铸造缺陷种类
铸造缺陷名称和分类

✓ 缩陷
sink marks, draw, suck-in
✓ 芯面缩孔 core shrinkage
✓ 内角缩孔 corner shrinkage, fillet shrinkage
✓ 出汗孔 extruded bead, exudation
✓ 线状缩孔 fissure like shrinkage
.
• I. 组织缺陷 ( 铸铁 )
✓ 球化不良 poor nodularity , degenerated graphite ✓ 蠕墨化不良 degenerated graphite ✓ 异常石墨 abnormal graphite ✓ 开花状石墨 exploded graphite ✓ 过冷石墨 under cooled graphite , D-type graphite ✓ 石墨细小颗粒 chunky graphite ✓ 石墨粗大 kish graphite , kish ✓ 整列石墨 aligned graphite ✓ 石墨漂浮 floated graphite ✓ 石墨魏氏组织 Widmannstatten graphite ✓ 麻口 mottled cast iron , mottle ✓ 灰点 mottle ✓ 反麻口 inverse mottle ( 与麻口相反,在薄断面处和尖角处形成的麻口) ✓ 白口 chill ✓ 反白口 reverse chill , inverse chill ✓ 冷豆 extruded bead , exudation , internal sweating ✓ 退火不足 miss annealing , incomplete annealing ✓ 粗大枝晶组织 coarsened dendritic ✓ 反偏析 inverse segregation ✓ 比重偏析 gravity segregation ✓ 溶质偏析 solute segregation ✓ 宏观偏析 macroscopic segregation ✓ 微观偏析 microscopic segregation
铸造缺陷及其对策.pptx

4、防止方法:
1、优化铸件结构设计,壁厚均匀,过渡平滑,肋板 厚度和分布的合理化; 2、优化浇注系统,控制浇温、浇速使铸件各部位冷 却速度趋于一致; 3、降低有害元素,合理控制合金元素添加量; 4、合理设定开箱时间。
5、补救措施:
1、开止裂孔后焊补; 2、采用工业修补剂; 3、如在重要面,报废重铸。
第16页/共28页
4、防止方法: 1、优化工艺设计,合理设置浇注系统; 2、考虑使用保温冒口、发热冒口; 3、优化铸件结构设计; 4、模拟分析(CAE); 5、调整成份; 6、控制炉料.
第17页/共28页
5、补救措施: 1、轻者焊补或采用工业修补剂; 2、重者报废重铸.
第18页/共28页
2.夹砂
的不同大小、形状的 孔洞缺陷的总称
缩孔 缩松
形状不规则,孔壁粗糙,常伴有粗大 树枝晶.夹杂物.裂纹等缺陷;
是细小的分散缩孔,断口呈海绵状;
疏松(显微缩松) 不作严格区分;
第3页/共28页
气 孔
第4页/共28页
针孔
2、裂纹、冷隔类缺陷
定义
缺陷名 称
特征
宏观(肉眼、PT、R T、MT、UT)或微 观(显微镜)判断发现 有开裂状纹络
1、铸件内部裂纹可采用超声波探伤(UT)、 磁粉探伤(MT)或射线探伤法(RT)进行检验; 2、铸件表面的裂纹可采用染色探伤法(PT)来 帮助确定,大部份是肉眼可直接发现的。
第24页/共28页
3、形成原因:
1、铸件结构或浇注系统设计不合理壁厚相差悬殊, 过渡圆角小; 2、铸造合金中有害元素(P、S等)超标,珠光体 元素过量; 3、铸件开箱过早,冷却过快; 4、合金收缩率大; 5、肋板设计不合理。
铸造缺陷对照表

铸造缺陷对照表铸造缺陷对照表1。
毛刺(铸件有多余的薄金属,披缝)---不正确的水/粉比例,造成强度较弱的石膏模---铸粉不正确储存,受潮---倒铸粉模操作时间超出工作时间,或石膏模杯静置时被移动---石膏模杯曾跌到或被错误处理---石膏模杯静置时间不足一小时---石膏模杯在失蜡后未能及时进行铸造2。
铸件形状不完整(缺铸)---植腊树时不正确---蜡样没有完全烧掉---当铸造时模杯温度偏低---当铸造时金属温度偏低---金属重量不足3。
酸处理前铸件已光亮---蜡样没有完全烧掉,残余碳质造成金属表面失去氧化保护膜4。
粗糙。
变黑---失蜡温度过高,超过780度---金属液温度过高5。
出现孔状---植腊树时不正确---蜡样没有完全烧掉---金属液温度过高---石膏模温度过高---旧金属比例过高(不要超过50%)---金属助熔剂不足,助熔剂过量6。
铸件出现其他物质---蜡树有尖曲形状---石膏模杯静置时间不足---石膏模杯加热过快---拆掉胶底座后没有检查注入孔是否清洁---金属含有过多杂质---熔锅过旧或破损7。
多孔---蜡树有尖曲形状---石膏模杯静置时间不足---石膏模杯加热过快---倒铸粉沫操作时间超过规定时间8。
