模具表面处理
模具表面处理技术

模具表面处理技术1. 概述模具是现代工业生产中不可或缺的工具,广泛应用于汽车制造、电子产品、玩具制造等行业。
模具的使用寿命和性能与其表面处理技术密切相关。
好的表面处理技术可以提高模具的耐磨性、防腐性和光洁度,从而延长模具的使用寿命和保证产品质量。
本文将介绍几种常见的模具表面处理技术,包括镀铬、氧化、喷涂和抛光等。
2. 镀铬技术镀铬是一种常见的模具表面处理技术。
在镀铬过程中,通过将金属镀铬在模具表面,可以形成一层坚硬的保护膜。
这层膜具有良好的耐磨性和耐腐蚀性,可以有效延长模具的使用寿命。
镀铬技术对于高温和高压环境下的模具尤为重要,可以保护模具免受腐蚀和氧化的影响。
3. 氧化技术氧化是一种将模具表面转化为氧化膜的技术。
氧化膜具有良好的抗腐蚀性和电绝缘性能,可以保护模具免受外界环境的影响。
同时,氧化膜还可以增加模具的硬度,提高其耐磨性。
氧化技术通常可以通过电解氧化、化学氧化或热氧化等方式实现。
4. 喷涂技术喷涂技术是一种将特殊涂层喷涂在模具表面的技术。
这些涂层可以提供模具表面额外的保护,增加其耐磨性和耐腐蚀性。
常见的喷涂涂层包括硬质涂层、陶瓷涂层和聚合物涂层等。
喷涂技术具有灵活性高、成本较低和加工周期短的特点,在模具制造中得到广泛应用。
5. 抛光技术抛光技术是一种将模具表面通过机械或化学方法进行抛光的技术。
抛光可以提高模具表面的光洁度和平整度,减少产品表面的摩擦和磨损。
抛光可以通过不同的抛光材料和工艺来实现,如砂纸抛光、金刚石抛光和磨料抛光等。
抛光技术对于模具的外观质量和产品质量有重要影响。
6. 总结模具表面处理技术是保证模具使用寿命和产品质量的关键因素。
不同的表面处理技术可以根据模具的具体需求选择使用,如镀铬技术适用于高温和高压环境下的模具,氧化技术适用于要求高度耐腐蚀性的模具。
喷涂技术和抛光技术则可以根据具体的模具材料和使用条件进行选择。
综合运用这些表面处理技术,可以大大提高模具的使用寿命和产品质量,满足不同行业的生产需求。
模具表面涂层处理的6种方式
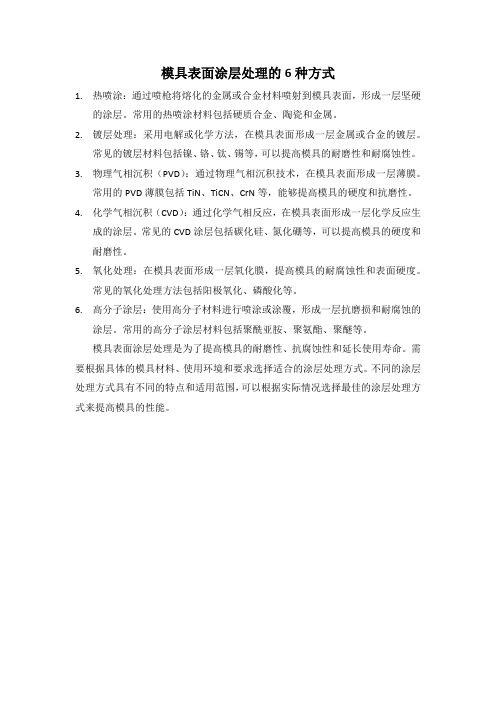
模具表面涂层处理的6种方式
1.热喷涂:通过喷枪将熔化的金属或合金材料喷射到模具表面,形成一层坚硬
的涂层。
常用的热喷涂材料包括硬质合金、陶瓷和金属。
2.镀层处理:采用电解或化学方法,在模具表面形成一层金属或合金的镀层。
常见的镀层材料包括镍、铬、钛、锡等,可以提高模具的耐磨性和耐腐蚀性。
3.物理气相沉积(PVD):通过物理气相沉积技术,在模具表面形成一层薄膜。
常用的PVD薄膜包括TiN、TiCN、CrN等,能够提高模具的硬度和抗磨性。
4.化学气相沉积(CVD):通过化学气相反应,在模具表面形成一层化学反应生
成的涂层。
常见的CVD涂层包括碳化硅、氮化硼等,可以提高模具的硬度和耐磨性。
5.氧化处理:在模具表面形成一层氧化膜,提高模具的耐腐蚀性和表面硬度。
常见的氧化处理方法包括阳极氧化、磷酸化等。
6.高分子涂层:使用高分子材料进行喷涂或涂覆,形成一层抗磨损和耐腐蚀的
涂层。
常用的高分子涂层材料包括聚酰亚胺、聚氨酯、聚醚等。
模具表面涂层处理是为了提高模具的耐磨性、抗腐蚀性和延长使用寿命。
需要根据具体的模具材料、使用环境和要求选择适合的涂层处理方式。
不同的涂层处理方式具有不同的特点和适用范围,可以根据实际情况选择最佳的涂层处理方式来提高模具的性能。
模具表面处理技术

第一节 模具表面处理概述
一、模具表面处理的意义
模具在现代生产中是生产各种工业产品的重要工艺装 备。随着社会经济的发展,特别是汽车、家电工业、航 空航天的迅猛发展,对模具工业提出了更高的要求。如 何提高模具的质量、使用寿命和降低生产成本成为当前 迫切需要解决的问题。
模具在工作中除了要求基体具有足够高的强度和韧性 的合理配合外,其表面性能对模具的工作性能和使用寿 命至关重要。模具性能的改善,单纯依赖基体材料的改 进和提高是非常有限的,也是不经济的,而通过表面处 理技术,往往可以收到事半功倍的效果,这也正是表面 处理技术在模具生产中得到迅速发展的原因。
第二节模具表面的化学热处理技术
渗氮的缺点
工艺复杂,成本高,氮化层薄。因而主要 用于耐磨性及精度均要求很高的零件,或要求 耐热、耐磨及耐蚀的零件。例如精密机床丝杠、 镗床主轴、气轮机阀门和阀杆、精密传动齿轮 和轴、发动机汽缸和排气阀以及热作模具等。
第二节模具表面的化学热处理技术
1、气体渗氮
气体渗氮在密闭的渗氮罐内进行。工件放入用镍铬不 锈、耐热钢等制成的渗氮罐内,用铬矿砂等进行密封。 通入经过干燥箱、流量计的氨气,氨气在380℃以上会 分解出活性氮原子渗入工件表面,废气通过排气管,泡 泡瓶排出炉外。一般炉内要保持30—50mm油柱的压 力。工件装入渗氮罐,密封并在加热炉内加热同时,立 即向渗氮罐内通入氨气。冷却时应随炉冷却,至炉温降 至200℃以下,停氨,出炉,开箱。
