我国汽车召回缺陷分析及启示
缺陷产品召回制度中存在的问题及对策

缺陷产品召回制度中存在的问题及对策缺陷产品召回制度中存在的问题及对策在现代社会中,随着科技的不断发展与进步,各行各业也在加速发展,产品种类繁多,每天都有各式各样的产品上市。
然而,随之而来的问题是,由于制造过程中的缺陷或者设计上的问题,一些产品可能存在安全隐患,可能给消费者带来潜在的危害。
为了保障消费者的权益,许多国家都建立了缺陷产品召回制度。
然而,这个制度本身也存在一些问题,本文将对这些问题进行探讨,并提出对策以改进召回制度。
1. 召回范围的定义问题在实施缺陷产品召回制度时,最关键的问题是确定召回的范围。
召回范围应该足够广泛,包括所有可能存在问题的产品,以确保消费者的安全。
另召回范围过于宽泛可能导致一些不必要的召回,给企业带来不必要的负担。
在确定召回范围时,需要权衡各方的利益,确保在保障消费者权益的不给企业带来过大的阻碍。
对策:建立统一的召回标准和程序,明确召回范围的确定原则,避免召回的主观性和随意性。
通过制定明确的召回标准,包括产品缺陷的程度和影响范围等指标,来确保召回的公平性和客观性。
2. 召回效果的监督问题召回制度的目的是确保消费者的权益得到保障,但是召回行动本身的效果和效率也是需要被监督的。
一些企业可能对召回行动不够重视,或者执行不力,导致召回行动的效果不佳,消费者的权益仍然没有得到保障。
一些企业可能会采取搪塞和推诿的方式,对消费者提出的召回要求不予理会,或者故意拖延执行,这严重损害了消费者的权益。
对策:建立严格的监督机制,监督和评估召回行动的执行情况。
加大对企业的监督和处罚力度,对屡教不改的企业采取强制措施,确保召回行动得到有效执行,消费者的权益得到保障。
加强与消费者之间的沟通,建立投诉和举报机制,让消费者能够及时向有关部门反映问题,保障消费者的权益。
3. 召回信息的传递问题召回制度的有效性依赖于召回信息的及时传递和消费者的知情权。
然而,一些企业在召回行动中并不积极主动,甚至故意压制召回信息的发布,以避免对企业声誉的负面影响。
召回心得体会感悟(3篇)

第1篇随着我国经济的快速发展,汽车行业作为国民经济的重要支柱,也迎来了前所未有的繁荣。
然而,在市场激烈竞争的背景下,一些汽车企业在追求市场份额的过程中,忽视了对产品质量的把控,导致部分汽车出现了质量问题。
为了维护消费者的合法权益,保障人民群众的生命财产安全,我国政府高度重视汽车召回工作。
近期,我有幸参与了某品牌汽车的召回活动,现将我的心得体会感悟分享如下。
一、召回活动的背景某品牌汽车在我国市场占有率较高,但在生产过程中,部分车型存在安全隐患。
为了消除潜在的安全风险,该品牌汽车决定主动召回,为消费者提供免费维修服务。
此次召回活动涉及全国范围内,共计数十万辆汽车。
二、召回活动的过程1. 筹备阶段召回活动开始前,企业成立了召回工作组,负责召回活动的策划、实施和监督。
工作组首先对召回车辆进行了详细排查,确定了召回范围和具体车型。
同时,与相关部门沟通协调,确保召回活动顺利进行。
2. 宣传阶段企业通过多种渠道向消费者宣传召回活动,包括电视、广播、网络、朋友圈等。
宣传内容涵盖了召回原因、召回范围、召回流程、维修方案等信息,让消费者充分了解召回活动。
3. 召回实施阶段消费者在了解召回活动后,可前往就近的4S店进行免费维修。
召回过程中,企业严格执行维修标准,确保召回车辆安全可靠。
同时,对召回车辆进行质量跟踪,确保召回效果。
4. 后期跟踪阶段召回活动结束后,企业对召回车辆进行后期跟踪,了解维修效果和消费者满意度。
对于发现的问题,及时进行整改,确保召回活动取得实效。
三、召回活动的感悟1. 企业责任担当召回活动是企业履行社会责任的体现。
面对产品质量问题,企业敢于正视,主动召回,充分体现了企业对消费者的关爱和对产品质量的重视。
这种责任担当精神值得赞扬。
2. 消费者权益保障召回活动有力保障了消费者的合法权益。
通过免费维修,消除了安全隐患,降低了消费者在用车过程中的风险。
同时,召回活动也让消费者感受到了企业的诚信和责任感。
3. 监管部门监管力度召回活动的顺利进行,离不开监管部门的严格监管。
论我国召回制度存在的主要问题及危害
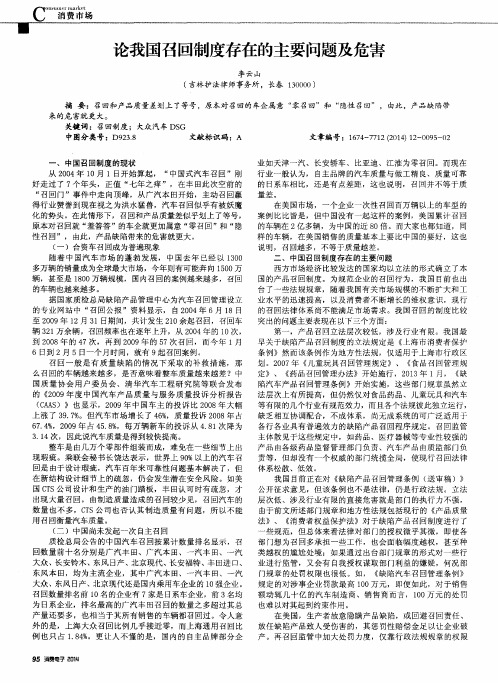
、
