铝压铸件最小壁厚标准
铝合金压铸结构设计规范

压铸齿轮的最小模数见表3-1-17
9、铸件设计中的凸台、凸纹及文字和图案
压铸凸台应有足够的高度,便于留切削余量,而不致使刀 具切削到铸件壁上,凸台的最小高度 h=2~2.5mm。当紧 固件的孔中心距L等于或小于表3-1-19 所列数值时,应将 相近的凸台连成一体,见图 3-1-22。
合金类别 铅锡合金 锌合金
铝合金
镁合金
最小宽度b
0.8
0.8
1.2
1.0
最大深度H
≈10
≈12
≈10
≈12
厚度h
≈10
≈12
≈10
≈12
说明:宽度b在具有铸造斜度时,表内值为小端部位值。
铜合金
1.5 ≈10 ≈8
8、铸件设计的压铸螺纹及齿轮
在一定的工艺条件下,锌、铝及镁等合金的压铸件,可以 直接压出螺纹。铜合金只是在个别情况下才压铸出螺纹。 压铸螺纹一般为国家标准规定的3级精度。压铸螺纹通常 为外螺纹较多。在必要时,也可以压铸内螺纹。外螺纹又 分两种,一种是由可分开的两半螺纹型腔构成,这种方式 的特点是易产生错扣,圆度稍差,但可以达到精度范围内, 使用前要经过简单修整加工。另一种是由螺纹型环构成, 其特点是不产生错扣,圆度好,但生产效率低,操作不安 全。内螺纹方式是由螺纹型芯构成,其特点是螺纹型芯的 螺纹在轴方向上要有斜度,通常为 10′~15′,螺纹长度有 限。压铸螺纹的牙形,应是平头或圆头的。
表3-1-19 紧固件中心距mm
紧固件直径 孔中心距
≤4
15
>4~6
18
>6~10
22
>10~14
30
>14~18
铸件最小壁厚

铸件最小壁厚一、引言铸件是制造领域常见的一种零件制造方式,其具有形状复杂、材料节约、生产周期短等优势。
而铸件的壁厚是决定其性能和质量的重要参数之一。
本文将就铸件最小壁厚进行探讨,包括最小壁厚的定义、影响因素以及如何选择合适的最小壁厚等。
二、最小壁厚的定义最小壁厚是指铸件在制造过程中最薄的部分的壁厚。
它是铸件工艺设计的重要参数之一,直接关系到铸件的质量和性能。
三、最小壁厚的影响因素最小壁厚的选择需要综合考虑多个因素,下面将介绍一些影响最小壁厚选择的重要因素。
1. 材料性质不同材料的性质不同,其对最小壁厚的要求也不同。
一般来说,强度较高的材料对最小壁厚要求较低,而较脆弱的材料则需要较厚的壁厚来保证铸件的质量和可靠性。
2. 铸造方法不同的铸造方法对最小壁厚也有影响。
例如,压力铸造和重力铸造的最小壁厚要求是不同的。
压力铸造能够通过增大压力来填充较薄壁的部分,因此其最小壁厚要求相对较低。
3. 零件形状和结构铸件的形状和结构对最小壁厚的选择也有一定的影响。
一般来说,复杂形状的零件需要较大的最小壁厚来避免浇注不充分或产生裂纹等问题。
4. 铸造工艺铸造工艺也决定了最小壁厚的选择。
例如,砂型铸造和金属型铸造的最小壁厚要求是不同的。
砂型铸造的最小壁厚由于砂型的强度限制较高,而金属型铸造可以实现较薄壁的铸造。
四、如何选择合适的最小壁厚选择合适的最小壁厚是保证铸件质量和性能的重要环节。
下面将介绍一些选择最小壁厚的方法和注意事项。
1. 参考标准和规范根据国家或行业相关的标准和规范,可以了解到不同材料和铸造方法对最小壁厚的要求。
这些标准和规范通常包含了实践经验和理论分析,是选择最小壁厚的重要依据。
2. 结构分析与模拟通过结构分析和模拟技术,可以预测铸件在实际使用中的性能和行为。
这些分析和模拟可以帮助选择合适的最小壁厚,并优化铸件的结构设计。
