某型柴油机高压油管振动优化
高压油管开裂原因分析及改进建议
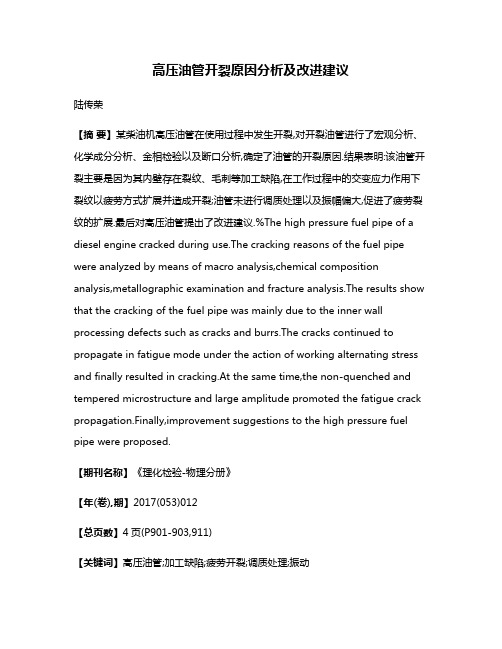
高压油管开裂原因分析及改进建议陆传荣【摘要】某柴油机高压油管在使用过程中发生开裂,对开裂油管进行了宏观分析、化学成分分析、金相检验以及断口分析,确定了油管的开裂原因.结果表明:该油管开裂主要是因为其内壁存在裂纹、毛刺等加工缺陷,在工作过程中的交变应力作用下裂纹以疲劳方式扩展并造成开裂;油管未进行调质处理以及振幅偏大,促进了疲劳裂纹的扩展.最后对高压油管提出了改进建议.%The high pressure fuel pipe of a diesel engine cracked during use.The cracking reasons of the fuel pipe were analyzed by means of macro analysis,chemical composition analysis,metallographic examination and fracture analysis.The results show that the cracking of the fuel pipe was mainly due to the inner wall processing defects such as cracks and burrs.The cracks continued to propagate in fatigue mode under the action of working alternating stress and finally resulted in cracking.At the same time,the non-quenched and tempered microstructure and large amplitude promoted the fatigue crack propagation.Finally,improvement suggestions to the high pressure fuel pipe were proposed.【期刊名称】《理化检验-物理分册》【年(卷),期】2017(053)012【总页数】4页(P901-903,911)【关键词】高压油管;加工缺陷;疲劳开裂;调质处理;振动【作者】陆传荣【作者单位】海军驻上海711所军事代表室,上海 201108【正文语种】中文【中图分类】TK428;TG115某柴油机高压油管在使用过程中发生开裂。
高压油管系统的研究与优化

高压油管系统的研究与优化近年来,高压油管系统已成为发动机研发领域中的重要课题。
与传统进气系统不同,高压油管系统采用高压直喷技术,将燃油喷射到气缸内燃烧室中,使得发动机的燃烧效率和动力性能都有了明显提升。
在本文中,我们将探讨高压油管系统的研究与优化,旨在为车辆制造商、工程师和研究人员提供一些有用的信息和建议。
一、高压油管系统的构成及原理高压油管系统主要由以下几个部分组成:高压油泵、高压油管、喷油嘴等。
其中高压油泵是整个系统的核心组成部分,其作用是将油箱中的燃油送到高压油管中,形成高压燃油,在喷油嘴的作用下,将燃油喷射到气缸内部。
高压油管系统的工作原理非常简单。
当油泵启动后,通过泵体内的柱塞和气体压力交替运动,将低压油从油箱中吸入,然后将其压缩成高压油,再将其送到高压油管中。
高压油管中的压力大约在1000~2000bar之间,主要与发动机型号、工作负荷和驾驶员的车速等因素有关。
二、高压油管系统的优化1. 提高燃油的喷射效率燃油的喷射效率直接关系到发动机的动力性能和燃油经济性。
因此,在设计高压油管系统时,需要考虑如何提高燃油的喷射效率。
一种常用的方法是采用缸内直喷(GDI)技术,该技术可以更加精确地控制燃油的喷射时间和喷射量,从而提高燃油的利用率。
此外,还可以采用先进的燃油喷嘴设计,如常规燃油喷射器、共轨喷油系统或直接喷射式燃油喷嘴等。
2. 降低系统的噪声和振动高压油泵在工作时会产生噪声和振动,这会对发动机的寿命和性能产生不利影响。
因此,在优化高压油管系统时,需要考虑如何降低系统的噪声和振动。
一种有效的方法是采用先进的降噪材料,如橡胶和聚酰亚胺等。
此外,还可以采用减震和减振技术,如阻尼器和减振器等。
3. 提高系统的可靠性和稳定性高压油管系统在不同的工作条件下可能会遇到各种问题,如逆流、管壁积碳等。
这些问题会影响系统的可靠性和稳定性,因此,在优化高压油管系统时,需要考虑如何提高系统的可靠性和稳定性。
一种常用的方法是通过调整燃油的压力和流量,使其达到最佳的喷射效果。
某型柴油机高压油管漏油故障攻关
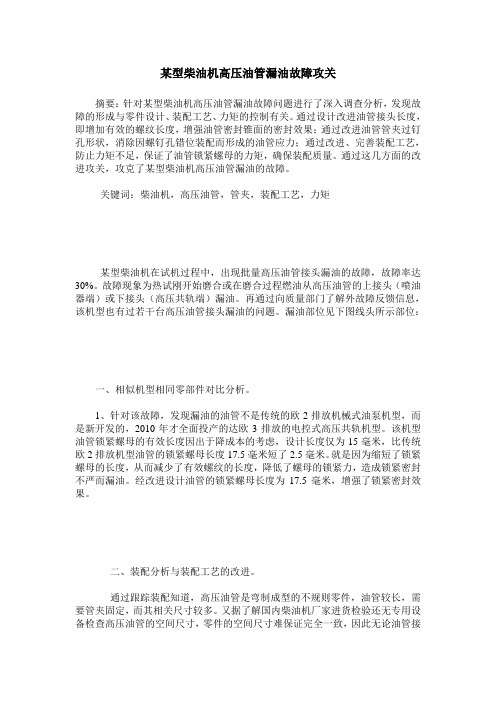
某型柴油机高压油管漏油故障攻关摘要:针对某型柴油机高压油管漏油故障问题进行了深入调查分析,发现故障的形成与零件设计、装配工艺、力矩的控制有关。
通过设计改进油管接头长度,即增加有效的螺纹长度,增强油管密封锥面的密封效果;通过改进油管管夹过钉孔形状,消除因螺钉孔错位装配而形成的油管应力;通过改进、完善装配工艺,防止力矩不足,保证了油管锁紧螺母的力矩,确保装配质量。
通过这几方面的改进攻关,攻克了某型柴油机高压油管漏油的故障。
关键词:柴油机,高压油管,管夹,装配工艺,力矩某型柴油机在试机过程中,出现批量高压油管接头漏油的故障,故障率达30%。
故障现象为热试刚开始磨合或在磨合过程燃油从高压油管的上接头(喷油器端)或下接头(高压共轨端)漏油。
