粗铜的火法精炼(楚雄)
2023年安全工程师-安全生产专业实务(金属冶炼安全)考试历年高频考点真题摘选附加答案

2023年安全工程师-安全生产专业实务(金属冶炼安全)考试历年高频考点真题摘选附带答案第1卷一.全考点押密题库(共50题)1.(单项选择题)(每题 1.00 分)对于在储煤仓、煤塔进行清理、检修作业的人员,下列劳动防护用品配备错误的是()。
A. 戴安全帽B. 佩戴安全带C. 戴防尘口罩D. 穿化纤工作服正确答案:D,2.(单项选择题)(每题 1.00 分)下列关于精苯加工工艺中安全的控制措施,说法正确的是()。
A. 精苯生产区域宜设高度不低于1.8m的围墙B. 精苯生产区域,不应布置化验室、维修间C. 禁止穿带钉鞋进入精苯生产区域,应穿化纤服、绝缘鞋正确答案:B,3.(单项选择题)(每题 1.00 分)下列关于焦炉推焦、装煤除尘装置的说法,错误的是()。
A. 各个除尘装置应连通,汇集到除尘总干管道B. 应设置阻断烟尘中高温明火颗粒的设施C. 净化装置内部不得存在死角,不得有积尘D. 应采取防静电措施并设置安全泄爆装置正确答案:A,4.(单项选择题)(每题 1.00 分)机械加工厂房内的噪声很大,很容易对作业者的听力造成损害。
为降低噪声危害,企业应优先选用的措施是()。
A. 高噪声车间与低噪声车间应分开布置B. 降低噪声源C. 设置隔声室D. 高噪声设备相对集中,并采取相应的隔声等控制措施正确答案:B,5.(单项选择题)(每题 1.00 分)某大型钢铁企业炼轧厂有3座120t转炉,采取氧气顶吹工艺。
下列关于转炉炼钢安全要求的说法,正确的是( )。
A. 氧气在枪体内最大设计流速不应超过60m/sB. 吹氧期间,氧枪出水温度低于规定值,应提枪停吹C. 转炉吹炼时发现冷却水泄漏,应立即停吹、停水,并将转炉摇至安全位置D. 停吹8h后的转炉,开始生产前应按新炉开炉的要求进行准备正确答案:D,6.(单项选择题)(每题 1.00 分)我国近几年基础设施建设和居民住宅有了长足发展,建(构)筑物多采用钢筋混凝土结构,其中各种A. 型钢轧制B. 棒线材轧制C. 热轧板卷轧制D. 无缝管轧制正确答案:B,7.(单项选择题)(每题 1.00 分)下列关于堆取料机安全控制措施的说法,正确的是()。
11粗铜的火法精炼[66页]
![11粗铜的火法精炼[66页]](https://img.taocdn.com/s3/m/7bcf5dfe7d1cfad6195f312b3169a4517723e561.png)
• 铅可以氧化成PbO与炉底或吹入的SiO2造渣。 • 硫在粗铜中主要以Cu2S形式存在,它在精炼初期
氧化得较缓慢,但在氧化期将结束时,便开始按 [Cu2S]+2[Cu2O]=6[Cu]+ SO2反应剧烈地放出 SO2,使铜水沸腾,有小铜液滴喷溅射出,形成 所谓“铜雨”。
• 为了加速反应,实践中常将氧的浓度提到0.9~ 1.0%,保持熔体中Cu2O为饱和状态。炉气中 SO2浓度应低于0.1%,温度为1200℃,并使炉 内为中性或微氧化性气氛。
• 燃烧室是回转炉的辅助设备,它利用稀释风继续 燃烧回转式精炼炉出来的烟气,烟气温度虽在 1200℃ ,但不起冲刷作用。它选用的耐火材料 是粘土砖、高铝砖、不定形耐火捣打料。
2、回转式精炼炉的主要附属设备
(1)燃烧炉
每台回转炉附设一台燃烧炉。烟气中未燃烧尽物质 继续燃烧,并在燃烧室内通入冷空气,以降低烟 气温度。钢壳内衬耐火砖。和炉体相连处有一个 桃形烟气接口,还有一个排出口,及二个控制清 理口。
• 实践认为,阳极含Ni<0.6%时,不会影响电解精 炼的进行。为此采用了保镍的措施。在工厂实践 中,将含镍不同的铜料进行搭配,使铜料含镍在 0.5%左右,并在还原期将脱氧限度由一般的 0.1%降至0.05%左右。这样绝大部分镍便会以金 属状态留在阳极铜中。
• 砷和锑与铜能形成一系列化合物和镍云母溶入铜 中,这便是砷锑难除的主要原因。可用反复氧化 还原的方法除去砷锑,即将砷锑氧化为As2O3.和 Sb2O3挥发。但此时有一部分砷锑会形成As2O5、 Sb2O5以及砷酸盐和锑酸盐,所以需进行还原, 使砷锑由高价还原为低阶氧化物再挥发除去。也 可用苏打或石灰等碱性熔剂使砷锑形成不溶于铜 中的砷酸盐和锑酸盐造渣除去。还可用石灰和萤 石混合熔剂使砷锑造渣。
安全工程师《金属冶炼安全》复习题集(第23篇)
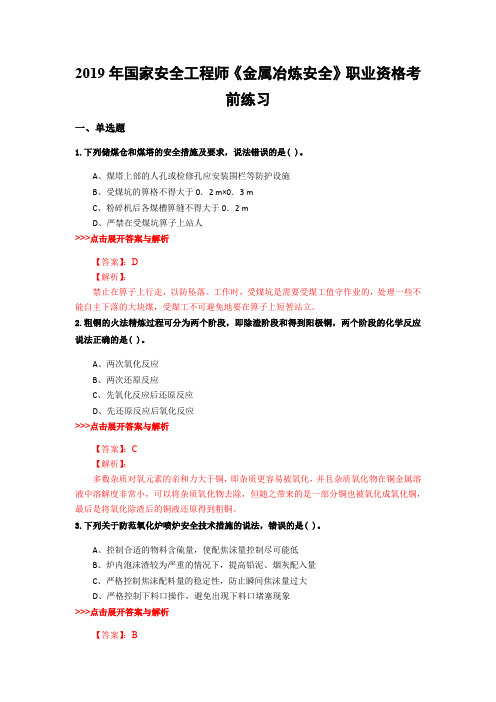
2019年国家安全工程师《金属冶炼安全》职业资格考前练习一、单选题1.下列储煤仓和煤塔的安全措施及要求,说法错误的是( )。
A、煤塔上部的人孔或检修孔应安装围栏等防护设施B、受煤坑的箅格不得大于0.2 m×0.3 mC、粉碎机后各煤槽箅缝不得大于0.2 mD、严禁在受煤坑箅子上站人>>>点击展开答案与解析【答案】:D【解析】:禁止在箅子上行走,以防坠落。
工作时,受煤坑是需要受煤工值守作业的,处理一些不能自主下落的大块煤,受煤工不可避免地要在箅子上短暂站立。
2.粗铜的火法精炼过程可分为两个阶段,即除渣阶段和得到阳极铜,两个阶段的化学反应说法正确的是( )。
A、两次氧化反应B、两次还原反应C、先氧化反应后还原反应D、先还原反应后氧化反应>>>点击展开答案与解析【答案】:C【解析】:多数杂质对氧元素的亲和力大于铜,即杂质更容易被氧化,并且杂质氧化物在铜金属溶液中溶解度非常小,可以将杂质氧化物去除,但随之带来的是一部分铜也被氧化成氧化铜,最后是将氧化除渣后的铜液还原得到粗铜。
3.下列关于防范氧化炉喷炉安全技术措施的说法,错误的是( )。
A、控制合适的物料含硫量,使配焦沫量控制尽可能低B、炉内泡沫渣较为严重的情况下,提高铅泥、烟灰配入量C、严格控制焦沫配料量的稳定性,防止瞬间焦沫量过大D、严格控制下料口操作,避免出现下料口堵塞现象>>>点击展开答案与解析【答案】:B【解析】:控制合适的物料含硫量,使配焦沫量控制尽可能低,可维持炉内热平衡。
