电镀过程中氢脆的产生及其抑制措施
电镀中酸洗改进与防氢脆措施全套
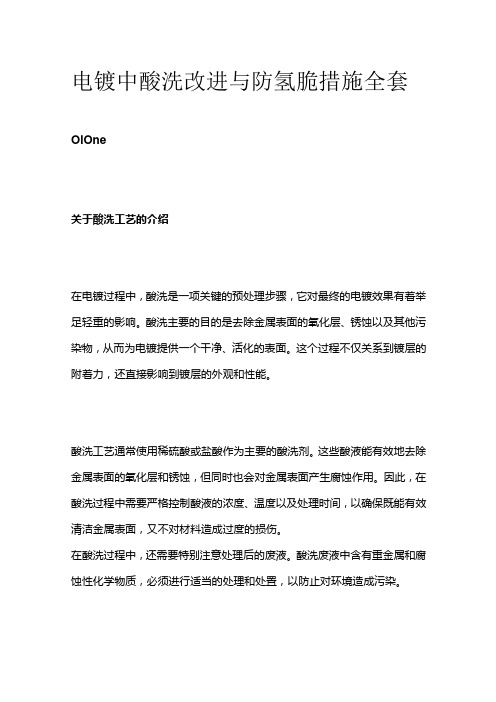
电镀中酸洗改进与防氢脆措施全套OlOne关于酸洗工艺的介绍在电镀过程中,酸洗是一项关键的预处理步骤,它对最终的电镀效果有着举足轻重的影响。
酸洗主要的目的是去除金属表面的氧化层、锈蚀以及其他污染物,从而为电镀提供一个干净、活化的表面。
这个过程不仅关系到镀层的附着力,还直接影响到镀层的外观和性能。
酸洗工艺通常使用稀硫酸或盐酸作为主要的酸洗剂。
这些酸液能有效地去除金属表面的氧化层和锈蚀,但同时也会对金属表面产生腐蚀作用。
因此,在酸洗过程中需要严格控制酸液的浓度、温度以及处理时间,以确保既能有效清洁金属表面,又不对材料造成过度的损伤。
在酸洗过程中,还需要特别注意处理后的废液。
酸洗废液中含有重金属和腐蚀性化学物质,必须进行适当的处理和处置,以防止对环境造成污染。
为了确保酸洗工艺的有效性和安全性,电镀工厂的管理者和操作人员需要对酸洗过程有深入的了解,并严格遵守操作规程。
下面,我们将详细探讨在电镀中进行酸洗时应注意的具体事项。
02Two酸洗工艺的改进及其注意事项在汽车行业的电镀过程中,酸洗是一个关键步骤,用于清除金属表面的锈蚀。
锈蚀主要由铁的氧化物和氢氧化物组成。
这些通常通过酸类组分(如盐酸)和表面活性剂的协同作用来清除,其过程涉及到溶解和剥落。
然而,传统的酸洗方法存在一些缺点,例如高酸浓度可能导致过腐蚀和环境问题。
为此,我们采取了以下改进措施:L降低酸浓度:降低酸浓度,如将盐酸从30%~35%的质量分数降低,可以减少酸液消耗,改善环境,并提高工件表面质量。
低浓度酸液在润湿剂的作用下,能迅速渗透到氧化皮和基体的界面,引发化学反应(Fe÷2HCI=2FeCI2+H2T),同时利用氢气的机械剥落作用来清洁表面。
使用DS857酸性除垢剂能够减少对裸露基体的腐蚀,降低酸的无用消耗。
2 .混合酸液的使用:将盐酸和硫酸按适当比例混合,结合两种酸的特性,能够提高除锈速度并降低操作温度。
3 .采用多功能高效除油除锈剂:如多功能酸洗除油粉和活化盐,这标志着钢铁酸洗工艺的进步。
镀铬工艺中的氢脆

镀铬工艺中的氢脆1.电镀装饰性铬工艺中,比较容易产生氢脆的工序有:阴极电化学除油、浸蚀、电镀等。
2.镀硬铬时因为工件表面大多经过磨光,因此不进行浸蚀。
加厚镀铬时吸氢多,镀铬后必须立即进行除氢。
对于高强度钢镀铬,严禁采用阴极电化学除油和浸蚀。
其目的都是为了防止氢脆。
3.除油可分化学除油和电化学除油两种。
1)化学除油多半是在碱性溶液中进行,对于一般钢材无多大影响,但对超高强度钢材料也及微脆化问题。
例如,氢氧化钠大于lOOg/L、温度高达1000C,就容易产生脆化。
在碱性溶液中产生脆性故称为碱脆。
但远不如阴极电化学除油严重。
2)电化学除油可分为阴极除油、阳极除油、先阴极后阳极联合除油。
4.在同样电流密度下,阴极析出的氢气要比阳极析出的氧气体积多一一倍,所以阴极除油率高,但受氢严重,一般适用有色金属除油。
对于绝大多数钢铁件,可采用先阴极后阳极的合除油法,这样既可以提高除油效率,5.于超高强度钢材料、氢脆敏感材料、受高负荷的零件、薄钢片和弹簧片等,为了避免由于渗氢而产生氢脆,只进行阳极除油。
阳极除油还有去氢的效果。
油也可以除净,可减少镀层起泡、脱皮、合力差等缺陷。
当工件侈电电镀等连续受氢,渗入金属内的氢逸出时就会有相当大的压力,当压力超过镀层极限时,镀层就会起泡,这种起泡是氢膨胀造成的,是指除油良好情况下产生的气泡,会造成返工。
因此,多数采用阳极除油法来解决。
由于渗氢问题,常常在技术标准中规定:严禁阴极除池。
:声要是针对高强度钢材料。
国际上对氢脆特别重视。
