压圈零件的冲压工艺分析与模具设计说明书(打印.莫星星)
冲压工艺及模具设计课程设计说明书

冲压工艺及模具设计课程设计说明书The Standardization Office was revised on the afternoon of December 13, 2020《冲压工艺与模具设计》课程设计设计题目外壳底孔冲压单工序模设计系别 ____机械系__专业班级 __09机械一班学生姓名 ___龚康康___学号 __0指导教师 ___张保丰_目录一、零件说明。
3二、零件工艺性分析。
41、材料分析。
42、结构分析。
43、精度分析。
4三、工艺方案确定。
4四、压力中心计算。
5五、冲裁力、卸料力、推件力、顶件力及总压力的计算。
5六、冲裁凸凹模刃口尺寸计算。
6七、其他主要零件的设计。
71、凹模设计。
72、凸模设计。
83、模架的选择。
94、卸料板的设计。
105、垫板的设计。
116、定位板的设计。
127、凸模固定板的设计。
128、弹簧的选用。
13八、压力机的选择。
13九、模柄的选用。
14十、紧固零件的选择。
14十一、各零部件的材料及要求。
15十二、该模具设计的优缺点。
15十三、心得体会。
15十四、参考文献。
17一、零件说明制件如下图所示:该制件名称为柴油滤清器外壳,其技术要求为:1,未注尺寸公差按GB/T15505的m级;2,毛刺小于;3,质件要求平整,不允许有拉裂、起皱的现象;4,中批量生产;材料:08F,t=1.5mm设计任务:冲出滤清器外壳底部的孔。
二、零件工艺性分析1、材料分析(摘自GB/T 699-1999)该制件材料为08F,属于优质碳素结构钢,强度、硬度低,塑性极好,深冲压、深拉延性好,冷加工性、焊接性好。
成分偏析倾向大,时效敏感性大,故冷加工时,可采用消除应力热处理或水韧处理,防止冷加工断裂。
化学成分(%):C:~,Si≦,Mn:~,Cr≦, Ni≦,Ca≦为270~340MP a,抗拉强度σb不小于300MP a,屈服力学性能:抗剪强度b强度σs为180MP a,断面收缩率60%,伸长率不小于35%。
冲压模具课程设计说明书(圆筒类)

冲压模具课程设计说明书学校:XXXXXX系别:XXXXXX专业:模具设计与制造学号:XXXXXXXXXX姓名:XX目录1、引言1.1零件设计任务1.2零件图2、冲裁件的工艺分析2.1工件材料2.2工件结构形状2.3工件的尺寸精度2.4确定工艺方案3、冲压模具总体设计3.1模具类型3.2操作与定位方式3.3卸料及出件方式4、冲压模具工艺及设计计算4.1排样设计及计算4.1.1零件展开尺寸计算4.1.2.各部分工作尺寸4.2设备选择5、总装图6、结论7、参考文献1、引言冲模在冲压中至关重要,没有符合要求的冲模,批量冲压生产就难以实现;没有先进的冲模,先进的冲压工艺也无法实现。
冲压工艺与模具,冲压设备与冲压材料构成冲压加工的三大要素,只有他们结合才能得出冲压件。
与机械加工及塑性加工的其他方法相比,冲压加工无论在技术方面还是经济方面都具有独特的优点,主要表现如下:(1)冲压加工的生产效率高,操作方便,易于实现机械化和自动化。
这是因为冲压是依靠冲模及冲压设备完成加工的,普通压力机的行程次数为每分钟几十次,高速压力要每分钟达数百次甚至上千次以上,而且每次冲压行程就可以得到一个冲压件。
(2)冲压时由于模具保证了冲压件的尺寸及形状精度,一般不破坏冲压件的表面质量,且模具寿命一般比较长,所以冲压的质量很稳定,互换性好,具有“一模一样”的特性。
(3)冲压可加工出尺寸范围较大、形状较复杂的零件,如小到钟表的秒表,大到汽车纵梁,覆盖件等,加上冲压时材料的冷变形硬化效应,冲压的强度和硬度都较高。
(4)冲压一般没有切削碎屑生成,材料的消耗较少,且不需要加热设备,所以是一种节省材料,节能的加工方法,冲压件的成本较低。
但是,冲压加工时模具一般具有专用性,又是一个复杂零件需要数套模具才能加工成形,且模具制造的精度高,技术要求高,是技术密集型产品。
所以,只有在冲压件生产批量较大的情况下,冲压加工的有点才能充分得到体现,从而获得较好的经济效益。
冲压成形工艺及模具设计课设说明书
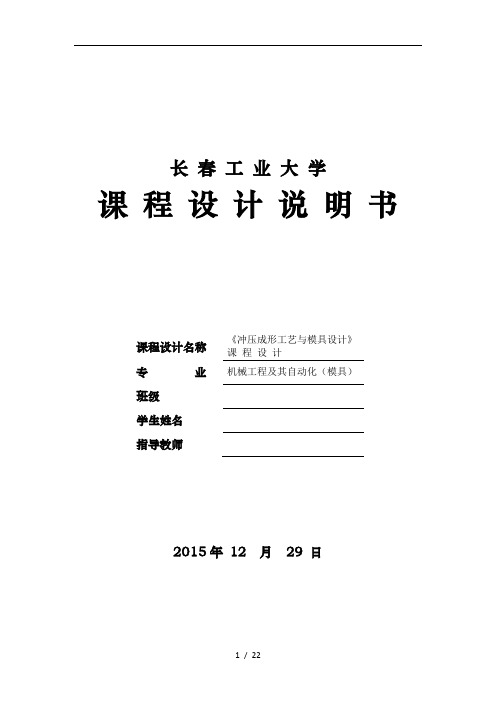
