制定整改措施,避免再次失效断裂。
1、基本情况某厂生产的两根不同批号的汽车半轴套管在使用过程中发生断裂,断裂情况类似,均发生于中的R2.5mm过渡圆角处。
对其中一件半轴套管进行了断裂分析。
图纸要求半轴套管采用45Mn2钢管生产,产品硬度要求为220~270HBW。
2、加工工艺分析将该桥的未断裂边拆解后,需对轮毂内轴承颈R角进行测量为4mm,设计要求为4~4.4mm,故该内轴承颈R角是符合设计要求,但在R 角根部与轴承颈之间存在一台阶,此台阶在设计中是不存在的,此处R角仅有1mm,将会引起应力集中,容易产生裂纹。
针对台阶产生的问题进行一番调查后,发现是由于轴承颈需要经过粗车-精车-磨削三个步骤,在实际操作中,磨削轴承颈时并未磨轮毂内轴承颈R角,导致产生台阶。
客车车身骨架局部开裂问题分析与改进

客车车身骨架局部开裂问题分析与改进摘要:随着计算机科学技术的不断发展,国内外众多学者在客车坚固化方面做出了深入的研究。
利用灵敏度分析和遗传算法相结合的方法对客车车身进行优化设计,使客车质量得到了加固,完成了对客车车身的坚固化设计。
关键词:客车车身;骨架局部;开裂问题引言我国地区道路情况复杂多样,客车行驶在盘山公路或崎岖的道路上,车身骨架会受到反复弯扭复杂工况作用,若结构设计不合理,容易导致客车骨架局部开裂,造成行驶过程中的巨大安全隐患。
对于局部开裂早期的解决方法多数是凭借工程经验进行加强改进,随着计算机技术的高速发展,CAE有限元法在解决骨架局部开裂问题分析与改进中得到了较好的应用,同时可在设计方案阶段,充分优化与验证结构设计,为提高客车可靠性和安全性上提供了有效的方法。
1蒙皮开裂问题分析出现蒙皮开裂问题的试制车是一款纯电动客车,底盘车架由高强度钢焊接而成,车身前后围、左右侧围和顶围材料均为铝合金,连接以铆接为主、焊接为辅。
该试制车在进行汽车道路可靠性试验中,进度完成约40%时中门顶部出现蒙皮开裂问题。
根据路试工程师的描述,在进行可靠性试验过程中,整车中部抖动较明显,初步分析认为蒙皮开裂是由车身刚度不足造成的。
1.1有限元模型建立建立有限元模型时,用Hypermesh进行前处理。
为方便建模,忽略蒙皮和内外饰件等非主要承载结构,只保留客车骨架等主要承载结构。
车架和车身等主要承载结构全部采用壳单元模拟,焊接用刚性杆单元RBE2模拟焊缝,铆接则在接头与接触型材之间分布适当数量的RBE2单元来近似模拟铆钉连接,车架和车身之间通过牛腿连接。
在进行刚度分析时,对整车不加其他载荷,包括空调、电池、玻璃、地板及地板革、仪表台、控制器、座椅和驾驶员、乘客等质量,但进行强度分析时,则需按实际情况加载。
1.2进行弯曲刚度分析时不考虑重力,分别约束左后轮空气弹簧安装座处X,Y和Z方向与右后轮空气弹簧安装座处X,Z方向的平动自由度和左前轮空气弹簧安装座处Y,Z方向与右前轮空气弹簧安装座处Z方向的平动自由度。
某车型后背门开裂问题分析及解决

