己内酰胺生产技术
己内酰胺生产技术及应用_王雪梅
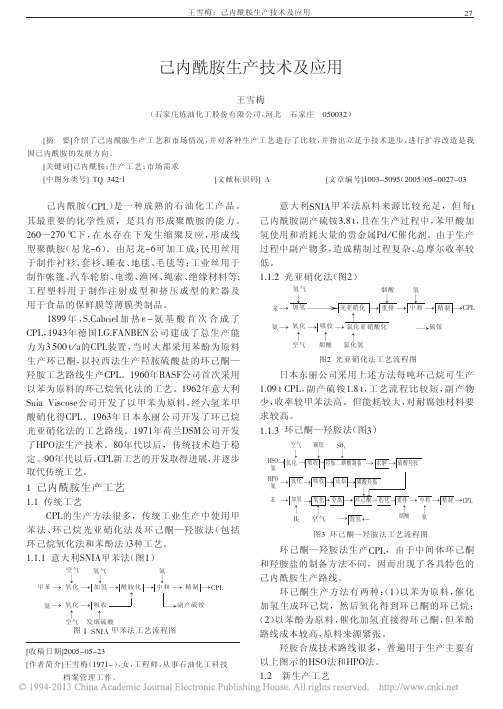
意大利 .<8; 甲苯法原料来源比较充足,但每 @ 己内酰胺副产硫铵 7/, @ , 且在生产过程中, 苯甲酸加 氢使用和消耗大量的贵金属"K A ! 催化剂。由于生产 过程中副产物多, 造成精制过程复杂、 总摩尔收率较 低。 (图$) +/+/$ 光亚硝化法
氢气 苯 " 加氢 氨 " 氧化 空气 烟酸 氢 中和
中国大陆
@ 9 9%= >%= ; ; $> ?%; ;%= 9%= $$ ? $= $$%: $> ?%& =
/6A6B
宇部 名古屋 东海 新居滨 新居滨 黑崎 头份 小港 蔚山
$%&%: 氨肟化 3 气相重排工艺
巴斯夫、 住友等公司都开展了在高温气相中用 固体酸催化剂进行贝克曼重排的研究。新工艺采取 流化床反应器, 环己酮肟 3 甲醇 3 氮气在高温下通过 分子筛, 转化率为 ;;%7< , 己内酰胺的产率为 ;=%7< , 该工艺在 = 万 5 3 6 的装置上得到验证,由于反应后回 收和循环甲醇, 可以避免硫酸铵生产。 目前中石化总公司, 组织对 !"# 工艺进行攻关, 在关键技术的国产化上取得突破性进展, 形成了有 在苯法!"#生产技术 自主产权的!"#先进生产技术。 的开发上,形成了环己烷仿生催化氧化制取环己 酮、 环己酮胺肟化制取环酮肟、 环己酮肟三级重排 在甲苯法!"#生产技术的开 工艺和!"#精制新工艺。 发上,形成了非晶态镍部分取代钯碳催化剂技术、 失活钯碳催化剂超临界萃取再生技术降低贵金属 催化剂的消耗。 石化纤联合各有关单位及设计院对六氢苯甲 酸—环己酮肟联产 !"# 组合工艺的研发成功,使石
RJS[)#(+ W4@=.1+-#=%,#.( .? .-,"./%(6 <%-%/".1.<"+(.2= .- ,"+#- +,"+-= ,. ,"+ 0.--+=<.(6#() 1+,%A-.1.<"+(.2= .- +,"+-= R*S4X* : JD JJ7 , DEMJ/78/7M4 R8SW%6%A% *W, \%==#+ !*4Y 0.(B+(#+(, =T(,"+=#= .? 1/%(#=#6#(+RUS4U ]-) 3"+1, DE8F , :: : 999/99H4
己内酰胺生产工艺及技术特点
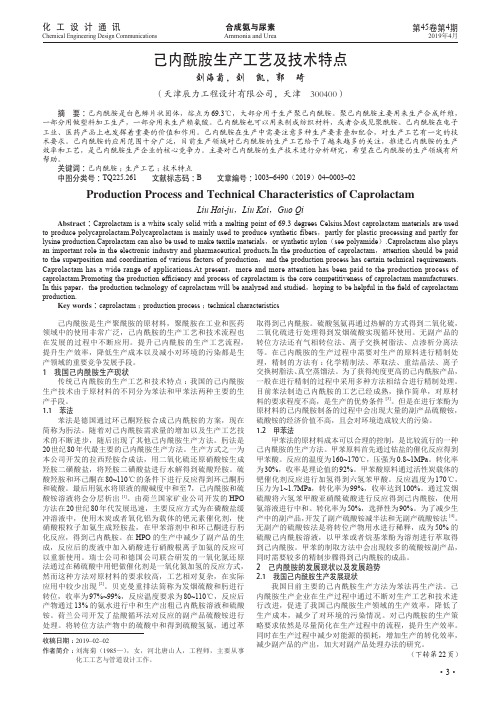
·3·合成氨与尿素化 工 设 计 通 讯Ammonia and UreaChemical Engineering Design Communications第45卷第4期2019年4月己内酰胺是生产聚酰胺的原材料,聚酰胺在工业和医药领域中的使用非常广泛,己内酰胺的生产工艺和技术流程也在发展的过程中不断应用。
提升己内酰胺的生产工艺流程,提升生产效率,降低生产成本以及减小对环境的污染都是生产领域的重要竞争发展手段。
1 我国己内酰胺生产现状传统己内酰胺的生产工艺和技术特点:我国的己内酰胺生产技术由于原材料的不同分为苯法和甲苯法两种主要的生产手段。
1.1 苯法苯法是德国通过环己酮羟胺合成己内酰胺的方案,现在简称为肟法。
随着对己内酰胺需求量的增加以及生产工艺技术的不断进步,随后出现了其他己内酰胺生产方法。
肟法是20世纪80年代最主要的己内酰胺生产方法。
生产方式之一为本公司开发的拉西羟胺合成法,用二氧化硫还原硝酸铵生成羟胺二磺酸盐,将羟胺二磺酸盐进行水解得到硫酸羟胺。
硫酸羟胺和环己酮在80~110℃的条件下进行反应得到环己酮肟和硫酸。
最后用氨水将原液的酸碱度中和至7,己内酰胺和硫酸铵溶液将会分层析出[1]。
由荷兰国家矿业公司开发的HPO 方法在20世纪80年代发展迅速,主要反应方式为在磷酸盐缓冲溶液中,使用木炭或者氧化铝为载体的钯元素催化剂,使硝酸根粒子加氨生成羟胺盐,在甲苯溶剂中和环己酮进行肟化反应,得到己内酰胺。
在HPO 的生产中减少了副产品的生成,反应后的废液中加入硝酸进行硝酸根离子加氨的反应可以重新使用。
瑞士公司和德国公司联合研发的一氧化氮还原法通过在稀硫酸中用钯做催化剂是一氧化氮加氢的反应方式,然而这种方法对原材料的要求较高,工艺相对复杂,在实际应用中较少出现[2]。
贝克曼重排法简称为发烟硫酸和肟进行转位,收率为97%~99%,反应温度要求为80~110℃,反应后产物通过13%的氨水进行中和生产出粗己内酰胺溶液和硫酸铵。
己内酰胺的生产工艺与技术路线的选择
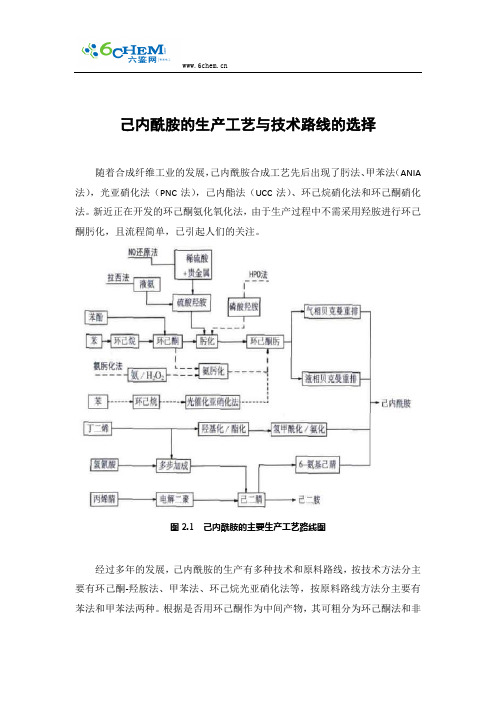
己内酰胺的生产工艺与技术路线的选择随着合成纤维工业的发展,己内酰胺合成工艺先后出现了肟法、甲苯法(ANIA 法),光亚硝化法(PNC法),己内酯法(UCC法)、环己烷硝化法和环己酮硝化法。
新近正在开发的环己酮氨化氧化法,由于生产过程中不需采用羟胺进行环己酮肟化,且流程简单,已引起人们的关注。
图2.1 己内酰胺的主要生产工艺路线图经过多年的发展,己内酰胺的生产有多种技术和原料路线,按技术方法分主要有环己酮-羟胺法、甲苯法、环己烷光亚硝化法等,按原料路线方法分主要有苯法和甲苯法两种。
根据是否用环己酮作为中间产物,其可粗分为环己酮法和非环己酮法。
2.1 环己酮法己内酰胺生产从环己酮合成开始,原料为苯酚或环己烷。
环己烷是优选原料,可生产KA油。
氧化过程通常采用硼酸或钴催化剂。
……2.1.1 环己酮的生产工艺2.1.1.1 苯酚法苯酚法(属苯法)是苯酚在镍催化剂作用下加氢生成环己醇,环己醇再进行提纯脱氢反应生成粗环己酮。
……2.1.1.2 环己烷法环己烷法(属苯法)首先是苯加氢制环己烷,加氢过程分以Ni为催化剂的常压加氢和以Pt为催化剂的加压加氢,然后环己烷氧化制环己醇、…….2.1.1.3 环己烯法环己烯法(属苯法)第一步是苯部分加氢生成环己烯,然后环己烯水合得环己醇,环己醇再进行脱氢反应生成环己酮。
