主轴套筒零件图
机床结构图ppt课件
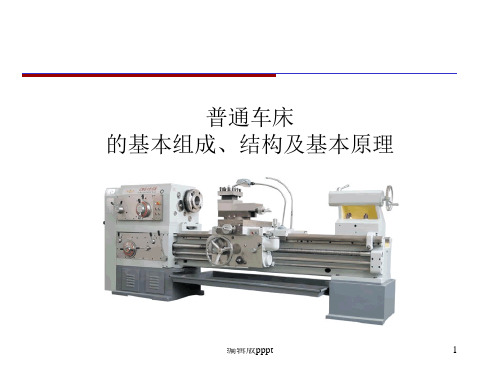
编辑版pppt
5
其它车床介绍
• 仿形车床 • 六角车床 • 单(双)柱立式车床 • 其它
编辑版pppt
6
• 卡盘
车床附件介绍
• 跟刀架
• 中心架
编辑版pppt
7
普通铣床 的基本组成、结构及基本原理
编辑版pppt
8
普通铣床的基本组成、结构及基本原理
• 按主轴方向分为立式和卧式铣床 • 立式升降台铣床,它是铣床中应用最多的一种。 • 卧式升降台铣床其主要组成部分: • 1.床身床身用来固定和支承铣床各部件。顶面上有供横梁移动用的水平导轨。前
编辑版pppt
9
普通铣床的基本组成、结构及基本原理
• 卧式铣床:质量稳定,操作方便,性能可靠。卧式铣床可用各种圆柱铣刀、圆片铣刀、 角度铣刀、成型铣刀和端面铣刀加工各种平面、斜面、沟槽等。如果使用适当铣床附件, 可加工齿轮、凸轮、弧形槽及螺旋面等特殊形状的零件,配置万能铣头、圆工作台、分 度头等铣床附件,采用镗刀杆后亦可对中、小零件进行孔加工。加装立铣头,可用立铣 刀进行切削加工,(立铣头为特殊附件) 可进一步扩大机床使用范围。本机床适用于各 种机械加工工业。
•
立式铣床铣头可在垂直平面内顺、逆时针调整 ±45°;立式铣床X、
Y、Z三方向机动进给;立式铣床主轴采用能耗制动,制动转矩大,停止
迅速,可靠。
•
底座、机身、工作台、中滑座、升降滑座、主轴箱等主要构件均采
用高强度材料铸造而成,并经人工时效处理,保证机床长期使用的稳定
性。
•
立铣头可在垂直平面内顺、逆回转调整 ±45°,拓展机床的加工范
4
普通车床的基本组成、结构及基本原理
• C6132(或C616)车床各部分的调整及其手柄的使用 • C6132车床采用操纵杆式开关,在光杆下面有一主轴启闭和变向手柄当手柄向上为反转,向下
车床尾座套筒的材料与加工工艺设计
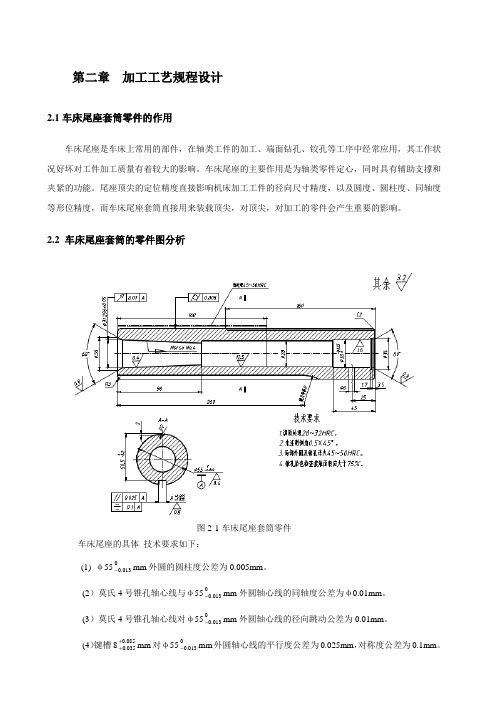
第二章 加工工艺规程设计2.1车床尾座套筒零件的作用车床尾座是车床上常用的部件,在轴类工件的加工、端面钻孔、铰孔等工序中经常应用,其工作状况好坏对工件加工质量有着较大的影响。
车床尾座的主要作用是为轴类零件定心,同时具有辅助支撑和夹紧的功能。
尾座顶尖的定位精度直接影响机床加工工件的径向尺寸精度,以及圆度、圆柱度、同轴度等形位精度,而车床尾座套筒直接用来装载顶尖,对顶尖,对加工的零件会产生重要的影响。
2.2 车床尾座套筒的零件图分析图2-1车床尾座套筒零件车床尾座的具体 技术要求如下:(1) φ550013.0-mm 外圆的圆柱度公差为0.005mm 。
(2)莫氏4号锥孔轴心线与φ550013.0-mm 外圆轴心线的同轴度公差为φ0.01mm 。
(3)莫氏4号锥孔轴心线对φ550013.0-mm 外圆轴心线的径向跳动公差为0.01mm 。
(4)键槽8085.0035.0++mm 对φ550013.0-mm 外圆轴心线的平行度公差为0.025mm ,对称度公差为0.1mm 。
(5)锥孔涂色检查其接触面积应大于75%。
(6)调质处理28~32HRC。
