铰刀直径公差
直柄机用铰刀
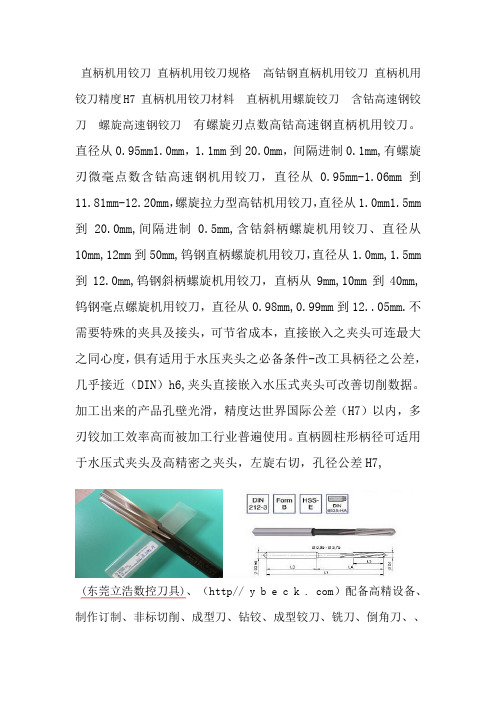
直柄机用铰刀直柄机用铰刀规格高钴钢直柄机用铰刀直柄机用铰刀精度H7 直柄机用铰刀材料直柄机用螺旋铰刀含钴高速钢铰刀螺旋高速钢铰刀有螺旋刃点数高钴高速钢直柄机用铰刀。
直径从0.95mm1.0mm,1.1mm到20.0mm,间隔进制0.1mm,有螺旋刃微毫点数含钴高速钢机用铰刀,直径从0.95mm-1.06mm到11.81mm-12.20mm,螺旋拉力型高钴机用铰刀,直径从1.0mm1.5mm 到20.0mm,间隔进制0.5mm,含钴斜柄螺旋机用铰刀、直径从10mm,12mm到50mm,钨钢直柄螺旋机用铰刀,直径从1.0mm,1.5mm 到12.0mm,钨钢斜柄螺旋机用铰刀,直柄从9mm,10mm到40mm,钨钢毫点螺旋机用铰刀,直径从0.98mm,0.99mm到12..05mm.不需要特殊的夹具及接头,可节省成本,直接嵌入之夹头可连最大之同心度,俱有适用于水压夹头之必备条件-改工具柄径之公差,几乎接近(DIN)h6,夹头直接嵌入水压式夹头可改善切削数据。
加工出来的产品孔壁光滑,精度达世界国际公差(H7)以内,多刃铰加工效率高而被加工行业普遍使用。
直柄圆柱形柄径可适用于水压式夹头及高精密之夹头,左旋右切,孔径公差H7,(东莞立浩数控刀具)、(http// y b e c k . com)配备高精设备、制作订制、非标切削、成型刀、钻铰、成型铰刀、铣刀、倒角刀、、等等、技术的支持、和询问、顾问、产品广泛用于航空制造业、模具制造业、眼镜制造业、汽车零部件制造业、手机零部件制造业、钟表制造业、电子产品制造业、金属和非金属、家具家私制造业、切削、加工、等等领域。
(东莞立浩数控刀具)、还将在技术资讯技术服务、加上我们完善销售团队和销后服务、相信我们能成您最理想的合作伙伴。
欢迎同行业和制造业的朋友们前来、咨询、磋商、洽谈、技术商讨、技术交流。
美标铰刀尺寸公差标准

美标铰刀尺寸公差标准全文共四篇示例,供读者参考第一篇示例:美标铰刀尺寸公差标准是指美国标准化协会制定的用于衡量铰刀尺寸的规范,旨在确保产品质量和尺寸精度符合国际标准。
铰刀是一种常用的切削工具,用于在工件上加工凹凸面或倒角。
铰刀的质量和精度对加工质量和效率有着重要影响,因此必须严格遵守相关的尺寸公差标准。
根据美标铰刀尺寸公差标准,铰刀的尺寸应该符合特定的公差范围,以确保铰刀的几何形状和尺寸精度满足加工要求。
铰刀的尺寸公差包括直径、长度、刃尖半径、切铣角度等多个方面的要求。
直径公差是指铰刀的直径与理论标准直径之间的允许差值范围,长度公差是指铰刀的长度与理论标准长度之间的误差范围。
刃尖半径公差是指刃尖半径与标准值之间的允许差值范围,切铣角度公差是指铰刀的切削角度与标准值之间的误差范围。
在生产过程中,制造商必须严格按照美标铰刀尺寸公差标准进行生产和质量控制,以确保铰刀的尺寸精度和几何形状满足客户的需求。
一旦铰刀的尺寸超出公差范围,可能导致工件加工精度下降,甚至影响产品质量和使用效果。
铰刀制造商必须严格控制生产工艺和质量检测,以确保产品质量。
除了尺寸公差标准外,美标铰刀还对铰刀材料、硬度、涂层、表面粗糙度等方面进行了规定。
铰刀材料应选用高品质的合金钢或硬质合金材料,以保证铰刀的强度和耐磨性。
铰刀的表面硬度应符合标准要求,以确保刀具在使用过程中不易磨损和变形。
铰刀的涂层应具有较好的耐磨性和切削性能,以延长铰刀的使用寿命。
美标铰刀尺寸公差标准是保证铰刀质量和精度的重要依据,制造商必须严格遵守相关规范进行生产和质量控制,以确保铰刀的质量和尺寸精度符合国际标准。
只有这样,才能满足客户的需求,提高产品质量,推动行业的发展和进步。
