教育训练教材
端子铆压教育训练教材

导体飞丝不良 功能区包胶不良 线皮后缩不良直视看不见线皮 导体伸入过长
三.铆压作业时所要注意的問題
1.在踩压脚踏开关之前必须注意手指不得伸入刀座内.
2.当作业过程中上刀片夹有端子时要停止机器运作,用剪刀或挑针将 夹住的端子挑出否责继续作业刀片将会被打断.
3.在作业过程中若需要离岗时须报告组长接机或把电源关闭后方可 离开避免他人擅自操作带来安全事故隐患!
铆压的作用
2.压接后连接金属導體使其導通,尽可能设计用向内卷向 收缩使金属導體连接后不易松动更为劳固使用受命更长.
3.作业动作比焊锡作业具有生产效率高,更容易快速掌握 作业标准动作和作业技能.
铆压的目的
4.电气作用:连接两个金属体,使其能容易进行导电作用.便於信
號或數據的傳輸.
Байду номын сангаас
5. 机械作用:连接两个金属体,使其两者位置能固定.可以承受较 大的拉伸力在特殊环境中使用更安全;不容易脱落,从而达到 高频率抗震!抗热溶在高温环境下不容易脱落!
5.在铆压作业时因手法操作不当或取线速度过慢导致端子被剥皮刀座夹变型不良!
五.端子机的保養維護
1>铆压作业前试踩脚踏开关是否正常有效控制机器运转.
2>机器送料是否正常.
3>下班前将机台电源关闭后用气枪吹走刀坐内的废线皮.若是假前清洁刀模上需喷防锈 油! 請看(付圖)
用气枪 吹
注意事項: 1.在机师调试好刀模后必须由品检人员IPQC或FQC拿与对招 作业相同的废线铆压3-5PCS端子做拉力实验.测量内高.外 高和宽度合格后做好首件才可正常投产批量作业,否则产生 不良所有损失责任人自己承担. 2.端子作业当天自己作业产生的不良自己在下班前提前10分 钟把不良修完,当天的不良不可以留到第二天;做到日清日毕 3.在作业过程中要做到制;三不’原则,不制造不良.不流出不良. 不接受不良! 制作人:丁合华 2010.02.26
SPC教育训练教材(chin0515)(1)
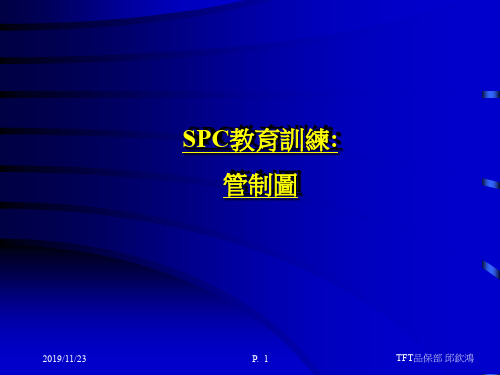
??
Prediction?
Time
Any process that is not stable is called an unstable or out-of-control process.
2019/11/23
P. 18
TFT品保部 邱欽鴻
Stable Process
如果僅存在機遇原因,隨著時 間的推移,製程的輸出可以形 成一個穩定分布並預測
99.99943%
過分充足
99.99%
充足, 維持理想狀態
99.73%
避免不良發生, 製程需改善
不足,95.45% 發Fra bibliotek不良全數選別,
製程立即改善
USL
非常不足,
68.27% 品質改善,追究原因,
採取緊急措施
Process Control: Three Types of Process Outputs
SPC教育訓練: 管制圖
2019/11/23
P. 1
TFT品保部 邱欽鴻
綱要
1. 統計製程管制(SPC)基本概念 2.製程能力分析
3.管制圖 管制圖原理 管制圖繪製 P管制圖 管制圖之種類 管制圖之判讀
2019/11/23
P. 2
TFT品保部 邱欽鴻
1.“拉力強度很好”算不算是有意義的資訊?
(c) Out of control. A process out of control having assignable causes of variation.特殊原因變 異
2019/11/23
P. 17
TFT品保部 邱欽鴻
Unstable Process
如果存在非機遇原因, 隨著時間的推移,製 程的輸出不穩定
质量检验人员教育训练教材
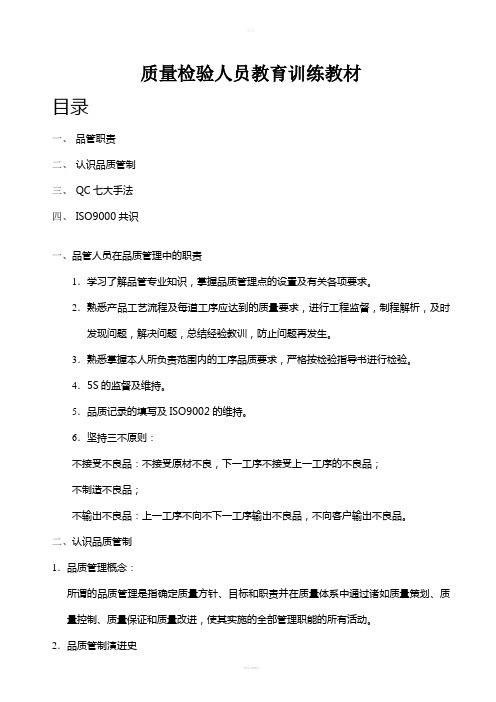
质量检验人员教育训练教材目录一、品管职责二、认识品质管制三、QC七大手法四、ISO9000共识一、品管人员在品质管理中的职责1.学习了解品管专业知识,掌握品质管理点的设置及有关各项要求。
2.熟悉产品工艺流程及每道工序应达到的质量要求,进行工程监督,制程解析,及时发现问题,解决问题,总结经验教训,防止问题再发生。
3.熟悉掌握本人所负责范围内的工序品质要求,严格按检验指导书进行检验。
4.5S的监督及维持。
5.品质记录的填写及ISO9002的维持。
6.坚持三不原则:不接受不良品:不接受原材不良,下一工序不接受上一工序的不良品;不制造不良品;不输出不良品:上一工序不向不下一工序输出不良品,不向客户输出不良品。
二、认识品质管制1.品质管理概念:所谓的品质管理是指确定质量方针、目标和职责并在质量体系中通过诸如质量策划、质量控制、质量保证和质量改进,使其实施的全部管理职能的所有活动。
2.品质管制演进史3.不良的来源——变异①变异的来源变异是宇宙现象,人类生活中任何过程都会有变异。
变异大,可以看出来,变异小,无法目视判别。
假如由生产线随机取出数个产品,测量产品的某些特性质,如果测量仪器足够精确的话,必将发现这些产品的测量值各不相同。
下面两图表示变异的来源,这些来源的总影响,形成产品之间之变异。
任何一个与制品有关的因素变动,制品(结果)也就随之变动,因素变动的大小,制品的特性(结果)也随之大小而变动。
变异来源之一机器如:切割机器刀具锋利度,冲压机冲程可能之变动,电镀处理液之变动,空压机气压之品质。
变异来源之二材料如:供应厂商更换,材料(部件)替换,材料机械性质或化学性质之变动,材料尺寸变动。
变异来源之三方法如:流程之变更,作业方法之变更,工具、夹具不当。
变异来源之四操作员如:操作员熟练度,操作员习惯性,操作员有没有依照操作标准作业,操作员之体力与情绪,操作员的工作场所及使用工具。
变异来源之五环境因素如:电源稳定度,水质稳定度,温度、湿度,空气粉尘,照明度,地板及工作场所清洁,工作场所物品之摆放。
推荐20本教育教学用书

1.《如何说孩子才会听怎么听孩子才肯说》,[美]玛兹丽施著,安燕玲译,中央编译出版社2012年7月出版本书将帮助你学会一种让孩子听话的神奇语言,这种爱的语言使孩子很容易接受您的要求和忠告。
世界上数以千万的父母用自身的亲身实践证明了书中提供的方法非常有效。
该书在美国畅销300多万册,并被翻译成30多种文字风靡全球。
世界各地的父母和专家热情洋溢地赞誉两位作者,她们在长期的实践中摸索出的这套语言是那样行之有效,的的确确能缓解所有年龄段的孩子与父母的紧张关系,结束父母与孩子的冲突对抗,带来父母和孩子的合作。
2.《笔记大自然——找寻一种探索周围世界的新途径》,[美]莱斯利、罗斯著,麦子译,华东师范大学出版社2012年8月出版本书是一本指导如何给大自然书写日记的入门书。
克莱尔和查尔斯是美国著名的自然观察家,艺术家,教育家。
他们用两种指尖艺术——书写与绘画,来传递大自然的色彩与神奇。
在日记的字里行间,有流动的色彩。
有疑固的字迹;有停驻的脚步,有飞扬的神思……其美感难以言喻,其宁静无以形容……似乎,所有珍贵而不被注意的,都选择隐遁在这朴素的书里。
3.《善解童贞2——6-13岁孩子的性发展与性教育》,胡萍著,广西科学技术出版社2011年4月出版本书提供了全面、系统的性关怀和教育的方法,引领我们科学地解读孩子的性发展,使我们能很恰当地帮助孩子。
“爸爸妈妈,我从哪里来?”几乎每位家长都会遇到孩子问这样的问题,然而,受传统观念的影响,我们碰到这类问题时总是有些欲言又止,不得要领。
确实,儿童性教育是个敏感而又不可回避的话题,它关乎孩子的身心健康与发展,不可掉以轻心。
“我们必须从孩子0岁起,就给予他性方面的关怀与照料。
”这是“中国儿童性教育第一人”胡萍在本书中提倡的儿童性教育原则。
告诉孩子真相吧,让孩子了解生命来源的真相,让身为父母的你洞悉孩子的心语,这样,孩子才会懂得珍惜自己的生命,才会懂得父母对自己的爱。
4.《做适合人的教育:斯坦纳教育理论和实践》,[英]吉尔伯特•蔡尔兹著,王荣亨译,新世界出版社2012年7月出版本书是对斯坦纳教育理念和华德福学校课程设置和原因的全面阐释。
模具课教育训练教材