(7)局部外圆及锥孔淬火45~50HRC。
2.3 车床尾座套筒的毛坯设计2.3.1毛坯材料的选择在制订机械加工工艺规程时,正确选择合适的毛坯,对零件的加工质量、材料消耗和加工时都有很大的影响。
显然毛坯的尺寸和形状越接近成品零件,机械加工的劳动量就越少,但是毛坯的制造成本就越高,所以应根据生产纲领,综合考虑毛坯制造和机械加工的费用来确定毛坯,以求得最好的经济效益。
机械加工中常用的毛坯有铸件、锻件、冲压件和型材等,选用时主要考虑一下因素。
(1)零件的材料与力学性能;(2)零件的结构形状与外形尺寸;(3)生产类型;(4)毛坯车间的生产条件;(5)利用新工艺、新技术、新材料的可能性。
本设计根据零件图的技术要求采用45钢作为毛坯材料。
2.3.2毛坯的成型方式、尺寸套筒类零件的毛坯制造形式主要有铸造与锻造(压)等方法。
Fanuc系统数控车加工工艺与技能训练模块六 内孔、内腔和套类零件加工

⑤钻φ16的孔,深为30 mm; ⑥镗φ18孔,深28 mm; ⑦镗φ20孔,深30 mm; ⑧倒内孔1×45º 的倒角 ⑨切断 (3)刀具选择 ①外圆刀,设为1号刀 ②φ3 mm钻头,设为2号刀 ③切断刀,设为3号刀 ④φ16 mm钻头,设为4号刀 ⑤镗刀,设为6号刀 2.程序编制 选取工件轴线与工件右端面的交点O为工件坐标原点。 程序如下:
图6.10 塞规
9.孔加工指令 (1)G01 在数控车床上加上孔,无论是钻孔还是镗孔,都可以 用G01指令来实现。 (2)固定循环(G71、G72、G90、G94) 前面学过的外圆粗车循环(G71)、端面粗车循环 (G72)、外圆(内圆)车削循环(G90)和端面车削循 环(G94)都可以用干孔的加工。详见本课题中前面所述 “孔加工的方法”。
(a)整体式镗刀 (b)机夹式镗刀 图6.4 常用镗刀 (6)铰刀 精度要求较高的内孔,除了采用高速精镗之外, 一般是经过镗孔后用铰刀铰削。 铰刀有机用铰刀和手用铰刀2种,由工作部分、颈 和柄等组成,如图6.5所示。
(a)机用铰刀 (b)手用铰刀 图6.5 铰刀 3.孔加工的方法 (1)钻孔 钻孔前,先车平零件端面,钻出一个中心孔。 (用短钻头钻孔时,只要车平端面,不一定要钻出 中心孔)。将钻头装在车床尾座套筒内,并把尾座 固定在适当位置上,这时开动车床就可以用手动进 刀钻孔,如图6.6所示。
7.孔的精度 套类零件的精度有下列几个项目。 (1)孔的位置精度。 同轴度(孔之间或孔与某些表面间的尺寸精度)、平 行度、垂直度、径向圆跳动和端面圆跳动等。 (2)孔径和长度的尺寸精度。 (3)孔的形状精度(如圆度、圆柱度、直线度等)。 (4)表面粗糙度 要达到哪一级表面粗糙度,一般按加工图样上的规 定。 8.孔的测量 (1)内径千分尺测量 当孔的尺寸小于25mm时,可用内径术 车孔是常用的孔加工方法之一,可用作粗加工,也可用 作精加工。车孔精度一般可达IT7~IT8,表面粗糙度 Ra1.6~3.2μm。车孔的关键技术是解决内孔车刀的刚性问 题和内孔车削过程中的排屑问题。 为了增加车削刚性,防止产生振动,要尽量选择粗的刀 杆,装夹时刀杆伸出长度尽可能短,只要略大于孔深即可。 刀尖要对准工件中心,刀杆与轴心线平行。精车内孔时, 应保持刀刃锋利,否则容易产生让刀,把孔车成锥形。 内孔加工过程中,主要是控制切屑流出方向来解决排屑问 题。精车孔时要求切屑流向待加工表面(前排屑),前排屑主 要是采用正刃倾角内孔车刀。加工盲孔时,应采用负的刃 倾角,使切屑从孔口排出。
