土木工程类外文文献翻译.d
土木工程专业毕业设计外文文献及翻译
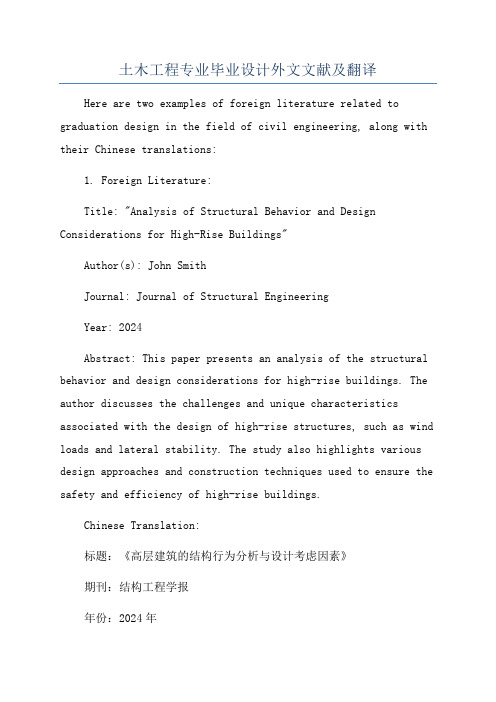
土木工程专业毕业设计外文文献及翻译Here are two examples of foreign literature related to graduation design in the field of civil engineering, along with their Chinese translations:1. Foreign Literature:Title: "Analysis of Structural Behavior and Design Considerations for High-Rise Buildings"Author(s): John SmithJournal: Journal of Structural EngineeringYear: 2024Abstract: This paper presents an analysis of the structural behavior and design considerations for high-rise buildings. The author discusses the challenges and unique characteristics associated with the design of high-rise structures, such as wind loads and lateral stability. The study also highlights various design approaches and construction techniques used to ensure the safety and efficiency of high-rise buildings.Chinese Translation:标题:《高层建筑的结构行为分析与设计考虑因素》期刊:结构工程学报年份:2024年2. Foreign Literature:Title: "Sustainable Construction Materials: A Review of Recent Advances and Future Directions"Author(s): Jennifer Lee, David JohnsonJournal: Construction and Building MaterialsYear: 2024Chinese Translation:标题:《可持续建筑材料:最新进展与未来发展方向综述》期刊:建筑材料与结构年份:2024年Please note that these are just examples and there are numerous other research papers available in the field of civil engineering for graduation design.。
土木工程英文文献及翻译-英语论文.doc
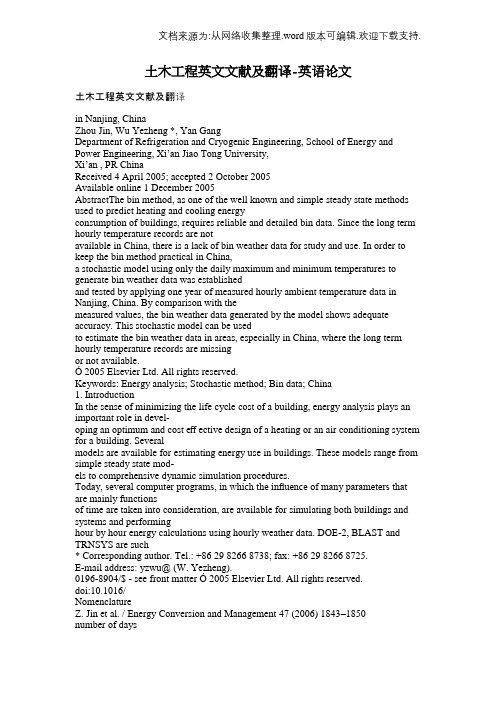
土木工程英文文献及翻译-英语论文土木工程英文文献及翻译in Nanjing, ChinaZhou Jin, Wu Yezheng *, Yan GangDepartment of Refrigeration and Cryogenic Engineering, School of Energy and Power Engineering, Xi’an Jiao Tong University,Xi’an , PR ChinaReceived 4 April 2005; accepted 2 October 2005Available online 1 December 2005AbstractThe bin method, as one of the well known and simple steady state methods used to predict heating and cooling energyconsumption of buildings, requires reliable and detailed bin data. Since the long term hourly temperature records are notavailable in China, there is a lack of bin weather data for study and use. In order to keep the bin method practical in China,a stochastic model using only the daily maximum and minimum temperatures to generate bin weather data was establishedand tested by applying one year of measured hourly ambient temperature data in Nanjing, China. By comparison with themeasured values, the bin weather data generated by the model shows adequate accuracy. This stochastic model can be usedto estimate the bin weather data in areas, especially in China, where the long term hourly temperature records are missingor not available.Ó 2005 Elsevier Ltd. All rights reserved.Keywords: Energy analysis; Stochastic method; Bin data; China1. IntroductionIn the sense of minimizing the life cycle cost of a building, energy analysis plays an important role in devel-oping an optimum and cost effective design of a heating or an air conditioning system for a building. Severalmodels are available for estimating energy use in buildings. These models range from simple steady state mod-els to comprehensive dynamic simulation procedures.Today, several computer programs, in which the influence of many parameters that are mainly functionsof time are taken into consideration, are available for simulating both buildings and systems and performinghour by hour energy calculations using hourly weather data. DOE-2, BLAST and TRNSYS are such* Corresponding author. Tel.: +86 29 8266 8738; fax: +86 29 8266 8725.E-mail address: yzwu@ (W. Yezheng).0196-8904/$ - see front matter Ó 2005 Elsevier Ltd. All rights reserved.doi:10.1016/NomenclatureZ. Jin et al. / Energy Conversion and Management 47 (2006) 1843–1850number of daysfrequency of normalized hourly ambient temperatureMAPE mean absolute percentage error (%)number of subintervals into which the interval [0, 1] was equally dividednumber of normalized temperatures that fall in subintervalprobability densityhourly ambient temperature (°C)normalized hourly ambient temperature (dimensionless)weighting factorSubscriptscalculated valuemeasured valuemax daily maximummin daily minimumprograms that have gained widespread acceptance as reliable estimation tools. Unfortunately, along withthe increased sophistication of these models, they have also become very complex and tedious touse [1].The steady state methods, which are also called single measure methods, require less data and provideadequate results for simple systems and applications. These methods are appropriate if the utilization ofthe building can be considered constant. Among these methods are the degree day and bin data methods.The degree-day methods are the best known and the simplest methods among the steady state models.Traditionally, the degree-day method is based on the assumption that on a long term average, the solarand internal gains will offset the heat loss when the mean daily outdoor temperature is 18.3 °C and thatthe energy consumption will be proportional to the difference between 18.3 °C and the mean daily tempera-ture. The degree-day method can estimate energy consumption very accurately if the building use and theefficiency of the HVAC equipment are sufficiently constant. However, for many applications, at least oneof the above parameters varies with time. For instance, the efficiency of a heat pump system and HVAC equip-ment may be affected directly or indirectly by outdoor temperature. In such cases, the bin method can yieldgood results for the annual energy consumption if different temperature intervals and time periods areevaluated separately. In the bin method, the energy consumption is calculated for several values of the outdoortemperature and multiplied by the number of hours in the temperature interval (bin) centered around thattemperature. Bin data is defined as the number of hours that the ambient temperature was in each of a setof equally sized intervals of ambient temperature.In the United States, the necessary bin weather data are available in the literature [2,3]. Some researchers[4–8] have developed bin weather data for other regions of the world. However, there is a lack of informationin the ASHRAE handbooks concerning the bin weather data required to perform energy calculations in build-ings in China. The practice of analysis of weather data for the design of HVAC systems and energy consump-tion predictions in China is quite new. For a long time, only the daily value of meteorological elements, such asdaily maximum, minimum and average temperature, was recorded and available in most meteorologicalobservations in China, but what was needed to obtain the bin weather data, such as temperature bin data,were the long term hourly values of air temperature. The study of bin weather data is very limited in China.Only a few attempts [9,10] in which bin weather data for several cities was given have been found in China.Obviously, this cannot meet the need for actual use and research. So, there is an urgent need for developing binweather data in China. The objective of this paper, therefore, is to study the hourly measured air temperaturedistribution and then to establish a model to generate bin weather data for the long term daily temperaturedata.2. Data usedZ. Jin et al. / Energy Conversion and Management 47 (2006) 1843–1850In this paper, to study the hourly ambient temperature variation and to establish and evaluate the model, aone year long hourly ambient temperature record for Nanjing in 2002 was used in the study. These data aretaken from the Climatological Center of Lukou Airport in Nanjing, which is located in the southeast of China(latitude 32.0°N, longitude 118.8°E, altitude 9 m).In addition, in order to create the bin weather data for Nanjing, typical weather year data was needed.Based on the long term meteorological data from 1961 to 1989 obtained from the China MeteorologicalAdministration, the typical weather year data for most cities in China has been studied in our former research[11] by means of the TMY (Typical Meteorological Year) method. The typical weather year for Nanjing isshown in Table 1. As only daily values of the meteorological elements were recorded and available in China,the data contained in the typical weather year data was also only daily values. In this study, the daily maxi-mum and minimum ambient temperature in the typical weather year data for Nanjing was used.3. Stochastic model to generate bin dataTraditionally, the generation of bin weather data needs long term hourly ambient temperature records.However, in the generation, the time information, namely the exact time that such a temperature occurredin a day, was omitted, and only the numerical value of the temperature was used. So, the value of each hourlyambient temperature can be treated as the independent random variable, and its distribution within the dailytemperature range can be analyzed by means of probability theory.3.1. Probability distribution of normalized hourly ambient temperatureSince the daily maximum and minimum temperatures and temperature range varied day by day, the con-cept of normalized hourly ambient temperature should be introduced to transform the hourly temperatures ineach day into a uniform scale. The new variable, normalized hourly ambient temperature is defined by^ ¼ttmintmaxtminwhere ^ may be termed the normalized hourly ambient temperature, tmaxand tminare the daily maximum andminimum temperatures, respectively, t is the hourly ambient temperature. Obviously, the normalized hourly ambient temperature ^ is a random variable that lies in the interval [0, 1].To analyze its distribution, the interval [0, 1] can be divided equally into several subintervals, and by means ofthe histogram method [12]iin each subinterval can be calculated by1137土木工程英文文献及翻译Based on the one year long hourly ambient temperature data in Nanjing, China, the probability density piwas calculated for the whole day and the 08:00–20:00 period, where the interval [0, 1] was equally divided into50 subintervals, namely n equals 50. The results are shown in Fig. 1.According to the discrete probability density data in Fig. 1, the probability density function of ^ can beobtained by a fitting method. In this study, the quadratic polynomialswere used to fit the probability density data, where a, b and c are coefficients. According to the property of theprobability density function, the following equation should be satisfiedAs shown in Fig. 1, the probability density curve obtained according to the probability density data pointsis also shown. The probability densit y functions that are fitted are described byp ¼ 2:7893^23:1228^ þ 1:6316 for the whole day periodp ¼ 2:2173^20:1827^ þ 0:3522 for the 08 : 00–20 : 00 period3.2. The generation of hourly ambient temperatureAs stated in the beginning of this paper, the objective of this study is to generate the hourly ambient tem-perature needed for bin weather data generation in the case that only the daily maximum and minimum tem-peratures are known. To do this, we can use the obtained probability density function to generate thenormalized hourly ambient temperature and then transform it to hourly temperature. This belongs to theproblem of how to simulate a random variable with a prescribed probability density function and can be doneon a computer by the method described in the literature [13]. For a given probability density function f ð^Þ, ifits distribution function F ð^Þ can be obtained and if u is a random variable with uniform distribution on [0, 1],thenF, we need only setAs stated above, the probability density function of the normalized ambient temperature was fitted using aone year long hourly temperature data. Based on the probability density function obtained, the random nor-malized hourly temperature can be generated. When the daily maximum and minimum temperature areknown, the normalized hourly temperature can be transformed to an actual temperature by the followingequationWhen the hourly temperature for a particular period of the day has been generated using the above method,the bin data can also be obtained. Because the normalized temperature generated using the model in this studyis a random variable, the bin data obtained from each generation shows somedifference, but it has much sim-ilarity. To obtain a stable result of bin data, the generation of the bin data can be performed enough times,and the bin data can be obtained by averaging the result of each generation. In this paper, 50 generations wereaveraged to generate the bin weather data.Z. Jin et al. / Energy Conversion and Management 47 (2006) 1843–18503.4. Methods of model evaluationThe performance of the model was evaluated in terms of the following statistical error test:土木工程英文文献及翻译一种产生bin气象数据的随机方法——中国南京周晋摘要:bin方法是一种众所周知且简捷的稳态的计算方法,可以用来预计建筑的冷热能耗。
土木工程 外文翻译 外文文献 英文翻译

Stress Limits in DesignHow large can we permit the stresses to be? Or conversely: How large must a part be to withstand a given set of loads what are the overall conditions or limits that will determine the size and material for a part?Design limits are based on avoiding failure of the part to perform its desired function. Because different parts must satisfy different functional requirements, the conditions which limit load-carrying ability may be quite different for different elements. As an example, compare the design limits for the floor of a house with those for the wing of an airplane.If we were to determine the size of the wooden beams in a home such that they simply did not break, we would not be very happy with them; they would be too ‘springy’. Walking across the room would be like walking out on a diving board.Obviously, we should be concerned with the maximum ‘deflection’that we, as individuals, find acceptable. This level will be rather subjective, and different people will give different answers. In fact, the same people may give different answers depending on whether they are paying for the floor or not!An airplane wing structure is clearly different. If you look out an airplane window and watch the wing during turbulentweather, you will see large deflections; in fact you may wish that they were smaller. However, you know that the important issue is that of ‘structural integrity’, not deflection.We want to be assured that the wing will remain intact. We want to be assured that no matter what the pilot and the weather do, that wing will continue to act like a good and proper wing. In fact, we really want to be assured that the wing will never fail under any conditions. Now that is a pretty tall order; who knows what the ‘worst’ conditions might be?Engineers who are responsible for the design of airplane wing structures must know, with some degree of certainty, what the ‘worst’ conditions are likely to be. It takes great patience and dedication for many years to assemble enough test data and failure analyses to be able to predict the ‘worst’case. The general procedure is to develop statistical data which allow us to say how frequently a given condition is likely to be encountered—once every 1000 hours, or once every 10000 hours, etc.As we said earlier, our object is to avoid failure. Suppose, however, that a part has failed in service, and we are asked; Why? ‘Error’ as such can come from three distinctly different sources, any or all of which can cause failure:1. Error in design: We the designers or the design analysts may have been a bit too optimistic: Maybe we ignored some loads; maybe our equations did not apply or were not properly applied; maybe we overestimated the intelligence of the user; may we slipped a decimal point.2. Error in manufacture: When a device involves heavily stressed members, the effective strength of the members can be greatly reduced through improper manufacture and assembly: May the wrong material was used; maybe the heat treatment was not as specified; maybe the surface finish was not as good as called for; may a part was ‘out of tolerance’; may be surface was damaged during machining; maybe the threads were not lubricated at assembly; or perhaps the bolts were not properly tightened.3. Error in use: As we all know, we can damage almost anything if we try hard enough, and sometimes we do so accidentally: We went too fast; we lost control; we fell asleep; we were not watching the gages; the power went off; the computer crashed; he was taking a coffee break; she forgot to turn the machine off; you failed to lubricate it, etc.Any of the above can happen: Nothing is designed perfectly; nothing is made perfectly; and nothing is used perfectly. Whenfailure does occur, and we try to determine the cause, we can usually examine the design; we can usually examine the failed parts for manufacturing deficiencies; but we cannot usually determine how the device was used (or misused). In serious cases, this can give rise to considerable differences of opinion, differences which frequently end in court.In an effort to account for all the above possibilities, we design every part with a safety factor. Simply put, the safety factor (SF) is the ratio of the load that we think the part can withstand to the load we expect it to experience. The safety factor can be applied by increasing the design loads beyond those actually expected, or by designing to stress levels below those that the material actually can withstand (frequently called ‘design stresses’).Safety factor=SF=failure load/design load=failure stress/design stress It is difficult to determine an appropriate value for the safety factor. In general, we should use larger values when:1. The possible consequences of failure are high in terms of life or cost.2. There are large uncertainties in the design analyses.Values of SF generally range from a low of about 1.5 to 5 ormore. When the incentives to reduce structural weight are great (as in aircraft and spacecraft), there is an obvious conflict. Safety dictates a large SF, while performance requires a small value. The only resolution involves reduction of uncertainty. Because of extreme care and diligence in design, test, manufacture, and use, the aircraft industry is able to maintain very enviable safety records while using safety factors as low as 1.5.We might not that the safety factor is frequently called the ‘ignorance factor’. This is not to imply that engineers are ignorant, but to help instill in them humility, caution, and care. An engineer is responsible for his or her design decisions, both ethically and legally. Try to learn from the mistakes of others rather than making your own.。
土木工程专业外文文献及翻译
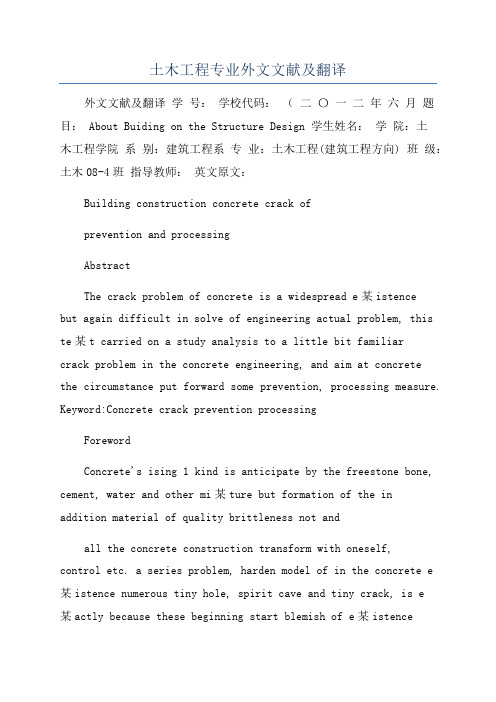
土木工程专业外文文献及翻译外文文献及翻译学号:学校代码:(二〇一二年六月题目: About Buiding on the Structure Design 学生姓名:学院:土木工程学院系别:建筑工程系专业:土木工程(建筑工程方向) 班级:土木08-4班指导教师:英文原文:Building construction concrete crack ofprevention and processingAbstractThe crack problem of concrete is a widespread e某istencebut again difficult in solve of engineering actual problem, this te某t carried on a study analysis to a little bit familiarcrack problem in the concrete engineering, and aim at concretethe circumstance put forward some prevention, processing measure. Keyword:Concrete crack prevention processingForewordConcrete's ising 1 kind is anticipate by the freestone bone, cement, water and other mi某ture but formation of the inaddition material of quality brittleness not andall the concrete construction transform with oneself,control etc. a series problem, harden model of in the concrete e某istence numerous tiny hole, spirit cave and tiny crack, is e某actly because these beginning start blemish of e某istencejust make the concrete present one some not and all the characteristic of tiny crack is a kind of harmless crack and accept concrete heavy, defend Shen and a little bit other use function not a creation to after the concrete be subjected to lotus carry, difference in temperature etc. function, tiny crack would continuously of e某pand with connect, end formation we can see without the aid of instruments of macro view the crack be also the crack that the concrete often say in the engineering.Concrete building and Gou piece usually all take sewer to make of, because of crack of e某istence and development usually make inner part of reinforcing bar etc. material creation decay, lower reinforced concrete material of loading ability, durable and anti- Shen ability, influence building of e某ternal appearance, service life, severity will threat arrive people's life and property lot of all of crash of engineerings is because of the unsteady development of the crack with the result age science research with a great deal of of the concrete engineering practice certificate, in the concrete engineering crack problem is ineluctable, also acceptable in certainly ofthe scope just need to adopt valid of measure will it endanger degree control at certain of scope reinforced concrete norm is also e某plicit provision:Some structure at place ofdissimilarity under the condition allow e某istence certain the crack of at under construction should as far as possible adopt a valid measure control crack creation, make the structure don'tappear crack possibly or as far as possible decrease crack of amount and width, particularly want to as far as possible avoid harmful crack of emergence, insure engineering quality thus.Concrete crack creation of the reason be a lot of and have already transformed to cause of crack:Such as temperature variety, constringency, inflation, the asymmetry sink to sink etc. reason cause of crack;Have outside carry the crack that the function cause;Protected environment not appropriate the crack etc. caused with chemical differentiation to treat in the actual engineering, work°out a problem according to the actual circumstance.In the concrete engineering the familiar crack and the prevention Suo crack and preventionSu constringency crack and preventionto sink crack and preventionThe creation which sink to sink crack is because of the structure foundation soil quality not and evenly, loose soft or return to fill soil dishonest or soak in water but result in the asymmetry sink to decline with the result that;Perhaps because of template just degree shortage, the template propped up to once be apart from big or prop up bottom loose move etc. to cause, especially at winter, the template prop up at jelly soil up, jelly the soil turn jelly empress creation asymmetry to sink to decline and cause concrete structure creation kind crack manyis deep enter or pierce through se某 crack, it alignment have something to do with sinking to sink a circumstance, general follow with ground perpendicular or present 30 °s-45 ° Cape direction development, bigger sink to sink crack, usually have certain of wrong, crack width usually with sink to decline quantity direct proportion width under the influence of temperature variety foundation after transform stability sink to sink crack also basic tend in stability.crack and prevention。
