钢的离子氮化处理
十三、钢铁零件渗氮(氮化)后的硬度及厚度检测方法: ----随着工业的
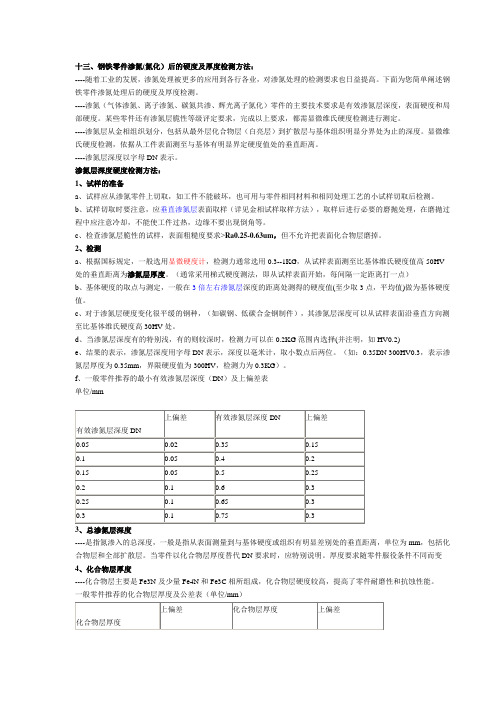
十三、钢铁零件渗氮(氮化)后的硬度及厚度检测方法:----随着工业的发展,渗氮处理被更多的应用到各行各业,对渗氮处理的检测要求也日益提高。
下面为您简单阐述钢铁零件渗氮处理后的硬度及厚度检测。
----渗氮(气体渗氮、离子渗氮、碳氮共渗、辉光离子氮化)零件的主要技术要求是有效渗氮层深度,表面硬度和局部硬度。
某些零件还有渗氮层脆性等级评定要求,完成以上要求,都需显微维氏硬度检测进行测定。
----渗氮层从金相组织划分,包括从最外层化合物层(白亮层)到扩散层与基体组织明显分界处为止的深度。
显微维氏硬度检测,依据从工件表面测至与基体有明显界定硬度值处的垂直距离。
----渗氮层深度以字母DN表示。
渗氮层深度硬度检测方法:1、试样的准备a、试样应从渗氮零件上切取,如工件不能破坏,也可用与零件相同材料和相同处理工艺的小试样切取后检测。
b、试样切取时要注意,应垂直渗氮层表面取样(详见金相试样取样方法),取样后进行必要的磨抛处理,在磨抛过程中应注意冷却,不能使工件过热,边缘不要出现倒角等。
c、检查渗氮层脆性的试样,表面粗糙度要求>Ra0.25-0.63um,但不允许把表面化合物层磨掉。
2、检测a、根据国标规定,一般选用显微硬度计,检测力通常选用0.3--1KG,从试样表面测至比基体维氏硬度值高50HV 处的垂直距离为渗氮层厚度。
(通常采用梯式硬度测法,即从试样表面开始,每间隔一定距离打一点)b、基体硬度的取点与测定,一般在3倍左右渗氮层深度的距离处测得的硬度值(至少取3点,平均值)做为基体硬度值。
c、对于渗氮层硬度变化很平缓的钢种,(如碳钢、低碳合金钢制件),其渗氮层深度可以从试样表面沿垂直方向测至比基体维氏硬度高30HV处。
d、当渗氮层深度有的特别浅,有的则较深时,检测力可以在0.2KG范围内选择(并注明,如HV0.2)e、结果的表示,渗氮层深度用字母DN表示,深度以毫米计,取小数点后两位。
(如:0.35DN 300HV0.3,表示渗氮层厚度为0.35mm,界限硬度值为300HV,检测力为0.3KG)。
离子渗氮工艺原理

离子渗氮工艺原理【2009-1-8】﹝一﹞钢的渗氮渗氮是把氮渗入钢件的表面,形成富氮硬化层的化学热处理过程。
在工业生产中,常用的工艺方法有:气体渗氮、盐浴渗氮和离子渗氮。
1.渗氮工艺的特点﹝1﹞渗氮后的零件表面具有高的硬度、耐磨性、疲劳强度和低的缺口敏感性。
﹝2﹞渗氮温度较低,一般在500-600℃,而且,渗氮层的高硬度可以由渗氮直接得到,不需要经过较高温度的加热和淬火。
所以,渗氮工艺的变形是最小的,常常作为零件的最后一道工序。
﹝3﹞渗氮层有较高的抗腐蚀性能。
2.渗氮工艺的化学过程渗氮和其他化学热处理工艺一样,也是由分解、吸收、扩散三个基本过程组成的。
﹝1﹞分解渗氮介质﹝通常为氨气﹞通过热分解或其他方法,生成活性氮原子。
﹝2﹞吸收钢表面吸收氮原子,形成氮在铁中的固溶体和氮化物。
﹝3﹞扩散氮从表面高浓度的饱和层向钢内层深处进行扩散,形成一定深度的渗氮层。
3.渗氮层的组织根据Fe-N状态图,渗氮层主要由α、γ、γ,、ε四个相组成。
﹝1﹞α相氮在α-Fe中的间隙固溶体。
最大溶解度为0.1%。
﹝2﹞γ相氮在γ-Fe中的间隙固溶体。
﹝3﹞γ,相为一可变成分的间隙相化合物,含氮量在5.7-6.1%之间,成分符合Fe4-N。
﹝4﹞ε相是含氮量变化范围相当宽的化合物,成分在8.25-11.0%之间变化。
ε相硬度高,脆性大。
4.合金元素的作用碳钢和合金钢中由于碳和合金元素的作用,也影响渗氮层的形成。
碳的存在会使氮的扩散受阻,减小渗氮层的厚度。
钢中大部分合金元素都能形成氮化物,按氮化物的稳定性﹝稳定性越高,硬度也越高﹞次序排列依次为:Ti、Al、V、W、Mo、Cr、Mn、Fe。
所以,为了在表面得到高的硬度和耐磨性,必须向钢中加入能与氮形成稳定氮化物的合金元素。
同时,V、W、Mo、Cr等合金元素还能改善钢的组织,提高心部的强韧性。
合金元素也会使氮的扩散受阻,减小渗氮层的厚度。
﹝二﹞离子渗氮工艺原理离子渗氮渗氮层的形成也是由分解、吸收、扩散三个基本过程组成的。
渗氮与氮化处理
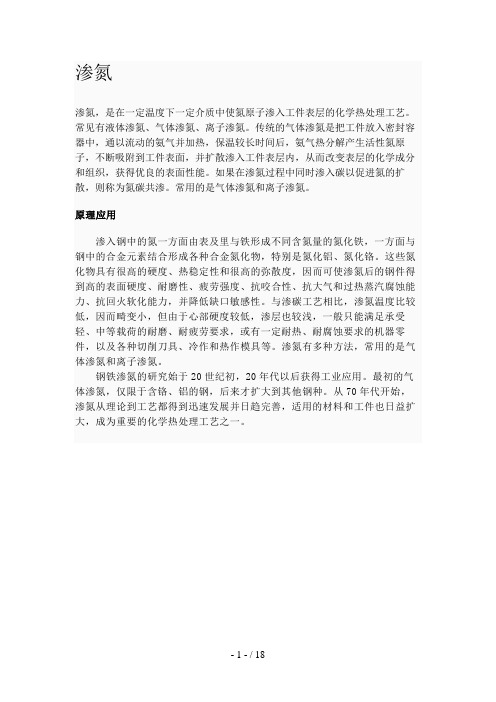
渗氮渗氮,是在一定温度下一定介质中使氮原子渗入工件表层的化学热处理工艺。