出现凸起或小珠形状---铸粉过稀,或没有充分混合及抽真空不充分---真空泵运行不正常---抽真空时没有震动9。
除凸起或小珠以外的表面粗糙---原始样板粗糙---植蜡树时不正确---水粉比例不对---石膏模杯静置时间不足---石膏模杯加热过快---样板杂质藏在石膏模内,加热时损坏石膏模表面---旧金属比例过高(不高于50%)10。
出现水漬---倒铸粉模操作时间过短(水温的高低直接影响操作时间,应调整水温保持操作时间在9~10分钟)。
铸造缺陷分类标准
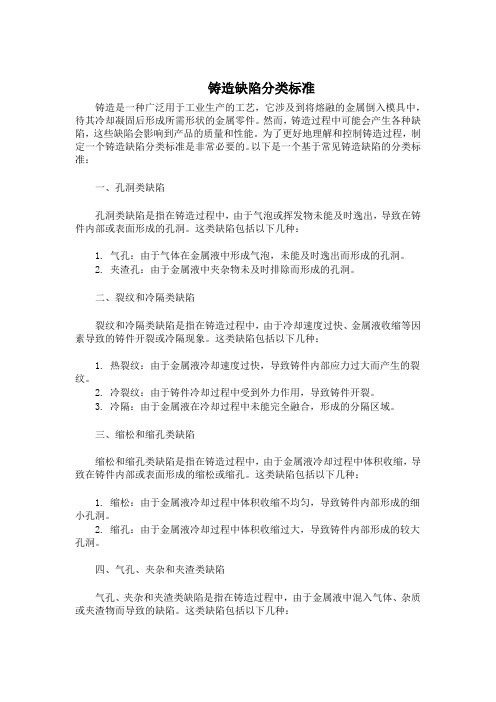
铸造缺陷分类标准铸造是一种广泛用于工业生产的工艺,它涉及到将熔融的金属倒入模具中,待其冷却凝固后形成所需形状的金属零件。
然而,铸造过程中可能会产生各种缺陷,这些缺陷会影响到产品的质量和性能。
为了更好地理解和控制铸造过程,制定一个铸造缺陷分类标准是非常必要的。
以下是一个基于常见铸造缺陷的分类标准:一、孔洞类缺陷孔洞类缺陷是指在铸造过程中,由于气泡或挥发物未能及时逸出,导致在铸件内部或表面形成的孔洞。
这类缺陷包括以下几种:1. 气孔:由于气体在金属液中形成气泡,未能及时逸出而形成的孔洞。
2. 夹渣孔:由于金属液中夹杂物未及时排除而形成的孔洞。
二、裂纹和冷隔类缺陷裂纹和冷隔类缺陷是指在铸造过程中,由于冷却速度过快、金属液收缩等因素导致的铸件开裂或冷隔现象。
这类缺陷包括以下几种:1. 热裂纹:由于金属液冷却速度过快,导致铸件内部应力过大而产生的裂纹。
2. 冷裂纹:由于铸件冷却过程中受到外力作用,导致铸件开裂。
3. 冷隔:由于金属液在冷却过程中未能完全融合,形成的分隔区域。
三、缩松和缩孔类缺陷缩松和缩孔类缺陷是指在铸造过程中,由于金属液冷却过程中体积收缩,导致在铸件内部或表面形成的缩松或缩孔。
这类缺陷包括以下几种:1. 缩松:由于金属液冷却过程中体积收缩不均匀,导致铸件内部形成的细小孔洞。
2. 缩孔:由于金属液冷却过程中体积收缩过大,导致铸件内部形成的较大孔洞。
四、气孔、夹杂和夹渣类缺陷气孔、夹杂和夹渣类缺陷是指在铸造过程中,由于金属液中混入气体、杂质或夹渣物而导致的缺陷。
这类缺陷包括以下几种:1. 气孔:由于金属液中混入气体而形成的气泡。
2. 夹渣:由于金属液中夹杂的固体颗粒物而形成的夹渣。
五、形状和表面类缺陷形状和表面类缺陷是指在铸造过程中,由于模具设计、制造或操作不当导致的铸件形状或表面质量的缺陷。
这类缺陷包括以下几种:1. 模具痕迹:由于模具设计或制造不当,导致铸件表面留下的痕迹。
2. 表面粗糙:由于金属液冷却过程中表面收缩不均匀,导致铸件表面粗糙。
铸件常见缺陷和处理

铸件常见缺陷、修补及检验一、常见缺陷1.缺陷的分类铸件常见缺陷分为孔眼、裂纹、表面缺陷、形状及尺寸和重量不合格、成份及组织和性能不合格五大类。
(注:主要介绍铸钢件容易造成裂纹的缺陷)1.1孔眼类缺陷孔眼类缺陷包括气孔、缩孔、缩松、渣眼、砂眼、铁豆。
1.1.1气孔:别名气眼,气泡、由气体原因造成的孔洞。
铸件气孔的特征是:一般是园形或不规则的孔眼,孔眼内表面光滑,颜色为白色或带一层旧暗色。
(如照片)气孔照片1产生的原因是:来源于气体,炉料潮湿或绣蚀、表面不干净、炉气中水蒸气等气体、炉体及浇包等修后未烘干、型腔内的气体、浇注系统不当,浇铸时卷入气体、铸型或泥芯透气性差等。
1.1.2缩孔缩孔别名缩眼,由收缩造成的孔洞。
缩孔的特征是:形状不规则,孔内粗糙不平、晶粒粗大。
产生的原因是:金属在液体及凝固期间产生收缩引起的,主要有以下几点:铸件结构设计不合理,浇铸系统不适当,冷铁的大小、数量、位置不符实际、铁水化学成份不符合要求,如含磷过高等。
浇注温度过高浇注速度过快等。
1.1.3缩松缩松别名疏松、针孔蜂窝、由收缩耐造成的小而多的孔洞。
缩松的特征是:微小而不连贯的孔,晶粒粗大、各晶粒间存在明显的网状孔眼,水压试验时渗水。
(如照片2)缩松照片2产生的原因同以上缩孔。
1.1.4渣眼渣眼别名夹渣、包渣、脏眼、铁水温度不高、浇注挡渣不当造成。
渣眼的特征是:孔眼形状不规则,不光滑、里面全部或局部充塞着渣。
(如照片3)渣眼照片3产生的原因是:铁水纯净度差、除渣不净、浇注时挡渣不好,浇注系统挡渣作用差、浇注时浇口未充满或断流。
1.1.5砂眼砂眼是夹着砂子的砂眼。
砂眼的特征是:孔眼不规则,孔眼内充塞着型砂或芯砂。
产生的原因是:合箱时型砂损坏脱落,型腔内的散砂或砂块未清除干净、型砂紧实度差、浇注时冲坏型芯、浇注系统设计不当、型芯表面涂料不好等。
1.1.6铁豆铁豆是夹着铁珠的孔眼、别名铁珠、豆眼、铁豆砂眼等。
铁豆的特征是:孔眼比较规则、孔眼内包含着金属小珠、常发生在铸铁件上。
铸造缺陷汇总

形状及重 变形 6 量差错类
铸件缺陷
铸件外形扭曲改变,与图纸不符。
错型(错箱) 铸件外形在分型面处错位,一侧多肉,另一侧缺肉;
错芯
铸件内腔沿分芯面错位,一侧多肉,一侧缺肉;
舂移
铸件外形在分型面附近局部突起,形成多肉,通常是单 侧多肉,另一侧不缺肉.
