无溶剂复合工艺
无溶剂复合工艺控制小窍门
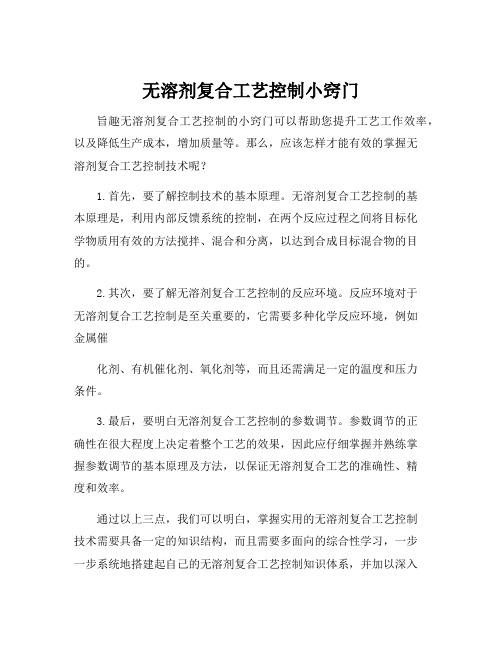
无溶剂复合工艺控制小窍门
旨趣无溶剂复合工艺控制的小窍门可以帮助您提升工艺工作效率,以及降低生产成本,增加质量等。
那么,应该怎样才能有效的掌握无
溶剂复合工艺控制技术呢?
1.首先,要了解控制技术的基本原理。
无溶剂复合工艺控制的基
本原理是,利用内部反馈系统的控制,在两个反应过程之间将目标化
学物质用有效的方法搅拌、混合和分离,以达到合成目标混合物的目的。
2.其次,要了解无溶剂复合工艺控制的反应环境。
反应环境对于
无溶剂复合工艺控制是至关重要的,它需要多种化学反应环境,例如
金属催
化剂、有机催化剂、氧化剂等,而且还需满足一定的温度和压力
条件。
3.最后,要明白无溶剂复合工艺控制的参数调节。
参数调节的正
确性在很大程度上决定着整个工艺的效果,因此应仔细掌握并熟练掌
握参数调节的基本原理及方法,以保证无溶剂复合工艺的准确性、精
度和效率。
通过以上三点,我们可以明白,掌握实用的无溶剂复合工艺控制
技术需要具备一定的知识结构,而且需要多面向的综合性学习,一步
一步系统地搭建起自己的无溶剂复合工艺控制知识体系,并加以深入
的研究,才能有效的掌握无溶剂复合工艺控制技术的相关知识,进而提升工作效率和生产质量,充分发挥无溶剂复合工艺控制的作用。
无溶剂复合工艺常见问题集锦

无溶剂复合工艺常见问题集锦近年来,无溶剂复合工艺因具有突出的节能、高效、低成本等优势而备受软包装企业的青睐,越来越多的软包装企业开始尝试采用无溶剂复合工艺。
但是,软包装企业在应用无溶剂复合工艺过程中,难免会遇到这样或那样的问题,甚至影响企业的正常生产。
在此,笔者结合自己的实践经验,总结了无溶剂复合工艺中的一些常见问题,在此与大家分享。
胶黏剂涂布后出现收缩现象如图1所示,在用VMPET阴阳膜复合第三层材料时,涂胶后在VMPET薄膜边缘出现胶液收缩现象,检查后发现系VMPET薄膜局部表面能不合格所致。
无溶剂胶液的表面张力远高于干法复合用的溶剂型胶液(稀释用溶剂乙酸乙酯的表面张力仅为26.29mN/ m),如果薄膜整体的表面能低于涂布胶液的表面张力,胶液在薄膜表面就会出现收缩现象;如果薄膜表面局部受一些低表面张力助剂的污染,则在该点就会出现胶液不润湿(收缩)现象,在最终的复合制品上形成气泡缺陷,甚至造成剥离不良的质量问题。
类似的涂胶后胶液收缩现象,在使用水性胶黏剂时也可能出现。
转移胶辊表面温度过高涂布系统的实际温度往往与设定温度有一定偏差,在机速300m/min、上胶量1.45g/m2的条件下,胶桶温度设定为35℃(实测38℃),计量辊温度设定为32℃,涂布辊温度设定为35℃,涂布系统的实测温度分布如图2。
由图2可见,转移胶辊表面温度高达44℃,已严重偏离设定值。
这是由于转移胶辊摩擦生热造成的,其影响因素主要有辊面光洁度、胶水黏度、压力大小等,其中辊面光洁度的影响最大,须严加控制。
胶辊表面胶液分布不均涂胶量太小时,胶辊表面的胶液分布不均匀,局部发涩(不反光),这在某种程度上也反映出涂布系统(转移胶辊)的精度高低。
理论上讲,对于某些复合结构(如BOPP/珠光膜),涂胶量在1.0g/m2就能满足复合强度要求,但如果设备涂布系统的精度不高,则需要适当增加涂胶量,以保证涂胶均匀。
材料起皱引起的复合气泡现象原材料皱褶将直接导致下机的复合产品出现气泡现象,原因是皱褶处复合时压不实,夹入空气。
如何确定无溶剂复合的工艺参数
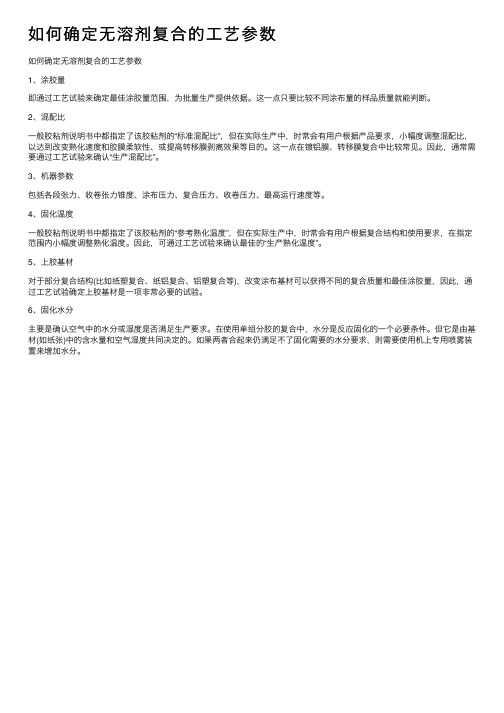
如何确定⽆溶剂复合的⼯艺参数