……2.1.2 环己酮肟的生产工艺环己酮肟是生产己内酰胺的重要中间产物,其可以由羟胺与环己酮反应制得,也可以由其它方法制得。
1943年,德国法本公司通过环己酮-羟胺合成(现在简称为肟法),……2.1.2.1 拉西法1887年拉西(Raschig)用亚硝酸盐和亚硫酸盐反应经水解制取羟胺获得成功,……2.1.2.2 HPO法磷酸羟胺法(HPO法,属苯法)由荷兰国家矿业(DSM)公司开发,在80年代发展很快。
HPO法是在磷酸盐缓冲溶液中,……2.1.2.3 NO法一氧化氮还原法也称BASF/Polimex-NO还原法(属苯法),是德国BASF公司和波兰Polimex公司开发的工艺。
己内酰胺生产总结:技术难点和优化方向探究

己内酰胺生产总结:技术难点和优化方向探究。
一、己内酰胺生产技术难点1、反应方法的选择及其影响目前,主要的己内酰胺生产方法有两种,间断式反应法和连续式反应法。
间断式反应法是通过一个闭合的反应釜进行反应,在运行过程中需要加入蒸汽加热反应物,生产效率低下;而连续式反应法则是采用了流动式反应器,可以通过调节蒸汽压力和流量等参数来控制反应温度,提高生产效率。
但由于连续式反应器的设备维护较为困难,需要周期性清洗和更换催化剂,操作难度大,因此目前大部分企业还是采用间断式反应法进行生产。
2、反应温度和压力的控制己内酰胺的合成是一个放热反应,反应温度和压力的控制是确保反应顺利进行的重要因素。
同时,温度和压力的过高或不足也会导致反应物转化率的下降,产品质量的降低等问题。
因此,在生产过程中,必须严格控制反应温度和压力,并根据不同的反应器和催化剂,优化反应条件,提高生产效率。
3、催化剂的选择催化剂在己内酰胺生产过程中发挥着至关重要的作用,可以提高反应速度和效率,降低反应温度和能耗消耗。
目前,常用的催化剂有氧化铜、氧化铝和碳酸钙等,但由于催化剂的特性和使用条件不同,对于催化剂的选择和使用也需要进行不断的探究和优化。
二、己内酰胺生产技术优化方向的探究1、新材料的应用随着科技的不断进步,新型材料的应用也成为了化工行业不可或缺的一环。
目前,已有很多新型材料在实验室阶段已取得非常突破性的进展。
这些材料不仅在己内酰胺生产中具有重要的应用前景,还可以在其他领域有所发挥。
因此,应该加大对新型材料的研究和应用力度,以提高己内酰胺生产的效率和质量。
2、设备的优化改进设备对于化工生产过程的影响是极大的,而精细化、智能化的化工设备则能够大大提高生产效率和质量,达到节能降耗、环保高效的目的。
因此,应该加强对己内酰胺生产设备的研发和改进,采用智能化、自动化的技术手段,提高设备的精准度和操作效率。
3、环保技术的应用随着环保意识的增强,对于化工生产过程中排放的废水和废气的处理问题也越来越重视。
《己内酰胺生产及应用》
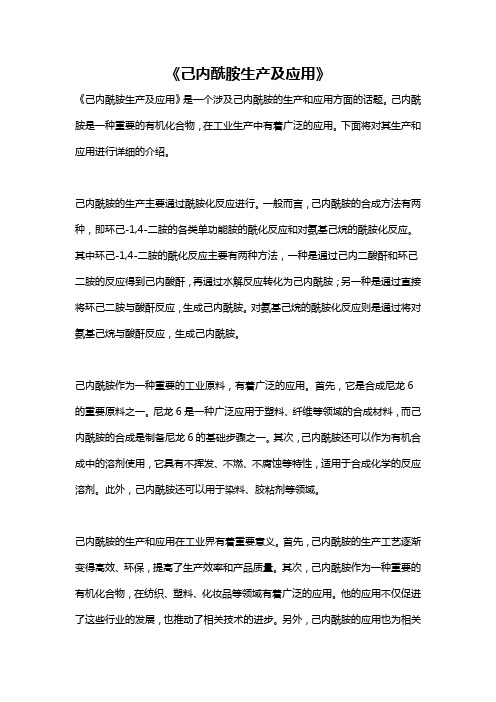
《己内酰胺生产及应用》《己内酰胺生产及应用》是一个涉及己内酰胺的生产和应用方面的话题。
己内酰胺是一种重要的有机化合物,在工业生产中有着广泛的应用。
下面将对其生产和应用进行详细的介绍。
己内酰胺的生产主要通过酰胺化反应进行。
一般而言,己内酰胺的合成方法有两种,即环己-1,4-二胺的各类单功能胺的酰化反应和对氨基己烷的酰胺化反应。
其中环己-1,4-二胺的酰化反应主要有两种方法,一种是通过己内二酸酐和环己二胺的反应得到己内酸酐,再通过水解反应转化为己内酰胺;另一种是通过直接将环己二胺与酸酐反应,生成己内酰胺。
对氨基己烷的酰胺化反应则是通过将对氨基己烷与酸酐反应,生成己内酰胺。
己内酰胺作为一种重要的工业原料,有着广泛的应用。
首先,它是合成尼龙6的重要原料之一。
尼龙6是一种广泛应用于塑料、纤维等领域的合成材料,而己内酰胺的合成是制备尼龙6的基础步骤之一。
其次,己内酰胺还可以作为有机合成中的溶剂使用,它具有不挥发、不燃、不腐蚀等特性,适用于合成化学的反应溶剂。
此外,己内酰胺还可以用于染料、胶粘剂等领域。
己内酰胺的生产和应用在工业界有着重要意义。
首先,己内酰胺的生产工艺逐渐变得高效、环保,提高了生产效率和产品质量。
其次,己内酰胺作为一种重要的有机化合物,在纺织、塑料、化妆品等领域有着广泛的应用。
他的应用不仅促进了这些行业的发展,也推动了相关技术的进步。
另外,己内酰胺的应用也为相关产品的研发和市场开拓提供了新的机遇。
总的来说,己内酰胺的生产和应用在工业界有着重要的意义。
随着科技的不断发展,己内酰胺的生产工艺将会更加高效,产品的质量也将得到进一步提高。
同时,己内酰胺在各个领域的应用也将更加广泛,推动相关行业的发展和技术的进步。
整体而言,己内酰胺的生产和应用将有助于推动工业的发展,促进经济的繁荣。
国内己内酰胺厂家生产工艺
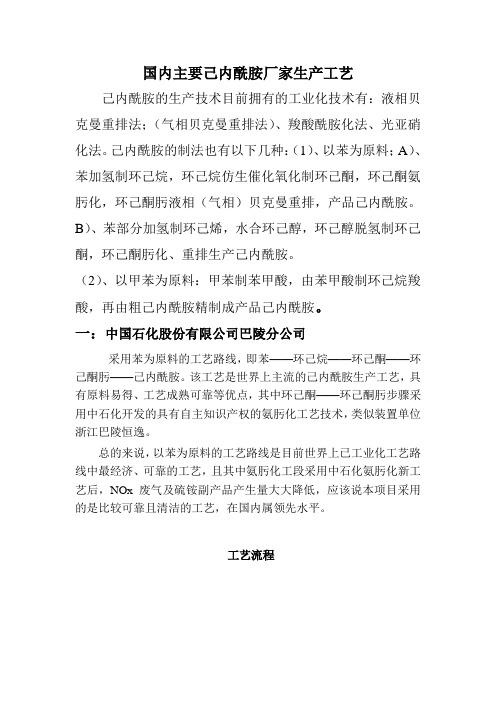
国内主要己内酰胺厂家生产工艺
己内酰胺的生产技术目前拥有的工业化技术有:液相贝克曼重排法;(气相贝克曼重排法)、羧酸酰胺化法、光亚硝化法。
己内酰胺的制法也有以下几种:(1)、以苯为原料;A)、苯加氢制环己烷,环己烷仿生催化氧化制环己酮,环己酮氨肟化,环己酮肟液相(气相)贝克曼重排,产品己内酰胺。
B)、苯部分加氢制环己烯,水合环己醇,环己醇脱氢制环己酮,环己酮肟化、重排生产己内酰胺。
(2)、以甲苯为原料:甲苯制苯甲酸,由苯甲酸制环己烷羧酸,再由粗己内酰胺精制成产品己内酰胺。
一:中国石化股份有限公司巴陵分公司
采用苯为原料的工艺路线,即苯——环己烷——环己酮——环己酮肟——己内酰胺。
该工艺是世界上主流的己内酰胺生产工艺,具有原料易得、工艺成熟可靠等优点,其中环己酮——环己酮肟步骤采用中石化开发的具有自主知识产权的氨肟化工艺技术,类似装置单位浙江巴陵恒逸。