3. 经验总结与实践验证准确选择最小壁厚需要多年的经验积累和实践验证。
通过总结以往的成功案例和失败经验,可以逐步积累并提高对最小壁厚选择的准确性。
最小铸造壁厚

最小铸造壁厚
最小铸造壁厚通常取决于铸造材料的特性、铸造工艺要求以及零件设计需求。
一般来说,在实际生产中,最小的可接受铸造壁厚应满足以下几个因素:
1. 铸造材料的特性:不同的材料具有不同的流动性,流动性越差的材料需要更大的壁厚来确保铸件完整度和避免缩孔、夹杂等缺陷。
2. 铸造工艺要求:铸造过程中需要注入熔融金属或合金,一定的壁厚可以确保足够的金属液体能够填充模具中的空腔。
3. 零件设计需求:根据零件的实际使用情况和力学要求,需要确定合适的壁厚来保证零件的强度和刚度。
一般来说,最小铸造壁厚可以在几毫米到几十毫米之间。
对于薄壁零件,通常要考虑使用其他工艺,如锻造、压铸等替代铸造。
对于较厚的零件,可以通过合理的几何形状设计、变薄区域的设置和局部加强来满足设计要求。
铝合金国标厚度

铝合金国标厚度
摘要:
1.铝合金的国标厚度
2.铝合金门窗的国标厚度
3.铝合金桥架的国标厚度
4.铝合金型材的国标厚度
5.结论
正文:
铝合金国标厚度是一个广泛关注的话题,其在不同领域的应用和标准都有所不同。
在这里,我们将探讨铝合金在门窗、桥架和型材等方面的国标厚度。
首先,对于铝合金门窗的国标厚度,根据gbt5237《铝合金建筑型材》规定,建筑铝型材最小公称壁厚应不小于1.2mm。
其中,实心型材壁厚允许偏差0.15mm,即壁厚不得低于1.05mm;含封闭空腔的空心型材部位壁厚允许偏差0.23mm,即壁厚不得低于0.97mm。
此外,铝合金门窗的国标壁厚不得小于1.2MM,而门框壁厚不小于2.0MM。
其次,对于铝合金桥架的国标厚度,虽然没有明确的国家标准规定,但一般来说,铝合金桥架的厚度并不比钢制桥架差,因为其强度并不比钢制桥架差。
再次,对于铝合金型材的国标厚度,由于铝合金产品繁多,不同的产品其厚度不一样。
在建材市场上供消费者选购的铝合金室内门,型材有0.8 毫米、1.0 毫米、1.2 毫米等多种厚度。
其中,厚度在1.0 毫米以上的铝合金门强度更好,在正常使用的前提下5~8 年都不会变形。
综上所述,不同领域的铝合金国标厚度有所不同。
铝合金压铸技术要求

1、范围本标准规定了铝合金压铸件的技术要求、试验方法、检验规那么、交货条件等。
本标准适用于汽车发电机铝合金端盖压铸件。
2、引用标准GB6414铸件尺寸公差铝及铝合金化学分析方法GB288-87金属拉力试验法GB/T13822-92 压铸有色合金试样GB6060.5 外表粗造度比拟样块抛(喷)丸、喷吵加工外表3、技术要求3.1 压铸铝合金的牌号压铸铝合金采用UNS-A03800〔美国,日本ADC10〕可选用材料UNS-A03830 〔美国,日本ADC12〕化学成份见表1表1供给商可选择上述四种牌号的任何一种,如在生产过程中更换其它牌号,需重新进展样件鉴定。
一级回炉料:浇道、化学成份合格的废铸件,后加工次品等不含水分和油污。
二级回炉料:集渣包、坩埚底部剩料、退货废品、存放时间长〔超过10天〕的一级回炉料。
三级回炉料:飞边、溅屑、细小的碎料、带有油污的渣料、因化学成份报废的铸件、从铝渣中捡出的铝粒。
使用单一某级回炉料:一级回炉料最大使用量50%,二级回炉料最大使用量40%。
