工业4.0智能制造工厂:美菱M线冰箱U壳自动化方案---李家浩7.22
美菱冰箱制造流程

美菱冰箱制造流程
•4、热交换器成型: •冷凝器、蒸发器总成外协;防凝管自制。 •冷凝器:钢管(镀铜、镀锌) •蒸发器总成:冷蒸使用铝管,冷冻使用钢管/铝管. •防凝管:铜管、钢管
美菱冰箱制造流程
•5、门体/箱体预装 •门体预装:冰箱的最大变化就在门体上,不同的结构会有不同的预 装流程。最基本的就是:预装 堵漏 预热 待发泡。 •箱体预装:是以侧板组装为主流程的工艺路线
美菱冰箱制造流程
➢ 加热设备 • 热塑性塑料片材和薄膜的真空吸塑成型过程,主要工序之一就是片材
加热。电加热的持续时间和质量取决于加热器的结构,辐射表面后温 度传热的热惯性,片材与加热器间的距离,辐射能吸收系数,加热器 表面的特性以及材料的热物理性能。常用的加热器有电加热器、晶体 辐射器和红外线加热器。
美菱冰箱制造流程
1、板材成型:
母料——搅拌——挤出——压延分割——电晕——切边——下料——包 装
真空成型工 艺 外感
钢性 耐久性
成本 装配 抗化学性 寿命
ABS
HIPS
成型工艺要求较严,加工困难;可直接发泡, 成型工艺与加工容易,需
与聚氨酯粘接良好。
电晕处理。
光泽好,对食品无污染,清洁后不留痕迹, 光泽不如ABS好 吸灰
美菱冰箱制造流程
真空吸塑的组成 夹紧设备 • 塑料片材成型时,片材被固定在夹紧装置上。在热成型的通用型和复合型的
热成型机上多采用便于固定各种尺寸片材的夹紧装置。有的是整个成型机配 一套夹紧框架。 • 夹紧装置可分为两类:一类是框架式,另一类是分瓣式。框架式夹紧装置由 上、下两个框架组成。片材夹在两个框架之间。框架打开时,下框架一般保 持固定状态。各种类型单工位成型机上框架的下部直接固定在成型室上。用 手装型坯和成品取出的手动和半自动成型机上,当框架尺寸很大时,都装有 在框架打开范围内的安全操作装置。对成型滑移性较大的型坯,要求夹紧力 能在比较宽的范围内调节,为此,采用两个包胶辊,用弹簧相互压紧,并配 有压力调节装置。连续拉片成型机的夹紧是两边拉链与前后闸的共同作用。 • 夹紧装置最好采用自动控制,以期动作迅速,可有助于提高制件质量和效率。
对开门U形冰箱壳成型生产线设计

( 4 ) 生产节拍 : 3 5 秒/ 套。
1 . 2 产 品成 型 工艺分 析
u型冰箱侧板包括多个装配槽形 、 定位孔 、 翻边 、 拼角和重叠边等 ,综合分析其加工过程应包括 冲切 落料 、 成型轧成型和折弯等多项技术 , 设 备包括 : 上 料工位 、 冲切工位 、 翻转工位 、 成 型轧工位 、 翻边 打 z 工位 、 贴敷工位 、 打 u工位 、 机械手下料工位 , 以及液 压站和 P L C电气控制操作台… 。
利用伺服电机驱动的宽皮带传送板料 , 同时 由工 人完成箱体内部各种管路的贴敷工作。 床身长 5 . 5 米, 运行速度约为 0 . 2 m / s , 由型材焊接而成 , 电机驱动大 径滚筒带动皮带传送 , 皮带的松紧可由张紧滚筒调节。
1 冰箱侧板概述
冰箱侧板分为拼装板 和 u形壳体两种 , U形壳 体则可省去盖板 , 直接和背板 、 门板装配成壳体 , 不 仅节省了装配过程 ,也避免了装配误差带来的各 种 变形 , 更达到了外型美观的效果。 但 u形壳体 的侧面 和顶面交界点处拼角的美观要求 ,给成型工艺的设 计和设备加工装配精度提出了更高的要求。本 U壳 冰箱侧板成型生产线为全 自动生产线 ,主要完成美 的集团华凌公司新基地项 目 对开门冰箱及大型冰箱 的 U形箱壳冰箱侧板 的生产任务 。 1 . 1 技 术参 数 ( 1 ) 功能 : 经过冲切 、 成型轧、 折弯等工序将平薄 板加工成符合尺寸形状要求的冰箱侧板壳体。 ( 2 ) 侧板材料 : P C M预涂钢板。 板料厚度 : 0 . 4 m m 0 . 6 a r m;宽度 范围: 5 0 0 m m~1 0 0 0 m m f 成型后尺 寸) ; 深度范围 : 5 0 0 m m~8 0 0 m m ( 成 型后 尺寸) ; 长度
美国U-Line公司的U304BW-1B 304钢内外厚实胶囊冰箱说明书

Overall Dims
W(in.) x D(in.) x H(in.)