另一种是无氰液体渗碳,主要盐浴成分是氯化钠、氯 化钾和碳酸钠,加上经过加工制作的渗碳剂:碳粉、碳 化硅和尿素。
4、离子渗碳
采用甲烷或其它渗碳气 体和氢气的混合气作为辉 光放电的气体介质,在渗 碳温度(例如930℃)下, 利用辉光放电对工件表面 进行离子渗碳。
模具表面处理
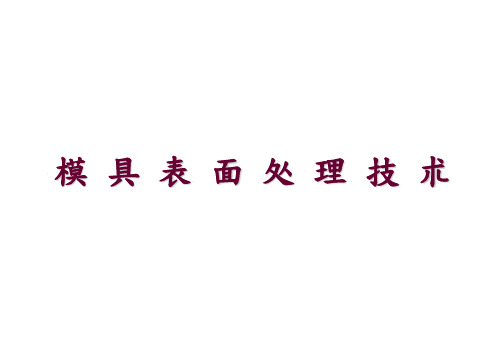
目
录
一﹑模具常規热处理 二﹑模具強韌化处理 三﹑模具化学热处理 四﹑其它表面強化技朮 五﹑真空镀硬质涂层 真空镀硬质涂层
前
言
模具是機械工業重要的基礎工藝裝備. 模具是機械工業重要的基礎工藝裝備. 模具成形具 有效率高﹑質量好﹑節約原材料﹑降低成本等優點. 有效率高﹑質量好﹑節約原材料﹑降低成本等優點. 模具的服役条件是选择模具材料及热处理的依据. 模具的服役条件是选择模具材料及热处理的依据. 影响模具失效的因素包括模具结构﹑模具材料﹑ 影响模具失效的因素包括模具结构﹑模具材料﹑热处理 及加工工艺等. 及加工工艺等. 主要用于金屬或非金屬冷態成形,承受拉伸﹑ 冷作模具主要用于金屬或非金屬冷態成形,承受拉伸﹑彎 壓縮﹑沖擊﹑疲勞等不同應力作用, 曲﹑壓縮﹑沖擊﹑疲勞等不同應力作用,而用于金屬冷 冷镦﹑冷拉伸的模具还要承受300℃ 300℃左右的交變溫 挤﹑冷镦﹑冷拉伸的模具还要承受300℃左右的交變溫 度作用. 度作用. 薄板冲压模主要失效形式是磨损,所以模具用钢要求 薄板冲压模主要失效形式是磨损, 主要失效形式是磨损 Cr4 MoV(120) CrNiSiMnMoV(GD) 具有高的耐磨性.Cr4W2MoV(120)﹑6CrNiSiMnMoV(GD)﹑
淬火后必须回火. 淬火后必须回火.
回火: 回火:
将淬火钢重新加热到A1点以下的预热温度, 将淬火钢重新加热到A1点以下的预热温度,保温预 A1点以下的预热温度 定时间,然后冷却下来.以消除含碳过饱和之马氏体、 定时间,然后冷却下来.以消除含碳过饱和之马氏体、 过冷残余奥氏体以及高密度位错、 过冷残余奥氏体以及高密度位错、大量相界面等晶体 缺陷、淬火应力等不稳定因素. 缺陷、淬火应力等不稳定因素. •低温回火: (150~200℃),得到回火马氏体组织,硬而耐 低温回火: (150~200℃),得到回火马氏体组织 得到回火马氏体组织, 低温回火 强度高,耐疲劳.多用于刃具, 冷冲模具等. 磨,强度高,耐疲劳.多用于刃具,量,冷冲模具等. •中温回火: (400~500℃),得到回火屈氏体组织,弹性好, 中温回火: (400~500℃),得到回火屈氏体组织 弹性好, 得到回火屈氏体组织, 中温回火 用于弹簧处理. 用于弹簧处理. •高温回火: (500~650℃),得到回火索氏体组织,强度和 高温回火: (500~650℃),得到回火索氏体组织 得到回火索氏体组织, 高温回火 韧性综合性能高. 用于轴类,连杆,连接件. 韧性综合性能高. 用于轴类,连杆,连接件.高温软化 回火,回火温度低于A1(20~24℃),得到回火珠光体组织, A1(20~24℃),得到回火珠光体组织 回火,回火温度低于A1(20~24℃),得到回火珠光体组织, 工艺性能好. 工艺性能好.
模具的表面处理技术

模具的表面处理技术模具在工作中除了要求基体拥有充足高的强度跟韧性的合理搭配外,其表面性能对模具的工作性能跟运用寿命至关紧要。
这些表面性能指:耐磨损性能、耐腐蚀性能、摩擦系数、疲乏性能等。
这些性能的改善,单纯倚靠基体材料的改进跟提升是非常有限的,也是不经济的,而通过表面处理技术,往往能够收到事半功倍的效果,这也正是表面处理技术得到快速进展的原因。
模具的表面处理技术,是通过表面涂覆、表面改性或复合处理技术,更改模具表面的形态、化学成分、组织结构跟应力状态,以取得所需表面性能的系统工程。
从表面处理的方式上,又可分为:化学方法、物理方法、物理化学方法跟机械方法。
虽然旨在提升模具表面性能新的处理技术连续涌现,但在模具制造中应用较多的重要是渗氮、渗碳跟硬化膜沉积。
渗氮工艺有气体渗氮、离子渗氮、液体渗氮等方式,每一种渗氮方式中,都有若干种渗氮技术,能够适应不一样钢种不一样工件的要求。
由于渗氮技术可形成优良性能的表面,而且渗氮工艺跟模具钢的淬火工艺有良好的协调性,同时渗氮温度低,渗氮后不需白热化冷却,模具的变形微小,因此模具的表面强化是采纳渗氮技术较早,也是应用zui广泛的。
模具渗碳的目标,重要是为了提升模具的整体强韧性,即模具的工作表面拥有高的强度跟耐磨性,由此引入的技术思路是,用较低级的材料,即通过渗碳淬火来取代较另外材料,从而降低制造成本。
硬化膜沉积技术目前较成熟的是CVD、PVD。
为了加添膜层工件表面的结合强度,现今进展了多种加强型CVD、PVD技术。
硬化膜沉积技术zui早在工具(刀具、刃具、量具等)上应用,效果,多种刀具已将涂覆硬化膜作为标准工艺。
模具自上个世纪80时代开始采纳涂覆硬化膜技术。