第二篇示例:美标铰刀尺寸公差标准是指美国标准协会(ANSI)制定的关于铰刀尺寸公差的规范,旨在确保铰刀的尺寸精度和质量,以提高产品的可靠性和稳定性。
铰刀是一种用于连接两个或多个部件并允许它们相对旋转的机械零件,广泛应用于各种工业领域,如机械制造、汽车制造、航空航天等。
机械加工如何选用铰刀
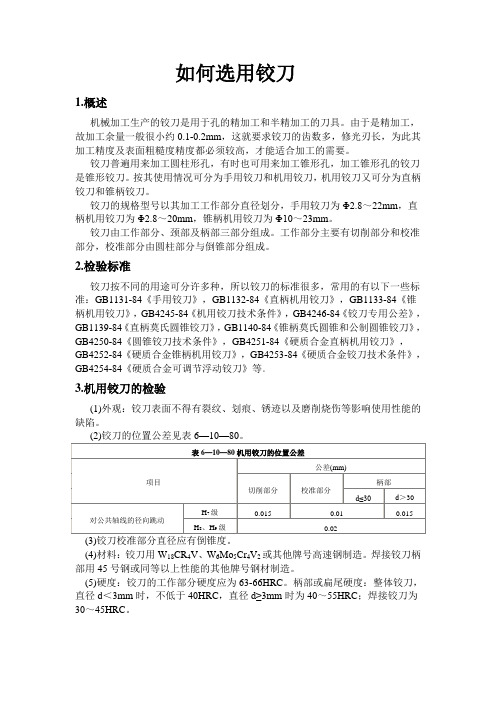
如何选用铰刀1.概述机械加工生产的铰刀是用于孔的精加工和半精加工的刀具。
由于是精加工,故加工余量一般很小约0.1-0.2mm,这就要求铰刀的齿数多,修光刃长,为此其加工精度及表面粗糙度精度都必须较高,才能适合加工的需要。
铰刀普遍用来加工圆柱形孔,有时也可用来加工锥形孔,加工锥形孔的铰刀是锥形铰刀。
按其使用情况可分为手用铰刀和机用铰刀,机用铰刀又可分为直柄铰刀和锥柄铰刀。
铰刀的规格型号以其加工工作部分直径划分,手用较刀为Φ2.8~22mm,直柄机用铰刀为Φ2.8~20mm,锥柄机用铰刀为Φ10~23mm。
铰刀由工作部分、颈部及柄部三部分组成。
工作部分主要有切削部分和校准部分,校准部分由圆柱部分与倒锥部分组成。
2.检验标准铰刀按不同的用途可分许多种,所以铰刀的标准很多,常用的有以下一些标准:GB1131-84《手用铰刀》,GB1132-84《直柄机用铰刀》,GB1133-84《锥柄机用铰刀》,GB4245-84《机用铰刀技术条件》,GB4246-84《铰刀专用公差》,GB1139-84《直柄莫氏圆锥铰刀》,GB1140-84《锥柄莫氏圆锥和公制圆锥铰刀》,GB4250-84《圆锥铰刀技术条件》,GB4251-84《硬质合金直柄机用铰刀》,GB4252-84《硬质合金锥柄机用铰刀》,GB4253-84《硬质合金铰刀技术条件》,GB4254-84《硬质合金可调节浮动铰刀》等。
3.机用铰刀的检验(1)外观:铰刀表面不得有裂纹、划痕、锈迹以及磨削烧伤等影响使用性能的缺陷。
(3)铰刀校准部分直径应有倒锥度。
(4)材料:铰刀用W18CR4V、W6Mo5Cr4V2或其他牌号高速钢制造。
焊接铰刀柄部用45号钢或同等以上性能的其他牌号钢材制造。
(5)硬度:铰刀的工作部分硬度应为63-66HRC。
柄部或扁尾硬度:整体铰刀,直径d<3mm时,不低于40HRC,直径d≥3mm时为40~55HRC;焊接铰刀为30~45HRC。
铰刀
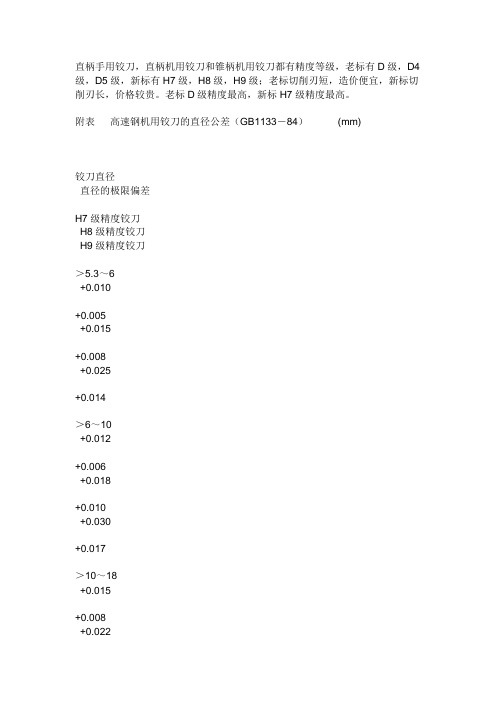
直柄手用铰刀,直柄机用铰刀和锥柄机用铰刀都有精度等级,老标有D级,D4级,D5级,新标有H7级,H8级,H9级;老标切削刃短,造价便宜,新标切削刃长,价格较贵。
老标D级精度最高,新标H7级精度最高。
附表高速钢机用铰刀的直径公差(GB1133-84)(mm)铰刀直径直径的极限偏差H7级精度铰刀H8级精度铰刀H9级精度铰刀>5.3~6+0.010+0.005+0.015+0.008+0.025+0.014>6~10+0.012+0.006+0.018+0.010+0.030+0.017>10~18+0.015+0.008+0.022+0.012+0.036+0.020>18~30 +0.017+0.009+0.028+0.016+0.044+0.025>30~50 +0.021+0.012+0.033+0.019+0.052+0.030>50~80 +0.025+0.014+0.039+0.022+0.062+0.036>80~100 +0.029+0.045+0.026+0.073+0.042硬质合金机用铰刀的直径公差(mm)铰刀直径直径的极限偏差H7级精度铰刀H8级精度铰刀H9级精度铰刀>5.3~6+0.012+0.007+0.018+0.001+0.030+0.019>6~10+0.015+0.009+0.022+0.014+0.036+0.023>10~18+0.011+0.027+0.017+0.043+0.027>18~30+0.021+0.013+0.033+0.021+0.052+0.033>30~40+0.025+0.016+0.039+0.025+0.062+0.040尊敬的杨增武先生,您好!以下是您的招商银行信用卡电子账单,如有任何疑问,请致电24小时客服热线400-820-5555,我们将竭诚为您服务!登录网上银行,更可立即查询12期以内的账单和未出账信息。