23-3/4” 26-7/8” 33-1/2”
25-3/8” 25-3/8” 16”
CONTACT US: phone 888.905.7463
24"
24"
NOTE:
33
1 2
"
is the height of the undercounter unit with the leveling legs screwed all the
standing up • 1” R-Tech high-performance insulated walls • Includes 5 individual condiment trays
• Convenient drain with 1/2” NPS connection and rubber stopper
way in. Leg levelers can add 3/4” of
height when fully extended.
Electrical Requirements
115V, 60Hz., 1 Phase, 1.1 amps
n/a
Aspire by Hestan products are approved for outdoor use only. Hestan Commercial Corporation reserves the right to change materials and specifications without notice.
OUTDOOR REFRIGERATOR
16
1 4
"
美菱冰柜 BC BD-200DTP 使用说明书

全国统一服务热线: (连拨,请勿加区号)4008 111 6664006 111 666图形仅为示意以实物为准产品型号:制冷部件电子电气部件隔热材料制冷剂印刷组件铅(Pb)汞(Hg)六价铬 CrVI )(多溴联苯(PBB)多溴二苯醚(PBDE)镉(Cd)()箱体及其组件门体及其组件部件名称有害物质本表格依据SJ/T11364的规定编制。
: 表示该有害物质在该部件所有均质材料中的含量均在GB/T26572规定的限量要求以下。
: 表示该有害物质至少在该部件的某一均质材料中的含量超出GB/T26572规定的限量要求。
但对于显示 的项目,我公司按照欧盟RoHS采用了豁免指标符合欧盟RoHS标准的要求。
有毒有害物质含量表使用说明书及保修凭证BC /BD -200DTP本产品已通过国推认证,绿色产品标识可扫描右侧二维码进行查询。
RoHS 扫一扫,查询RoHS认证注:某些特征和装置的说明可能与您的冰柜本说明书仅为冰柜示意图, 不完全一致,请以实物为准.为避免意外触碰导致错误设置温度,部分冰柜采用特殊的无极旋钮设计。
需要旋转旋钮时,用工具插入旋钮中的旋槽旋转(通常使用一元硬币即可)。
产品概述电源指示灯(绿灯)门体门把手门内衬塑料衬口铰链箱体通风罩吊篮产品概述 安全注意事项 安放环境、初次使用 食物贮存、疑难解答 维护保养 技术数据、装箱单与电气原理图保修政策录目 产品执行标准:★ 由于产品的改进,您所购买的美菱冰柜可能与说明书中的介绍不完全一致,请以实物为准,谨此致歉。
尊敬的美菱用户:感谢您选择美菱冰柜!为了您安全、方便地使用及合理地维护,请您在使用前仔细阅读本使用说明书,并妥善守本说明书操作规程及注意事项。
若冰柜出现故障,请勿自行拆卸修理或交由本公司未授 及保修凭证》上的联系方式与我们客服电话联系。
告之您的姓名、地保存以备查看。
请遵权的维修部门修理,请按本《使用说明书址、电话、冰柜型号、购机时间、故障现象等,我们将竭诚为您服务。
美菱风冷冰箱202升的使用说明书

美菱风冷冰箱202升的使用说明书一、外观和结构美菱风冷冰箱202升采用了现代简约的外观设计,外壳采用高强度金属材料制成,具有耐用性和美观性。
冰箱内部分为冷藏室和冷冻室两个部分,合理分隔,可以满足不同食材的冷藏和冷冻需求。
冷藏室采用了多层网格设计,可以根据需要调节层板高度,方便存放不同高度的食物。
冷冻室则配备了冷冻盒和冷冻架,可以容纳各种冷冻食品。
二、温控和除霜功能美菱风冷冰箱202升具有精确的温度控制功能,可以根据用户的设定来调节冷藏室和冷冻室的温度。
用户可以根据需要将温度调节在适宜的范围内,保持食物的新鲜度和营养价值。
此外,冰箱还配备了自动除霜功能,可以定期自动除去冰箱内部的霜,保持冷藏室和冷冻室的良好状态。
三、储存和使用注意事项1. 在使用前,请将冰箱放置在通风良好的地方,避免阳光直射和与热源接触。
2. 冰箱背后的通风孔不要被遮挡,以确保正常的散热和通风效果。
3. 冰箱内部不宜过度装满食物,以免影响空气流通和制冷效果。