总的来说,以苯为原料的工艺路线是目前世界上已工业化工艺路线中最经济、可靠的工艺,且其中氨肟化工段采用中石化氨肟化新工艺后,NOx废气及硫铵副产品产生量大大降低,应该说本项目采用的是比较可靠且清洁的工艺,在国内属领先水平。
工艺流程
各主体生产装置和辅助生产装置工艺技术路线
二:浙江巴陵恒逸
生产工艺与中国石化股份有限公司巴陵分公司基本相同,都是采用苯为原料的工艺路线,即苯——环己烷——环己酮——环己酮肟——己内酰胺。
三:中石化石家庄炼化
以甲苯为原料制取苯甲酸,经亚硝化反应后生产己内酰胺的苏尼亚工艺过程(意大利SNIA亚硝化法)。
己内酰胺绿色生产技术的化学和工程基础

走向绿色的未来:己内酰胺的环保生产技术随着环境保护意识的不断增强,绿色生产技术的研发和应用已成为当今世界工业发展的必然趋势。
其中,己内酰胺生产技术的绿色化成为了发展的方向之一。
一、己内酰胺的化学基础己内酰胺分子式为C6H9NO,是一种重要的化学中间体,广泛应用于医药、橡胶、塑料、粘合剂等行业中。
传统的己内酰胺生产方法中,使用的是环己烯作为原料,酸性催化剂和氢气进行加氢反应合成己内酰胺。
但这种方法存在反应条件苛刻、环境污染严重等问题。
二、己内酰胺绿色生产技术的化学基础随着环保意识的增强和科技的进步,己内酰胺的绿色生产技术应运而生。
目前,常用的绿色生产技术有两种:1. 生物法:利用微生物酶或细胞进行代谢合成,具有高效、低成本、无二次污染等优点。
同时,该方法还可以利用生物方法将己内酰胺合成化学原料γ-氨基丁酸,为生物技术带来了更多的应用前景。
2. 绿色化学法:采用新型催化剂和独特的反应体系,将有机物与氨在温和条件下反应合成己内酰胺。
与传统方法相比,绿色化学法更加环保,省时省力,也更符合绿色环保理念。
同时,绿色化学法还可利用生物质资源代替传统的化石能源,实现了资源的高效利用。
三、己内酰胺绿色生产技术的工程基础绿色生产技术的成功应用离不开工程基础的支撑。
己内酰胺绿色生产技术需要从原材料的选择、反应体系和催化剂的设计、反应控制、设备设计等方面进行优化。
同时,工业化应用需要进一步提高生产效率、降低成本、减少二次污染等方面的考虑。
综上所述,己内酰胺的绿色生产技术具有化学基础的支持和工程基础的保障,其绿色化的特点符合当今社会对环保和可持续发展的要求。
随着技术不断突破和实践探索的深入,相信这种技术会在未来得到更广泛的应用。
世界己内酰胺技术简介

2)己内酰胺制备工艺
• 世界己内酰胺制备98%为环己酮肟贝克曼重排而来的。 而环己酮肟贝克曼重排法又分为:
• a)液相贝克曼重排; • b)气相贝克曼重排; • c)溶剂-液相贝克曼重排; • 其中前者a)占98%,后两者b)、c)各占1%。
2)己内酰胺制备工艺
• a)环己酮肟液相贝克曼重排
• 环己酮肟在含SO3(8~20%)的发烟硫酸存 在下,发生液相贝克曼重排反应,形成己内酰胺硫酸 溶液,并放出大量的热,反应热由外循环冷却器移走。 主反应式如下:
4、世界己内酰胺生产技术简介
• 世界已工业化的己内酰生产工艺,按所使用的原料不同, 可以划分为甲苯法、苯酚法和苯法,它们在己内酰胺总产 能中各占的份额为1%、19%和80%。 • 世界己内酰胺生产按所使用的方法不同,可以划分为亚硝 化法(酰胺化),环己烷光亚硝化法,环己酮肟贝克曼重 排法;其中环己酮肟贝克曼重排法占98%以上。 • 环己酮肟贝克曼重排法又分为液相重排、气相重排、溶剂 -液相重排;其中前者占98%,后两者各占1%。
5、苯法制备CPL各种工艺路线介绍
• • 1)环己酮肟制备工艺 环己酮肟制备按羟胺合成方法的不同,可分为 硫酸羟胺法(拉西法HSO)、一氧化氮(NO)还 原法、磷酸羟胺法(HPO)和氨肟化法(HAO)。
1)环己酮肟制备工艺
• A、硫酸羟胺法(拉西法HSO)
• 首先将亚硝酸盐、氨水和二氧化硫进行反应,生成羟 胺二磺酸盐;羟胺二磺酸盐水解得到羟胺硫酸盐(简称羟 胺);羟胺溶液再与环己酮进行肟化反应,生成环己酮肟。
C =O COCl2 NH C Cl N C Cl
O
HNO3 /H2SO4
NO2 C=O NH
(硝基己内酰胺)
NH2 H2 C NH (氨基己内酰胺) H2O NH2 (CH2) 4 CH COOH (D,C-赖氨酸) NH2
己内酰胺生产工艺及技术特点

己内酰胺生产工艺及技术特点<i>己内酰胺</i>路线见图1。
(NH4)2SO4溶液中的环己酮用蒸汽气提回收后返回反应系统。
反应生成的环己酮肟经过饱和浓度的硫铵母液干燥脱水。
环己酮肟在发烟H2SO4催化作用下经两级串联贝克曼重排器制得己内酰胺,用气氨在真空条件下进行中和反应,并利用反应热蒸发部分水分,同时(NH4)2SO4结晶从母液中分离出来。
己内酰胺精制过程有萃取、蒸馏,流程较短。
图1 SNIA工艺Fig.1 SNIAtechnic该工艺可以避免羟胺制备过程中生成(NH4)2SO4,因而该工艺技术被迅速推广,BASF公司也成为目前世界上最大的己内酰胺生产商,现生产能力为1015kt a,占世界己内酰胺总生产能力的19.00%,生产装置分布在美国、德国和比利时。
工艺路线见图2。
-1在SNIA工艺制备己内酰胺中,含己内酰胺60%左右的酰胺油先经NH3 H2O苛化,然后经甲苯萃取、水萃取制成30%的己内酰胺水溶液。
己内酰胺水溶液经KMnO4氧化和过滤、三效蒸发、脱水浓缩、预蒸馏、NaOH处理和蒸馏、轻副产物蒸馏和精馏、重副产物蒸馏和精馏等精制过程,才能得到符合标准的纤维级己内酰胺成品。
1999年,中国石化石家庄化纤责任有限公司采用意大利SNIA公司甲苯法生产技术,耗资35亿-1元,建成一套生产能力为50kt a的己内酰胺生产装置,2002年与中国石化科学研究院合作开发并应用非晶态镍催化剂引入苯甲酸加氢反应系统部分取代Pd/C催化剂以及己内酰胺水溶液加氢取代KMnO4工艺技术,将生产能力扩建到70kt a。