机械制造装备设计(第2章 金属切削机床设计5-6 主轴&支承)
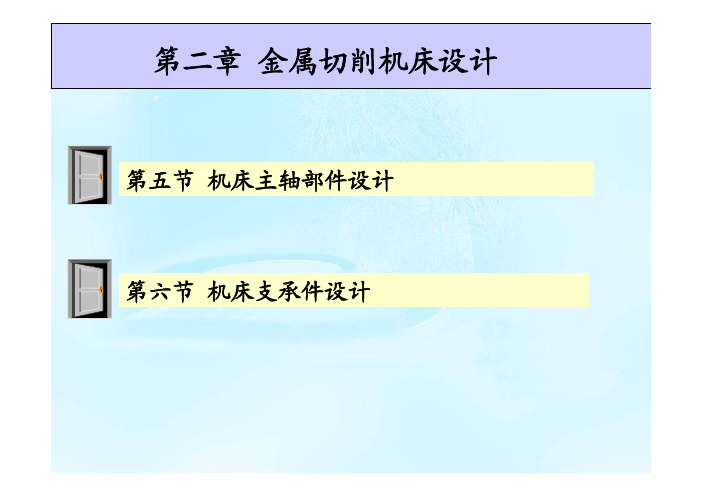
2.5.3 主轴部件结构设计
(二)推力轴承的位置配置型式 (2)后端配置 两个方向的推力轴承都布置在后支承处。 这类配置方案前支承处轴承较少,发热小,
温升低;但主轴受热后向前伸长,影响轴向精度。 这种配置用于轴向精度要求不高的普通精度
机床,如立铣、多刀车床等。
2.5.3 主轴部件结构设计
(二)推力轴承的位置配置型式 (3)两端配置 两个方向的推力轴承分别布置在前后两个支承
2.5.3 主轴部件结构设计
(三)主轴传动件位置的合理布置
合理布置传动件在主轴上的轴 向位置,可以改善主轴的受力情况 ,减少主轴变形,提高主轴的抗振 性。
主轴上传动件轴向布置时,应 尽量靠近前支承,有多个传动件时 ,其中最大传动件应靠近前支承。
2.5.3 主轴部件结构设计
(四)主轴主要结构参数的确定 主轴前、后轴径直径D1和D2,主轴内孔直径d,主轴前端悬 伸量a和主轴主要支承间的跨距L,这些参数将直接影响主 轴旋转精度和主轴刚度。
2.5.3 主轴部件结构设计 (一)主轴部件的支承数目 也可以前、中支承为主要支承,后支承为辅助支承。
角接触 球轴承 背对背
安装
2.配置型式
(1)前端配置 两个方向的推力轴承都布置在前支承处。 这类配置方案在前支承处轴承较多,发热大, 温升高;但主轴受热后向后伸长,不影响轴向精度 ,精度高,对提高主轴部件刚度有利。 这种配置用于轴向精度和刚度要求较高的高精 度机床或数控机床。
离和主轴前端的悬伸量,传动件的布置方式,主轴组
件的制造和装配质量等。 刚度不足,影响机床的加工精 度、传动质量及工作的平稳性。
2.5.1 主轴部件应满足的基本要求
(3)抗振性:指抵抗受迫振动和自激振动的能力。 主轴振动有两种类型:
套筒零件的机械加工工艺规程及夹具设计(含全套CAD图纸)

算; 4)、夹具总装图绘制。
9、刀具、量具没计。(绘制刀具量具工作图)
10、某工序数控编程程序设计。
四、上交资料(除资料 2 使用标准 A3 手写外,其余电子文稿指导教师审核后,打印上交)
1、零件机械加工工艺规程制订设计说明书一份;(按统一格式撰写)
2、工艺文件一套(含工艺过程卡片、每一道工序的工序卡片,工序附图);
第五章 第 30、35、65、70 号工序数控编程设计说明书 ........................... 23 1.数控加工工艺性分析.................................................... 23