鞠痳材料表面氧化层需要浸蚀除去,在浸蚀时伴随氧化皮去除过程,还同时发生氢脆的危险因时伴随氧化皮去除过程,还同时发生氢脆的危险因素。
因此,高强度6.浸蚀过程中的氢并不是全部渗入金属中,有一部分变成氢气跑到空气中,只有少部分原子态的氢向金属中扩散。
向金属扩散的氢很容易在缺陷处聚集,重新化合成氢分子,并在这里形成很高的压力,尤其是弹簧、弹簧片,因经常变形,而且产生及微裂缝存在,该部位很容易产生脆断,这种脆断及微裂缝【电镀设备厂】仔仕巴不同材料和不同的浸蚀所产生渗氢的结果是不同的。
去氢脆处理原因与措施

文章主要说明氢脆产生的原因,并以液压主控阀阀芯为例讲述发生氢脆的薄弱点,最后阐明了去氢脆处理的主要措施。
一、氢脆的定义氢脆是溶于钢中的氢聚合为氢分子,造成应力集中,超过钢的强度极限,在钢内部形成细小的裂纹,又称白点。
氢脆主要发生在低合金高强度钢、不锈钢及弹性零件上,造成氢脆的主要原因是表面处理,如电镀、氮化等零件的处理过程中产生的氢渗入到金属内部导致晶格排列混乱,产生扭曲,造成内应力增加,使金属或镀层产生脆性,从而引起零件的断裂或镀层的脱落。
在过程中氢脆的发生需要满足两个条件:金属有较高的含氢量;有一定的外力作用。
由于氢脆所导致的滞后开裂的特性,严重影响零部件的使用性能,存在较大的安全隐患。
因此在零件的设计加工时,尤其是液压元件工作在高压下,更需要严格控制。
二、去氢脆处理适用的范围及工序并不是所有金属在表面处理过程中都会产生氢脆现象,通过研究数据及实践来看,在零件表面处理后氢脆主要产生于以下材料中。
(1)抗拉强度在981N/mm2(或硬度在38HRC)以上的经过热处理的碳素钢及合金钢零件。
(2)硬度为370HV以上的弹簧钢(包含琴钢丝、油回火钢丝、高碳钢丝)的零件。
(3)在抗拉强度1236N/mm2以上(或36HRC以上)实施热处理的马氏体的不锈钢产品。
现在的加工中,可导致氢脆的工序主要有酸洗、电镀、氮化、电解,以上工序在处理零件表面时,会产生氢且渗入到零件中,从而导致氢脆。
三、氢脆的案例分析液压产品一般需在高压下工作,部分零件承受的力较大,当零件吸氢后,在其薄弱地方会发生断裂,如图1所示的阀芯。
阀芯内部为中空,由于功能要求,中空处需要与单向阀配合密封,阀芯处于高压工作,这就需要与单向阀的配合处具有较强的抗冲击性及韧性,同时为了达到一定的耐磨要求,许多厂家选择该种阀芯表面镀铬处理,而且要求的镀层较厚,但由于镀铬工艺本身电流效率低,因此需要电镀的时间较长,渗氢严重。
图1 主控阀阀芯示意该阀芯材质为42CrMo,调质处理后硬度为32~36HRC,装配后要求镀铬层厚度0.04~0.06mm。
氢脆的避免消除措施

金属材料的两种经常有关而又有别的被破坏(或断裂)的现象。
目前,由延迟断裂氢脆引发的弹性紧固件断裂自然是一个严重的产品质量问题,人们可以采取各种技术来减少和预防弹性紧固件的氢脆问题。
1.材料缺陷的影响
弹性紧固件材料表面缺陷对电镀锌的有害影响是不容忽视的,比如钢板表面轻微裂纹折叠、斑痕蚀坑夹杂和超过允许深度的脱碳层,都会对弹性紧固件镀锌产生十分有害的影响,压弯成型不当造成表面插划伤,局部应力集中等都会有不良影响。
⑶应选择氢脆性较小的镀锌电解液,一般而言,氯化物型镀锌电解液相对析氢较少,产生氢脆的可能性也小;而氰化物镀锌电解液析氢、渗氢较多,产生氢脆的机率也较大。
⑷采用有效的驱氢工序驱散渗氢,减少氢脆应力。驱氢温度一般为190-230℃,驱氢时间6-8h。在电镀锌后钝化前2h内进行,停留时间越短越好。
我要评论查看评论
2.热处理工艺的影响
热处理工艺对弹性紧固件电镀锌后的氢脆是有较大影响的,若硬度≥45HRc时,均会诱发或导致弹性紧固件断裂。
