涵洞通道施工工法
(整理)涵洞通道工法

郑州至民权高速公路(郑州段)TJ-2合同段涵洞(通道)现浇混凝土墙身、台帽施工工法郑州至民权高速公路郑州段土建二标起讫桩号为K2+000-K13+000,全长11km,项目位于中牟境内。
本标段共有涵通道24道,其中通道16道,涵洞8道,根据本标段的设计情况,结合施工队伍安排,制定本工法。
一、特点1、提高了涵通道的砼外观质量,能够达到混凝土表面平整光滑,色泽均匀,无碰损和污染,对拉螺栓及施工缝的设置应整齐美观,且不出现普通混凝土的质量通病。
2、采用移模法施工,加快了施工进度。
3、施工工艺简单,施工质量可靠,施工安全。
二、适用范围各类涵洞通道现浇墙身的施工,现浇挡土墙、截水墙等也可参考使用。
三、工艺原理通过对模板的加工、拼接、立模进行严格的控制,对对拉螺栓的位置进行规整布置,对混凝土的制备和振捣进行控制,保证模板的刚度、强度、加工精度,保证模板表面平整、光滑、方正,接缝严密无漏浆,保证浇筑完成的混凝土达到清水混凝土的标准。
四、材料与设备的要求:1、水泥要求必须采用业主准入指定厂家水泥,严禁采用小厂水泥、杂牌水泥,同一个涵洞通道应采用同一厂家同一批次的水泥。
3、中粗砂要求采用级配良好、质地坚硬、颗粒洁净(含泥量小于2%、粒径小于5mm的河砂。
4、碎石要求采用颗粒级配均匀,质地坚硬,含泥量小于1%的碎石。
原材料应有足够的存量,保证同一结构物混凝土颜色基本一致。
5、外加剂。
可采用EA-1(2)普通型减水剂,要求定厂商、定品牌、定掺量。
对首批进场的原材料经监理取样复试合格后,应立即进行"封样",以后进场的每批来料均与"封样"进行对比,发现有明显色差的不得使用。
清水混凝土生产过程中,一定要严格按试验确定的配合比投料,不得带任何随意性,并严格控制水灰比和搅拌时间,随气候变化随时抽验砂子、碎石的含水率,及时调整用水量。
6、原则要求每3-6道涵洞通道配置一个专业队伍。
每一涵洞通道施工作业队要求配备模板工15人,混凝土工10人,电焊工3人,钢筋工8人,技术人员2人,安全保通人员1人。
涵洞工程施工办法(3篇)

第1篇一、工程概况涵洞是道路、铁路、河道等线性工程中常见的结构物,主要用于跨越河流、沟渠、铁路、道路等。
涵洞工程具有施工复杂、技术要求高、工期长等特点。
为确保涵洞工程的质量、安全和进度,以下提供涵洞工程施工办法。
二、施工准备1. 设计资料:熟悉设计图纸,了解涵洞结构形式、尺寸、材料要求等。
2. 施工图纸:根据设计图纸进行施工放样,确保涵洞中心线、进出口位置、高程等符合设计要求。
3. 施工材料:准备施工所需材料,如水泥、砂石、钢筋、模板等。
4. 施工设备:准备挖掘机、装载机、自卸车、混凝土搅拌站、振动器等施工设备。
5. 人员组织:成立施工队伍,明确各岗位人员职责,确保施工顺利进行。
三、施工步骤1. 施工测量:根据设计图纸进行施工放样,确定涵洞中心线、进出口位置、高程等。
2. 基坑开挖:采用挖掘机、装载机等设备进行基坑开挖,确保基坑尺寸、形状符合设计要求。
3. 基坑处理:对基坑进行平整、夯实,确保地基承载力满足设计要求。
4. 基础施工:根据设计要求,采用混凝土或浆砌石等方法进行基础施工。
5. 模板制作与安装:制作涵洞模板,确保模板尺寸、形状符合设计要求。
安装模板,保证模板稳定、垂直。
6. 钢筋加工与绑扎:根据设计要求,加工钢筋,进行钢筋绑扎,确保钢筋间距、位置符合设计要求。
7. 混凝土浇筑:混凝土搅拌均匀后,采用振动器进行浇筑,确保混凝土密实、无蜂窝、麻面等缺陷。
8. 防水层施工:在混凝土达到一定强度后,进行防水层施工,确保涵洞防水性能。
9. 涵洞回填:在涵洞混凝土强度达到设计要求后,进行回填,确保回填土密实、稳定。
10. 附属工程:进行涵洞进出口、八字墙等附属工程施工,确保涵洞与道路、铁路、河道等设施衔接顺畅。
四、施工注意事项1. 施工过程中,加强质量、安全、进度管理,确保工程顺利进行。
2. 严格控制施工材料、设备的质量,确保施工质量。
3. 严格按照设计图纸进行施工,确保涵洞结构安全、稳定。
4. 加强施工现场文明施工,确保施工环境整洁、有序。
涵洞及通道施工方案

涵洞及通道施工方案一、概述在道路、铁路等基础设施建设过程中,涵洞及通道的施工方案至关重要。
涵洞是指在河道、山洼、交通要道等地方建造的一种通行设施,通道则是指连接两个地方的通路。
本文就涵洞及通道的施工方案进行探讨。
二、前期准备在进行涵洞及通道的施工前,需要进行充分的前期准备工作。
首先,要对施工现场进行勘测,确定地形、地质条件等情况。
其次,要制定详细的施工方案,包括施工工艺、流程、安全措施等内容。
同时,还需要采购必要的施工设备和材料,确保施工进度顺利进行。
三、施工工艺1. 地基处理施工开始前,需要对地基进行处理,包括挖土、填方、夯实等工序。
地基处理的质量直接影响到后续结构的稳定性,因此必须认真对待。
2. 结构施工涵洞及通道的结构施工包括地基支护、拱顶施工、墙体施工等内容。
在施工过程中,要严格按照设计要求进行,确保结构的稳定性和安全性。
3. 排水系统为保证涵洞及通道的正常使用,必须建立完善的排水系统。
在施工过程中,要注意排水系统的设计和施工,确保通道内部没有积水。
4. 防水处理涵洞及通道的防水工程也是至关重要的一环。
在施工过程中,要采取有效的防水措施,确保结构的防水性能。
四、安全措施在涵洞及通道的施工过程中,安全是第一位的。
施工单位必须制定详细的安全方案,加强施工现场的安全管理,确保施工人员和设备的安全。
