几种球化处理比较
球化处理工艺

1/球化处理工艺
对球墨铸铁曲轴其球化处理工艺非常重要,曲轴的力学性能主要依靠球化质量来保证,我们选用低镁球化剂,球化反应比较平缓,铁水一次出完,球化效果比较好。
具体球化、覆盖等工艺改进如下。
球化剂(5%-7%Mg)→铁屑覆盖(1.5-2kg)→加铁水(400 g)一球化反应(50-70s)。
2/孕育处理工艺
加硅铁(一次孕育)→浇包加硅铁粉(二次孕育)→浇注随铁水流孕育(三次孕育)。
3 曲轴的清理
曲轴浇注后,大约在50~60min,可以翻箱倒铁丸取件,铸件冷却到50℃以下,可以去除冒口和浇注系统,曲轴用悬挂式抛丸机进行表面抛丸,每组20件,大约抛丸15min左右,曲轴表面要达到无粘砂,光亮为好。
采用电动角磨机和风动工具清理飞边毛刺。
4.1铁水的检验
要铸造优质的曲轴,必须保证铁水质量,特别是铁水的化学成分,其次是铁水的出炉温度(球化处理时铁水温度)和浇注温度。
铁水化学成分检验元素及检验频次见表4。
在重要铸件生产中,对材质要求高,如球墨铸铁要求P≯0.04%、S≯0.02%,铸钢要求P、S均≯0.025%,采用热分析技术及时准确控制C、Si含量,。
球化退火工艺

球化退火工艺
球化退火工艺是一种常用的金属材料热处理工艺,通常用于改善
材料的机械性能和耐腐蚀性能。
球化退火工艺的基本原理是将金属加
热至一定温度,保持一定时间后,冷却速率适中,使内应力得到消除,晶粒得到细化。
这样可以提高金属的延展性、塑性和硬度,并改善其
耐腐蚀性能。
球化退火工艺适用于多种金属材料,如钢材、铜材、铝材等。
一
般来说,球化退火工艺可以分为两种类型:全球化处理和局部球化处理。
全球化处理是将整个材料进行加热和冷却,常用于改善材料的均
匀性和稳定性。
而局部球化处理则是只对材料的局部区域进行加热和
冷却,常用于处理材料的局部结构不均匀的问题。
球化退火工艺可以在不改变材料基本化学成分的情况下实现材料
性能的改善,被广泛应用于制造业中,如汽车、机械、航空航天、电
子等领域。
球化退火过程中的组织转变

球化退火过程中的组织转变
球化退火是一种热处理技术,其主要目的是将钢中珠光体转变为球状组织,以便改善钢的塑性和切削性。
这个过程中发生的主要组织转变是由珠光体向球状体的转变,通常由三个阶段组成:
1. 奥氏体转变:将钢材加热到适当的温度,使其处于奥氏体状态。
这通常需要一个特定的温度范围,根据不同钢材和应用,通常在725℃至1050℃之间。
2. 等温球化:将钢材置于特定温度下进行处理,以促进球状体的形核和生长。
这个过程的时间通常是根据钢材的种类和规格而定的,从数分钟到数小时不等。
3. 退火:将钢材从等温球化处理的温度冷却到室温,这通常需要数小时到数天的时间,以便使钢材内部的组织转变充分完成。
