压铸模具保养规定
压铸模具的保养规定

压铸模具的保养规定第一压铸网1.目的规范压铸模具日常保养的管理,减少损坏频率,保证生产顺畅高效进行,确保产品的符合性。
2.范围本公司所有正式生产压铸模具(新模具没有验收合格且正式移交压铸车间的除外)的日常保养与维修管理。
3.职责3.1模具一级、二级保养由压铸车间模具保养与维修小组负责。
3.2压铸车间领班负责压铸模具一级保养,并配合模具保养与维修小组完成二级保养。
3.3压铸车间模具保养与维修组负责模具保养台账的建立及相关记录的操持。
3.4模具三级保养由模具车间主管负责,模具保养小组主导及相关记录的填写。
4.定义4.1压铸模具一级保养:指压铸模具的上油、清扫、清洁等工作内容。
4.2压铸模具二级保养:更换型芯配件,抽芯油缸的维修,模具抛光,浇道修改等工作。
4.3压铸模具三级保养:模具结构改变,产品尺寸改变,型腔修补和更换及配镶块等工作。
5.工作要求5.1压铸模具管理台账5.1.1压铸模具保养与维修小组负责建立《压铸模具台帐》,编制《模具易损件清单》,清单内每个配件应有模具易损件图纸(图纸获取方法:新模具配件图由制模具人提供,老模具原则上由模具车间提供,找不到制模具人由模具保养小组绘制草图报模具车间和研发部批准)。
压铸模具台账上需注明模具编号,库存位置编码,启用日期,模具名称,制模人等内容。
模具易损件通常指顶杆、顶套、滑块抽芯、重要型芯等。
5.1.2压铸模具保养与维修小组负责建立《模具使用维修流程卡》,卡上注明:模具保养责任人,制模人,模具名称,模具编号,库存位置编码,设计寿命,生产日期,生产模数,当前累计模数,维修记录等等。
5.2模具保养要求5.2.1一级保养工作内容:A)清除模具上的污垢:用相应工具(清理型腔用铜刷、毛刷和抹布等,禁用钢刷;清理模板才可用钢刷、钢铲、铜刷、抹布、毛刷)对模具进行清除,遵循自上而下原则清除模具上所有锌渣、铝渣、油污、灰尘等污垢。
注意不能磕碰划伤型腔型芯等各产品部位。
B)清洗:①先用煤油对模具进行清洗,保证各直角凹槽孔等易藏污纳垢处无锌渣、铝渣、灰尘、污垢,分型面、型腔、抽芯等滑动部件及模具外观清洁如新。
压铸模具使用维护说明书

压铸模具使用维护说明书压铸模具使用维护说明书1. 引言1.1 目的本文档旨在提供压铸模具的使用和维护指南,以确保其正常运行并延长使用寿命。
1.2 范围本文档适用于所有使用压铸模具的操作人员和维护人员。
2. 使用指南2.1 安全操作2.1.1 在使用压铸模具之前,操作人员必须接受相关培训,了解模具的使用和安全操作规程。
2.1.2 确保在操作期间戴上所需的个人防护设备,如安全眼镜、安全手套和防护服。
2.1.3 严禁使用损坏或未经授权的模具。
2.1.4 在操作期间保持工作区域整洁,清除杂物和障碍物,以防止意外发生。
2.2 正确使用2.2.1 在使用模具之前,仔细检查其外观和工作条件。
如发现任何损坏或异常情况,请立即报告给维护人员。
2.2.2 确保按照产品要求装配和调整模具,以确保产品质量。
2.2.3 在进行压铸过程中,注意观察模具的工作状态,发现异常情况时及时采取措施进行修复或报告。
2.2.4 遵循模具的使用和维护手册中的操作流程和参数设置。
3. 维护指南3.1 日常保养3.1.1 定期清洁模具表面和内部部件,确保无异物和积聚的材料。
3.1.2 对模具润滑部位进行定期润滑,使用指定的润滑剂。
3.1.3 定期检查紧固件和各个零部件的紧固程度,确保其安全可靠。
3.1.4 维护模具的配件和附件的完整性,定期更换磨损和老化的部件。
3.2 故障排除3.2.1 如发现模具运行异常或故障,应立即停止使用,并报告给维护人员进行检修。
3.2.2 维护人员应及时检查并修复模具故障,确保其正常运行。
4. 附件本文档附带以下附件:- 压铸模具操作手册- 压铸模具维护手册- 压铸模具润滑剂使用手册5. 法律名词及注释5.1 法律名词1:依法律《XX法》解释解释:依照国家《XX法》规定进行操作和处理。
5.2 法律名词2:依法律《YY法》解释解释:依照国家《YY法》规定进行操作和处理。
5.3 ....(根据需要添加)。
压铸模具保养

保养周期与保养计划的制定
定期检查
根据模具的使用情况和材质,制 定合理的保养周期,定期对模具
进行检查和维护。
预防性保养
采取预防性保养措施,如定期润滑 、清洁和防锈等,以延长模具的使 用寿命。
保养计划