4. 不要将过热的食物直接放入冰箱,应等待其自然冷却至室温后再放入。
5. 避免在冰箱内放置过多的开放式容器,以防止食物散发异味和交叉污染。
6. 定期清洁冰箱内部和外部,可以使用中性洗涤剂和柔软的布进行清洁,避免使用腐蚀性或磨损性物质。
7. 冰箱门密封条应保持清洁和灵活,避免受损或老化影响密封效果。
8. 冰箱不应长时间处于未使用状态,应定期通电并保持冷藏和冷冻功能的正常运行。
四、故障排除和维修1. 如果冰箱无法正常运行或温度无法调节,请检查是否有电源故障或线路故障,可以尝试更换插座或检查电源线是否接触良好。
2. 如果冰箱发出异常噪音或震动,可能是因为冰箱不稳或内部零部件松动,应检查并适时进行调整和维修。
3. 如果冰箱出现漏水情况,请检查是否有水箱或水管破损,应及时更换或修复。
4. 如果冰箱出现严重故障或无法自行解决的问题,请及时联系售后服务中心进行维修和处理。
总结:美菱风冷冰箱202升是一款功能齐全、性能稳定的家用电器,其精确的温控和除霜功能可以保持食物的新鲜度和营养价值。
美菱公开“水分子激活保鲜技术”.创造M_鲜生冰箱

47电器2017/12优化。
“最近一个热点是无人商铺。
无人商铺这个场景对空调的需求到底有什么不同?我们观察到,所有无人便利店里,顾客停留时间只有2~3分钟,就是扫码,开门进去,拿完东西结账然后出来。
另外,我们普通的店里面都有店长,管理人员控制空调,无人便利店里面是没有的。
于是,我们发布了首款无人商铺用中央空调。
当时用户最关注的点就是节能,海尔物联网中央空调可以解决这个痛点。
”杨宝林举例说明:“我们研发了自适应技术,可以根据室外的温度和湿度自动调节室内的舒适度。
以无人商铺为例,室外35℃的环境不应该影响到26℃的室内环境。
行业内数据显示,人体感觉比较舒适的温差在5℃就够了。
同时,我们发现,普通便利店可能吃饭时间人最多,但无人便利店里面人流量高峰期是凌晨,海尔物联网中央空调可以做到根据人流负荷自适应调节。
”除此之外,据杨宝林介绍,海尔可以为用户提供物联网能源模块,把用户所使用的其他品牌的中央空调接到海尔平台上面,实时了解包括节能数据在内的用户数据。
海尔中央空调还可以提供全生命周期的节能服务。
在整个用户使用过程当中,海尔可以做到随时给用户推送更节能运转程序。
王利表示:“这间工厂让我最满意的是,工厂真正实现了全流程节点,让每一位员工都跟用户零距离,员工更加关注用户需求和感受。
”器曾担任长虹空调总经理的吴定刚,在出任美菱公司总裁后的第一次大场合亮相,就抛出了备受业界瞩目的冰箱保鲜新技术。
此项被命名为“水分子激活保鲜技术”的最新研发成果,在11月初全国最热的三亚,向众多经销商和媒体进行充分展示。
美菱此举,得到业界众多技术专家的关注。
美菱方面表示,这一技术不仅触及了行业的保鲜极限,还将引发行业第三次保鲜革命。
美菱公司副总裁钟明博士表示,水是生命之源,生命体70%以上由水分子构成。
“水分子激活保鲜技术”可以使食物中的水分子振动,激活水分子等同于激活细胞,可快速降温、减少食物细胞破坏、抑制细菌滋生,从而延长食品保鲜期。
冰箱制造加工工艺流程简介
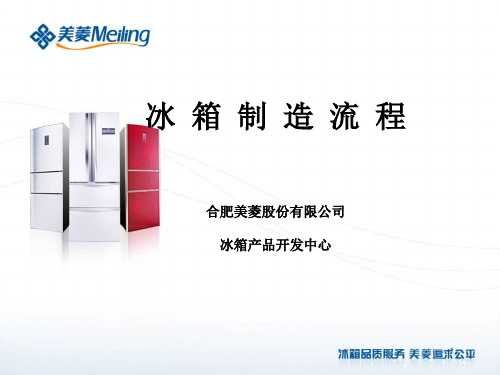
3、箱体:分拼装式、整体式。
绝热材料 电冰箱发展至今,其绝热材料经历了木屑、硅藻土、超细玻璃
棉、聚苯乙烯泡沫,直至现在的硬质聚氨脂泡沫,其导热系数越低,绝 热性越来越好,使电冰箱绝热层越来越薄。
聚氨脂泡沫:多异氰酸脂、多元醇、崔化剂、稳定剂、发泡剂等。 聚氨脂泡沫老化情况:
美菱公司冰箱制造工艺流程
一、冰箱知识简介
1、电冰箱定义
家用冰箱,不管是单门还是双门,不管是直冷还是间冷,不管是 普通CFC还是无CFC环保冰箱,虽然其外形多样,千差万别,但主要结 构大致相同,即家用电冰箱一般均由以下四部份组成: 箱体(包括门体) 制冷系统 电气系统 附件
2、家用电冰箱的分类
1)按门体分类 单门:一个门、冷藏室(0℃-8℃)、冷冻(-6℃— -12 ℃),可冷冻食品
及制冰。 双门:其冷冻室和冷藏室各有一个门,冷冻室< -18℃,具有速冻功能。
冷藏室:0-10 ℃ 三门:冷冻、冷藏、果菜盒(8-14 ℃ )、冰温室(-2-3 ℃)或变温
室。 四门:各温度度点下的保质、保鲜室 五门:各温度度点下的保质、保鲜室
4、制冷系统
5)干燥过滤器
分为两种:单孔进口、双孔进口 铜制壳体两端设置过滤网(80-120目的金属网)。
4、制冷系统
电冰条用的过滤器器都采用球状分子筛作为干燥剂,根据所用工质的不 同选用不同的分子筛吸附口么径。
