物料管理和生产计划基础知识
生产计划与物料控制224页

编制日期: 年 月 日
说明:1、计划周期:三个月(季)为一期,每月计划一次; 2、计划安排量通过产销协调会决定。
13
定期产销协调会议制度
资货状况 及客户要求。
生产管理部门
1、生产计划及生产异动 状况; 2、产能负荷状况; 3、物料需求及进料状况。
其他部门
26
途程计划表
27
负荷计划
负荷计划又称为工时计划(以工时 作为负荷与能力的测定基准),在生产计 划里只是基本的机能。此计划为追求工作 量(负荷)与能力(人、机)的平衡而拟 定。
为使生产计划尤其是日程计划切实 可行,有一可靠的负荷计划是必不可少的。
28
负荷计划的目的和标准
一、目的 1、负荷、能力的实态把握; 2、确保生产量与交期的对策与警报; 3、维持生产的适当作业率。 二、计划标准 1、基准负荷
(200) ②
丙
0.25(H) 0.25 ×200=50(H)
说明:*甲、乙、丙表示各制程使用的加工机械
基准能力:
*机械配置:甲3台、乙1台、丙2台
甲机械=3×180=540(H)
*机械能力(单机)
乙机械=1×180=180(H)
=25(天) ×8(小时/天) ×90%=180(小时) 丙机械=2×180=360(H)
1
机 Machine
料 Material
人 Man
5M1E
法 Method
环境 Environment
测 Measure
2
生产的型态
一、预估生产型 为因应一个由不特定顾客所构成的
市场需求,对产品的式样、品质、规格等 先做预估,再从事生产的型态。如食品、 服装、汽车、家电等行业。
怎样做好生产计划与物料控制

怎样做好生产计划与物料控制1. 充分了解需求:在制定生产计划之前,需要充分了解市场的需求。
这包括了解销售预测,以及客户的实际订单情况。
只有了解了市场的需求,才能制定出合理的生产计划。
2. 确保准确的物料清单:在做生产计划之前,需要确保有一个准确的物料清单。
这包括每种产品所需要的原材料、零部件以及所需的数量。
只有准确地掌握了物料清单,才能做出合理的生产计划。
3. 制定合理的生产计划:根据市场需求和物料情况,制定一个合理的生产计划。
这个生产计划应该考虑到生产设备的利用率、人力资源的情况以及生产周期等因素。
4. 建立物料控制系统:建立一个完善的物料控制系统,确保每一种物料的库存都能得到有效的控制。
这包括设定合理的物料采购计划,做好物料的入库管理,以及及时的补充物料等措施。
5. 使用信息化系统:在今天的生产环境中,信息化系统是非常重要的。
通过使用ERP等信息化系统,可以更加有效地管理生产计划和物料控制。
总的来说,做好生产计划与物料控制需要综合考虑市场需求、物料情况、生产设备和人力资源等因素。
只有在这些因素都得到充分考虑的情况下,才能制定出一个合理的生产计划和物料控制措施。
同时,建立有效的信息化系统也是非常重要的。
通过这些措施,企业可以提高生产效率,降低成本,从而提高竞争力。
在今天的高度竞争的市场环境中,企业要想在生产领域取得成功,必须要做好生产计划与物料控制。
这不仅仅是为了确保生产过程的顺利进行,更是为了提高企业的竞争力、降低成本、提高生产效率和客户满意度。
在制定生产计划和进行物料控制时,企业可以采取一些关键的策略和措施,以确保生产流程的顺畅和高效。
首先,要保持良好的供应链管理。
一个健康的供应链对于企业的生产计划和物料控制至关重要。
企业需要与供应商建立良好的关系,确保供应商能够提供高质量的原材料和零部件,并且按时交付。
定期审查和评估供应商的绩效是非常必要的,以便及时解决潜在的问题,保持供应链的顺畅。
其次,要进行精细化的生产计划。
pmc生产计划与物料控制

pmc生产计划与物料控制PMC生产计划与物料控制生产计划与物料控制(Production Planning and Material Control,简称PMC)是现代企业生产管理的重要手段和方法之一,它通过有效的计划与物料控制,帮助企业合理组织生产过程,最大化地发挥生产设备的效益,提高生产效率和制造质量,从而实现企业的利润最大化。
一、生产计划生产计划是PMC的核心组成部分,它直接影响到生产的进度和质量。
生产计划是指在一定时间内,根据生产目标和生产能力,合理安排生产任务的计划,包括生产数量、生产时间、生产方式及物料需求等内容。
生产计划的编制应按照以下步骤进行:1、生产目标的确定生产目标要与市场需求紧密结合,根据市场需求合理分配生产计划中各个品种的产量。
2、产能分析通过对生产资源的分析和评估,考虑设备的使用率、工艺流程、作业时间等因素,确定生产能力。
3、计划制定结合生产目标和产能分析,确定生产计划中的各项详细内容。
包括指定生产时间、安排生产方式、制定物料需求计划、确定生产过程控制计划等。
4、计划调整随着市场需求的变化,生产计划也要不断调整。
调整生产计划时必须考虑到生产效益、企业形象和市场需求等的影响。
二、物料控制物料控制是很重要的一环,它对于确保生产计划的顺畅实施有着至关重要的作用。
物料控制的主要任务是根据生产计划,精确地控制和管理各物料在生产过程中的流动和使用,以确保生产过程的顺利进行,从而保障生产的正常运作。
物料控制主要包括以下内容:1、物料需求计划(MRP)物料需求计划是根据生产计划,制定每个物料的采购计划和生产计划,保证这些物料在所需时间内到达工厂,并保持合理的库存水平。
2、进料检验通过对进厂物料的检验,可以确保物料的质量符合要求。
检验的结果可以对进料的订货单位进行评估和管理,从而使订货单位更加重视物料的质量和供货能力。
3、仓库管理仓库管理包括物料的分类、盘点、入库、出库、移库、报废等工作,它直接影响到生产计划和物料管理的效率和质量。
pmc生产计划与物料控制