五、施工质量检查施工结束后,要对涵洞及通道的施工质量进行检查。
包括结构的稳定性、防水性能、排水系统等方面。
必要时,可以进行钢筋混凝土的检测,确保施工质量符合标准要求。
结束语涵洞及通道的施工是一项复杂的工程,需要施工单位和相关人员的共同努力才能成功完成。
只有严格按照施工方案进行,加强安全管理,确保施工质量,才能建造出安全、稳定的涵洞及通道,为交通运输提供良好的条件。
涵洞及通道工程施工方案

涵洞及通道工程施工方案一、工程概况涵洞和通道工程是指在铁路、公路、城市地下管网等工程中为了穿越山体、河流、交叉道路、地下管线等障碍物而建设的专门的隧洞工程。
随着社会和经济的不断发展,城市建设越来越复杂,交通基础设施需求不断增长,因此涵洞及通道工程的建设变得越来越重要。
本工程施工方案旨在对涵洞及通道工程的具体施工方案进行详细规划,确保工程的安全、高效、质量可控。
二、工程背景及施工地点本工程位于XX市某地区,是一座铁路通道工程,涉及到山体交越和河流穿越两处涵洞工程及一处地下通道工程。
施工地点地形复杂,交通不便,且部分区域存在较大的地质风险,需要严格的规划和施工。
三、工程组织管理1. 组织架构制定项目经理部、质量监督部、安全管理部、技术研发部等各部门的组织架构,并明确各部门的职责和权限。
2. 项目管理严格遵守国家相关法规和标准,确保施工过程的合法合规;成立项目组,每个岗位人员都需要签订责任书,并进行工作内容的规划和安排。
3. 安全管理制定安全生产手册,对每一位施工人员进行安全生产教育和培训,并进行定期的模拟逃生演练;安排专业的安全监督人员,确保工地安全生产。
4. 质量管理设立专门的质量监督部门,对施工过程中的质量进行全程监控,并进行定期的自检和互检。
四、施工工艺1. 地质勘察在施工前,进行详细的地质勘察,查清隧洞和通道工程周边的地质情况和水文情况,确定工程建设的可行性和稳定性。
2. 分段开挖针对地质情况复杂的区域,采取分段开挖的施工方式,减少地质灾害的发生。
在开挖过程中,要对挖掘的材料进行分类和处理,并进行合理的堆放。
3. 支护措施针对不同的地质情况,选用不同的支护材料和方式。
对于易塌、易滑、易陷的地质环境,要加强支护措施,确保施工安全。
4. 排水处理通道工程区域常常会有地下水的渗漏,因此在施工过程中需要进行排水处理,以防止施工材料和设备受潮损坏,并保证施工人员的安全。
5. 建筑工程针对往复开挖,循环同步施工,逐步开挖填充的工程特点,组织开挖初期、顶进中后期、拱形支护、桩工支护、合拢前后、周边绿化等分部工程,根据天气、节假日等情况,确定合理的时间节点。
涵洞及通道施工方案

涵洞及通道施工方案一、项目背景为满足城市交通发展的需要,我市计划在地区建设一座涵洞及通道。
该项目主要涉及道路拓宽、建设涵洞以及通道的施工工程。
二、施工目标1.完成道路拓宽工程,确保道路通行能力的提升。
2.安全、高效地建设涵洞,解决地下交通通道问题。
3.建设通道,保证车辆以及行人的顺畅通行。
三、施工方案1.道路拓宽工程道路拓宽工程主要包括挖掘土方、填方、道路面层铺设等工作。
在施工过程中,要严格按照设计要求进行施工,并确保施工质量。
重点工作包括:(1)挖掘土方:根据地质勘测结果,合理选择挖掘方式和挖掘工序,确保挖掘过程中不对周围建筑物和管线造成影响。
(2)填方:选择符合标准要求的填土,并进行适当的夯实,以提高道路承载力和抗沉降能力。
(3)道路面层铺设:根据设计要求,选择适当的材料进行道路面层铺设,确保道路平整、耐久。
2.涵洞建设工程涵洞建设工程主要包括涵洞基础施工、墙体施工和顶板施工。
涵洞建设需要结合地下管线的布置进行施工,保证涵洞的稳定和安全。
重点工作包括:(1)涵洞基础施工:根据设计要求进行基础开挖和回填,确保基础的稳定性和承载力。
(2)墙体施工:根据涵洞设计要求,选择适当的施工方式进行墙体施工,包括桩基施工、支护结构施工等。
(3)顶板施工:采用适当的模板进行混凝土顶板浇筑,并进行养护,保证顶板的承载力和稳定性。
3.通道建设工程通道建设工程主要包括通道开挖、支护及管线布置等工作。
通道的建设需要考虑到通行车辆的安全和行人通行的便利。
重点工作包括:(1)通道开挖:根据设计要求进行通道开挖,确保开挖的尺寸和位置准确无误。
(2)支护:根据地质条件选择适合的支护方式进行支护施工,确保通道的稳定性。
(3)管线布置:根据通道功能需求进行管线布置,确保通道内各种管线的安全、合理。
四、施工安全措施1.建立完善的施工组织管理体系,分工明确,责任到人。
2.严格遵守施工安全操作规程,确保施工过程中的安全。
3.加强对施工人员的安全教育培训,提高施工人员的安全意识。
涵洞通道工程创优施工方案
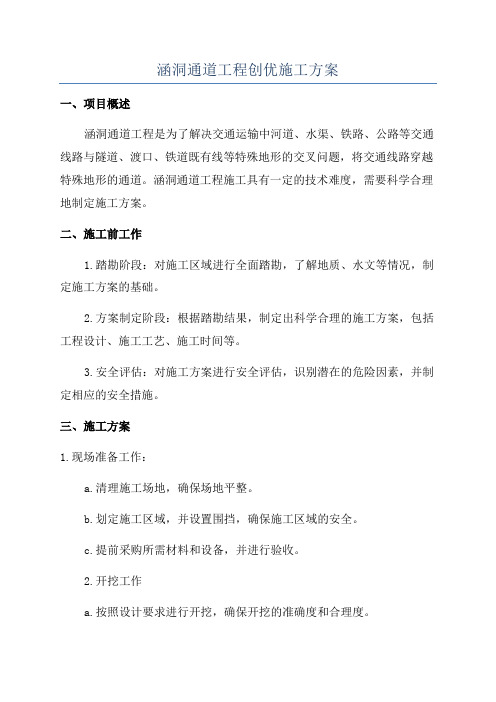
涵洞通道工程创优施工方案一、项目概述涵洞通道工程是为了解决交通运输中河道、水渠、铁路、公路等交通线路与隧道、渡口、铁道既有线等特殊地形的交叉问题,将交通线路穿越特殊地形的通道。
涵洞通道工程施工具有一定的技术难度,需要科学合理地制定施工方案。
二、施工前工作1.踏勘阶段:对施工区域进行全面踏勘,了解地质、水文等情况,制定施工方案的基础。
2.方案制定阶段:根据踏勘结果,制定出科学合理的施工方案,包括工程设计、施工工艺、施工时间等。
3.安全评估:对施工方案进行安全评估,识别潜在的危险因素,并制定相应的安全措施。
三、施工方案1.现场准备工作:a.清理施工场地,确保场地平整。
b.划定施工区域,并设置围挡,确保施工区域的安全。
c.提前采购所需材料和设备,并进行验收。