再通过向质量部门了解外故障反馈信息,该机型也有过若干台高压油管接头漏油的问题。
漏油部位见下图线头所示部位:一、相似机型相同零部件对比分析。
1、针对该故障,发现漏油的油管不是传统的欧2排放机械式油泵机型,而是新开发的,2010年才全面投产的达欧3排放的电控式高压共轨机型。
该机型油管锁紧螺母的有效长度因出于降成本的考虑,设计长度仅为15毫米,比传统欧2排放机型油管的锁紧螺母长度17.5毫米短了2.5毫米。
就是因为缩短了锁紧螺母的长度,从而减少了有效螺纹的长度,降低了螺母的锁紧力,造成锁紧密封不严而漏油。
经改进设计油管的锁紧螺母长度为17.5毫米,增强了锁紧密封效果。
二、装配分析与装配工艺的改进。
通过跟踪装配知道,高压油管是弯制成型的不规则零件,油管较长,需要管夹固定,而其相关尺寸较多。
又据了解国内柴油机厂家进货检验还无专用设备检查高压油管的空间尺寸,零件的空间尺寸难保证完全一致,因此无论油管接头或固定管夹的过钉孔均有错位现象。
如装配或设计上无法消除错位则必然造成撬装。
这样油管都会因错位撬装而使密封面配合不佳或产生应力,使油管密封失效,造成漏油。
对管夹固定孔错位可通过把过钉孔由圆孔改为长U孔来消除。
某输油管道的振动疲劳分析案例

某输油管道的振动疲劳分析案例
1、某输油管管道在预应力载荷下的模态提取
实际工程问题中往往需要考虑在一定负载和预应力载荷条件下非线性的模态提取分析,以便和工程实际状态及问题相符合。
管道的预应力载荷作用下的模态提取分析,首先实现管道在外部载荷(内部压力)作用下的几何非线性分析,然后在此基础上实现模态提取。
(1)有限元建模
v 创建三维几何模型,厚度方向创建三层网格单元。
v 定义线弹性材料本构模型,赋于材料属性;
v 创建两端参考点进行几何约束;
v 定义几何非线性,进行模型分析;
v 在内部施加15MPa的内表面压力;
v 为了体现后续振动疲劳的分析,在一端施加约束,另一端耦合一个400kg的质量点;
(2)预应力模型分析结果
(3)基于预应力条件下的模态提取
v 在进行预应力载荷模型分析的基础上采用Lanczos算法,实现模型前10阶模态的提取;v 保持模型参考点的约束状态。
前十阶模态提取结果
2、基于基础运动的随机响应分析与振动疲劳
(1)有限元模型
v 采用随机响应分析实现,管道在外部基础运动激励条件下的模型分析。
v 定义功率谱密度以及基础运动相应谱载荷定义。
其中频域范围为1~1200,结构阻尼为0.1。
v 输出管道模型的广义位移历史场变量
(2)分析结果
v 随机响应功率谱密度激励,前十阶广义位移与频率关系曲线
(3)实现振动疲劳寿命预测分析
v 完成模型材料,应力-应变导入以及载荷定义等步骤,并提交模型
v 输出按照上述载荷谱响应进行循环分析的寿命结果,即10E+5.359~10E6.523,结构的整体寿命差异不大,疲劳寿命较危险的位置为弯管下方。
高压调速油泵振动大原因分析及消除论文
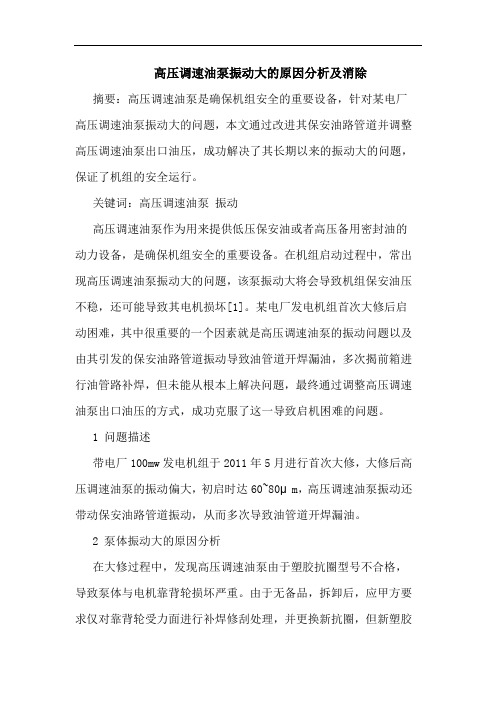
高压调速油泵振动大的原因分析及消除摘要:高压调速油泵是确保机组安全的重要设备,针对某电厂高压调速油泵振动大的问题,本文通过改进其保安油路管道并调整高压调速油泵出口油压,成功解决了其长期以来的振动大的问题,保证了机组的安全运行。
关键词:高压调速油泵振动高压调速油泵作为用来提供低压保安油或者高压备用密封油的动力设备,是确保机组安全的重要设备。
在机组启动过程中,常出现高压调速油泵振动大的问题,该泵振动大将会导致机组保安油压不稳,还可能导致其电机损坏[1]。
某电厂发电机组首次大修后启动困难,其中很重要的一个因素就是高压调速油泵的振动问题以及由其引发的保安油路管道振动导致油管道开焊漏油,多次揭前箱进行油管路补焊,但未能从根本上解决问题,最终通过调整高压调速油泵出口油压的方式,成功克服了这一导致启机困难的问题。
1 问题描述带电厂100mw发电机组于2011年5月进行首次大修,大修后高压调速油泵的振动偏大,初启时达60~80μm,高压调速油泵振动还带动保安油路管道振动,从而多次导致油管道开焊漏油。
2 泵体振动大的原因分析在大修过程中,发现高压调速油泵由于塑胶抗圈型号不合格,导致泵体与电机靠背轮损坏严重。
由于无备品,拆卸后,应甲方要求仅对靠背轮受力面进行补焊修刮处理,并更换新抗圈,但新塑胶抗圈型号依然不合格。
该机组的高压调速油泵为天津润津泵业出产的三螺杆泵,主要参数如表1所示。
通过对多次启机过程的实验观察,发现每次开启高备泵的前5~10分钟,泵体振动较为剧烈,达60~80μm,而此后关闭高备泵再重新启动,则振动大大减小,仅为30~50μm。
因此推断该机组高压调速油泵振动导致油管路开焊的原因主要有以下几点:2.1 设计泵型问题螺杆泵是利用螺杆的回转来吸排液体的,其自吸性能好、吸油连续可靠。
由于各螺杆的相互啮合以及螺杆与衬筒内壁的紧密配合,在泵的吸入口和排出口之间,就会被分隔成一个或多个密封空间。
随着螺杆的转动和啮合,这些密封空间在泵的吸入端不断形成,将吸入室中的液体封入其中,并自吸入室沿螺杆轴向连续地推移至排出端,将封闭在各空间中的液体不断排出,犹如一螺母在螺纹回转时被不断向前推进的情形那样,因此其本身在输送保安油的过程中就容易产生脉冲式的振动[2]。
某轮主机燃油管路振动分析及对策

造、 马脚换 型等处 理措 施 。
对 缸体 的不 平衡 侧推 力引起 的。
3 2 管 系现场放 样设 计不 合理 .