在确保热处理技术参数的前提下,选择适宜的加热温度,合理的加热时间,充分予以回火。以最大限度地消除组织应力和热应力,避免其有害影响。淬火加热时应严防氧化和脱碳,网带炉碳势控制在0.60%-0.70%,盐浴炉必须认真脱氧捞渣,进行硬度检测时,严格注意表面层造成硬度虚假现象,使硬度測试值失真。一般应控制在42-44HRc为佳,不要超过45HRc。
(1)
式中α为形状因子,可从断裂力学手册中查到。裂纹深度(a)的扩展速度(da/dt)随KI的变化,一般有图3所示的三阶段的关系,依据Ⅱ阶段的da/dt以及(1)式,可以估算寿命。
氢脆的原理与预防

去氢处理,也称除氢处理,一般对电镀前后必须进行工序,特别是对高强度高硬度的零件在电镀工艺中。
氢脆的原理与预防在任何电镀溶液中,由于水分子的离解,总或多或少地存在一定数量的氢离子。
因此,电镀过程中,在阴极析出金属(主反应)的同时,伴有氢气的析出(副反应)。
析氢的影响是多方面的,其中最主要的是氢脆。
氢脆是表面处理中最严重的质量隐患之一,析氢严重的零件在使用过程中就可能断裂,造成严重的事故。
表面处理技术人员必须掌握避免和消除氢脆的技术,氢脆的影响降低到最低限度。
一、氢脆1氢脆现象氢脆通常表现为应力作用下的延迟断裂现象。
曾经出现过汽车弹簧、垫圈、螺钉、片簧等镀锌件,在装配之后数小时内陆续发生断裂,断裂比例达40%~50%。
某特种产品镀镉件在使用过程中曾出现过批量裂纹断裂,曾组织过全国性攻关,制订严格的去氢工艺。
另外,有一些氢脆并不表现为延迟断裂现象,例如:电镀挂具(钢丝、铜丝)由于经多次电镀和酸洗退镀,渗氢较严重,在使用中经常出现一折便发生脆断的现象;猎枪精锻用的芯棒,经多次镀铬之后,堕地断裂;有的淬火零件(内应力大)在酸洗时便产生裂纹。
这些零件渗氢严重,无需外加应力就产生裂纹,再也无法用去氢来恢复原有的韧性。
2 氢脆机理延迟断裂现象的产生是由于零件内部的氢向应力集中的部位扩散聚集,应力集中部位的金属缺陷多(原子点阵错位、空穴等)。
氢扩散到这些缺陷处,氢原子变成氢分子,产生巨大的压力,这个压力与材料内部的残留应力及材料受的外加应力,组成一个合力,当这合力超过材料的屈服强度,就会导致断裂发生。
氢脆既然与氢原子的扩散有关,扩散是需要时间的,扩散的速度与浓差梯度、温度和材料种类有关。
因此,氢脆通常表现为延迟断裂。
氢原子具有最小的原子半径,容易在钢、铜等金属中扩散,而在镉、锡、锌及其合金中氢的扩散比较困难。
镀镉层是最难扩散的,镀镉时产生的氢,最初停留在镀层中和镀层下的金属表层,很难向外扩散,去氢特别困难。
经过一段时间后,氢扩散到金属内部,特别是进入金属内部缺陷处的氢,就很难扩散出来。
氢脆的原理与预防
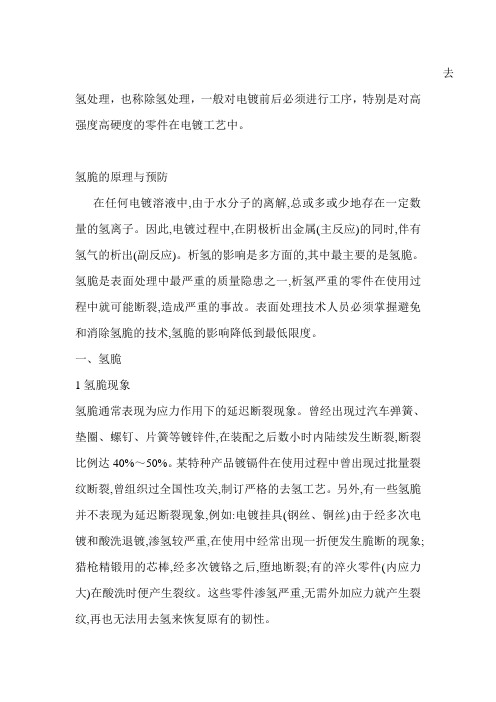
去氢处理,也称除氢处理,一般对电镀前后必须进行工序,特别是对高强度高硬度的零件在电镀工艺中。
氢脆的原理与预防在任何电镀溶液中,由于水分子的离解,总或多或少地存在一定数量的氢离子。
因此,电镀过程中,在阴极析出金属(主反应)的同时,伴有氢气的析出(副反应)。
析氢的影响是多方面的,其中最主要的是氢脆。
氢脆是表面处理中最严重的质量隐患之一,析氢严重的零件在使用过程中就可能断裂,造成严重的事故。
表面处理技术人员必须掌握避免和消除氢脆的技术,氢脆的影响降低到最低限度。
一、氢脆1氢脆现象氢脆通常表现为应力作用下的延迟断裂现象。
曾经出现过汽车弹簧、垫圈、螺钉、片簧等镀锌件,在装配之后数小时内陆续发生断裂,断裂比例达40%~50%。
某特种产品镀镉件在使用过程中曾出现过批量裂纹断裂,曾组织过全国性攻关,制订严格的去氢工艺。
另外,有一些氢脆并不表现为延迟断裂现象,例如:电镀挂具(钢丝、铜丝)由于经多次电镀和酸洗退镀,渗氢较严重,在使用中经常出现一折便发生脆断的现象;猎枪精锻用的芯棒,经多次镀铬之后,堕地断裂;有的淬火零件(内应力大)在酸洗时便产生裂纹。