在 美 国 市场 , 一 个 企 业 一 次 性 召 回 百万 辆 以上 的 车 型 的 案 例 比 比 皆 是 ,但 中 国 没 有 一 起 这 样 的案 例 , 美 国 累 计 召 回 的车辆在 2 亿 多辆 ,为 中国的近 8 0倍 。而大家 也都知道 ,同 样 的车 辆 ,在 美 国销 售 的 质 量 基 本 上 要 比 中 国 的 要 好 ,这 也 说 明 ,召 回 越 多 ,不 等 于 质 量 越 差 。 二 、中国召 回制度存在的主要 问题 西 方 市 场 经 济 比较 发 达 的 国家 均 以立 法 的 形 式 确 立 了本 国 的产 品 召 回 制 度 。 为 规 范 企 业 的召 回行 为 , 我 国 目前 也 出 台了一些法 规规 章,随着我 国有关市场规模 的不断扩大和工 业 水 平 的 迅 速 提 高 , 以及 消 费者 不 断 增 长 的 维 权 意 识 ,现 行 的召回法律 体系 尚不能满足市场 需求 。我 国召回的制度 比较 突 出 的 问题 主 要 表现 在 以下 三 个 方 面 : 第 一,产品召回立法层次较低 ,涉及 行业有限 。我 国最 早关于缺 陷产品召回制度的立法规定 是 《 上海 市 消 费 者 保 护 条例 》然而该条例作为地方性法规 ,仅适 用于上海市行政 区 划 。2 0 0 7 年 《 儿童玩具 召回管理规定 》、 《 食 品召回管 理规 定 》、 《 药 品召 回管 理 办 法 》 开始 施行 ,2 0 1 3年 1月 , 《 缺 陷汽车产 品召回管理条例》开始 实施 ,这 些部 门规章虽然立 法层 次上有 所提高 ,但仍然仅对食 品药品、儿童玩具和汽 车 等有 限的几个行业有规范效力 ,而且各个法 规彼此独立运行 , 缺 乏相互协调配合 ,不成体系 ,尚无成 系统的可广泛适 用于 各行各 业具有普遍效力 的缺 陷产 品召回程序规定 。召回监管 主体散 见于这些规定 中,如药 品、医疗器 械等专业性较 强的 产 品由各级药品监督管理部 门负责、汽 车产品 由质监部 门负 责 等,但却没有一个权威 的部门统揽全局 ,使现行 召回法律 体 系 松 散 、低 效 。 我国 目前正在对 《 缺 陷产 品召回管理条例 ( 送 审稿 )》 公开征求意见 ,但该条例也 不是法律,仍是行政法规 。立法 层 次低 、涉 及行业有 限的直接危 害就 是部 门的执行 力不强, 由于前文所述部 门规章和地 方性法规包括现行 的 《 产 品质量 法 》、 《 消 费 者 权 益 保 护 法 》对 于缺 陷 产 品召 回制 度 进 行 了
汽车召回论文:我国汽车召回探析

汽车召回论文:我国汽车召回探析摘要:在西方国家,汽车召回大多是企业的主动行为,而不是迫于政府或者什么部门的压力。
而我国的大多数企业则认为汽车召回不可行,原因在于目前的市场不成熟。
成熟的市场,需要成熟的企业。
只有在相互促进的动态发展过程中,企业、政府和消费者才会一起成熟起来。
从暂时来看,召回对企业的发展的确不利,企业不仅免费维修要耗费巨资,而且信誉会受到很大影响,甚至产生品牌危机,股价大跌。
但是,从长远来看,它对企业是有利的,因为此举有效地避免了消费者因汽车本身的原因受到人身伤害,同时可以促使制造商更加关注产品质量,改进设计和生产。
因此,企业不仅应该对缺陷产品实施召回,而且应该主动召回。
关键词:汽车;召回;价值;理念一、汽车企业召回的战略价值分析成功的供应链管理确实能使企业在激烈的市场竞争中,明显提升企业的核心竞争力,其精髓表现在:以满足顾客的需求为目标,透过供应链内各企业间的紧密合作,高效地为顾客创造更多附加价值;逆向物流的出现正是符合这一思想的具体表现之一,无论何时,企业的生存与发展必须依靠供应链上的每个节点,包括其上游供应商和下游顾客,倾听顾客的呼声,满足顾客的退货需求。
同时适应时代和社会的发展,建立及时的产品召回制度。
使用再生材料以响应环保需求,这些都将为企业构造战略优势。
改善新的利润绩效。
汽车企业召回正是基于这些战略价值。
(一)改善和提高顾客价值对于顾客,最终消费者来说,逆向物流的成功运作能够确保不符合订单要求的产品及时退货;保证有质量问题的商品能够及时被召回,增加其对企业的信任感及回头率。
另一方面。
供应链和逆向供应链中的上下游结构不同。
传统的供应链关系是“一对多”(One-to-More)。
即上游的单位供应商面对下游数个顾客;而逆向供应链关系是“多对一”More-to-One),当发生逆向物流时,出现的退货和产品召回将是众多的下游顾客面对单位上游供应商,如果上游企业采取宽松的退货和产品召回策略,就能够减少下游顾客的投诉意见,容易形成彼此之间的共鸣与合作,改善供需关系,增强企业在整个供应链中的竞争优势。
缺陷汽车产品召回之立法——简评《缺陷汽车产品召回管理条例》的进步与缺失

2014年11期总第750期缺陷汽车产品召回之立法———简评《缺陷汽车产品召回管理条例》的进步与缺失姻杜一薇宁波大学法学院摘要:本文首先从理论角度探讨召回制度设立的原因。
通过比较2012年颁布的《缺陷汽车产品召回管理条例》和2004年《缺陷汽车产品召回管理条例》,探讨《条例》的立法进步之处以及立法背后的法律原理,再提出进一步完善的建议。