2 燃 油 管 系振 动 的 危 害
2 1 安全 隐患 .
燃 油管 系不 长 , 但转 弯过 多 , 管路布 置离舱 底 的 高度 过 高 , 马脚 支 撑长度 过大 , 提供 了管 系振 动的弹 性 空间 。这 种 管 系 布 置 不 能 有 效 地 吸 收 和 传 递 振
油, 挥发 性强 , 长期 振动极 有 可能导 致燃 油管 系磨损 破 裂 , 成燃 油大 量 泄 漏 , 成 极 为 严 重 的火 灾 隐 造 形
患。
2 2 设 备 的磨 损 .
振 动 的传递 性 、 坏性 强 , 期 的管系 振动极 易 破 长
引起 与管道 连接 的滤器 、 泵 、 路连 接法 兰等设 备 油 管
体 本身 的振 动 比较 大 , 柴油 机底 座采用 弹性 安装 。 且 所 以主 机运行 时 , 特别是 在高 速运 行时 , 柴油机 机体
自身 振动 比较 明显 , 必 会 将 振 动传 递 至 与其 相 连 势
的燃 油管 路 , 引起 管 路 的振 动 。柴油 机 在 额定 转 速
5 5rm n工 况 下 工 作 时 , 动 的 频 率 为 5 5×8÷ 1 i / 振 1 2÷ 0=3 . z 这 主要 是 由于各 缸 发 火 时 产 生 的 6 44H ,
第 3 2卷(0 0 第 3期 21)
柴油机
Dis lEn i e e e gn
’ 。
…
一
~
’
{ 使 用维修 {
I… 一 一 】。‘ -
某 轮 主 机燃 油 管 路振 动分 析 及 对 策
内燃机高压油管的波登效应及振动诊断
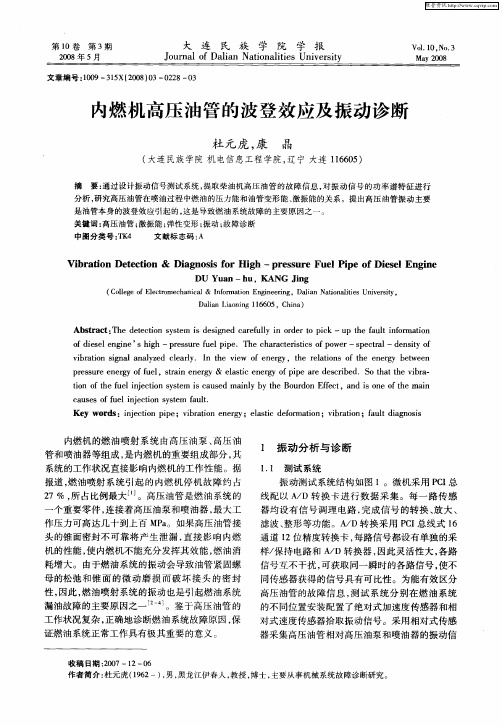
个重要 零 件 , 连接 着 高压油 泵和喷 油器 , 最大 工 头的锥 面密封 不 可靠 将 产 生 泄漏 , 直接 影 响 内燃
器均 设 有信 号 调 理 电路 , 成信 号 的转 换 、 大 、 完 放 滤波 、 整形 等功 能 。A D转 换采 用 P I / C 总线 式 l 6
A b t a t: e d tc in s se i e i n d c r f ly i r e o p c — u h a l n o mai n s r c Th ee t y t m s d sg e a eu l n o d r t ik — p t e fu ti fr to o o i s le gn S h g — p e s r u lp p . T e c a a trsis o we fd e e n i e’ ih r s u e f e i e h h r ce tc fpo r— s e ta — d n i f i p crl e st o y
通道 l 2位精 度转换 卡 , 每路 信号都 设有 单独 的采 样/ 持 电路和 A D转 换器 , 保 / 因此灵 活性 大 , 路 各
作 压力 可高 达几十 到上百 M a P 。如果 高 压油管 接 机的性 能 , 内燃机 不能充 分发 挥其效 能 , 油 消 使 燃
耗 增大 。 由于燃油 系统 的振动会 导致 油管 紧 固螺
文 章 编 号 :09— 1X(0 8 0 0 2 0 10 3 5 20 )3— 2 8— 3
内燃机高压 油管的波登效应及振动诊断
杜元 虎 , 康 晶
( 大连 民族 学院 机 电信息 工程 学院 , 宁 大连 16 0 ) 辽 16 5
摘 要: 通过设计振 动信号测试 系统 , 提取 柴油机高压油管 的故障信息 , 对振 动信号 的功率谱特征 进行
开题报告 某柴油机机械泵高压油管数值模态分析

汽车工程系湖北汽车工业学院科技学院THE SCIENCE AND TECHNOLOGY COLLEGE OF HUBEI UNIVERSITY OF AUTOMOTIVE TECHNOLOGY 毕业设计开题报告题目某柴油机机械泵高压油管数值模态分析班号2008K430301 专业车辆工程学号2008k430301 学生姓名房中华指导教师张继伟柴油机喷油泵高压油管是柴油机燃油系统高压油路的重要组成部分,其主要失效形式是由于谐振产生疲劳裂纹而最终导致的破坏。
对某柴油机高压油管进行了三维布置设计;并对高压油管进行了模态分析,比较了高压油管无管夹固定与管夹固定两种情况下前5 阶模态频率以及振形。
分析结果表明,增加固定管夹可以明显提高高压油管的固有频率,能有效延长高压油管的寿命,并得到发动机台架试验的佐证[1]。
一、课题来源湖北汽车工业学院科技2008级毕业设计。
二、国内外现状为了保持柴油机作为交通领域主要动力的地位,满足其高速、轻型、大功率的发展要求,并面对世界各国日益严格的排放法规,必须进一步改善其燃烧特性,提高供油压力近年来,柴油机厂大多采用了高泵端压力的喷油泵,加剧了机体振动,供油系高压油管在使用中要承受更高的泵端喷射压力,事故率上升明显,给柴油机厂和用户带来了极大的损失本文结合现阶段柴油机装配大马力喷油泵而造成的高压油管故障率上升的实际,以某型号六缸柴油机为研究对象,对其故障件进行统计,并结合疲劳理论进行分析,确定了易受损的危险部位将局部应力-应变实验测量法应用到高压油管危险部位的测量当中,对危险部位的因受周期性外力而产生的应变的大小、应变变化的频率和振幅进行测量,为分析疲劳破坏提供了必要的数据支持,并为改进提供了理想的检验标准通过疲劳理论和流体力学理论对其工作状况和破坏机理进行分析,在国标的基础上,结合柴油机厂的生产实际,制定了厂内部的高压油管设计规范,为油管的设计提供了依据结合有限元分析方法,建立柴油机高压油管-管夹模型,对其工作规律和工作模态进行了研究,得出了油管的动态特征信息,为设计及优化提供了有效地参考数据结合模态分析理论,提出了改进管形、管夹的设计方案,并利用有限元分析方法,指导高压油管的改进改进结果经实验验证和产品信息反馈,降低了高压油管的应变,提高了高压油管的整体抗疲劳性能,进而提高了高压油管的整体可靠性,对于解决实际问题缩短各机型油管试验分析具有很好的指导意义[2]。
车用发动机高压油管振动分析与控制
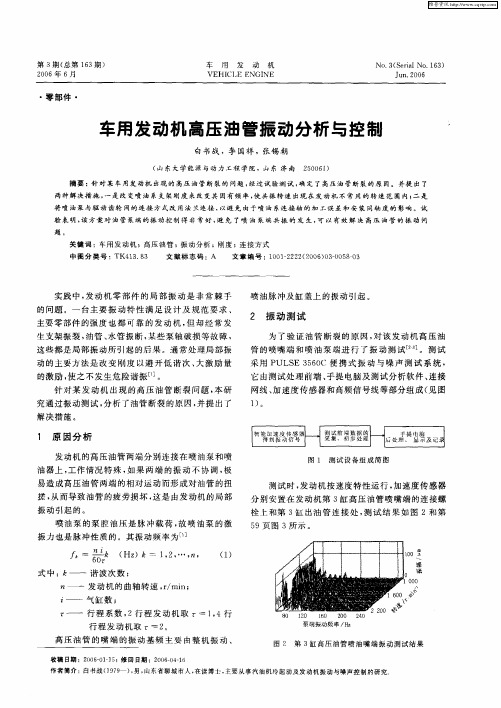
的激励 , 使之 不 发生 危 险谐振I 一 。 针 对某 发 动 机 出现 的 高压 油管 断 裂 问题 , 研 本
究 通 过振动 测试 , 析 了油管 断裂 的原 因 , 分 并提 出 了
动 的 主要方 法是 改 变 刚 度 以避 开低 谐 次 、 大激 励 量
喷油 脉 冲及缸 盖 上 的振动 引起 。
2 振 动 测 试
