合成氨工艺操作规程
合成氨的工艺流程
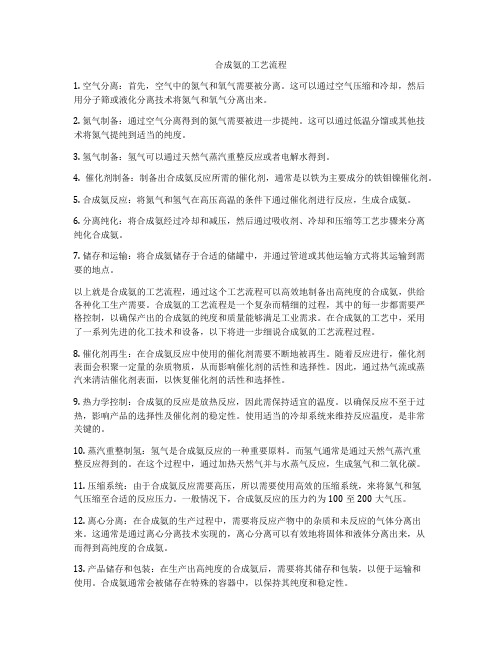
合成氨的工艺流程1. 空气分离:首先,空气中的氮气和氧气需要被分离。
这可以通过空气压缩和冷却,然后用分子筛或液化分离技术将氮气和氧气分离出来。
2. 氮气制备:通过空气分离得到的氮气需要被进一步提纯。
这可以通过低温分馏或其他技术将氮气提纯到适当的纯度。
3. 氢气制备:氢气可以通过天然气蒸汽重整反应或者电解水得到。
4. 催化剂制备:制备出合成氨反应所需的催化剂,通常是以铁为主要成分的铁钼镍催化剂。
5. 合成氨反应:将氮气和氢气在高压高温的条件下通过催化剂进行反应,生成合成氨。
6. 分离纯化:将合成氨经过冷却和减压,然后通过吸收剂、冷却和压缩等工艺步骤来分离纯化合成氨。
7. 储存和运输:将合成氨储存于合适的储罐中,并通过管道或其他运输方式将其运输到需要的地点。
以上就是合成氨的工艺流程,通过这个工艺流程可以高效地制备出高纯度的合成氨,供给各种化工生产需要。
合成氨的工艺流程是一个复杂而精细的过程,其中的每一步都需要严格控制,以确保产出的合成氨的纯度和质量能够满足工业需求。
在合成氨的工艺中,采用了一系列先进的化工技术和设备,以下将进一步细说合成氨的工艺流程过程。
8. 催化剂再生:在合成氨反应中使用的催化剂需要不断地被再生。
随着反应进行,催化剂表面会积聚一定量的杂质物质,从而影响催化剂的活性和选择性。
因此,通过热气流或蒸汽来清洁催化剂表面,以恢复催化剂的活性和选择性。
9. 热力学控制:合成氨的反应是放热反应,因此需保持适宜的温度。
以确保反应不至于过热,影响产品的选择性及催化剂的稳定性。
使用适当的冷却系统来维持反应温度,是非常关键的。
10. 蒸汽重整制氢:氢气是合成氨反应的一种重要原料。
而氢气通常是通过天然气蒸汽重整反应得到的。
在这个过程中,通过加热天然气并与水蒸气反应,生成氢气和二氧化碳。
11. 压缩系统:由于合成氨反应需要高压,所以需要使用高效的压缩系统,来将氮气和氢气压缩至合适的反应压力。
一般情况下,合成氨反应的压力约为100至200大气压。
合成氨工艺操作规程
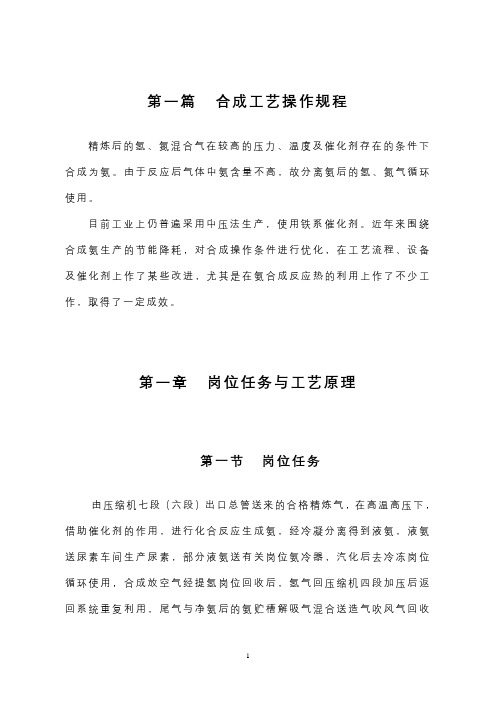
第一篇合成工艺操作规程精炼后的氢、氮混合气在较高的压力、温度及催化剂存在的条件下合成为氨。
由于反应后气体中氨含量不高,故分离氨后的氢、氮气循环使用。
目前工业上仍普遍采用中压法生产,使用铁系催化剂。
近年来围绕合成氨生产的节能降耗,对合成操作条件进行优化,在工艺流程、设备及催化剂上作了某些改进,尤其是在氨合成反应热的利用上作了不少工作,取得了一定成效。
第一章岗位任务与工艺原理第一节岗位任务由压缩机七段(六段)出口总管送来的合格精炼气,在高温高压下,借助催化剂的作用,进行化合反应生成氨,经冷凝分离得到液氨,液氨送尿素车间生产尿素,部分液氨送有关岗位氨冷器,汽化后去冷冻岗位循环使用,合成放空气经提氢岗位回收后,氢气回压缩机四段加压后返回系统重复利用,尾气与净氨后的氨贮槽解吸气混合送造气吹风气回收燃烧炉助燃。
第二节基本原理1氨合成的生产原理氨合成反应的化学方程式:N2+3H22NH3+Q氨合成反应的特点:①可逆反应②放热反应:A标准状况下(25℃)101325KPaB每生成1mol NH3放出46.22KJ热量③体积缩小的反应:3摩尔氢与1摩尔氮生成2摩尔氨,压力下降④必需有催化剂存在才能加快反应2 氨合成反应的平衡氨合成反应是一个可逆反应,正反应与逆反应同时进行,反应物质浓度的减少量与生成物质浓度的增加量达到相等,氨含量不再改变,反应就达到一种动态平衡。
从平衡观点来看:提高反应温度,可使平衡向吸热反应方向移动,降低温度向放热方向移动。
3 氨合成反应速度及影响合成反应的因素反应速度是以单位时间内反应物浓度的减少或生成物浓度的增加量来表示的。
影响氨反应速度的因素:3.1压力:提高压力可以加快氨合成的速度,提高压力就是提高了气体浓度,缩短了气体分子间的距离,碰撞机会增多,反应速度加快。
3.2温度:温度提高使分子运动加快,分子间碰撞的次数增加,又使分子克服化合反应时阻力的能力增大,从而增加了分子有效结合的机会,对于合成反应当温度升高,加速了对氮的活性吸附,又增加了吸附氮与氢的接触机会,使氨合成反应速度加快。
合成氨的工艺流程
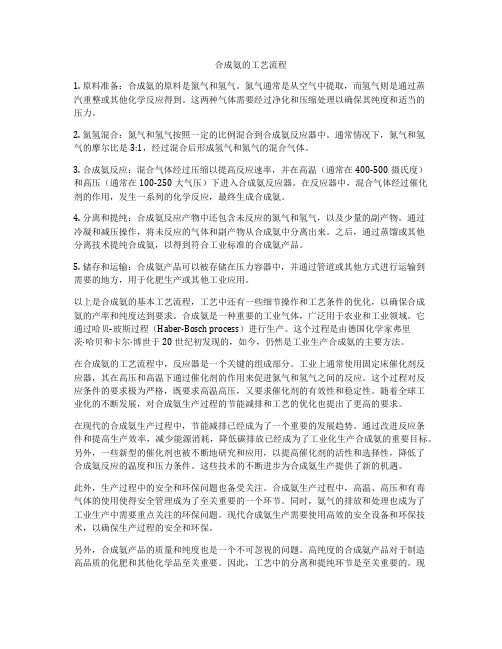
合成氨的工艺流程1. 原料准备:合成氨的原料是氮气和氢气。
氮气通常是从空气中提取,而氢气则是通过蒸汽重整或其他化学反应得到。
这两种气体需要经过净化和压缩处理以确保其纯度和适当的压力。
2. 氮氢混合:氮气和氢气按照一定的比例混合到合成氨反应器中。
通常情况下,氮气和氢气的摩尔比是3:1,经过混合后形成氢气和氮气的混合气体。
3. 合成氨反应:混合气体经过压缩以提高反应速率,并在高温(通常在400-500摄氏度)和高压(通常在100-250大气压)下进入合成氨反应器。
在反应器中,混合气体经过催化剂的作用,发生一系列的化学反应,最终生成合成氨。
4. 分离和提纯:合成氨反应产物中还包含未反应的氮气和氢气,以及少量的副产物。
通过冷凝和减压操作,将未反应的气体和副产物从合成氨中分离出来。
之后,通过蒸馏或其他分离技术提纯合成氨,以得到符合工业标准的合成氨产品。
5. 储存和运输:合成氨产品可以被存储在压力容器中,并通过管道或其他方式进行运输到需要的地方,用于化肥生产或其他工业应用。
以上是合成氨的基本工艺流程,工艺中还有一些细节操作和工艺条件的优化,以确保合成氨的产率和纯度达到要求。
合成氨是一种重要的工业气体,广泛用于农业和工业领域。
它通过哈贝-玻斯过程(Haber-Bosch process)进行生产。
这个过程是由德国化学家弗里茨·哈贝和卡尔·博世于20世纪初发现的,如今,仍然是工业生产合成氨的主要方法。
在合成氨的工艺流程中,反应器是一个关键的组成部分。