长春工业大学课程设计说明书课程设计名称《冲压成形工艺与模具设计》课程设计专业机械工程及其自动化(模具)班级学生姓名指导教师2015年12 月29 日目录1、设计目的、任务32、工艺分析42.1零件功能42.2尺寸及精度42.3结构分析42.4材料分析42.5工艺分析42.6拟定工艺方案52.7模具的结构形式分析53、排样与搭边设计64、工艺力计算74.1冲裁力74.2卸料力74.3推件力74.4冲压工艺力总和75、压力机的选择86、工序工艺尺寸计算97、压力中心计算108、冲模设计108.1、凸凹模设计118.2模架的选择138.3卸料板的设计148.4凸模固定板的设计158.5紧固零件的选择158.6弹簧的选用--------------------------------------------------------------------------------------169、模具装配179.1 冲模装配的技术要求179.2 冲模的装配方法179.3 冲模的装配工艺过程179.4 冲模的调试199.5 冲模的安装1910、设计总结2111、参考资料221、设计目的、任务课程设计是在学习专业基础课程的基础上,综合运用所学知识,进行模具设计的基本训练过程。
目的是帮助学生具体运用和巩固《冲压工艺与模具设计》课程及相关的理论知识,了解设计冲压模具的一般程序。
使学生能够熟练地运用有关技术资料,如《冷冲模国家标准》、《模具设计与制造简明手册》、《冷冲压模具结构图册》及其它有关规范等。
训练学生初步设计冷冲压模具的能力,为以后的工作打下初步基础。
设计内容为应用所学冲压工艺学和冲模设计知识,结合给定产品零件图纸,设计一套典型的落料冲孔复合模具,并完成相应技术文件。
图1该制件名称为支板,其技术要求为:1.本产品为落料冲孔件,材料为20钢,厚度为0.8mm;2.工件对公差要求不高,未注尺寸公差按IT14级制造;3.工件外观必须平顺,毛边物等均需去除;4.大批量生产。
垫圈冲压模具设计和零word文档
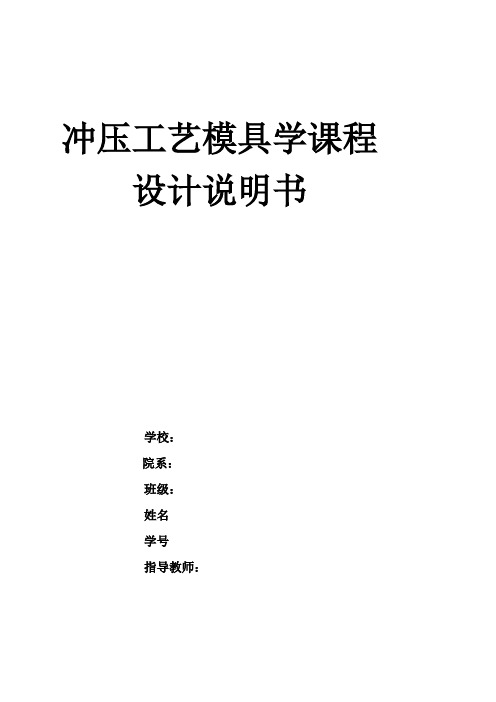
冲压工艺模具学课程设计说明书学校:院系:班级:姓名学号指导教师:《冲压工艺模具学实训》说明书摘要本次的课程设计是一个简单的防滑垫圈及其复合模设计,此副模具是采用落料—冲孔两道工序相结合的复合模,本人经查阅相关书籍、资料以及对设计此副模具所要用到的相关公式、数据作出了一个准确的依据。
本次课程设计一共分为两部分,和其他模具的设计一样,第一部是对零件进行工艺分析,接着对工艺方案进行比较,最终确定选用复合模加工制件的工艺方案。
然后画工序图、排样图以及对材料利用率的计算,计算冲压力,选择冲压机。
然后填写冲压工艺规程卡。
第二部分是冲压模具的设计,选择冲模类型以及结构形式,定位方式,卸料方式,模具设计计算(主要计算各类主要零件的外形尺寸),最后确定凸凹模工作部分尺寸。
关键词:垫圈落料冲孔前言在现代工业生产中,模具是重要的工艺装备之一,它在铸造、锻造、冲压橡胶等生产行业中得到了广泛应用。
由于采用模具进行生产能够提高生产效率,节约原材料,降低成本,并可保证一定的加工质量要求。
所以,汽车、飞机、拖拉机、电器、仪表、玩具等的零部件很多采用模具来加工。
随着科学技术的发展,产品的更新换代加快,对产品质量外观不断提出新要求,对模具质量要求也越来越高。
模具的设计、制造工业部门肩负着为相关企业和部门提供产品的重任。
如果模具设计及制造水平落后,产品质量低劣,制造周期长,必将影响产品的更新换代,使产品失去竞争能力,阻碍生产和经济的发展。
因此,模具设计及制造技术在国民经济中的地位是显而易见的。
金属板料冲压是模具在工业生产中应用广泛的加工形式之一,随着市场竞争日趋加剧,产品质量不断提高,对生产的安全性,操作的方便性等要求也日益提高。
模具作为冲压生产的基本要素,其设计制造技术受到普遍重视。
因此学习模具课程,进行模具设计也是适应现代化工业要求的。
这次课程设计的内容是利用CAD等系列软件设计材料为H62-M的黄铜垫圈冲压模具,说明书有四部分内容,叙述了整个设计的过程。
冲压模具设计书
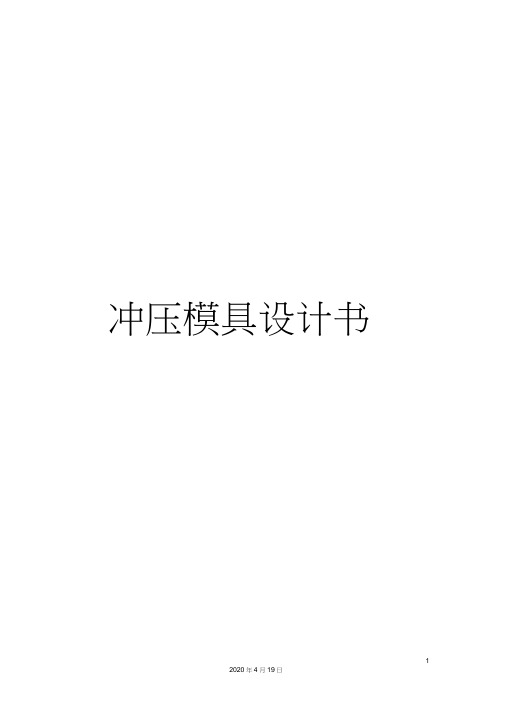