小
分子大小
大
XH-9(3A)
XH-7
XH-5(4A)
选择的原则:比水分子直径大,比制冷剂分子直径小
开始 0.018 W/m.K
一个星期 0.025 W/m.Kຫໍສະໝຸດ 一个月 0.025 W/m.K
美菱

工商2班 张刚茹 08工商 班 0816105013 工商
内容概要
6建议 建议 1公司简介 公司简介
5外部公共关系 外部公共关系
概要
2环境分析 环境分析
4管理创新 管理创新
3发展战略 发展战略
1公司简介
1 2 3 4 美菱股份有限公司简介 历任领导与公司发展 部分荣誉展示 企业文化
中 பைடு நூலகம் 冰 箱 大 王
世 界 白 电 航 母
2环境分析
建议 外部公共关系
美菱股份有限公司
管理 创新
创新管理案例分析
企业 简介
发展 战略
环境 分析
2环境分析
微观环境 五力模型
• • • • • • 政治法律环境 经济环境 社会文化环境 技术环境
新 进 入 者 供 替 应 代 方 品 购 买 者
内部分析 SWOT分析 分析
在良好的研发基础上, 在良好的研发基础上, 美菱技术研发成就卓著 服务创新和合资营销 抓住家电下乡良机
公司发展较平稳
1.3部分荣誉展示 1.3部分荣誉展示
1.4企业文化 1.4企业文化
企业 精神 企业 宗旨 企业 价值观 企业 愿景
亮剑 创新 奉献 团队
员工满意 客户满意 股东满意
诚信 纪律 责任 公开 公平
1.2历任领导与公司发展
4、短暂的二度接手——王家章 、短暂的二度接手 王家章
2005年8月2日,公司董事会审议通过了有关决议, 年 月 日 公司董事会审议通过了有关决议, 鉴于董事长顾雏军不能正常履行董事长职权, 鉴于董事长顾雏军不能正常履行董事长职权,决定 由公司副董事长王家章代行董事长职权。 由公司副董事长王家章代行董事长职权。 2005年,年产65万台冰箱新生产线建立投产 年 年产 万台冰箱新生产线建立投产。 万台冰箱新生产线建立投产
美菱540冰箱总体设计方案

合肥美菱股份有限公司出口大容积540系列冰箱总体设计方案编制:唐涛审核:李毅会签:王靖宇批准:韩百顺美菱研究院2004年7月目 录1 产品基本要求……………………………………………………………………………… 1.1规格……………………………………………………………………………… 1.2外观……………………………………………………………………………… 1.3结构……………………………………………………………………………… 1.4性能………………………………………………………………………………2 具体技术方案……………………………………………………………………………… 2.1容积……………………………………………………………………………… 2.2外观……………………………………………………………………………… 2.3型号……………………………………………………………………………… 2.4结构………………………………………………………………………………3 主要零部件………………………………………………………………………………4 主要自制件工装模具………………………………………………………………………5 主要工艺问题……………………………………………………………………………… 5.1 全冷藏箱温差……………………………………………………………… 5.2 瓶框翻盖结构………………………………………………………………6 工作量及分工………………………………………………………………………………附件 设计草样附件1 平面效果图附件2 CAD 图 附件3 装箱图3 3 3 3 3 3 34 4 4 6 7 7 7 7 7出口大容积540系列冰箱总体设计方案1产品基本要求1.1规格四款540系列冰箱,分别为:双门冷藏冷冻箱、单门冷藏箱、单门冷冻箱、单门带四星冷冻室冷藏箱;要求双门冰箱容积在210升左右,其余冰箱容积按相同整机高度设计。
美菱实习作文冰箱组装