工业上通常使用固定床催化剂反应器,其在高压和高温下通过催化剂的作用来促进氮气和氢气之间的反应。
这个过程对反应条件的要求极为严格,既要求高温高压,又要求催化剂的有效性和稳定性。
随着全球工业化的不断发展,对合成氨生产过程的节能减排和工艺的优化也提出了更高的要求。
在现代的合成氨生产过程中,节能减排已经成为了一个重要的发展趋势。
通过改进反应条件和提高生产效率,减少能源消耗,降低碳排放已经成为了工业化生产合成氨的重要目标。
合成氨操作规程

醇氨厂合成氨操作规程目录第一章造气车间岗位操作规程...................... 错误!未定义书签。
造气岗位......................................... 错误!未定义书签。
一、工艺指标.................................. 错误!未定义书签。
(一)、煤气炉控制......................... 错误!未定义书签。
(二)、炉条机............................. 错误!未定义书签。
(三)、风机............................... 错误!未定义书签。
二、工艺流程(五个阶段)...................... 错误!未定义书签。
三、开停车步骤................................ 错误!未定义书签。
(一)、开车步骤........................... 错误!未定义书签。
(二)、停车步骤........................... 错误!未定义书签。
四、不正常现象以及处理方法.................... 错误!未定义书签。
五、巡检部位以及内容.......................... 错误!未定义书签。
六、大修后开车造气制惰方案.................... 错误!未定义书签。
(一)、制惰原理:......................... 错误!未定义书签。
(二)、制惰步骤........................... 错误!未定义书签。
吹风气岗位....................................... 错误!未定义书签。
一、工艺指标.................................. 错误!未定义书签。
二、工艺流程.................................. 错误!未定义书签。
合成氨车间岗位操作规程
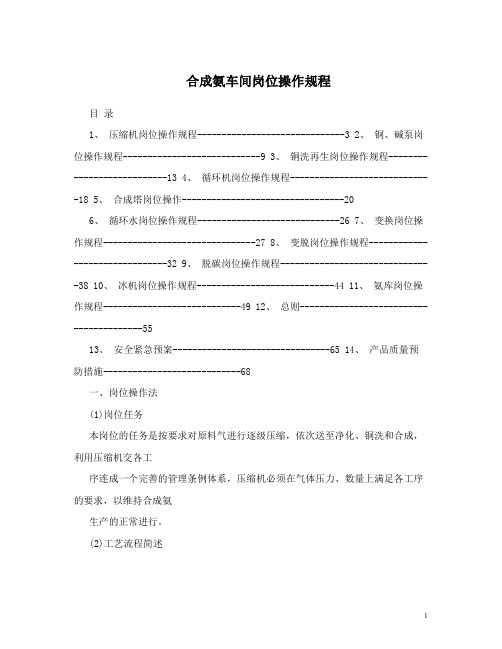
合成氨车间岗位操作规程目录1、压缩机岗位操作规程------------------------------32、铜、碱泵岗位操作规程----------------------------93、铜洗再生岗位操作规程---------------------------134、循环机岗位操作规程-----------------------------185、合成塔岗位操作---------------------------------206、循环水岗位操作规程-----------------------------267、变换岗位操作规程-------------------------------278、变脱岗位操作规程-------------------------------329、脱碳岗位操作规程-------------------------------38 10、冰机岗位操作规程----------------------------44 11、氨库岗位操作规程----------------------------49 12、总则----------------------------------------5513、安全紧急预案--------------------------------65 14、产品质量预防措施----------------------------68一、岗位操作法(1)岗位任务本岗位的任务是按要求对原料气进行逐级压缩,依次送至净化、铜洗和合成,利用压缩机交各工序连成一个完善的管理条例体系,压缩机必须在气体压力、数量上满足各工序的要求,以维持合成氨生产的正常进行。
(2)工艺流程简述从造气脱硫来的半水煤气,经水封槽进入一段缸压缩,此时气体的温度和压力升高,以一段冷却分离器进行冷却分离,再进入二段缸压缩,然后再土星变坏事为好事段冷却分离器进行冷却分离,再进入三段缸压缩,压力提高至2.0Mpa左右,进三段冷却分离器经冷却分离后,送至净化工序进行CO变换和脱除CO,然后回压缩机四段前分离器除去带入的雾状钾碱液,以四段缸压缩后,再经四段2缓冲器、水冷器、气液分离器,再进入五段缸压力13Mpa,再经缓冲器、水冷器、气液分离器送往铜洗工序。
合成氨厂安全操作规程

1.目的:对生产设备安全操作程序进行规定,使设备安全操作规范化、制度化,确保设备安全运行和使用,保障员工人身安全,特制订本操作规程。
2.范围:适用于合成氨生产过程主要(重要)设备安全操作管理。
3.职责:3.1合成氨厂厂长负责组织制定并审核批准实施;3.2技术员、安全员负责制定规程并给予必要的修订;3.3各工段负责人组织学习规程并监督实施;3.4工序操作人员按照规程操作并记录。
4.解释:4.1有重要和主要设备的岗位,制定设备安全操作规程:4.2无重要(主要)设备的岗位,制定岗位安全操作规程。
5.安全操作规程:5.1原煤输送加工工序5.1.1原煤输送机(TD2-18:5-6)a.操作人员进入岗位前必须穿戴好劳动保护用品;b.开车前认真检查区域内设备及电路、水带喷淋等安全防护设备设施处于工作状态;c.检查输煤皮带机、附属设备等相关设备,确认完好;巡检设备周围是否有人在工作、活动;d.确认无人后开车空转,观察设备运转是否符合安全要求;e.上料实转,随时巡查设备运转情况,运转过程中严禁将手或身体进入皮带运转区域,防止挤伤或卷入;巡视过程中操作人员严禁横越皮带机和下料口;开车时不许用皮带运送其它物品。