在配焦沫量较大,炉内泡沫渣较为严重的情况下,降低铅泥、烟灰配入量,同时降低焦沫配入量。
严格控制焦沫配料量的稳定性,防止瞬间焦沫量过大。
4.下列关于铁水预处理的安全要求,说法错误的是( )。
A、铁水罐内铁水面以上自由空间高度.喷吹法时不应小于500mmB、铁水罐内铁水面以上自由空间高度,机械搅拌法时不应小于700mmC、采用CaC2与镁粉作脱硫剂时,其贮粉仓应采用氮气保护D、CaC2仓附近区域,应设一氧化碳检测和报警装置>>>点击展开答案与解析【答案】:D【解析】:CaC2仓附近区域,应设乙炔检测和报警装置。
粗铜火法精炼技术的发展趋势
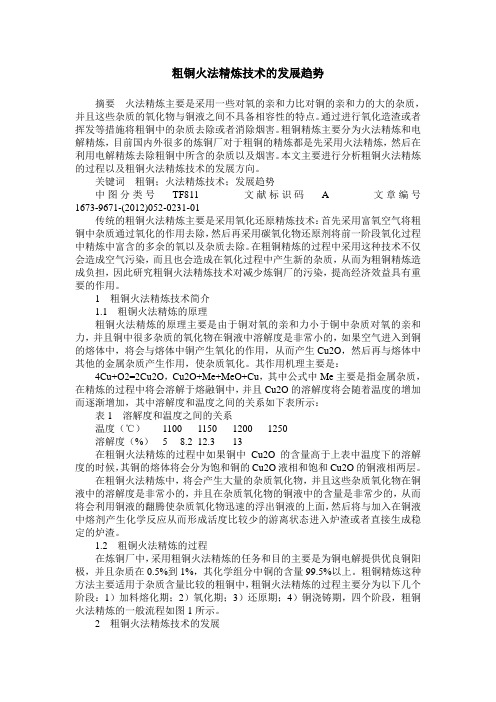
粗铜火法精炼技术的发展趋势摘要火法精炼主要是采用一些对氧的亲和力比对铜的亲和力的大的杂质,并且这些杂质的氧化物与铜液之间不具备相容性的特点。
通过进行氧化造渣或者挥发等措施将粗铜中的杂质去除或者消除烟害。
粗铜精炼主要分为火法精炼和电解精炼,目前国内外很多的炼铜厂对于粗铜的精炼都是先采用火法精炼,然后在利用电解精炼去除粗铜中所含的杂质以及烟害。
本文主要进行分析粗铜火法精炼的过程以及粗铜火法精炼技术的发展方向。
关键词粗铜;火法精炼技术;发展趋势中图分类号TF811 文献标识码 A 文章编号1673-9671-(2012)052-0231-01传统的粗铜火法精炼主要是采用氧化还原精炼技术:首先采用富氧空气将粗铜中杂质通过氧化的作用去除,然后再采用碳氧化物还原剂将前一阶段氧化过程中精炼中富含的多余的氧以及杂质去除。
在粗铜精炼的过程中采用这种技术不仅会造成空气污染,而且也会造成在氧化过程中产生新的杂质,从而为粗铜精炼造成负担,因此研究粗铜火法精炼技术对减少炼铜厂的污染,提高经济效益具有重要的作用。
1 粗铜火法精炼技术简介1.1 粗铜火法精炼的原理粗铜火法精炼的原理主要是由于铜对氧的亲和力小于铜中杂质对氧的亲和力,并且铜中很多杂质的氧化物在铜液中溶解度是非常小的,如果空气进入到铜的熔体中,将会与熔体中铜产生氧化的作用,从而产生Cu2O,然后再与熔体中其他的金属杂质产生作用,使杂质氧化。
其作用机理主要是:4Cu+O2=2Cu2O,Cu2O+Me+MeO+Cu,其中公式中Me主要是指金属杂质,在精炼的过程中将会溶解于熔融铜中,并且Cu2O的溶解度将会随着温度的增加而逐渐增加,其中溶解度和温度之间的关系如下表所示:表1 溶解度和温度之间的关系温度(℃)1100 1150 1200 1250溶解度(%) 5 8.2 12.3 13在粗铜火法精炼的过程中如果铜中Cu2O的含量高于上表中温度下的溶解度的时候,其铜的熔体将会分为饱和铜的Cu2O液相和饱和Cu2O的铜液相两层。
粗铜的火法精炼(楚雄)
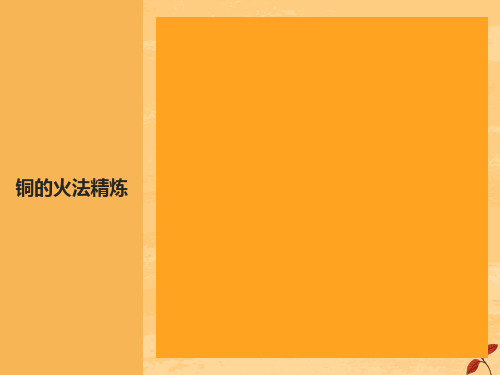
炉子密封性差,散热损失大,烟气泄漏多,车间环境差。
氧化、还原作业,对于氧化剂和还原剂的利用率低。
风管及辅助材料消耗大,操作效率低。
炉子操作安全性不如回转精炼炉和倾动精炼炉。
氧化、还原、扒渣和出铜等作业全部是手工操作。劳动量和劳动强度大,劳动条件差,难以实现机械化和自动化。
1、固定式射炉的缺点
固定式反射炉结构
三、固定式反射炉
固定式反射炉是传统的火法精炼设备,是一种表面加热的膛式炉,结构简单,操作容易,可以处理冷料,也可以热料,可以烧固体燃料、液体燃料或气体燃料。炉子容积可大、可小,波动范围较大。为了在精炼时使各部分熔体的温度保持均匀,从而使熔体各部分的杂质(特别是气体)含量及浇铸温度均匀,炉子作业空间不能太长以免发生温度降,为使熔池温度趋于一致,精炼炉有1.5~2m的燃烧前室,而且把炉顶做成下垂式,保证炉尾温度与炉子中央的温度相近。
无论采用固体、液体或气体燃料,燃烧过程的好坏是决定反射炉供热状况的首要条件。燃烧过程与烧嘴构造、烧嘴性能、燃烧条件以及操作等因素有关。诸如燃料与空气混合均匀、燃料入炉的扩散角适当、入炉后能尽快着火、及合理的火焰长度和温度等,都是保证燃料有效燃烧的重要条件。此外,由结构型式和尺寸决定的炉子本身的热工特性,也影响着炉内的传热。
火法冶炼铜及湿法冶炼铜工艺介绍

题,不利于贵金属等有价伴生元素的回收, 因此在工业上未得到广泛应用。
• 我国铜冶炼主要以火法冶炼为主,总产量占全 部铜产量约96%,我国也是采用铜冶炼工艺种 类最多的国家,国际上先进的铜冶炼技术在我 国大多已采用,且生产规模远大于其它国家, 同时仍存在大量采用落后生产工艺、污染严重 的中小型铜冶炼企业,根据《有色金属产业调 整和振兴规划》的要求,铜冶炼行业规划目标 是:按期淘汰落后产能,节能减排取得积极成 效,企业重组取得进展,创新能力明显增强, 资源保障能力进一步提高。
• 火法炼铜的原则流程如下,流程图见图
• 铜精矿(15~30%Cu)——造锍熔炼——冰 铜 (铜锍25~70%Cu)——吹炼——粗铜 (98~99%Cu)——火法精炼——阳极铜 (99%Cu)——电解精炼——电铜(99.9599.98%Cu)。
• 火法炼铜生产过程一般由以下几个工序组 成:备料、熔炼、吹炼、火法精炼、电解 精炼,最终产品为电解铜。配套工序:阳 极泥处理、余热回收、余热发电、烟气收 尘、烟气制酸、循环水系统等。
• 火法冶炼铜主要产物环节如下:
• 除火法工艺外,近20 年来湿法炼铜工艺也取 得了长足的进步,湿法工艺不仅可以处理一些 难选的氧化矿和表外矿、铜矿废石等,而且随 着细菌浸出和加压浸出的发展,亦可以处理硫 化铜矿石,并能获得较好的经济效益,从而大 大拓宽了铜资源综合利用范围。该法是在常温 常压或高压下,用溶剂浸出矿石或焙烧矿中的 铜,经过净液,使铜和杂质分离,而后用萃取 -电积法,将溶液中的铜提取出来。对氧化矿 和自然铜矿,大多数工厂用溶剂直接浸出;对 硫化矿,一般先经焙烧,而后浸出。
火法冶炼及湿法冶炼 铜工艺介绍
• 铜的冶炼工艺有火法冶炼和湿冶炼两种 方法。
粗铜的火法精炼工艺