制定详细的保养计划,包括保养项 目、时间、人员和工具等,确保保 养工作的顺利进行。
保持模具存放环境的干燥和清洁 ,防止锈蚀和氧化,延长模具的
使用寿命。
保证产品质量
良好的模具保养可以保证压铸件尺寸的稳定性和精度,减少产品缺陷和不良率。
定期清理模具内的残留物和杂质,避免对产品表面和内部质量的影响。
保养过程中对模具进行检测和调整,确保模具处于良好的工作状态,提高产品的合 格率。
降低生产成本
模具维修与更换
总结词
模具维修是指对损坏或磨损的部位进行修复,而模具更换则是指整副模具的替换。
详细描述
对于损坏或磨损的部位,应根据实际情况进行维修或更换。在维修过程中,应遵循正确的工艺流程,确保维修质 量。如无法修复或修复成本过高,则需考虑整副模具的更换。在更换模具时,应选择质量可靠、性能稳定的模具 ,以确保生产效率和产品质量。
详细描述
在生产过程中,应控制模具温度,避免长时间的高温状态。 同时,要确保模具在使用过程中不受外力冲击,保持稳定的 生产环境。发现裂纹后,应及时停止使用,进行修复或更换 。
模具变形
总结词
模具变形通常是由于热处理不当或使用过程中受力不均所导致的。
详细描述
在进行热处理时,应遵循正确的工艺流程,确保热处理质量。在使用过程中, 要确保受力均匀,避免局部受力过大的情况。如发现模具变形,可采用适当的 矫形工艺进行修复。
模具保养管理办法
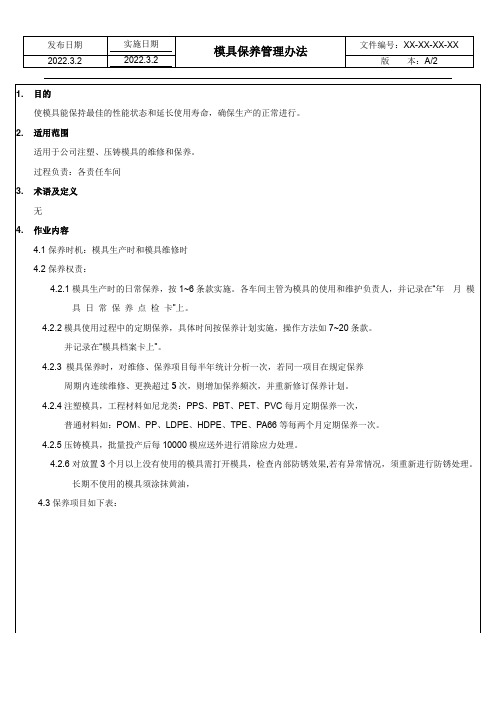
NO保养项目示例图片处理方式保养类别责任部门1检查模具开合动作是否灵活,锁模螺丝,安装螺丝是否有松动重新上紧螺丝,模具清洁干净后,上润滑油保证开合动作灵活。
日常保养责任车间2注塑:目视模面上是否有油污、料丝及其他杂物1.带手套并用碎布清理干净2.清理完成后需用清洗剂喷涂,再用汽枪吹干日常保养责任车间压铸:目视模面上是否有粘铝、及其他杂物将粘铝和其他杂物清理干净3检查导柱与导套、滑块与锁紧块是否出现松动与磨损1.上油2.若轻微松动、磨损则车间自行处理,若不能处理则提交模具车间处理。
日常保养责任车间查看所有螺丝侧面图锁模螺丝导柱模芯面为主要确认面正面图自行处1.2.顶针水管接头导套NO保养项目示例图片处理方式保养类别责任部门6注塑:目视产品是否有拉伤、多料、毛边、孔堵等不良现象无1. 轻微现象,责任车间自行处理。
2. 如经判定为模具引起,则提交给模具车间做维修。
日常保养责任车间压铸:目视产品是否有拉伤、多料、毛刺、孔堵等不良现象定期保养71.对模具实施拆解;2.确认型芯插穿面、前端面/碰穿面是否有伤痕、磨损、烧损、凹陷等现象;1.当检查出模芯有异常现象时,则提交模具车间实施维修。
2.确认模芯没有异常或维修完成时,应用清洗剂对模芯进行清洗并用气枪吹干。
(如如图)定期保养责任车间/模具车间8确认潜浇口、点浇口是否磨损、变形1.潜浇口损坏时,重新更换工件。
2.点浇口损坏时,看是否可以重新进行扩孔处理使用,或者重新更换工件。
定期保养责任车间/模具车间模芯清洗牙刷潜浇口1.2.1.新给工件上润滑油,并且告知车间人员进行日常点检润滑。
2.推杆孔 类推杆类点浇口1.2.3.当发生磨损时,则立即.弹簧顶针浇口套与机台射嘴的接触面清理异物,树脂完成后清理异物,粘铝完成后如图:排气槽上有树脂(粘铝)需清理1.2.3.滑块1.2.3.定模框1.再用气枪吹气。
2.水管。
压铸模安全操作保养规定

压铸模安全操作保养规定压铸模是压铸工艺中不可缺少的重要设备之一。
其生产效率和产品质量的优劣直接关系到企业的经济效益和声誉。
然而,由于操作不当或没有进行及时的维护保养,不仅会影响生产效率和产品质量,还会有安全隐患。
因此,压铸模的安全操作和保养是非常重要的。
安全操作1. 压铸模的检查和准备工作在进行开模操作之前,必须对压铸模进行检查和准备工作。
包括检查压铸模的工作状态、检查模具芯、模具部件、易损部件和紧固螺栓是否牢固等。
准备工作包括喷涂模具分离剂,擦拭模具各个部件,对模腔喷涂模具保护剂等。
2.开模开模是压铸模的一项重要操作。
在开模时,必须按照操作步骤进行操作,避免操作失误。
开模时,首先将模具有序的分开,并将零件从模腔中取出。
3.模具的安装和调试在进行模具的安装和调试工作之前,必须对模具进行检查,确保模具的各个部件完整、无损坏、无严重磨损等情况。
安装后,进行调试前,还需对模具加热炉、喷水系统和冷却器等进行检查和调整。