f.下煤不畅及其它故障必须先停皮带输送机,通知值班长协调解决,严禁输煤人员私自处理;g.皮带输送机运转时,操作人员不得擅自脱离岗位,人员不要接近裸露的运转部位。
运转中严禁将手或其他物品进入皮带机运转区域,防止人身伤害;不许用皮带运送其它物品。
h.皮带在运行中禁止加油、清扫周围粉尘和维修作业;动火、登高等作业必须办证,采取有效安全措施后方可作业。
生产正常情况下,不能带负荷起停车。
i.厂房及皮带走廊做好通风防护,每班最少清扫2次,减少粉尘危害。
除尘风机处于常开状态。
j.设备检修时,通知电工切断所检修设备的电源,并挂上“有人工作,禁止合闸”警示牌,并设有专人监护。
一定要做到有效沟通,防止在检修时误操作造成人员伤害。
k.输煤管廊动火时,必须先停止皮带输送机,清除地上粉尘,加强通风,备好水管及消防喷淋;待到无粉尘飞扬时,方可动火,动火过程必须双人监护到位。
氨合成岗位操作规程
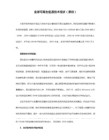
③ 氢氮比失调
④ 惰性气体含量高
⑤ 微量高
⑥ 合成塔副线阀
或冷激气阀开得过大
⑦ 新鲜气量减少
⑧冷凝塔内件漏
⑨合成塔内件漏 ① 开透平循环机近路阀及系统近路阀调节
② 查明原因并对应处理:
a适当多加氨
b联系冰机岗位处理
c排放油水
d加大水量降低循环气温度
e迅速开大放氨阀,适当减循环量,
⑷根据调度命令决定是否用电炉,若不用电炉则停透平循环机,塔内保持正压,催化剂层温度自然下降。
⑸若启用电炉保温,则系统留压8.0—10.0MPa,开一台透平循环机,保证安全气量,保温420℃待命ห้องสมุดไป่ตู้
5.5紧急停车:紧急停车常常是在发生事故时被迫进行的,所以首先应迅速判断事故发生的原因,沉着冷静地正确处理。
⑶合成系统的弛放气由H2、N2、NH3、CH4等气体组成,其中H2、NH3都是经过多个工段的工艺处理后得到的,如果能对合成系统弛放气中的H2、NH3进行回收再利用,将有效地降低整个合成系统的消耗定额。因此,将合成弛放气送往氢氨回收工段进行回收处理。
1.2管辖范围:合成工段所属的所有设备,氨合成塔、中锅、水加热器、塔外换热器、水冷器、氨分离器、氨冷凝塔、氨冷器、油分离器、透平循环机及其附机、保护气系统等,以及相应连接的高、中、低压管道、阀门等。
⑷导气过程中密切注意氨分和冷凝塔液位的变化,必要时可将自调打全手动位置,以手动方式控制其液位在工艺指标内,待液位稳定后再按自调。
⑸将各工艺参数控
制在正常的指标范围内,待其稳定一段时间后,即可加量。
5.2升温:
⑴接到调度指令后,由新鲜气大阀控制,向系统充压至80—100kgf/cm2,关闭新鲜气大阀。⑵启动一台透平循环机并入系统,按电炉操作规程送电升温,升温阶段系统不得低于50 kgf/cm2,循环气量不得低于电炉的安全气量,以防电炉烧坏。⑶用循环机近路阀、系统近路阀以及升降电压等手段控制电炉升温速率35—40℃/h,升至400℃即可开启新鲜气大阀向系统导入新鲜气。⑷导气时的温度根据催化剂的型号以及使用阶段可作适当升高或降低。
合成氨的操作规程

合成氨的操作规程操作规程:合成氨1. 实验目的:合成氨是一种重要的化学原料,广泛应用于肥料、药品和化学工业等领域。
本实验旨在通过催化剂的作用,在适当的条件下,实现氮气和氢气的催化合成,产生氨气。
2. 实验原理:合成氨的基本反应为N2 + 3H2 →2NH3,该反应需要高温和高压的催化条件。
传统工业上主要采用哈柏—博氏法来合成氨气,该法采用铁、铁锆或铁铬催化剂,在高温(350-500℃)和高压(100-250atm)的条件下进行。
3. 实验步骤及操作规程:(1)准备操作环境:a. 确保实验室内通风良好,避免氨气泄漏造成人员伤害;b. 穿戴防护设备,如防护眼镜、实验服和手套等;c. 确保实验平台清洁整洁,没有易燃和易爆物品。
(2)操作前准备:a. 检查实验设备的完整性和可用性,如反应釜、催化剂、电炉等;b. 根据实验需要,将氮气和氢气储存罐连接到反应釜上,并确保连接处严密可靠;c. 将催化剂粉末装入适量的催化剂包,装入反应釜中;d. 在反应釜上设置压力表和温度计,以监测反应压力和温度。
(3)操作步骤:a. 打开氮气源和氢气源,分别调节流量计使其在适宜范围内;b. 打开反应釜的气阀,调节进气量,使气体在一定速度进入反应釜;c. 打开电炉,调节温度使其逐渐升高到所需反应温度;d. 根据实验要求控制反应时间,一般为几小时至一天不等;e. 反应结束后,关闭电炉和气阀,断开氮气和氢气源,停止气体进入反应釜;f. 等待反应釜冷却后,将催化剂包取出,检查反应产物。
(4)实验后处理:a. 将反应釜清洗干净,并妥善保管;b. 处理反应产物,如收集氨气、检测氨气纯度等。
4. 实验安全注意事项:a. 氨气具有刺激性气味,入侵人体可造成眼睛和呼吸道刺激,应避免直接接触;b. 实验时要保持通风良好,避免氨气积聚;c. 确保催化剂包装密封良好,避免催化剂散落或泄漏;d. 高温和高压环境下操作,注意防爆和防烫伤;e. 实验后妥善处理反应产物,避免对环境造成污染。
合成氨工艺流程
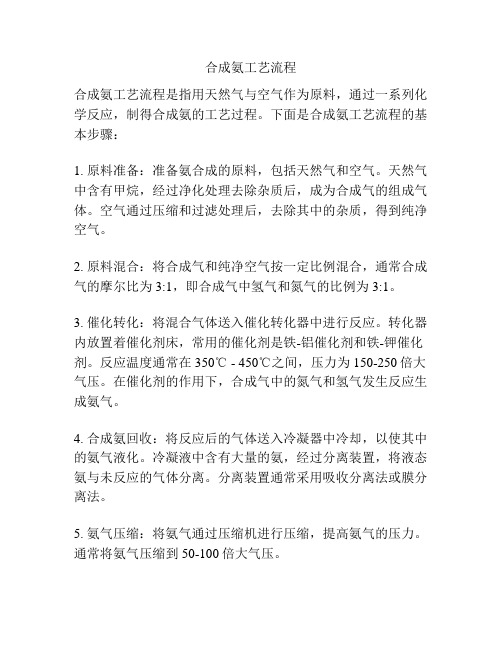
合成氨工艺流程合成氨工艺流程是指用天然气与空气作为原料,通过一系列化学反应,制得合成氨的工艺过程。
下面是合成氨工艺流程的基本步骤:1. 原料准备:准备氨合成的原料,包括天然气和空气。
天然气中含有甲烷,经过净化处理去除杂质后,成为合成气的组成气体。
空气通过压缩和过滤处理后,去除其中的杂质,得到纯净空气。
2. 原料混合:将合成气和纯净空气按一定比例混合,通常合成气的摩尔比为3:1,即合成气中氢气和氮气的比例为3:1。
3. 催化转化:将混合气体送入催化转化器中进行反应。