在整个球化退火过程中,还会发生其他一些组织转变,如高温下的马氏体转变、低温下的马氏体和贝氏体转变等。
然而,球化退火过程中的主要组织转变是由珠光体向球状体的转变,这种转变可以提高钢材的塑性和切削性,从而使其更加适合各种应用。
均匀化退火处理
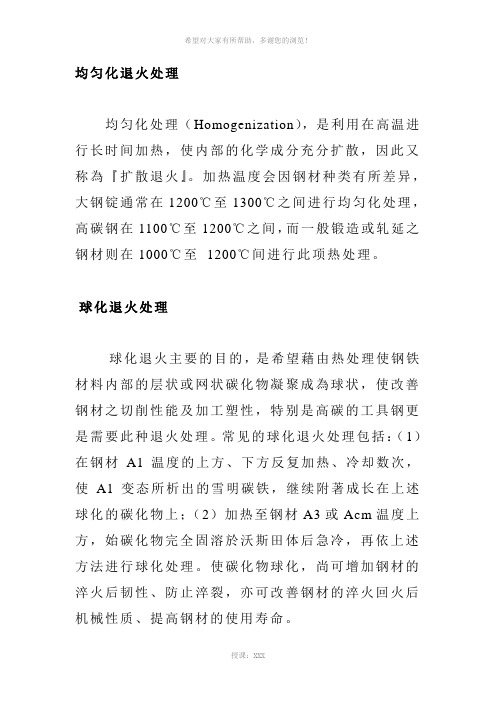
均匀化退火处理均匀化处理(Homogenization),是利用在高温进行长时间加热,使内部的化学成分充分扩散,因此又称為『扩散退火』。
加热温度会因钢材种类有所差异,大钢锭通常在1200℃至1300℃之间进行均匀化处理,高碳钢在1100℃至1200℃之间,而一般锻造或轧延之钢材则在1000℃至1200℃间进行此项热处理。
球化退火处理球化退火主要的目的,是希望藉由热处理使钢铁材料内部的层状或网状碳化物凝聚成為球状,使改善钢材之切削性能及加工塑性,特别是高碳的工具钢更是需要此种退火处理。
常见的球化退火处理包括:(1)在钢材A1温度的上方、下方反复加热、冷却数次,使A1变态所析出的雪明碳铁,继续附著成长在上述球化的碳化物上;(2)加热至钢材A3或Acm温度上方,始碳化物完全固溶於沃斯田体后急冷,再依上述方法进行球化处理。
使碳化物球化,尚可增加钢材的淬火后韧性、防止淬裂,亦可改善钢材的淬火回火后机械性质、提高钢材的使用寿命。
软化退火处理软化退火热处理的热处理程序是将工件加热到600℃至650℃范围内(A1温度下方),维持一段时间之后空冷,其主要目的在於使以加工硬化的工件再度软化、回復原先之韧性,以便能再进一步加工。
此种热处理方法常在冷加工过程反覆实施,故又称之為製程退火。
大部分金属在冷加工后,材料强度、硬度会随著加工量渐增而变大,也因此导致材料延性降低、材质变脆,若需要再进一步加工时,须先经软化退火热处理才能继续加工钢之退火处理退火处理一般是指将钢升温至某一温度,浸置一段时间后,再以一特定速率冷却下来之处理。
主要目的是软化钢材。
有时亦用以改变其他性质或显微结构。
常见的退火处理有下列几种1. 退火温度:在很多之应用退火处理中,我们只注名所需之退火温度,然后让其在炉中冷却即可。
表4-1所列為一般常见之碳钢退火温度与结果硬度。
在进行退火处理时,最容易造成失败的原因是未能维持炉中温度之均匀性。
越大之炉子越有此种问题。
球化剂怎么选
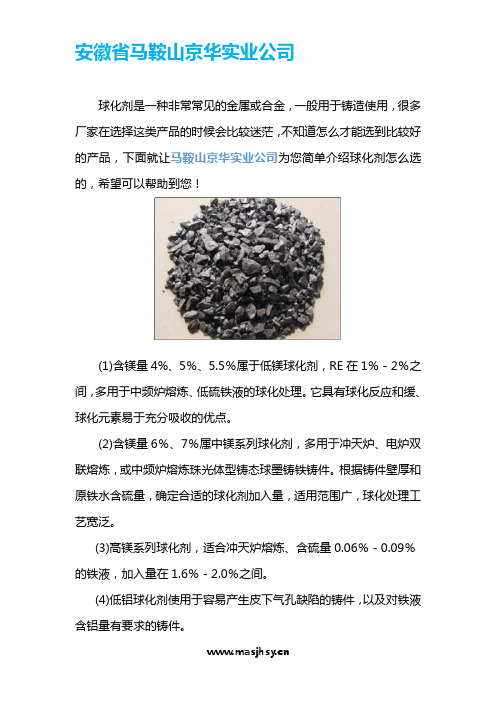
球化剂是一种非常常见的金属或合金,一般用于铸造使用,很多厂家在选择这类产品的时候会比较迷茫,不知道怎么才能选到比较好的产品,下面就让马鞍山京华实业公司为您简单介绍球化剂怎么选的,希望可以帮助到您!