第一章模具概念一.概述模具具有非常广泛的应用,可以说各个行业都离不开模具.模具已成为生产各种工业产品不可缺少的重要工艺装备.在这里只介绍冷冲模具.冷冲压模具可以分为单工程模具和连续模具,而单工程模具又可以分为冲孔模,下料模,折弯模和复合模等.二.模具组成及结构每一套模具都由几块模板,冲头和入块等组成.下面我们来了解一下各个模板的名称: 上模座(USET),上垫板(UPHUB),固定板(UPH),背脱板(STRUB),脱料板(STR),母模(DIE),下垫板(DIEDB),下模座(DSET),冲头(P),小冲(SP),大冲(BP),内脱板(KO),下固定板(DPH)等.每一套模具都至少具有上模座,下模座,冲头,脱料板,母模,固定板等几块模板.我们组装的模具有冲孔模,下料模,复合模和连续模. 冲孔模是指经过机器加工以后落到下面的料是没用的那种模具.是整套模具生产中的一个环节,它只是加工模具的内孔.下料模是指经过机器加工以后落到下面的料是有用的那种模具,它也是整套模具生产中的一个环节,它是加工模具的外形.复合模是可以一次完成模具的外形和内孔加工的模具,它和上面的两组模具一样也不能做折弯的工程.如果模具有折弯的部分,那还需要折弯模的工序,在这里我也不作介绍了.而连续模则可以一次完成整套模具的加工,它一道一道的工序做,所以对准确度要求较高.三.模具配合间隙1.剪断间隙(GAP)=料厚(T)*6%2.活动间隙一般情况下为一条半(一条=0.01mm),但绝对不能大于剪断间隙.3.螺丝在模板中间隙缩放关系一般为单边放大0.5-0.1 mm.(铣床加工)4.固定销在模板中间隙缩放关系一般为单边放大0.004mm.(线割)5.导柱在模板中间隙缩放关系一般为单边放大0.002mm.(线割)6.在固定板(UPH)层中图形冲单边放0.008mm,异形冲单边放0.01mm.(线割)7.母模的大小=冲头的大小+剪断间隙. 脱料板(STR)的大小=冲头的大小+活动间隙.内脱板(KO)的大小=母模的大小—活动间隙8.在连续模中上垫板(UPHUB),背脱板(STRUB),下垫板(DIEDB)都只是起通过作用,所以缩放间隙为单边放大0.5-1mm.9.螺丝的头部或其它一些零件的头部所在的图层中要逃孔的大小为零件头部大小再单边加1mm.10.连续模中下垫板(DIEDB),下模座(DSET)中的冲头孔只是起漏料作用,每一层比上一层单边放大0.5-1mm.四.常见冲头尺寸计算:1.闭模高度的确认(UPH, STR, STRUB的高度组合).如UPH=20mm, STR=20mm, STRUB=15mm,则闭模高度=55mm.2.冲孔冲头必须隐藏于脱料板.所以冲孔冲头长度L=上闭合高(UPH+STRUB+STR)+料厚t+(2~3)mm例如:UPH厚度为20mm,STRUB为15mm,STR为20mm. t=0.8则L=20+15+20+0.8+2=58mm.3.成型冲的确认(即向下打凸1.0高) 则冲子=闭模高+1.0,母模入块向下降1.0.(成型冲=打凸N或V字型,卷弯,斜度,冲剪成凸,翻边打断差等.)均属成型.4. 抽芽冲,折弯冲的确认.(即:视抽芽长宽及折弯高度来决定冲子长度,一般抽芽长直升部位必须有3~4mm, 视抽芽高度而定,折弯冲一般如果成品超过8.0高,不含R角)方能使90°成型.5. 入块的确认(若为冲孔入块则必须下孔为锥度状(上模冲成型2.0,下模入块则必须刚好低于模面2.0)6.向上拆弯入块突出母模面高度一般应为折弯深度的一半,避免划伤),而压料入块应高出拆弯入块1mm以上.第二章模具课组立作业规范一.组立前置作业:1.在一组模具图纸到手后,首先认真分析产品图,模具结构图,将产品结构,生产工艺以及模具制造中会遇到的问题牢记于心.2.对照模板图,零件图以及五金零件申购单检查模板,零件是否齐全,是否正确,包括模板厚度,光洁度,有无倒角以及各孔位大小位置.若有不妥,要及时反应并追踪到位.3.对照图面及模板将冲头,入块挂台方向,挂台高度以及总高度标示好,以做研磨加工.4.模板导柱及刀口检对,模板到齐后可以将母模板与脱料板迭好,装入导柱,然后进行刀口对正,所有剪口冲头必须滑配,以手轻轻推入为准.检验好后再依此将夹板与脱料板对正,直至上下模板可以顺利配置.5.模板刀口OK后,最后需将各相关联模板迭对,以确保其孔位加工有准,特别是冲孔落屑一定要顺畅,以免在组立中反复拆卸.6.以上若有问题点需记录于组立日志,以便积累经验,以及核算成本.二.组立要点:1.等高套筒,弹簧的选用与计算.(1) 套筒计算方式=最长冲子-脱板厚+1~2.0的高度.(冲子内缩量)若等高套筒吊在上垫板,则冲子长+上垫板厚-脱板厚+1~2.0. (冲子内缩量)(2) 弹簧选用=一般视材料成型及模具结构而定.折弯弹簧一般使用红色或绿色,材料较薄0.6以下则用红色,0.6以上则用绿色.抽牙弹簧一般使用绿色或茶色;成型冲弹簧一般使用红色或绿色;冲孔冲弹簧一般使用绿色.(3) 弹簧压缩量计算方式为: DF—50%极轻荷重(黄色) DL—40%轻荷重(蓝色) DM—30%中荷重(红色) DH—24%重荷重(绿色) DB—20%极重荷重(茶色).2.五金零件的选择与制作:(1) 内外定位及其顶料销的制作: 外定位要比内定位的直身位高至少1t(t表示料带厚度),而内定位旁的顶料销要比内定位的直身位低1 t.(2)导正销(引导销)的制作: 导正销的直身位伸出脱料板的长度为料厚+0.5t,而其旁的顶料销的长度伸出脱料面大于导正销直身位1.0t,特别注意的是此顶料销用圆线弹簧,力度不要过大,一般用0.4~0.7线径即可.(3)定位销的使用: 定位销在装入模中之前,要试配合模板中的孔是否过紧,必要时要铰孔处理加油使其便利进入.(4)导柱,导套的运用: 辅助导柱在无脱背的情况下,要检查导柱末端部与上夹紧配合的长度看是否长于上夹的厚度,若有长出则要铣深逃孔,避免和脱板发生干涉;导柱与各模板在正常间隙下活动,其长度则要根据模具的结构作选择;外导柱装入模座中,最好用油压机置入,这样可以避免受力倾斜,外导套与模座孔的单边间隙为0.08mm.(5)制高块的制作: 制高块的高度为h(制高块)=t(母模)+(冲件材料厚度t-0.2mm)左右作制高块的目的主要是:A.连续模中刚送料时,避免整个脱料板的受力倾斜,不平衡.B.避免模板中字模,压线印等零件的损坏.(6)灌胶的注意事项: 灌胶时要把模座孔内擦干净,光洁,要让导套与滚珠,导柱在孔内便活动,用等高块置于上下模座之间,并测量是否等高,然后开始灌胶. 灌胶4小时后即可开模,做装弹簧等动作,装入的顶料销浮升块等零件用手压缩,不至于让弹簧打死,全部工作完成,等待试模.3. 冲子装配要点:冲子或入块装入模板前需先用卡尺量测挂位沉头深度及冲子挂位长度(一般为5mm),确认OK后方可将冲子入块置入模板中,冲子若凸出太高,则需将沉头铣至低于模面0.1之高度,不可用打磨机磨掉,亦不可猛砸使其凹下,若沉头太亦应立即反应(不得低于模式面0.5以下),否遇会使冲子被拉出脱板外造成脱料板不顺之现象.4.闭模及灌胶要点:组模时在配入刀口与成型块确定间隙OK,长度尺寸,螺丝孔,等高套筒,固定梢,导柱孔,定位梢,避位处均无干涉现象时即可进行闭模,外导柱灌胶或装独立导柱三作业.(灌胶间隙为导柱尾部大于内孔0.05). 导套为导套正尺寸小导套孔+0.1灌胶时需确认每一块模板均紧贴齐面.灌胶作业于4小时后拆模将弹簧及顶料浮升零件置入,完成组模程序.5.组模后再对照整组模具认真检查每块模板之外观及模具内部结构,如避位是否确实避开,所有紧固螺丝是否锁紧,关键部位有无润滑,定位是否有松动,落屑是否顺畅等现象.三.常见模具之对模方式:在完成各项组立前置工作,确保模具在结构上及装配上无误后,可进行模具组立装配工作.一般常见模具的对模方式及过程有以下几种:(一)下料模: 开始组立模具时,一般应由下模开始组立.1.将下夹板与下脱料板装入导柱,公模放入下夹板上定位梢.2. 上紧套筒待完成后将套筒顶至高出公模半块成品料厚(此为正常下料模下模套筒长度,若下模有上下成型冲则脱料板与成型冲平齐)3. 放入弹簧上螺丝不能完全锁紧,把定位梢固定下模板架构方能上紧螺丝.4.组装上模,将脱料板放入母模盖上夹板,开始组模.(※上模脱料板需超出母模1m/m长)(二)冲孔模:1.在组立模具之前最好将以往的试模经验加以溶合.如:脱料上的问题,如折弯脱料,凸点脱料,抽牙脱料,铆合抽孔脱料等,以上种种问题皆需顾及弹簧的弹力与压缩量.2.注意导柱长度是否在适当长度,下模导柱避位深度是否足够,上模座导柱挂台避位3.预估你组立的模具试模时会产生何种现象,当现象发生时你将作何处置.(三)折弯模: 一般向上折弯可区分为三种:1.线割外形向上折弯模2.利用下夹板精铣沟槽以定位折弯块之向上折弯模3.以90° V形成型之折弯模(1)线割外形向上折弯模最常见的线割外形折弯模,它通常做为公母模共享,故我们组立时需在留意公母模的料厚间隙问题.A.先将测量母模线割外形尺寸.不得小于成品外形.B.查出公模所要研磨的尺寸(预留精修)将公模配入夹板定位,再与母模利用导柱将两块模板定位,用间隙片测量折弯公模式与母模之间的间隙进行配刀,直到材料厚度(t)准时即可.(※注意间隙不可过紧)C.组立下模进注意,弹簧压缩量,预压量,是否在正常值下.