2.开挖工作a.按照设计要求进行开挖,确保开挖的准确度和合理度。
b.注意地质情况的变化,采取相应的应对措施,确保工程安全。
c.定期进行地质检测,对地表沉降情况进行监测。
3.结构施工a.按照设计要求进行涵洞结构的施工,确保结构的强度和稳定性。
b.加强质量检验,确保施工质量符合要求。
c.进行必要的材料试验,提前解决可能出现的质量问题。
4.排水系统建设a.建立完善的排水系统,确保涵洞通道的排水畅通。
b.安装排水设备,如排水管道、泵站等,并进行测试。
c.制定排水方案,预防洪水或强降雨等异常气候条件下的灾害。
5.施工过程中的安全措施a.设置安全警示标志,明确施工区域的禁止入内。
b.对施工人员进行安全培训,加强安全意识和应急处理能力。
c.定期进行检查,确保施工工地的安全。
四、施工监督与质量控制1.对施工过程进行监督检查,保证施工按照方案进行。
2.加强质量控制,严格遵循工程质量管理制度,确保质量符合设计要求。
3.施工过程中及时发现和解决问题,确保工程进度和质量。
五、环境保护1.对施工区域进行环境保护评估,制定相关措施。
2.对工地产生的垃圾、废弃物进行及时处理,保持施工区域的整洁。
装配式钢筋混凝土涵洞(通道)施工工法

装配式钢筋混凝土涵洞(通道)施工工法装配式钢筋混凝土涵洞(通道)施工工法一、前言装配式钢筋混凝土涵洞是一种先制成各个构件,然后进行组装安装的结构形式。
它具有施工速度快、质量可控、使用寿命长等优点,已经在很多工程中得到了广泛应用。
本文将详细介绍装配式钢筋混凝土涵洞的施工工法以及相关的技术措施和要点。
二、工法特点装配式钢筋混凝土涵洞采用工厂化生产和现场组装的方式,具有以下特点:1. 施工速度快:工厂化生产可以与现场施工同步进行,大大提高了施工效率。
2. 质量可控:采用工厂化生产,能够严格控制材料质量和施工工艺,保证构件的质量稳定。
3. 制造周期短:构件通过标准化生产,减少了施工周期,提高了工程进度。
4. 具有良好的抗震性能和耐久性,满足现代建筑要求。
三、适应范围装配式钢筋混凝土涵洞适用于各种路桥工程或地下通道。
1. 高速公路、城市道路,特别是在交通繁忙的地区,能够减少对交通的影响。
2. 地铁、铁路、隧道等地下交通工程,提高施工速度和质量。
3. 河道、沟渠等水利工程,能够保证工程的安全和稳定。
四、工艺原理装配式钢筋混凝土涵洞的施工工法与实际工程之间的联系主要包括以下几个方面:1. 设计和制造:根据具体工程需求进行设计,并将该设计转化为涵洞的各个构件的制造工艺。
2. 施工轴线和控制点的确定:根据设计要求,确定施工轴线和控制点的位置,并进行标志。
3. 地基处理和预埋件安装:进行地基处理,确保涵洞的基础稳定。
同时,根据设计要求,在地基上预埋所需的构件。
4. 板垫层施工:安装标准化的板垫层,为涵洞的组装提供平整的基础。
5. 涵洞构件组装:按照设计图纸和工艺要求,将预制构件进行组装安装,并进行调整和修正。
6. 防水层施工和细部处理:对涵洞进行防水处理,并对其它细部进行处理。
7. 吊装和安装:运用吊装设备将构件进行安装,并进行固定。
五、施工工艺1. 地基处理:清除现场杂物,进行地基平整和夯实处理。
2. 预埋件安装:按照设计要求进行预埋件的安装,以保证后续工序的顺利进行。
涵洞、通道专项施工方案(内容+排版)

涵洞、通道专项施工方案一、前言公路建设中,涵洞和通道是重要的交通设施,对于保障道路的畅通起着至关重要的作用。
本文将介绍涵洞、通道专项施工方案,包括施工准备、施工方法和质量控制等内容。
二、施工准备1. 项目概况本项目涉及涵洞和通道的施工,涵洞总长度为XXX米,通道总长度为XXX米。
2. 人员组织1.项目经理:负责项目的总体管理和决策。
2.技术负责人:负责施工中的技术指导。
3.施工人员:包括机械操作人员、砌筑工人等。
3. 材料采购确保所采购的材料符合相关质量标准,保证施工质量。
三、施工方法1. 涵洞施工1.开挖:根据设计要求,进行土方开挖,确保开挖范围准确。
2.砌筑:采用优质的混凝土进行砌筑,保证涵洞的结构稳固。
3.防水处理:涵洞内部应进行防水处理,以保证涵洞的使用寿命。
2. 通道施工1.路基处理:进行路基的填筑和夯实,保证通道的平整度。
2.铺设路面:根据设计要求,铺设适合的路面材料,确保通道的使用舒适性。
3.安装设施:安装照明设施、标志牌等,保证通道的安全通行。
四、质量控制1. 施工过程监督在施工过程中,技术负责人应进行现场监督,确保施工按照设计要求进行。
2. 质量检测对涵洞和通道的材料和施工质量进行检测,确保达到相关标准。
五、总结通过本文的介绍,可以看出涵洞、通道专项施工方案的重要性和施工步骤。
在实际施工中,要严格按照相关规范和要求进行施工,确保涵洞和通道的质量和安全性。
以上就是涵洞、通道专项施工方案的相关内容,希望对施工过程有所帮助。
涵洞通道专项施工方案

涵洞通道专项施工方案一、总体方案1.施工目标:完成涵洞、通道的建设和改造,保障交通安全和顺畅运行。
2.施工内容:包括涵洞结构的施工、通道的铺设和道路的复建等。
3.施工时间:根据实际情况确定,尽量避免交通高峰期进行。
二、涵洞施工方案1.涵洞结构设计:根据实际需求,确定涵洞的尺寸、形状和材料等。
2.施工准备:确定涵洞施工的平面布置和材料准备等。
3.基础施工:进行涵洞基础的开挖和垫层的铺设。
4.框架施工:安装涵洞的框架结构,包括支撑系统和梁柱等。
5.壁板施工:进行涵洞壁板的施工,包括混凝土浇筑和墙体的养护等。
6.顶板施工:进行涵洞顶板的施工,包括浇筑预制板和梁柱的安装等。