常见有液体渗氮、气体渗氮、离子渗氮。
传统的气体渗氮是把工件放入密封容器中,通以流动的氨气并加热,保温较长时间后,氨气热分解产生活性氮原子,不断吸附到工件表面,并扩散渗入工件表层内,从而改变表层的化学成分和组织,获得优良的表面性能。
如果在渗氮过程中同时渗入碳以促进氮的扩散,则称为氮碳共渗。
常用的是气体渗氮和离子渗氮。
原理应用渗入钢中的氮一方面由表及里与铁形成不同含氮量的氮化铁,一方面与钢中的合金元素结合形成各种合金氮化物,特别是氮化铝、氮化铬。
这些氮化物具有很高的硬度、热稳定性和很高的弥散度,因而可使渗氮后的钢件得到高的表面硬度、耐磨性、疲劳强度、抗咬合性、抗大气和过热蒸汽腐蚀能力、抗回火软化能力,并降低缺口敏感性。
与渗碳工艺相比,渗氮温度比较低,因而畸变小,但由于心部硬度较低,渗层也较浅,一般只能满足承受轻、中等载荷的耐磨、耐疲劳要求,或有一定耐热、耐腐蚀要求的机器零件,以及各种切削刀具、冷作和热作模具等。
渗氮有多种方法,常用的是气体渗氮和离子渗氮。
钢铁渗氮的研究始于20世纪初,20年代以后获得工业应用。
最初的气体渗氮,仅限于含铬、铝的钢,后来才扩大到其他钢种。
从70年代开始,渗氮从理论到工艺都得到迅速发展并日趋完善,适用的材料和工件也日益扩大,成为重要的化学热处理工艺之一。
气体渗氮一般以提高金属的耐磨性为主要目的,因此需要获得高的表面硬度。
它适用于38CrMoAl等渗氮钢。
渗氮后工件表面硬度可达HV850~1200。
渗氮温度低,工件畸变小,可用于精度要求高、又有耐磨要求的零件,如镗床镗杆和主轴、磨床主轴、气缸套筒等。
但由于渗氮层较薄,不适于承受重载的耐磨零件。
气体参氮可采用一般渗氮法(即等温渗氮)或多段(二段、三段)渗氮法。
前者是在整个渗氮过程中渗氮温度和氨气分解率保持不变。
温度一般在480~520℃之间,氨气分解率为15~30%,保温时间近80小时。
钢的离子渗氮层的组织结构特点
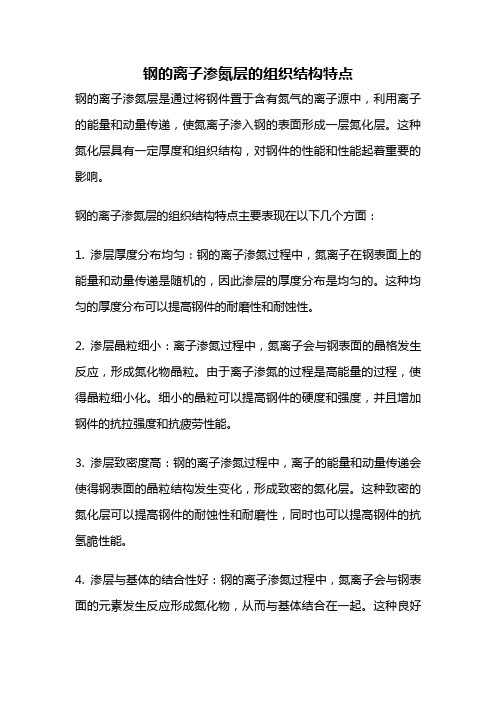
钢的离子渗氮层的组织结构特点钢的离子渗氮层是通过将钢件置于含有氮气的离子源中,利用离子的能量和动量传递,使氮离子渗入钢的表面形成一层氮化层。
这种氮化层具有一定厚度和组织结构,对钢件的性能和性能起着重要的影响。
钢的离子渗氮层的组织结构特点主要表现在以下几个方面:1. 渗层厚度分布均匀:钢的离子渗氮过程中,氮离子在钢表面上的能量和动量传递是随机的,因此渗层的厚度分布是均匀的。
这种均匀的厚度分布可以提高钢件的耐磨性和耐蚀性。
2. 渗层晶粒细小:离子渗氮过程中,氮离子会与钢表面的晶格发生反应,形成氮化物晶粒。
由于离子渗氮的过程是高能量的过程,使得晶粒细小化。
细小的晶粒可以提高钢件的硬度和强度,并且增加钢件的抗拉强度和抗疲劳性能。
3. 渗层致密度高:钢的离子渗氮过程中,离子的能量和动量传递会使得钢表面的晶粒结构发生变化,形成致密的氮化层。
这种致密的氮化层可以提高钢件的耐蚀性和耐磨性,同时也可以提高钢件的抗氢脆性能。
4. 渗层与基体的结合性好:钢的离子渗氮过程中,氮离子会与钢表面的元素发生反应形成氮化物,从而与基体结合在一起。
这种良好的结合性可以提高钢件的粘结强度和抗剥离性能。
5. 渗层中氮的含量高:离子渗氮过程中,氮离子会大量渗入钢的表面形成氮化层,使得渗层中氮的含量较高。
高含氮量的渗层可以提高钢件的硬度和抗磨性能,并且增加钢件的耐蚀性和耐高温性能。
钢的离子渗氮层的组织结构特点包括渗层厚度分布均匀、渗层晶粒细小、渗层致密度高、渗层与基体的结合性好以及渗层中氮的含量高。
这些特点使得钢的离子渗氮层具有优异的性能,提高了钢件的耐磨性、耐蚀性、抗拉强度、抗疲劳性能和耐高温性能,广泛应用于各个领域。
离子氮化技术的特点
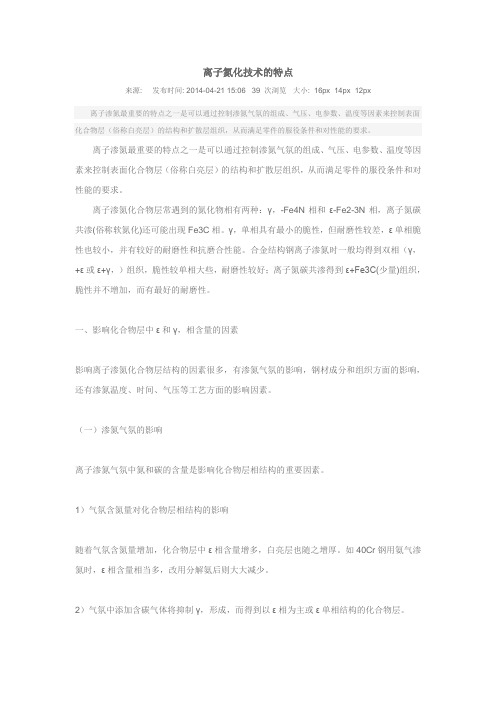
离子氮化技术的特点来源: 发布时间: 2014-04-21 15:06 39 次浏览大小: 16px 14px 12px 离子渗氮最重要的特点之一是可以通过控制渗氮气氛的组成、气压、电参数、温度等因素来控制表面化合物层(俗称白亮层)的结构和扩散层组织,从而满足零件的服役条件和对性能的要求。
离子渗氮最重要的特点之一是可以通过控制渗氮气氛的组成、气压、电参数、温度等因素来控制表面化合物层(俗称白亮层)的结构和扩散层组织,从而满足零件的服役条件和对性能的要求。
离子渗氮化合物层常遇到的氮化物相有两种:γ,-Fe4N相和ε-Fe2-3N相,离子氮碳共渗(俗称软氮化)还可能出现Fe3C相。