美菱实习作文冰箱组装英文回答:As an intern at Meiling, I had the opportunity to participate in the assembly process of refrigerators. Itwas an interesting and valuable experience that allowed meto gain insights into the manufacturing industry.The first step in the refrigerator assembly process isto gather all the necessary components and materials. This includes the fridge body, doors, shelves, drawers, and various electrical and mechanical parts. Each component is carefully inspected to ensure its quality and functionality. Once all the components are ready, the actual assembly process begins.The assembly process starts with attaching the doors to the fridge body. This requires precision and attention to detail to ensure that the doors are properly aligned and securely attached. Once the doors are in place, the shelvesand drawers are installed. This involves adjusting the height and position of the shelves to accommodate different storage needs. The electrical and mechanical parts, such as the compressor and thermostat, are then installed and connected.After the components are assembled, the next step is to test the functionality of the refrigerator. This includes checking the temperature control, ensuring that the compressor is working properly, and testing the door seals. Any issues or defects are identified and addressed before the final inspection.Once the assembly and testing process is complete, the refrigerator undergoes a final inspection to ensure its quality and performance. This includes checking for any cosmetic defects, verifying that all components are properly installed, and conducting a thorough functionality test. Only after passing the inspection is the refrigerator ready for packaging and shipment.中文回答:作为美菱的实习生,我有机会参与冰箱的组装过程。
冰箱制造加工工艺流程简介
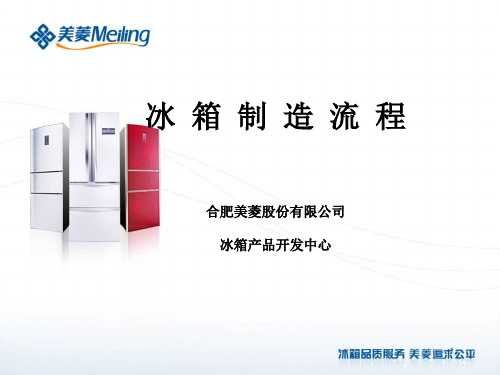
开始 0.018 W/m.K
一个星期 0.025 W/m.K
一个月 0.025 W/m.K
3、箱体:分拼装式、整体式。
发泡剂的替代
CFC-11(ODP=1,GWP=1,POPC)
沸点 导热系数 可燃性 ODP GWP
HCFC-141B (美国、日本)
CFC-11 23.8 ℃ 8.7mw/m.k
无 1 1
制冷系统热交换器 用于R12系统的冷凝器和蒸发器同样适用于R600a系统,但需做必要的匹配调整。
材料相容性 异丁烷与钢、紫铜、黄铜、铝、氯丁橡胶、尼龙和聚四氯乙烯相容的,这些相容的 材料均可用于R600a制冷系统,天然胶和硅因R600a不相容,故不能用于R600a系统。
4、制冷系统
