多线切割工艺对研磨去除量的影响
中走丝线切割

中走丝切割但由于丝绸是近几年才开始去,那么多走在处理技术的不熟悉丝绸。
现在DuoNian结合生产实践,根据走在编程和操作切割机的丝绸加工过程中出现的问题及遇到的困难,总结了一些处理方法和加工操作计划(仅供参考)为了满足用户需要,我保持公司在快速走丝线切割机床结构简单、成本低、效率高、使用过程中技术如消费的特点,在此基础上借鉴国际,精密模具加工设备先进的理念和照顾切断电线DuoCi技术(比如:第一次降息与较大的电规则允许高速切削,纯提物和粗规则允许被允许和微妙的规则为二、三、四、五次,甚至将削减加工表面光亮,获得“理想的加工表面质量和加工精度),发展可以实现智能化系统DuoCi切割中速(WEDM-CS丝电火花线切割机走)。
这台机器比去更快、更友好的用户界面,更多的个性化丝绸更宽的范围。
越来越多的厂家所青睐。
目前已在市场后500余台,用户普遍反映这条线切割机加工质量较好。
我公司生产的“中速去,不仅电极丝线”的移动速度之间的“高速”和“低”之间,加工质量高于丝机、高速和低速走”的方法去丝机。
一、DuoCi切割工艺参数的设第一个任务是要减少高速稳定切割(1):选择脉冲参数的峰值电流,长脉冲宽度的规则被允许为大电流的切割,以获得较高裁断速度快。
(2)电极丝中心的小补偿金额声道女= 1/2φ三角洲d + S型、列车为F(mm)补偿量;三角洲第一次切割(mm);间隙放电电极丝直径φd(mm);火车为了离开第二切削加工余量(mm)是为精致盈余(mm)。
在峰值电流厚规则必须切割、单方面的间隙放电状态约0.02毫米,通常只有精致津贴,0.003毫米少。
与加工津贴取决于火车第一次切割后工件表面粗糙度和刀具加工精度,大约在0.03 ~ 0.04毫米的范围。
所以,第一次在切削赔偿数额的0.05 ~ 0.06毫米,选择影响第二大的速度减少,选择小,难以消除的第一次降息的痕迹。
(3)去丝绸道:高速公路丝,去线速8至12米/秒,达到最大生产效率。
多线切割金属丝张力控制技术的研究现状
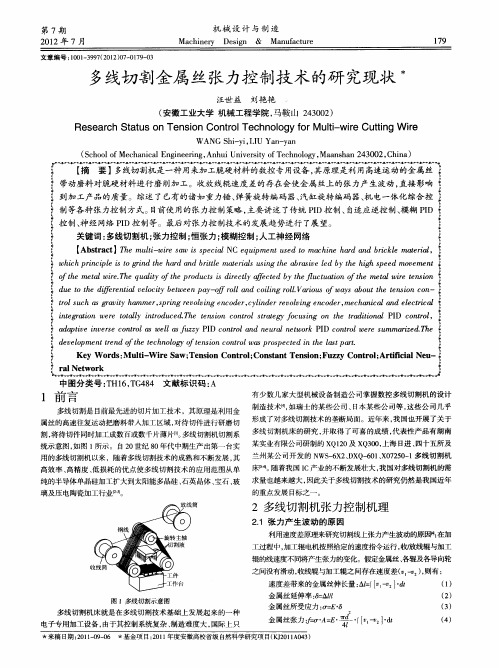
金属丝张力: ̄-= ・ 一』 f A E ・ - -
:・t ] d
() 4
★来稿 日期 :01- 9 0 ★基金项 目:0 1 2 10—6 2 1 年度安徽高校省级 自然科学研究项 目( J0 1 0 3 K 2 1A 4 )
10 8
汪世 益等 : 多线切 割金属 丝张力控 制技 术 的研 究现状
r l e wo k a t r N
中图分类 号 :H1 , G 8 文献标 识码 : T 6T 44 A
1 前 言
多线切割是 目前最先进 的切片加工技术 ,其原理是利用 金
有 少数几家大型机械设备制造公司掌握数控多线切割机的设计 制造技术 如瑞士的某些公司 、t , E本某些公 司等 , 这些公 司几乎
筒
的重 点 发展 目 之 一 。 标
2多 线切 割机 张力 控 制 机理
21张力产 生波动的原 因 .
利 用速 度差 原理 来研 究切 割线 上张力产 生波 动 的原 因H在 加 :
工过程 中, 加工辊电机按照给定 的速度指令运行 , J I 做线辊与加工 I 殳 辊的线速度不同将产生张力的变化。假定金属丝、 各辊及各导向轮 之间没有滑动, 收线辊与加工辊之间存在速度差(. , , )则有 :
制 等各种 张力控 制方式 。 目前使 用的 张力控 制策略 , 讲述 了传统 PD控 制 、 主要 I 自适应逆 控制 、 模糊 PD I
控 制、 经 网络 PD控 制等 。最后对 张力控 制技 术的发展趋 势进 行 了展 望 。 神 I 关键词 : 多线切 割机 ; 张力控 制 ; 张力 ; 控制 ; 工神 经 网络 恒 模糊 人 【 b ta t T em l — i a p ca N q im n sdt m c ieh r n r kem tr , A s c 】 h ut wr sw i sei C e u e t e ahn ada dbi l aei r i e s l p u o c l a
多线切割机排线机构参数优化设计

多线切割机排线机构参数优化设计汪世益;陶河水;杜冰辉【摘要】多线切割机排线机构是走线系统正常运行的主要机构.传统的排线机构存在各导轮之间钢丝张力波动较大、易造成钢丝拉断的缺陷.文中介绍了一种新的设计方法通过建立导轮张力包角模型,得出导轮两边张力与包角大小和摩擦系数之间的关系;由排线机构中导轮与滑轮之间相对的几何位置,推导出钢丝张力和包角与设计参数L1、H之间的关系表达式.利用优化方法确定导轮与滑轮之间最佳的几何位置,使排线机构工作时钢丝张力波动最小,在多线切割机往复走线过程中,有利于放线辊上的钢丝会逐渐过渡到收线辊上,保证了收放线系统平稳、有序地运行.【期刊名称】《机械工程师》【年(卷),期】2012(000)001【总页数】3页(P65-67)【关键词】多线切割;排线机构;金属丝张力;参数优化【作者】汪世益;陶河水;杜冰辉【作者单位】安徽工业大学,安徽马鞍山243002;安徽工业大学,安徽马鞍山243002;安徽工业大学,安徽马鞍山243002【正文语种】中文【中图分类】TH1611 引言多线切割机主要用于半导体硬脆性材料加工,其加工原理是由钢丝线为载体带动高硬度的研磨砂粒对材料进行研磨去除,实现对材料的切片。