目前的技术条件下,硬化膜沉积技术(重要是设备)的成本较高,依旧只在一些精密、长寿命模具上应用,假如采纳建设热处理中心的方式,则涂覆硬化膜的成本会大大降低,越来越多的模具假如采纳这一技术,能够整体提升我国的模具制造水平。
模具表面处理技术PPT课件
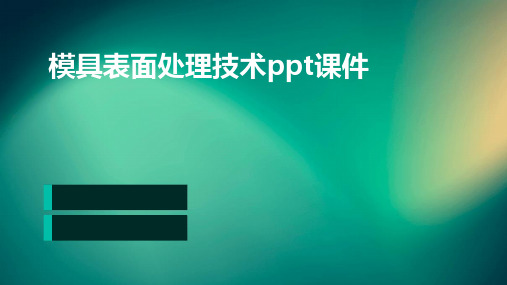
要点二
等离子喷涂技术
通过等离子喷涂将金属或非金属粉末熔融并喷射到模具表 面,形成均匀、致密的涂层,提高表面耐久性和抗腐蚀性 。
智能化和自动化技术的应用
智能监控系统
利用传感器和监测技术实时监测模具表面处理过程,实 现自动化控制和处理。
自动化处理设备
开发自动化表面处理设备,减少人工干预,提高处理效 率和一致性。
耐久性。
提高产品质量和生产效率
提高产品精度和一致性
通过表面处理技术,可以改善模具表 面的粗糙度和形貌,减小产品尺寸和 形状的误差,提高产品的精度和一致 性,从而提高生产效率。
降低生产成本
通过表面处理技术,可以提高模具的 耐磨性和耐久性,减少维修和更换模 具的频率和成本,降低生产成本。
降低生产成本
04 模具表面处理技术的优势 与挑战
提高模具使用寿命
增强模具表面硬度和耐磨 性
通过表面处理技术,可以在模具表面形成一 层高硬度的硬化层,从而提高模具的耐磨性 和抗疲劳性能,延长模具的使用寿命。
降低摩擦系数
通过表面处理技术,可以在模具表面形成一 层低摩擦系数的涂层,减小模具与材料之间 的摩擦力,降低磨损和摩擦热,提高模具的
优化生产流程
通过表面处理技术,可以优化模具的 设计和制造流程,减少加工时间和成 本,提高生产效率。
降低能耗和资源消耗
一些表面处理技术可以降低模具的能 耗和资源消耗,例如离子注入和激光 熔覆等,从而降低生产成本。
技术更新换代快
技术发展迅速
随着科学技术的不断发展,模具 表面处理技术也在不断更新换代 ,新的技术和工艺不断涌现。
常用的五金模具表面处理技术包括喷涂、电镀和化学热处理等。这些技术可以提 高模具表面的硬度和耐久性,降低生产成本和提高产品质量。
模具设计中的表面处理与耐磨性提升
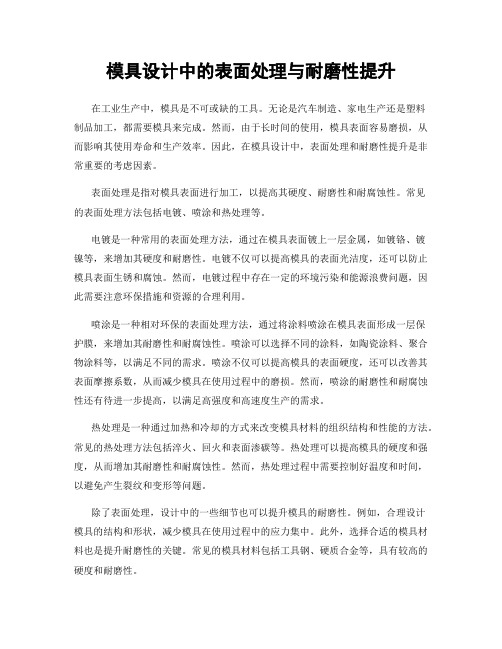
模具设计中的表面处理与耐磨性提升在工业生产中,模具是不可或缺的工具。
无论是汽车制造、家电生产还是塑料制品加工,都需要模具来完成。
然而,由于长时间的使用,模具表面容易磨损,从而影响其使用寿命和生产效率。
因此,在模具设计中,表面处理和耐磨性提升是非常重要的考虑因素。
表面处理是指对模具表面进行加工,以提高其硬度、耐磨性和耐腐蚀性。
常见的表面处理方法包括电镀、喷涂和热处理等。
电镀是一种常用的表面处理方法,通过在模具表面镀上一层金属,如镀铬、镀镍等,来增加其硬度和耐磨性。
电镀不仅可以提高模具的表面光洁度,还可以防止模具表面生锈和腐蚀。
然而,电镀过程中存在一定的环境污染和能源浪费问题,因此需要注意环保措施和资源的合理利用。
喷涂是一种相对环保的表面处理方法,通过将涂料喷涂在模具表面形成一层保护膜,来增加其耐磨性和耐腐蚀性。
喷涂可以选择不同的涂料,如陶瓷涂料、聚合物涂料等,以满足不同的需求。
喷涂不仅可以提高模具的表面硬度,还可以改善其表面摩擦系数,从而减少模具在使用过程中的磨损。
然而,喷涂的耐磨性和耐腐蚀性还有待进一步提高,以满足高强度和高速度生产的需求。
热处理是一种通过加热和冷却的方式来改变模具材料的组织结构和性能的方法。
常见的热处理方法包括淬火、回火和表面渗碳等。
热处理可以提高模具的硬度和强度,从而增加其耐磨性和耐腐蚀性。
然而,热处理过程中需要控制好温度和时间,以避免产生裂纹和变形等问题。
除了表面处理,设计中的一些细节也可以提升模具的耐磨性。
例如,合理设计模具的结构和形状,减少模具在使用过程中的应力集中。
此外,选择合适的模具材料也是提升耐磨性的关键。
常见的模具材料包括工具钢、硬质合金等,具有较高的硬度和耐磨性。
在模具设计中,还可以通过改变模具的工艺参数来提升耐磨性。
例如,合理选择切削速度、进给量和切削液等,以减少切削过程中的磨损。
此外,定期对模具进行维护和保养也是提升耐磨性的重要措施。
及时清洁模具表面的污垢和油渍,修复和更换磨损严重的部件,可以延长模具的使用寿命。
第5章 模具钢料的热处理-模具表面处理技术

第二节模具表面处理工艺概述模具是现代工业之母。
随着社会经济的发展,特别是汽车、家电工业、航空航天、食品医疗等产业的迅猛发展,对模具工业提出了更高的要求。
如何提高模具的质量、使用寿命和降低生产成本,成为各模具厂及注塑厂当前迫切需要解决的问题。
模具在工作中除了要求基体具有足够高的强度和韧性的合理配合外,其表面性能对模具的工作性能和使用寿命至关重要。
这些表面性能指:耐磨损性能、耐腐蚀性能、摩擦系数、疲劳性能等。
