STS〈免检制度〉的介绍
物料免检程序

1.Purpose 目的Establish this procedure to define the qualification criteria of STS material, to define the operation procedure for STS materials, to enhance IQC work efficiency of inspection.Note: This procedure can’t as the supplier’s excuse who wants to relax or exempt the quality liability for their products.建立免检物料的评价标准,规范免检物料的操作流程,提高IQC的检验效率。
注:本程序的建立和执行旨在提高IQC的检验效率,鼓励供应商持续高品质的为我司供货,但并不作为供应商对其产品质量责任豁免的依据。
2.Scope 适用范围This procedure applied for all production materials which in mass purchasing stage, but not include critical part, subcontract part, customer’s part or customer have special request.适用于本公司量产采购阶段所有的生产性物料,但关键元器件、外协加工件、客供料或客户有特别要求的物料除外。
3.Definition 定义3.1 STS Ship To Store / 直接入仓,即物料免检3.2 RDS Request of Disqualify STS / 物料免检资格取消申请4.Responsibility 职责SQE 供应商品质工程师Drive supplier to improve the quality performance to get STS certification for their product;推动供应商进行品质改善,以促其产品达到STS状态;Review the <STS Material Application List>;《STS物料评审表》的复审;IQE 来料品质工程师Prepare and update the <STS Material Application List>, and submit to SQE to review and submit to quality manager for approval;制备和更新《STS物料评审表》,提交SQE复审以及品质经理批准;Release RDS, to disqualify the STS material;发出RDS,以取消物料的STS资格;Update ERP system data about the material inspection type;更新ERP系统物料检验模式信息;IQC 进料检验组Inspect and mark the STS materials base on ERP system information;根据ERP系统信息检验和标识STS物料5.Procedure 工作程序5.1 The qualification criteria of STS material / STS物料评定标准The materials may apply to STS if all conditions in below are achieved:符合下述全部条件的物料,可以申请成为STS物料:a.Continual pass 10 lots by IQC, without any abnormal case or reject;连续10批IQC检验无异常、无退货;b.The material DPPM in process under the control limit last for 3 month:在我司生产制程中,该物料连续三个月DPPM达成下述指标:Electrical part and active optical part / 电子物料及有源光器件:100DPPMMechanical part / 结构件:500DPPMPassive optical part / 无源光器件:500DPPMPCB / 印刷电路板:500DPPMPacking materials / 包材:1000DPPMComments / 注:The total incoming qty and consumed qty should more than 30kpcs.来料总数量和我司使用的总数量须在30K以上。
安全生产免检制度范本

安全生产免检制度范本一、目的和原则为确保我国安全生产形势的稳定,提高企业和员工的安全意识,促进安全生产管理水平的持续提升,根据《中华人民共和国安全生产法》等相关法律法规,制定本免检制度。
本制度遵循公开、公平、公正的原则,对符合条件的企业实行安全生产免检制度。
二、免检范围和条件1. 免检范围:适用于全国范围内的一切企业和生产经营单位。
2. 免检条件:(1)严格遵守国家安全生产法律法规,认真贯彻执行国家安全生产方针、政策和标准;(2)建立健全安全生产责任制,明确各级领导和部门的安全生产职责;(3)落实安全生产规章制度,严格执行安全生产操作规程;(4)配备完善的安全生产设施,保障安全生产条件;(5)开展安全生产教育和培训,提高员工安全意识;(6)实行安全生产标准化管理,不断提升安全生产管理水平;(7)积极参加国家、地方和行业组织的安全生产活动;(8)无安全生产事故,或者事故发生率低于全国平均水平;(9)国家和地方安全生产监管部门规定的其他条件。
三、免检程序1. 企业向所在地级以上人民政府安全生产监管部门提出免检申请;2. 安全生产监管部门对企业进行初步审查,对符合免检条件的企业进行实地核查;3. 实地核查合格的企業,由安全生产监管部门报请人民政府审批;4. 人民政府审批通过后,对企业进行公告;5. 企业自公告之日起,享受安全生产免检待遇。
四、免检待遇1. 在免检期间,企业免受安全生产监管部门的日常检查;2. 企业在申请安全生产许可证、危险化学品经营许可证等相关许可时,予以优先办理;3. 企业在评选安全生产先进、优质项目时,予以优先考虑;4. 企业在融资、税收等方面,享受国家规定的优惠政策;5. 企业的人员在职称评定、职务晋升等方面,给予适当倾斜;6. 国家和地方其他优惠政策。
五、监督管理1. 免检企业应定期向所在地级以上人民政府安全生产监管部门报告安全生产情况;2. 安全生产监管部门对免检企业实施动态管理,发现问题及时督促整改;3. 免检企业如发生安全生产事故,立即取消免检待遇,严肃追究相关责任;4. 企业如违反国家安全生产法律法规,一经查实,取消免检待遇,并依法予以处罚;5. 各级人民政府安全生产监管部门应加强对免检企业的指导和服务,帮助企业提高安全生产管理水平。
产品质量免检保证体系