关键词:缺陷汽车产品;召回制度;《规定》;《条例》自2004年《缺陷汽车产品召回管理条例》实施,我国正式在立法上确立了缺陷汽车的召回制度。
然而,无论是在立法层级还是法律的内容方面,均存在着不足,这直接制约了召回制度应有作用的发挥。
因此,国务院于2012年颁布《缺陷汽车产品召回管理条例》,这标志着汽车领域的召回制度正在逐步借鉴国外经验和结合国内实际情况下走向完善。
一、召回制度设立之必要召回制度的最大特点,在于其并非是调整平等主体关系的法律制度,而是建立在国家干预之上,是经济法这一部门法的一项特有制度。
它体现了经济法的一般价值:即对弱势群体的倾斜保护和对社会整体经济秩序的规制调控。
召回制度是典型的消费者权益保护制度,但除此之外,现代社会的经济发展赋予了其更大的调节功能。
首先,高额的召回费用能够促进企业加强管理和规范生产。
其次,它能够规范市场竞争秩序,遏制“劣币驱逐良币”现象的蔓延。
最后,该制度能在一定程度上调节产业。
从我国汽车业现状而言,虽然自主品牌汽车发展势头强盛,但同国外汽车相比,仍然有很多弊端。
譬如:汽车质量上仍有差距,主要表现在零部件质量和装配质量;车内环境污染严重,损害人体健康;同时汽车产业结构亦不合理。
因此,完善我国的缺陷汽车产品召回制度,势在必行。
二、与《规定》想比,《条例》的进步之处新出台的《条例》同2004年的《规定》想比,在以下几方面进行了修改与完善:1.法律层级提高2004的《规定》是由国家质检总局、发改委、商务部、海关总署联合发布,从法律渊源而言,其属于部门规章,效力较低,缺乏权威性。
缺陷汽车产品召回制度存在的法律问题及完善措施

缺陷汽车产品召回制度存在的法律问题及完善措施作者:张晓来源:《西部论丛》2019年第25期一、我国缺陷汽车召回制度存在的法律问题1、缺少专门的产品召回立法2004年,国务院正式出台了《缺陷汽车召回管理规定》,国家质检总局先后发布了《召回专家库建立与管理办法》等四部配套法律法规。
2012年出台了《缺陷产品召回管理条例》明确强化了质检部门的调查取证权。
2015年,《缺陷汽车产品召回管理条例实施办法》颁布,于2016年开始实施。
我国现阶段对该制度并没有太多的规制,缺乏关于汽车召回的专门立法,并且部分制度即使法律有相关规定也缺乏实施细则,在实践中很难操作和落实。
2、缺乏认证缺陷汽车的公正、独立的第三方检测机构首先,我国质检总局目前公布的用于认真缺陷汽车的检测机构,或多或少与制造商都有利害关系的存在,根本无法保证检测机构的中立性。
检测机构就像中间商,接受国家质检总局的委托又是制造商的科研合作对象。
有车辆需要检测的时候,检测结构确是制造商的科研合作对象,这样的检测是不公平公正的。
其次,我国缺陷产品检测机构缺乏权威性。
这些检验汽车的机构都不是专业的检测缺陷汽车的机构,他們同时也去检测食品和药品,所以专业性是无法得到保证的。
3、我国强制汽车召回缺失《缺陷汽车产品召回管理条例实施办法》第23条规定,质检总局在一定的条件下,可以让生产者召回缺陷产品。
但我国目前还缺乏一套完整的国家强制召回的体系。
在资金上,我国缺乏财政支持;在技术上,我们缺乏专业的检测机构,也缺乏专业的检测技术。
这些都与发达国家有较大的差距。
二、缺陷汽车召回制度中存在的法律问题的完善措施1、制定配套的法规及实施细则我们应以立法的形式出台《中华人民共和国产品召回法》,明确缺陷汽车召回的部门,明确关于缺陷汽车召回的原则、条件、对象、检测的标准、召回的流程和各个召回主体应该承担的法律责任、惩罚性措施等具体的规定。
同时,我们也应该去增添《产品质量法》和《消费者权益保护法》的相关规定来提高缺陷汽车召回制度的法律位阶。
中国缺陷汽车产品召回管理与效果分析
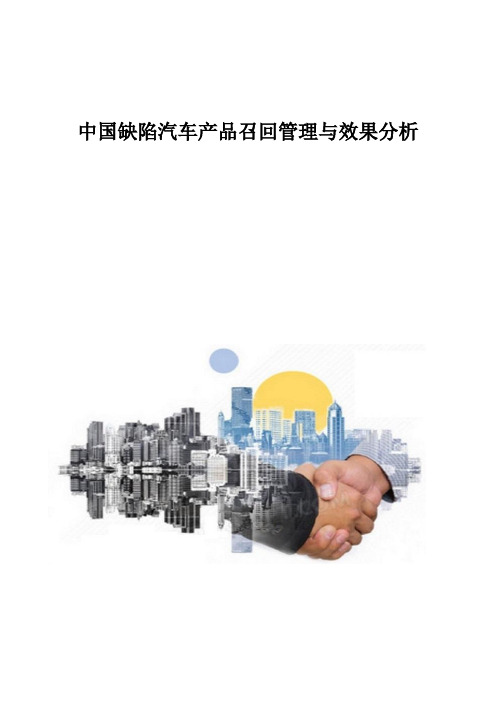
中国缺陷汽车产品召回管理与效果分析一中国缺陷汽车产品召回制度概述2004年3月,国家质量监督检验检疫总局(以下简称“国家质检总局”)等四部门联合发布了《缺陷汽车产品召回管理规定》,自此,我国开始实行缺陷汽车产品召回制度。
该项制度在保证汽车产品使用安全、促使生产者高度重视并不断提高汽车产品质量等方面发挥了重要作用。
同时,从实践来看,该项规定在召回程序、监管措施等方面还需要进一步完善,尤其是作为部门规章,受立法层级低的限制,对隐瞒汽车产品缺陷、不实施召回等违法行为的处罚过低(最高为3万元罚款),威慑力明显不足,从而影响召回制度的有效实施。
为此,在认真总结实践经验的基础上,将部门规章上升为行政法规,进一步加强和完善我国缺陷汽车产品召回管理,保障汽车产品的使用安全十分必要。
2012年10月10日,国务院第219次常务会议通过《缺陷汽车产品召回管理条例》(以下简称《条例》),自2013年1月1日起施行。
由此,我国缺陷产品召回制度的进程又向前迈了一大步。