主要有走线系统、供砂系统、主轴冷却系统、润滑系统、工作台进给系统等。
多线切割机结构简图如图1 所示。
排线机构是保证走线系统正常运行的关键机构之一[1-5],排线机构中排线滑轮的直线运动速度大小跟随收线电机的转速,通过排线导轮的周期性往复运动,收线电机能使切割线整齐地缠绕在收线辊上,有效防止多层缠绕时钢丝线乱卷、相互缠绕等现象。
通过建立导轮包角模型及确定导轮与排线滑轮之间的几何位置得出导轮两边张力与包角和摩擦系数之间的关系,通过优化确定排线机构导轮与滑轮之间最佳几何位置,使排线机构运行过程中张力波动更小。
图1 多线切割机结构示意图1.放线辊 2.收线辊 3.排线机构 4.偏转辊 5.张力控制部分 6.测量辊 7.偏转辊 8.加工辊 9.待加工物2 排线系统结构本文排线机构主要有滚珠丝杆、排线滑轮、收线辊、伺服电机、机架几部分组成。
多线切割阿

多线切割机在切割半导体材料时,锯丝由于高压和强烈的摩擦,以及可能的高温作用,碳化硅微粒的运动切割以及大的拉力和循环往复运动使锯丝产生拉断和疲劳断裂,降低了锯丝的使用寿命,碳化硅微粒的磨损和刃口便钝决定了锯切效果,因此,研究多线切割机磨损机理具有很现实的意义。
线锯切割的失效形式:线锯锯丝的失效形式可归结为两类,宏观失效和微观失效,宏观的失效主要表现为:锯丝的拉断和疲劳断裂:微观的失效形式主要有砂浆磨料的磨损、破碎、变钝等失去切削功能。
多线切割机在工作时,只要控制工作台压力即工作台进给速度,锯丝就不会直接被打断,但由于导轮的往复运动,锯丝在长期的交变应力作用下,很容易产生疲劳断裂,转速越高,应力交变频率越大,疲劳断裂增加,锯丝寿命越短,在保持工作台进给速度不变的情况下,尽可能增大导轮直径,或降低锯切速度,从而提高疲劳寿命,当然导轮直径会受到所切晶体直径,最低切割速度及整体尺寸多线切割机切割失效形式有(1)锯丝的拉断和锯丝的疲劳断裂,(2)碳化硅颗粒的磨损和破碎,刃口变钝,失去锯切能力在切片过程中硅片因机械作用造成的刀痕、损伤、破损会导致产生,包括机械应力和热应力在内的应力,进而产生滑移位错,当机械应力和热应力在高温处理过程中的作用超过晶体滑移临界应力时,会产生硅片的破碎[1]。
对于翘曲度、弯曲度、总厚度误差、中心厚度误差等方面的质量控制,可以通过调整线张力进给速度,冷却剂流量等一系列工艺操作来达到目的及要求,它大大降低了生产成本,提高了生产效率,实验证明,线切割机切出的硅片的厚度和质量都很好的满足了下一道工艺的要求[2]。
在硅片加工的过程中,人们越来越多认识到ULSI硅衬底加工过程中消除损伤和应力,去除微粒、边沿和表面的完美性及表面状态等已成为微电子进一步发展的十分重要的因素[3]。
随着改革开放和经济建设的发展,以及竞争激烈的国际市场的需求状况,对硅片加工实现科学控制、确保硅片质量,提高成品率,降低生产成本,增强竞争能力,提高经济效益。
影响线切割加工表面粗糙度的因素及应对措施

影响线切割加工表面粗糙度的因素及应对措施【摘要】阐述了影响线切割加工工件表面质量的原因以及相对应的改进措施,分析得出的结果对保证线切割加工工件的粗糙度有很大的参考价值。
【关键词】线切割;措施;粗糙度;钼丝线切割技术在现代模具加工中起着非常重要的作用,我国的模具产品也在向着大型和精密方向发展,加工的表面质量严重影响着模具的品质。
在线切割加工中除了人为因素以外,还有钼丝因素、机床因素、参数因素和工件因素影响着加工表面粗糙度。
现对这四个因素分别找出应对措施。
1、钼丝因素及应对措施1.1减少钼丝的震动保证贮丝筒和导轮的制造和安装精度,控制贮丝筒和导轮的轴向及径向跳动,导轮转动要灵活,防止导轮跳动和摆动,有利于减少钼丝的振动,促进加工过程的稳定。
1.2降低走丝速度必要时可适当降低钼丝的走丝速度,增加钼丝正反换向及走丝时的平稳性。
1.3加大钼丝的有效长度根据线切割工作的特点,钼丝的高速运动需要频繁地换向来进行加工,钼丝在换向的瞬间会造成其松紧不一,钼丝张力不均匀,从而引起钼丝振动,直接影响加工表面粗糙度,所以应尽量减少钼丝运动的换向次数。
试验证明,在加工条件不变的情况下,加大钼丝的有效工作长度,可减少钼丝的换向次数,减少钼丝的抖动,促进加工过程的稳定,提高加工表面质量。
1.4调整钼丝的张力采用专用机构张紧的方式将钼丝缠绕在贮丝筒上,可确保钼丝排列松紧均匀。
尽量不采用手工张紧方式缠绕,因为手工缠绕很难保证钼丝在贮丝筒上排列均匀及松紧一致。
松紧不均匀,钼丝各段的张力不一样,就会引起钼丝在工作中抖动,从而增大加工表面粗糙度。
2、参数因素及应对措施2.1工件的进给速度要适当因为在线切割过程中,如工件的进给速度过大,则被腐蚀的金属微粒不易全部排出,易引起钼丝短路,加剧加工过程的不稳定;如工件的进给速度过小,则生产效率低。