产品质量免检保证体系1.目的通过实施产品质量免检保证体系,提升企业产品质量水平和质量管理水平,达到满足客户需求,增强客户对企业的满意和信任,从而增加市场效益。
2.范围适用于公司实现产品质量免检活动的全过程控制3.术语和定义3.1产品质量免检标准:是指产品达到或超过某种规定的质量标准。
公司开展产品质量免检活动或形成制度,旨在增强顾客对企业的满意和信任;实施产品质量免检标准并不排除顾客的现场检验、接收检验(包括正常检验、放宽与加严检验和免检)。
3.2 全面质量管理:就是必须由市场调查、研究开发、品质设计、原料管理、制造管理、品质保证、售后服务等部门串接一起,此种一惯性的制度建立与推展的系统,就是全面品质管制系统。
4.为实现产品质量免检的目标,我们所要利用的方法是:全面质量管理。
具体方法如下:4.1全面质量管理的基本方法可以概况为四句话十八字,即,一个过程,四个阶段,八个步骤,数理统计方法。
A. 一个过程,即企业管理是一个过程。
企业在不同时间内,应完成不同的工作任务。
企业的每项生产经营活动,都有一个产生、形成、实施和验证的过程。
B. 四个阶段,根据管理是一个过程的理论,美国的戴明博士把它运用到质量管理中来,总结出“计划(plan)—执行(do)—检查(check)—处理(act)”四阶段的循环方式,简称PDCA循环,又称“戴明循环”。
C.八个步骤,为了解决和改进质量问题,PDCA循环中的四个阶段还可以具体划分为八个步骤。
1)计划阶段:分析现状,找出存在的质量问题;分析产生质量问题的各种原因或影响因素;找出影响质量的主要因素;针对影响质量的主要因素,提出计划,制定措施。
2)执行阶段:执行计划,落实措施。
3)检查阶段:检查计划的实施情况。
4)处理阶段:总结经验,巩固成绩,工作结果标准化;提出尚未解决的问题,转入下一个循环。
在应用PDCA四个循环阶段、八个步骤来解决质量问题时,需要收集和整理大量的书籍资料,并用科学的方法进行系统的分析。
免检管理制度

免检管理制度免检管理制度1.目的:为强化预防为主的质量理念,规范外购零部件免检流程,降低产品成本,避免质量风险,确保免检工作得到有序的开展,特制定本制度。
2.范围:本制度适用于所有的外协件。
3.定义:免检产品是供应商提供质量优良的零组件给本公司,并在其生产制程中做好质量管理作业,达到本公司要求的质量标准,本公司不需再经进料检验,即可直接供料使用,所建立的一种管理作业办法。
4.职责4.1 供应商和零部件检验员申请免检需向本公司SQE提出4.2 零部件检验员负责填写《免检物料质量报告》4.3 过程检验员和IPQC负责将免检物料上线PPM的统计结果和来料质量问题反馈给SQE4.4 品质部经理负责批准免检物料5.对供方的要求:5.1实施免检的供方必须通过:ISO9000(2000)/ ISO/TS16949-2002/VDA6.1之一。
5.2申请免检的供应商为合格供应商且必须是连续批量供货的,同时满足以下条件:5.2.1 A类产品必须连续10批上线PPM为零;指产品的主要零部件,如:连接器、线材、电子元件、塑胶、五金、PCB等零配件5.2.1 B类产品必须连续8批上线PPM为零;指产品的次要零部件,如:PVC /PE塑胶料、套管、胶布、包装材料等。
5.2.1 C类产品为特殊管制物料;指锡丝/锡条、松香水/助焊剂、清洗剂、MEK、酒精、胶水、纸张、油墨、油漆、笔等。
5.3在对A、B类外购零配件实施免检供货前,必须制定可行的应急计划(如安全库存、确定潜在供方或第二供方等),没有应急计划不得对该类零配件实施免检;6.特殊管制物料免检要求:6.1 针对C类产品为特殊管制物料,由采购填写《内部免检申请单》向SQE提出申请,并同时必须提供供应商有效的SGS报告,如果没有有效的SGS报告,不得对该类产品申请免检和实施免检。
6.2 SQE根据采购申请的免检物料,进行审查以确定是否满足环保要求,并要求供应商签署环保声明书或环保协议,品质部经理负责批准,符合要求的纳入《免检物料清单》。
安全生产免检制度

安全生产免检制度安全生产免检制度是指在一定的条件下,对安全生产工作中的某些事项减少或免除常规检查、验收的制度。
其目的在于优化检查力度,提高工作效率,促进安全生产工作的科学化、规范化和有效性。
首先,安全生产免检制度能够对一些固定、稳定而且风险较低的事项进行免检。
在生产过程中,存在一些工作环节相对简单,工艺稳定可靠,没有明显的安全隐患的项目,这些事项进行常规检查或许会浪费大量的时间和人力资源。
因此,实行免检制度可以避免不必要的重复劳动,提高工作效率。
其次,安全生产免检制度能够针对某些高风险项目进行重点检查。
在安全生产工作中,有些环节风险较高,一旦出现问题后果严重,如设备维护、操作规范、安全培训等。
对于这些事项,应当加强监管力度,进行重点检查和验收。
通过实施免检制度,可以将检查资源集中于关键环节,确保高风险项目的安全运行。
另外,安全生产免检制度还能够激发企业的积极性和责任感。
在企业中,往往存在着一种“形式主义”的思想,即只注重完成文件手续,而忽视了实际的安全生产工作。
采取免检制度后,将逼迫企业自觉进行风险评估和管理,提升企业的安全意识和责任感。
只有企业真正做到安全生产的“真抓实干”,才能确保从根本上消除事故隐患。
最后,安全生产免检制度应当建立在科学、合理的基础上。
免检制度不是为了减少工作量而采取的一种简化措施,而是基于对各环节的科学判断和充分论证的基础上所采取的措施。
相关部门应当通过系统的分析和研究,确定免检范围和条件,并建立相应的风险评估和监管机制。
同时,相关部门应当及时总结借鉴各单位的经验,不断完善和调整免检制度,确保其科学性和有效性。
综上所述,安全生产免检制度是一项重要的管理制度,其实施能够提高工作效率,降低因常规检查带来的工作负担,同时也能够加强对高风险环节的监管力度,提升企业的安全意识和责任感。
但其实施应当基于科学、合理的原则,确保各项工作都得到充分的关注和管理。
只有这样,才能够更好地促进安全生产工作的开展,确保人员和财产的安全。
《免检办法》产生的背景-管理资料