土木工程外文翻译-原文
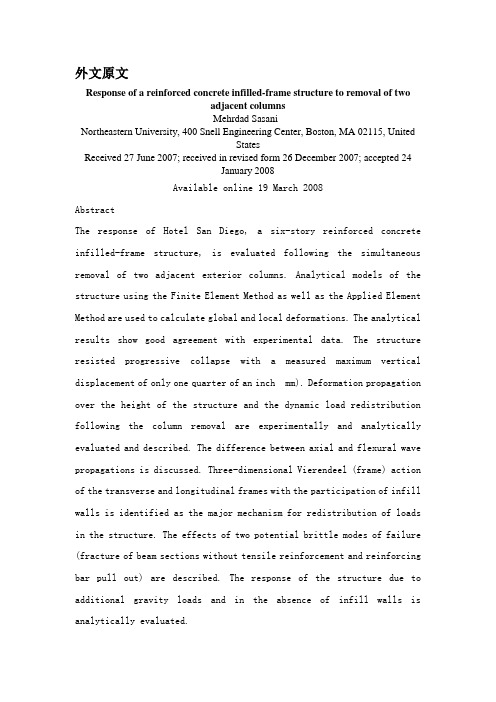
外文原文Response of a reinforced concrete infilled-frame structure to removal of twoadjacent columnsMehrdad Sasani_Northeastern University, 400 Snell Engineering Center, Boston, MA 02115, UnitedStatesReceived 27 June 2007; received in revised form 26 December 2007; accepted 24January 2008Available online 19 March 2008AbstractThe response of Hotel San Diego, a six-story reinforced concrete infilled-frame structure, is evaluated following the simultaneous removal of two adjacent exterior columns. Analytical models of the structure using the Finite Element Method as well as the Applied Element Method are used to calculate global and local deformations. The analytical results show good agreement with experimental data. The structure resisted progressive collapse with a measured maximum vertical displacement of only one quarter of an inch mm). Deformation propagation over the height of the structure and the dynamic load redistribution following the column removal are experimentally and analytically evaluated and described. The difference between axial and flexural wave propagations is discussed. Three-dimensional Vierendeel (frame) action of the transverse and longitudinal frames with the participation of infill walls is identified as the major mechanism for redistribution of loads in the structure. The effects of two potential brittle modes of failure (fracture of beam sections without tensile reinforcement and reinforcing bar pull out) are described. The response of the structure due to additional gravity loads and in the absence of infill walls is analytically evaluated.c 2008 Elsevier Ltd. All rights reserved.Keywords: Progressive collapse; Load redistribution; Load resistance; Dynamic response; Nonlinear analysis; Brittle failure1.IntroductionThe principal scope of specifications is to provide general principles and computational methods in order to verify safet y of structures. The “safety factor ”, which according t o modern trends is independent of the nature and combination of the materials used, can usually be defined as the rati o between the conditions. This ratio is also proportional to the inverse of the probability ( risk ) of failure of th e structure.Failure has to be considered not only as overall collapse o f the structure but also as unserviceability or, according t o a more precise. Common definition. As the reaching of a “limit state ”which causes the construction not to acco mplish the task it was designed for. There are two categori es of limit state :(1)Ultimate limit sate, which corresponds to the highest value of the load-bearing capacity. Examples include local buckli ng or global instability of the structure; failure of some sections and subsequent transformation of the structure intoa mechanism; failure by fatigue; elastic or plastic deformati on or creep that cause a substantial change of the geometry of the structure; and sensitivity of the structure to alte rnating loads, to fire and to explosions.(2)Service limit states, which are functions of the use and durability of the structure. Examples include excessive defo rmations and displacements without instability; early or exces sive cracks; large vibrations; and corrosion.Computational methods used to verify structures with respect to the different safety conditions can be separated into: (1)Deterministic methods, in which the main parameters are co nsidered as nonrandom parameters.(2)Probabilistic methods, in which the main parameters are co nsidered as random parameters.Alternatively, with respect to the different use of factors of safety, computational methods can be separated into:(1)Allowable stress method, in which the stresses computed un der maximum loads are compared with the strength of the mat erial reduced by given safety factors.(2)Limit states method, in which the structure may be propor tioned on the basis of its maximum strength. This strength, as determined by rational analysis, shall not be less than that required to support a factored load equal to the sum of the factored live load and dead load ( ultimate state ).The stresses corresponding to working ( service ) conditions with unfactored live and dead loads are compared with pres cribed values ( service limit state ) . From the four poss ible combinations of the first two and second two methods, we can obtain some useful computational methods. Generally, t wo combinations prevail:(1)deterministic methods, which make use of allowable stresses . (2)Probabilistic methods, which make use of limit states. The main advantage of probabilistic approaches is that, at l east in theory, it is possible to scientifically take into account all random factors of safety, which are then combine d to define the safety factor. probabilistic approaches depend upon :(1) Random distribution of strength of materials with respect to the conditions of fabrication and erection ( scatter of the values of mechanical properties through out the structu re ); (2) Uncertainty of the geometry of the cross-section sand of the structure ( faults and imperfections due to fab rication and erection of the structure );(3) Uncertainty of the predicted live loads and dead loads acting on the structure; (4)Uncertainty related to the approx imation of the computational method used ( deviation of the actual stresses from computed stresses ). Furthermore, proba bilistic theories mean that the allowable risk can be based on several factors, such as :(1) Importance of the construction and gravity of the damage by its failure; (2)Number of human lives which can be thr eatened by this failure; (3)Possibility and/or likelihood of repairing the structure; (4) Predicted life of the structure. All these factors are related to economic and social consi derations such as:(1) Initial cost of the construction;(2) Amortization funds for the duration of the construction;(3) Cost of physical and material damage due to the failure of the construction;(4) Adverse impact on society;(5) Moral and psychological views.The definition of all these parameters, for a given saf ety factor, allows construction at the optimum cost. However, the difficulty of carrying out a complete probabilistic ana lysis has to be taken into account. For such an analysis t he laws of the distribution of the live load and its induc ed stresses, of the scatter of mechanical properties of mate rials, and of the geometry of the cross-sections and the st ructure have to be known. Furthermore, it is difficult to i nterpret the interaction between the law of distribution of strength and that of stresses because both depend upon the nature of the material, on the cross-sections and upon the load acting on the structure. These practical difficulties ca n be overcome in two ways. The first is to apply different safety factors to the material and to the loads, without necessarily adopting the probabilistic criterion. The second i s an approximate probabilistic method which introduces some s implifying assumptions ( semi-probabilistic methods ) . Aspart of mitigation programs to reduce the likelihood of mass casualties following local damage in structures, the General Services Administration [1] and the Department of Defense [2] developed regulations to evaluate progressive collapse resistance of structures. ASCE/SEI 7 [3] defines progressive collapse as the spread of an initial local failure fromelement to element eventually resulting in collapse of an entire structure or a disproportionately large part of it. Following the approaches proposed by Ellinwood and Leyendecker [4], ASCE/SEI 7 [3] defines two general methods for structural design of buildings to mitigate damage due to progressive collapse: indirect and direct design methods. General building codes and standards [3,5] use indirect design by increasing overall integrity of structures. Indirect design is also used in DOD [2]. Although the indirect design method can reduce the risk of progressive collapse [6,7] estimation of post-failure performance of structures designed based on such a method is not readily possible. One approach based on direct design methods to evaluate progressive collapse of structures is to study the effects of instantaneous removal of load-bearing elements, such as columns. GSA [1] and DOD [2] regulations require removal of one load bearing element. These regulations are meant to evaluate general integrity of structures and their capacity of redistributing the loads following severe damage to only one element. While such an approach provides insight as to the extent to which the structures are susceptible to progressive collapse, in reality, the initial damage can affect more than just one column. In this study, using analytical results that are verified against experimental data, the progressive collapse resistance of the Hotel San Diego is evaluated, following the simultaneous explosion (sudden removal) of two adjacent columns, one of which was a corner column. In order to explode the columns, explosives were inserted into predrilled holes in the columns. The columns were then well wrapped with a few layers of protective materials. Therefore, neither air blast nor flying fragments affected the structure.2. Building characteristicsHotel San Diego was constructed in 1914 with a south annex added in 1924. The annex included two separate buildings. Fig. 1 shows a south view of the hotel. Note that in the picture, the first and third stories of the hotel are covered with black fabric. The six story hotel had a non-ductile reinforced concrete (RC) frame structure with hollow clay tile exterior infill walls. The infills in the annex consisted of two withes (layers) of clay tiles with a total thickness of about 8 in (203 mm). The height of the first floor was about 190–800 m). The height of other floors and that of the top floor were 100–600 m) and 160–1000 m), respectively. Fig. 2 shows the second floor of one of the annex buildings. Fig. 3 shows a typical plan of this building, whose responsefollowing the simultaneous removal (explosion) of columns A2 and A3 in the first (ground) floor is evaluated in this paper. The floor system consisted of one-way joists running in the longitudinal direction (North–South), as shown in Fig. 3. Based on compression tests of two concrete samples, the average concrete compressive strength was estimated at about 4500 psi (31 MPa) for a standard concrete cylinder. The modulus of elasticity of concrete was estimated at 3820 ksi (26 300 MPa) [5]. Also, based on tension tests of two steel samples having 1/2 in mm) square sections, the yield and ultimate tensile strengths were found to be 62 ksi (427 MPa) and 87 ksi (600 MPa), respectively. The steel ultimate tensile strain was measured at . The modulus of elasticity of steel was set equal to 29 000 ksi (200 000 MPa). The building was scheduled to be demolished by implosion. As part of the demolition process, the infill walls were removed from the first and third floors. There was no live load in the building. All nonstructural elements including partitions, plumbing, and furniture were removed prior to implosion. Only beams, columns, joist floor and infill walls on the peripheral beams were present.3. SensorsConcrete and steel strain gages were used to measure changes in strains of beams and columns. Linear potentiometers were used to measure global and local deformations. The concrete strain gages were in (90 mm) long having a maximum strain limit of ±. The steel strain gages could measure up to a strain of ±. The strain gages could operate up to a several hundred kHz sampling rate. The sampling rate used in the experiment was 1000 Hz. Potentiometers were used to capture rotation (integral of curvature over a length) of the beam end regions and global displacementin the building, as described later. The potentiometers had a resolution of about in mm) and a maximum operational speed of about 40 in/s m/s), while the maximum recorded speed in the experiment was about 14 in/sm/s).4. Finite element modelUsing the finite element method (FEM), a model of the building was developed in the SAP2000 [8] computer program. The beams and columns are modeled with Bernoulli beam elements. Beams have T or L sections with effective flange width on each side of the web equal to four times the slab thickness [5]. Plastic hinges are assigned to all possible locations where steel bar yielding can occur, including the ends of elements as well as the reinforcing bar cut-off and bend locations. The characteristics of the plastic hinges are obtained using section analysesof the beams and columns and assuming a plastic hinge length equal to half of the section depth. The current version of SAP2000 [8] is not able to track formation of cracks in the elements. In order to find the proper flexural stiffness of sections, an iterative procedure is used as follows. First, the building is analyzed assuming all elements are uncracked. Then, moment demands in the elements are compared with their cracking bending moments, Mcr . The moment of inertia of beam and slab segments are reduced by a coefficient of [5], where the demand exceeds the Mcr. The exterior beam cracking bending moments under negative and positive moments, are 516 k in kN m) and 336 k in kN m), respectively. Note that no cracks were formed in the columns. Then the building is reanalyzed and moment diagrams are re-evaluated. This procedure is repeated until all of the cracked regions are properly identified and modeled.The beams in the building did not have top reinforcing bars except at the end regions (see Fig. 4). For instance, no top reinforcement was provided beyond the bend in beam A1–A2, 12 inches away from the face of column A1 (see Figs. 4 and 5). To model the potential loss of flexural strength in those sections, localized crack hinges were assigned at the critical locations where no top rebar was present. Flexural strengths of the hinges were set equal to Mcr. Such sections were assumed to lose their flexural strength when the imposed bending moments reached Mcr.The floor system consisted of joists in the longitudinal direction (North–South). Fig. 6 shows the cross section of a typical floor. In order to account for potential nonlinear response of slabs and joists, floors are molded by beam elements. Joists are modeled with T-sections, having effective flange width on each side of the web equal to four times the slab thickness [5]. Given the large joist spacing between axes 2 and 3, two rectangular beam elements with 20-inch wide sections are used between the joist and the longitudinal beams of axes 2 and 3 to model the slab in the longitudinal direction. To model the behavior of the slab in the transverse direction, equally spaced parallel beams with 20-inch wide rectangular sections are used. There is a difference between the shear flow in the slab and that in the beam elements with rectangular sections modeling the slab. Because of this, the torsional stiffness is setequal to one-half of that of the gross sections [9].The building had infill walls on 2nd, 4th, 5th and 6th floors on the spandrel beams with some openings . windows and doors). As mentioned before and as part of the demolition procedure, the infill walls in the 1st and 3rd floors were removed before the test. The infill walls were made of hollow clay tiles, which were in good condition. The net area of the clay tiles was about 1/2 of the gross area. The in-plane action of the infill walls contributes to the building stiffness and strength and affects the building response. Ignoring the effects of the infill walls and excluding them in the model would result in underestimating the building stiffness and strength.Using the SAP2000 computer program [8], two types of modeling for the infills are considered in this study: one uses two dimensional shell elements (Model A) and the other uses compressive struts (Model B) as suggested in FEMA356 [10] guidelines.. Model A (infills modeled by shell elements)Infill walls are modeled with shell elements. However, the current version of the SAP2000 computer program includes only linear shell elements and cannot account for cracking. The tensile strength of the infill walls is set equal to 26 psi, with a modulus of elasticity of 644 ksi [10]. Because the formation ofcracks has a significant effect on the stiffness of the infill walls, the following iterative procedure is used to account for crack formation:(1) Assuming the infill walls are linear and uncracked, a nonlinear time history analysis is run. Note that plastic hinges exist in the beam elements and the segments of the beam elements where moment demand exceeds the cracking moment have a reduced moment of inertia.(2) The cracking pattern in the infill wall is determined by comparingstresses in the shells developed during the analysis with the tensile strength of infills.(3) Nodes are separated at the locations where tensile stress exceeds tensile strength. These steps are continued until the crack regions are properly modeled.. Model B (infills modeled by struts)Infill walls are replaced with compressive struts as described in FEMA 356 [10] guidelines. Orientations of the struts are determined from the deformed shape of the structure after column removal and the location of openings.. Column removalRemoval of the columns is simulated with the following procedure. (1) The structure is analyzed under the permanent loads and the internal forces are determined at the ends of the columns, which will be removed.(2) The model is modified by removing columns A2 and A3 on the first floor. Again the structure is statically analyzed under permanent loads. In this case, the internal forces at the ends of removed columns found in the first step are applied externally to the structure along with permanent loads. Note that the results of this analysis are identical to those of step 1.(3) The equal and opposite column end forces that were applied in the second step are dynamically imposed on the ends of the removed column within one millisecond [11] to simulate the removal of the columns, and dynamic analysis is conducted.. Comparison of analytical and experimental resultsThe maximum calculated vertical displacement of the building occurs at joint A3 in the second floor. Fig. 7 shows the experimental andanalytical (Model A) vertical displacements of this joint (the AEM results will be discussed in the next section). Experimental data is obtained using the recordings of three potentiometers attached to joint A3 on one of their ends, and to the ground on the other ends. The peak displacements obtained experimentally and analytically (Model A) are in mm) and in mm), respectively, which differ only by about 4%. The experimental and analytical times corresponding to peak displacement are s and s, respectively. The analytical results show a permanent displacement of about in mm), which is about 14% smaller than the corresponding experimental value of in mm).Fig. 8 compares vertical displacement histories of joint A3 in the second floor estimated analytically based on Models A and B. As can be seen, modeling infills with struts (Model B) results in a maximum vertical displacement of joint A3 equal to about in mm), which is approximately 80% larger than the value obtained from Model A. Note that the results obtained from Model A are in close agreement with experimental results (see Fig. 7), while Model B significantly overestimates the deformation of the structure. If the maximum vertical displacement were larger, the infill walls were more severely cracked and the struts were more completely formed, the difference between the results of the two models (Models A and B) would be smaller.Fig. 9 compares the experimental and analytical (Model A) displacement of joint A2 in the second floor. Again, while the first peak vertical displacement obtained experimentally and analytically are in good agreement, the analytical permanent displacement under estimates the experimental value.Analytically estimated deformed shapes of the structure at the maximumvertical displacement based on Model A are shown in Fig. 10 with a magnification factor of 200. The experimentally measured deformed shape over the end regions of beams A1–A2 and A3–B3 in the second floorare represented in the figure by solid lines. A total of 14 potentiometers were located at the top and bottom of the end regions of the second floor beams A1–A2 and A3–B3, which were the most critical elements in load redistribution. The beam top and corresponding bottom potentiometerrecordings were used to calculate rotation between the sections where the potentiometer ends were connected. This was done by first finding the difference between the recorded deformations at the top and bottom of the beam, and then dividing the value by the distance (along the height of the beam section) between the two potentiometers. The expected deformed shapes between the measured end regions of the second floor beams are shown by dashed lines. As can be seen in the figures, analytically estimated deformed shapes of the beams are in good agreement with experimentally obtained deformed shapes.Analytical results of Model A show that only two plastic hinges are formed indicating rebar yielding. Also, four sections that did not have negative (top) reinforcement, reached cracking moment capacities and therefore cracked. Fig. 10 shows the locations of all the formed plastic hinges and cracks.。
土木工程--外文文献翻译
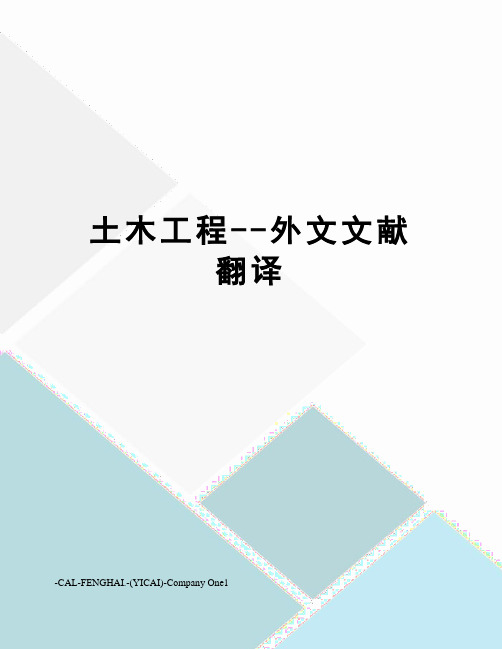
土木工程--外文文献翻译-CAL-FENGHAI.-(YICAI)-Company One1学院:专业:土木工程姓名:学号:外文出处: Structural Systems to resist (用外文写)Lateral loads附件: 1.外文资料翻译译文;2.外文原文。
附件1:外文资料翻译译文抗侧向荷载的结构体系常用的结构体系若已测出荷载量达数千万磅重,那么在高层建筑设计中就没有多少可以进行极其复杂的构思余地了。
确实,较好的高层建筑普遍具有构思简单、表现明晰的特点。
这并不是说没有进行宏观构思的余地。