这些零件渗氢严重,无需外加应力就产生裂纹,再也无法用去氢来恢复原有的韧性。
2 氢脆机理延迟断裂现象的产生是由于零件内部的氢向应力集中的部位扩散聚集,应力集中部位的金属缺陷多(原子点阵错位、空穴等)。
氢扩散到这些缺陷处,氢原子变成氢分子,产生巨大的压力,这个压力与材料内部的残留应力及材料受的外加应力,组成一个合力,当这合力超过材料的屈服强度,就会导致断裂发生。
氢脆既然与氢原子的扩散有关,扩散是需要时间的,扩散的速度与浓差梯度、温度和材料种类有关。
因此,氢脆通常表现为延迟断裂。
氢原子具有最小的原子半径,容易在钢、铜等金属中扩散,而在镉、锡、锌及其合金中氢的扩散比较困难。
镀镉层是最难扩散的,镀镉时产生的氢,最初停留在镀层中和镀层下的金属表层,很难向外扩散,去氢特别困难。
经过一段时间后,氢扩散到金属内部,特别是进入金属内部缺陷处的氢,就很难扩散出来。
预防电镀氢脆断裂解决方案
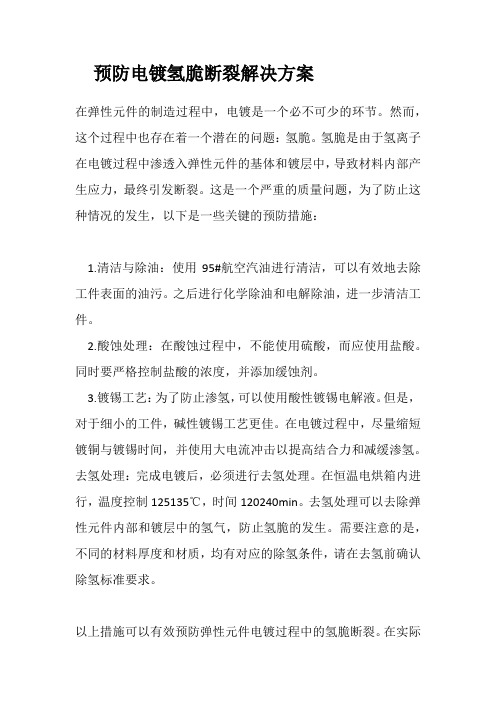
预防电镀氢脆断裂解决方案
在弹性元件的制造过程中,电镀是一个必不可少的环节。
然而,这个过程中也存在着一个潜在的问题:氢脆。
氢脆是由于氢离子在电镀过程中渗透入弹性元件的基体和镀层中,导致材料内部产生应力,最终引发断裂。
这是一个严重的质量问题,为了防止这种情况的发生,以下是一些关键的预防措施:
1.清洁与除油:使用95#航空汽油进行清洁,可以有效地去除工件表面的油污。
之后进行化学除油和电解除油,进一步清洁工件。
2.酸蚀处理:在酸蚀过程中,不能使用硫酸,而应使用盐酸。
同时要严格控制盐酸的浓度,并添加缓蚀剂。
3.镀锡工艺:为了防止渗氢,可以使用酸性镀锡电解液。
但是,对于细小的工件,碱性镀锡工艺更佳。
在电镀过程中,尽量缩短镀铜与镀锡时间,并使用大电流冲击以提高结合力和减缓渗氢。
去氢处理:完成电镀后,必须进行去氢处理。
在恒温电烘箱内进行,温度控制125135℃,时间120240min。
去氢处理可以去除弹性元件内部和镀层中的氢气,防止氢脆的发生。
需要注意的是,不同的材料厚度和材质,均有对应的除氢条件,请在去氢前确认除氢标准要求。
以上措施可以有效预防弹性元件电镀过程中的氢脆断裂。
在实际
操作中,还需要注意一些细节问题。
比如在电镀过程中,要避免暴露在酸性环境中;烘烤处理时要注意控制时间和温度,避免过高的温度导致镀层失效;避免使用过高的电荷或强酸和/或腐蚀性清洁剂;减少或消除弹簧渗氢;注意金属材料的硬度等。
总之,预防弹性元件电镀过程中的氢脆断裂需要从多个方面入手,严格控制工艺条件和操作流程。
只有这样,才能保证产品质量和可靠性。
金属氢脆原因及去氢脆方法
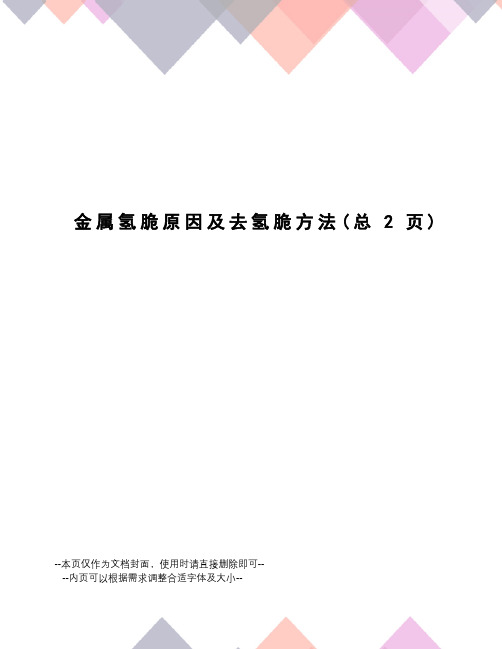
金属氢脆原因及去氢脆方法(总2页)--本页仅作为文档封面,使用时请直接删除即可----内页可以根据需求调整合适字体及大小--金属氢脆原因及去氢脆方法?在任何电镀溶液中,由于水分子的离解,总或多或少地存在一定数量的氢离子。
因此,电镀过程中,在阴极析出金属(主反应)的同时,伴有氢气的析出(副反应)。
析氢的影响是多方面的,其中最主要的是氢脆。
氢脆是表面处理中最严重的质量隐患之一,析氢严重的零件在使用过程中就可能断裂,造成严重的事故。
表面处理技术人员必须掌握避免和消除氢脆的技术,以使氢脆的影响降低到最低限度。
一、氢脆1氢脆现象氢脆通常表现为应力作用下的延迟断裂现象。
曾经出现过汽车弹簧、垫圈、螺钉、片簧等镀锌件,在装配之后数小时内陆续发生断裂,断裂比例达40%~50%。
某特种产品镀镉件在使用过程中曾出现过批量裂纹断裂,曾组织过全国性攻关,制订严格的去氢工艺。