(1)含镁量4%、5%、5.5%属于低镁球化剂,RE在1%-2%之间,多用于中频炉熔炼、低硫铁液的球化处理。
它具有球化反应和缓、球化元素易于充分吸收的优点。
(2)含镁量6%、7%属中镁系列球化剂,多用于冲天炉、电炉双联熔炼,或中频炉熔炼珠光体型铸态球墨铸铁铸件。
根据铸件壁厚和原铁水含硫量,确定合适的球化剂加入量,适用范围广,球化处理工艺宽泛。
(3)高镁系列球化剂,适合冲天炉熔炼、含硫量0.06%-0.09%的铁液,加入量在1.6%-2.0%之间。
(4)低铝球化剂使用于容易产生皮下气孔缺陷的铸件,以及对铁液含铝量有要求的铸件。
(5)纯Ce、纯La生产的球化剂,球化处理后铁液纯净夹杂物少、石墨球圆整。
钇基重稀土生产的球化剂适合于大断面铸件,延缓球化衰退、防止块状石墨。
含Sb球化剂用于珠光体型球墨铸铁。
(6)低硅球化剂适用于使用大量回炉料的铸造工厂;镍镁球化剂则用于高镍奥氏体球墨铸铁。
马鞍山京华实业公司是炼钢、铸造用增碳剂、煅后石油焦以及石墨化增碳剂,孕育剂,碳化硅等专业生产厂家。
公司能按增碳剂客户的要求加工成各种粒度规格的增碳剂,对产品高质量的追求户及对顾客称心满意的服务是马鞍山京华的经营宗旨。
马鞍山京华实业公司秉承着“凭质量铸造现在,靠信誉开拓未来”的经营理念,为客户提供最优质的增碳剂和贴心的服务。
如果您想进一步了解,可以直接点击官网马鞍山京华实业公司进行在线咨询。
球化分级

球化分级(摘自GB/T9441-1988) 发布时间:2007-3-1 13:34:34 浏览次数:4球化分级说明球化率/%1级石墨呈球状,少量团状,允许极少量团絮状》952级石墨大部分呈球状,余为团状和极少量团絮状90-<953级石墨大部分呈团状和球状,余为团絮状,允许有极少量蠕虫状80-<904级石墨大部分呈团絮状和团状,余为球状和少量蠕虫状70-<805级石墨呈分散分布的蠕虫状、球状、团状、团絮状60-<706级石墨呈聚集分布的蠕虫状、片状及球状、团状、团絮状资讯来源:国家标准化管理委员会发布人:国际铸业咨询单铸试块的力学性能(摘自GB/T1348-1988) 发布时间:2007-3-1 12:17:46 浏览次数:5单铸试块的力学性能(摘自GB/T1348-1988)牌号抗拉强度σ/Mpa屈服强度σ/Mpa断后伸长率σ/Mpa供参考最小值硬度HBS 主要金相组织QT400-18 400 250 18 130-180 铁素体QT400-15 400 250 15 130-180 铁素体QT450-10 450 310 10 160-210 铁素体QT500-7 500 320 7 170-230 珠光体+铁素体QT600-3 600 370 3 190-270 珠光体+铁素体QT700-2 700 420 2 225-305 珠光体QT800-2 800 480 2 245-335 珠光体或回火组织QT900-2 900 600 2 280-360 贝氏体或回火马氏体资讯来源:国家标准化管理委员会发布人:国际铸业咨询网3强化熔化及球化孕育工艺,引进和推广包外孕育工艺。
3.1冲天炉在熔炼之前,必须要根据铸件要求进行配料计算,而配料计算的基础是必须先知道铸件所需的化学成份以及原材料(生铁、回炉铁、废钢、铁合金等)的化学成份,同时要根据以往的熔炼经验得出各元素的烧损率。
一般是碳、硫增加,硅锰烧损。
球墨铸铁球化处理方法
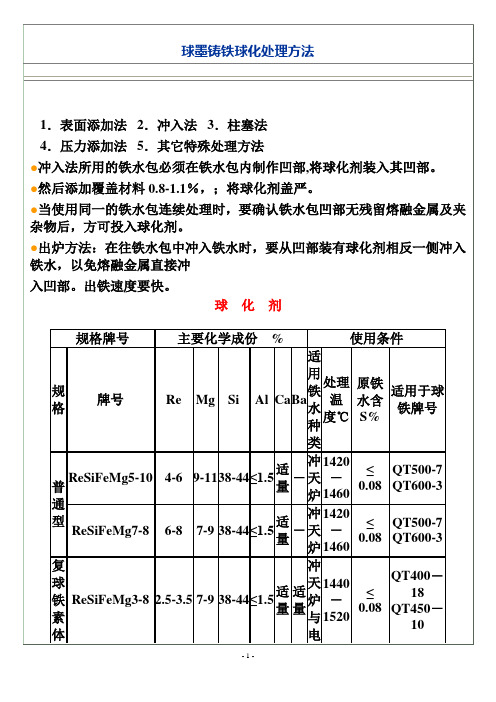
2.1 炉料选择
球铁球化剂的加入效果条件是:高碳、低硅、大孕育量。
为了稳定化学成分和有效地控制促进白口化元素和反球化元素,保证熔炼铁水的质量,选用张钢Z14生铁,其化学成分:C>3.3%,Si 1.25%~1.60%,P≤0.06%,
S≤0.04%。
2.2 球化剂的选择
球化剂的选用应根据熔炼设备的不同,即出铁温度及铁液的纯净度(如含硫量、氧化程度等)而定。
我国最常用的是稀土镁硅铁球化剂,采用这种球化剂处理时,由于合金中含硅量较高,可显著降低镁处理时反应的剧烈程度。
同时也能因增硅而有些孕育作用。
电炉生产时,因温度相对较高,所用球化剂的化学成分见表1。
表1 球化剂FeSiMg8Re7化学成分
项目
出铁温度
/℃S %
球化剂成分/%
Mg Re Si
电炉1420~1480≤0.047.0~9.0 6.0~8.0≤44.0
3 炉前控制
3.1 化学成分选择
球铁原铁液应高碳、低硅、低硫、低磷。
控制好硫的含量,是生产球铁的一个重要条件。
几种牌号的球铁的化学成分见表2。
3.2 球化和孕育处理
球化剂加入量应根据铁液成分、铸件壁厚、球化剂成分和球化处理过程的吸收率等因素分析比较确定。