某车型后背门开裂问题分析及解决李国亮;辛勇;师德钦【摘要】由于某车型后背门受力较大且比较集中,其后背门铰链安装点处钣金在前期道路试验中,多次出现疲劳开裂问题.为解决此问题,通过CAE分析,对耐久强度薄弱点直接进行加强,并对后背门限位方式进行优化,有效地提高了安装点强度,并减小行车中后背门摆动,成功地消除了该位置的疲劳开裂.【期刊名称】《汽车工程师》【年(卷),期】2014(000)009【总页数】2页(P54-55)【关键词】铰链安装点;疲劳开裂;CAE分析;后背门【作者】李国亮;辛勇;师德钦【作者单位】海马轿车有限公司;海马轿车有限公司;海马轿车有限公司【正文语种】中文某车型在海南试验场进行道路耐久试验时,多次反馈后背门上部铰链安装面出现焊点及钣金开裂问题。
文章结合CAE分析的结果和该部位结构及受力特点,提出了一系列优化方案,最终通过了道路试验验证,问题得到成功解决。
1 问题分析1.1 问题情形该车型前期开发时,在不同的道路试验里程出现后背门铰链安装点处,钣金和焊点开裂,开裂情形,如图1和图2所示。
裂纹从焊点处发展,向外延伸,随试验进行不断扩展。
图1 铰链安装面开裂情况1图2 铰链安装面开裂情况2对出现该问题的试验车和其行驶里程进行统计,如表1所示。
表1 某车型后背门试验问题统计表试验里程无法达到预期的要求,且试验车出现开裂频次很高,需要有针对性地进行强度分析,进行优化整改。
1.2 开裂区域耐久强度分析对后背门该部位进行耐久强度分析,分析结果,如图3所示。
从图3可以看出,可以看到铰链安装部位钣金存在4个主要疲劳损伤点,与道路试验中反馈的开裂部位完全一致。
按照前期设定的目标,损伤值不能超过0.2,否则开裂风险会大大增加。
图3中数值为分析计算的疲劳耐久累积损伤值与目标设定值的比值,要求BM(车身基础材料)≤0.2,S(焊点)≤1.0,W(焊缝)≤1.0,图3中红色和紫色区域即表示已超过目标值。
图3 后背门开裂区耐久强度分析结果该车型耐久强度分析是通过实测,获取标准工况下作用在车轮上的载荷谱,再通过多体动力学计算分解到白车身与悬吊系统的连接点上,结合有限元的非线性强度分析和失效疲劳分析,完成对基于实测载荷下的疲劳寿命的计算和预测,分析过程,如图4所示。
ZG40Cr车桥桥壳断裂原因分析与改进

四川兵工学报
ZG40Cr车桥桥壳断裂原因分析与改进
张小忠
重庆大扛信达车辆股份有限公司,重庆401321 捕要:分析重车车桥桥壳(材料zG帅o JB/r64∞一1992)的断裂原周,提出改进措施 关t词:挢壳断裂;机槭性能;成分控制 中田分类号:L1463 218 文献标识码:B
&:l表十镕自部分*{告格g序号4,5n挤母163.210*《&梓 2袁十斌验桥n A%.z%值§燕也*低口6有&著M提高
作者简介:张小忠(J舭),男,口川人,高级I程师.主要从事金属材料与热蛐理的I艺技术研究
张小忠:ZG40Cr车桥桥壳断裂原因分析与改进
是否全部都进行了正火都无法确定.
115
3断裂原因分析
生产过程不能使铸件质餐满足产品机械性能指标的 要求.从试验报告中可见断裂桥的机械性能指标A%,z% 值(延伸率与断面收缩率)详见报告,与标准要求差距过 大,也与金相组织的分析结果是相对应的.由此导致其铸 件材料的韧性大大降低,抵抗产生脆断的能力不足. 以上分析显示,该铸钢公司生产的车桥桥壳毛坯产品 生产过程质量失控,产品存在重大质量隐患,也给问题产 品的追溯造成极大的困难. 2)随即公司对该铸钢公司下达了停止供货,限期进行 质量整改的通知. 3)对公司内部的生产过程与工艺质量的检查显示该 批产品的加工无异常.