γ,单相具有最小的脆性,但耐磨性较差,ε单相脆性也较小,并有较好的耐磨性和抗磨合性能。
合金结构钢离子渗氮时一般均得到双相(γ,+ε或ε+γ,)组织,脆性较单相大些,耐磨性较好;离子氮碳共渗得到ε+Fe3C(少量)组织,脆性并不增加,而有最好的耐磨性。
一、影响化合物层中ε和γ,相含量的因素影响离子渗氮化合物层结构的因素很多,有渗氮气氛的影响,钢材成分和组织方面的影响,还有渗氮温度、时间、气压等工艺方面的影响因素。
(一)渗氮气氛的影响离子渗氮气氛中氮和碳的含量是影响化合物层相结构的重要因素。
1)气氛含氮量对化合物层相结构的影响随着气氛含氮量增加,化合物层中ε相含量增多,白亮层也随之增厚。
如40Cr钢用氨气渗氮时,ε相含量相当多,改用分解氨后则大大减少。
2)气氛中添加含碳气体将抑制γ,形成,而得到以ε相为主或ε单相结构的化合物层。
如气氛中加入丙烷(C3H8)后,化合物层中ε含量迅速增多,基本由ε单相组成。
含碳量再增多则化合物层中开始出现Fe3C,含碳量继续增多,则Fe3C增多,ε减少直到完全消失。
离子渗氮需要严格控制气氛中含碳量,使之能得到ε单相或ε+少量Fe3C的双相组织。
这样的组织其硬度和耐磨性均比单纯离子氮化有较大提高。
如45钢在含80%N2的氮氢气氛中570℃渗氮3小时,表面硬度只有575-603HV0.5,加入丙烷气后,当含碳量达到临界值(不出现Fe3C的最大含碳量)时,ε相化合物层的硬度达730-781 HV0.5。
热处理科普氮化知识
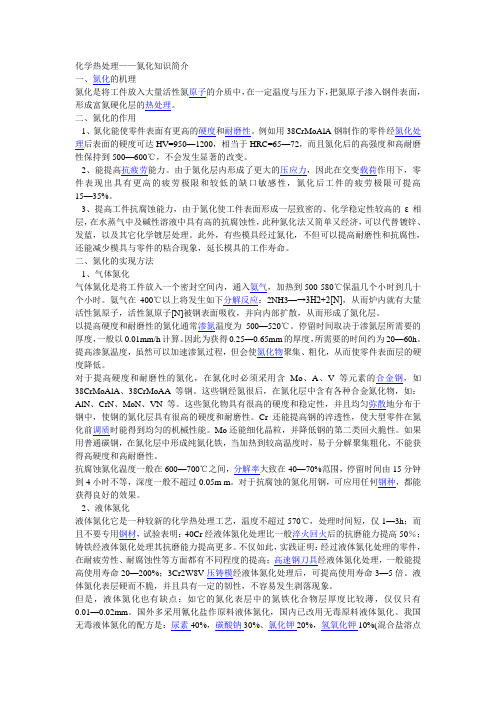
化学热处理——氮化知识简介一、氮化的机理氮化是将工件放入大量活性氮原子的介质中,在一定温度与压力下,把氮原子渗入钢件表面,形成富氮硬化层的热处理。
二、氮化的作用1、氮化能使零件表面有更高的硬度和耐磨性。
例如用38CrMoAlA钢制作的零件经氮化处理后表面的硬度可达HV=950—1200,相当于HRC=65—72,而且氮化后的高强度和高耐磨性保持到500—600℃,不会发生显著的改变。
2、能提高抗疲劳能力。
由于氮化层内形成了更大的压应力,因此在交变载荷作用下,零件表现出具有更高的疲劳极限和较低的缺口敏感性,氮化后工件的疲劳极限可提高15—35%。
3、提高工件抗腐蚀能力,由于氮化使工件表面形成一层致密的、化学稳定性较高的ε相层,在水蒸气中及碱性溶液中具有高的抗腐蚀性,此种氮化法又简单又经济,可以代替镀锌、发蓝,以及其它化学镀层处理。
此外,有些模具经过氮化,不但可以提高耐磨性和抗腐性,还能减少模具与零件的粘合现象,延长模具的工作寿命。
二、氮化的实现方法1、气体氮化气体氮化是将工件放入一个密封空间内,通入氨气,加热到500-580℃保温几个小时到几十个小时。
氨气在400℃以上将发生如下分解反应:2NH3—→3H2+2[N],从而炉内就有大量活性氮原子,活性氮原子[N]被钢表面吸收,并向内部扩散,从而形成了氮化层。
以提高硬度和耐磨性的氮化通常渗氮温度为500—520℃。
停留时间取决于渗氮层所需要的厚度,一般以0.01mm/h计算。
因此为获得0.25—0.65mm的厚度,所需要的时间约为20—60h。
提高渗氮温度,虽然可以加速渗氮过程,但会使氮化物聚集、粗化,从而使零件表面层的硬度降低。
对于提高硬度和耐磨性的氮化,在氮化时必须采用含Mo、A、V等元素的合金钢,如38CrMoAlA、38CrMoAA等钢。
这些钢经氮很后,在氮化层中含有各种合金氮化物,如:AlN、CrN、MoN、VN等。
这些氮化物具有很高的硬度和稳定性,并且均匀弥散地分布于钢中,使钢的氮化层具有很高的硬度和耐磨性。
离子氮化对高速钢表面类金刚石膜性能的影响
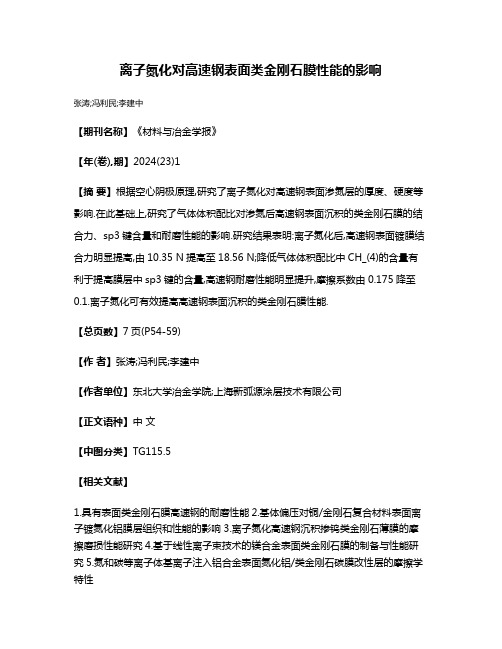
离子氮化对高速钢表面类金刚石膜性能的影响
张涛;冯利民;李建中
【期刊名称】《材料与冶金学报》
【年(卷),期】2024(23)1
【摘要】根据空心阴极原理,研究了离子氮化对高速钢表面渗氮层的厚度、硬度等影响.在此基础上,研究了气体体积配比对渗氮后高速钢表面沉积的类金刚石膜的结合力、sp3键含量和耐磨性能的影响.研究结果表明:离子氮化后,高速钢表面镀膜结合力明显提高,由10.35 N提高至18.56 N;降低气体体积配比中CH_(4)的含量有利于提高膜层中sp3键的含量,高速钢耐磨性能明显提升,摩擦系数由0.175降至0.1.离子氮化可有效提高高速钢表面沉积的类金刚石膜性能.