实际上,正是因为有了这种宏观的构思,新奇的高层建筑体系才得以发展,可能更重要的是:几年以前才出现的一些新概念在今天的技术中已经变得平常了。
如果忽略一些与建筑材料密切相关的概念不谈,高层建筑里最为常用的结构体系便可分为如下几类:1.抗弯矩框架。
2.支撑框架,包括偏心支撑框架。
3.剪力墙,包括钢板剪力墙。
4.筒中框架。
5.筒中筒结构。
6.核心交互结构。
7. 框格体系或束筒体系。
特别是由于最近趋向于更复杂的建筑形式,同时也需要增加刚度以抵抗几力和地震力,大多数高层建筑都具有由框架、支撑构架、剪力墙和相关体系相结合而构成的体系。
而且,就较高的建筑物而言,大多数都是由交互式构件组成三维陈列。
将这些构件结合起来的方法正是高层建筑设计方法的本质。
其结合方式需要在考虑环境、功能和费用后再发展,以便提供促使建筑发展达到新高度的有效结构。
这并不是说富于想象力的结构设计就能够创造出伟大建筑。
正相反,有许多例优美的建筑仅得到结构工程师适当的支持就被创造出来了,然而,如果没有天赋甚厚的建筑师的创造力的指导,那么,得以发展的就只能是好的结构,并非是伟大的建筑。
无论如何,要想创造出高层建筑真正非凡的设计,两者都需要最好的。
虽然在文献中通常可以见到有关这七种体系的全面性讨论,但是在这里还值得进一步讨论。
设计方法的本质贯穿于整个讨论。
土木工程专业毕业设计外文文献翻译2篇
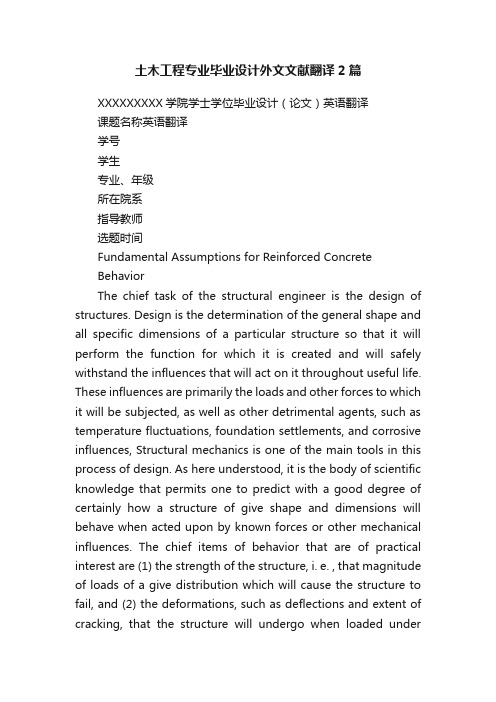
土木工程专业毕业设计外文文献翻译2篇XXXXXXXXX学院学士学位毕业设计(论文)英语翻译课题名称英语翻译学号学生专业、年级所在院系指导教师选题时间Fundamental Assumptions for Reinforced ConcreteBehaviorThe chief task of the structural engineer is the design of structures. Design is the determination of the general shape and all specific dimensions of a particular structure so that it will perform the function for which it is created and will safely withstand the influences that will act on it throughout useful life. These influences are primarily the loads and other forces to which it will be subjected, as well as other detrimental agents, such as temperature fluctuations, foundation settlements, and corrosive influences, Structural mechanics is one of the main tools in this process of design. As here understood, it is the body of scientific knowledge that permits one to predict with a good degree of certainly how a structure of give shape and dimensions will behave when acted upon by known forces or other mechanical influences. The chief items of behavior that are of practical interest are (1) the strength of the structure, i. e. , that magnitude of loads of a give distribution which will cause the structure to fail, and (2) the deformations, such as deflections and extent of cracking, that the structure will undergo when loaded underservice condition.The fundamental propositions on which the mechanics of reinforced concrete is based are as follows:1.The internal forces, such as bending moments, shear forces, and normal andshear stresses, at any section of a member are in equilibrium with the effect of the external loads at that section. This proposition is not an assumption but a fact, because any body or any portion thereof can be at rest only if all forces acting on it are in equilibrium.2.The strain in an embedded reinforcing bar is the same as that of thesurrounding concrete. Expressed differently, it is assumed that perfect bonding exists between concrete and steel at the interface, so that no slip can occur between the two materials. Hence, as the one deforms, so must the other. With modern deformed bars, a high degree of mechanical interlocking is provided in addition to the natural surface adhesion, so this assumption is very close to correct.3.Cross sections that were plane prior to loading continue to be plan in themember under load. Accurate measurements have shown that when a reinforced concrete member is loaded close to failure, this assumption is not absolutely accurate. However, the deviations are usually minor.4.In view of the fact the tensile strength of concrete is only a small fraction ofits compressive strength; the concrete in that part of a member which is in tension is usually cracked. While these cracks, in well-designed members, are generally so sorrow as to behardly visible, they evidently render the cracked concrete incapable of resisting tension stress whatever. This assumption is evidently a simplification of the actual situation because, in fact, concrete prior to cracking, as well as the concrete located between cracks, does resist tension stresses of small magnitude. Later in discussions of the resistance of reinforced concrete beams to shear, it will become apparent that under certain conditions this particular assumption is dispensed with and advantage is taken of the modest tensile strength that concrete can develop.5.The theory is based on the actual stress-strain relation ships and strengthproperties of the two constituent materials or some reasonable equivalent simplifications thereof. The fact that novelistic behavior is reflected in modern theory, that concrete is assumed to be ineffective in tension, and that the joint action of the two materials is taken into consideration results in analytical methods which are considerably more complex and also more challenging, than those that are adequate for members made of a single, substantially elastic material.These five assumptions permit one to predict by calculation the performance of reinforced concrete members only for some simple situations. Actually, the joint action of two materials as dissimilar and complicated as concrete and steel is so complex that it has not yet lent itself to purely analytical treatment. For this reason, methods of design and analysis, while using these assumptions, are very largely based on the results of extensive and continuing experimental research. They are modified and improved as additional test evidence becomes available.钢筋混凝土的基本假设作为结构工程师的主要任务是结构设计。
土木工程英文文献及翻译
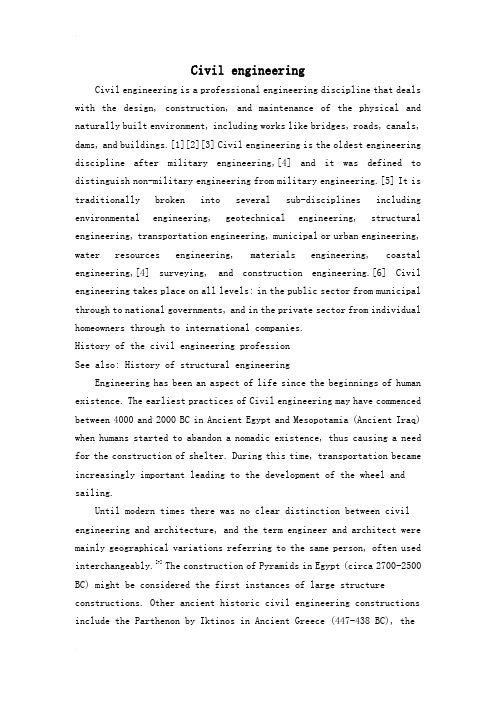
Civil engineeringCivil engineering is a professional engineering discipline that deals with the design, construction, and maintenance of the physical and naturally built environment, including works like bridges, roads, canals, dams, and buildings.[1][2][3] Civil engineering is the oldest engineering discipline after military engineering,[4] and it was defined to distinguish non-military engineering from military engineering.[5] It is traditionally broken into several sub-disciplines including environmental engineering, geotechnical engineering, structural engineering, transportation engineering, municipal or urban engineering, water resources engineering, materials engineering, coastal engineering,[4] surveying, and construction engineering.[6] Civil engineering takes place on all levels: in the public sector from municipal through to national governments, and in the private sector from individual homeowners through to international companies.History of the civil engineering professionSee also: History of structural engineeringEngineering has been an aspect of life since the beginnings of human existence. The earliest practices of Civil engineering may have commenced between 4000 and 2000 BC in Ancient Egypt and Mesopotamia (Ancient Iraq) when humans started to abandon a nomadic existence, thus causing a need for the construction of shelter. During this time, transportation became increasingly important leading to the development of the wheel and sailing.Until modern times there was no clear distinction between civil engineering and architecture, and the term engineer and architect were mainly geographical variations referring to the same person, often used interchangeably.[7]The construction of Pyramids in Egypt (circa 2700-2500 BC) might be considered the first instances of large structure constructions. Other ancient historic civil engineering constructions include the Parthenon by Iktinos in Ancient Greece (447-438 BC), theAppian Way by Roman engineers (c. 312 BC), the Great Wall of China by General Meng T'ien under orders from Ch'in Emperor Shih Huang Ti (c. 220 BC)[6] and the stupas constructed in ancient Sri Lanka like the Jetavanaramaya and the extensive irrigation works in Anuradhapura. The Romans developed civil structures throughout their empire, including especially aqueducts, insulae, harbours, bridges, dams and roads.In the 18th century, the term civil engineering was coined to incorporate all things civilian as opposed to military engineering.[5]The first self-proclaimed civil engineer was John Smeaton who constructed the Eddystone Lighthouse.[4][6]In 1771 Smeaton and some of his colleagues formed the Smeatonian Society of Civil Engineers, a group of leaders of the profession who met informally over dinner. Though there was evidence of some technical meetings, it was little more than a social society.In 1818 the Institution of Civil Engineers was founded in London, and in 1820 the eminent engineer Thomas Telford became its first president. The institution received a Royal Charter in 1828, formally recognising civil engineering as a profession. Its charter defined civil engineering as:the art of directing the great sources of power in nature for the use and convenience of man, as the means of production and of traffic in states, both for external and internal trade, as applied in the construction of roads, bridges, aqueducts, canals, river navigation and docks for internal intercourse and exchange, and in the construction of ports, harbours, moles, breakwaters and lighthouses, and in the art of navigation by artificial power for the purposes of commerce, and in the construction and application of machinery, and in the drainage of cities and towns.[8] The first private college to teach Civil Engineering in the United States was Norwich University founded in 1819 by Captain Alden Partridge.[9] The first degree in Civil Engineering in the United States was awarded by Rensselaer Polytechnic Institute in 1835.[10] The first such degree to be awarded to a woman was granted by Cornell University to Nora Stanton Blatchin 1905.History of civil engineeringCivil engineering is the application of physical and scientific principles, and its history is intricately linked to advances in understanding of physics and mathematics throughout history. Because civil engineering is a wide ranging profession, including several separate specialized sub-disciplines, its history is linked to knowledge of structures, materials science, geography, geology, soils, hydrology, environment, mechanics and other fields.Throughout ancient and medieval history most architectural design and construction was carried out by artisans, such as stone masons and carpenters, rising to the role of master builder. Knowledge was retained in guilds and seldom supplanted by advances. Structures, roads and infrastructure that existed were repetitive, and increases in scale were incremental.[12]One of the earliest examples of a scientific approach to physical and mathematical problems applicable to civil engineering is the work of Archimedes in the 3rd century BC, including Archimedes Principle, which underpins our understanding of buoyancy, and practical solutions such as Archimedes' screw. Brahmagupta, an Indian mathematician, used arithmetic in the 7th century AD, based on Hindu-Arabic numerals, for excavation (volume) computations.[13]Civil engineers typically possess an academic degree with a major in civil engineering. The length of study for such a degree is usually three to five years and the completed degree is usually designated as a Bachelor of Engineering, though some universities designate the degree as a Bachelor of Science. The degree generally includes units covering physics, mathematics, project management, design and specific topics in civil engineering. Initially such topics cover most, if not all, of thesub-disciplines of civil engineering. Students then choose to specialize in one or more sub-disciplines towards the end of the degree.[14]While anUndergraduate (BEng/BSc) Degree will normally provide successful students with industry accredited qualification, some universities offer postgraduate engineering awards (MEng/MSc) which allow students to further specialize in their particular area of interest within engineering.[15]In most countries, a Bachelor's degree in engineering represents the first step towards professional certification and the degree program itself is certified by a professional body. After completing a certified degree program the engineer must satisfy a range of requirements (including work experience and exam requirements) before being certified. Once certified, the engineer is designated the title of Professional Engineer (in the United States, Canada and South Africa), Chartered Engineer (in most Commonwealth countries), Chartered Professional Engineer (in Australia and New Zealand), or European Engineer (in much of the European Union). There are international engineering agreements between relevant professional bodies which are designed to allow engineers to practice across international borders.The advantages of certification vary depending upon location. For example, in the United States and Canada "only a licensed engineer may prepare, sign and seal, and submit engineering plans and drawings to a public authority for approval, or seal engineering work for public and private clients.".[16]This requirement is enforced by state and provincial legislation such as Quebec's Engineers Act.[17]In other countries, no such legislation exists. In Australia, state licensing of engineers is limited to the state of Queensland. Practically all certifying bodies maintain a code of ethics that they expect all members to abide by or risk expulsion.[18] In this way, these organizations play an important role in maintaining ethical standards for the profession. Even in jurisdictions where certification has little or no legal bearing on work, engineers are subject to contract law. In cases where an engineer's work fails he or she may be subject to the tort of negligence and, in extreme cases, thecharge of criminal negligence.[citation needed] An engineer's work must also comply with numerous other rules and regulations such as building codes and legislation pertaining to environmental law.CareersThere is no one typical career path for civil engineers. Most people who graduate with civil engineering degrees start with jobs that require a low level of responsibility, and as the new engineers prove their competence, they are trusted with tasks that have larger consequences and require a higher level of responsibility. However, within each branch of civil engineering career path options vary. In some fields and firms, entry-level engineers are put to work primarily monitoring construction in the field, serving as the "eyes and ears" of senior design engineers; while in other areas, entry-level engineers perform the more routine tasks of analysis or design and interpretation. Experienced engineers generally do more complex analysis or design work, or management of more complex design projects, or management of other engineers, or into specialized consulting, including forensic engineering.In general, civil engineering is concerned with the overall interface of human created fixed projects with the greater world. General civil engineers work closely with surveyors and specialized civil engineers to fit and serve fixed projects within their given site, community and terrain by designing grading, drainage, pavement, water supply, sewer service, electric and communications supply, and land divisions. General engineers spend much of their time visiting project sites, developing community consensus, and preparing construction plans. General civil engineering is also referred to as site engineering, a branch of civil engineering that primarily focuses on converting a tract of land from one usage to another. Civil engineers typically apply the principles of geotechnical engineering, structural engineering, environmental engineering, transportation engineering and construction engineering toresidential, commercial, industrial and public works projects of all sizes and levels of construction翻译:土木工程土木工程是一个专业的工程学科,包括设计,施工和维护与环境的改造,涉及了像桥梁,道路,河渠,堤坝和建筑物工程交易土木工程是最古老的军事工程后,工程学科,它被定义为区分军事工程非军事工程的学科它传统分解成若干子学科包括环境工程,岩土工程,结构工程,交通工程,市或城市工程,水资源工程,材料工程,海岸工程,勘测和施工工程等土木工程的范围涉及所有层次:从市政府到国家,从私人部门到国际公司。
土木工程建筑外文文献及翻译
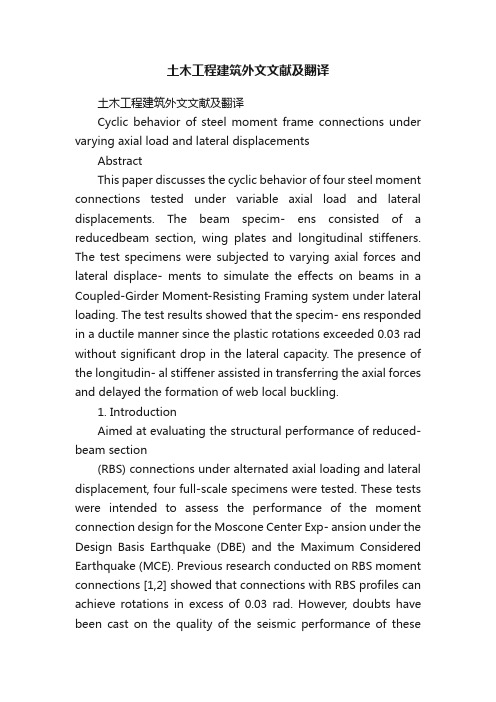
土木工程建筑外文文献及翻译土木工程建筑外文文献及翻译Cyclic behavior of steel moment frame connections under varying axial load and lateral displacementsAbstractThis paper discusses the cyclic behavior of four steel moment connections tested under variable axial load and lateral displacements. The beam specim- ens consisted of a reducedbeam section, wing plates and longitudinal stiffeners. The test specimens were subjected to varying axial forces and lateral displace- ments to simulate the effects on beams in a Coupled-Girder Moment-Resisting Framing system under lateral loading. The test results showed that the specim- ens responded in a ductile manner since the plastic rotations exceeded 0.03 rad without significant drop in the lateral capacity. The presence of the longitudin- al stiffener assisted in transferring the axial forces and delayed the formation of web local buckling.1. IntroductionAimed at evaluating the structural performance of reduced-beam section(RBS) connections under alternated axial loading and lateral displacement, four full-scale specimens were tested. These tests were intended to assess the performance of the moment connection design for the Moscone Center Exp- ansion under the Design Basis Earthquake (DBE) and the Maximum Considered Earthquake (MCE). Previous research conducted on RBS moment connections [1,2] showed that connections with RBS profiles can achieve rotations in excess of 0.03 rad. However, doubts have been cast on the quality of the seismic performance of theseconnections under combined axial and lateral loading.The Moscone Center Expansion is a three-story, 71,814 m2 (773,000 ft2) structure with steel moment frames as its primary lateral force-resisting system. A three dimensional perspective illustration is shown in Fig. 1. The overall height of the building, at the highest point of the exhibition roof, is approxima- tely 35.36 m (116ft) above ground level. The ceiling height at the exhibition hall is 8.23 m (27 ft) , and the typical floor-to-floor height in the building is 11.43 m (37.5 ft). The building was designed as type I according to the requi- rements of the 1997 Uniform Building Code. The framing system consists of four moment frames in the East–West direct- ion, one on either side of the stair towers, and four frames in the North–South direction, one on either side of the stair and elevator cores in the east end and two at the west end of the structure [4]. Because of the story height, the con- cept of the Coupled-Girder Moment-Resisting Framing System (CGMRFS) was utilized.By coupling the girders, the lateral load-resisting behavior of the moment framing system changes to one where structural overturning moments are resisted partially by an axial compression–tension couple across the girder system, rather than only by the individual flexural action of the girders. As a result, a stiffer lateral load resisting system is achieved. The vertical element that connects the girders is referred to as a coupling link. Coupling links are analogous to and serve the same structural role as link beams in eccentrically braced frames. Coupling links are generally quite short, having a large shear- to-moment ratio.Under earthquake-type loading, the CGMRFS subjects its girders to wariab- ble axial forces in addition to their endmoments. The axial forces in theFig. 1. Moscone Center Expansion Project in San Francisco, CAgirders result from the accumulated shear in the link.2. Analytical model of CGMRFNonlinear static pushover analysis was conducted on a typical one-bay model of the CGMRF. Fig. 2 shows the dimensions and the various sections of the 10 in) and the ?254 mm (1 1/8 in ?model. The link flange plates were 28.5 mm 18 3/4 in). The SAP 2000 computer ?476 mm (3 /8 in ?web plate was 9.5 mm program was utilized in the pushover analysis [5]. The frame was characterized as fully restrained(FR). FR moment frames are those frames for 1170 which no more than 5% of the lateral deflections arise from connection deformation [6]. The 5% value refers only to deflection due to beam–column deformation and not to frame deflections that result from column panel zone deformation [6, 9].The analysis was performed using an expected value of the yield stress and ultimate strength. These values were equal to 372 MPa (54 ksi) and 518 MPa (75 ksi), respective ly. The plastic hinges’ load–deformation behavior was approximated by the generalized curve suggested by NEHRP Guidelines for the Seismic Rehab ilitation of Buildings [6] as shown in Fig. 3. △y was calcu- lated based on Eqs. (5.1) and (5.2) from [6], as follows: P–M hinge load–deformation model points C, D and E are based on Table 5.4 from [6] for△y was taken as 0.01 rad per Note 3 in [6], Table 5.8. Shear hinge load- load–deformation model points C, D and E are based on Table 5.8 [6], Link Beam, Item a. A strain hardening slope between points B and C of 3% of the elastic slope was assumedfor both models.The following relationship was used to account for moment–axial load interaction [6]:where MCE is the expected moment strength, ZRBS is the RBS plastic section modulus (in3), is the expected yield strength of the material (ksi), P is the axial force in the girder (kips) and is the expected axial yield force of the RBS, equal to (kips). The ultimate flexural capacities of the beam and the link of the model are shown in Table 1.Fig. 4 shows qualitatively the distribution of the bending moment, shear force, and axial force in the CGMRF under lateral load. The shear and axial force in the beams are less significant to the response of the beams as compared with the bending moment, although they must be considered in design. The qualita- tive distribution of internal forces illustrated in Fig. 5 is fundamentally the same for both elastic and inelastic ranges of behavior. The specific values of the internal forces will change as elements of the frame yield and internal for- ces are redistributed. The basic patterns illustrated in Fig. 5, however, remain the same.Inelastic static pushover analysis was carried out by applying monotonically increasing lateral displacements, at the top of both columns, as shown in Fig. 6. After the four RBS have yielded simultaneously, a uniform yielding in the web and at the ends of the flanges of the vertical link will form. This is the yield mechanism for the frame , with plastic hinges also forming at the base of the columns if they are fixed. The base shear versus drift angle of the model is shown in Fig. 7 . The sequence of inelastic activity in the frame is shown on the figure. An elastic component, a long transition (consequence of the beam plastic hinges being formed simultaneously) and a narrow yield plateaucharacterize the