氯化丁基橡胶与其它橡胶的并用胶
天然橡胶/溴化丁基橡胶并用胶性能的研究
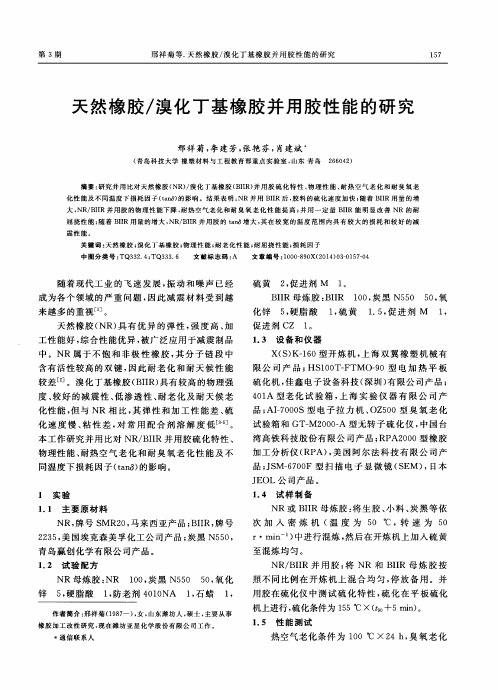
NR母 炼胶 : NR 1 0 0 , 炭 黑 N5 5 O 5 0 , 氧 化 锌 5 , 硬脂 酸 1 , 防老剂 4 0 1 0 NA 1 , 石蜡 1 ,
作者简介 : 邢祥菊( 1 9 8 7 一) , 女, 山东 潍 坊 人 , 硕士 , 主要 从 事 橡胶加工改性研究 , 现 在潍 坊 亚 星化 学 股 份 有 限 公 司工 作 。
1 . 4 试 样 制 备
同温度 下损 耗 因子 ( t a n S ) 的影 响 。
1 实 验
1 . 1 主 要 原 材 料
N R或 B I I R母 炼胶 : 将生胶、 小料 、 炭黑 等 依
次加 入 密 炼 机 ( 温 度 为 5 0 ℃ ,转 速 为 5 O
NR, 牌号 S MR2 0 , 马来西 亚产 品 ; B I I R, 牌 号
第 3期
邢 祥 菊 等. 天然橡胶/ 溴化 丁基 橡 胶 并 用 胶 性 能 的 研 究
天 然橡 胶/ 溴 化 丁 基 橡 胶 并 用 胶 性 能 的研 究
邢祥 菊 , 李建 芳 , 张艳芬 , 肖建斌
( 青岛科技大学 橡塑材料与工程教育部重点实验室, 山 东 青 岛 2 6 6 0 4 2 )
*通信联系人
热 空气 老化 条件 为 1 0 0℃ ×2 4 h , 臭 氧 老 化
1 5 8
橡
胶
工
业
2 0 1 4年 第 6 1 卷
条件 : 温度
4 0℃ , 时间
X ( S ) K- 1 6 0型 开炼 机 , 上 海 双翼 橡 塑机 械 有 限公 司 产 品 ; HS 1 0 0 T - F TMO - 9 0型 电 加 热 平 板
NB、BR和SBR的并用

威 海 职 业 学 院 09
1. 橡胶并用必须具有一定的相溶性,对 橡胶并用必须具有一定的相溶性, 橡胶来说天然、顺丁、 橡胶来说天然、顺丁、异戊橡胶等能以 任何比例均一地混合, 任何比例均一地混合,最终达到相溶状 态。 2.分散性。 分散性。 分散性 3.同步硫化。 同步硫化。 同步硫化 4.共硫化,除了相容性和分散性外,橡 共硫化, 共硫化 除了相容性和分散性外, 胶并用的另一个重要因素是共硫化性。 胶并用的另一个重要因素是共硫化性。
6.
7.
BR 丁苯橡胶( 丁苯橡胶(SBR) 是最大的通用合成橡胶品 海 职 种,也是最早实现工业化生产的橡胶之一。 也是最早实现工业化生产的橡胶之一。 业 学 其物理机构性能, 院 其物理机构性能,加工性能及制品的使用 性能接近于天然橡胶,有些性能如耐磨、 性能接近于天然橡胶,有些性能如耐磨、 耐热、 耐热、耐老化及硫化速度较天然橡胶更为 优良,可与天然橡胶及多种合成橡胶并用, 优良,可与天然橡胶及多种合成橡胶并用, 广泛用于轮胎、胶带、胶管、电线电缆、 广泛用于轮胎、胶带、胶管、电线电缆、 医疗器具及各种橡胶制品的生产等领域。
• 烟片胶一般按外形来分级,分为特级、一级、二级、三级 、四级、五级等共六级,达不到五级的则列为等外胶。
3 基本性能
威 海 职 业 学 院 09
1. 纯粹的橡胶呈无色透明状态,但制成的白色胶片是白色或 纯粹的橡胶呈无色透明状态, 淡黄色,烟胶片呈红褐色。 淡黄色,烟胶片呈红褐色。 2. 热 性 能 : 天 然 橡 胶无 一 定熔 点 , 加 热后 慢 慢 软化 , 到 定 熔点 130~140℃时则完全软化到熔融状态,至200℃左右开始分 ℃时则完全软化到熔融状态, ℃ 解,270℃则急剧分解。 ℃则急剧分解。 3. 高弹性:天然橡胶在常温下柔软而富有弹力,能减弱震动 高弹性:天然橡胶在常温下柔软而富有弹力, 牢固度很强,耐磨擦,揉曲性很大, ,牢固度很强,耐磨擦,揉曲性很大,在一定限度内拉长 后又能缩回。 后又能缩回。 4. 高强度:结晶型橡胶,自补强性大,故具有很好的机械强 高强度:结晶型橡胶,自补强性大, 度
氯化丁基橡胶概述

生产商 ExxonMobil Chemical Lanxess JSR-Japan Butyl Company NKNH
表1 氯化丁基橡胶产能分布
工厂地点 Baton Rouge La Fawley Zwijndrecht/Antwerp Sarnia Kashima Kawasaki Nizhenkamsk
国家 美国 英国 比利时 加拿大 日本 日本 俄罗斯
产能/(kt·a-1) 150 110 150 150 80 98 160
产品 IIR、BIIR、CIIR IIR、BIIR、CIIR IIR、BIIR、CIIR IIR、BIIR、CIIR IIR、HIIR IIR、HIIR IIR、BIIR、CIIR
structure, performance and the applications of CIIR. Key words:CIIR;production status;structure;performance;application
氯化丁基橡胶 (CIIR) 是含有活性氯原子的异丁 烯–异戊二烯共聚物弹性体,是丁基橡胶(IIR)的改 性产物,此类橡胶首次面市于1961年,由埃克森公司生 产。其氯化反应主要发生在异戊二烯部分,且大部分为 氯的取代反应。工业品级的氯化丁基橡胶结合氯含量为 1.1wt%~1.3wt%,双键含量为1.0mol%~1.7mol%。由于丁 基橡胶主链没有改变,被氯取代的氢原子数有限,所以氯 化丁基橡仍具有丁基橡胶的耐热、耐臭氧、耐化学腐蚀介 质和透气性低等优点,同时改善了与不饱和橡胶的相容 性,提高了自粘性、互粘性及共交联能力,被广泛应用于 各个领域,其加工应用研究越来越受到广大科技工作者的 重视。
1
工业、生产
2016年第7期
丁腈胶与氯醇胶及PVC并用胶的性能和应用