召回程序是否明确具体、是否具有针对性和可操作性,是确保生产者履行召回责任的前提。
对此,《条例》从以下三个方面作了规定。
1.明确了召回启动程序生产者获知汽车产品可能存在缺陷的,应当立即组织调查分析;确认汽车产品存在缺陷的,应当立即停止生产、销售、进口缺陷汽车产品,并实施召回;国务院产品质量监督部门经缺陷调查认为汽车产品存在缺陷的,也应当通知生产者实施召回。
生产者认为其汽车产品不存在缺陷的,可以在规定期限内向国务院产品质量监督部门提出异议,国务院产品质量监督部门应当组织有关专家进行论证、技术检测或者鉴定。
生产者既不按照通知实施召回又不在规定期限内提出异议的,或者经国务院产品质量监督部门组织论证、技术检测或者鉴定确认汽车产品存在缺陷的,国务院产品质量监督部门应当责令生产者实施召回,生产者应当立即停止生产、销售、进口缺陷汽车产品,并实施召回。
2.规定了召回实施程序生产者应当按照国务院产品质量监督部门的规定制定召回计划,并按照计划实施召回。
缺陷汽车产品召回效果评估的研究综述

缺陷汽车产品召回效果评估的研究综述缺陷汽车产品召回是汽车行业中常见的现象,而召回的目的是为了消除汽车产品中的安全隐患,保障消费者的权益和安全。
召回行为不仅仅是企业的一种自我修复行为,同时也是对汽车产品质量和企业公信力的一种考量。
为了评估缺陷汽车产品召回的效果,了解召回对汽车行业和消费者的影响,有必要对相关研究进行综述和评估。
一、缺陷汽车产品召回的概念和背景缺陷汽车产品召回是指汽车制造商根据相关法规和标准,主动对已经销售的汽车产品进行召回修复,以消除产品存在的质量缺陷和安全隐患。
召回通常涉及到零部件更换、系统升级、软件更新等修复措施。
汽车产品召回的目的是防止因产品缺陷导致的安全事故和消费者投诉,维护企业的声誉和品牌形象。
缺陷汽车产品召回的背景是汽车产品的复杂性和多样性。
现代汽车产品包含了大量的电子系统、智能化装置和高科技材料,这些零部件和系统的复杂性使得汽车产品存在着更多的潜在缺陷和安全隐患。
加之汽车产品的生产和销售具有全球化的特点,跨国企业和供应链的延伸也增加了汽车产品召回的频率和难度。
缺陷汽车产品召回不仅对企业和消费者产生直接影响,还对整个汽车行业和社会产生了一定的影响。
1. 对企业的影响召回影响了企业的产品质量声誉和品牌形象。
一次召回行为可能导致企业在消费者心目中的信任度下降,并且对企业的销售和市场份额产生影响。
召回还增加了企业的成本和管理负担,包括召回产品的修复成本、服务成本、公关成本等,同时还需要投入更多的人力和物力资源进行召回活动的组织和执行。
对于跨国企业而言,召回还牵涉到不同国家和地区的法律法规和标准的协调,增加了召回的难度和成本。
召回对消费者意味着产品的质量和安全受到了保障,一方面召回可以消除安全隐患和消费者的担忧,另一方面也表明了企业对消费者权益的尊重和维护。
召回也给消费者带来了不便和损失,包括时间成本、维修成本、使用权益的限制等。
召回还可能对二手车市场产生影响,因为召回的车辆在售后市场上的价值可能会受到影响。
缺陷产品召回制度中存在的问题及对策
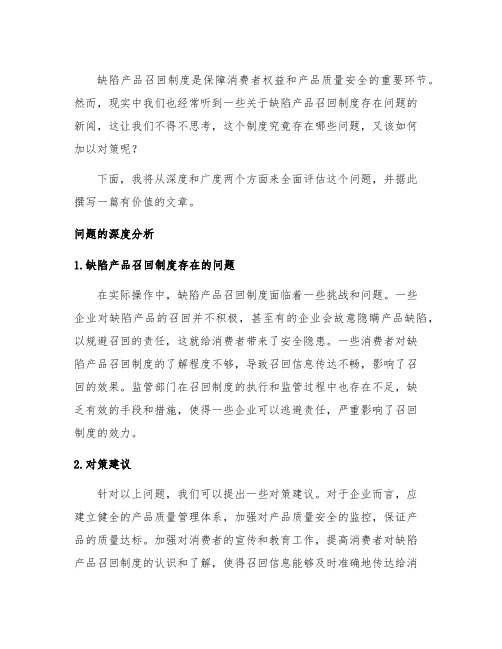
缺陷产品召回制度是保障消费者权益和产品质量安全的重要环节。
然而,现实中我们也经常听到一些关于缺陷产品召回制度存在问题的新闻,这让我们不得不思考,这个制度究竟存在哪些问题,又该如何加以对策呢?下面,我将从深度和广度两个方面来全面评估这个问题,并据此撰写一篇有价值的文章。
问题的深度分析1.缺陷产品召回制度存在的问题在实际操作中,缺陷产品召回制度面临着一些挑战和问题。
一些企业对缺陷产品的召回并不积极,甚至有的企业会故意隐瞒产品缺陷,以规避召回的责任,这就给消费者带来了安全隐患。
一些消费者对缺陷产品召回制度的了解程度不够,导致召回信息传达不畅,影响了召回的效果。
监管部门在召回制度的执行和监管过程中也存在不足,缺乏有效的手段和措施,使得一些企业可以逃避责任,严重影响了召回制度的效力。
2.对策建议针对以上问题,我们可以提出一些对策建议。
对于企业而言,应建立健全的产品质量管理体系,加强对产品质量安全的监控,保证产品的质量达标。
加强对消费者的宣传和教育工作,提高消费者对缺陷产品召回制度的认识和了解,使得召回信息能够及时准确地传达给消费者。
监管部门也应该加强对缺陷产品召回制度的监管和执行力度,建立更加严格的监管制度,对违规企业进行严厉处罚,确保召回制度的有效实施。
问题的广度分析为了更全面地了解缺陷产品召回制度存在的问题及对策,我们还需要从更广的角度来分析这个问题。
1.行业现状分析通过对当前缺陷产品召回制度执行情况的调研,我们可以发现不同行业在召回制度执行上存在的共性和差异性。