2.2减小脉冲宽度和减小峰值电流脉冲电源同样是影响加工表面粗糙度的重要因素。
脉冲电源采用矩形波脉冲,因为它的脉冲宽度和脉冲间隔均连续可调,不易受各种因素干扰。
单多晶太阳能硅片切割线痕问题研究
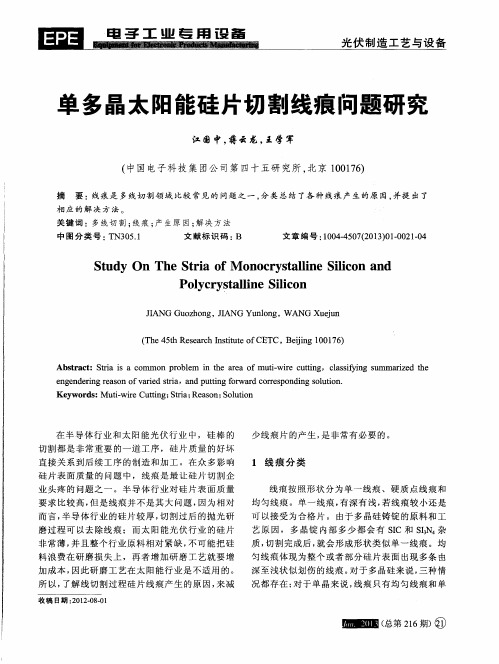
2 单 一 线 痕
造 成 单 一 线痕 的原 因 有 很 多种 因素 , 主 要有 : ( 1 ) 停机 。 切 割机 有 时在 某 些 警 报 下会 自动 停 机, 比如 : 砂 浆 流 量 过低 , 冷却液异常, 电气 柜 温 度 过高 ; 有 时 也 需 要 人 为停 机 , 比如 : 雷 电 天 气 致 供
J I A NG G u o z h o n g , J I A NG Yu n l o n g , WA NG Xu  ̄ u n ( T h e 4 5 t h R e s e a r c h I n s t i t u t e o f C E T C, Be i j i n g 1 0 0 1 7 6 )
收 稿 日期 : 2 0 1 2 . 0 8 . 0 1
光 伏 制 造 工 艺 与设 备
电 子 工 业 苣 用 设 菁
-
一
线痕【 ” 。
过 程 中要 特 别 注 意 : 倒料 时应慢倒 , 控制在 2 . 5 ~ 3 mi n一 袋 , 避 免 猛 倒 造 成 微 粉 沉 底 结 块 搅 拌 不
变 。如 果 改 为 自 化 硅 微 粉 在 8 0  ̄9 0  ̄ C烘箱 里 , 烘8 h 以上 , 来 优 化 碳 化 硅 微 粉 的各 项 指 标 。一 般 来 说 ,
非常薄 , 并且整个行业原料相对紧缺 , 不 可 能 把 硅
料浪 费在 研 磨 损 失 上 ,再 者 增 加 研 磨 工 艺 就 要 增
加成本 , 因此 研 磨 工 艺在 太 阳 能行 业 是 不 适 用 的 。 所 以, 了解 线切 割 过 程 硅 片 线 痕产 生 的 原 因 , 来 减
金刚石线切割技术简析

金刚石线切割技术简析技术简介以生产工艺划分,金刚石线可以分为电镀金刚石线和树脂金刚石线。
金刚石切割线是通过一定的方法,将金刚石镀覆在钢线上制成,通过金刚石切割机,金刚石切割线可以与物件间形成相对的磨削运动,从而实现切割的目的。
金刚石线是用复合电镀的方法将高硬,高耐磨性的金刚石微粉固结在钢丝基体上,而制成固结磨料金刚石锯线。
在切割过程中90%的抗拉强度来自钢丝线,因此钢丝线对金刚石线至关重要。
在自由磨料线锯切割过程中,研磨液由喷嘴直接喷到钢丝线与硅晶体上,由线网的钢丝线带动游离磨料对硅晶体进行切割。
与游离磨料不同,金刚石线将金刚石微分固结到钢丝线上,钢丝线往复移动对硅晶体进行切割。
图:金刚石线构成轴剖面图技术优势传统砂浆的利用钢丝的快速运动将含磨料的液体带入到工件切缝中,产生切削作用。
在切割过程中,碳化硅被冲刷下来,唯有持续进行滚动磨削,而减少切割效率。
碳化硅的硬度9.5(莫氏),而金刚石硬度在10(莫氏)。
金钢线切割线速度基本在15m/s,正常切割的砂浆线速度基本在9-11.5m/s。
而若金钢线再做突破的话,就应该是要更硬,同时兼有更好的自锐性(多晶金刚石),更稳定的固结方式,更快的线速度。
金刚石切割线相比传统工艺有三大优势:1)金刚石线切割漏损少,寿命长,切割速度快,切割效率高,提升产能;2)品质受控,单片成本低,金刚石线切割造成的损伤层小于砂浆线切割,有利于切割更薄的硅片;3)环保,金刚石线使用水基磨削液(主要是水),有利于改善作业环境,同时简化洗净等后道加工程序。
添加剂原理随着金刚石线切割技术的发展及单多晶竞争的日益激烈,多晶硅片将全部由砂浆线切割转变为金刚石线切割。
不过由于金刚石线切割多晶硅片的损伤层浅、线痕明显等问题,常规砂浆线的酸制绒难以在其表面刻蚀出有效的减反射绒面。
目前,针对金刚石线多晶硅片制绒的难题,主要解决办法包括:金刚石线直接添加剂法、干法黑硅(RIE)及湿法黑硅(MCCE)等,由于RIE和MCCE成本及工艺等原因,目前大多数企业以金刚石线直接添加剂法制备金刚石线切割多晶硅片的减反射绒面,当然由于添加剂法制备的电池转换效率低等因素,决定其只是金刚石线切割多晶硅片全面推广的一个过渡阶段。
线切割应力产生的原因及消除应力的方法

线切割产生应力变形的原因电火花线切割是制造冲裁凸模、凹模常用的加工方法,但是在加工过程中会出现模块变形的现象,它限制了线切割加工技术的广泛应用,特别是在精密微细加工中的推广使用。
其原因在于,工件在线切割加工前,模块经历了热加工、冷加工,产生了较大的残余应力,而残余应力是一个相对平衡的应力系统,当线切割去除大量的工件材料时,改变了表层、中间区域和部等诸层与层之间的应力场分布状态,随着电极丝切割轨迹的移动,残余应力不断转变为塑性功,其能量被释放出来,应力的平衡状态被破坏,内应力将重新分布,直至达到一个新的平衡。
在这个过程中,材料产生了变形,导致加工后的工件形状与切割轨迹不一致,破坏了加工精度,甚至使工件报废。