pmc生产计划与物料控制PMC生产计划与物料控制是企业生产管理中至关重要的环节。
它涉及到对生产计划的制定和调整,以及对物料的采购、管理和控制等方面的工作。
本文将从PMC生产计划和物料控制两个方面进行详细介绍。
一、PMC生产计划1.1 生产计划的概念生产计划是企业根据市场需求和资源情况,合理安排和调度生产活动的工作。
它涉及到生产量、生产时间、生产顺序等方面的决策,是企业实现生产目标的重要手段。
1.2 生产计划的编制流程生产计划的编制一般包括以下几个环节:明确生产目标和任务、制定生产计划方案、安排生产资源、编制生产计划和下达任务单、调整和监控生产计划。
1.3 生产计划的内容和要求生产计划的内容包括产品的生产数量、生产时间、生产顺序以及所需的资源和工艺等。
生产计划要求合理、稳定和可操作,确保生产活动的高效运行。
二、物料控制2.1 物料控制的概念物料控制是指对企业物料采购、存储和使用过程进行有效管理和控制的工作。
它涉及到物料需求的确定、采购计划的制定、库存管理和物料使用的控制等方面。
2.2 物料控制的方法和手段物料控制的方法和手段主要包括物料需求计划、物料采购控制、库存管理和物料使用控制等。
通过科学合理的控制手段,确保物料的供应和使用的平衡,防止过剩和缺货等问题的发生。
2.3 物料控制的目标和要求物料控制的目标是实现物料的合理需求和有效供应,确保生产活动的顺利进行。
物料控制要求准确性、及时性和稳定性,提高企业的生产效率和经济效益。
三、PMC生产计划与物料控制的关系3.1 生产计划与物料控制的联系生产计划与物料控制是密切相关的两个环节。
合理的生产计划需要基于准确的物料需求计划,而物料控制的有效性也依赖于生产计划的准确性和稳定性。
3.2 生产计划与物料控制的整合生产计划与物料控制应当进行有效整合,形成一个有机的管理体系。
通过信息化技术的支持,实现生产计划和物料控制的高效协同,提升企业生产管理的水平。
四、总结PMC生产计划与物料控制是企业生产管理中的关键环节。
简述生产现场管理的基本内容

简述生产现场管理的基本内容
生产现场管理是指对企业生产过程中的各个环节进行有效管理和控制,以确保生产效率、质量和安全。
它涉及到多个方面的内容,包括生产计划、生产组织、物料管理、质量管理、设备维护等。
下面将对这些内容进行简要描述。
1. 生产计划
生产计划是生产现场管理的基础,它确定了生产的时间、数量和所需资源。
生产计划要充分考虑市场需求、产品特性以及企业资源情况,合理安排生产任务,确保生产满足需求且高效进行。
2. 生产组织
生产组织是指对生产过程进行合理组织和调度,使生产能够按照计划有序进行。
它包括生产线布局、工序安排、人员管理等。
合理的生产组织可以提高生产效率,减少生产成本。
3. 物料管理
物料管理是指对生产所需的原材料、零部件和成品进行合理的供应和管理。
它包括物料采购、入库管理、库存控制等。
物料管理的目标是保证物料的充足性和及时性,避免因物料不足或过多而影响生产。
4. 质量管理
质量管理是生产现场管理的重要内容,它涉及到产品的质量控制和
质量改进。
质量管理包括质量检验、质量标准制定、不良品处理等。
通过质量管理,可以确保产品符合质量要求,提高客户满意度。
5. 设备维护
设备维护是保证生产设备正常运行的重要环节。
它包括设备的日常维护、故障排除和设备更新等。
良好的设备维护可以提高设备的可靠性和使用寿命,减少生产中断和质量问题。
生产现场管理的基本内容包括生产计划、生产组织、物料管理、质量管理和设备维护等方面。
通过对这些内容的有效管理,可以提高生产效率、质量和安全,实现企业的可持续发展。
精益化生产计划排程和物料控制管理(精华版)

案例:2013年年度预测
2013年预测销售订单分析
年度
2012
2013
年度
2012
2013
平张 彩盒 总额
110% 100% 90% 80% 70% 60% 50% 40% 30% 20% 10%
0%
2.77 4.06 6.93
2.58 6.5 9.08
平张 彩盒
58.59%
71.59%
39.97% 2012年
企业保留最小生产单元; 超出部份借用外部资源完成
成
本 外包策略
要求企业资源无限大 属于刚性计划
配合需求 策略
均衡化策略 平稳化策略
13
准确把握客户需求、合理 配置公司资源;整合外部 资源,提升内部生产能力
库存
视订单持续稳定, 有库存产生
13
1.4 生产计划的制定
1.4.3 生产计划的层次
公司发展战略、长远发展规划
精益化生产计划排程和 物料控制管理
1
1
案例:
二战期间,美国刚开始保持中立态度,后期被逼仓促加入战争,因前 期没有做好准备,故临时召集一些高端人才成立了“军统局”。
飞机 大炮 军队
订单 二战
固定资产
军统局
计划
前线-日本
生 产
前线-德国
按时 交货
二战 胜利
2
采购
后勤供给 ……
2
名人名言
●博观而约取, 厚积而薄发
经过与财务部门多次沟通,情况有所好转,正在系统解决。
案例分析:做为交货统筹部门,必须对影响的每 一个环节进行改善或推动改善 41
41
2.2 评审周期标准化
2.2.1 缩短评审时间
生产计划与物料控制PPT课件

合理安排运输方式、优化运输路线等 方式降低运输成本。
降低仓储成本
合理规划仓储空间、提高仓储效率等 方式降低仓储成本。
05 生产计划与物料控制协同
生产与采购的协同
采购计划与生产计划相匹配
01
确保采购的原材料、零部件等能够满足生产需求,避免生产中
断。
供应商管理
02
建立和维护与供应商的良好关系,确保供应商能够按时、按质、
建立完善的物料需求预测体系
通过收集历史数据和市场信息,建立完善的物料需求预测体系,提高预测准确性。
引入大数据分析技术
利用大数据分析技术,对市场数据和物料需求进行深度挖掘和分析,提高预测精度。
定期评估和调整预测模型
定期评估预测模型的准确性和适用性,及时调整和优化模型,提高预测准确性。
优化库存管理策略
THANKS FOR WATCHING
感谢您的观看
实施零库存管理
通过精细化的生产和物料控制,逐步实现零库存管理,降 低库存成本。
引入先进的库存管理技术
采用先进的库存管理技术,如实时库存监控、智能补货等, 提高库存周转率。
建立合理的库存管理制度
建立完善的库存管理制度,明确各部门的职责和操作规范, 确保库存管理的有效性和准确性。
提高生产计划与物料控制的信息化水平
详细描述
根据销售预测、生产计划、库存状况等因素,运用统计方法或预测模型,对未 来一段时间内的物料需求量进行预测,为制定采购计划提供数据支持。
物料采购计划制定
总结词
根据物料需求预测结果,制定相应的采购计划。
详细描述
根据物料需求预测结果,综合考虑库存状况、供应商能力、运输等因素,制定合 理的采购计划,包括采购品种、数量、时间、供应商选择等。
生产计划与物料管理