这些性能的改善,单纯依赖基体材料的改进和提高是非常有限的,也是不经济的,而通过表面处理技术,往往可以收到事半功倍的效果;模具的表面处理技术,是通过表面涂覆、表面改性或复合处理技术,改变模具表面的形态、化学成分、组织结构和应力状态,以获得所需表面性能的系统工程。
从表面处理的方式上,又可分为:化学方法、物理方法、物理化学方法和机械方法。
在模具制造中应用较多的主要是渗氮、渗碳和硬化膜沉积。
◆提高模具的表面的硬度、耐磨性、摩擦性、脱模性、隔热性、耐腐蚀性;◆提高表面的高温抗氧化性;◆提高型腔表面抗擦伤能力、脱模能力、抗咬合等特殊性能;减少冷却液的使用;◆提高模具质量,数倍、几十倍地提高模具使用寿命。
减少停机时间;◆大幅度降低生产成本与采购成本,提高生产效率和充分发挥模具材料的潜能。
◆减少润滑剂的使用;◆涂层磨损后,还退掉涂层后,再抛光模具表面,可重新涂层。
在模具上使用的表面技术方法多达几十种,从表面处理的方式上,主要可以归纳为物理表面处理法、化学表面处理法和表面覆层处理法。
模具表面强化处理工艺主要有气体氮化法、离子氮化法、点火花表面强化法、渗硼、TD法、CVD化学气相淀积、PVD物理气相沉积、PACVD离子加强化学气相沉积、CVA铝化化学气相沉积、激光表面强化法、离子注入法、等离子喷涂法等等。
下面综述模具表面处理中常用的表面处理技术:一、物理表面处理法:表面淬火是表面热处理中最常用方法,是强化材料表面的重要手段,分高频加热表面淬火、火焰加热表面淬火、激光表面淬火。
第十章-模具表面强化技术

*
表面化学热处理技术
二、渗氮(氮化)
(一)气体渗氮
表2 部分模具钢的气体渗氮工艺规范
牌号
处理 方法
渗氮工艺规范
渗氮层 深度/mm
表面硬度
阶段
渗氮温度/℃
时间/h
氨分解率/%
30CrMnSiA
一段
—
500±5
25~30
20~30
0.2~0.3
(一)气体渗氮
(1) 经过渗氮后钢表面形成一层极硬的合金氮化物,渗氮层的硬度一般可达到68~72HRC,不需要再经过淬火便具有很高的表面硬度和耐磨层,而且还可以保持到600~650℃而不明显下降。
(2) 渗氮后钢的疲劳极限可提高15%~35%。这是由于渗氮层的体积增大,使工件表面产生了残余压应力。
(3) 渗氮后的钢具有很高的抗腐蚀能力。
>58HRC
Cr12MoV
760~800HV
*
表面化学热处理技术
二、渗氮(氮化)
(二)离子渗氮
离子渗氮有如下特点:
(1) 渗氮速度快,生产周期短。
(2) 渗氮层质量高。
(3) 工件的变形小。
(4) 对材料的适应性强。
氮碳共渗
提高硬度、耐磨性、抗粘附性、抗蚀性、耐热疲劳性
冷挤模、拉深模、挤压模穿孔针
渗硼
具有极好的表面硬度、耐磨性、抗粘附性、抗氧化性、热硬性、良好的抗蚀性
挤压模、拉深模
碳氮硼三元共渗
提高硬度、强度、耐磨性、耐疲劳性、抗蚀性
挤压模、冲头针尖
盐浴覆层 (TD处理)
提高硬度、耐磨性、耐热疲劳性、抗蚀性、抗粘附性、抗氧化性
模具表面处理工艺
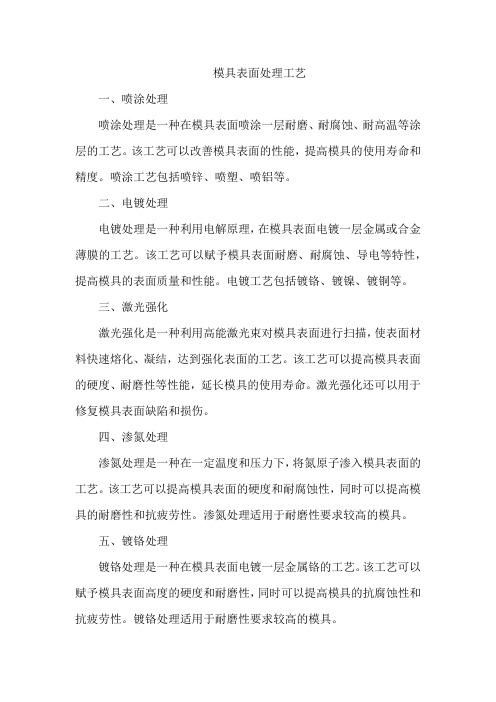
模具表面处理工艺一、喷涂处理喷涂处理是一种在模具表面喷涂一层耐磨、耐腐蚀、耐高温等涂层的工艺。
该工艺可以改善模具表面的性能,提高模具的使用寿命和精度。
喷涂工艺包括喷锌、喷塑、喷铝等。
二、电镀处理电镀处理是一种利用电解原理,在模具表面电镀一层金属或合金薄膜的工艺。
该工艺可以赋予模具表面耐磨、耐腐蚀、导电等特性,提高模具的表面质量和性能。
电镀工艺包括镀铬、镀镍、镀铜等。
三、激光强化激光强化是一种利用高能激光束对模具表面进行扫描,使表面材料快速熔化、凝结,达到强化表面的工艺。
该工艺可以提高模具表面的硬度、耐磨性等性能,延长模具的使用寿命。
激光强化还可以用于修复模具表面缺陷和损伤。
四、渗氮处理渗氮处理是一种在一定温度和压力下,将氮原子渗入模具表面的工艺。
该工艺可以提高模具表面的硬度和耐腐蚀性,同时可以提高模具的耐磨性和抗疲劳性。
渗氮处理适用于耐磨性要求较高的模具。
五、镀铬处理镀铬处理是一种在模具表面电镀一层金属铬的工艺。
该工艺可以赋予模具表面高度的硬度和耐磨性,同时可以提高模具的抗腐蚀性和抗疲劳性。
镀铬处理适用于耐磨性要求较高的模具。
六、喷丸处理喷丸处理是一种利用高速气流将弹丸喷射到模具表面,使表面材料发生塑性变形的工艺。
该工艺可以改善模具表面的粗糙度和形状精度,同时可以提高模具的抗疲劳性和耐磨性。
喷丸处理适用于各种类型的模具。
七、氧化处理氧化处理是一种将金属表面氧化成氧化膜的工艺。
该工艺可以提高模具表面的硬度和耐磨性,同时可以增强模具的抗腐蚀性和抗氧化性。
氧化处理适用于钢铁、铝合金等金属材质的模具。
八、抛光处理抛光处理是一种利用抛光机械对模具表面进行抛光加工的工艺。
该工艺可以改善模具表面的粗糙度和形状精度,同时可以提高模具的抗腐蚀性和抗疲劳性。
抛光处理适用于各种类型的模具。
九、渗碳处理渗碳处理是一种在高温下将碳原子渗入模具表面的工艺。