消除线切割产生的应力的方法1、研磨去掉白层。
用研磨的办法去掉表层20HRC的灰白层(即白层)后便进行装配使用。
这样做虽然可以去掉硬度低的白层,但没有改变线切割造成的应力区的应力状态。
2、回火处理。
在线切割后,研磨去零件表面的白层,再在160~180℃回火2h,则白层下面的高硬层可降低5~6HRC,线切割产生的热应力亦有所下降,但是由于回火时间短,热应力消除不彻底。
3、磨削加工。
线切割后磨削加工,可去掉低硬度的白层和高硬层,提高冲模寿命。
但磨削形状复杂的冲模必须采用价格昂贵的坐标磨床和光学曲线磨床,而这两种设备一般厂家都不具备,故推广困难。
4、喷丸处理后再低温回火。
喷丸处理受设备条件和冲模零件形状(内表面)限制,难以普遍应用。
以上方法只能解决部分问题,受各种原因的限制,往往效果并不理想,随着振动时效技术的发展,在线切割加工行业逐渐有了应用。
振动时效技术消除线切割应力或者变形的工艺措施如下:1.在线切割之前使用振动时效消除工件内部的残余应力,降低工件内部的应力水平,使其在切割过程中,即使产生了新的应力,叠加之后的数值仍然低于材料的屈服极限从而也不会有变形。
采用这种工艺对振动时效设备要求很高,希望能最大可能的消除残余应力,华云频谱谐波振动时效设备,消除应力的水平高达70%。
提高织针冲裁模具寿命的措施
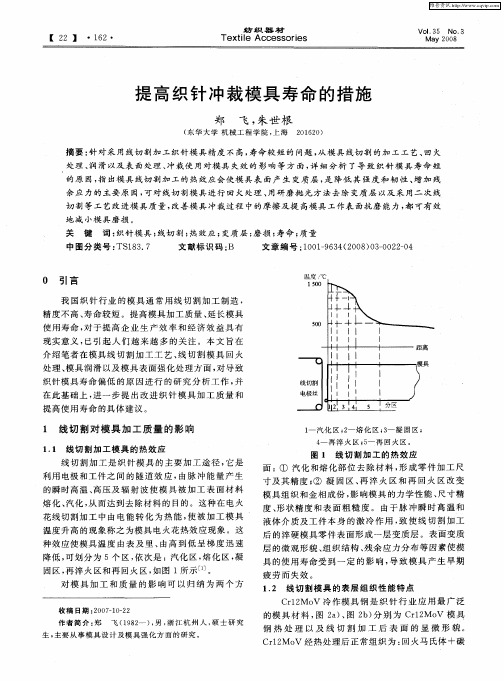
精 度不 高 、 寿命 较短 。提高模 具加 工质 量 、 长模 具 延 使 用寿命 , 于提 高企 业 生 产 效 率 和 经济 效 益 具 有 对
现 实意义 , 已引起 人 们 越 来 越 多 的关 注 。本 文 旨在 介 绍笔者 在模 具线 切 割 加 工 工艺 、 切割 模 具 回火 线 处 理 、 具润 滑 以及 模 具表 面强化 处理 方面 , 模 对导 致 织 针模具 寿命 偏低 的原 因进行 的研 究 分 析工 作 , 并 在 此基础 上 , 进一 步提 出改 进 织 针模 具 加 工 质 量 和
关 键 词 : 织针 模具 ; 线切 割 ; 热效应 ; 变质层 ; 磨损 ; 寿命 ; 量 质
中图分 类号 : S 8 . T 137 文献标 识 码 : B 文章编 号 :0 19 3 (0 8 0 - 0 20 1 0 -6 4 2 0 ) 30 2 —4
0 引 言
我 国织 针 行 业 的模 具 通 常用 线 切 割加 工制 造 ,
后 的淬硬 模 具零件 表 面形 成一 层变 质层 。表 面变质
的瞬时 高温 、 高压及 辐 射 波 使 模 具 被 加工 表 面 材 料
熔 化 、 化 , 而达 到去 除材 料 的 目的。这种 在 电火 汽 从
花 线切 割加工 中由 电能 转 化 为 热能 , 使被 加 工 模 具
温 度升 高 的现象称 之 为模具 电火 花热效 应 现象 。这
生 , 要 从 事 模 具 设 计 及 模 具 强 化 方 面 的研 究 。 主
维普资讯
第3 5卷
第
Te tI c s ore x . Ac e s i s e
化物 +残 留奥 氏体 。经 线 切 割 加 工后 , 表 面 组 织 其
切磨抛工艺
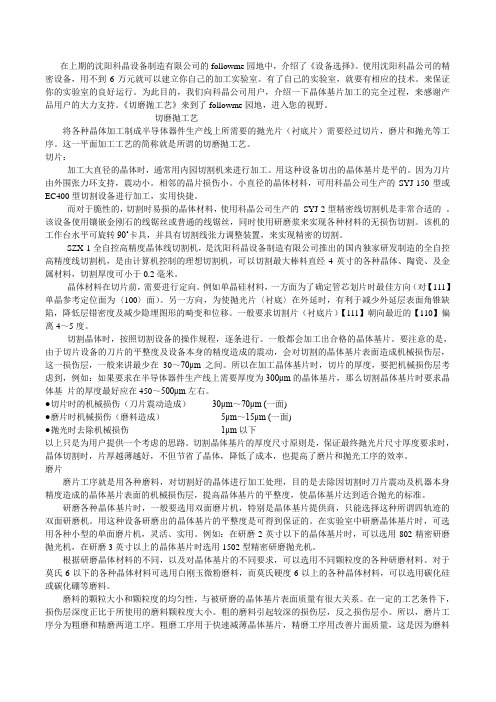
在上期的沈阳科晶设备制造有限公司的followme园地中,介绍了《设备选择》。
使用沈阳科晶公司的精密设备,用不到6万元就可以建立你自己的加工实验室。
有了自己的实验室,就要有相应的技术。
来保证你的实验室的良好运行。
为此目的,我们向科晶公司用户,介绍一下晶体基片加工的完全过程,来感谢产品用户的大力支持。
《切磨抛工艺》来到了followme园地,进入您的视野。
切磨抛工艺将各种晶体加工制成半导体器件生产线上所需要的抛光片(衬底片)需要经过切片,磨片和抛光等工序。
这一平面加工工艺的简称就是所谓的切磨抛工艺。
切片:加工大直径的晶体时,通常用内园切割机来进行加工。
用这种设备切出的晶体基片是平的。
因为刀片由外围张力环支持,震动小。
相邻的晶片损伤小。
小直径的晶体材料,可用科晶公司生产的SYJ-150型或EC400型切割设备进行加工,实用快捷。
而对于脆性的,切割时易损的晶体材料,使用科晶公司生产的SYJ-2型精密线切割机是非常合适的。
该设备使用镶嵌金刚石的线锯丝或普通的线锯丝,同时使用研磨浆来实现各种材料的无损伤切割。
该机的工作台水平可旋转90˚卡具,并具有切割线张力调整装置,来实现精密的切割。
SZX-1全自控高精度晶体线切割机,是沈阳科晶设备制造有限公司推出的国内独家研发制造的全自控高精度线切割机,是由计算机控制的理想切割机,可以切割最大棒料直经4英寸的各种晶体、陶瓷、及金属材料,切割厚度可小于0.2毫米。
晶体材料在切片前,需要进行定向。
例如单晶硅材料,一方面为了确定管芯划片时最佳方向(对【111】单晶参考定位面为〈100〉面)。
另一方向,为使抛光片〈衬底〉在外延时,有利于减少外延层表面角锥缺陷,降低层错密度及减少隐埋图形的畸变和位移。