生产计划与物料管理概述生产计划与物料管理是制造企业中非常重要的一个环节,它涉及到生产活动的组织和调度,以及物料的采购、仓储和配送等方面。
一个高效的生产计划和物料管理体系能够确保企业生产活动的顺利进行,并减少生产成本和库存压力。
生产计划生产计划的定义和目的生产计划是指根据市场需求和企业资源情况,合理安排生产任务和生产资源,以确保生产活动能够按时完成并达到预期目标的一项管理活动。
它的主要目的是实现生产过程的高效稳定,提高生产效率和产品质量。
生产计划的步骤1.市场需求分析:根据市场的需求情况确定生产计划的基本目标和指标,包括生产数量、生产周期等。
2.生产资源评估:评估企业现有的生产资源情况,包括人力、设备、原材料等,以确定生产计划的可行性。
3.生产任务划分:将整体的生产计划划分为不同的生产任务,按照合理的逻辑和顺序进行排列,确保各个任务之间的衔接和协调。
4.生产进度管理:对每个生产任务进行进度管理,及时掌握生产进展情况,防止出现生产延误和资源浪费的情况。
5.生产计划调整:根据实际情况对生产计划进行调整,包括增减生产任务、调整生产顺序等,以适应市场和企业资源的变化。
生产计划的要点1.合理安排生产资源:根据生产计划的目标和实际情况,合理分配和调度生产资源,避免资源过度闲置或过度利用。
2.紧密协调各环节:生产计划需要协调不同环节的生产活动,确保各环节之间的衔接和协作,提高整体生产效率。
3.灵活应对变化:生产计划需要具备灵活性,能够及时应对市场需求和企业资源变化,调整生产计划以实现最佳效果。
物料管理物料管理的定义和目的物料管理是指对企业所需物料进行统一的采购、仓储和配送管理的一项重要工作。
通过物料管理,企业能够实现物料采购的合理化、仓储的有效控制和配送的高效运作,以保证生产活动的顺利进行。
物料管理的流程1.物料需求计划:根据生产计划和市场需求,确定所需要的物料种类、数量和采购时间等信息,编制物料需求计划。
2.供应商评估和选择:评估和选择合适的供应商,与供应商建立良好的合作关系,确保物料的质量和供应的及时性。
pmc生产计划与物料控制

pmc生产计划与物料控制PMC生产计划与物料控制随着现代企业生产规模的不断扩大和技术的不断发展,PMC (Product Material Control)生产计划与物料控制在企业生产经营中的作用愈发重要。
本文将从PMC生产计划与物料控制的定义、目的、流程和关键要素等方面进行探讨,以期为读者对该话题有一个全面的理解。
1. 定义:PMC生产计划与物料控制是指企业通过合理的计划和控制手段,对生产过程中的物料进行全过程的控制和管理,从而实现生产计划的准确执行,并确保物料的合理利用和供给。
2. 目的:PMC生产计划与物料控制的主要目的是提高企业生产计划的满足度和物料利用率,从而降低生产成本,提高生产效率和产品质量。
3. 流程:(1) 生产计划制定:根据企业的生产能力、市场需求和资源情况等因素,制定合理的生产计划。
生产计划应包括生产数量、生产周期和交货期等重要信息。
(2) 物料需求计划:根据生产计划和物料需求情况,制定物料需求计划。
物料需求计划应包括物料种类、数量和采购时间等信息。
(3) 物料采购:根据物料需求计划,进行物料采购工作。
在采购过程中,应考虑物料价格、供应商信誉度和交货时间等因素。
(4) 物料接收和入库:对采购的物料进行检验和验收,合格后及时入库。
入库时应按照物料种类和质量要求进行分类管理。
(5) 物料发放和使用:根据生产计划和物料需求,及时将物料发放给相应的生产部门。
在使用过程中,应严格遵守使用规范,避免物料的浪费和损坏。
(6) 物料库存管理:对物料库存进行及时、准确的记录和统计,实时监控库存情况。
根据库存情况,及时调整物料采购计划和生产计划,避免库存过多或过少。
(7) 物料退货和报废:对于质量不合格的物料,应及时退货给供应商。
对于过期或损坏的物料,应按照公司制度进行报废处理。
4. 关键要素:(1) 生产计划的准确性:生产计划是整个PMC生产计划与物料控制的基础,只有准确的生产计划才能实现生产计划的准确执行。
生产计划与物料控制主要工作内容
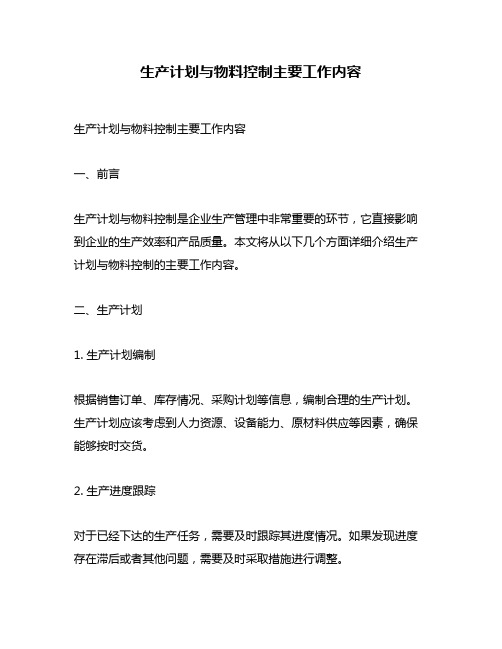
生产计划与物料控制主要工作内容生产计划与物料控制主要工作内容一、前言生产计划与物料控制是企业生产管理中非常重要的环节,它直接影响到企业的生产效率和产品质量。
本文将从以下几个方面详细介绍生产计划与物料控制的主要工作内容。
二、生产计划1. 生产计划编制根据销售订单、库存情况、采购计划等信息,编制合理的生产计划。
生产计划应该考虑到人力资源、设备能力、原材料供应等因素,确保能够按时交货。
2. 生产进度跟踪对于已经下达的生产任务,需要及时跟踪其进度情况。
如果发现进度存在滞后或者其他问题,需要及时采取措施进行调整。
3. 交期跟踪在整个生产过程中,需要不断地关注产品交期是否能够按照客户要求完成。
如果发现有延误的情况,需要及时通知客户并协商解决方案。
三、物料控制1. 物料需求计划根据销售订单和生产计划等信息,编制合理的物料需求计划。
物料需求计划应该考虑到库存情况、供应商能力等因素,确保原材料的及时供应。
2. 采购计划根据物料需求计划,编制合理的采购计划。
采购计划应该考虑到供应商能力、价格等因素,确保能够按时采购到所需原材料。
3. 供应商评估对于新的供应商,需要进行评估并确定其质量、交货能力等指标。
对于已有的供应商,需要进行定期评估并及时处理问题。
4. 库存管理对于已经采购到的原材料和半成品,需要进行合理的库存管理。
库存管理包括库存监控、库龄控制、安全库存设置等方面。
四、总结生产计划与物料控制是企业生产管理中非常重要的环节。
通过合理的生产计划和物料控制,可以确保企业生产效率和产品质量。
在实际工作中,需要不断地完善和优化相关工作流程,并及时处理出现的问题。
生产计划与物料控制管理流程
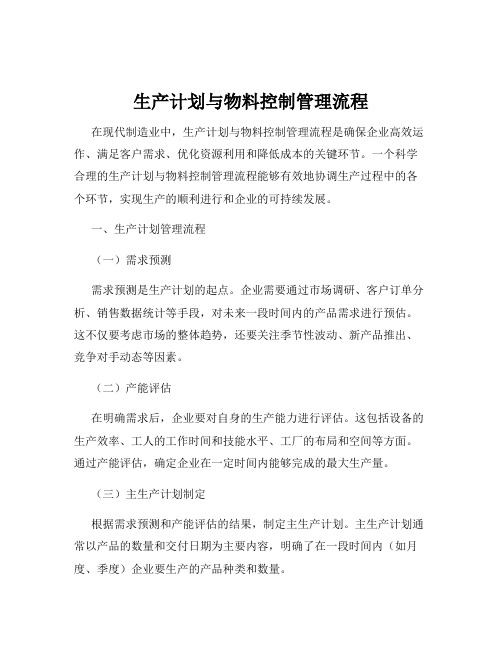
生产计划与物料控制管理流程在现代制造业中,生产计划与物料控制管理流程是确保企业高效运作、满足客户需求、优化资源利用和降低成本的关键环节。
一个科学合理的生产计划与物料控制管理流程能够有效地协调生产过程中的各个环节,实现生产的顺利进行和企业的可持续发展。
一、生产计划管理流程(一)需求预测需求预测是生产计划的起点。
企业需要通过市场调研、客户订单分析、销售数据统计等手段,对未来一段时间内的产品需求进行预估。
这不仅要考虑市场的整体趋势,还要关注季节性波动、新产品推出、竞争对手动态等因素。
(二)产能评估在明确需求后,企业要对自身的生产能力进行评估。
这包括设备的生产效率、工人的工作时间和技能水平、工厂的布局和空间等方面。
通过产能评估,确定企业在一定时间内能够完成的最大生产量。
(三)主生产计划制定根据需求预测和产能评估的结果,制定主生产计划。
主生产计划通常以产品的数量和交付日期为主要内容,明确了在一段时间内(如月度、季度)企业要生产的产品种类和数量。
(四)物料需求计划主生产计划确定后,需要制定物料需求计划。
物料需求计划是根据产品的结构清单(BOM)和主生产计划,计算出所需各种原材料、零部件的数量和时间。
(五)生产排程根据物料需求计划,进行生产排程。
生产排程要考虑到设备的可用性、工人的排班、工序的先后顺序等因素,以确定每个产品在各个生产环节的具体生产时间和顺序。
(六)生产进度跟踪在生产过程中,要对生产进度进行实时跟踪。
通过信息化系统、现场巡查等方式,及时了解生产的实际情况与计划的偏差,并采取相应的调整措施。
(七)计划调整当出现市场需求变化、原材料供应短缺、设备故障等意外情况时,需要对生产计划进行及时调整。
调整要综合考虑各种因素,以最小化对生产的影响。
二、物料控制管理流程(一)物料采购计划根据物料需求计划,制定物料采购计划。
采购计划要明确采购的物料种类、数量、供应商、交货时间等。
(二)供应商管理选择合适的供应商是物料控制的重要环节。
生产计划与物料控制思维导图