丁腈胶与氯醇胶及PVC并用胶的性能和应用氧④丁腈胶与氯醇胶及PVC并用胶的性能和应用z)一巡(柳州市氟硅橡胶制品厂545005)丁腈胶的耐油性能良好,汽车的橡胶配件制品常应用它.但它有一个极大的缺点,在天候老化或暴露在空气中时,极易被氧或臭氧老化,导致橡胶制品发生龟裂,从而失去使用价值.尤其是橡胶制品受到压缩应力或曲挠应力时,更容易发生龟裂.均聚型氯醇胶(CHR)是由环氧氯丙烷共聚台而成,其分子结构成为fCHz——cH一),可见它的主链上含有lCH2Cl醚键,侧链上含有氯甲基fCHCI],这种特有的化学结构,决定它有部分特殊的性能.主链上的醚键,使它具有良好的耐热老化性和耐臭氧性.侧链的极性基因氯甲基使它具有优异耐油性和耐透气性(即气密性),良好耐曲挠性和拉伸强度.丁腈胶与氯醇胶都是极性橡胶分子量相接近,门尼粘度亦相接近,两者的相容性好,容易并用混炼均匀.但两者的硫化体系不同,必须使它们达到同步硫化,才能获得良好的物理机械性能.丁腈胶因为主链上有不饱和双键是不饱和橡胶可用硫磺硫化.氯醇胶因主链上无双键,不能用硫磺硫化体系,而是用促进剂NA--22和氧化铅硫化体系.聚氯乙烯是一种热塑性树脂(缩写为PVC树脂)它是无定形的线形分子,呈非结晶性,它的链节排列规整与丁腈胶并用时宜选用乳液法聚合的糊状聚氯乙烯树脂,其分子结构如下:fCH:—cH,它与丁睛胶Cl并用之后,其硫化胶的拉伸强度,撕裂强度都下;f能提高,耐磨性能,耐油性能耐臭氧老化性能等等获得改善,但是拉伸变形,压缩永久变形增大.PVC树指与丁腈胶并用时须先将PVC粉末与塑化剂(邻苯二甲酸二丁酯)混合搅拌均匀.使之膨润,再在密炼机中并炼,炼胶温度为130'C~140C.在高温下掺合时,高温下的PVC的分子链呈无序状态,分子链间的互相吸引力减弱,分子链段易于移动,使它能在橡胶中分散均匀,最终获得的并用胶质量均一,性能稳定.并炼胶配方及性能如下丁腈胶(日本产N.1型)60.0氯醇胶(武汉产,均聚型)20.0PVC树脂(糊状)20.0氧化镁5.0硬脂酸5.0硫磺1.5促进剂cZ1.2促进剂DM0.5促进剂NA一220.5 防老剂A1.O防老剂RD0.5高耐磨炭黑35.0半朴强炭黑15.0氧化铅3.0髂,矫聚《原材料》氧化铁邻苯二甲酸二丁酯硫化143℃5.020.0胶科性能T104.5rainT口08.5rain拉伸强度12.3MPa 扯断伸长率330老化系数(70℃×96h)0.68耐溶剂试验(25℃x24h)在120汽油75+苯25的混合溶剂中浸泡后增重17.71胶料混炼工艺1.1丁腈胶与聚氯乙烯树脂混炼(用密炼机)1.1.1在粉末状的PVC树脂中加人邻苯二甲酸二丁酯,同时搅拌均匀,放置24h使它膨润后呈糊状.1.1.2在密炼机中投入经塑炼后的丁腈胶,然后加入经过膨润的PVC树脂,使它在13O.~140~C的高温下混炼均匀,然后下料降温至6oc~80℃.1.1.3将上述的并用胶与氯醇胶在密炼机上再混炼,获得三元并用胶.1.1.4将此三元胶在开炼机上陆续加入各种配合剂,加料顺序如下:三元并混胶一加硬脂酸一氧化锌一防老剂一炭黑一氧化铁一氧化镁,氧化铅一硫磺一促进剂CZ,促进剂DM,促进剂NA22等一混炼均匀,薄通下片待用.2几点说明和应用效果2.1丁腈胶须经过塑炼提高可塑度,这样方能使得它与PVC或氯醇胶混练均匀. PVC树脂必须在邻苯二甲酸二丁酯中搅拌膨润呈糊状后方可加入混炼,而且必须在高温下混炼,方能使两者互相分散均匀.氯醇胶则不需塑炼,因能氯醇胶在开炼机辊筒上轧炼时易粘辊.在丁腈胶/PVC并用胶包辊后, 就可以投入氯醇胶混炼,这样避免了粘辊.2.2丁腈胶的硫化体系是硫磺,促进剂CZ和促进剂DM.氯醇胶的硫化体系是促进剂NA一22和氧化铅,氧化镁则可以吸收氯醇胶受热分解出来的HCI.因为两种胶的硫化体系不一样,所以要适当地控制两种胶的硫化速度,使两者能够达到同步硫化,方能获得良好的性能.2.3氯醇胶的耐臭氧老化性能良好,只有在高浓度臭氧,高伸长率的试验条件下,较长的时问才可能见到龟裂现象.因为臭氧与高聚物反应时,主链上为C—C键,不饱和的c=C键受空气中的臭氧作用,将迅速产生龟裂,丁腈胶或天然胶就是实例.而主链上为醚键的饱和高聚物(氯醇胶),基本上不产生氧化龟裂.氯醇胶与丁腈胶并用,既能提高胶料的物理机械性能,又能维持或提高其耐油性,此种胶不仅在静态时耐臭氧性能好,而且在动态时耐臭氧性能也良好.适于制造油封.丁腈胶与PVC两者并用时,它的静态性能虽好,但动态性能则较差.2.4丁腈胶或氯醇胶在元补强剂时,其硫化胶的物理机械性能:拉伸强度,耐撕裂性,耐磨性都较差,必须加入细粒子补强性好的炭黑,方能提高性能.2.5使用效果:用此种并用胶试制一批铁骨架油封,经装车试用半年,行程~万多公里,卸下后观察,设出现龟裂和漏油,可见其性能是良好的,有些产品仍在正常使用之中.。
改善丁腈橡胶仨元乙丙橡胶并用胶相容性的研究

2 1 4 0 0 0
摘要 :研究氯化聚乙烯 ( C P E)和甲基丙烯酸锌 ( Z D MA) 对 丁腈橡胶 ( N B R) / 三元乙丙橡胶 ( E P D M)并用胶相容性和物理 陛能 的影响。结果表明 :随着C P E 用量增 大 ,N B R / E P D M并用胶 的硬度、1 0 0 %定伸应力 、拉伸强度和撕裂强度呈增大趋势 ;随 着Z D MA 用量增大 ,N B R / E P D M并用胶的硬度、l 0 o %定伸应力和撕裂强度呈增大趋势 , z D M A 用量过大导致胶料的拉伸强度等物理陛能下 降,Z D MA 用量以5 ~ 1 0 份为宜 ;添加
改善丁腈橡胶仨 元乙丙橡胶并用胶 相容性的研究
孟逸 东L ,陈理 想 ,肖建斌
( 1 . 青 岛科技大学 ,山东 青 岛 2 6 6 0 4 2 ;2 . 无锡市华安橡 塑密封科技有 限公司 ,江苏 无锡
3 . 江苏扬 州合 力橡胶制 品有 限公司 ,江苏 扬州 2 2 5 0 0 )
胶料 ,本工作研究氯化聚 乙烯 ( C P E)和 甲基丙烯酸
锌 ( Z D M A) 对N B R / E P D M并用胶相 容性和物理性 能
的影响 。
1 . 4 主要设备 与仪器
1 实 验 1 . 1 原 材 料
N B R,牌号 1 0 5 2 ,丙烯 腈质 量分数 3 3 %,中国 台湾南帝化 学工业股份有 限公 司产 品 ;E P D M,牌号
2 结果 与讨 论 2 . 1 CPE 用 量 对 NBR / EP DM并 用 胶 物 理 性 能的影响
C P E 具有 良好类 橡胶 混合 ,且 具有 良好 的高温稳 定性 和 耐溶剂 性 能 。橡 胶硫化 过程 中 ,在 引发剂 的 作用 下 ,不饱 和羧 酸金 属盐 既能 与橡胶 结合 ,本 身 又 能均 聚 ,并 因分 子结 构 中具 有 由金属 阳离 子和羧
【doc】丁基橡胶和三元乙丙橡胶在内胎中的并用