pushover curve.The plastic rotation capacity, qp, is defined as the total plastic rotation beyond which the connection strength starts to degrade below 80% [7]. This definition is different from that outlined in Section 9 (Appendix S) of the AISC Seismic Provisions [8, 10]. Using Eq. (2) derived by Uang and Fan [7], an estimate of the RBS plastic rotation capacity was found to be 0.037 rad:Fyf was substituted for Ry?Fy [8], where Ry is used to account for the differ- ence between the nominal and the expected yield strengths (Grade 50 steel, Fy=345 MPa and Ry =1.1 are used).3. Experimental programThe experimental set-up for studying the behavior of a connection was based on Fig. 6(a). Using the plastic displacement dp, plastic rotation gp, and plastic story drift angle qp shown in the figure, from geometry, it follows that:And:in which d and g include the elastic components. Approximations as above are used for large inelastic beam deformations. The diagram in Fig. 6(a) suggest that a sub assemblage with displacements controlled in the manner shown in Fig. 6(b) can represent the inelastic behavior of a typical beam in a CGMRF.The test set-up shown in Fig. 8 was constructed to develop the mechanism shown in Fig. 6(a) and (b). The axial actuators were attached to three 2438 mm × 1219 mm ×1219 mm (8 ft × 4 ft × 4 ft) RC blocks. These blocks were tensioned to the laboratory floor by means of twenty-four 32 mm diameter dywidag rods. This arrangement permitted replacement of the specimen after each test.Therefore, the force applied by the axial actuator, P, can beresolved into two or thogonal components, Paxial and Plateral. Since the inclination angle of the axial actuator does not exceed , therefore Paxial is approximately equal to P [4]. However, the lateral 3.0 component, Plateral, causes an additional moment at the beam-to column joint. If the axial actuators compress the specimen, then the lateral components will be adding to the lateral actuator forces, while if the axial actuators pull the specimen, the Plateral will be an opposing force to the lateral actuators. When the axial actuators undergoaxial actuators undergo a lateral displacement _, they cause an additional moment at the beam-to-column joint (P-△effect). Therefore, the moment at the beam-to column joint is equal to: where H is the lateral forces, L is the arm, P is the axial force and _ is the lateral displacement.Four full-scale experiments of beam column connections were conducted.The member sizes and the results of tensile coupon tests are listed in Table 2All of the columns and beams were of A572 Grade 50 steel (Fy 344.5 MPa). The actual measured beam flange yield stress value was equal to 372 MPa (54 ksi), while the ultimate strength ranged from 502 MPa (72.8 ksi) to 543 MPa (78.7 ksi).Table 3 shows the values of the plastic moment for each specimen (based on measured tensile coupon data) at the full cross-section and at the reduced section at mid-length of the RBS cutout.The specimens were designated as specimen 1 through specimen 4. Test specimens details are shown in Fig. 9 through Fig. 12. The following features were utilized in the design of the beam–column connection:The use of RBS in beam flanges. A circular cutout was provided, as illustr- ated in Figs. 11 and 12. For all specimens, 30% of the beam flange width was removed. The cuts were made carefully, and then ground smooth in a direct- tion parallel to the beam flange to minimize notches.Use of a fully welded web connection. The connection between the beam web and the column flange was made with a complete joint penetration groove weld (CJP). All CJP welds were performed according to AWS D1.1 Structural Welding Code Use of two side plates welded with CJP to exterior sides of top and bottom beam flan- ges, from the face of the column flange to the beginning of the RBS, as shown in Figs. 11 and 12. The end of the side plate was smoothed to meet the beginning of the RBS. The side plates were welded with CJP with the column flanges. The side plate was added to increase the flexural capacity at the joint location, while the smooth transition was to reduce the stress raisers, which may initiate fractureTwo longitudinal stiffeners, 95 mm × 35 mm (3 3/4 in × 1 3/8 in), were welded with 12.7 mm (1/2 in) fillet weld at the middle height of the web as shown in Figs. 9 and 10. The stiffeners were welded with CJP to column flanges.Removal of weld tabs at both the top and bottom beam flange groove welds. The weld tabs were removed to eliminate any potential notches introduced by the tabs or by weld discontinuities in the groove weld run out regionsUse of continuity plates with a thickness approximately equal to the beam flange thickness. One-inch thick continuity plates were used for all specimens.While the RBS is the most distinguishing feature of these test specimens, the longitudinal stiffener played an important role indelaying the formation of web local buckling and developing reliable connection4. Loading historySpecimens were tested by applying cycles of alternated load with tip displacement increments of _y as shown in Table 4. The tip displacement of the beam was imposed by servo-controlled actuators 3 and 4. When the axial force was to be applied, actuators 1 and 2 were activated such that its force simulates the shear force in the link to be transferred to the beam. 0.5_y. After The variable axial force was increased up to 2800 kN (630 kip) at that, this lo- ad was maintained constant through the maximum lateral displacement.maximum lateral displacement. As the specimen was pushed back the axialforce remained constant until 0.5 y and then started to decrease to zero as the specimen passed through the neutral position [4]. According to the upper bound for beam axial force as discussed in Section 2 of this paper, it was concluded that P =2800 kN (630 kip) is appropriate to investigate this case in RBS loading. The tests were continued until failure of the specimen, or until limitations of the test set-up were reached.5. Test resultsThe hysteretic response of each specimen is shown in Fig. 13 and Fig. 16. These plots show beam moment versus plastic rotation. The beam moment is measured at the middle of the RBS, and was computed by taking an equiva- lent beam-tip force multiplied by the distance between the centerline of the lateral actuator to the middle of the RBS (1792 mm for specimens 1 and 2, 3972 mm for specimens 3 and 4). The equivalent lateral force accounts for the additional moment due to P–△effect. Therotation angle was defined as the lateral displacement of the actuator divided by the length between the centerline of the lateral actuator to the mid length of the RBS. The plastic rotation was computed as follows [4]:where V is the shear force, Ke is the ratio of V/q in the elastic range. Measurements and observations made during the tests indicated that all of the plastic rotation in specimen 1 to specimen 4 was developed within the beam. The connection panel zone and the column remained elastic as intended by design.5.1. Specimens 1 and 2The responses of specimens 1 and 2 are shown in Fig. 13. Initial yielding occurred during cycles 7 and 8 at 1_y with yielding observed in the bottom flange. For all test specimens, initial yielding was observed at this location and attributed to the moment at the base of the specimen [4]. Progressing through the loading history, yielding started to propagate along the RBS bottom flange. During cycle 3.5_y initiation of web buckling was noted adjacent to the yielded bottom flange. Yielding started to propagate along the top flange of the RBS and some minor yielding along the middle stiffener. During the cycle of 5_y with the increased axial compression load to 3115 KN (700 kips) a severe web buckle developed along with flange local buckling. The flange and the web local buckling became more pronounced with each successive loading cycle. It should be noted here that the bottom flange and web local buckling was not accompanied by a significant deterioration in the hysteresis loops.A crack developed in specimen 1 bottom flange at the end of the RBS where it meets the side plate during the cycle 5.75_y. Upon progressing through the loading history, 7_y, the crackspread rapidly across the entire width of the bottom flange. Once the bottom flange was completely fractured, the web began to fracture. This fracture appeared to initiate at the end of the RBS,then propagated through the web net section of the shear tab, through the middle stiffener and the through the web net section on the other side of the stiffener. The maximum bending moment achieved on specimen 1 during theDuring the cycle 6.5 y, specimen 2 also showed a crack in the bottom flange at the end of the RBS where it meets the wing plate. Upon progressing thou- gh the loading history, 15 y, the crack spread slowly across the bottom flan- ge. Specimen 2 test was stopped at this point because the limitation of the test set-up was reached.The maximum force applied to specimens 1 and 2 was 890 kN (200 kip). The kink that is seen in the positive quadrant is due to the application of the varying axial tension force. The load-carrying capacity in this zone did not deteriorate as evidenced with the positive slope of the force–displacement curve. However, the load-carrying capacity deteriorated slightly in the neg- ative zone due to the web and the flange local buckling.Photographs of specimen 1 during the test are shown in Figs.14 and 15. Severe local buckling occurred in the bottom flange and portion of the web next to the bottom flange as shown in Fig. 14. The length of this buckle extended over the entire length of the RBS. Plastic hinges developed in the RBS with extensive yielding occurring in the beam flanges as well as the web. Fig. 15 shows the crack that initiated along the transition of the RBS to the side wing plate. Ultimate fracture of specimen 1 was caused by a fracture in the bottom flange. This fracture resulted in almost total loss of the beam- carrying capacity. Specimen 1 developed0.05 rad of plastic rotation and showed no sign of distress at the face of the column as shown in Fig. 15.5.2. Specimens 3 and 4The response of specimens 3 and 4 is shown in Fig. 16. Initial yielding occured during cycles 7 and 8 at 1_y with significant yielding observed in the bottom flange. Progressing through the loading history, yielding started to propagate along the bottom flange on the RBS. During cycle 1.5_y initiation of web buckling was noted adjacent to the yielded bottom flange. Yielding started to propagate along the top flange of the RBS and some minor yielding along the middle stiffener. During the cycle of 3.5_y a severe web buckle developed along with flange local buckling. The flange and the web local buckling bec- ame more pronounced with each successive loading cycle.During the cycle 4.5 y, the axial load was increased to 3115 KN (700 kips) causing yielding to propagate to middle transverse stiffener. Progressing through the loading history, the flange and the web local buckling became more severe. For both specimens, testing was stopped at this point due to limitations in the test set-up. No failures occurred in specimens 3 and 4. However, upon removing specimen 3 to outside the laboratory a hairline crack was observed at the CJP weld of the bottom flange to the column.The maximum forces applied to specimens 3 and 4 were 890 kN (200 kip) and 912 kN (205 kip). The load-carrying capacity deteriorated by 20% at the end of the tests for negative cycles due to the web and the flange local buckling. This gradual reduction started after about 0.015 to 0.02 rad of plastic rotation. The load-carrying capacity during positive cycles (axial tension applied in the girder) did not deteriorate as evidenced with the slope of the force–displacement envelope for specimen 3 shownin Fig. 17.A photograph of specimen 3 before testing is shown in Fig.18. Fig. 19 is aFig. 16. Hysteretic behavior of specimens 3 and 4 in terms of moment at middle RBS versus beam plastic rotation.photograph of specimen 4 taken after the application of 0.014 rad displacem- ent cycles, showing yielding and local buckling at the hinge region. The beam web yielded over its full depth. The most intense yielding was observed in the web bottom portion, between the bottom flange and the middle stiffener. The web top portion also showed yielding, although less severe than within the bottom portion. Yielding was observed in the longitudinal stiffener. No yiel- ding was observed in the web of the column in the joint panel zone. The un- reduced portion of the beam flanges near the face of the column did not show yielding either. The maximum displacement applied was 174 mm, and the maximum moment at the middle of the RBS was 1.51 times the plastic mom ent capacity of the beam. The plastic hinge rotation reached was about 0.032 rad (the hinge is located at a distance 0.54d from the column surface,where d is the depth of the beam).5.2.1. Strain distribution around connectionThe strain distribution across the flanges–outer surface of specimen 3 is shown in Figs. 20 and 21. The readings and the distributions of the strains in specimens 1, 2 and 4 (not presented) showed a similar trend. Also the seque- nce of yielding in these specimens is similar to specimen 3.The strain at 51 mm from the column in the top flange–outer surface remained below 0.2% during negative cycles. The top flange, at the same location, yielded in compression only Thelongitudinal strains along the centerline of the bottom–flange outer face are shown in Figs. 22 and 23 for positive and negative cycles, respectively. From Fig.23, it is found that the strain on the RBS becomes several times larg- er than that near the column after cycles at –1.5_y; this is responsible for theflange local buckling. Bottom flange local buckling occurred when the average strain in the plate reached the strain-hardening value (esh _ 0.018) and the reduced-beam portion of the plate was fully yielded under longitudinal stresses and permitted the development of a full buckled wave.5.2.2. Cumulative energy dissipatedThe cumulative energy dissipated by the specimens is shown in Fig. 24. The cumulative energy dissipated was calculated as the sum of the areas enclosed the lateral load–lateral displacement hysteresis loops. Energy dissipation sta- rted to increase after cycle 12 at 2.5 y (Fig. 19). At large drift levels, energy dissipation augments significantly with small changes in drift. Specimen 2 dissipated more energy than specimen 1, which fractured at RBS transition. However, for both specimens the trend is similar up to cycles at q =0.04 radIn general, the dissipated energy during negative cycles was1.55 times bigger than that for positive cycles in specimens 1 and2. For specimens 3 and 4 the dissipated energy during negative cycles was 120%, on the average, that of the positive cycles. The combined phenomena of yielding, strain hardening, in-plane and out- of-plane deformations, and local distortion all occurred soon after the bottom flange RBS yielded.6. ConclusionsBased on the observations made during the tests, and on the analysis of the instrumentation, the following conclusions weredeveloped:1. The plastic rotation exceeded the 3% radians in all test specimens.2. Plastification of RBS developed in a stable manner.3. The overstrength ratios for the flexural strength of the test specimens were equal to 1.56 for specimen 1 and 1.51 for specimen4. The flexural strength capacity was based on the nominal yield strength and on the FEMA-273 beam–column equation.4. The plastic local buckling of the bottom flange and the web was not accompanied by a significant deterioration in the load-carrying capacity.5. Although flange local buckling did not cause an immediate degradation of strength, it did induce web local buckling.6. The longitudinal stiffener added in the middle of the beam web assisted in transferring the axial forces and in delaying the formation of web local buckling. How ever, this has caused a much higher overstrength ratio, which had a significant impact on the capacity design of the welded joints, panel zone and the column.7. A gradual strength reduction occurred after 0.015 to 0.02 rad of plastic rotation during negative cycles. No strength degradation was observed during positive cycles.8. Compression axial load under 0.0325Py does not affect substantially the connection deformation capacity.9. CGMRFS with properly designed and detailed RBS connections is a reliable system to resist earthquakes.AcknowledgementsStructural Design Engineers, Inc. of San Francisco financially supported the experimental program. The tests were performedin the Large Scale Structures Laboratory of the University of Nevada, Reno. The participation of Elizabeth Ware, Adrianne Dietrich and of the technical staff is gratefully acknowledged.References受弯钢框架结点在变化轴向荷载和侧向位移的作用下的周期性行为摘要这篇论文讨论的是在变化的轴向荷载和侧向位移的作用下,接受测试的四种受弯钢结点的周期性行为。
土木工程专业毕业设计外文文献及翻译

英文原文:Rehabilitation of rectangular simply supported RC beams with shear deficiencies using CFRP compositesAhmed Khalifa a,*,Antonio Nanni ba Department of Structural Engineering,University of Alexandria,Alexandria 21544, Egyptb Department of Civil Engineering,University of Missouri at Rolla,Rolla,MO 65409,USAReceived 28 April 1999;received in revised form 30 October 2001; accepted 10 January 2002AbstractThe present study examines the shear performance and modes of failure of rectangular simply supported reinforced concrete(RC) beams designed with shear deficiencies. These members were strengthened with externally bonded carbon fiber reinforced polymer (CFRP) sheets and evaluated in the laboratory。
The experimental program consisted of twelve full-scale RC beams tested to fail in shear. The variables investigated within this programincluded steel stirrups,and the shear span-to—effective depth ratio,as well as amount and distribution of CFRP。
土木工程类外文文献翻译.d

1 中文翻译摘要:为了研究连续型拓扑优化理论在实际工程中的应用,该文给出了一种多层钢框架支撑体系连续型拓扑优化设计方法。
基于灵敏度分析,探讨了连续体结构在多工况荷载作用下、同时受应力和多位移约束的拓扑优化删除准则。
为保证拓扑优化结果的合理性,提出了设计区域平均厚度的概念。
在该文给出的优化设计方法中,首先在不考虑位移约束的情况下对无支撑钢框架进行优化设计,然后在有位移约束的条件下采用渐进结构优化算法和删除准则对支撑体系进行连续型拓扑优化设计,并将获得的支撑最优拓扑构形转化成相应的杆件。
通过一个3跨12层钢框架支撑体系的拓扑优化设计实例验证了该文给出的钢框架支撑体系连续型拓扑优化设计方法的有效性。
关键词:钢框架;支撑体系;连续型;拓扑优化;渐进结构优化1.1钢筋混凝土素混凝土是由水泥、水、细骨料、粗骨料(碎石或;卵石)、空气,通常还有其他外加剂等经过凝固硬化而成。
将可塑的混凝土拌合物注入到模板内,并将其捣实,然后进行养护,以加速水泥与水的水化反应,最后获得硬化的混凝土。
其最终制成品具有较高的抗压强度和较低的抗拉强度。
其抗拉强度约为抗压强度的十分之一。
因此,截面的受拉区必须配置抗拉钢筋和抗剪钢筋以增加钢筋混凝土构件中较弱的受拉区的强度。
由于钢筋混凝土截面在均质性上与标准的木材或钢的截面存在着差异,因此,需要对结构设计的基本原理进行修改。
将钢筋混凝土这种非均质截面的两种组成部分按一定比例适当布置,可以最好的利用这两种材料。
这一要求是可以达到的。
因混凝土由配料搅拌成湿拌合物,经过振捣并凝固硬化,可以做成任何一种需要的形状。
如果拌制混凝土的各种材料配合比恰当,则混凝土制成品的强度较高,经久耐用,配置钢筋后,可以作为任何结构体系的主要构件。
浇筑混凝土所需要的技术取决于即将浇筑的构件类型,诸如:柱、梁、墙、板、基础,大体积混凝土水坝或者继续延长已浇筑完毕并且已经凝固的混凝土等。
对于梁、柱、墙等构件,当模板清理干净后应该在其上涂油,钢筋表面的锈及其他有害物质也应该被清除干净。
土木工程-毕业设计-论文-外文翻译-中英文对照
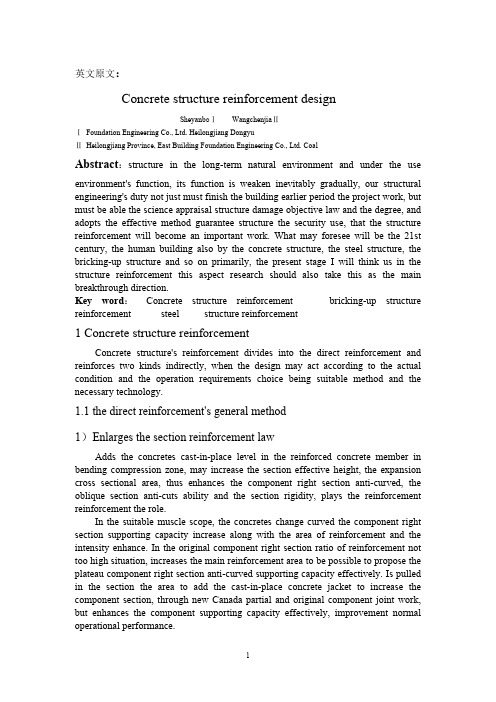
英文原文:Concrete structure reinforcement designSheyanb oⅠWangchenji aⅡⅠFoundation Engineering Co., Ltd. Heilongjiang DongyuⅡHeilongjiang Province, East Building Foundation Engineering Co., Ltd. CoalAbstract:structure in the long-term natural environment and under the use environment's function, its function is weaken inevitably gradually, our structural engineering's duty not just must finish the building earlier period the project work, but must be able the science appraisal structure damage objective law and the degree, and adopts the effective method guarantee structure the security use, that the structure reinforcement will become an important work. What may foresee will be the 21st century, the human building also by the concrete structure, the steel structure, the bricking-up structure and so on primarily, the present stage I will think us in the structure reinforcement this aspect research should also take this as the main breakthrough direction.Key word:Concrete structure reinforcement bricking-up structure reinforcement steel structure reinforcement1 Concrete structure reinforcementConcrete structure's reinforcement divides into the direct reinforcement and reinforces two kinds indirectly, when the design may act according to the actual condition and the operation requirements choice being suitable method and the necessary technology.1.1the direct reinforcement's general method1)Enlarges the section reinforcement lawAdds the concretes cast-in-place level in the reinforced concrete member in bending compression zone, may increase the section effective height, the expansion cross sectional area, thus enhances the component right section anti-curved, the oblique section anti-cuts ability and the section rigidity, plays the reinforcement reinforcement the role.In the suitable muscle scope, the concretes change curved the component right section supporting capacity increase along with the area of reinforcement and the intensity enhance. In the original component right section ratio of reinforcement not too high situation, increases the main reinforcement area to be possible to propose the plateau component right section anti-curved supporting capacity effectively. Is pulled in the section the area to add the cast-in-place concrete jacket to increase the component section, through new Canada partial and original component joint work, but enhances the component supporting capacity effectively, improvement normal operational performance.Enlarges the section reinforcement law construction craft simply, compatible, and has the mature design and the construction experience; Is suitable in Liang, the board, the column, the wall and the general structure concretes reinforcement; But scene construction's wet operating time is long, to produces has certain influence with the life, and after reinforcing the building clearance has certain reduction.2) Replacement concretes reinforcement lawThis law's merit with enlarges the method of sections to be close, and after reinforcing, does not affect building's clearance, but similar existence construction wet operating time long shortcoming; Is suitable somewhat low or has concretes carrier's and so on serious defect Liang, column in the compression zone concretes intensity reinforcement.3) the caking outsourcing section reinforcement lawOutside the Baotou Steel Factory reinforcement is wraps in the section or the steel plate