一级、二级回炉料混合使用:回炉料总量不超过40%,其中二级回炉料最大使用量20%。
三级回炉料:不能直接使用,必须经过重熔、精炼且化学成份分析合格后才能使用,其最大使用量10%,仅与铝锭混合使用。
小颗粒回炉料大块回炉料铝锭,如此循环。
3.2 力学性能采用单铸拉力试样检验,其力学性能应满足抗拉强度≥240Mpa,伸长率≥1%,HB85〔5/250/30〕。
试样尺寸及形状应符合GB/T 13822-92?压铸有色合金试样?的规定。
3.3 压铸件尺寸压铸件的几何形状和尺寸应符合铸件图的规定。
3.4 待加工外表用符号“〞标明,尖头指向被加工面。
例:0.5 表示该外表留有加工余量3.5 外表质量3.5.1 铸件清理后的外表质量铸件的浇口、飞边、溢流口、隔皮等应清理干净,但允许留有清理痕迹。
在不影响使用的情况下,因去除浇口、溢流口时所形成的缺肉或高出均不得超过壁厚的四分之一,并且不得超过1.5 mm。
铝合金压铸件一般技术要求
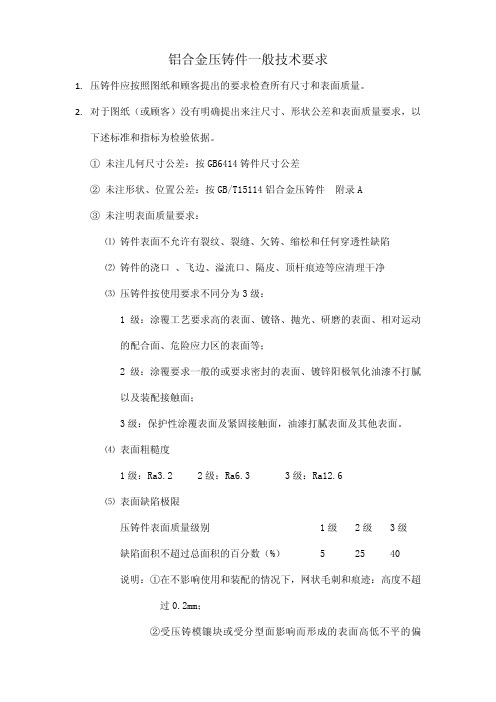
铝合金压铸件一般技术要求1.压铸件应按照图纸和顾客提出的要求检查所有尺寸和表面质量。
2.对于图纸(或顾客)没有明确提出来注尺寸、形状公差和表面质量要求,以下述标准和指标为检验依据。
①未注几何尺寸公差:按GB6414铸件尺寸公差②未注形状、位置公差:按GB/T15114铝合金压铸件 附录A③未注明表面质量要求:⑴铸件表面不允许有裂纹、裂缝、欠铸、缩松和任何穿透性缺陷⑵铸件的浇口 、飞边、溢流口、隔皮、顶杆痕迹等应清理干净⑶压铸件按使用要求不同分为3级:1级:涂覆工艺要求高的表面、镀铬、抛光、研磨的表面、相对运动的配合面、危险应力区的表面等;2级:涂覆要求一般的或要求密封的表面、镀锌阳极氧化油漆不打腻以及装配接触面;3级:保护性涂覆表面及紧固接触面,油漆打腻表面及其他表面。
⑷表面粗糙度1级:Ra3.2 2级:Ra6.3 3级:Ra12.6⑸表面缺陷极限压铸件表面质量级别 1级 2级 3级缺陷面积不超过总面积的百分数(%) 5 25 40说明:①在不影响使用和装配的情况下,网状毛刺和痕迹:高度不超过0.2mm;②受压铸模镶块或受分型面影响而形成的表面高低不平的偏差,不超过相关的公差尺寸;③推杆痕迹表面凸出或凹入铸件表面的深度,一般为±0.2mm;⑹表面质量要求(见附表)⑺挫痕:目视挫痕应均匀、一致,不允许有明显的凹凸。
经锉加工的表面和未经锉加工的表面允许有角度,但角度应在10°以内;⑻变形:压铸件成型后,如有变形应进行调整,经调整后的压铸件表面不允许有明显的打击痕迹。
调整部分的平面度:0.2mm;⑼对于顾客的特殊要求,要形成相应的工艺文件,规定其相关的工艺过程和检验方法。
附表: 缺陷名称 缺陷范围表面质量级别 备注1级2级 3级 流痕深度(mm )≤ 0.05 0.07 0.15面积不超过总面积的百分数515 30冷隔深度(mm )≤ 不允许1/5壁厚 1/4壁厚 1.在同一部分对应出不允许同时存在2.长度是指缺陷流向的展开长度长度不大于铸件的最大轮廓尺寸的(mm ) 1/101/5所在面上的不允许超过的数量 2处 2处 离铸件边缘距离(mm )≥ 4 4 两冷隔间距(mm )≥10 10 拉伤深度(mm )≤ 0.05 0.1 0.25 除一级表面外,浇道部位允许增加一倍面积不超过总面积的百分数35 10 凹陷 凹入深度(mm ) 0.10.3 0.5 粘附物痕迹整个铸件缺陷不允许超过 不允许1处 2处 占带缺陷的表面面积的百分比5 10气泡平均直径≤3mm1.每100cm 2缺陷个数不超过不允许 1 2 允许两种气泡同时存在,但大气泡不超过3个,总数不超过10个。