丁基橡胶和三元乙丙橡胶在内胎中的并用槲.确协旧丁基橡胶和三元乙丙橡胶在内胎中的并用L.JT/"lomas等着赳梦雄译刘作雄校.研,/-J一丁基橡胶(IIR),邵异丁烯一异戊二烯橡胶,由于其具有极好的气密性能而得到普遍的关注.因而这种橡胶较多地用于内胎【,轮胎气密层_|等胶料中.但是,丁基橡胶的确也有一些块点.谤胶用于制造内胎时,硫化前其胶料强度一般.在内胎使用时,这种橡胶也仅具有中等的抗臭氧,抗热和抗硫化返原的性能.胶料硫化前的强度对保持内胎压出形状起重要的作用.抗臭氧性能则对内盼生产后避免储存产生龟裂具有重要的意义.由于内胎在比较高的温度和载荷条件下工作对,会发生氧化作用,如果丁基橡胶硫化胶具有抗热和抗硫化返原性能的话,便可使氧化作用所产生的内胎软化现象减到最小.丁基橡胶的这些缺点可用通过并部分EPDM(三元乙丙橡胶)加以克服.EPDM有完全饱和的主链,相反,IIR由于结构中的异戊二烯单元使其具有某些不饱和性.EPDM完全饱和的主链使得它具有较好的抗氧和臭氧作用的性能.由于在硫化时IIR发生断链反应而EPDM发生交联反应,因而这两种胶的并用给出一种具有极好的抗老化特性的产品.本文研究iIR/EPDM并用胶的比率,EPDM的类型和配料变化对内胎使用关键性能的影响.试验本文所讨论的胺料按表l的配方混炼.这种配方是典型的内胎胶料配方,在文献中1O可以壹到.配方中使用具有中等不饱和度的丁基橡胶,这种丁基橡胶具有较怏的硫化速度和较好的抗热性能的综台平衡性能.试验中改变EPDM的类型和用量,总的胶含量(IiR加EPDM)则慑持为100份.峻料盔BR型密炼机中混炼(混炼室容量为1.57升),除硫化剂外,所有的配合剂在混炼周期的l:始便全部加人密炼机中,一分钟后打开下顶栓,排胶温度为150℃.在开炼机上将硫化剂加到已冷却的胶料中.混炼后,按加压硫化法进行硫化,然后对制品按ASTMD412方法进行物理性能试验.热老化试验按ASTMD573进行.抗臭氧性试验按ASTMD1149方法进行,试样暴露于38℃,50MPa(50pphm)的臭氧中,同时试样作20的拉伸.表1内胎胶爱方IIREPDMN660炭黑石蜡汕氧化锌促进剂MBT促进剂TMTD硫黄按文中所述按文中所述7030b0.51.5l量208硫化前的胶科强度按两种方法进行测定.在第一种方法中,按照AsTMD412的方法, ,,f-//,一D【将未硫化的肢料进行l00%定伸应力的试验.第二种方法为尤尼罗伊尔化学公司内部的方法.这种方法由于模拟内胎生产【f1的成型操作已得到推广,在预测胶制弛能方面,这种方法已成功地得到应用.该涪在附录1中详细叙述,其主要程序是把未硫化的胶料拉仲到100%的形变,然后让该胶料保持这种状态两分钟,测定最大张力和两分钟后的张力,计算张力的百分保持率<i00×(最大张力一两分钟后的张力)/最大张力].胶料的粘着性能按孟山都Tel—Takf方法进行测定.施加l千克重量到来硫化混烁胶的胶条上,作用时问为6O秒钟,然后测定剥离试样所需的力.放置一块0.5ram厚的来硫化胶料的试样于Aminco--Goodrich气透仪上进行气透率测定.使试验气体(空气)在恒定压力下作肘在试样的一侧,通过该试验隔片的气体收集在一彻压管中并进行测定,其结果转换成标准温度和压力下的数据.结果与讨论聚合物变化的影响l,聚合物类型为了确定关键性的加工性能以及物理性能的差g《,将4种不同品级的EPDM用于75/z5 的iiR/EPDM胶料中与l00%IIR胶料进行比较.其中Z~IEPDM为ENB(乙叉降冰片烯)型共聚物,第四种EPDM为DCPD(二聚环戊二烯)型共聚物,其性质如表2所述.在ENB类型的EPDM~,脏料硫化前的表2EPDM的性质强度随乙烯含量的增加而增加(EPDMC> EPDMB>EPDMA),这是由于在EPDM主链中乙烯单体的结晶度增加的缘故.对胶料硫化前的强度(即未硫化胶料的定伸应力)的两种标准的试验来说,这利结果都是相符的,未硫化胶料的定伸应力试验结果见图l,而模拟内胎生产测定胶料硫化前的定伸应力的试验结果见图2.所有的IIR和EPDM并用胶料都比单用IIR强度高.虽然EPDMD的乙烯含量与EPDMA一样,但其胶料的硫化前的定伸应力I:LEPDMA 低得多.其原因是由于EPDMD粘度(或分子量)]:~EPDMA低以及EPMDD是一种DCPD型EPDM,而EPDMA是一种ENB型EPDM的缘故.第三单体为DCPD型的EPDM 有较高程度的分支(在这里,即有较低的结晶度),这导致其并用胶的硫化前强度稍低.胶料硫化后的拉伸强度的趋势与胶料硫化前的定伸应力的趋势相同,具有较高乙烯含量的ENB型EPDM有比较高的拉伸强度.DCPD 型的EPDMD比具有相同的乙烯/丙烯比率的ENB型的EPDMc强度要低,这主要是由于DCPD型的EPDMD的分子量比较低.不过这种并用胶的强度仍~LlooiiR胶料的强度高(见图3).IIR/EPDM并用胶料与l0OIIR胶料比11?较,撕裂强度表现出C口型撕裂强度稍高而B口型的撕裂强度稍低,各种类型的EPDM之间未看到显着的差别(见图4).豳T最t,盱JKr幽T2I1.KI.【■保持事【,孽《IIREPDM%ElDM娄型围1胶料硫化前的100定伸应力与EPDM类型的关系(100IIR与IIR/EPD.M井用胶比较)JlRi0o755,sEPDM.25252,EPDM类型一^.co圈3拉伸强度与EPDM类型的关系(100IIR与IIR/EPDM井用胶比较)胶料存15OoC下经24或48/J',时的苛刻条件进行老化.其结果表明:与EDPM并用的胶料比100IIR胶料有较好的强度性能保持率.图5表示胶料经热老化后拉伸强度和扯断伸长率的变化百分率.IIR/EPDM并用胶拉伸强度l2'圈2黢料破化前的定伸应力与EPDM类型的关系[100%IIR与IIR/EPDM并用胶比较(模拟内胎生产的试验)]l翌}}C口型撕裂_B口型撕裂】IRlIO,3,,EPDM<0:725PDM眷垫c圈4撕裂强度与EPDM类型的关系(100%IIR与IIR/EPDM井用胶比较)下降比IIR胶科要小,然而,对于老化后扯断仲疑率的变化百分率,100IIR胶料表现出其性能变化好于并用胺科.由于IIR股在氧化时发生降解反应,实际上IIR胶料的扯断伸长率有了增加.在热老化后,100IIR胶料存々J_4H¨^一"u_1.玛c"a站∞0~扣∞n\2在返原的迹象,其表面显着发精.图6表示B口型和c口型两种试片热老化话的撕裂强吱变化昀百分率.老化后IIR/ EPDM并用胶的撕裂强度损失比100%IIR胶的撕裂强发损失要小.采.ijEPDMD的并用拉伸强度Ij50C老化2,瞄盈150℃老化48小别扯渐伸艮率口150℃老化24小时Ej5O℃老化48列^v褂jIR%I∞"拈冲Er,DM%oz57,5EPDM安,一一A日cD圉5热老化后拉伸强度及扯断冲长率与EPDM的关系(1O0IIR与lIR/EPDM并用胶比较)胶,综台性能的像持比采川其它品级的EPDM 并用胶要稍好一些.列在表3巾1'1~3有关烁驳的辅藉陛能值表明:IIR胶料和IIR/EFDMDHI【鲫前与着性能最好,就它们的辅藉况来看,超出了粘着试验的限度(求出现剥离).总的说来,它们的粘着划离度超出了』胶料硫化前的定伸强度.采刚它类型I}<JEPMD的IIR/EPDM 并用歧,虽也表现出较高的精着性能,但这些试片确实出现了离现象抗臭氧陆自试验表j:DCPD型O~EPDM,~OEPDMD,比其它类型的EPDM的抗臭氧龟裂性能好得多.