为 了验 证 油 管 断 裂 的原 因 , 该 发 动机 高 压油 对 管 的喷 嘴端 和 喷 油 泵 端进 行 了振 动 测 试口 ] 。 。测 试
题 。
关 键 词 :车 用 发 动 机 }高 压 油 管 ; 动 分 析 ; 度 ;连 接 方 式 振 刚
中国 分 类 号 : K4 3 8 T 1 .3 文 献 标 志 码 :A 文 章 编 号 : 0 12 2 (0 60 —0 80 10 —2 2 2 0 ) 30 5 3
实 践 中 , 动机 零 部 件 的 局 部 振 动是 非 常 棘 手 发 的问题 。一 台 主要 振 动 特 性 满 足设 计 及 规 范 要 求 、 主要 零 部件 的强 度 也 都 可靠 的发 动 机 , 却 经 常 发 但 生 支架 振裂 , 油管 、 水管 振断 , 某些 泵轴 破损 等故 障 , 这 些都 是局 部振 动所 引起 的后 果 。通 常处 理局部 振
易 造成 高压 油管 两端 的相对 运动 而形 成对 油管 的扭 搓 , 而导致 油管 的疲 劳损 坏 , 是 由发 动机 的局部 从 这
振 动 引起的 。
匝
匿巫H蒌
图 1 测 试 设 备 组 成 简 图
某柴油机机械泵高压油管数值模态分析

摘要机械泵高压油管是柴油机供油系统高压油路的重要组成部分。
高压油管通过压力波的形式将柴油以一定的压力和速度输送到喷油器,所以对燃油喷射特性有着不可忽视的影响。
国际上许多国家都对影响液力特性的高压油管的制造提出了严格要求,制定了相应标准。
对柴油机高压油管的模拟分析必不可少,首先进行几何清理,四面体网格划分,网格质量检查,然后采用刚性连接,对高压油管进行模态分析。
关键词:高压油管;模态分析;四面体网格;网格质量AbstractMechanical pump fuel injection system of diesel engine high pressure oil pipe is an important part of the high voltage circuit.High pressure oil pipe through a pressure wave form to diesel oil with certain pressure and speed delivery to the fuel injector,soon fuel injection characteristic has the effect can not be ignored.A lot of countries on the influence of hydraulic characteristics of high pressure pipe manufacturing requirements, established corresponding standard.On high pressure oil pipe of diesel engine simulation analysis is indispensable,the first geometry clean,tetrahedral mesh, mesh quality check, and then adopt the rigid connection,modal analysis on high pressure oil pipe.Key words:high pressure oil;modal analysis;Tetrahedral mesh;mesh quality目录摘要 (I)Abstract (II)第一章绪论 (1)1.1 引言 (1)1.2 有限元分析的基本概念 (2)1.3 计算机辅助工程简介 (2)1.4 有限元法在国内汽车分析中的应用 (3)1.4.1 有限元法在国内汽车分析中的应用 (3)1.4.2 有限元法在国外汽车分析中的应用 (4)1.5 研究内容 (4)1.6 小结 (4)第二章有限元模型建立的基本方法 (6)2.1 有限单元法基本理论 (6)2.2 软件前处理简介 (8)2.3 应用Hypermesh的几个重要步骤 (9)2.3.1 Collector概念 (9)2.3.2 几何清理 (9)2.3.3 网格的划分 (10)2.4 网格优化算法类型 (10)2.4.1 点插入 (11)2.4.2 点删除 (11)2.4.3 点重叠 (11)2.5 单元的质量检查 (12)2.6 小结 (14)第三章高压油管前期处理 (15)3.1 几何清理 (15)3.2 单元质量评价分析 (16)3.3 网格划分 (18)3.4 连接 (20)3.5 小结 (22)第四章高压油管模态分析 (24)4.1 模态分析的基本理论 (24)4.2 高压油管有限元模态分析及结果分析 (24)4.2.1 自由模态分析 (25)4.2.2 约束模态分析 (30)4.3 本章小结 (35)第五章总结与展望 (36)5.1 总结 (36)5.2 展望 (36)致谢 (37)参考文献 (38)第一章绪论1.1 引言在汽车发展的早期,人们对汽车结构的分析主要依靠经验判断和试验模拟。
核电站柴油机管线振动问题的分析

核电站柴油机管线振动问题的分析摘要:柴油机作为核电站重要设备,执行在全厂失电的情况下应急供电的功能。
以某核电厂柴油机系统供油回路管线振动问题为例,通过PEPS 6.0动力学时程分析的方法,找出管线振动的原因,并给出具体的解决方案。
同时对管线在自重、内压、热膨胀、地震等载荷工况下的应力进行计算。
最后总结此类问题的通用解决方法,用于解决柴油机管线振动问题。
关键词:柴油机;管线;振动;PEPS1 引言某核电站在进行柴油机系统附属管线进行振动普查的过程中,发现回油管线普遍存在振动超标状况。
轻微的振动可以通过管线的刚性及固定支架等处理,不会对管线产生塑性破坏。
如果柴油机管线出现振动频率高、振动幅度大的情况,管线与附件的连接部位、管线与支架的连接部分会产生较大的交变应力,导致管线产生疲劳破坏,主要表现为焊缝开裂,支架变形、仪表损坏等。
核电厂应急柴油机的功能是在全厂失电情况下,对中低压核辅助设备电力提供保障,确保核电厂安全停机停堆。
根据运行要求,在紧急启动信号发出10秒内,应急柴油机需启动并达额定转速和额定电压。
燃油回油管线(下称回油管线)是维持日用油箱8m3储存油量的重要设备。
若回油管线处于振动超标状态,将加速该管线材质疲劳损伤,使管线破损几率增大,从而影响柴油机的应急启动,威胁核电厂的安全稳定运行。