2.走刀路线的确定........................................................ 23 3.刀具及切削用量确定.................................................... 23 4.编程原点的确定及数值计算.............................................. 24 5.程序编写及说明........................................................ 25 第六章 毕业设计体会........................................................ 29 第七章 参考资料............................................................ 30 致 谢....................................................................... 31
典型零件加工工艺(轴和套筒)

25
1)主要表面及其精度要求 ①支承轴颈
是两个锥度为1:12的圆锥面,分别与两个双列 短圆锥轴承相配合。
支承轴颈是主轴部件的装配基准,其精度直接 影响主轴部件的回转精度,尺寸精度一般为IT5。
主轴两支承轴颈的圆度允差和对其公共轴线的 斜向圆跳动允差均为0.005 mm,表面粗糙度Ra值不 大于0.63µm。
21
热处理工序的安排
结构尺寸不大的中碳钢普通轴类锻件,一般在切削加工 前进行调质热处理。
对于重要的轴类零件(如机床主轴),则:
一般在毛坯锻造后安排正火处理,达到消除锻造应 力,改善切削性能的目的;
粗加工后安排调质处理,以提高零件的综合力学性 能,并作为需要表面淬火或氮化处理的零件的预备热处 理;
5
二、轴类零件的材料和毛坯
1、轴类零件的常用毛坯:
①光轴、直径相差不大的阶梯轴常采用热轧或 冷拉的圆棒料;
②直径相差较大的阶梯轴和比较重要的轴大都 采用锻件。
③当轴的结构形状复杂或尺寸较大时,也有采
用铸件的。
自由锻
中小批
毛坯锻造
模锻
大批大量
6
2、轴类零件的材料:
1)一般轴类零件:45钢应用最多,一般须经调
轴上有相对运动的轴颈和经常拆卸的表面,需要进
行表面淬火处理,安排在磨削前。或在粗磨后、精磨前
渗氮处理
22
四、 机床主轴加工工艺及其分析
23
24
(1)零件分析 对机床主轴的共同要求是必须满足机床
的工作性能:即回转精度、刚度、热变形、 抗振性、使用寿命等多方面的要求。
车床主轴是带有通孔的多阶台轴,普通 精度等级,材料为45钢。
9
顶尖的实施
汽车机械基础任务8 熟悉常用零部件
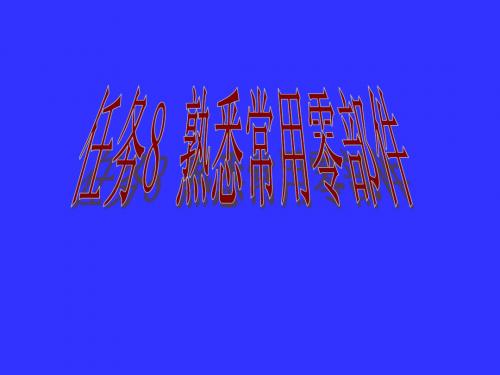
轴向固定
周向固定
轴端 轴头
轴颈 轴身
轴头
轴上零件的轴向固定
目的——保证零件在轴上有确定的轴向位置, 防止零件作轴向移动,并能承受轴向力。 轴肩 轴环 轴套 轴端 挡圈 弹性 挡圈 紧定 螺钉 双螺母
圆锥销
轴肩或轴环结构
阶梯轴的截面变化部位
轴肩
轴环
结构简单,定位可靠, 承受较大的轴向力。
用于轴端要求固定可靠或 承受较大轴向力的场合。
弹性挡圈结构
承受轴向力小或不承受轴向 力的场合,常用作滚动轴承的 轴向固定。
紧定螺钉结构
承受轴向力小或不 承受轴向力的场合。 还可兼作周向固定。