冲压模具设计书文档仅供参考冲压模具设计书班级学号姓名同心圆垫片冲压模具设计目录一.冲压件1.1. 冲压件零件图二.零件的工艺性分析2.1. 零件的工艺性分析2.2.冲裁件的精度和粗糙度2.3. 确定工艺方案三.冲压模具总体结构设计2.1. 模具类型2.2. 操作及定位方式2.3. 卸料及出料方式2.4. 模架类型及精度四.冲压模具工艺及计算4.1. 排样设计及条料宽度计算4.2.设计冲裁压力及压力中心,初选压力机五.冲裁模间隙的分析及确定5.1. 冲裁模间隙的分析5.2. 冲裁模间隙的确定六.凸凹模刃口尺寸的计算6.1. 刃口尺寸的计算的基本原则6.2.刃口尺寸的计算6.2.1 凸凹模的刃口尺寸计算七.主要零部件的设计7.1. 工作零件设计及计算7.2.模架及其与它零件的设计一.冲压件2.1.零件工艺性分析该零件只有冲孔落料两个工序,材料为15钢,强度极限为450MPa,具有良好的冲压性能,适合普通冲裁。
该零件冲孔及落料的尺寸均满足冲裁要求22冲裁件的精度和粗糙度按零件的尺寸公差查公差表得零件的冲裁精度不超过IT11,故冲孔的精度为IT11,落料的精度为IT12,均满足普通冲裁要求。
23确定工艺方案以上分析可得,有冲孔落料两道工序,结构简单,可采用两工位连续冲裁,可选择级进模或复合模。
三.冲压模具总体结构设计2.1.模具类型复合模和级进模均只需要一副模具,可是复合模结构相对复杂,设计难度较大,而级进模的结构简单,更容易设计和制作,故选级进模。
22操作及定位方式。
推荐-旋转座圈零件冲压工艺及模具设计说明书 精品

目录摘要 (1)Abstract (2)第一章绪论 (3)1.1 冲压模具发展方面 (3)1.2 冲压工艺方面 (5)第二章汽油机旋转座圈 (6)2.1 汽油机旋转座圈 (6)第三章汽油机旋转座圈-外罩 (7)3.1 旋转座圈外罩工艺性分析 (8)3.2 合理方案的选择 (9)第四章外罩落料拉深模的设计与计算 (9)4.1 排样设计 (9)4.2 冲压力计算 (10)4.3 压力中心 (11)4.4 工件零件尺寸计算 (11)4.5 冲床选用 (14)4.6 模具结构零件尺寸 (15)4.7 落料拉深模及落料拉深后的半成品 (20)第五章外罩冲孔模的设计与计算 (21)5.1 工件冲压力的计算 (22)5.2 冲底孔模工作零件尺寸计算 (22)5.3 压力机的选择 (23)5.4 模具零件结构尺寸 (24)5.5 外罩冲底孔模及冲孔后的产品 (25)第六章外罩整形模的设计与计算 (26)6.2 模具尺寸的确定 (26)6.3 外罩整形模冲床的选用及弹簧的选用 (27)6.4 模具零件结构尺寸 (28)6.5 整形模的装配图及整形后的产品图 (29)第七章汽油机旋转座圈-内圈 (30)7.1 旋转座圈内圈工艺性分析 (30)7.2 分析比较和确定工艺方案 (32)第八章内圈落料拉深模的设计与计算 (34)8.1 排样设计 (34)8.2 冲压力计算 (35)8.3 压力中心 (36)8.4 工件零件尺寸计算 (36)8.5 冲床选用 (38)8.6 模具结构零件尺寸 (39)8.7 内圈落料拉深模及落料拉深后的半成品 (40)第九章内圈二次拉深兼整形模的设计与计算 (41)9.1 拉深力与整形力的计算 (41)9.2 模具尺寸的确定 (41)9.3 拉深兼整形模冲床的选用及弹簧的计算 (44)9.4 模具零件结构尺寸 (45)9.5 二次拉深兼整形模及成形后的半成品 (46)第十章内圈挤压模的设计与计算 (47)10.1 工件挤压力的计算 (47)10.2 挤压模工作零件尺寸计算 (47)10.3 压力机的选择及弹簧的计算 (48)10.4 模具零件结构尺寸 (49)10.5 挤压模及挤压后的半成品 (50)第十一章内圈冲底孔模及切边模的设计与计算 (51)11.2 冲底孔模工作零件尺寸计算 (51)11.3 压力机的选择和弹簧的计算 (53)11.4 模具零件结构尺寸 (54)11.5 冲底孔模及冲孔后的产品 (56)11.6 切边模及切边后的产品 (57)结束语 (58)参考文献 (59)摘要随着全球经济的发展,新的技术革命不断取得新的进展和突破,技术的飞跃发展已经成为推动世界经济增长的重要因素。
冲压工艺课程设计说明书
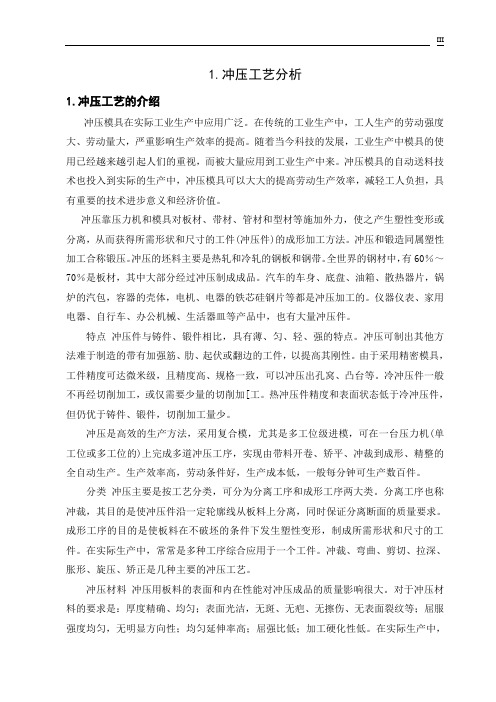
III1.冲压工艺分析1.冲压工艺的介绍冲压模具在实际工业生产中应用广泛。