2 管线振动原因分析从管线振动的振源可知,管线振动可分为机械导致的受迫振动和管线内介质导致的振动,回油管路的振动主要是由于柴油机本体振动导致,分析如下:柴油机回油管一端连接柴油机本体,一端连接软管。
柴油机在启机过程引发设备振动,从而带动回油管线振动,柴油机和回油管线相对位置如图2-1所示。
回油管线整体刚度交底,在图片标示处受到柴油机本体振动的激励,导致管线受迫振动。
4.PEPS时程分析回油管线振动的通用方法4.2 1 静力及地震分析PEPS管线应力分析软件的理论基础为结构力学理论,在对方程进行求解时有如下假设:1.梁或杆单元不存在大变形。
基于流固耦合的高压油管振动疲劳特性研究

基于流固耦合的高压油管振动疲劳特性研究田新伟;周帅;胡亮;李伟东;何文运【摘要】以高压油管为研究对象,开展了基于流固耦合方法的振动疲劳特性研究.通过计算流体力学(computational fluid dynamics,简称CFD)仿真获取高压油管内部燃油脉冲压力,并建立高压油管流固耦合模型进行振动特性仿真分析,能更准确地预测高压油管的振动疲劳寿命.结合发动机振动激励功率谱密度(power spectral density,简称PSD)信号、材料S-N曲线和传递函数结果,通过疲劳损伤累积模型进行了两种高压油管模型的振动疲劳寿命预测,对比分析了考虑燃油脉冲压力对振动疲劳寿命的影响,为后期高压油管的优化设计提供了指导.【期刊名称】《振动、测试与诊断》【年(卷),期】2018(038)006【总页数】6页(P1234-1239)【关键词】高压油管;燃油脉冲压力;流固耦合;振动疲劳特性【作者】田新伟;周帅;胡亮;李伟东;何文运【作者单位】内燃机可靠性国家重点实验室潍坊,261061;潍柴动力股份有限公司潍坊,261061;天津大学内燃机燃烧学国家重点实验室天津,300072;内燃机可靠性国家重点实验室潍坊,261061;潍柴动力股份有限公司潍坊,261061;内燃机可靠性国家重点实验室潍坊,261061;潍柴动力股份有限公司潍坊,261061;天津大学内燃机燃烧学国家重点实验室天津,300072;内燃机可靠性国家重点实验室潍坊,261061;潍柴动力股份有限公司潍坊,261061【正文语种】中文【中图分类】TK402;TH113引言高压油管是柴油机燃油供给系统的重要零部件,它连接着高压油泵和喷油器,其振动疲劳行为影响着柴油机运行的可靠性。
高压油管通过压力波的形式将燃油以一定的压力和速度输送到喷油器,其可靠性对燃油的正常供给有着不可忽视的影响。
近年来,为了提高柴油机的经济性,改善排放性能,满足日益严格的排放法规的要求,柴油机逐渐向着高泵端压力的燃油喷射泵发展,增大了燃油油压对高压油管的冲击。
柴油机振动分析研究

柴油机振动分析研究柴油机是一种重要的动力设备,用于汽车、船舶、发电机等领域。
然而,由于柴油机运转时有振动产生,这给机器的工作效率和使用寿命带来了负面影响。
因此,对柴油机振动进行研究和分析,可以优化其结构和工作参数,达到减少振动的目的。
柴油机振动主要有以下几种:1.机械振动机械振动主要是由于发动机内部的机械部件运转时带来的振动,如活塞、连杆、曲轴等。
这些部件在高速运转时会产生很大的震荡力,从而导致机器整体产生振动。
2.气动振动气动振动主要是由于柴油机排放废气过程中的前、后冲冲击波,会导致机器内部产生气体振动。
这些振动会通过机器整体传递,使得工作环境产生较大的噪音和震感。
3.热应力振动当柴油机在高温、高压环境下工作时,机器内部的金属材料会发生热膨胀和收缩,从而产生不均匀的应力分布。
这些应力分布会引起机器的微小振动,从而对机器的工作效率和寿命产生影响。
针对以上振动问题,我们可以采取以下措施进行研究和分析,优化柴油机的振动性能:1. 机械结构优化通过改善柴油机的机械结构设计,降低机器内部的滑动摩擦和压力差,从而减少活塞、连杆、曲轴等机械部件的振动。
常见的优化措施包括改进柴油机的径向和轴向运动精度、提高机械部件的装配精度和润滑性能等。
2. 气动特性优化通过改善柴油机的进、排气系统,增加气体的流动稳定性,减少排气压力冲击波的大小和频率,从而降低振动产生。
常见的优化措施包括改进燃油喷射系统、加强气流引导和缓冲设计等。
3. 热应力控制通过改进柴油机的材料性能,增加机器内部金属材料的韧性和抗疲劳性,从而减少因温度变化引起的振动。
常见的优化措施包括优化柴油机的密封装配和预热控制、采用高抗疲劳性材料等。
通过以上研究和分析,我们可以优化柴油机的结构和工作参数,降低机器产生的振动,从而提高机器的工作效率、延长机器的使用寿命,甚至减少对环境的影响。
因此,柴油机振动研究和分析具有重要意义,是改进柴油机性能的关键要素。
为了更好地理解和分析柴油机振动情况,我们需要收集和分析相关数据。
柴油机高压油管振动优化
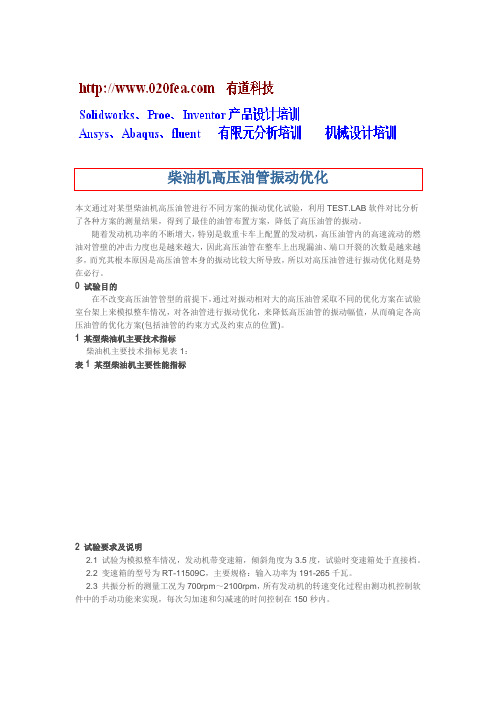
本文通过对某型柴油机高压油管进行不同方案的振动优化试验,利用B软件对比分析了各种方案的测量结果,得到了最佳的油管布置方案,降低了高压油管的振动。
随着发动机功率的不断增大,特别是载重卡车上配置的发动机,高压油管内的高速流动的燃油对管壁的冲击力度也是越来越大,因此高压油管在整车上出现漏油、端口开裂的次数是越来越多,而究其根本原因是高压油管本身的振动比较大所导致,所以对高压油管进行振动优化则是势在必行。
0 试验目的在不改变高压油管管型的前提下,通过对振动相对大的高压油管采取不同的优化方案在试验室台架上来模拟整车情况,对各油管进行振动优化,来降低高压油管的振动幅值,从而确定各高压油管的优化方案(包括油管的约束方式及约束点的位置)。
1 某型柴油机主要技术指标柴油机主要技术指标见表1:表1 某型柴油机主要性能指标2 试验要求及说明2.1 试验为模拟整车情况,发动机带变速箱,倾斜角度为3.5度,试验时变速箱处于直接档。
2.2 变速箱的型号为RT-11509C,主要规格:输入功率为191-265千瓦。
2.3 共振分析的测量工况为700rpm~2100rpm,所有发动机的转速变化过程由测功机控制软件中的手动功能来实现,每次匀加速和匀减速的时间控制在150秒内。
2.4 每次额定工况测量时,记录发动机的最大功率和相应的扭矩。
实测最大功率为2100r/min 时的功率为250.2KW,,铭牌额定功率为258KW,功率损失比为3.1%,根据经验知道该损失在正常功率损失5%范围之内。
3 试验仪器与设备具体试验仪器与设备详细情况见表2:表2 试验仪器与设备清单4 试验过程4.1 测试坐标定义为:上下(活塞运动方向)为Z向,左右为Y向,前后(曲轴方向)为X向,符合右手定则,见图1:图1 试验坐标系示意图4.2 试验前更换机油;4.3 各缸高压高压油管优化方案的确定。