尽管SNIA工艺为己内酰胺生产提供了新的原料路线,采用甲苯为原料,不经过环己酮肟直接生产己内酰胺,但酰胺化反应过程条件苛刻,收率较低,生成的副产物成分复杂,每生产1t己内酰胺副产3.8t(NH4)2SO4。
而且工艺精制过程存在流程长、工艺控制复杂、能耗大、产品质量不稳定、优级品率低的问题,投资大,生产设备高度专业化,难以转换用途。
己内酰胺流程

己内酰胺流程己内酰胺是一种重要的有机合成中间体,具有广泛的应用价值。
它可以用于合成聚酰胺树脂、润滑剂、塑料助剂等化工产品,也可以作为医药、农药等领域的原料。
己内酰胺的生产工艺一直备受关注,其生产流程的优化和改进对提高生产效率、降低成本具有重要意义。
首先,己内酰胺的生产主要通过氨解己内酰胺酸盐来实现。
具体的生产流程包括以下几个步骤:1. 原料准备,首先需要准备己内酰胺酸盐和氨水作为原料。
己内酰胺酸盐是通过己内酰胺和酸反应得到的中间体,而氨水则是氨气溶解在水中得到的溶液。
2. 反应器装载,将适量的己内酰胺酸盐溶解在水中,加入反应器中。
然后向反应器中通入氨气,控制反应温度和压力。
3. 反应进行,在适当的温度和压力条件下,己内酰胺酸盐和氨水发生氨解反应,生成己内酰胺和相应的盐类产物。
4. 分离提纯,将反应产物进行分离,得到己内酰胺的粗品。
然后通过蒸馏、结晶等工艺对其进行提纯,得到合格的己内酰胺产品。
5. 产品储存,最后,将得到的己内酰胺产品进行包装、标识和储存,待用或出售。
在整个生产流程中,需要特别注意反应条件的控制、产品的分离提纯以及安全生产等环节。
通过优化反应条件、改进分离提纯工艺和加强安全管理,可以提高己内酰胺的生产效率,降低生产成本,保证产品质量。
此外,随着环保意识的提升,己内酰胺的生产过程也需要考虑减少废弃物和减少对环境的影响。
因此,在生产流程中应当注重资源的合理利用和废物的处理,采取节能减排措施,实现清洁生产。
总的来说,己内酰胺的生产流程是一个复杂的化工过程,需要综合考虑反应条件、分离提纯、安全生产和环保等方面的因素。
只有不断优化流程、提高生产技术水平,才能更好地满足市场需求,推动己内酰胺产业的健康发展。
己内酰胺生产工艺
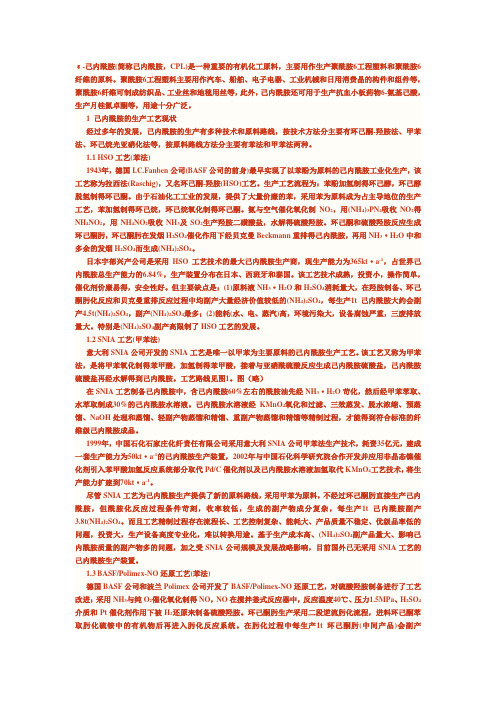
ε-己内酰胺(简称己内酰胺,CPL)是一种重要的有机化工原料,主要用作生产聚酰胺6工程塑料和聚酰胺6纤维的原料。
聚酰胺6工程塑料主要用作汽车、船舶、电子电器、工业机械和日用消费晶的构件和组件等,聚酰胺6纤维可制成纺织品、工业丝和地毯用丝等,此外,己内酰胺还可用于生产抗血小板药物6-氨基己酸,生产月桂氮卓酮等,用途十分广泛。
1 己内酰胺的生产工艺现状经过多年的发展,己内酰胺的生产有多种技术和原料路线,按技术方法分主要有环己酮-羟胺法、甲苯法、环己烷光亚硝化法等,按原料路线方法分主要有苯法和甲苯法两种。
1.1 HSO工艺(苯法)1943年,德国I.C.Fanben公司(BASF公司的前身)最早实现了以苯酚为原料的己内酰胺工业化生产,该工艺称为拉西法(Raschig),又名环己酮-羟胺(HSO)工艺。
生产工艺流程为:苯酚加氢制得环己醇,环己醇脱氢制得环己酮。
由于石油化工工业的发展,提供了大量价廉的苯,采用苯为原料成为占主导地位的生产工艺,苯加氢制得环己烷,环己烷氧化制得环己酮。
氨与空气催化氧化制NO2,用(NH4)3PN4吸收NO2得NH4NO2,用NH4NO2吸收NH3及SO2生产羟胺二磺酸盐,水解得硫酸羟胺。
环己酮和硫酸羟胺反应生成环己酮肟,环己酮肟在发烟H2SO4催化作用下经贝克曼Beckmann重排得己内酰胺,再用NH3·H2O中和多余的发烟H2SO4而生成(NH4)2SO4。
日本宇部兴产公司是采用HSO工艺技术的最大己内酰胺生产商,现生产能力为365kt·a-1,占世界己内酰胺总生产能力的6.84%,生产装置分布在日本、西班牙和泰国。
该工艺技术成熟,投资小,操作简单,催化剂价廉易得,安全性好。
但主要缺点是:(1)原料液NH3·H2O和H2SO4消耗量大,在羟胺制备、环己酮肟化反应和贝克曼重排反应过程中均副产大量经济价值较低的(NH4)2SO4,每生产1t己内酰胺大约会副产4.5t(NH4)2SO4,副产(NH4)2SO4最多;(2)能耗(水、电、蒸汽)高,环境污染大,设备腐蚀严重,三废排放量大。
己内酰胺工艺总结:提高产率和质量的技术创新与实践
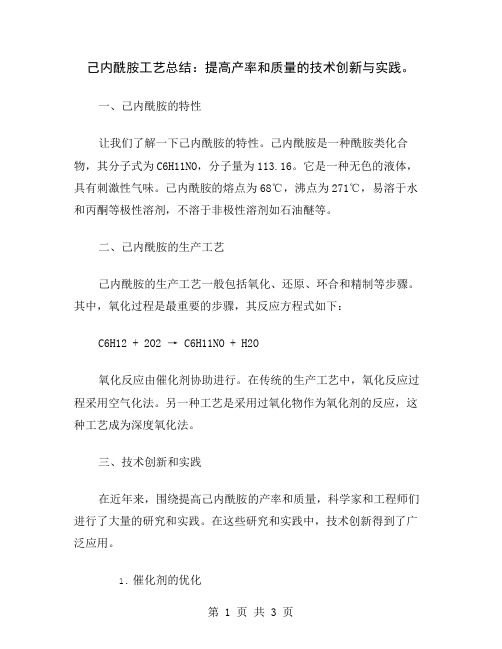
己内酰胺工艺总结:提高产率和质量的技术创新与实践。
一、己内酰胺的特性让我们了解一下己内酰胺的特性。
己内酰胺是一种酰胺类化合物,其分子式为C6H11NO,分子量为113.16。
它是一种无色的液体,具有刺激性气味。
己内酰胺的熔点为68℃,沸点为271℃,易溶于水和丙酮等极性溶剂,不溶于非极性溶剂如石油醚等。
二、己内酰胺的生产工艺己内酰胺的生产工艺一般包括氧化、还原、环合和精制等步骤。
其中,氧化过程是最重要的步骤,其反应方程式如下:C6H12 + 2O2 → C6H11NO + H2O氧化反应由催化剂协助进行。
在传统的生产工艺中,氧化反应过程采用空气化法。
另一种工艺是采用过氧化物作为氧化剂的反应,这种工艺成为深度氧化法。
三、技术创新和实践在近年来,围绕提高己内酰胺的产率和质量,科学家和工程师们进行了大量的研究和实践。
在这些研究和实践中,技术创新得到了广泛应用。
1.催化剂的优化作为反应的关键流程,催化剂的优化可以显著提高己内酰胺的产率和质量。
例如,采用钒、钴、镍等元素的复合氧化物作为催化剂,可以减小氧化反应的温度和压力,从而实现产率和质量的提高。