压铸产品结构设计的工艺要求

压铸类产品结构设计的工艺要求
压力铸造是将熔融状态或者(半)熔融状态合金浇入压铸机的压室,以极高的速度在高压的作用下充填在压铸模的型腔内,使熔融合金在高压下冷却凝固成型的方法。
常见的压铸材料包括:铝合金、锌合金、镁合金、铜合金等,铝合金又分为铝镁合金、铝铜合金、铝锌合金、铝硅合金等。
压铸类产品在结构设计时的工艺要求注意的几个方面。
①压铸件的厚度
压铸件产品的厚度一般指料厚,料的厚薄直接影响压铸的难易,一般情况下,压铸产品的料厚≥0.8mm,具体料厚根据产品设计。
压铸产品不会因为局部料厚产生缩水的现象,相反,在一些尖钢薄钢处要加料填充,避免模具强度低而损坏。
压铸产品的外观面局部最小料厚≥0.7mm,非外观面局部最小料厚度建议≥0.4mm,太薄会导致填充不良、无法成型,薄的区域面积也不能太大,否则无法成型。
②压铸件的拔模角
压铸件与塑胶件一样,内外表面都需要拔模角,压铸件外表面的
拔模角一般在1°~3°,内表面拔模角比外表面拔模角大一点,方便产品出模。
③压铸件的后续加工
压铸件有时达不到设计的要求,需要后续加工。
其中螺丝柱中的螺纹就是后续加工的,在设计产品时只需留出底孔就可以。
压铸件有深孔时,压铸件需要做出孔位置,再通过后续机械钻孔加工完成。
压铸件有些表面要求较高的精度,一般也需要后续加工,在设计时可在需要后续加工的地方留出加工余量,加工余量一般在0.5mm 左右。
④压铸件产品不能变形,一般是螺丝连接,在做扣位连接,连接的对应产品必须能变形,如塑胶产品等。
⑤压铸件产品加强筋不能太多,对于薄壁类零件,需适当设计加强筋,以增加产品的抗弯强度,防止产品变形损坏。
压铸件设计规范(2013)V1.0

压铸件设计规范目录铸圆脱铸缘压铸压铸内压铸压铸级压铸压铸一、壁厚1、压铸件的壁厚对铸件质量有很大的影响。
以铝合金为例,薄壁比厚壁具有更高的强度和良好的致密性。
因此,在保证铸件有足够的强度和刚性的条件下,应尽可能减少其壁厚,并保持壁厚均匀一致。
2、铸件壁太薄时,使金属熔接不好,影响铸件的强度,同时给成型带来困难;壁厚过大或严重不均匀则易产生缩瘪及裂纹。
厚壁压铸件,其壁中心层的晶粒粗大,易产生缩孔、缩松等缺陷,同样降低铸件的强度。
3、压铸件的壁厚一般以2.5~4mm为宜,同一压铸件内昀大壁厚与昀小壁厚之比不要大于3∶1,壁厚超过6mm的零件不宜采用压铸。
推荐值见表1。
我司的铝压铸件,按如下要求选取壁厚:散热齿一般取2.0~2.5mm,(自然散热)间距取10~12mm,(强迫风冷)间距取8~10mm.其余壁厚取4.5~5.0mm;螺纹孔为M3的PCB支撑柱,直径取6.5~7.5mm;接地螺纹孔处的壁厚取:M4 9.5~10.5mm, M5 10.5~11mm。
表1 压铸件的最小壁厚和正常壁厚二、铸造圆角和脱模斜度1、铸造圆角压铸件各部分相交应有圆角(分型面处除外),使金属填充时流动平稳,气体容易排出,并可避免因锐角而产生裂纹。
对于需要进行电镀和涂饰的压铸件,圆角可以均匀镀层,防止尖角处涂料堆积。
压铸件的圆角半径R一般不宜小于1mm,最小圆角半径为0.5 mm,见表2。
铸造圆角半径的计算见表3。