有些行业在召回制度的执行过程中更加积极主动,而有些行业则存在较多问题和困难。
这需要我们对不同行业的制度执行情况进行深入研究,找出问题所在,并提出针对性的对策建议。
2.国际经验借鉴除了国内的情况,我们还可以借鉴国际上其他国家和地区的经验。
不同国家和地区对于缺陷产品召回制度的规定和执行方式可能存在着一些差异,通过对比分析,我们可以发现一些值得借鉴和学习的经验和做法,以提升我国缺陷产品召回制度的执行效果。
我国近年汽车安全性召回改正结果与分析
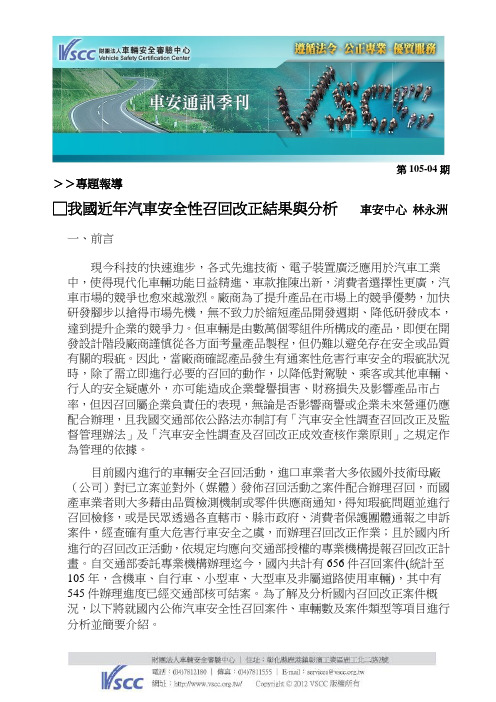
第105-04期>>專題報導□我國近年汽車安全性召回改正結果與分析車安中心林永洲一、前言現今科技的快速進步,各式先進技術、電子裝置廣泛應用於汽車工業中,使得現代化車輛功能日益精進、車款推陳出新,消費者選擇性更廣,汽車市場的競爭也愈來越激烈。
廠商為了提升產品在市場上的競爭優勢,加快研發腳步以搶得市場先機,無不致力於縮短產品開發週期、降低研發成本,達到提升企業的競爭力。
但車輛是由數萬個零組件所構成的產品,即便在開發設計階段廠商謹慎從各方面考量產品製程,但仍難以避免存在安全或品質有關的瑕疵。
因此,當廠商確認產品發生有通案性危害行車安全的瑕疵狀況時,除了需立即進行必要的召回的動作,以降低對駕駛、乘客或其他車輛、行人的安全疑慮外,亦可能造成企業聲譽損害、財務損失及影響產品市占率,但因召回屬企業負責任的表現,無論是否影響商譽或企業未來營運仍應配合辦理,且我國交通部依公路法亦制訂有「汽車安全性調查召回改正及監督管理辦法」及「汽車安全性調查及召回改正成效查核作業原則」之規定作為管理的依據。
目前國內進行的車輛安全召回活動,進口車業者大多依國外技術母廠(公司)對已立案並對外(媒體)發佈召回活動之案件配合辦理召回,而國產車業者則大多藉由品質檢測機制或零件供應商通知,得知瑕疵問題並進行召回檢修,或是民眾透過各直轄市、縣市政府、消費者保護團體通報之申訴案件,經查確有重大危害行車安全之虞,而辦理召回改正作業;且於國內所進行的召回改正活動,依規定均應向交通部授權的專業機構提報召回改正計畫。
自交通部委託專業機構辦理迄今,國內共計有656件召回案件(統計至105年,含機車、自行車、小型車、大型車及非屬道路使用車輛),其中有545件辦理進度已經交通部核可結案。
為了解及分析國內召回改正案件概況,以下將就國內公佈汽車安全性召回案件、車輛數及案件類型等項目進行分析並簡要介紹。
二、國內已辦理之召回改正案件及車輛數(一)召回改正案件及車輛數統計目前國內已進行召回改正之案件,概分為管理辦法公佈前為58件、管理辦法公佈後至105年度則有598件,合計656件召回改正案,涉及召回改正車輛總數達3,233,568輛次(含機車、自行車、小型車、大型車及非屬道路使用車輛)。
我国缺陷产品召回制度存在的问题及其发展对策分析

我国缺陷产品召回制度存在的问题及其发展对策分析摘要:社会经济和科学技术的发展带来了产品的多样化,然而缺陷产品却越发成为威胁消费者健康和生命安全的重大隐患,因此完善缺陷产品召回制度对保障消费者权益,发展社会经济尤为重要。
现从缺陷产品召回制度的定义和我国缺钱产品召回制度的现状出发,分析其存在的问题及完善的必要性,并得出我国缺陷产品召回制度的发展对策。
关键词:缺陷产品召回制度问题发展1、前言近几年来,苏丹红事件、雀巢事件、三鹿奶粉事件、丰田召回事件在国内市场上频频发生,缺陷产品越发威胁消费者健康和生命安全,这使得人们越来越意识到完善缺陷产品召回对保护消费者权益、维护经济平稳发展的重要性和紧迫性。
2、缺陷产品召回制度概述对于缺陷产品召回制度,各国说法不一。
通说认为,缺陷产品召回制度是指产品的制造商或者销售商等在发现或得知其生产、进口或销售的产品存在可能引发消费者人身或财产安全问题的缺陷时,依法履行报告义务并及时通知消费者,从市场上和消费者手中收回缺陷产品,并进行或协助进行免费修理、更换或收回的制度。
建立缺陷产品召回制度的优点是显而易见的,它能够有效地保护消费者权益,提高企业产品的质量,推动政府加强对市场的监管力度,促进经济平稳发展。
在我国,长期以来召回制度缺位,引发了很多亟待解决的新问题,近年来,苏丹红事件、雀巢事件、三鹿奶粉事件、丰田召回事件在国内市场上频频发生,充分证明因缺陷产品进入市场所产生的公共安全问题已成为社会热点。
总体上来说,我国的缺陷产品召回基本上局限于汽车、食品等少数几类产品,企业主动召回产品的积极性不高,愿为成为政府对经济进行调控管理的常用手段。
3、我国缺陷产品召回制度中存在的问题3.1 法律体系上存在缺位现象我国目前尚未建立完善的产品召回法律制度,使得广大消费者的利益无法得到有效地保护。
中国目前缺乏对缺陷产品召回的基本法律规定,大部分召回主要依靠媒体监督以及舆论压力,未能从根本上达到改变保护消费者的合法权益、控制缺陷产品混乱局面的效果。