金属夹杂物 铸件中存在不同金属夹杂物
原料混料。
1、型腔内沙粒没清净。
1、浇铸前型腔内砂粒清理干净; 2、浇冒口处保持清洁; 3、加强砂型强度; 4、调整浇铸工艺,调整温度和浇铸速度; 5、合理选择浇冒口位置。
检查合模力或增压情况,调整压射增压机构,使压射增 压峰值降低。
1、改进铸件结构设计,壁厚力求均匀,平滑过渡,铸 件内腔圆角够大; 2、工艺设计合理,尽量减少铸件收缩阻力; 3、适当降低浇注温度; 4、提高模温; 5、缩短开模及抽芯时间; 6、严格控制有害杂质,锌合金降低铅,锡,镉,铁的含 量,铝合金降低锌,铜,铁的含量。
铸造缺陷汇总
序 缺陷类 号型
种类
特征
产生原因
易出现部位
避免措施
反应气孔
析出气孔 1、 气孔
侵入气孔
卷入气孔
飞翅(飞边,
披峰)
2
多肉类铸 件缺陷 毛刺
抬型(抬箱)
冷裂
热裂
白点(发裂) 裂纹,冷
3 隔类铸件
缺陷
冷隔
拉模
4 表面缺陷 流痕 皱皮 缩陷
1、反应气孔一般为针孔。有时反应气孔形成皮下气 孔,位于铸件表层,形状呈针头形或细长圆形。
属本色。
泡,在凝固 过程中气泡未能及时排出而形成气孔 。
3、侵入气孔多呈梨形或椭圆形,位于铸件表层或近 表层,比较集中,尺寸较大,孔壁光滑,表面常呈氧 化色或蓝色。
铸造缺陷

铸件缺陷的分类铸件缺陷的种类很多,形式不一,各有其特点。
按缺陷性质可分为孔眼类;裂纹类;表面缺陷;形状、尺寸和重量不合格;成分、组织和性能不合格五大类。
普通铸铁件在生产过程中,各工序可能产生缺陷的情况不同,铸件容易产生气孔,而产生缺陷主要在造型、熔炼、浇注、配砂和清理等工序上。
下面我对铸造缺陷种类进行详细的解释。
一.孔眼类孔眼类一般表现为气孔、缩孔、缩松、渣眼、砂眼、铁豆。
1. 气孔是指在铸件内部、表面或者近于表面处有大小不等的光滑孔眼。
形状有圆的、长的及不规则的;有单个的,也有聚集成片的。
颜色为白色或者带一层暗色,有时覆有一层氧化皮。
2. 缩孔是指在铸件厚断面内部、两交接面的内部及厚断面和薄断面交接处的内部或表面。
形状不规则,孔内壁粗糙不平,晶粒粗大。
3. 缩松指在铸件内部有微小而不连贯的缩孔,聚集在一处或多处,晶粒粗大,各晶粒间存在很多的孔眼,水压实验时渗水。
4. 渣眼指在铸件内部或者表面有不规则的孔眼,孔眼内不光滑,里面全部或者部分充塞着熔渣。
5. 砂眼是指在铸件内部或者表面有冲塞着型砂的孔眼。
6. 铁豆是指在铸件内部或者表面有包含金属小珠的孔眼,常常发生在铸铁件上。
二.裂纹类裂纹一般表现为热烈、冷裂、温裂。
1. 热裂:在铸件上有穿透或者不穿透的裂纹(主要是弯曲形状的0,开裂处金属表面氧化。
2. 冷裂:在铸件上有穿透或者不穿透的裂纹(主要是直线的),开裂处金属表面未氧化。
3. 温裂:在铸件上有穿透或者不穿透的裂纹.开裂处的金属表面氧化。
由于气割、焊接或者热处理不当所引起的。
三.表面缺陷表面缺陷一般表现为粘砂、结疤、夹砂、冷隔。
1. 粘砂指在铸件表面上全部或者部分覆盖着金属(或者金属氧化物)与砂(或涂料)的混合物(或化合物),或一层烧结的型砂,致使铸件表面粗糙。
2. 结疤是指在铸件表面上,有金属夹杂或包含型砂或渣的片状或瘤状物。
3. 夹砂是指在铸件表面上,有一层金属瘤状物或者片状物。
在金属瘤片和铸件之间夹有一层型砂。
铸件常见铸造缺陷

铸造常见缺陷特点
缺陷名称:披缝 缺陷特点:铸件表面在分模 面处的规则缩陷。 产生原因: 砂型或砂芯分模 面处的飞边未去除
铸造常见缺陷特点
缺陷名称:表面多肉 缺陷特点:铸件表面有多余 的部分。 产生原因:砂型或砂芯的相 应部分掉肉。
铸造常见缺陷特点
缺陷名称:黑皮(其二)
铸造常见缺陷特点
缺陷名称:气孔 缺陷特点:铸件内部或表面 有大小不同的孔眼,孔的内 壁光滑,多呈圆形。 产生原因:砂型太紧或型砂 透气性差;型砂太湿;砂芯 通气孔堵塞;浇注系统不正 确,气体排不出去
铸造常见缺陷特点
缺陷名称:缩孔(大而集中 的空洞 ) 缺陷特点:铸件厚、断面处 出现形状不规则的孔眼,孔 的内壁粗糙。 产生原因:冒口设置不正确 ;合金成分不合格,收缩过 大;浇注温度过高;铸件设 计不合理,无法进行补缩
铸造常见缺陷特点
缺陷名称:砂眼 缺陷特点:铸件内部或表面 有充满砂粒的孔眼,孔形不 规则 产生原因:型砂强度不够或 局部没舂紧,掉砂;型腔、 浇口内散砂未吹净;合箱时 砂型局部挤坏,掉砂;浇注 系统不合理,冲坏砂型
铸造常见缺陷特点