( ※所谓正常值:即是弹簧力量过大于90°,),此时可用压线克服加强90°之稳定性;若弹簧力量过小则会产生90°内弯现象,此时则需测量产品高度,不可倒过大的角度,若产品折弯高度已在上限则以放开间隙,降低折弯深度或加强弹簧以相互利用,达成90°之需求.D.组立下模时需注意冲制品以三边成型,则需先折对称两边折弯约1.5~3 m/m(视素材t厚而改变);再折另外一边此种方式可避免产品拉料现象.E.组立上模时需注意,公模脱料的浮升梢跟刀口距离;其浮升梢四分点刀口不得超过3.5m/m;(一般料厚1.6 m/m以下皆可适用),再则留意弹簧力量.(以1.0 m/m素材而言,大约25m/m折线就需有2条绿色,直径为10;行程10m/m~12m/m弹簧).F.注意公模本身侧面的表面粗糙度,因为它将增强脱料的磨擦系数严重将使其脱节料不顺畅,其解决方式可用细目油刀石将表面推亮.(2)向上折弯模,其中若折弯块上割有滚轮时就必须注意,滚轮与折弯块装配后是不是可以很顺畅的滚动,若无法滚动时就必须利用砂布将沟槽拋光,直到滚坳顺畅.(3)测量,检测滚轮与折弯块装配后宽度,高度是否与入块同一尺寸,若侧割滚轮有偏位则心须做局部修整,再进一步将入块装入下夹键槽内,装入滚轮,测量两侧折刀尺寸,其尺寸可大于成品外形+N;--0.如:(4)折弯块之成型,当内脱料板厚为20mm;折弯块为35 mm时折弯块从底部算起23 mm以上的位置须让位0.1 mm以避免成品在折弯过程中被滚轮下端尖端锐角刮伤.(5)在组模时折弯块底部须做倒角约(0.3~0.5 mm)以避免下键槽壁刮伤损坏,如此即可准备组模动作.(内脱料板需高出下模折弯块1 mm)(6)上折弯公模虽然没有较具体的技巧性,但仍须注意下列三项A.压线问题考虑冲制的素材是否须要压筋;压筋的深度是否过深,因为将影响90°向上折弯与成品高度.B.脱料问题无论任何一种90°向上折弯皆需要装置浮升梢顶料,如:三面折弯;二面折弯甚至一面或四面折弯原理在于如何让冲制品在最佳平衡状态下脱模.C.滑块间隙问题滑块间隙不可过松或过紧,一般最大值间隙为0.05m/m若折弯成品0.1m/m~0.3m/m时其滑块间隙为0.03m/m以下.※滑块加有顶料梢时,顶料梢最佳放制点为滑块的1/3点.(接近公模位置的1/3~1/4点为最佳位置,但注意顶料梢浮升时不可撞击公模斜边.)四. 试模及模具维修:1.试模规范: 在模具组立及检查完毕后方可试模,新进员工由于对机床熟练程度可能不够,试模时请务必知会班组长.同时班组长在试模期间也需在现场做技术指导与监督,以免发生突发及意外事件,并做好试模报告记录.2.试模常见异常及维修:A连续模: (1)送料不顺: 发生原因多为浮升两用梢的送料宽度与试模料不符,或者所放间隙过小,再者下模浮升引导梢, 浮升块有无过高造成挡料.(2)上模带料: 发生原因多为: a上模导正梢直身过长或较为粗糙. b. 送料步距有误. C.上模冲头或向上折弯脱料不顺.(3)废料反弹: 连续模在快速冲压情况下多会发生废料反弹现象.原因常有几种: a.冲孔间隙过大. b. 冲头有磁性. C.冲入深度不够,此时可以适当调整间隙及冲孔深度.再者可以将冲头研磨斜面减小真空吸附力或者做子母冲.B.下料模: (1)脱料不顺: 检查模具内外脱板是否滑配,脱料弹簧力是否够大,是否均衡.(2)产品与料带或外脱夹料,难以取出,解决方法:a.降低外脱b.外脱脱料力量减弱(3)产品毛边过大检查对策: a.冲减间隙是否过大或过小. b. 刀口是否锋利 c.刀口配合是否有准.C.成型模: (1)脱料不顺: 原因应有多方面应针对实际情况解决,常见原因主要有:a. 脱料力不足b. 折弯入块光洁度不足c.脱料力不均衡,造成掊料不一致此时可增加顶料梢或增加弹簧预压量,或者将折弯入块用小油石或拋光砂轮拋光滑,再者就是调整脱料力所分布位置及大小使其均衡.(2)角度不准:常发生情况有:(一)角度过大: a.间隙过大 b.折弯直身过短 c.压料力量过大 d.外定位过紧 e模具闭合不良(二)角度过小: a.间隙过小 b.压线过深 c.压料力量过小 d.模具闭合不良(3)尺寸不准: 造成尺寸不准的原因可能有: a. 定位不准 b.展开错误 c. 折弯成型时拉料针对以上情况可用以下方法调整: a.增加定位或定位调整 b.展开计算检查 c.加强压料力(4)外观模痕: 改善对策: a.折块R角适当加大,拋光至圆滑过渡 b.适当放大折弯间隙 c.做滚轴式折块五.模具后期工作:模具后期工作主要是对模具外观及细节的检查,以免交模后发生不必要的错误,主要可以从以下方面着手:1.模具包观良好,上下模座必须研磨光亮,无明显刮痕,凹痕以及锈斑.2.冲小孔入块必须背面逃孔,所有冲孔处落屑检查,必须顺畅,以免废料堵孔造成爆模.3.下料模限位柱,上下模位置对正,大小一致,表面不应过于粗糙.4.模具闭合高度以及上模架模螺丝孔是否符合客户要求.内外导柱配合是否顺畅.5.模内清洁,关键部位必须加以润滑.另外案内梢使产品定位良好,不得太紧,且案内梢本身不得过松,以防生产过程中跳出造成爆模.所有模板及冲头,入块完全无磁性.附冲压操作规范 :使用冲床试模时﹐务必将安全检测器开启﹐方能试模﹐试模人数不能超过3人﹐操机者必须由组长或资深人员进行﹒操机人员身后不得站人及围观﹐每次冲压检查模料时安全开关一律按下﹐未按下时﹐头部﹑手部不得伸入模面﹐冲压进行中切勿让眼睛与母模面闭合同高度﹐以免异物弹出造成眼睛受损﹐试模时不得使用脚踏开关﹐如需用脚踏开关必需经理及组长在现场﹐非主管部任何人均不得用脚踏开关。
教育培训 经典书籍

教育培训经典书籍教育培训是每个人都会经历的一段重要阶段,因此教育培训类的经典书籍也是非常值得我们去了解和学习的。
下面是一些经典的教育培训类书籍,希望对你有所帮助。
1.《教育的艺术》这是美国教育学家艾伦·伯洛克的经典之作,他在书中阐述了教育的真谛和教育家的责任,对于教育者来说是一本不可多得的指南。
2.《教育心理学》由玛格丽特·格特纳和约翰·萨瓦尼编写的教育心理学教材,涵盖了教育心理学的基本理论和实践应用,对于教师和教育工作者非常有价值。
3.《学会学习》该书是美国心理学家约翰·霍尔的代表作,他通过深入研究学习过程和方法,阐述了如何更有效地学习和教育,对于学生和教育者都有很大的借鉴意义。
4.《教育的故事》由美国历史学家大卫·波普编写的教育史著作,详细讲述了教育的发展历程和各个时期的教育制度,对于了解教育的演变和发展具有重要意义。
5.《教育改革》美国教育家约翰·杜威的经典之作,他在书中提出了一系列的教育改革理念和方法,对于推动教育改革具有重要的指导意义。
6.《学习的艺术》该书是教育学家艾伦·德·博顿的著作,他通过对学习过程和学习方法的研究,提出了一系列有效的学习策略和技巧,对于学生和教育者都非常有益。
7.《教育的本质》美国教育学家约瑟夫·鲍尔斯基的代表作,他在书中探讨了教育的本质和目标,对于理解教育的意义和价值具有重要的启示。
8.《教育的哲学》由英国哲学家纳尔逊·格拉斯哥编写的教育哲学著作,他通过对教育哲学的研究,探讨了教育的基本原理和理念,对于教育工作者具有重要的指引作用。
9.《教育的未来》美国教育学家托马斯·福勒的著作,他在书中展望了未来教育的发展趋势和挑战,对于教育改革和创新具有重要的启示。
10.《教育的力量》美国作家乔纳森·库恩的作品,他通过讲述真实的教育故事,展现了教育的力量和影响,对于理解教育的重要性和意义具有很大的启发作用。
德尔福教育训练教材
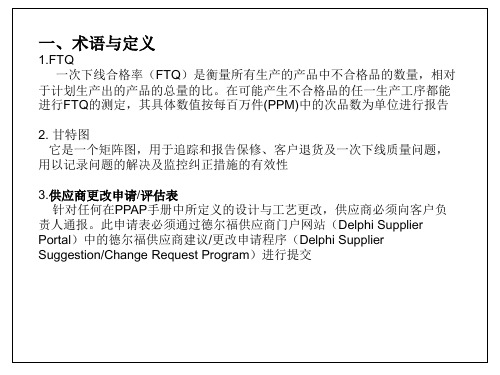
1.FTQ 一次下线合格率(FTQ)是衡量所有生产的产品中不合格品的数量,相对 于计划生产出的产品的总量的比。在可能产生不合格品的任一生产工序都能 进行FTQ的测定,其具体数值按每百万件(PPM)中的次品数为单位进行报告 2. 甘特图 它是一个矩阵图,用于追踪和报告保修、客户退货及一次下线质量问题, 用以记录问题的解决及监控纠正措施的有效性 3.供应商更改申请/评估表 针对任何在PPAP手册中所定义的设计与工艺更改,供应商必须向客户负 责人通报。此申请表必须通过德尔福供应商门户网站(Delphi Supplier Portal)中的德尔福供应商建议/更改申请程序(Delphi Supplier Suggestion/Change Request Program)进行提交
所有权变化 : 如果公司所有权有任何变化,供应商必须马上通知德尔福