在图7中列出的数据表明: 印使最差的IIR/EPDM3t-用胶也比全IIR胶料龟裂叫问推迟一倍以上.遥率试验表叫含25份EPDM与75份IIR^v褂制B口Jl=ll撕裂_l50C老化24小削圈I50C老{L48~J',1],lC口型撕裂L-q150XS老化24小时暖I150℃老化d8小时1It2T∞,5EPDM0跨2巧2,EPDM类型….口图8热老化后B口型撕裂强度爱c口型撕裂强度_~zPOM类型的关系(100IIR与IIR/EPDM并用胶比较)的并用胶具有较高的气透率,其气透率大约是100IIR胶的2.倍(见图8).在使用不同类型的EPDM的并用胶之间则未见到显着的差别.虽然测定出的值表明气遥率增大,这意眯着严格要求的话,不利于IIR/EPDM并用胶的使用,但在实际用于内眙时对压力授失并没有明显的影响.内眙中的气体压力损失可按下面的公式计算tP【=P0c-at式中Ⅱ:(PoAu)/VH13婚加""∞"们俯冲怕∞婚0吣西阳∞帅弦∞P-是指时间为t(天数)时的压力,P0是初始压力,A是内胎的表面积,u是测定到的气透率,V是充气内胎的体积,而H是内胎的厚度.一-7r=soo:=蚕=IIREPDM%EPDM类型圈圜圈震围7抗臭氲性能与EPDM类型的关系(1OOIIR与IIR/EPDM并用胶比较)试验条件:50MPa臭氧.拉伸20,38其充气压力为620KPa(90磅/每平方英寸)的lO.o0×20载重轮胎内眙所计算的压力损失亦在图8中列出,其结果表明:超过3O天的压力损失虽然可以测量出,但其值很小._气±单搿IdiKPa甜:皇哪埘妲々宕围8气遗牢及空气压力损失与EPDM类型的关系(1O0%IIR~IIR/EPDM并用胶比较)试样为lO.00×20载重汽车内胎,~,620kPa表3轱着性能与EPDM类型的关系(10OIIR与IIR/EPDM并用吱比较) 丁基胶EPDMAEPDMBEPDMCEPDMD粘着值(kPa)IIR%EPDMEPDM类型220100O2697525A2697525B2837525C3487525D注:1)束在界面损坏2,聚合物比率由于EPDMD和其它的EPDM橡胶相比具有较好的抗臭氧性能和耐热性能以及较好的粘着特性,而其它的性能相类似,所以我们选择这种橡胶与IIR并用作进一步的研究.我们用标准的内胎胶配方对EPDMD与IIR的并用进行了评价,IIR/EPDM的并用比最高达到75/25.现已发现;某些关键性的性能臆聚台物比的变化而发生变化.硫化前胶料的定仲应力一一IlR与EPDM14并用的来硫化胶科的定伸应力一般将增加,增加的量取决于所使用的EPDM的类型.具有较高分子量和较高乙烯含量的EPDM将比较低分子量和较低乙烯含量的EPDM给出较高的硫化前定伸应力.图9表明:IIR/EPDM并用胶胶科的硫化前定伸应力随EPDM含量增加呈线性增加.硫化后的拉伸强度一~硫化后的拉伸强度如图lO所示,臆EPDM增加成线性关系而稍有提高.这样就可以增加填料和油的用量而能获^\5\,g一_0_[×v讣魁.E^E×V褂喇_气透网3o灭后的Krc:皱n009…-.J∞,2015/!IR/EPDMD的比率圈l3气透率爱空气压力与IIR/EPDM比率的关系诮样为lO.tiff×:O戟重胎内胎.内压620KPa填料/油含量对于IIR/EPDMD并用胶料来说,由于拉伸性能得到提高,在成品内胎的脏料中就可以使用较高填充量的填科和操作油来获得与100IIR胶料相同的物理性能.图14表示改变袋黑和操作浊用量对IIR/EPDMD并用股的拉伸强度的影响.预计拉伸强度随填料稆操作油用量的增加而下降,怛是,图14表明:其填充量从7O份炭黑和28份操作油增加到78份炭黑和31份操作油时,仍能保持住100%IIR胶料所具有的11.5MPa的拉伸强度.如图3已经看到时,其它几种EPDM给出更高的拉伸强度.因此,在IIR/EPDM并用胶中,可以较多增加填料和操作油的用量,仍可以得到与对比的10OIIR胺一样的拉伸强度.如上所述,对于获得相比较的拉伸强变来说,可允许使用更高用量的填料和操作油.炭黑和操作油的用量亦对气透率稍有影响,如图I5所示,气透率随操作油增加而稍有增加:随炭黑用量增加而稍有下降.调整炭黑和油的用量将使得胶抖最终的气透率不产生什么变化16^V虐蛰N660炭黑(份数)圈¨炭黑和操作油用■与75/25IIR/EPDMD的拉伸强度(MPa)的关系7072777800820,5N660炭黑(份数)圈l5炭黑和操作油用■与75/25IIR/EPDMD吱科的气遵率关系(1O..×m/m./天)结论业已证明,由于EPDM具有抗臭氧,抗热,抗硫化返原及其胶料硫化前强度较好的性能, 对于内胎使用fls,JIIR胶来说,它是一种很有价值的井用添加物.虽然气透率随EPDM用量的增加而变大,但气遭率的这种差别对这种并用¨如砷l胶在载重汽车,公共汽车等机动车辆的内胎实际应用来说几乎没有什么影响.我们对不同类型的EPDM进行了评价. EPDMD(一种DCPD型EPDM)赋予并娜皎最好的抗臭氧和抗热性能.EPfC(一种ENB型EPDM)使并用胶料具葙最高的硫化前定伸应力和硫亿后拉伸强度.如果考虑抗臭氧性能的话,为了获得比t00fIR胶料更好的抗臭氧性能,需要2O或20 份以上的EPDM用量.tlR/EPDM并用胶通常比100%IIR胶料有驶高的拉伸强度,因此,这些井用胶一般可采用较高填充量的填科和操作油,从而可获得较低成本的配方.附录,内胎胶料硫化前的定伸应力试验该试验模拟内胎生产中的成型操作并已成功地用于预测胶料性能.试样制备用于生产的内胎胶料或试验室混炼后的胶科按如下方法制备试样一1,在热开炼机(70~80℃)的后滚简上热炼胶科,滚距调到2.5~3.8mm.2,加足量的胶料保持少量的薄堆积胶,热炼到胶料光滑并无空气.3,停止热炼一一出片.4,标出压出方向,并用滑石粉处理胶片的两面.5,在试验前至少停放4小时,沿压出方阿冲切出12.7ram宽哑铃状拉伸用试片,测量试片厚度.步骤使用INSTRON试验机,4.5kg(10)测力传感器.拉伸速度为50ero/分,夹具打开相距7.6era.将试样夹持在夹具中~一使用最小的空气压力.然后将试样拉伸到I5.2cm一一大约1O0定伸(拉伸时间约0.015分钟).拉伸后保持1.85分钟(总对问为2分钟).把试样从夹具取出,让其松驰,然后将其固定.计算T…,T2,保持张力百分数.结果计算张力(最大)¨M=拉伸至两分钟时的张力T2,MP:坌壁厚度,mIll张力保持百分数=T2×100/Tmt附景2聚台物说明参考文献:3篇(略)译自《JournalofElastomersandplastics》23[2),119(199I) -每平方英寸磅数t张力≈i{羹r寸17.。