缺陷名称:砂眼(其二)
铸造常见缺陷特点
缺陷名称:砂眼(名称:表面多肉肉(其 二)
铸造常见缺陷特点
缺陷名称:缺肉(缺料) 缺陷特点:铸件表面有缺少 一块,可能导致报废。 产生原因:浇冒口切除时带 掉一块;
铸造常见缺陷特点
缺陷名称:表面缩凹 缺陷特点:铸件表面有缩凹。 产生原因:铸件内部收缩
铸造常见缺陷特点
缺陷名称:黑皮 缺陷特点:加工面有加工不 到的地方 产生原因:铸件加工量不足, 铸件变形,夹偏
铸造缺陷的种类和原因
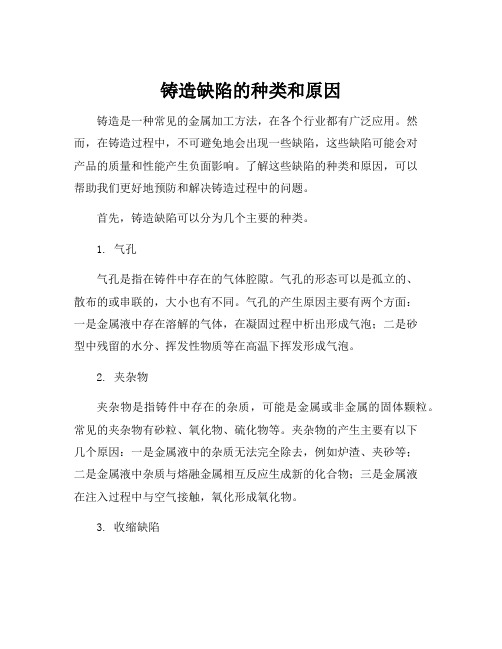
铸造缺陷的种类和原因铸造是一种常见的金属加工方法,在各个行业都有广泛应用。
然而,在铸造过程中,不可避免地会出现一些缺陷,这些缺陷可能会对产品的质量和性能产生负面影响。
了解这些缺陷的种类和原因,可以帮助我们更好地预防和解决铸造过程中的问题。
首先,铸造缺陷可以分为几个主要的种类。
1. 气孔气孔是指在铸件中存在的气体腔隙。
气孔的形态可以是孤立的、散布的或串联的,大小也有不同。
气孔的产生原因主要有两个方面:一是金属液中存在溶解的气体,在凝固过程中析出形成气泡;二是砂型中残留的水分、挥发性物质等在高温下挥发形成气泡。
2. 夹杂物夹杂物是指铸件中存在的杂质,可能是金属或非金属的固体颗粒。
常见的夹杂物有砂粒、氧化物、硫化物等。
夹杂物的产生主要有以下几个原因:一是金属液中的杂质无法完全除去,例如炉渣、夹砂等;二是金属液中杂质与熔融金属相互反应生成新的化合物;三是金属液在注入过程中与空气接触,氧化形成氧化物。
3. 收缩缺陷收缩缺陷是指铸件因为金属凝固收缩而产生的缺陷。
由于金属凝固时体积缩小,如果铸型或冷却速度不合理,就会出现收缩缺陷。
常见的收缩缺陷有未凝固收缩孔、凝固收缩裂缝等。
4. 热裂缺陷热裂缺陷是指铸件在冷却过程中由于温度梯度或应力引起的裂纹。
热裂缺陷的主要原因有两个方面:一是铸型或冷却系统的设计不合理,导致温度梯度过大;二是铸件内部存在应力集中区域,如尖角、过薄或结构设计不佳的地方。
了解了铸造缺陷的种类,接下来我们需要探究这些缺陷产生的原因。
铸造缺陷的产生原因是多方面的,需要从金属液、模具和操作等多个方面综合考虑。
首先,金属液质量是产生铸造缺陷的关键因素之一。
金属液中的杂质和气体含量过高,会导致气孔和夹杂物的产生。
此外,金属液的温度、合金成分、浇注速度等也会影响铸造缺陷的形成。
其次,模具的设计和制造也是铸造缺陷的重要原因。
模具的结构设计不合理,如冷却系统不畅、浇注系统设计不良等,都会导致铸造缺陷的产生。
此外,模具材料的选择和加工工艺的控制也会对铸造质量产生影响。
铸造过程中常见的几种缺陷
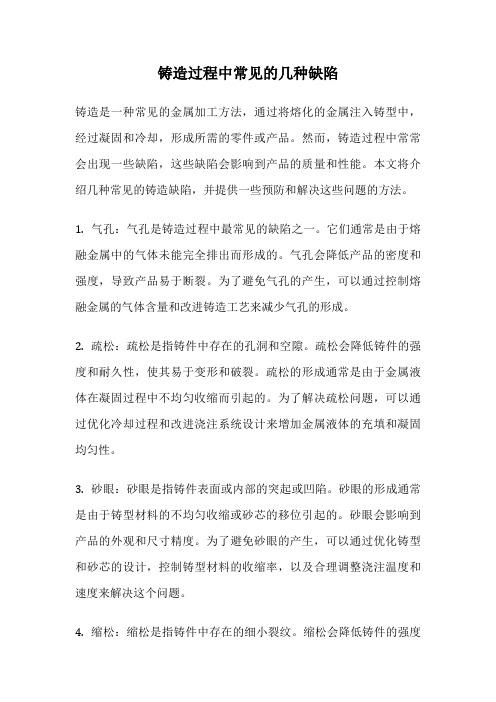
铸造过程中常见的几种缺陷铸造是一种常见的金属加工方法,通过将熔化的金属注入铸型中,经过凝固和冷却,形成所需的零件或产品。
然而,铸造过程中常常会出现一些缺陷,这些缺陷会影响到产品的质量和性能。
本文将介绍几种常见的铸造缺陷,并提供一些预防和解决这些问题的方法。
1. 气孔:气孔是铸造过程中最常见的缺陷之一。
它们通常是由于熔融金属中的气体未能完全排出而形成的。
气孔会降低产品的密度和强度,导致产品易于断裂。
为了避免气孔的产生,可以通过控制熔融金属的气体含量和改进铸造工艺来减少气孔的形成。
2. 疏松:疏松是指铸件中存在的孔洞和空隙。
疏松会降低铸件的强度和耐久性,使其易于变形和破裂。
疏松的形成通常是由于金属液体在凝固过程中不均匀收缩而引起的。
为了解决疏松问题,可以通过优化冷却过程和改进浇注系统设计来增加金属液体的充填和凝固均匀性。
3. 砂眼:砂眼是指铸件表面或内部的突起或凹陷。
砂眼的形成通常是由于铸型材料的不均匀收缩或砂芯的移位引起的。
砂眼会影响到产品的外观和尺寸精度。
为了避免砂眼的产生,可以通过优化铸型和砂芯的设计,控制铸型材料的收缩率,以及合理调整浇注温度和速度来解决这个问题。
4. 缩松:缩松是指铸件中存在的细小裂纹。
缩松会降低铸件的强度和韧性,使其易于断裂。
缩松的形成通常是由于金属液体在凝固过程中体积收缩而引起的。
为了避免缩松的产生,可以通过增加浇注温度和压力,以及优化铸型设计和浇注系统来减少金属液体的收缩。
5. 夹杂物:夹杂物是指铸件中存在的杂质和非金属物质。
夹杂物会降低铸件的强度和耐久性,导致其易于断裂。
夹杂物的形成通常是由于金属液体中的杂质和氧化物未能完全排除而引起的。