圆锥销结构
轴上零件的周向固定
目的——传递运动和转矩
平键 联接 花键 联接
销 联接
过盈 配合
传递转矩较大,对中性要求一般的 场合,使用最为广泛。
轴是机器中的重要零件之一,用来支持 旋转零件(如带轮、链轮、齿轮等),并 通过轴来传递运动和扭矩。
心轴
根据承受载荷的不同
传动轴 转轴
轴的分类
直轴
光轴 阶梯轴 曲轴
根据轴线的几何形状
软轴
传动轴
在轴的全长上直径都相等的直轴。
各段直径不相等的直轴。
便于轴上零件的装拆和固定,节省材料, 减轻重量,机械中应用最普遍。
或加
尺寸系列代号
宽(高)度 直径系列 系列代号 代号
注: 代表字母; 代表数字 3. 后置代号 ---- 用字母(或加数字)表示。 表7 轴承后置代号排列顺序
后置代号组 含 义 1 2 3 4 5 6 7 8
内部 密封与防尘 保持架 轴承 公差 结构 套圈变形 及材料 材料 等级 游隙 配置 其它
CA6140车床介绍
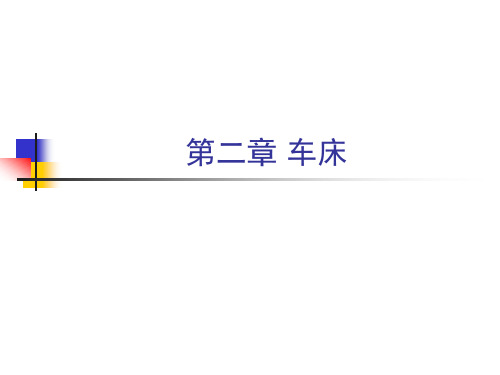
传动路线:离合器M3、M4和M5全部啮合 ,被加工螺纹的导程L工 依靠调整挂轮的传动比u挂来实现。
运动平衡式 :
L工
1(主轴)
58 58
33 33
u挂
12mm
换置公式:
u挂
a c bd
L工 12
由于传动链短,误差小,若选择高精度的齿轮作挂轮,则可加工 精密螺纹。
③纵向和横向进给传动链
机动进给传动链主要是用来加工圆柱面和端面,为了减少螺纹 传动链丝杠及开合螺母磨损,保证螺纹传动链的精度,机动进给 是由光杠经溜扳箱传动的。
u倍
12
式中
64 100 25 7
100 97 36 48
化简后得
7 m 4k u基u倍
只要变换u基和u倍,就可车削各种不同模数的螺纹。
CA6140型车床模数螺纹表(k=1时,m/mm)
ⅳ)车削径节螺纹
径节螺纹主要用于同英制蜗轮相配合,即为英制蜗杆。其标准 参数为径节,用DP表示,其定义为:对于英制蜗轮,将其总齿 数据径折节算到的每定义一可英得寸蜗分度轮圆齿距直为径:上蜗所轮齿得距的p 齿zD数 值z , D称P 为i径n 节。根
a) 纵向机动进给传动链
两末端件:主轴1r-----刀架f(mm) 运动平衡式 :
f纵
1(主轴)
58 33 63 100 58 33 100 75
25 36
u
基
25 36
36 25
u
倍
28 56
36 32 32 56
4 40 30 28 2.5 12mm / r
29 30 48 80
第三节 CA6140A型卧式车床的传动系统
(一)机床传动系统图
CA6140车床传动系统图
数控机床主传动系统

数控机床主传动系统
• 课程导引 • (1)主传动系统
如图3-2所示为VMC-15加工中心的主传动结构,其主 传动路线为:交流主电动机(150~7500r/min无级调 速)→1∶1多楔带传动→主轴。
a)各种钻床
b)铣、镗床
c)外圆磨床、平面磨统
• 3.2 主轴及其部件结构
• 2.主轴的主要尺寸参数 • (1)主轴直径
主轴直径越大,其刚度越高,但增加直径使得轴承和 轴上其他零件的尺寸相应增大。轴承直径越大,同精度等 级的轴承公差值也越大,同时轴承极限转速下降,要保证 主轴的旋转精度就越困难。