生产计划与物料控制制订排程关键的几个要素制订排程的五大要素人人力负荷=(标准工时×生产数量)/实有工时机设备负荷=(工序标准工时×生产数量)/(实有工时×实际可动率)物准时到/备料率=准时到/备料批次/总到/备料批次法生产效率=实际产出工时/实际投入工时环环境因素,工作环境,如天气等因素而对生产效率、工艺品质的影响波动。
时间跨度短期周生产计划在满足五大编排要素的前提下,生产部门日常生产执行的标准。
通常情况下,我们精确到日生产计划。
中期月生产计划每月进行整体分析、指导各生产要素的前期准备与相应调整(生产、物料、销售)长期年生产计划结合现有订单预测状况,动态体现各生产要素的负荷状况,以指导订单的评估、物料和生产的准备、以及订单的需求。
计划需具备的特点准确性按照计划准确的达成后,需满足当初设计的目的(如标准工时BOM.存货周转、产量等)稳定性第一周的生产计划不能随意更改、变动,要保持计划的稳定性与权威性连续性前后工序间、上下周计划间,时间与数量都必须保持连续性,不能断节或自相矛盾可执行性生产部门的资源(五大要素)可以满足计划的执行异常防范性也即弹性准备,预防、避免生产过程中 的异常发生而致使计划的延误或反复调整10 大浪费过量生产原因与需要相比,过早的,过多的生产影响在制品积压,存放场地增加使先入先出作业困难增加周转箱、工位器具等设备成本库存增加资金积压潜在的质量危险库存原因库存量过大,资金积压越多影响在大量购买原材料和零部件,造成积压,占用很多的流动资金,增加了防护、保管的费用设备布局不合理,前后工序不能形成“一个流”生产和搬运,造成场地占用,先入先出困难共享设备,加工品种多,换型时间长,只好采用批量生产能力不足被掩盖搬运原因物料的临时放置、堆积、移动、倒装、整理 以及零星搬运等影响物料移动所需空间的浪费人工、工具的占用时间的浪费推车的移动改进改进工序设计!优化布局!! 改进搬运方式检验和返工原因第一次不能把事情做对而带来的额外工作和浪费影响检验返工重复点数校正过程不当原因参数选择不当,产生多余的加工或者过分精确的加工影响机器的加工动作移动行程过长,造成多余的作业时间机器速度选择不当,引起加工时间延长、生产资源如电、水等浪费因材质或工艺设计不合理,产生附加工序,造成加工、管理工时增加加工精度/加工余量选择过高或不足等待原因因断料、作业不平衡、计划不当、设备故障等导致人、机处于等待状态影响生产线机种切换工位间由于不平衡造成等待的浪费机器设备故障导致等待的浪费因为缺料等导致人和设备等待的浪费生产计划安排不平衡导致人机闲置断料措施要求供应商按时按量提供供应商能否快速、准确地接收我们的订单供应商能否将我们的订单快速、准确地布产多余动作原因对工序进展无推动作用/不创造附加简直的现场作业动作。
生产计划与物料控制
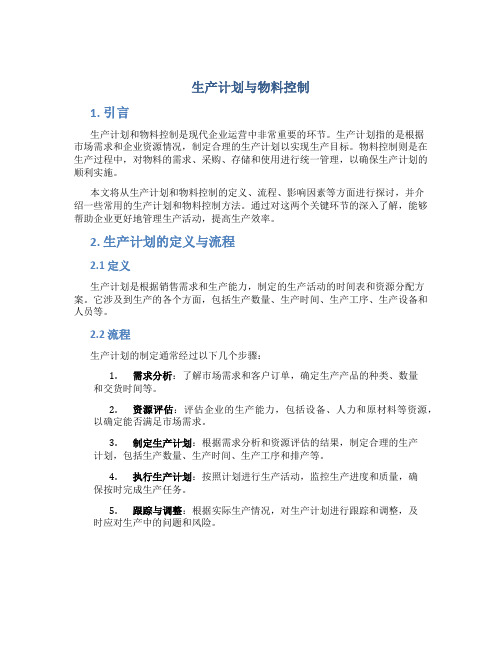
生产计划与物料控制1. 引言生产计划和物料控制是现代企业运营中非常重要的环节。
生产计划指的是根据市场需求和企业资源情况,制定合理的生产计划以实现生产目标。
物料控制则是在生产过程中,对物料的需求、采购、存储和使用进行统一管理,以确保生产计划的顺利实施。
本文将从生产计划和物料控制的定义、流程、影响因素等方面进行探讨,并介绍一些常用的生产计划和物料控制方法。
通过对这两个关键环节的深入了解,能够帮助企业更好地管理生产活动,提高生产效率。
2. 生产计划的定义与流程2.1 定义生产计划是根据销售需求和生产能力,制定的生产活动的时间表和资源分配方案。
它涉及到生产的各个方面,包括生产数量、生产时间、生产工序、生产设备和人员等。
2.2 流程生产计划的制定通常经过以下几个步骤:1.需求分析:了解市场需求和客户订单,确定生产产品的种类、数量和交货时间等。
2.资源评估:评估企业的生产能力,包括设备、人力和原材料等资源,以确定能否满足市场需求。
3.制定生产计划:根据需求分析和资源评估的结果,制定合理的生产计划,包括生产数量、生产时间、生产工序和排产等。
4.执行生产计划:按照计划进行生产活动,监控生产进度和质量,确保按时完成生产任务。
5.跟踪与调整:根据实际生产情况,对生产计划进行跟踪和调整,及时应对生产中的问题和风险。
3. 物料控制的定义与流程3.1 定义物料控制是对企业物料需求、采购、存储和使用等环节进行规划和管理,以保证生产计划的顺利进行。
它主要包括以下几个方面:•物料需求计划:根据生产计划和库存情况,确定物料的需求量及采购时间。
•物料采购:根据物料需求计划,进行供应商选择、采购谈判和合同签订等操作。
•物料收货:对收到的物料进行检验和入库,确保物料的质量和数量符合要求。
•物料存储:对入库的物料进行分类、标识和存储,以便于管理和使用。
•物料使用:根据生产计划和工艺要求,将物料送入生产线进行加工和组装。
•物料盘点:定期对库存物料进行盘点,核实实际库存与系统记录之间的差异。
制造业企业管理基础知识