转化器内放置着催化剂床,常用的催化剂是铁-铝催化剂和铁-钾催化剂。
反应温度通常在350℃ - 450℃之间,压力为150-250倍大气压。
在催化剂的作用下,合成气中的氮气和氢气发生反应生成氨气。
4. 合成氨回收:将反应后的气体送入冷凝器中冷却,以使其中的氨气液化。
冷凝液中含有大量的氨,经过分离装置,将液态氨与未反应的气体分离。
分离装置通常采用吸收分离法或膜分离法。
5. 氨气压缩:将氨气通过压缩机进行压缩,提高氨气的压力。
通常将氨气压缩到50-100倍大气压。
6. 氨气净化:将压缩后的氨气送入净化装置,去除其中的杂质。
常见的净化方法包括活性炭吸附法和干燥剂吸附法。
7. 氨气脱水:为了提高氨气的纯度,通常还需对氨气进行脱水处理。
常用的方法是通过吸附剂或分子筛吸附剂去除氨气中的水分。
8. 氨气储存:将经过净化和脱水处理后的氨气储存起来,常用的储存方式有液氨储罐和气氨储罐。
合成氨工艺流程是一个复杂的过程,需要控制好各个环节的温度、压力和反应速度等参数,保证反应效果和产品质量。
合成氨被广泛用于制造化肥、合成树脂、合成纤维等各种化学工业领域。
合成氨各工序工艺详细流程
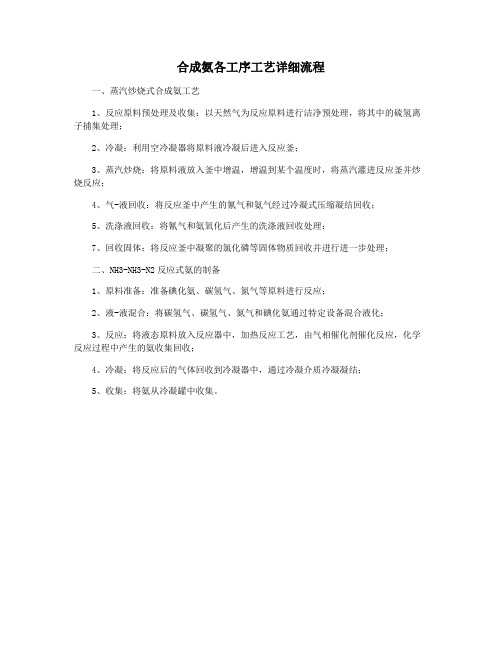
合成氨各工序工艺详细流程
一、蒸汽炒烧式合成氨工艺
1、反应原料预处理及收集:以天然气为反应原料进行洁净预处理,将其中的硫氢离子捕集处理;
2、冷凝:利用空冷凝器将原料液冷凝后进入反应釜;
3、蒸汽炒烧:将原料液放入釜中增温,增温到某个温度时,将蒸汽灌进反应釜并炒烧反应;
4、气-液回收:将反应釜中产生的氰气和氨气经过冷凝式压缩凝结回收;
5、洗涤液回收:将氰气和氨氧化后产生的洗涤液回收处理;
7、回收固体:将反应釜中凝聚的氯化磷等固体物质回收并进行进一步处理;
二、NH3-NH3-N2反应式氨的制备
1、原料准备:准备碘化氨、碳氢气、氮气等原料进行反应;
2、液-液混合:将碳氢气、碳氢气、氮气和碘化氨通过特定设备混合液化;
3、反应:将液态原料放入反应器中,加热反应工艺,由气相催化剂催化反应,化学反应过程中产生的氨收集回收;
4、冷凝:将反应后的气体回收到冷凝器中,通过冷凝介质冷凝凝结;
5、收集:将氨从冷凝罐中收集。
合成氨合成工段岗位操作规程
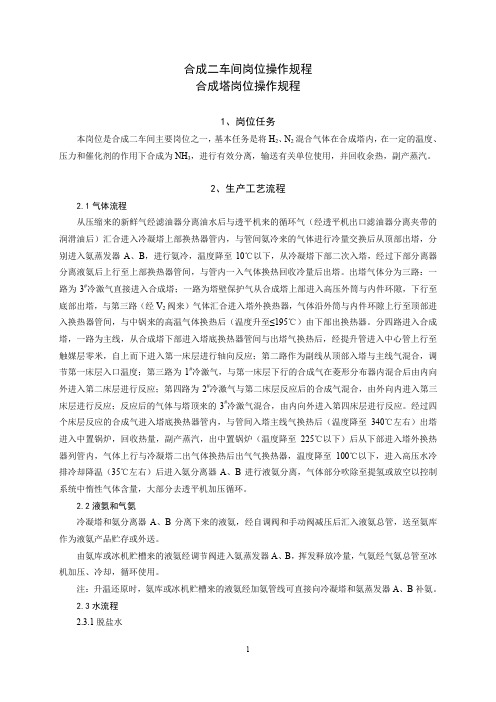
合成二车间岗位操作规程合成塔岗位操作规程1、岗位任务本岗位是合成二车间主要岗位之一,基本任务是将H2、N2混合气体在合成塔内,在一定的温度、压力和催化剂的作用下合成为NH3,进行有效分离,输送有关单位使用,并回收余热,副产蒸汽。
2、生产工艺流程2.1气体流程从压缩来的新鲜气经滤油器分离油水后与透平机来的循环气(经透平机出口滤油器分离夹带的润滑油后)汇合进入冷凝塔上部换热器管内,与管间氨冷来的气体进行冷量交换后从顶部出塔,分别进入氨蒸发器A、B,进行氨冷,温度降至10℃以下,从冷凝塔下部二次入塔,经过下部分离器分离液氨后上行至上部换热器管间,与管内一入气体换热回收冷量后出塔。
出塔气体分为三路:一路为3#冷激气直接进入合成塔;一路为塔壁保护气从合成塔上部进入高压外筒与内件环隙,下行至底部出塔,与第三路(经V2阀来)气体汇合进入塔外换热器,气体沿外筒与内件环隙上行至顶部进入换热器管间,与中锅来的高温气体换热后(温度升至≤195℃)由下部出换热器。
分四路进入合成塔,一路为主线,从合成塔下部进入塔底换热器管间与出塔气换热后,经提升管进入中心管上行至触媒层零米,自上而下进入第一床层进行轴向反应;第二路作为副线从顶部入塔与主线气混合,调节第一床层入口温度;第三路为1#冷激气,与第一床层下行的合成气在菱形分布器内混合后由内向外进入第二床层进行反应;第四路为2#冷激气与第二床层反应后的合成气混合,由外向内进入第三床层进行反应;反应后的气体与塔顶来的3#冷激气混合,由内向外进入第四床层进行反应。
经过四个床层反应的合成气进入塔底换热器管内,与管间入塔主线气换热后(温度降至340℃左右)出塔进入中置锅炉,回收热量,副产蒸汽,出中置锅炉(温度降至225℃以下)后从下部进入塔外换热器列管内,气体上行与冷凝塔二出气体换热后出气气换热器,温度降至100℃以下,进入高压水冷排冷却降温(35℃左右)后进入氨分离器A、B进行液氨分离,气体部分吹除至提氢或放空以控制系统中惰性气体含量,大部分去透平机加压循环。
氨的合成操作规程
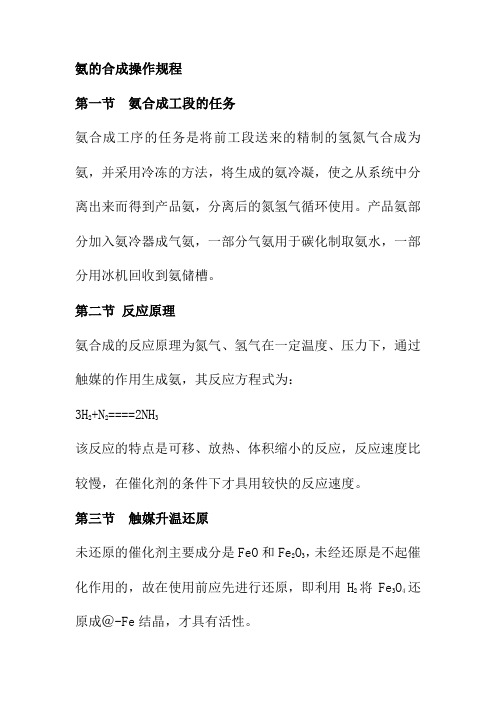
氨的合成操作规程第一节氨合成工段的任务氨合成工序的任务是将前工段送来的精制的氢氮气合成为氨,并采用冷冻的方法,将生成的氨冷凝,使之从系统中分离出来而得到产品氨,分离后的氮氢气循环使用。
产品氨部分加入氨冷器成气氨,一部分气氨用于碳化制取氨水,一部分用冰机回收到氨储槽。
第二节反应原理氨合成的反应原理为氮气、氢气在一定温度、压力下,通过触媒的作用生成氨,其反应方程式为:3H2+N2====2NH3该反应的特点是可移、放热、体积缩小的反应,反应速度比较慢,在催化剂的条件下才具用较快的反应速度。
第三节触媒升温还原未还原的催化剂主要成分是FeO和Fe2O3,未经还原是不起催化作用的,故在使用前应先进行还原,即利用H2将Fe3O4还原成@-Fe结晶,才具有活性。
一、升温还原控制指标如下表,根据催化剂性能不同,控制指标也有所不同。
1、升温阶段升温阶段以循环量及电炉功率来调节升温速率。
控制好轴径向温差。
径向应小于10℃,轴向在40~60℃为宜。
2、还原初期有水生成但量不多,氨冷温度在-10℃以下,循环氢含量>70%,同时要求采用高氢、低氨冷温度,有利还原,除去水汽。
3、恒温阶段当还原接近主期时,为防止水汽浓度超指标和径向温差增大,一般采用恒温操作,使各项控制指标在稳定范围之内,以便转入还原主期。
4、还原主期有大量的水,水汽浓度较高。
部分催化剂已得到还原,可以适当提高压力以增加氨的合成反应,以便利用反应热提高空速降低水气浓度,但提压时,必须注意平面温差,如平面温差大,提压宜慢或暂不提。