为了避免夹杂物的产生,可以通过改进金属液体的净化和过滤系统,以及优化浇注工艺和铸型设计来减少夹杂物的形成。
铸造过程中常见的缺陷包括气孔、疏松、砂眼、缩松和夹杂物。
这些缺陷会影响到铸件的质量和性能,因此在铸造过程中需要采取相应的措施来预防和解决这些问题。
铸造常见的缺陷与产生原因

铸造常见的缺陷与产生原因铸造是一种常用的金属加工方法,其用途广泛,但在生产过程中常常会产生一些缺陷,如气孔、夹渣、缩孔等。
这些缺陷不仅会影响铸件的外观质量,还可能降低其力学性能和使用寿命。
下面我将从不同的缺陷类型和产生原因两个方面详细介绍。
一、缺陷类型1. 气孔:气体在铸造过程中产生,并被封入铸件内部,形成孔隙。
气孔的尺寸和分布形态不同,可能是小孔、球形孔、管状孔等。
气孔的产生主要与以下几个因素有关:(1) 铝液中的气体:铝液中含有的氧和氢会在高温下产生氧化反应和水解反应,释放出氧气和氢气。
(2) 表面液相:铝液在铸模表面形成的氧化膜或润滑剂残留等可能导致铝液表面的液相存在,进一步促使气体产生。
(3) 细小颗粒:铝液中存在的颗粒会成为气体生成的核心,进而形成气孔。
2. 夹渣:铝液在充填过程中携带入模型腔内的杂质、氧化物或熔渣等,最终导致铸件内部出现夹杂物。
夹渣的产生原因主要有:(1) 原材料中的杂质:铝合金原材料中可能含有一些杂质,如氧化物、砂粒等。
(2) 熔化过程中的氧化:铝液在高温条件下容易与空气发生氧化反应,形成氧化物。
(3) 流动过程中的杂质:铝液在流动过程中可能带动模具内部的砂粒、润滑剂残留等。
3. 缩孔:铸件内部或者表面出现的凹陷或裂纹。
缩孔的产生原因主要有:(1) 升温不均:铝液升温不均会导致热胀冷缩不一致,从而在铸件内部产生收缩应力,进一步造成缩孔。
(2) 施加过大应力:当铸件过早地受到了外界应力(例如从模型中取出时),铸件内部的温度还没有完全降低,容易产生缩孔。
(3) 金属液体凝固时的收缩:铝合金在凝固过程中会出现一定的收缩,如果凝固过程中支撑不稳定,就会导致缩孔产生。
二、缺陷产生的原因1. 原材料:如果原材料中含有过多的杂质或者粒度过大、成分不均匀等情况,会直接导致铝液在充填模具的过程中产生缺陷。
2. 熔化处理:熔炼过程中的温度不稳定、炉温控制不当,以及熔化时间过长等问题都会导致铝液中含气量增加,从而产生气孔等缺陷。
铸造过程中常见的几种缺陷
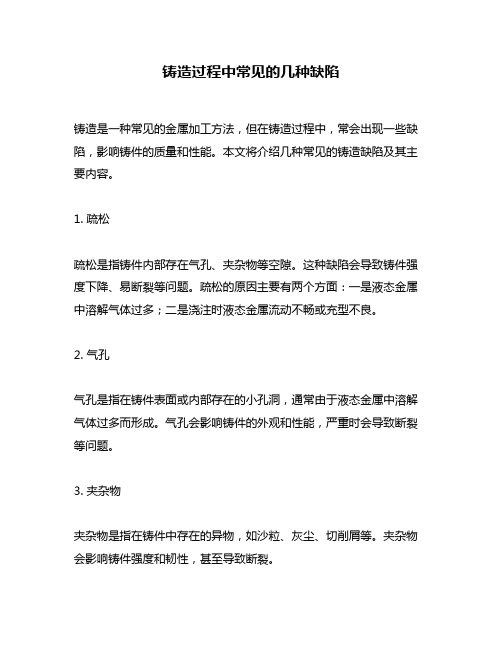
铸造过程中常见的几种缺陷
铸造是一种常见的金属加工方法,但在铸造过程中,常会出现一些缺陷,影响铸件的质量和性能。
本文将介绍几种常见的铸造缺陷及其主要内容。
1. 疏松
疏松是指铸件内部存在气孔、夹杂物等空隙。
这种缺陷会导致铸件强度下降、易断裂等问题。
疏松的原因主要有两个方面:一是液态金属中溶解气体过多;二是浇注时液态金属流动不畅或充型不良。
2. 气孔
气孔是指在铸件表面或内部存在的小孔洞,通常由于液态金属中溶解气体过多而形成。
气孔会影响铸件的外观和性能,严重时会导致断裂等问题。
3. 夹杂物
夹杂物是指在铸件中存在的异物,如沙粒、灰尘、切削屑等。
夹杂物会影响铸件强度和韧性,甚至导致断裂。
4. 热裂纹
热裂纹是指在冷却过程中,由于金属内部应力过大而导致的裂纹。
热裂纹通常发生在厚度不均匀的铸件部位,如壁厚变化处、边缘等。
5. 缩孔
缩孔是指铸件内部存在的凹陷或空洞,通常由于液态金属在凝固过程中收缩而形成。
缩孔会影响铸件的强度和密封性能。
为避免上述铸造缺陷的出现,可以采取以下措施:
1. 控制液态金属中溶解气体含量,如采用真空熔炼等方法。
2. 优化浇注系统设计,确保液态金属流动畅通。
3. 严格控制充型质量,如采用振动充型、压力充型等方法。
4. 控制冷却速度和温度梯度,避免产生应力过大的情况。
5. 优化铸件结构设计,避免壁厚变化过大、边角过于尖锐等情况。
总之,在铸造过程中要注意各个环节的质量控制和优化设计,以确保铸件质量和性能。
铸造缺陷分析资料

铁豆 夹砂 结疤
在铸件内部或表面有包含金属小珠的孔眼
指在铸件表面上,有一层金属瘤状和片状 物,在金属瘤片和铸件之间夹有一层型砂。
指在铸件表面上,有金属夹杂或包含型砂 或渣的片状或瘤状物
铁豆(1)
铁豆(2)
夹砂和结疤
夹砂
分类(11)
大 类
序 号
缺陷名称
特征
31
硬度不符
硬度测试值不在规格之内或落差较大不符 合要求者
气孔
不规则的。有单个存在也有多个聚集存