一般要求切割片(衬底片)【111】朝向最近的【110】偏离4~5度。
切割晶体时,按照切割设备的操作规程,逐条进行。
一般都会加工出合格的晶体基片。
要注意的是,由于切片设备的刀片的平整度及设备本身的精度造成的震动,会对切割的晶体基片表面造成机械损伤层,这一损伤层,一般来讲最少在30~70μm之间。
多线切割晶体表面质量研究

线 轮 上 均 由横 移 架 台系 统 进 行 排 线 以确 保 切 割 线
整 齐 的排 列在 收 放线 轮 上 。 浆 在 晶体 的两 侧直 接 砂
均 匀 的 向下 喷到 高 速往 复 运动 的切 割线 上 , 由于 切
割 线 有 微 量 震 动 ,会 使 砂 浆 很 容 易 的 进 入 切 割 区 域, 同时对 切割 线 和 晶体冷 却 。
硅 单 晶 的表 面质 量 要求 越 来越 高 ,硅 片 经过 切 割 、
研 磨和 抛 光后 , 工损 伤 的程 度和 深 度 是硅材 料 切 加 割 的 关键 因素之 一 ,内 圆切割 机 虽然 有 其优 越 性 ,
如 技 术成 熟 、 片 稳定 性好 等 。但 通 过近 年对 内 圆 刀
切 割硅 片 的损 伤 及作 用 机 理 的研 究认 为 : 方面 内 一 圆切 割 硅 片 的损 伤 层近 表 面 的微 裂 纹 使 硅 片 强 度
机床 结 构 , 分为 往 复式 和 单 向式 线锯 。 目前 在 光 可
电子 工业 中使用 最 为广泛 的是往 复式 多 线锯 。 线锯
大 为 降低 ; 一方 面 , 对 于线 锯切 割 而 言 , 的直 另 相 线
22 实验 分析 .
小 、 片薄 、 厚一 致性 好 、 割 尺 寸大 、 量 大 , 切 片 切 产 效 率 高、 材 并具 有 效益 高 等特 点 。随着 晶体直 径 的 省 增大, 多线 切 割将 完 全 替代 内 圆切 割 。
I 制造设备 与工艺 ・ C
・
பைடு நூலகம்
电 子 工 业 专 用 i 殳备
■
多线切割晶体表面质量研究
徐 旭 光 ,周 国安
( 中国 电子 科技 集 团公 司第 四十 五研 究所 , 北京 东 燕郊 1 1 0 ) 061
光学球面专业知识资料

光学专业知识:光学球面镜片的一般外形:1.双凸 2.一凸一凹 3.一凸一平 4.双凹 5.一凹一平(如图所示)光学镜片分类:化学成分和光学性质相近的玻璃,在阿贝图上也分布在相邻的位置。
肖特玻璃厂的阿贝图有一组直线和曲线,将阿贝图分成许多区,将光学玻璃分类;列如冕牌玻璃K5、K7、K10在K区,燧石玻璃F2、F4、F5在F区。
玻璃名称中的符号:F 代表燧石 K 代表冕牌 B 代表硼 BA 代表钡 LA 代表镧 N 代表无铅 P 代表磷光学冷加工工序:铣磨→精磨→抛光→清洗→磨边→镀膜→涂墨→胶合1.铣磨(荒摺/球铣/粗磨):镜片研磨第一道工序,去除镜片表面凹凸不平的气泡和杂质,(约0.05-0.08mm),起到成型作用。
如下图所示:●原理:如上图所示金刚石磨轮刃口通过镜片顶点,磨轮轴线与镜片轴线相交于0点,磨具轴线绕自身轴线高速旋转,镜片绕自身轴线低速旋转,运动轨迹包络面形成球面。
荒摺加工设备:QM0.8A,厂家:韩国时代,无倒角功能,相对精度较低。
CG2.0,厂家:韩国光进,有倒角功能,相对精度高。
测量工具:中心厚度检测量具(千分尺);球面R值检测量具(矢高表);等厚检测量具。
2.精磨(砂挂):将铣磨出来的镜片将其的破坏层给消除掉,使镜片表面的凹凸层减少,固定R值(光圈,牛顿环)原理:镜片在砂挂皿(根据材质选定金刚石丸片胶制而成)中,砂挂皿沿自身轴线高速转动,镜片沿自身轴线高速转动,且来回摆动,如下图所示,通过金刚丸片磨削镜片表面,从而使镜片表面凹凸层深度减少,使得镜片表面曲率半径精度或平面度进一步提高。
流程:领料→一面第一道砂挂→一面第二道砂挂→二面第一道砂挂→二面第二道砂挂→砂挂提检→流入研磨砂挂设备:小球面单片砂挂设备;大球面单片砂挂设备。
(如下图)检测工具:中心厚度检测量具(千分尺);面精度检测(原器),如下图:单片弹盘工艺(精磨),如下图:多片弹盘工艺(精磨),如下图:3.抛光(研磨):将精磨镜片在一次抛光,这道工序主要是把外观做的更好,注:抛光有的客户做二次抛光,第一道为粗抛,第二道为精抛,现市场大多数客户做一道工序即可。
关于多线切割线痕问题
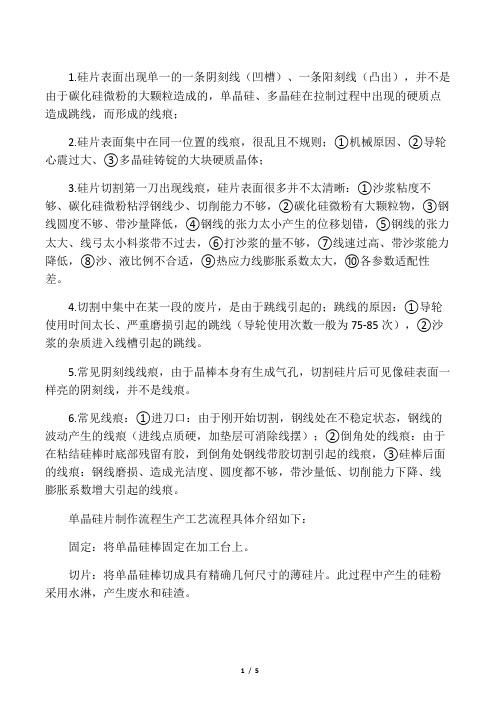
1.硅片表面出现单一的一条阴刻线(凹槽)、一条阳刻线(凸出),并不是由于碳化硅微粉的大颗粒造成的,单晶硅、多晶硅在拉制过程中出现的硬质点造成跳线,而形成的线痕;2.硅片表面集中在同一位置的线痕,很乱且不规则;①机械原因、②导轮心震过大、③多晶硅铸锭的大块硬质晶体;3.硅片切割第一刀出现线痕,硅片表面很多并不太清晰:①沙浆粘度不够、碳化硅微粉粘浮钢线少、切削能力不够,②碳化硅微粉有大颗粒物,③钢线圆度不够、带沙量降低,④钢线的张力太小产生的位移划错,⑤钢线的张力太大、线弓太小料浆带不过去,⑥打沙浆的量不够,⑦线速过高、带沙浆能力降低,⑧沙、液比例不合适,⑨热应力线膨胀系数太大,⑩各参数适配性差。