一般为1.6%~2.0%,若球化剂放置时间较。
均匀化退火处理

均匀化退火处理均匀化处理(Homogenization),是利用在高温进行长时间加热,使内部的化学成分充分扩散,因此又称為『扩散退火』。
加热温度会因钢材种类有所差异,大钢锭通常在1200℃至1300℃之间进行均匀化处理,高碳钢在1100℃至1200℃之间,而一般锻造或轧延之钢材则在1000℃至1200℃间进行此项热处理。
球化退火处理球化退火主要的目的,是希望藉由热处理使钢铁材料内部的层状或网状碳化物凝聚成為球状,使改善钢材之切削性能及加工塑性,特别是高碳的工具钢更是需要此种退火处理。
常见的球化退火处理包括:(1)在钢材A1温度的上方、下方反复加热、冷却数次,使A1变态所析出的雪明碳铁,继续附著成长在上述球化的碳化物上;(2)加热至钢材A3或Acm温度上方,始碳化物完全固溶於沃斯田体后急冷,再依上述方法进行球化处理。
使碳化物球化,尚可增加钢材的淬火后韧性、防止淬裂,亦可改善钢材的淬火回火后机械性质、提高钢材的使用寿命。
软化退火处理软化退火热处理的热处理程序是将工件加热到600℃至650℃范围内(A1温度下方),维持一段时间之后空冷,其主要目的在於使以加工硬化的工件再度软化、回復原先之韧性,以便能再进一步加工。
此种热处理方法常在冷加工过程反覆实施,故又称之為製程退火。
大部分金属在冷加工后,材料强度、硬度会随著加工量渐增而变大,也因此导致材料延性降低、材质变脆,若需要再进一步加工时,须先经软化退火热处理才能继续加工钢之退火处理退火处理一般是指将钢升温至某一温度,浸置一段时间后,再以一特定速率冷却下来之处理。
主要目的是软化钢材。
有时亦用以改变其他性质或显微结构。
常见的退火处理有下列几种1. 退火温度:在很多之应用退火处理中,我们只注名所需之退火温度,然后让其在炉中冷却即可。
表4-1所列為一般常见之碳钢退火温度与结果硬度。
在进行退火处理时,最容易造成失败的原因是未能维持炉中温度之均匀性。
越大之炉子越有此种问题。
【精品】几种球化处理比较介绍

几种球化处理比较介绍各种球化处理方法述评发布时间:2012-06-26 07:01:42 浏览次数:217来源:张忠仇,李克锐( 郑州机械研究所,河南,郑州,450052 )摘要:球化处理是生产高质量球铁件的重要环节之一。
通过对国内外球化处理方法的介绍和分析,提出应按照球化剂种类、铸件大小,产量规模、生产方法和环保等条件选择最合适的球化处理方法,逐步改变我国大多数工厂只采用冲入法球化处理的状况。
关键词:球墨铸铁;球化处理方法球化处理是生产高质量球铁件的重要环节之一,我国大多数工厂只采用敞口包冲入法球化处理工艺。
这种方法,球化剂烧损大、镁的回收率低,球化不稳定,特别是镁光烟雾,造成铸造车间环境污染。
人们也在寻求别的途径进行球化处理,如盖包、转包、喂线等等。
某些工厂经过摸索,积累了很好的经验,不断改进,取得很好效果,但也有相当一部分工厂,由于没有掌握要领,采用新方法出现了这样那样的问题,又重新采用冲入法处理。
全国铸铁及熔炼专委会在征求部分专家的意见后,认为有必要在第八届学术会议上展开重点研讨。
1、铸铁石墨球化有关问题自1948年英国莫勒Morrogh和美国INCO公司宣布往铸铁中加入稀土元素铈和镁获得球状石墨,并在1949年开始生产球墨铸铁以来,人们从实践中认识到,使铸铁石墨球化的元素,主要是镁,其它元素(稀土、钙、锂、锶等)在不同条件下虽也有一定的球化能力,但只是用于抑制干扰元素的影响,起辅助球化作用,过量反而会影响球墨的圆整度,影响球化,起不良作用。
郑州机械研究所早在上世纪70~80年代就开始进行稀土、镁元素对铸铁变质作用的研究。
试验表明,镁是最好的球化元素,单独用稀土处理,也能球化,但稀土元素球化效果不好、球形差,易出现各种变态石墨、白口倾向大。
球化剂中含少量稀土元素能降低保证球化的残余镁量,增加石墨球数,消除干扰元素的作用和减少氧化夹杂,因此球化剂应以镁为主,辅以少量稀土。
[1]国外研究工作者如Lalich[2]、Barton[3]也得出了同样的试验结果。
球化处理工艺

加盖铁液包示意图
盖包法球化处理时,球化合金的加入与冲入法 相同,然后将包盖安放在铁液包上,并使其周边封好. 出铁时,将铁液以较大液流注入包盖浇口盆内(保证 铁液在盆内的高度在5~15mm),铁液会通过包盖一 侧的注孔(注孔不得直接对准合金堆放处)流入包 内.这样可使外界的气体与包内完全隔离,减少镁的 氧化烧损,提高镁的吸收率(一般在60℅~65℅以上), 改善劳动环境.球化反应结束后,去除包盖.