如何确定⽆溶剂复合的⼯艺参数
1、涂胶量
即通过⼯艺试验来确定最佳涂胶量范围,为批量⽣产提供依据。
这⼀点只要⽐较不同涂布量的样品质量就能判断。
2、混配⽐
⼀般胶粘剂说明书中都指定了该胶粘剂的“标准混配⽐”,但在实际⽣产中,时常会有⽤户根据产品要求,⼩幅度调整混配⽐,以达到改变熟化速度和胶膜柔软性、或提⾼转移膜剥离效果等⽬的。
这⼀点在镀铝膜、转移膜复合中⽐较常见。
因此,通常需要通过⼯艺试验来确认“⽣产混配⽐”。
3、机器参数
包括各段张⼒、收卷张⼒锥度、涂布压⼒、复合压⼒、收卷压⼒、最⾼运⾏速度等。
4、固化温度
⼀般胶粘剂说明书中都指定了该胶粘剂的“参考熟化温度”,但在实际⽣产中,时常会有⽤户根据复合结构和使⽤要求,在指定范围内⼩幅度调整熟化温度。
因此,可通过⼯艺试验来确认最佳的“⽣产熟化温度”。
5、上胶基材
对于部分复合结构(⽐如纸塑复合、纸铝复合、铝塑复合等),改变涂布基材可以获得不同的复合质量和最佳涂胶量,因此,通过⼯艺试验确定上胶基材是⼀项⾮常必要的试验。
6、固化⽔分
主要是确认空⽓中的⽔分或湿度是否满⾜⽣产要求。
在使⽤单组分胶的复合中,⽔分是反应固化的⼀个必要条件。
但它是由基材(如纸张)中的含⽔量和空⽓湿度共同决定的。
如果两者合起来仍满⾜不了固化需要的⽔分要求,则需要使⽤机上专⽤喷雾装置来增加⽔分。
如何确定无溶剂复合制品的工艺参数

如何确定无溶剂复合制品的工艺参数引言无溶剂复合制品是一种绿色环保的新型材料,其制备工艺参数的确定对于产品的质量和性能具有重要影响。
本文将介绍如何确定无溶剂复合制品的工艺参数,以保证产品的质量稳定性和性能优良性。
步骤一:材料选择在确定无溶剂复合制品的工艺参数之前,首先需要根据产品的要求选择合适的材料。
考虑到无溶剂复合制品的绿色环保特性,选择可再生或可回收利用的材料是一个明智的选择。
同时,还需要考虑材料的物理性质和化学性质,以确保其与其他材料的相容性和复合工艺的可行性。
步骤二:复合工艺设计在进行无溶剂复合制品的工艺参数确定之前,需要进行复合工艺的设计。
复合工艺的设计包括以下几个方面:温度控制确定适宜的复合温度是保证产品质量的重要因素之一。
可以通过调整温度来控制复合材料的粘度和流动性,从而影响材料的分布均匀性和成型性能。
压力控制在无溶剂复合制品的制备过程中,合适的压力能够保证材料的充填性能和密实度,影响产品的强度和稳定性。
通过对压力的控制,可以调节复合制品的力学性能和物理性能。
时间控制复合工艺中的时间控制是影响产品成型和固化的重要因素。
合适的时间控制可以确保复合材料的反应充分,从而影响产品的硬度、耐久性和稳定性。
步骤三:实验验证确定无溶剂复合制品的工艺参数后,需要进行实验验证。
通过不同工艺参数的调整,制备一系列样品,并进行性能测试和分析。
根据实验结果,可以评估和优化工艺参数,以获得最佳的产品性能。
结论通过以上步骤,可以确定无溶剂复合制品的工艺参数,从而保证产品的质量稳定性和性能优良性。
在实际应用中,还可以根据不同的产品要求和工艺条件进行适当的调整和优化,以满足特定的需求和要求。
参考文献:- 张三, 李四. 无溶剂复合材料的制备工艺与性能研究. 材料科学与工程学报, 2018, 36(4): 123-135.- 王五, 赵六. 无溶剂复合制品的制备及其应用. 化学工业, 2019, 45(2): 67-76.。
知识点21 软包装无溶剂复合工艺.
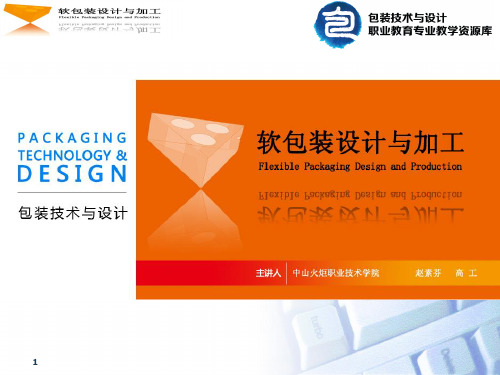
第一放卷:刚性较大、形变较小、涂布性能好。
第二放卷:易拉伸、形变大。
BOPP 和 CPP分别是哪个放卷装置?