5 高压油管优化结果分析5.1 试验结果评估依据按照国外某发动机公司的试验规范来评估柴油机零部件的振动水平,评估依据分速度和位移两种(V和S均为测量有效值RMS):V<40mm/s,低振动S<100um,低振动40mm/s<V<80 mm/s,高振动100um<S<400 um,高振动V>80 mm/s,剧烈振动S>400 um,剧烈振动5.2 进行优化的高压油管的确定根据油管原方案的测试结果分析,确定对第2缸和共轨轨前高压油管进行振动优化。
船舶柴油机高压油管异常振动故障的处理与启示

喷射系统2 号高压油管略有小幅度振动 ,但不 明显 , 倾听无异声 ,接头处无渗油 ,查看主机各缸运行参数
均 正 常 ,故 未 做进 一 步检 查 和处理 。 1 9日1 :0 9 0 ,值
压油泵的振动 ,与高压油泵的喷油频率和喷油压力密
切相关 ;二是汽 缸 内燃 烧过 程 的冲击作用 和运 动部 件 的惯性 力 引起 的低频振 动通 过机体 传给 高压油 管 的振 动 ;三是 高压油 管 中的压力 变化 引起 的高压油 管 的弹 性变形 ,即波登 管效应 引起 的振 动 ,通 常认 为这也是
一
是 轮 机 长 决 定 第 3 停 车 ,检 查 更 换 高 压 油 泵 出 油 次
阀,然而故障还是没有得到消除。在无法明确判断故 障原 因的困惑下 ,大管 轮建议更换N . o 缸排气阀试 2 试 ,结果还是没有排除故障。2 日0 :0 0 2 0 ,轮机长决
N . 发生 高压 油管 溢油 报警 ,经 检查 ,油管 近喷 油 o缸 2
班机工发现该高压油管呈蛇形大幅度振动 ,即刻报告
大 管轮 ,大管 轮查看 主机 运行 工况 ,未见 异常 ,检查 油 管紧 固螺栓 ,没有 发现松 动 ,触摸 高压 油管 ,其脉
引发燃油系统故障的主要原因。在正常喷射状况下 ,
高压油 管振 动信 号脉动 明显 ,峰谷 点 比较 清 晰 ,主 波 段 以外 的振 动较 小 。为有效 进行 柴油机机 械性故 障 的
船舶柴油机高压油管异常振动 故障的 处理 与启示
浙江 交通职业技术学院海运学院 徐红 明
摘要 :通过对 一起诡 异的船舶柴 油机 高压 油管异常振动故障 的处理分析 ,归纳总结 高压油 管振动 的原 因及 不 同故障状况下 高压 油管振动的特点 ,并对 同类故障的排查、预防提 出故障分析依据要充分 、故障排查考虑要全 面和加强振动 源管理等建议。 关键词 :柴油机 ;高压油管 ;振动 ;故障
基于振动测试的发动机高压油管断裂问题分析
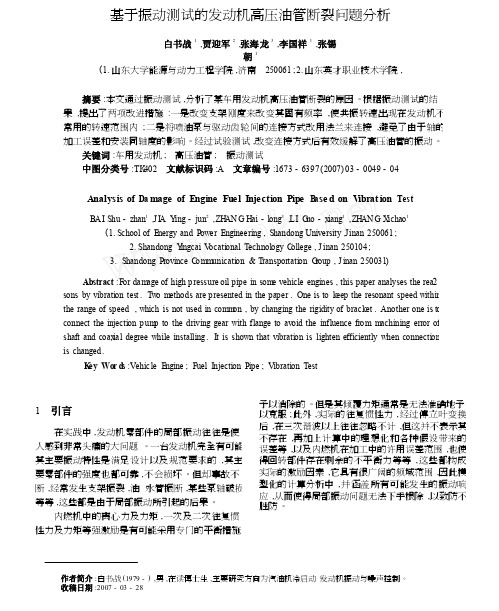
基于振动测试的发动机高压油管断裂问题分析白书战 1 ,贾迎军 2 ,张海龙3 ,李国祥 1 ,张锡朝1(1 . 山东大学能源与动力工程学院 ,济南 250061 ;2 . 山东英才职业技术学院 ,济南 250104 ;3 . 山东省交通运输集团 ,济南 250031)摘要 :本文通过振动测试 ,分析了某车用发动机高压油管断裂的原因 。
根据振动测试的结果 ,提出了两项改进措施 :一是改变支架刚度来改变其固有频率 ,使共振转速出现在发动机不 常用的转速范围内 ;二是将喷油泵与驱动齿轮间的连接方式改用法兰来连接 ,避免了由于轴的 加工误差和安装同轴度的影响 。
经过试验测试 ,改变连接方式后有效缓解了高压油管的振动 。
关键词 :车用发动机 ; 高压油管 ; 振动测试中图分类号 : T K 402 文献标识码 :A 文章编号 :1673 - 6397 (2007) 03 - 0049 - 04Analysis of Da mage of E ngine Fuel I njection Pipe B a s e d on V ibrat ion TestB A I Shu - zhan 1,J I A Y ing - jun 2,ZH AN G Hai - l ong 3,L I G uo - xiang 1,ZH AN G X ichao1(1 . School of E nergy and P ower Engineering , Shandong University ,J i nan 250061 ;2 . Shandong Y ingcai V ocati onal T echnol ogy C ollege , J inan 250104 ;3 . Shandong Province C omm unicati on & T ransportati on G roup , J inan 250031)Abstract : F or dam age of high pressure oil pipe in som e vehicle engines , this paper analyses the rea 2 sons by vibrati on test . T w o m ethods are presented in the paper . One is to keep the resonant speed within the range of speed , which is not used in comm on , by changing the rigidity of bracket . Another one is t o connect the injecti on pum p to the driving gear with flange to avoid the influence from m achining error of shaft and coax ial degree while installing. It is shown that vibrati on is lighten efficiently when connecti on is changed.K ey Wor d s :Vehicle E ngine ; Fuel Injecti on Pipe ; Vibrati on T est予以消除的 。
基于ANSYS Workbench的柴油机高压油管仿真分析