在传统的工业生产中,工人生产的劳动强度大、劳动量大,严重影响生产效率的提高。
随着当今科技的发展,工业生产中模具的使用已经越来越引起人们的重视,而被大量应用到工业生产中来。
冲压模具的自动送料技术也投入到实际的生产中,冲压模具可以大大的提高劳动生产效率,减轻工人负担,具有重要的技术进步意义和经济价值。
冲压靠压力机和模具对板材、带材、管材和型材等施加外力,使之产生塑性变形或分离,从而获得所需形状和尺寸的工件(冲压件)的成形加工方法。
冲压和锻造同属塑性加工合称锻压。
冲压的坯料主要是热轧和冷轧的钢板和钢带。
全世界的钢材中,有60%~70%是板材,其中大部分经过冲压制成成品。
汽车的车身、底盘、油箱、散热器片,锅炉的汽包,容器的壳体,电机、电器的铁芯硅钢片等都是冲压加工的。
仪器仪表、家用电器、自行车、办公机械、生活器皿等产品中,也有大量冲压件。
特点冲压件与铸件、锻件相比,具有薄、匀、轻、强的特点。
冲压可制出其他方法难于制造的带有加强筋、肋、起伏或翻边的工件,以提高其刚性。
由于采用精密模具,工件精度可达微米级,且精度高、规格一致,可以冲压出孔窝、凸台等。
冷冲压件一般不再经切削加工,或仅需要少量的切削加[工。
热冲压件精度和表面状态低于冷冲压件,但仍优于铸件、锻件,切削加工量少。
冲压是高效的生产方法,采用复合模,尤其是多工位级进模,可在一台压力机(单工位或多工位的)上完成多道冲压工序,实现由带料开卷、矫平、冲裁到成形、精整的全自动生产。
生产效率高,劳动条件好,生产成本低,一般每分钟可生产数百件。
分类冲压主要是按工艺分类,可分为分离工序和成形工序两大类。
分离工序也称冲裁,其目的是使冲压件沿一定轮廓线从板料上分离,同时保证分离断面的质量要求。
成形工序的目的是使板料在不破坯的条件下发生塑性变形,制成所需形状和尺寸的工件。
在实际生产中,常常是多种工序综合应用于一个工件。
冲压模具成型工艺与模具设计说明书

冲压模具成型工艺及模具设计说明书设计课题:工件如下图所示,材料Q235,板料厚度1mm,年产量8万件,表面不允许有明显的划痕。
设计成型零件的模具。
一、冲压工艺分析1、该零件的材料是Q235,是普通的碳素工具钢,板厚为1mm,具有良好的可冲压性能。
2、该零件结构简单,并在转角处有R1的圆角,所冲的两个孔都是Φ8的尺寸,工艺性比较好,整个工件的结构工艺性好。
3、尺寸精度,零件上的两个孔的尺寸精度为IT12~13级,两个孔的位置精度是IT11~12级,其余尺寸的公差为IT12~14,精度比较低。
结论:适合冲压生产。
二、工艺方案确定该工件包括落料、冲孔两个基本工序,有以下3种工艺方案:方案一:先落料,后冲孔。
采用单工序模具生产。
方案二:落料—冲孔复合冲压,采用复合模生产。
方案三:冲孔—落料级进冲压,采用级进模生产。
方案一模具结构简单,但需要两道工序两幅模具,成本高而生产率低,难以满足中批量生产需求。
方案二只需一副模具,工件精度及生产效率都较高。
方案三也只需要一副模具,生产效率高,操作方便,但位置精度不如复合模具冲裁精度高。
通过对上述三种方案的分析比较,成型该零件应该采用方案二复合模具成型。
三、确定模具类型及结构形式1、该零件质量要求不高,板的厚度有1mm, 孔边距有14mm,所以可以选用倒装复合模。
2、定位方式的选择:控制条料的送进方向采用两个导料销,控制条料的送进步距采用挡料销。
3、卸料、出件方式的选择:采用弹性卸料。
下出件,上模刚性顶件。
4、导向方式的选择:为了方便操作,该模具采用后侧导柱的导向方式。
冲压件的形状简单、精度要求不高、生产批量为中批量,为了使得模具寿命较高,采用有导向、弹性卸料、下出件的模具结构形式。
四、工艺计算1、确定最佳排样方式,并计算材料利用率,选择板料规格。
该零件为近似矩形零件,设计排样1、排样2两种排样方式,如图:排样1排样2查《冲压手册》表2-18,最小搭边值是:工件间:1.2mm、侧边:1.5mm。
压圈冲压模具设计说明书(终极版)2

第1章绪论1.1冲压工艺概述1.1.1 冲压工艺简介冲压是塑性加工的基本方法之一,它是利用安装在压力机上的模具,在室温下对材料施加压力使其产生变形或分离,从而获得具有一定形状、尺寸和精度的制件的一种压力加工方法。
因为它主要用于加工板料制件,所以也称板料冲压。