涂布单元:是无溶剂复合机的中心部分,胶黏剂在此混合 、加热、计量和涂布。
涂布由计量辊、转移钢辊、转 移胶胶辊、涂布钢辊和涂布压 辊组成。
• 1辊固定不动,它起到刮胶作用;
• 1和2辊两辊的间槽起储胶作用,两者的间隙决定了上胶
收卷装置:因无溶剂复合初粘力低,要求收卷时尽量收紧。
pressure
无溶剂复合
优点: 1.环保适性好
2. 安全性好
3. 产品质量得到保证 4.可明显降低成本
无溶剂复合
缺点:
实际生产中,由于无溶剂胶黏剂的初始黏度很低,操作
控制难度加大,容易出现各种质量问题。
软包装设计与加工
主讲人:赵素芬
1
软包装无溶剂复合工艺
无溶剂复合是采用无溶剂类胶粘剂,使膜状基材(塑
料薄膜或其它膜状材料)相互帖合,然后经熟化(胶粘剂的 化学反应)使各层基材牢固地结合在一起,从而取得多层复 合薄膜的一种加工方法。
无溶剂复合由第一放卷、涂布单元、复合单元、第二
放卷和收卷单元组成。
量的量,1辊也称之为计量辊;
• 涂布量的大小的调节是根据辊2转移钢辊、辊3转移胶
辊和辊4涂布钢辊之间速比变化和温度的稳定性来调节 的,它们分别使用单个直流电机控制;
复合单元:把第一基材和第二基材复合在一起。
复合辊
复合膜
白点/气泡
复合强度高 外观优
复合强度低 外观差
检验方法:放复写纸在2张打印纸中间/压合在左、中、右/ 测量复写纸在打印纸上的压痕宽度/进行比较
无溶剂复合机工艺流程

无溶剂复合机工艺流程
1、准备工作。
检查无溶剂复合机的电源、机械传动和液压系统是否正常工作;准备复合膜和基材,并确保其质量符合标准;对基材表面进行清洗处理,以提高复合效果;确定复合机的工作参数,如复合温度、压力和速度。
2、操作步骤。
开启无溶剂复合机,等待设备升温至设定温度;将基材放入放卷装置中,并拉出一定长度的基材,同时将复合膜放入复合装置中;通过操作控制台调整复合参数,使设备达到最佳操作状态;开始复合操作,将基材和复合膜送入复合装置,设备自动完成复合过程;复合完成后关闭设备开关,并使用切断机将复合膜和基材分开。
无溶剂复合工艺试验及质量控制

无溶剂复合工艺试验及质量控制无溶剂复合主要工艺流程(1)放卷:在一定张力控制下,将待复合基材(料卷)平稳地展开,以便进行涂胶和复合等操作。
两层复合基材中,被涂胶的基材称为主基材,另一基材则称为副基材,相应的放卷操作分别称为主放卷和副放卷。
(2)上胶:一定温度下,将双组分胶黏剂按照一定比例(通常为重量比)进行均匀混合,再输送到无溶剂复合机的储胶部位,或将单组分胶黏剂直接输送到无溶剂复合机的储胶部位。
(3)涂布:按照复合结构和具体使用要求,将混合好的无溶剂胶黏剂适量地涂覆在基材上。
(4)复合:在适当均匀的压力下,将已涂胶的基材与另一基材进行黏合。
(5)收卷:将黏合的复合膜在适当的张力和收卷压力下进行卷取。
(6)固化:将复合卷材放置在一定温度的环境中,使无溶剂胶黏剂充分反应,从而得到期望的复合强度。
固化是无溶剂复合的一个重要工序,该过程通常需要在特定的温度和持续较长时间的条件下才能基本完成。
通常情况下,双组分胶黏剂常见的固化温度为35〜45C,常见的固化时间为24〜48小时,视胶黏剂类型、复合结构和使用场合不同而异,通常后加工工序为分切或再次复合时,固化时间可以较短,而后加工工序为制袋时则固化时间较长。
无溶剂复合工艺试验当初次使用无溶剂复合工艺时,或无溶剂复合生产过程中所使用的复合基材、油墨、胶黏剂及包装成品使用条件等任一因素发生变更时,都应进行无溶剂复合工艺试验。
1.目的和内容无溶剂复合工艺试验的目的是检验无溶剂复合工艺的适用性,确认复合基材、油墨和胶黏剂等因素的符合性,确定复合产品的外观质量和使用性能,并探讨最佳的无溶剂复合工艺方案或标准。
简单地说,无溶剂复合工艺试验要解决3 个问题,即能否复合?复合后产品能否合格?如何确定批量生产的工艺条件?无溶剂复合工艺试验通常包含以下几方面内容:印刷油墨与无溶剂胶黏剂的相容性检测;复合产品外观质量检测;复合产品表面摩擦系数检测;镀铝转移检测;其他使用性能检测;涂胶量、混配比、设备参数、固化温度、固化时间等生产工艺参数的确定。
无溶剂复合工艺三大技术风险,有什么控制要点
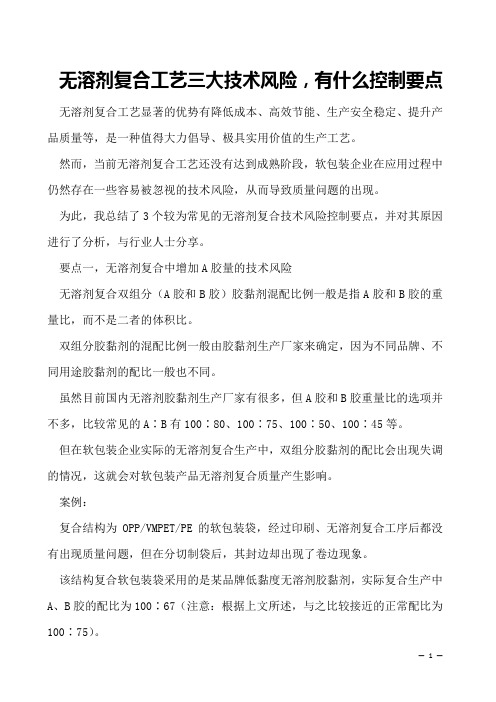
无溶剂复合工艺三大技术风险,有什么控制要点无溶剂复合工艺显著的优势有降低成本、高效节能、生产安全稳定、提升产品质量等,是一种值得大力倡导、极具实用价值的生产工艺。
然而,当前无溶剂复合工艺还没有达到成熟阶段,软包装企业在应用过程中仍然存在一些容易被忽视的技术风险,从而导致质量问题的出现。
为此,我总结了3个较为常见的无溶剂复合技术风险控制要点,并对其原因进行了分析,与行业人士分享。
要点一,无溶剂复合中增加A胶量的技术风险无溶剂复合双组分(A胶和B胶)胶黏剂混配比例一般是指A胶和B胶的重量比,而不是二者的体积比。
双组分胶黏剂的混配比例一般由胶黏剂生产厂家来确定,因为不同品牌、不同用途胶黏剂的配比一般也不同。
虽然目前国内无溶剂胶黏剂生产厂家有很多,但A胶和B胶重量比的选项并不多,比较常见的A∶B有100∶80、100∶75、100∶50、100∶45等。
但在软包装企业实际的无溶剂复合生产中,双组分胶黏剂的配比会出现失调的情况,这就会对软包装产品无溶剂复合质量产生影响。