is reinforced component's outside, outside the Baotou Steel Factory reinforces reinforced concrete Liang to use the wet outsourcing law generally, namely uses the epoxy resinification to be in the milk and so on methods with to reinforce the section the construction commission to cake a whole, after the reinforcement component, because is pulled with the compressed steel cross sectional area large scale enhancement, therefore right section supporting capacity and section rigidity large scale enhancement.This law also said that the wet outside Baotou Steel Factory reinforcement law, the stress is reliable, the construction is simple, the scene work load is small, but is big with the steel quantity, and uses in above not suitably 600C in the non-protection's situation the high temperature place; Is suitable does not allow in the use obviously to increase the original component section size, but requests to sharpen its bearing capacity large scale the concrete structure reinforcement.4) Sticks the steel reinforcement lawOutside the reinforced concrete member in bending sticks the steel reinforcement is (right section is pulled in the component supporting capacity insufficient sector area, right section compression zone or oblique section) the superficial glue steel plate, like this may enhance is reinforced component's supporting capacity, and constructs conveniently.This law construction is fast, the scene not wet work or only has the plastering and so on few wet works, to produces is small with the life influence, and after reinforcing, is not remarkable to the original structure outward appearance and the original clearance affects, but the reinforcement effect is decided to a great extent by the gummy craft and the operational level; Is suitable in the withstanding static function, and is in the normal humidity environment to bend or the tension member reinforcement.5) Glue fibre reinforcement plastic reinforcement lawOutside pastes the textile fiber reinforcement is pastes with the cementing material the fibre reinforcement compound materials in is reinforced the component to pull the region, causes it with to reinforce the section joint work, achieves sharpens the component bearing capacity the goal. Besides has glues the steel plate similar merit, but also has anticorrosive muddy, bears moistly, does not increase the self-weight of structure nearly, durably, the maintenance cost low status merit, but needs special fire protection processing, is suitable in each kind of stress nature concrete structure component and the general construction.This law's good and bad points with enlarge the method of sections to be close; Is suitable reinforcement which is insufficient in the concrete structure component oblique section supporting capacity, or must exert the crosswise binding force to the compressional member the situation.6) Reeling lawThis law's good and bad points with enlarge the method of sections to be close; Is suitable reinforcement which is insufficient in the concrete structure component oblique section supporting capacity, or must exert the crosswise binding force to the compressional member the situation.7) Fang bolt anchor lawThis law is suitable in the concretes intensity rank is the C20~C60 concretes load-bearing member transformation, the reinforcement; It is not suitable for already the above structure which and the light quality structure makes decent seriously. 1.2The indirect reinforcement's general method1)Pre-stressed reinforcement law(1)Thepre-stressed horizontal tension bar reinforces concretes member in bending,because the pre-stressed and increases the exterior load the combined action, in the tension bar has the axial tension, this strength eccentric transmits on the component through the pole end anchor (, when tension bar and Liang board bottom surface close fitting, tension bar can look for tune together with component, this fashion has partial pressures to transmit directly for component bottom surface), has the eccentric compression function in the component, this function has overcome the bending moment which outside the part the load produces, reduced outside the load effect, thus sharpened component's anti-curved ability. At the same time, because the tension bar passes to component's pressure function, the component crack development can alleviate, the control, the oblique section anti-to cut the supporting capacity also along with it enhancement.As a result of the horizontal lifting stem's function, the original component's section stress characteristic by received bends turned the eccentric compression, therefore, after the reinforcement, component's supporting capacity was mainly decided in bends under the condition the original component's supporting capacity 。
土木工程外文文献翻译(含中英文)
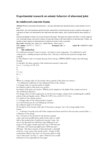
Experimental research on seismic behavior of abnormal jointin reinforced concrete frameAbstract :Based on nine plane abnormal joint s , one space abnormal joint experiment and a p seudo dynamic test of a powerplant model , the work mechanism and the hysteretic characteristic of abnormal joint are put to analysis in this paper. A conception of minor core determined by the small beam and small column , and a conclusion that the shear capacity of ab2normal joint depends on minor core are put forward in this paper. This paper also analyzes the effect s of axial compres2 sion , horizontal stirrup s and section variation of beam and column on the shear behavior of abnormal joint . Finally , the formula of shear capacity for abnormal joint in reinforced concrete f rame is provided.Key words : abnormal j oint ; minor core ; seismic behavior ; shear ca paci t yCLC number :TU375. 4 ; TU317. 1 Document code :A Article ID :100627930 (2006) 022*******1 Int roductionFor reinforced concrete f rame st ructure , t he joint is a key component . It is subjected to axialcomp ression , bending moment and shear force. The key is whet her the joint has enough shear capaci2ty. The Chinese Code f or S eismic Desi gn of B ui l di ngs ( GB5001122001) adopt s the following formulato calculate t he shear capacity of the reinforced concrete f rame joint .V j = 1. 1ηj f t b j h j + 0. 05ηj Nb jb c+ f yv A svjh b0 - a′ss(1)Where V j = design value of t he seismic shear capacity of the joint core section ;ηj = influential coefficient of t he orthogonal beam to the column ;f t = design value of concrete tensile st rength ;b j = effective widt h of the joint core section ;h j = dept h of the joint core section , Which can be adopted as t he depth of the column section int he verification direction ;N = design value of axial compression at t he bot tom of upper column wit h considering the combi2 nation of the eart hquake action , When N > 015 f c b c h c , let N = 0. 5 f c b c h c ;b c = widt h of t he column section ;f yv = design value of t he stirrup tensile st rengt h ;A svj = total stirrup area in a set making up one layer ;h b0 = effective dept h of t he beam.If t he dept h of two beams at the side of t he joint is unequal , h b0 = t he average depth of two beams.a′s = distance f rom the cent roid of the compression beam steel bar to the ext reme concrete fiber . s = distance of t he stirrup .Eq. 1 is based on t he formula in t he previous seismiccode[1 ] and some modifications made eavlicr and it is suit2able to the normal joint of reinforced concrete f rame , butnot to t he abnormal one which has large different in t hesection of t he upper column and lower one (3 600 mm and1 200 mm) , lef t beam and right beam (1 800 mm and 1200 mm) . The shear capacity of abnormal joint s calculat2ed by Eq. 1 may cause some unsafe result s. A type of ab2normal joint which of ten exist s in t he power plant st ruc2t ure is discussed ( see Fig. 1) , and it s behavior was st ud2ied based on t he experiment in t his paper2 Experimental workAccording to the above problem , and t he experiment of plane abnormal joint s and space abnormal joint , a p seudo dynamic test of space model of power plant st ruct ure was carried out . The aim of t hisst udy is to set up a shear force formula and to discuss seismic behavior s of t he joint s.According to the characteristic of t he power plant st ruct ure , nine abnormal joint s and one space abnormal joint were designed in t he experiment . The scale of the model s is one2fif t h. Tab. 1 and Tab.2 show t he dimensions and reinforcement detail s of t he specimens.Fig. 2 shows the typical const ruction drawing of t he specimen. Fig. 3 shows the loading set up . These specimens are subjected to low2cyclic loading , the loading process of which is cont rolled by force and displacement , t he preceding yield loading by force and subsequent yield by t he displacement .The shear deformation of the joint core , t he st rain of the longit udinal steel and t he stirrup are main measuring items.3 Analysis of test result s3. 1 Main resultsTab. 3 shows t he main result s of t he experiment .3. 2 Failure process of specimenBased on t he experiment , t he process of t he specimens’failure includes four stages , namely , t he initial cracking , t he t horough cracking , the ultimate stage and t he failure stage.(1) Initial cracking stageWhen t he first diagonal crack appears along t he diagonal direction in t he core af ter loading , it s widt h is about 0. 1mm , which is named initial cracking stage of joint core. Before t he initial cracking stage , t he joint remains elastic performance , and the variety of stiff ness is not very obvious on t hep2Δcurve. At t his stage concrete bear s most of the core shear force while stirrup bears few. At t he timewhen t he initial crack occur s , t he st ress of t he stirrup at t he crack increase sharply and t he st rain is a2bout 200 ×10 - 6 —300 ×10 - 6 . The shear deformation of t he core at t his stage is very small (less than 1×10 - 3 radian ,generally between 0. 4 ×10 - 3 and 0. 8 ×10 - 3 radian) .(2) Thorough cracking stageWit h the load increasing following t he initial cracking stage , the second and t hird crossing diago2 nal cracks will appear at t he core. The core is cut into some small rhombus pieces which will become at least one main inclined crack across t he core diagonal . The widt h of cracks enlarges obviously , andt he wider ones are generally about 0. 5mm , which is named core t horough cracking stage. The st ress of stirrup increases obviously , and the stirrup in t he middle of t he core is near to yielding or has yiel2 ded. The joint core shows nonlinear property on t he p2Δcurve , and it enter s elastic2plastic stage. Theload at t horough cracking stage is about 80 % —90 % load.(3) Ultimate stageAt t his stage , t he widt h of t he cracks is about 1mm or more and some new cracks continue to oc2 cur . The shear deformation at t he core is much larger and concrete begins to collap se. Af ter several cyclic loading , the force reaches the maximum value , which is called ultimate stage. The load increase is due to t he enhancing of the concrete aggregate mechanical f riction between cracks. At t he same timet he st ress of stirrup increases gradually. On t he one hand stirrup resist s t he horizontal shear , and on t he ot her hand the confinement effect to t he expanding compression concrete st rengthens continuous2ly , which can also improve t he shear capacity of diagonal compression bar mechanism.(4) Failure stageAs the load circulated , concrete in t he core began to collap se , and t he deformation increased sharply , while the capacity began to drop . It was found t hat t he slip of reinforcement in t he beam wasvery serious in t he experiment . Wit h t he load and it s circulation time increasing , t he zoon wit houtbond gradually permeated towards t he internal core , enhancing t he burden of t he diagonal compressionbar mechanism and accelerates the compression failure of concrete. Fig. 4 shows t he p hotos of typical damaged joint s.A p seudo dynamic test of space model ofpower plant st ruct ure was carried out to researcht he working behavior of t he abnormal joint s in re2al st ructure and the seismic behavior of st ructure.Fig. 5 shows the p hoto of model .The test includes two step s. The fir st is thep seudo dynamic test . At t his step , El2Cent rowave is inp ut and the peak acceleration variesf rom 50 gal to 1 200 gal . The seismic response is measured. The second is t he p seudo static test . Theloading can’t stop until t he model fail s.Fig. 7 Minor coreThe experiment shows t hat t he dist ribution and development of t hecrack is influenced by t he rest rictive effect of the ort hogonal beam , andt he crack of joint core mainly dist ributes under t he orthogonal beam( see Fig. 6) , which is different f rom t he result of t he plane joint test ,but similar to J 4210.3. 3 Analysis of test results3. 3. 1 Mechanical analysisIn t he experiment , t he location of the initial crack of t he exteriorjoint and the crushed position of concrete both appear in the middle oft he joint core , and t he position is near t he centerline of t he upper col2umn. The initial crack and crushed position of t he concrete of the interior joint both appear in t he mi2 nor core ( see Fig. 4 ,Fig. 7) . For interior abnormal joint t he crack doesn’t appear or develop in t he ma2j or core out side of the mi nor core until t horough cracking takes place , while t he crack seldom appearsin t he shadow region ( see Fig. 7) as the joint fail s. Therefore , for abnormal joint , t he shear capacity oft he joint core depends on t he properties of t he mi nor core , namely , on t he st rengt h grades of concrete ,t he size and the reinforcement of t he mi nor core , get t he effect of t he maj or core dimension can’t be neglected.Mechanical effect s are t he same will that of t he normal joint , when t he forces t ransfer to t he mi2 nor core t hrough column and beam and reinforcement bar . Therefore , t he working mechanisms of nor2mal joint , including t russ mechanism , diagonal compression bar mechanism and rest rictive mechanismof stirrup , are also suitable for mi nor core of t he abnormal joint , but their working characteristic is not symmet rical when the load rever ses. Fig. 8 illust rates t he working mechanism of t he abnormal joint .When t he load t ransfer to mi nor core , t he diagonal compression bar area of mi nor core is biggert han normal joint core2composed by small column and small beam of abnormal joint , which is due to t he compressive st ress diff usion of concrete compressive region of the beam and column , while at t hesame time t he compression carried by the diagonal compression bar becomes large. Because t he main part of bond force of column and beam is added to t he diagonal comp ression bar but cont rasting wit h t he increased area of diagonal compression bar , t he increased action is small . The region in the maj orcore but out of the mi nor core has less st ress dist ribution and fewer cracks. The region can confine t heexpansion of t he concrete of t he mi nor core diagonal compression bar concrete , which enhances t he concrete compressive st rengt h of mi nor core diagonal compression bar .Making t he mi nor core as st udy element , the area increment of concrete diagonal compression barin mi nor core is related to t he st ress diff usion of t he beam and column compressive region. The magni2t ude of diff usion area is related to height difference of t he beam sections and column sections. Name2ly , it is related to t he size of mi nor core section and maj or core section. Thus , the increased shearst rengt h magnit ude caused by mi nor core rest rictive effect on maj or core can be measured quantitative2ly by t he ratio of maj or core area to mi nor core area. And it al so can be expressed that t he rest rictive effect is quantitatively related to t he ratio. Obviously , t he bigger t he ratio is and t he st ronger t he con2finement is , t he st ronger t he bearing capacity is.The region in the maj or core but under the mi nor core still need stirrup bar because of t he hori2 zontal force t ransferred by bigger beam bar . But force is small .3. 3. 2 load2displacement curves analysisFig. 9 shows t he typical load2displacement curves at t he beam end of t he exterior and interiorjoint . The figure showing t hat t he rigidity of t he specimens almo st doesn’t degenerate when t he initialcrack appear s in t he core , and a turning point can be found at t he curve but it isn’t very obvious. Wit ht he crack developing , an obvious t urning point can be found at t he curve , and at t his time , t he speci2men yields. Then t he load can increase f urt her , but it can’t increase too much f rom yielding load to ultimate load. When t he concrete at t he core collap ses and the plastic hinge occured at t he beamend ,t he load begins to decrease rat her t han increase.The ductility coefficient of two kinds of joint s is basically more than 3 (except for J 3 - 9) . But it should be noted t hat the design of specimens is based on the principle of joint core failure. The ratio of reinforcement of beam and column tends to be lower t han practical project s. If t he ratio is larger , t he failure of joint is probably prior to t hat of beam and column , so t he hysteretic curve reflect s t he ductil ity property of joint core.Joint experiment should be a subst ruct ure test (or a test of composite body of beams and col2 umns) . So t he load2displacement curves at t he beam end should be a general reflection of t he joint be2havior work as a subst ruct ure. Providing t hat the joint core fails af ter t he yield of beam and column (especially for beam) , t he load2displacement curves at t he beam end is plump , so the principle of “st rong col umn and weak beam , st ron ger j oi nt" should be ensured which conforms to t he seismic re2sistant principle.The experiment shows t hat t he stiff ness of joint core is large. Before the joint reaches ultimatestage , t he stiff ness of joint core decreases a little and the irrecoverable residual deformation is very small under alternate loading. When joint core enter s failure stage , t he shear deformation increases sharply , and t he stiff ness of joint core decreases obviously , and t he hysteretic curve appears shrink2 age , which is because of t he cohesive slip of beam reinforcement .3. 4 Influential Factors of Abnormal Joint Shear CapacityThe fir st factor is axial compression. Axial compression can enlarge t he compression area of col2 umn , and increase t he concrete compression area of joint core[124 ] . At t he same time , more shearst ransferred f rom beam steel to t he edge of joint core concrete will add to t he diagonal compression bar ,which decreases t he edge shear t hat leads to the crack of joint core concrete. So t he existence of axial comp ression cont ributes to imp roving t he capacity of initial cracks at joint core.The effect of axial compression on t horough cracking load and ultimate load isn’t very obvious[1 ] . The reason is t hat cont rasting wit h no axial compression , the accumulated damage effect of joint coreunder rever sed loading wit h axial compression is larger . Alt hough axial compression can improve t heshear st rengt h of concrete , it increases accumulated damage effect which leads to a decrease of the ad2vantage of axial compression. Therefore t he effect of axial compression on t horough cracking loadandultimate load is not very obvious.Hence , considering the lack of test data of abnormal joint , t he shear capacity formula of abnormal joint adopt 0. 05 nf c b j h j to calculate the effect of axial compression , which is based on the result s of t his experiment and referenced to t he experimental st udy and statistical analysis of Meinheit and J irsa ,et [5 ] .The second factor is horizontal stirrup . Horizontal stirrup has no effect on t he initial crackingshear of abnormal joint , while greatly improves t he t horough cracking shear . Af ter crack appeared , t he stirrup begins to resist t he shear and confines t he expansion of concrete[ 6 ] . This experiment showst hat t he st ress of stirrup s in each layer is not equal . When the joint fail s , t he stirrup s don’t yield simultaneous. Fig. 10 shows t he change of st ress dist ribution of stirrup s along core height wit h t he loadincreasing. Through analyzing test result s , it can be known t hat 80 percent of the height at the joint core can yield.The last factor is the change of sec2tion size of t he beam and column. Thesection change decreases t he initial crack2ing load about 30 p resent of abnormaljoint and makes t he initial crack appear att he position of joint mi nor core. The rea2son for t his p henomenon is t hat small up2per column section makes t he confinementof mi nor core concrete decrease and t heedge shear increase. But t he section change has lit tle effect on thorough cracking load. Af ter t horoughcracking , the joint enter s ultimate state while the external load can’t increase too much , which is dif2 ferent f rom t he behavior of abnormal joint t hat can carry much shear af ter thorough cracking.3. 5 Shear force formula of abnormal jointAs a part of f rame , t he design of joint shall meet t he requirement s of the f rame st ruct ure design , namely , t he joint design should not damage t he basic performance of t he st ruct ure.According to the principle of st ronger j oi nt , it is necessary for joint to have some safety reserva2 tion. The raised cost for conservational estimation of t he joint bearing capacity is small . But t he con2 servational estimation is very important to t he safety of the f rame st ruct ure. At t horough cracking stage , t he widt h of most cracks is more t han 0. 2 mm , which is bigger than t he suggested limit value in t he concrete design code. Big cracks will influence t he durability of st ruct ure. Hence , the bearing capacity at t horough cracking stage is applied to calculating t he bearing capacity of joint . According to t he analysis of t he working mechanisms of abnormal joint , it could be concludedt hat t he bearing capacity of joint core mainly depends on mi nor core when t he force t ransferred f rommaj or core to mi nor core. All kinds of working mechanisms are suitable to mi nor core element . Thus , a formula for calculating t he shear capacity of abnormal joint can be obtained based on Eq. 1. According to the above analysis of influential factor s of shear capacity of abnormal joint , and ref2 erence to Eq. 1 , a formula for calculating t he shear capacity of reinforced concrete f rame abnormal jointis suggested as followsV j = 0. 