橡胶并用知识
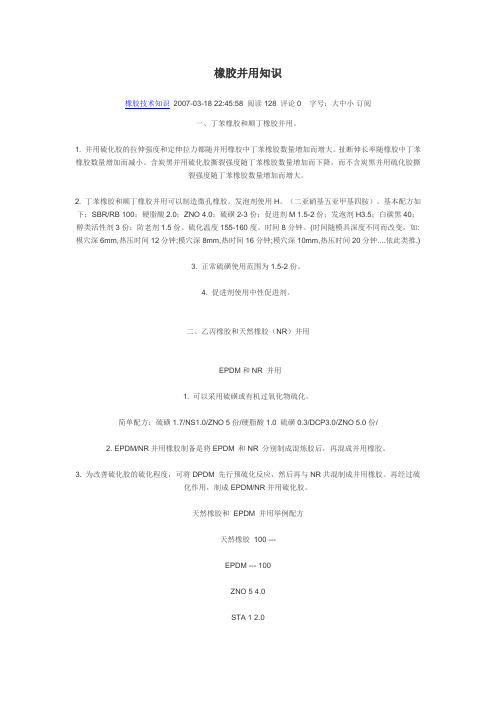
橡胶并用知识橡胶技术知识2007-03-18 22:45:58 阅读128 评论0 字号:大中小订阅一、丁苯橡胶和顺丁橡胶并用。
1. 并用硫化胶的拉伸强度和定伸拉力都随并用橡胶中丁苯橡胶数量增加而增大。
扯断伸长率随橡胶中丁苯橡胶数量增加而减小。
含炭黑并用硫化胶撕裂强度随丁苯橡胶数量增加而下降,而不含炭黑并用硫化胶撕裂强度随丁苯橡胶数量增加而增大。
2. 丁苯橡胶和顺丁橡胶并用可以制造微孔橡胶。
发泡剂使用H。
(二亚硝基五亚甲基四胺)。
基本配方如下:SBR/RB 100;硬脂酸2.0;ZNO 4.0;硫磺2-3份;促进剂M 1.5-2份;发泡剂H3.5;白碳黑40;醇类活性剂3份;防老剂1.5份。
硫化温度155-160度。
时间8分钟。
(时间随模具深度不同而改变,如:模穴深6mm,热压时间12分钟;模穴深8mm,热时间16分钟;模穴深10mm,热压时间20分钟....依此类推.)3. 正常硫磺使用范围为1.5-2份。
4. 促进剂使用中性促进剂。
二、乙丙橡胶和天然橡胶(NR)并用· EPDM和NR 并用1. 可以采用硫磺或有机过氧化物硫化。
简单配方:硫磺1.7/NS1.0/ZNO 5份/硬脂酸1.0 硫磺0.3/DCP3.0/ZNO 5.0份/2. EPDM/NR并用橡胶制备是将EPDM 和NR 分别制成混炼胶后,再混成并用橡胶。
3. 为改善硫化胶的硫化程度,可将DPDM 先行预硫化反应,然后再与NR共混制成并用橡胶。
再经过硫化作用,制成EPDM/NR并用硫化胶。
天然橡胶和EPDM 并用举例配方天然橡胶100 ---EPDM --- 100ZNO 5 4.0STA 1 2.0加工油1-5 1-5碳黑50 50硫磺 2.5 1.5MBTS 0.6 0.6TMTD 0.2 1.0例如:EPDM 与NR 配方中,EPDM 经过160度15分钟预硫化后与NR 制成50:50并用橡胶,拉伸强度可以达到17.4MPA。
丁苯橡胶与氯化丁基橡胶共硫化方法
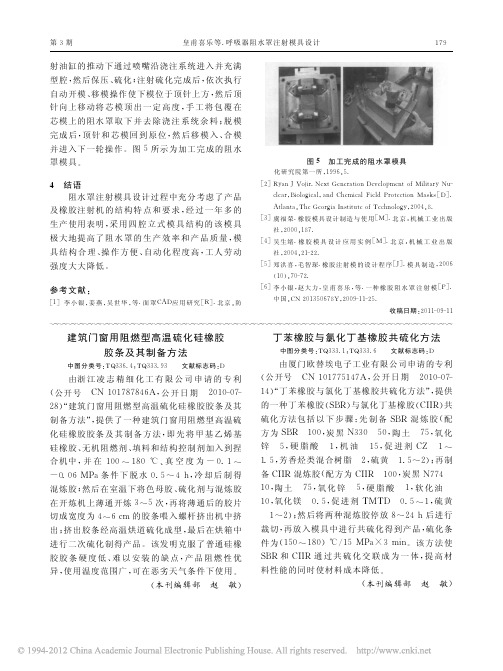
1 7 9
射油缸的推动下通过喷嘴沿浇注系统进入并充满 型腔 , 然后保压 、 硫化 ; 注射硫化完成后 , 依次执行 移模操作使下模位于顶针上方 , 然后顶 自动开模 、 针向上移动将芯 模 顶 出 一 定 高 度 , 手工将包覆在 脱模 芯模上的阻水罩 取 下 并 去 除 浇 注 系 统 余 料 ; 完成 后 , 顶 针 和 芯 模 回 到 原 位, 然 后 移 模 入、 合模 并进入下一轮操作 。 图 5 所示为加工完成的阻水 罩模具 。 4 结语 阻水罩注射模具设计过程中充分考虑了产品 及橡胶注射机的 结 构 特 点 和 要 求 , 经过一年多的 采用四腔立式模具结构的该模具 生产使用表明 , 极大地提高了阻 水 罩 的 生 产 效 率 和 产 品 质 量 , 模 具结 构 合 理 、 操 作 方 便、 自 动 化 程 度 高, 工人劳动 强度大大降低 。 参考文献 :
由浙 江 凌 志 精 细 化 工 有 限 公 司 申 请 的 专 利 ( 公开号 C 公 开 日 期 2 N 1 0 1 7 8 7 8 4 6 A, 0 1 0 0 7 - - ) “ 建筑门窗用阻燃型高温硫化硅橡胶胶条及其 2 8 , 制备方法 ” 提供了一种建筑门窗用阻燃型高温硫 即先将甲基乙烯基 化硅橡胶胶条及 其 制 备 方 法 , 硅橡胶 、 无机阻燃剂 、 填料和结构控制剂加入到捏 合机中 , 并在1 真 空 度 为 -0. 0 0~1 8 0 ℃、 1~ 冷却后制得 -0 . 0 6 MP a条 件 下 脱 水 0. 5~4h, 然后在室温下将色母胶 、 硫化剂与混炼胶 混炼胶 ; 在开炼机上薄通开炼 3~5 次 , 再将薄通后的胶片 切成宽度为 4~6c m 的胶条喂入螺杆挤出机中挤 出; 挤出胶条经高温烘道硫化成型 , 最后在烘箱中 进行二次硫化制得产品 。 该发明克服了普通硅橡 胶胶 条 硬 度 低 、 难 以 安 装 的 缺 点, 产品阻燃性优 异, 使用温度范围广 , 可在恶劣天气条件下使用 。 ( 本刊编辑部 赵 敏 )
丁腈橡胶与氯丁橡胶并用生产彩印胶辊

处理方面 的应用将会越来越 广泛 。
参 考 文 献
1 粱汉 昌 .痕量 物质分 析
中国 石 化 出 版 社 .0 0 2 0 Βιβλιοθήκη 气 相色谱 法 .北 京 .
2 沈 培 明 .固 相 萃 取 (P ) 痕 量 有 机 污 染 物 气 SE在 相 色谱 分 析 中的 应 用 .第 八 次 全 国 色 谱 学 术 报 告 会文 集 ,9 18 4 ) 1 9 (8 8 9 3 李玲颖等译 现代蔽相色 谱 天 津 .甫 开 大 学
热、 耐化 学腐 蚀 性 能 , 改善 了 NB R耐 臭氧 及
抗 老 化性能 . 同时也降低 了混 炼胶 的成本 。 ( ) R/ R 并 用 后 , 以 根 据 C 的 3 NB C 可 R
先 将 胶辊 的轴 芯 表 面 除锈 , 轴 芯 表 面 在 涂涮 开 姆洛 克 25 粘 剂 或硬 质 胶 浆 , 烘 0胶 待 干 后 , 上底 层硬质 胶 。 胶时需 排 除胶 片上 包 包 的气 泡 , 匀压 实 , 均 再包 上 已准备 好 的胶 片 。
檬 竖 并 用 法 简单 , 合 在 小型 胶 厂 推广 应 用 。并 甩 后 腔 料 的 综 合性 能较 好 , 高 了 产 品 的耐 热 、 化学 腐蚀 性 适 提 耐
能. 同时也降低了成本。还可根据 C R的并甩份数调 整产 品的硬度 。 关键调 : 丁腈橡 胶( B ; N R)氯丁橡胶 ( R) 井甩 c ;
以薄 通 i0次 为一 段 , 放 2 0 停 4h后 , 续 塑 继 炼 二段 或三 段 , 可 塑度 控制 在 04左 右 为 使 .
宜。
经 多 次 试验 , 定 下列 配 方 进 行 生 产 : 确 NB 7 、 C 0 硫 磺 1 5 促 C 2 促 R0 R3 、 .、 Z、 F MTD . 5 0 1、 Z O5 n 、 硬脂 酸 2 、 防
氯化丁基橡胶CIIR的特性
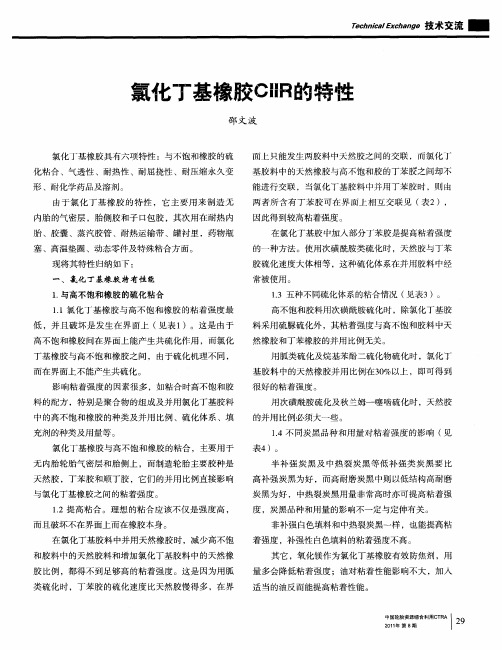
料采用硫脲硫化外 ,其粘着强度与高不饱和胶料 中天 然橡胶和丁苯橡胶的并用比例无关。
用 胍类 硫化 及烷 基苯 酚 二硫化 物 硫化 时 ,氯化 丁 基胶 料 中的天 然橡 胶并 用 比例 在3 %以上 ,即 可得 到 0
很 好 的粘 着强 度 。
1与高不饱和橡胶 的硫化粘合 .