客户代表变更 : 当供应商的客户代表有变动,供应商不仅要在10天内通知德尔福的相关部 门(采购,供应商质量,工程及生产计划),还要在门户网站的“供应商信 息”中更新联系信息 询问 : 所有的供应商都必须通过书面的或电子邮件方式在询问中说明的到期日或之 前回复所有的询问 给美国发货的供应商,海关反恐计划(C-TPAT) : 给美国发货的德尔福供应商必须提供并确认所有相关地点(按邓白氏编号区 分)“供应商信息”里关于C-TPAT部分的所有要求信息 客户沟通——补充 : 汽车零件的直接供应商有责任按零件号及制造场所来提供最新的有效的合适 的原产地证明和制造商宣誓书给德尔福。每年的一月一号德尔福的直接汽车零 件供应商都有责任去更新NAFTA原产地证明。NAFTA原产地证明只适用于以 下国家—美国,加拿大和墨西哥
供应商只可用下列方式之一将 NAFTA/ 制造商宣誓书/ 其它的发运场所单 发给 “NAFTA 贸易项目小组方式 1 – 发送电子邮件,地址见右 方式 2 – 传真到美国 传真号 1 – 915-612-6628 传真号 2 – 915-612-6763 方式 3 – 邮寄地址 M/C: 799-MTC-309 Attention: Trade Program Group –NAFTA 48 Walter Jones Blvd. El Paso, TX 79906-5315 原产地证明 : 可以去海关及边境(CBP) 网站获得一个可在线打印的 NAFTA 原产地证明表 (CF434)和填表说明 德尔福的原产国申报 : 德尔福是根据供应商提供的生产场所邓白氏编码来申报所采购的产品和零件的 供应商的原产国。如果邓白氏编码所对应的地址信息不正确,或者产品不是在这 个邓白氏编码所对应的地点生产的,供应商都有责任立即以书面形式提供正确的 信息给德尔福 供应商变更 : 供应商责任通过德尔福的供应商门户网站(见 7.2.3)上的供应商建议/变更 申请功能(DSS/CRP)来和德尔福的各个事业部沟通供应商提议的变更
SPC教育训练教材

制程能力数值方法 (1)
Ca(制程准确度 (Capability of Accuracy) 制程准确度) 制程准确度 衡量 制程实绩平均值 与 规格中心值 之偏差程度 Ca = ( X-μ ) / ( T / 2 )*100% μ
T = USL - LSL (规格公差 规格公差) 规格公差 单边规格因没有规格中心值, 故不能算 . 单边规格因没有规格中心值 故不能算Ca A: |Ca|≤12.5% | B: 12.5%<| |≤25.0% <|Ca| <| C: 25.0%<| |≤50.0% <|Ca| <| D: 50.0%<| | <|Ca| <|
CpU = (USL - X) / 3σ 或CpL = (X - LSL) / 3σ---单边规格 σ σ A: B: C: D: 1.33 ≤ Cp 1.00 ≤ Cp < 1.33 0.83 ≤ Cp < 1.00 Cp < 0.83
3 2 1 + 1 + 2 + 3
与规格中 心无关
SPC基本概念 基本概念
SPC之意义 之意义: 之意义 SPC( Control;统计制程管制) SPC(Statistical Process Control;统计制程管制)是指在制 造工程中去搜集资料,并利用统计分析,管制图, 造工程中去搜集资料,并利用统计分析,管制图,及制 程能力分析等技巧,从分析中去发觉制程异常原因, 发觉制程异常原因 程能力分析等技巧,从分析中去发觉制程异常原因,立 即采取改善措施,使制程恢复稳定状态, 即采取改善措施,使制程恢复稳定状态,避免及减少不 良品的发生. 良品的发生. SPC之效益 之效益: 之效益 (1)有效应用抽样计划进行管制,具有经济性. (1)有效应用抽样计划进行管制,具有经济性. 有效应用抽样计划进行管制 (2)可即时发现制程异常,预防不良发生. (2)可即时发现制程异常,预防不良发生. 可即时发现制程异常 (3)掌握制程能力,做为改善之提示. (3)掌握制程能力,做为改善之提示. 掌握制程能力
仓库管理人员教育训练教材-简体板

工业五部仓库管理人员教育训练教材培训目的:1.规范仓库人员的物料管理作业,落实“人有定责,事有定规,物有定位”2.提高仓库人员工作意识,了解“所作为何,为何而做”3.提高人员仓库管理的文化素养及职业道德,成为称职的仓库管理人员4.促使仓库人员自觉自主的自我改进,加强仓库管理水平,提高工作质量及效率培训课程纲要1.仓库管理概论2.仓库管理实务3.安全高效的仓库管理4.仓库管理观念与辅助工具制作人:李建松2010第一章仓库管理概论仓库属于服务单位,存在价值在于协助生产单位,为了保证物料计划的准确性,并依据实际情况及需求,建立并即时修正合适的仓库管理及作业流程,避免因为库存管理的缺失,使得物料库存庞大资金压滞,或停工待料耽误生产.1何谓仓库管理所谓仓库,就是指储存物料(包含原材料,半成品,成品,工具,设备等)的场所,仓库管理就是对物料依据正常程序,妥善管理进出与存放在仓库内的物料2仓库管理的功能仓库管理并非只是把物料堆积在仓库内,以下列举仓库管理的基本功能执行物料的分类,整理,保管执行物料的进仓,出仓管理确保物料实物,管理工具(帐簿,帐卡,计算机辅助管理系统),财务数量一致,为决策部门提供真实的生产及会计数据即时供应生产,保障出货销售情况,协助企业经营,达成营利的成果3仓库管理的目的仓库管理的目的,是为了准确的控制物料库存的水平,使物料不会发生匮乏,导致停工待料以及无法准时交货的状况;且避免因为库存数量过多,导致资金积压,财务周转困难增加贷款利息损失,造成持有成本的负担,而为了过多的物料,又必须增加管理人员及仓储土地及工具(储物框及货架),进一步增加了企业的成本负担仓库管理的基本工作,是执行货物出入库动作,和记录货物出入库存讯息,如进,领,退,补物料记录,库存移动,库存调整以及妥善保护库存物料等等;料帐的准确性可以提供管理者了解物料存货情况,适时做出合理的采购或存货处理等等决策4仓库地点规划的参考原则仓库的设置是为了满足企业生产经营,对物料进行周转和储备的要求,因此仓库的地点规划应满足以下原则符合生产工艺的原则仓库在地理位置上,应满足产品加工工序的特点,相关仓位应尽可能与加工生产现场相连接,减少物料的迂回运输符合进出顺畅的原则在仓库的规划上,应考虑到物料的运输问题,尽可能将进出仓门与出入通道或电梯相连,并规划出相应的运输通道,充分考虑运输路线的合理性及便利性满足货物安全的原则仓库是企业物资的主要集散区域,在规划仓库时,要特别考虑安全因素,除了要有足够的光线,电源,通风,消防器材外,也要注意物料的特性,是否具有可燃易爆及挥发,或毒性等等潜在危险因素并加以防护,对于外在环境方面,过度的光源是否会造成物料的损毁与退胶退色,或仓库内是否有漏水及虫鼠破坏的隐患第二章仓库管理实务一仓库管理实务1决定仓库位置应考虑的因素物料容易验收-进料检验区域的规划物料进出容易-通道及电梯的设置物料储存合理-外在环境因素物料发放容易-物料仓储与使用地点仓储空间应具有扩充的弹性2仓库区域规划应考虑的因素仓库与生产现场接近,并且通道顺畅仓库应有进仓门及出仓门并有明显的告示牌仓库人员的办公区域尽可能设置在仓库区域附近,并有明显的告示牌仓库内应留有必要的废次品存放区,物料暂存区,待验区,发货区仓库规划必须将安全因素考虑在内,并明确规定消防器材设置数量及所在位置每仓的仓门外,需张贴“仓库平面图”,反应该仓所在的地理位置外围环境,仓区货架仓位及通道3仓库物料堆放应考虑的因素尽可能的利用仓库空间,并采取立式堆栈的方式不同的物料依物料本身外形,性质,价值等等,来考虑不同的堆放方式物料的仓储要考虑先进先出的原则,对于立即会被领出的材料,可另设一处暂存区物料的堆置摆放方式,要考虑容器合理及仓储数量容易读取物料堆放应容易识别与检查,且良品,半成品,不良品,呆料,废料都要分开处理通道应有适当的空间,保持装卸的便利性,对于高处存放的时候,要有合适的辅助工具,使物料搬运得以顺畅进行二仓库物料的收发运作1仓库货物验收的注意事项品名,品号,规格-确认出入库的货物,是否与相关单据上的品名,品号,规格一致,并确认所存储的仓位是否正确数量-确认出入库货物的计量单位,货物进出仓前应严格点数或过磅质量-物料需附有相关检验合格证明方可入库,在物料仓储期间,证明文件必须妥善保管,且仓管员应主动注意相关物料的质量情况,适时对存储物料做适当处理,确保不良品不流出仓库凭据-单据不全不收发,手续不齐不办理2物料的直接需求与间接需求直接需求-经由生产计划延伸的工作指派,指生产部门为求生产正常运作,而导致对物料产生的需求间接需求-除以上生产运作以外,而对物料产生的需求,即为间接需求※我部对物料的定义不同于以上的讲述,直接需求物料,为出现在出货产品上的物料,其余在生产当中需要的物料包含刀具,耗材,劳保用品等等统称为间接物料,各公司经营及生产模式不同,因此就会产生不同的定义3发料与领料的定义发料-仓库单位