案例:复合结构为OPP/VMPET/PE的软包装袋,经过印刷、无溶剂复合工序后都没有出现质量问题,但在分切制袋后,其封边却出现了卷边现象。
该结构复合软包装袋采用的是某品牌低黏度无溶剂胶黏剂,实际复合生产中A、B胶的配比为100∶67(注意:根据上文所述,与之比较接近的正常配比为100∶75)。
在分析故障原因时,发现袋子卷边的同时还伴随内层胶黏剂不干的现象。
原本以为是复合膜熟化程度不完全所致,后延长熟化时间再进行分切制袋,袋子卷边问题依然存在,且开口性也严重变差。
在干式复合工艺中存在“提高固化剂(-NCO组分)可以提高复合强度”的说法,行业人士很容易将这种思路也“复制”到无溶剂复合工艺中,从而导致了较严重的质量事故。
事实上,在无溶剂复合工艺中,无论是-OH过量还是-NCO过量,都可能导致无溶剂胶黏剂不干的现象,只是-OH过量造成的是永久性不干,而-NCO过量造成的是短暂性不干,其还可以与空气中的水分子发生反应而继续固化。
无溶剂复合工艺--控制要点
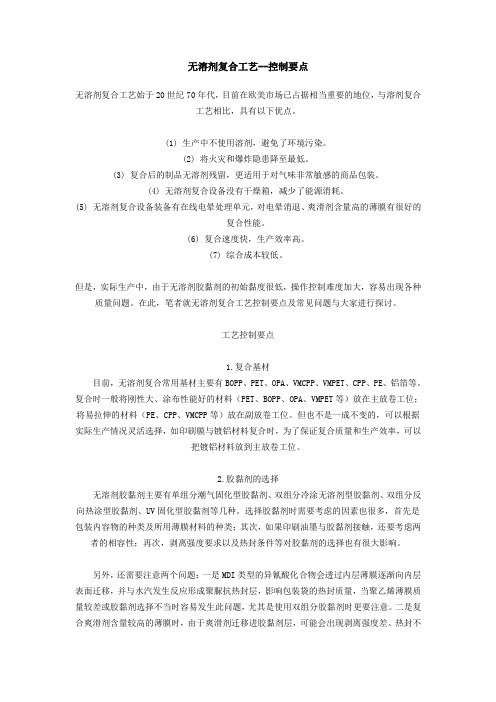
无溶剂复合工艺--控制要点无溶剂复合工艺始于20世纪70年代,目前在欧美市场已占据相当重要的地位,与溶剂复合工艺相比,具有以下优点。
(1) 生产中不使用溶剂,避免了环境污染。
(2) 将火灾和爆炸隐患降至最低。
(3) 复合后的制品无溶剂残留,更适用于对气味非常敏感的商品包装。
(4) 无溶剂复合设备没有干燥箱,减少了能源消耗。
(5) 无溶剂复合设备装备有在线电晕处理单元,对电晕消退、爽滑剂含量高的薄膜有很好的复合性能。
(6) 复合速度快,生产效率高。
(7) 综合成本较低。
但是,实际生产中,由于无溶剂胶黏剂的初始黏度很低,操作控制难度加大,容易出现各种质量问题。
在此,笔者就无溶剂复合工艺控制要点及常见问题与大家进行探讨。
工艺控制要点1.复合基材目前,无溶剂复合常用基材主要有BOPP、PET、OPA、VMCPP、VMPET、CPP、PE、铝箔等。
复合时一般将刚性大、涂布性能好的材料(PET、BOPP、OPA、VMPET等)放在主放卷工位;将易拉伸的材料(PE、CPP、VMCPP等)放在副放卷工位。
但也不是一成不变的,可以根据实际生产情况灵活选择,如印刷膜与镀铝材料复合时,为了保证复合质量和生产效率,可以把镀铝材料放到主放卷工位。
2.胶黏剂的选择无溶剂胶黏剂主要有单组分潮气固化型胶黏剂、双组分冷涂无溶剂型胶黏剂、双组分反向热涂型胶黏剂、UV固化型胶黏剂等几种。
选择胶黏剂时需要考虑的因素也很多,首先是包装内容物的种类及所用薄膜材料的种类;其次,如果印刷油墨与胶黏剂接触,还要考虑两者的相容性;再次,剥离强度要求以及热封条件等对胶黏剂的选择也有很大影响。
另外,还需要注意两个问题:一是MDI类型的异氰酸化合物会透过内层薄膜逐渐向内层表面迁移,并与水汽发生反应形成聚脲抗热封层,影响包装袋的热封质量,当聚乙烯薄膜质量较差或胶黏剂选择不当时容易发生此问题,尤其是使用双组分胶黏剂时更要注意。
二是复合爽滑剂含量较高的薄膜时,由于爽滑剂迁移进胶黏剂层,可能会出现剥离强度差、热封不良、摩擦系数增大等问题,影响其在包装生产线上的操作性。
无溶剂胶复合工艺三大异常现象的处理对策,简单实用!

无溶剂胶复合工艺三大异常现象的处理对策,简单实用!本文详细分析了无溶剂复合工艺中常见的纸塑脱离、镀铝转移、气泡等质量问题出现的原因,并介绍了相应的解决方法,希望能为使用无溶剂复合工艺的生产企业带来一些技术借鉴。
一、纸塑脱离现象纸塑脱离现象主要表现为复合膜剥离强度不足,胶不干,纸张印刷品与塑料薄膜上面的胶粘层脱离。
此现象容易在印刷面积比较大及大实地产品中出现。
因表面油墨层较厚,胶水难以润湿、扩散、渗透。
1、主要原因影响纸塑脱离的因素有许多,纸张的平滑度、匀度、含水量、塑料薄膜的各项性能、印品墨层的厚薄度、辅助材料用量、纸塑复合时的温度与压力、生产环境卫生状况以及温度、相对湿度等都会对纸塑复合的最终结果产生一定影响。
2、处理方法(1)油墨的墨层太厚,造成胶粘剂的渗透和扩散,使得纸塑脱离。
处理方法是增加胶粘剂的涂布量以及增加压力。
(2)墨层未干或未干透时,墨层中残留溶剂的成分使粘合力减弱形成纸塑脱离。
处理方法是等产品油墨干透后,再进行复合。
(3)印刷品表面残留的喷粉也会阻碍纸张与塑料薄膜的粘合形成纸塑脱离。
处理方法是利用机械和人工方式擦除印刷品表面的粉质后再复合。
4)操作工艺不规范、压力偏小,机速较快,导致纸塑脱离。
处理方法是严格按工艺规范操作,适当增加覆膜的压力、降低机速。
(5)胶粘剂被纸张及印刷油墨吸收,涂布量不足引起的纸塑脱离。
应对胶粘剂重新配方和按厂家要求确定上胶量。
(6)塑料薄膜表面电晕处理不够或超过使用期,使处理面失效引起的纸塑脱离。
应按薄膜覆膜的电晕标准对塑料基材电晕或更新塑料薄膜。
(7)在使用单组分胶粘剂时,因空气湿度不足引起的纸塑脱离,则应根据单组分胶粘剂加工工艺的湿度要求,进行人工加湿。
(8)确保胶粘剂在保质期内,并按生产厂家要求保管和使用,如双组分自动混胶机处于良好状态,保证配比的准确、均匀、充分。
二、镀铝转移现象镀铝膜既有塑料薄膜的特性,又在某种程度上替代了铝箔,起到提高产品档次的作用,而且相对成本较低。
无溶剂复合机生产工艺流程