11氯 化 丁 基橡 胶 与 高 不饱 和 橡胶 的粘 着 强度 最 . 低 ,并且 破 坏是 发 生 在 界 面 上 ( 表 1 见 )。这是 由 于 高 不饱 和 橡胶 间在界 面 上能 产 生共 硫化 作 用 ,而 氯化 丁基 橡 胶 与高 不饱 和 橡胶 之 间 ,由于硫 化 机理 不 同 ,
的一种方法。使用次磺酰胺类硫化时 ,天然胶与丁苯
胶 硫 化速 度 大体 相等 ,这 种 硫化 体 系在并 用 胶料 中经 常被 使用 。 1 . 种不 同硫 化体 系 的粘合 情况 ( 表3)。 3五 见 高 不饱 和胶 料 用次磺 酰 胺硫 化时 ,除氯化 丁基 胶
、
氯化 丁基橡胶 特有 性能
而且破坏不在界面上而在橡胶本身。 在氯化丁基胶料 中并用天然橡胶时 ,减少高不饱 和胶料 中的天然胶料和增加氯化丁基胶料 中的天然橡 胶 比例 ,都得不到足够高的粘着强度。这是因为用胍
类硫 化 时 ,丁苯胶 的硫 化速 度 比天 然胶 慢 得 多 ,在界
着强度 ,补强性 白色填料的粘着强度不高。
ThcEh g 技术交流 ■ enax a e cil cn ■
氯化丁基橡胶Ci的特性 i R
邵 文 波
面 上 只能 发生 两胶 料 中天 然胶 之 间 的交联 ,而氯 化 丁
氯化丁基橡胶具有六项特性 :与不饱和橡胶的硫
汽车软管及其质量的检验

车用胶管及其质量的检验汽车胶管在汽车底盘、发动机和车身三大系统中起着输送油、气、水及传递动力的作用,是汽车的重要零部件。
汽车胶管主要有制动软管、空调器管、散热器管、燃料油管、动力转向管、输油管、液压管、异型胶管等。
主体材料一般采用丁腈橡胶(NBR)、氯丁橡胶(CR)、氯化聚乙烯(CPE)、氯磺化聚乙烯(CSM)、二元乙丙橡胶(EPDM)、氯醚橡胶和氢化丁腈橡胶(HNBR)及它们的并用胶,骨架材料一般为维纶、聚酯帘线等。
成型工艺多为硬芯法、软芯法和无芯法3种。
车用橡胶连接软管类别和特点汽车上的橡胶连接软管大致可以分为低压软管、耐高压软管和耐油软管三大类。
软管的构造虽然各不一样,但大致都由内胶层、增强层和外胶层等三个根本局部组成。
内胶层是软管接触介质的工作层,起着密封介质、保护增强层的作用。
增强层是软管承受压力的局部,同时还给整个软管以必要的刚度和强度。
外胶层是软管的保护层。
1.低压软管有散热器连接软管、制动放气软管。
对低压软管的机械性能要求不高。
2.耐高压软管有制动系统、液压系统连接软管。
耐高压软管的增强层采用编织胶管和缠绕胶管,要求耐高压软管的耐压、耐油、耐挠曲性好,在低温下无裂纹,耐振动,膨胀性小。
内胶层必须均匀、外表平整,不得有气孔;增强层应紧紧缚住内胶层;外胶层同样要紧贴增强层,使之不受损伤。
两端的金属接头螺纹应紧紧地嵌在胶面中。
3.耐油软管有汽油、柴油、润滑油软管。
耐油软管有良好的耐油性,且在工作压力下能持久使用。
车用主要胶管的功用与使用要求1.散热器胶管汽车散热器胶管是连接汽车发动机与散热器之间的柔性管路,是汽车关键部位中的关键部件之一。
随着汽车工业的飞速开展,尤其汽车向节能和低污染方向开展,近年来发动机舱温度提升了15~50℃,整车性能的不断提高,对汽车使用的橡胶软管提出了更高的技术要求,胶管必须经受发动机周围的高温考验,适应野外极高温和极低温的条件使用,市场需求量也相应不断扩大。
因此原来采用硫磺硫化体系生产的散热器胶管逐渐被用过氧化氢体系生产产品所替代,主要采用的材料为三元乙丙橡胶。
硫化体系对氢化丁腈橡胶/氯丁橡胶并用胶性能的影响

HNB R, 牌号 Z e p t o l 2 0 1 0 L, 日本 瑞翁公 司产
品; C R, 牌号 1 2 1 , 重 庆 长寿 化 工 有 限 责任 公 司 产 品; 氧化锌 和硬脂酸 , 上 海 京 华 化 工 有 限公 司 产 品; 硫 化剂 D C P、 助 交联 剂 TAI C, 荷 兰 阿克 苏诺
第 2期
王滕滕等. 硫 化体 系 对 氢 化 丁 腈 橡 胶 / 氯 丁橡 胶并 用胶 性 能 的 影 响
8 5
硫 化 体 系对 氢 化 丁腈 橡 胶 / 氯 丁橡 胶 并 用胶 性 能 的影 响
王滕滕 , 周 丽玲 ¨ , 钟 国伦 孙
( 1 . 青 岛科 技 大 学 橡 塑 材 料 与 工 程 教 育 部 重点 实 验 室 , 山 东 青 岛 2 6 6 0 4 2 ; 2 . 浙江大学 宁波理工 学院 , 浙 江 宁 波
贝 尔公 司产 品 。
1 . 2 试 验 配 方
低 于 HNB R, 因此将 HN B R与 C R并 用具有 一定 的 理 论 与 实 际 意 义 。 M. R u d i g e r等 研 究 过
试验 配 方如表 1 所示。
表 1 并 用胶 的试 验 配 方 份
HNB R / C R的并 用 , 并 申请 了 专 利 。但 国 内对
伸 长率 较 大 , 拉断永久变形较小 , 耐热老化性能较好 ; 当硫化剂 D C P用 量 为 5份 、 助硫 化 剂 TAI C用 量 为 3份 时 , 并 用
胶 的硫 化 速 率 较 大 , 加工安全性 、 耐油性能 、 综 合 物 理 性 能 和 耐 热 老 化性 能 较好 。 关键 词 : 氢化丁腈橡胶 ; 氯丁橡胶 ; 并用 ; 硫化体系 ; 耐热老化性能; 耐 油性 能
氯化丁基橡胶和氯丁橡胶的并用研究

善 C R 的耐臭 氧老化 性 能 。这 两种 橡胶 的 并用具
有现 实 意义 和 可行 性 ,本文 主 要探 讨 并用 比例 、 硫化 体系 、炭 黑 品种及用 量 等 因素 对 C I I C R 并
用胶 物 理机 械性 能 、耐 老化 性 能及 耐臭 氧 老化 性
橡 塑 资源 利 用
0 . 5 0 兆牛 半 自动压 力成 型机 ,上海 西 玛伟 力公 司
性 的氯侧 基 , 降低 了双键 电子密 度 ,使 双键 活 性
下 降,从 而使 得 氯丁 橡胶 具有 优 良的耐 候性 、 耐
热 氧 老化 性 能 、 阻燃 性和 耐 介质 性 能等 【 l 】 。氯化 丁 基橡胶 C I I R是 由丁基 橡胶 I I R通过取 代 反应 氯
耐 天候 老化 性 能非 常有 帮助 , 同时也 可大 幅度 改