4.模具的加热和冷却为了确保压铸模具的正常运行,必须进行适当的加热和冷却工作。
在加热前,必须检查并清除模具腔的污物和杂质,并调整好模具和加热炉之间的距离。
在冷却前,必须检查并调整冷却水的流量和温度,并测量降温水的出水温度。
5.模具的维护保养在生产中,必须对压铸模具进行定期维护保养,包括表面清洗和维修等。
对模具表面进行清洗时,可以使用干净的清水或温和的清洗剂。
对于维修,最好是在模具寿命末期或出现质量问题时进行。
保养规定1. 模具的表面清洗模具表面清洗是常规的维护保养工作之一,其作用是去除模具表面的污垢和氧化物,保持模具的光洁度、耐磨性和抗腐蚀性。
使用清洗剂时应注意不能使用强烈的酸碱性清洗剂,应选用pH值在中性范围内的清洗剂。
2. 模具的保护工作在生产过程中,对模具的表面进行喷涂模具保护剂,有助于防腐、防锈和延长模具使用寿命。
喷涂模具保护剂应当在模具表面清洗彻底而且干燥后进行。
3. 模具的检查和维修为了确保压铸模具的正常运行,需要定期检查和维修模具,保证模具的完整性和精度。
压铸模具维修规章制度范本

第一章总则第一条为确保压铸模具的正常使用和延长模具使用寿命,提高生产效率,降低生产成本,特制定本规章制度。
第二条本规章制度适用于公司所有压铸模具的维修、保养及管理工作。
第三条压铸模具维修工作应遵循“预防为主、维护保养并重”的原则,确保模具的稳定性和可靠性。
第二章维修人员职责第四条维修人员应具备以下条件:1. 具备模具维修的专业知识和技能;2. 熟悉公司压铸模具的结构、性能及生产工艺;3. 具有良好的职业道德和责任心。
第五条维修人员职责:1. 按照维修保养计划,定期对压铸模具进行检查、保养和维修;2. 对损坏、磨损的模具进行修复,确保模具性能;3. 及时发现模具潜在问题,提出改进措施;4. 记录维修保养情况,做好维修保养档案。
第三章维修保养流程第六条维修保养流程如下:1. 检查:定期对压铸模具进行外观检查,发现异常情况及时报告;2. 保养:根据模具使用情况和保养计划,进行清洁、润滑、紧固等保养工作;3. 维修:对损坏、磨损的模具进行修复,确保模具性能;4. 质量验收:维修完成后,进行质量验收,确保模具达到规定要求。
第四章维修保养注意事项第七条维修保养注意事项:1. 维修保养过程中,严禁私自更改模具尺寸;2. 严格按照《模修维护保养管理规定》执行,不得使用不符合规定的工具;3. 对于易损件,如顶杆、型芯等,应仔细检查,发现问题及时更换;4. 抛光模具时,注意控制抛光力度,避免损伤模具表面;5. 针对粘铝、粘砂等问题,及时清理,防止模具堵塞。
第五章维修保养记录第八条维修保养记录应包括以下内容:1. 模具名称、型号、编号;2. 维修保养日期;3. 维修保养内容;4. 维修保养责任人;5. 维修保养结果。
第六章责任追究第九条违反本规章制度的,根据情节轻重,给予批评教育、罚款、降职等处分。
第七章附则第十条本规章制度由公司质量管理部门负责解释。
第十一条本规章制度自发布之日起施行。
(注:本范本仅供参考,具体内容可根据公司实际情况进行调整。
铝合金压铸模具的管理与终身维护和保养

铝合金压铸模具的管理与终身维护和保养模具是压铸生产中三大必备因素之一,模具使用的好坏直接影响到模具的寿命,生产效率和产品的质量,关系着压铸的成本。
对于压铸车间来说,模具良好的维护和保养是正常生产顺利进行的有力保障,有利于产品质量的稳定性,在很大程度上降低无形的生产成本,从而提高生产效率。
根据在实际生产中遇到的问题,我们探讨一下怎么去把模具的维护保养做得更好。
首先:建立模具档案,做好准备(1)也就是给每一套模具在入厂时建立一套完整的使用记录,这是保证以后保养和维护的一个重要依据,每一条都要做的细致,清晰,包括每日的生产模次在内~~(2)作为一名模具管理人员,模具自入厂以后,模具每一部分的结构配件必须要详细记入模具档案里,并且要根据需要,把模具内的易损部分列出,提前准备配件,比如顶杆,型芯,等~~设立易损备件的最低库存量,从而不至于因准备不足而延误生产。
因为在公司里这样的教训很多,有备才能无患。
如果因为自己没有准备备件而耽误生产,对于压铸企业来说所造成的成本是很大的,时间,人力,保温炉用电(或者液化气)等都不是小数字,最主要是延误了生产,耽误了交货损失会更大!(3)给模具在做履历卡的同时有必要在模具本身刻上永久性标记,易于分辨。
这样只要不傻的人都不会造成装错模具的闹剧。