2.反应条件的优化为了提高己内酰胺的产率和质量,反应条件的优化也是非常重要的。
例如,在氧化过程中,反应温度和压力的优化可以减少副产物的生成,从而提高己内酰胺的纯度和收率。
此外,反应时间的优化也可以实现将反应时间缩短到一定程度的目的。
3.精制工艺的优化在己内酰胺的精制工艺中,采用物理-化学联合处理技术可以有效地提高己内酰胺的纯度和质量。
例如,采用吸附-凝聚-萃取精制工艺,可以将己内酰胺中的杂质气体和液体有效地去除,实现更高的纯度和回收率。
四、结论总体来说,己内酰胺的生产工艺中一系列的技术创新和实践已经为提高其产率和质量做出了重大的贡献。
同时,这些创新也可以借鉴到其他领域,提高其他化学品的工艺效率、质量和可持续性。
在未来,我们可以期待着更多的创新和实践,让己内酰的生产更加高效、清洁和智能化。
煤制己内酰胺工艺
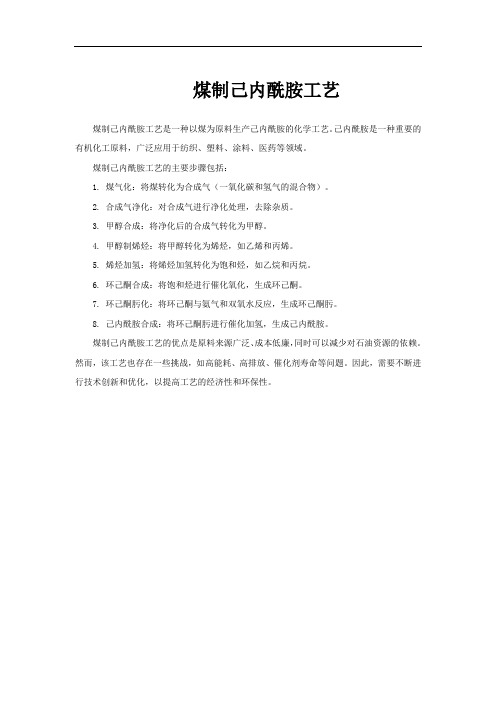
煤制己内酰胺工艺
煤制己内酰胺工艺是一种以煤为原料生产己内酰胺的化学工艺。
己内酰胺是一种重要的有机化工原料,广泛应用于纺织、塑料、涂料、医药等领域。
煤制己内酰胺工艺的主要步骤包括:
1. 煤气化:将煤转化为合成气(一氧化碳和氢气的混合物)。
2. 合成气净化:对合成气进行净化处理,去除杂质。
3. 甲醇合成:将净化后的合成气转化为甲醇。
4. 甲醇制烯烃:将甲醇转化为烯烃,如乙烯和丙烯。
5. 烯烃加氢:将烯烃加氢转化为饱和烃,如乙烷和丙烷。
6. 环己酮合成:将饱和烃进行催化氧化,生成环己酮。
7. 环己酮肟化:将环己酮与氨气和双氧水反应,生成环己酮肟。
8. 己内酰胺合成:将环己酮肟进行催化加氢,生成己内酰胺。
煤制己内酰胺工艺的优点是原料来源广泛、成本低廉,同时可以减少对石油资源的依赖。
然而,该工艺也存在一些挑战,如高能耗、高排放、催化剂寿命等问题。
因此,需要不断进行技术创新和优化,以提高工艺的经济性和环保性。
己内酰胺生产工艺
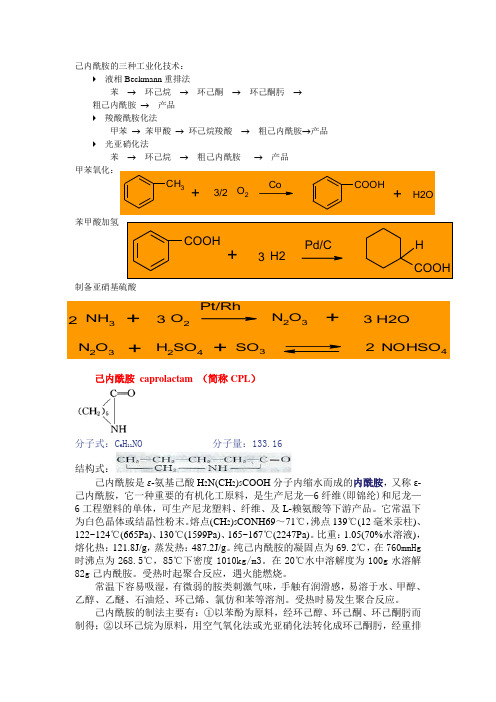
己内酰胺的三种工业化技术:液相Beckmann 重排法苯 → 环己烷 → 环己酮 → 环己酮肟 →粗己内酰胺 → 产品羧酸酰胺化法甲苯 → 苯甲酸 → 环己烷羧酸 → 粗己内酰胺→产品光亚硝化法苯 → 环己烷 → 粗己内酰胺 → 产品苯甲酸加氢制备亚硝基硫酸己内酰胺 caprolactam (简称CPL )分子式:C 6H 11NO 分子量:133.16结构式:己内酰胺是ε-氨基己酸H 2N(CH 2)5COOH 分子内缩水而成的内酰胺,又称ε-己内酰胺,它一种重要的有机化工原料,是生产尼龙—6纤维(即锦纶)和尼龙—6工程塑料的单体,可生产尼龙塑料、纤维、及L-赖氨酸等下游产品。
它常温下为白色晶体或结晶性粉末。
熔点(CH 2)5CONH69~71℃,沸点139℃(12毫米汞柱)、122~124℃(665Pa)、130℃(1599Pa)、165~167℃(2247Pa)。
比重:1.05(70%水溶液),熔化热:121.8J/g ,蒸发热:487.2J/g 。
纯己内酰胺的凝固点为69.2℃,在760mmHg 时沸点为268.5℃,85℃下密度1010kg/m3。
在20℃水中溶解度为100g 水溶解82g 己内酰胺。
受热时起聚合反应,遇火能燃烧。
常温下容易吸湿,有微弱的胺类刺激气味,手触有润滑感,易溶于水、甲醇、乙醇、乙醚、石油烃、环己烯、氯仿和苯等溶剂。
受热时易发生聚合反应。
己内酰胺的制法主要有:①以苯酚为原料,经环己醇、环己酮、环己酮肟而制得;②以环己烷为原料,用空气氧化法或光亚硝化法转化成环己酮肟,经重排而制得;③以甲苯为原料,用斯尼亚法合成。
此外,也可以糠醛或乙炔为原料合成。
在制造过程中,环己酮(cyclohexanone)是主要的关键性中间原料,此关键性原料可藉由环己烷氢化或苯酚氢化得到,这两种制程相当类似,不同点仅在于触媒的使用和操作条件的不同而已。
不同制程方法比较1.传统制程:本制程是由环己酮与(NH2OH)2-H2SO4和氨水反应得环己酮圬(cyclohexanone oxime)后,再经贝克曼重排反应(Beckmann rearrangement)而制成CPL。
己内酰胺生产工艺
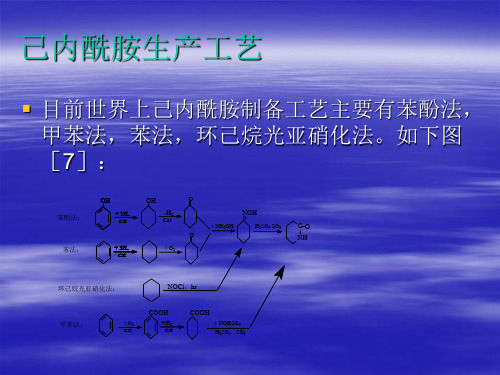
目前世界上己内酰胺制备工艺主要有苯酚法, 甲苯法,苯法,环己烷光亚硝化法。如下图 [7]:
OH 苯酚法:
+ 3H2 Cat
OH -H2
Cat
O
NOH
+NH2OH H2SO4.SO3
C=O NH
O
苯法:
+ 3H2 Cat
+O2
环己烷光亚硝化法:
NOCl,hr
COOH 甲苯法:
+O2
Cat
苯加氢制环己烷工艺有两种,即液相和气相加氢两种。
+3H 2 Cat
苯法制己内酰胺
2.环己烷氧化制环己醇和环己酮: 2.环己烷氧化制环己醇和环己酮:
环己烷氧化主要有催化氧化和无催化氧化。 反应式如下:
= O +O 2 Cat
或无
OH + +H 2O
OOH
苯法制己内酰胺
3.环己醇再脱氢为环己酮: 3.环己醇再脱氢为环己酮:
=NOH.2HCl
+NOCl +HCl
λ
<600nm
(环己酮肟盐酸盐)
环己烷光亚硝化法制己内酰胺
环己酮肟盐酸盐在发烟硫酸的作用下贝克曼重排为己内酰 胺:
C =O NH . H 2SO 4
+2NH 3
C =O NH +(NH 4) 2SO 4
甲苯法制己内酰胺