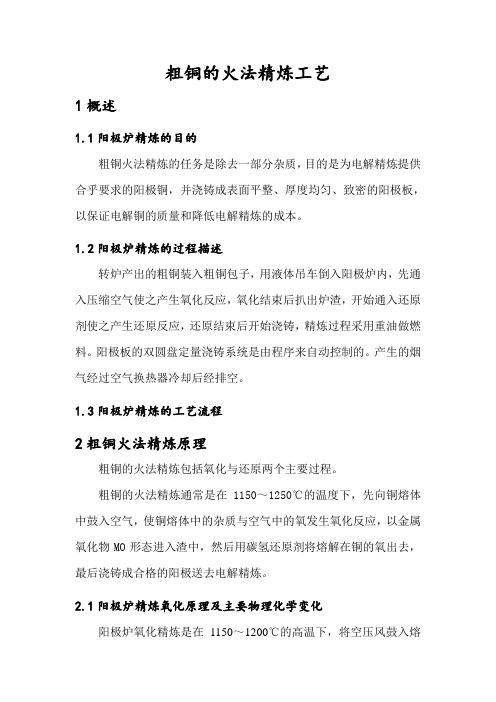
粗铜的火法精炼工艺1概述1.1阳极炉精炼的目的粗铜火法精炼的任务是除去一部分杂质,目的是为电解精炼提供合乎要求的阳极铜,并浇铸成表面平整、厚度均匀、致密的阳极板,以保证电解铜的质量和降低电解精炼的成本。
1.2阳极炉精炼的过程描述转炉产出的粗铜装入粗铜包子,用液体吊车倒入阳极炉内,先通入压缩空气使之产生氧化反应,氧化结束后扒出炉渣,开始通入还原剂使之产生还原反应,还原结束后开始浇铸,精炼过程采用重油做燃料。
阳极板的双圆盘定量浇铸系统是由程序来自动控制的。
产生的烟气经过空气换热器冷却后经排空。
1.3阳极炉精炼的工艺流程2粗铜火法精炼原理粗铜的火法精炼包括氧化与还原两个主要过程。
粗铜的火法精炼通常是在1150~1250℃的温度下,先向铜熔体中鼓入空气,使铜熔体中的杂质与空气中的氧发生氧化反应,以金属氧化物MO形态进入渣中,然后用碳氢还原剂将熔解在铜的氧出去,最后浇铸成合格的阳极送去电解精炼。
2.1阳极炉精炼氧化原理及主要物理化学变化阳极炉氧化精炼是在1150~1200℃的高温下,将空压风鼓入熔铜中,由于铜液中大多数杂质对氧的亲合力都大于铜对氧的亲合力,且多数杂质氧化物在铜水中的溶解度很小,当空气中的氧通入铜熔体中便优先将杂质氧化除去。
脱硫是在氧化过程中进行的。
向铜熔体中鼓入空气时,除了O2直接氧化熔铜中的硫产生SO2之外,氧亦熔于铜中。
但熔体中铜占绝大多数,而杂质占极少数,按质量作用定律,优先反应的是铜的大量氧化:4Cu+O2=2Cu2O所生成的Cu2O 溶解于铜水中,其溶解度随温度升高而增大。
1100℃,溶解的Cu2O=5%,相应的O2=0.56%1150℃,溶解的Cu2O=8.3%,相应的O2=0.92%1200℃,溶解的Cu2O=12.4%,相应的O2=1.38%1250℃,溶解的Cu2O=13.1%,相应的O2=1.53% 500℃1083℃20406080100Cu 重量% CuO700℃900℃1065℃1200℃1230℃3.4712.41300℃当Cu2O 含量超过该温度下的溶解度时,则熔体分为两层,下层是饱和了Cu2O 的铜液相,上层是饱和了铜的Cu2O 液相。
粗铜的火法精炼

书山有路勤为径,学海无涯苦作舟粗铜的火法精炼铜锍吹炼产出的粗铜含有较高的硫、氧和其他一些杂质,如铁、钴、锌、铅、锡、镍、砷、锑、铅等,此外还有含有硒、碲、锗、金、银等稀有元素和贵金属,其总含量可达0.5%~2%。
为除去粗铜中的杂质和回收贵金属等有价元素,应将粗铜进行火法精炼和电解精练。
火法精炼只能将对氧亲和力较大的杂质除到一定的程度,而贵金属仍留于火法精炼铜中。
粗铜火法精炼的目的是为电解精炼提供合乎要求的阳极铜,并浇铸成表面平整、厚均匀、致密的阳极板,以保证电解铜的质量和降低电解精炼的成本。
在火法精炼时,由于铜是主体,杂质浓度很低,故铜首先被氧化:4[Cu]+O2=2[Cu2O] 生成的氧化亚铜溶于铜熔体中,将铜液中的杂质Me 氧化:[Cu2O]+[Me]=2[Cu]+(MeO)欲使杂质残留于铜液中的极限浓度最低,应控制以下因素:(1)氧化亚铜始终保持饱和状态;(2)降低杂质氧化物的活度;(3)温度不宜太高。
粗铜火法精炼多采用固定式精炼炉、回转式精炼炉,也还有倾动式精炼炉。
表1 和表2 列出了国内外一些火法精炼过程的指标。
表1 国内火法精炼技术经济指标(一)厂别铜精炼回收率/%铜精炼真收率/%床能率/t·(m2·d)-1 燃料还原剂种类单耗/kg·t-1 种类单耗/kg·t-1 鑫冶(上海)99.9199.28.28 重油80~90 重油6 白银99.6958~12 重油70~90 重油8 云冶99.898.74 重油87 木炭粉13 重冶99.698.54.36 天然气167m3/t 柴油11 株冶99.797 重油90~110 重油10~20 广冶99.0296.83.1 重油180 重油6 贵冶99 重油50~60 液化石油气4~6 大冶98 重油42 重油5~6 表1 国内火法精炼技术经济指标(二)厂别烟气废热利用每炉还原时间/h 渣率/%渣含铜/%电耗/kW·h·t-1 水耗/t·t-1 铸模消耗/个·t-1(阳极)利用方式利用率/%鑫冶(上海)锅炉空气预热器生产蒸汽热风621.50.5~0.610~30301.8 铸铁120。
铜火法精炼和湿法精炼

铜火法精炼和湿法精炼铜火法火法精炼是利用某些杂质对氧的亲和力大于铜,而其氧化物又不溶于铜液等性质,通过氧化造渣或挥发除去。
其过程是将液态铜加入精炼炉升温或固态铜料加入炉内熔化,然后向铜液中鼓风氧化,使杂质挥发、造渣;扒出炉渣后,用插入青木或向铜液中注入重油、石油气或氨等方法还原其中的氧化铜。
还原过程中用木炭或焦炭覆盖铜液表面,以防再氧化。
精炼后可铸成点解精炼所用的铜阳极或铜锭。
精炼炉渣含铜较高,可返回转炉处理。
精炼作业在反射炉或回转精炉内进行。
火法精炼的产品叫火精铜,一般含铜99.5%以上。
火精铜中常含有金、银等贵金属和少量杂质,通常要进行电解精炼。
若金、银和有害杂质含量很少,可直接铸成商品铜锭。
粗铜火法精炼主要由鼓风氧化和重油还原两个操作环节构成。
铜中有害杂质除去的程度主要取决于氧化过程,而铜中氧的排除程度则取决于还原程度。
1.氧化过程由于粗铜含铜98%以上,所以在氧化过程中,首先是铜的氧化:4Cu+O2=2Cu2O生成的Cu2O溶解于铜液,在操作温度1373~1523K条件下,Cu2O在铜中的杂质金属(Me)发生反应:Cu2O +Me=2Cu+MeO反映平衡常数:K=[MeO]*[Cu]/[Cu2O][Me]因为MeO在铜里溶解度小,很容易饱和;而铜的浓度更大,杂质氧化时几乎不发生变化,故都可视为常数,因此K*=[Me]/[Cu2O]所以,Cu2O的浓度越大,杂质金属Me的浓度就越小。
因此,为了迅速完成地出去铜中的杂质,必须使铜液中Cu2O的浓度达到饱和。