(4)如果附带有油缸抽芯器的模具,尽快给其配上快换接头,不然每次拆装模具从油缸里漏出的油所浪费的钱足够你支付好几个员工一个月的工资,你也可以用省下来的钱给员工改善一下伙食。
这样也大大缩短了压铸操作工装卸模具的时间,一举几得的事。
切记买一些质量好的快接头,否则适得其反。
(5)提前制定模具管理规定,对员工进行系统培训,切实的执行下去。
其次:模具在生产过程中的注意事项~提到模具的维护与保养,在很多压铸操作工的脑海里会立即闪现出一个概念,总认为那是模修工的事,和他关系不大,其实正好相反。
所有模具的命运如何可以说都在压铸操作工的手里掌握着。
打个比方说,你是有一部车,开了几年坏掉了,你能说都是那些个洗车的造成的吗?所以模具在使用过程中以下几点要特别注意:(1)模具冷却系统的使用。
压铸模具保养维修十大原则【完整】

模具工应熟知压铸模具保养维修十大原则如下:
1、模具保养维修前,必须保留最后一个压铸产品。
2、全面清理模具各处金属屑和积垢,清洁清洗模具,恢复模具本色。
3、检查最后压铸产品:有无拉伤、粘模、压蹋、掉肉,以及尺寸、孔位变化。
4、全面检查模具:有无小型芯弯曲或折断,有无活动型芯插入定位不准,有无断推杆或推杆长度发生变化,有无镶块定位不准,有无紧固螺栓松动等。
根据损坏情况,确定修理或更换。
5、对导致铸件轻微拉伤的型腔塌陷、裂纹、掉块等,局部焊补修理,焊补应严格按规程工艺操作。
6、对滑动部位如抽芯机构、导向装置等,应进行彻底清理,仔细检查、维修。
用高温润滑脂重新润滑后装配。
7、如果有液压抽芯,液压部分与模具同时维修。
液压部分维修特别注意清洁,防止污染,否则将会污染整个压铸机液压系统。
8、当模具在生产过程中出现故障或受到损伤时,应按具体情况确定修理方案。
模具平时必须制定相应的保养维修计划。
9、完成维修保养的模具,将成型表面、分型面、安装面等整套模具做好防锈处理。
模具在正确组装后,放在规划区域,做好标识,同时模具附件与模具必须放在一起。
10、模具生产一定模次,应该退火处理后,进行相应热处理和表面处理。
压铸模具的管理以及维护保养
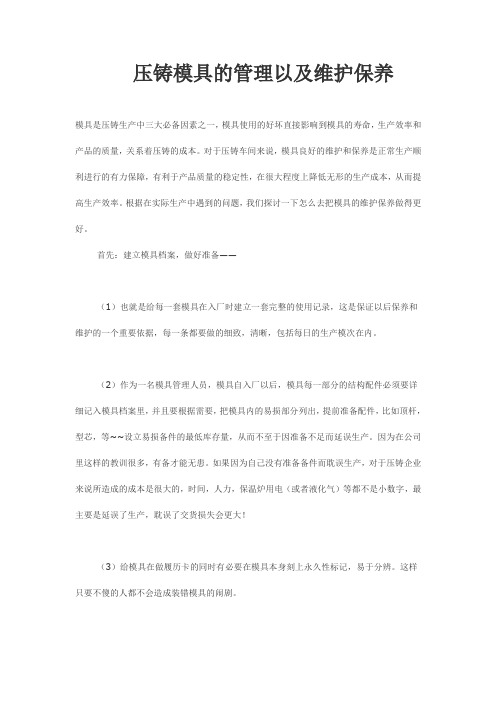
压铸模具的管理以及维护保养模具是压铸生产中三大必备因素之一,模具使用的好坏直接影响到模具的寿命,生产效率和产品的质量,关系着压铸的成本。
对于压铸车间来说,模具良好的维护和保养是正常生产顺利进行的有力保障,有利于产品质量的稳定性,在很大程度上降低无形的生产成本,从而提高生产效率。
根据在实际生产中遇到的问题,我们探讨一下怎么去把模具的维护保养做得更好。
首先:建立模具档案,做好准备——(1)也就是给每一套模具在入厂时建立一套完整的使用记录,这是保证以后保养和维护的一个重要依据,每一条都要做的细致,清晰,包括每日的生产模次在内。
(2)作为一名模具管理人员,模具自入厂以后,模具每一部分的结构配件必须要详细记入模具档案里,并且要根据需要,把模具内的易损部分列出,提前准备配件,比如顶杆,型芯,等~~设立易损备件的最低库存量,从而不至于因准备不足而延误生产。
因为在公司里这样的教训很多,有备才能无患。
如果因为自己没有准备备件而耽误生产,对于压铸企业来说所造成的成本是很大的,时间,人力,保温炉用电(或者液化气)等都不是小数字,最主要是延误了生产,耽误了交货损失会更大!(3)给模具在做履历卡的同时有必要在模具本身刻上永久性标记,易于分辨。
这样只要不傻的人都不会造成装错模具的闹剧。
(4)如果附带有油缸抽芯器的模具,尽快给其配上快换接头,不然每次拆装模具从油缸里漏出的油所浪费的钱足够你支付好几个员工一个月的工资,你也可以用省下来的钱给员工改善一下伙食。
这样也大大缩短了压铸操作工装卸模具的时间,一举几得的事。
切记买一些质量好的快接头,否则适得其反。
(5)提前制定模具管理规定,对员工进行系统培训,切实的执行下去。
其次,模具在生产过程中的注意事项~提到模具的维护与保养,在很多压铸操作工的脑海里会立即闪现出一个概念,总认为那是模修工的事,和他关系不大,其实正好相反。
所有模具的命运如何可以说都在压铸操作工的手里掌握着。
打个比方说,你是有一部车,开了几年坏掉了,你能说都是那些个洗车的造成的吗?所以模具在使用过程中以下几点要特别注意:(1)模具冷却系统的使用。
压铸模具保养计划指导书

压铸模具保养计划指导书
编号:EMCO/SJ-19-04-001所有压铸模具
注意:维护保养人员必须经过专业培训!