毛细管 用于R12的毛细管同样适用于R600a系统,只是流量稍有区别。 干燥过滤器 目前用于R12系统的干燥剂均可用于R600a系统中,生产维修中考虑到R600a的 结构性质要求使用专用干燥过滤器XH-9. 充注量 异丁烷的充入量相当于R12的40%左右,因此需要高精度的制冷剂灌注设备, 校准设备。 电磁阀 用于R12系统的电磁阀同样适用于R600a.。 冰箱的安全性能 不管系统是否泄漏,所有打火的区域R600a的浓度不能达到爆炸极限。 因R600a的比重比空气重,因此要求维修现场保证良好的通风条件。 在灌注制冷剂时,为避免可能产生静电从而产生打火,要求设备必须可靠接 地,所有的接线牢固,绝对不允许有接错现象。
4、制冷系统
冰箱使用的制冷剂为中温制冷剂
项目
制冷剂
t0(℃)
PK(MPa)
举例
高温制冷剂
中温制冷剂
低温制冷剂
0—70
-60—0
≤ -60
≤ 0.3
美菱冰箱说明书手册365

产品型号及规格
本说明书适用于美菱冰箱BCD365WPC型号。
该型号冰箱采用对开门设计,总 容积为365升,其中冷藏室容积 为225升,冷冻室容积为140升。
冰箱外观尺寸为宽790mm×深 666mm×高1830mm,适合家
远程控制功能演示
温度调节
01
用户可以通过手机APP远程控制冰箱的温度,随时随地调节冷
藏室和冷冻室的温度,满足不同食物的存储需求。
模式切换
02
根据实际需求,用户可以在手机APP上切换冰箱的工作模式,
如速冷模式、速冻模式等。
故障诊断与报修
03
当冰箱出现故障时,用户可以通过手机APP进行故障诊断,并
在线报修,享受便捷的售后服务。
美菱冰箱说明书手册365
目录
• 产品概述与特点 • 外观结构与操作指南 • 冷藏冷冻技术解析 • 智能互联与远程控制 • 清洁保养与故障排除 • 附件选购与使用指南
01
产品概述与特点
Chapter
Байду номын сангаас
美菱冰箱品牌介绍
美菱是中国知名的家电品牌,专注于制冷行业多年,拥 有丰富的研发、生产经验。
美菱冰箱以其卓越的品质、创新的技术和完善的售后服 务赢得了广大消费者的信赖。
际需求进行节能设置。
04
智能互联与远程控制
Chapter
智能互联技术应用
1 2 3
物联网技术 美菱冰箱采用先进的物联网技术,实现冰箱与互 联网的连接,为用户提供智能化、便捷化的服务。
大数据分析
通过收集用户使用数据,利用大数据技术进行分 析,为用户提供更加个性化的使用建议和节能方 案。
美菱破门体自动化实现智能制造

美菱破门体自动化实现智能制造当种种工业4.0概念、智能制造模式正不绝于耳之时,在工序相对复杂、劳动非常密集的冰箱制造业,这种生产模式的改变显得有心而无力。
如何挖掘智造的潜力?怎样改变传统的人工生产模式?在家电行业里每个传统的中坚力量正在找寻企业创造的答案。
站在专业制造冰箱企业——美菱的智能豪华冰箱生产线前,被头顶无处不在的网格惊住,密密麻麻的网格,各种井然有序流动门体,自动化流转智能小车,记者正置于另一个时空。
很难想象这是一个劳动密集型的家电制造型工厂,所有的普通工序变得自动化,网格就像蔓延开来的触角,更高效的传输每一个关键性的冰箱门体。
(美菱冰箱自动化门体配送系统)事实上,在复杂的冰箱制造行业,门体柔性自动化技术一直成为各家企业竞逐的主流智能制造战场之一。
类似美菱的空中互联门体自动化工程,采用多阶容错、RFID等先进技术实现智能柔性控制,通过精准的信息计算即可实现各类冰箱门体的任意柔性调配,在产品超高稳定性的基础上,实现门体调配的高效率运转。
有业内人士称,复杂的冰箱制造业正在迎来变天,门体自动化技术完成的是智能制造的落地,其或将成为行业变革的又一突破口。
面对如此繁杂的门体自动化智造系统,在操作现场的美菱智能制造所所长胡明勇表示,互联网时代,智能制造正在改变着企业的常规运营方式,美菱属于主动去推翻传统制造的开拓者。
在该类门体柔性自动化系统上,美菱在行业内属于首次技术尝试,每一个环节都充满着挑战,同样也是机遇重重,我们想通过自动化技术的改变,在提升效率减少浪费同时,为行业的转型抛砖引玉。
在门体自动化的强势破局之下,美菱内部的智能制造建设正在形成一连串的连锁反应。
据了解,美菱智能制造从各方向开展建设,主要包括信息化、自动化以及智能物流体系,逐步实现产品制造过程的监测、反馈、动态预警,最终实现制造透明化、智能化、柔性化制造工厂。
(自动化系统中流转的门体)事实上,美菱在智能制造揭开企业创新制造一角的同时,更多的变化正在企业内部铺陈开来。
美菱冰箱 BCD-527WPCX 使用说明书