在机械制造中是一种高效率的加工方式。
冲压广泛应用于金属制品各行业中,尤其在汽车、仪表、军工、家用电器等工业中占有极其重要的地位。
冲压工艺有如下特点:1.能冲压出其它加工方法难以加工或无法加工的形状复杂的零件。
比如,从仪器仪表小型零件到汽车覆盖件、纵梁等大型零件,均由冲压加工完成。
2.冲压件质量稳定,尺寸精度高。
由于冲压加工是有模具成型,模具制造精度高、使用寿命长,故冲压件质量稳定,制件互换性好。
尺寸精度一般可达IT10~IT14级,最高可达到IT6级,有的制件不需要在加工,便可满足装配和使用要求。
3.冲压件具有重量轻、强度高、刚性好和表面粗糙度小等特点。
4.冲压加工生产效率极高,没有其它任何一种机械加工方法能与之相比。
比如,汽车覆盖件这样的大型冲压件的生产效率,可达每分钟数件;高速冲压小型制件,可达每分钟上千件。
5.材料利用率高,一般为70%~85%。
因此冲压件能实现少废料或无废料生产。
在某些情况下,边角余料也可充分利用。
6.操作简单,便于组织生产,易于实现机械化和自动化生产。
对操作工人的技术素质要求不高,新工人经短时培训便能上岗操作。
7.冲压的特点是模具制造时间长、制造成本高,故不适宜于单件小批量生产。
另外,冲压生产多采用机械压力机,由于滑块往复运动快,手工操作时,劳动强度大,易发生事故,故必须特别重视安全生产、安全管理以及采取必要的安全技术措施。
8.冲压模设计需要有很强的想象力与创造力,对于模具的设计者和制造者无论在理论、经验、创造力方面都要有很高的要求。
1.1.2 冲压模具的发展近年来,我国冲压模具水平已有很大提高。
大型冲压模具已能生产单套重量达50多吨的模具。
冲压工艺和模具设计课程设计任务书
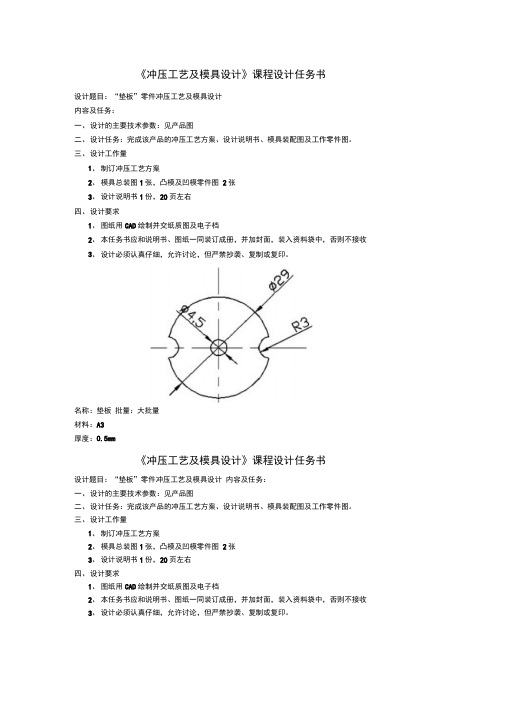
《冲压工艺及模具设计》课程设计任务书设计题目:“垫板”零件冲压工艺及模具设计内容及任务:一、设计的主要技术参数:见产品图二、设计任务:完成该产品的冲压工艺方案、设计说明书、模具装配图及工作零件图。
三、设计工作量1、制订冲压工艺方案2、模具总装图1张,凸模及凹模零件图2张3、设计说明书1份,20页左右四、设计要求1、图纸用CAD绘制并交纸质图及电子档2、本任务书应和说明书、图纸一同装订成册,并加封面,装入资料袋中,否则不接收3、设计必须认真仔细,允许讨论,但严禁抄袭、复制或复印。
名称:垫板批量:大批量材料:A3厚度:0.5mm《冲压工艺及模具设计》课程设计任务书设计题目:“垫板”零件冲压工艺及模具设计内容及任务:一、设计的主要技术参数:见产品图二、设计任务:完成该产品的冲压工艺方案、设计说明书、模具装配图及工作零件图。
三、设计工作量1、制订冲压工艺方案2、模具总装图1张,凸模及凹模零件图2张3、设计说明书1份,20页左右四、设计要求1、图纸用CAD绘制并交纸质图及电子档2、本任务书应和说明书、图纸一同装订成册,并加封面,装入资料袋中,否则不接收3、设计必须认真仔细,允许讨论,但严禁抄袭、复制或复印。
名称:垫板批量:大批量材料:QS n 6.5-0.1厚度:0.3mm《冲压工艺及模具设计》课程设计任务书设计题目:“垫板”零件冲压工艺及模具设计内容及任务:一、设计的主要技术参数:见产品图二、设计任务:完成该产品的冲压工艺方案、设计说明书、模具装配图及工作零件图。
三、设计工作量1、制订冲压工艺方案2、模具总装图1张,凸模及凹模零件图2张3、设计说明书1份,20页左右四、设计要求1、图纸用CAD绘制并交纸质图及电子档2、本任务书应和说明书、图纸一同装订成册,并加封面,装入资料袋中,否则不接收3、设计必须认真仔细,允许讨论,但严禁抄袭、复制或复印。
《冲压工艺及模具设计》课程设计任务书设计题目:“垫片”零件冲压工艺及模具设计内容及任务:一、 设计的主要技术参数:见产品图二、 设计任务:完成该产品的冲压工艺方案、设计说明书、模具装配图及工作零件图。
压圈冲压模具设计说明书终极版

第1章绪论冲压工艺概述冲压工艺简介冲压是塑性加工的基本方法之一,它是利用安装在压力机上的模具,在室温下对材料施加压力使其产生变形或分离,从而获得具有一定形状、尺寸和精度的制件的一种压力加工方法。
因为它主要用于加工板料制件,所以也称板料冲压。
在机械制造中是一种高效率的加工方式。