在。颜色为白色或带有一定暗色。孔壁
常伴有一层氧化皮。
常存在于铸件厚大断面、铸件壁厚交接
缩孔
部位。形状不规则,孔壁粗糙、晶粒粗
大。
气孔(1):气孔的形状
气孔(2):按位置分类
表 面 气 孔
内部气孔
皮下 气孔
按形成原因或形成机理分类: A. 侵入气孔; B. 裹携气孔(或卷入气孔); C. 析出气孔; D. 内生式反应气孔; E. 外生式反应气孔
此些 检测 方法 和前 面的 硬度 检测 一起 可统 称为 材料 检测
超声波、磁粉、着色、X射线检测
超声波及X射线检测 主要检测铸件内部缩 孔、缩松、气孔、渣 孔等缺陷。两种检测 机制和原理不同
磁粉及着色检测主要 检测铸件表面缺陷, 如线性缺陷(裂纹、氧 化渣)、非线性缺陷。
以上四种方法统称为 无损检测(NDT)
由于模具或型腔原因造成铸件部分缺损
打箱、搬运、清理或热处理时,损坏了铸 件的完整性
浇不足
由于铁水流动 性不足或浇注 系统截面积太 小等原因造成 铸件部分结构
未充满
漏箱
由于漏 箱致使 产品上 表面未 完全填
充
少肉
铸造缺陷及其解决方法
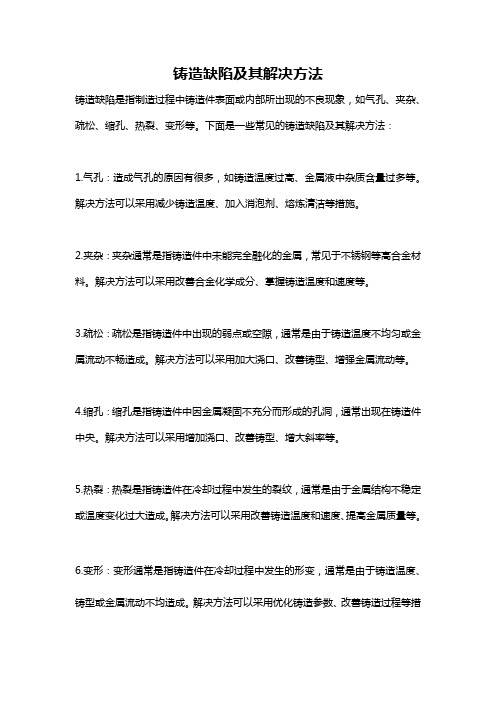
铸造缺陷及其解决方法
铸造缺陷是指制造过程中铸造件表面或内部所出现的不良现象,如气孔、夹杂、疏松、缩孔、热裂、变形等。
下面是一些常见的铸造缺陷及其解决方法:
1.气孔:造成气孔的原因有很多,如铸造温度过高、金属液中杂质含量过多等。
解决方法可以采用减少铸造温度、加入消泡剂、熔炼清洁等措施。
2.夹杂:夹杂通常是指铸造件中未能完全融化的金属,常见于不锈钢等高合金材料。
解决方法可以采用改善合金化学成分、掌握铸造温度和速度等。
3.疏松:疏松是指铸造件中出现的弱点或空隙,通常是由于铸造温度不均匀或金属流动不畅造成。
解决方法可以采用加大浇口、改善铸型、增强金属流动等。
4.缩孔:缩孔是指铸造件中因金属凝固不充分而形成的孔洞,通常出现在铸造件中央。
解决方法可以采用增加浇口、改善铸型、增大斜率等。
5.热裂:热裂是指铸造件在冷却过程中发生的裂纹,通常是由于金属结构不稳定或温度变化过大造成。
解决方法可以采用改善铸造温度和速度、提高金属质量等。
6.变形:变形通常是指铸造件在冷却过程中发生的形变,通常是由于铸造温度、铸型或金属流动不均造成。
解决方法可以采用优化铸造参数、改善铸造过程等措
施。
铸造缺陷

iii.不充满式浇注系统而裹入气泡
表4-2 裹携气孔形成原因和防治措施图示3 充满式浇注系统(直浇道为上大下小的倒锥 形),比不充满式浇注系统(圆柱形)有利于克服裹 入气泡。
3) 析出气孔
①.定义:以原子态溶解于金属液中的氢、氮气体元素, 金属液凝固时它们以分子态气相析出,形成气泡而使铸件产 生的气孔,称为析出气孔。由于氢析出而形成的析出气孔, 称为氢气孔;由于氮析出而形成的析出气孔,称为氮气孔。
V.分布:大多数情况下,是单个或几个聚集的,尺寸较 大的气孔。有时成为局部聚集的蜂窝状气孔(如图4-10 示),很少成为弥散性气孔或针孔。
③.形成机理
分三个阶段形成:第一阶段,气体侵入金属液;第二阶 段,型壁上气泡形成;第三阶段,气泡在型腔金属液中的滞 留或排出。
侵入性气孔形成的条件是:
pA>(p0+pm+pz) pA――“金属-铸型”界面上气泡所在处的压力; p0――型腔中的气体压力,一般为标准大气压力; pm――金属液静压力,pm=ρ•g•h; pz――金属液的表面阻力。
(3)位置:气孔可分布在铸件的任何位置。可分为: 内部气孔、皮下气孔、表面气孔。
内部气孔存在于铸件的内部,目视检查无法发现;如图 4-10所示。
皮下气孔成串横列于铸件表面以下1~3mm,一般为圆球 形、团球形、泪滴形或长针形;如图4-3、图4-4所示。
表面气孔存在于铸件毛坯表面,落砂清理后可以发现, 如图4-6所示。
形成该气孔的气体来自外部气体源,所以侵入气孔是一 种外生式气孔。
②.目视特征
i.形状――圆球形、团球 形的异形孔洞;有时是梨形 气孔,如图4-11示。
ii.孔壁表面面貌:孔壁平 滑。
iii.尺寸大小:尺寸通常较 大,最大尺寸达几毫米以上。
铸造缺陷及其对策书

铸造缺陷及其对策书(实用版)目录一、铸造缺陷的概述二、铸造缺陷的种类三、铸造缺陷产生的原因四、铸造缺陷的对策五、结论正文一、铸造缺陷的概述铸造缺陷是指在铸造过程中,由于各种原因导致的铸件不符合设计要求的缺陷。