若水汽浓度高,平面温差大,采用恒温的办法,待水气浓度降低后,再提压、提温,当水气浓度小于0.2g/m3,且底部温度达到490~500℃时,可转入还原末期。
5、还原末期催化剂大部分水分已基本出完,为了获得更高的还原温度,需将温度提高到催化剂要求的最终还原温度,达到490~500℃,还原基本结束,可转入轻负荷阶段。
6、轻负荷阶段刚还原好的催化剂不宜过早加载,以免产生大量的反应热,造成局部过热而降低催化剂活性,必须在一定时间内进行轻负荷运转。
化工企业氨合成岗位安全操作规程
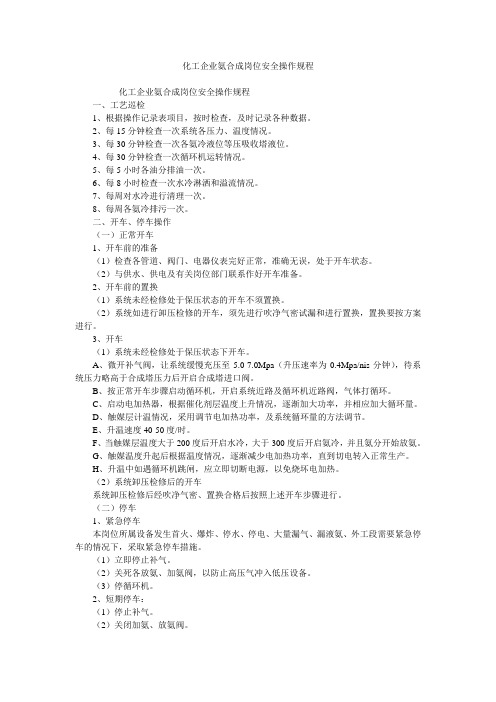
化工企业氨合成岗位安全操作规程化工企业氨合成岗位安全操作规程一、工艺巡检1、根据操作记录表项目,按时检查,及时记录各种数据。
2、每15分钟检查一次系统各压力、温度情况。
3、每30分钟检查一次各氨冷液位等压吸收塔液位。
4、每30分钟检查一次循环机运转情况。
5、每5小时各油分排油一次。
6、每8小时检查一次水冷淋洒和溢流情况。
7、每周对水冷进行清理一次。
8、每周各氨冷排污一次。
二、开车、停车操作(一)正常开车1、开车前的准备(1)检查各管道、阀门、电器仪表完好正常,准确无误,处于开车状态。
(2)与供水、供电及有关岗位部门联系作好开车准备。
2、开车前的置换(1)系统未经检修处于保压状态的开车不须置换。
(2)系统如进行卸压检修的开车,须先进行吹净气密试漏和进行置换,置换要按方案进行。
3、开车(1)系统未经检修处于保压状态下开车。
A、微开补气阀,让系统缓慢充压至5.0-7.0Mpa(升压速率为0.4Mpa/nis分钟),待系统压力略高于合成塔压力后开启合成塔进口阀。
B、按正常开车步骤启动循环机,开启系统近路及循环机近路阀,气体打循环。
C、启动电加热器,根据催化剂层温度上升情况,逐渐加大功率,并相应加大循环量。
D、触媒层计温情况,采用调节电加热功率,及系统循环量的方法调节。
E、升温速度40-50度/时。
F、当触媒层温度大于200度后开启水冷,大于300度后开启氨冷,并且氨分开始放氨。
G、触媒温度升起后根据温度情况,逐渐减少电加热功率,直到切电转入正常生产。
H、升温中如遇循环机跳闸,应立即切断电源,以免烧坏电加热。
(2)系统卸压检修后的开车系统卸压检修后经吹净气密、置换合格后按照上述开车步骤进行。
(二)停车1、紧急停车本岗位所属设备发生首火、爆炸、停水、停电、大量漏气、漏液氨、外工段需要紧急停车的情况下,采取紧急停车措施。
(1)立即停止补气。
(2)关死各放氨、加氨阀,以防止高压气冲入低压设备。
(3)停循环机。
2、短期停车:(1)停止补气。
合成氨工艺流程详解
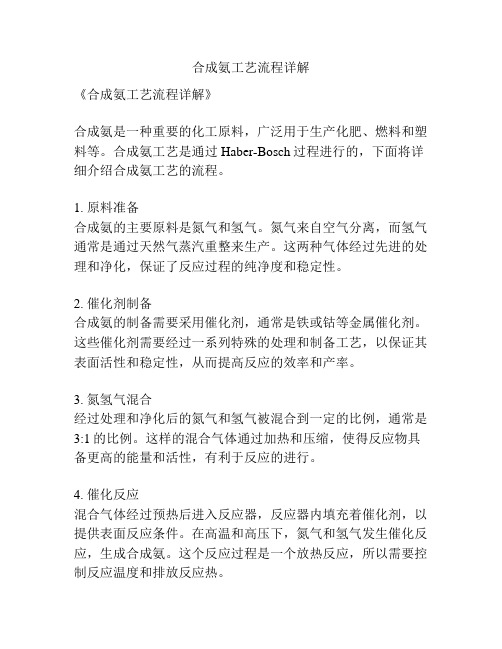
合成氨工艺流程详解
《合成氨工艺流程详解》
合成氨是一种重要的化工原料,广泛用于生产化肥、燃料和塑料等。
合成氨工艺是通过Haber-Bosch过程进行的,下面将详细介绍合成氨工艺的流程。
1. 原料准备
合成氨的主要原料是氮气和氢气。
氮气来自空气分离,而氢气通常是通过天然气蒸汽重整来生产。
这两种气体经过先进的处理和净化,保证了反应过程的纯净度和稳定性。
2. 催化剂制备
合成氨的制备需要采用催化剂,通常是铁或钴等金属催化剂。
这些催化剂需要经过一系列特殊的处理和制备工艺,以保证其表面活性和稳定性,从而提高反应的效率和产率。
3. 氮氢气混合
经过处理和净化后的氮气和氢气被混合到一定的比例,通常是3:1的比例。
这样的混合气体通过加热和压缩,使得反应物具备更高的能量和活性,有利于反应的进行。
4. 催化反应
混合气体经过预热后进入反应器,反应器内填充着催化剂,以提供表面反应条件。
在高温和高压下,氮气和氢气发生催化反应,生成合成氨。
这个反应过程是一个放热反应,所以需要控制反应温度和排放反应热。
5. 分离和提纯
产生的混合气体经过冷却后进入分离装置,将产生的合成氨和未反应的氮氢气体进行分离。
分离得到的合成氨会进一步进行脱水和提纯处理,使其符合工业用途的级别。
通过以上的工艺流程,合成氨可以有效地得到,而且具有较高的产率和纯度。
这个工艺流程成为了化工工业中的一种重要生产方式,为生产化肥和其他化工产品提供了重要的原料支持。
合成氨工艺操作规程

第一篇合成工艺操作规程精炼后的氢、氮混合气在较高的压力、温度及催化剂存在的条件下合成为氨。
由于反应后气体中氨含量不高,故分离氨后的氢、氮气循环使用。
目前工业上仍普遍采用中压法生产,使用铁系催化剂。
近年来围绕合成氨生产的节能降耗,对合成操作条件进行优化,在工艺流程、设备及催化剂上作了某些改进,尤其是在氨合成反应热的利用上作了不少工作,取得了一定成效。
第一章岗位任务与工艺原理第一节岗位任务由压缩机七段(六段)出口总管送来的合格精炼气,在高温高压下,借助催化剂的作用,进行化合反应生成氨,经冷凝分离得到液氨,液氨送尿素车间生产尿素,部分液氨送有关岗位氨冷器,汽化后去冷冻岗位循环使用,合成放空气经提氢岗位回收后,氢气回压缩机四段加压后返回系统重复利用,尾气与净氨后的氨贮槽解吸气混合送造气吹风气回收燃烧炉助燃。
第二节基本原理1氨合成的生产原理氨合成反应的化学方程式:N2+3H22NH3+Q氨合成反应的特点:①可逆反应②放热反应:A标准状况下(25℃)101325KPaB每生成1mol NH3放出46.22KJ热量③体积缩小的反应:3摩尔氢与1摩尔氮生成2摩尔氨,压力下降④必需有催化剂存在才能加快反应2 氨合成反应的平衡氨合成反应是一个可逆反应,正反应与逆反应同时进行,反应物质浓度的减少量与生成物质浓度的增加量达到相等,氨含量不再改变,反应就达到一种动态平衡。
从平衡观点来看:提高反应温度,可使平衡向吸热反应方向移动,降低温度向放热方向移动。
3 氨合成反应速度及影响合成反应的因素反应速度是以单位时间内反应物浓度的减少或生成物浓度的增加量来表示的。