另外,有一些氢脆并不表现为延迟断裂现象,例如:电镀挂具(钢丝、铜丝)由于经多次电镀和酸洗退镀,渗氢较严重,在使用中经常出现一折便发生脆断的现象;猎枪精锻用的芯棒,经多次镀铬之后,堕地断裂;有的淬火零件(内应力大)在酸洗时便产生裂纹。
这些零件渗氢严重,无需外加应力就产生裂纹,再也无法用去氢来恢复原有的韧性。
2?氢脆机理延迟断裂现象的产生是由于零件内部的氢向应力集中的部位扩散聚集,应力集中部位的金属缺陷多(原子点阵错位、空穴等)。
氢扩散到这些缺陷处,氢原子变成氢分子,产生巨大的压力,这个压力与材料内部的残留应力及材料受的外加应力,组成一个合力,当这合力超过材料的屈服强度,就会导致断裂发生。
氢脆既然与氢原子的扩散有关,扩散是需要时间的,扩散的速度与浓差梯度、温度和材料种类有关。
因此,氢脆通常表现为延迟断裂。
氢原子具有最小的原子半径,容易在钢、铜等金属中扩散,而在镉、锡、锌及其合金中氢的扩散比较困难。
镀镉层是最难扩散的,镀镉时产生的氢,最初停留在镀层中和镀层下的金属表层,很难向外扩散,去氢特别困难。
电镀中金属氢脆原因及解决方法

电镀中金属氢脆原因及解决方法电镀中的金属氢脆是指金属在电镀过程中吸收氢气后表现出的脆性现象。
这种现象会导致电镀金属的脆性增加,降低了金属的强度和韧性,从而使其容易发生开裂和断裂。
下面将详细介绍金属氢脆的原因和解决方法。
一、金属氢脆的原因:1.金属原料中的杂质:金属原料中的杂质,特别是含碳量较高的杂质,会促进金属吸氢。
2.电解液中的氢离子:电解液中的氢离子会随着电流和电压的作用,被还原为氢气,并通过金属的表面吸附到其中,从而导致金属吸氢。
3.电镀过程中的金属与溶液接触时间过长:如果金属与电镀液接触时间过长,会增加金属吸氢的机会。
二、金属氢脆的解决方法:1.提高金属材料的纯度:降低金属材料中的杂质含量可以有效地减少金属吸氢的机会。
在金属制备过程中,可以根据需要采取加热处理、熔融冶炼等方法来提高金属的纯度。
2.选择合适的电镀工艺:在电镀过程中,可以选择低氢化物电镀工艺,如钴合金电镀、镍合金电镀等,这些电镀工艺可以减少金属吸氢的机会。
3.控制电镀过程中的工艺参数:要注意控制电镀过程中的温度、电流、电压等参数。
在控制电流密度时,应选择合适的值以避免金属吸氢。
4.加强表面处理:在电镀之前,可以对金属材料进行一些适当的表面处理,如酸洗、研磨、抛光等,可以清除金属表面的氧化物和杂质,减少金属吸氢的机会。
5.合理控制电镀时间:尽量减少金属与电镀液接触的时间,可以有效地减少金属吸氢的机会。
以上是金属氢脆的原因及解决方法的一些建议,希望能对您有所帮助。
在实际应用中,除了以上措施外,还需要根据具体情况制定相应的解决方案,以获得更好的效果。
电镀产品的氢脆隐患及预防措施
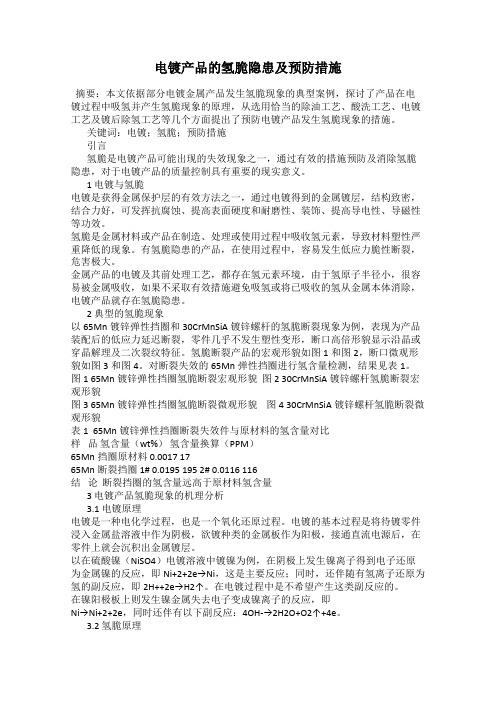
电镀产品的氢脆隐患及预防措施摘要:本文依据部分电镀金属产品发生氢脆现象的典型案例,探讨了产品在电镀过程中吸氢并产生氢脆现象的原理,从选用恰当的除油工艺、酸洗工艺、电镀工艺及镀后除氢工艺等几个方面提出了预防电镀产品发生氢脆现象的措施。
关键词:电镀;氢脆;预防措施引言氢脆是电镀产品可能出现的失效现象之一,通过有效的措施预防及消除氢脆隐患,对于电镀产品的质量控制具有重要的现实意义。
1 电镀与氢脆电镀是获得金属保护层的有效方法之一,通过电镀得到的金属镀层,结构致密,结合力好,可发挥抗腐蚀、提高表面硬度和耐磨性、装饰、提高导电性、导磁性等功效。
氢脆是金属材料或产品在制造、处理或使用过程中吸收氢元素,导致材料塑性严重降低的现象。
有氢脆隐患的产品,在使用过程中,容易发生低应力脆性断裂,危害极大。
金属产品的电镀及其前处理工艺,都存在氢元素环境,由于氢原子半径小,很容易被金属吸收,如果不采取有效措施避免吸氢或将已吸收的氢从金属本体消除,电镀产品就存在氢脆隐患。