球墨铸铁的一关键环节
———球化处理工艺
继此, 转包法、盖包法和包芯喂线法在我国 先后得到了推广和应用.现在我就生产中常 见的球化处理方法作个简要介绍:
(一)压力加镁法 (二)冲入法 (三)转包法 (四)盖包法 (五)包芯线喂线法
(一)压力加镁法
压力加镁法是五十外代就已经开始釆用的 一种球化处理方法,它的基本原理是,当物体周 围介质的压力增加时,该物质的沸腾温度相应 提高,例如,当铁液表面的压力达到0.9MPa时, 镁的沸腾温度提高到1400℃左右,若使球化处 理温度略高于该温度,则镁在铁液中刚刚气化, 产生一定的翻腾,有利于镁的吸收,同时减少了 气化烧损,因而可以有效提高镁的吸收率.
冲入法球化处理前,就将球化处理包预热到暗红色, 预热的目的是减少铁液热量损失.并且防止覆盖剂下 桩实较紧的合金粘结在包底.球化处理时,将球化合 金堆放在预热的包底,上面覆盖硅铁合金,稍加紧实, 然后再覆盖无锈铁屑,苏打等覆盖剂,铁液过高时,可 盖铁板.
这种方法的优点是,处理方式和设备简单,容易操 作,在生产中有较大的灵活性,一般可使用含镁量较 低(<10℅)的各种合金球化剂.但是该工艺在球化处 理过程中镁光,烟尘非常大,劳动环境差,镁的吸收率 不太高,球化剂消耗量大,球化效果及球铁性能不太 稳定.目前应该改进冲入法或换用其它球化处理工艺.
GCr15球化退火类型

GCr15球化退火类型
GCr15钢是轴承钢的主要钢种,一般以热轧态交货,在轴承制造前需要进行球化退火处理。
该退火工艺之所以称为球化,是因为通过退火工艺,可以获得铁素体基体上均匀分布细小的球状碳化物颗粒组织,提高轴承钢性能,并降低轴承钢的硬度,切削加工方便。
一般的GCr15轴承钢的球化退火工艺分为:连续的球化退火工艺、等温的球化退火工艺、周期球化退火工艺3种。
1、连续的球化退火工艺
是指在略高于钢的Ac1温度保温一定时间后,随炉缓冷至650℃后控冷至室温。
GCr15轴承钢连续球化退火一般采用780-810℃的加热温度,奥氏体化以后一般以10-25℃/h的冷速缓冷,这种工艺需要20h以上时间,且球化退火质量不好。
2、等温球化退火
是将轴承钢加热到略高于Ac1温度保温一定时间后,快冷至Ar1以下温度(一般为680-740℃)等温处理,然后出炉空冷至室温。
等温球化退火工艺同样时间较长,一般为10-16h。
3、周期球化退火工艺
是将轴承钢加热到略高于Ac1温度保温一定时间后,快冷至Ar1以下温度等温一定时间,然后再加热至Ac1温度保温一定时间,快冷至Ar1以下温度等温一定时间,此过程重复进行n次,后缓冷至650℃后空冷至室温。
一周期球化退火类似于等温球化退火。
周期球化退火工艺适合轴承钢,其球化效果充分,但控制频繁,所以以往工业上应用不多。
铸造铁液球化处理常用方法介绍
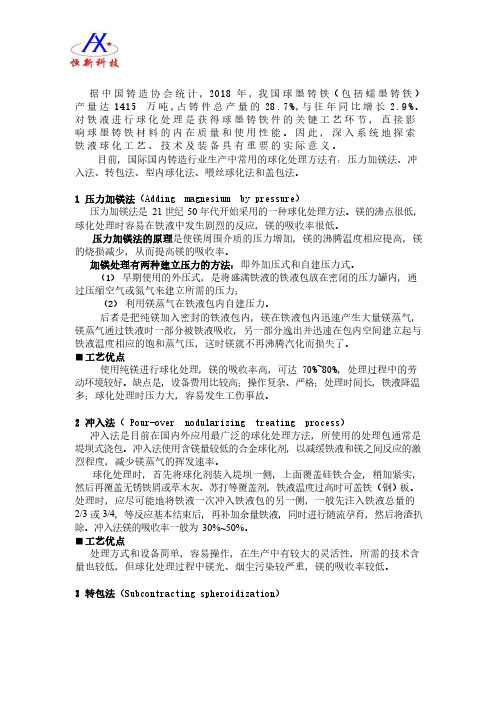
据中国铸造协会统计,2018年,我国球墨铸铁(包括蠕墨铸铁)产量达1415万吨,占铸件总产量的28.7%,与往年同比增长2.9%。