影响氨反应速度的因素:3.1压力:提高压力可以加快氨合成的速度,提高压力就是提高了气体浓度,缩短了气体分子间的距离,碰撞机会增多,反应速度加快。
3.2温度:温度提高使分子运动加快,分子间碰撞的次数增加,又使分子克服化合反应时阻力的能力增大,从而增加了分子有效结合的机会,对于合成反应当温度升高,加速了对氮的活性吸附,又增加了吸附氮与氢的接触机会,使氨合成反应速度加快。
合成氨的工艺流程[大全五篇]
![合成氨的工艺流程[大全五篇]](https://img.taocdn.com/s3/m/5878b6cefbb069dc5022aaea998fcc22bcd1431a.png)
合成氨的工艺流程[大全五篇]第一篇:合成氨的工艺流程工艺流程1.合成氨的工艺流程(1)原料气制备将煤和天然气等原料制成含氢和氮的粗原料气。
对于固体原料煤和焦炭,通常采用气化的方法制取合成气;渣油可采用非催化部分氧化的方法获得合成气;对气态烃类和石脑油,工业中利用二段蒸汽转化法制取合成气。
(2)净化对粗原料气进行净化处理,除去氢气和氮气以外的杂质,主要包括变换过程、脱硫脱碳过程以及气体精制过程。
① 一氧化碳变换过程在合成氨生产中,各种方法制取的原料气都含有CO,其体积分数一般为12%~40%。
合成氨需要的两种组分是H2和N2,因此需要除去合成气中的CO。
变换反应如下:CO+H2OH→2+CO2 =-41.2kJ/mol 0298HΔ由于CO变换过程是强放热过程,必须分段进行以利于回收反应热,并控制变换段出口残余CO含量。
第一步是高温变换,使大部分CO转变为CO2和H2;第二步是低温变换,将CO含量降至0.3%左右。
因此,CO变换反应既是原料气制造的继续,又是净化的过程,为后续脱碳过程创造条件。
② 脱硫脱碳过程各种原料制取的粗原料气,都含有一些硫和碳的氧化物,为了防止合成氨生产过程催化剂的中毒,必须在氨合成工序前加以脱除,以天然气为原料的蒸汽转化法,第一道工序是脱硫,用以保护转化催化剂,以重油和煤为原料的部分氧化法,根据一氧化碳变换是否采用耐硫的催化剂而确定脱硫的位置。
工业脱硫方法种类很多,通常是采用物理或化学吸收的方法,常用的有低温甲醇洗法(Rectisol)、聚乙二醇二甲醚法(Selexol)等。
粗原料气经CO变换以后,变换气中除H2外,还有CO2、CO和CH4等组分,其中以CO2含量最多。
CO2既是氨合成催化剂的毒物,又是制造尿素、碳酸氢铵等氮肥的重要原料。
因此变换气中CO2的脱除必须兼顾这两方面的要求。
一般采用溶液吸收法脱除CO2。
根据吸收剂性能的不同,可分为两大类。
一类是物理吸收法,如低温甲醇洗法(Rectisol),聚乙二醇二甲醚法(Selexol),碳酸丙烯酯法。
合成作业安全操作规程(通用版)

( 操作规程 )单位:_________________________姓名:_________________________日期:_________________________精品文档 / Word文档 / 文字可改合成作业安全操作规程(通用版)Safety operating procedures refer to documents describing all aspects of work steps and operating procedures that comply with production safety laws and regulations.合成作业安全操作规程(通用版)一、岗位任务1、在高温、高压和有触媒的条件下,将合格的H2、N2混合气合成氨。
2、合成氨经分离、冷凝得液氨,贮存于氨罐。
3、液氨在氨冷器中气化送往吸收,制取NH4HCO3。
3H2+N22NH3+Q二、工艺流程图(另附)三、岗位工艺指标1、压力:合成塔进口:≤31.4MPa合成塔进出口压差:≤0.8MPa液氨贮罐:≤1.6MPa循环机压差:≤2。
8MPa•循环机油压:≥0。
15~0.25MPa气氨总管压力:≤0.2MPa系统升降压速率:每分钟0.4-0.6MPa2、温度:合成塔出口温度<300℃触媒层温度波动:≤±5℃热点温度:一二段:480±5℃:三段:480±5℃:四段:460±5℃水冷器出口:<35℃氨冷出口一5℃~一20℃合成塔热点升降温速率:每小时45℃气体成份微量CO+CO2≤25PPM,正常生产:30-50PPM,半量生产:﹥50PPM,停止送气。
氢氮比2.0~2.8,合成塔进口氨含量<3.0%。
冰机:(1)压力:进口气氨压力:0.18~0.3MPa出口气氨压力:≤1.6MPa油泵油压≥0.15~0.25MPa(2)温度:冰机出口温度<150℃循环油位:1/2~2/3四、岗位开停车步骤:l、正常开车:(1)接通知后,检查阀门(补充气、塔进出口、付线、循环机及各段冷、热激各阀门开关位置是否正确及排放阀位置)。
- 1、下载文档前请自行甄别文档内容的完整性,平台不提供额外的编辑、内容补充、找答案等附加服务。
- 2、"仅部分预览"的文档,不可在线预览部分如存在完整性等问题,可反馈申请退款(可完整预览的文档不适用该条件!)。
- 3、如文档侵犯您的权益,请联系客服反馈,我们会尽快为您处理(人工客服工作时间:9:00-18:30)。
第一篇 合成工艺操作规程精炼后的氢、氮混合气在较高的压力、温度及催化剂存在的条件下合成为氨。
由于反应后气体中氨含量不高,故分离氨后的氢、氮气循环使用。
目前工业上仍普遍采用中压法生产,使用铁系催化剂。
近年来围绕合成氨生产的节能降耗,对合成操作条件进行优化,在工艺流程、设备及催化剂上作了某些改进,尤其是在氨合成反应热的利用上作了不少工作,取得了一定成效。
第一章 岗位任务与工艺原理第一节 岗位任务由压缩机七段(六段)出口总管送来的合格精炼气,在高温高压下,借助催化剂的作用,进行化合反应生成氨,经冷凝分离得到液氨,液氨送尿素车间生产尿素,部分液氨送有关岗位氨冷器,汽化后去冷冻岗位循环使用,合成放空气经提氢岗位回收后,氢气回压缩机四段加压后返回系统重复利用,尾气与净氨后的氨贮槽解吸气混合送造气吹风气回收燃烧炉助燃。