冲压广泛应用于金属制品各行业中,尤其在汽车、仪表、军工、家用电器等工业中占有极其重要的地位。
冲压工艺有如下特点:1.能冲压出其它加工方法难以加工或无法加工的形状复杂的零件。
比如,从仪器仪表小型零件到汽车覆盖件、纵梁等大型零件,均由冲压加工完成。
2.冲压件质量稳定,尺寸精度高。
由于冲压加工是有模具成型,模具制造精度高、使用寿命长,故冲压件质量稳定,制件互换性好。
尺寸精度一般可达IT10~IT14级,最高可达到IT6级,有的制件不需要在加工,便可满足装配和使用要求。
3.冲压件具有重量轻、强度高、刚性好和表面粗糙度小等特点。
4.冲压加工生产效率极高,没有其它任何一种机械加工方法能与之相比。
比如,汽车覆盖件这样的大型冲压件的生产效率,可达每分钟数件;高速冲压小型制件,可达每分钟上千件。
5.材料利用率高,一般为70%~85%。
因此冲压件能实现少废料或无废料生产。
在某些情况下,边角余料也可充分利用。
6.操作简单,便于组织生产,易于实现机械化和自动化生产。
对操作工人的技术素质要求不高,新工人经短时培训便能上岗操作。
7.冲压的特点是模具制造时间长、制造成本高,故不适宜于单件小批量生产。
另外,冲压生产多采用机械压力机,由于滑块往复运动快,手工操作时,劳动强度大,易发生事故,故必须特别重视安全生产、安全管理以及采取必要的安全技术措施。
8.冲压模设计需要有很强的想象力与创造力,对于模具的设计者和制造者无论在理论、经验、创造力方面都要有很高的要求。
冲压模具的发展近年来,我国冲压模具水平已有很大提高。
大型冲压模具已能生产单套重量达50多吨的模具。
为中档轿车配套的覆盖件模具内也能生产了。
- 1、下载文档前请自行甄别文档内容的完整性,平台不提供额外的编辑、内容补充、找答案等附加服务。
- 2、"仅部分预览"的文档,不可在线预览部分如存在完整性等问题,可反馈申请退款(可完整预览的文档不适用该条件!)。
- 3、如文档侵犯您的权益,请联系客服反馈,我们会尽快为您处理(人工客服工作时间:9:00-18:30)。
第1章.冲压零件的工艺性分析该零件形状简单、对称,是由圆弧和直线组成的。
冲裁件内外形所能达到的经济精度为IT13~IT14。
凡产品图样上没有标注公差等级或者公差的尺寸,其极限偏差数值通常按IT14级处理。
将以上精度与零件的精度要求相比较,可以为该零件的精度要求能够在冲裁加工中得到保证,其他尺寸标注、生产批量等情况,也均符合冲裁的工艺要求,故决定采用冲压方式进行加工。
经查公差表,各尺寸公差为:φ60-00.62mm φ32+0.52mm 35+0.52mm 6+0.3mm第2章.确定工艺方案及模具结构形式该工件所需的冲压工序包括落料、冲孔两个基本工序,可以拟定出以下三种工艺方案:方案一:先落料,后冲孔,采用单工序模分两次加工。
方案二:落料-冲孔复合冲压,采用复合模加工。
方案三:落料-冲孔级进冲压,采用级进模加工。
方案一模具结构简单,但需两道工序两副模具,成本高而生产效率低,难以满足顾客的要求,而且工件的累积误差大,操作不方便。
由于该工件大批量生产,所以方案二和方案三更具优越性。
·该零件φ32mm×35mm的孔与φ60mm的最小距离为25mm,大于此零件要求的最小壁厚(1.2mm),可以采用冲孔、落料复合模或冲孔、落料级进模,复合模模具的形位精度和尺寸精度容易保证,且生产率也高,尽管模具结构比较复杂,但由于零件的几何形状简单对称,模具制造并不困难。
级进模虽生产率也高,但零件的冲裁精度稍差,欲保证冲压件的形位精度,需要在模具上设置导正销导正,故模具制造、安装较复合模复杂。
通过对上述三种方案的分析比较,该零件的冲压生产采用方案二的复合模为佳。
第3章.模具设计计算3.1排样方式的确定及其计算设计复合模时,首先要设计条料的排样图,因该零件外形为圆形,可采用有废料排样的直排比较合适。
参考《冲压工艺与模具设计》表2.8确定其排样方式为直排画出排样图排样图由于R=30﹥2×2查表2.9最小搭边值可知:最小工艺搭边值a(侧面)=1.5mma 1(工件间)=1.2mm 分别取a=2㎜ a1=2㎜计算条料的宽度:B=60+2×2=64mm步距:S=60+2=62mm材料利用率的计算:计算冲压件毛坯的面积:A=π×R2 =π×302 =2826mm 2一个步距的材料利用率:η=%100BSnA=2826/(64×62)=61.21﹪3.2计算凸、凹模刃口尺寸查《冲压工艺与模具设计》书中表2.4得间隙值Zmin=0.246mm,Zmax=0.360mm。