升高温度可以增加铜液中Cu2O的浓度,但温度太高会使燃料消耗增加,也会使下一步还原时间延长,所以氧化期间温度以1373~1423K为宜。
此时Cu2O的饱和浓度为6%-8%。
氧化除杂质时,为了减少铜的损失和提高过程效率,常加入各种溶剂如石英砂,石灰和苏打等,使各种杂质生成硅酸铅、砷酸钙等造渣除去。
脱硫是在氧化精炼最后进行,这是因为有其他对氧亲和势力的金属时,铜的硫化物不易被氧化,但只要氧化除杂质金属结束,立即就会发生剧烈的相互反应,放出SO2: CuS+2Cu2O=6Cu+SO2这时铜水出现沸腾现象,称为“铜雨”。
火法炼铜

铜精矿冶炼(火法)火法炼铜主要工艺主要包括:(1)铜精矿的造锍熔炼;(2)铜锍吹炼成粗铜;(3)粗铜火法精炼;(4)阳极铜电解精炼。
经冶炼产出最终产品-电解铜(阴极铜)。
目前世界铜冶炼厂使用的主要熔炼工艺为闪速熔炼和熔池熔炼。
1.熔池熔炼:精矿被抛到熔体的表面或者被喷入熔体内,通常向熔池中喷入氧气和氮气使熔池发生剧烈搅拌,精矿颗粒被液体包围迅速融化,因此,吹炼反应能够产生维持熔炼作业所需的大部分热量,使含有氧气的气泡和包裹硫化铜/铁的溶液发生质量传递。
而闪速熔炼中的干精矿是散布在氧气和氮气的气流中的,精矿中所含的硫和铁发生燃烧,在熔融颗粒进入反应空间时即产生熔炼和吹炼。
当这些颗粒与熔池融为一体时,有些反应还会继续进行,但大部分是在飞行过程中发生的。
2.闪速炼铜:其基本流程是各种精矿在闪速炉熔炼产出冰铜,然后将冰铜水淬,磨粉并干燥,再在另一规格较小的闪速炉中用富氧空气吹炼成粗铜,产出的粗铜通过溜槽加至阳极炉。
闪速吹炼具有生产能力大、工艺技术先进、成熟可靠、环保好、自动化程度高、运行费用低、烟气量小、二氧化硫浓度高且稳定等优点,具有良好的推广应用价值,尤其适合于新建大型铜冶炼厂和对环保要求非常严格的炼铜厂改造。
3.粗铜火法精炼:以回转炉精炼为主,由于传统固定式精炼炉主要依靠人工操作、劳动强度大、环保效果差、易跑铜、难控制,已逐步被机械化程度高、炉体密闭易操作的回转式阳极炉所替代。
4.电解精炼:电解精炼工艺主要分为传统始极片工艺和不锈钢永久性阴极工艺,永久阴极电解工艺是当前电解工艺的发展趋势。
主要是因不锈钢阴极法采用不锈钢板做成阴极代替铜始极片,阴极铜产品再从不锈钢阴极上剥取,不锈钢阴极再返回电解槽中继续使用。
该方法无始极片生产系统,简化了生产过程。
且由于不锈钢阴极平直,生产过程中短路现象少,不但提高了产品质量,而且可使用较高的电流密度和较小的极距。
国内外火法炼铜进展及发展趋势熔池熔炼:1.诺兰达连续炼铜法:该法很适于使用氧气。
铜火法精炼和湿法精炼

铜火法精炼和湿法精炼铜火法火法精炼是利用某些杂质对氧的亲和力大于铜,而其氧化物又不溶于铜液等性质,通过氧化造渣或挥发除去。
其过程是将液态铜加入精炼炉升温或固态铜料加入炉内熔化,然后向铜液中鼓风氧化,使杂质挥发、造渣;扒出炉渣后,用插入青木或向铜液中注入重油、石油气或氨等方法还原其中的氧化铜。
还原过程中用木炭或焦炭覆盖铜液表面,以防再氧化。
精炼后可铸成点解精炼所用的铜阳极或铜锭。
精炼炉渣含铜较高,可返回转炉处理。
精炼作业在反射炉或回转精炉内进行。
火法精炼的产品叫火精铜,一般含铜99.5%以上。
火精铜中常含有金、银等贵金属和少量杂质,通常要进行电解精炼。
若金、银和有害杂质含量很少,可直接铸成商品铜锭。
粗铜火法精炼主要由鼓风氧化和重油还原两个操作环节构成。
铜中有害杂质除去的程度主要取决于氧化过程,而铜中氧的排除程度则取决于还原程度。
1.氧化过程由于粗铜含铜98%以上,所以在氧化过程中,首先是铜的氧化:4Cu+O2=2Cu2O生成的Cu2O溶解于铜液,在操作温度1373~1523K条件下,Cu2O在铜中的杂质金属(Me)发生反应:Cu2O +Me=2Cu+MeO反映平衡常数:K=[MeO]*[Cu]/[Cu2O][Me]因为MeO在铜里溶解度小,很容易饱和;而铜的浓度更大,杂质氧化时几乎不发生变化,故都可视为常数,因此K*=[Me]/[Cu2O]所以,Cu2O的浓度越大,杂质金属Me的浓度就越小。
因此,为了迅速完成地出去铜中的杂质,必须使铜液中Cu2O的浓度达到饱和。
升高温度可以增加铜液中Cu2O的浓度,但温度太高会使燃料消耗增加,也会使下一步还原时间延长,所以氧化期间温度以1373~1423K为宜。
此时Cu2O的饱和浓度为6%-8%。
氧化除杂质时,为了减少铜的损失和提高过程效率,常加入各种溶剂如石英砂,石灰和苏打等,使各种杂质生成硅酸铅、砷酸钙等造渣除去。
脱硫是在氧化精炼最后进行,这是因为有其他对氧亲和势力的金属时,铜的硫化物不易被氧化,但只要氧化除杂质金属结束,立即就会发生剧烈的相互反应,放出SO2: CuS+2Cu2O=6Cu+SO2这时铜水出现沸腾现象,称为“铜雨”。
粗铜火法精炼
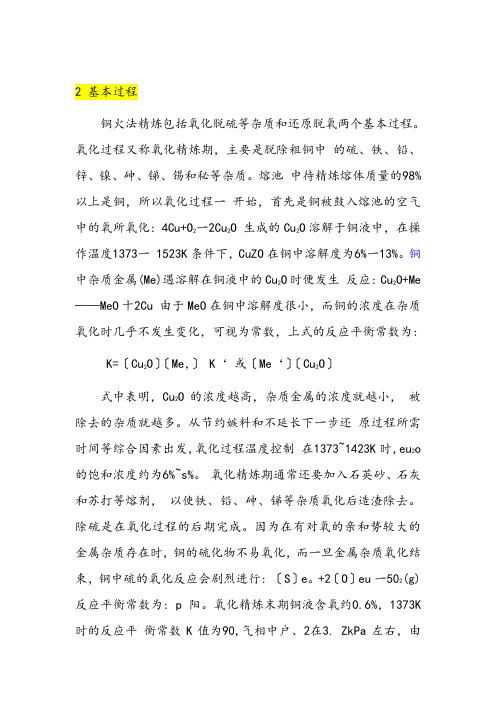
2 基本过程铜火法精炼包括氧化脱硫等杂质和还原脱氧两个基本过程。
氧化过程又称氧化精炼期,主要是脱除粗铜中的硫、铁、铅、锌、镍、砷、锑、锡和秘等杂质。
熔池中待精炼熔体质量的98%以上是铜,所以氧化过程一开始,首先是铜被鼓入熔池的空气中的氧所氧化: 4Cu+O2一2Cu2O 生成的Cu2O溶解于铜液中,在操作温度1373一1523K条件下,CuZO在铜中溶解度为6%一13%。
铜中杂质金属(Me)遇溶解在铜液中的Cu2O时便发生反应: Cu2O+Me——MeO十2Cu 由于MeO在铜中溶解度很小,而铜的浓度在杂质氧化时几乎不发生变化,可视为常数,上式的反应平衡常数为:K=〔Cu2O〕〔Me,〕K‘或〔Me‘〕〔Cu2O〕式中表明,Cu2O的浓度越高,杂质金属的浓度就越小,被除去的杂质就越多。
从节约嫉料和不延长下一步还原过程所需时间等综合因素出发,氧化过程温度控制在1373~1423K时,eu2o的饱和浓度约为6%~s%。
氧化精炼期通常还要加入石英砂、石灰和苏打等熔剂,以使铁、铅、砷、锑等杂质氧化后造渣除去。
