橡胶制品产生的气泡原因分析
硅胶产生气泡的原因
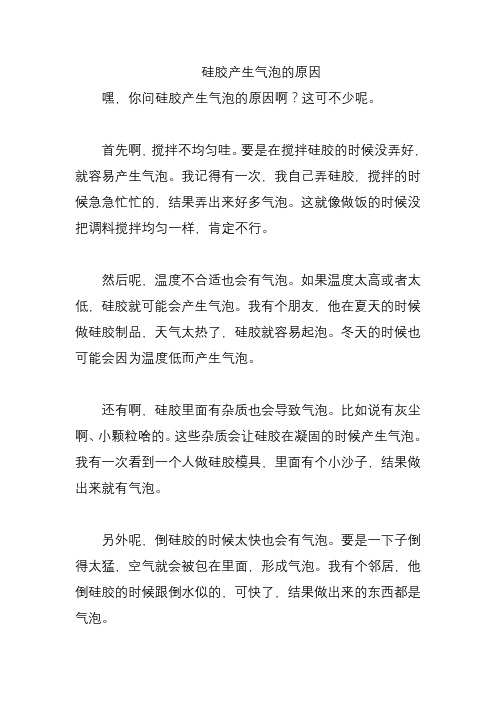
硅胶产生气泡的原因
嘿,你问硅胶产生气泡的原因啊?这可不少呢。
首先啊,搅拌不均匀哇。
要是在搅拌硅胶的时候没弄好,就容易产生气泡。
我记得有一次,我自己弄硅胶,搅拌的时候急急忙忙的,结果弄出来好多气泡。
这就像做饭的时候没把调料搅拌均匀一样,肯定不行。
然后呢,温度不合适也会有气泡。
如果温度太高或者太低,硅胶就可能会产生气泡。
我有个朋友,他在夏天的时候做硅胶制品,天气太热了,硅胶就容易起泡。
冬天的时候也可能会因为温度低而产生气泡。
还有啊,硅胶里面有杂质也会导致气泡。
比如说有灰尘啊、小颗粒啥的。
这些杂质会让硅胶在凝固的时候产生气泡。
我有一次看到一个人做硅胶模具,里面有个小沙子,结果做出来就有气泡。
另外呢,倒硅胶的时候太快也会有气泡。
要是一下子倒得太猛,空气就会被包在里面,形成气泡。
我有个邻居,他倒硅胶的时候跟倒水似的,可快了,结果做出来的东西都是气泡。
还有哦,硅胶的质量也有关系。
如果买的硅胶质量不好,就容易产生气泡。
我有一次买了便宜的硅胶,结果做出来全是气泡,后来换了好一点的硅胶就好了。
我给你讲个事儿吧。
有一次我去一个工厂,看到他们在做硅胶产品。
有一批产品就有很多气泡,后来一检查,发现是搅拌不均匀,温度也有点高。
从那以后,他们就注意这些问题了。
所以啊,硅胶产生气泡的原因有搅拌不均匀、温度不合适、有杂质、倒得太快、质量不好等。
下次你用硅胶的时候,可别犯这些错误哦。
橡胶挤出缺陷的原因
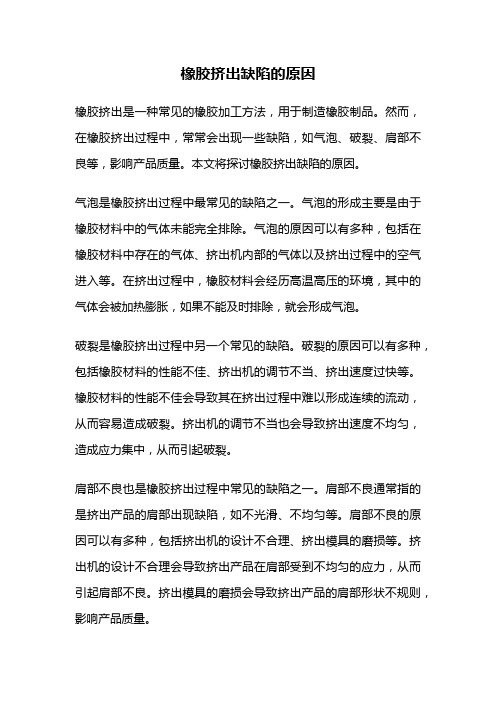
橡胶挤出缺陷的原因橡胶挤出是一种常见的橡胶加工方法,用于制造橡胶制品。
然而,在橡胶挤出过程中,常常会出现一些缺陷,如气泡、破裂、肩部不良等,影响产品质量。
本文将探讨橡胶挤出缺陷的原因。
气泡是橡胶挤出过程中最常见的缺陷之一。
气泡的形成主要是由于橡胶材料中的气体未能完全排除。
气泡的原因可以有多种,包括在橡胶材料中存在的气体、挤出机内部的气体以及挤出过程中的空气进入等。
在挤出过程中,橡胶材料会经历高温高压的环境,其中的气体会被加热膨胀,如果不能及时排除,就会形成气泡。
破裂是橡胶挤出过程中另一个常见的缺陷。
破裂的原因可以有多种,包括橡胶材料的性能不佳、挤出机的调节不当、挤出速度过快等。
橡胶材料的性能不佳会导致其在挤出过程中难以形成连续的流动,从而容易造成破裂。
挤出机的调节不当也会导致挤出速度不均匀,造成应力集中,从而引起破裂。
肩部不良也是橡胶挤出过程中常见的缺陷之一。
肩部不良通常指的是挤出产品的肩部出现缺陷,如不光滑、不均匀等。
肩部不良的原因可以有多种,包括挤出机的设计不合理、挤出模具的磨损等。
挤出机的设计不合理会导致挤出产品在肩部受到不均匀的应力,从而引起肩部不良。
挤出模具的磨损会导致挤出产品的肩部形状不规则,影响产品质量。
除了以上几种常见的缺陷外,还有一些其他缺陷也会在橡胶挤出过程中出现。
例如,表面粗糙、收缩、断面不均匀等。
这些缺陷的形成原因各不相同,但都与橡胶挤出过程中的操作参数、材料性能以及挤出设备的状态有关。
为了避免橡胶挤出过程中的缺陷,可以采取一些措施。
首先,要选择合适的橡胶材料,确保其性能符合产品要求。
其次,要合理调节挤出机的操作参数,如温度、压力、速度等,以保证橡胶材料能够均匀流动。
此外,还需要定期检查和维护挤出设备,确保其状态良好。
橡胶挤出缺陷的原因包括气泡、破裂、肩部不良等。
这些缺陷的形成与橡胶材料的性能、挤出机的调节、挤出过程的操作等有关。
为了避免这些缺陷的出现,可以采取合适的措施,如选择合适的橡胶材料、合理调节挤出机的操作参数以及定期检查和维护挤出设备。
注塑常见缺陷和原因分析
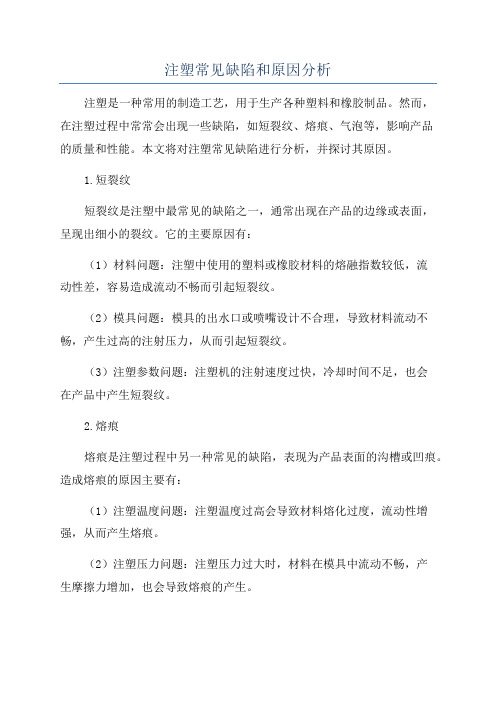
注塑常见缺陷和原因分析注塑是一种常用的制造工艺,用于生产各种塑料和橡胶制品。
然而,在注塑过程中常常会出现一些缺陷,如短裂纹、熔痕、气泡等,影响产品的质量和性能。