产 品 ;XH S . A 邵尔 硬度 计 ,营 口新兴试 验机 械 厂 产 品 ;橡胶 流 变仪 ,江都 市道 纯试 验机 械厂 产 品 ; 电子拉 力试 验机 ,江都 精 艺试 验机 械 有 限公 司产 品;热 空气 老化 箱 、臭 氧 老化 试验 箱 ,江 都金 刚 试验 机械 厂产 品 。
化 改性 的产物 ,其 主 链结 构与 丁基 橡 胶相 同 ,使 得C I I R具有 I I R分 子主链 所 固有 的一切特 性 ,例 如 耐 热 、耐 臭氧 、滞 后损 失 大 、透 气 性低 等 [ 。
将 C R与 C I I R 并用对 于 改进 C I I R 的阻燃性 能及
硫 化 胶 物 理 机 械 性 能 相 对较 好 。
关键词 : 氯化丁基橡胶 ;氯丁橡胶 ;并用胶 ,耐 热老化性 能
性 能不 同的各种 橡 胶并 用 广泛 应用 于 制造 橡
橡胶配方(摘录)【范本模板】

橡胶配方(摘录)一、橡胶的并用.无论是什么橡胶不可能具有十全十美的性能,使用部门往往对产品提出多方面的性能要求,为了满足此目的,而采用橡胶并用的方法。
如,为提高二烯烃类橡胶耐热、耐光老化性能,可加入氯磺化聚乙烯.丁睛橡胶的耐粙性很好,但耐寒性不好,若并用10%的天然胶,便可改善它的耐寒性。
在橡胶中并用高苯乙烯、改性酚醛树脂、三聚氰胺树脂等都可改善橡胶的补强性能.合成橡胶的工艺性能一般都不够好,特别是饱和较高的合成橡胶,无论是炼胶、压延、贴合、硫化等性能都比较差,所以常加入天然橡胶或树脂。
以改善其未硫化胶的加工性能。
如,丁苯橡胶加入5—20份低压聚乙烯,可减少丁苯橡胶的收缩率。
乙丙橡胶中加入酚醛树脂可提高粘性。
加入天然胶对一般合成橡胶的工艺性能都会有所改善。
为了改进工艺加工性能,并用天然胶或树脂的比例一般都在20%以下。
有些合成橡胶性能优良,但价格昂贵,在不损害原物性的前提下,并用其它橡胶或树脂是完全可行的,如,丁睛胶中并用聚氯乙烯或丁苯胶中掺入天然橡胶,都能起到这一作用.1. 橡胶并用必须具有一定的相溶性,对橡胶来说天然、顺丁、异戊橡胶等能以任何比例均一地混合,最终达到相溶状态。
而天然胶与丁基橡胶就不能均一地混合.若硬性机械地混合,所得硫化胶的实际使用性能会显着地下降,这是因为它们的相溶性很差。
并用体系最重要的因素是相溶性,从应用的观点来看,如果混合不均,非但达不到并用的目的,反而影响工艺加工,特别是硫化。
因此,并用问题的焦点是两种橡胶能否相互混合,以及混合后达到什么样的相容程度。
固体橡胶并用时,因橡胶本身粘度很大,高分子的布朗运动不像液体那么容易,扩散速度较慢,对大分子的位移造成很大的阻力,严重影响橡胶间的互容作用。
为此在工业生产中都采用机械力强化分子运动,用提高温度和加入软化剂的方法来降低粘度,以促进两种橡胶的混合,所以产物从宏观上来看虽没有相分离,但真正达到溶解状态也不是很多的,其原因包括下来有以下几点,橡胶的极性、内聚能密度、橡胶的结晶、橡胶的分子量等。
丁苯橡胶与氯化丁基橡胶共硫化方法

丁苯橡胶与氯化丁基橡胶共硫化方法的报告,800字
丁苯橡胶和氯化丁基橡胶共硫化技术是橡胶行业中重要的一项技术,具有重要的经济价值和社会效益。
本文将阐述丁苯橡胶和氯化丁基橡胶的共硫化方法,以及它们的优缺点。
丁苯橡胶和氯化丁基橡胶的共硫化技术主要有四种,即干热反应、湿热反应、湿冷反应和静电热反应。
干热反应的共硫方式是将丁苯橡胶和氯化丁基橡胶按特定比例混合,然后在低温情况下加热,使其充分混合和熔融,形成共硫物。
湿热反应是将丁苯橡胶和氯化丁基橡胶等份混合,再加入硫酸铵催化剂,以低温加热至90-95℃,形成丁苯橡胶和氯化丁基橡胶的共硫物。
湿冷反应的方法是将丁苯橡胶和氯化丁基橡胶等份混合,然后加入催化剂硫酸铵,用冷却水冷却,使共硫化反应完成。
静电热反应也是将丁苯橡胶和氯化丁基橡胶等份混合,然后经微波辐射处理,在低温低压条件下加热,使反应完成。
这些共硫化技术都有自己优点和缺点。
干热反应和湿热反应是反应速度快、混合均匀,反应温度低、热处理时间短,操作简单、成本低廉、节能环保的优点,但反应的活性低,热处理的条件苛刻,抗老化性能差;湿冷反应和静电热反应的反应活性高,反应条件宽松,抗老化性能好,可以满足高性能橡胶材料的要求,但反应时间较长,技术成本较高。
因此,丁苯橡胶和氯化丁基橡胶的共硫技术有不同的选择,在实际应用中应充分考虑反应的条件、反应的活性、抗老化性能和技术成本等因素,采用最合适的技术,从而开发出具有高性能和高经济价值的橡胶产品。
丁基橡胶的改性

丁基橡胶的改性普通丁基橡胶的硫化速度慢,与高不饱和橡胶的相容性差,自粘性和共粘都不好,因此人们致力于普通丁基橡胶的改性。
60年代初,美国ESSO公司开发成功氯化丁基橡胶。
随后,加拿大Polysar公司于七十年代开发出溴化丁基橡胶。
上述问题得到比较满意的解决,从而扩大了丁基橡胶的应用范围。
一、氯化丁基橡胶(一)制备方法氯化丁基橡胶(Chlorinated isobutene-isoprene rubber缩写为CIIR)的制备方法分干胶混炼氯化和溶液氯化两种方法。
1.干胶混炼氯化法在开炼机上将氯载体或氯化剂混入丁基橡胶中,氯载体在加热下放出氯气与丁基橡胶发生氯化反应,生成氯化丁基橡胶。
工业上常用的氯载体是活性炭。
活性炭吸氯量一般为2.0~ 2.5mg·mol/g 时,活性炭用量为4~ 5份。
当活性炭含氯量较高时,可以相应地减少其用量,而胶料的物理机械性能可相应提高(见表8-27)。
表8-27 活性炭吸附氯量对丁基橡胶物理机械性能的影响注:配方为丁基橡胶 100, 高耐磨炉黑 55, 凡士林油 5, 硬脂酸 1, 吸氯活性炭 5, 树脂 8, 氯化亚锡 2。
随着丁基橡胶溶液连续氯化法的工业化,干胶混炼法已很少使用。
2.溶液氯化法溶液氯化法生产氯化丁基橡胶是先将丁基橡胶溶于四氯化碳、氯仿或己烷等溶剂中,然后在常温下通入氯气进行氯化,即制得氯化丁基橡胶。
由于氯的负电性比溴大得多,氯化反应过程进行太快,所以反应溶液中要添加抑制剂以控制反应速度,并将结合氯含量控制在1%左右。
丁基橡胶的氯化反应主要是发生取代作用,因此保存了橡胶中的异戊二烯双键,在大分子中仍具有不饱和性,同时,丁基橡胶中接上了氯原子,加速了硫化作用。