铸造缺陷不仅会影响铸件的性能和质量,还会增加生产成本,甚至可能导致设备损坏和安全事故。
因此,研究铸造缺陷及其对策对于提高铸件质量具有重要意义。
二、铸造缺陷的种类铸造缺陷种类繁多,根据缺陷的性质和形态,可以分为以下几类:1.表面缺陷:如砂眼、气孔、麻点、裂纹等。
2.内部缺陷:如缩孔、缩松、夹杂、偏析等。
3.形状缺陷:如变形、歪曲、尺寸偏差等。
4.成分缺陷:如碳、硅、锰等元素含量偏离设计要求。
5.组织缺陷:如晶粒粗大、组织不均匀、白口组织等。
三、铸造缺陷产生的原因1.原材料方面:如铸造砂质量差、石英砂含泥量过高、熔炼过程中元素烧损等。
2.工艺方面:如熔炼温度过高或过低、浇注速度过快或过慢、浇注过程中气泡产生等。
3.设备方面:如砂箱振动不均匀、浇注器设计不合理、炉子温度控制不准确等。
4.操作方面:如砂型制作不规范、合箱时压实不均匀、浇注高度不够等。
四、铸造缺陷的对策1.选择优质的原材料,提高铸型的质量。
2.优化熔炼工艺,控制熔炼温度、元素烧损和气体含量。
3.改进浇注工艺,合理控制浇注速度、压注压力和浇注高度。
4.完善设备设施,提高设备的精度和稳定性。
5.加强操作培训,提高工人的操作技能和质量意识。
五、结论通过对铸造缺陷及其对策的研究,可以降低铸件的缺陷率,提高铸件的质量和性能。
铸造质量缺陷知识点总结
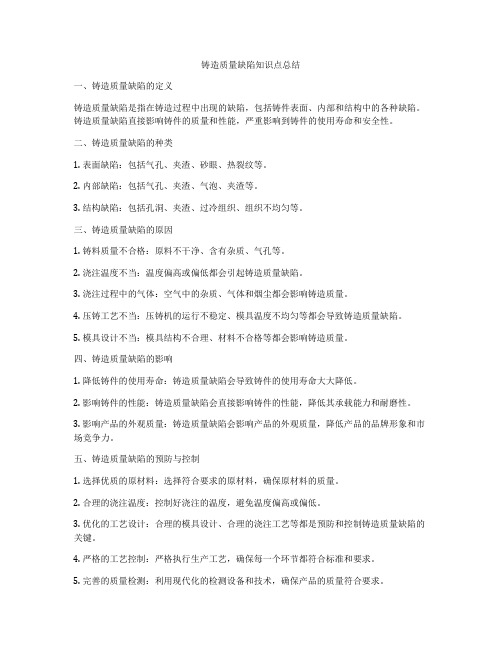
一、铸造质量缺陷的定义铸造质量缺陷是指在铸造过程中出现的缺陷,包括铸件表面、内部和结构中的各种缺陷。
铸造质量缺陷直接影响铸件的质量和性能,严重影响到铸件的使用寿命和安全性。
二、铸造质量缺陷的种类1. 表面缺陷:包括气孔、夹渣、砂眼、热裂纹等。
2. 内部缺陷:包括气孔、夹渣、气泡、夹渣等。
3. 结构缺陷:包括孔洞、夹渣、过冷组织、组织不均匀等。
三、铸造质量缺陷的原因1. 铸料质量不合格:原料不干净、含有杂质、气孔等。
2. 浇注温度不当:温度偏高或偏低都会引起铸造质量缺陷。
3. 浇注过程中的气体:空气中的杂质、气体和烟尘都会影响铸造质量。
4. 压铸工艺不当:压铸机的运行不稳定、模具温度不均匀等都会导致铸造质量缺陷。
5. 模具设计不当:模具结构不合理、材料不合格等都会影响铸造质量。
四、铸造质量缺陷的影响1. 降低铸件的使用寿命:铸造质量缺陷会导致铸件的使用寿命大大降低。
2. 影响铸件的性能:铸造质量缺陷会直接影响铸件的性能,降低其承载能力和耐磨性。
3. 影响产品的外观质量:铸造质量缺陷会影响产品的外观质量,降低产品的品牌形象和市场竞争力。
五、铸造质量缺陷的预防与控制1. 选择优质的原材料:选择符合要求的原材料,确保原材料的质量。
2. 合理的浇注温度:控制好浇注的温度,避免温度偏高或偏低。
3. 优化的工艺设计:合理的模具设计、合理的浇注工艺等都是预防和控制铸造质量缺陷的关键。
4. 严格的工艺控制:严格执行生产工艺,确保每一个环节都符合标准和要求。
5. 完善的质量检测:利用现代化的检测设备和技术,确保产品的质量符合要求。
1. 热处理修复:利用热处理技术对铸件进行修复,提高其结构和性能。
2. 焊接修复:对于一些大型铸件,可以使用焊接技术对其进行修复。
3. 精密加工:对于一些表面缺陷较大的铸件,可以利用精密加工技术进行修复。
4. 重新铸造:对于一些严重的缺陷,可以考虑重新铸造。
七、发展趋势随着科学技术的不断进步,铸造质量缺陷的预防和控制技术也在不断提高。
铸造缺陷总结汇报

铸造缺陷总结汇报铸造是一种常见的制造工艺,用于制造各种金属制品。
然而,在铸造过程中,常常会出现一些缺陷,这些缺陷会对产品的质量和性能产生不良影响。
因此,及时总结和汇报铸造缺陷是非常重要的,下面我们来详细讨论一下。
首先,铸造缺陷的种类非常多样。
常见的铸造缺陷主要包括气孔、夹杂物、缩孔、疏松、铸钢、铸锻件表面缺陷等。
这些缺陷的产生原因可以是多方面的,比如金属液内含的气体未能完全排出,金属液流动不畅导致夹杂物的进入,铸型砂中水分过多导致疏松缩敛等等。
其次,针对不同种类的铸造缺陷,需要采取相应的解决方法。
对于气孔和夹杂物来说,需要通过提高浇注温度和浇注速度来减少气体的溶解度和夹杂物的进入;对于缩孔和疏松来说,主要应采用合适的浇注系统和优化固化过程,以提高金属液的流动性和减少气体和夹杂物的进入。
至于铸钢和铸锻件表面的缺陷,则需要采用相应的表面处理方法,提高表面的光洁度和平整度。