实验的2件桥壳分别宴物取样.进行的理化对№分析结果
如表1 表中未列出的指标:抗拉强度6b(N/tmF)、屈服强度t
等I作,吼查证失效原因
2)将在库相邻批扶的谈产品车桥抽样到有资质的检 验机构再改进行疲劳试驻,“验证强度同时*月对公司
(Ⅳ瑚F)厦硬度哪值等基本满足标准要求
表1女R柞与4过试验柞日点》、性n时E
某SUV轮罩开裂问题的分析及设计改进
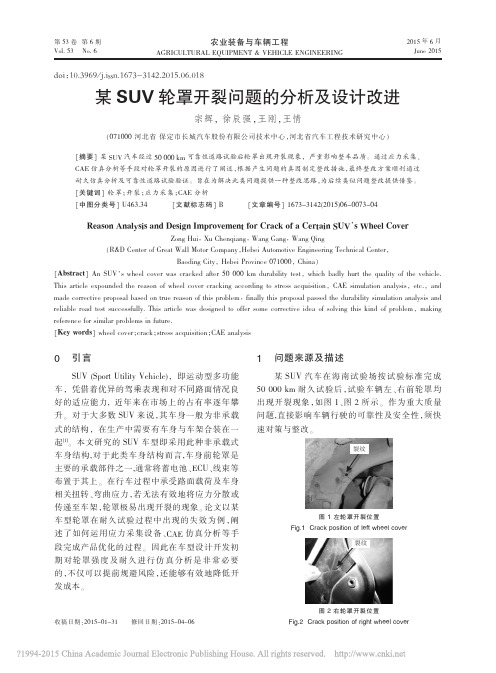
0 引言
SUV (Sport Utility Vehicle), 即运动型多功能 车, 凭借着优异的驾乘表现和对不同路面情况良 好的适应能力, 近年来在市场上的占有率逐年攀 升。 对于大多数 SUV 来说,其车身一般为非承载 式的结构, 在生产中需要有车身与车架合装在一 起[1]。 本文研究的 SUV 车型即采用此种非承载式 车身结构,对于此类车身结构而言,车身前轮罩是 主要的承载部件之一,通常将蓄电池、ECU、线束等 布置于其上。 在行车过程中承受路面载荷及车身 相关扭转、弯曲应力,若无法有效地将应力分散或 传递至车架,轮罩极易出现开裂的现象。 论文以某 车型轮罩在耐久试验过程中出现的失效为例,阐 述了如何运用应力采集设备、CAE 仿真分析等手 段完成产品优化的过程。 因此在车型设计开发初 期对轮罩强度及耐久进行仿真分析是非常必要 的,不仅可以提前规避风险,还能够有效地降低开 发成本。
表 4 仿真分析结果对比 Tab.4 Comparison of two structures’ simulative results
优化前
优化后
开裂点处应力寿命
左前轮罩 右前轮罩 左前轮罩 右前轮罩
材料
DC53D+Z
HC220YD+Z
屈服极限 / MPa
160
230
最大应力 / MPa
159
168
通过鉴定, 开裂制件的材质性能达到设计状 态,供应商所用材质与设计相符。 2.2 工艺过程控制原因排查
通过现场对开裂车辆确认及焊点剥离试验, 焊点均满足设计要求, 查焊装焊接设备参数亦满 足工艺标准。 故工艺过程控制不存在问题,可排除 人员技能不足及焊接设备的问题。 2.3 应力采集及仿真分析
(1)应 力 采 集 : 分 别 抽 取 同 一 批 次 生 产 的 车 辆 进行应力测试。 根据裂纹走向确定裂纹的主应力 方向, 沿该方向布置若干应变片, 贴片方向与裂 纹方向垂直[2]。 部分贴片的位置如图 4、图 5 所示。
重型载货汽车车架开裂分析与减重优化

重型载货汽车车架开裂分析与减重优化重型载货汽车的车架是整个车身的基础,负责承载车身、发动机、传动系统等各种重要部件的负荷。
然而,在长期的实际使用中,由于道路的震动、负荷的波动等因素,车架会遭受各种压力和挑战,可能会出现裂纹,严重时甚至会导致车身失稳,危及行车安全。
因此,对于重型载货汽车车架的开裂问题,需要进行深入的分析,并实施有效的减重优化措施。
首先,车架开裂的可能原因有很多,其中最常见的原因是由于车架本身的材质问题和设计问题。
例如,使用质量较差的钢材或焊接不良容易导致车架出现弯曲、变形、脆化等问题;车架的结构设计不合理或过于复杂,容易形成应力集中,从而导致裂纹的产生。
因此,在车架的设计、制造环节中,需要严格控制原材料的质量、加强工艺过程的监控,减少结构复杂度,同时根据承载能力和路况等因素进行科学合理的设计和结构优化。
其次,针对车架开裂问题,需要采取有效的减重措施。