点击这里打开招商银行信用卡网站点击右上角“信用卡网上营业厅”即可登录。
硬质合金铰刀制造公差值的设计
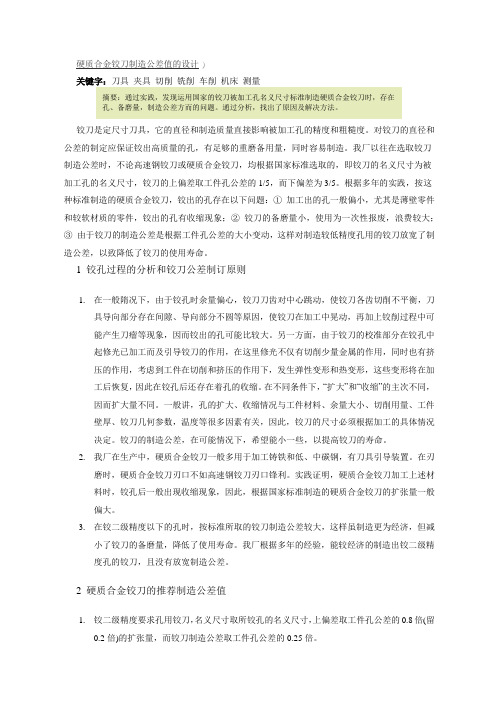
硬质合金铰刀制造公差值的设计)关键字:刀具夹具切削铣削车削机床测量摘要:通过实践,发现运用国家的铰刀被加工孔名义尺寸标准制造硬质合金铰刀时,存在孔、备磨量,制造公差方而的问题。
通过分析,找出了原因及解决方法。
铰刀是定尺寸刀具,它的直径和制造质量直接影响被加工孔的精度和粗糙度。
对铰刀的直径和公差的制定应保证铰出高质量的孔,有足够的重磨备用量,同时容易制造。
我厂以往在选取铰刀制造公差时,不论高速钢铰刀或硬质合金铰刀,均根据国家标准选取的,即铰刀的名义尺寸为被加工孔的名义尺寸,铰刀的上偏差取工件孔公差的1/5,而下偏差为3/5。
根据多年的实践,按这种标准制造的硬质合金铰刀,铰出的孔存在以下问题:①加工出的孔一般偏小,尤其是薄壁零件和较软材质的零件,铰出的孔有收缩现象;②铰刀的备磨量小,使用为一次性报废,浪费较大;③由于铰刀的制造公差是根据工件孔公差的大小变动,这样对制造较低精度孔用的铰刀放宽了制造公差,以致降低了铰刀的使用寿命。
1 铰孔过程的分析和铰刀公差制订原则1.在一般隋况下,由于铰孔时余量偏心,铰刀刀齿对中心跳动,使铰刀各齿切削不平衡,刀具导向部分存在间隙、导向部分不圆等原因,使铰刀在加工中晃动,再加上铰削过程中可能产生刀瘤等现象,因而铰出的孔可能比较大。
另一方面,由于铰刀的校准部分在铰孔中起修光已加工而及引导铰刀的作用,在这里修光不仅有切削少量金属的作用,同时也有挤压的作用,考虑到工件在切削和挤压的作用下,发生弹性变形和热变形,这些变形将在加工后恢复,因此在铰孔后还存在着孔的收缩。
在不同条件下,“扩大”和“收缩”的主次不同,因而扩大量不同。
一般讲,孔的扩大、收缩情况与工件材料、余量大小、切削用量、工件壁厚、铰刀几何参数,温度等很多因素有关,因此,铰刀的尺寸必须根据加工的具体情况决定。
铰刀的制造公差,在可能情况下,希望能小一些,以提高铰刀的寿命。
2.我厂在生产中,硬质合金铰刀一般多用于加工铸铁和低、中碳钢,有刀具引导装置。
[刀具制造技术资料]铰刀知识介绍以及铰刀的刃磨和检验
![[刀具制造技术资料]铰刀知识介绍以及铰刀的刃磨和检验](https://img.taocdn.com/s3/m/95510c64178884868762caaedd3383c4bb4cb437.png)
[刀具制造技术资料]铰刀知识介绍以及铰刀的刃磨和检验铰刀具有一个或多个刀齿、用以切除已加工孔表面薄层金属的旋转刀具,具有直刃或螺旋刃的旋转精加工刀具,用于扩孔或修孔。
铰刀(卷名:机械工程)具有一个或多个刀齿、用以切除已加工孔表面薄层金属的旋转刀具。
[reamer]∶具有直刃或螺旋刃的旋转精加工刀具,用于扩孔或修孔,因切削量少其加工精度要求通常高于钻头. 可以手动操作或安装在钻床上工作.主要用途铰刀具有一个或者多个刀齿,用以切除孔已加工表面薄金属层的旋转刀具。
经过绞刀加工后的孔可以获得精确的尺寸和形状。
铰刀用于铰削工件上已钻削(或扩孔)加工后的孔,主要是为了提高孔的加工精度,降低其表面的粗糙度,是用于孔的精加工和半精加工的刀具,加工余量一般很小。
用来加工圆柱形孔的铰刀比较常用。