7.杂项工程施工:进行涵洞的排水系统、通风系统和照明系统等的安装和调试。
三、通道施工方案1.通道设计:根据实际需求,确定通道的规格、坡度和材料等。
2.施工准备:确定通道施工的平面布置和材料准备等。
3.基础施工:进行通道基础的开挖和垫层的铺设。
4.铺设施工:进行通道铺设的工作,包括路面的铺装和路缘石的安装等。
5.排水施工:进行通道排水系统的安装和调试,包括雨水管道和检查井等。
6.路灯施工:进行通道路灯的安装和调试,保证夜间行车的安全。
7.绿化施工:进行通道的绿化和景观建设,美化环境。
8.安全设施施工:进行交通标志和护栏等安全设施的安装和调试。
四、道路复建方案1.施工范围:根据实际需求,确定道路复建的范围,涵盖涵洞和通道周围的道路。
2.施工准备:进行道路复建的规划和布局,确定施工顺序和时间。
3.老化层拆除:拆除道路上的老化破损层,清理垃圾和杂物。
4.基层处理:进行道路基层的修补和加固,保证道路的承载能力。
5.路面铺装:进行新的路面铺装,包括沥青混凝土和水泥混凝土等。
6.路肩修复:对道路的路肩进行修复,保证行车安全和舒适度。
7.标线划设:进行道路标线的涂刷,包括车道线和限速标志等。
五、安全措施1.施工现场设立围挡,标明施工区域和危险区域。
2.安排专业施工队伍,确保施工质量和安全。
涵洞 通道工程施工方案

涵洞通道工程施工方案一、工程概况涵洞通道工程是指为了解决交通运输中的水体交叉问题而建设的工程。
涵洞通道工程具有隧道和桥梁的功能,是由涵洞和辅助设施组成的综合工程。
涵洞通道工程的建设将对交通运输、水资源和环境等方面产生积极影响,对于改善城乡交通状况,保障交通安全,促进经济发展都具有重要意义。
本文针对涵洞通道工程施工方案进行详细阐述,包括工程背景、施工过程、技术要点、安全保障等内容,旨在全面系统地展现涵洞通道工程的施工流程,为工程建设提供参考。
二、工程背景涵洞通道工程的建设需满足交通运输需求,促进区域发展,提高人民生活水平,保障生态环境等需求。
工程背景对于施工方案的制定至关重要,只有充分了解工程背景,才能有效制定出合理的施工方案。
我国交通运输建设不断推进,城乡交通网逐渐完善,但仍有不少地方存在水体交叉问题,影响了交通运输效率。
此外,随着城市化进程加快,人口流动加剧,对交通需求提出了更高的要求。
因此,为了加强交通运输设施建设,提高交通运输服务水平,需要建设涵洞通道工程,解决水体交叉问题,改善交通状况。
三、施工流程1.前期准备工作(1)工程测量施工前需要对涵洞通道工程的场地进行详细的测量,获得场地的地形、地貌、地势等相关数据,为后续施工提供准确的基础数据。
(2)场地准备对施工场地进行清理、平整、开挖等工作,确保施工区域的环境整洁,便于施工人员进行作业。
(3)技术准备配备施工所需的机械设备、工具、材料和人员,做好技术人员培训和施工队伍组织,确保施工准备充分。
2.地基处理涵洞通道工程的地基处理是整个施工过程中的重要环节,地基的稳固与否直接决定了工程的质量。
地基处理包括挖土、填土、加固、浇筑混凝土等工序,需要根据实际情况进行灵活处理。
3.结构施工结构施工主要包括涵洞和辅助设施的建设工作,其中包括桥墩、桥台、桥梁、管廊等设施的施工工序,这些工序需要根据设计图纸和规范要求进行施工。
施工过程中需要处理好土方开挖、混凝土浇筑、钢筋绑扎等工艺环节。
涵洞通道工程施工方案
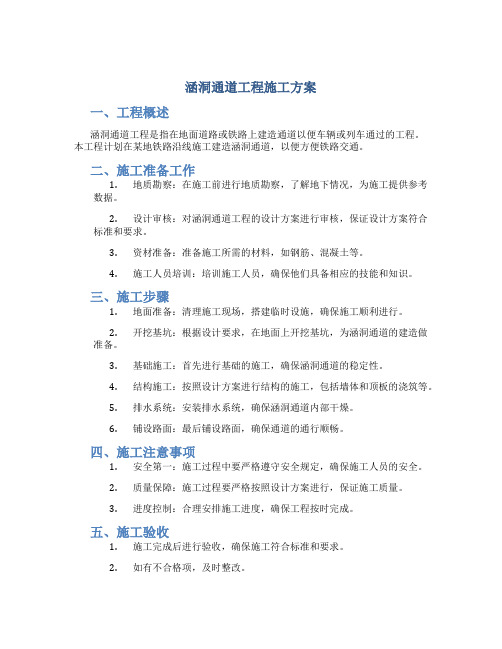
涵洞通道工程施工方案
一、工程概述
涵洞通道工程是指在地面道路或铁路上建造通道以便车辆或列车通过的工程。
本工程计划在某地铁路沿线施工建造涵洞通道,以便方便铁路交通。
二、施工准备工作
1.地质勘察:在施工前进行地质勘察,了解地下情况,为施工提供参考
数据。
2.设计审核:对涵洞通道工程的设计方案进行审核,保证设计方案符合
标准和要求。
3.资材准备:准备施工所需的材料,如钢筋、混凝土等。
4.施工人员培训:培训施工人员,确保他们具备相应的技能和知识。
三、施工步骤
1.地面准备:清理施工现场,搭建临时设施,确保施工顺利进行。
2.开挖基坑:根据设计要求,在地面上开挖基坑,为涵洞通道的建造做
准备。
3.基础施工:首先进行基础的施工,确保涵洞通道的稳定性。
4.结构施工:按照设计方案进行结构的施工,包括墙体和顶板的浇筑等。
5.排水系统:安装排水系统,确保涵洞通道内部干燥。
6.铺设路面:最后铺设路面,确保通道的通行顺畅。
四、施工注意事项
1.安全第一:施工过程中要严格遵守安全规定,确保施工人员的安全。
2.质量保障:施工过程要严格按照设计方案进行,保证施工质量。
3.进度控制:合理安排施工进度,确保工程按时完成。
五、施工验收
1.施工完成后进行验收,确保施工符合标准和要求。
2.如有不合格项,及时整改。
六、工程总结
涵洞通道工程施工是一项复杂的工程,需要认真准备和实施。
通过合理的施工
准备和规范的操作,可以保证工程质量和进度的顺利进行,最终完成工程建设目标。
各种涵洞施工方案
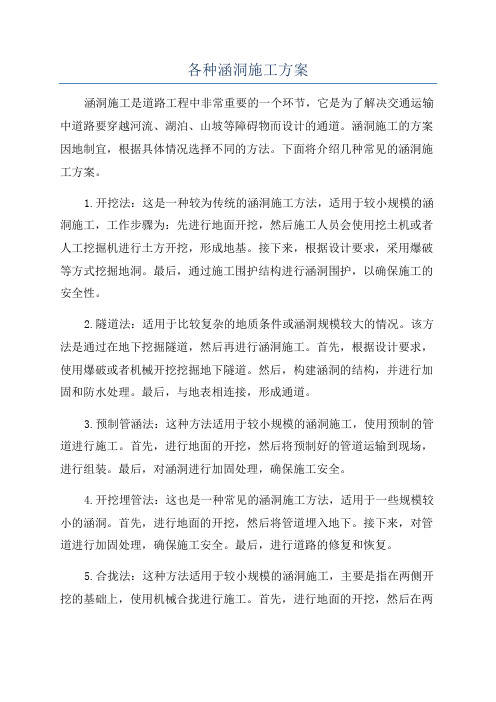
各种涵洞施工方案涵洞施工是道路工程中非常重要的一个环节,它是为了解决交通运输中道路要穿越河流、湖泊、山坡等障碍物而设计的通道。
涵洞施工的方案因地制宜,根据具体情况选择不同的方法。
下面将介绍几种常见的涵洞施工方案。
1.开挖法:这是一种较为传统的涵洞施工方法,适用于较小规模的涵洞施工,工作步骤为:先进行地面开挖,然后施工人员会使用挖土机或者人工挖掘机进行土方开挖,形成地基。