1)冲孔φ32mm ×35mm 凸、凹模刃口尺寸的计算由于制件结构简单,精度要求不高,所以采用凹模和凸模分开加工的方法制作凸、凹模。
其凸、凹模刃口尺寸计算如下:查《冲压工艺与模具设计》书中表2.5得φ32mm 凸、凹模制造公差: δ凸 =0.020mm δ凹 =0.025mm 校核: Z max -Z min =(0.360-0.246)㎜=0.114mm 而δ凸+δ凹 =(0.020+0.025)㎜=0.045mm 满足 Z max -Z min ≥δ凸+δ凹的条件查《冲压工艺与模具设计》书中表2.6得:IT14级时标准公差△=0.52㎜,因为0.52>0.20所以磨损系数X=0.5,按式(2.5) d 凸=[]X∆+min d =(32+0.5×0.52)-00.020=0020.026.32-mm D 凹=[]min Z d+凸=025.00)246.026.32(++=025.00506.32+mm 查《冲压工艺与模具设计》书中表2.5得2.2mm ×4mm 的矩形凸、凹模制造公差:δ凸 =0.020mm δ凹 =0.020mm δ凸+δ凹 =0.020+0.020=0.040mm 满足 Z max -Z min ≥δ凸+δ凹的条件3.3外形落料凸、凹模刃口尺寸的计算由于外形形状简单,精度要求不高,所以采用凸模和凹模分开加工的方法制作凸、凹模。
其凸、凹模刃口尺寸计算如下:查《冲压工艺与模具设计》书中表2.5得凸、凹模制作公差 δ凸=0.020mm δ凹 =0.030mm 校核:Z max -Z min =0.360-0.246=0.114mm而δT +δA =0.050mm满足 Z max -Z min ≥δ凸+δ凹的条件查《冲压工艺与模具设计》书中表2.6得:IT14级时磨损系数X=0.5,按式(2.5) d凸=[]X∆+mind=64.26-00.020mmd凹=[]minZd+凸=64.506+0.030mm3.4冲压力的计算落料力 F落 = Ltτb=(2πR×2×450)N=169.56KN冲孔力 F冲= Ltτb=(336.9×10π/180+4+2×2.2)×2 ×450=60.453KN冲孔时的推件力F推=n K推F孔由《冲压工艺与模具设计》书中表2.21得h=6mm 则n=h/t=6mm/2=3个查《冲压工艺与模具设计》书中表2.7得K推=0.05F推=n K推F孔=3×0.05×60.453=9.068KN落料时的卸料力 F卸=K卸F落查《冲压工艺与模具设计》书中表2.7取K卸=0.04故 F卸=K卸F落=0.04×169.56=6.7824KN总冲压力为:F总=F落+F孔+F推+F卸=(169.56+60.453+9.068+4.748)KN=243.829KN为了保证冲压力足够,一般冲裁时压力机吨位应比计算的冲F总′=1.3×F总=1.3×243.829=316.9777KN3.5压力中心的计算用解析法求模具的压力中心的坐标,建立如下图所示的坐标系XOY.由图可知工件上下对称,将工件冲裁周边分成L1、L2、L3、L4、L5基本线段,求出各段长度的重心位置:因工件相对x轴对称,所以Yc=0,只需计算XCL 1=2πR=188.4㎜ X1=0L 2=58.77mm X2=-0.68L 3=L5=2.2mm X3=X5=10.9㎜L 4=4mm X4=12㎜将以上数据代入压力中心坐标公式X=(L1 X1+L2X2+…+ L5X5)/ L1+ L2+…+ L5X=[188.4×0+58.77×(-0.68)+2.2×10.9+4×12+2.2×10.9]/(188.4+58.77+2.2+4+22.2)=0.28mm第4章.模具的总体设计根据上述分析,本零件的冲压包括冲压和落料两个工序,且孔边距较大,可采用倒装复合模,可直接利用压力机的打杆装置进行推件,卸料可靠,便于操作。
工件留在落料凹模空洞中,应在凹模孔设置推件块,卡于凸凹模上的废料可由卸料板推出;而冲孔废料则可以在下模座中开设通槽,使废料从空洞中落下。