4.切割中集中在某一段的废片,是由于跳线引起的;跳线的原因:①导轮使用时间太长、严重磨损引起的跳线(导轮使用次数一般为75-85次),②沙浆的杂质进入线槽引起的跳线。
5.常见阴刻线线痕,由于晶棒本身有生成气孔,切割硅片后可见像硅表面一样亮的阴刻线,并不是线痕。
6.常见线痕:①进刀口:由于刚开始切割,钢线处在不稳定状态,钢线的波动产生的线痕(进线点质硬,加垫层可消除线摆);②倒角处的线痕:由于在粘结硅棒时底部残留有胶,到倒角处钢线带胶切割引起的线痕,③硅棒后面的线痕:钢线磨损、造成光洁度、圆度都不够,带沙量低、切削能力下降、线膨胀系数增大引起的线痕。
单晶硅片制作流程生产工艺流程具体介绍如下:固定:将单晶硅棒固定在加工台上。
切片:将单晶硅棒切成具有精确几何尺寸的薄硅片。
此过程中产生的硅粉采用水淋,产生废水和硅渣。
退火:双工位热氧化炉经氮气吹扫后,用红外加热至300~500℃,硅片表面和氧气发生反应,使硅片表面形成二氧化硅保护层。
倒角:将退火的硅片进行修整成圆弧形,防止硅片边缘破裂及晶格缺陷产生,增加磊晶层及光阻层的平坦度。
此过程中产生的硅粉采用水淋,产生废水和硅渣。
分档检测:为保证硅片的规格和质量,对其进行检测。
影响线切割加工工艺指标的因素

影响线切割加工工艺指标的因素可分为电量与非电量因素的影响。
(1)电参量对加工工艺指标的影响电参量——是指脉冲电源的参变量,包括脉冲峰值、脉冲宽度、脉冲频率和电源电压。
1) 脉冲峰值电流对加工工艺指标的影响在其他参数不变的情况下,脉冲峰值电流的增大会增加单个脉冲放电的能量,加工电流也会随之增大。
线切割速度会明显增加,表面粗糙度变差。
2)脉冲宽度对加工工艺指标的影响①在加工电流保持不变的情况下,使脉冲宽度和脉冲停歇时间成一定比例变化。
②脉冲宽度增加,切割速度会随之增大,但脉宽增大到一定数值后,加工速度不再随脉冲的增大而增大。
③线切割加工的脉冲宽度一般不大于50μs。
④增大脉宽,表面粗糙度会有所上升。
3)脉冲频率对加工工艺指标的影响①单个脉冲能量一定的条件下,提高脉冲放电次数,即提高脉冲频率,加工速度会提高。
②理论上,单个脉冲能量不变,则加工表面的粗糙度也不变。
③事实上,对快走丝线切割,当脉冲频率加大时,加工电流会随之增大,引起换向切割条纹的明显不同,切割工件的表面粗糙度会随之变差。
4)电源电压对加工工艺参数的影响①峰值电流和加工电流保持不变的条件下,增大电源电压,能明显提高切割速度,但对表面粗糙度的影响不大。
②在排屑困难、小能量、小粗糙度条件下,以及对高阻抗、高熔点材料进行切割加工时,电源电压的增高会提高加工的稳定性,切割速度和加工面质量都会有所改善。
(2)非电参量对加工工艺指标的影响1)走丝速度①对切割速度的影响:主要是通过改变排屑条件来实现的。
②提高走丝速度有利于:电极丝把工作液带入较大厚度的工件放电间隙中;电蚀产物的排出,使加工稳定,提高加工速度。
③走丝速度过高:会导致机械振动加大、加工精度降低和表面粗糙度增大,并易造成断丝。
④对快走丝线切割,应考虑由于丝电极速度的改变所产生的换向切割条纹对表面粗糙度的影响。
2)电极丝张力对加工工艺指标的影响①提高电极丝的张力可以减小加工过程中丝的振动,从而提高加工精度和切割速度。
多工位线割的参数

多工位线割的参数多工位线切割的参数设置是影响加工效果的关键因素,包括但不限于以下几点:1. 脉宽和脉间:脉宽(Pulse Width)通常指的是电流脉冲的持续时间,而脉间(Pulse Off Time)则是电流脉冲之间的间隔时间。
一般来说,加工厚度在100以下的材料,可以使用脉宽30us,脉间150us作为参考参数。
脉宽越大,电流越大,加工速度会加快,但光洁度可能会降低;相反,脉间越大,电流越小,加工速度会减慢,但光洁度会提高。
2. 张力控制:在进行多线切割时,切割线的张力控制是非常重要的。
适当的张力可以保证切割的精度和质量,避免断线或材料损坏。
3. 同步技术:收放线电机和主电机的同步技术也是影响切割质量的重要因素。
良好的同步可以减少切割过程中的振动,提高切割精度。
4. 刀补点数:在编程时,刀补点数的设置会影响加工路径的精确度。
刀补点数决定了进刀、退刀或刀补移动量分成的段数,这直接关系到加工的精度和效率。
5. 进刀和退刀运动:进刀和退刀运动的设置会影响材料的进入和退出切割区域的方式,这也会直接影响到加工的效率和质量。
6. 加工速度:加工速度需要根据材料的特性和厚度来调整,以确保加工质量和效率。
7. 磨料类型和浓度:磨料的类型和浓度也会影响切割效果,不同的材料可能需要不同的磨料。
8. 机床稳定性:机床的稳定性和刚性也是保证加工精度的重要因素。
9. 环境条件:如温度和湿度等环境条件也可能影响切割过程和结果。
10. 材料特性:被加工材料的特性,如硬度、韧性等,也需要在选择参数时考虑。
11. 冷却系统:冷却系统的有效性对于保持切割区域的温度稳定,防止过热损害材料至关重要。