第二节 基本原理1 氨合成的生产原理氨合成反应的化学方程式:N2+3H 22NH 3+Q氨合成反应的特点:①可逆反应②放热反应: A 标准状况下(25℃)101325KPaB 每生成1mol NH 3放出46.22KJ 热量③体积缩小的反应:3摩尔氢与1摩尔氮生成2摩尔氨,压力下降 ④必需有催化剂存在才能加快反应 2 氨合成反应的平衡氨合成反应是一个可逆反应,正反应与逆反应同时进行,反应物质浓度的减少量与生成物质浓度的增加量达到相等,氨含量不再改变,反应就达到一种动态平衡。
从平衡观点来看:提高反应温度,可使平衡向吸热反应方向移动,降低温度向放热方向移动。
3 氨合成反应速度及影响合成反应的因素反应速度是以单位时间内反应物浓度的减少或生成物浓度的增加量来表示的。
影响氨反应速度的因素:3.1压力:提高压力可以加快氨合成的速度,提高压力就是提高了气体浓度,缩短了气体分子间的距离,碰撞机会增多,反应速度加快。
3.2温度:温度提高使分子运动加快,分子间碰撞的次数增加,又使分子克服化合反应时阻力的能力增大,从而增加了分子有效结合的机会,对于合成反应当温度升高,加速了对氮的活性吸附,又增加了吸附氮与氢的接触机会,使氨合成反应速度加快。
3.3反应物浓度:反应物浓度的增加,增加了分子间碰撞的机会,有利于加快反应速度。
归纳起来如下:反应过程必须在高压下进行,压力越高,越有利于氨合成反应的平衡和速度。
反应温度对氨合成反应平衡和速度的影响互相制约。
混合气中氮和氢的含量越高越有利于反应,惰性气体越少越好。
3.4 催化剂的影响:①催化剂又称触媒,它在化学反应中能改变物质反应速度,而本身的组成和质量在反应前后保持不变。
②催化剂的主要作用是降低反应的活化能,加快反应速度,缩短达到反应平衡的时间。
③既然温度对合成氨反应平衡和速度的影响互相矛盾,就存在一个最佳的温度,反应速度对温度的要求是借助于催化剂实现的。
4 合成催化剂的组成和结构3+铁系催化剂活性组分为金属铁,未还原前为FeO和Fe2O3,Fe2+/ Fe在0.47-0.57之间,可视为Fe3O4具有尖晶石结构。
作为促进剂的成份有K2O 、CaO、MgO、Al2O3、SiO2等。
Al2O3的作用是当催化剂用氢还原时,氧化铁被还原成a-Fe,未被还原Fe3O4保持着尖晶石结构起到骨架作用,防止铁细晶长大,因而增大了催化剂表面,提高了活性。
MgO的作用与Al2O3相似,也是结构型促进剂,通过改善还原态铁的结构而呈现出促进作用。
CaO为电子型促进剂,同时能降低熔体的熔点和粘度,有利于Al2O3与Fe3O4固熔体形成,还可以提高催化剂的热稳定性。
K2O为电子型促进剂,它可以使金属电子逸出功降低,有助于氮的活性吸附,从而提高其活性。
SiO2具有中和K2O、CaO碱性组分的作用。
SiO2还具有提高催化剂抗水毒害和耐烧结性能,通常制成的催化剂为黑色不规则颗粒,有金属光泽。
还原态催化剂的内表面积为4-16㎡/g ,催化剂的活性温度一般为350-550℃之间。
5 催化剂的还原Fe2O3和FeO并不能加快氨合成的反应速度,真正起催化作用是具有活性的a-Fe晶粒。
5.1 还原方法分类:将Fe2O3和FeO变成金属a-Fe是催化剂还原过程。
催化剂活性不仅与其组成和制造方法有关,而且还与还原过程的条件和控制方法有关。
催化剂还原反应式为:Fe3O4+4H2=3Fe+4H2O △H298=149.9kj/mol 触媒整个还原过程为吸热反应,还原温度借助于电加热维持,随着还原的进行,催化剂开始具有活性,并伴有氨生成和放热。
催化剂还原也可在塔外进行,即预还原,预还原有以下优点:(1)不受热能、塔结构和氨生成的影响,避免了合成塔内不适宜的还原条件对催化剂活性的损害,使催化剂得以在最佳条件下进行还原,有利于提高催化剂的活性。
(2)缩短合成塔的升温还原时间,有利于强化生产。
预还原后的催化剂,需用少量含O2气体加以钝化保护才能转移至合成塔。
5.2 还原条件的确定确定还原条件的原则:一方面是使Fe3O4和FeO充分还原为a-Fe,另一方面是还原生成铁结晶不因重结晶而长大,以保证有最大的比表面积和更多的活性中心,宜选取合适的还原温度,压力,空速和还原气组成。
还原温度的控制对催化剂活性影响很大,提高还原温度能加快还原反应速度,缩短还原时间。
还原温度过高会导致a-Fe晶体长大,催化剂表面积减小,活性降低。
因此,在实际还原温度不超过它的正常使用温度。
还原气中氢含量尽可能高(>75%)水汽浓度尽可能低(<2g/m3)水汽浓度的高低对催化剂的活性影响很大,尽可能采用高空速以保证还原气中的低水汽含量。
在保证空速的前提下,还原压力低些为好。
5.3 催化剂的还原操作根据塔型号、催化剂还原分为分层还原和整体还原两种:根据温度变化、出水情况将整个还原分为升温阶段,还原期(初期、主期、未期)降温期、轻负荷等几个阶段。
升温期按40-50℃/小时,迅速将催化剂升温至300℃左右,此时基本无水放出。
还原期根据出水情况提温,出水与提温交替进行。
初期为吸附水,主期为化学水,初还原的催化剂活性高,床层升温快,容易过热进行一段时间,轻负荷生产可以避免催化剂衰老延长使用寿命。
还原操作要点如下:还原期间温度、压力、循环量、气体成分等工艺条件要稳定。
在正常情况下,不得同时变更多项工艺条件。
严格控制水汽浓度或出水速度,合成塔出水汽浓度不大于3g/m 3。
还原过程中要尽量做到高氢比、高空速、低压力,调节温度一般用循环量和电加热器,还原时一般不用副阀调节。
视出水情况提温提压。
严格控制升温曲线,避免温度出现反复波动。
要定时分析合成塔出口气的水汽浓度。
当前工序出现问题时,要及时切断新鲜气。
还原放出水中氨含量大于80%达3小时可放入贮槽。
当出塔水汽浓度连续三次分析<0.1g/m 3时,还原即可结束。
(10)还原期间,因循环机跳闸应先停电加热器,保证足够的安全,以免烧断电炉丝。