制造业企业管理基础知识制造业企业管理基础知识1. 引言制造业是一个重要的经济部门,它对国家的经济发展和就业创造起着不可忽视的作用。
在如今竞争激烈的市场环境中,制造业企业需要有效地管理和组织各项资源,以提高生产效率、降低成本、提高产品质量,从而保持竞争力。
本文将介绍制造业企业管理的基础知识,包括生产计划、物料管理、质量管理和人力资源管理等方面。
2. 生产计划生产计划是制造业企业管理的重要组成部分。
它涉及到制定生产目标、制定生产计划、安排生产资源以及跟踪生产进度等。
制造业企业应根据市场需求、原材料供应情况等因素,合理制定生产计划,并根据实际情况进行调整。
,制造业企业还需要根据生产计划安排生产资源,包括设备、人力和原材料等,以确保生产的顺利进行。
3. 物料管理物料管理是制造业企业管理的重要环节。
它包括采购、仓储和库存管理等方面。
制造业企业需要根据生产计划的需求,准确地采购所需的原材料和零部件,并合理地进行仓储和库存管理。
物料管理的目标是确保原材料和零部件的及时供应,尽量减少库存数量,以降低资金占用成本。
4. 质量管理质量管理是制造业企业管理的关键环节。
它涉及到产品的设计、生产过程的控制和产品的检验等。
制造业企业需要根据市场需求和客户要求,设计出合理的产品规格,并制定相应的生产工艺和控制流程,以确保产品的质量符合标准。
,制造业企业还需要进行产品的检验和监控,以及及时处理质量问题,提供优质的产品给客户。
5. 人力资源管理人力资源管理是制造业企业管理的重要组成部分。
它涉及到员工的招聘、培训、考核和激励等方面。
制造业企业需要根据业务需求,招聘和选拔优秀的员工,并提供相关的培训和发展机会,以提高员工的专业素养和工作能力。
,制造业企业还需要对员工进行考核和激励,以激发员工的工作积极性和创造力,提高企业的综合竞争力。
6.制造业企业管理涉及到多个方面的知识和技能,包括生产计划、物料管理、质量管理和人力资源管理等。
合理的生产计划、有效的物料管理、严格的质量管理和科学的人力资源管理,能够帮助制造业企业提高生产效率、降低成本、提高产品质量,从而保持竞争力。
生产计划及物料控制程序