氯化丁基橡胶中;烯丙基位置上的氯是非常活泼的。
氯化丁基橡胶的化学结构式如下:氯化丁基橡胶的质量指标为:氯含量1.1~1.3%灰分 0.5%挥发分<0.7% 硬脂酸钙<0.5%水分<0.3% 防老剂 0.1~0.2%(二)品种氯化丁基橡胶根据其门尼粘度的差别,分为三个级别,见表8-28。
天然橡胶与氯丁橡胶的并用
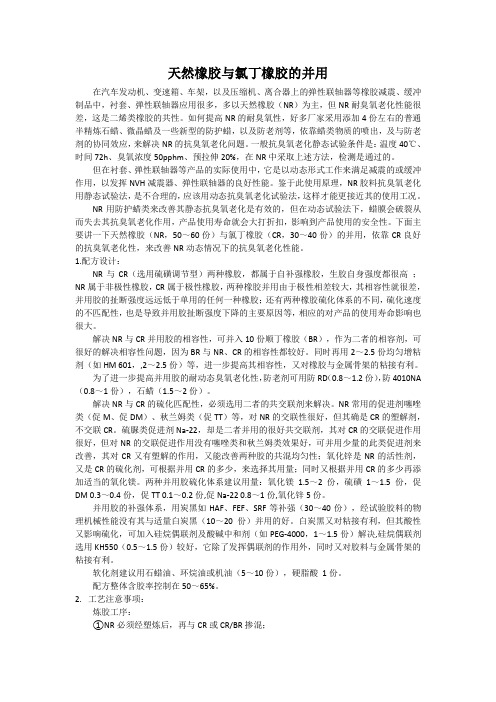
天然橡胶与氯丁橡胶的并用在汽车发动机、变速箱、车架,以及压缩机、离合器上的弹性联轴器等橡胶减震、缓冲制品中,衬套、弹性联轴器应用很多,多以天然橡胶(NR)为主,但NR耐臭氧老化性能很差,这是二烯类橡胶的共性。
如何提高NR的耐臭氧性,好多厂家采用添加4份左右的普通半精炼石蜡、微晶蜡及一些新型的防护蜡,以及防老剂等,依靠蜡类物质的喷出,及与防老剂的协同效应,来解决NR的抗臭氧老化问题。
一般抗臭氧老化静态试验条件是:温度40℃、时间72h、臭氧浓度50pphm、预拉伸20%,在NR中采取上述方法,检测是通过的。
但在衬套、弹性联轴器等产品的实际使用中,它是以动态形式工作来满足减震的或缓冲作用,以发挥NVH减震器、弹性联轴器的良好性能。
鉴于此使用原理,NR胶料抗臭氧老化用静态试验法,是不合理的,应该用动态抗臭氧老化试验法,这样才能更接近其的使用工况。
NR用防护蜡类来改善其静态抗臭氧老化是有效的,但在动态试验法下,蜡膜会破裂从而失去其抗臭氧老化作用,产品使用寿命就会大打折扣,影响到产品使用的安全性。
下面主要讲一下天然橡胶(NR,50~60份)与氯丁橡胶(CR,30~40份)的并用,依靠CR良好的抗臭氧老化性,来改善NR动态情况下的抗臭氧老化性能。
1.配方设计:NR与CR(选用硫磺调节型)两种橡胶,都属于自补强橡胶,生胶自身强度都很高;NR属于非极性橡胶,CR属于极性橡胶,两种橡胶并用由于极性相差较大,其相容性就很差,并用胶的扯断强度远远低于单用的任何一种橡胶;还有两种橡胶硫化体系的不同,硫化速度的不匹配性,也是导致并用胶扯断强度下降的主要原因等,相应的对产品的使用寿命影响也很大。
解决NR与CR并用胶的相容性,可并入10份顺丁橡胶(BR),作为二者的相容剂,可很好的解决相容性问题,因为BR与NR、CR的相容性都较好。
同时再用2~2.5份均匀增粘剂(如HM 601,,2~2.5份)等,进一步提高其相容性,又对橡胶与金属骨架的粘接有利。
丁基橡胶

丁基橡胶功能化品种丁基橡胶(IIR)是第1个高饱和的橡胶品种,少量的异戊二烯的引入是为了获得可供硫化的双键。
由于结构上的特点,丁基橡胶有良好的气密性和耐老化性。
但也限制了其与聚二烯烃橡胶的并用,此外,分子中缺少极性基团,也使其与金属或橡胶的粘合性能差,随着合成橡胶工业发展和应用的需要,IIR现已开发成拥有衍生橡胶、改性橡胶、热塑性弹性体和热塑性硫化胶等品种的通用橡胶。
1 氯化丁基橡胶氯化丁基橡胶(CIIR)的制备方法分干胶混炼氯化和溶液氯化两种方法。
前一法是在开炼机上把吸附了氯气的活性炭或其它氯化剂混入丁基橡胶中经加热和混炼后制得;后一法是先把其橡胶溶于四氯化碳、氯仿或己烷等溶剂中,然后在常温下通过氯气进行氯化,即制得氯化丁基橡胶,由于该法已实现连续氯化工艺生产,故已成为主要的制造方法。
极性氯原子的引入,可克服丁基橡胶硫化速度慢、粘合性能差,与高不饱和橡胶难于共硫化等的问题。
该胶能以单用或并用方式制造无内胎轮胎的气密层、浅色或白色胎侧、内胎、胶带、胶管、密封、绝缘或粘合等用胶料。
2 溴化丁基橡胶溴化丁基橡胶(BIIR)的制备方法分干混炼法和溶液法等两种方法。
按前一法可分别把N-溴代琥珀酰亚胺10%,二溴二甲基乙内酰脲7.5%或活性炭吸附溴(31.2%重量比)30%加入到在开炼机上的丁基橡胶中进行热混炼而制得;而后一法是将丁基橡胶溶解于氯化烃溶剂,再通入约3%的溴而制取的,该溴化过程是连续的,其产品质量均匀且稳定。
溴化丁基胶与上述氯化丁基胶比,有更多的活性硫化点,硫化速度快,与不饱和型橡胶能更好粘合,有更高的耐老化、较低的焦烧安全性。
主要可用作轮胎的气密层、胎侧、内胎、容器衬里、药品瓶塞和胶垫等。
3.磺化丁基橡胶磺化丁基橡胶(SIIR)是丁基橡胶经磺化后所得的产品,作为磺化剂可用二氧化硫或其它磺化物。
该橡胶由于也含极性基团,故也能得到用氯化或溴化的改性效果,因而也宜于作聚合物改性剂和胶粘剂等。
4.马来酸酐改性丁基橡胶马来酸酐改性丁基橡胶(MIIR)是在丁基橡胶上接枝马来酸酐的橡胶。
氯化丁基专用硫化剂ASH
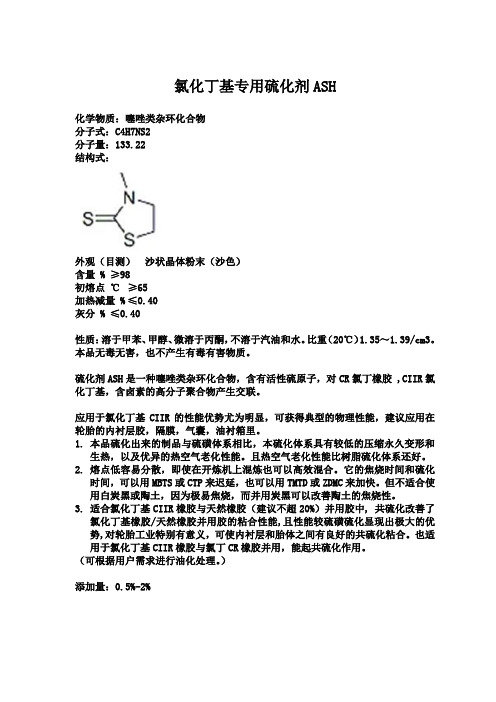
氯化丁基专用硫化剂ASH
化学物质:噻唑类杂环化合物
分子式:C4H7NS2
分子量:133.22
结构式:
外观(目测)沙状晶体粉末(沙色)
含量 % ≥98
初熔点℃≥65
加热减量 % ≤0.40
灰分 % ≤0.40
性质:溶于甲苯、甲醇、微溶于丙酮,不溶于汽油和水。
比重(20℃)1.35~1.39/cm3。
本品无毒无害,也不产生有毒有害物质。
硫化剂ASH是一种噻唑类杂环化合物,含有活性硫原子,对CR氯丁橡胶 ,CIIR氯化丁基,含卤素的高分子聚合物产生交联。
应用于氯化丁基CIIR的性能优势尤为明显,可获得典型的物理性能,建议应用在轮胎的内衬层胶,隔膜,气囊,油衬箱里。
1.本品硫化出来的制品与硫磺体系相比,本硫化体系具有较低的压缩永久变形和
生热,以及优异的热空气老化性能。
且热空气老化性能比树脂硫化体系还好。
2.熔点低容易分散,即使在开炼机上混炼也可以高效混合。
它的焦烧时间和硫化
时间,可以用MBTS或CTP来迟延,也可以用TMTD或ZDMC来加快。
但不适合使用白炭黑或陶土,因为极易焦烧,而并用炭黑可以改善陶土的焦烧性。
3.适合氯化丁基CIIR橡胶与天然橡胶(建议不超20%)并用胶中, 共硫化改善了
氯化丁基橡胶/天然橡胶并用胶的粘合性能,且性能较硫磺硫化显现出极大的优势,对轮胎工业特别有意义,可使内衬层和胎体之间有良好的共硫化粘合。
也适用于氯化丁基CIIR橡胶与氯丁CR橡胶并用,能起共硫化作用。
(可根据用户需求进行油化处理。
)
添加量:0.5%-2%。