重型载货汽车的质量和尺寸较大,车架是造成不必要的质量和能耗消耗的最主要原因之一,而减重不仅可以提高车架的强度和稳定性,降低物体的能量消耗,同时还能提高汽车的燃油效率,节约燃料成本。
减重的具体方案可以根据不同的实际需求进行调整,例如,采用轻量化材料,如铝镁合金、碳纤维等;减少车架结构的重量,如简化结构、减少节点数量、优化连接方式等;加强车身的信号控制和自适应控制等,从而提高汽车的驾驶效率和安全性能。
总的来说,重型载货汽车车架的开裂问题,需要从多方面进行分析和解决。
而减重优化应该是车架维护和改进的一个重要方向,通过适当的材料和结构优化,可以提高车架的稳定性和相应的经济效益。
除了材料选择和结构优化,在车架维护和改进方面,也应该考虑到合理的使用和保养。
特别是对于已经出现了开裂问题的车架,需要进行及时的维修和更换。
在日常使用中,谨慎驾驶和合理的负载分配也是避免车架开裂的重要措施。
过高的行驶速度和不合理的负载分布都会给车架带来额外的压力和挑战,而且在道路行驶时,需要注意避免颠簸和跌落等问题,保持平稳的行驶。
汽车零部件断裂失效分析简述(岑举
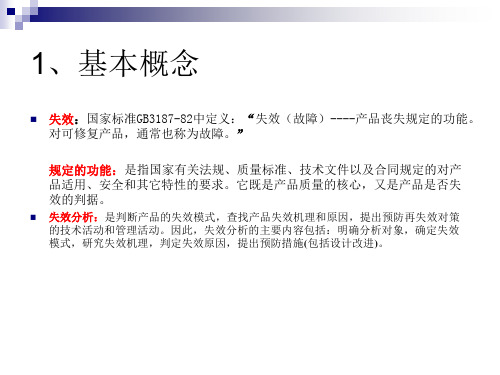
结构和配合的特性、载荷的性质和幅值、大多的内在质量缺陷、工作 和运行的状态、应力状态等等,都属于力学分析的范畴。他们不仅决 定了是否开裂,还总体上决定了以什么形式或在什么部位开裂。
设计的使用应力(各种指标)和强度(各种指标)技术条件;
关注实际的使用应力(工况)及制造质量分布的偏移和变化; 两者分布曲线相交则产生失效。 目前的失效分析和认知程度、评价主要还是在定性的水平上。
技术条件 设计应力
制造质量 使用应力、工况
2.5 断裂分析要素
从可靠性理论中断裂的应力模型得知,应力和强度是断裂分析的两大 要素,两个要素中哪一个贡献较大?最为活跃?如何地感知和评价是 断裂分析中的一个焦点;
关于灰色系统
是对内部结构可以部分了解或可以综合运用逻辑推理的方法进行 分析的系统。
从人类实践的绝对性来看,人类可以穷尽对机电失效规律及其预 防的认识,但从对失效分析的个别实践和认识来看,又总是在有 限的空间内进行的。因此,对失效特点和规律的认识又往往是有 限的和相对的,这就决定了失效分析的研究和发展总是处于一 个灰色系统内。 (失效分析的持续性、阶段性、可认知性和无止境性) (失效分析的病理学研究方法和流行病学研究方法)
式等原因引发局部产生微动磨损现 象,导致疲劳开裂。这类问题在轴 孔配合结构中最多体现。
疲劳断裂
案例20、某连杆销孔疲劳开裂 在挤压载荷作用下的疲劳开裂; 表现出了对油孔边缘处应力集中
的敏感性。
疲劳断裂
案例22、剪切应力疲劳开裂
半轴、钢板弹簧等零件,产生在高强韧性的零件中; 属于应变疲劳的性质,也称为高应力低周疲劳; 扭转的应力状态更有部件及断裂失效特性
汽车后桥壳工艺分析及解决方案

王 樑
( 安阳工学院, 河南 安阳 %&&’’’ ) 摘 要: 通过对汽车后桥壳的工艺分析, 介绍了汽车焊接式后桥在组合机床上的常规工艺流程, 并针对用户 的一些特殊要求, 提出了解决方案, 总结出一条规范可靠的加工工艺方案。 关键词: ’&()#*’ +%*’,-)- &% .$" /*0 1"*0 +2’" *%3 4.- 5&’6.)&%()*+ ,-./0 ( )/1./0 2/34-4546 78 96:;/7<701,)/1./0 %&&’’’ ,=>*) !"#$%&’$ :9;?750; 4;6 ./.<13-3 78 46:;/7<701 87? 4;6 :.? ?6.? .