生产计划及物料控制程序引言生产计划和物料控制是现代企业管理中非常重要的环节,它直接关系到企业的生产效率、产品质量和客户满意度。
因此,建立一套科学合理的生产计划及物料控制程序对企业的长期发展具有重要意义。
本文将详细介绍生产计划及物料控制程序的相关内容,包括生产计划的制定与执行、物料需求计划、物料采购与入库控制、物料使用与消耗控制等方面。
1. 生产计划的制定与执行1.1 制定生产计划制定生产计划是企业进行生产组织和协调的第一步。
生产计划应根据市场需求、产品周期、生产能力等因素制定,确定生产量和生产时间。
1.2 执行生产计划执行生产计划是将制定好的计划转化为具体的生产活动。
在执行生产计划过程中,需要考虑生产设备的准备、原材料的准备、工时的安排等因素,确保按计划进行生产,并及时调整计划以适应生产实际情况。
2. 物料需求计划物料需求计划是根据生产计划,对所需物料进行合理的估计和安排。
它能够帮助企业根据实际需求,合理安排物料采购和供应,避免库存过剩或不足的情况。
物料需求计划应根据产品的生产工艺、生产周期和库存情况等因素进行合理估计,并及时更新以适应实际生产情况的变化。
3. 物料采购与入库控制3.1 物料采购流程物料采购流程包括:制定采购计划、选择供应商、编制采购订单、签订合同、实施采购、验收入库等步骤。
在物料采购过程中,需要关注采购周期、供应商的稳定性、物料质量等因素,确保采购及时、准确和合理。
3.2 入库控制入库控制是对采购的物料进行管理和控制,包括入库检验、入库记录、物料分类储存等。
通过严格的入库控制,可以确保采购的物料符合质量要求,并有效管理物料库存。
4. 物料使用与消耗控制4.1 物料使用计划物料使用计划是根据生产需求,对物料的使用进行合理安排和预测。
通过制定物料使用计划,可以提前安排物料供应,避免物料不足导致生产延误。
4.2 物料消耗控制物料消耗控制是对物料的消耗进行监控和控制,包括物料出库、物料使用记录、物料耗用统计等。
生产计划与物料控制
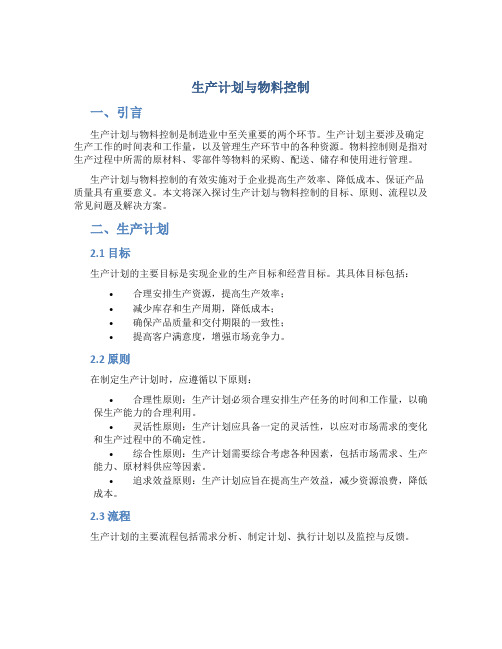
生产计划与物料控制一、引言生产计划与物料控制是制造业中至关重要的两个环节。
生产计划主要涉及确定生产工作的时间表和工作量,以及管理生产环节中的各种资源。
物料控制则是指对生产过程中所需的原材料、零部件等物料的采购、配送、储存和使用进行管理。
生产计划与物料控制的有效实施对于企业提高生产效率、降低成本、保证产品质量具有重要意义。
本文将深入探讨生产计划与物料控制的目标、原则、流程以及常见问题及解决方案。
二、生产计划2.1 目标生产计划的主要目标是实现企业的生产目标和经营目标。
其具体目标包括:•合理安排生产资源,提高生产效率;•减少库存和生产周期,降低成本;•确保产品质量和交付期限的一致性;•提高客户满意度,增强市场竞争力。
2.2 原则在制定生产计划时,应遵循以下原则:•合理性原则:生产计划必须合理安排生产任务的时间和工作量,以确保生产能力的合理利用。
•灵活性原则:生产计划应具备一定的灵活性,以应对市场需求的变化和生产过程中的不确定性。
•综合性原则:生产计划需要综合考虑各种因素,包括市场需求、生产能力、原材料供应等因素。
•追求效益原则:生产计划应旨在提高生产效益,减少资源浪费,降低成本。
2.3 流程生产计划的主要流程包括需求分析、制定计划、执行计划以及监控与反馈。
2.3.1 需求分析需求分析是生产计划的第一步,需要对市场需求进行分析和预测,确定所需产品的数量、质量要求以及交付期限。
2.3.2 制定计划在制定生产计划时,需要综合考虑生产能力、原材料供应、设备状况等因素,确保计划的可行性。
同时,还需要确定生产过程中所需资源的安排和使用,以及生产任务的分配和排程。
2.3.3 执行计划执行计划是将制定好的生产计划转化为实际行动的过程。
在执行计划过程中,需要确保各项生产任务按时完成,并进行生产过程中的监控和控制。
2.3.4 监控与反馈在生产过程中,需要对计划的执行情况进行监控,并及时反馈和调整计划。
监控和反馈的目的是及时发现和解决生产中的问题,以确保计划的顺利实施。
如何做好物料控制和生产计划

如何做好物料控制和生产计划在制造业领域,物料控制和生产计划是非常重要的环节。
物料控制指的是对原材料或零部件进行的计划、采购、运输、库存管理和调配;生产计划则是指制定生产计划、排产计划、生产指令、控制生产进度和计划完成情况等。
下面将介绍如何做好物料控制和生产计划。
一、建立完善的供应链管理体系物料控制和生产计划的关键在于建立一个完整的供应链管理体系。
这个体系应当包含供应商管理、采购管理、运输管理和库存管理。
通过建立供应链合作伙伴,以达到“共建、共享、共赢”的愿景,可以使制造企业和供应商之间共同提升供应链的效率。
例如,对于长期供应商,可以签订长期协议保证稳定供应;对于短期供应商,要及时沟通和跟进,保证原材料的及时供应。
二、合理制定采购计划在物料控制中,采购计划是核心环节。
制造企业要根据销售计划和生产计划,合理制定采购计划。
采购计划的核心目的是保证原材料的供应充足,避免库存过多或供应不足的风险。
在制定采购计划时,需要考虑以下几点:1. 预估需求量预估需求量是制定采购计划的前提。
需要预测的数据包括销售计划、生产计划、存货量、历史交易流水等。
通过这些数据的综合分析,才能制定出准确的采购计划。
2. 分析供应商的供货情况要做好物料控制,还需要综合考虑供应商的情况。
建立供应商快速响应机制,及时掌握供应商的供货情况和突发事件的影响,做出相应的应对方案。
3. 建立库存管理制度建立库存管理制度是控制采购成本和库存风险的重要手段。
合理的库存水平可以保证生产的顺利进行,并且降低运营成本。
要定期分析和评估库存情况,及时处理库存过多或过少的问题,调整采购计划,保证库存水平在合理范围内。
三、制定合理的生产计划制造企业应该根据市场需求和生产能力,制定合理的生产计划。
生产计划的核心目的是保证产品的质量和交货时间,以提高客户满意度和市场竞争力。
以下是制定合理生产计划的几个关键点:1. 根据订单进行灵活排产生产计划的首要任务是根据订单进行灵活排产。
生产计划与物料控制之物料控制PPT课件