用来加工锥形孔的铰刀是锥形铰刀,比较少用。
按使用情况来看有手用铰刀和机用铰刀,机用铰刀又可分为直柄铰刀和锥柄铰刀。
手用的则是直柄型的。
铰刀种类铰刀结构大部分由工作部分及柄部组成。
工作部分主要起切削和校准功能,校准处直径有倒锥度。
而柄部则用于被夹具夹持,有直柄和锥柄之分。
按不同的用途铰刀可分许多种,因此关于铰刀的标准也比较多,我们较常用的一些标准有GB/T1131手用铰刀,GB/T1132直柄机用铰刀,GB/T1139直柄莫氏圆锥铰刀等等。
铰刀按使用方式分为手用铰刀和机用铰刀;按铰孔形状分为圆柱铰刀和圆锥铰刀,(标准锥铰刀有1:50锥度销子铰刀和莫氏锥度铰刀两种类型).铰刀的容屑槽方向,有直槽和螺旋槽.常用的材质为高速钢.硬质合金镶片.手用铰刀一般材质为合金工具钢(9SiCr),机用铰刀材料为高速钢(HSS),机用铰刀分为直柄机用铰刀和锥柄机用铰刀铰刀精度有D4,H7,H8,H9等精度等级。
按铰孔的形状分圆柱形、圆锥形和阶梯形3种;安装夹方法分带柄式和套装式两种;按齿槽的形状分直槽和螺旋槽两种;一.手工铰孔一般注意事项:1.工件要夹正.2.铰削过程中,两手用力要平衡.3.铰刀退出时,不能反转,因铰刀有后角,铰刀反转会使切屑塞在铰刀刀齿后面和孔壁之间,将孔壁划伤;同时,铰刀易磨损.4.铰刀使用完毕,要清擦干净,涂上机油,装盒以免碰伤刃口.二.机铰时注意铰削速度和走刀量(查金属切削手册)三.铰削中,必须采用合理的冷却润滑液.手用的导锥锥度较小,前角、后角较小,刃口较锋利,一般刃带较窄,或导锥处干脆没有。
确定铰刀直径公差

确定铰刀直径公差
假设被加工零件孔的上偏差和下偏差分别为ES和EI,而铰刀直径的上偏差和下偏差分别为es和ei。
则:
es=2/3 (ES-EI)+EI ei=es-1/4(ES-EI)
例如:我们要铰10H9(0+0、036)的孔,饺刀的上偏差依据上述公式应为:
es=2 (0、036-0)+0=0、024 铰刀的下偏差据上述公式应为:ei=0、024-1 (0、036-0)=0、015 则:铰10H9(0+0、036)孔的铰刀尺寸及公差带为10+0、015+0、024。
查资料,10H9铰刀尺寸公差为10+0、013+0、023与计算得出公差相差甚微,可以满足使用要求。
该方法可为按被加工孔的尺寸精度来设计或研磨铰刀提供参考。
但铰孔时还受机床主轴径向跳动、铰刀的安装偏差、铰刀各刀齿的径向跳动、冷却液、切削用量等因素的影响,使铰出孔的直径往往会扩大或收缩.因此,为满足工艺要求,一般要先试铰,根据试铰情况来修正计算出的公差带,再刃磨铰刀,投入使用。
第 1 页共 1 页。
铰刀设计原则及铰孔失效模式分析
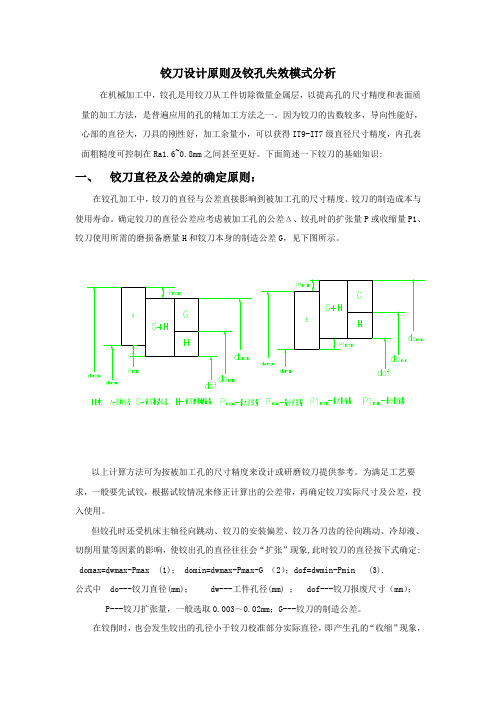
铰刀设计原则及铰孔失效模式分析在机械加工中,铰孔是用铰刀从工件切除微量金属层,以提高孔的尺寸精度和表面质量的加工方法,是普遍应用的孔的精加工方法之一。
因为铰刀的齿数较多,导向性能好,心部的直径大,刀具的刚性好,加工余量小,可以获得IT9-IT7级直径尺寸精度,内孔表面粗糙度可控制在Ra1.6~0.8mm之间甚至更好。
下面简述一下铰刀的基础知识:一、铰刀直径及公差的确定原则:在铰孔加工中,铰刀的直径与公差直接影响到被加工孔的尺寸精度、铰刀的制造成本与使用寿命。
确定铰刀的直径公差应考虑被加工孔的公差Δ、铰孔时的扩张量P或收缩量P1、铰刀使用所需的磨损备磨量H和铰刀本身的制造公差G,见下图所示。
以上计算方法可为按被加工孔的尺寸精度来设计或研磨铰刀提供参考。
为满足工艺要求,一般要先试铰,根据试铰情况来修正计算出的公差带,再确定铰刀实际尺寸及公差,投入使用。