除硫是在氧化过程的后期完成。
因为在有对氧的亲和势较大的金属杂质存在时,铜的硫化物不易氧化,而一旦金属杂质氧化结束,铜中硫的氧化反应会剧烈进行: 〔S〕e。
+2〔O〕eu一502(g) 反应平衡常数为: p阳。
氧化精炼末期铜液含氧约0.6%,1373K时的反应平衡常数K值为90,气相中户、2在3. ZkPa左右,由此计算铜液中含硫量可以降到0.001%。
铜液中以Cu2O 形态存在的氧在下一步还原过程中除去。
还原过程又称还原精炼期。
用重油、丙烷等还原剂将CuZO还原成金属铜,使铜中氧含量降到0.05% ~0.10%的过程。
重油等还原剂受热裂解为HZ、CO、C等成分,还原反应为: Cu2O十H2—2Cu+H2O Cu:O+CO—2Cu+CO2Cu2O+C一2Cu+CO 还原精炼期的终点控制十分重要,如过还原,氢气在铜液中的溶解量会急剧增加,在浇铸铜阳极板时析出,使阳极板多孔;而还原不足时,就不能产生一定量的水蒸气,以抵消铜冷凝时的体积收缩部分,降低了阳极板的物理规格,同样不利。
铜精炼工艺操作规程

铜精炼工艺操作规程1、工艺原理一般粗铜含有 0.5~1.5%的杂质,紫杂铜含有 1~5%的杂质。
这些杂质的存在,使铜的抗腐性弱,机械性能差,导热、导电率低,不适合机械加工及电气工业的应用。
火法精炼主要是将金、银等贵重金属以外的杂质含量降低到相应限度,以满足电解精炼的要求。
火法精炼是将粗铜、紫杂铜装入精炼炉内熔化后,向熔体铜内通入空气,使其中对氧亲和力较大的杂质 Zn 、Fe 、Pb 、Sn 、As 、S 等发生氧化,以氧化物的形态与参加炉内的熔剂发生氧化反响,于铜液外表形成炉渣,或挥发进入炉气而除去。
残留在铜液中的氧,经复原脱去后,即可浇铸成电解精炼用的阳极板。
因此,铜火法精炼可分成以下两个主要反响阶段: 1.1 氧化阶段在 1160℃的温度条件下,使铜液中的杂质发生氧化而除去。
主要反响式: 4Cu+O =2Cu O22Cu O+Me=2 Cu+MeO2MeO+SiO = Me O·SiO222Cu 2O+ Cu 2S=6 Cu+SO ↑21.2 复原阶段经氧化后铜熔体约含有 8%左右的氧,需进展复原以脱除铜熔体中的氧。
其主要反响式〔用煤粉作复原剂〕:Cu O+C=2 Cu+CO24 Cu2O+CH4=8 Cu+CO2+2 H O2Cu O+CO=2 Cu+CO2 2Cu O+H =2 Cu + H O2 2 26Cu O+2C H =12 Cu+2CO+m H + 2CO2 2 m 22 2、工艺流程3、主要工艺设备一览表序号 设备名称规格型号数 量主要技术参数 备注69-12-8D7空气压缩机 3LA-16/3.5风量 6763-7981m 3/h3 风 压 21732-21947Pa打气量 16m 3/min 4出口压力 0.35MPa75Kw电机 75 Kw冷却水泵JS80-65-160配 用 电 机 Y132S -2 282扬 程 28m 流 量 7.5 Kw50m 3/h热水泵 JS100-65-250扬 程 20m 流 量 配 用 电 机 Y132S-4 9250m 3/h7.5 Kw10 贮油罐200m 32 Φ 6500*6800玻璃钢冷塔80,100t桓台宏玉玻璃钢生产11 212 切割机J3G-400 113 电焊机BX1-3002沟通 〔打〕齿轮流量 33.3L/minY100 L 2-42.2 Kw14油泵KCB-33.3 41.45MPa(卸)齿轮流量 300L/minY132 M 2-615 油泵KCB-300 20.36MPa5.5Kw1 铜阳极 精炼炉炉 膛 4900*2600 4 容量:60-75t 熔池面积:13 ㎡ 燃料:煤焦油最大熔池深度:680㎜ 2 圆盘浇铸机Φ 8600-9000 铸模 18-20 块 配用电机㎜ 2 浇铸速度 100 块/时 2.2Kw 3 地轨加料机 自制 2加料力量 1t/次电动单梁桥式起重量 3-5 吨 Zd 41-4 14 起重机6 电机 7.5 Kw起重量 2.5t5 卷扬机 JJK 20 平均绳速 25m/min Y100L1-42.2Kw风机9-12 风量 7133m 3/h 55Kw2 风压 16729Pa4、工艺技术条件4.1铜阳极板技术标准4.1.1铜阳极板的化学成分Cu≥99.0%~99.5% As ≤0.09%Sb ≤0.02%Bi ≤0.02% Zn≤0.02%Fe≤0.05%Pb≤0.15%Ni≤0.25%S≤0.05% 4.1.2.1 每块阳极板的重量为200±20Kg(外购板±5Kg)〔鹏辉〕;每块铜阳极板的重量 265Kg,每块重量允差±5Kg。
火法炼铜

Cu2O+FeS→Cu2S+FeO
2FeS+3O2+SiO2→2FeO·SiO2+2SO2
2FeO+SiO2→2FeO·SiO2
造锍熔炼的传统设备为鼓风炉、反射炉、电炉等,新建的现代化大型炼铜厂多采用闪速炉。
鼓风炉熔炼 鼓风炉是竖式炉,小国很早就用它直接炼铜。传统的方法为烧结块鼓风炉熔炼。硫化铜精矿先经烧结焙烧脱去部分硫,制成烧结块,与熔剂、焦炭等按批料呈层状加入炉内,熔炼产出冰铜和弃渣,此法烟气含SO2低,不易经济地回收硫。为消除烟害,回收精矿中的硫,20世纪50年代,发展了精矿鼓风炉熔炼法,即将硫化铜精矿混捏成膏状,再配以部分块料、熔剂、焦炭等分批从炉顶中心加料口加入炉内,形成料封,减少漏气,提高SO2浓度。混捏料在炉内经热烟气干燥、焙烧形成烧结料柱,块状物料也呈柱状环绕在烧结料柱的周围,以保持透气性,使熔炼作业正常进行。中国沈阳冶炼厂、富春江冶炼厂等采用此法。