本文将对注塑常见缺陷进行分析,并探讨其原因。
1.短裂纹短裂纹是注塑中最常见的缺陷之一,通常出现在产品的边缘或表面,呈现出细小的裂纹。
它的主要原因有:(1)材料问题:注塑中使用的塑料或橡胶材料的熔融指数较低,流动性差,容易造成流动不畅而引起短裂纹。
(2)模具问题:模具的出水口或喷嘴设计不合理,导致材料流动不畅,产生过高的注射压力,从而引起短裂纹。
(3)注塑参数问题:注塑机的注射速度过快,冷却时间不足,也会在产品中产生短裂纹。
2.熔痕熔痕是注塑过程中另一种常见的缺陷,表现为产品表面的沟槽或凹痕。
造成熔痕的原因主要有:(1)注塑温度问题:注塑温度过高会导致材料熔化过度,流动性增强,从而产生熔痕。
(2)注塑压力问题:注塑压力过大时,材料在模具中流动不畅,产生摩擦力增加,也会导致熔痕的产生。
(3)模具设计问题:如果模具中的出水口或喷嘴设计不合理,也会在产品表面形成熔痕。
3.气泡气泡是注塑中常见的缺陷,表现为产品内部或表面的空腔。
气泡的形成原因有:(1)材料问题:注塑材料中含有过多的水分或挥发性物质,注塑过程中被加热蒸发,生成气泡。
(2)注塑温度过高:高温会导致材料熔化过度,容易产生气泡。
(3)注塑压力问题:过高的注塑压力会使材料在注塑过程中产生剧烈的振动,从而引起气泡。
(4)模具问题:模具中存在堵塞或不良的冷却系统,也会导致气泡的产生。
4.缩短问题缩短是指产品在冷却过程中出现尺寸缩小的现象。
产生缩短的主要原因有:(1)注塑温度过低:低温会使注塑材料的熔融程度不足,流动性降低,产生缩短。
(2)冷却时间不足:注塑材料冷却时间不足会导致产品未完全固化,容易产生缩短。
(3)注塑压力问题:过大的注塑压力会使产品产生内部的应力,引起尺寸缩小。
(4)模具问题:模具中存在过多的冷却系统,会导致材料过度冷却而使产品缩短。
橡胶产品基本缺陷产生原因及解决措施

浇口设计不合理
浇口设计不合理,导致充型困难或产 生气孔等缺陷。
模具加工精度低
模具加工精度不高
导致模具配合不良,出现飞边、 溢料等问题。
模具表面粗糙
模具表面粗糙导致制品表面质量差 。
模具材料不当
使用不当材料制作模具,导致制品 不符合要求。
设备性能不良
注射机精度不高
注射机精度不高,导致注射不稳 定,制品出现气泡、银纹等缺陷
配方比例不当
橡胶配方中各种原材料的 比例不当,会影响橡胶产 品的性能。
配方设计不合理
硫化体系不合理
硫化体系是橡胶配方设计 的重要部分,硫化剂、促 进剂等配比不当,会影响 橡胶产品的性能。
补强体系不合理
补强剂的种类和用量不当 ,会影响橡胶产品的强度 和耐磨性等性能。
增塑体系不合理
增塑剂的种类和用量不当 ,会影响橡胶产品的柔软 度和耐寒性等性能。
建立完善的设备维护和保养制度 ,定期对设备进行检查、维修和
更换。
保持生产环境的清洁和卫生,减 少污染和杂质对产品质量的影响
。
加强产品使用及环境监控
对产品使用进行严格的监管和控制,避免滥用和误用。 对产品使用环境进行评估和监控,确保其符合产品要求。
建立完善的质量检测和监控体系,对产品进行定期检查和测试。
压力不均
总结词
压力不均是指在橡胶加工过程中,压力 分布不均匀,导致橡胶制品出现鼓包、 厚度不均等问题。
VS
详细描述
压力不均的原因包括模具设计不合理、压 力控制不稳定、注射速度过快或过慢等。 此缺陷会导致橡胶制品形状变形、精度降 低,影响使用性能和外观质量。
时间控制不当
总结词
时间控制不当是指在橡胶加工过程中,时间控制过长或过短,导致橡胶制品出现老化、不耐用等问题。
橡胶产品表面有气泡的原因分析

橡胶产品表面有气泡的原因分析橡胶硫化后样品表面总是有些气泡,大小不等,切开后,样品中间也有少数气泡。
橡胶产品表面有气泡的原因分析
1、橡胶混炼不均匀,操作工不规范。
2、橡胶胶片停放不规范,环境不卫生。
管理不规范。
3、材料有水份(混炼时加点氧化钙)
4、硫化不充分,不熟看起来有气泡。
5、硫化压力不足。
6、硫化剂杂质较多,小分子的杂质提前变成分解,气泡残留制品中
7、模具本身排气设计不合理,胶料冲线时气不能及时排出!