• 3.1 数控机床的主轴系统
数控机床主传动系统
• 3.1.2 主传动变速的方式
•
数控机床主运动调速范围很宽,其主轴的传动变速方
式主要有以下几种:
图3-4 数控机床主传动的四种配置方式 a)齿轮变速 b)带传动 c)两个电动机分别驱动 d)电主轴
• 1.带有变速齿轮的主轴传动(分段无级变速)
数控机床主传动系统
数控机床结构与故障检修
Structure and maintenance of NC
第3章 数控机床主传动系统
The main drive system of NC
CONTENTS 目 录
一 数控机床的主轴系统 二 主轴及其部件结构 三 典型机床主轴结构
• 课程导引
数控机床主传动系统
如图所示VMC-15加工中 心,工作台行程X/Y/Z向 20in/16in/20in( 1inc=25.4mm),快进速 度400in/min,主轴转速 150—7500r/min,定位精 度±0.0002in,主电机功 率11.2KW。
典型套筒类零件加工工艺分析
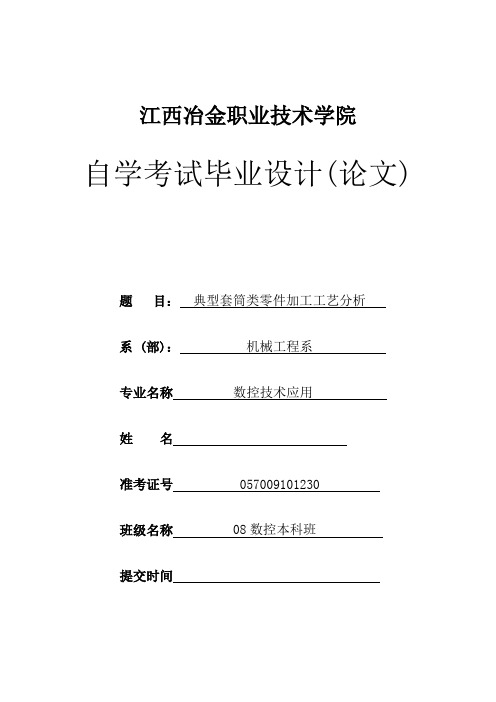
江西冶金职业技术学院自学考试毕业设计(论文)题目:典型套筒类零件加工工艺分析系 (部):机械工程系专业名称数控技术应用姓名准考证号 0570********班级名称 08数控本科班提交时间摘要高效率、高精度加工是套筒类最主要特点之一。
利用套筒零件加工,其产品加工的质量一致性好,尤其在轮廓不规则、复杂的曲线或曲面、多工艺复合化加工和高精度要求的产品加工时,其优点是传统数控零件加工所无法比拟的。
随着科学技术飞速发展和经济竞争的日趋激烈,机械产品的更新速度越来越快,数控加工技术作为先进生产力的代表,在机械及相关行业领域发挥着重要的作用,机械制造的竞争,其实质是数控技术的竞争。
本次设计就是进行套类零件的数控加工工艺,对套类零件的加工工艺分析,并绘制零件图。
其中零件工艺规程的分析是此次论文的重点和难点。
关键字:套筒类零件;液压缸;工艺分析目录引言 (1)一、套筒类零件的结构特点及工艺分析 (1)1.1轴承套加工工艺分析加工 (1)1.2液压缸加工工艺分析 (2)二、套筒类零件加工中的主要工艺问题 (4)2.1 保证相互位置精度 (4)2.2 防止变形的方法 (6)三、套筒类零件的程序编程 (8)四、套筒类零件加工中的主要工艺问题 (11)4.1 保证相互位置精度 (11)五、套简类零件的功用及结构特点 (11)5. 1 套筒类零件技术要求 (12)5.2 套筒类零件的材料、毛坯及热处理 (13)结束语 (14)致谢 (15)参考文献 (16)典型套筒类零件加工工艺分析引言理想的加工程序不仅应保证加工出符合图样的合格工件,同时应能使数控机床的功能得到合理的应用和充分的发挥。
数控机床是一种高效率的自动化设备,它的效率高于普通机床的2~3倍,要充分发挥数控机床的这一特点,必须在编程之前对工件进行工艺分析,根据具体条件,选择经济、合理的工艺方案。
数控加工工艺考虑不周是影响数控机床加工质量、生产效率及加工成本的重要因素。
CAD课程设计-套筒.