此外,铸造缺陷的发生与操作人员的技术水平和操作规范密切相关。
因此,在铸造过程中,必须加强操作人员的培训和管理,提高他们的技能水平和操作规范,从而减少铸造缺陷的发生。
同时,还需要加强对原材料的检验和质量控制,以确保原材料的质量符合要求,减少缺陷的发生。
最后,为了及时发现和解决铸造缺陷,必须建立起完善的缺陷检测和处理体系。
在铸造过程中,需要定期对铸造产品进行检测,及时发现并处理缺陷。
对于已经发生的缺陷,需要采取相应的补救措施,以保证产品的质量和性能。
此外,还需要建立起缺陷统计和分析的机制,对不同缺陷的发生频率和原因进行统计和分析,以便进一步改进铸造工艺和提高产品质量。
综上所述,铸造缺陷的总结和汇报对于保证产品质量和提高铸造工艺至关重要。
只有及时总结和汇报铸造缺陷,才能不断改进铸造工艺,提高产品质量,推动企业的发展。
因此,我们应该重视铸造缺陷的问题,加强对其的研究和解决,为企业的可持续发展做出贡献。
铸造缺陷及防止方法

铸造缺陷及防止方法铸造是一种常用的金属加工工艺,可以将熔化的金属倒入铸型中,通过冷却凝固形成所需形状的金属制品。
然而,在铸造过程中,由于多种因素的影响,往往会导致一些缺陷出现在铸件上。
这些缺陷可能会降低铸件的质量和性能,因此有必要研究和防止铸造缺陷的发生。
一、常见的铸造缺陷类型1.气孔:气孔是铸造缺陷中最常见的一种,它是由金属液中残留的气体在凝固过程中形成的小空洞。
气孔会降低铸件的强度和密封性能,并且可能导致泄漏的发生。
2.夹杂物:夹杂物是指固体杂质或其他金属液滴等不溶于基体金属的颗粒物质。
夹杂物会引起局部应力集中和腐蚀等问题,从而降低铸件的耐蚀性和机械性能。
3.砂眼:砂眼是指铸件表面上的凹陷或孔洞,主要由于铸型中的砂粒脱落或重叠造成。
砂眼会影响铸件的外观和尺寸精度,降低其使用价值。
4.缩孔:缩孔是铸件内部或表面上的凹陷,它是由于金属凝固过程中产生的体积收缩引起的。
缩孔会降低铸件的强度和韧性,增加冲击和断裂的风险。
二、铸造缺陷的防止方法1.优化铸造工艺:通过合理设计铸造工艺参数,如浇注温度、浇注速度、浇注方式等,可以减少金属液中的气体吸收,并降低气孔和夹杂物的形成。
2.提高模具质量:优质的模具能够提供良好的液态金属充填条件,并且减少金属液和砂模接触引起的气体和杂质污染。
因此,选择高质量的模具材料和加工工艺非常重要。
3.合理选择铸造材料:根据铸件的要求选择适合的铸造材料,如选用低气性和低杂质含量的金属,可以减少铸造缺陷的发生。
4.加强铸造设备维护:定期检查和维护铸造设备,特别是容易产生污染和损坏的部件,可以减少外来杂质和缺陷的产生。
5.实施严格的质量控制和检验:建立科学的质量控制体系,制定详细的工艺规范和操作规程,严格按照要求进行检验和记录,及时发现和解决潜在的缺陷问题。
总结:铸造缺陷是铸件制造过程中经常面临的问题,但通过合理的措施和方法,可以有效地预防和减少铸造缺陷的发生。
优化铸造工艺、提高模具质量、合理选择铸造材料、加强设备维护以及实施严格的质量控制和检验,是有效预防铸造缺陷的关键。
- 1、下载文档前请自行甄别文档内容的完整性,平台不提供额外的编辑、内容补充、找答案等附加服务。
- 2、"仅部分预览"的文档,不可在线预览部分如存在完整性等问题,可反馈申请退款(可完整预览的文档不适用该条件!)。
- 3、如文档侵犯您的权益,请联系客服反馈,我们会尽快为您处理(人工客服工作时间:9:00-18:30)。
铸造缺陷种类
1、气孔缺陷。
铸铁件在凝固过程中未能逸出的气体留在铸件内部形成的小孔洞,内壁光滑,有气体。
表面一般情况下呈球状或椭球状,对于超声波具有较高的反射率,因此可以通过超声波进行检测。
2、缩松、缩孔缺陷。
铸铁件在冷却凝固时,体积收缩,在最后凝固的时候得不到充足的铁液的补充便会形成空洞状的缺陷,内壁粗糙,周围多伴有许多杂质和细小的气孔。
缩松呈现细小而分散的空隙,缩孔呈现大而集中的空洞。
3、偏析缺陷。
指铁合金在冶炼过程中或铁金属在熔化的过程中因为成分分布不均而形成的成分偏析,有偏析存在的区域其力学性能和整个金属的力学性能有较大的差别。
4、裂纹缺陷。
铸铁件中的裂纹主要时由于金属材料的强度难以支撑金属在冷却凝固时的收缩应力,这与金属中的合金含量、铸铁件的形状设计和铸造工艺有很大的关系。
5、冷隔缺陷。
这是指在浇注铁液时,由于飞溅、浇注中断或来自不同方向的两股金属流相遇,液态金属表面冷却形成的半固态薄膜留在铸铁件内而形成的一种隔膜状的面积型缺陷。