接下来,根据设计要求,采用爆破等方式挖掘地洞。
最后,通过施工围护结构进行涵洞围护,以确保施工的安全性。
2.隧道法:适用于比较复杂的地质条件或涵洞规模较大的情况。
该方法是通过在地下挖掘隧道,然后再进行涵洞施工。
首先,根据设计要求,使用爆破或者机械开挖挖掘地下隧道。
然后,构建涵洞的结构,并进行加固和防水处理。
最后,与地表相连接,形成通道。
3.预制管涵法:这种方法适用于较小规模的涵洞施工,使用预制的管道进行施工。
首先,进行地面的开挖,然后将预制好的管道运输到现场,进行组装。
最后,对涵洞进行加固处理,确保施工安全。
4.开挖埋管法:这也是一种常见的涵洞施工方法,适用于一些规模较小的涵洞。
首先,进行地面的开挖,然后将管道埋入地下。
接下来,对管道进行加固处理,确保施工安全。
最后,进行道路的修复和恢复。
5.合拢法:这种方法适用于较小规模的涵洞施工,主要是指在两侧开挖的基础上,使用机械合拢进行施工。
首先,进行地面的开挖,然后在两侧同时施工。
施工过程中要注意合拢的质量和安全。
最后,进行涵洞的加固和清理。
总的来说,不同的涵洞施工方案适用于不同的地质条件和涵洞规模。
施工方案的选择要合理,施工过程中要注重安全和质量控制。
涵洞施工需要进行详细的设计和周密的施工计划,以确保施工的顺利进行。
同时,也要注重环境保护和社会效益的综合考虑,以促进交通运输的发展。
桥梁涵洞通道工程施工方案方法

桥梁涵洞通道工程施工方案方法桥梁、涵洞及通道工程施工方案、方法一、工程概述本合同段主线内没有桥梁结构(不含互通)。
本合同段内涵洞、通道数量如下表所示:涵洞及通道数量表(主线)二、总体施工方案1、互通区通道桥基础工程采用钻孔灌注桩基础施工。
对于旱地应先开辟作业场地及支线便道,以便于施工机具运到施工桩号;并设置沉淀池和排污管道,为施工创造适宜的环境。
2、墩柱及盖、系梁的施工采用整体钢模,支架法一次立模到顶,整体灌注,减少混凝土接茬。
3、为满足质量要求和解决施工场地狭小问题,钢筋加工安装采用现场作业,混凝土的搅拌采用集中拌合,混凝土运输车运输,混凝土输送泵灌注。
4、后张法预应力空心板梁在预制场预制,汽车吊设安装。
5、梁体安装结束后迅速开始梁体现浇连续施工,待全梁安装结束后,统一进行护栏及桥面铺装作业。
三、主要的施工工艺和施工方法(一)涵洞及通道工程本合同段内涵洞、通道的主要形式有钢筋砼盖板涵、圆管涵、箱涵及通道桥等。
通道、盖板涵均采用预制钢筋混凝土盖板、现浇混凝土基础;箱涵采用现浇;圆管涵采用预制管节安装的方法。
通道桥基础采钻孔灌注桩,墩台采用整体模板支架法现浇,空心板梁在预制场内预制。
1、施工方法(1)上场后,立即组织涵洞、通道施工,处于填方路段的通道和涵洞尽早完工,为路基填筑创造条件。
(2)基础采用机械开挖,人工整型,混凝土采用强制式搅拌机及自动计量配料系统现场拌合。
模板采用组合钢模板。
钢筋混凝土盖板及通道由预制场集中预制,汽车运输到现场,吊装就位。
(3)箱涵采用现浇,采用组合钢模板支架法施工。
2、涵洞施工要点(1)钢筋砼盖板涵、通道及圆管涵施工要点1)涵洞开工前,应根据设计资料,结合现场实际地形、地质情况,对其位置、方向、长度、出入口高程以及与排灌系统的连接等进行核对。
2)涵洞盖板、涵管节在预制场集中预制,施工中确保盖板和涵管节尺寸符合设计要求,安装盖板和涵管节时应注意下列事项:①予制成品达到设计强度的70%才允许搬运、安装。
涵洞箱涵通道施工方案
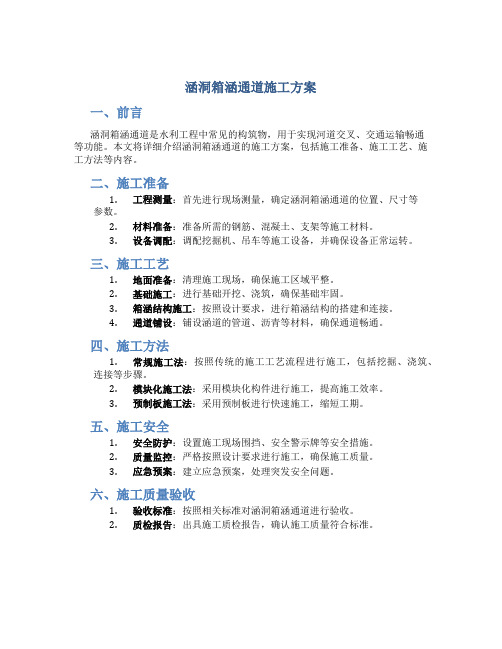
涵洞箱涵通道施工方案一、前言涵洞箱涵通道是水利工程中常见的构筑物,用于实现河道交叉、交通运输畅通等功能。
本文将详细介绍涵洞箱涵通道的施工方案,包括施工准备、施工工艺、施工方法等内容。
二、施工准备1.工程测量:首先进行现场测量,确定涵洞箱涵通道的位置、尺寸等参数。
2.材料准备:准备所需的钢筋、混凝土、支架等施工材料。
3.设备调配:调配挖掘机、吊车等施工设备,并确保设备正常运转。
三、施工工艺1.地面准备:清理施工现场,确保施工区域平整。
2.基础施工:进行基础开挖、浇筑,确保基础牢固。
3.箱涵结构施工:按照设计要求,进行箱涵结构的搭建和连接。
4.通道铺设:铺设涵道的管道、沥青等材料,确保通道畅通。
四、施工方法1.常规施工法:按照传统的施工工艺流程进行施工,包括挖掘、浇筑、连接等步骤。
2.模块化施工法:采用模块化构件进行施工,提高施工效率。
3.预制板施工法:采用预制板进行快速施工,缩短工期。
五、施工安全1.安全防护:设置施工现场围挡、安全警示牌等安全措施。
2.质量监控:严格按照设计要求进行施工,确保施工质量。
3.应急预案:建立应急预案,处理突发安全问题。
六、施工质量验收1.验收标准:按照相关标准对涵洞箱涵通道进行验收。
2.质检报告:出具施工质检报告,确认施工质量符合标准。
七、施工总结涵洞箱涵通道的施工是一项复杂的工程,需要严格按照施工方案进行操作,确保施工质量和安全。
只有在施工中不断总结经验教训,才能提高施工效率,满足人们对道路交通、水利设施等需求。
以上就是涵洞箱涵通道施工方案的相关内容,希望对您有所帮助。
涵洞通道工程施工技术方案

涵洞通道工程施工技术方案全线涵洞通道工程按照分部划分,每个分部配置1个涵洞通道工程作业队,负责各分部涵洞通道工程。
1.圆管涵施工方案(1)基坑开挖测量放出基坑开挖边线,确定开挖深度,采用挖掘机开挖基坑,预留不少于20cm采用人工清理整平。
在涵洞施工期前,根据图纸设计要求对涵洞基底进行软基处理,满足地基承载力要求后,方能进行下道工序。