为了使模具能够保持最佳的性能状态和延长模具的使用寿命,确保正常生产,需对模具进行及时的保养和维护工作,维护及保养工作内容如下:
一、生产前模具的保养。
1.1.对模具的表面的油污,铁锈清理干净,检查模具的冷却水孔是否有异物,是否有水路不通。
1.2.需检查模具浇口是否损伤,是否有残留的异物,活动部件是否有异响,动作是否顺畅。
1.3.检查滑块是否顺畅,弹簧是否完整齐全,顶针是否有断掉或缺失的。
二、生产中模具的保养(由操作者执行)。
2.1.每班检查模具的所有的导柱、导套、顶针是否损伤,包括模具导柱、滑块等部件。
每班对其加油保养。
2.2.每班清洁模具分型面和滑块槽的异物、锌屑等,并检查模具的顶针是否有异常,并每班给油。
三、停机拆卸前模具的保养。
3.1.停机之前须先关闭冷却水路,吹尽模具内的余水。
3.2.对模具分型面、模穴、模芯面、滑块等部位的进行清洁。
3.3.模具运动部件的清洁和润滑,对松弛的螺栓进行紧固。
四、定期检查,主要对放置三个月以上的模具进行清理维护。
4.1.每六个月至1年对模具拆卸检查(检查内容有:除锈、防锈、润滑、型腔磨损、密封件、孔、销的溢料飞边及其它多余物、冷却水垢的清除等)。
五、以上所有保养项目均有书面记录,完成后模具归位。
保养责任人除指定操作者外均有设备模具部负责。
压铸模具管理规定

制订部门:~~~ 文件编号:~~~ 版本: A0
压铸模具管理规定
编制日期: ~~~ 生效日期: ~~~ 页号:
4.2.2 量 产 模 具 定 期 保 养 规 划 ( 拆 解 与 清 洁 )
制订部门:~~~ 文件编号:~~~ 版本: A0
压铸模具管理规定
编制日期: ~~~ 生效日期: ~~~ 页号:
转到量产,若不合格则有项目 PE 通知模具厂商维修.
7.4.2 技术员负责对维修,保养后的模具试做,并做好相关参数记录,对合乎生产的模具进
行生产,如不合格退回模具厂进行维修.
7.4.3 模具师对验收合格的模具做登记管理,并填写模具履历表 7.6 模具镶件更换
7.6.1 技术员根据生产计划排程对需要更换镶件知会模具维修组更换.
看 板 , 需 包 含 三 星 CODE NO.,位 置 及 状 态 等 , 如 下 图
5.3 緾绕膜。
5.2.2 模 具 摆 放 时 需 保 持 合 适 的 距 离 5.2.3 模 具 需 有 下 模 脚 , 以 离 开 地 面 10CM 左 右 5.2.4 模 具 摆 放 时 需 将 所 有 铭 牌 置 于 南 侧 上 方 , 以 便 观 察 取 放 。 模具防尘 5.3.1 模 具 摆 放 后 需 于 四 周 架 防 尘 架 , 以 緾 绕 膜 覆 盖 , 每 半 年 更 换 一 次
儀表檢查
3 確認合模紅丹狀況;PL95%靠破。滑块入子合模状况,合模红丹靠破95%以上。
4 實測公母模降面處于成型面尺寸.