@<6 ,./ -/4?7A5:4-7/ 47 4;6 :7/B6/4-7/.< 46:;/7<70-:.< C?7:633 87? D6<A-/0 4;6 :.? .@<6 7/ E7A5<.? E.:;-/6 477< -3 0-B6/F 9;6 C.C6? :7E63 5C 37E6 37<54-7/3 .::7?A-/0 47 4;6 536?3G 3C6:-8-: A6E./A3 ,./A 35E3 5C . 34./A.?A ./A ?6<-.H<6 46:;/7<70-:.< C<./F ()*+,%-#:=.?;I6.? )@<6 ;)/.<13-3 78 96:;/7<701;J7<54-7/ 随着我国汽车工业的不断发展, 组合机床在汽车 行业中的应用也越来越广, 产量也越来越大, 生产周期 要求越来越短。这就要求专机生产厂家, 对一些典型 的汽车零件的加工应有一套成熟的、 可靠的工艺方案, 以缩短设计周期, 为生产提供空间, 使企业跟上市场发 展的要求。 下面就近几年来的汽车后桥壳这一典型零件的专 机工艺方案加以介绍、 分析, 并希望与各位同行共同商 榷。 再次, 采用卧式单面移动工作台钻、 攻机床完成中 间琵琶孔端面上螺纹钻孔、 攻螺纹, 见图 K 。然后采用 卧式双面钻孔机床完成两端轴承孔端面上的螺纹底孔 加工, 见图 % 。 其次, 采用卧式双面精镗机床完成两端油封孔和 轴承孔的精加工, 见图 " 。
道路桥梁施工中的裂缝原因及其改进措施探析 贺生成

道路桥梁施工中的裂缝原因及其改进措施探析贺生成摘要:道路桥梁施工过程中涉及内容多,设计、环境、材料等多方面都有可能导致裂缝问题的发生。
针对这种质量病害,积极采取有效措施,才能保证道路桥梁整体施工水平的提升。
文章主要从裂缝危害及原因入手,探讨具体的改进对策。
关键词:道路桥梁;裂缝原因;道路裂缝;改进措施引言道路桥梁裂缝是道路桥梁日常施工中比较常见的通病。
道路桥梁裂缝间接影响道路桥梁的正常应用,有一些裂缝由于受到天气、应力作用逐渐变成严重的裂缝,这样会缩短道路桥梁的使用寿命,通过分析道路桥梁中产生裂缝的原因,提出合理解决道路桥梁裂缝的措施。
1道路桥梁裂缝的危害道路桥梁裂缝的种类较多,在开展工程建设施工的过程中一旦产生施工裂缝,就会使得工程主体结构的稳定性与安全性受到影响。
这种结构损害会影响工程建设施工质量,使得道路桥梁交通难以维持稳定性。
在产生裂缝的情况下,混凝土钢筋会长期暴露在外,受到气候条件的影响导致其发生腐蚀。
道路桥梁裂缝的产生会威胁工程整体施工,使得施工进度延误,降低施工质量,还会使得施工难度增大。
2造成道路桥梁施工时出现裂缝原因的分析2.1设计初期不完善,存在缺陷设计过程中没有密切联系施工实际环境是造成裂缝出现的主要原因,对裂缝产生和发展有关的因素有很多,在进行施工现场考察时,能够发现很多可能造成裂缝的因素。
关于这些影响因素,在设计时要进行相应的标注和措施设计。
同时,在进行主体设计的过程中要严格按照行业相关规范进行设计。
2.2建筑材料存在质量问题在路桥施工中要用到的各类材料都严格的要求,材料管理也是工程管理中非常关键的部分,其中水泥、石灰石等各类材料都是有质量的要求,要达到设计对材料的各类标准。
在路桥施工的材料搅拌中,技术操作也是要符合相关规范,结合当地的气候条件以及空气质量,对温度以及风度都要进行全面考虑,让路桥施工的材料达到相关的要求,一些路桥施工中材料的控制不够完善。
混凝土的不合格,导致出现裂缝的问题。
车后桥锻压件开裂原因分析