【总页数】7页(P54-59)
【作者】张涛;冯利民;李建中
【作者单位】东北大学冶金学院;上海新弧源涂层技术有限公司
【正文语种】中文
【中图分类】TG115.5
【相关文献】
1.具有表面类金刚石膜高速钢的耐磨性能
2.基体偏压对铜/金刚石复合材料表面离子镀氮化铝膜层组织和性能的影响
3.离子氮化高速钢沉积掺钨类金刚石薄膜的摩擦磨损性能研究
4.基于线性离子束技术的镁合金表面类金刚石膜的制备与性能研究
5.氮和碳等离子体基离子注入铝合金表面氮化铝/类金刚石碳膜改性层的摩擦学特性
因版权原因,仅展示原文概要,查看原文内容请购买。
离子氮化变形

离子氮化变形
【原创版】
目录
1.离子氮化变形的定义
2.离子氮化变形的过程
3.离子氮化变形的影响因素
4.离子氮化变形的应用
5.离子氮化变形的未来发展
正文
1.离子氮化变形的定义
离子氮化变形,是一种金属材料在离子氮化气氛中进行的一种表面处理技术。
这种技术可以使金属材料在保持其原有性能的基础上,提高其硬度、耐磨性、抗腐蚀性等一系列性能。
2.离子氮化变形的过程
离子氮化变形的过程主要分为两个阶段。
第一阶段是离子氮化,也就是在氮气离子轰击的金属材料表面形成氮化物。
第二阶段是变形,也就是在离子轰击的过程中,金属材料表面产生应力,从而形成一定的变形。
3.离子氮化变形的影响因素
离子氮化变形的影响因素主要包括离子轰击的能量、氮气离子的流量、处理时间和温度等。
这些因素都会影响离子氮化变形的效果。
4.离子氮化变形的应用
离子氮化变形技术广泛应用于各种金属材料的表面处理,如钢铁、铝合金、铜合金等。
它可以提高金属材料的硬度、耐磨性、抗腐蚀性,从而提高金属材料的使用寿命。
5.离子氮化变形的未来发展
随着科技的发展,离子氮化变形技术也在不断改进。
第1页共1页。
氮化处理资料整理
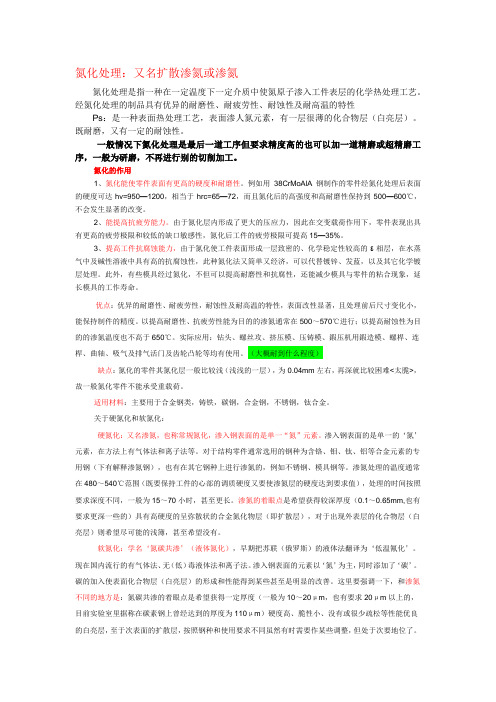
氮化处理:又名扩散渗氮或渗氮氮化处理是指一种在一定温度下一定介质中使氮原子渗入工件表层的化学热处理工艺。
经氮化处理的制品具有优异的耐磨性、耐疲劳性、耐蚀性及耐高温的特性Ps:是一种表面热处理工艺,表面渗人氮元素,有一层很薄的化合物层(白亮层)。
既耐磨,又有一定的耐蚀性。
一般情况下氮化处理是最后一道工序但要求精度高的也可以加一道精磨或超精磨工序,一般为研磨,不再进行别的切削加工。
氮化的作用1、氮化能使零件表面有更高的硬度和耐磨性。
例如用38CrMoAlA钢制作的零件经氮化处理后表面的硬度可达hv=950—1200,相当于hrc=65—72,而且氮化后的高强度和高耐磨性保持到500—600℃,不会发生显著的改变。
2、能提高抗疲劳能力。
由于氮化层内形成了更大的压应力,因此在交变载荷作用下,零件表现出具有更高的疲劳极限和较低的缺口敏感性,氮化后工件的疲劳极限可提高15—35%。
3、提高工件抗腐蚀能力,由于氮化使工件表面形成一层致密的、化学稳定性较高的ε相层,在水蒸气中及碱性溶液中具有高的抗腐蚀性,此种氮化法又简单又经济,可以代替镀锌、发蓝,以及其它化学镀层处理。
此外,有些模具经过氮化,不但可以提高耐磨性和抗腐性,还能减少模具与零件的粘合现象,延长模具的工作寿命。
优点:优异的耐磨性、耐疲劳性,耐蚀性及耐高温的特性,表面改性显著,且处理前后尺寸变化小,能保持制件的精度。
以提高耐磨性、抗疲劳性能为目的的渗氮通常在500~570℃进行;以提高耐蚀性为目的的渗氮温度也不高于650℃。
实际应用:钻头、螺丝攻、挤压模、压铸模、鍜压机用鍜造模、螺桿、连桿、曲轴、吸气及排气活门及齿轮凸轮等均有使用。
(大概耐到什么程度)缺点:氮化的零件其氮化层一般比较浅(浅浅的一层),为0.04mm左右,再深就比较困难<太脆>,故一般氮化零件不能承受重载荷。
适用材料:主要用于合金钢类,铸铁,碳钢,合金钢,不锈钢,钛合金。
关于硬氮化和软氮化:硬氮化:又名渗氮,也称常规氮化,渗入钢表面的是单一“氮”元素。
渗氮及氮化处理资料
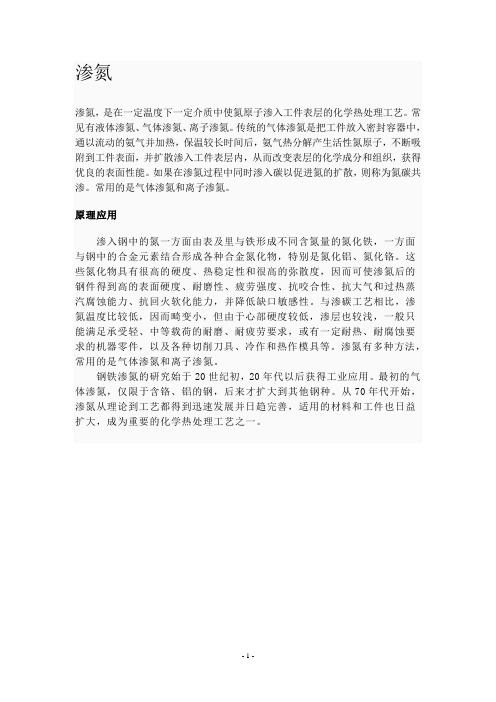
渗氮渗氮,是在一定温度下一定介质中使氮原子渗入工件表层的化学热处理工艺。
常见有液体渗氮、气体渗氮、离子渗氮。
传统的气体渗氮是把工件放入密封容器中,通以流动的氨气并加热,保温较长时间后,氨气热分解产生活性氮原子,不断吸附到工件表面,并扩散渗入工件表层内,从而改变表层的化学成分和组织,获得优良的表面性能。
如果在渗氮过程中同时渗入碳以促进氮的扩散,则称为氮碳共渗。
常用的是气体渗氮和离子渗氮。
原理应用渗入钢中的氮一方面由表及里与铁形成不同含氮量的氮化铁,一方面与钢中的合金元素结合形成各种合金氮化物,特别是氮化铝、氮化铬。
这些氮化物具有很高的硬度、热稳定性和很高的弥散度,因而可使渗氮后的钢件得到高的表面硬度、耐磨性、疲劳强度、抗咬合性、抗大气和过热蒸汽腐蚀能力、抗回火软化能力,并降低缺口敏感性。
与渗碳工艺相比,渗氮温度比较低,因而畸变小,但由于心部硬度较低,渗层也较浅,一般只能满足承受轻、中等载荷的耐磨、耐疲劳要求,或有一定耐热、耐腐蚀要求的机器零件,以及各种切削刀具、冷作和热作模具等。
渗氮有多种方法,常用的是气体渗氮和离子渗氮。
钢铁渗氮的研究始于20世纪初,20年代以后获得工业应用。
最初的气体渗氮,仅限于含铬、铝的钢,后来才扩大到其他钢种。
从70年代开始,渗氮从理论到工艺都得到迅速发展并日趋完善,适用的材料和工件也日益扩大,成为重要的化学热处理工艺之一。
气体渗氮一般以提高金属的耐磨性为主要目的,因此需要获得高的表面硬度。
它适用于38CrMoAl等渗氮钢。
渗氮后工件表面硬度可达HV850~1200。
渗氮温度低,工件畸变小,可用于精度要求高、又有耐磨要求的零件,如镗床镗杆和主轴、磨床主轴、气缸套筒等。
但由于渗氮层较薄,不适于承受重载的耐磨零件。