对铁液进行球化处理是获得球墨铸铁件的关键工艺环节,直接影响球墨铸铁材料的内在质量和使用性能。
因此,深入系统地探索铁液球化工艺、技术及装备具有重要的实际意义。
目前,国际国内铸造行业生产中常用的球化处理方法有:压力加镁法、冲入法、转包法、型内球化法、喂丝球化法和盖包法。
1压力加镁法(Adding magnesium by pressure)压力加镁法是21世纪50年代开始采用的一种球化处理方法。
镁的沸点很低,球化处理时容易在铁液中发生剧烈的反应,镁的吸收率很低。
压力加镁法的原理是使镁周围介质的压力增加,镁的沸腾温度相应提高,镁的烧损减少,从而提高镁的吸收率。
加镁处理有两种建立压力的方法:即外加压式和自建压力式。
(1)早期使用的外压式,是将盛满铁液的铁液包放在密闭的压力罐内,通过压缩空气或氮气来建立所需的压力;(2)利用镁蒸气在铁液包内自建压力。
后者是把纯镁加入密封的铁液包内,镁在铁液包内迅速产生大量镁蒸气,镁蒸气通过铁液时一部分被铁液吸收,另一部分逸出并迅速在包内空间建立起与铁液温度相应的饱和蒸气压,这时镁就不再沸腾汽化而损失了。
■工艺优点使用纯镁进行球化处理,镁的吸收率高,可达70%~80%,处理过程中的劳动环境较好。
缺点是,设备费用比较高;操作复杂、严格;处理时间长,铁液降温多;球化处理时压力大,容易发生工伤事故。
2冲入法(Pour-over nodularizing treating process)冲入法是目前在国内外应用最广泛的球化处理方法,所使用的处理包通常是堤坝式浇包。
冲入法使用含镁量较低的合金球化剂,以减缓铁液和镁之间反应的激烈程度,减少镁蒸气的挥发速率。
球化处理时,首先将球化剂装入堤坝一侧,上面覆盖硅铁合金,稍加紧实,然后再覆盖无锈铁屑或草木灰、苏打等覆盖剂,铁液温度过高时可盖铁(钢)板。
钢材球化退火处理及碳化物球化程度评估介绍

钢材球化退火处理及碳化物球化程度评估介绍许传宗金属工业研究发展中心检测技术发展组摘要棒钢(直径14mm以上者称之)及线材(直径14mm以下者称之)系以小钢胚为原料,经加热轧延后制作成盘元,并依客户的要求,再经不同线径抽线加工、退火处理后供应下游业者作为生产原料,而主要的下游市场则为钢线钢缆、螺丝及螺帽等。
其中当盘元加工制作螺丝时,由于易造成破裂现象,因此须经球化退火处理将盘元中之碳化物予以球化,藉以提升延展性,降低硬度以利后续加工处理。
由此可知,球化退火处理乃是螺丝业常用的热处理方法之一,因此本文特针对钢材球化退火处理及碳化物球化程度评估作一简单介绍,以期能对工业界有所裨益。
一、球化退火之简介球化退火(Spheroidizing Annealing)系指将钢材中之层状或网状碳化物,经加热至适当温度后,使其成为球状化的一种热处理方法,特别是高碳的工具钢更是需要进行此退火热处理,而其经球化退火处理后的显微组织如图1所示。