车后桥锻压件开裂原因分析陈诚;宋锦柱【摘要】应用化学分析、机械性能检测、扫描电镜分析等对车后桥锻压件开裂原因进行了分析,结果表明:钢板次表层存在的相对集中分布的孔洞缺陷,是导致钢板热锻压成型开裂的主要原因.【期刊名称】《现代冶金》【年(卷),期】2012(040)001【总页数】3页(P17-19)【关键词】锻压件;孔洞缺陷;开裂【作者】陈诚;宋锦柱【作者单位】江苏省产品质量监督检验研究院,江苏南京210007;江苏省产品质量监督检验研究院,江苏南京210007【正文语种】中文【中图分类】TG316.1+4;TG115.2引言某公司采用16 MnR(16 mm×1.8 m×8 m)钢板生产车后桥锻压件。
一批钢板在高温锻压车后桥时,于折弯处出现多处开裂。
将锻压成型温度从780~810°C提高至920~950°C,开裂现象有所缓解,但开裂现象依然存在。
钢板执行标准为GB 6654-1996。
1 宏观分析及取样说明车后桥热锻压件开裂形貌照片见图1,这些车后桥锻压件的开裂部位完全相同,均出现在热锻压折弯最大变形处。
从宏观断口上看,断裂既不是完全沿晶的,也不是完全穿晶的,且断裂部位无明显颈缩现象,表明断裂时材料的承载能力很低(见图2)。
此外,断口表面有较厚的氧化皮覆盖,影响了断口形貌的扫描电镜微观分析。
图1 车后桥热锻压件开裂形貌照片图2 断裂部位宏观照片按GB 6654-1996要求,对尚未使用的钢板,随机选取3个批号(编号:1#~3#),各切取试样一块,用作化学元素分析及机械性能检测;选取一个开裂的完整车后桥锻压件及一条未经热锻压的原始钢板横条(长1.8 m)用作开裂原因分析;选取车后桥开裂部位切取金相试样数枚,在未经热锻压的原始钢板上切取对比金相试样一枚进行金相检验;并用扫描电镜在金相试样上进行电镜观察分析。
2 试验研究与分析2.1 化学成分分析与机械性能检测钢板化学成分、机械性能检测结果见表1。
- 1、下载文档前请自行甄别文档内容的完整性,平台不提供额外的编辑、内容补充、找答案等附加服务。
- 2、"仅部分预览"的文档,不可在线预览部分如存在完整性等问题,可反馈申请退款(可完整预览的文档不适用该条件!)。
- 3、如文档侵犯您的权益,请联系客服反馈,我们会尽快为您处理(人工客服工作时间:9:00-18:30)。
科技与企业 221
科技
汽车后桥壳开裂的分析与改进
【摘要】针对某汽车在丘陵地带矿区路上行驶过程中出现故后桥壳
一侧弹簧座附近、近似垂直于轴向短焊缝末端开裂现象,通过桥壳断口形
貌进行了宏微观观察,对桥壳基体进行了组织检查,确定了桥壳的开裂性
质,分析了开裂的可能原因并提出改进方向。
【关键词】后桥壳;分析;开裂性质;改进
随着汽车底盘技术日新月异的发展,汽车用高强度金属板材的应用
与研究已经逐步引起了汽车制造厂商的重视,关于汽车桥壳强度的分
析,有必要得到更深层次研究和开发。
1.概述
某汽车在丘陵地带矿区路上行驶过程中出现故障,停车分解检查,
发现后桥壳一侧弹簧座附近、近似垂直于轴向短焊缝末端开裂。
截止
至发现后桥壳开裂时,汽车累计行驶路程为27662km。
故障发现前司机
没有发现行车异常情况。
该桥壳为冲焊结构,首先经弯曲对接,然后用
CO
2
气体保护焊焊接成型。
桥壳材料为A510L钢。
2.试验过程与结果
2.1外观检查
板桥外观及开裂位置均在桥壳的背面,位于弹簧座附近,与车辆的
前进方向相反,沿桥壳周向分布;开裂区域未见异常损伤。
2.2断口宏观观察
断口的整体形貌显示断口表面较为平整,有少量的塑性变形。