儀表檢查
5 根據3D圖確認模仁有無漏加工.公模特征:
母模特征: 滑块:
依3D仔细确认
6 檢查模仁 模板,湯口套水路和油路是否畅通,无泄露。接口牙型及牙深是否标
(完整版)压铸模具管理及保养规范

压铸模具管理及维护规范1、目的:加强压铸模管理,保证压铸模正常维护,保证压铸正常生产和产品质量、延长压铸模使用寿命、降低成本。
2、适用范围与职责:本公司所有的压铸模具管理与保养。
压铸车间负责模具的日常保养;工艺部模修人员负责模具维护及维修3、操作程序:3.1压铸模必须整齐摆放在规定区域和位置。
3.2压铸模维护、保养、维修、管理由专人负责。
3.3压铸模验收:3.3.1新压铸模制作完毕,应经压铸模验收小组根据《压铸模技术条件》对压铸模进行验收,验收合格后,方可交到车间,压铸模管理员要清点浇口套、顶杆、型芯等压铸模备件,做好标识并分类存放。
3.3.2因生产需要,压铸模转出或运回车间时,压铸模管理员要做好交接工作,有关人员做好验收工作。
3.4压铸模档案:压铸模验收合格后,必须建立《压铸模使用维修档案本》,以备定期检查、校对。
3.5压铸模检查:3.5.1有冷却水的压铸模,用接自来水检查压铸模冷却水管,不应堵塞或破损。
3.5.2检查压铸模滑块、顶杆、导柱等应运行平稳,无断裂、无卡滞现象。
3.5.3仔细检查压铸模型腔和分型面,型腔、型芯不允许有碰伤现象和粘有异物;分型面、排气槽不允许有铝(铜或锌)渣和污物,如有必须清理干净。
3.5.4检查压铸模顶杆推板和顶杆固定板,联接必须牢固,顶杆推板上拉杆孔螺纹必须完好。
3.5.5检查压铸模吊环螺钉不能有裂纹,吊环螺钉与压铸模联接必须牢固。
3.5.6压铸模合模时应保证复位杆与分型面齐平,插芯到位。
3.6压铸模维护与保养:压铸模的保养分为日常保养与周期性保养日常保养主要将模具外表面铝渣及污垢清理干净。
周期性保养要求如下:压铸模卸下后,压铸工必须将其吊到指定位置摆放,由压铸模维修工进行以下维护、保养。
a)清理压铸模(包括滑块、型腔、型芯、排气系统等)上铝(铜或锌)屑、污垢物,保证压铸模清洁和排气通畅。
清理粘铝部分后进行打磨抛光。
b)擦净模具和冷却水管上的油污。
c)按3.5进行压铸模检查。
模具保养维修使用规范

模具保养维修使用规范模具验收合格后,为了能使模具保持最佳的性能状态和使用寿命的延长,也确保生产的正常进行和产品的质量,尽可能降低生产成本,使用时请按以下事项进行必要的维护和保养。
一、模具生产前的检查及安装要求1、上岗前必须穿戴好防护用具,如:安全帽、工作服和劳保鞋。
严禁穿着短袖上衣、短裤和拖鞋上岗。
2、模具安装前,首先要确认压铸机床的规格与模具设计要求是否匹配。
3、压铸工必须全面了解模具结构状况,包括:A、检查模具有无抽芯(动模抽芯、静模抽芯、斜杆抽芯及液压抽芯)。
B、是否需要安装顶杆预复位倒拉杆或强力弹簧。
C、检查浇口套、法兰与熔杯大小结合尺寸是否一致。
D、是否为中心浇口。
E、检查顶棒位置是否无干涉且顶出平衡。
4、根据模具情况更换熔杯冲头,必要时调节压射升降机构。
5、再检查模具外围紧固螺栓,确认无松动现象后,方可上机安装模具,以保证模具安装可靠。
6、检查压铸机和模具的动静模板装帖面:表面无异物,无高点。
7、模具装入压铸机内,需正确的安装压板并且安装牢固拧紧后,再对模具进行空模运转,检查模具的开合是否顺畅?观察其各部位运行动作是否灵活?是否有不正常现象?顶出行程,开启行程是否到位?合模时分型面是否吻合严密?压板螺丝是否拧紧?水路、油路是否畅通?8、特别是模具上滑动相关零件部位的运行进行检查。
《如导柱、导套、顶针、推杆顶出等活动部件(位)要随时观察,定时检查,适时擦洗并加注润滑油脂, 以保证这些滑动件运行正常灵活,防止紧涩咬死。
》调好合模、顶出的压力和距离。
并安装好各种辅助件(如:水管、油管、抽气装置),在调试过程中检查水管接头、油管接头是否有破损、泄漏、堵塞现象。
9、模具安装压板螺栓牢固并没有松动现象时,模具再连续空开合三、四次压铸机调试,当开合顺畅、没有异常情况出现,模具各运行工件平稳、可靠、灵活后才能开始进行试模生产。
生产过程中模具导向部位和滑动部位应经常清理、润滑,确保运动顺畅、到位、无卡滞现象。
压铸模具维修及维护保养规定

1 目的Purpose规定压铸模具维护保养的流程和方法,以确保模具得到有效的维护保养,投入压铸生产时处于合格可控的状态Stipulate maintenance process and methods of die casting mold,ensure that all molds maintenance are available,and they are controlled during die casting production.2 适用范围Scope of application适用于压铸模具的维护和保养Apply to die casting mold maintenance3 定义Definition无N/A4 职责4 Responsibilities4.1 压铸技术部负责压铸模具维护保养的归口管理部门,负责维护保养作业指导书的编制和执行Production development department is responsible for die casting mold maintenance,also is responsible for compile and execute maintenance work instruction.4.2生产部负责模具生产过程中模具点检、清洁和状态的监控和反馈模具状态给模具组 Production department is responsible for monitor mold status during the production process and feedback to mold group.5 工作程序 Working routine5.1模具验收合格后,入模具库,登记模具台帐,建模具履历,建立备品备件清单后可正式投入使用。