一般而言,球化退火处理的主要目的有二:其一为提高高碳钢的延展性,并降低加工抵抗性使其后续之切削加工或塑性加工易于进行;其二作为工具钢的淬火前处理,使淬火后的碳化物组织分布均匀,进而防止淬裂或变形的发生,同时提高淬火后的韧性与硬度。
值得一提的是,所谓的「碳化物」系指高碳钢中之Fe3C组织;工具钢中之M23C6、M7C3及M3C等组织;高速钢中之M23C6、M6C及MC等组织;轴承钢中之M23C6、M6C及M3C等组织。
图1.1.2%C碳钢之球状碳化物显微组织图二、球化退火之方法如2图所示为各种球化退火的操作方法,至于要采用何种操作方法,主要系根据钢材种类、冷加工程度及球状化程度等来加以判定。
時 間溫度图2.球化退火之操作方法示意图1.长时间加热法(A 1下方的加热):此法乃是将钢材加热至A 1下方的温度范围(约650~700℃),然后长时间保温后徐冷,如图2(a)所示。
此法较适用于淬火钢材及冷加工钢材,但粗大的网状碳化物不易采用此法予以球化。
几种球化处理比较介绍
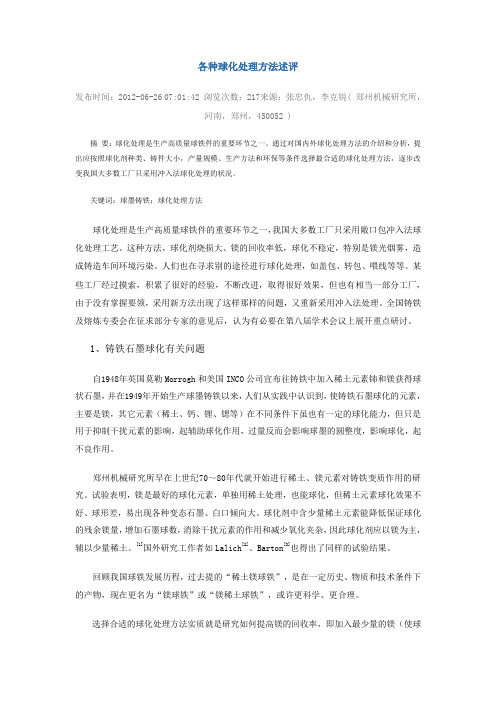
这是撤渣能力好的盖包形式(图11),但包子制造维修麻烦。单嘴茶壶盖包的壶嘴,兼作注入原铁液和倾出处理后的铁液两用,双嘴茶壶盖包(图12),装合金的门设在包盖中间,包底装合金的凹坑也在中间,原铁液从一个嘴流入,处理完的铁液从另一个嘴流出。
2.3 多孔塞(通气搅拌)法
多孔塞法是铁液流入包子,处理合金经过放在包子上方的漏斗加入包内,在包底安装耐火砖多孔塞,通入N2气或其它惰性气体,产生搅拌和对流的处理方法(见图13)。
镁元素的物理性能列于表1。
表1 镁的部分物理性能
在元素周期
表中的序数
原子量
晶格排列
密度
熔点
沸点
比热
熔化潜热
汽化潜热
12
24.32
紧密六
方晶格
1.73g/cm3
651℃
1107℃
0.25卡/克.℃
86.3卡/克
1254±61.8卡/克
图1 敞口包一般冲入法,高径比=2:1
将镁加入铁液中会产生以下问题:
2.1.2 夹层覆盖冲入法(Sardwich, 三明治法)
在包底凹坑装入球化剂上再覆盖一定数量的球铁、废钢、铁屑、硅铁(有时还加入碳化钙)压实,最上面再盖一块预先浇铸的铁板,覆盖一夹层,所谓的Sandwich,三明治法(见图2),可以延缓镁合金的反应(几秒~十几秒),使冲入的铁液有一定高度,建立一个压头后才起反应,使镁蒸气上升过程中尽量被铁液吸收,减小反应激烈程度,提高镁的回收率。
关键词:球墨铸铁;球化处理方法
球化处理是生产高质量球铁件的重要环节之一,我国大多数工厂只采用敞口包冲入法球化处理工艺。这种方法,球化剂烧损大、镁的回收率低,球化不稳定,特别是镁光烟雾,造成铸造车间环境污染。人们也在寻求别的途径进行球化处理,如盖包、转包、喂线等等。某些工厂经过摸索,积累了很好的经验,不断改进,取得很好效果,但也有相当一部分工厂,由于没有掌握要领,采用新方法出现了这样那样的问题,又重新采用冲入法处理。全国铸铁及熔炼专委会在征求部分专家的意见后,认为有必要在第八届学术会议上展开重点研讨。
球化包芯线

一、前言管的生产行业,而且普及很快。