对订单进行跟踪、监控和调整,确保按时交货,及时处理异常情况。
采购质量控制与物流管理
质量控制
对采购物品进行质量检验,确保符合要求, 对不合格品进行处理和追溯。
物流管理
合理安排运输工具、仓储设施和配送路线, 降低物流成本,提高物流效率。
05 生产计划与物料控制的关 系
生产计划对物料控制的影响
目标
确保生产所需物料的及时供应, 降低库存成本,提高生产效率和 产品质量。
物料控制的重要性
保障生产顺畅
提高生产效率
有效的物料控制可以确保生产所需的原材 料、零部件等物料的及时供应,避免因缺 料而导致的生产中断。
通过合理的物料计划和控制,可以减少物 料短缺和过剩的现象,提高生产线的利用 率和生产效率。
控制生产成本
保证产品质量
有效的物料控制可以降低库存成本,减少 资金占用,同时避免因物料过剩而导致的 浪费。
合理的物料控制可以确保使用合格的原材 料和零部件,从而保证产品的质量。
物料控制的基本原则
计划性原则
制定科学的物料需求计划, 根据生产计划和实际需求预 测物料需求量,并提前安排 采购和库存计划。
库存控制方法
总结词
库存控制方法是企业通过一系列手段对 库存进行管理和调整的方法。
VS
详细描述
常见的库存控制方法包括实时监控、安全 库存设置、联合库存管理等。实时监控是 通过实时数据对库存进行监控,及时发现 异常并进行调整。安全库存设置是为了应 对不确定因素而设置的一定数量的额外库 存。联合库存管理是通过协调供应链上下 游的库存管理,实现整个供应链的库存优 化。
物料供应的差异。
持续改进提高协同效率
03
通过不断优化生产计划和物料控制流程,提高两者之间的协同
生产计划与物料控制