《免检办法》产生的背景-管理资料
1991年国家停止评优工作后,各级质量技术监督部门一直在探索落实《产品质量法》规定的有关扶优扶强的措施,。
一些地方尝试了在监督检查中根据企业的情况,对检查周期采取加严放宽的做法。
即对质量不稳定的产品,缩短检查周期;对经多次检查合格,质量稳定的产品,延长检查周期。
在此基础上,一些地方开展了免检工作,对连续几年国家、省监督检查合格的产品,在一定时期内免于监督检查。
但在实行过程中,由于国家没有统一的管理办法,各地自行探索,因此造成各地免检工作的开展不平衡,做法不尽一致,免检产品的水平也参差
不齐。
同时,还出现了一些背离初衷的错误做法:一是有的地方层层推选,层层审查,加重了企业负担;二是有的地方以追求经济利益为目的,把“免检”作为“创收”的手段;三是有的地方层层搞免检,致使一些质量水平不高的企业打着免检的牌子,到处进行广告宣传,导致了企业间的不平等竞争等,
管理资料
《《免检办法》产生的背景》(https://www.)。
鉴于各地免检工作开展中出现的诸多问题,原国家技术监督局于1997年8月发文,要求各地暂停免检工作,同时,着手开展调查研究,制订统一规范。
1999年12月5日,国务院以国发[1999]24号文印发了《国务院关于进一步加强产品质量工作若干问题的决定》(以下简称《决定》),其中第十六条规定:“对产品质量长期稳定、市场占有率高、企业标准达到或严于国家有关标准的,以及国家或省、自治区、直辖市质量技术监督部门连续三次以上抽查合格的产品,可确定为免检产品”。
根据国务院的《决定》,原国家质量技术监督局于2000年3月14日以国家质量技术监督局令第7号的形式,发布了《产品免于质量监督检查管理办法》。
食品安全法中免检制度

一、引言食品安全问题一直是关系到人民群众身体健康和生命安全的重大问题。
近年来,我国食品安全事件频发,引起了全社会的高度关注。
为了保障食品安全,我国制定了一系列法律法规,其中,《中华人民共和国食品安全法》是我国食品安全领域的核心法律。
在食品安全法中,免检制度是一项重要的制度安排,旨在减轻企业负担,提高食品安全监管效率。
本文将重点探讨食品安全法中的免检制度。
二、免检制度的定义及意义1. 定义免检制度是指在食品安全监管中,对某些符合条件的食品实施免于检验的制度。
根据《中华人民共和国食品安全法》的规定,免检制度适用于以下几种情况:(1)生产者提供的检验报告符合国家标准或者行业标准的;(2)生产者提供的产品抽样检验合格,且连续三年未发生食品安全事件的;(3)生产者提供的其他符合免检条件的。
2. 意义(1)减轻企业负担:免检制度可以减轻企业负担,降低企业成本,提高企业竞争力。
(2)提高监管效率:免检制度可以简化检验程序,提高监管效率,减少监管资源浪费。
(3)保障食品安全:免检制度可以促使企业加强自律,提高产品质量,保障食品安全。
三、免检制度的实施条件1. 产品符合国家标准或者行业标准根据《中华人民共和国食品安全法》的规定,免检制度适用于生产者提供的检验报告符合国家标准或者行业标准的食品。
这意味着,企业必须按照国家标准或者行业标准生产食品,确保产品质量。
2. 产品抽样检验合格,且连续三年未发生食品安全事件企业要申请免检,必须满足产品抽样检验合格,且连续三年未发生食品安全事件的条件。
这一条件旨在确保企业产品质量稳定,降低食品安全风险。
3. 其他符合免检条件的除上述条件外,企业还可以根据实际情况申请免检。
例如,企业可以提供产品生产过程控制记录、质量管理体系认证证书等证明材料,证明其产品质量安全可靠。
四、免检制度的监管措施1. 加强企业自律企业要自觉遵守食品安全法律法规,加强内部管理,确保产品质量安全。
监管部门要加强对企业的监督检查,对违法行为依法予以查处。
免检作业规定