1ηjξ1 f c b j h j + 0. 1ηj nξ2 f c b j h j +ξ3 f yv A svj h0 - a′s s(2)Where h0 = effective dept h of small beam section in abnormal joint ;ξ1 = influential coefficient consider2ing mi nor core on working as cont rol element for calculating ;ξ2 = influential coefficient considering effect of axial compression ratio , it s value is 0. 5 , andξ3 = influential coefficient considering t hestir2rup doesn’t yield simultaneous , it s value is 0. 8 , n = N/ f c b c h j .From Fig. 8 , the shear capacity of abnormal joint depends on mi nor core , while maj or core has re2st rictive effect on mi nor core. The effect is related to t he ratio of maj or core area to mi nor core area , so assumingξ1 =αA d A x (3)Where A d = area of abnormal joint maj or core , choosing it as t he value of t he dept h of big beam multiplying t he height of lower column ; A x = area of abnormal joint mi nor core , choosing it as t he value oft he depth of small beam multiplying the height of upper column ; andα= parameter to be defined , it s value is 0. 8 derived f rom t he result s of t he experiment ( see Tab. 4)Then Eq. 2 can be replaced byV j = 0. 1ηjαA d A x f c b j h j + 0. 05ηj n f c b j h j + 0. 8 f yv h0 - a′s s(4)4 ConclusionsThe following conclusions can be drawn f rom t his study.(1) The seismic behavior of abnormal joint in reinforced concrete f rame st ruct ure is poor . Af tert horough cracking , t he joint enter s ultimate state while the external load can’t increase too much , andt he safety reservation of joint isn’t sufficient .(2) The characteristic of bearing load of minor core is similar to that of normal joint , but t he area bearing load is different . The shear capacity depend on t he size , t he st rengt h of concrete and the rein2forcement of mi nor core in abnormal joint . The maj or core has rest rictive effect on mi nor core. (3) Joint experiment should be a subst ruct ure test or a test of composite body of beams and col2 umns. Therefore t he load2displacement curves of t he beam end should be a general reflection of t he joint behavior working as a subst ruct ure. Studies of t he hysteretic curve of subst ruct ure should be based on t he whole st ructure. It is critical to guarantee t he stiff ness and st rengt h of joint core in prac2tice.(4) The formula of shear capacity for abnormal joint in reinforced concrete f rame is provided.References[1 ] TAN GJ iu2ru . The seismic behavior of steel reinforced concrete f rame [M] . Nanjing :Dongnan University Press ,1989 :1572163.[2 ] The research group of reinforcement concrete f rame joint . Shear capacity research of reinforced concrete f rame jointon reversed2cyclic loading[J ] . Journal of Building St ructures , 1983 , (6) :9215.[3 ] PAULA Y T ,PARK R. Joint s reinforced concrete f rames designed for earthquake resistance[ R] . New Zealand :De2partment of civil Engineering , University of Canterbury , Christchurch , 1984.[4 ] FU Jian2ping. Seismic behavior research of reinforced concrete f rame joint with the consideration of axialforce[J ] .Journal of Chongqing Univ , 2000 , (5) :23227.[5 ] MEINHEIT D F ,J IRSA J O. Shear st rength of R/ C beam2column connections [J ] . ACI St ructural Journal , 1993 ,(3) :61271.[6 ] KITA YAMA K, OTANI S ,AO YAMA H. Development of design criteria for RC interior beam2column joints ,de2sign of beam2column joint s for seismic resistance[ R] . SP123 ,ACI ,Det roit , 1991 :61272.[7 ] GB5001122001 ,Code for seismic design of buildings [ S] . Beijing : China Architectural and BuildingPress ,2001.钢筋混凝土框架异型节点抗震性能试验研究摘要:基于8个钢筋混凝土框架异型节点的试验研究,分析了异型框架节点的受力与常规框架节点的异同。
土木工程类专业英文文献及翻译

土木工程类专业英文文献及翻译第一篇:土木工程类专业英文文献及翻译PAVEMENT PROBLEMS CAUSEDBY COLLAPSIBLE SUBGRADESBy Sandra L.Houston,1 Associate Member, ASCE(Reviewed by the Highway Division)ABSTRACT: Problem subgrade materials consisting of collapsible soils are com-mon in arid environments, which have climatic conditions and depositional and weathering processes favorable to their formation.Included herein is a discussion of predictive techniques that use commonly available laboratory equipment and testing methods for obtaining reliable estimates of the volume change for these problem soils.A method for predicting relevant stresses and corresponding collapse strains for typical pavement subgrades is presented.Relatively simple methods of evaluating potential volume change, based on results of familiar laboratory tests, are used.INTRODUCTION When a soil is given free access to water, it may decrease in volume,increase in volume, or do nothing.A soil that increases in volume is called a swelling or expansive soil, and a soil that decreases in volume is called a collapsible soil.The amount of volume change that occurs depends on the soil type and structure, the initial soil density, the imposed stress state, and the degree and extent of wetting.Subgrade materials comprised of soils that change volume upon wetting have caused distress to highways since the be-ginning of the professional practice and have cost many millions of dollars in roadway repairs.The prediction of the volume changes that may occur in the field is the first step in making an economic decision for dealing withthese problem subgrade materials.Each project will have different design considerations, economic con-straints, and risk factors that will have to be taken into account.However, with a reliable method for making volume change predictions, the best design relative to the subgrade soils becomes a matter of economic comparison, and a much more rational design approach may be made.For example, typical techniques for dealing with expansive clays include:(1)In situ treatments with substances such as lime, cement, or fly-ash;(2)seepage barriers and/ or drainage systems;or(3)a computing of the serviceability loss and a mod-ification of the design to “accept” the anticipated expansion.In order to make the most economical decision, the amount of volume change(especially non-uniform volume change)must be accurately estimated, and the degree of road roughness evaluated from these data.Similarly, alternative design techniques are available for any roadway problem.The emphasis here will be placed on presenting economical and simple methods for:(1)Determining whether the subgrade materials are collapsible;and(2)estimating the amount of volume change that is likely to occur in the 'Asst.Prof., Ctr.for Advanced Res.in Transp., Arizona State Univ., Tempe, AZ 85287.Note.Discussion open until April 1, 1989.To extend the closing date one month,a written request must be filed with the ASCE Manager of Journals.The manuscriptfor this paper was submitted for review and possible publication on February 3, 1988.This paper is part of the Journal of Transportation.Engineering, Vol.114, No.6,November, 1988.ASCE, ISSN 0733-947X/88/0006-0673/$1.00 + $.15 per page.Paper No.22902.673field for the collapsible soils.Then this information will place the engineerin a position to make a rational design decision.Collapsible soils are fre-quently encountered in an arid climate.The depositional process and for-mation of these soils, and methods for identification and evaluation of theamount of volume change that may occur, will be discussed in the followingsections.COLLAPSIBLE SOILSFormation of Collapsible SoilsCollapsible soils have high void ratios and low densities and are typicallycohesionless or only slightly cohesive.In an arid climate, evaporation greatlyexceeds rainfall.Consequently, only the near-surface soils become wettedfrom normal rainfall.It is the combination of the depositional process andthe climate conditions that leads to the formation of the collapsible soil.Although collapsible soils exist in nondesert regions, the dry environment inwhich evaporation exceeds precipitation is very favorable for the formationof the collapsible structure.As the soil dries by evaporation, capillary tension causes the remainingwater to withdraw into the soil grain interfaces, bringing with it soluble salts,clay, and silt particles.As the soil continues to dry, these salts, clays, andsilts come out of solution, and “tack-we ld” the larger grains together.Thisleads to a soil structure that has high apparent strength at its low, naturalwater content.However, collapse of the “cemented” structure may occurupon wetting because the bonding material weakens and softens, and the soilis unstable at any stress level that exceeds that at which the soil had beenpreviously wetted.Thus, if the amount of water made available to the soilis increased above that which naturally exists, collapse can occur at fairlylow levels of stress, equivalent only to overburden soil pressure.Additionalloads, such as traffic loading or the presence of a bridge structure, add tothe collapse, especially of shallow collapsible soil.The triggering mechanismfor collapse, however, is the addition of water.Highway Problems Resulting from Collapsible SoilsNonuniform collapse can result from either a nonhomogeneous subgradedeposit in which differing degrees of collapse potential exist and/or fromnonuniform wetting of subgrade materials.When differential collapse ofsubgrade soils occurs, the result is a rough, wavy surface, and potentiallymany miles of extensively damaged highway.There have been several re-ported cases for which differential collapse has been cited as the cause ofroadway or highway bridge distress.A few of these in the Arizona and NewMexico region include sections of 1-10 near Benson, Arizona, and sectionsof 1-25 in the vicinity of Algadonas, New Mexico(Lovelace et al.1982;Russman 1987).In addition to the excessive waviness of the roadway sur-face, bridge foundations failures, such as the Steins Pass Highway bridge,1-10, in Arizona, have frequently been identified with collapse of foundationsoils.Identification of Collapsible SoilsThere have been many techniques proposed for identifying a collapsiblesoil problem.These methods range from qualitative index tests conducted on4disturbed samples, to response to wetting tests conducted on relatively un-disturbed samples, to in situ meausrement techniques.In all cases, the en-gineer must first know if the soils may become wetted to a water contentabove their natural moisture state, and if so, what the extent of the potentialwetted zone will be.Most methods for identifying collapsible soils are onlyqualitative in nature, providing no information on the magnitude of the col-lapse strain potential.These qualitative methods are based on various func-tions of dry density, moisture content, void ratio, specific gravity, and At-terberg limits.In situ measurement methods appear promising in some cases, in that manyresearchers feel that sample disturbance is greatly reduced, and that a morenearly quantitative measure of collapse potential is obtainable.However,in situ test methods for collapsible soils typically suffer from the deficien-cy of an unknown extent and degree of wetting during the field test.Thismakes a quantitative measurement difficult because the zone of materialbeing influenced is not well-known, and, therefore, the actual strains, in-duced by the addition of stress and water, are not well-known.In addition,the degree of saturation achieved in the field test is variable and usuallyunknown.Based on recently conducted research, it appears that the most reliablemethod for identifying a collapsible soil problem is to obtain the best qualityundisturbed sample possible and to subject this sample to a response to wet-ting test in the laboratory.The results of a simple oedometer test will indicatewhether the soil is collapsible and, at the same time, give a direct measureof the amount of collapse strain potential that may occur in the field.Potentialproblems associated with the direct sampling method include sample distur-bance and the possibility that the degree of saturation achieved in the fieldwill be less than that achieved in the laboratory test.The quality of an undisturbed sample is related most strongly to the arearatio of the tube that is used for sample collection.The area ratio is a measureof the ratio of the cross-sectional area of the sample collected to the cross-sectional area of the sample tube.A thin-walled tube sampler by definitionhas an area ratio of about 10-15%.Although undisturbed samples are bestobtained through the use of thin-walled tube samplers, it frequently occursthat these stiff, cemented collapsible soils, especially those containing gravel,cannot be sampled unless a tube with a much thicker wall is used.Samplershaving an area ratio as great as 56% are commonly used for Arizona col-lapsible soils.Further, it may take considerable hammering of the tube todrive the sample.The result is, of course, some degree of sample distur-bance, broken.bonds, densification, and a correspondingly reduced collapsemeasured upon laboratory testing.However, for collapsible soils, which arecompressive by definition, the insertion of the sample tube leads to localshear failure at the base of the cutting edge, and, therefore, there is lesssample disturbance than would be expected for soils that exhibit general shearfailure(i.e., saturated clays or dilative soils).Results of an ongoing studyof sample disturbance for collapsible soils indicate that block samples some-times exhibit somewhat higher collapse strains compared to thick-walled tubesamples.Block samples are usually assumed to be the very best obtainableundisturbed samples, although they are frequently difficult-to-impossible toobtain, especially at substantial depths.The overall effect of sample distur-bance is a slight underestimate of the collapse potential for the soil.675译文:湿陷性地基引起的路面问题作者:...摘要:在干旱环境中,湿陷性土壤组成的路基材料是很常见的,干旱环境中的气候条件、沉积以及风化作用都有利于湿陷性土的形成。
土木工程文献外文翻译(中英互译版)

使用加固纤维聚合物增强混凝土梁的延性作者:Nabil F. Grace, George Abel-Sayed, Wael F. Ragheb摘要:一种为加强结构延性的新型单轴柔软加强质地的聚合物(FRP)已在被研究,开发和生产(在结构测试的中心在劳伦斯技术大学)。
这种织物是两种碳纤维和一种玻璃纤维的混合物,而且经过设计它们在受拉屈服时应变值较低,从而体现出伪延性的性能。
通过对八根混凝土梁在弯曲荷载作用下的加固和检测对研制中的织物的效果和延性进行了研究。
用现在常用的单向碳纤维薄片、织物和板进行加固的相似梁也进行了检测,以便同用研制中的织物加固梁进行性能上的比较。
这种织物经过设计具有和加固梁中的钢筋同时屈服的潜力,从而和未加固梁一样,它也能得到屈服台阶。
相对于那些用现在常用的碳纤维加固体系进行加固的梁,这种研制中的织物加固的梁承受更高的屈服荷载,并且有更高的延性指标。
这种研制中的织物对加固机制体现出更大的贡献。
关键词:混凝土,延性,纤维加固,变形介绍外贴粘合纤维增强聚合物(FRP)片和条带近来已经被确定是一种对钢筋混凝土结构进行修复和加固的有效手段。
关于应用外贴粘合FRP板、薄片和织物对混凝土梁进行变形加固的钢筋混凝土梁的性能,一些试验研究调查已经进行过报告。
Saadatmanesh和Ehsani(1991)检测了应用玻璃纤维增强聚合物(GFRP)板进行变形加固的钢筋混凝土梁的性能。
Ritchie等人(1991)检测了应用GFRP,碳纤维增强聚合物(CFRP)和G/CFRP板进行变形加固的钢筋混凝土梁的性能。
Grace等人(1999)和Triantafillou(1992)研究了应用CFRP薄片进行变形加固的钢筋混凝土梁的性能。
Norris,Saadatmanesh和Ehsani(1997)研究了应用单向CFRP薄片和CFRP织物进行加固的混凝土梁的性能。
在所有的这些研究中,加固的梁比未加固的梁承受更高的极限荷载。
(完整版)土木工程毕业设计外文文献翻译
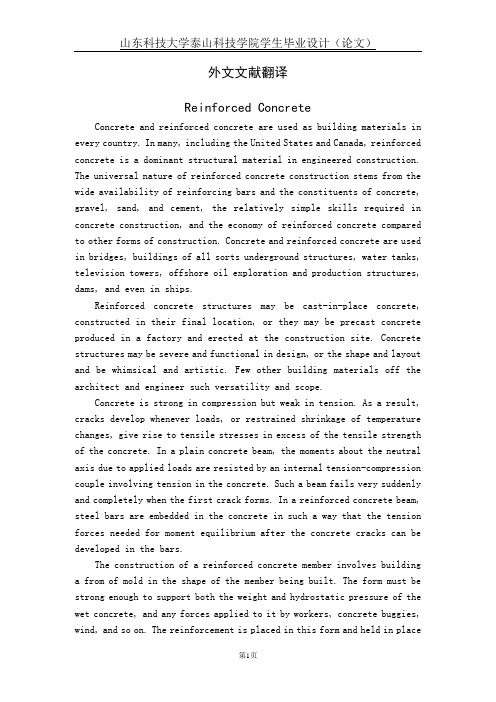
外文文献翻译Reinforced ConcreteConcrete and reinforced concrete are used as building materials in every country. In many, including the United States and Canada, reinforced concrete is a dominant structural material in engineered construction. The universal nature of reinforced concrete construction stems from the wide availability of reinforcing bars and the constituents of concrete, gravel, sand, and cement, the relatively simple skills required in concrete construction, and the economy of reinforced concrete compared to other forms of construction. Concrete and reinforced concrete are used in bridges, buildings of all sorts underground structures, water tanks, television towers, offshore oil exploration and production structures, dams, and even in ships.Reinforced concrete structures may be cast-in-place concrete, constructed in their final location, or they may be precast concrete produced in a factory and erected at the construction site. Concrete structures may be severe and functional in design, or the shape and layout and be whimsical and artistic. Few other building materials off the architect and engineer such versatility and scope.Concrete is strong in compression but weak in tension. As a result, cracks develop whenever loads, or restrained shrinkage of temperature changes, give rise to tensile stresses in excess of the tensile strength of the concrete. In a plain concrete beam, the moments about the neutral axis due to applied loads are resisted by an internal tension-compression couple involving tension in the concrete. Such a beam fails very suddenly and completely when the first crack forms. In a reinforced concrete beam, steel bars are embedded in the concrete in such a way that the tension forces needed for moment equilibrium after the concrete cracks can be developed in the bars.The construction of a reinforced concrete member involves building a from of mold in the shape of the member being built. The form must be strong enough to support both the weight and hydrostatic pressure of the wet concrete, and any forces applied to it by workers, concrete buggies, wind, and so on. The reinforcement is placed in this form and held in placeduring the concreting operation. After the concrete has hardened, the forms are removed. As the forms are removed, props of shores are installed to support the weight of the concrete until it has reached sufficient strength to support the loads by itself.The designer must proportion a concrete member for adequate strength to resist the loads and adequate stiffness to prevent excessive deflections. In beam must be proportioned so that it can be constructed. For example, the reinforcement must be detailed so that it can be assembled in the field, and since the concrete is placed in the form after the reinforcement is in place, the concrete must be able to flow around, between, and past the reinforcement to fill all parts of the form completely.The choice of whether a structure should be built of concrete, steel, masonry, or timber depends on the availability of materials and on a number of value decisions. The choice of structural system is made by the architect of engineer early in the design, based on the following considerations:1. Economy. Frequently, the foremost consideration is the overall const of the structure. This is, of course, a function of the costs of the materials and the labor necessary to erect them. Frequently, however, the overall cost is affected as much or more by the overall construction time since the contractor and owner must borrow or otherwise allocate money to carry out the construction and will not receive a return on this investment until the building is ready for occupancy. In a typical large apartment of commercial project, the cost of construction financing will be a significant fraction of the total cost. As a result, financial savings due to rapid construction may more than offset increased material costs. For this reason, any measures the designer can take to standardize the design and forming will generally pay off in reduced overall costs.In many cases the long-term economy of the structure may be more important than the first cost. As a result, maintenance and durability are important consideration.2. Suitability of material for architectural and structural function.A reinforced concrete system frequently allows the designer to combine the architectural and structural functions. Concrete has the advantage that it is placed in a plastic condition and is given the desired shapeand texture by means of the forms and the finishing techniques. This allows such elements ad flat plates or other types of slabs to serve as load-bearing elements while providing the finished floor and / or ceiling surfaces. Similarly, reinforced concrete walls can provide architecturally attractive surfaces in addition to having the ability to resist gravity, wind, or seismic loads. Finally, the choice of size of shape is governed by the designer and not by the availability of standard manufactured members.3. Fire resistance. The structure in a building must withstand the effects of a fire and remain standing while the building is evacuated and the fire is extinguished. A concrete building inherently has a 1- to 3-hour fire rating without special fireproofing or other details. Structural steel or timber buildings must be fireproofed to attain similar fire ratings.4. Low maintenance.Concrete members inherently require less maintenance than do structural steel or timber members. This is particularly true if dense, air-entrained concrete has been used for surfaces exposed to the atmosphere, and if care has been taken in the design to provide adequate drainage off and away from the structure. Special precautions must be taken for concrete exposed to salts such as deicing chemicals.5. Availability of materials. Sand, gravel, cement, and concrete mixing facilities are very widely available, and reinforcing steel can be transported to most job sites more easily than can structural steel. As a result, reinforced concrete is frequently used in remote areas.On the other hand, there are a number of factors that may cause one to select a material other than reinforced concrete. These include:1. Low tensile strength.The tensile strength concrete is much lower than its compressive strength ( about 1/10 ), and hence concrete is subject to cracking. In structural uses this is overcome by using reinforcement to carry tensile forces and limit crack widths to within acceptable values. Unless care is taken in design and construction, however, these cracks may be unsightly or may allow penetration of water. When this occurs, water or chemicals such as road deicing salts may cause deterioration or staining of the concrete. Special design details are required in such cases. In the case of water-retaining structures, special details and /of prestressing are required to prevent leakage.2. Forms and shoring. The construction of a cast-in-place structure involves three steps not encountered in the construction of steel or timber structures. These are ( a ) the construction of the forms, ( b ) the removal of these forms, and (c) propping or shoring the new concrete to support its weight until its strength is adequate. Each of these steps involves labor and / or materials, which are not necessary with other forms of construction.3. Relatively low strength per unit of weight