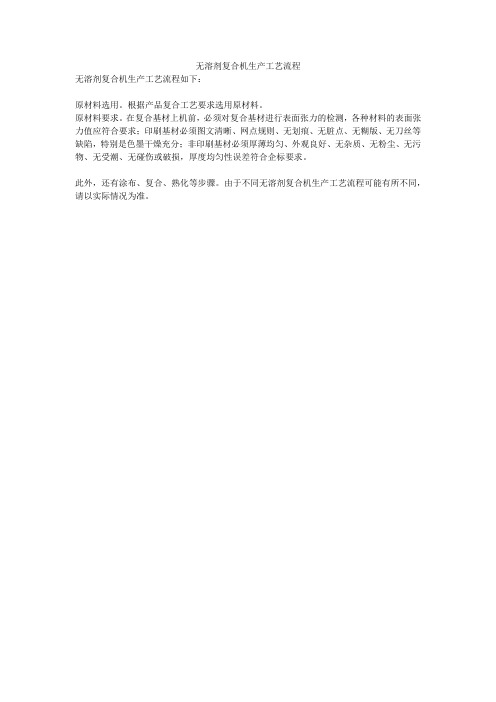
无溶剂复合机生产工艺流程
无溶剂复合机生产工艺流程如下:
原材料选用。
根据产品复合工艺要求选用原材料。
原材料要求。
在复合基材上机前,必须对复合基材进行表面张力的检测,各种材料的表面张力值应符合要求;印刷基材必须图文清晰、网点规则、无划痕、无脏点、无糊版、无刀丝等缺陷,特别是色墨干燥充分;非印刷基材必须厚薄均匀、外观良好、无杂质、无粉尘、无污物、无受潮、无碰伤或破损,厚度均匀性误差符合企标要求。
此外,还有涂布、复合、熟化等步骤。
由于不同无溶剂复合机生产工艺流程可能有所不同,请以实际情况为准。
无溶剂复合工艺关键控制点

无溶剂复合工艺关键控制点一、无溶剂复合工艺的概述无溶剂复合工艺是指在制备复合材料时不使用任何有机溶剂,通过物理或化学方法将两种或多种材料组合成一种新的材料。
该工艺具有环保、高效、节能等优点,越来越受到人们的关注和重视。
二、无溶剂复合工艺的步骤1.原材料准备首先需要准备好所需的原材料,包括基础材料和添加剂等。
基础材料可以是纤维素类、聚酰胺类、聚碳酸酯类等不同类型的高分子材料;添加剂可以是增强剂、填充剂、稳定剂等。
2.预处理预处理包括去除原材料表面污染、调整原材料粒度大小等步骤。
这个步骤可以通过机械研磨或化学清洗等方式进行。
3.混合将预处理好的原材料按比例混合均匀,确保每个组成部分在混合过程中都得到充分地分散和悬浮。
4.挤出将混合好的物质通过挤出机进行挤出,形成所需的形状和尺寸。
这个过程中需要控制挤出速度和温度,确保物质能够均匀地流动。
5.固化将挤出的物质放置在恰当的温度下进行固化。
这个过程中需要控制温度和时间,确保物质可以充分反应并且达到所需的强度和硬度。
6.加工将固化后的复合材料进行后续加工,如切割、打孔、磨削等,以满足不同应用场景下的要求。
三、无溶剂复合工艺的关键控制点1.原材料选择选择适合自己产品要求的原材料非常重要。
不同类型的高分子材料具有不同的特性,需要根据实际情况进行选择。
同时,在选择添加剂时也需要考虑其对基础材料性能影响。
2.混合均匀度混合是影响复合材料性能的重要因素之一。
如果混合不均匀,会导致复合材料强度低、韧性差等问题。
因此,在混合过程中需要掌握好比例,并采用适当的混合方式。
3.挤出速度和温度挤出过程中需要控制挤出速度和温度,以确保物质能够均匀地流动,并且不会产生气泡、缺陷等问题。
4.固化温度和时间固化过程中需要控制温度和时间,以确保物质可以充分反应并且达到所需的强度和硬度。
如果固化不足或者过度,都会影响复合材料的性能。
5.后续加工后续加工是为了满足不同应用场景下的要求。
在进行后续加工时需要注意刀具选择、切割方式等因素,以避免对复合材料造成损伤。
蒸煮包装采用无溶剂复合工艺

蒸煮包装采用无溶剂复合工艺,关键都在这蒸煮型无溶剂复膜胶的技术还没有完全成熟,而同时无溶剂复合应用于蒸煮包装也存在一些瓶颈和关键控制点,本文针对这些问题做一些初步的探讨和分析,以供参考。
1、环境的控制无溶剂复合(包括通用产品和蒸煮产品的复合)对生产的环境要求很高环境卫生方面要求:生产车间、蚊虫等,干式复合设备卫生方面要求。
确保无溶剂复合机上所有胶辊、钢辊及设备其他部件表面干净、无污渍。
温度方面要求:胶粘剂的操作温度必须严格按照产品的使用说明书进行操作。
温度过高会造成反应速度过快,缩短操作时间,并且会造成胶粘剂初始粘度较低,上胶困难-温度过低,会造成胶粘剂粘度较高不便于操作。
环境湿度的要求:要求环境湿度控制在合理的范围内,一般控制在相对湿度30% - 70%(或根据各胶粘剂生产厂家的技术指导书),环境湿度控制不好,对耐蒸煮无溶剂复合有着致命的影响(蒸煮材料很多使用尼龙材料,而尼龙极易吸潮),对复合产品的外观、剥离强度甚至最终的耐蒸煮性能都会产生负面的影响。
2、上胶量的控制应根据印刷油墨的厚度、包装内容物的要求、基材薄膜的种类及现场的复合外观调整上胶量。
上胶量控制不好不仅会影响产品的外观,还会影响其最终的剥离强度和耐蒸煮性能。
无溶剂蒸煮的上胶量一般控制在1.8-2.2 g/㎡,对于印刷油墨面积较小的材料,上胶量可以少一些,对于印刷油墨面积较大或者内容物为辛辣、麻辣及油腻的产品时,应适当增加上胶量。
在小试试验时,可以试验两三个不同的上胶墨进行试验,以供选择出最优的工艺。
3、熟化条件的控制应该在胶粘剂生产厂家提供的熟化温度、时间范围内进行熟化,熟化温度、时间不够会严重影响产品最终的耐蒸煮性能。
熟化过程,通常要求一次性熟化完成,避免没有完全熟化就进行测试、试验,发现没有熟化完全后,再重新放回熟化时进行二次熟化,这样会影响产品的最终性能。
通常情况下,熟化条件控制在40~50℃条件下48~72h,具体需根据胶粘剂生产厂家的技术指导书进行控制。
无溶剂复合工艺与干式复合工艺应用差异谈

无溶剂复合工艺与干式复合工艺应用差异谈【内容提要】干式复合是一项成熟的复合技术,是我国软包装行业的主导复合工艺,然而,在生产过程中,干式复合工艺需要使用大量的溶剂型胶黏剂,由此产生的溶剂挥发与溶剂残留在所难免,导致干式复合工艺在环境保护、卫生安全和综合成本等方面颇为受制。
干式复合是一项成熟的复合技术,是我国软包装行业的主导复合工艺,然而,在生产过程中,干式复合工艺需要使用大量的溶剂型胶黏剂,由此产生的溶剂挥发与溶剂残留在所难免,导致干式复合工艺在环境保护、卫生安全和综合成本等方面颇为受制。