第一章概述1、CAD/CAM的基本概念CAD/CAM是自50年代以来,随着电子计算机的发展而产生、发展起来的一门综合性的计算机应用技术。
它是指应用计算机及其外围设备,协助工程技术人员完成产品的设计制造。
近几年来,3D技术、网络技术、数据库和电子商务等技术的飞速发展促进了CAD/CAM 技术的发展,心的制造方式,如分散化网络制造、面向客户的大批量定制等也对CAD/CAM 系统提出了心得要求。
目前,以产品创新、网络协同和应用集成为突出特征的面向行业与过程不的三维数字化设计系统成为现在CAD/CAM的发展方向。
2、设计制造过程的分析根据设计方法学的观点,设计过程可分为若干个设计阶段,各设计阶段又可分为若干设计步骤。
这些阶段和步骤的划分意味设计从抽象到具体,从定性到定量,从全局到局部,从系统的上层结构到下层结构。
任何产品设计、制造往往是从市场需求开始的,根据需求确定产品的性能,建立产品的总体设计方案,进行综合分析论证。
在此基础上,设计具体结构,包括结构方案的优化,评估,几何参数和力学特性的分析计算,最后得到设计结果。
3、数控加工数控加工是在机床上进行零件加工的一种工艺方法。
数控加工的基本特点同常规加工相比,数控加工有如下特点。
①自动化程度高。
②加工精度高,质量稳定。
③对加工对象的适应性强。
④生产效率高。
⑤易于建立计算机通信网络。
4、通过本次课程设计,达到以下目的:1)掌握pro/E软件的基本功能。
2)熟悉并掌握零件图的方法,能熟练运用拉伸,旋转,阵列,孔,壳等功能绘制零件图。
3)掌握pro/E中零件装配方法和仿真的步骤和方法。
4)掌握工程图的创建方法。
5)能够通过本次设计达到举一反三的效果。
第二章套筒零件的三维造型1 制造1 启动Pro、ENGINER,选择“文件-——新建”,如图所示2-1 选择零件。
点确定。
图2-1 新建文件类型2-2新建文件选项然后进入Pro、ENGINER的界面。
2.2 选择top面,点击创建新的基准平面。
机械基础轴类零件完整版

1
键槽设置在同一方位上,
且键顶部与轮毂键槽之
间应有间隙,键应局部 剖开;
2
6
7.轴过长; 8.不应该开键槽,且此段轴过长,顶住了端盖; 9.轴肩过高,不便于轴承拆卸; 10.轴承没有轴向定位,可设轴套定位,且轴承内圈外侧未
WT=πd3/16≈0.2d3;
d——轴的直径,mm; n——轴的转速,r/min。
对实心圆轴,设计计算式:
3
d?
9.55 ? 10 6
0.2[? T ]
3
?
P n
3
? C?
P n
mm
C——与轴的材料和承载情况有关的系数。
计算说明: 1)求得的d为受扭部分的最小直径,通常为
轴端;
2)该轴段有键槽适当加大直径,单键槽增 大5%,双键槽增大10%,将所计算的直径 圆整为标准值,即:
斜齿轮:
两斜齿轮旋向应相同
行星齿轮减速器:多个行星轮均布
3.改变支点位置,改善轴的强度和刚度。
a)悬臂支承方案
b)简支支承方案
c)悬臂支承方案(正安装)
4.改善轴的表面质量 表面粗糙度和表面强化处理会对轴的疲劳强度产生影响。
1)表面愈粗糙? 疲劳强度愈低; ? 提高表面粗糙度。 2)表面强化处理的方法有:
机械基础
——机械零件
第五章 机械零件——轴
§5-1 概述 §5-2 轴径的初步估算 §5-3 轴的结构设计 §5-4 轴的强度和刚度计算
§5-1 概述
一、轴的主要功用 1、支承轴上回转零件(如齿轮) 2、传递运动和动力
3、受弯矩,抵抗变形,保证轴上零件正常工作。
二、轴的分类
1、按承载情况分 转轴:既传递转矩(T)、又承受弯矩(M)