我司铝压铸件的圆角一般取R1.0mm,无配合处最小取R3.0mm(有外观要求的除外)。
表2 压铸件的最小圆角半径(mm)①、对锌合金铸件,K=1/4;对铝、镁合金铸件, K=1/2。
②、计算后的最小圆角应符合表2的要求。
表3 铸造圆角半径的计算(mm)2、脱模斜度设计压铸件时,就应在结构上留有脱模斜度,无脱模斜度时,在需要之处,必须有脱模的工艺斜度。
斜度的方向,必须与铸件的脱模方向一致。
推荐的脱模斜度见表4。
我司现采用的脱模斜度一般取前模1.5°,后模1.0°。
压铸件料饼厚度大小对压铸的影响

料饼厚度大小对压铸的影响旭东压铸(上海)有限公司技术部刘遵建料饼厚度超差,产品易形成欠铸、冷隔(汤回)、气孔、发黑、浇口分层缺肉、疏松、缩孔、产品机械性能下降等缺陷。
一、料饼厚度的大小规范1、一般情况下料饼厚度为:Φ50为16±5mmФ60为18±5mmФ70为20±5mmФ80为22±5mmФ90为24±5mmФ100为26±5mm。
2、当产品的气孔要求比较严格时,料饼厚度应适当加厚2~5mm 即:Φ50为20±5mmФ60为22±5mmФ70为25±5mm3、当模具的浇口套和分流锥不用通水冷却时,料饼厚度应适当减小2~3mm即:Φ50为4±5mmФ60为16±5mmФ70为18±5mm等。
二、料饼的材料组成料饼是由料缸周围温度较低流动性较差的铝水、浇入压室铝水表面的杂质、氧化皮和一部分高温流动性好的合金组成。
高温的铝水流动性较好,一般都在前边流动;靠后边的都是温度较低流动性较差的铝水。
三、料饼厚度过薄对产品质量产生的影响料饼过薄,料饼中无高温的、流动性好和可流动充填型腔的铝水,也无能够向型腔传递压力的铝水。
产品容易形成欠铸、冷隔、气孔、发黑、疏松、缩孔、产品机械性能下降等缺陷。
原因如下:1、型腔中的铝水接受不到压射和增压时的压力,铝水不能在高压下结晶,形成不了大量细小的内部晶粒组织。
产品内部组织粗大、疏松,结构不致密、机械强度低、易断裂。
2、起不到把浇道中的铝水压入型腔补缩的作用,型腔中的铝水不能在压力下凝固收缩。
产品内部较厚的部位凝固收缩时接受不到压力,容易出现缩孔和缩松,增加了产品内部的孔隙率。
3、型腔中的铝水不在压力下凝固,铝水中冷却、凝固时析出的氢气接受不到压力会膨胀,形成较大的气孔。
4、若是因浇注量过少引起料饼过薄,是铝水没有充满浇道就开始高速压射时,没有很好地排除浇道和型腔中的气体,产品易形成气孔、憋气、表面汤回(冷隔)、发黑等缺陷。
- 1、下载文档前请自行甄别文档内容的完整性,平台不提供额外的编辑、内容补充、找答案等附加服务。
- 2、"仅部分预览"的文档,不可在线预览部分如存在完整性等问题,可反馈申请退款(可完整预览的文档不适用该条件!)。
- 3、如文档侵犯您的权益,请联系客服反馈,我们会尽快为您处理(人工客服工作时间:9:00-18:30)。
铝压铸件最小壁厚标准
铝压铸件的最小壁厚标准通常根据铸件的结构和尺寸来确定。
以下是一些常见的铝压铸件最小壁厚标准的范例:
1. 对于普通的铝合金压铸件,最小壁厚通常为2-3mm。
2. 对于较大尺寸的铝合金压铸件,最小壁厚可能需要大于
3mm,以确保足够的强度和耐用性。
3. 对于一些特殊的结构设计,可能需要更大的最小壁厚,以满足特定的要求。
需要注意的是,最小壁厚标准可能因不同的应用和需求有所不同。
因此,在设计铝压铸件时,应该根据具体的要求和使用条件,进行合理的设计和选择最小壁厚。