根据生产计划,将仓库储存的物料,直接向生产单位发放的现象称为发料领料-物料由生产单位人员,在执行生产计划时,根据生产计划填写合格领料单据,向仓库领取物料的现象称为领料4发料与领料模式的适用范围物料的发放模式有其适用范围,并非所有的物料都可由仓库发料,相对于直接需求的物料,较适合使用发料模式,而间接需求的物料,较适合使用领料模式5采取发料模式的原因稳定的订单生产计划生产产品较单纯化建立准确的标准损耗量质量异常的发生率低防止生产物料供应不继6采取领料模式的原因ABC级物料中,C级物料偏多生产计划经常更改产品多样化及物料共享性高生产半成品断阶频繁各公司经营观念及管理手法的差异,习惯性做法三仓库物料的保管与储存搬运1仓库储存的三个原则保质:防火,防水,防压,防虫鼠,防一切可能的破坏保量:定点,定位,定量,定员,确保数量正确无误先进先出2仓库储存应注意事项危险物品依据特性,妥善保存定点存放避免选用潮湿的区域做仓库保持适当的温湿度,注意通风和良好的照明条件考虑防火,防水,防盗等等的保护措施通道及消防器材放置区域,保持畅通不可堆放物品做好货物防压措施,存放时不可超过地板及货架承重负荷货物放置平稳整齐,货架及货框合理选用仓库空间保持整齐清洁,按“5S”要求进行维护3仓库管理所指的帐物卡证帐:仓库物资的管理纸账本,或计算机系统物:仓库储存的物料卡:记载仓库储存物料进出的数据卡证:出入库的有效凭证(料单),及质量合格纪录等等4物料搬运的注意事项搬运过程中,尽量使用工具协助,提高工作效率在合理的情况下,减少搬运次数及搬运时间缩减搬运距离节省人力通道不得有障碍物,以防阻碍运输及人员与货物的安全物料,半成品,成品,不良品等等应有明确的产品判定及位置标示,不可因搬运而造成混乱,甚至导致生产混乱搬运时注意人员本身及物料的安全四呆废料的管理1何谓呆废料呆料为仓储物料摆放超过一定时间,耗用量极少,且库存周转率极低的物料,这种物料可能偶尔耗用少许,甚至摆放一年都用不上废料是指报废的物料,经过相当使用后,本身已残破磨损或超过保质期限,以至失去原有功能,或本身存在其它异常状况,无法使用的物料2呆废料处理的目的物尽其用,减少损失减少资金积压节约仓储空间减少人力及管理费用正确的体现公司的经营成本,提供决策者正确的信息3呆料产生的原因销售部门a市场预测错误,造成销售计划不准确,导致生产计划变更b客户订单不确定,订单频繁更改c客户变更产品型号规格,内部信息传递不即时计划与生产部门a产销衔接不良,生产计划频繁变更,生产计划错误,造成备料错误b生产线的管理操作不良,对生产线物料的发放及领取,与退料管理不当,造成生产线呆料的产生物料控制与仓库部门a备料计划不当,物料过分采购,造成呆料的产生b库存管理不良,存量控制不当,帐料不符,造成呆料的产生c因仓储设备不理想或人为疏失,因而发生的灾害损及物料采购部门a物料采购过程疏失,造成数量异常b供货商辅导不足,产生供货商质量,交期,数量,规格,等无法相互配合,导致呆料的产生质量管理部门a进料检验人员检验疏忽b进料采取抽样检验,允收的合格品中掺杂不良品c检验仪器设备不够精良4废料产生的原因物料储存环境不良,造成腐蚀,退化,变质等物理及化学变化物料储存时间过长,导致发生物理及化学变化因正常生产而导致的边角料,无法再加以利用因生产异常而导致物料不合乎正常规范,且无法返修或修改再使用因客户或功能设计需求而变更物料,且无法返修或修改后再使用5呆废料处理的途径调拨给其它单位利用返修或修改使其得以再利用使用于新款产品打折扣出售给原来的供货商,或与其协商以物易物处理报废物料可依据材质加以收集,再以废品卖出五仓库的盘点管理1物料盘点的步骤仓库内部先期准备工作确定盘点方法决定盘点日期培训盘点人员依据计划进行盘点差异原因的追查分析与检讨物料盈亏的后续处理2准备工作及盘点方法说明确定盘点程序盘点日期需配合财务部门成本会计的决算按级别程序决定盘点复盘,监盘的程序及相关人员盘点用的报表和表格需规范化,并确认相关盘点人员皆了解,最好能事先进行讲解或演练仓库的清理清洁与帐目结清3盘点后的处理措施修补改善措施a依据盘点结果,对分管人员进行检讨及沟通b料,帐,卡的修正处理c不足物料的后续补料处理d呆,废物料的后续处理e加强整理,整顿工作预防改善措施a若发现库存呆料比率过重,应邀集相关单位人员研究,设法改善或降低b存货周转率低,存料金额过大造成财务负担时,应设法降低库存量c物料供应不继率过高时,设法强化物料计划与库存管理d物料盘点工作完成后,对于发生的差额,错误,呆滞报废物料,盈亏,损耗等结果,加以分析与检讨,并制定相关防制办法,以避免以后再发生第三章安全高效的仓库管理1仓库管理的相关事项仓库位置合理,距离生产车间适当平面及整体性得当储位立体化,节约并尽可能放大储存空间通道,照明,防水,防火,防盗,及辅助工具等措施物料包装,标示统一并合乎规范物料依序整齐摆放保持整齐清洁,将5S精神落实到日常工作建立完整正确的料,帐,卡数据当日作业,当日完成依相关规定进行收,发,补料作业呆,废物料实时正确处理随时做好盘点工作,时时保证料帐一致做好生产的后勤服务2仓库管理的安全性考虑仓库外在环境对物料可能造成的安全威胁物料仓储过程可能对环境造成的安全威胁物料仓储周转过程中,可能对物料造成的安全威胁物料处理过程可能对人身安全造成的威胁a使用手推车或拖车运送货物时,应注意物料堆栈高度,不可超过操作人员的视线高度,搬运速度适中,迎面有人或在下坡及转角处时,要提前减速,以免发生工安危害事件b使用手推车或拖车堆栈物料时,要确保物料不会因堆栈过高,而发生倾斜或倒塌的情况c使用手推车或拖车堆栈物料时,要注意物料堆栈的重量,避免因过重而导致搬运过程发生工安危害事件d手推车或拖车只能在平稳的地面运行,不可强行越过台阶或过大的坑洞3高效率的仓库管理仓库管理不可仅仅因为安全与质量,就忽视了对效率的要求考虑成本因素以外,所有仓管员应主动的设法提高工作效率,例如:a使用手推车,减少人工搬运b使用大纸箱或塑料框,对产品进行批次转运c充分利用货物储存空间,以纸箱代替塑料框节约成本d缩短货物周转时间,降低呆滞废料的储存时间4积极的仓库管理仓库是服务单位,因此需要与内外部人员保持良好互动关系仓库部份作业会关系到厂商请款,而且会与公司财务及采购单位关联,因此仓管员必须拥有责任与荣誉感,以严谨的态度处理好每一份单据仓管管理条例一旦发布执行,仓管员必须确实明白并严加遵守仓库管理可能因时事而做修正,因此仓管员日常工作需保持弹性,但不可因人情世故,而造成违规操作5仓库当中的5S管理操作1整理确认仓库内所有的物料项目及数量将仓库内所有物料加以分类定期对库房内的呆滞报废物料进行处理确认仓库内空间的使用率将仓库管理的辅助工具造册,并规划保管人2整顿仓库空间进行规划,并制作规画图悬挂在各仓入口处按规画图进行区域标示物料按规划区域放置物料放置必须整齐,容易收发物料放置后要有明显且易于辨认的标示仓库通道必须确保畅通,不可有堵塞的情况仓库管理的辅助工具也要加以规划,使用后放置定位并摆放整齐消防器材必须摆放于明显处,并容易拿取使用3清扫地面,墙壁,天花板,门窗都要打扫干净储存货物的货架空间要加以打扫,针对需求加以防锈防蚀保护物料不能裸露摆放,包装外表也要清扫干净物料储存区保持通风,并有适当的光线照明仓库管理的辅助工具要保持清洁,并视需要加以上油或维修保养仓库人员办公区域应随时保持整齐,并每日加以打扫4清洁随时自我检查,互相检查,定期或不定期进行检查对不符合的情况实时进行纠正处理每天上下班花5分钟时间进行5S清洁工作物料每次收取后,随手对货架进行清理动作5素养穿着服装保持整洁得体,仪容整齐大方上班时间精神饱满,待人言谈举止文明有礼亲切大方工作时有团队精神互帮互助,遵守相关规定事项做好自己的每一项工作,珍重自己的每一个签名不推委不卸责,将荣誉表现在工作成果上第四章仓库管理观念与辅助工具1订货点法与物料需求计划MRP(Material Requirements Planning)订货点库存法,为给库存物料制定一个最低存量标准,当库存数量低于这一标准时,就下单采购或生产该项物料,此做法适合稳定消耗的物料20世纪60年代,生产产品渐趋复杂,针对订货点库存法的不足,提出分层式产品结构,及物料的独立需求与相关需求的概念。
GA教育训练教材(For STAFF)

一 GA 基本常識
GA 產品係指以下產品 a 由ASUS自行設計、製造、銷售或配銷之綠色產品。 b ASUS委託第三者設計、製造,貼有ASUS商標而銷售或配 銷之綠色產品。 c 由第三者外包給ASUS設計或製造之綠色產品。
自有 品牌 GA 產品 OEM
委外 加工
一 GA 基本常識
產品環境管理物質 經ASUS 判斷在零組件及元件組成中,含有對人類及地球環境 存在顯著影響之物質.