8. 制品太厚,胶料过少,橡胶传热慢,外表硫化后,橡胶流动性下降,造成缺料,所以就可能产生气泡。
9.硫化过程中排气没排好。
10、配方问题,硫化体系要改善。
解决办法:
在硫化压力和时间上加以改善
1、延长硫化时间或提高硫化速度。
2、硫化前薄通几次。
3、硫化时排气次数多一点。
—1 —。
橡胶产品基本缺陷产生原因及解决措施

•引言•橡胶产品常见缺陷概述•产生缺陷的原因分析•解决措施及建议目•案例分析与应用•结论与展望录背景介绍本文旨在分析橡胶产品生产过程中可能出现的缺陷及其产生原因,并提出相应的解决措施。
这有助于提高产品质量、降低生产成本、增强市场竞争力,同时保障使用安全。
通过深入探讨和研究,我们将更好地了解橡胶产品的性能和特点,为进一步优化其生产工艺和提高产品质量提供理论支持和实践指导。
目的和意义原因原材料中含有水分或挥发性物质硫化过程中产生的气体未完全排胶料混合不均匀或炼胶时间过长解决措施确保原材料干燥、无挥发性物质优化硫化工艺,增加排气时间控制炼胶时间和温度,确保胶料混合均匀原因橡胶老化或劣化应力集中或外部应力作用02030102030430102 030102橡胶硬度不均优化橡胶制品结构设计,确保厚度均匀和稳定性橡胶材料质量差配合剂问题填充剂问题030201材料因素加工工艺不合理模具设计不当设备问题人员操作问题材料选择与控制是解决橡胶产品基本缺陷的重要手段之一。
详细描述应基于产品的性能要求和工艺条件,选择适宜的橡胶材料,并严格控制其成分和性能指标,避免因材料问题而导致缺陷的产生。
对于重要的橡胶部件,可以考虑添加适量的增塑剂、补强剂、抗氧剂等助剂,以改善其加工性能和耐久性。
总结词材料选择与控制VS工艺优化及改进总结词详细描述其他措施和建议总结词详细描述针对以上原因,可以采取以下措施:严格控制原材料的质量和配方;适当延长硫化时间;优化模具设计,确保模具排气顺畅。
案例一:某橡胶密封圈的气泡问题解决措施解决措施原因原因橡胶轮胎出现龟裂可能是由于原材料质量问题、硫化时间不当、氧化老化、使用环境恶劣等因素导致的。
要点一要点二解决措施为改善橡胶轮胎的龟裂问题,可以采取以下措施:严格把控原材料的质量和配方;合理调整硫化时间;加强生产过程中的质量控制和老化试验;提高产品的抗老化性能和使用寿命;同时,在使用过程中定期检查和维护。
PVC胶产生气泡的原因及控制措施

PVC胶产生气泡的原因及控制措施
首先,材料的问题是引起PVC胶产生气泡的主要原因之一、PVC材料
中可能含有水分、溶剂、挥发物等揮發性物质,在胶料制备过程中,这些
物质会释放出来,产生气泡。
此外,如果使用的PVC材料本身质量不过关,可能会含有较多的杂质,这些杂质在加工过程中也会形成气泡。
其次,工艺问题也是导致PVC胶产生气泡的原因之一、例如,当工作
温度过高时,胶料中的挥发物会挥发得更快,导致产生气泡的概率增加。
此外,如果搅拌不充分,胶料中的杂质无法得到均匀分散,也容易形成气泡。
为了控制PVC胶产生气泡,可以考虑以下措施:
1.优化材料选择:选用质量可靠的PVC材料,减少杂质的含量,降低
材料中挥发性物质的含量。
慎重选择添加剂,并确保其质量可靠。
2.控制工艺参数:合理控制胶料的加工温度和时间,避免过高的温度,适当延长加工时间,确保材料充分熔融,挥发物释放均匀。
3.充分搅拌:确保胶料在制备过程中充分搅拌,使其内部的杂质得到
均匀分散,减少气泡产生的可能性。
4.提高工作环境的控制:尽量控制制备PVC胶的工作环境中的湿度,
避免湿气进入胶料中引起气泡。
保持相对稳定的温湿度,符合制备要求。
5.完善包装条件:在包装过程中,尽量避免产生气泡过程,并采取措
施确保胶料包装密封,防止外界湿气和杂质污染导致密封措施破裂。
总之,对于PVC胶产生气泡的原因和控制措施,需要从材料的选择、工艺参数的控制以及工作环境的管理等多个方面进行综合考虑和改进,以减少气泡产生,提高产品的质量。
硅胶 低温 气泡

硅胶低温气泡
硅胶在低温下可能会产生气泡,主要原因有以下几点:
1.排气不足:在硅胶原料放置于成型模具后,如果排气处理不当,可能导致空气被困在硅胶原料中,从而在成型后产生气泡。