断口
上可观察到较为明显的疲劳源区和疲劳弧线,裂纹扩展方向为沿桥壳
周向,瞬断区出现了严重的磨损。
源区起源于焊缝区外表面一侧。
为进
一步对断口进行观察,将断口放于体视显微镜下进行观察。
桥壳断口的
宏观形貌分别见图1。
由图1可以看出,桥壳的源区起源于焊缝外表面
一侧,为点源特征。
源区被少量油污覆盖,但仍能观察到明显的疲劳弧
线,弧线大小间距不等。
疲劳扩展区所占面积较小,而在整个断口上瞬
断区所占面积较大,瞬断区大部分区域都因磨损而呈现光亮。
2.3断口微观观察
将断口经超声波清洗后放入扫描电镜下观察。
桥壳断口低倍形貌
见图2a,源区的局部放大图见图2b。
从图中可以观察到明显的疲劳弧
线。
源区旁边是焊缝区,该区域存在较为严重的磨损,应为桥壳开裂后
形成,见图2c。
疲劳弧线附近的高倍形貌见图2d,该区域为疲劳条带扩
展前期,从图中可以看到少量短小的疲劳条带。
可见,瞬断区也主要以
韧窝和准解理特征为主,并伴有磨损特征。
2.4金相组织观察
分别沿平行和垂直于断口的方向即沿桥壳的横向和纵向,制取桥
壳基体的金相试样,进行组织形貌观察。
由桥壳基体横向和纵向基体的
金相组织可见主要为铁素体和颗粒状物,均存在带状颗粒物偏析。
3.分析
以上试验表明,桥壳开裂断口表面可见明显的疲劳弧线、疲劳条带
特征,可见发生了疲劳开裂。
断口观察表明,桥壳开裂断口呈疲劳开裂
特征,间距大小不等的疲劳弧线形貌则表明开裂过程中经历了受力大
小不等的多个阶段。
桥壳断口裂纹源均位于桥壳表面,为点源特征。
裂
何清 柴龙 刘朋朋
保定长城汽车桥业有限公司 河北保定 071000
纹源附近均未见气孔、夹杂和加工缺陷等特征。
金相组织分析表明,桥
壳基体组织中含有带状颗粒物偏析,但偏析程度较弱,对桥壳疲劳性能
影响较小。
桥壳开裂应该是由于承受较大应力较大引起。
后桥壳的功能
是支承汽车重量,工作过程中的受力特征非常复杂,除了受弯矩的作用
还有扭矩的作用,并承受由车轮传来的路面冲击载荷作用。
桥壳的疲劳
寿命不仅随冲击载荷的应力幅和应力循环次数增大而减小,同时与所
承受的应力平均值的大小密切相关。
综上所述,桥壳工作过程受到较大
应力作用,在易于萌生裂纹、工作应力较大的焊缝区域萌生裂纹。
裂纹
萌生后在疲劳载荷的作用下逐渐扩展,最终导致桥壳开裂。
4.结论及建议
1.桥壳的开裂性质为疲劳开裂,在焊缝区域萌生裂纹,因此为提升
焊缝区质量将CO
2
气体保护焊改为混合气体保护焊(Ar、CO
2
),并对焊
接参数进行调整,从而保证焊缝质量;
2.桥壳疲劳开裂主要由工作过程中受到较大应力作用引起,为增
加桥壳的承载能力可以考虑增加桥壳轴管直径或增加垫板长度。
参考文献
[1]机械工程材料测试手册:物理金相卷/机械工业部科技与质量监
督司.中国机械工程学会理化检验分会边.-沈阳:辽宁科学技术出版社,
1999.11.
[2]Brant C L,Banerji S K. International Metals Reviews,1978,23(4):164.
[3]Part Y J,Bernstein I M.Metall.Trans,1979,10A(11):1653.
[4]《汽车工程手册》编辑委员会.汽车工程手册设计篇[M].北京:人民交
通出版社,2001.
[5]焊接工程师手册/陈祝年编著.- 2版.-北京:机械工业出版
社,2009.10.
a b
图1 桥壳断口宏观形貌
图2 桥壳断口微观形貌DOI:10.13751/ki.kjyqy.2015.14.210。