a) 存在於天然材料中,在精製過程中,技術上不能完全去除的 物
b) 質(如天然雜質)々 b) 合成反應過程中產生,而在技術上不能完全去除的物質。
三 ASUS 技術標準 S-AT2-001簡介
塑膠
由人造高分子聚合物組成之材料以及原物料
明確而言,“塑膠”意指由高分子聚合物所組成之物質,包含有樹 脂 、薄膜、黏著劑、黏貼膠帶、射出成型物,以及合成橡膠產品等。 天然樹脂與上述任一物質所合成之物質亦視為塑膠。
電纜
被覆線材
彩色部分
內部被覆 被覆線材上的油墨
外部被覆
二 WEEE & ROHS 法規簡介
何謂WEEE & ROHS ?
歐盟官方公報于2003年2月13日正式頒布了兩項指令 WEEE-2002/96/EC <<報廢電子電器設備指令>> - Directive 2002/96/EC on the Waste Electrical and Electronic Equipment
S-AT2-001
目前最新版本是Rev.5
主要內容:
外購模組,零部件,副資材和材料中所含環境管理物質之管理規定
三 ASUS 技術標準 S-AT2-001簡介
外購模組,零部件與材料的適用範圍
7S教育训练简明教材
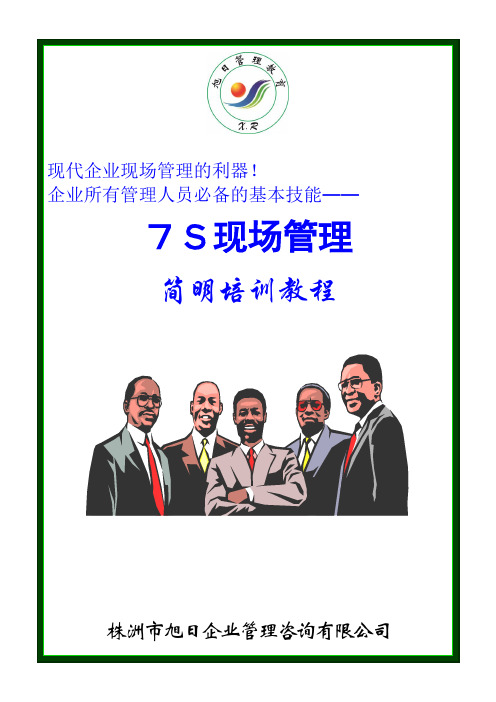
现代企业现场管理的利器!企业所有管理人员必备的基本技能——7S现场管理简明培训教程株洲市旭日企业管理咨询有限公司序: 公共汽车改善个案(生产力的提高):①②③④⑤RRRR RRRICRBPI 改善阶段BPR 改善阶段★整理★整顿★清扫★清洁★素养★安全★节约(维护)7S的意义7S定义效果目的整理(Seiri)区分要与不要的东西,把不要的东西处理掉♦库存量减少●♦把场地弄宽并能有效应用●♦物品不要纷失●♦不会再漏油或漏气●♦不再浪费时间在找●♦没有不安全的情形●整顿(Seiton)厂区安排、定位、规划、使要用的东西能立刻拿到清扫(Seiso)把整理整顿后留下的垃圾、污秽、异物清理干净♦维持并提高设备的性能●♦能扫除设备的重要地方,并给予检查●♦把工作环境弄好●♦消弱灾害发生的原因●♦保持了所有场所的干净、卫生与整洁●清洁(Seiketsu)不论是工作区或公共场所都有要保持整洁素养(Shitsukei)养成遵守既定的规章制度的良好习惯♦大意减少●♦遵守规定的事●♦有好的人际关系●安全(Safety)安全是一种行为,主要是塑造一种每个人都能安心工作且愉快的工作环境。
♦确保遵守标准作业●♦塑造安定感●♦培养危险预知的能力●节约/维护(Sparing/ Safeguard) 节约是一种习惯性行为,主要是塑造每个人都有能养成一种良好的从内心出发的减少浪费的行为。
♦确保降低运作成本,节省开支●♦培养开源节流的整体素质●减低成本提高效率提高品质降低故障安全保障提高干劲推行7S的目的和作用一、推行7S的目的:1.改善提升企业的形象;2.促成生产效率的提高;3.改善零部件的周转率;4.减少或消灭故障发生;5.保障企业的生产安全;6.降低企业的生产成本;7.改善员工的精神面貌;8.确保订单的交货日期。
二、推行7S的八大作用:有效推行7S,可以使企业追求“八个零”,创造现代企业的“八零”工厂:1.企业的亏损为零;2.企业的无益消耗为零;3.企业的浪费为零;4.企业的故障为零;5.企业的不合格产品为零;6.企业的事故为零;7.企业的投诉为零;8.企业的缺勤为零。
Manual Guide i教育训练教材

CH01 Manual Guide *介紹 (5)1. Manual Guide *機能介紹 (5)1.1 畫面簡介 (5)1.2 支援功能簡介 (5)CH02 加工前準備機能 (6)1. 機能概述: (6)1.1 概要 (6)1.2 量測種類: (6)1.3 量測使用的工具: (6)1.4 量測的方法: (6)1.5 回傳資料: (7)2. 操作流程 (7)2.1 加工前準備量測畫面 (7)2.2 端面量測(Single surface measurement) (8)2.3 外徑量測(Outside diameter work setup) (10)2.4 內徑量測(Inside diameter work setup) (12)2.5 外側寬度量測(Outside width work setup) (13)2.6 內側寬度量測(Inside width work setup) (15)2.7 轉角外側量測(Measurement of corner outside) (17)2.8 轉角內側量測(Measurement of corner Inside) (20)2.9 傾斜工件量測(Angled work measurement) (24)CH03 Manual Guide *的加工程式製作 (27)1. 銑床範例-1 (27)1.1 加工圖 (27)1.2 加工程式製作內容 (28)1.3 加工程式內容 (53)1.4 圖形模擬結果 (54)2. 銑床範例-2 (測驗用) (55)2.1 加工圖 (55)2.2 圖形模擬結果 (55)3. 銑床範例-3 (5面加工應用傾斜工作面TWP機能來製作) (56)3.1 加工圖 (56)3.2 加工程式製作簡介 (56)3.3 加工程式內容 (59)3.4 圖形模擬結果 (60)4. 車床範例-1 (61)4.1 加工圖 (61)4.2 加工程式製作內容 (62)4.3 加工程式內容 (83)4.4 圖形模擬結果 (83)5. 車床範例-2 (極座標補間範例) (84)5.1 加工圖 (84)5.2 加工程式製作流程 (85)5.3 加工程式內容 (99)5.4 圖形模擬結果 (100)6. 車床範例-3 (圓筒補間範例) (101)6.1 加工圖 (101)6.2 加工程式製作內容 (101)6.3 加工程式內容 (104)6.4 圖形模擬結果 (104)7. 車床範例-4 (測驗用) (105)7.1 加工圖 (105)7.2 圖形模擬結果 (105)CH04 將Manual Guide *轉換成ISO碼程式 (106)CH05 螺紋修復機能 (107)1. THREAD REPAIR(螺牙修復機能)操作說明 (107)CH06 基本參數設定流程 (112)CH07 Manual Guide *機能更新一覽説明 (114)1. 