浅析我国汽车召回制度
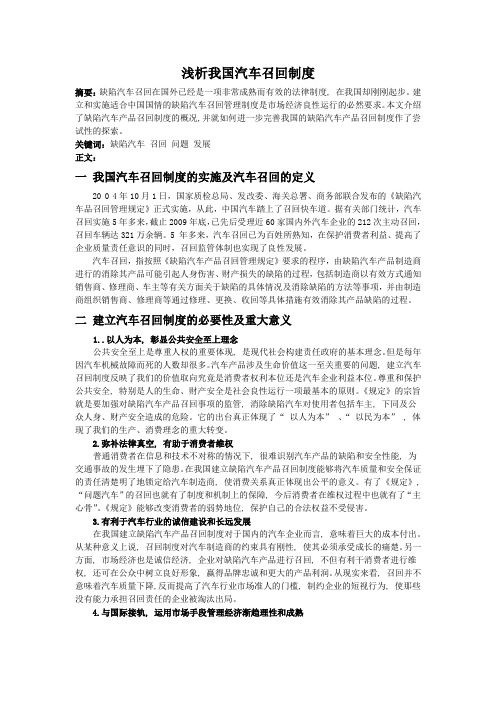
浅析我国汽车召回制度摘要:缺陷汽车召回在国外已经是一项非常成熟而有效的法律制度, 在我国却刚刚起步。
建立和实施适合中国国情的缺陷汽车召回管理制度是市场经济良性运行的必然要求。
本文介绍了缺陷汽车产品召回制度的概况,并就如何进一步完善我国的缺陷汽车产品召回制度作了尝试性的探索。
关键词:缺陷汽车召回问题发展正文:一我国汽车召回制度的实施及汽车召回的定义20 0 4年10月1日,国家质检总局、发改委、海关总署、商务部联合发布的《缺陷汽车品召回管理规定》正式实施,从此,中国汽车踏上了召回快车道。
据有关部门统计,汽车召回实施5年多来,截止2009年底,已先后受理近60家国内外汽车企业的212次主动召回,召回车辆达321万余辆。
5 年多来,汽车召回已为百姓所熟知,在保护消费者利益、提高了企业质量责任意识的同时,召回监管体制也实现了良性发展。
汽车召回,指按照《缺陷汽车产品召回管理规定》要求的程序,由缺陷汽车产品制造商进行的消除其产品可能引起人身伤害、财产损失的缺陷的过程,包括制造商以有效方式通知销售商、修理商、车主等有关方面关于缺陷的具体情况及消除缺陷的方法等事项,并由制造商组织销售商、修理商等通过修理、更换、收回等具体措施有效消除其产品缺陷的过程。
二建立汽车召回制度的必要性及重大意义1..以人为本, 彰显公共安全至上理念公共安全至上是尊重人权的重要体现, 是现代社会构建责任政府的基本理念。
但是每年因汽车机械故障而死的人数却很多。
汽车产品涉及生命价值这一至关重要的问题, 建立汽车召回制度反映了我们的价值取向究竟是消费者权利本位还是汽车企业利益本位。
尊重和保护公共安全, 特别是人的生命、财产安全是社会良性运行一项最基本的原则。
《规定》的宗旨就是要加强对缺陷汽车产品召回事项的监管, 消除缺陷汽车对使用者包括车主, 下同及公众人身、财产安全造成的危险。
它的出台真正体现了“以人为本”、“以民为本” , 体现了我们的生产、消费理念的重大转变。
关于丰田召回事件的分析报告

关于丰田召回事件的分析报告第一篇:关于丰田召回事件的分析报告关于丰田召回事件的分析报告班级:xxxxx姓名:xxx学号:xxxx 摘要:2009年8月24日,丰田在华两家合资企业——广汽丰田、一汽丰田宣布,由于零部件出现缺陷,自8月25日开始,召回部分凯美瑞、雅力士、威驰及卡罗拉轿车,涉及车辆总计688314辆。
这是我国2004年实施汽车召回制度以来,数量最大的一项召回。
此次召回的车辆包括了丰田在中国市场的所有主力车型。
丰田宣称,大规模召回的原因是同一供应商供应给两家企业的零部件出现缺陷,广汽丰田和天津一汽丰田承诺将对召回范围内的车辆免费更换电动车窗主控开关缺陷的零部件,以消除安全隐患。
众多汽车产业专家则开始怀疑丰田的质量神话是否依旧坚挺。
有关人士指出,丰田连续大规模召回与它的零件通用化战略、捆绑式管理模式有关。
更有专家指出,丰田质量的下降,与其产量快速膨胀忽视科学管理有直接的关系。
丰田公司充分利用了公共关系中的各种原则1、真实守信原则首先,它遵守了公共关系中的真实守信的基本原则她将消息公开,不管是好的还是坏的,它认为顾客都有知道真实情况的权力,不采用故弄玄虚、无中生有或有胡乱吹嘘、抬高自己的宣传伎俩。
在事情发生后,丰田公司立即采用召回车辆以降低名誉损失,丰田这几年连续召回已经大大触动全球消费者的神经,尤其当丰田汽车引以为傲的雷克萨斯也发生召回时,有关丰田汽车质量的神话广遭质疑。
在一系列对外解释中,丰田汽车竭力否认质量问题与其成本之间的关系,其相关高管在一次道歉之后,不得不进行下一次道歉。
同时丰田自己也承认质量有问题。
丰田社长丰田章男近日提出“质量比数量更重要”,丰田宣布放弃夺取全球15%市场份额地目标,从而退出全球销量第一的争夺战。
2、全员关公原则随后,丰田公司发动全员参与此次召回事件,上下一心合理搞好公关工作。
在事件处理中不仅丰田公司的领导人丰田章男发表声明并对此事件所带来的各种损失道歉,甚至丰田公司所有员工都工作积极配合公关工作。
我国缺陷产品召回制度引发的思考
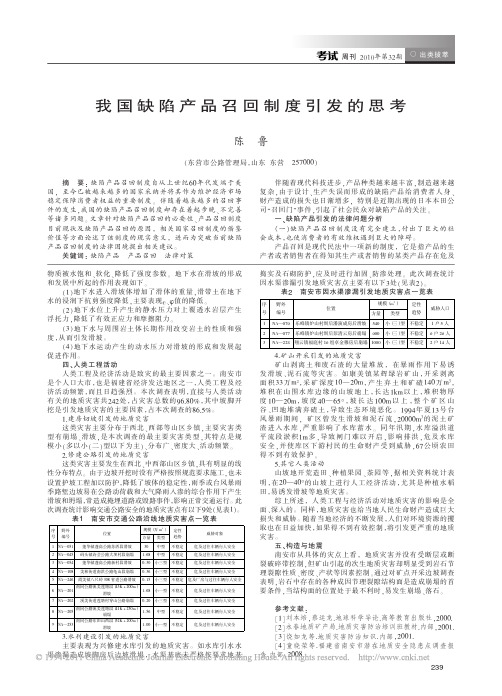
参考文献: [1]刘 本 培 ,蔡 运 龙.地 球 科 学 导 论 .高 等 教 育 出 版 社 ,2000. [2]永春地质矿产局.地质灾害防治培训班教材.内部,2001. [3]饶 如 龙 等 .地 质 灾 害 防 治 知 识 .内 部 ,2001. [4]童 晓 荣 等 . 福 建 省 南 安 市 潜 在 地 质 安 全 隐 患 点 调 查 报 告 .内 部 ,2008.