2.硫化温度过低:硫化温度是硅橡胶成型的重要参数,通常设定在160~200℃。
但当硫化温度过低时,会导致成型时间延长,硅胶在未完全硫化的情况下易产生气泡。
3.硫化温度过高:过高的硫化温度可能使硅胶原料在成型过程中就开始硬化,导致空气被困在硅胶原料中,从而产生气泡。
4.硫化时间过短:硫化时间的长短决定了硅胶能否被完全硫化,时间过短可能导致部分硅胶未完全硫化,从而产生气泡。
5.配合剂问题:某些配合剂,特别是增塑剂(包括软化剂),在硅胶中可能会产生气泡。
这是因为这些配合剂含有低温挥发物和水份,当温度升高时,这些物质可能会挥发或产生气体,导致硅胶中出现气泡。
为了减少硅胶中的气泡,可以采取以下措施:
1.优化模具设计,使模具具有合理的气孔位置和足够的排气孔数,以及保证胶料在模具中能均匀受热受压。
2.控制硫化温度和时间,使其达到最佳的硫化状态。
3.控制填料的粒径和添加量,减少填料与其它组分产生
的化学反应。
4.避免使用含有易挥发物质或易产生气体的配合剂。
5.在生产过程中加强操作和管理,避免混入杂质或空
气。
6.对于已经产生气泡的硅胶制品,可以通过后处理如热
处理、真空处理等方式来减少气泡。
总之,要减少硅胶中的气泡,需要从原料、配方、生产工艺和设备等方面进行综合考虑和优化。
最全橡胶模压制品常见问题与解决方案
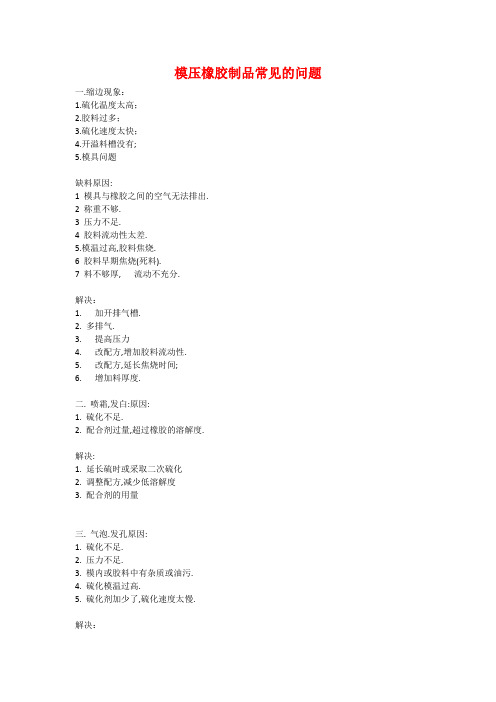
模压橡胶制品常见的问题一.缩边现象:1.硫化温度太高;2.胶料过多;3.硫化速度太快;4.开溢料槽没有;5.模具问题缺料原因:1 模具与橡胶之间的空气无法排出.2 称重不够.3 压力不足.4 胶料流动性太差.5.模温过高,胶料焦烧.6 胶料早期焦烧(死料).7 料不够厚, 流动不充分.解决:1. 加开排气槽.2. 多排气.3. 提高压力4. 改配方,增加胶料流动性.5. 改配方,延长焦烧时间;6. 增加料厚度.二. 喷霜,发白:原因:1. 硫化不足.2. 配合剂过量,超过橡胶的溶解度.解决:1. 延长硫时或采取二次硫化2. 调整配方,减少低溶解度3. 配合剂的用量三. 气泡.发孔原因:1. 硫化不足.2. 压力不足.3. 模内或胶料中有杂质或油污.4. 硫化模温过高.5. 硫化剂加少了,硫化速度太慢.解决:1. 加压2. 加长硫时3 . 调整配方,加快硫化速度.4. 多排气.5. 模温不能过高.6. 增加硫化剂用量.四. 重皮.开裂原因:1. 硫化速度太快,胶流动不充分.2. 模具脏或胶料粘污迹.3. 隔离剂或脱模剂太多4. 胶料厚度不够.解决:1. 降低模温,减慢硫化速度.2. 保持胶料.模具清洁.3. 少用隔离剂或脱模剂.4. 胶料够厚.五. 产品脱模破裂原因:1. 模温过高或者硫时过长.2. 硫化剂用量过多.3. 脱模方法不对.解决措施:1. 降低模温.2. 缩短硫时.3. 减少硫化剂用量.4. 喷脱模剂.5. 采取正确的脱模方法.六. 难加工原因:1. 产品撕裂强度太好,(如高拉力胶).这种难加工表现为毛边撕不下来.2. 产品强度太差,表现为毛边很脆,会连产品一起撕破.解决措施:1. 如果是撕不掉, 就得调整配方,多填充配合剂,减小收缩率.2. 如果是撕破,a 降低模温,缩短硫时.b 减少硫化剂用量.c 调整配方,增加胶料强度..。
硅胶管在生产过程中会不会出现气泡?

硅胶管产生气泡的原因
1、气体是在加工过程中混入胶料的,还有是填料吸附的水分,填料内部孔洞附带的空气,在加热后就会膨胀溢出。
2、气体溢出后如果橡胶没有开始交联,气体就会顺着胶料的膨胀排出模具。
3、如果橡胶交联完成,气体的流动被限制,不能形成可以看见的气泡、微孔,但气体还在。
4、如果橡胶制品的外部硫化完成,内部尚未达到正硫化,在模具压力松开后,内部的气体流动聚集形成微孔。
2、低温短时间硫化,胶料部分交联,气体不能完全排出,气泡就产生了,此时的气泡多在制品表面。
3、高温短时间,尤其是对厚制品,表面已完成硫化,内部刚刚开始,泄压后内部气体膨胀,此时的气泡多在制品中心。
4、高温长时间,制品内部的气体被压制,表观上没有缺陷,但微观上气体一直存在于橡胶内部,容易产生较多的缺陷,物理性能不高。
硅胶管在生产过程中会不会出现气泡?