反射炉熔炼 适于处理浮选的粉状精矿。反射炉熔炼过程脱硫率低,仅20%~30%,适于处理含铜品位较高的精矿。如原料含铜低、含硫高,熔炼前要先进行焙烧。反射炉生产规模可大型化,对原料,燃料的适应性强,长期来一直是炼铜的主要设备,至80年代初,全世界保有的反射炉能力仍居炼铜设备的首位。但反射炉烟气量大,且含SO2仅1%左右,回收困难。反射炉的热效率仅25%~30%,熔炼过程的反应热利用较少,所需热量主要靠外加燃料供给。70年代以来,世界各国都在研究改进反射炉熔炼,有的采用氧气喷撒装置将精矿喷入炉内,加强密封,以提高SO2浓度。中国白银公司第一冶炼厂将铜精矿加到反射炉中的熔体内,鼓风熔炼,提高了熔炼强度,烟气可用于制取硫酸。
铜的火法冶炼工艺原理
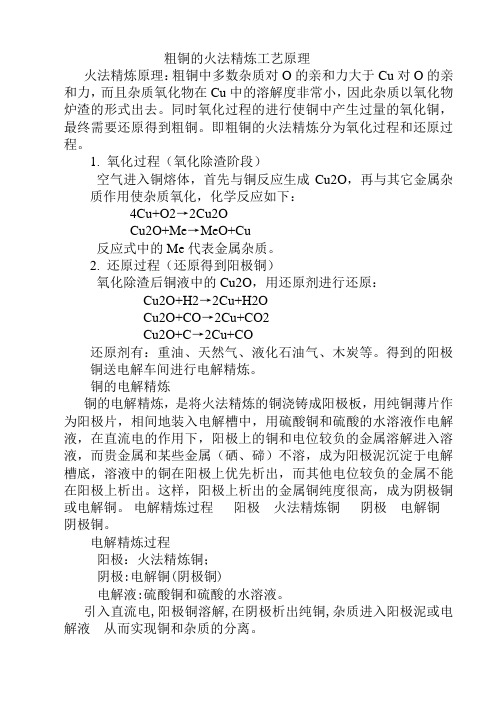
粗铜的火法精炼工艺原理火法精炼原理:粗铜中多数杂质对O的亲和力大于Cu对O的亲和力,而且杂质氧化物在Cu中的溶解度非常小,因此杂质以氧化物炉渣的形式出去。
同时氧化过程的进行使铜中产生过量的氧化铜,最终需要还原得到粗铜。
即粗铜的火法精炼分为氧化过程和还原过程。
1.氧化过程(氧化除渣阶段)空气进入铜熔体,首先与铜反应生成Cu2O,再与其它金属杂质作用使杂质氧化,化学反应如下:4Cu+O2→2Cu2OCu2O+Me→MeO+Cu反应式中的Me代表金属杂质。
2.还原过程(还原得到阳极铜)氧化除渣后铜液中的Cu2O,用还原剂进行还原:Cu2O+H2→2Cu+H2OCu2O+CO→2Cu+CO2Cu2O+C→2Cu+CO还原剂有:重油、天然气、液化石油气、木炭等。
得到的阳极铜送电解车间进行电解精炼。
铜的电解精炼铜的电解精炼,是将火法精炼的铜浇铸成阳极板,用纯铜薄片作为阳极片,相间地装入电解槽中,用硫酸铜和硫酸的水溶液作电解液,在直流电的作用下,阳极上的铜和电位较负的金属溶解进入溶液,而贵金属和某些金属(硒、碲)不溶,成为阳极泥沉淀于电解槽底,溶液中的铜在阳极上优先析出,而其他电位较负的金属不能在阳极上析出。
这样,阳极上析出的金属铜纯度很高,成为阴极铜或电解铜。
电解精炼过程 阳极 火法精炼铜 阴极 电解铜 阴极铜。
电解精炼过程阳极:火法精炼铜;阴极:电解铜(阴极铜)电解液:硫酸铜和硫酸的水溶液。
引入直流电,阳极铜溶解,在阴极析出纯铜,杂质进入阳极泥或电解液 从而实现铜和杂质的分离。
1.阳极反应电解液中含有H+、Cu2+、SO42-和水分子,当通入直流电时,在阳极上可能的氧化反应为:Cu-2e→Cu2+Me-2e→Me2+SO42--2e→SO3+1/2O2H2O-2e→2H++1/2O2Me指Fe、Pb、Ni、As、Sb等,电极电位比铜负,与铜一起溶解进入电解液:SO42-和H2O电极电位比铜正得多,在阳极上不可能进行,反应。
粗铜的火法精炼工艺
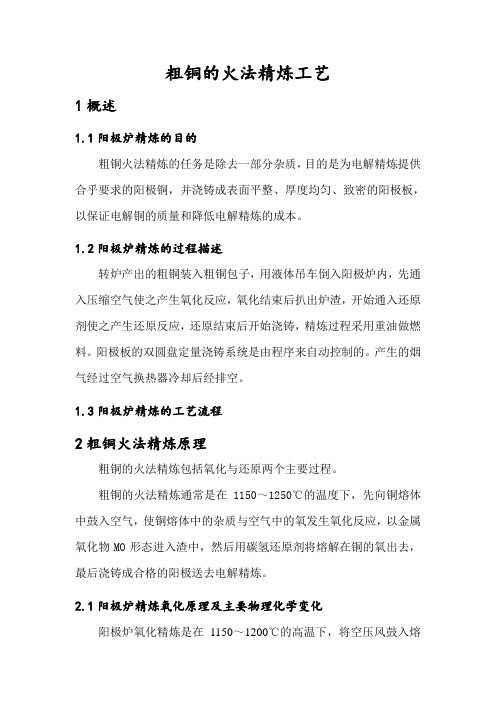
粗铜的火法精炼工艺1概述1.1阳极炉精炼的目的粗铜火法精炼的任务是除去一部分杂质,目的是为电解精炼提供合乎要求的阳极铜,并浇铸成表面平整、厚度均匀、致密的阳极板,以保证电解铜的质量和降低电解精炼的成本。
1.2阳极炉精炼的过程描述转炉产出的粗铜装入粗铜包子,用液体吊车倒入阳极炉内,先通入压缩空气使之产生氧化反应,氧化结束后扒出炉渣,开始通入还原剂使之产生还原反应,还原结束后开始浇铸,精炼过程采用重油做燃料。
阳极板的双圆盘定量浇铸系统是由程序来自动控制的。
产生的烟气经过空气换热器冷却后经排空。
1.3阳极炉精炼的工艺流程2粗铜火法精炼原理粗铜的火法精炼包括氧化与还原两个主要过程。
粗铜的火法精炼通常是在1150~1250℃的温度下,先向铜熔体中鼓入空气,使铜熔体中的杂质与空气中的氧发生氧化反应,以金属氧化物MO形态进入渣中,然后用碳氢还原剂将熔解在铜的氧出去,最后浇铸成合格的阳极送去电解精炼。
2.1阳极炉精炼氧化原理及主要物理化学变化阳极炉氧化精炼是在1150~1200℃的高温下,将空压风鼓入熔铜中,由于铜液中大多数杂质对氧的亲合力都大于铜对氧的亲合力,且多数杂质氧化物在铜水中的溶解度很小,当空气中的氧通入铜熔体中便优先将杂质氧化除去。
脱硫是在氧化过程中进行的。
向铜熔体中鼓入空气时,除了O2直接氧化熔铜中的硫产生SO2之外,氧亦熔于铜中。
但熔体中铜占绝大多数,而杂质占极少数,按质量作用定律,优先反应的是铜的大量氧化:4Cu+O2=2Cu2O所生成的Cu2O 溶解于铜水中,其溶解度随温度升高而增大。
1100℃,溶解的Cu2O=5%,相应的O2=0.56%1150℃,溶解的Cu2O=8.3%,相应的O2=0.92%1200℃,溶解的Cu2O=12.4%,相应的O2=1.38%1250℃,溶解的Cu2O=13.1%,相应的O2=1.53% 500℃1083℃20406080100Cu 重量% CuO700℃900℃1065℃1200℃1230℃3.4712.41300℃当Cu2O 含量超过该温度下的溶解度时,则熔体分为两层,下层是饱和了Cu2O 的铜液相,上层是饱和了铜的Cu2O 液相。
第五章 粗铜的精炼
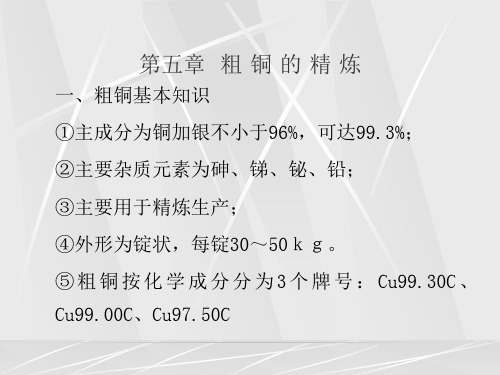
可产出含铜99.95%以上的电铜,而金、银、硒、
碲等富集在阳极泥中。 电解过程中,大部分铁、镍、锌和一部分砷、 锑等进入溶液,使电解液中的杂质逐渐积累,铜 含量也不断增高,硫酸浓度则逐渐降低。因此,
必须定期引出部分溶液进行净化,并补充一定量
的硫酸。
三、粗铜的火法精炼 1、火法精炼的基本原理
再生粗铜火法精炼过程与原生粗铜火法精炼一 样,即向铜熔体中鼓入压缩空气使杂质氧化并造 渣而除去,在扒渣后进行氧化铜的还原及铜的铸 造。
三粗铜的火法精炼1火法精炼的基本原理再生粗铜火法精炼过程与原生粗铜火法精炼一样即向铜熔体中鼓入压缩空气使杂质氧化并造渣而除去在扒渣后进行氧化铜的还原及铜的铸粗铜火法精炼的基本原理是基于不同金属对氧的亲和力不同使质质金属优先氧化后造渣并与主体金属铜分离
第五章 粗 铜 的 精 炼
一、粗铜基本知识 ①主成分为铜加银不小于96%,可达99.3%; ②主要杂质元素为砷、锑、铋、铅; ③主要用于精炼生产; ④外形为锭状,每锭30~50kg。 ⑤ 粗 铜 按 化 学 成 分 分 为 3 个 牌 号 : Cu99.30C 、 Cu99.00C、Cu97.50C