但铰孔时还受机床主轴径向跳动、铰刀的安装偏差、铰刀各刀齿的径向跳动、冷却液、切削用量等因素的影响,使铰出孔的直径往往会“扩张”现象,此时铰刀的直径按下式确定: domax=dwmax-Pmax (1); domin=dwmax-Pmax-G (2);dof=dwmin-Pmin (3).公式中 do---铰刀直径(mm); dw---工件孔径(mm) ; dof---铰刀报废尺寸(mm); P---铰刀扩张量,一般选取0.003~0.02mm;G---铰刀的制造公差。
在铰削时,也会发生铰出的孔径小于铰刀校准部分实际直径,即产生孔的“收缩”现象,例如用很小的切削锥的铰刀加工薄壁的韧性材料或用硬质合金铰刀高速铰孔时,铰后孔因弹性恢复而缩小。
此时铰刀直径应按下式确定:domax=dwmax+P1min (4); domin=dwmax-G (5);dof=dwmin+P1max (6).公式中P1---孔径收缩量,一般选取0.005~0.02mm。
铰刀磨损储备量H按下式确定:铰孔后有扩张时 H=domin-dof=domin-dwmin-Pmin (7);铰孔后有收缩时 H=domin-dof=domin-dwmin-P1max (8)。
铰刀
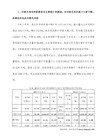
铰刀外径尺寸设计值偏小;切削速度过低;进给量过大;铰刀主偏角过小;切削液选择不合适;刃磨时铰刀磨损部分未磨掉,弹性恢复使孔径缩小;铰钢件时,余量太大或铰刀不锋利,易产生弹性恢复,使孔径缩小;内孔不圆,孔径不合格。
铰出的内孔不圆
铰刀过长,刚性不足,铰削时产生振动;铰刀主偏角过小;铰刀刃带窄;铰孔余量偏;内孔表面有缺口、交叉孔;孔表面有砂眼、气孔;主轴轴承松动,无导向套,或铰刀与导向套配合间隙过大;由于薄壁工件装夹过紧,卸下后工件变形。
孔径缩小
更换铰刀外径尺寸;适当提高切削速度;适当降低进给量;适当增大主偏角;选择润滑性能好的油性切削液;定期互换铰刀,正确刃磨铰刀切削部分;设计铰刀尺寸时,应考虑上述因素,或根据实际情况取值;作试验性切削,取合适余量,将铰刀磨锋利。
铰出的内孔不圆
刚性不足的铰刀可采用不等分齿距的铰刀,铰刀的安装应采用刚性联接,增大主偏角;选用合格铰刀,控制预加工工序的孔位置公差;采用不等齿距铰刀,采用较长、较精密的导向套;选用合格毛坯;采用等齿距铰刀铰削较精密的孔时,应对机床主轴间隙进行调整,导向套的配合间隙应要求较高;采用恰当的夹紧方法,减小夹紧力。
孔的内表面有明显的棱面
铰孔余量过大;铰刀切削部分后角过大;铰刀刃带过宽;工件表面有气孔、砂眼;主轴摆差过大。
内孔表面粗糙度值高
切削速度过高;切削液选择不合适;铰刀主偏角过大,铰刀刃口不在同一圆周上;铰孔余量太大;铰孔余量不均匀或太小,局部表面未铰到;铰刀切削部分摆差超差、刃口不锋利,表面粗糙;铰刀刃带过宽;铰孔时排屑不畅;铰刀过度磨损;铰刀碰伤,刃口留有毛刺或崩刃;刃口有积屑瘤;由于材料关系,பைடு நூலகம்适用于零度前角或负前角铰刀。
铰刀的齿数及齿槽
铰制孔公差标注
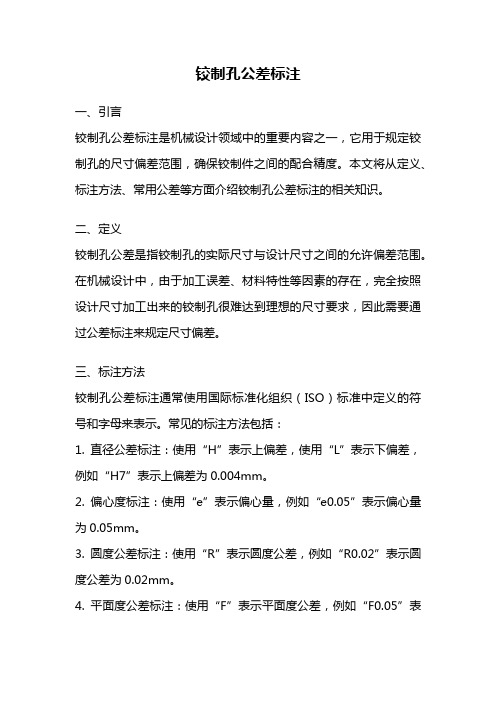
铰制孔公差标注一、引言铰制孔公差标注是机械设计领域中的重要内容之一,它用于规定铰制孔的尺寸偏差范围,确保铰制件之间的配合精度。
本文将从定义、标注方法、常用公差等方面介绍铰制孔公差标注的相关知识。
二、定义铰制孔公差是指铰制孔的实际尺寸与设计尺寸之间的允许偏差范围。
在机械设计中,由于加工误差、材料特性等因素的存在,完全按照设计尺寸加工出来的铰制孔很难达到理想的尺寸要求,因此需要通过公差标注来规定尺寸偏差。
三、标注方法铰制孔公差标注通常使用国际标准化组织(ISO)标准中定义的符号和字母来表示。
常见的标注方法包括:1. 直径公差标注:使用“H”表示上偏差,使用“L”表示下偏差,例如“H7”表示上偏差为0.004mm。