气体参氮可采用一般渗氮法(即等温渗氮)或多段(二段、三段)渗氮法。
前者是在整个渗氮过程中渗氮温度和氨气分解率保持不变。
温度一般在480~520℃之间,氨气分解率为15~30%,保温时间近80小时。
hb∕z 20023-2014 航空钢制件离子渗氮、离子氮碳共渗工艺

hb∕z 20023-2014 航空钢制件离子渗氮、离子氮碳共渗工艺全文共四篇示例,供读者参考第一篇示例:航空制造业一直是高科技领域的代表之一,其所需材料和工艺要求也非常高。
在航空制造中,钢材是一种常用的材料,而离子渗氮和离子氮碳共渗工艺是常用的表面处理工艺之一。
hb∕z 20023-2014是我国航空钢制件离子渗氮、离子氮碳共渗工艺的标准,它规定了航空钢制件表面渗氮、渗氮碳的要求和工艺规范,保证了航空钢制件的使用性能和寿命。
离子渗氮是一种常见的表面处理工艺,通过在高温高压下,将氮气分子离子化后使其在工件表面沉积形成氮化层。
离子渗氮工艺可以有效提高航空钢制件的硬度、耐磨性、耐蚀性等性能,延长其使用寿命。
而离子氮碳共渗工艺是在离子渗氮的基础上添加少量的碳源,使得在渗氮的同时还能渗碳,形成氮碳复合层,提高钢件的总体性能。
hb∕z 20023-2014标准主要包括了钢件离子渗氮和离子氮碳共渗的工艺条件、设备要求、工艺流程、控制要求等内容。
要求渗氮、渗碳层的厚度、硬度、成分、晶粒度等满足标准要求,确保表面处理的质量和稳定性。
还要求对设备、工艺参数进行严格控制,确保工艺的可重复性和稳定性,防止因变量波动导致产品质量不稳定。
航空钢制件的表面处理对于提高其耐磨性、耐腐蚀性、抗氧化性等性能至关重要。
hb∕z 20023-2014标准为航空钢制件的表面处理提供了一套科学、规范的工艺流程,确保了航空钢制件的质量和性能。
该标准的实施也促进了我国航空制造产业的发展和提高,推动了相关技术的研究和创新,提升了整个产业的竞争力。
第二篇示例:随着现代航空工业的发展,对航空钢制件的材料性能要求越来越高。
在航空工程中,航空钢制件不仅需要具备优异的强度和硬度,同时还需要具备耐磨、耐腐蚀等性能。
为了提高航空钢制件的性能,离子渗氮和离子氮碳共渗工艺成为了航空工业中重要的表面处理方法。
hb∕z 20023-2014标准对航空钢制件的离子渗氮以及离子氮碳共渗工艺进行了规范,确保了航空钢制件的质量和性能。
钢铁零件渗氮氮化后的硬度及厚度

钢铁零件渗氮氮化后的硬度及厚度检测方法:----随着工业的发展,渗氮处理被更多的应用到各行各业,对渗氮处理的检测要求也日益提高。
下面上海中研仪器制造厂为您简单阐述钢铁零件渗氮处理后的硬度及厚度检测。
----渗氮(气体渗氮、离子渗氮、碳氮共渗、辉光离子氮化)零件的主要技术要求是有效渗氮层深度,表面硬度和局部硬度。
某些零件还有渗氮层脆性等级评定要求,完成以上要求,都需显微维氏硬度检测进行测定。
----渗氮层从金相组织划分,包括从最外层化合物层(白亮层)到扩散层与基体组织明显分界处为止的深度。
显微维氏硬度检测,依据从工件表面测至与基体有明显界定硬度值处的垂直距离。
----渗氮层深度以字母DN表示。
渗氮层深度硬度检测方法:1、试样的准备a、试样应从渗氮零件上切取,如工件不能破坏,也可用与零件相同材料和相同处理工艺的小试样切取后检测。
b、试样切取时要注意,应垂直渗氮层表面取样(详见金相试样取样方法),取样后进行必要的磨抛处理,在磨抛过程中应注意冷却,不能使工件过热,边缘不要出现倒角等。
c、检查渗氮层脆性的试样,表面粗糙度要求>Ra0.25-0.63um,但不允许把表面化合物层磨掉。
2、检测a、根据国标规定,一般选用显微硬度计,检测力通常选用0.3--1KG,从试样表面测至比基体维氏硬度值高50HV处的垂直距离为渗氮层厚度。
(通常采用梯式硬度测法,即从试样表面开始,每间隔一定距离打一点)b、基体硬度的取点与测定,一般在3倍左右渗氮层深度的距离处测得的硬度值(至少取3点,平均值)做为基体硬度值。
c、对于渗氮层硬度变化很平缓的钢种,(如碳钢、低碳合金钢制件),其渗氮层深度可以从试样表面沿垂直方向测至比基体维氏硬度高30HV处。
d、当渗氮层深度有的特别浅,有的则较深时,检测力可以在0.2KG范围内选择(并注明,如HV0.2)e、结果的表示,渗氮层深度用字母DN表示,深度以毫米计,取小数点后两位。
(如:0.35DN 300HV0.3,表示渗氮层厚度为0.35mm,界限硬度值为300HV,检测力为0.3KG)。
氮化工艺中的事项
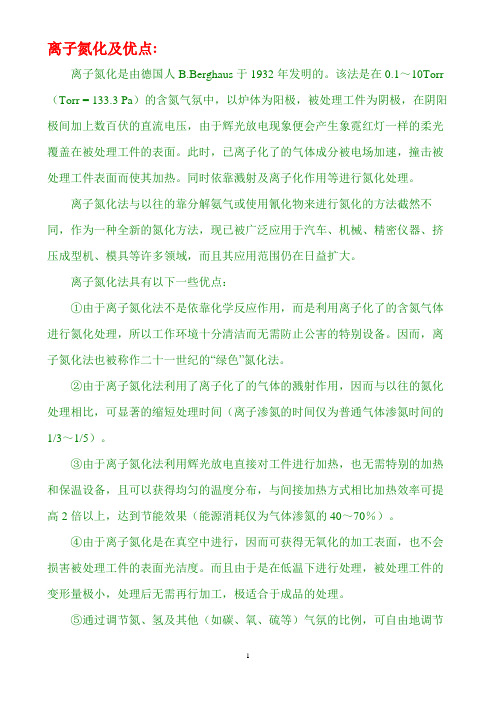
离子氮化及优点:离子氮化是由德国人B.Berghaus于1932年发明的。
该法是在0.1~10Torr (Torr = 133.3 Pa)的含氮气氛中,以炉体为阳极,被处理工件为阴极,在阴阳极间加上数百伏的直流电压,由于辉光放电现象便会产生象霓红灯一样的柔光覆盖在被处理工件的表面。
此时,已离子化了的气体成分被电场加速,撞击被处理工件表面而使其加热。
同时依靠溅射及离子化作用等进行氮化处理。
离子氮化法与以往的靠分解氨气或使用氰化物来进行氮化的方法截然不同,作为一种全新的氮化方法,现已被广泛应用于汽车、机械、精密仪器、挤压成型机、模具等许多领域,而且其应用范围仍在日益扩大。
离子氮化法具有以下一些优点:①由于离子氮化法不是依靠化学反应作用,而是利用离子化了的含氮气体进行氮化处理,所以工作环境十分清洁而无需防止公害的特别设备。
因而,离子氮化法也被称作二十一世纪的“绿色”氮化法。
②由于离子氮化法利用了离子化了的气体的溅射作用,因而与以往的氮化处理相比,可显著的缩短处理时间(离子渗氮的时间仅为普通气体渗氮时间的1/3~1/5)。
③由于离子氮化法利用辉光放电直接对工件进行加热,也无需特别的加热和保温设备,且可以获得均匀的温度分布,与间接加热方式相比加热效率可提高2倍以上,达到节能效果(能源消耗仅为气体渗氮的40~70%)。