铅:阳极中的铅在电解过程中与硫酸作用生成 白色的硫酸铅。在酸性溶液中又可能氧化成PbO2 复盖于阳极表面,使阳极钝化槽电压升高。因而 阳极含铅最好控制在0.2%以下。 金银和铂族金属:它们在电解精炼过程中不溶 解而进入阳极泥中。
四、再生粗铜阳极电解精炼的实践 1、电解装置和电解液 再生粗铜电解精炼时用的阳极是再生铜经火法 精炼后铸成的长方形铜块,而阴极则由厚为0.40.7mm的铜片做成,其尺寸比阳极稍大。 电解槽是由钢筋混凝土制成并内衬防腐材料的 长方形槽子,其大小由电极数量和尺寸来决定。 电解液的主要成分是Cu2 +和H2SO4以及阳极电溶 解入溶液的杂质,为了改善电解铜的质量,常在 电解液中加入各类添加剂(如动物胶、硫脲、干 酪素等)。
- 1、下载文档前请自行甄别文档内容的完整性,平台不提供额外的编辑、内容补充、找答案等附加服务。
- 2、"仅部分预览"的文档,不可在线预览部分如存在完整性等问题,可反馈申请退款(可完整预览的文档不适用该条件!)。
- 3、如文档侵犯您的权益,请联系客服反馈,我们会尽快为您处理(人工客服工作时间:9:00-18:30)。
1、固定式射炉的缺点
• 氧化、还原、扒渣和出铜等作业全部是手工操作。劳 动量和劳动强度大,劳动条件差,难以实现机械化和 自动化。 • 炉子密封性差,散热损失大,烟气泄漏多,车间环境 差。 • 氧化、还原作业,对于氧化剂和还原剂的利用率低。 • 风管及辅助材料消耗大,操作效率低。 • 炉子操作安全性不如回转精炼炉和倾动精炼炉。
铜的火法精炼
目录
一、粗铜火法精炼的目的 粗铜火法精炼的目的 二、铜火法精炼炉的结构 三、固定式反射炉 四、反射炉生产的基本原理 五、杂质在精炼过程中的行为 六、生产工艺流程图 七、反射炉精炼作业实践
一、粗铜火法精炼的目的
目前使用的精炼方法有两类: 1)粗铜火法精炼,直接生产 含铜99.5%以上的精铜。该法 仅适用于金、银和杂质含量较 低的粗铜,所产精铜仅用于对 纯度要求不高的场合。 2)粗铜先经过火法精炼除去 部分杂质,浇铸成阳极,再进 行电解精炼。产出含铜99.95% 以上杂质含量达到标准的精铜。 这是铜生产的主要流程。
三、固定式反射炉
• 固定式反射炉是传统的火法精炼 设备,是一种表面加热的膛式炉, 结构简单,操作容易,可以处理 冷料,也可以热料,可以烧固体 燃料、液体燃料或气体燃料。炉 子容积可大、可小,波动范围较 大。为了在精炼时使各部分熔体 的温度保持均匀,从而使熔体各 部分的杂质(特别是气体)含量 及浇铸温度均匀,炉子作业空间 不能太长以免发生温度降,为使 熔池温度趋于一致,精炼炉有 1.5~2m的燃烧前室,而且把炉顶 做成下垂式,保证炉尾温度与炉 子中央的温度相近。
2.铁 铁与铜在一定范围内互溶,但不生成化合 物。在熔化阶段铁能部分地氧化并生成炉 渣;大部分在铜水的氧化阶段初期呈氧化 亚铁和亚铁酸盐进入炉渣内。在熔融铜内 靠Cu2O使铁氧化成Fe2O3是不可能的,因 为Fe2O3的离解压比Cu2O的离解压大得多。 铁对氧的亲和力很大,再加上它的造渣性 能好,可生成硅酸盐和铁酸盐炉渣,故铁 在铜火法精炼过程中很易除去,可除低到 10ppm以下
3.钴 铜与钴在一定含量范围内互溶,钴的行为与铁相似, 在铁之后和镍之前形成硅酸盐和铁酸盐进入炉渣。 4.锌 在处理杂铜时会带入较多的锌。锌与铜在液态时 完全互溶,并生成化合物。锌沸点为906℃,精炼时大 部分锌在熔化阶段即以金属形态挥发,然后被炉气中的 氧氧化成ZnO而随炉气排出,其余的锌在氧化初期被氧 化成ZnO,并形成硅酸锌(2ZnO. SiO2)和铁酸锌 (ZnO. Fe2O3)进入炉渣。当精炼含锌高的铜料时(例 如精炼黄杂铜、黑铜),为了加速锌的蒸发,在熔化期 和氧化期限均提高炉温,并在熔体表面盖一层木炭或不 含硫焦炭颗粒,使氧化锌还原成金属锌蒸发,以免生成 氧化锌结壳妨碍蒸发锌的过程正常进行。
• a)为了把溶解的S浓度降低到0.008%以下,在1200℃ 时铜水中的氧浓度保持在0.1%也就足够了,但在实 际生产中氧的浓度往往提高到0.9~1.0%之间。这是 因为随着硫反应接近平衡状态,反应速度势必减慢, 反应时间必然延长,为了加快反应速度,熔体中Cu2O 的饱和是必要的。b)炉气SO2的分压愈大,则铜中含 硫愈高,如果在铜熔体上的炉气中含有较高SO2时, 要将铜中的SO2除净是不可能的,因此应采用低硫燃 料供热。在1200℃时,与铜水中的S和O保持平衡的 SO2分压为101Pa时,氧化期的炉气中含有0.1%SO2是 无害的 c)温度和SO2分压对铜水中S和O的平衡浓度 有不同的影响。当提高温度时,炉气中SO2的分压应 控制低一些,相反,降低温度时则允许SO2分压稍高 一些。SO2分压与温度相比,有更大的作用,因此它 是主要的影响因素。在实践中采用含硫较少的燃料是 必要的。
• 5.铅 固态时铅不溶于铜中,而在液态时溶解 极为有限。在火法精炼过程中,铅易氧 化成PbO,PbO的密度为9.2 ,因PbO比重 比铜大,沉于炉底下部,与SiO2成小比 重的硅酸铅(хPbO.уSiO2)很容易上浮 至熔体表面,而被除去。当粗铜含铅高 时,须在精炼炉加入一定量的SiO2,同 时,由于PbO比重大,须增大风量,增强 搅动能量,使氧化铅结合成硅酸盐而浮 到熔体表面,通过扒渣除去。
二、铜火法精炼炉的结构
• 用于铜火法精炼的炉型有固 定式反射炉、回转式精炼炉、 倾动式精炼炉三种。 • 回转式精炼炉是20世纪50年 代后期开发的火法精炼设备。 它是一个圆筒形的炉体,在 炉体上配置有2—4个风口、 一个炉口和一个出铜口,可 作360度回转。转动炉体进行 氧化、还原作业。回转炉体 可进行加料、放渣、出铜, 操作简便、灵活。
2、固定式反射炉结构 • 固定反射炉主要 由炉体部分、骨 架部分、余热利 用及烟道部分、 炉子供热系统等 设备组成。
2.1 炉体部分