2. 偏心度标注:使用“e”表示偏心量,例如“e0.05”表示偏心量为0.05mm。
3. 圆度公差标注:使用“R”表示圆度公差,例如“R0.02”表示圆度公差为0.02mm。
4. 平面度公差标注:使用“F”表示平面度公差,例如“F0.05”表示平面度公差为0.05mm。
5. 其他特殊公差标注:根据具体要求,可以使用特殊符号和字母来表示其他类型的公差,例如“⊥”表示垂直度公差。
四、常用公差铰制孔公差的选择应根据具体的设计要求和加工工艺来确定。
以下是常用的几种公差:1. H7/g6:适用于一般要求较高的铰制孔配合,具有较好的配合精度和通用性。
2. H8/f7:适用于精度要求较高的轴孔配合,具有较高的配合紧度和传动精度。
3. H9/h9:适用于一般要求较低的铰制孔配合,具有较大的配合间隙,适用于一些需要调整的装配情况。
4. H11/p11:适用于较大尺寸的铰制孔配合,具有较大的配合间隙,适用于一些需要调整和安装的情况。
五、注意事项在进行铰制孔公差标注时,需要注意以下几点:1. 标注应明确、准确,避免歧义和误解。
2. 公差选择应符合实际需求和加工工艺的要求。
3. 标注应尽量简洁明了,避免过多的冗余信息。
铰刀的合适使用
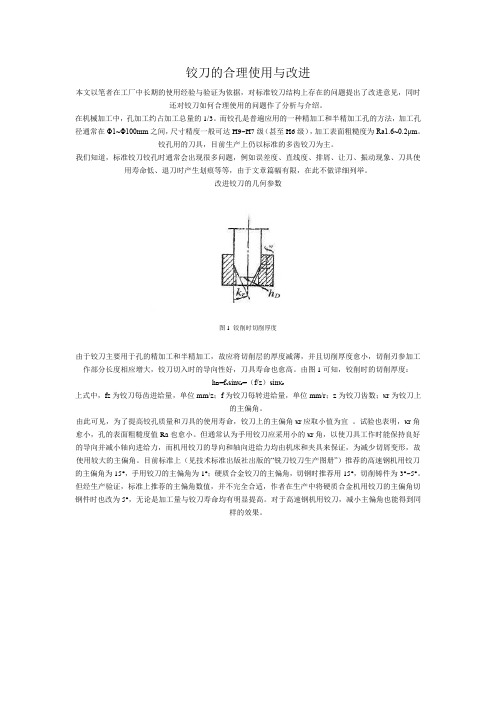
铰刀的合理使用与改进本文以笔者在工厂中长期的使用经验与验证为依据,对标准铰刀结构上存在的问题提出了改进意见,同时还对铰刀如何合理使用的问题作了分析与介绍。
在机械加工中,孔加工约占加工总量的1/3。
而铰孔是普遍应用的一种精加工和半精加工孔的方法,加工孔径通常在Φ1~Φ100mm之间,尺寸精度一般可达H9~H7级(甚至H6级),加工表面粗糙度为Ra1.6~0.2μm。
铰孔用的刀具,目前生产上仍以标准的多齿铰刀为主。
我们知道,标准铰刀铰孔时通常会出现很多问题,例如误差度、直线度、排屑、让刀、振动现象、刀具使用寿命低、退刀时产生划痕等等,由于文章篇幅有限,在此不做详细列举。
改进铰刀的几何参数图1 铰削时切削厚度由于铰刀主要用于孔的精加工和半精加工,故应将切削层的厚度减薄,并且切削厚度愈小,切削刃参加工作部分长度相应增大,铰刀切入时的导向性好,刀具寿命也愈高。
由图1可知,铰削时的切削厚度:h D=f z sinκr=(f/z)sinκr上式中,fz为铰刀每齿进给量,单位mm/z;f为铰刀每转进给量,单位mm/r;z为铰刀齿数;κr为铰刀上的主偏角。
由此可见,为了提高铰孔质量和刀具的使用寿命,铰刀上的主偏角κr应取小值为宜。
试验也表明,κr角愈小,孔的表面粗糙度值Ra也愈小。
但通常认为手用铰刀应采用小的κr角,以使刀具工作时能保持良好的导向并减小轴向进给力,而机用铰刀的导向和轴向进给力均由机床和夹具来保证,为减少切屑变形,故使用较大的主偏角。
目前标准上(见技术标准出版社出版的“铣刀铰刀生产图册”)推荐的高速钢机用铰刀的主偏角为15°,手用铰刀的主偏角为1°;硬质合金铰刀的主偏角,切钢时推荐用15°,切削铸件为3°~5°。
但经生产验证,标准上推荐的主偏角数值,并不完全合适,作者在生产中将硬质合金机用铰刀的主偏角切钢件时也改为5°,无论是加工量与铰刀寿命均有明显提高。
铰刀标准直径规格表
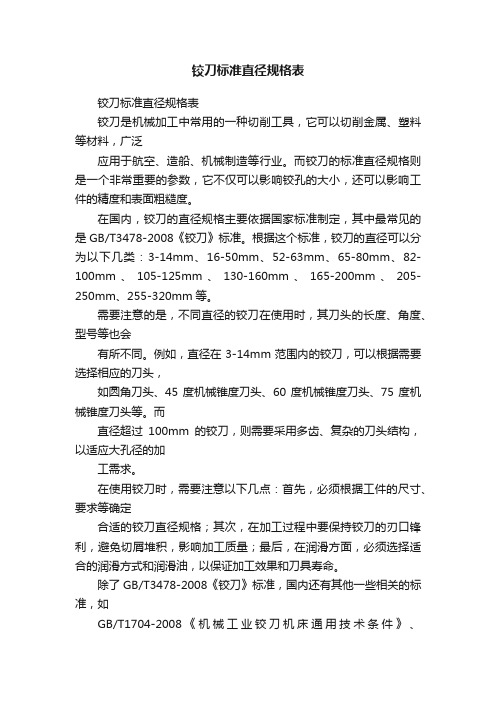
铰刀标准直径规格表铰刀标准直径规格表铰刀是机械加工中常用的一种切削工具,它可以切削金属、塑料等材料,广泛应用于航空、造船、机械制造等行业。
而铰刀的标准直径规格则是一个非常重要的参数,它不仅可以影响铰孔的大小,还可以影响工件的精度和表面粗糙度。
在国内,铰刀的直径规格主要依据国家标准制定,其中最常见的是GB/T3478-2008《铰刀》标准。