硅胶管在生产技术不好的情况下会出现气泡,出现气泡的原因和形式有那几种?下面奇裕小编将为大家讲解出现气泡的原因和形式有那几种,希望能帮助遇到这些问题不知道怎么解决的人。
硅胶管产生气泡的几种形式。
1、低温长时间硫化,胶料受热时间长,硫化起步慢,,气体有足够的时间排出模具,此时橡胶内部的缺陷较少,硫化后的物理性能较高。
深圳奇裕硅橡胶有限公司,专注品质十多品问题都能很好解决,如果有什么疑问可以咨询。
喜欢本文或觉得本文对您有帮助,请分享给您的朋友 ^_^
橡胶制品常见问题及解决方法
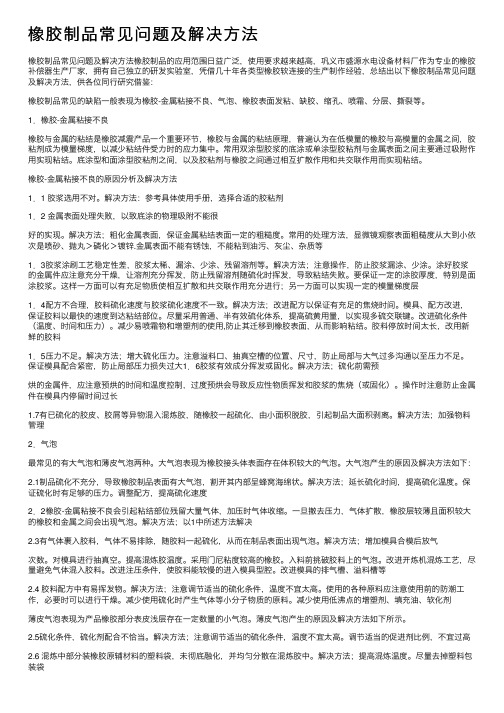
橡胶制品常见问题及解决⽅法橡胶制品常见问题及解决⽅法橡胶制品的应⽤范围⽇益⼴泛,使⽤要求越来越⾼,巩义市盛源⽔电设备材料⼚作为专业的橡胶补偿器⽣产⼚家,拥有⾃⼰独⽴的研发实验室,凭借⼏⼗年各类型橡胶软连接的⽣产制作经验,总结出以下橡胶制品常见问题及解决⽅法,供各位同⾏研究借鉴:橡胶制品常见的缺陷⼀般表现为橡胶-⾦属粘接不良、⽓泡、橡胶表⾯发粘、缺胶、缩孔、喷霜、分层、撕裂等。
1.橡胶-⾦属粘接不良橡胶与⾦属的粘结是橡胶减震产品⼀个重要环节,橡胶与⾦属的粘结原理,普遍认为在低模量的橡胶与⾼模量的⾦属之间,胶粘剂成为模量梯度,以减少粘结件受⼒时的应⼒集中。
常⽤双涂型胶浆的底涂或单涂型胶粘剂与⾦属表⾯之间主要通过吸附作⽤实现粘结。
底涂型和⾯涂型胶粘剂之间,以及胶粘剂与橡胶之间通过相互扩散作⽤和共交联作⽤⽽实现粘结。
橡胶-⾦属粘接不良的原因分析及解决⽅法1.1 胶浆选⽤不对。
解决⽅法:参考具体使⽤⼿册,选择合适的胶粘剂1.2 ⾦属表⾯处理失败,以致底涂的物理吸附不能很好的实现。
解决⽅法;粗化⾦属表⾯,保证⾦属粘结表⾯⼀定的粗糙度。
常⽤的处理⽅法,显微镜观察表⾯粗糙度从⼤到⼩依次是喷砂、抛丸>磷化>镀锌.⾦属表⾯不能有锈蚀,不能粘到油污、灰尘、杂质等1.3胶浆涂刷⼯艺稳定性差,胶浆太稀、漏涂、少涂、残留溶剂等。
解决⽅法;注意操作,防⽌胶浆漏涂、少涂。
涂好胶浆的⾦属件应注意充分⼲燥,让溶剂充分挥发,防⽌残留溶剂随硫化时挥发,导致粘结失败。
要保证⼀定的涂胶厚度,特别是⾯涂胶浆。
这样⼀⽅⾯可以有充⾜物质使相互扩散和共交联作⽤充分进⾏;另⼀⽅⾯可以实现⼀定的模量梯度层1.4配⽅不合理,胶料硫化速度与胶浆硫化速度不⼀致。
解决⽅法;改进配⽅以保证有充⾜的焦烧时间。
模具、配⽅改进,保证胶料以最快的速度到达粘结部位。
尽量采⽤普通、半有效硫化体系,提⾼硫黄⽤量,以实现多硫交联键。
改进硫化条件(温度、时间和压⼒)。
减少易喷霜物和增塑剂的使⽤,防⽌其迁移到橡胶表⾯,从⽽影响粘结。
胶膜气泡的原因

胶膜气泡的原因
胶膜气泡的原因有多种,主要包括以下几点:
1.胶膜质量不佳,含有过多的水分、空气或杂质,导致胶膜在热压过程中不
能完全融合,从而产生气泡。
2.胶膜的存放环境湿度过高,或者在加工过程中,胶膜暴露在空气中时间过
长,导致胶膜表面氧化或者吸湿,使得胶膜在热压过程中不能完全融合,从而产生气泡。
3.胶膜的热压温度、压力和时间等工艺参数控制不当,也会导致胶膜气泡的
产生。
例如,温度过高或过低、压力过小或过大、时间过短或过长等,都可能导致胶膜气泡的产生。
4.在使用胶膜时,由于人为操作不当或者设备故障等原因,导致胶膜表面被
划伤、污染或者破损等,也会导致胶膜气泡的产生。
为了避免胶膜气泡的产生,可以采取以下措施:
1.选择质量优良的胶膜,避免使用含有过多水分、空气或杂质的胶膜。
2.保持胶膜的存放环境干燥、清洁,避免胶膜长时间暴露在空气中,或者在
加工过程中采取适当的保护措施,防止胶膜氧化或吸湿。
3.控制好热压温度、压力和时间等工艺参数,根据胶膜的种类和规格选择合
适的工艺参数。
4.在使用胶膜时,注意操作方法,避免划伤、污染或破损胶膜表面。
5.如果发现胶膜气泡问题严重,可以尝试采用贴合前对胶膜进行预热、增加
压力等措施,以促进胶膜的融合和排除气体。
如果气泡数量过多或过大,可能需要重新选择合适的胶膜或者进行返工处理。
pur胶管中的气泡
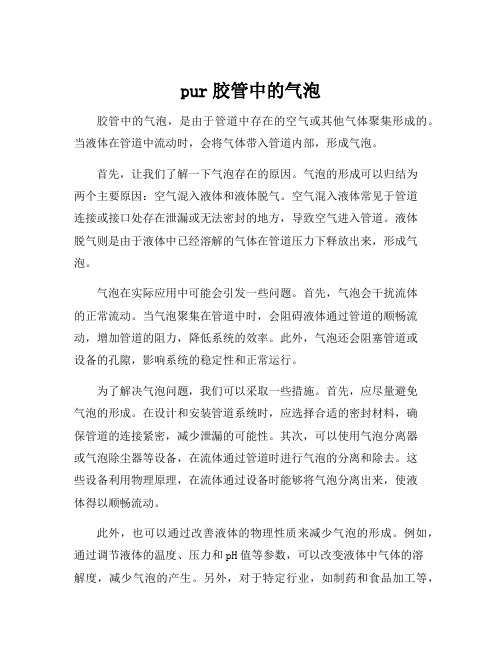
pur胶管中的气泡胶管中的气泡,是由于管道中存在的空气或其他气体聚集形成的。
当液体在管道中流动时,会将气体带入管道内部,形成气泡。
首先,让我们了解一下气泡存在的原因。
气泡的形成可以归结为两个主要原因:空气混入液体和液体脱气。
空气混入液体常见于管道连接或接口处存在泄漏或无法密封的地方,导致空气进入管道。
液体脱气则是由于液体中已经溶解的气体在管道压力下释放出来,形成气泡。
气泡在实际应用中可能会引发一些问题。
首先,气泡会干扰流体的正常流动。
当气泡聚集在管道中时,会阻碍液体通过管道的顺畅流动,增加管道的阻力,降低系统的效率。
此外,气泡还会阻塞管道或设备的孔隙,影响系统的稳定性和正常运行。