这些参数需要根据具体的机器设备、材料特性以及加工要求来综合设定,以达到最佳的加工效果。
在实际操作中,可能需要通过多次试验和调整来找到最合适的参数组合。
多型孔零件电火花线切割加工工艺研究
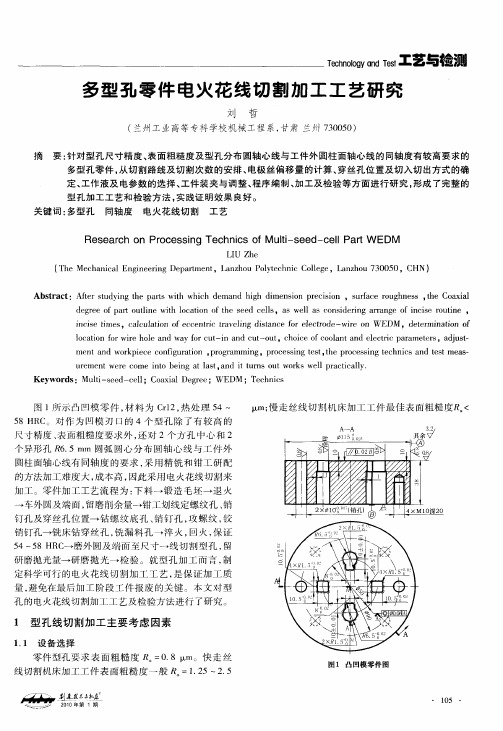
l;)/ / /A V I? / "/ / II ,
1
车外 圆及 端面 , 留磨 削余 量一 钳工 划线 定螺 纹孔 、 销
2 1 、 0
( 孔) 销
一
{ I MO2 l ( ×  ̄
钉孔 及 穿丝孔 位 置一 钻 螺 纹 底 孔 、 钉 孔 , 螺 纹 , 销 攻 铰 销 钉孔一 铣 床钻 穿丝 孔 , 漏 料 孔 一 淬 火 , 铣 回火 , 证 保 5 5 R 一 磨外 圆及 端 面至 尺 寸一 线切 割 型孔 , 4~ 8H c 留 研磨 抛光 量一研 磨 抛 光 一 检 验 。就 型 孔 加 工 而 言 , 制 定科 学 可行 的 电火 花 线 切 割 加工 工 艺 , 保 证 加 工 质 是
i cs i s,c l u ai n o c e ti r v l itn e f re e to e n ie t me ac lto fe c n rc ta c i d sa c o lc r d —wie o ng r n WEDM ,d tr n to f ee mi ain o
m; 走 丝线 切 割 机 床加 工 工 件 最佳 表 面 粗糙 度 R < 慢 。
2 I
~
里 《 I
圆柱面 轴心 线有 同轴 度 的要 求 , 用 精 铣 和 钳 工研 配 采 的方法 加工难 度 大 , 本 高 , 成 因此 采 用 电火花 线切 割来 加 工 。零件加 工 工艺 流程 为 : 料一 锻 造 毛坯 一 退 火 下
Ab t a t s r c :Afe t dyn he p rswi i h d ma d hih d me so r cso ,s ra e r ug n s ,h a il t r su i g t a t t wh c e n g i n i n p e ii n h u f c o h e s t e Co x a
硅片的倒角、研磨和热处理工艺技术

硅片倒角 简介 工艺 流程 主要参数
1. 倒角
倒角
定义:采用高速运转的金刚石磨轮,对进行 转动的硅片边缘进行摩擦,从而获得钝圆形 边缘的过程。属于固定磨粒式磨削。
作用:消除边缘锋利区,大大减小边缘崩裂 的出现,利于释放应力。
崩裂原因:边缘凸凹不平、存在边缘应力、 受热边缘膨胀系数不同等等。
c. 塑性变形。获得非晶的塑性层,最终去除。
(2) 研磨浆主要包括:
a. 磨料:粒度小,则磨削的表面粗糙度小,加 工精度高. 但是加工速度慢。粒度大,则加 工速度快,但是加工粗糙度大。
基于效率和精度要求:先用粗磨料加工,再 用细磨料加工。
磨片中,磨粒通常采用金刚砂,即SiC颗粒。
不同大小磨粒的磨削比较
磨削 表面粗 划痕 效率 糙度
大磨粒 高 大
深
比表 摩擦力 面积 发热量
小 摩擦小, 发热少
小磨粒 低 小
浅 大 摩擦大,
发热多
b. 磨削液的作用: 冷却作用:把切割区的热量带走。 排渣作用:将研磨屑和破碎的磨粒冲走。 润滑作用:减小磨粒和表面的机械摩擦。 防锈作用:磨粒除了磨削工件,对金属底盘 也进行切削,要防止金 属底盘生锈。
1)硅片研磨
磨片:多线切割以后的硅片,表面有一定 的损伤层,(存在晶格畸变、划痕以及较 大起伏度),为了获得光滑而平整的晶体 表面,需要将损伤层去除,通常分两步: 第一,机械研磨,第二,表面抛光。而采 用研磨方式,来去除损伤层,就是磨片。
磨片方式:研磨浆中的磨粒在一定压力作 用下,研磨工件的表面。
硅片的倒角、研磨和热处理
加工工艺: 1. 边缘倒角 2. 表面研磨 3. 热处理
工艺介绍
倒角:通过金刚石砂轮对硅片边缘进行打磨, 使其边缘钝圆光滑,而不易破碎。
- 1、下载文档前请自行甄别文档内容的完整性,平台不提供额外的编辑、内容补充、找答案等附加服务。
- 2、"仅部分预览"的文档,不可在线预览部分如存在完整性等问题,可反馈申请退款(可完整预览的文档不适用该条件!)。
- 3、如文档侵犯您的权益,请联系客服反馈,我们会尽快为您处理(人工客服工作时间:9:00-18:30)。
多线切割工艺对研磨去除量的影响
摘要:
在晶体加工过程中,随着硅单晶尺寸的增大,多线切割技术正被广泛应用于晶体切割工序。
线切割不会明显改善翘曲,但是切割时硅的损耗显著减小,同时损伤深度减小。
这进一步反馈到后续工艺,减小了颗粒产生、残余损伤引起的位错形成、硅片破裂等可能性[5]。
硅切片的损伤层深度直接受晶体切割工艺影响,并影响着后续的晶片研磨工序的去除量。
此外,切片的几何参数[如弯曲度(TTV)、翘曲度(Warp)和平整度(Bow)]也间接影响着研磨工序的去除量。
因此,本文从降低切片损伤层深度、控制切片几何参数精度两方面对多线切割工艺进行研究。
1.1样品