(2)管基施工管基砼施工时,先铺设10cm厚砂砾垫层夯实,然后浇筑管底以下部分,并预留管壁厚度及安放管节坐浆砼2~3cm,待安放管节后再浇筑管底以上部分,并使新旧砼及管基砼与管壁有良好结合。
(3)管节安装圆管涵的管节运至现场后,人工配合吊车安装就位。
安装从下游开始,逐节向上游安装,每隔2m设置一道沉降缝,安装完成后浇筑管身混凝土。
管节接缝用沥青麻絮填塞接缝内、外缝,再用两道150mm 宽的浸透沥青的油毛毡包缠,并用铅丝绑扎接缝部位。
(4)洞口施工:按照设计要求浇筑或砌筑端墙、翼墙、锥坡等。
(5)两侧回填管节安装结束,经监理工程师许可后即可进行回填。
回填采用设计规定的填料,在洞身两侧不小于两倍孔径范围内对称分层回填压实。
施工中,当涵顶填土厚度大于0.5m时,方可允许施工机械和车辆通过。
2.箱涵及通道施工方案(1)基坑开挖测量放出基坑开挖边线,确定开挖深度,采用挖掘机开挖基坑,预留不少于20cm采用人工清理整平。
在涵洞施工期前,根据图纸设计要求对涵洞基底进行软基处理,满足地基承载力要求后,方能进行下道工序。
(2)基础及涵身施工在涵洞施工期前,根据图纸设计要求对涵洞基底进行软基处理,满足地基承载力要求后,铺设50cm厚砂砾垫层夯实,然后再浇筑10cm 厚C20砼垫层。
基础及涵身所用钢筋统一在钢筋加工场制作,小托板车运至现场安装、固定。
模板采用组合钢模板拼装,转角部分采用定型钢模板,由三角支撑和井字内撑加固。
混凝土由拌合站集中生产,由输送车运至现场,经溜槽或料斗入模,分节浇筑,振捣密实。
盖板涵洞(通道)施工方案

盖板涵洞(通道)施工方案一、前期准备在进行盖板涵洞(通道)的施工前,首先需要进行详细的方案设计和施工准备工作。
这其中包括以下几个步骤:1.调研与勘测:对施工地点进行细致的调研,了解地形、地质情况,进行勘测,确定施工区域的具体位置和条件。
2.设计方案:根据勘测结果和设计需求,制定盖板涵洞(通道)的具体设计方案,包括结构、材料选用、施工工艺等。
3.材料准备:根据设计方案,提前准备所需的材料,确保施工过程中材料供应充足,不会出现延期等问题。
二、施工过程在前期准备工作完成后,开始进行盖板涵洞(通道)的施工过程。
具体步骤如下:1.挖掘基坑:根据设计要求,对施工区域进行挖掘基坑,确保基坑深度和大小符合设计要求。
2.浇筑基础:在基坑内进行混凝土浇筑,形成坚固的基础,以支撑后续结构的施工。
3.搭建支模:根据设计方案,搭建盖板涵洞(通道)的支模结构,确保结构稳固,能够承受后续的施工过程和荷载。
4.浇筑混凝土:在支模搭建完成后,进行混凝土浇筑,形成盖板涵洞(通道)的主体结构。
5.施工完成:待混凝土达到强度要求后,进行拆模,清理施工现场,完成盖板涵洞(通道)的施工。
三、验收与保养施工完成后,需要进行验收和保养工作,以确保盖板涵洞(通道)的使用安全和持久。
具体步骤如下:1.验收:组织专业机构进行验收,检查盖板涵洞(通道)的结构完整性和质量标准,确保符合设计要求。
2.保养:在验收合格后,进行盖板涵洞(通道)的保养工作,定期检查、清理,确保结构稳固,延长使用寿命。
3.注意事项:在使用过程中,避免超载、碰撞等情况,保持盖板涵洞(通道)的清洁和干燥,及时进行维修和补救,确保安全使用。
四、总结盖板涵洞(通道)的施工是一个复杂的工程过程,需要精心设计、精准施工和严格验收。
只有通过科学规划和精细执行,才能确保施工质量和使用效果。
在未来的施工过程中,我们将继续秉承“质量第一、安全第一”的原则,不断提升施工水平,为社会交通建设贡献力量。
涵洞、通道施工方案

涵洞、通道施工方案在道路建设和基础建设中,涵洞及通道是一种非常重要的结构工程,其施工方案的设计和实施对工程质量和进度都具有至关重要的影响。
本文将重点探讨涵洞和通道的施工方案设计原则及实施方法。
1. 涵洞施工方案设计原则在设计涵洞施工方案时,需要遵循以下原则:1.1 安全第一涵洞施工过程中需确保施工人员和设备的安全,严格按照相关标准和规范进行施工作业,防止安全事故的发生。
1.2 环保可持续在涵洞施工过程中,要注重环境保护和资源利用,采用新型环保材料和工艺,以实现可持续发展的目标。
1.3 施工质量涵洞施工质量是保证工程稳定性和使用寿命的关键因素,施工过程中应严格把控质量,确保施工符合设计要求。
2. 涵洞施工实施方法2.1 土方开挖涵洞施工的第一步是进行土方开挖,按照设计要求进行挖土,保证截面准确无误。
2.2 结构施工完成土方开挖后,进行涵洞的结构施工,包括基础、墙体和拱顶等部分的建造,确保结构稳固可靠。
2.3 设备安装涵洞施工完毕后,需要进行设备安装工作,包括通风设备、照明设备等的安装和调试。
3. 通道施工方案设计原则3.1 交通便利通道施工方案设计应考虑到交通便利性,尽量减少对周边交通的影响,确保施工过程顺利进行。
3.2 强度耐久通道作为承载车辆和行人的重要结构,其施工方案应确保通道的强度和耐久性,以满足使用要求。
3.3 美观实用通道施工方案设计需要兼顾美观性和实用性,使其既能满足功能需要,又能融入周边环境,提升景观价值。
4. 通道施工实施方法4.1 地基处理通道施工的第一步是进行地基处理,保证基础稳固可靠,符合设计要求。
4.2 结构施工完成地基处理后,进行通道的结构施工,包括墙体、栏杆等部分的建造,确保结构牢固。
4.3 防水处理通道施工完毕后,需要进行防水处理,保证通道结构不受水侵蚀,延长使用寿命。
综上所述,涵洞和通道施工方案的设计和实施需要考虑到安全、质量、环保和实用性等因素,通过科学合理的施工方案设计和实施方法,可以保证工程的顺利进行和质量可控,达到预期的使用效果。