该工艺可以提高模具表面的硬度和耐磨性,同时可以增强模具的抗疲劳性和韧性。
模具表面处理种类及规格

Fine Fine Medel Grov
符号 VDI12 VDI15 VDI18 VDI21 VDI24 VDI27 VDI30 VDI33 VDI36 VDI39 VDI42 VDI45
粗糙度 Ra 0.40 Ra 0.50 Ra 0.80 Ra 1.12 Ra 1.60 Ra 2.24 Ra 3.15 Ra 4.50 Ra 6.30 Ra 9.00 Ra 12.5 Ra 18.0
SPIB-1
SPIC-1
SPID-1
SPIA-2
(良好脱模和外观)
SPIB-2
SPIC-2
SPID-2
SPIA-3
(良好脱模,外观无 需高光)
SPIB-3
SPIC-3
SPID-3
火花纹(Thin Fire Texture)
号码
0 1 2 3 4 5 6 7 8 9 10 11 12 13 14 15 16 17 18 19 20
MT Specification
单位:mm
咬花深度
0.0102
0.0254
0.0381
0.0508
0.0762
0.1143
0.0762
0.0762
0.0508
0.0889
0.1524
0.0635
0.0508
0.0635
0.0635
0.0698
0.1016
Ptn.# MT-11000 MT-11010 MT-11020 MT-11030 MT-11040 MT-11050 MT-11060 MT-11070 MT-11080 MT-11090 MT-11100 MT-11110 MT-11120 MT-11130 MT-11140 MT-11150 MT-11160
模具表面处理
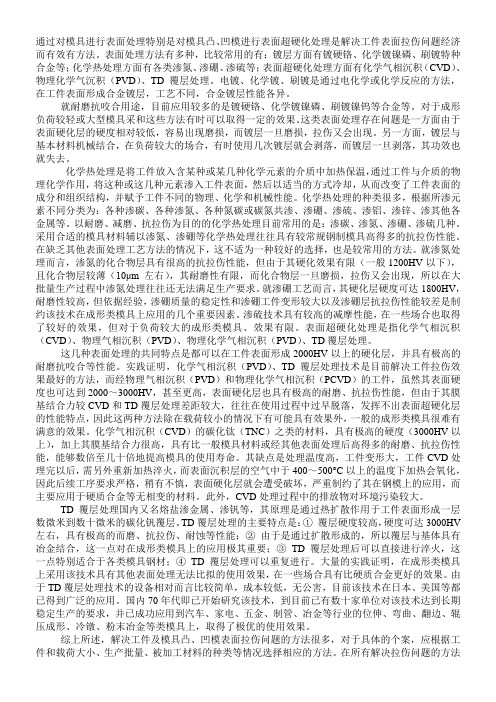
通过对模具进行表面处理特别是对模具凸、凹模进行表面超硬化处理是解决工件表面拉伤问题经济而有效有方法。
表面处理方法有多种,比较常用的有:镀层方面有镀硬铬、化学镀镍磷、刷镀特种合金等;化学热处理方面有各类渗氮、渗硼、渗硫等;表面超硬化处理方面有化学气相沉积(CVD)、物理化学气沉积(PVD)、TD覆层处理。
电镀、化学镀、刷镀是通过电化学或化学反应的方法,在工件表面形成合金镀层,工艺不同,合金镀层性能各异。
就耐磨抗咬合用途,目前应用较多的是镀硬铬、化学镀镍磷、刷镀镍钨等合金等。
对于成形负荷较轻或大型模具采和这些方法有时可以取得一定的效果。
这类表面处理存在问题是一方面由于表面硬化层的硬度相对较低,容易出现磨损,而镀层一旦磨损,拉伤又会出现。
另一方面,镀层与基本材料机械结合,在负荷较大的场合,有时使用几次镀层就会剥落,而镀层一旦剥落,其功效也就失去。
化学热处理是将工件放入含某种或某几种化学元素的介质中加热保温,通过工件与介质的物理化学作用,将这种或这几种元素渗入工件表面,然后以适当的方式冷却,从而改变了工件表面的成分和组织结构,并赋予工件不同的物理、化学和机械性能。
化学热处理的种类很多,根据所渗元素不同分类为:各种渗碳、各种渗氮、各种氮碳或碳氮共渗、渗硼、渗硫、渗铝、渗锌、渗其他各金属等。
以耐磨、减磨、抗拉伤为目的的化学热处理目前常用的是:渗碳、渗氮、渗硼、渗硫几种。
采用合适的模具材料辅以渗氮、渗硼等化学热处理往往具有较常规钢制模具高得多的抗拉伤性能。
在缺乏其他表面处理工艺方法的情况下,这不适为一种较好的选择,也是较常用的方法。
就渗氮处理而言,渗氮的化合物层具有很高的抗拉伤性能,但由于其硬化效果有限(一般1200HV以下),且化合物层较薄(10μm左右),其耐磨性有限,而化合物层一旦磨损,拉伤又会出现,所以在大批量生产过程中渗氮处理往往还无法满足生产要求。
就渗硼工艺而言,其硬化层硬度可达1800HV,耐磨性较高,但依据经验,渗硼质量的稳定性和渗硼工件变形较大以及渗硼层抗拉伤性能较差是制约该技术在成形类模具上应用的几个重要因素。
模具消光处理的流程
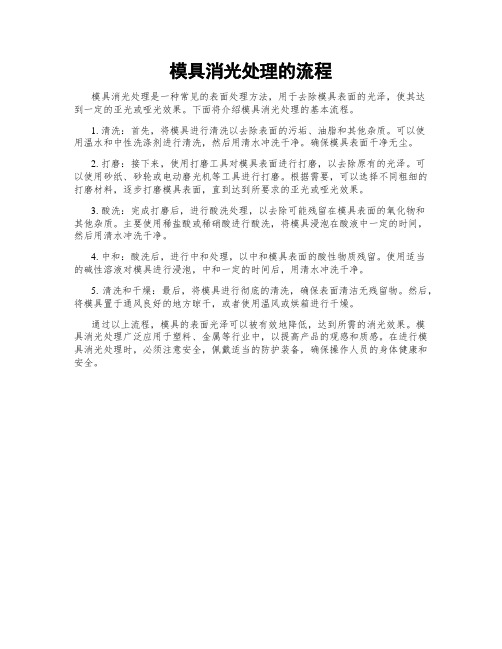
模具消光处理的流程
模具消光处理是一种常见的表面处理方法,用于去除模具表面的光泽,使其达
到一定的亚光或哑光效果。
下面将介绍模具消光处理的基本流程。
1. 清洗:首先,将模具进行清洗以去除表面的污垢、油脂和其他杂质。
可以使
用温水和中性洗涤剂进行清洗,然后用清水冲洗干净。
确保模具表面干净无尘。
2. 打磨:接下来,使用打磨工具对模具表面进行打磨,以去除原有的光泽。
可
以使用砂纸、砂轮或电动磨光机等工具进行打磨。
根据需要,可以选择不同粗细的打磨材料,逐步打磨模具表面,直到达到所要求的亚光或哑光效果。
3. 酸洗:完成打磨后,进行酸洗处理,以去除可能残留在模具表面的氧化物和
其他杂质。
主要使用稀盐酸或稀硝酸进行酸洗,将模具浸泡在酸液中一定的时间,然后用清水冲洗干净。
4. 中和:酸洗后,进行中和处理,以中和模具表面的酸性物质残留。
使用适当