美菱微信美菱微博使用说明书BCD-527WPCX产品概述产品特点...................................................................................... 各部分构件名称..........................................................................使用须知安全注意事项......................................................................... 使用准备..............................................................................使用说明功能介绍............................................................................. 食物储藏............................................................................ 食物储藏小常识.........................................................................保养与服务保养与清洁......................................................................... 冰箱工作时的非故障现象、简单故障分析与排除..............主要技术参数、装箱单产品中有害物质的名称及含量表保修凭证技术参数.................................................................................. ............................................产品中有害物质的名称及含量表 保修凭证.................................................................................. 装箱单......................................................................................目录123~67~1011~1314~161718~1920~2122242523尊敬的用户:感谢您选择、使用美菱冰箱!★ 为了您安全、方便地使用及合理地维护,请在使用前仔细阅读本 使用说明书,并妥善保存以备查看。
- 1、下载文档前请自行甄别文档内容的完整性,平台不提供额外的编辑、内容补充、找答案等附加服务。
- 2、"仅部分预览"的文档,不可在线预览部分如存在完整性等问题,可反馈申请退款(可完整预览的文档不适用该条件!)。
- 3、如文档侵犯您的权益,请联系客服反馈,我们会尽快为您处理(人工客服工作时间:9:00-18:30)。
注:控制系统设置有自动清空
模具存储功能,点击此功能按 钮后,升降移载自动升降,移 载机构自动将模具依次从存储 区转移到上模区域,清空模具 存储货架。
自动换模方案分析
1、采用堆垛的方式存储模具---节省空间;
2、采用上下两层结构的取模机构,减短了换模的时间 ---利用空间的置换,换得时间;
10.移载托举2复位,模具8到达移载机构平台;
11.提升机构带动移载机构上移一个工位, 模具6到达预备上模区
自动上冲模流程
提升机构
模具8 前置 挡块
模具6
“模具8”---模具8 此时在移载机构上部
模具7
“模具6”---模具6 此时在冲压台上
模具5
模具4 模具3
模具2 模具1
人工上 模具位置
旋转 下压气缸
M线冰箱U壳自动化方案
A
工厂需求
B
产线位置区域
C
冰箱U壳自动换模方案
D
U壳钢板自动上料方案
E
U壳物流输送
客户需求 实现M线U壳自动化 基本功能:
信息化: 实现控制系统对U的自动生产、调度; 自动化:
1)实现冲模的快速换模;
2)U壳钢板的自动切换;
3)U壳的自动物流与存储;
按照1500台,每天工作时间10小时,节拍为24秒
钢板自动上料
1、当一种钢板缺料时,人工 点击操作台,选中该型钢板按 钮,该型钢板的平台沿着地轨 滑出;系统接收上料信号,不 再发出更换该型冲模的指令;
2、工人驾驶叉车将新的钢板 装置到该型钢板底盘上,输入 钢板的型号与尺寸修正系数;
3、上料完成后,点击按钮, 该钢板平台复位,进入工作区
4、系统接收反馈信号,开始 发出更换该型冲模的指令;