for volume.The compressive strength of concrete is roughly 5 to 10% that of steel, while its unit density is roughly 30% that of steel. As a result, a concrete structure requires a larger volume and a greater weight of material than does a comparable steel structure. As a result, long-span structures are often built from steel.4. Time-dependent volume changes. Both concrete and steel undergo-approximately the same amount of thermal expansion and contraction. Because there is less mass of steel to be heated or cooled, and because steel is a better concrete, a steel structure is generally affected by temperature changes to a greater extent than is a concrete structure. On the other hand, concrete undergoes frying shrinkage, which, if restrained, may cause deflections or cracking. Furthermore, deflections will tend to increase with time, possibly doubling, due to creep of the concrete under sustained loads.In almost every branch of civil engineering and architecture extensive use is made of reinforced concrete for structures and foundations. Engineers and architects requires basic knowledge of reinforced concrete design throughout their professional careers. Much of this text is directly concerned with the behavior and proportioning of components that make up typical reinforced concrete structures-beams, columns, and slabs. Once the behavior of these individual elements is understood, the designer will have the background to analyze and design a wide range of complex structures, such as foundations, buildings, and bridges, composed of these elements.Since reinforced concrete is a no homogeneous material that creeps, shrinks, and cracks, its stresses cannot be accurately predicted by the traditional equations derived in a course in strength of materials forhomogeneous elastic materials. Much of reinforced concrete design in therefore empirical, i.e., design equations and design methods are based on experimental and time-proved results instead of being derived exclusively from theoretical formulations.A thorough understanding of the behavior of reinforced concrete will allow the designer to convert an otherwise brittle material into tough ductile structural elements and thereby take advantage of concrete’s desirable characteristics, its high compressive strength, its fire resistance, and its durability.Concrete, a stone like material, is made by mixing cement, water, fine aggregate ( often sand ), coarse aggregate, and frequently other additives ( that modify properties ) into a workable mixture. In its unhardened or plastic state, concrete can be placed in forms to produce a large variety of structural elements. Although the hardened concrete by itself, i.e., without any reinforcement, is strong in compression, it lacks tensile strength and therefore cracks easily. Because unreinforced concrete is brittle, it cannot undergo large deformations under load and fails suddenly-without warning. The addition fo steel reinforcement to the concrete reduces the negative effects of its two principal inherent weaknesses, its susceptibility to cracking and its brittleness. When the reinforcement is strongly bonded to the concrete, a strong, stiff, and ductile construction material is produced. This material, called reinforced concrete, is used extensively to construct foundations, structural frames, storage takes, shell roofs, highways, walls, dams, canals, and innumerable other structures and building products. Two other characteristics of concrete that are present even when concrete is reinforced are shrinkage and creep, but the negative effects of these properties can be mitigated by careful design.A code is a set technical specifications and standards that control important details of design and construction. The purpose of codes it produce structures so that the public will be protected from poor of inadequate and construction.Two types f coeds exist. One type, called a structural code, is originated and controlled by specialists who are concerned with the proper use of a specific material or who are involved with the safe design of a particular class of structures.The second type of code, called a building code, is established to cover construction in a given region, often a city or a state. The objective of a building code is also to protect the public by accounting for the influence of the local environmental conditions on construction. For example, local authorities may specify additional provisions to account for such regional conditions as earthquake, heavy snow, or tornados. National structural codes genrally are incorporated into local building codes.The American Concrete Institute ( ACI ) Building Code covering the design of reinforced concrete buildings. It contains provisions covering all aspects of reinforced concrete manufacture, design, and construction. It includes specifications on quality of materials, details on mixing and placing concrete, design assumptions for the analysis of continuous structures, and equations for proportioning members for design forces.All structures must be proportioned so they will not fail or deform excessively under any possible condition of service. Therefore it is important that an engineer use great care in anticipating all the probable loads to which a structure will be subjected during its lifetime.Although the design of most members is controlled typically by dead and live load acting simultaneously, consideration must also be given to the forces produced by wind, impact, shrinkage, temperature change, creep and support settlements, earthquake, and so forth.The load associated with the weight of the structure itself and its permanent components is called the dead load. The dead load of concrete members, which is substantial, should never be neglected in design computations. The exact magnitude of the dead load is not known accurately until members have been sized. Since some figure for the dead load must be used in computations to size the members, its magnitude must be estimated at first. After a structure has been analyzed, the members sized, and architectural details completed, the dead load can be computed more accurately. If the computed dead load is approximately equal to the initial estimate of its value ( or slightly less ), the design is complete, but if a significant difference exists between the computed and estimated values of dead weight, the computations should be revised using an improved value of dead load. An accurate estimate of dead load is particularly important when spans are long, say over 75 ft ( 22.9 m ),because dead load constitutes a major portion of the design load.Live loads associated with building use are specific items of equipment and occupants in a certain area of a building, building codes specify values of uniform live for which members are to be designed.After the structure has been sized for vertical load, it is checked for wind in combination with dead and live load as specified in the code. Wind loads do not usually control the size of members in building less than 16 to 18 stories, but for tall buildings wind loads become significant and cause large forces to develop in the structures. Under these conditions economy can be achieved only by selecting a structural system that is able to transfer horizontal loads into the ground efficiently.钢筋混凝土在每一个国家,混凝土及钢筋混凝土都被用来作为建筑材料。
土木工程毕业论文中英文翻译
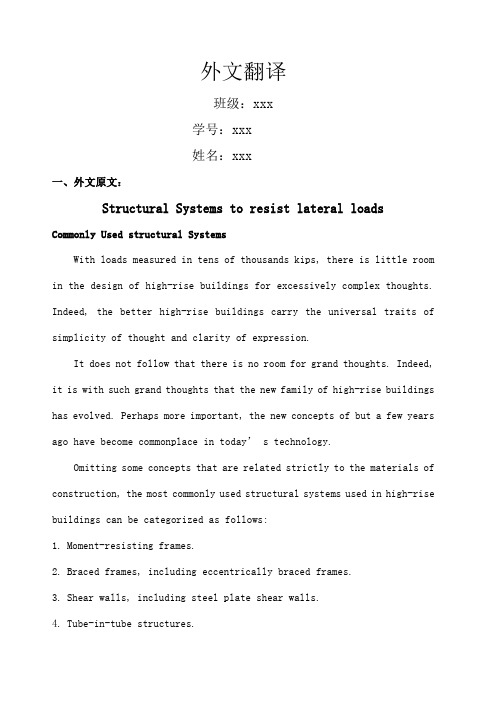
外文翻译班级:xxx学号:xxx姓名:xxx一、外文原文:Structural Systems to resist lateral loads Commonly Used structural SystemsWith loads measured in tens of thousands kips, there is little room in the design of high-rise buildings for excessively complex thoughts. Indeed, the better high-rise buildings carry the universal traits of simplicity of thought and clarity of expression.It does not follow that there is no room for grand thoughts. Indeed, it is with such grand thoughts that the new family of high-rise buildings has evolved. Perhaps more important, the new concepts of but a few years ago have become commonplace in today’ s technology.Omitting some concepts that are related strictly to the materials of construction, the most commonly used structural systems used in high-rise buildings can be categorized as follows:1.Moment-resisting frames.2.Braced frames, including eccentrically braced frames.3.Shear walls, including steel plate shear walls.4.Tube-in-tube structures.5.Core-interactive structures.6.Cellular or bundled-tube systems.Particularly with the recent trend toward more complex forms, but in response also to the need for increased stiffness to resist the forces from wind and earthquake, most high-rise buildings have structural systems built up of combinations of frames, braced bents, shear walls, and related systems. Further, for the taller buildings, the majorities are composed of interactive elements in three-dimensional arrays.The method of combining these elements is the very essence of the design process for high-rise buildings. These combinations need evolve in response to environmental, functional, and cost considerations so as to provide efficient structures that provoke the architectural development to new heights. This is not to say that imaginative structural design can create great architecture. To the contrary, many examples of fine architecture have been created with only moderate support from the structural engineer, while only fine structure, not great architecture, can be developed without the genius and the leadership of a talented architect. In any event, the best of both is needed to formulate a truly extraordinary design of a high-rise building.While comprehensive discussions of these seven systems are generally available in the literature, further discussion is warranted here .The essence of the design process is distributed throughout the discussion.Moment-Resisting FramesPerhaps the most commonly used system in low-to medium-rise buildings, the moment-resisting frame, is characterized by linear horizontal and vertical members connected essentially rigidly at their joints. Such frames are used as a stand-alone system or in combination with other systems so as to provide the needed resistance to horizontal loads. In the taller of high-rise buildings, the system is likely to be found inappropriate for a stand-alone system, this because of the difficulty in mobilizing sufficient stiffness under lateral forces.Analysis can be accomplished by STRESS, STRUDL, or a host of other appropriate computer programs; analysis by the so-called portal method of the cantilever method has no place in today’s technology.Because of the intrinsic flexibility of the column/girder intersection, and because preliminary designs should aim to highlight weaknesses of systems, it is not unusual to use center-to-center dimensions for the frame in the preliminary analysis. Of course, in the latter phases of design, a realistic appraisal in-joint deformation is essential.Braced Frame sThe braced frame, intrinsically stiffer than the moment –resisting frame, finds also greater application to higher-rise buildings. The system is characterized by linear horizontal, vertical, and diagonal members, connected simply or rigidly at their joints. It is used commonly inconjunction with other systems for taller buildings and as a stand-alone system in low-to medium-rise buildings.While the use of structural steel in braced frames is common, concrete frames are more likely to be of the larger-scale variety.Of special interest in areas of high seismicity is the use of the eccentric braced frame.Again, analysis can be by STRESS, STRUDL, or any one of a series of two –or three dimensional analysis computer programs. And again, center-to-center dimensions are used commonly in the preliminary analysis. Shear wallsThe shear wall is yet another step forward along a progression of ever-stiffer structural systems. The system is characterized by relatively thin, generally but not always concrete elements that provide both structural strength and separation between building functions.In high-rise buildings, shear wall systems tend to have a relatively high aspect ratio, that is, their height tends to be large compared to their width. Lacking tension in the foundation system, any structural element is limited in its ability to resist overturning moment by the width of the system and by the gravity load supported by the element. Limited to a narrow overturning, One obvious use of the system, which does have the needed width, is in the exterior walls of building, where the requirement for windows is kept small.Structural steel shear walls, generally stiffened against buckling by a concrete overlay, have found application where shear loads are high. The system, intrinsically more economical than steel bracing, is particularly effective in carrying shear loads down through the taller floors in the areas immediately above grade. The system has the further advantage of having high ductility a feature of particular importance in areas of high seismicity.The analysis of shear wall systems is made complex because of the inevitable presence of large openings through these walls. Preliminary analysis can be by truss-analogy, by the finite element method, or by making use of a proprietary computer program designed to consider the interaction, or coupling, of shear walls.Framed or Braced TubesThe concept of the framed or braced or braced tube erupted into the technology with the IBM Building in Pittsburgh, but was followed immediately with the twin 110-story towers of the World Trade Center, New York and a number of other buildings .The system is characterized by three –dimensional frames, braced frames, or shear walls, forming a closed surface more or less cylindrical in nature, but of nearly any plan configuration. Because those columns that resist lateral forces are placed as far as possible from the cancroids of the system, the overall moment of inertia is increased and stiffness is very high.The analysis of tubular structures is done using three-dimensional concepts, or by two- dimensional analogy, where possible, whichever method is used, it must be capable of accounting for the effects of shear lag.The presence of shear lag, detected first in aircraft structures, is a serious limitation in the stiffness of framed tubes. The concept has limited recent applications of framed tubes to the shear of 60 stories. Designers have developed various techniques for reducing the effects of shear lag, most noticeably the use of belt trusses. This system finds application in buildings perhaps 40stories and higher. However, except for possible aesthetic considerations, belt trusses interfere with nearly every building function associated with the outside wall; the trusses are placed often at mechanical floors, mush to the disapproval of the designers of the mechanical systems. Nevertheless, as a cost-effective structural system, the belt truss works well and will likely find continued approval from designers. Numerous studies have sought to optimize the location of these trusses, with the optimum location very dependent on the number of trusses provided. Experience would indicate, however, that the location of these trusses is provided by the optimization of mechanical systems and by aesthetic considerations, as the economics of the structural system is not highly sensitive to belt truss location.Tube-in-Tube StructuresThe tubular framing system mobilizes every column in the exterior wallin resisting over-turning and shearing forces. The term‘tube-in-tube’is largely self-explanatory in that a second ring of columns, the ring surrounding the central service core of the building, is used as an inner framed or braced tube. The purpose of the second tube is to increase resistance to over turning and to increase lateral stiffness. The tubes need not be of the same character; that is, one tube could be framed, while the other could be braced.In considering this system, is important to understand clearly the difference between the shear and the flexural components of deflection, the terms being taken from beam analogy. In a framed tube, the shear component of deflection is associated with the bending deformation of columns and girders , the webs of the framed tube while the flexural component is associated with the axial shortening and lengthening of columns , the flanges of the framed tube. In a braced tube, the shear component of deflection is associated with the axial deformation of diagonals while the flexural component of deflection is associated with the axial shortening and lengthening of columns.Following beam analogy, if plane surfaces remain plane , the floor slabs,then axial stresses in the columns of the outer tube, being farther form the neutral axis, will be substantially larger than the axial stresses in the inner tube. However, in the tube-in-tube design, when optimized, the axial stresses in the inner ring of columns may be as high, or evenhigher, than the axial stresses in the outer ring. This seeming anomaly is associated with differences in the shearing component of stiffness between the two systems. This is easiest to under-stand where the inner tube is conceived as a braced , shear-stiff tube while the outer tube is conceived as a framed , shear-flexible tube.Core Interactive StructuresCore interactive structures are a special case of a tube-in-tube wherein the two tubes are coupled together with some form of three-dimensional space frame. Indeed, the system is used often wherein the shear stiffness of the outer tube is zero. The United States Steel Building, Pittsburgh, illustrates the system very well. Here, the inner tube is a braced frame, the outer tube has no shear stiffness, and the two systems are coupled if they were considered as systems passing in a straight line from the “hat” structure. Note that the exterior columns would be improperly modeled if they were considered as systems passing in a straight line from the “hat” to the foundations; these columns are perhaps 15% stiffer as they follow the elastic curve of the braced core. Note also that the axial forces associated with the lateral forces in the inner columns change from tension to compression over the height of the tube, with the inflection point at about 5/8 of the height of the tube. The outer columns, of course, carry the same axial force under lateral load for the full height of the columns because the columns because the shearstiffness of the system is close to zero.The space structures of outrigger girders or trusses, that connect the inner tube to the outer tube, are located often at several levels in the building. The AT&T headquarters is an example of an astonishing array of interactive elements:1.The structural system is 94 ft wide, 196ft long, and 601ft high.2.Two inner tubes are provided, each 31ft by 40 ft , centered 90 ft apartin the long direction of the building.3.The inner tubes are braced in the short direction, but with zero shearstiffness in the long direction.4.A single outer tube is supplied, which encircles the buildingperimeter.5.The outer tube is a moment-resisting frame, but with zero shearstiffness for the center50ft of each of the long sides.6.A space-truss hat structure is provided at the top of the building.7.A similar space truss is located near the bottom of the building8.The entire assembly is laterally supported at the base on twinsteel-plate tubes, because the shear stiffness of the outer tube goes to zero at the base of the building.Cellular structuresA classic example of a cellular structure is the Sears Tower, Chicago,a bundled tube structure of nine separate tubes. While the Sears Towercontains nine nearly identical tubes, the basic structural system has special application for buildings of irregular shape, as the several tubes need not be similar in plan shape, It is not uncommon that some of the individual tubes one of the strengths and one of the weaknesses of the system.This special weakness of this system, particularly in framed tubes, has to do with the concept of differential column shortening. The shortening of a column under load is given by the expression△=ΣfL/EFor buildings of 12 ft floor-to-floor distances and an average compressive stress of 15 ksi 138MPa, the shortening of a column under load is 15 1212/29,000 or per story. At 50 stories, the column will have shortened to in. 94mm less than its unstressed length. Where one cell of a bundled tube system is, say, 50stories high and an adjacent cell is, say, 100stories high, those columns near the boundary between .the two systems need to have this differential deflection reconciled.Major structural work has been found to be needed at such locations. In at least one building, the Rialto Project, Melbourne, the structural engineer found it necessary to vertically pre-stress the lower height columns so as to reconcile the differential deflections of columns in close proximity with the post-tensioning of the shorter column simulatingthe weight to be added on to adjacent, higher columns.二、原文翻译:抗侧向荷载的结构体系常用的结构体系若已测出荷载量达数千万磅重,那么在高层建筑设计中就没有多少可以进行极其复杂的构思余地了;确实,较好的高层建筑普遍具有构思简单、表现明晰的特点;这并不是说没有进行宏观构思的余地;实际上,正是因为有了这种宏观的构思,新奇的高层建筑体系才得以发展,可能更重要的是:几年以前才出现的一些新概念在今天的技术中已经变得平常了;如果忽略一些与建筑材料密切相关的概念不谈,高层建筑里最为常用的结构体系便可分为如下几类:1.抗弯矩框架;2.支撑框架,包括偏心支撑框架;3.剪力墙,包括钢板剪力墙;4.筒中框架;5.筒中筒结构;6.核心交互结构;7.框格体系或束筒体系;特别是由于最近趋向于更复杂的建筑形式,同时也需要增加刚度以抵抗几力和地震力,大多数高层建筑都具有由框架、支撑构架、剪力墙和相关体系相结合而构成的体系;而且,就较高的建筑物而言,大多数都是由交互式构件组成三维陈列;将这些构件结合起来的方法正是高层建筑设计方法的本质;其结合方式需要在考虑环境、功能和费用后再发展,以便提供促使建筑发展达到新高度的有效结构;这并不是说富于想象力的结构设计就能够创造出伟大建筑;正相反,有许多例优美的建筑仅得到结构工程师适当的支持就被创造出来了,然而,如果没有天赋甚厚的建筑师的创造力的指导,那么,得以发展的就只能是好的结构,并非是伟大的建筑;无论如何,要想创造出高层建筑真正非凡的设计,两者都需要最好的;虽然在文献中通常可以见到有关这七种体系的全面性讨论,但是在这里还值得进一步讨论;设计方法的本质贯穿于整个讨论;设计方法的本质贯穿于整个讨论中;抗弯矩框架抗弯矩框架也许是低,中高度的建筑中常用的体系,它具有线性水平构件和垂直构件在接头处基本刚接之特点;这种框架用作独立的体系,或者和其他体系结合起来使用,以便提供所需要水平荷载抵抗力;对于较高的高层建筑,可能会发现该本系不宜作为独立体系,这是因为在侧向力的作用下难以调动足够的刚度;我们可以利用STRESS,STRUDL 或者其他大量合适的计算机程序进行结构分析;所谓的门架法分析或悬臂法分析在当今的技术中无一席之地,由于柱梁节点固有柔性,并且由于初步设计应该力求突出体系的弱点,所以在初析中使用框架的中心距尺寸设计是司空惯的;当然,在设计的后期阶段,实际地评价结点的变形很有必要;支撑框架支撑框架实际上刚度比抗弯矩框架强,在高层建筑中也得到更广泛的应用;这种体系以其结点处铰接或则接的线性水平构件、垂直构件和斜撑构件而具特色,它通常与其他体系共同用于较高的建筑,并且作为一种独立的体系用在低、中高度的建筑中;尤其引人关注的是,在强震区使用偏心支撑框架;此外,可以利用STRESS,STRUDL,或一系列二维或三维计算机分析程序中的任何一种进行结构分析;另外,初步分析中常用中心距尺寸;剪力墙剪力墙在加强结构体系刚性的发展过程中又前进了一步;该体系的特点是具有相当薄的,通常是而不总是混凝土的构件,这种构件既可提供结构强度,又可提供建筑物功能上的分隔;在高层建筑中,剪力墙体系趋向于具有相对大的高宽经,即与宽度相比,其高度偏大;由于基础体系缺少应力,任何一种结构构件抗倾覆弯矩的能力都受到体系的宽度和构件承受的重力荷载的限制;由于剪力墙宽度狭狭窄受限,所以需要以某种方式加以扩大,以便提从所需的抗倾覆能力;在窗户需要量小的建筑物外墙中明显地使用了这种确有所需要宽度的体系;钢结构剪力墙通常由混凝土覆盖层来加强以抵抗失稳,这在剪切荷载大的地方已得到应用;这种体系实际上比钢支撑经济,对于使剪切荷载由位于地面正上方区域内比较高的楼层向下移特别有效;这种体系还具有高延性之优点,这种特性在强震区特别重要;由于这些墙内必然出同一些大孔,使得剪力墙体系分析变得错综复杂;可以通过桁架模似法、有限元法,或者通过利用为考虑剪力墙的交互作用或扭转功能设计的专门计处机程序进行初步分析框架或支撑式筒体结构:框架或支撑式筒体最先应用于IBM公司在Pittsburgh的一幢办公楼,随后立即被应用于纽约双子座的110层世界贸易中心摩天大楼和其他的建筑中;这种系统有以下几个显着的特征:三维结构、支撑式结构、或由剪力墙形成的一个性质上差不多是圆柱体的闭合曲面,但又有任意的平面构成;由于这些抵抗侧向荷载的柱子差不多都被设置在整个系统的中心,所以整体的惯性得到提高,刚度也是很大的;在可能的情况下,通过三维概念的应用、二维的类比,我们可以进行筒体结构的分析;不管应用那种方法,都必须考虑剪力滞后的影响;这种最先在航天器结构中研究的剪力滞后出现后,对筒体结构的刚度是一个很大的限制;这种观念已经影响了筒体结构在60层以上建筑中的应用;设计者已经开发出了很多的技术,用以减小剪力滞后的影响,这其中最有名的是桁架的应用;框架或支撑式筒体在40层或稍高的建筑中找到了自己的用武之地;除了一些美观的考虑外,桁架几乎很少涉及与外墙联系的每个建筑功能,而悬索一般设置在机械的地板上,这就令机械体系设计师们很不赞成;但是,作为一个性价比较好的结构体系,桁架能充分发挥它的性能,所以它会得到设计师们持续的支持;由于其最佳位置正取决于所提供的桁架的数量,因此很多研究已经试图完善这些构件的位置;实验表明:由于这种结构体系的经济性并不十分受桁架位置的影响,所以这些桁架的位置主要取决于机械系统的完善,审美的要求,筒中筒结构:筒体结构系统能使外墙中的柱具有灵活性,用以抵抗颠覆和剪切力;“筒中筒”这个名字顾名思义就是在建筑物的核心承重部分又被包围了第二层的一系列柱子,它们被当作是框架和支撑筒来使用;配置第二层柱的目的是增强抗颠覆能力和增大侧移刚度;这些筒体不是同样的功能,也就是说,有些筒体是结构的,而有些筒体是用来支撑的;在考虑这种筒体时,清楚的认识和区别变形的剪切和弯曲分量是很重要的,这源于对梁的对比分析;在结构筒中,剪切构件的偏角和柱、纵梁例如:结构筒中的网等的弯曲有关,同时,弯曲构件的偏角取决于柱子的轴心压缩和延伸例如:结构筒的边缘等;在支撑筒中,剪切构件的偏角和对角线的轴心变形有关,而弯曲构件的偏角则与柱子的轴心压缩和延伸有关;根据梁的对比分析,如果平面保持原形例如:厚楼板,那么外层筒中柱的轴心压力就会与中心筒柱的轴心压力相差甚远,而且稳定的大于中心筒;但是在筒中筒结构的设计中,当发展到极限时,内部轴心压力会很高的,甚至远远大于外部的柱子;这种反常的现象是由于两种体系中的剪切构件的刚度不同;这很容易去理解,内筒可以看成是一个支撑或者说是剪切刚性的筒,而外筒可以看成是一个结构或者说是剪切弹性的筒;核心交互式结构:核心交互式结构属于两个筒与某些形式的三维空间框架相配合的筒中筒特殊情况;事实上,这种体系常用于那种外筒剪切刚度为零的结构;位于Pittsburgh的美国钢铁大楼证实了这种体系是能很好的工作的;在核心交互式结构中,内筒是一个支撑结构,外筒没有任何剪切刚度,而且两种结构体系能通过一个空间结构或“帽”式结构共同起作用;需要指出的是,如果把外部的柱子看成是一种从“帽”到基础的直线体系,这将是不合适的;根据支撑核心的弹性曲线,这些柱子只发挥了刚度的15%;同样需要指出的是,内柱中与侧向力有关的轴向力沿筒高度由拉力变为压力,同时变化点位于筒高度的约5/8处;当然,外柱也传递相同的轴向力,这种轴向力低于作用在整个柱子高度的侧向荷载,因为这个体系的剪切刚度接近于零;把内外筒相连接的空间结构、悬臂梁或桁架经常遵照一些规范来布置;美国电话电报总局就是一个布置交互式构件的生动例子;1、结构体系长米,宽米,高米;2、布置了两个筒,每个筒的尺寸是米×米,在长方向上有米的间隔;3、在短方向上内筒被支撑起来,但是在长方向上没有剪切刚度;4、环绕着建筑物布置了一个外筒;5、外筒是一个瞬时抵抗结构,但是在每个长方向的中心米都没有剪切刚度;6、在建筑的顶部布置了一个空间桁架构成的“帽式”结构;7、在建筑的底部布置了一个相似的空间桁架结构;8、由于外筒的剪切刚度在建筑的底部接近零,整个建筑基本上由两个钢板筒来支持;框格体系或束筒体系结构:位于美国芝加哥的西尔斯大厦是箱式结构的经典之作,它由九个相互独立的筒组成的一个集中筒;由于西尔斯大厦包括九个几乎垂直的筒,而且筒在平面上无须相似,基本的结构体系在不规则形状的建筑中得到特别的应用;一些单个的筒高于建筑一点或很多是很常见的;事实上,这种体系的重要特征就在于它既有坚固的一面,也有脆弱的一面;这种体系的脆弱,特别是在结构筒中,与柱子的压缩变形有很大的关系,柱子的压缩变形有下式计算:△=ΣfL/E对于那些层高为米左右和平均压力为138MPa的建筑,在荷载作用下每层柱子的压缩变形为1512/29000或毫米;在第50层柱子会压缩94毫米,小于它未受压的长度;这些柱子在50层的时候和100层的时候的变形是不一样的,位于这两种体系之间接近于边缘的那些柱需要使这种不均匀的变形得以调解;主要的结构工作都集中在布置中;在Melbourne的Rialto项目中,结构工程师发现至少有一幢建筑,很有必要垂直预压低高度的柱子,以便使柱不均匀的变形差得以调解,调解的方法近似于后拉伸法,即较短的柱转移重量到较高的邻柱上;。