的碱性溶液对模具进行浸泡,中和一定的时间后,用清水冲洗干净。
5. 清洗和干燥:最后,将模具进行彻底的清洗,确保表面清洁无残留物。
然后,将模具置于通风良好的地方晾干,或者使用温风或烘箱进行干燥。
通过以上流程,模具的表面光泽可以被有效地降低,达到所需的消光效果。
模
具消光处理广泛应用于塑料、金属等行业中,以提高产品的观感和质感。
在进行模具消光处理时,必须注意安全,佩戴适当的防护装备,确保操作人员的身体健康和安全。
模具表面处理技术的研究
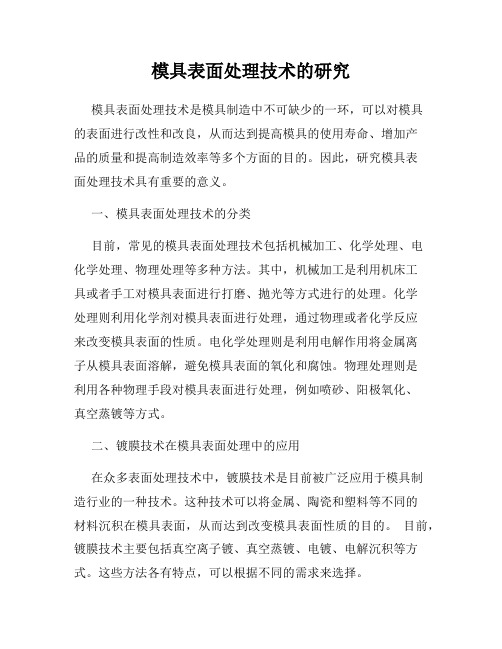
模具表面处理技术的研究模具表面处理技术是模具制造中不可缺少的一环,可以对模具的表面进行改性和改良,从而达到提高模具的使用寿命、增加产品的质量和提高制造效率等多个方面的目的。
因此,研究模具表面处理技术具有重要的意义。
一、模具表面处理技术的分类目前,常见的模具表面处理技术包括机械加工、化学处理、电化学处理、物理处理等多种方法。
其中,机械加工是利用机床工具或者手工对模具表面进行打磨、抛光等方式进行的处理。
化学处理则利用化学剂对模具表面进行处理,通过物理或者化学反应来改变模具表面的性质。
电化学处理则是利用电解作用将金属离子从模具表面溶解,避免模具表面的氧化和腐蚀。
物理处理则是利用各种物理手段对模具表面进行处理,例如喷砂、阳极氧化、真空蒸镀等方式。
二、镀膜技术在模具表面处理中的应用在众多表面处理技术中,镀膜技术是目前被广泛应用于模具制造行业的一种技术。
这种技术可以将金属、陶瓷和塑料等不同的材料沉积在模具表面,从而达到改变模具表面性质的目的。
目前,镀膜技术主要包括真空离子镀、真空蒸镀、电镀、电解沉积等方式。
这些方法各有特点,可以根据不同的需求来选择。
例如,在压铸模具中,模具表面往往需要耐磨、耐蚀、耐热等性质,这时可以采用真空离子镀的方法,在模具表面形成一层具有这些性质的陶瓷类薄膜,从而达到保护模具、延长模具寿命的目的。
而在注塑模具中,则需要的是表面光滑、不粘连、易脱模等特性,这时可以选择电镀的方法,在模具表面形成一层镀铬、镀钴等金属薄膜,从而达到这些目标。
三、模具表面处理技术发展趋势随着现代制造业的发展,不断出现新的材料和新的工艺,模具表面处理技术也在不断更新和改进。
如今,人们开始将纳米技术、激光技术、等离子技术等先进技术应用到模具表面处理领域。
这些技术可以将模具表面改良到更细微的层次,进一步提高模具表面的耐磨、耐蚀、光滑、不粘附等性能,使模具的制造和使用更加高效、安全、可靠。
四、模具表面处理技术未来的发展方向模具表面处理技术的未来发展方向,除了大量应用新兴技术外,还应该加强多学科交叉、多层次协同的研究模式。
模具注塑表面处理工艺

模具注塑表面处理工艺
模具注塑表面处理工艺包括以下几种:
1. 喷涂:将漆料喷涂在模具表面,可以起到保护和美化的作用。
2. 喷砂:用高压空气将细颗粒喷射到模具表面,去除表面的氧化层和污垢,增加表面粗糙度,提高增粘能力。
3. 喷丸:用高速运动的金属颗粒将模具表面冲击打磨,去除表面的氧化物和污垢,提高表面硬度和光洁度。
4. 镀铬:将模具表面浸泡在铬酸盐溶液中,通过电化学反应形成一层铬膜,提高模具的硬度和耐腐蚀能力。
5. 锕化处理:将模具表面暴露在氨气中,形成一层箍化层,提高模具的硬度和抗腐蚀能力。
6. 动电沉积:利用电化学原理,在模具表面沉积一层金属薄膜,提高模具的硬度和抗磨损能力。
7. 渗碳处理:将模具加热至高温,然后浸泡在含有碳元素的介质中,使碳元素渗入模具的表面,提高模具的硬度和耐磨性。
8. 氮化处理:将模具表面暴露在含氨气的高温环境中,使氮元素渗入模具表面形成氮化层,提高模具的硬度和耐腐蚀能力。
以上是常见的模具注塑表面处理工艺,不同的工艺可以根据模具的具体需要进行选择和组合使用。
模具表面处理
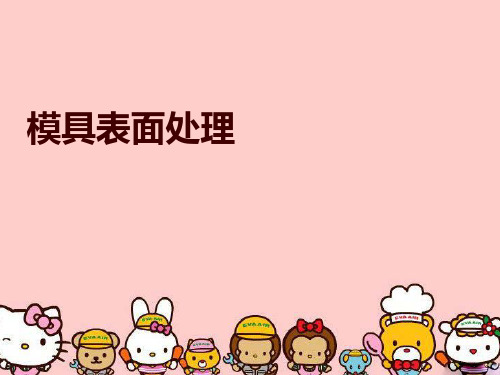
三、模具表面处理分类
2.3 TD覆层工艺流程
温度:通常在850-1050℃之间,核心工艺在900-960℃之间,不同的 材料有 不 同的处理温度。 加工周期:核心工序约12-20小时,全部工序大约为40-60小时之间。
工件收入检查 抛光 装夹 预热
清洗
回火 TD核心工艺
预检测 抛光 检测 公差调整
三、二模、具冲表压面尺处寸理类分型类
3.2 PPD原理 PPD 技术是通过氮离子渗透到模具基体表面来形成超硬抗磨损表面。 在真空环境中,通过腔体壁之间的电压和载荷,氮气和氢气分子电离(工具表面可
见)。气体离子开始与模具基体离子反应形成硬化渗氮区域。处理工艺是通过渗透扩散而 非涂层进行的。
3.3 PPD工艺流程
三、模具表面处理分类
分类 通过对模具进行表面处理特别是对模具进行表面超硬化处理是解决工件表面拉伤问题经
济而有效的方法。表面处理方法有多种,比较常用的如下。
镀层方面
表面超硬化处理方面
镀刷化
化学气 物理气
物理化
TD
硬镀学