3.水 利 建 设 引 发 的 地 质 灾 害
主要表现为兴修建水库引发的地质灾害。 如水库引水水
渠渗漏造成坡脚房后边坡滑塌, 水渠基底未严格按要求地基
伴随着现代科技进步,产品种类越来越丰富,制造越来越 复杂,由于设计、生产失误而形成的缺陷产品给消费者人身、 财产造成的损失也日渐增多, 特别是近期出现的日本本田公 司“召回门”事件,引起了社会民众对缺陷产品的关注。
表2 南安市因水渠渗漏引发地质灾害点一览表
序 野外 号 编号
位置
规模(m3 ) 方量 类型
定性 威胁人口
趋势
1 NA—076 乐峰镇炉山村圳后潘演成房后滑坡 540 小(三)型 不稳定 1 户 5 人
2 NA—077 乐峰镇炉山村圳后彭清云房后崩塌 600 小(三)型 不稳定 6 户 26 人
3 NA—228 翔云镇福庭村 16 组卓金穆房后崩塌 1000 小(三)型 不稳定 2 户 14 人
作为专门保护消费者利益的消费者权益保护法, 它只是 从消费者的角度规定了产品质量存在问题时的救济手段,而 没有强调经营者主动召回全部缺陷产品的义务, 如果特定消 费者不主动行使上述救济手段, 缺陷产品仍然可能处于流通 和生活使用当中, 很可能造成对其他公民人身安全和财产保 障的威胁。 当然,我国有关的行政法规和规章中规定了缺陷产 品召回制度, 例如国家质检总局颁布了缺陷汽车产品召回管 理规定, 国务院出台了关于加强食品等产品安全监督管理的 特别规定,要求生产企业发现其产品存在安全隐患的,应主动 召回;国家食品药品监督管理局也制定了药品召回管理办法。 这些法规和规章对于促进产品召回制度起到了积极的作用。 但是毕竟这些规定在效力层次上较低, 使得这一制度的构建 和实施受到了很大的局限,在发生有关召回争议的时候,不能 够作为裁判规则予以适用。
- 1、下载文档前请自行甄别文档内容的完整性,平台不提供额外的编辑、内容补充、找答案等附加服务。
- 2、"仅部分预览"的文档,不可在线预览部分如存在完整性等问题,可反馈申请退款(可完整预览的文档不适用该条件!)。
- 3、如文档侵犯您的权益,请联系客服反馈,我们会尽快为您处理(人工客服工作时间:9:00-18:30)。
例所称召回,是指汽车产品生产者对其已售出的汽车产 品采取措施消除缺陷的活动”。 从2004年10月1日起至2013年12月31日止,我国累 计汽车召回609次,召回汽车14157577辆。详见下表1: 从表1可见:近几年我国汽车召回的次数及数量 (2010年的召回次数属于例外)呈逐年递增的趋势,汽 车召回的范围和影响也越来越大。
4~6月接连发生多次安全气囊自爆伤人的事故。安全气
囊自爆的原因是气囊控制模块软件太敏感,在停车、慢
行、外部并无冲击等情况下,安全气囊可能产生误爆。
该缺陷产生的根本原因,企业一开始就清楚,但因涉及 的车辆数较多,更换成本较高,另该企业是全国质量万 里行会员单位,考虑企业形象,迟迟不愿召回。随着气 囊自爆案例的不断增多,尤其在国家质量监督检验检疫 总局的多次干预下,经历两年多时间,该企业才于2012 年6月8日实施了主动召回。 召回启示:汽车生产、经销企业为了自身的利益, 绝不会自愿主动地实施缺陷汽车召回工作。只有当认识到
并做到既提高汽车产品的人身、财产安全|兰E,又不会增加
太多的成本,并且能大大提高企业在行业和市场中的竞争 力时,他们才能积极地消除安全缺陷,自觉地实施汽车召
回。
缺陷召回汽车11次。
两年比较,2012年因装配缺陷召回次数比2010年 减少了4次。这表明由于在产品认证监管环节,增加了 监督检查频次,产品的一致性有了进一步的改善,认证 机构加强了针对加工装配质量方面的监管。
起火燃烧进行召回。这次召回的直接原因是几次汽车
的意外燃烧。燃烧的原因是变速器油因高温从通气孔喷 溅溢出,气化遇热而燃烧。变速器油高温溢出的原因在 于:车辆在长时间、高负荷、沙地等极端行驶工况下运
矛盾最关键、最主要的方面是国家行政职能部门,
必须真正代表并维护好国家和社会群众的根本利益,承 担起领导和管理的责任。首先要健全法律法规;要责成 和监督汽车企业,对其设计制造产生的汽车缺陷,尤其
报召回,普通群众从意识淡薄、不愿配合缺陷调查到积 极投诉、主动配合缺陷调查:汽车召回已越来越得到国 家、汽车企业、汽车用户及社会群众的高度重视。2003 年11月1日,开始实施中华人民共和国国务院令第390号 《中华人民共和国认证认可条例》。2009年9月1日实 施国家质量监督检验检疫总局第11 7号令《强制性产品 认证管理规定》。我国汽车产品认证工作也日益完善, 汽车产品的准入监管也越来越严格。 《缺陷汽车产品召回管理条例》中规定: “本条例
万方数据
表1 2004年10月1[]一2013年12月31日汽车召回情况
召回次数 10 27 40 31
47
由95次减少N79次,下降16.84%。其中,2010年包括
整车设计和部件设计在内的设计缺陷占52.63%;含制
召回数量(辆)
307527 57825 336140 605211 538620 1361266 1176995 1827257 2575399 5371337 14157577
万方数据
●◆
将汽车被动安
全性的重要部
件——安全气
囊系统尽快纳入
到部件认证的范
畴;尽快研究是否
增加汽车产品在
的吐撇证。
特定使用环境下
●●
是所造成的社会危害,承担起改正缺陷、对危害必须完
全赔赏的责任。只有严格执法,加强对召回工作管理, 才能真正保护消费者应有的合法权利。关于企业对待产 品认证和召回的关系,则只有当企业的产品认证成本低 于召同成本时,企业才能主动提高产品在生产前和生产 中的质量保证工作,积极主动地搞好产品认证的工作。 这次召回丁作拖长的原因,还有一点是因为至今我
移;一些直观判断属于安全性的缺陷,经过深入分
析,其实属于极限工况下的系统可靠性缺陷。笔者通 过对典型缺陷汽车召回案例的深入研究,发现汽车质 量售前一售后监管工作的基本矛盾及其解决的规律,从 而启示我国汽车产品质量的售前一售后监管工作,也需 相应改进和完善。