補充説明及參數設定 (114)2. TMN12-032E (TMN12-032E -2-1) (115)3. TMN12-060 (118)4. TMN13-006 (119)5. TMN13-027 (120)6. TMN13-089 (121)7. TMN13-100 (123)8. TMN13-144 (124)9. TMN14-035 (125)10. TMN15-039 (126)11. TMN15-040 (128)12. TMN16-077~078 (129)13. TMN16-079 (129)14. TMN17-029~030 (131)15. TMN17-055 (132)16. TMN17-056 (142)17. TMN17-057 (143)CH08 Manual Guide i Set-up Guidance量測功能設定説明 (149)8. 手動模式量測時的設定方式: (149)8.1 適用機型:一般機型FS30i/31i/32i-B、FS0i-F、FS0i-D (149)8.2 OPTION:S790 (149)8.3 參數設定: (149)8.4 PMC設定: (150)8.5 操作範例: (152)9. 傾斜面分度指令的量測功能: (156)9.1 適用機型:有旋轉軸機型FS30i/31i/32i-B、FS0i-F、FS0i-D (156)10. 5軸加工機的旋轉軸量測循環 (157)10.1 適用機型:有旋轉工作台的機型、刀具旋轉型式FS30i/31i/32i-B (157)10.2 OPTION:S790 (157)10.3 參數設定: (157)11. 探針長度量測以及Stylus Ball直徑量測 (159)11.1 說明: (159)11.2 適用CNC: (159)11.3 使用說明: (160)CH01 Manual Guide * 介紹1. Manual Guide * 機能介紹操作導引的機能,支援所有日常加工的工作,包含建立程式、加工前準備、工件量測…等等,全部在all-in-one 畫面中來操作。
SAP教育训练教材
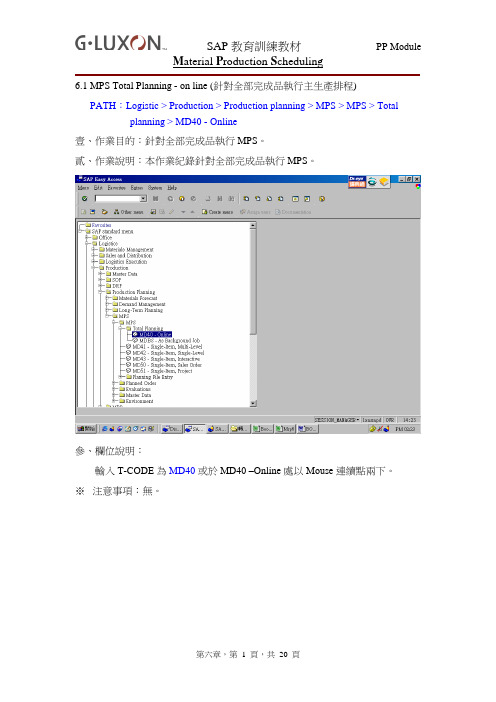
6.1 MPS Total Planning - on line (針對全部完成品執行主生產排程)PATH:Logistic > Production > Production planning > MPS > MPS > Total planning > MD40 - Online壹、作業目的:針對全部完成品執行MPS。
貳、作業說明:本作業紀錄針對全部完成品執行MPS。
參、欄位說明:輸入T-CODE為MD40或於MD40 –Online處以Mouse連續點兩下。
※注意事項:無。
參、欄位說明:1.Plant:選擇廠別代號LDG1。
2.Processing key:MPS執行的原則(1)NETCH –針對所有改變的部份執行MPS。
(2)NETPL –針對計劃改變的部份執行MPS。
(3)NEUPL–針對全部完成品重新執行MPS。
3.Create Purchase req.:建立請購是根據(1)Purchase requisitions –根據請購需求。
(2)Purchase requisitions in openingperiod –根據未到期之請購。
(3)Planned orders –根據計劃訂單。
4.Schedule lines:排程時間(1)No schedule lines –不需要排程。
(2)Schedule lines in the opening period –根據未到期的做排程。
(3) Schedule lines –需要排程。
5.Create MRP list:建立MRP需求表(1) MRP list –要。
(2)Depending on the exceptionmessages–根據訊息建立。
(3)NO MRP list –不要。
6. Planning Mode:執行計劃方式(1)Adept planning data–容許先前資料。
(2)Re-explode BOM and Routing–重展BOM及製程。
FSME040075次因分析教育训练教材

人員未按 SOP作業
作業人員忽略 檢查動作
未明確告知作業 員檢查之目的
人員對不良的警 覺性不高
安規SOP 電源 線檢驗圖示不
完整
監管機制不 強
對策
修訂安規教育訓練教材 及差異料教材
以警示語的形式提醒作 業員必須加強檢查各安 規部品
QA與PD共同運行安規不 良品混入機制
修訂PKG3站安規SOP.加 入電源線插頭圖示,並完 成教育訓練
重新定義流程並完 成教育訓練
---1/21`05
退料區域未合 理規劃
重新定義流程並完 成教育訓練
---1/21`05
重新規劃退料區 ----1/20`05
• Power Cord 誤放之要因及對策 ---02
問題 點
一次因
二次因
三次因
四次因
重複教育訓練體 系不完善
誤
放
電
源
線 機
人員未
台
檢出
流
出
原
因
5次因分析教育訓練
報告作成: OEM 戴剛
概論
問題分析解決流程
發掘問題真因 原因分析 執行改善 成果追蹤確認.
最有效方法之一,就是持續地問 “為什麼?”.因為問了5次為什麼,
就很有發掘問題真因的機會.
SAMPLE:
假設你看到一位工人,正將鋸屑灑在機器之間的通道地面上.
你問:"為何你將鋸屑灑在地面上?" 他答:"因為地面有點滑,不安全. " 你問:"為什麼會滑不安全? " 他答: "因為那兒有油漬"
何時?
程度,傾向
甚麼樣的場合,狀況,在那之後如何? 問題的大小,衍生性問題
5M Check 教育训练教材
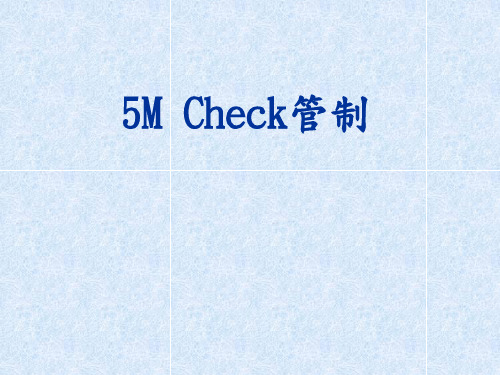
【二】
■ 5M_Check的解读. Material
5M_Check的构成
物料
□采购→检验→储存→投入→使用 □是否对产品质量发生影响? □控制部品质量及信赖性 □使用正确的物料进行生产
生产中每天必做的4M1E
料:
1.(物流员要报告)物料是否备齐?欠料是否 会及时到位? 2.物料有无变更(物流报告)?版本是否正确 (作业员自检)? 3.是否有不同物料放在一起?有无正确标示 ?
生产中每天必做的4M1E
法:
1.SOP是否齐备?版本是否正确? 2.作业者反应SOP异常是否得到处理? 3.员数管理是否正确?作业员是否理解员数 管理自检意义?
5M Check管制
项目
一.5M 定义及解读 二.每日生产的4M1E
一.5M_Check的构成
■ 5M_Check的构成:
人
人员应接受足够充分的教育及训练 使用优良及正确的物料 选用正确的机器(设备,治具)操作 遵守已确认,规范化的标准 具有符合要求的性能及满足客户的质量需求
物 料
机 器 方 法 基 准
5M_Check的构成
■ 5M_Check的解读.
Measurement
基准
□设计单位制订出正确的产品标准. □设计单位选用最能满足标准的部品. □制定出最能满足产品标准的制程并标准化. □制造选用最能满足产品标准的设备并规范化. □生产准予→出货放行 有判定标准.