2 典型的氢脆现象以65Mn镀锌弹性挡圈和30CrMnSiA镀锌螺杆的氢脆断裂现象为例,表现为产品装配后的低应力延迟断裂,零件几乎不发生塑性变形,断口高倍形貌显示沿晶或穿晶解理及二次裂纹特征。
氢脆断裂产品的宏观形貌如图1和图2,断口微观形貌如图3和图4。
对断裂失效的65Mn弹性挡圈进行氢含量检测,结果见表1。
图1 65Mn镀锌弹性挡圈氢脆断裂宏观形貌图2 30CrMnSiA镀锌螺杆氢脆断裂宏观形貌图3 65Mn镀锌弹性挡圈氢脆断裂微观形貌图4 30CrMnSiA镀锌螺杆氢脆断裂微观形貌表1 65Mn镀锌弹性挡圈断裂失效件与原材料的氢含量对比样品氢含量(wt%)氢含量换算(PPM)65Mn挡圈原材料 0.0017 1765Mn断裂挡圈 1# 0.0195 195 2# 0.0116 116结论断裂挡圈的氢含量远高于原材料氢含量3 电镀产品氢脆现象的机理分析3.1 电镀原理电镀是一种电化学过程,也是一个氧化还原过程。
电镀紧固件的氢脆和去氢处理

电镀紧固件的氢脆和去氢处理紧固件由于氢脆产生的脆性断裂一般发生得很突然,是无法预料的。
故这种失效形成造成的后果是很严重的。
尤其是在安全性能要求时,减少氢脆是很必要的,因此,电镀紧固件去除氢脆是一项很重要的工作。
1、减少电镀紧固件氢脆的产生a、加工硬度大于或等于320HV的电镀紧固件,在清洗过程前,应增加应力释放过程;在清洗过程中,应使用防腐蚀酸、碱性或机械方法进行。
浸入到防腐酸的时间尽可能地设计为最小持续时间。
B、硬度超过320HV的紧固件在进行冷拔、冷成形、机械加工、磨削后进行热处理工序时,则应符合ISO9587的规定。
c、应尽可能避免有意引人残余应力办法,如:螺栓、螺钉在热处理后碾制螺纹。
d、经热处理或冷作硬化的硬度超过385HV或性能等级12.9级及其以上的紧固件,不适宜采用酸洗处理应使用无酸的特殊方法,如:碱性清洗、喷砂等方法。
e、热处理或冷作硬化的硬度超过365HV的紧固件,应采用大阴极功率电镀溶液电镀工艺。
f、钢制紧固件为了进行电镀,表面应经特殊处理,即经最小浸入时间清洗后再进行电镀。
G、选择合适的镀层厚度,因为随着镀层厚度的增加,氢释放的难度也增加了。
2、对以下紧固件产品电镀后必须有进行去除氢脆处理a、性能等级大于或等于10.9%级的螺栓、螺钉和螺柱;b、硬度大于或等于372HV的弹性垫圈或弹性垫圈组合件;c、性能等级大于或等于12级的螺母;d、自攻螺钉、自攻自钻螺钉、自攻锁紧螺钉等表面淬硬类紧固件;e、抗拉强度大于或等于1000MPa或硬度大于或等于365HV金属弹性夹等紧固件。
3、去除氢脆的措施去除氢脆的措施实际上就是烘干过程,可以说是为了使氢脆减少到最小,在给定的温度下和规定的时间内,将零件加热的过程。
电镀后烘干过程就是将钢中的氢蒸发和不可逆收集而释放氢原子的过程,在GB/T5267.1附录A中给出了烘干过程的详细资料。
根据零件的产品品种、几何形状、材料、性能等级或硬度、清洗工艺、镀层种类及电镀工艺的不同,制定的烘干工艺也不同。
金属氢脆原因及去氢脆方法
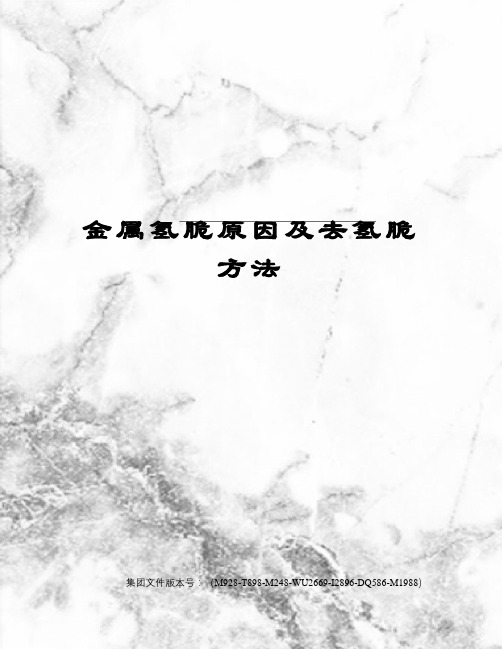
金属氢脆原因及去氢脆方法集团文件版本号:(M928-T898-M248-WU2669-I2896-DQ586-M1988)在任何电镀溶液中,由于水分子的离解,总或多或少地存在一定数量的氢离子。
因此,电镀过程中,在阴极析出金属(主反应)的同时,伴有氢气的析出(副反应)。
析氢的影响是多方面的,其中最主要的是氢脆。
氢脆是表面处理中最严重的质量隐患之一,析氢严重的零件在使用过程中就可能断裂,造成严重的事故。
表面处理技术人员必须掌握避免和消除氢脆的技术,以使氢脆的影响降低到最低限度。