甲苯法制CPL是由意大利SNIA公司在上世纪六十年代初开发 甲苯法制CPL是由意大利SNIA公司在上世纪六十年代初开发 研制的,并于1962年实现工业化,1968年、1975年分别在 研制的,并于1962年实现工业化,1968年、1975年分别在 意大利的MARFLIDONIA,前苏联乌兹别克的CIRCIK建成8 意大利的MARFLIDONIA,前苏联乌兹别克的CIRCIK建成8 万吨/年工业装置,但目前均已停产。1996年,中国石家庄 万吨/年工业装置,但目前均已停产。1996年,中国石家庄 引进该技术建成5万吨/ 引进该技术建成5万吨/年己内酰胺装置,至今运行良好,并 已扩能至6.5万吨/ 已扩能至6.5万吨/年。该工艺主要有如下步骤: 1.甲苯氧化制苯甲酸 1.甲苯氧化制苯甲酸
己内酰胺生产技术及市场分析

己内酰胺生产技术及市场分析1. 前言- 己内酰胺的定义和用途2. 己内酰胺生产技术分析- 己内酰胺生产原理和工艺流程- 己内酰胺生产的不同方法及其优缺点- 己内酰胺生产中的关键技术3. 己内酰胺市场分析- 己内酰胺市场概述- 己内酰胺主要生产商和消费者- 己内酰胺市场供需变化及趋势4. 己内酰胺的应用领域- 己内酰胺的主要应用领域- 己内酰胺的应用前景5. 己内酰胺生产的环境问题及解决方案- 己内酰胺生产对环境的影响- 己内酰胺生产的环保方案- 己内酰胺生产的未来趋势6. 结论- 己内酰胺生产技术和市场的总结- 己内酰胺生产中需要注重的问题和解决方案第一章节:前言己内酰胺是一种有机化合物,它属于酰胺类化合物。
己内酰胺是一种有着广泛应用领域的化学原料,其被广泛用于生产尿素树脂、塑料、合成纤维等。
己内酰胺作为一种基础化学品,随着化学工业的不断发展和进步,其重要性和用途日益增加。
己内酰胺是由己二酸和氨经过反应得到的,它的化学式为C6H11NO。
己内酰胺是无色透明的液体,它有很强的亲水性,可以溶于水和醇类溶剂。
己内酰胺具有良好的物化性质,它的熔点为24~27℃,沸点为230~235℃,相对密度为0.94,闪点为117℃。
己内酰胺的应用十分广泛,其主要应用领域包括树脂、涂料、合成纤维、医药、食品等行业。
例如,己内酰胺可以用于生产尿素树脂,以及制造高强度尼龙纤维、人造丝和其他合成纤维等。
此外,己内酰胺还可以被用作溶剂、催化剂、纺织染料中的中间体等。
己内酰胺的生产技术日益成熟,主要生产过程分为氨法和胺法两种方法。
氨法是己内酰胺生产的传统方法,该方法通过己二酸和氨反应制得己内酰胺。
胺法则是近几年发展起来的方法,通过己烷胺和环氧丙烷反应制得己内酰胺。
两种方法各有特点,但随着生产技术的进步和工艺水平的提高,己内酰胺的生产工艺也愈加完善。
总之,己内酰胺作为一种具有广泛应用领域和经济价值的有机化合物,其生产技术和市场前景在不断发展与改进。
己内酰胺生产方法介绍

己内酰胺的主要生产方法介绍1899年德国学者S.Cabriel 等人加热ε-氨基酸首次合成了己内酰胺,半个世纪后,德国的法本公司由于解决了己内酰胺开环聚合和纺丝的有关技术问题,而首先实现了工业化,建成了总生产能力为3500 t/a的己内酰胺装置,从而促进了己内酰胺的发展。
当时大都采用苯酚为原料生产环己酮,以拉西法生产羟胺硫酸盐的环己酮-羟胺工艺路线生产己内酰胺。
二战结束后,聚酰胺6纤维从军用扩大到民用和其他工业领域,世界各国竞相开发,使得己内酰胺生产技术得以迅猛发展,先后出现了一些新的合成方法。
1960年BASF公司首次采用以苯为原料的环己烷氧化法的工艺,1962年意大利Snia Viscose公司开发了以甲苯为原料,经六氢苯甲酸硝化得己内酰胺,1963年日本东丽公司开发了环己烷光亚硝化法的工艺路线,1971年荷兰DSM公司开发了HPO法生产技术,80年代以后,传统技术趋于稳定。
90年代以后,己内酰胺新工艺的开发取得进展,并逐步取代传统工艺。
目前,工业化生产己内酰胺的路线一般分成两类:第一类生产方法的特点是以环己酮为中间产物,肟化,Beckmann 重排,环己酮肟可从环己酮或其它母体合成,这是迄今最重要的制造方法。
另一类生产方法避开环己酮的生产环节,涉及其它中间体或其它工艺步骤,如采用甲苯路线工艺、环己烷光亚硝化技术等。
主要生产工艺有:1 环己酮-羟胺法环己酮-羟胺法是目前世界己内酰胺生产工业中最广泛使用的方法。
环己酮的生产方法,早年是由苯酚加氢得环己醇再脱氢而制得,后来又开发了苯酚选择加氢直接制得环己酮的方法,而近30年来,由苯加氢制环己烷,再空气氧化而制得环己酮的方法占据了重要地位。
环己酮-羟胺法生产己内酰胺以苯为主要原料,主要生产过程包括:苯加氢制备环己烷、环己酮的合成、羟胺的合成、环己酮肟化、环己酮肟重排。
其中羟胺的合成主要方法有拉西法(Raschig法)、硫酸羟胺法(HSO)、磷酸羟胺法(DSM/HPO)、氧化氮还原法(NO)等。
己内酰胺生产工艺

己内酰胺的三种工业化技术:液相Beckmann 重排法苯 → 环己烷 → 环己酮 → 环己酮肟 →粗己内酰胺 → 产品羧酸酰胺化法甲苯 → 苯甲酸 → 环己烷羧酸 → 粗己内酰胺→产品光亚硝化法苯 → 环己烷 → 粗己内酰胺 → 产品苯甲酸加氢制备亚硝基硫酸己内酰胺 caprolactam (简称CPL )分子式:C 6H 11NO 分子量:133.16结构式:己内酰胺是ε-氨基己酸H 2N(CH 2)5COOH 分子内缩水而成的内酰胺,又称ε-己内酰胺,它一种重要的有机化工原料,是生产尼龙—6纤维(即锦纶)和尼龙—6工程塑料的单体,可生产尼龙塑料、纤维、及L-赖氨酸等下游产品。
它常温下为白色晶体或结晶性粉末。
熔点(CH 2)5CONH69~71℃,沸点139℃(12毫米汞柱)、122~124℃(665Pa)、130℃(1599Pa)、165~167℃(2247Pa)。
比重:1.05(70%水溶液),熔化热:121.8J/g ,蒸发热:487.2J/g 。
纯己内酰胺的凝固点为69.2℃,在760mmHg 时沸点为268.5℃,85℃下密度1010kg/m3。
在20℃水中溶解度为100g 水溶解82g 己内酰胺。
受热时起聚合反应,遇火能燃烧。