④由于离子氮化是在真空中进行,因而可获得无氧化的加工表面,也不会损害被处理工件的表面光洁度。
而且由于是在低温下进行处理,被处理工件的变形量极小,处理后无需再行加工,极适合于成品的处理。
⑤通过调节氮、氢及其他(如碳、氧、硫等)气氛的比例,可自由地调节化合物层的相组成,从而获得预期的机械性能。
⑥离子氮化从380℃起即可进行氮化处理,此外,对钛等特殊材料也可在850℃的高温下进行氮化处理,因而适应范围十分广泛。
⑦由于离子氮化是在低气压下以离子注入的方式进行,因而耗气量极少(仅为气体渗氮的百分之几),可大大降低处离子氮化的常见缺陷:一、硬度偏低生产实践中,工件氮化后其表面硬度有时达不到工艺规定的要求,轻者可以返工,重者则造成报废。
氮化钢的介绍

一、氮化用钢简介传统的合金钢料中之铝、铬、钒及钼元素对渗氮甚有帮助。
这些元素在渗氮温度中,与初生态的氮原子接触时,就生成安定的氮化物。
尤其是钼元素,不仅作为生成氮化物元素,亦作为降低在渗氮温度时所发生的脆性。
其他合金钢中的元素,如镍、铜、硅、锰等,对渗氮特性并无多大的帮助。
一般而言,如果钢料中含有一种或多种的氮化物生成元素,氮化后的效果比较良好。
其中铝是最强的氮化物元素,含有0.85~1.5%铝的渗氮结果最佳。
在含铬的铬钢而言,如果有足够的含量,亦可得到很好的效果。
但没有含合金的碳钢,因其生成的渗氮层很脆,容易剥落,不适合作为渗氮钢。
一般常用的渗氮钢有六种如下:(1)含铝元素的低合金钢(标准渗氮钢)(2)含铬元素的中碳低合金钢SAE 4100,4300,5100,6100,8600,8700,9800系。
(3)热作模具钢(含约5%之铬)SAE H11 (SKD – 61)H12,H13(4)肥粒铁及麻田散铁系不锈钢SAE 400系(5)奥斯田铁系不锈钢SAE 300系(6)析出硬化型不锈钢17 - 4PH,17 – 7PH,A– 286等含铝的标准渗氮钢,在氮化后虽可得到很高的硬度及高耐磨的表层,但其硬化层亦很脆。
相反的,含铬的低合金钢硬度较低,但硬化层即比较有韧性,其表面亦有相当的耐磨性及耐束心性。
因此选用材料时,宜注意材料之特徵,充分利用其优点,俾符合零件之功能。
至于工具钢如H11(SKD61)D2(SKD – 11),即有高表面硬度及高心部强度。
二、氮化处理技术:调质后的零件,在渗氮处理前须彻底清洗干净,兹将包括清洗的渗氮工作程序分述如下:(1)渗氮前的零件表面清洗大部分零件,可以使用气体去油法去油后立刻渗氮。
但在渗氮前之最后加工方法若采用抛光、研磨、磨光等,即可能产生阻碍渗氮的表面层,致使渗氮后,氮化层不均匀或发生弯曲等缺陷。
此时宜采用下列二种方法之一去除表面层。
第一种方法在渗氮前首先以气体去油。
氮化工艺中的事项
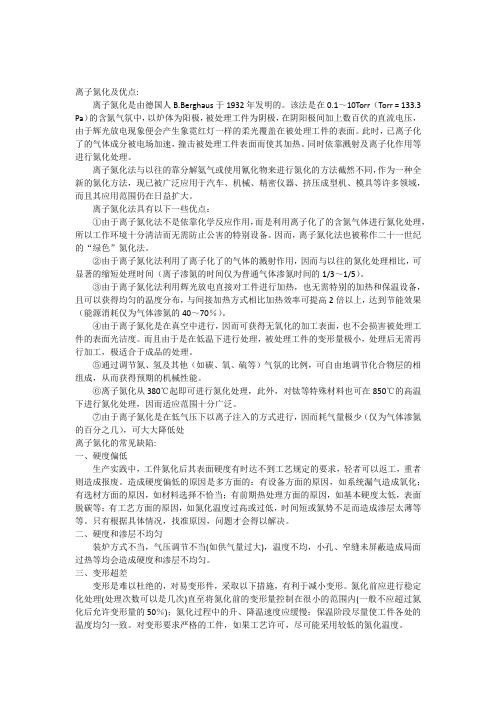
离子氮化及优点:离子氮化是由德国人B.Berghaus于1932年发明的。
该法是在0.1~10Torr(Torr = 133.3 Pa)的含氮气氛中,以炉体为阳极,被处理工件为阴极,在阴阳极间加上数百伏的直流电压,由于辉光放电现象便会产生象霓红灯一样的柔光覆盖在被处理工件的表面。
此时,已离子化了的气体成分被电场加速,撞击被处理工件表面而使其加热。
同时依靠溅射及离子化作用等进行氮化处理。
离子氮化法与以往的靠分解氨气或使用氰化物来进行氮化的方法截然不同,作为一种全新的氮化方法,现已被广泛应用于汽车、机械、精密仪器、挤压成型机、模具等许多领域,而且其应用范围仍在日益扩大。
离子氮化法具有以下一些优点:①由于离子氮化法不是依靠化学反应作用,而是利用离子化了的含氮气体进行氮化处理,所以工作环境十分清洁而无需防止公害的特别设备。
因而,离子氮化法也被称作二十一世纪的“绿色”氮化法。
②由于离子氮化法利用了离子化了的气体的溅射作用,因而与以往的氮化处理相比,可显著的缩短处理时间(离子渗氮的时间仅为普通气体渗氮时间的1/3~1/5)。
③由于离子氮化法利用辉光放电直接对工件进行加热,也无需特别的加热和保温设备,且可以获得均匀的温度分布,与间接加热方式相比加热效率可提高2倍以上,达到节能效果(能源消耗仅为气体渗氮的40~70%)。
④由于离子氮化是在真空中进行,因而可获得无氧化的加工表面,也不会损害被处理工件的表面光洁度。
而且由于是在低温下进行处理,被处理工件的变形量极小,处理后无需再行加工,极适合于成品的处理。
⑤通过调节氮、氢及其他(如碳、氧、硫等)气氛的比例,可自由地调节化合物层的相组成,从而获得预期的机械性能。
⑥离子氮化从380℃起即可进行氮化处理,此外,对钛等特殊材料也可在850℃的高温下进行氮化处理,因而适应范围十分广泛。
⑦由于离子氮化是在低气压下以离子注入的方式进行,因而耗气量极少(仅为气体渗氮的百分之几),可大大降低处离子氮化的常见缺陷:一、硬度偏低生产实践中,工件氮化后其表面硬度有时达不到工艺规定的要求,轻者可以返工,重者则造成报废。
碳钢离子氮化工艺
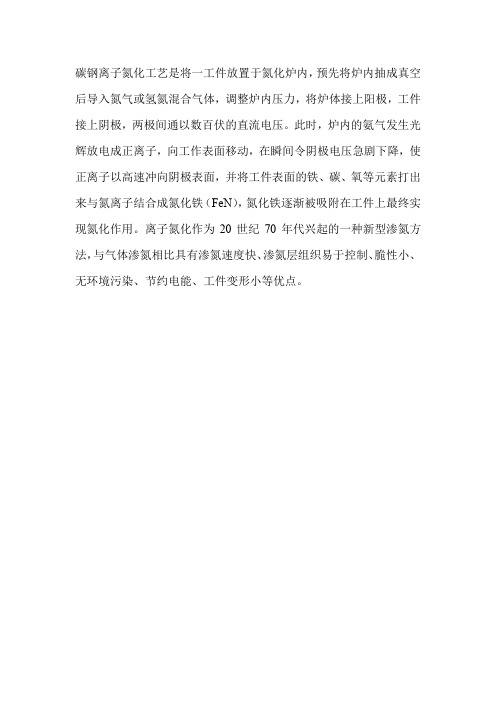
碳钢离子氮化工艺是将一工件放置于氮化炉内,预先将炉内抽成真空后导入氮气或氢氮混合气体,调整炉内压力,将炉体接上阳极,工件接上阴极,两极间通以数百伏的直流电压。
此时,炉内的氨气发生光辉放电成正离子,向工作表面移动,在瞬间令阴极电压急剧下降,使正离子以高速冲向阴极表面,并将工件表面的铁、碳、氧等元素打出来与氮离子结合成氮化铁(FeN),氮化铁逐渐被吸附在工件上最终实现氮化作用。
离子氮化作为20世纪70年代兴起的一种新型渗氮方法,与气体渗氮相比具有渗氮速度快、渗氮层组织易于控制、脆性小、无环境污染、节约电能、工件变形小等优点。
离子氮化 4340表面硬度