直径:151mm±0.2mm;长度:260mm±10mm;导电类型:P型;电阻率:8~13Ω·cm。
1.2工艺流程
经断头尾、单晶滚圆工序后,得到符合多线切割机加工要求的硅单晶,经定向粘接、多线切割、脱胶、清洗等工艺过程获得厚度为780μm±20μm的硅切割片,对硅切割片的参数进行测试,通过倒角、磨片等工序进行验证。
1.3试验验证
将硅切割片进行倒角、研磨,双面去除量30μm时,表面质量符合
GB/T12965硅单晶切割片和研磨片的要求。
2、结果与讨论
2.1表面损伤层的控制
2.1.1表面损伤层形成机理
多线切割过程中砂浆因切割线往复运动带到切割区域,其中的碳化硅颗粒在切割线高速运动下通过滚压、镶嵌、刮擦过程完成切割。
在一定压力下,与负载轴产生的塑性区域平行的材料开始破裂、变碎并向表面扩散。
同时,塑性区域的边缘还产生了浅径向裂纹;外力卸载后残余压力组成的弹塑性区域可能导致表面产生平行横向裂纹。
当裂纹到达表面后,碎屑材料即被移除。
然而放射状裂纹和中心状裂纹仍然存在且直达表面,这就是多线切割工艺中晶片表面损伤层的形成机理。
2.1.2多线切割工艺对表面损伤层的影响
通常情况下,硅切片损伤层深度与碳化硅的粒径大小有关,碳化硅粒径越大,损伤层深度越深。
由于砂浆的黏度随使用时间的增加而降低[6],将导致金属线携带砂浆的能力逐步降低。
考虑到砂浆的配比决定着砂浆的密度以及碳化硅在砂浆中的分布,故使用不同体积比的砂浆(即绿碳化硅和切削液的混合液)进行试验。
由表1可知,当砂浆中绿碳化硅浓度过大或过小时,晶片表面研磨作用弱化,金属线的切削力加强,增加了表面损伤层的深度,导致表面粗糙度变差。
因此,绿碳化硅的浓度是晶片表面损伤层的影响因素。
2.2多线切割工艺对切片几何参数的影响
2.2.1多线切割工艺对切片TTV的影响
在砂浆流量一定的条件下,提高供线速度,金属线上的砂浆分布均匀,砂浆与单晶的接触面积增大,由于砂浆的研磨作用,切片表面凹点与凸点之间的差异降低,提高切片的TTV水平。
在供线速度一定的条件下,提高砂浆流量,金属线的负载增加且在切割方向的波动增大,容易出现断线。
本研究中,开展了不同供线速度、不同砂浆流量的多线切割工艺的正交试验,试验结果如表2所示。
从表2表中可知,砂浆流量一定时,若供线速度为30m/min,硅片的TTV数值较为理想;供线速度一定时,硅片的TTV随流量的增大而减小。
为获得较好的TTV,确定供线速度为30m/min,砂浆流量为25~30LPM。
2.2.2多线切割工艺对切片Warp的影响
在实际切割过程中,随着晶片直径增大,碳化硅磨削路径加长,为确保金
属线携带砂浆的能力,需要较高的供线速度和耗线量[7]。
因此在大直径单晶切割过程中磨削发热产生热应力,造成晶片的翘曲增大。
本研究中开展了砂浆温度对晶片翘曲度影响方面的工艺试验,试验结果如图1所示。
从图中可以看出,砂浆温度过低或过高,均会使晶片表面各点的温度差异变大而产生热应力,造成硅片的翘曲度增大。
为获得较好的Warp,确定砂浆的温度为24℃~26℃。
若以固定速率进行单晶切割,金属线上某一固定点通过单晶端面的时间将按公式(1)变化,由于固定点通过端面的时间与单晶的半径成正比,导致金属线上各点所携带砂浆通过端面的时间不同,不能实现对端面一致的切割效果而导致翘曲增大。
设计了图2所示的变速切割曲线,利用该曲线对硅单晶进行变速切割,从单晶的头部、中部、尾部各取5片进行翘曲度测试,测试结果如表3所示。
分析可知,变速切割使得头部、中部、尾部的Warp 变化不大且Warp 数值较为理想。
在单晶的进线端,固定点几乎瞬时通过端面,砂浆对单晶的磨削力较大而造成进线端塌边,引起晶片的翘曲突变。
因此在进线端增加导向条,使金属
线上均匀携带砂浆,试验结果见表4所示。
对比可知,使用导向条后晶片的TTV和Warp均有了明显的降低,有利于几何参数的控制。
采用本研究确定的多线切割工艺所得的硅切割片,经脱胶清洗、多槽超声清洗、晶片甩干、晶片检验等过程后,利用本单位的双面研磨机进行了验证,硅切割片双面研磨去除量不超过30μm即可获得表面质量合格的硅研磨片。
由此可见,多线切割工艺与研磨去除量直接相关,通过优化多线切割工艺参数来减少研磨去除量是一种获得硅研磨片经济实惠的有效途径。
参考文献:
[1]邓志杰,郑安生.半导体材料[M].北京:化学工业出版社,2004.19-20.
[3]刘玉岭,檀柏梅,张楷亮.超大规模集成电路衬底材料性能及加工测试技术工程[M].北京:冶金工
业出版社,2002.2-3.
[4]翁寿松.ITRS2001与芯片特征尺寸的缩小[J].微纳电子技术,2002,39(11):1-4.
[5]周旗钢.300mm硅片技术发展现状与趋势[J].电子工业专用设备,2005,34(129):1-6.
[6]侯贺,李金杰.线切割单、多晶硅机床砂浆液调配的研究[J].制造技术与机床,2011,(9):119-
121.
[7]张立,于晋京,李耀东,等,切割速度对硅片翘曲的影响[J].半导体技术,2011,36(5):368-
372.。