为了解决气泡问题,我们可以采取一些措施。
首先,应尽量避免气泡的形成。
在设计和安装管道系统时,应选择合适的密封材料,确保管道的连接紧密,减少泄漏的可能性。
其次,可以使用气泡分离器或气泡除尘器等设备,在流体通过管道时进行气泡的分离和除去。
这些设备利用物理原理,在流体通过设备时能够将气泡分离出来,使液体得以顺畅流动。
此外,也可以通过改善液体的物理性质来减少气泡的形成。
例如,通过调节液体的温度、压力和pH值等参数,可以改变液体中气体的溶解度,减少气泡的产生。
另外,对于特定行业,如制药和食品加工等,可以采用真空抽取的方法,在液体中引入负压,促使气泡脱气,减少气体的存在。
总之,了解气泡在胶管中的形成原因及其对系统的影响,选择适当的措施来减少和排除气泡,对于维持管道系统的正常运行至关重要。
同时,在管道系统的设计和安装中要做好密封工作,严防泄漏。
此外,定期检查管道系统,清除积存的气泡,保持系统的畅通与高效。
橡胶起泡后的解决方法

橡胶起泡后的解决方法
橡胶起泡一般是由于橡胶中的气体被加热后膨胀引起的。
对于橡胶起泡的解决方法可以有以下几种:
1. 控制生产工艺:在橡胶制造过程中,对于橡胶的加热过程要进行控制,避免过高的温度或加热时间过长,造成橡胶起泡问题。
2. 选择合适的橡胶原料:在选择橡胶原料的时候,要注意橡胶的热稳定性,选择具有较高热稳定性的橡胶原料,可以减少橡胶起泡的概率。
3. 添加抗起泡剂:在橡胶制造过程中,可以添加一定的抗起泡剂,如硅油、矽烷等,来防止橡胶起泡问题的发生。
4. 进行热收缩处理:对于已经起泡的橡胶制品,可以进行热收缩处理,即在一定的温度下加热后收缩,使得橡胶中的气泡被挤出,从而减少橡胶的起泡情况。
需要注意的是,具体的解决方法要根据起泡问题的具体情况来确定,建议在实际工作中根据实际情况进行分析和解决。
8挤出工艺中出现气泡与海绵的质量问题形成原因及改进措施

8挤出工艺中出现气泡与海绵的质量问题形成原因及改进措
施
一、原因分析
1、原材料中的水分和挥发分过多或者挤出机温度过高导致配合剂分解,致使胶料中的气体在口型,机筒中不断被排出,在挤出半成品中产生气孔。
2、半成品挤出速度过快,胶料中的空气来不及排出。
3、密炼机转子或者挤出机漏水。
4、挤出机螺杆与衬套间隙超标。
5、胶料塑性低,挤出机供胶量不足,胶料密实性差,造成机头压力低。
6,挤出机头温度过高。
二、解决方法
1、严把原材料质量关,重点检查生胶,炭黑等主要原材料的挥发分和水分含量,杜绝水分和挥发分含量超标的原材料投入使用。
2、适当降低挤出速度,确保滞留在胶料和挤出口型中的气体可以顺利排出。
3、严格控制混炼胶质量,确保使用的混炼胶性能符合加工和使用要求。
4、监控设备运行情况,严防密炼机转子和挤出机漏水。
5、检查挤出机螺杆与衬套间隙是否超标,如果间隙过大需要更换衬套。
6、规范热炼操作方法,严格按照工艺要求设定热炼辑距,辗温以及时间,监控挤出喂料情况,严防出现供料间断,空车,滞料和供料不均现象。
7、加大橡胶挤出机以及辅助设备的检修频次,确保工艺参数和感应装置准确无误。
硅橡胶制品压延生产可能遇到的问题及解决措施

硅橡胶制品压延生产可能遇到的问题及解决措施
硅橡胶制品压延生产是一种重要的生产工艺,在生产过程中可能会遇到一些问题,下面介绍几个可能的问题及解决措施:
1. 压延出现气泡:气泡是由于硅橡胶与辊子之间的空气没有被排出而造成的。
解决方法是在硅橡胶表面喷洒一些减摩剂,减少空气的粘附,然后逐渐加压,使空气逐渐排出。
2. 压延后产生翘曲变形:翘曲变形是由于硅橡胶在压延过程中受到的压力不均匀,使得硅橡胶产生了内部应力。
解决方法是在压延前先进行预压,使硅橡胶中的气泡排出,并且在压延过程中要保证辊子之间的间距均匀。
3. 硅橡胶表面出现条纹:条纹是由于辊子之间的温度不均匀、压力不均匀等原因造成的。
解决方法是要保证辊子表面的温度均匀,调整辊子的压力,使得硅橡胶在压延过程中受到的压力均匀。
4. 硅橡胶表面出现氧化现象:氧化是由于硅橡胶在空气中长时间暴露产生的。
解决方法是在生产过程中加入抗氧剂,保证硅橡胶不会长时间暴露在空气中。
总之,硅橡胶制品压延生产过程中可能会遇到各种问题,需要根据具体情况进行解决。
在生产过程中,要保证设备的正常运行,加强质量管理,保证产品的质量。
- 1 -。
PVC胶产生气泡的原因及控制措施

PVC胶产生气泡的原因及控制措施PVC胶产生气泡是由于胶料中的气体在加热、压力或一些化学反应条件下被释放出来,形成小气泡或大气泡的现象。
气泡在PVC胶料中是一种常见的缺陷,会影响产品的外观、性能和使用寿命。
下面将介绍PVC胶产生气泡的几种常见原因及相应的控制措施。
一、原材料中的成分1.添加剂:PVC胶料中的添加剂可能会产生气泡。
例如,过量的起泡剂添加剂会导致气泡的生成。
处理方法是需严格按照配方要求控制添加剂的用量,并进行充分的混合和分散。