常温下容易吸湿,有微弱的胺类刺激气味,手触有润滑感,易溶于水、甲醇、乙醇、乙醚、石油烃、环己烯、氯仿和苯等溶剂。
受热时易发生聚合反应。
己内酰胺的制法主要有:①以苯酚为原料,经环己醇、环己酮、环己酮肟而制得;②以环己烷为原料,用空气氧化法或光亚硝化法转化成环己酮肟,经重排CH 3+3/2O 2COOH +H2O Co COOH +3H2Pd/C H COOH 2NH 3+3O 2N 2O 3+3H2O N 2O 3+H 2SO 4+SO 32NOHSO 4Pt/Rh而制得;③以甲苯为原料,用斯尼亚法合成。
此外,也可以糠醛或乙炔为原料合成。
在制造过程中,环己酮(cyclohexanone)是主要的关键性中间原料,此关键性原料可藉由环己烷氢化或苯酚氢化得到,这两种制程相当类似,不同点仅在于触媒的使用和操作条件的不同而已。
- 1、下载文档前请自行甄别文档内容的完整性,平台不提供额外的编辑、内容补充、找答案等附加服务。
- 2、"仅部分预览"的文档,不可在线预览部分如存在完整性等问题,可反馈申请退款(可完整预览的文档不适用该条件!)。
- 3、如文档侵犯您的权益,请联系客服反馈,我们会尽快为您处理(人工客服工作时间:9:00-18:30)。
己内酰胺概况己内酰胺简介一、性质及用途己内酰胺(CPL),分子量113.16,分子式C6H11ON。
分子式CH2(CH2)4CONH。
己内酰胺(CPL)在液态下为无色,在固态下为白色(片状),手触有吸湿性,易溶于水和苯等,受热起聚合反应,与火能燃烧。
熔点68℃~69℃,0.1MPa 下沸点为270℃,85℃下密度为1010kg/m3。
己内酰胺是重要的有机化工原料之一,主要用途是通过聚合生成聚酰胺切片,通常叫尼龙-6切片,或锦纶纤维、工程塑料、塑料薄膜。
尼龙-6切片随着质量和指标的不同,有不同的侧重应用领域:①高质量、粘度在2.4-2.45消光切片,主要用于民用高速纺行业、短纤纺丝,由于锦纶-6具优良的染色性能和耐磨性能,一直用在织高品质布和羊毛纺织上,这是尼龙-6切片最初的用途,也是目前-6切片的一个主要用途。
②粘度在3.2以上的切片,主要用于帘子布纺丝,随着我国汽车工业的发展,对帘子线的需求量日益增加,是目前尼龙-6切片的另一个重要用途。
③粘度在2.4-2.6的切片,主要应用于常规纺丝及部分质量要求不高的短纤纺丝,在这方面的使用,因纺丝工艺落后,替代品增加,需求量逐渐萎缩。
④粘度在2.7-3.0的切片,主要用于地毯骨架丝、渔网丝,在这方面因下游产品质量参差不齐,对尼龙-6切片的质量要求也有很大差别。
⑤工程塑料和塑料薄膜用切片,是目前尼龙-6发展的一个重要发展方向。
二、国内外己内酰胺生产状况1、国外己内酰胺生产状况近年来,全球己内酰胺的生产稳步发展,2006年总生产能达到493.7万吨/年,比2005年增加了16万吨/年,同比增长了3.58%。
全球己内酰胺的生产能力集中在欧洲、亚洲以及北美洲,其中北美地区的生产能力为122.4万吨/年,占全球己内酰胺总产能的22.8%;西欧地区的生产能力为107.0万吨/年,占总生产能力的21.7%;日本生产能力为54.2万吨/年,占总生产能力的11%;亚洲其它国家的生产能力为120.5万吨/年,占总生产能力的24.4%。
己内酰胺生产能力比较集中,前14大生产商的生产能力占全球生产能力的73.3%。
全球最大的己内酰胺生产商是BASF,其生产能力达到72.5万吨/年,占全球总生产能力的14.7%,BASF在全球有三家企业,分别在美国、比利时及德国;排名第二的己内酰胺生产厂商是DSM,其生产能力达到46.0万吨/年(不含在华合资企业),占全球总生产能力的9.3%。
DSM在全球建有2家企业及一家合资企业,分别在荷兰、美国及中国。
亚洲地区的生产厂商主要集中在日本、中国大陆和中国台湾省。
全球主要己内酰胺生产商如表1所示:表1 全球主要己内酰胺生产商(万吨/年)2、国内己内酰胺生产状况国内己内酰胺工业起步于上世纪60年代,己内酰胺工业的发展大致可分为两个阶段。
第一个阶段为二十世纪50年代至70年代,主要以自己开发的技术建设小型规模生产装置,均采用环己烷氧化法制环己酮。
己内酰胺另一主要原料羟胺的生产方法则采用古老的拉西法,即以亚硝酸盐为原料,用二氧化硫还原,该法在生产中副产了大量硫铵,每吨己内酰胺副产硫铵达4.5吨之多,成为制约己内酰胺大规模生产的重要因素。
第二阶段为二十世纪八十年代至今,以规模较大和引进国外先进技术为特征。
1989年我国引进荷兰DSM公司HPO工艺同时在南京、岳阳分别建设5万吨/年己内酰胺装置,并分别于1993年和1995年投产。
1999年,中石化集团石家庄化纤公司引进意大利SINA公司甲苯法技术建设的5万吨/年己内酰胺项目正式投产。
1992年,国内己内酰胺装置最大规模只有7000吨/年,总生产能力不到2万吨/年,年产不到1万吨。
1993年以来,随着三套引进装置的建成投产,国内己内酰胺产量达到29.08万吨,14年增长了17倍。
之后,三大企业扩能改造,小型生产企业退出市场,到2006年底,我国己内酰胺总产能达到36.5万吨/年。
国内历年己内酰胺总产能、总产量见表2;各家己内酰胺生产企业的产能、原料路线、改扩建情况见表3:表2 国内历年己内酰胺总产能及总产量(单位:万吨)表3 至2010年前国内己内酰胺生产企业概况3、国内生产厂家拟建情况江苏骏马集团有限公司计划在张家港新建一套20万吨/年生产装置,河北沧州化学工业股份有限公司合资建设一套12万吨/年生产装置等,具体细节不详。
三、己内酰胺生产技术目前生产CPL的起始原料是苯/环己烷、苯酚和甲苯,三种原料占生产能力的比例分别为78.6%、19.90%和1.5%。
己内酰胺生产工艺与原料息息相关。
以甲苯为原料的采用意大利的SINA公司开发的甲苯法工艺。