目前,一些发达国家和地区已经逐渐淘汰或局限在某一特定情况下使用干式复合工艺。
在这样的背景下,无溶剂复合工艺迎来了最佳发展机遇。
无溶剂复合是一项绿色复合技术,代表着复合工艺未来的发展方向,在一些发达国家和地区已经得到普遍应用。
然而,在不少国家和地区这种复合工艺还属于一种新型工艺,尚未受到广泛关注和应用,我国亦是如此。
一些初次使用无溶剂复合工艺的软包装企业往往简单地认为无溶剂复合设备只是干式复合设备的一种简化型式,而忽略了这两种复合工艺的本质区别,易导致在实际生产中不能有效把握无溶剂复合工艺的控制要点,从而大大提高了废品率。
笔者认为,在实际应用中,无溶剂复合工艺与干式复合工艺相比,在技术原理、工艺控制、外观质量、适用范围等方面大有不同,要想成功应用无溶剂复合工艺,软包装企业的管理和技术人员必须全面理解二者之间的差异。
技术原理之差异无溶剂复合工艺与干式复合工艺在技术原理上的差异是较大的,主要体现在涂布方式、涂胶膜和复合牢度形成机理,以及干燥、冷却、固化等工序的作用和要求方面。
(1)涂布方式干式复合工艺采用的是凹辊涂布方式;胶层较厚,表面呈凹凸(波峰)状,厚薄极不均匀;涂布量主要由凹辊网线数决定,只能通过更换凹辊进行有限调整。
无溶剂复合工艺采用的是多辊转移涂布方式;胶层薄,厚薄均匀;涂布量主要由各辊转速决定,可在线无级调整。
无溶剂复合工艺的最新技术

无溶剂复合工艺的最新技术无溶剂复合工艺是一种环保、高效的复合技术,在纺织、电子、医疗器械等领域有广泛应用。
最新的无溶剂复合技术主要集中在以下几个方面:1. 研发新型无溶剂复合剂:目前,研发更环保且性能卓越的无溶剂复合剂是研究的热点之一。
例如,采用有机溶剂替代传统的有害溶剂,以减少对环境和人体的危害;开发纳米颗粒复合剂,提高复合物的力学性能和耐久性。
2. 优化复合工艺参数:通过对复合工艺参数进行优化调整,可以获得更好的复合效果。
例如,通过改变复合压力、温度和时间等参数,可以控制复合材料的厚度、孔隙率和结晶度,以及减少杂质和缺陷的生成。
3. 应用新型复合设备:新型无溶剂复合设备的引入也推动了无溶剂复合技术的发展。
例如,采用微波辅助复合、超声波辅助复合和等离子体辅助复合等新型设备,可以提高复合速度和复合质量,并降低能耗。
4. 开展混合复合技术研究:混合复合技术是无溶剂复合技术的一个新的研究方向。
将无溶剂复合技术与其他复合技术相结合,如热压、熔融和胶粘等,可以制备具有多种功能的复合材料。
例如,将无溶剂复合与热压技术相结合,可以在复合过程中实现与材料的填充、熔融和热固化等多个过程的一体化。
5. 应用无溶剂复合技术制备新型材料:无溶剂复合技术不仅适用于传统材料的制备,还可以用于制备新型功能材料。
例如,在电子领域,利用无溶剂复合技术可以制备高性能的导电复合材料、柔性电路和导热材料。
在医疗器械领域,也可以利用无溶剂复合技术制备具有生物相容性和生物活性的医用材料。
综上所述,无溶剂复合工艺的最新技术主要包括研发新型无溶剂复合剂、优化复合工艺参数、应用新型复合设备、开展混合复合技术研究以及应用无溶剂复合技术制备新型材料。
这些技术的不断进步和发展将进一步推动无溶剂复合技术在各个领域的应用。
无溶剂复合工艺简介

无溶剂复合工艺简介【内容提要】无溶剂复合工艺始于20世纪70年代,目前在欧美市场已占据相当重要的地位,与溶剂复合工艺相比,具有以下优点(1)生产中不使用溶剂,避免了环境污染。
(2)将火灾和爆炸隐患降至最低。
(3)复合后的制品无溶剂残留,更适用于对气味非常敏感的商品包装。
无溶剂复合工艺始于20世纪70年代,目前在欧美市场已占据相当重要的地位,与溶剂复合工艺相比,具有以下优点。
(1)生产中不使用溶剂,避免了环境污染。
(2)将火灾和爆炸隐患降至最低。
(3)复合后的制品无溶剂残留,更适用于对气味非常敏感的商品包装。
(4)无溶剂复合设备没有干燥箱,减少了能源消耗。
(5)无溶剂复合设备装备有在线电晕处理单元,对电晕消退、爽滑剂含量高的薄膜有很好的复合性能。
(6)复合速度快,生产效率高。
(7)综合成本较低。
但是,实际生产中,由于无溶剂胶黏剂的初始黏度很低,操作控制难度加大,容易出现各种质量问题。
在此,笔者就无溶剂复合工艺控制要点及常见问题与大家进行探讨。
工艺控制要点1.复合基材目前,无溶剂复合常用基材主要有BOPP、PET、OPA、VMCPP、VMPET、CPP、PE、铝箔等。
复合时一般将刚性大、涂布性能好的材料(PET、BOPP、OPA、VMPET等)放在主放卷工位;将易拉伸的材料(PE、CPP、VMCPP等)放在副放卷工位。
但也不是一成不变的,可以根据实际生产情况灵活选择,如印刷膜与镀铝材料复合时,为了保证复合质量和生产效率,可以把镀铝材料放到主放卷工位。
2.胶黏剂的选择无溶剂胶黏剂主要有单组分潮气固化型胶黏剂、双组分冷涂无溶剂型胶黏剂、双组分反向热涂型胶黏剂、UV固化型胶黏剂等几种。
选择胶黏剂时需要考虑的因素也很多,首先是包装内容物的种类及所用薄膜材料的种类;其次,如果印刷油墨与胶黏剂接触,还要考虑两者的相容性;再次,剥离强度要求以及热封条件等对胶黏剂的选择也有很大影响。