1目的
1.1為提高品質水準及生產效率,使免檢作業有一規范可依,特制定本程序.
2范圍
2.1凡本廠入料之原材料均適用之.
3定義
3.1免檢:因協力廠商一向品質水準符合要求,而對其物料免於檢驗.
3.2IQC統計同一屬性類別的進料檢驗表,如連續10批都達到要求及制程
中該物料無不良發生,予列入免檢.必要時請廠商提供品質保證書或出
貨檢驗報告.
3.3對於一些與產品品質無直接關系之物料列入免檢,但需合並
在制程檢驗或成品檢驗中予以監控.
4權責
4.1IQC:負責免檢執行.
4.2采購課:負責提出免檢及擬訂免檢物料一覽表.
5.內容
5.1免檢作業程序(見3/3頁)
5.2IQC依據「進料檢驗作業程序」對來料進行檢驗,並填寫“進料檢驗報告”
或“進料(標簽)檢驗報告”(附件一、二).
5.3采購對達到免檢資格的物料提出免檢需求,並列入“免檢物料一覽表”(附
件三).
5.4IQC核對“免檢物料一覽表”如果為其所列,則對其物料貼上“免檢”標示.
5.5免檢物料品質管制
5.5.1在制程中發現物料不良時,則取消其免檢資格,並參照「不合格品管
制作業程序」處理.
5.5.2IQC應主動對免檢物料進行不定期抽檢,如發現物料有異常,則取
消其免檢資格予以管制.參照「不合格品管制作業程序」.
6參考資料
6.1進料檢驗作業程序(QCP001)
6.2不合格品管制作業程序(QCP006)
7附件
7.1進料檢驗報告(QCR001.03)
7.2進料(標簽)檢驗報告(QCR001.07)
7.3免檢物料一覽表(QCR004.01)。
免检和抽检管理制度范文

免检和抽检管理制度范文免检和抽检管理制度第一章总则第一条为规范和优化企业质量管理体系,提高产品质量,保障消费者利益,制定本免检和抽检管理制度。
第二条本制度适用于所有生产和销售产品的企业,包括但不限于制造业、服务业等。
第二章免检和抽检的概念和目的第三条免检是指产品在生产过程中和销售过程中不被抽取进行质量抽检的管理方式,即产品出厂前不需要经过严格的检验程序。
第四条抽检是指在产品生产过程中和销售过程中,按一定比例随机抽取产品进行质量抽检的管理方式,即在产品出厂前需要进行一定比例的检验程序。
第五条本制度的目的是保证产品质量,提高企业市场竞争力,加强对产品质量的监督管理,保障消费者权益。
第三章免检和抽检的依据和程序第六条免检和抽检应当依据国家相关法律法规和标准进行执行。
第七条企业应当建立健全产品质量管理体系,包括生产过程控制、质量监测等环节,确保产品质量的可控性和可追溯性。
第八条对于符合免检标准的产品,企业应当申请免检,并经过相关部门的审批,持有免检证书后方可生产。
第九条对于不符合免检标准的产品,企业应当按照抽检的要求进行质量抽检,在产品出厂前进行检测,确保产品质量达到标准要求。
第四章免检和抽检的政策和措施第十条对于取得免检证书的产品,企业可以享受以下政策和措施:1. 免检证书持有人可以减少一定比例的质量抽检。
2. 免检证书持有人可以享受一定比例的税收优惠。
3. 免检证书持有人可以享受相关奖励和荣誉。
第十一条对于没有取得免检证书的产品,企业应当按照抽检的要求进行质量抽检,不得对抽检的结果进行篡改和伪造,并及时改进和整改不合格产品。
第十二条对于拒绝抽检或者抽检结果不合格的企业,相关部门有权采取上报、停产、吊销许可证等措施,并对相关责任人进行追责。
第五章免检和抽检的监督和检查第十三条监督和检查机构应当加强对企业的监督和检查,对产品质量的免检和抽检情况进行定期的或者不定期的检查。
第十四条监督和检查机构应当对免检和抽检的结果进行评估,及时发现问题并提出改进建议。
材料及零件进料免检制度

适用范围:本办法适用于(辅助材料及办工用品)之零件材料和本厂无特殊仪器检验材料。
目的:为降低检验成本及人力资源而同时又能维持品质水准,特制订本规定。
内容方法:
1.免检资格之取得:
1.1本公司承认之厂商并已在使用之零件材料。
1.2连续20批检验无不良记录而厂商又能提供质量保证。
1.3国内厂商符合上述两项条件,经品保部和研发部确定合格后,列入免检。
2.免检资格之取消:
1.1免检材料或零件在生产线上,引起产品不良之抱怨,经分析属该材料或零件之
缺点时,或客户抱怨产品而经分析,确实属材料或零件影响品质者。
2.2因品质变异不良或交期延误,导致生产线停工损失或产品发生重大不良而导致本
公司蒙受重大损失者。
2.3免检资格之取消,概以书面通知。
2.4免检资格取消后之进料检查,依正常流程办理。
3.相关表单
免检材料一览表。
原材料免检管理办法GRT-STS 3