近几年还开发以非芳烃为原料的工艺路线,如DSM、Shell 合作的以丁二烯和CO为原料生产CPL工艺已申请专利;巴斯夫和杜邦公司合作的丁二烯/HCN工艺,已建成1000t/a实验装置,宣称要与我国合作在国内建厂,每吨CPL生产成本降低300美元,但尚未付诸实施。
对于苯、环己烷酚等大宗原料,除了两套装置采用日本东丽公司开发的光亚硝化(PNC)法外,其余均为“酮-肟”主流工艺。
该生产工艺包括:(1)苯加氢、环己烷氧化剂制环己酮;(2)环己酮肟化制环己酮肟;(3)环己酮肟贝克曼转位生产己内酰胺,各工艺分述如下:①传统法:其关键工艺是环己酮与硫酸羟胺发生亏化反应,生成环己酮肟,环己酮肟在发烟硫酸作用下经贝克曼重排反应生成CPL,对传统拉西法的改进,主要着眼于降低硫酸铵的副产量。
②DSM-HPO法该工艺的羟胺合成和环己酮肟化分两个阶段都是在循环使用的磷酸缓冲液中完成的,不产生硫酸铵。
该工艺的优势在于仅在环己酮肟重排反应阶段使用硫酸,因而大大降低硫酸铵副产量。
该工艺设备复杂,分离精制环节多,工艺控制难度大,催化剂较为昂贵。
③BASF法该工艺的硫酸羟胺是控制氨氧化生成一氧化氮,再在硫酸中用氢气还原而生成的,硫酸铵副产量比传统拉西法少得多。
④Invents法该工艺在环己烷氧化剂制环己酮环节有一定特点,使用了钯催化剂,降低了氢氧化钠的消耗量和废碱液的生成,与BASF类似。
但在反应器材质和催化剂方面有所改进。
另一改进是硫酸铵分解回收氨与SO2,但未工业化应用。
⑤Allied法该工艺特点是用异丙苯法生产的苯酚为原料。
苯酚加氢生成环己酮,环己酮与硫酸羟胺经肟化反应生成环己酮肟,环己酮肟在发烟硫酸作用下经贝克曼重排反应生成CPL。
硫酸铵副产量仍然较高。
上述工艺主要在于从环己酮生产环己酮肟过程中的肟化工艺差异,比较如下:表4 己内酰胺生产工艺比较根据上述工艺比较,采用DSM/HPO 法副产硫酸铵仅为1.7~1.8吨,是各种方法中最少的,是目前己内酰胺工业中主要生产方法之一,它可以以苯、环己烷或苯酚作为原料。
该法以硝酸根加氢制备羟胺磷酸盐用于环己酮生产。
羟胺盐合成的主要反应为:2H 3PO 3+NO 3—+3H 2 → NH 3OH ++2H 2PO 4—+2H 2O环己酮合成的主要反应为:NH 4OH ++2H 2PO 4-+2H 2O+→3PO 4 + H 2PO 4- + 3H 2O对于HPO 法工艺的基本参数见下表:表5 HPO 法的一些基本参数注:以苯酚为原料,理论收率94%,每吨苯酚生产1.12t己内酰胺,而以环己烷为原料,收率至少为74%,每吨环己烷生产1吨己内酰胺。
四、己内酰胺技术发展1、国内技术进展国内己内酰胺行业起步较晚,生产规模和生产成本等还无法与国外企业相竞争。
十余年来中石化公司在引进技术的基础上消化吸收不断创新形成自己的技术,提高企业的竞争力。
主要有:1)研发国产的催化剂由中石化南化研究院开发有自主知识产权的DHO21型环己醇脱氢制环己酮催化剂和NCH1-1型铂系苯加氢制环己烷催化剂,并分别进行工业化和工业侧线试验主要性能指标达到国外同类型催化剂产品的先进水平。
2)环己烷仿生催化氧化新工艺目前环己酮装置普遍采用环己烷无催化氧化工艺,其缺点是单程转化率低,醇酮选择性不高,导致物耗、能耗较高。
近年中石化和湖南大学合作,开发仿生催化氧化工艺,保留空气为氧源优点,应用锰、钴和铁卟啉仿生催化剂(浓度3~4mg/g),在0.8MPa,145℃下,环己烷转化率达6~10%,环己酮、环己醇和环己基过氧化合物选择性>85%,(其中酮和醇占75%以上),环己烷的转化率提高一倍意味着装置产能提高一倍,氧化副反应主要组分为己二酸,可回收利用,并大幅度减少分解用的碱和废碱液,是一个扩能、节能、减排的新工艺。
应用该法对巴陵公司70kt/年环己酮老装置扩能改进,使改造后环己酮能力达到125kt/a。
另一条100kt/a环己酮仿生催化技术生产线正在石家庄化纤厂新建。
3)环己酮氨肟化技术中石化石科院、清华大学共同开发环己酮氨肟化技术,对巴陵公司原有50kt/a己内酰胺装置改造,于2000年使产能达到70kt/a,该技术包括:①磁稳定床用于己内酰胺加氢精制;②采用新型非晶态合金SRNA-4催化剂和磁稳定床新反应工程,产品质量大幅度提高;③研制不同于TS-1的钛硅分子筛(HTS)催化剂。
采用单釜连续淤浆床氨肟化反应器(带轴向流翼型搅拌机桨),反应产物与催化剂分离采用陶瓷膜分离器。
与老工艺相比工艺流程短,操作简便,投资少、排放少,成本大幅度降低。
据称每吨己内酰胺可降低成本约1000元,在此基础上于2003年7月70kt/a装置在巴陵公司建成,8月一次投料成功,实现该技术与国外同步完成工业化并在延缓催化剂失活和催化剂的回收利用方面领先国外技术。
石科院已完成100kt/a环己酮氨肟化装置工艺包。
4)其它技术中石化石家庄化纤公司开发“六氢苯――环己酮肟联产己内酰胺新工艺”,对以甲苯为原料的SINA法的一个重大改进,是石家庄化纤扩能的技术基础。
其它一些关键工艺及设备如高纯氮(O2<2ppm)制备和高速(转速15000转/分)离心式空压机制造等实现国产化。
2、国外技术进展国外技术动态主要在一下几个方面:1)以非苯基丁二烯作为己内酰胺原料:有BASF与杜邦开发的丁二烯与HCN 合成己二腈法工艺和DSM、Shell公司开发的丁二烯与CO、水、醇合成3-戌烯酯法工艺。
据称实现非苯基原料。
可节约费用达30%。
2)无副产硫铵(或少产硫铵)己内酰胺新工艺:日本佳友提出气相法Beckmann重排法转化己内酰胺,新工艺在80℃空气下,己内酰胺产率65~78%,转化率尚低,有望通过催化剂提高。
如能实现将成为最具影响力的工艺。
3)其它在苯加氢、环己醇、酮氧化以及环己酮的肟化等工序的各种改进,近期可供工业化的成果与国内开发的相似。