另外,还需要注意两个问题:一是MDI类型的异氰酸化合物会透过内层薄膜逐渐向内层表面迁移,并与水汽发生反应形成聚脲抗热封层,影响包装袋的热封质量,当聚乙烯薄膜质量较差或胶黏剂选择不当时容易发生此问题,尤其是使用双组分胶黏剂时更要注意。
无溶剂复合工艺中常见的异常现象,原因及解决方法

无溶剂复合工艺中常见的异常现象,原因及解决方法随着广大消费者对食品药品包装的卫生要求不断提高,国内包装行业的环保标准更加严格,无溶剂复合作为一种绿色环保工艺,正被越来越多的国内软包装印刷企业所采用。
但无溶剂复合在我国的应用还处于初步阶段,初用无溶剂复合的企业和人员,由于经验的原因,在工艺实施中同样会遇到这样或那样的工艺异常问题,但这些都是有其成因并可以解决的。
本文就近几年来我们对无溶剂复合工艺的探索过程中的心得,以及常遇到的工艺异常现象,其原因分析和解决办法,与大家共同分享。
一、在生产操作层面应关注的几个环节与溶剂型干式复合相比,无溶剂复合具有“初粘力低、涂布量较小、固化时间较长”等特点,因此,在实际生产操作时,应真正了解和掌握无溶剂复合工艺、设备特点,关注几个关键环节,以减少或消除质量事故。
一是针对无溶剂复合“初粘力低”的特点,生产操作中应特别注意对料带张力匹配性、收卷张力和压力的调控。
二是针对无溶剂复合“涂布量较小”的特点,应特别注意对涂布均匀性、复合均匀性、收卷的松紧度控制。
三是针对无溶剂复合“固化时间较长”的特点,应敏感地认识到固化过程其实是双组份胶水的反应过程,该进程对复合质量有较大的影响。
因此,应特别注意固化条件(如温度、湿度、环境)的设定,并对固化过程进行监控。
四是在使用双组分无溶剂胶黏剂时,应特别关注胶水混配比的设定和监控,对双组分自动混胶机正确使用、维护保养,确保其始终处于良好状态尤为重要。
此外,对新的复合结构坚持进行涵盖“参数确定、剥离强度、胶水/油墨/材料的相容性、热封制袋、摩擦系数变化”等内容的工艺试验,“工艺试验一一小批量试生产一一批量生产”的流程应成为一种工作制度。
二、若干工艺异常现象的原因剖析和解决方法-)关于复合产品中出现“点”的现象与干法复合工艺一样,无溶剂复合工艺实施中,复合膜出现“点”是比较常见的异常现象。
产生“点”其成因不外有物理原因和化学原因。
但物理原因造成的“点”和化学原因造成的“点”无论从外在表象、形成机理和解决办法都不同。
无溶剂复合工艺

SF复合工艺特点
不使用溶剂,避免环境污染 最低火灾和爆炸隐患 复合后制品无溶剂残留 复合设备无需干燥箱,减少能源消耗 在线电晕处理单元,对电晕消退、爽 滑剂含量高的薄膜有很好的复合性能 复合速度快,生产效率高 综合成本低
3
• 对设备的依赖性比较大, 主要 依赖进口
• 初粘力低,对张力的控制很关 键
测试条件
1. 1/10000或 1/1000 电子分析天平 2. 10 x 10 cm的取样板 3. 纸巾 / 刀 4. EAC试剂
12
调整涂布量
1. 调整速比 2. 调整涂胶缝隙
张力控制 Surface tension
N/15mm
1.6
1.4
1.2
1
0.8
1.5
0.6
0.4
0.2
0
溶剂型
无溶剂
0.01 0.35 40°C 70°C
1 检查并确认正确的混合比例 2 确认设备干净 3 注意盘寿命 4 确认压力正常 5 检测涂布量 6检测张力匹配 7检验温度 8 控制熟化条件
– 根据 PDS – 应该同新的一样 / 各辊筒 – 20 ~ 30分钟 – 压力 / 压力平衡
– 1.5 ~ 2.5 g / m2 视不同结构
– 没有或轻微卷曲 / 收卷 锥度张力 – 使用测温仪 / 温度确认后 / 调整缝隙 – 40C ~ 50C / 48小时
= 抹布/ 浸 EA
- 旋转滚筒,抹布从左到右缓慢移动并施以稳固的压力。 - 加快移动抹布,从左到右,用一定的时间来达到理想的清洗效果。 - 一块抹布只用一次。
-- 清洗后的滚筒应该象新的一样
21
工艺控制要点 – 复合基材
• 常用基材 BOPP、PET、OPA、VMCPP、VMPET、CPP、
- 1、下载文档前请自行甄别文档内容的完整性,平台不提供额外的编辑、内容补充、找答案等附加服务。
- 2、"仅部分预览"的文档,不可在线预览部分如存在完整性等问题,可反馈申请退款(可完整预览的文档不适用该条件!)。
- 3、如文档侵犯您的权益,请联系客服反馈,我们会尽快为您处理(人工客服工作时间:9:00-18:30)。
小结:贴合型复合工艺将两种不同的基材贴合 而生产复合薄膜,适应面极广,理论上可用于任何 两种基材贴合而生产如何结构的复合薄膜,但实际 上由于挤出复合与热熔胶复合,依靠的是物理结合, 层间粘合力强度收到限制,因此一般只用于生产复 合强度要求较低的产品;湿法复合在贴合之后,需 要通过基材排除溶剂型粘合剂中的溶剂(或乳液型 粘合剂中的分散液),使粘合剂的干燥,才能得到 最终的复合制品,只适用于至少一个具有疏松结构 的基材(比如纸张)的复合,应用面受到极大的限 制,在贴合型复合工艺中惟有干法复合、无溶剂 复合是目前真正应用面广、应用量极大的两种复 合工艺。