原材料免检管理办法文件编号:XXXXXXXX制订:陈玉玲审核:批准:生效日期:变更记录一、目的1。
1针对品质稳定之材料供应商给予进料免检之优惠,相对降低公司之检验成本。
1。
2提高供应商品质系统与制程管制,全面贯彻其品质保证责任,提高产品品质。
1。
3配合减少JIT物料在我司的储存时间及周转时间,实现真正的JIT。
二、范围2.1 被本公司列入合格供应商名录中之材料供应商2。
2 经审核通过列于免检原材料及耗材之材料2.3 客户提供之材料或客户指定协力厂商提供之材料,可申请列入免检。
三、定义STS:(Ship To Stock). 直接出货到仓库。
是指将Growatt IQC的检验方式复制或移转到供应商处。
通过对供应商品质体系的培训,辅导,考核,和对供应商检验员的培训,考核合格后指定检验员按Growatt 的检验方式对物料进行检验。
而通过供应商的检验后的物料直接出货至Growatt后不再检验的过程。
JIT(Just in Time)物料:钣金,散热器,电感,包材,变压器等适合做及时入料的物料。
四、职责4.1采购部:采购部负责协助推进免检工作,配合品质部对供应商的甄选,管理和稽核。
以及针对JIT()物料需求的提出。
4.2品质部:4.2.1品质部负责此程序的制订,修改与执行,SQE工程师负责依据供应商来料品质状况对供应商免验资格的取消及恢复提出申请.4.2。
2品质部主导免检工作的推行/管理/监控,追踪免检材料上线之品质状况.4.2。
3品质部协助供应商建立健全的品质系统,并协助其持续推展推行。
4.2.4主导处理材料异常品质状况,并追踪至供应商改善OK.4。
2。
5 材料免检申请、材料免检取消及恢复申请需由品质部最高负责人批准,方可生效.4.2。
6 品质部负责提供免检物料清单给K3系统维护员对K3系统进行维护.4.3仓库:4。
3.1对于免检物料,仓库在收料时直接办理收料,入库、发料及退货作业,而无需再经IQC检验。
外协外购产品入厂免检管理制度

1.目的1.1促进供应商提高产品质量,提升配套体系的质量保证能力;1.2避免重复检验,提高效率,降低成本;2.适应范围指定的质量稳定的成熟产品的零部件。
3.术语3.1免检:对取得免检资格的供应商零部件及自检报告的直接接受。
3.2免检零部件:供应商对零部件已检验,并且确认能保证质量而不再需要检验的零部件。
4.职责4.1技质部4.1.1质量部负责制定本办法,负责免检零部件的清单的审核,负责免检零部件免检时期质量监控;4.1.2每年第一季度和第四季度,技质部SQE集中组织检验员、物流收货员、分供方及相关管理人员进行培训。
4.2 物流部4.2.1 物流部收货员按免检零部件清单办理入库手续。
5.内容和要求5.1免检零件要求:5.1.1成熟产品的零部件,过去一年没有重大、特大及批量质量问题;5.1.2产品性能及可靠性在无法用日常检测手段检查;5.1.3供应商按ISO/TS16949的要求建立并维持有效的质量管理体系,并注册通过ISO/TS16949质量体系第三方认证。
5.1.4零部件连续3个月入厂检验和生产过程中均未出现批量不合格品,主机厂未反馈零部件质量问题。
5.2免检零件名单确认和发布:5.2.1SQE根据免检零部件条件的要求编制免检零部件名单;5.2.2SQE将编制的免检零部件名单报质量部经理审核、物流部会签;5.2.3《免检零部件清单》审批后,由质量部发布。
5.3免检产品的入库管理5.3.1供应商到货后,将《送货单》交外检登录台帐后,盖“免检”章。
5.3.2物流部收货人员根据“免检章”直接收货。
6.免检流程7.取消免检流程6.记录Q-P8-04-W-03-R-01:《免检零部件清单》;保存地点:技质部、物流部;保存时间:长期。
下面是诗情画意的句子欣赏,不需要的朋友可以编辑删除!!谢谢1. 染火枫林,琼壶歌月,长歌倚楼。
岁岁年年,花前月下,一尊芳酒。
水落红莲,唯闻玉磬,但此情依旧。
2. 玉竹曾记凤凰游,人不见,水空流。
进出口商品免验办法

进出口商品免验办法第一条为了保证进出口商品质量,促进对外贸易关系的顺利发展,根据《中华人民共和国进出口商品检验法》第五条和《中华人民共和国进出口商品检验法实施条例》第八条的规定,制定本办法。
第二条凡列入《商检机构实施检验的进出口商品种类表》的进出口商品,经收货人、发货人和生产企业(以下简称申请人)提出申请,国家商检局审查批准,可以免予检验。
第三条申请人申请免验,应当具备以下条件:㈠申请免验的进出口商品的生产企业,必须建立完善的质量体系。
进口商品的生产企业应当经国家商检局认可或者有认证协议的有关机构实施考核,并获得其颁发的质量体系评审合格证书。
出口商品的生产企业应当由中国出口商品生产企业质量体系(ISO9000)工作委员会认可、并经国家商检局注册的评审机构考核,获得其颁发的生产企业质量体系评审合格证书。
㈡申请免验的进出口商品质量应当长期稳定,商检机构检验合格率连续3 年达到100%;㈢进口商品的中国用户或者出口商品的外国用户对申请免验的进出口商品没有质量异议。
第四条涉及安全、卫生和下列有特殊要求的进出口商品不能申请免验:㈠粮油食品、玩具、化妆品、电器等;㈡列入进口商品安全质量许可证管理的商品;㈢品质易发生变化的商品或者散装货物;㈣合同要求按照商检证书所列成份、含量计价结汇的商品;㈤用于进出口危险货物的包装容器。
第五条申请人申请免验按照以下程序办理:㈠申请人应当填写并向国家商检局提交免验申请表及有关材料(包括:质量体系评审合格证书质量标准、生产工艺文件、商检合格率证明、商检机构初审意见、用户意见)。
㈡申请人申请出口商品的免验,应当经生产企业所在地的商检机构按照本办法及有关规定实施初审合格后,方可向国家商检局提出免验申请。
第六条国家商检局收到申请人提交的免验申请,经审查对免验申请作出如下处理:㈠免验申请符合本办法规定的,予以受理;㈡免验申请内容不全或者随附单证不全的,将免验申请退回申请人,限期补证。
过期不补的,视为撤销申请;㈢免验申请不符合本办法规定的,不予受理,书面通知申请人。
什么是免检制度