每批次的钢板尺寸有 差异,所以人工输入 尺寸修正系数,便于 换模时,模具自动变 换位置
每套模具的 底部均设置 有二维运动 模组,由伺 服电机驱动 , 快速实
现模具 的前后 、 左右移动
U壳物流---自动上挂
U 壳上挂 机器人
1、U壳成型后,机 器人将其放在输送机 上,U壳向左输送到 人工上挂点;
2、人工根据系统提 示,输入U壳类型, 机器人将U壳上挂到 积放链上的U壳输送 挂具上;
丝杠 导轨
(伺服电机可通过动丝杆 驱动模具整体左右移动)
移载机构
取料机构分上下两 层, 下层(移载托举1) 负责上料和取料;
上层(移载托举2) 负责模具从冲压台 退模
ห้องสมุดไป่ตู้
同步带 提升机构
移载托 举2
同 步 带 夹 紧 块
移载托举1
移载托举在此处托起模具
1.电机带动同步 带,驱动取料机 构上升到取料位置;
人工上 模具位置
1.换模系统接收控制系统换模 (例如:将工作的8号模具换成 6号模具)指令;
2.提升机构带动移载机构上移到 模具6存储区;
3.移载托举1伸出,到达模具6 侧边空隙;
4.提升机构带动移载机构上移 20mm,向上托举模具6离开存 储平台;
5.移载托举1复位,模具6到达 移载机构平台;
6.提升机构带动移载机构下降到 最底部等待换模命令;
冲模自动上料
模具8
模具7 模具6
模具5 模具4 模具3 模具2 模具1 用叉车将模具放 置在上模位置
人工上 模具位置
1.用叉车将模具放置在上模位置;
2.升降机构带动移载机构到达最底 部,移载托举1将模具托举进入移载 机构平面;
3.人工在触摸屏选择模具存储区域, 点击确认,升降机构带动移载机构到 达相应模具存储区;
产线区域位置
U壳区域
U壳成型共有10个冲模工位,每个工位 的模具种类约有20种,每天使用大约6种模 具,产线节拍为24S。
单体换模机构三维
升降机构
移载机构
压机
现有伺服电机的 转速与功率较小,此 处应更换转速高、功 率大的电机,保证15 秒内的换模节拍~
模具存放架(可存放 8组,高约2.3米)
每个模具加装一个底 板,保证所有模具底 部尺寸相同。
U壳钢板自动上料
钢板 8组滑车 地轨
龙门架
滑动取料 在原有基础上,左侧
增加两套滑板机构;
右侧增加四套滑板机 构,每套滑板机构宽 度为1.1m
输送机 自动换模组 钢板
U壳钢板自动上料
采用电机—齿条的传动方式,线速度2.4米/秒
钢板 上料 位置
工作 位置
钢板抓取机构的平移, 采用电机—齿条传动的 方式,能保证所有钢板 在15秒钟内的切换
2.移载机构驱动移载 托举伸出,到达模具 侧边空隙; 3.提升机构带动移载 机构上升,模具向上 脱离模具存放架; 4.移载机构复位,模 具到达取料机构内
自动取模具流程
提升机构 移载托举2 移载托举1 移载机构
模具8
“模具8”---模具8 此时在工位上 模具7
模具6 模具5
模具4
模具3 模具2
模具1
1、控制系统发送换模 信息,自动换模组在 15S内完成自动换模( 换模方式包括位置的改 变和模具的变更两种)
2 、控制系统发送取料 型号信息,取料机械手 运动到相应钢板上方待 命;
3、当上一个钢板进入 冲模区域后,取料机械 手吸取钢板、复位。将 钢板放到输送机上,输 送机带动钢板进入冲模 区域,完成U壳的自动 成型。
自动卸模流程
提升机构
模具8 移载 托举2
“模具8”---模具8 此时在工位上
模具7
“模具6”---模具6此 时在移载机构最底部
模具5
模具4 模具3
模具2 模具1
人工上 模具位置
模具6
前置挡块
旋转 下压气缸 7.两侧的旋转下压气缸旋转松开模具8;
8.移载机构上层的移载托举2向左伸出,到达 模具8侧边空隙; 9.提升机构带动移载机构上升20mm,向上托举模具8 离开冲压台;
3、设计模具自动读入软件(人工输入或扫码输入), 实现控制系统对模具的实时调配;
4、在冲模底座增加丝杆,实现冲模左右平移可调,减 轻换模人力;
5、原来手工换模的时间大于10分钟,采用自动换模方 案后,换模时间可缩短至15S;
6、此自动换模方案,对原有压机和冲模底盘基本没有 改动,占用空间小,在现有基础上改进成本更低。
12.移载托举1托举模具6进入冲压工作台区域, 前置挡块对模具6进行限位;
13.提升机构下降20mm,将模具6放置在冲压工 作台上,移载托举1复位;
14.冲压工作台两侧的旋转下压气缸转动,压紧 模具6,模具更换完成;
15.提升机构将移载机构提升到模具8存储区, 移载托举2将模具8移载到存储平台,提升机构 下移20mm,移载托举2复位。移载机构复位;