- 1、下载文档前请自行甄别文档内容的完整性,平台不提供额外的编辑、内容补充、找答案等附加服务。
- 2、"仅部分预览"的文档,不可在线预览部分如存在完整性等问题,可反馈申请退款(可完整预览的文档不适用该条件!)。
- 3、如文档侵犯您的权益,请联系客服反馈,我们会尽快为您处理(人工客服工作时间:9:00-18:30)。
涵洞、通道施工工法1 前言****改建工程****标段全线拱涵1道,涵洞、通道11道,本标段选定RK183+224.216钢筋混凝土盖板暗涵台身做为首件项目,该盖板涵(孔数-孔径×孔高)为1-2.0×2.0米,属于旧涵接长,涵接长21.33米,交角90度。
2工法特点2.1 提高了涵洞通道的砼外观质量,混凝土表面平整光滑,色泽均匀,无碰损和污染,对拉螺栓及施工缝的设置整齐美观,能有效解决混凝土施工的质量通病。
提高了钢筋保护层厚度的保证率。
2.2采用移模法施工,加快了施工进度。
2.3施工工艺简单,质量有保证,施工安全。
3 适用范围******改扩建工程*******标段的各类涵洞、通道的施工。
4 工艺原理通过对模板的加工、拼接、立模进行严格的控制,对对拉螺栓的位置进行规整布置,对混凝土的制备和振捣进行控制,保证模板的刚度、强度、加工精度,保证模板表面平整、光滑、接缝严密无漏浆,保证浇筑完成的混凝土外露面达到清水混凝土的标准。
通过对钢筋保护层垫块的选择和安装控制,工前保护层检查控制,保证钢筋保护层合格率达到80%以上。
5 施工工艺流程及操作要点5.1工艺流程见下图涵洞通道施工工艺流程图5.2操作要点5.2.1 测量放样1 精确放样。
2 用木桩在通道基础四角固定。
5.2.2基础施工1 基础施工选用面板厚度大于6㎜的钢模板作为基础模板,模板加工选用经过准入的厂家,模板必须经过项目部和监理工程师的出厂验收和进场验收。
2 模板接缝处用海绵条封塞或用泡沫填充剂填充,以防漏浆3 砼的振捣采用插入式振捣器5.2.3 墙身施工1涵洞通道墙身采用整体移模法施工即先施工墙身中的一节,拼装墙身的模板和内钢管支撑架,浇完该段墙身混凝土后,松开模板和内架,移动模板和内架到下一节,固定调整好后浇混凝土。
2模板系应由以下几部分构成:1)竖纵横钢管、内撑钢管等用扣件牢固连接的内架、拉杆固定的内外侧带纵向钢管的拼装模板、滑动装置(施工中用短钢管代替)、外斜撑钢管等。
为保证涵洞通道墙身表面平整、光滑、密实,颜色一致,必须采用单块面积大于2平方米的整体钢模板。
2)对穿螺栓位置应进行设计,保证纵横向在一条线。
对穿螺栓宜采用由2个锥形连接的三节式螺栓,螺栓宜选用T16*6-T20*6冷挤压螺栓,中间一节螺栓留在混凝土内,两端的锥形接头拆除后周转使用。
锥形孔眼用水泥浆封堵,并用专用的封孔模具装饰。
3)对穿螺栓也可采用可周转的对拉螺栓,截面范围内螺栓采用塑料套管,两端要用锥形堵头和橡胶海绵垫。
3 在已经浇注好的涵洞基础上精确定位墙身平面位置,用墨线弹出模板立设位置。
4 用钢管组装内架,最下层横钢管支撑在涵洞基础上。
5 搭建拼装外模板时用的临时脚手架。
6 按墙身设计高度和最长节段长度拼装墙身模板。
墙身模板拼装前要进行打磨、刷隔离剂后要用塑料薄膜进行覆盖,避免污染。
7 安装已套好套管的拉杆,固定模板,保证模板平面位置、竖直度满足规范要求。
8 报验合格后分层对称浇注涵洞两侧墙身混凝土。
9混凝土强度达到2.5mpa后,松开内撑钢管,滑动装置处用钢管内架到下一节段。
10 抽出拉杆,把内外侧拼装模板垫起,装上滚轮(段钢管)后,滑移拼装模板到下一节段,准备施工下一节墙身。
11 混凝土施工完毕后要节水保湿养护膜养生,其标准应满足JG/T188-2006标准要求。
如表面有砂眼等瑕疵,可拆模后即清除表面浮浆和松动的沙子,采用相同强度等级的水泥拌制成水泥浆体,修复和批嵌缺陷部位,待水泥浆体硬化后,用细沙纸将整个构件表面均匀地打磨光洁,并用水冲洗洁净,确保表面无色差。
如拆模后有20cm²跑浆、蜂窝和松动的砂子的情况,整个混凝土应拆除。
5.2.4 涵洞通道台帽的施工1 台帽采用整体定型钢模。
定型钢模的制作按盖板模板的标准要求,确保棱角线的顺直。
模板制作长度按同类型台帽最长的控制,以消除接缝。
2 加强模板支撑与加固台帽正面模板加固采用对撑顶托,背面采用拉杆。
顶托用钢管支撑架固定,拉杆焊接在墙身预留茬钢筋上。
5.2.5八字墙的施工1 考虑到八字墙的不规则性,模板采用刚度、强度符合要求的覆膜竹胶合板进行设计、加工制作,2 为了杜绝烂根漏浆现象,模板底部用砂浆抹实。
3 堵头模板用竹胶板加工,后钉方木,固定牢靠,竖直度、线性要符合要求。
4为了避免模板上浮,模板底部采用地钉施工控制或膨胀螺丝固定。
5 八字墙上顶斜面施工时,上口每隔1m放横向钢管,顶住一块宽度为40cm方木板,避免斜面砼流落,便于振捣收面,同时在模板上画出坡面线,由专人收面使坡面线形畅,坡面坡度与路基坡度一致,由于坡面砼斜度大,刚浇注完的砼要多次收面才能保证砼外观质量。
6 振实时料面每层不超过30cm,采用二次振捣尽量杜绝气泡。
5.2.6 混凝土的拌和、浇筑1 施工前对出骨料进行水洗,晾干后拌合一遍,对中砂进行过筛,并同时增加拌和机内干料和湿料的搅拌时间,湿料的搅拌时间≥180秒。
严格控制水灰比和混凝土坍落度,从施工开始到结束保持一致,到现场的混凝土坍落度,控制在140mm到160mm,混凝土采用聚羧酸高效减水剂,以减少泌水的可能性。
同时控制混凝土含气量不超过1.7%,初凝时间6-8h。