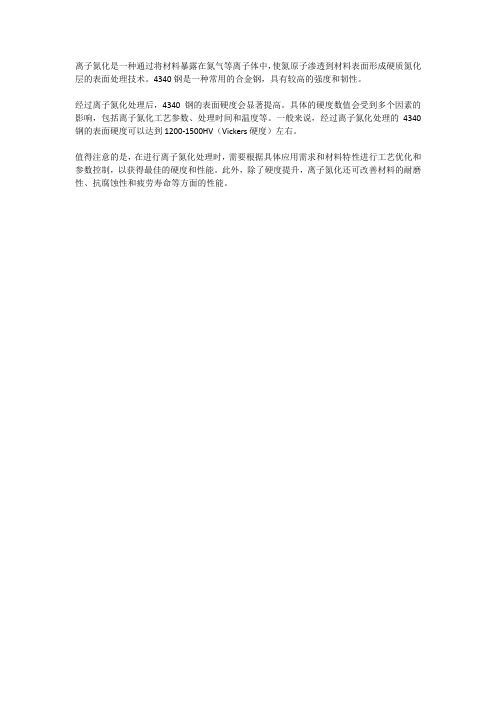
离子氮化是一种通过将材料暴露在氮气等离子体中,使氮原子渗透到材料表面形成硬质氮化层的表面处理技术。
4340钢是一种常用的合金钢,具有较高的强度和韧性。
经过离子氮化处理后,4340钢的表面硬度会显著提高。
具体的硬度数值会受到多个因素的影响,包括离子氮化工艺参数、处理时间和温度等。
一般来说,经过离子氮化处理的4340钢的表面硬度可以达到1200-1500HV(Vickers硬度)左右。
值得注意的是,在进行离子氮化处理时,需要根据具体应用需求和材料特性进行工艺优化和参数控制,以获得最佳的硬度和性能。
此外,除了硬度提升,离子氮化还可改善材料的耐磨性、抗腐蚀性和疲劳寿命等方面的性能。
- 1、下载文档前请自行甄别文档内容的完整性,平台不提供额外的编辑、内容补充、找答案等附加服务。
- 2、"仅部分预览"的文档,不可在线预览部分如存在完整性等问题,可反馈申请退款(可完整预览的文档不适用该条件!)。
- 3、如文档侵犯您的权益,请联系客服反馈,我们会尽快为您处理(人工客服工作时间:9:00-18:30)。
三.實驗原理1.鋼的氮化處理【1~4】1鋼的氧化處理氮化處理是使氮元素滲入鋼材表面,硬化鋼件表面的方法。
早在1923年即由德國克魯伯兵工廠的A. Fry博士發明了把含有鋁或鉻的合金鋼在無水氨氣中加熱至500~550℃之間保持20~100小時,可在鋼表面形成氮化層,使鋼表面硬化的氨氣氮化法。
隨後,經過不斷的改良與發展,目前已有處理時間較短、溫度較低和適用鋼種更廣泛的氮化法。
現在常用的方法有:氧化處理是使氧元素參入鋼材表面﹐硬化鋼件表面的方法。
早在1923年即由德國泊兵工廠的A.博士發明了把含的合金鋼在無水氨中加熱之使鋼表面的溫度表情廣之間保持20_100小時﹐可在鋼表嘛形成氧化層﹐使鋼表面硬化的氨畫法﹐隨后﹐經過不斷的改良與發展﹐目前已有處理時間較短﹐溫度較抵河底用鋼種更慣犯的氧化載荷現在常用的方法有﹕(1)硬氮化法:氣體氮化法(氨氣氮化法),液體氮化法(2)硬氧化法﹕氧化化方法(氨氧艷化法)﹐液體氧化法(3)。
(4)軟氮化法:氣體軟氮化法(混合氣體、尿素法),(5)軟氧化法﹕氧體軟艷化法(混合氣體﹐了樣法)。
液體軟氮化法(Tufftride法、Sulinuz法)。
(6)離子氮化法及電漿氮化法等。
(7)離子氧化法及電狡猾化法鄧。
2.離子氮化法【2】2.離子氧化法由於早期應用的氣體氮化法生產週期太長,並在表面形成脆性薄層,容易在使用時剝落,能處理的鋼材有侷限性,使其應用受到很大的限制。
其後,工業上又發展了液體氮化法,具有設備簡單、處理時間短及可氮化的鋼種較多等優點,但所得的硬化層較薄、使用的液體含有劇毒的氰話物鹽類,會產生公害問題。
離子氮化法在很大程度上克服了上述缺點,是對金屬零件進行表面處理的新技術,其目的乃為提高金屬零件的表面硬度、耐磨耗性、耐疲勞性和抗腐蝕性。
使用的液體含有劇毒的氰話物體類﹐會產生公害問題。
離子氧化法在很大程度上克增里上樣缺點﹐是對金屬零件進行表面處理的新技朮﹐其目是微提高盡速零件的表嘛硬度﹐那那霸為﹐勞性荷抗副食性。
此法於1932年起源於德國,由Bernhard Berghaus首先在低壓的氮氣和氨氣的混合氣體中,利用輝光放電發明輝光離子氮化法。
由於當時尚未掌握大電流的電源供應技術而未能實際應用於工業上。
於1967年德國Klockner Ionon公司的Oppel和Endenhofer 發表工業化成功後,此法開始風行。
此法與1932年起源于德國﹐有BERNHARD BERGHAUS 首先在低壓的荷氨煙袋氧體中﹐利用輝光放電發明輝光離子氧化法。
由于當時尚未中掌握大電流的電源而未能史記應用與工葉上。
與1967年德國KLOCHENER公司的OPPELENG FER 發表工業化成功后此法開始風行。
工業用離子氮化設備如圖2之概略圖,將工件放置於氮化爐內,預先將爐內抽成0.01~0.001 Torr的壓力後,導入氮氣或氮和氫的混合氣體,使爐內氣壓達1~10 Torr,此時爐體接陽極,工件接陰級,兩級間施以數百至數千伏特之直流電壓,使爐內氣體產生離子放電而進行氮化處理。
氮氣和氫氣之分壓比及處理溫度應視處理工件之材質、所需表層組織等情況作適當之調整。
溫度可用熱電偶或紅外線溫度計測定,由調整放電電壓而把溫度控制在氮化溫度範圍。
工業用離子氧化設備如涂2只開痧﹐將工件放置與氧化盧所﹐預先巨人抽成工業0.01-0.01TORR的壓力后﹐到拉詎虎產赫赫荷慶氣體﹐椒拉里氣壓低110TORR,表陳的澄清虧進行適當肢體煤正﹐溫度可用熱電有或紅外線溫度于今測定﹐有調整電壓而把溫度控制在氧化溫度范圍離子氮化法和其他氮化法比較時,有下列的主要特徵:不排放廢氣或污水,不發生公害。
(1)氮化時間短,又能做較低溫度的處理。
(1) 氧化時間短﹐又能做較低溫度的處理。
(2)利用輝光放電加熱,無須外加的加熱裝置。
(2) 利用輝光放電加熱﹐無須外加的加熱裝置。
(3)只有工件被加熱節省能源,不需設定昇溫時間,也不需保溫設備(3)利用工件倍加扔接生能源﹐不需流下渥升溫進﹐也不需保溫社。
(4)不要氮化的部位只要用軟鋼板覆蓋即可,不需鍍覆。
(5)(6)容易控制表面化合層的氮化物組織。
(7)氮化所消耗的氣體少,較經濟。
(8)沒有火災和爆炸的危險。
(9)可氮化不銹鋼和鈦等其他氮化法不易處理的材料。
(10)為了確保輝光放電,工件的放置密度有限,難做大量的處理。
3.鋼之離子氮化離子氮化向工件滲入的氮元素,不像氣體氮化是由氨氣分解而產生的活性氮原子,是被電場加速的電子碰撞含氮氣體的分子或原子而形成的離子,在工件表面富集形成的強活性氮原子。
鋼離子氮化的機構如圖3所示,爐內電漿與工件產生如下的交互作用:(1)氣氛中的氮原子被電離成氮離子與電子,此時,帶正電的氮離子向工件(負極)移動而帶負電的電子向爐壁(正極)移動。