相沉积 相沉积
学气相
覆
铬特镀
CVD PVD
沉积
层
种镍
PCVD
处
合磷
理
金
渗入处理方面
类、翻边模具
类、翻边模具
型类模具
模具镶块
4.3 优点
工艺
二四、、冲优压缺尺点寸对类比型
PPD
镀硬铬
PVD,PCVD
TD覆层处理
场合
工艺环保、抗磨损效 果好
成本低、处理周期短
具有极高的耐磨抗 咬合等性能
耐磨、成本低、工 艺环保
4.4 缺点
工艺
模具表面处理对塑件质量
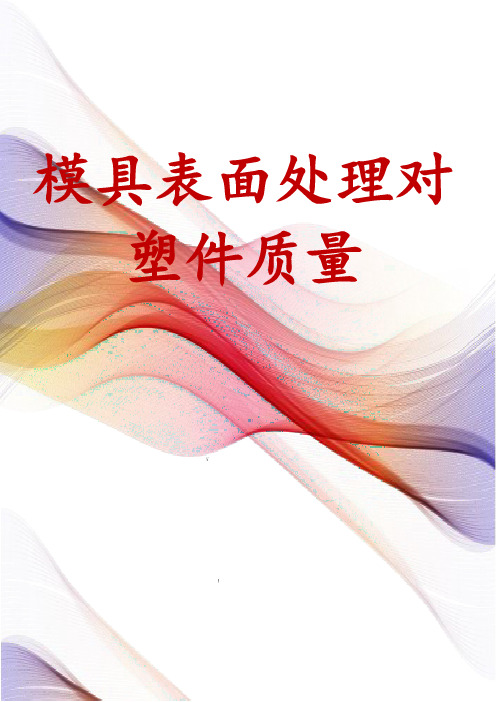
模具表面处理对塑件质量一、模具表面处理技术概述模具表面处理技术是塑料加工行业的一项关键技术,它直接影响到塑料制品的质量和生产效率。
模具表面处理技术主要包括表面抛光、表面涂层、表面硬化处理等。
通过这些处理方式,可以显著提高模具的耐用性、减少生产过程中的摩擦、提高塑件的表面质量等。
模具表面处理技术的发展,不仅能够推动塑料加工行业的进步,还将对整个制造业产生深远的影响。
1.1 模具表面处理技术的核心特性模具表面处理技术的核心特性主要包括以下几个方面:- 耐磨性:通过表面处理,模具表面能够抵抗磨损,延长模具的使用寿命。
- 耐腐蚀性:模具表面处理能够提高模具的耐腐蚀性,减少因腐蚀而导致的模具损坏。
- 表面光洁度:通过表面抛光和涂层处理,模具表面能够达到更高的光洁度,从而提高塑件的表面质量。
- 减少粘附性:表面处理可以减少模具与塑料材料之间的粘附性,降低生产过程中的不良品率。
1.2 模具表面处理技术的应用场景模具表面处理技术的应用场景非常广泛,包括但不限于以下几个方面:- 汽车零部件:汽车零部件对模具的耐磨性和表面光洁度要求极高,模具表面处理技术在这一领域应用广泛。
- 家用电器:家用电器如冰箱、洗衣机等的塑料外壳,需要模具表面处理技术来保证其外观和耐用性。
- 医疗器械:医疗器械的塑料部件需要模具表面处理技术来提高其耐腐蚀性和表面光洁度。
- 包装行业:包装行业的塑料制品如瓶子、盒子等,也需要模具表面处理技术来提高其外观和耐用性。
二、模具表面处理技术的分类与工艺模具表面处理技术的种类繁多,每种技术都有其独特的工艺和应用领域。
以下是几种常见的模具表面处理技术及其工艺。
2.1 表面抛光技术表面抛光技术是通过对模具表面进行物理或化学处理,使其达到所需的光洁度。
常见的表面抛光技术包括:- 机械抛光:通过机械摩擦的方式,去除模具表面的毛刺和不平整,提高表面光洁度。
- 化学抛光:通过化学腐蚀的方式,去除模具表面的氧化物和杂质,提高表面光洁度。
模具表面处理种类和作用

模具是作为制造业的重要工艺装备,它的使用性能,特别是使用寿命反映了一个国家的工业水平,并直接影响到产品的更新换代和在国际市场上的竞争能力。
因此,各国都非常重视模具工业的发展和模具寿命的提高工作。
目前,我国模具的寿命还不高,模具消耗量很大,因此,提高我国的模具寿命是一个十分迫切的任务。
模具热处理对使用寿命影响很大。
我们经常接触到的模具损坏多半是热处理不当而引起。
据统计,模具由于热处理不当,而造成模具失效的占总失效率的50%以上,所以国外模具的热处理,愈来愈多地使用真空炉、半真空炉和无氧化保护气氛炉。
模具热处理工艺包括基体强韧化和表面强化处理。
基体强韧化在于提高基体的强度和韧性,减少断裂和变形,故它的常规热处理必须严格按工艺进行。
表面强化的主要目的是提高模具表面的耐磨性、耐蚀性和润滑性能。
表面强化处理方法很多,主要有渗碳、渗氮、渗硫、渗硼、氮碳共渗、渗金属等。
采用不同的表面强化处理工艺,可使模具使用寿命提高几倍甚至于几十倍,近几年又出现了一些新的表面强化工艺,本文着重四个方面介绍,供同行参考。
一、低温化学热处理1.离子渗氮为了提高模具的抗蚀性、耐磨性、抗热疲劳和防粘附性能,可采用离子渗氮。
离子渗氮的突出优点是显著地缩短了渗氮时间,可通过不同气体组份调节控制渗层组织,降低了渗氮层的表面脆性,变形小,渗层硬度分布曲线较平稳,不易产生剥落和热疲劳。
可渗的基体材料比气体渗氮广,无毒,不会爆炸,生产安全,但对形状复杂模具,难以获得均匀的加热和均匀的渗层,且渗层较浅,过渡层较陡,温度测定及温度均匀性仍有待于解决。
离子渗氮温度以450~520℃为宜,经处理6~9h后,渗氮层深约0.2~0.3m m。
温度过低,渗层太薄;温度过高,则表层易出现疏松层,降低抗粘模能力。
离子渗氮其渗层厚度以0.2~0.3m m为宜。
磨损后的离子渗氮模具,经修复和再次离子渗氮后,可重新投入使用,从而可大大地提高模具的总使用寿命。
2.氮碳共渗氮碳共渗工艺温度较低(560~570℃),变形量小,经处理的模具钢表面硬度高达900~1000H V,耐磨性好,耐蚀性强,有较高的高温硬度,可用于压铸模、冷镦模、冷挤模、热挤模、高速锻模及塑料模,分别可提高使用寿命1~9倍。
- 1、下载文档前请自行甄别文档内容的完整性,平台不提供额外的编辑、内容补充、找答案等附加服务。