由于在该模具中压料是由落料凸模与卸料板一起配合工作来实现的,所以卸料板还应有压料的作用,应选用弹性卸料板卸下条料。
因是大批量生产,采用手动送料方式,从前往后送料。
因该零件采用的是倒装复合模,所以直接用挡料销和导料销即可。
为确保零件的质量及稳定性,选用导柱、导套导向。
由于该零件导向尺寸较小,且精度要求不是太高,所以宜采用后侧导柱模架。
第5章.模具主要零部件的结构设计5.1凸模、凹模、凸凹模的结构设计①落料凸、凹模的结构设计在落料凹模内部,由于要放置推件块,所以凹模刃口应采用直筒形刃口,并查《冲压工艺与模具设计》书中表2.21,取得刃口高度h=6mm,该凹模的结构简单,宜采用整体式。
查《冲压工艺与模具设计》书中表2.22,得k=0.40即凹模高度H=ks=0.40×60mm=24mm凹模壁厚C=1.5H=1.5×=36mm凹模外形尺寸的确定:凹模外形长度:L=(30+16×2)㎜=62㎜凹模外形宽度:B=(30+16×2)㎜=62㎜凹模整体尺寸标准化,取为80mm×80mm×40mm凹模的工艺路线为了增加凸模的强度与刚度,凸模固定板厚度取25mm,因凸模比较长,所以选用带肩的台阶式凸模,凸模长度根据结构上需要来确定。
L= h凸模固定板+h落料凹模=(25+24)mm=49mm (取50mm)③凸凹模的结构设计本模具为复合冲裁模,除了冲孔凸模和落料凹模外还有一个凸凹模。
根据整体模具的结构设计需要,凸凹模的结构简图如下图所示:确定凸凹模安排在模架上的位置时,要依据计算的压力中心的数据,使压力中心与模柄中心重合。
校核凸凹模的强度:查《冲压工艺与模具设计》书中表2.23得凸凹模的最小壁厚为4.9mm,而实际最小壁厚为9mm。
故符合强度要求。
凸凹模的刃口尺寸按落料凹模尺寸配制,并保证双间隙为0.246mm~0.360mm.5.2卸料弹簧的设计根据模具的结构初选6根弹簧,每根弹簧的预压力≥F卸/n=(4.75×103/6)N=791.7N根据预压力和模具结构尺寸,初选序号62~67的弹簧,其最大工作负荷F1=1120N >791.7N虽弹簧的最大工作负荷符合要求,但其弹簧太长,会使模具的高度增加,所以选用最大工作负荷为1550N范围内的弹簧。
试选68~72号中69号弹簧,校验弹簧最大许可压缩量Lmax大于弹簧实际总压缩量L总。
69号弹簧的具体参数是:弹簧外径D=45mm,材料直径d=9mm,自由高度H=80mm,节距t=11.5mm,F1=1550N,极限载荷时弹簧高度H1=58.2mm。
弹簧的最大的最大许可压缩量Lmax=(80-58.2)mm=21.8mm弹簧预压缩量L/=LmaxF/F1=791.7×21.8/1550=11.13mm校核:卸料板工作行程t+h1+h2=2+1+0.5=3.5mm凸模刃磨量和调节量 h3=6mm弹簧实际总压缩量L总=L/+t+h1+h2+h3=(11.13+3.5+6)mm =24.23mm由于25.65>24.23,即Lmax >L总,所以所选弹簧是合适的。
69号弹簧规格为:外径: D=50mm钢丝直径: d=9mm自由高度: H=80mm装配高度: H2= H- L/=(90-11.13)=78.87mm弹簧的窝座深度:h= H0-Lmax+ h卸料板+ t +1- h凸凹模- h修模=(90-24.23+14+2+1-58-6)mm=18.77mm弹簧外露高度:H3= H2-h- h卸料板窝深=(78.87-18.77.-10)mm=50.1mm5.3 模具主要零件尺寸 1.模柄2.上模座3.垫板4.凹模5.凸模6.凹模卸料板7.垫板8.下模板9. 凸凹模10.凸模固定板5.4模架的设计模架各零件标记如下:上模座:140mm×140mm×35mm下模座:140mm×140mm×35mm导柱: 116mm×22mm导套:22mm×65mm×33mm模柄:φ42mm×52mm垫板厚度:140mm×140mm×16mm卸料板厚度:140mm×140mm×24mm凸模固定板厚度:140mm×140mm×20mm模具的闭合高度:H闭= h上模座+h垫板+h凸模固定板+h落料凹模+t+ h卸料板+h橡胶垫+h下模座=(25+10+28+24+2+14+50+30)(mm) =183mm第6章.冲压设备的选择6.1压力机类型的选择(1)中、小型冲压件选用开式机械压力机。