根据这个标准,铰刀的直径可以分为以下几类:3-14mm、16-50mm、52-63mm、65-80mm、82-100mm、105-125mm、130-160mm、165-200mm、205-250mm、255-320mm等。
需要注意的是,不同直径的铰刀在使用时,其刀头的长度、角度、型号等也会有所不同。
例如,直径在3-14mm范围内的铰刀,可以根据需要选择相应的刀头,如圆角刀头、45度机械锥度刀头、60度机械锥度刀头、75度机械锥度刀头等。
而直径超过100mm的铰刀,则需要采用多齿、复杂的刀头结构,以适应大孔径的加工需求。
在使用铰刀时,需要注意以下几点:首先,必须根据工件的尺寸、要求等确定合适的铰刀直径规格;其次,在加工过程中要保持铰刀的刃口锋利,避免切屑堆积,影响加工质量;最后,在润滑方面,必须选择适合的润滑方式和润滑油,以保证加工效果和刀具寿命。
除了GB/T3478-2008《铰刀》标准,国内还有其他一些相关的标准,如GB/T1704-2008《机械工业铰刀机床通用技术条件》、GB/T9731.1-2010《见森有关铰刀工具的术语第1部分:铰孔刀》等。
这些标准的制定和执行,有助于推动中国机械加工行业的发展,提高铰孔加工的精度和效率。
总之,铰刀的标准直径规格表是机械加工中重要的参考参数之一,它关系到加工产能、工艺效率和产品质量等方面。
对于机械加工从业人员来说,熟悉和掌握这个参数,是提高加工技术和水平的基础。
铰刀铰孔注意事项
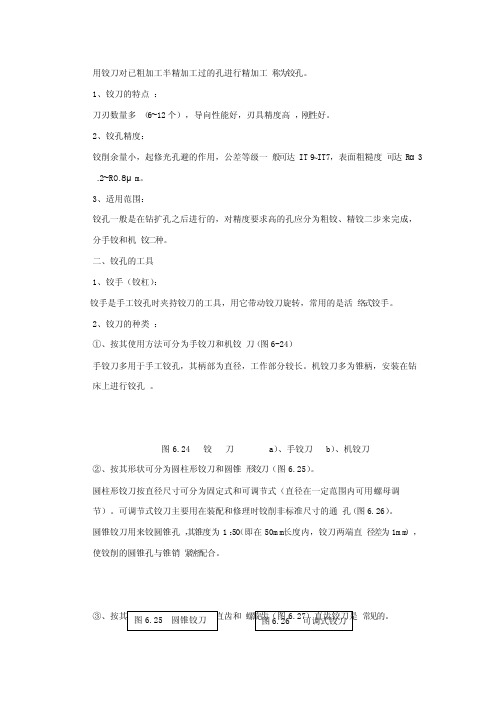
用铰刀对已粗加工半精加工过的孔进行精加工称为铰孔。
1、铰刀的特点:刀刃数量多(6~12个),导向性能好,刃具精度高,刚性好。
2、铰孔精度:铰削余量小,起修光孔避的作用,公差等级一般可达IT9~IT7,表面粗糙度可达Rα3.2~R0.8μm。
3、适用范围:铰孔一般是在钻扩孔之后进行的,对精度要求高的孔应分为粗铰、精铰二步来完成,分手铰和机铰二种。
二、铰孔的工具1、铰手(铰杠):铰手是手工铰孔时夹持铰刀的工具,用它带动铰刀旋转,常用的是活络式铰手。
2、铰刀的种类:①、按其使用方法可分为手铰刀和机铰刀(图6-24)手铰刀多用于手工铰孔,其柄部为直径,工作部分较长。
机铰刀多为锥柄,安装在钻床上进行铰孔。
图6.24 铰刀 a)、手铰刀 b)、机铰刀②、按其形状可分为圆柱形铰刀和圆锥形铰刀(图6.25)。
圆柱形铰刀按直径尺寸可分为固定式和可调节式(直径在一定范围内可用螺母调节)。
可调节式铰刀主要用在装配和修理时铰削非标准尺寸的通孔(图6.26)。
圆锥铰刀用来铰圆锥孔,其锥度为1:50(即在50mm长度内,铰刀两端直径差为1mm),使铰削的圆锥孔与锥销紧密配合。
常见的。
图6.27 螺旋铰刀螺旋铰刀有左旋也有右旋,多用于铰有缺口或带槽的孔,其特点是在铰削时刀刃不被槽边钩住,而且切削平稳。
三、铰孔方法1、铰削余量:铰孔前所留的铰削余量是否合适,直接影响到铰孔后的精度和粗糙度。
余量过大,铰削时吃刀太深,孔壁不光,而且铰刀容易磨损。
余量太小,上道工序留下的刀痕不易铰去,达不到铰孔的要求,一般情况下,铰削余量的可见表6.2。
表6.2 铰孔余量mm注:二次铰时,粗铰余量可取一次铰余量的较小值通常对于IT9~IT8级的孔可一次性铰出,对IT7级以上的孔应分两次铰出(粗铰和精铰),对于孔径大于20mm的孔,可先钻孔,再扩孔,然后再进行铰孔。
铰刀直径公差如何确定【详解】

在机械制造中,根据被加工孔的尺寸精度来确定铰刀直径公差是常有的事。
铰刀的直径公差对被加工孔的尺寸精度、铰刀的制造成本和铰刀的使用寿命均有直接影响。
为此,我们根据实践经验,总结了铰刀直径公差确定法,介绍如下。
假设被加工零件孔的上偏差和下偏差分别为ES和EI,而铰刀直径的上偏差和下偏差分别为es和ei。