- 1、下载文档前请自行甄别文档内容的完整性,平台不提供额外的编辑、内容补充、找答案等附加服务。
- 2、"仅部分预览"的文档,不可在线预览部分如存在完整性等问题,可反馈申请退款(可完整预览的文档不适用该条件!)。
- 3、如文档侵犯您的权益,请联系客服反馈,我们会尽快为您处理(人工客服工作时间:9:00-18:30)。
1 中文翻译摘要:为了研究连续型拓扑优化理论在实际工程中的应用,该文给出了一种多层钢框架支撑体系连续型拓扑优化设计方法。
基于灵敏度分析,探讨了连续体结构在多工况荷载作用下、同时受应力和多位移约束的拓扑优化删除准则。
为保证拓扑优化结果的合理性,提出了设计区域平均厚度的概念。
在该文给出的优化设计方法中,首先在不考虑位移约束的情况下对无支撑钢框架进行优化设计,然后在有位移约束的条件下采用渐进结构优化算法和删除准则对支撑体系进行连续型拓扑优化设计,并将获得的支撑最优拓扑构形转化成相应的杆件。
通过一个3跨12层钢框架支撑体系的拓扑优化设计实例验证了该文给出的钢框架支撑体系连续型拓扑优化设计方法的有效性。
关键词:钢框架;支撑体系;连续型;拓扑优化;渐进结构优化1.1钢筋混凝土素混凝土是由水泥、水、细骨料、粗骨料(碎石或;卵石)、空气,通常还有其他外加剂等经过凝固硬化而成。
将可塑的混凝土拌合物注入到模板内,并将其捣实,然后进行养护,以加速水泥与水的水化反应,最后获得硬化的混凝土。
其最终制成品具有较高的抗压强度和较低的抗拉强度。
其抗拉强度约为抗压强度的十分之一。
因此,截面的受拉区必须配置抗拉钢筋和抗剪钢筋以增加钢筋混凝土构件中较弱的受拉区的强度。
由于钢筋混凝土截面在均质性上与标准的木材或钢的截面存在着差异,因此,需要对结构设计的基本原理进行修改。
将钢筋混凝土这种非均质截面的两种组成部分按一定比例适当布置,可以最好的利用这两种材料。
这一要求是可以达到的。
因混凝土由配料搅拌成湿拌合物,经过振捣并凝固硬化,可以做成任何一种需要的形状。
如果拌制混凝土的各种材料配合比恰当,则混凝土制成品的强度较高,经久耐用,配置钢筋后,可以作为任何结构体系的主要构件。
浇筑混凝土所需要的技术取决于即将浇筑的构件类型,诸如:柱、梁、墙、板、基础,大体积混凝土水坝或者继续延长已浇筑完毕并且已经凝固的混凝土等。
对于梁、柱、墙等构件,当模板清理干净后应该在其上涂油,钢筋表面的锈及其他有害物质也应该被清除干净。
浇筑基础前,应将坑底土夯实并用水浸湿6英寸,以免土壤从新浇的混凝土中吸收水分。
一般情况下,除使用混凝土泵浇筑外,混凝土都应在水平方向分层浇筑,并使用插入式或表面式高频电动振捣器捣实。
必须记住,过分的振捣将导致骨料离析和混凝土泌浆等现象,因而是有害的。
水泥的水化作用发生在有水分存在,而且气温在50°F以上的条件下。
为了保证水泥的水化作用得以进行,必须具备上述条件。
如果干燥过快则会出现表面裂缝,这将有损与混凝土的强度,同时也会影响到水泥水化作用的充分进行。
设计钢筋混凝土构件时显然需要处理大量的参数,诸如宽度、高度等几何尺寸,配筋的面积,钢筋的应变和混凝土的应变,钢筋的应力等等。
因此,在选择混凝土截面时需要进行试算并作调整,根据施工现场条件、混凝土原材料的供应情况、业主提出的特殊要求、对建筑和净空高度的要求、所用的设计规范以及建筑物周围环境条件等最后确定截面。
钢筋混凝土通常是现场浇注的合成材料,它与在工厂中制造的标准的钢结构梁、柱等不同,因此对于上面所提到的一系列因素必须予以考虑。
对结构体系的各个部位均需选定试算截面并进行验算,以确定该截面的名义强度是否足以承受所作用的计算荷载。
由于经常需要进行多次试算,才能求出所需的截面,因此设计时第一次采用的数值将导致一系列的试算与调整工作。
选择混凝土截面时,采用试算与调整过程可以使复核与设计结合在一起。
因此,当试算截面选定后,每次设计都是对截面进行复核。
手册、图表和微型计算机以及专用程序的使用,使这种设计方法更为简捷有效,而传统的方法则是把钢筋混凝土的复核与单纯的设计分别进行处理。
1.2土方工程由于和土木工程中任何其他工种的施工方法与费用相比较,土方挖运的施工方法与费用的变化都要快得多,因此对于有事业心的人来说,土方工程是一个可以大有作为的领域。
在1935年,目前采用的利用轮胎式机械设备进行土方挖运的方法大多数还没有出现。
那是大部分土方是采用窄轨铁路运输,在这目前来说是很少采用的。
当时主要的开挖方式是使用正铲、反铲、拉铲或抓斗等挖土机,尽管这些机械目前仍然在广泛应用,但是它们只不过是目前所采用的许多方法中的一小部分。
因此,一个工程师为了使自己在土方挖运设备方面的知识跟得上时代的发展,他应当花费一些时间去研究现代的机械。
一般说来,有关挖土机、装载机和运输机械的唯一可靠而又最新的资料可以从制造厂商处获得。
土方工程或土方挖运工程指的是把地表面过高处的土壤挖去(挖方),并把它倾卸到地表面过低的其他地方(填方)。
为了降低土方工程费用,填方量应该等于挖方量,而且挖方地点应该尽可能靠近土方量相等的填方地点,以减少运输量和填方的二次搬运。
土方设计这项工作落到了从事道路设计的工程师的身上,因为土方工程的设计比其他任何工作更能决定工程造价是否低廉。
根据现有的地图和标高,道路工程师应在设计绘图室中的工作也并不是徒劳的。
它将帮助他在最短的时间内获得最好的方案。
费用最低的运土方法是用同一台机械直接挖方取土并且卸土作为填方。
这并不是经常可以做到的,但是如果能够做到则是很理想的,因为这样做既快捷又省钱。
拉铲挖土机。
推土机和正铲挖土机都能做到这点。
拉铲挖土机的工作半径最大。
推土机所推运的图的数量最多,只是运输距离很短。
拉铲挖土机的缺点是只能挖比它本身低的土,不能施加压力挖入压实的土壤内,不能在陡坡上挖土,而且挖。
卸都不准确。
正铲挖土机介于推土机和拉铲挖土机的之间,其作用半径大于推土机,但小于拉铲挖土机。
正铲挖土机能挖取竖直陡峭的工作面,这种方式对推土机司机来说是危险的,而对拉铲挖土机则是不可能的。
每种机械设备应该进行最适合它的性能的作业。
正铲挖土机不能挖比其停机平面低很多的土,而深挖坚实的土壤时,反铲挖土机最适用,但其卸料半径比起装有正铲的同一挖土机的卸料半径则要小很多。
在比较平坦的场地开挖,如果用拉铲或正铲挖土机运输距离太远时,则装有轮胎式的斗式铲运机就是比不可少的。
它能在比较平的地面上挖较深的土(但只能挖机械本身下面的土),需要时可以将土运至几百米远,然后卸土并在卸土的过程中把土大致铲平。
在挖掘硬土时,人们发现在开挖场地经常用一辆助推拖拉机(轮式或履带式),对返回挖土的铲运机进行助推这种施工方法是经济的。
一旦铲运机装满,助推拖拉机就回到开挖的地点去帮助下一台铲运机。
斗式铲运机通常是功率非常大的机械,许多厂家制造的铲运机铲斗容量为8 m ³,满载时可达10 m³。
最大的自行式铲运机铲斗容量为19立方米(满载时为25 m ³),由430马力的牵引发动机驱动。
翻斗机可能是使用最为普遍的轮胎式运输设备,因为它们还可以被用来送混凝土或者其他建筑材料。
翻斗车的车斗位于大橡胶轮胎车轮前轴的上方,尽管铰接式翻斗车的卸料方向有很多种,但大多数车斗是向前翻转的。
最小的翻斗车的容量大约为0.5立方米,而最大的标准型翻斗车的容量大约为4.5m³。
特殊型式的翻斗车包括容量为4 m³的自装式翻斗车,和容量约为0.5 m³的铰接式翻斗车。
必须记住翻斗车与自卸卡车之间的区别。
翻斗车车斗向前倾翻而司机坐在后方卸载,因此有时被称为后卸卡车。
1.3结构的安全度规范的主要目的是提供一般性的设计原理和计算方法,以便验算结构的安全度。
就目前的趋势而言,安全系数与所使用的材料性质及其组织情况无关,通常把它定义为发生破坏的条件与结构可预料的最不利的工作条件之比值。
这个比值还与结构的破坏概率(危险率)成反比。
破坏不仅仅指结构的整体破坏,而且还指结构不能正常的使用,或者,用更为确切的话来说,把破坏看成是结构已经达到不能继续承担其设计荷载的“极限状态”。
通常有两种类型的极限状态,即:(1)强度极限状态,它相当于结构能够达到的最大承载能力。
其例子包括结构的局部屈曲和整体不稳定性;某此界面失效,随后结构转变为机构;疲劳破坏;引起结构几何形状显著变化的弹性变形或塑性变形或徐变;结构对交变荷载、火灾和爆炸的敏感性。
(2)使用极限状态,它对应着结构的使用功能和耐久性。
器例子包括结构失稳之前的过大变形和位移;早期开裂或过大的裂缝;较大的振动和腐蚀。
根据不同的安全度条件,可以把结构验算所采用的计算方法分成:(1)确定性的方法,在这种方法中,把主要参数看作非随机参数。
(2)概率方法,在这种方法中,主要参数被认为是随机参数。
此外,根据安全系数的不同用途,可以把结构的计算方法分为:(1)容许应力法,在这种方法中,把结构承受最大荷载时计算得到的应力与经过按规定的安全系数进行折减后的材料强度作比较。
(2)极限状态法,在这种方法中,结构的工作状态是以其最大强度为依据来衡量的。
由理论分析确定的这一最大强度应不小于结构承受计算荷载所算得的强度(极限状态)。
计算荷载等于分别乘以荷载系数的活载与恒载之和。
把对应于不乘以荷载系数的活载和恒载的工作(使用)条件的应力与规定值(使用极限状态)相比较。
根据前两种方法和后两种方法的四种可能组合,我们可以得到一些实用的计算方法。
通常采用下面两种计算方法:确定性的方法,这种方法采用容许应力。
概率方法,这种方法采用极限状态。
至少在理论上,概率法的主要优点是可以科学的考虑所有随机安全系数,然后将这些随机安全系数组合成确定的安全系数。
概率法取决于:(1)制作和安装过程中材料强度的随机分布(整个结构的力学性能数值的分散性);(2)截面和结构几何尺寸的不确定性(由结构制作和安装造成的误差和缺陷而引起的);对作用在结构上的活载和恒载的预测的不确定性;所采用的近似计算方法有关的不精确性(实际应力与计算应力的偏差)。
此外,概率理论意味着可以基于下面几个因素来确定允许的危险率,例如:建筑物的重要性和建筑物破坏造成的危害性;(2)由于建筑物破坏使生活受到威胁的人数;(3)修复建筑的可能性;(4)建筑物的预期寿命。
所有这些因素均与经济和社会条件有关,例如:(1)建筑物的初始建设费;(2)建筑物使用期限内的折旧费;(3)由于建筑物破坏而造成的物质和材料损失费;(4)在社会上造成的不良影响;(5)精神和心理上的考虑。
就给定的安全系数而论,所有这些参数的确定都是以建筑物的最佳成本为依据的。
但是,应该考虑到进行全概率分析的困难。
对于这种分析来说,应该了解活载及其所引起的盈利的分布规律、材料的力学性能的分散性和截面的结构几何尺寸的分散性。
此外,由于强度的分布规律和应力的分布规律之间的相互关系是困难的。
这些实际困难可以采用两种方法来克服。
第一种方法对材料和荷载采用不同的安全系数,而不需要采用概率准则;第二种方法是引入一些而简化假设的近似概率方法(半概率方法)。
2 外文翻译Abstract:To study the application of continuum structural topology optimization methods to real engineering structures,an optimization method for an optimal topology design of multistory steel frame bracing systems is presented.On a sensitivity analysis,an element removal criterion for continuum structures with stress and multi-displacement constraints under multiple lateral loading conditions is proposed.A concept of mean thickness of a design domain is provided to ensure the reasonableness of optimal results.In the proposed optimization method,the optimal design of an unbraced steel frame without displacement constraints is performed firstly,and then the optimal topology of a bracing system for the multistory steel frame considering displacement constraints is obtained by using evolutionary structural optimization and the given removal criterion,and finally the optima layout of the bracing system is interpreted as bracing members.An example of 3-bay 12-story plane steel frame shows that it is effective for the given optimization method in the optimal design of bracing systems for multistory steel frames.Key words:steel frame;bracing system;continuum;topology optimization;evolutionary structural optimization2.1 Reinforced ConcretePlain concrete is formed from a hardened mixture of cement ,water ,fine aggregate, coarse aggregate (crushed stone or gravel),air, and often other admixtures. The plastic mix is placed and consolidated in the formwork, then cured to facilitate the acceleration of the chemical hydration reaction lf the cement/water mix, resulting in hardened concrete. The finished product has high compressive strength, and low resistance to tension, such that its tensile strength is approximately one tenth lf its compressive strength. Consequently, tensile and shear reinforcement in the tensile regions of sections has to be provided to compensate for the weak tension regions in the reinforced concrete element.It is this deviation in the composition of a reinforces concrete section from the homogeneity of standard wood or steel sections that requires a modified approach to the basic principles of structural design. The two components of the heterogeneous reinforced concrete section are to be so arranged and proportioned that optimal use is made of the materials involved. This is possible because concrete can easily be given any desired shape by placing and compacting the wet mixture of the constituent ingredients are properly proportioned, the finished product becomes strong, durable, and, in combination with the reinforcing bars, adaptable for use as main members of anystructural system.The techniques necessary for placing concrete depend on the type of member to be cast: that is, whether it is a column, a bean, a wall, a slab, a foundation. a mass columns, or an extension of previously placed and hardened concrete. For beams, columns, and walls, the forms should be well oiled after cleaning them, and the reinforcement should be cleared of rust and other harmful materials. In foundations, the earth should be compacted and thoroughly moistened to about 6 in. in depth to avoid absorption of the moisture present in the wet concrete. Concrete should always be placed in horizontal layers which are compacted by means of high frequency power-driven vibrators of either the immersion or external type, as the case requires, unless it is placed by pumping. It must be kept in mind, however, that over vibration can be harmful since it could cause segregation of the aggregate and bleeding of the concrete.Hydration of the cement takes place in the presence of moisture at temperatures above 50°F. It is necessary to maintain such a condition in order that the chemical hydration reaction can take place. If drying is too rapid, surface cracking takes place. This would result in reduction of concrete strength due to cracking as well as the failure to attain full chemical hydration.It is clear that a large number of parameters have to be dealt with in proportioning a reinforced concrete element, such as geometrical width, depth, area of reinforcement, steel strain, concrete strain, steel stress, and so on. Consequently, trial and adjustment is necessary in the choice of concrete sections, with assumptions based on conditions at site, availability of the constituent materials, particular demands of the owners, architectural and headroom requirements, the applicable codes, and environmental reinforced concrete is often a site-constructed composite, in contrast to the standard mill-fabricated beam and column sections in steel structures.A trial section has to be chosen for each critical location in a structural system. The trial section has to be analyzed to determine if its nominal resisting strength is adequate to carry the applied factored load. Since more than one trial is often necessary to arrive at the required section, the first design input step generates into a series of trial-and-adjustment analyses.The trial-and –adjustment procedures for the choice of a concrete section lead to the convergence of analysis and design. Hence every design is an analysis once a trial section is chosen. The availability of handbooks, charts, and personal computers and programs supports this approach as a more efficient, compact, and speedy instructionalmethod compared with the traditional approach of treating the analysis of reinforced concrete separately from pure design.2.2 EarthworkBecause earthmoving methods and costs change more quickly than those in any other branch of civil engineering, this is a field where there are real opportunities for the enthusiast. In 1935 most of the methods now in use for carrying and excavating earth with rubber-tyred equipment did not exist. Most earth was moved by narrow rail track, now relatively rare, and the main methods of excavation, with face shovel, backacter, or dragline or grab, though they are still widely used are only a few of the many current methods. To keep his knowledge of earthmoving equipment up to date an engineer must therefore spend tine studying modern machines. Generally the only reliable up-to-date information on excavators, loaders and transport is obtainable from the makers.Earthworks or earthmoving means cutting into ground where its surface is too high ( cuts ), and dumping the earth in other places where the surface is too low ( fills). Toreduce earthwork costs, the volume of the fills should be equal to the volume of the cuts and wherever possible the cuts should be placednear to fills of equal volume so as to reduce transport and double handlingof the fill. This work of earthwork design falls on the engineer who lays out the road since it is the layout of the earthwork more than anything else which decides its cheapness. From the available maps ahd levels, the engineering must try to reach as many decisions as possible in the drawing office by drawing cross sections of the earthwork. On the site when further information becomes available he can make changes in jis sections and layout,but the drawing lffice work will not have been lost. It will have helped him to reach the best solution in the shortest time.The cheapest way of moving earth is to take it directly out of the cut and drop it as fill with the same machine. This is not always possible, but when it canbe done it is ideal, being both quick and cheap. Draglines, bulldozers and face shovels an do this. The largest radius is obtained with the dragline,and the largest tonnage of earth is moved by the bulldozer, though only over short distances.The disadvantages of the dragline are that it must dig below itself, it cannot dig with force into compacted material, it cannot dig on steep slopws, and its dumping and digging are not accurate.Face shovels are between bulldozers and draglines, having a larger radius of action than bulldozers but less than draglines. They are anle to dig into a vertical cliff face in a way which would be dangerous tor a bulldozer operator and impossible for a dragline.Each piece of equipment should be level of their tracks and for deep digs in compact material a backacter is most useful, but its dumping radius is considerably less than that of the same escavator fitted with a face shovel.Rubber-tyred bowl scrapers are indispensable for fairly level digging where the distance of transport is too much tor a dragline or face shovel. They can dig the material deeply ( but only below themselves ) to a fairly flat surface, carry it hundreds of meters if need be, then drop it and level it roughly during the dumping. For hard digging it is often found economical to keep a pusher tractor ( wheeled or tracked ) on the digging site, to push each scraper as it returns to dig. As soon as the scraper is full,the pusher tractor returns to the beginning of the dig to heop to help the nest scraper.Bowl scrapers are often extremely powerful machines;many makers build scrapers of 8 cubic meters struck capacity, which carry 10 m ³ heaped. The largest self-propelled scrapers are of 19 m ³ struck capacity ( 25 m ³ heaped )and they are driven by a tractor engine of 430 horse-powers.Dumpers are probably the commonest rubber-tyred transport since they can also conveniently be used for carrying concrete or other building materials. Dumpers have the earth container over the front axle on large rubber-tyred wheels, and the container tips forwards on most types, though in articulated dumpers the direction of tip can be widely varied. The smallest dumpers have a capacity of about 0.5 m ³, and the largest standard types are of about 4.5 m ³. Special types include the self-loading dumper of up to 4 m ³and the articulated type of about 0.5 m ³. The distinction between dumpers and dump trucks must be remembered .dumpers tip forwards and the driver sits behind the load. Dump trucks are heavy, strengthened tipping lorries, the driver travels in front lf the load and the load is dumped behind him, so they are sometimes called rear-dump trucks.2.3 Safety of StructuresThe principal scope of specifications is to provide general principles and computational methods in order to verify safety of structures. The “ safety factor ”, which according to modern trends is independent of the nature and combination of the materials used, can usually be defined as the ratio between the conditions. This ratio is also proportional to the inverse of the probability ( risk ) of failure of the structure.Failure has to be considered not only as overall collapse of the structure but also as unserviceability or, according to a more precise. Common definition. As the reaching of a “ limit state ” which causes the construction not to accomplish the task it was designedfor. There are two categories of limit state :(1)Ultimate limit sate, which corresponds to the highest value of the load-bearing capacity. Examples include local buckling or global instability of the structure; failure of some sections and subsequent transformation of the structure into a mechanism; failure by fatigue; elastic or plastic deformation or creep that cause a substantial change of the geometry of the structure; and sensitivity of the structure to alternating loads, to fire and to explosions.(2)Service limit states, which are functions of the use and durability of the structure. Examples include excessive deformations and displacements without instability; early or excessive cracks; large vibrations; and corrosion.Computational methods used to verify structures with respect to the different safety conditions can be separated into:(1)Deterministic methods, in which the main parameters are considered as nonrandom parameters.(2)Probabilistic methods, in which the main parameters are considered as random parameters.Alternatively, with respect to the different use of factors of safety, computational methods can be separated into:(1)Allowable stress method, in which the stresses computed under maximum loads are compared with the strength of the material reduced by given safety factors.(2)Limit states method, in which the structure may be proportioned on the basis of its maximum strength. This strength, as determined by rational analysis, shall not be less than that required to support a factored load equal to the sum of the factored live load and dead load ( ultimate state ).The stresses corresponding to working ( service ) conditions with unfactored live and dead loads are compared with prescribed values ( service limit state ) . From the four possible combinations of the first two and second two methods, we can obtain some useful computational methods. Generally, two combinations prevail:(1)deterministic methods, which make use of allowable stresses.(2)Probabilistic methods, which make use of limit states.The main advantage of probabilistic approaches is that, at least in theory, it is possible to scientifically take into account all random factors of safety, which are then combined to define the safety factor. probabilistic approaches depend upon :(1) Random distribution of strength of materials with respect to the conditions offabrication and erection ( scatter of the values of mechanical properties through out the structure );(2) Uncertainty of the geometry of the cross-section sand of the structure ( faults and imperfections due to fabrication and erection of the structure );(3) Uncertainty of the predicted live loads and dead loads acting on the structure;(4)Uncertainty related to the approximation of the computational method used ( deviation of the actual stresses from computed stresses ).Furthermore, probabilistic theories mean that the allowable risk can be based on several factors, such as :(1) Importance of the construction and gravity of the damage by its failure;(2)Number of human lives which can be threatened by this failure;(3)Possibility and/or likelihood of repairing the structure;(4) Predicted life of the structure.All these factors are related to economic and social considerations such as:(1) Initial cost of the construction;(2) Amortization funds for the duration of the construction;(3) Cost of physical and material damage due to the failure of the construction;(4) Adverse impact on society;(5) Moral and psychological views.The definition of all these parameters, for a given safety factor, allows construction at the optimum cost. However, the difficulty of carrying out a complete probabilistic analysis has to be taken into account. For such an analysis the laws of the distribution of the live load and its induced stresses, of the scatter of mechanical properties of materials, and of the geometry of the cross-sections and the structure have to be known. Furthermore, it is difficult to interpret the interaction between the law of distribution of strength and that of stresses because both depend upon the nature of the material, on the cross-sections and upon the load acting on the structure. These practical difficulties can be overcome in two ways. The first is to apply different safety factors to the material and to the loads, without necessarily adopting the probabilistic criterion. The second is an approximate probabilistic method which introduces some simplifying assumptions ( semi-probabilistic methods ) .11。