3、贴合型复合工艺 贴合型复合工艺,指应用粘合的方法,将两基材贴(粘)合而 生产复合薄膜的方法,包括挤出复合、热熔胶复合、干法复合、湿 法复合、无溶剂复合等等 挤出复合:使用挤出机将热塑性塑料熔融,然后经过T型模头, 流淌涂覆在一基材薄膜的表面上,趁热将另一基膜压贴在它的上面 而生产复合薄膜的工艺。 热熔胶复合:采用熔胶池(或者挤出机)使热熔胶熔融,再通 过辊涂(或T模头)涂布到一基膜表面上,趁热将另一基材贴合到 其上面而生产复合薄膜的工艺。 干法复合:将溶剂型化学反应性胶粘剂涂布在一基材薄膜的表 面,然后干燥挥发胶中的溶剂,再与另一基材薄膜贴合,经化学反 应(熟化)而生产复合薄膜的工艺; 湿式复合:将溶剂型化学反应性胶粘剂涂布一基材薄膜的表面,随 即使其上贴合另一基膜,然后使胶粘剂干燥、固化而生产复合薄膜 的工艺。 无溶剂复合:将无溶剂型化学反应性胶粘剂涂布一基材薄膜的 表面,随即使其上贴合另一基膜,然后使胶粘剂熟化而生产复合薄 膜的工艺。
复合薄膜的常用工艺盘点
• 复合薄膜的常用工艺有三个大类,即共挤 出、表面涂覆和贴(粘)合型复合三个大 类。
1、共挤出复合:使用两台和两台以上的挤出机将 塑料熔融体,供入一个共挤出模头中,在共挤出模内 分层汇合后从模唇挤出,从而生产多层复合薄膜的方 法; 共挤出复合的突出优点是直接由塑料粒子生产复 合薄膜,工艺路线短、能耗小且可把价格昂贵的塑料 层做得很薄(比如2μ左右),降低生产成本; 它在生产过程中,不产生任何有毒有害物质,是 典型的清洁化生产工艺,是一种值得大力倡导的复合 工艺。 共挤出复合的两大局限: ⑴它只能生产全部由热塑性塑料生产的塑料复合 薄膜; ⑵它只能生产表面印刷的复合薄膜而不能生产里 印的复合薄膜;
4、可明显地降低生产成本 ⑴无溶剂复合单位面积上胶量少,上胶成本低,有 望节约粘合剂成本30 % ~50%(无溶剂复合单位 面积胶粘剂用量约为干法复合单位面积胶粘剂干基 涂布量2/5~1/2,且不耗用溶剂); ⑵无溶剂复合一次性投资少,设备回收折旧成本也 比较小(复合设备没有预干燥烘道,设备造价较低, 可降低30%或者更多;设备占地面积小,可明显降 低车间面积;无溶剂复合黏合剂的体积小且不用储 藏溶剂,可以减少仓储面积;); ⑶无溶剂复合,节能显著 ; ⑷无溶剂复合生产线速度明显提高,因而可以使生 产成本降低; ⑸无溶剂复合不需治理三废
无溶剂复合较之干法复合的的主要优点 1、安全、卫生性好 无溶剂复合生产中不使用可燃、易爆性有机溶剂,故安全性 好;复合薄膜中不会因残余溶剂的存在导致卫生性能下降, 产品卫生性能可靠性佳。 2、环保适应性好 无溶剂复合使用的胶粘剂是百分之百的胶,不含任何溶剂, 因而在生产过程中,除停机时需要用少量溶剂对涂胶部分进 行清洗之外,没有溶剂排放,生产中没有三废物质产生,不 会由于大量溶剂的排放影响生产工人的身体健康,也不会对 周边环境产生污染,有利于清洁化生产。 3、节约资源显著: 不使用溶剂; 没有烘道干燥过程,可节约大量能源; 上胶料少:无溶剂复合单位面积胶粘剂涂布量约为干法复合 单位面积胶粘剂干基涂布量的五分之二;
2、表面涂覆型复合工艺 表面涂覆型复合工艺,包括挤出涂敷、溶液(或乳液)涂布、 热熔胶涂布与蒸镀等工艺。 挤出涂敷:使用挤出机将热塑性塑料熔融,然后经过T型模头, 流淌涂覆在一基材薄膜的表面上而生产复合薄膜的工艺。 溶液(或乳液)涂布:该法将所溶液(或乳液)涂布到基材的 表面,然后干燥而生产复合薄膜的工艺。 热熔胶涂布:采用熔胶池(或者挤出机)使热熔胶熔融,再通 过辊涂(或T模头)涂布到一基膜表面上而生产复合薄膜的工 艺。 蒸镀亦称喷涂:在高真空条件下使铝或低沸点的氧化物挥发 (或者通过化学反应形成等离子体)、再使之沉积于基材的表 面,形成致密的涂层而生产复合薄膜的工艺。 表面涂覆型复合工艺,可以通过在基材的表面,涂覆一层薄薄 的涂层,甚至于纳米级的涂层,达到复合改性的目的,但局限 性较大,除用于生产一些特定的复合薄膜(如表面保护膜)等 终端产品之外,大量用于生产复合薄膜的基材。
无溶剂复合与干法复合两种工艺的工艺过程的比较: 无溶剂复合: 基材1→放卷→涂胶(涂无溶剂型胶粘剂)→贴合→收卷→ ↑ 放卷 ↑ 基材2 熟化→成品 干法复合 : 基材1→放卷→涂胶(涂溶剂型胶粘剂)→烘道干燥→贴合→ ↑ 放卷 ↑ 基材2 收卷→熟化→成品
两种工艺的相同之处在于:它们都是利用粘 合剂,将两种膜状基材粘合而制取复合薄膜,由于 在复合过程中有粘合剂的熟化过程(化学反应), 粘合效果较好、层间复合牢度较高,对基材的适应 好、应用面广。 两种工艺之间,也有一个“细微的”差别, 即干法复合工艺使用的是溶剂型(或水分散型)黏 合剂,在生产复合软包装材料的过程中,涂胶以后 两基材贴合(复合)之前 ,需要把粘合剂中的溶 剂(或分散剂水)烘干;而无溶剂复合工艺使用的 是无溶剂粘合剂,涂胶以后两基材不经过烘干处理, 即将两基材贴合(复合),也正因为这一“微小的 差异”,无溶剂复合较之干法复合,呈现出一系列 突出的优点。
无溶剂复合工艺
中包联塑料委专家委员会副主任兼秘书长 上海市包协会绿色包装委员会秘书长 陈昌杰
无溶剂复合是经典的、成熟的、常 用的一种生产复合薄膜的工艺;
• 西德Herbert公司继上世纪六十年初期干法复合工 艺产业化之后,即开始了无溶剂复合的研究,并 于1974年推出了无溶复合工艺,自二十世纪八十 年代以后,逐渐成为欧洲工业发达国家的塑料剂复合生 产线,经历了漫长的孕育期,至2008年全国仅30 来条生产线,2008年以后,有了飞速的发展,目 前无溶剂复合生产线已发展到100条左右。