- 2、"仅部分预览"的文档,不可在线预览部分如存在完整性等问题,可反馈申请退款(可完整预览的文档不适用该条件!)。
- 3、如文档侵犯您的权益,请联系客服反馈,我们会尽快为您处理(人工客服工作时间:9:00-18:30)。
随着现代工业的快速发展、人们视觉美观要求的不断提高、模具行业本身的客观要求,模具蚀纹的发展越来越迅速,新工艺不断涌现,新材料不断应用,造就了现在模具蚀纹行业的新辉煌。
模具蚀纹,模具咬花,模具晒纹,模具烂纹,模具烂花,模具蚀刻之类都是模具里的同一工艺,只是名称叫法不同。
里面又有幼纹,细纹,粗纹,皮纹等纹路粗细的种类。
英文一般如下写法mould texture,mold texture,mould texturing,mold texturing。
模具蚀纹的应用:
起装饰产品的作用,使产品更加美观,高雅:
克服了印字,喷漆易磨掉的缺点;
满足了视觉要求:由于光洁如镜的产品表面极易划伤,易沾上灰尘和指纹,而且在形成过程中产生的疵点、丝痕和波纹会在产品的光洁表面上暴露无疑,而一些皮革纹、橘皮纹、木纹、雨花纹、亚光面等装饰花纹,可以隐蔽产品表面在成形过程中产生的缺点,使产品外观美观,迎合视觉的需要。
制作花纹,可以使产品表面与型腔表面之面能容纳少许的空气,不致形成真空吸附,使得脱模变得容易。
防滑、防转、有良好的手感。
制成麻面或亚光面,防止光线反射、消除眼部疲劳等等。
模具蚀纹的方式:
花式纹路技术是经过化学药水作用,在不同金属制品的表面造成各类图案,例如:沙纹、条纹、图象、木纹、皮纹及绸缎图案等。
不同的技术流程制作出不同的纹路风格。
其中也包括喷纹程序,例如:办公室文件器材、录音机、录映机、照相机、汽车的防撞架、镜面、花盆、餐具等表面都是用喷纹制作而成。
模具蚀纹的流程:
洗膜-粘膜-化学检验-表面处理-印花处理-化学蚀刻-表面处理-QC-防锈处理-包装
模具纹分类:
有对称形图纹如正方形对应,圆形对应,非对称形图纹,花纹,木纹,类似家装材料瓷砖的图纹,这个纹理当然不是平的,是有纹理的,有立体感的,有凹凸不来的。
还有包括蚀字等。
一般可以总体概括:各种塑料工模皮纹、木纹、布纹、立体纹、(电视,电脑,电话,手机,汽车,摩托,空调,冰箱等)大小电器外壳各类花纹滚筒;鞋底纹、不锈钢、压铸模蚀刻、凹凸文字商标、图案、喷沙。
2012-3-9 10:17 上传
下载附件(37.4 KB)
模具蚀纹的选择:
蚀纹做为模具加工的最后工序对整个模具的成型起着至关重要的作用。
优秀的模具设计工程师应对不同的纹理有所了解,以便于在设计阶段做出正确的选择,减少模具加工的风险。
具体来说蚀纹选择可根据不同的要素作为条件。
归纳起来分以下几类:
1、客户要求。
客户的要求是最终的决定,但客户大多数是站在美观的角度做为考虑,若发现客户指定的纹路对模具的生产以及产品的出模有相对的缺陷,就应及时和客户做好沟通工作,说明风险以便客户做出正确的选择。
2、产品出模要求。
在模具设计的初始阶段对模具的各个侧壁做综合考虑,若整个拔模角度比较小,就应选择比较幼、比较小、比较圆滑的纹理。
3、模具不同部件的功能要求。
前模做为产品的外观面要求都比较高,可尽量站在美学的角度做选择。
后模相对而言做纹理的比较少,通常以“拉力”为主,一般是为防止产品出模时容易粘前模。
4、模具结构的要求。
若模具上有比较窄小并且很深的沟槽要尽量选择幼一些的纹理,并且尽量选择喷纹的纹路。
如果最终选择仍然是印纹的纹理,那就要考虑在沟槽处开镶件。
否则后续的纹理加工会很麻烦。
要和蚀纹厂商做好及时的沟通工作,把各个部位的拔模角度及时通知蚀纹厂。
模具的碰穿位、镶件位容易发生圆角,段差,披锋。
这些地方设计选择也是很有讲究的。
蚀纹厂商的选择
全世界小蚀纹厂不计其数,顶级的蚀纹厂商就屈指可数了。
模具厂选择合适的蚀纹厂做为合
作伙伴是很重要的。
蚀纹做为手工工艺加工除了技术还有艺术涵盖在里面。
没有一定的技术功力和深厚的底蕴是很难上层次的。
模纹国际做为知名的蚀纹厂商在行业里面赢得了广泛的赞誉和口碑。
加工模具涵盖汽车、电子、家居等领域。
在蚀纹行业里面第一个成立了品质部、客服部,第一时间解决客户的所有问题。
交期准、品质好、价格公道、服务一流。
模纹国际是绝对首选的。
蚀纹是模具表面的一种加工处理方法。
香港人称之为晒纹,台湾人叫咬花,内地有些地方叫做“烂皮纹”。
(皮革纹理,示例)
之所以有如上“咬”和“烂”的说法,是因为蚀纹是通过“化学腐蚀”
的方法,把花纹加工到模具表面上,(一般需要蚀纹的塑胶模具居多)
(化学腐蚀中……)
注塑后,塑胶产品便可有各种各样的花纹呈现在产品外观面,既增加其美观,也可以防滑等。
而“晒”呢,则指通过菲林,曝光等手段进行纹理加工。
(菲林示例图片及加工后的效果)
蚀纹跟产品有着密不可分的关系,相信很多设计师和工程师,越来越体会到蚀纹的重要性。
2010-7-7 11:56 上传
下载附件(29.44 KB)。