When molds are accepted,then put it to mold library,register mold account,create mold record and create spare parts list,after these,the mold can be normal used.5.2 模具上线前检查:Inspection before mold go to production line5.2.1 由模具维修主管在模具出库前检查,检查项目如下:Mold keeper check the items before mold out of mold library,inspection items:– 水管接头是否全部装好Water pipe connector is or not qualified installed.– 月份是否正确Month is or not correct.5.3 模具上机前检查: Mold inspection before install machine5.3.1 模具上机,由压铸调试工检查以下项目完好,方可开始生产;否则退回模具间。
模具使用、维修及保养规程

东大汽车工业有限公司DONGDA.AUTOMOBILE.INDUSTRY.CO LTD.压铸模具使用、维修及保养规程持有处发布日期:2011 年2月15日1、目的:为了保证产品质量和压铸模具能够有效的使用和维护、维修,从而保证或延长模具使用寿命及产品交付率。
2、范围:公司所有压铸模具维修、保养。
3、职责:3.1品质部负责不合格处理通知单的开具和修模后产品的验证.3.2技术部负责产品设计变更方面修模指令的开具.3.3修模单位负责按进度表及修模指令对模具进行维修、保养及确保移交后的模具零缺陷。
3.4压铸车间负责对修模的全过程跟踪并对维修模具进行试模并会同技术部、品质部人员共同确认维修之模具。
4、内容4.1未移交模具的维修4.1.1未移交的模具,由于工艺或产品设计更改引起的变更由技术部下发修模通知单,同时更新图纸,交与开模厂家或修模单位进行更改或维修,由技术部对相关技术资料存档。
4.1.2模具修复或制造完成后,由开模厂家或修模单位开具《试模通知单》通知生产部试模,生产部签字确认后安排试模,压铸车间试模时提前通知品质部检验员准备对产品进行验证,同时需检验可能因修模出现异常的关联尺寸或结构。
4.1.3验证完成后,品质部验证人员在新产品流转单上签字。
最终结论由商贸部与顾客沟通后将信息发到各个部门。
4.2移交后的模具使用:4.2.1产前的模具在投入使用前应进行预热处理,预热温度为130℃~180℃。
预热温度不能太高,否则会在压铸时由于模具温度太高而引起模具再回火。
可采用先慢压射生产20模(铝合金)以上,提高模温后再快压生产。
有镶块的模具,必须缓和加热以便使镶块和型腔保持同步膨胀。
4.2.2生产过程中,模具温度逐步升高,应通进适量的冷却水来控制模具生产过程的温度变化,使模具能在稳定均匀的温度范围生产,为了减少热龟裂的危险性,模具温度保持在170-250℃(测量型腔表面温度),从而延长模具寿命。
4.2.3模具导滑部位如导柱、导套、顶板导柱、顶板导套、滑块导轨等必须进行润滑,型腔、型芯润滑剂(脱模剂)可避免铝液和模具直接接触和有利脱模,从而避免粘模,并可起到一定冷却作用。
- 1、下载文档前请自行甄别文档内容的完整性,平台不提供额外的编辑、内容补充、找答案等附加服务。
- 2、"仅部分预览"的文档,不可在线预览部分如存在完整性等问题,可反馈申请退款(可完整预览的文档不适用该条件!)。
- 3、如文档侵犯您的权益,请联系客服反馈,我们会尽快为您处理(人工客服工作时间:9:00-18:30)。
1.目的
规范压铸模具日常保养的管理,减少损坏频率,保证生产顺畅高效进行,确保产品的符合性。
2.范围
本公司所有正式生产压铸模具(新模具没有验收合格且正式移交压铸车间的除外)的日常保养与维修管理。
3.职责
3.1模具一级、二级保养由压铸车间模具保养与维修小组负责。
3.2压铸车间领班负责压铸模具一级保养,并配合模具保养与维修小组完成二级保养。
3.3压铸车间模具保养与维修组负责模具保养台账的建立及相关记录的操持。
3.4模具三级保养由模具车间主管负责,模具保养小组主导及相关记录的填写。
4.定义
4.1压铸模具一级保养:指压铸模具的上油、清扫、清洁等工作内容。
4.2压铸模具二级保养:更换型芯配件,抽芯油缸的维修,模具抛光,浇道修改等工
作。
4.3压铸模具三级保养:模具结构改变,产品尺寸改变,型腔修补和更换及配镶块等
工作。
5.工作要求
5.1 压铸模具管理台账
5.1.1压铸模具保养与维修小组负责建立《压铸模具台帐》,编制《模具易损件清单》,清单内每个
配件应有模具易损件图纸(图纸获取方法:新模具配件图由制模具人提供,老模具原
则上由模具车间提供,找不到制模具人由模具保养小组绘制草图报模具车间和研发部
批准)。
压铸模具台账上需注明模具编号,库存位置编码,启用日期,模具名称,制模