(2)向爐壁移動的電子群會從電場中穫得足夠能量來與中性氣體原子碰撞,使氣體原子被離子化成離子和電子,或被激發而成激發原子。
當激發原子返回基態而釋出能量時,部份能量化為可見光覆蓋在負極(工件)表面,形成一層悅目的紫紅色輝光,如圖3(b)所示。
(3)氮離子群移動至離工件表面數mm處的陰極電位降區時(圖3(a)),由於電壓的急速下降所伴生的高電場強度所賦予的能量而被加速,因而以極高的速度轟擊工件,此時的氮離子引起兩種主要作用;(a)使工件因被碰撞而加熱。
(b)將工件表面的Fe、C和O等原子撞出並產生二次電子;被敲離表面的Fe與因離子放電而生成的氮原子或氮離子結合為FeN後,因吸附作用而回到工件表面,二次電子則在向正極遷移時又與氣氛中的分子或原子碰撞,產生新的氮和氫離子,使放電程序繼續進行,如圖3(c)所示。
(4)吸附在工件的FeN在溫度上昇及離子不斷轟擊下,逐漸不安定而分解放出氮原子而成為含氮較低的化合物Fe2N、Fe3N或Fe4N等,放出的活性氮原子一部份從表面向工件內部擴散形成擴散層;一部份重回到電漿中再與不斷被轟擊出來的Fe結合成為FeN,如圖3(d)所示。
如此反覆進行,使工件達到離子氮化的目的,而其氮化深度及顯微組織就依處理的溫度及時間來控制。
反應氣體除了氮氣之外,常再添加適量的氫氣,因氫氧有下述的幾個作用:(1)因離子化成為氫離子,亦會轟擊工件表面而幫忙加熱工件。
(2)可將工件表面的氧化物和碳化物等雜質還原,使表面保持在活化狀態而有助於氮的擴散效果。
(3)能夠使工件表層產生脫碳作用,促進氮的向內擴散。
(4)利用氫氣調節氮氣濃度,以穫得欲求的表層相結構;氮比例小時,表面易生成Fe4N相,而氮比例大時,則易生Fe3N相。
綜合相關文獻及上面圖3的說明,可將鐵系金屬的離子氮化機構分成如圖4所示的四個步驟:(1)離子的濺射與佈植,(2)氮化鐵的沉積與氮原子的吸附,(3)氮化鐵的分解與擴散,(4)反應與氮化物的成長。
四.實驗方法與步驟1.將研磨拋光後的試片泡在丙酮內,以超音波清洗器振盪3~5分鐘後,以鑷子取出試片,新鮮丙酮沖洗,吹風機吹乾。
2.把洗淨的試片迅速放入爐內,以免在空氣中暴露過久而遭受汙染或生成氧化物。
3.試片置放在工件架上應有適當距離,亦應確保試片及爐腔之乾淨,故工作人員應戴塑膠手套以免沾污試片、工件架或爐體。
4.確定試片已牢靠的置放於工件架後,關閉爐門,開始抽真空。
5.爐內真空度達10-2~10-3Torr後,導入氮氣和氫氣,利用氣體流量計調好氮與氫比例流量,在真空幫浦繼續運轉中將爐內壓力調至2 Torr。
6.啟動DC Power Supply的電源,打開冷卻風扇並確認運轉。
7.慢慢增加電壓(上升太快會產生電弧),同時利用紅外線幅射溫度計觀測爐內溫度,接著將爐內壓力升至所需壓力。
8.依試片材質設定溫度,通常在450~570℃,利用電壓及電流來控制。
9.等爐溫穩定後開始計處理時間,通常是1~10小時。
10.達到所需時間後,將DC Power Supply的電壓緩慢降至0,關閉直流電源。
11.關閉氮氣,待冷卻至室溫後,再關閉氫氣,因為氫氣在冷卻過程中有保護氣體的功能,可避免氮化後的試片被氧化。
12.確定旋緊氮化爐下方的Bellow V alve後,再關閉真空幫浦,以避免油氣回流污染了爐艙及試片。
13.打開洩氣閥,待氮化爐恢復長壓後,打開艙門取出試片,關閉冷卻風扇。
14.將離子氮化後試片之橫斷面研磨、拋光及腐蝕後,進行微硬度量測和金相觀察:(1)利用維克式硬度計,先量測試片表面硬度後,再自試片表面向內部每隔0.05 mm量測一次Hv硬度值。
(2)利用光學顯微鏡攝取氮化層、擴散層及心部的金相組織。
五.實驗結果1.繪製試片離子氮化後之硬度分佈曲線,並量取硬度大於Hv500的硬化深度。
2.分析金相組織照片,辨認化合物層(氮化層)及擴散層組織。
六.問題與討論1.鋼的氮化法有那些?離子氮化法有那些特性?2.試片表面的化合物層,主要的氮化物有那些?如何利用離子氮化的處理條件來控制表面生長的相?3.比較金相組織和硬度分佈曲線,並討論氮化層及擴散層與硬度和硬化深度之間的關係。
七.補充資料1.離子氮化處理時應注意事項:(1)離子氮化的實驗時間較長,使用的流量計、壓力表、真空計及電壓表等,應在實驗進行中定時檢查,遇有變動須立即調整。
(2)實驗進行中若有重大意外發生(尤其是有火發產生)時,第一優先步驟是:馬上關閉氫氣瓶之開闢。
(3)應保持室內空氣流動並絕對盡止火源接近,氫氣為爆炸性危險氣體。
(4)開機中絕對避免觸碰高壓導入端子,以免觸電。
2.試片研磨、拋光及硬度量測時應注意事項:(1)為避免化合物層在研磨或拋光時剝落或表面形成弧形面,應使用兩片銅片夾住氮化層,如圖5所示。
(2)表面硬度之量測若平行化合物層實施,則易崩落,使測定值誤差大,故常以從表面垂直化合物層實施而得。
八.參考文獻1.陳克昌,”鋼的氮化處理”,經濟部專業人員研究中心工程材料與熱處理研究班講義(編號83PIT23-05),台灣糖業股份有限公司訓練中心,1994。
2.陳克昌、莊國章,”鈦金屬及其合金之離子氮化”,表面工業雜誌,第53期,第28~40頁。
3.黃振賢,金屬熱處理,文京圖書公司,1985,第187~202頁。
4.金重勳,熱處理,復文書局,1986,第184~191頁。
5.莊國章、黃文澔、林嘉彥,”離子氮化系統操作手冊說明”,逢甲大學材料科學系表面工程與薄膜實驗室,1995年編寫,2001年修正。
圖1 離子氮化系統示意圖【5】圖2 工業用離子氮化設備概圖【5】圖3 習知的鐵系金屬離子氮化機構示意圖。
(a)電位在兩極之間的分佈情形;(b)輝光的分佈情形;(c)電將中的活性物種與基材之間的交互作用;(d)FeN的吸附與分解【5】圖4 修正後之鐵系金屬離子氮化機構示意圖【5】。