则:es= 2/3 (ES-EI)+EIei=es- 1/4(ES-EI)例如:我们要铰Ø10H9(0+0.036)的孔,饺刀的上偏差依据上述公式应为:es= 2 (0.036-0)+0=0.024铰刀的下偏差据上述公式应为:ei=0.024- 1 (0.036-0)=0.015则:铰Ø10H9(0+0.036)孔的铰刀尺寸及公差带为Ø10+0.015+0.024。
查资料,Ø10H9铰刀尺寸公差为Ø10+0.013+0.023与计算得出公差相差甚微,可以满足使用要求。
该方法可为按被加工孔的尺寸精度来设计或研磨铰刀提供参考。
但铰孔时还受机床主轴径向跳动、铰刀的安装偏差、铰刀各刀齿的径向跳动、冷却液、切削用量等因素的影响,使铰出孔的直径往往会扩大或收缩。
因此,为满足工艺要求,一般要先试铰,根据试铰情况来修正计算出的公差带,再刃磨铰刀,投入使用。
扩展资料:铰刀的直径尺寸:铰刀最大直径的尺寸是30mm,最小的直径尺寸是2mm,铰刀精度有D4,H7,H8,H9等精度等级,直径一般分为2、2.5、3、3.5、4、4.5等尺寸。
铰刀结构大部分由工作部分及柄部组成。
工作部分主要起切削和校准功能,校准处直径有倒锥度。
而柄部则用于被夹具夹持,有直柄和锥柄之分。
按不同的用途铰刀可分许多种,因此关于铰刀的标准也比较多,我们较常用的一些标准有GB/T1131手用铰刀,GB/T1132直柄机用铰刀,GB/T1139直柄莫氏圆锥铰刀等等。
铰刀按使用方式分为手用铰刀和机用铰刀;按铰孔形状分为圆柱铰刀和圆锥铰刀,铰刀的容屑槽方向,有直槽和螺旋槽。
铰刀直径公差的确定

铰刀直径公差的确定
李惠朝;王巧
【期刊名称】《金属加工:冷加工》
【年(卷),期】2013(000)023
【摘要】我公司是一个具有60余年气缸盖专业生产的工厂,现生产品种达数10个,广泛用于农机、汽车及船用机械,并有部分出口。
在气缸盖机加工工艺中,孔加工精度十分重要,其精度直接影响到发动机的性能。
孔加工的尺寸精度主要靠精铰刀具保证,我公司刀具基本上都是自制,因而根据被加工孔的尺寸公差来确定铰刀直径公差就成了我们设计刀具时必须做的事情。
【总页数】2页(P49-50)
【作者】李惠朝;王巧
【作者单位】辛集市辛缸汽缸盖有限公司河北052360;辛集市辛缸汽缸盖有限公司河北052360
【正文语种】中文
【相关文献】
1.铰刀直径尺寸公差的确定
2.铰刀直径公差的经验确定法
3.铰削中“孔现象”的分析及铰刀直径的简化确定
4.铰刀直径尺寸的确定
5.铰刀直径极限尺寸的设计计算——对《铰刀专用公差》标准(GB4246—84)的一点建议
因版权原因,仅展示原文概要,查看原文内容请购买。
铰刀外径公差的计算

铰刀外径公差的计算
王转柱;董敏
【期刊名称】《机械工人:冷加工》
【年(卷),期】1997(000)002
【摘要】众所周知,铰刀设计时,其外形和其他几何参数一般可按被加工零件的特性从国标表列数值中直接选择,而其外径尺寸公差除标准中规定的常备精度等级(H7、H8、H9)可直接从国标表列数值中查取外,多数情况下则必须通过计算加以确定。
但由于计算时要考虑的因素较多,诸如铰刀本身的制造公差、被加工孔的公差等,使得计算过程极为繁杂。
【总页数】2页(P18-19)
【作者】王转柱;董敏
【作者单位】河北邢台鑫明电器有限公司;河北邢台市仪表厂技术科
【正文语种】中文
【中图分类】TG713.4
【相关文献】
1.铰刀直径公差的确定 [J], 李惠朝;王巧
2.铰刀直径尺寸公差的确定 [J], 曲贵龙
3.铰刀直径公差的经验确定法 [J], 葛树才
4.工件,铰刀,量规的公差带和计算 [J], 陈强
5.铰刀直径极限尺寸的设计计算——对《铰刀专用公差》标准(GB4246—84)的一点建议 [J], 王勇
因版权原因,仅展示原文概要,查看原文内容请购买。