• 包括炉基、炉底、炉 墙和炉顶组成 • 炉基由钢筋/耐热混 凝土与炉底支墩整体 浇灌而成 • 炉底分为三/四层, 总厚为910mm。 • 炉 墙 厚 度 为 680mm , 主要材质为镁质和镁 铬质两种。 • 炉 顶 厚 度 为 380mm , 村质为镁质/镁铬质。
• 粗铜火法精炼是要达到下面两个目的:一是尽可 能地除去部份杂质(包括SO2、O2、Pb、As、Sb、 Ni、Bi等),将阳极板含铜提高到99.0~99.8%; 二是浇铸出板面光滑、厚薄均匀、无飞边毛刺、 悬吊垂直好的阳极板,达到电解工艺的要求。阳 极板属于中间产品,由于原料与工艺的差异,它 的化学成分标准是由工厂各自制定,Cu主品位一 般为99.0%~99.8%, • 电解对阳极铜的物理外形规格要求,各工厂的控 制标准不同,但要求阳极铜厚度均匀;阳极铜耳 部饱满、坚固、不许有明显裂纹,耳子底部无飞 边,耳部顶端对板面的弯曲度不大于10mm;板面 平整、细花纹、不夹渣;飞边、毛刺不超过6mm, 板面起泡不超过6mm;不允许有冷隔层,不允许 上薄下厚。
• 无论采用固体、液体或气体燃料,燃烧过程的好坏是决 定反射炉供热状况的首要条件。燃烧过程与烧嘴构造、 烧嘴性能、燃烧条件以及操作等因素有关。诸如燃料与 空气混合均匀、燃料入炉的扩散角适当、入炉后能尽快 着火、及合理的火焰长度和温度等,都是保证燃料有效 燃烧的重要条件。此外,由结构型式和尺寸决定的炉子 本身的热工特性,也影响着炉内的传热。 • 采用预热空气燃烧,可以使燃料预热,提前着火,促进 充分燃烧,特别是对着火点较高的粉煤尤有好处。预热 空气带进的物理热,可提高燃料燃烧温度,降低燃料消 耗。空气在烟道中预热至300~500℃,燃烧温度可提高 100~200℃,燃料消耗可降低10%~20%。由于精炼炉的 冶炼温度不是很高,一般燃料燃烧温度都能满足冶炼工 艺的要求。在空气换热器之前还需设置废热锅炉以降低 烟气温度,况且换热器的维护保养麻烦,还增加设备投 资。因此,多数工厂都不愿采用预热空气,只是安装废 热锅炉或汽化冷却水套来回收余热。
• 6. 镍 • 镍与铜能生成一系列固熔体,镍在熔化期和氧 化期均受到氧化,但既缓慢又不完全。并且在 氧化期所生成的NiO分布于铜水和炉渣之间, 溶入炉渣中的NiO部分与其中的Fe2O3结合成 NiO. Fe2O3。NiO. Fe2O3不溶于铜水而溶于炉渣, 这部分镍是可以氧化除去的,一般情况下铜中 的镍可降低到0.2~0.4%。由于铜水中经常含有 少量的砷和锑,溶于铜水中的NiO便以 6Cu2O.8NiO.2As2O5和6Cu2O.8NiO.2Sb2O5(镍云 母)的形态存在,这种三元氧化物的形成是很难 避免的,这是镍之所以难除去的主要原因。
五、杂质在精炼过程中的行为
1.硫 在粗铜中硫主要以硫化亚铜形态存在,少量呈 其他硫化物形态存在。由于铜对硫的亲和力很大, Cu2S在精炼过程中最初氧化缓慢,但在氧化阶段将 结束,铁和钴等杂质氧化之后,便开始按下列反应 剧烈地放出SO2。 [Cu2S] + 2[Cu2O] = 6[Cu] + SO2 - 27720卡 在T和Pso2一定的条件下,铜水中溶解的氧浓度增加, 可以促进硫浓度的减少甚至完全消失,故在氧化脱 硫过程中,应该将Cu2O浓度提高到必需的程度,特 别是在硫浓度已降到相当低的时候。同时Cu2S和 Cu2O的交互反应是吸热的,而且有SO2气体发生,因 此提高铜水温度和降低SO2分压,都有利于脱硫。
• 由于精炼产出的渣量不多, 且铜与渣的比重差别大, 故精炼炉不需要澄清分离 区。现代精炼反射炉的作 业空间长度一般为10~15m, 宽度4~5m,炉长与炉宽之 比为1.7~3.5m其容量为5 至400t,精炼炉的熔池深 为为0.6~1.2m,以便在炉 内维持一定的热量储备, 可在一定程度内补偿炉内 作业空间温度的波动。
2.2 骨架部分 • • • • • 围板 立柱 拉杆 弹簧 水 套 构 件
2.3 余热回收及烟道部分 • 反射炉的排烟方式有自然排 烟和强制排烟两种。一般都 采用自然排烟方式,烟气经 竖直烟道、斜烟道和余热回 收及烟尘收集系统,由烟囱 排出。烟尘的收集采用重力 沉降收尘,无任何的收尘设 备。余热回收采用低压板箱 式汽化水套,中间加对流管 束。
• 倾动式精炼炉是20世纪60年代中期,由 瑞士人研究发明的。它是在反射炉和回 转炉基础上,吸取了两种炉型的长处而 设计的。炉膛形状像反射炉,保持较大 的换热面积,采取了回转炉可转动的方 式,增设了固定风口,取消了插风管和 扒渣作业,减轻了劳动强度,既能处理 热料又能处理冷料。倾动炉由炉基、摇 座、炉体、驱动装置、燃烧器及燃烧室 组成。炉基由耐热钢筋混凝土筑成,在 炉基上装设钢结构摇座,摇座上沿为圆 弧形,装有若干个滚轮。炉体底部也是 圆弧形,座在摇座上。液压缸底部装在 基础上,上部与炉底底部连接。伸缩液 压缸带动炉体倾动,倾动角度为±300 , 有快慢两种倾转速度,氧化、还原、倒 渣用快速倾转,浇铸用慢速倾转。
四、反射炉生产的基本原理
• 粗铜火法精炼在反射炉内进行,可以分为进料、熔化、氧 化、扒渣、还原、浇铸五个阶段。 • 氧化基本原理:氧化过程实质上是依据不同元素对氧的 亲和力大小不同的性质将压缩空气通入铜熔体中,利用空 气中的氧将硫及部份杂质氧化造渣或以气态形式挥发除去 的过程。铜熔体中元素对氧的亲和力从大到小排列顺序为: 铝、硅、锰、锌、铁、镍、砷、锑、铅、硫、铋、铜、银、 金、硒、碲。但铜熔体中铜占绝大多数,故铜与氧的接触 机率远远大于氧与杂质的接触,铜首先发生氧化作用生成 Cu2O随着熔体中Cu2O浓度的升高,Cu2O与金属杂质发生 反应,杂质氧化造渣/挥发除去,Cu2S与Cu2发生交互反应 生成SO2挥发除去其,基本反应式如下: 4Cu+O2=2Cu2O [Cu2O]+[Me’]=2[Cu]+[Me’O] Cu2S+2Cu2O=6[Cu]+SO2↑ • 式中:[Me’]——金属杂质。 [Me’O]——金属氧化物。