2.高分子物质:PVC胶料中的高分子物质含有一定量的残余溶剂或气体,这些溶剂或气体有可能在加热或加压过程中逸出。
在使用高分子物质时,要选择符合标准的品牌,并注意对其进行预处理以去除溶剂。
3.PVC树脂:PVC树脂的纯度和分子量也会对气泡的产生产生一定影响。
选择高纯度和分子量合适的PVC树脂可以有效地减少气泡的生成。
二、加工过程中的因素1.加热过程:加热不均匀或温度过高都可能导致PVC胶料产生气泡。
加热设备应调整加热区域的温度均匀性,并且按照合适的温度和时间进行加热,以避免气泡产生。
2.压力控制:过高的压力会导致PVC胶料中的气体无法逸出,从而产生气泡。
应对压力进行合理的控制,避免过高的压力。
3.冷却过程:PVC胶料在冷却过程中,如果速度过快或温度过低,也容易产生气泡。
应根据胶料的特性和加工过程的要求,采取适当的冷却措施,保持恰当的冷却速度和温度。
三、设备和环境因素1.设备:设备的质量和性能会对PVC胶产生气泡产生影响。
应选择适用的设备,并保持设备的良好状态,定期进行维护。
2.环境:工作环境中的湿度和温度都可能引起气泡的产生。
要根据不同的工艺要求和材料特性,保持合适的环境条件。
四、其他因素1.工艺参数:工艺参数的调整会对气泡产生产生重要影响。
应根据具体情况来调整各项参数,包括温度、时间、压力等。
2.气体排除:在PVC胶料中注入气体的处理方式也会影响气泡的产生。
应合理设计气体排除结构和顺序,确保气体能够及时有效地排出。
橡胶发泡(小知识)

小知识---橡胶硫化中的发泡现象自然界中各种物体都含有气体,无论是液体、固体内。
液体会蒸发气化、固体会升华,皆会产生气体。
因此如液体内除了自身的气体物外还带有其他类气体物质,最简单的例子是鱼类常年生活在水中,它们就是靠呼吸水中的空气(氧气);同样固体内也会有气体物质,但固体含有气体的现象难以确定,往往会被忽视(人们的嗅觉,视觉仅能感觉到有味有色的气体)。
气体有其独特的可压缩性,受热会膨胀撑大液体介质或固体介质,介质有一定的伸张本领,因此会形成气泡;当气体因膨胀的压力超过介质的伸张强度,气泡就破裂。
而我们所看到的发泡形成的气孔均为气体压力未超过介质的伸张强度。
日常看到的爆米花,膨化食品,海绵制品,水泥发泡材料,金属发泡材料等,均采用各种手段使介质内所含的气体膨胀发泡。
橡胶制成的混炼胶在加工过程中均会产生发泡现象,譬如胶料的混炼、热炼、挤出出型等,因加工中胶料温度的升高,所含气体欲膨胀,但在较高压力下是溶于胶内,当突然减压,如胶料离开辊筒之间的受力面、离开挤出口等,气体因内压而膨胀发泡,形成气孔。
当然炼胶过程中出现的气孔主要来自湿气及低挥发物,但也含有裹挟的空气等其他气体。
在硫化中橡胶也会发泡,虽然硫化的温度较高,绝大部分的湿气及低挥发份从排气线中排除,但是溶于橡胶内的气体会在某个时间段发泡---即我们所关注的BP (发泡点),只有过了此BP 时间,胶料就不会发泡而形成气孔。
众所周知,橡胶的硫化历程是个粘度变化的过程,初始阶段因受热粘度降低,若此时停止加热硫化,胶料呈流动状,当到达时刻t B (t---时间,B---Bubble 泡,起泡时间),若此时中断硫化打开模具,就会发现发泡的气孔,而且泡较大,此时因粘度较低,易膨胀;到达时刻t BP ,(t---时间,BP---Blow Point发泡时间点),此时间为发泡终止时间,过了此时间继续硫化,胶料不会发泡,所含的气体皆被牢牢的囚禁在橡胶的交联网格内。
- 1、下载文档前请自行甄别文档内容的完整性,平台不提供额外的编辑、内容补充、找答案等附加服务。
- 2、"仅部分预览"的文档,不可在线预览部分如存在完整性等问题,可反馈申请退款(可完整预览的文档不适用该条件!)。
- 3、如文档侵犯您的权益,请联系客服反馈,我们会尽快为您处理(人工客服工作时间:9:00-18:30)。
一、模压制品产生气泡的原因分析:
主要原因有:
1、材料的问题,橡胶材料来混炼、储存、使用过程中有湿气,湿气未排除,导致产生气泡,或天气变化原因受潮。
大多数原因可能是原材料有问题,我们以前也出现过类似情况,换另外一个批次材料就好了;
2、模具排气孔设置不当或者堵塞也会产生气泡,排气的时候没有排好。
原材料在炼胶中,空气被裹附在材料内部,导致在加工的过程中,材料和空气一起进入模具,假如模具没加排气槽或加工中没有设置排气工艺的话,空气很容易被困在模具里面,使得产品产生气泡或气孔。
3、生产橡胶制品,硫化后有气泡,可能是橡胶配方中的问题,可以找技术人家给调整一下配方。
二、橡胶制品硫化时有气泡原因
1、橡胶混炼不均匀,操作工不规范。
2、橡胶胶片停放不规范,环境不卫生。
管理不规范。
3、材料有水份(混炼时加点氧化钙)
4、硫化不充分,不熟看起来有气泡。
5、硫化压力不足。
6、硫化剂杂质较多,小分子的杂质提前变成分解,气泡残留制品中
7、模具本身排气设计不合理,胶料冲线时气不能及时排出!