6 催化剂的使用6.1催化剂的中毒和老化:原料气中引起催化剂中毒的成分有:暂时性中毒:O2、CO 、CO2、H2O等永久性中毒:H2S、SO2、铜液等催化剂的衰老受温度影响,催化剂在使用的过程中,由于过热或由于可逆中毒而被反复氧化还原,从而使细晶粒长大,改变了催化剂的结构,导致活性下降。
6.2催化剂的保护①催化剂升温还原之前应控制速度为30-50℃/h。
防止产生平面温差。
还原出水期间要缓慢升温,防止温度升得太快,防止晶粒长大降低活性。
②新还原的催化剂要保持一段时间的低负荷使未还原的部分继续还原。
③触媒用于生产期间,应稳定操作,使热温度波动在10度以下。
④合成系统停车检修时,升降温速度30-50℃/h。
⑤停车后,合成塔要保持正压,关死进出口阀及副阀,开车时,要将管道内空气用氮气置换合格。
6.3气固相催化反应机理①气体反应物扩散到催化剂外表面②反应物扩散到催化剂的内表面③气体被催化剂表面活性吸附④在催化剂表面上反应,生成氨⑤产物自催化剂表面解吸⑥产物自内表面向外扩散⑦产物自催化剂外表面扩散到气相气相中气相中气相中N2(气相)→N2(吸附)—→2NH(吸附)—→2NH2(吸附)—→2NH(吸附)—→NH3(气相)H2H2H26.4 工艺条件的选择(1)根据触媒的型号及不同的使用时期控制较适宜的反应温度。
(2)根据设备的材质及动力消耗选择适宜的操作压力,30MPa左右对氨合成比较有利。
(3)根据触媒层的温度及管道尺寸选择适宜的空间速度。
(4)氨含量接近平衡时,最佳氢氮比趋近3:1。
同时氮在氨中的溶解度比氢大,溶解于液氨中损失多于氢,因此在生产控制入塔氢氮比低于3:1,一般为2.8-2.9:1第二章工艺流程与工艺指标第一节工艺流程1 工艺流程简述:1.11#合成工艺流程由压缩机七段(六段)出口总管送来的铜洗精炼气经导入阀送入氨冷器出口管,与循环气混合后,进入冷凝塔底部分离套筒内,分离气体中的液氨与油水后进入上部换热器管间,与管内来自水冷排的热气体换热后去循环机加压,气体自循环机出来后进入油分,分离掉油水后气体分四路进入合成塔(一路主线、一路冷副、二路冷激),主线气体由合成塔顶部一次入口进入合成塔内外筒间的环隙,换热后从一次出口出塔,进入气气换热器管间,和管内气体换热后从合成塔二次入口进入塔内下部换热器,与催化剂层来的反应气体换热提温后经中心管进入催化剂层反应,反应后的气体自塔二次出口进入废热锅炉管内。
与废锅内的软水换热,使软水汽化,副产的饱和蒸汽,供变换使用,从废锅出来的混合气体进入软水加热器进行换热,换热后的热软水供铜洗再生使用,出水加热器的气体再进入气气换热器管内,和合成塔一出气体换热。
换热后自换热器底部出,进入水冷却器冷却降温,出冷却器的气体再进入冷凝塔上部换热器管内进一步冷却后进入氨分,分离掉部分液氨,其后气体再进入氨冷器进一步冷却降温,出氨冷器后的循环气和补入的新鲜气混合后一同进入冷凝塔分离液氨,并洗除油水后送循环机加压进行下一个循环,不断产生液氨。
本流程中塔后放空设在氨分离器后,放空气体送提氢岗位回收氢。
氨分和冷交换器分离出来的液氨,放入液氨贮槽。
液氨贮槽的液氨分别再输送到尿素车间生产氨及有关岗位,或送氨冷器做冷冻剂使用,各个氨冷器蒸发后的气氨送至冷冻岗位重新液化成液氨后循环使用。
1.22#合成工艺流程由压缩六段.七段送来合格的精练气经导入阀与氨冷器出口的循环气混合后进入超虑的上部,液氨被分离下来,分离后气体从顶部出来进入冷凝塔底部氨分离套筒内,分离气体中的液氨,油水后进入上部换热气器的管间,与管内冷排来的热气体换热后从上部出来进入循环机,气体经循环机加压后进入油分离器,分离掉油水后的气体分两路进入合成塔(一路线.一路冷副)主线从上部进入沿内外筒环隙顺流而下进入螺旋板换热器板间,从下部螺旋板换热器板间出来进入上部列管换热器的管间,换热后的气体与冷副管来的气体混合进入分器盒,气体被分配到三套管的内管,从外冷管进入集器盒,提温后的气体经中心进入触媒反应,反应后的气体经上部列管内出来进入废锅的管内,气体从废锅出来从二进进入下部螺旋板换热器的板内,经降温后的气体从二出出来进入水冷排下部,气体在冷排被水降温后由上部出来进入冷交上部,气体经换热后从塔顶部出来进入氨分的上部,气体中的氨进一部分离后从顶部出来进入氨冷器的上部,气体在氨冷器降温,气体从底部出来与导入来的气体混合进行下一步的循环.放空气去提氢岗位.2 工艺流程图第二节工艺指标催化剂热点温度:445-500℃(根据催化剂活性情况调整, A±5℃)成品氨的纯度:≥99.6%循环气中入口甲烷:10-14%循环气中入口氨含量:≤3.5%1#合成塔压差:≤1.0MPa2#合成塔压差:≤2.0MPa废锅炉水碱度:≤10mgN/L废锅炉水氯根:≤30 mgN/L循环机出口压力:≤32.0MPa系统压力:≤31.0MPa系统压差:≤2.5MPa循环机油压:0.3-0.6 MPa循环机填料加氨:0.3-0.4MPa1#合成废锅压力:≤1.4MPa2#合成废锅压力:≤1.3MPa中间槽压力:≤2.1 MPa系统升压速率≤0.5MP/分氨冷器气氨压力:≤0.3MPa合成塔塔壁上部温度:≤100℃合成塔塔壁中下部温度:≤150℃水冷温度:≤50℃氨冷温度:-5-5℃废热锅炉液位:1/2~2/3中间槽液位:10-30吨冷交液位:0-50循环机曲轴箱液位:1/2-2/3电炉绝缘电阻值:≥0.2兆欧催化剂同平面温差:≤30℃运行中电机绝缘: >0.5兆欧注油量:20-30滴/分保护气温度:5-20℃保护气流量:500-800m3/h轴承温度:<75℃定子温度:<120℃透平机电流:<1150A透平机功率:<680KWh循环气入口温度:<40℃循环氢:>60%轴承运行时间:2880小时功率记录仪指示无突跳.轴承定子运行温度记录平稳透平机进出口压差:≤3.0Mpa第三章主要设备构造及设备一览表第一节主要设备构造1 1#氨合成塔(1)构造合成塔由高压外筒和内件两部分组成:主要有触媒筐、菱形分布器、层间换热器、下部换热器、电加热器组成。