基于ANSYS Workbench的柴油机高压油管仿真分析李龙;冯国胜;苏海峰【摘要】为解决柴油机高压油管在工作环境中出现破裂的问题,该文以某柴油机高压油管为研究对象,通过ANSYS Workbench有限元软件对其进行静力学和模态仿真分析,得到在静力作用下应力和位移的最大值点,以及模态振动频率值,通过数据优化分析,结果表明,柴油机主要激励频率和高压油管固有频率重合,产生的共振导致了油管的破裂,采用添加管夹的方式改变油管的固有频率,避免了共振的产生,为提高油管使用寿命提供了理论依据.【期刊名称】《汽车工程师》【年(卷),期】2018(000)012【总页数】3页(P27-29)【关键词】柴油机;高压油管;ANSYSWorkbench;仿真【作者】李龙;冯国胜;苏海峰【作者单位】石家庄铁道大学;石家庄铁道大学;石家庄职业技术学院【正文语种】中文随着柴油机功率的不断提升,人们对柴油机的排放也提出更高的要求,同时,各个厂家也对柴油机进行了不断的强化,用以提高柴油机的性能。
高压油管是柴油机燃油系统必不可少的重要组成部分[1],在使用过程中,发现高压油管在工作一段时间后常常会出现柴油渗漏的现象,说明高压油管出现裂纹,这就意味着柴油机不能长久正常地工作,由此造成的损失难以想象。
因此,对柴油机高压油管的强度和模态振动分析就显得尤为重要。
文章针对该情况,采用有限元静力分析与模态分析相结合的方法,求解得到柴油机高压油管应力最大值点和模态振动频率,发现是由于柴油机主要激励频率和高压油管固有频率产生共振导致了油管的破裂,通过添加管夹的方式,避免了共振产生,达到了提高高压油管使用寿命的效果,对提高整个柴油机工作寿命具有重要意义。
1 柴油机高压油管静力分析柴油机高压油管静力分析是计算在油压均布载荷作用下高压油管的位移和应力,为分析油管破裂原因提供重要参考。
通过SolidWorks与ANSYS的数据接口将油管模型导入ANSYSWorkbench中,以便分析油管在油压均布载荷下的位移和应力。
应急柴油机燃油管道振动高原因分析和改造

应急柴油机燃油管道振动高原因分析和改造发布时间:2021-11-15T07:40:38.492Z 来源:《科学与技术》2021年8月23期作者:周长广[导读] 应急柴油机大多应用于电厂中,作为备用发电系统的核心动力源,由于涉及到比较重要的生活生产项目,因此对其运行稳定性的要求比较高。
周长广中国核工业二三建设有限公司, 北京 101300摘要:应急柴油机大多应用于电厂中,作为备用发电系统的核心动力源,由于涉及到比较重要的生活生产项目,因此对其运行稳定性的要求比较高。
但其经常会发生燃油管道振动过高的现象。
分析其原因并加以针对性改造,不但可以提高生产效率,还可以延长使用寿命。
关键词:应急燃油机;燃油管道;振动;改造应急柴油机的燃油体系主要负责应急燃油机原材料,即燃油的提供和回收。
如果燃油管道振动过高会直接影响燃油体系的运行状态,不但不能保证燃油的正常流转,更会由于长期高幅高频振动而加快管道的老化,缩短设备使用寿命。
找出原因加以改造意义重大。
1、改造作用1.1提升机器效率工业生产中效率是核心价值点,提升生产效率就是提高经济效益。
对整个行业来说都具有重大意义。
应急柴油机燃油管道由于长期处于工业发电生产体系中的关键位置,反复使用次数高,需要长期处于工作状态,其中的燃油经过管道时受到各种复杂因素的影响,会导致燃油管道发生振动,且随着时间的推移,振动越来越高。
这会直接导致燃油管道的损耗,影响燃油管道的正常运转,进而影响到了整个应急柴油机的工作效率。
对应急柴油机的燃油管道进行改造,可以很大程度上减小燃油管道的振动,燃油管道振动低了到一定程度之后就不再会对燃油管道构成威胁,也不再影响燃油管道的正常运行,从而保障了应急柴油机的正常运转。
因此,对应急柴油机的燃油管道进行管道振动方面的改造,可以有效的提升应急柴油机应急管道的工作效率。
从而使应急柴油机在同样的时间内工作,可以产生更大的经济价值。
1.2延长设备寿命毋庸置疑,现代工业体系是非常庞大和复杂的,各种机器和设备之间或多或少的会有相互之间的关连或者配合。
- 1、下载文档前请自行甄别文档内容的完整性,平台不提供额外的编辑、内容补充、找答案等附加服务。
- 2、"仅部分预览"的文档,不可在线预览部分如存在完整性等问题,可反馈申请退款(可完整预览的文档不适用该条件!)。
- 3、如文档侵犯您的权益,请联系客服反馈,我们会尽快为您处理(人工客服工作时间:9:00-18:30)。
在不改变高压油管管型的前提下,通过对振动相对大的高压油管采取不同的优化方案在试验室台架
上来模拟整车情况,对各油管进行振动优化,来降低高压油管的振动幅值,从而确定各高压油管的优化
方案(包括油管的约束方式及约束点的位置)。
1. 某型柴油机主要技术指标
柴油机主要技术指标见表 1:
表 1 某型柴油机主要性能指标
参考文献: 1. LMS 公司第四届汽车 NVH 技术研讨会 2. 振动分析 张准 汪凤泉 编著 3. LMS b 4B 培训资料 模态分析及旋转机械 2004 年 4. 机械振动 清华大学工程力学系编 5. 内燃机学 周龙保 主编 机械工业出版社
返回目录
-6-
3
1122 55.9
案
clamp2
Y(down-full load)
3
1738 87.38
一
Y(up-full load)
3
1867 92.92
速度 mm/s
289
66 41.5 66.3 143.9 131.1 64 90.1 61 181 184.3 161.7 184.8 148.2 125
位移 um
6.2.2 第二缸高压油管优化结果对比
几种不同方案的测量结果见表 3:
表 3 高压油管几种方案测量结果
测点名称
方向 X/Y/Z
阶次
转速 rpm
频率 Hz
hpline2-1
Z(up-full load)
27 1906 859
原
Y(down-full load)
10 1935 337
状
hpline2-2
阶次
27 33 27 3 3 3 3 3 3 11
转速 rpm 1862 1403 1837 2037 1868 1368 1538 1662 1368 1463
频率 Hz 832 771 826 101 93 68 78 83 68 256
速度 mm/s 184.3 224.8 201.1 212 57.5 73.6 69.6 146.1 181.8 166.9
3
1409 69.98
3
1120 56.05
Y(up-full load)
3
1266 63.29
案
Z(down-full load)
3
1590 79.06
hpline2-2 二
Z(up-full load) Y(up-full load)
3
1437 72.21
3
1362 67.75
方
Z(down-full load)
显,可以参考采用。
-5-
某型柴油机高压油管振动优化
2006 LMS 首届用户大会论文集