8. 制品太厚,胶料过少,橡胶传热慢,外表硫化后,橡胶流动性下降,造成缺料,所以就可能产生气泡。
9.硫化过程中排气没排好。
10、配方问题,硫化体系要改善。
解决办法:在硫化压力和时间上加以改善
1、延长硫化时间或提高硫化速度。
2、硫化前薄通几次。
3、硫化时排气次数多一点。
三、橡胶产品表面有气泡的原因分析
1.有水份(混炼时加点氧化钙);
2.未充分硫化,不熟看起来有气泡;
3.硫化剂杂质较多,小分子的杂质提前变成分解,气泡残留制品中;
4.模具本身排气设计不合理,胶料冲线时气不能及时排出;
5.分散不良;
6.胶料塑炼时间长,产品硫化时也有气泡。
四、硅胶成型产生气泡是什么原因呢?
1、排气不足,硅胶原料放置于成型模具后,在合模的瞬间会带入许多空气,而空气是不可能与硅胶原料融为一体的,如果没有将这些空气排放出来,就会造成硅胶按键成型后表面产生气泡。
2、硫化温度过低,硫化温度是硅橡胶成型时的一项重要参数,通常的硅胶制品都设定在160~200摄氏度,但有时候由于模外操作时间太长或其他原因使模具长时间未开入硫化机加温,导致硅胶成型模具的温度偏低与硅胶的硫化温度,此时就会造成成型后产品气泡。
对此我们只需加高成型温度,或者将空模开入机器加温一段时间在操作即可解决问题了。
3、硫化温度过高,刚刚说了硫化温度过低会造成硅胶成型气泡,其实,很多时候成型温度过高同样会造成硅胶成型气泡。
为什么呢?个人是这么理解的,成型温度过高时,在合模加压的过程中表面的硅胶原料已经开始成型,此时的空气已经被困在里面很难排出,所以会造成成型气泡。
针对此原因,只需将成型温度适当降低即可。
4、硫化时间过短,跟硫化温度一样,硫化时间也是硅胶成型的重要参数之一,硫化时间的长短决定了硅胶是否能被完全硫化。
如果硫化时间过短,不仅造成硅胶成型后发软,更容易造成表面气泡。
出现此类不良可适当延长硅胶的硫化时间。
5、模具的结构不合理,硅胶成型模具的设计不太合理也会造成硅胶成型产生气泡,例如模具中产品的排列方式、分区方式、模具分模方式,模具大小的设计等都会造成气泡不良,但开一套模具的成本很高,且修改起来也不太容易,如果因为模具的结构造成硅胶成型气泡,那么通常都是从上面所提到的几点想办法下手解决。
公司简介
佛山市南方橡塑有限公司成立于1986年,是一家从事研发和生产橡胶制品的技术型的生产企业,主要生产各类:橡胶模压制品、橡胶挤出制品、橡胶发泡制品、热塑性弹性体制品、软性PVC挤出制品、热塑性弹性体制品、密封条、硅胶管、发泡管、发泡条、EPDM胶条、橡胶管、橡胶挤出制品、橡胶发泡制品、密封圈、硅胶板等产品。
本公司是获得ISO9001:2000质量管理体系认证的生产研发型企业,为保证我们公司所生产的产品符合客户对原料到生产以及出货等环节的环保与技术要求(RoHS,FDA,UL等),公司对生产设备与产品研发技术、检测等部门的设备进行不断更新升级;为实现与配合客户产品的研发与功能的完善,公司独立设置了工程研发部门并为其配备了独立的产品设计开发实验室,独立的模具制作部门、配方试制室、理化试验室、模拟运输试验室、模拟生产实验室等,因此很多国内外客户选择我们公司成为他们的合作伙伴。
生产部门设备有油压橡胶硫化机、橡胶、橡塑挤出机及其连续硫化和连续生产线、试制和生产使用的开放式炼胶机、密封式炼胶机、模具制造专用的车床、铣床、磨床以及火花机等。
检测部门设备有拉力试验机、热空气老化试验箱、高温试验箱、火花试验机、耐电压测试仪、直流双臂电桥、投影仪、百分厚度计、邵尔硬度计、快速可塑测试机、阿克隆磨耗试验机、读数显微镜以及振台等。
检测部门设备有拉力试验机、热空气老化试验箱、高温试验箱、火花试验机、
耐电压测试仪、直流双臂电桥、投影仪、百分厚度计、邵尔硬度计、快速可塑测试机、阿克隆磨耗试验机、读数显微镜以及振台等。
(欢迎广大C新老客户来电、来邮、来图、来样定做各类橡胶橡塑制品,我们竭诚为您提供优质的产品和服务。
)我们将歇尽所能为客户提供质量放心和有保障的优质产品和服务!。