什么是免检制度什么是免检制度免检制度是指根据国家法律法规规定,在特定条件下,某些产品、设备、工程项目等可以免去检验检疫手续的行政管理制度。
在现代经济社会发展过程中,为了促进国际贸易、提高市场竞争力,许多国家逐渐建立了免检制度。
免检的对象可以是进出口商品、特定工业产品、新技术设备、出境运输工具等。
免检制度的设立,可以提升产品的流通效率,减少进出口企业的成本压力,促进经济的发展。
免检制度的实施不是无条件的,而是有一定限定条件的。
一般来说,免检制度包含以下几个方面的要求:首先,免检企业或产品必须符合国家的法律、法规和标准。
免检制度并不意味着企业可以任意自由,免除对产品质量和安全的监管。
相反,免检企业必须保证其产品的质量安全,符合国家相关标准。
其次,免检制度通常要求企业具有一定的信誉度和自律能力。
国家对于申请免检资格的企业或产品,往往会进行审查和评估,确保其具备一定的生产能力和管理水平。
再次,免检制度要求企业建立健全的追溯体系。
追溯体系可以帮助企业从原材料到生产过程再到产品销售的各个环节进行监管。
这样可以及时发现和解决可能存在的质量问题,保证产品的质量安全。
最后,免检制度还要求企业履行相关的报告和登记义务。
免检不代表不需要监管,相反,国家对于免检企业或产品仍然要求进行定期或不定期的监督检查,确保其正常运营和符合要求。
免检制度的实施可以为企业提供便利和机遇。
免检可以减少检验检疫程序的时间和流程,降低企业的成本压力,提升企业的市场竞争力。
同时,免检也可以促进技术创新和产业升级,加快国内企业与国际市场的对接和交流。
然而,免检制度的实施也存在一定的风险和挑战。
过度扩大免检范围可能导致产品质量和安全隐患的忽视,给消费者和社会带来不良影响。
同时,免检制度的管理也需要各级行政部门加强监管和控制,确保制度的透明和公正。
总的来说,免检制度是现代经济社会发展的需要,是一种行政管理措施。
免检的实施要求企业具备一定的资质和信誉度,保证产品的质量安全。
安全生产免检制度汇编范本
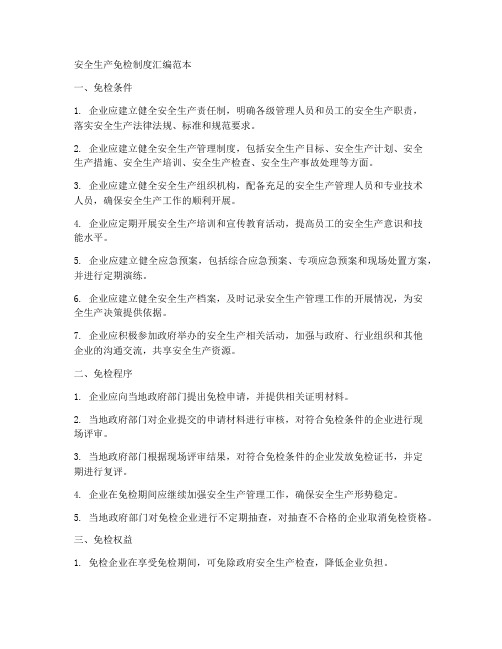
安全生产免检制度汇编范本一、免检条件1. 企业应建立健全安全生产责任制,明确各级管理人员和员工的安全生产职责,落实安全生产法律法规、标准和规范要求。
2. 企业应建立健全安全生产管理制度,包括安全生产目标、安全生产计划、安全生产措施、安全生产培训、安全生产检查、安全生产事故处理等方面。
3. 企业应建立健全安全生产组织机构,配备充足的安全生产管理人员和专业技术人员,确保安全生产工作的顺利开展。
4. 企业应定期开展安全生产培训和宣传教育活动,提高员工的安全生产意识和技能水平。
5. 企业应建立健全应急预案,包括综合应急预案、专项应急预案和现场处置方案,并进行定期演练。
6. 企业应建立健全安全生产档案,及时记录安全生产管理工作的开展情况,为安全生产决策提供依据。
7. 企业应积极参加政府举办的安全生产相关活动,加强与政府、行业组织和其他企业的沟通交流,共享安全生产资源。
二、免检程序1. 企业应向当地政府部门提出免检申请,并提供相关证明材料。
2. 当地政府部门对企业提交的申请材料进行审核,对符合免检条件的企业进行现场评审。
3. 当地政府部门根据现场评审结果,对符合免检条件的企业发放免检证书,并定期进行复评。
4. 企业在免检期间应继续加强安全生产管理工作,确保安全生产形势稳定。
5. 当地政府部门对免检企业进行不定期抽查,对抽查不合格的企业取消免检资格。
三、免检权益1. 免检企业在享受免检期间,可免除政府安全生产检查,降低企业负担。
2. 免检企业可获得政府给予的优惠政策,如税收减免、资金扶持等。
3. 免检企业可在行业组织、金融机构等方面获得更多的支持和信任。
4. 免检企业可作为行业榜样,参与政府、行业组织举办的安全生产宣传活动。
5. 免检企业可在同等条件下,优先参与政府、行业组织举办的安全生产项目投标。
四、免检期限1. 免检期限为三年,自免检证书发放之日起计算。
2. 企业在免检期限内,如发生重大安全生产事故,取消免检资格。
物流免检管理制度