一、氢脆1氢脆现象氢脆通常表现为应力作用下的延迟断裂现象。
曾经出现过汽车弹簧、垫圈、螺钉、片簧等镀锌件,在装配之后数小时内陆续发生断裂,断裂比例达40%~50%。
某特种产品镀镉件在使用过程中曾出现过批量裂纹断裂,曾组织过全国性攻关,制订严格的去氢工艺。
另外,有一些氢脆并不表现为延迟断裂现象,例如:电镀挂具(钢丝、铜丝)由于经多次电镀和酸洗退镀,渗氢较严重,在使用中经常出现一折便发生脆断的现象;猎枪精锻用的芯棒,经多次镀铬之后,堕地断裂;有的淬火零件(内应力大)在酸洗时便产生裂纹。
这些零件渗氢严重,无需外加应力就产生裂纹,再也无法用去氢来恢复原有的韧性。
2 氢脆机理延迟断裂现象的产生是由于零件内部的氢向应力集中的部位扩散聚集,应力集中部位的金属缺陷多(原子点阵错位、空穴等)。
氢扩散到这些缺陷处,氢原子变成氢分子,产生巨大的压力,这个压力与材料内部的残留应力及材料受的外加应力,组成一个合力,当这合力超过材料的屈服强度,就会导致断裂发生。
氢脆既然与氢原子的扩散有关,扩散是需要时间的,扩散的速度与浓差梯度、温度和材料种类有关。
因此,氢脆通常表现为延迟断裂。
氢原子具有最小的原子半径,容易在钢、铜等金属中扩散,而在镉、锡、锌及其合金中氢的扩散比较困难。
镀镉层是最难扩散的,镀镉时产生的氢,最初停留在镀层中和镀层下的金属表层,很难向外扩散,去氢特别困难。
氢脆的原理与预防
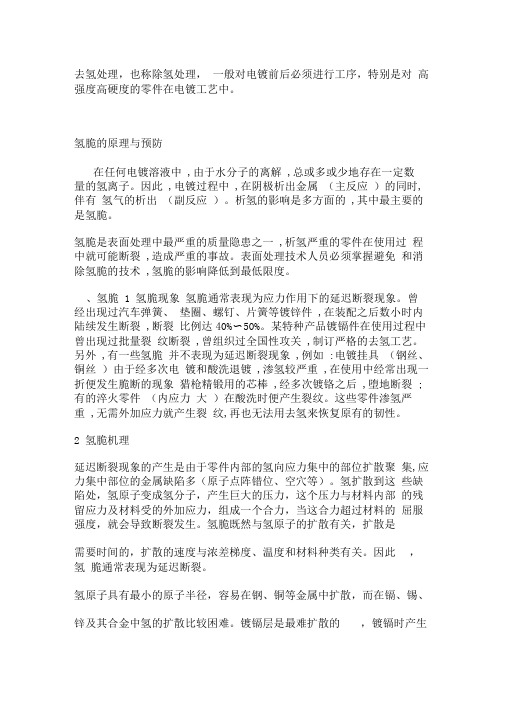
去氢处理,也称除氢处理,一般对电镀前后必须进行工序,特别是对高强度高硬度的零件在电镀工艺中。
氢脆的原理与预防在任何电镀溶液中 ,由于水分子的离解 ,总或多或少地存在一定数量的氢离子。
因此 ,电镀过程中 ,在阴极析出金属(主反应)的同时,伴有氢气的析出(副反应)。
析氢的影响是多方面的 ,其中最主要的是氢脆。
氢脆是表面处理中最严重的质量隐患之一 ,析氢严重的零件在使用过程中就可能断裂 ,造成严重的事故。
表面处理技术人员必须掌握避免和消除氢脆的技术 ,氢脆的影响降低到最低限度。
、氢脆 1 氢脆现象氢脆通常表现为应力作用下的延迟断裂现象。
曾经出现过汽车弹簧、垫圈、螺钉、片簧等镀锌件 ,在装配之后数小时内陆续发生断裂 ,断裂比例达40%〜50%。
某特种产品镀镉件在使用过程中曾出现过批量裂纹断裂 ,曾组织过全国性攻关 ,制订严格的去氢工艺。
另外 ,有一些氢脆并不表现为延迟断裂现象 ,例如 :电镀挂具(钢丝、铜丝)由于经多次电镀和酸洗退镀 ,渗氢较严重 ,在使用中经常出现一折便发生脆断的现象猎枪精锻用的芯棒 ,经多次镀铬之后 ,堕地断裂 ;有的淬火零件(内应力大)在酸洗时便产生裂纹。
这些零件渗氢严重 ,无需外加应力就产生裂纹,再也无法用去氢来恢复原有的韧性。
2 氢脆机理延迟断裂现象的产生是由于零件内部的氢向应力集中的部位扩散聚集,应力集中部位的金属缺陷多(原子点阵错位、空穴等)。
氢扩散到这些缺陷处,氢原子变成氢分子,产生巨大的压力,这个压力与材料内部的残留应力及材料受的外加应力,组成一个合力,当这合力超过材料的屈服强度,就会导致断裂发生。
氢脆既然与氢原子的扩散有关,扩散是需要时间的,扩散的速度与浓差梯度、温度和材料种类有关。
因此,氢脆通常表现为延迟断裂。
氢原子具有最小的原子半径,容易在钢、铜等金属中扩散,而在镉、锡、锌及其合金中氢的扩散比较困难。
镀镉层是最难扩散的,镀镉时产生的氢,最初停留在镀层中和镀层下的金属表层,很难向外扩散,去氢特别困难。
表面处理氢脆的控制
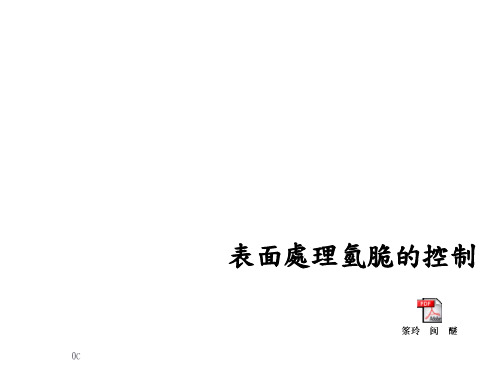
5
四、除了鋼材硬度外,還應綜合考慮以下幾點:
(1)零件的使用安全係數:安全重要性大的零件,應加強去氫。 (2)零件的幾何形狀:帶有容易產生應力集中的缺口,小R等的零件應加 強去氫。 (3)零件的截面積:細小的彈簧鋼絲、較薄的片簧極易被氫飽和,應加強 去氫。 (4)零件的滲氫程度:在表面處理中產生氫多、處理時間長的零件,應加 強去氫。 (5)鍍層種類:如鍍鎘層會嚴重阻擋氫向外擴散,所以要加強去氫。 (6)零件使用中的受力性質:當零件受到高的張應力時應加強去,只受 壓應力時不會產生氫脆。 (7)零件的表面加工狀態:對冷彎、拉伸、冷紮彎形、淬火、焊接等內部 殘留應力大的零件,不僅鍍後要加強去氫,而且鍍前要去應力。 (8)零件的歷史情況:對過去生產中發生過氫脆的零件應特別加以注意, 並作好相關記錄。
3
3、鍍前去應力和鍍後去氫以消除氫脆隱患: 若零件經淬火、焊接等工序後內部殘留應力較大,鍍前應進行回火處理減 少發生嚴重滲氫的隱患。 對電鍍過程中滲氫較多的零件原則上應儘快去氫,因為鍍層中的氫和表層 基體金屬中的氫在向鋼基體內部擴散,其數量隨時間的延長而增加。新的 國際標準草案規定“最好在鍍後1h內,但不遲於3h,進行去氫處理”。 國內也有相應的標準,對電鍍鋅前、後的去氫處理作了規定。電鍍後去氫 處理工藝廣泛採用加熱烘烤,常用的烘烤溫度為150~300°C、保溫2~24 h。具體的處理溫度和時間應根據零件大小、強度、鍍層性質和電鍍時間 的長短而定。去氫處理常在烘箱內進行。鍍鋅零件的去氫處理溫度為110 ~220°C,溫度控制的高低應根椐基體材料而定。對於彈性材料、0.5m m以下的薄壁件及機械強度要求較高的鋼鐵零件,鍍鋅後必須進行去氫處 理。為了防止“鎘脆”,鍍鎘零件的去氫處理溫度不能太高,通常為180 ~200°C。
工艺氢脆原因机理及常见控制手段

工艺丨氢脆原因机理及常见控制手段一、氢脆产生的机理因热处理、机加工、电镀、电焊、酸洗、磷化、材料腐蚀等因素导致氢原子渗入钢和其他金属如铝、钛合金中,由于在每一个铁离子的立方晶格中只能容纳一个氢原子,所以它虽自由的移动和扩散,但不可能有二个氢原子相遇形成氢分子,但被吸收的氢原子具有向应力集中的部位扩散和移动的能力,这时,如果在应力集中部位由于位错而产生晶格缺陷时,氢原子进入晶格间隙,相互汇合形成氢分子,从而致使钢的组织破坏,形成钢的氢脆。
而由于氢原子向应力集中的部位扩散和积聚需要时间,这就是为何氢脆主要的表现特征为延迟断裂。
二、造成产品氢脆的几大因素1、原材料钢的强度越高越容易导致氢脆。
高强度钢的韧性会随着其强度的增高而下降,因此这种材料对缺口、氢脆以及应力腐蚀很敏感,尤其是氢脆性会使这些材料在其设计载荷能力以下发生破坏。
也就是说材料在渗氢的情况下,在低于其屈服强度的应力条件下,容易发生早期脆性断裂,而且材料强度级别越高,渗氢程度越严重,所受应力越大,氢脆风险性也越大。
美国对氢脆敏感的SAE4340钢做过实验,当其抗拉强度低于1250MPa时,吸收了1~10PPM的氢而不会发生氢脆,但经过热处理后,强度达到1760MPa~1920MPa时,仅吸收了0.03~0.05PPM 的氢,就会发生显著的氢脆断裂。
而采用抗拉强度小于780MPa的普通钢,即使吸收了10~30PPM的氢,也未发现有氢脆断裂现象。
2、机械加工在电镀前的加工过程中,如轧制成型、机械加工、钻孔、磨削中,由于润滑剂的选用不当造成分解会导致氢渗入金属中。
硬化热处理后经机械加工、磨削、冷成型冷矫直处理的制件对氢脆损伤特别敏感。
同时如在冷轧、冲裁、压弯、磨削等机加工过程中使得零件表面产生加工裂纹,会导致零件裂纹处渗氢后很难经烘烤将氢析出。
同时裂纹处又是应力集中区,很容易造成零件在裂纹处延时断裂。
下图所示为一款65Mn材料的组合螺母,因表面有严重的机加工裂纹,导致在电镀后采用GBT/3098.17进行氢脆测试过程中发生氢脆断裂。