□品质三不原则:不接受不良品、不制造不良、不流出不 良品
生产中每天必做的4M1E
- 1、下载文档前请自行甄别文档内容的完整性,平台不提供额外的编辑、内容补充、找答案等附加服务。
- 2、"仅部分预览"的文档,不可在线预览部分如存在完整性等问题,可反馈申请退款(可完整预览的文档不适用该条件!)。
- 3、如文档侵犯您的权益,请联系客服反馈,我们会尽快为您处理(人工客服工作时间:9:00-18:30)。
五﹑抽样计划之讲解与使用
实例說明﹕ 2. 9/10白班生产LM7R上盖300PCS,依A.Q.L.批量 “281~500”,品管于检验中需抽样50Pcs,后发现1PC铜 钉漏埋,此料件A.Q.L.为Ma.:0.65 Mi.:1.0 ﹐根据缺 点之定义,判定为Ma. 如在正常检验阶段﹐依A.Q.L. Ma.为0.65%其允收水 准为Ac.:1 Re.:2﹐即“1收2退”﹐故判定為OK. 如在加严检验阶段﹐依A.Q.L.的允收水准为﹕Ac.:1 Re.:2 ﹐即“1收2退”﹐故判定為OK. 如在減量检验阶段﹐依A.Q.L.允收水准为Ac.:0 Re.:1﹐即“0收1退”﹐故判定此批產品为NG,需重新 sorting。
量测大小
1CM
量测间距
五﹑抽样计划之讲解与使用 5.1 目的﹕
希望由少量的样本检验﹐以对整体之【检验批】作正 确的品质判定﹐并因此可減少检验所投入成本﹐并能适 切的确保产品品质。
5.2
基本名詞﹕
5.2.1检验:对实体的一个或多个特性进行的诸如测量/检查/ 试验或度量并将结果与规定要求进行比较以确定每项特性的 合格情况所进行的活动. 产品质量检验是采用测量/检查/试验等方法,将单个产品与 技术要求相比较的过程. 5.2.2单位产品:为实施抽样检查的需要而划分的基本单位,如 一个齿轮/一台电视/一双鞋/一个发电机组等
一﹑电脑外壳之基本构造
N/B
TV
N/B
TV
前框
后盖
上盖
下盖
枕手蓋 K/B
枕手盖
二﹑检查面之定义及区分
A级面﹕用户正常使用或放置时﹐正视明显外露可见之 外观面﹐如正面﹑正侧面﹑顶面。 B级面﹕用户正常使用或放置时﹐正视非明显外露可见 的部分﹐如两侧。 C级面﹕用户正常使用或放置时﹐不会经常看到的面﹐ 如后面(I/O面)﹑底部。 D级面﹕部分组件经拆卸后可见的面。
八﹑品質管制名詞
PPM (Percent Per Million)百万分之一 ECN (Engineering change notice )工程变更通知单 PCN (Process change notice )制程变更通知单 ECR (Engineering change request)工程变更申请单 PCR (Process change request) 制程变更申请单 QA (Quality Assurance)品质保证 QC (Quality Control)品质控制 QM (Quality Managerment)品质管理 TQM (Total Quality Managerment)全面品质管理 SPC (Satistic process control)统计制程管制 QIT (Quality Impovement Team)品质改善小组 SQC (satistic quality control)统计品质管制 Sorting 挑选﹑选別(检查手法 用治具选别好坏) Rework 重工(用工具作矫正,使不良变为良品)
5.5、品质检验应用的抽样标准:
(1) 机械电子轻工等行业标准:
MIL-STD-105D抽样标准(ISO 2859) (2) PC业界常用标准: C=0抽样计划 即针对检验项目,只要有不 合格一律拒收 MIL-STD-105E( Major/Minor/Critical ) 目前厂内使用之抽样计划为MIL-STD-105E抽样标准, ISO 2859为调整型抽样检查,见附件
2
0.5mm
10mm
1
量测线条 量测线条 之宽度 之长度
四﹑黑点表之使用
• 实例說明(2)﹕ • Spec.: 棉絮 、颗粒S≦1.0m㎡ 允許二点﹐D≥10cm .现发现此产 品有棉絮与颗粒﹐则用黑点表进行 量测﹕首先于黑点表中找到用于量 测面积之区域(如右图所示)﹐如可完 全覆盖且两点之间的距离量测后 ≥10cm则判定OK2.抽样计划表
3.图纸
4.样品(客签标准样/限度 签样)
3.样品(客签标准样/限度签样)
八﹑品质管制名词
IQC (IN coming quality control)进料检验 IPQC (In process quality control)巡检或制程检验 FQC (Final quality control)成品检验 OQA (Outing quality assurance)出货品质保证 A.Q.L.(acceptable quality level)允收品质水准 SIP (Standard inspection process)检验标准书 SOP (Standard operation precess)作业标准书 Acc (Accept)允收 Rej. (Reject)拒收 Maj. (Major defect)主要缺点 Min. (Minor defect)次要缺点 PMP (Process Management Plan)制程管制计划 PM (Porject Managerment)专案管理 批(Lot)具有相同来源﹐在相同条件下﹐生产所得的一群相同规 格的产品
六﹑缺点之定义 严重缺点(Cr.): 对使用﹑维护或依赖该产品之人员﹐有 发生危险或不安全结果之缺点。
主要缺点(Ma.)﹕严重缺点以外之缺点﹐其结果可能会 导致故障或实质上降低或影响产品功 能﹐无法达成期望目标之缺点。
次要缺点(Mi.)﹕有瑕疵﹐但不会影响产品功能。
七﹐产品检验之依据 一﹑首件产品检验之依据 二﹑成品检验之依据 1. 作业标准书(Sop.) 1.成品检验标准书(Sip.)
5.2.3样本单位;从检查批中抽取用于检查的单位产品称为 样本单位. 5.2.4样本:样本单位的全体称为样本是指从[检验批]中所 抽取一个或一个以上的产品所組成的。其代表符号以英 文字母小写[n]代表. 5.2.5样本大小:是指样本中所包含的样本单位数量. 5.2.6全数检验:将送验批之产品或物料进行全检. 5.2.7抽样检验:从送验批产品中抽取一定数量之样本进行 检验,然后根据不合格品的多少或质量特性,按一定规则 对产品总体(或产品批)的质量进行判断,就称为抽样检验 5.2.8批:同种产品或物料集聚在一起作为抽验对象的称为 批. 5.2.9送验批:送去进行检验之批称为送验批. 5.2.10样本数;从送验批中抽取之样本数量称之为样本数.
五﹑抽样计划之讲解与使用
五﹑抽样计划之讲解与使用
实例說明﹕ 1.使用此抽样计划表对产品进行抽样检验时, 首先找出检验批量所在的范围,依 检验批机种之(减量/ 正常/加严)之代码(A/B/C/D/E„),从样本大小代码找 出抽样数进行抽样检验,从检验结果之不良现象依据主要 缺点,次要缺点,严重缺点的定义,依据SIP中之允收品 质水准进行判定,例如、使用此抽样计划表对某批产品进 行抽样检验,此批产品N(批量)=1250PCS,AQL(允收品质水 准)Ma.(主要缺点)0.65% Mi.(次要缺点)1.0%。 则:依正常检验之抽样方案: n=125.不良为主要缺点时 Ac=2,Re=3,不良为次要缺点时Ac=3,Re=4 依加严检验之抽样方案:n=200,不良为主要缺点时 Ac=3,Re=4,不良为次要缺点时Ac=5,Re=6 依减量检验之抽样方案:n=80,不良为主要缺点时 Ac=1,Re=2,不良为次要缺点时Ac=2,Re=3
如客户有特殊要求则以客户要求定义之
三﹑外观检查条件
产品处的光源为800-1200LUX
产品与水平面 成30度角
眼睛至产品表面距离为30-50cm
水平面 产品
四﹑黑点表之使用
黑点表﹕检验人员无法以目视对不良点 进行明确判定时﹐以辅助完成判定之工 具。 针对不良点有用直径/面积两种不 同之定义。(直径定义﹕mm﹐面积定 义﹕mm2) S 代表面积 N 代表数量 D 代表两处缺陷之间距 L 代表长度 W 代表宽度 Φ 代表直径 一般外观检验标准中有以下几种不 良﹐均可用黑点表加以判定﹕ 颗粒﹑碰伤﹐斑点﹐凹陷﹐污点 有﹑无感刮伤﹐棉絮
如客户有特殊定义则以客户要求定义之。
二﹑检查面之定义及区分
N/B
C B
A
二﹑检查面之定义及区分
TV
A B C
D
三﹑外观检查条件
照明条件﹕最小照度要求在800-1200lux 检查视力﹕矫正后1.0以上 检视距离﹕30-50cm 检视时间﹕依产品大小及检验项目而定大件<上盖﹑下盖﹑前 框﹑后盖﹑K/B﹑枕手盖> 20秒以内﹔小件10秒以内 检视角度﹕检验员手持被测物与水平面成30度,并以垂直轴为 轴心向左或右作30度旋转。当零件有多个面时,每个面都必 须当作独立面进行检验。
苏州大昶/大智电脑配件有限公司
NOTE BOOK
基础知识与检验技巧
涂裝品管
目录﹕
一﹑电脑外壳之基本构造 二﹑检查面之定义及区分 三﹑外观检验条件 四、黑点表之使用 五﹑抽样计划之讲解与使用 六、缺点之定义 七﹑产品检验之依据 八﹑品质管制名词 九﹑五大件检验之方法
一、电脑外壳之基本构造
上盖 (top cover/up cover/logic up) 下盖 (bottom cover/low cover/logic low/base) 前盖 (bezel/lcd bezel) 后盖 (lcd cover/panel/display) K/B (Strip cover) 枕手盖 (Palmrest) 小件 (Hdd door/DDR door/DVD Panel/Battery cover/Hinger cover/I/O cover) N/B基本上由以上六大件及小件组成。
5.2.11批量:构成批之所有个数称之为批量,是指每个[检验 批]内产品的总数量﹐其代表符号以英文字母大写[N]代表. 5.2.12允收品质水准:购买者满意的产品检验批中所含最高 之不良率。其代表符号以英文字母大写[AQL]代表。 5.2.13合格判定数﹕判定一批产品是否合格或不合格的基 准不良个数称爲[合格判定数].其代表符号以英文字母[Ac] 代表. 5.2.14不合格判定数﹕其代表符号以英文字母[Re]代表. 5.3、抽样检验的概念: 3.1在生产实践中工序与工序/库房与车间/生产者与使用 者之间进行産品检验时,要把产品划分为批.一个产品批总 是由一定产品数量组成,抽样检验就是从产品批里取一 部分产品进行检验,然后根据样本不合格品数或质量特性 的规定界限,来判断整批产品是否合格.