物流免检管理制度一、总则为落实国家推行“放管服”改革政策,促进物流行业的发展,提高运输效率,减少企业运营成本,降低货物检测费用,我司制定本制度。
二、适用范围本制度适用于所有我司运输和物流相关业务。
三、免检申请条件1.货物性质符合国家相关规定;2.货物来源合法,无任何违禁材料;3.货物来源国或地区无传染性疾病,无疫情;4.货物运输车辆符合国家标准,无超标超载;5.货物从业人员持有相关职业资格证;6.货物运输车辆、设备符合安全标准。
四、免检申请流程1.货物运输企业准备相关免检申请资料,包括货物证明、车辆证明、从业人员资格证明等;2.提交免检申请资料给货物检测部门;3.货物检测部门对申请资料进行初审;4.初审通过后,将申请资料提交给相关部门审批;5.相关部门对申请资料进行终审;6.终审通过后,将免检申请提请运输监管部门审批;7.运输监管部门审批通过后,发放免检证明。
五、免检证明管理1.获得免检证明的货物运输企业,需按规定在货物运输车辆上粘贴免检证明标志;2.免检证明的有效期根据具体情况而定,一般在一年内;3.货物运输企业需妥善保管免检证明,如遗失需及时补办。
六、监督管理1.免检货物运输企业需按规定的运输路线、时间进行货物运输;2.货物运输车辆需按照规定的安全标准运行,运输过程中不得临时更改路线;3.货物运输企业需配合运输监管部门、货物检测部门开展不定期现场检查。
七、免检证明失效1.免检证明在有效期内,如发生违法违规行为,将被取消免检资格;2.如货物运输企业的申请资料存有虚假信息,将取消免检资格,并可能被列入不良名单;3.货物运输企业在免检有效期内连续发生不良行为,将被取消免检资格。
八、违规处罚1.货物运输企业如违规使用免检证明,将受到相应处罚;2.相关责任人员将受到严肃处理,并可能被追究刑事责任。
九、附则1.免检证明的办理、使用、管理和查验均应严格遵守国家相关法律法规;2.货物检测部门、运输监管部门应建立健全相关管理制度,确保免检证明的合规性和有效性;3.货物运输企业应加强自律,严格按照免检证明管理制度开展货物运输活动。
免检制度的利弊