生产计划与物料控制生产计划与物料控制是企业生产管理中极为重要的一环,它直接关系到企业的生产效率、成本控制和客户满意度。
一个科学合理的生产计划和物料控制可以帮助企业提高生产效率,降低库存成本,保证产品质量,提高客户满意度,从而获得竞争优势。
首先,生产计划是企业生产活动的指导方针,它需要根据市场需求、生产能力、原材料供应情况等因素进行合理安排。
在制定生产计划时,需要充分考虑市场需求的变化,避免因为市场需求变化而导致生产计划无法执行。
同时,还需要考虑生产设备的利用率,避免因为生产设备的闲置而增加生产成本。
因此,制定生产计划需要全面考虑各种因素,确保生产计划的科学性和合理性。
其次,物料控制是生产计划执行的关键环节,它直接关系到原材料的供应、库存的管理和生产进度的控制。
在物料控制中,需要合理安排原材料的采购计划,避免因为原材料的短缺而导致生产计划无法执行。
同时,还需要合理管理原材料的库存,避免因为库存过多而增加库存成本。
在生产过程中,还需要及时掌握生产进度,确保生产计划的及时执行。
因此,物料控制需要全面考虑原材料的供应、库存的管理和生产进度的控制,确保生产计划的顺利执行。
最后,生产计划和物料控制需要不断进行优化和改进,以适应市场需求的变化和生产技术的进步。
在市场需求发生变化时,需要及时调整生产计划,确保生产计划与市场需求保持一致。
在生产技术进步时,需要及时更新物料控制系统,提高物料控制的精度和效率。
因此,生产计划和物料控制需要不断进行优化和改进,以适应外部环境的变化和内部技术的进步。
综上所述,生产计划与物料控制是企业生产管理中极为重要的一环,它直接关系到企业的生产效率、成本控制和客户满意度。
一个科学合理的生产计划和物料控制可以帮助企业提高生产效率,降低库存成本,保证产品质量,提高客户满意度,从而获得竞争优势。
因此,企业需要重视生产计划与物料控制,不断进行优化和改进,以适应市场需求的变化和生产技术的进步。
- 1、下载文档前请自行甄别文档内容的完整性,平台不提供额外的编辑、内容补充、找答案等附加服务。
- 2、"仅部分预览"的文档,不可在线预览部分如存在完整性等问题,可反馈申请退款(可完整预览的文档不适用该条件!)。
- 3、如文档侵犯您的权益,请联系客服反馈,我们会尽快为您处理(人工客服工作时间:9:00-18:30)。
f.合理的仓储(搬运,包装等)A.B.C 类物料利用
g.高效的领料过程(流料的预防和处理 j.把关和控制进料的品质 k.产品的设计
4.18 呆滞料成因
A.订单Forecast不准 B.设计变更和欠标准化 C.产/销协调不良 D.ECN跟踪不彻底 E.仓库管理不当 F.超PO订料/MOQ… G.规格/性能不符要求 H.进料品质不当
物料管理和生产计划 基础知识
William Huang
1 一 2 3 4 5
物料管理概念 物料管理意义 物料管理目标 物料和生产计划管控内容 灵活应用
1.物料管理概念
为了保证生产过程连续均衡地进行,就要做好物料
的采购,供应,存储,保管,使用等各项组织管理工作,这些 工作称为物料管理.
2.物料管理意义
不断料,不呆料,不囤料(物控的精髓) 减少浪费,降低成本 适时供料,以确保生产稳定 适量备料,以减少资金压力 适质/适价购买,以降低生产成本 核实发/收/存料,得以帐物准确,及正常使用 材料的安全保管
3.2 物控不好造成的损失
停工待料 物料积压 影响生产进度
4.物料/生产计划管控内容
4.7 客户状况
Wonderland XX3 Laird XX2 XX1 0 XX1 天数 21 10 20 XX2 33 30 Laird 40 40 XX3 50 50 60 天数
Wonderla nd 22
4.8 订单和forecast
N-1 1W 2W 3W 4W 1W 2W N 3W 4W
4.9 物料计划与存量管制
物料短缺的原因和应对措施:
紧急订单——了解现在和未来的状况,预测和微调制度 供应商跳票——建立欠料预防制度(表格) 损耗超预算——欠料分析和跟进制度 产品设计临时更改——欠料分析和跟进制度 库存记录不准——备料齐套制度 资金流转问题——相关部门要定期维护数据 人为疏忽——培训员工遵守制度 突发事件——建立例会制度(定人/地/时/内容)
4.2.1 MPS 五大功能
a . 对生产订单和能力进行预测及分析(需求工时和提 供评估工时) b. 产/供/销平衡制度的建立(能否给出预测给到供应 商) c. 插单/急单/补单的制度 d. 计划微调 e. 计划前事务的跟进(设备,厂房,人力,物供体系)
4.2.2 二级计划
(周/月度生产计划,或生产线内部排出的计划) A计划 (n+2)
准备结果追踪与调整
4.2.6 月计划
订单需求 → 物料状况分析 ─ 设备负荷分析 ─ 人力负荷分析 ─ 生产效率分析 ─ 工作环境分析 ─ 月计划 物控 生产 确认 做好 物料 生产前 需求 准备
↓
工程 待证 生产 工序
BD 做好 订单 需求 准备
准备结果追踪与调整
↓
2周的生产计划
4.3 短期产能调整的八大方法
Model S/O QTY 单位 产能
一 二
第8周执行计划
三 四 五 六 日 一 二
第9周锁定预测
三 四 五 六 日 一 二
第10周预排
三 四 五 六
4.2.3 编生产计划要素
4M1E 人-人力负荷=(标准工时 X 生产数量)/实有工时 机-设备负荷=(工序标准工时 X 生产数量)/实有工时 X 实际稼动率 物-物料负荷=准时到/备料批次 法-生产效率=实际产线工时/实际投入工时 环-环境因素,工作环境,天气因素对生产效率,工艺品质的影响波动。
B.介于A,C之间的物资,品种:20-30%,资金占15-20% C.品种多,占资金少,品种:60-65%,资金占5-10%
100 75 50 25 0 A B C D 金额百分比
通用物料:安全存量,最高存量 专用物料:最高存量 特殊物料:零存量
4.14 三种物料的库存设置
4.15 库存指标管理
1〉、保证生产的正常进行 2〉、降低制造成本的基础 3〉、加快企业资金周转速度 4〉、保证产品质量的基础
3.物料管理目标
1〉、正确计划用料 2〉、适当的存量管制 3〉、发挥盘点的功效 4〉、保证产品的品质 5〉、优化采购管理 6〉、发挥储运功能 7〉、合理处理异常物料 8〉、降低成本
3.1 物控人员职责
4.16 造成库存的原因
营销管理问题
1.市场预测错误 2.市场变化超出营销预测能力 3.订单管理和客户衔接失误 生产管理问题 1.生产批量与计划吻合不严密 2.安全库存量的基准设定太高 3.生产流程产能不均衡 4.产品加工时间太长(如外发)
物料供应来源问题
1.供应商L/T过长,供应不及时
2.供应商产能不稳定
3.个别物料的欠缺而不齐套
4.担心供应商的供应能力,增大库存以规避风险
4.17 从物控角度如何控制物料成本?
a.降低物料库存,提高物料周转率(库存量的大小) b.防止停工待料现象的发生 c.合理的物料计划(材料/MRP/零部件的标准化)
d.合理的物料采购计划(物料的价格/MOQ/SPQ /L/T) e.高效地验收方法
4.12 订购前置时间
供应商的生产时间 供应商的备料时间 供应商的交通运输时间 供应商的来料检查时间
4.13 ABC分类法(定义,分类,运用)
A.品种小,资金占用比例大,品种:10-15%,资金占75-80%
1.选择最优的订购批量,库存压缩到最低,与供应商建立战略合 作伙伴关系 2.对该物料进行动态盘点 3.预测更加严格
1.周转率:(定义) ITO=Inventory Turnover 2.MFC:(定义)
MC:RM周转天数
PC:WIP周转天数
BD:FG周转天数
例: 一年内使用金额1200万,年初存货金额80万,年未存货金 额120万,月平均存料金额100万; 周转率=期间使用金额/(期初存货金额+期末存货金额)/ =1200/[(80+120)/2]=12 周转速度=360天/周转率 =360天/12 =30天 存料率=平均存货金额/期内用料金额 =100/1200=8.3%
4.19 生产计划的管控
制定/协调销售计划 → 分析产能负荷 → 制定生产计划 ↓
生产异常协调←控制生产进度←生产数据统计←督促物料进度
涉及到: ①产供销作业流程 ②生产计划控制流程
③产能负荷分析控制点 a.订单分析 b.瓶颈产能跟踪 c.物料分析 d.采购进度 e.委外进度 f.检验进度 g.技术资料 h.设备保养维护 i.人力需求评估
4.20 生产协调会议—PRB会议
1.计划成品的产值
2.计划达成率分析
3.各车间的废品统计及分析 4.设备利用图表分析 5.设备故障停机时间图表分析 6.物料领用费用分析 7.半成品库存状况分析 8.新产品进度
5. 活用所需的五个步骤
自我对比差异化,评估差异系列性 ↓ ①可行性→②效益(成本)→③什么时候→④上司支持→⑤其 它(以瓶颈问题着手) ↓
70
①、增加机械台数 ②、增加员工 提前 ③、提升效率 ④、改良生产工艺和流程 ⑤、利用库存(安全库存) ⑥、变动劳动时间(OT/放假/培训) ⑦、利用外部资源(外发加工) ⑧、推迟交期
60 50 40 30 20 10 0 1 2
推后 提前
生产能力 正常生产
3
4
5
6
4.4 生产排程的两种方法
①、生产进度排程法(每小时产量,每天的产量) ②、生产工艺排程法 故计划部门应凌驾于其它部门之上,能调动资源。 F/G(交货提前期)随时出货视生产时间按订单半成 品/FG/生产
生产订单
N+1
N+2
N+3
Lead time 正式订单 协议订单
1次订单下发日
Lead time 较正式订单 修改生产订单
2订单下发日
MPS → MRP → PR to PO → production order
↓ Production planning ↓ 出货 ← 成品入库 ← 异常协调 ← 生产进度跟进
4.10 物控的六道关口
物料开发阶段,降低成本,质量把关 SCM主导,监控供应商的生产数据 看供应商的成品,物料,WIP等日报 提前计划审查法 物料与实物料核对确认 车间监督检查物料的数量,质量并报给物控。
4.11 库存量
安全存量=紧急订单所需时间X每天使用量
最高存量=一个生产周期天数X每日使用量+安全存 量(FG,WIP,R.M. )
建议/提案方式或给部门小组形成展开
↓ 制定推引计划,定期汇报进度结果 ↓ 适时适当发表
4.2.5 周计划
订单需求 → 物料状况分析 ─ 设备负荷分析 人力负荷分析 生产效率分析 工作环境分析 ─ ─ ─ ─
→ 2周的生产计划 ↓
第一周生产计划 → ↓ 执行生产计划 ↓ 追踪进度异常处理 ↓ 计划调整 ↓ 计划与进度一致 ↓ 生产入库 第二周生产计划 ↓ 物 控 确 认 物 料 需 求 生 产 做 好 前 期 准 备 工 程 /PIE 保 证 工 艺 协 调
4.1 物料控制/生产计划/销售计划的管理 PMC扮演仲裁与决策之角色,使产/销/供紧密结合,物 料控制是对企业物料的进/储/出/耗所有环节进行控制; 物控的三个灰色地带: ①追踪物料欠料报告 ②提供物料状态报表 ③呆滞物料及处理 4.2 主生产计划,MPS,也称一级生产计划,由此派生 出的计划为二级生产计划。
4.2.4 时间跨度上区分
短期—周计划,通常情况下有2周波动排程 中期—月计划,每月进行整体分析,指导各生产要素的 前期准备的相应调整(生产/物料/销售) 长期—MPS 主生产计划,以推移图或其它的方式,结合 现有订购 forecast 状况,动态体现各生产要素的负荷状 况,以指导订单的评估,物料和生产的准备,以及订单的需 求。
4.5 四种生产类型