人等内容。
模具易损件通常指顶杆、顶套、滑块抽芯、重要型芯等。
5.1.2压铸模具保养与维修小组负责建立《模具使用维修流程卡》,卡上注明:模具保养责任人,
制模人,模具名称,模具编号,库存位置编码,设计寿命,生产日期,生产模数,当
前累计模数,维修记录等等。
5.2模具保养要求
5.2.1一级保养工作内容:
A)清除模具上的污垢:用相应工具(清理型腔用铜刷、毛刷和抹布等,禁用钢刷;清理模板才可用钢刷、钢铲、铜刷、抹布、毛刷)对模具进行清除,遵循自上而下原则清除模具
上所有锌渣、铝渣、油污、灰尘等污垢。
注意不能磕碰划伤型腔型芯等各产品部位。
B)清洗:
①先用煤油对模具进行清洗,保证各直角凹槽孔等易藏污纳垢处无锌渣、铝渣、灰尘、
污垢,分型面、型腔、抽芯等滑动部件及模具外观清洁如新。
②后用压缩空气吹干模具,特别保证行程开关、插头部位干燥无积油。
③认真检查模具各部位,有问题部件及时转到模具维修区进行维修。
④无问题模具吊装至保养区对导柱、导套、型腔、分型面及各部滑动部件涂防锈油。
⑤最后吊至“模具保养存放区”定置定位存放,并填写《模具使用维修流程卡》,在本卡
填写生产日期、总模数与累计模数等信息。
5.2.2二级保养工作内容:
完成清洗的模具吊装至维修区进行点检,点内容如下:
A)检查产品部:
①型腔、滑块型芯是否粘铝或锌、龟裂、压塌、变形、崩块;
②型芯是否有断、弯、粘铝和锌、崩缺及定位角度偏位等;
③排气道是否堵塞、粘铝和锌;
④内浇口是否龟裂、增厚或腐蚀。
B)检查机构部:
①分型面是否粘铝或锌、压塌;检查模具外浇口是否有变形;
②油管及水管是否泄漏、堵塞;
③顶杆是否断、弯、崩缺;
④复位杆是否变形,长度是否一致;
⑤滑块动作是否到位、卡滞、自如;
⑥顶杆板、模座、限位块螺栓是否松动;
⑦导柱、导套是否变形、开裂、磨损过大、松动;
⑧配线是否撕裂、断开;行程开关、插头是否进水,行程开关各触点是否灵敏正常;
⑨吊环是否有裂纹,磨损过大。
C)完成清洗的模具吊装至维修区进行点检、抛光,对损坏折断的型芯、顶杆等的损坏部位进行维修、维护、上油后,并做好记录。
更换备件时应将更换件与模具上的被更换件
进行检查对照(并将被更换件保留2个月时间,以便待查),确保无误后方可进行装配。
5.2.3模具三级保养:
模具存在的较大的问题必须向模具车间技术人员汇报,如模具需要焊补、更改尺寸以及更改流道,必须有模具维修方案审定单(注:以工作联系单形式报请研发部、
生产部、品管部、模具车间审核)后方可进行,并做好记录;如有维修并更换了模具
型芯等涉及产品尺寸可能发生变化的需要车间检验员或车间主管验收确认。
维修保养完成时,压铸车间模具保养与维修组长需做好以下记录:
●《模具使用维修流程卡》;
●《模具履历(或叫病历)卡》;
●《模具维修审定单》(即工作联系单形式也可)
5.3模具配件的制作与验收
5.3.1模具配件由原制模人负责制作,压铸车间模具保养与维修小组按配件图纸验收,车间QC再次确认。
5.3.2老模具配件制模人不在时,由压铸车间模具保养与维修小组负责制作,车间QC负责验收。
结构复杂配件需交由模具车间制作的,上报模具车间制作或委外加工等,验收方式按5.3.1。
6、绩效考核
6.1 考核指标之一:下道工序就是用户原则
模具维修与保养负责人的工作主题是对压铸车间生产服务,保证生产顺畅高效进行,确保产品的符合性。
他的顾客就是压铸车间各个班组,因此,压铸生产效率将直接与其挂钩,我们不但要求模具按期保养到位一,最终的结果是保证压铸高效生产,保质保量完成任务。
6.1.1生产效率
压铸生产效率=计划加工周期/实际加工周期*100%
如生产10万只TBH03标准基体需要15天完成,实际上用了20天完成,那么生产效率为15/20*100=75%,如果10天完成,那么生产效率为15/10*100%=150%。
生产效率越高,说明生
产过程的模具保障度高。
为了应对小品种小批量考核,应将考核的单位“天”改按“小时”计算。
质量考核:生产部当月统计每个模具在压铸的生产效率,月末汇总。
汇总公式:当月A模具生产效率95分,B模具120分,C模具80分,D模具60分;
则当月综合生产效率=(95+120+80+60)/4*100%=88.75%
6.1.2考核
压铸模具维修与保养组长月度绩效考核金额定为2000元/月,月度考核后的金额=2000*当月综合生产效率。
6.1.3奖励
当月度综合生产效率达到95%以上的,一次奖励300元,达98%以上的,一次奖励500元。
6.2考核指标之二:工作责任事故考核
6.2.1下列情况模具维修与保养组长将承担主要责任,并处罚款200元以上500元以下:
6.2.1.1模具型芯换错导致模具损坏造成经济损失2000元以上;
6.2.1.2模具维修保养不到位,导致交期延期15天以上;
6.2.1.3模具生锈,导致模具无法正常使用的;
6.2.1.4模具尺寸维修不当,导致大批量产品报废的。
6.2.2下列情况模具维修与保养组长承担直接责任,并处罚款50-200元。
6.2.2.1模具抽芯换错,但没有损失坏模具,在压铸生产过程发现的;
6.2.2.2模具保养不到位,导致交期推迟1周以上的。
6.2.2.3没按要求建立模具管理台账、模具维修履历卡和模具使用与维修流程卡等相关记录,空白期达1周以上的。
6.2.3奖励
6.2.3.1 当月没有发生模具责任事故奖励100元;
6.2.3.2模具维修保养各个零配件尺寸到位,给压铸和装配工序带来非常大的便利,除了提高压铸效率外,还提升装配效率,并获得生产部好评的奖励300元。