项长期经常性工作,而产品免检制度放松了
质监部门的监测职责。连续三个批次的产品
抽检没问题,并不能代表其他批次的产品质
量绝对可靠;加强对不同批次产品的随时抽
查尤为必要,而一免三年不检查,显然是一
种对食品安全不负责任的行为。
三是免检制容易造成对消费者的误导。
企业享有的“免检”资格,可能只是一种产
品。个别企业为了使同类产品享受“免检”
待遇,借光造势,便会在广告宣传中弄虚作
假,放大“免检”效应。免检的是产品,还
是企业?由此极大地误导了消费者,其危害
作用更大。ቤተ መጻሕፍቲ ባይዱ
四是免检制导致了行政监管部门的职能
松懈。加强产品质量监管是质量监督部门一
二、免检制度的弊处
一是免检制从制度体系上保护了不公平竞争。面对同 样的市场环境,免检产品因为享受“国家免检” 无 须进行入市检查,可直接进入绿色通道,而非免检产 品则必须经过严格的质量检验,并在保证全检合格的 前提下获得入市资格,这在无形之中为两种不同界定 的产品设置了两套标准,人为制造了两条不同起跑线 上的差别竞争,显然对免检产品以外的其它企业构成 了一种事实上的不公平。 二是免检制掩盖了食品生产企业的不诚信行为。 因为市场环境的瞬息万变,企业的生产经营活动和产 品质量处于不断的变化之中,基于质量控制等各项管 理的难度随之加大,一旦为维护产品质量的成本投入 与追求利润最大化产生矛盾,个别企业在获得免检资 格以后,就会以牺牲诚实守信为代价追逐目前利益, 在“国家免检”的遮掩下,从事违法违规经营活动。 这时,“免检”无疑就成了个别企业掺杂使假的保护 伞,直接损害消费者利益。
二、从企业的角度理解,名牌是企 业迈向国际市场的“绿色”通行证。 卫冕“国家免检”桂冠,是企业的殊 荣,是铸造企业名牌工程的坚强基石。 在这块耀眼光环的策动下,企业应视 产品质量为其生存发展的生命线,严 格执行产品质量零缺陷管理,充分发 挥“免检”这把商战利器,把企业做 大做强,争创“百年老字号”。
- 1、下载文档前请自行甄别文档内容的完整性,平台不提供额外的编辑、内容补充、找答案等附加服务。
- 2、"仅部分预览"的文档,不可在线预览部分如存在完整性等问题,可反馈申请退款(可完整预览的文档不适用该条件!)。
- 3、如文档侵犯您的权益,请联系客服反馈,我们会尽快为您处理(人工客服工作时间:9:00-18:30)。
STS〈免检制度〉的介绍
STS是 Ship To Stock,是直接入库,不必再检验的「免检制度」,也就是购入产品由供货商处出货后,不必经过检验就可以直接入库使用。
这代表着对供货商产品品质的信赖,也代表着对产品品质的最高要求。
随着产业快速的成长,检验已经无法满足良率的要求;顾客从以前的允收标准(AQL;AcceptedQuality Level)规范到现在的零缺点 (Zero Defect)的要求,都在说明对于产品品质的要求水准愈来愈高,几乎到了「鸡蛋里挑骨头」的境界了。
因此要在这个竞争环境中保持原有的竞争优势,甚至更强的竞争力,就必须要有比同业更突出的表现,比竞争对手更好的品质水准,才能降低内部品质成本,获取更佳的利润。
以往对品质的要求是以不良率百分比为基准,可是现在的要求规格已经进入 DPPM (Defect Parts Per Million;每百万分之一的不良产品数) 的时代了,例如最近国内有几家厂商已展开对供货商要求500 DPPM的绩效,以达到免检的目标,甚至国外厂商也有要求国内供货商要达到20 DPPM 绩效的案例。
下图则将国内厂商所要求的免检管理流程 (STS) 作一个简单的介绍,以便能更了解免检制度的精神所在。
由上图可清楚看出,在正常的检验程序中,由一般的抽样开始,若在连续五批交货中都达到允收标准,则可进入减量抽样检验的阶段;接下来若是连续交货五批允收、无客户的重大抱怨、以及达到DPPM 的目标,则就可正式被列入免验入库合格的供货商了。
同样的,若是产生线上重大异常、或是连续两个月超出DPPM 的目标、或是品质成绩低于所要求的分数,则就会被取消免验的资格,变成减量检验的厂商。
而在这期间,若是连续交货五批中有一批遭到拒收,则就会成为正常检验的厂商。
如果厂商再不求改进,或是仍然依照以往的做法,连续发生两次相同的问题或是连续发生三次不同的问题,则就成为被严格检验的对象,甚至丧失资格,订单从此不再有的命运。
因此对于供货商而言,若要争取更多的订单,成为合格的免验厂商是必然的趋势。
虽然实施免检是为了节省彼此的检验成本,但相对的,若是符合免检程序之供货商的产品品质不稳定,而造成生产线或客户端发生异常时,也被要求要负起责任,通常是要自负检验费用、停线损失(生产人数x 停线小时x 每小时费用)、作业成本(协助作业人数x 作
业小时x 每小时费用)、作价费用(材料报废成本+ 管理费用)、客户索赔(客户索赔费用+ 管理费用)、及惩罚性扣款等。
如何达成STS免检的要求?
品质是企业的生命,对于所有的供货商而言,除了顾客对产品品质的要求外,本身也要有这个认知,因此当产业生命周期与来愈短时,高品质低成本就成了最佳的竞争武器。
以免检制度而言,中心厂要求卫星厂共同推动这隔制度,无异是为了要使中心与卫星厂整体提升品质与降低检验费用,使产业能真正适应环境的变迁。
但以另一个角度来思考,中心厂因为人才资源都比较充裕,可是卫星厂往往企业规模并不是很大,不仅人才资源欠缺,甚至经营管理方面都不是很成熟,若要像日本丰田汽车在推行实时供应 (Just In Time) 管理项目那般的整体动员,老实说有其困难度存在,一方面是因为国内中心厂的经营模式与日系经营模式有相当的差异,另一方面日本丰田汽车在实时供应管理方面的经验相当丰富,要将成功的管理模式推广到卫星协力厂商,其实只要将管理模式稍加作修改即可。
但相对于电子产业的免检制度来说,要使产品品质都能符合PPM的目标,其实并不是那么容易,一方面受限于以往中心厂并没有比较成熟的管理系统来协助卫星厂达成所要求的 PPM目标,另一方面则是卫星厂本身的条件并无法在短期内就可以达成要求目标。
6σ的项目计划是希望能达到 3.45PPM的目标,几乎是零缺点的境界,虽然截至目前为止,国内、外还没有一家企业能达到6σ的水准,纵使是全球竞争力排名第一的奇异公司,也只号称达到5.5个σ而已,但这已经使奇异公司节省了好几百万美金的成本,甚至超过上千万美金的金额,而且是目前推行6σ项目计划最成功的企业之一。
因此只要遵循成功的轨迹与模式,纵使无法达到3.45 PPM 的目标,但要达到几百个或上千个PPM的目标要求其实并不是一件难事,而且6σ的推行手法在经过国际上多家知名企业的推陈出新后,已经相当成熟了,从摩托罗拉、3M到奇异、杜邦,可说已经是一套具有相当可信度的品质保证的工具。