2 严格控制每次下料的高度和厚度,保证分层厚度不超过30cm.3 振捣不得漏振和过振。
可采用二次振捣法,以减少表面气泡,即第一次在混凝土浇筑时振捣,第二次待混凝土静置一段时间再振捣,而顶层一般在0.5h后进行第二次振捣。
严格控制振捣时间和振捣棒插入下一层混凝土的深度,保证插入下层深度在5-10cm,振捣时间以混凝土翻浆不再下沉和表面无气泡泛起为止,一般为15s左右。
4 要求砼浇注现场由试验员、施工员或技术员全过程旁站值班,试验人员每车检测砼坍落度。
施工员督促班组人员有专人2人负责观察模板的情况,随时紧固栏杆。
5 必须注意混凝土的浇注方法,每段的两侧边墙混凝土均要分层对称浇筑,防止不对称浇注混凝土造成偏压,把边墙模板挤偏向一侧。
6 施工过程中避免施工人员踏踩拉杆,必须保证拉杆直顺。
7 在涵洞基础上一次把整条边墙的支模线放好,用墨线浓浓底弹在涵洞基础上。
一条边墙支模不要多次放线,避免多次放线造成误差。
8 模板与检测底部缝隙,先用1cm厚泡沫板塞缝,再用水泥砂浆抹带,避免接缝漏浆及底部“烂根”现象。
5.2.7 养生混凝土拆模后要立即覆盖进行养生。
养生采用塑料薄膜全覆盖洒水养生,养生时间不得小于7天。
采用双面胶贴到养护膜内侧进行养护膜的固定。
养生膜外边沿要满贴双面胶,确保养生膜覆盖严密。
如覆盖前混凝土表面较干,可以进行洒水后在覆盖养生膜。
5.2.8 沉降缝采用高分子弹性材料进行灌缝。
为保证沉降缝顺直,采用U型塑料条处理,保证了线形平顺美观。
6 材料与设备6.1 水泥要求必须采用业主准入选定厂家水泥,严禁采用小厂水泥、杂牌水泥,同一个涵洞通道应采用同一厂家同一批次的水泥。
6.2中粗砂要求采用级配良好、质地坚硬、颗粒洁净(含泥量小于2%、粒径小于5mm)的河砂。
6.3 碎石要求采用颗粒级配均匀,质地坚硬,含泥量小于1%的碎石。
原材料应有足够的存量,保证同一结构物混凝土颜色基本一致。
6.4 外加剂。
采用聚羧酸高效减水剂,要求固定厂商、品牌、掺量。
对首批进场的原材料经监理取样复试合格后,应立即进行“封样”,以后进场的每批来料均与“封样”进行对比,发现有明显色差的不得使用。
混凝土生产过程中,一定要严格按试验确定的配合比投料,并严格控制水灰比和搅拌时间,随气候变化随时抽检砂子、碎石的含水率,及时调整用水量。
6.5 要求每4道涵洞通道配置一个专业队伍。
每一施工作业队配备混凝土运输车1台,电动振捣器4台,电焊机2台,20吨吊车1台,发电机2台;整体新钢模板200平方米以上。
6.6 钢模板应选择6mm以上的原平板做面板,钢模板的质量应符合≤全钢大模板应用技术规程≥(DBJ01-89-2004)。
模板表面应平整、光滑、无凹凸、无伤痕、无修补痕迹。
6.7 模板在定制、立模前要进行分块设计,分块应力求定型化、整体化、模数化和通用化。
以钢板为面板的模板,其面板分割宜竖向布置,一般不涉及横缝,当钢板竖向接高时,其模板横缝应在同一高度。
总体上分割应做到均匀对称。
7质量控制7.1涵洞基础及墙身现浇施工质量标准;检测项目和检测频率应符合JTGF80/1-2004《公路工程质量检验评定标准》表9.22﹑9.3.3﹑9.11.3及有关试验检测的规定。
7.2外观质量标准:7.2.1颜色墙体混凝土应表现混凝土的自然色,表面颜色润泽﹑颜色一致。
在同一视觉空间内,混凝土表面颜色一致,色泽均匀。
自然光下,4m处肉眼看不到明显色差。
7.2.2表面质量混凝土表面不得出现蜂窝,麻面,砂带,冷接缝和表面损伤等;不得受到污染和现斑迹;表面裂纹宽度不得超过0.2mm.7.2.3 表面气泡表面1平方米面积上的气泡面积总和不大于0.0003㎡,最大气泡直径不大于3mm,深度不大于3mm;7.2.4 分格缝直线度与对拉螺栓孔眼分格缝直线偏差不大于4mm,对拉螺栓孔眼排列整齐均匀,拆模后封堵密实,颜色同墙面一致;若封堵的对拉螺栓颜色与墙体不一致,应形成有规律的装饰效果。
7.2.5 混凝土墙面的细微冷接缝不超过2/500(m/㎡).7.2.6 模板拼缝印记整齐、均匀,且印记宽度不大于1.5mm.7.2.7 混凝土修补面积不超过总面积的0.2%8 劳动力组织要求每4道涵洞通道配置一个专业队伍。
每施工作业队劳动力组织见下表:9安全措施9.1 进入施工现场人员,必须佩戴安全帽,特殊工种按规定要佩戴好防护用品。
9.2 根据各工种特点,有计划按时配发保护用品。
9.3 施工现场的布置符合防火、防爆、防雷电等安全规定和文明施工的要求,不舍足够的消防水源和消防设施网点,施工现场的生活办公用房、仓库、材料堆放场、停车场、修理场等按批准的总平面布置图进行布置。
9.4 施工现场在醒目的地方设置齐全的安全宣传标语牌、操作规程牌。
9.5 基坑开挖后应在周围设置钢管围栏。
9.6 用电施工机具应配触电保护器。
9.7 吊装盖板时应防止坍塌事故。
9.8 成立安全领导小组。
9.9 完善各项安全生产管理制度。
9.10 建立以安全岗位责任制为中心的安全生产责任制。
9.11 施工前进行施工技术交底和安全技术交底。
9.12 电器及各种用电设备严格禁止非电工人员操作。
9.13 电工经常检查电路。
9.14 现场设立专职安全员。
9.15采取安全保护措施。
9.16立模时吊具栓挂妥当、牢靠。
9.17 严格检查钢管支架支模,及时修复。
9.18 多人抬运长钢筋时,负荷应均匀。
9.19 上下传递钢筋,不得站在同一垂直线上。
9.20 雷雨天气应停止露天作业,以防电击伤人。
9.21 掌握砼施工常识和使用的机具性能,作业对象的技术要求。