(3) 高压油管的振动和管夹的不同约束位置有很大关系,在以后的高压油管的总布局中可以提前把该 因素考虑进去,以降低高压油管的振动。
(4) 至于高压油管的优化方案对于整车上的高压油管是否有同样的作用,还有待整车的道路试验来做 进一步检验。
Y(up-full load)
3
1867 92.92
态
Z(up-no load)
1
1894 33.84
hpline2-2
Y(down-full load) Y(up-no load)
3
1814 91.26
1
1745 30.29
Z(up-full load)
方
hpline2-1
Y(down-full load)
轨前高压油管的两种方案的测量结果见表 4:
表 4 轨前高压油管优化结果
方 测点名称 案
原 upline-1 状 态 downline-1
方
upline1
案
一
downline1
方向 X/Y/Z Z(down-full load) Z(up-no load) Z(down-full load) Z(up-full load) Z(up-full load) Y(down-full load) Y(up-full load) Z(down-full load) Y(down-full load) Y(up-full load)
CAE 分析主要针对第二缸高压油管进行,油管本身采用管单元进行网格划分,用约束油管两端 x、y、 z 三个自由度的方式模拟油管固定,中间管夹约束了两个自由度(沿油管方向除外)。采用钢材的特性来 模拟油管材料,提取了 0 Hz~700 Hz 之间的所有模态,具体的模态结果如下:
-4-
某型柴油机高压油管振动优化
4. 试验过程
4.1 测试坐标定义为:上下(活塞运动方向)为 Z 向,左右为 Y 向,前后(曲轴方向)为 X 向,符合右
手定则,见图 1:
图 1 试验坐标系示意图
4.2 试验前更换机油;
4.3 各缸高压高压油管优化方案的确定。
5. 高压油管优化结果分析
5.1 试验结果评估依据
按照国外某发动机公司的试验规范来评估柴油机零部件的振动水平,评估依据分速度和位移两种(V
6.2 高压油管优化结果分析
6.2.1 第二缸高压油管优化方案
第二缸高压油管的优化方案具体见图 2 和图 3:
-2-
某型柴油机高压油管振动优化
新增管夹
2006 LMS 首届用户大会论文集
新增管夹
原管夹
图 2 第二缸高压油管方案一
图 3 第二缸高压油管方案二
(取消原来管夹,新增一个管夹)
(在原始状态上增加一个管夹)
2006 LMS 首届用户大会论文集
把第二缸高压油管的 CAE 模态分析结果和实际测量的阶次图比较分析,可以看出,没有出现共振 频率。另外也对高压油管的不同的约束方式进行了 CAE 分析,发现管夹的约束位置对高压油管的模态结 果有很大的影响。 7. 结论及建议
通过对目前的高压油管进行振动优化,可以得出以下结论及建议: (1) 对于第二缸高压油管,采用方案一的优化措施效果是最明显的,因此建议采用该方案。 (2) 对于轨前的两根高压油管来说,采用方案一的优化方案可以减小油管的振动,但效果不是很明
-1-
某型柴油机高压油管振动优化
2006 LMS 首届用户大会论文集
具体试验仪器与设备详细情况见表 2:
仪器名称
表 2 试验仪器与设备清单 仪器型号
厂家
发动机台架自动试验系统
FCT-1301
日本小野
测试系统前端
SC316
比利时
振动分析软件 加速度传感器
Testlab5A 356A26 等
比利时 PCB、扬州联能
型号
XXXX-XXXX
型式
直列、四冲程、水冷、增压中冷
缸径×冲程(mm×mm)
112×145
额定功率(kW)
258
额定转速(r/min)
2100
最大扭矩(N·m)
1500
最大扭矩转速(r/min)
1300~1500
压缩比
17.5:1
2. 试验要求及说明 2.1 试验为模拟整车情况,发动机带变速箱,倾斜角度为 3.5 度,试验时变速箱处于直接档。 2.2 变速箱的型号为 RT-11509C,主要规格:输入功率为 191-265 千瓦。 2.3 共振分析的测量工况为 700rpm~2100rpm,所有发动机的转速变化过程由测功机控制软件中的手动功
某型柴油机高压油管振动优化
2006 LMS 首届用户大会论文集
某型柴油机高压油管振动优化
童树波 夏 恒 卜耀宇 ( 地址:一汽解放公司无锡柴油机厂 产品开发室 214000)
摘要:本文通过对某型柴油机高压油管进行不同方案的振动优化试验,利用 B 软件对比分析了各种方案的测量结
果,得到了最佳的油管布置方案,降低了高压油管的振动。
位移 um 150 243 166 158
71.3 81.7 68.8 164 202 174
加速度 g 23 21 25 29 7 9
8.5 17 20 16
从表 4 中轨道前高压油管的优化结果可以看出,通过改进油管的支撑结构,轨道前高压油管 upline1 的振动幅值下降效果明显,而轨道前高压油管 downline-1 的振动也有所改善。 6. 高压油管 CAE 模态分析
231
51.7 51 53.2 120 168 69.1 123 73.4 174 195 181 252 131 131
加速度 g
36.9
8.58 5.17 8.41 17.49 15.32 6.04 9.9 5.25 19.29 17.72 18.81 13.92 17.27 15.64
从表 3 中的测量对比结果可以看出,方案一改进的第二缸高压油管振动虽然有些工况的振动速度幅 值超过了 80 mm/s ,但整体 呈下降趋势,并且峰值从 289mm/s 降到了 143.9mm/s,降幅超过了一半;方案 二中油管的振动与原状态时的振动相比也有很大的改善,但两种方案比较来看,方案一更理想一些。方
关键词:高压油管 振动 优化
引言 随着发动机功率的不断增大,特别是载重卡车上配置的发动机,高压油管内的高速流动的燃油对管
壁的冲击力度也是越来越大,因此高压油管在整车上出现漏油、端口开裂的次数是越来越多,而究其根
本原因是高压油管本身的振动比较大所导致,所以对高压油管进行振动优化则是势在必行。
0.试验目的
能来实现,每次匀加速和匀减速的时间控制在 150 秒内。 2.4 每次额定工况测量时,记录发动机的最大功率和相应的扭矩。实测最大功率为 2100r/min 时的功率为
250.2KW,,铭牌额定功率为 258KW,功率损失比为 3.1%,根据经验知道该损失在正常功率损失 5%范 围之内。 3. 试验仪器与设备
-3-