所称缺陷,是指由于设计、制造、标识等原因导致的在 同一批次、型号或者类别的汽车产品中普遍存在的不符 合保障人身、财产安全的国家标准、行业标准的情形或
————————————————————TnEND黎————————————...—————。———————
文/王东(中国质量认证中心)
汽车产品认证是汽车产品的售前质量监管,汽车召回是 汽车产品的售后质量监管。对于汽车产品质量的保证,两
者是既不可缺少又相互补充、促进和完善的监管环节。
本文根据我国汽车召回工作的实践,特别是2010 年、20l 2年的典型资料,通过对召回汽车缺陷的类 型、特征分析,找出缺陷产生的主要原因及消除举 措,发现缺陷变化呈现出如下基本趋势:从设计向制 造装配、部件向系统、大件主件向小件附件、自制向 协作外购、硬件向软件、一般工况向极限工况重点转
行,变速器内前进挡离合器摩擦片磨损打滑,变速器内
外冷却散热不良,通气孔位置设计不当,又未配油温过
热警示系统以及时提醒司机采取措施降温。这许多因素 综合在一起,才是造成变速器起火燃烧的真实原因。这 一直观判断属于部件安全性的缺陷,其实属于整车在沙
地、长时间、高负荷行驶等极限工况下的可靠性缺陷。 召回启示:部件设计需要从整车实际复杂的使用工 况出发,周密考虑变速器与其周围相邻部件的间隙、通 风、着火危险等因素,处理好变速器本身的散热、通气
减少的29次,实际是同一品牌车型的29家进口商和改装
车企业,其行驶记录仪后部接头的密封盖及铅封未在工 厂安装,导致不能有效防止对行驶记录仪信号线的非法
2012年因部件设计缺陷召回汽车31次。因电子调
控系统选配不当或软件缺陷被召回汽车共3次;因特 定、极端工况导致部件缺陷被召回共9次,占因部件设 计缺陷召回的29.03%1因为部件材质、强度原因召回汽 车共8次,占因部件设计缺陷召回的25
因部件设计缺陷 召回次数及占比 37;38 95% 31:39.24%
因制造缺陷召 回次数及占比 27;28.42% 30;3298%
因装配缺陷召 回次数及占比 15:15.79% 11:13.92%
因其它缺陷召回 次数及占比 3:316% 2:2.53%
干涉的情况等。 2010年因整车设计缺陷召回汽车13次。其中因零 部件间隙不足或运动干涉缺陷而召回汽车达11次,占因 整车设计缺陷召回的84 62%。 2012年因整车设计缺陷召回汽车5次。其中因间隙 不足或运动干涉召回汽车3次.占因整车设计缺陷召回 的60%。
27.03%。
及启示
2010年、2012年召回概况 2010年我国汽车召回123次.召回汽车1176995 辆,涉及车型161个。其中,已经认证的召回77次,未 经认证环节的46次。 2012年我国汽车召回79次,召回汽车2575399辆, 涉及车型115个。已经认证的召回33次,未经认证环节 的46次。 根据汽车召回的缺陷内容及原因,可分整车设计、 部件设计、制造、装配和其它五个方面。 与2010年相比,2012年召回总次数由123次下降到 79次。其主要原因是其它类缺陷由31次下降N2次。这
只有在部件及整车设计中切实加强系统可靠性的设
计,并经过特定使用环境下的可靠性验证。才能确保
汽车的安全性。 随着科技的发展,新结构、新产品、新技术在汽车 上的应用不断增加,为了保证部件及整车的安全性,必 须将那些关系到人身、财产安全的新产品、新配件、新 元件,及时扩展进国家认证的范围中。 通过典型缺陷汽车召回案例的深入研究,发现汽 车召回工作的基本矛盾是:汽车安全缺陷产生及消除的 主体是汽车生产企业及经销商。而缺陷造成的后果及 危害,却由车主、司机、客户和国家社会所承受。这 种责、权、利的分离和错位,只有通过国家的法律、
次与2010年同样原因召回10次相比差别不大,说明零
部件企业考虑在极限工况使用条件的情况不够,有待进 一步改进;2012年因为部件材质、强度原因召回汽车共
8次,比2010年的0次增幅较大,说明零部件供应商在
降低采购成本的情况下,性能无法得以保证,需进一步
加强零部件供应商的进货检验。
因制造缺陷召回 制造缺陷,包括:供应商的铆接工艺不稳定,导致 制动液由软管的中间层与外层之间渗出从而引起鼓包, 极端情况下,会有制动液少量渗漏的情况等,均是因设 备、材料、工艺不当等因素造成。 2010年因制造缺陷召回汽车27次,2012年因制造 缺陷召回汽车30次。 两年比较,2012年因制造缺陷召回次数比2010年 增加了3次。这表明因制造缺陷召回有增加的趋势。尤 其是随着供应商的扩展,如何切实加强对供应商产品的 质量控制,成了整车产品安全能否保障的关键问题。我 们认为这方面的监管措施必须加强。 因装配缺陷召回 装配缺陷,包括:转向机固定螺栓的固定扭矩值不 符合设计标准,可能使转向机无法有效固定,甚至使驾 驶者无法实现车辆的转向情况等,多数是因为连接件拧 紧力矩不足及工人装配不当造成的。 2010年因装配缺陷召回汽车15次,2012年因装配
孔位置、油液的冷却、油温过热警示等措施,并经特殊
工况下的可靠性验证,才是消除安全缺陷的根本保证。 对于汽车产品的认证工作,也应考虑尽快把某些极限工 况的可靠性验证纳入认证范畴。 案例二某品牌轿车的召回 2012年6月某品牌轿车因安全气囊控制模块设计缺 陷导致误爆伤人召回。这次召回的直接原因是:2010年
56 123 71 79 125
年加 加 加 加 加 合 份∞晒;宝凹∞ 们"他侣计
609
表2 2010年、2012年召回概况
年份 总召回次数 及占比 2010 2012
95:100
整车设计缺陷,包括:方向盘转至极限位置并紧急 制动的极端工况下,前轮轮胎与底盘的推力杆部件可能
因整车设计缺路 召回次数及占比 13:13.68% 5:6.33%
造缺陷和装配缺陷在内的生产缺陷占44.21%;其它缺 陷占3 16%。2012年的设计缺陷占45.57%、生产缺陷
占51.90%、其它缺陷占2.53%。两年比较,设计缺陷下