这种球化方法之所以得到广泛的推广和应用,同冲入法球化相比,有如下优点:剂的比重3-4kg/cm3,要轻于铁水的比重7.5kg/cm3。
所以,有一部份球化剂还没有熔化就已经漂浮在熔化剂用钢带包起来,加工成线状再盘起来使用,称为“包芯线”。
球化时再用喂丝机将“包芯线”直接插到球化包内已调好成份的原铁水里进行球化反应,这种喂丝球化,球化剂的吸收率可达到90%以上。
2、采用冲入法球化,每吨铁水需要球化剂15kg-18kg。
采用“包芯线”喂丝球化,每吨铁水需要“包芯线”25m,约10kg。
3、喂丝球化是边送丝边球化,“包芯线”几乎插到球化包的下1/3处进行球化反应,铁水随着球化反应的沸腾而进行搅拌,使铁水球化均匀,达到良好的球化效果。
4、冲入法球化时的除尘,在国内和国际都是很难解决的大问题,烟尘不但污染了环境,而且烟尘中排放的mgo、mgs等有害原素,直接侵害劳动者的身体健康。
喂丝球化是在球化房内进行球化处理的,球化时散发出的烟尘通过除尘器处理掉了,即保护了环境又保护了劳动者的身体健康。
5、冲入法球化包是靠机械传动,人工摇包将铁水翻到扇形包内,即消耗掉一定的机械备件,又增加了工人的劳动强度。
而喂丝球化包,是吊车工自己主、付钩配合,将铁水翻到扇形包内。
二、喂丝球化设备1、喂丝房喂丝房有如下设备构成:⑴喂丝房;⑵喂丝机;⑶台车;⑷液压站;⑸包盖升降机构;⑹包盖;⑺除尘设备;包盖、台车如下图:双工位喂丝房如下图:单工位喂丝房如下图:2、球化包及包梁3、小管使用的中间包4、吊钩称三、喂丝球化对原铁水的要求C≥3.9%,Si≥1.0%,P≤0.03%,S≤0.03%,Mn:0.4一0.6%。
四、“包芯线”的基本化学成份(25-30)Mg :29-31% Si :40-45% Ca :2--7% Re :1—3% Ba ; 1--2% MgO :≤1.0% Al :≤1.5%五、纯镁球化剂“包芯线”加工规范1、芯料粒度:0—6mm, 其中0.5—4mm含量>75%;2、芯线直径13mm(+0.6mm-0),铁皮厚度4.2mm,芯料重230-250g/m;六、“包芯线”质量检查1、包覆应牢固、缝正、不漏粉、不开缝、不折线、无虚包、空包、表面光洁、无油污。
图文讲解:冲入法、盖包法、转包法7种球化处理方法,清楚易懂!
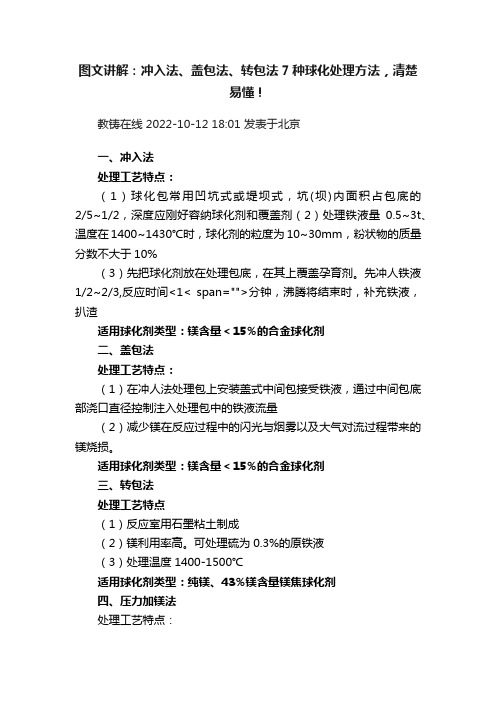
图文讲解:冲入法、盖包法、转包法7种球化处理方法,清楚易懂!教铸在线 2022-10-12 18:01 发表于北京一、冲入法处理工艺特点:(1)球化包常用凹坑式或堤坝式,坑(坝)内面积占包底的2/5~1/2,深度应刚好容纳球化剂和覆盖剂(2)处理铁液量0.5~3t、温度在1400~1430℃时,球化剂的粒度为10~30mm,粉状物的质量分数不大于10%(3)先把球化剂放在处理包底,在其上覆盖孕育剂。
先冲人铁液1/2~2/3,反应时间<1< span="">分钟,沸腾将结束时,补充铁液,扒渣适用球化剂类型:镁含量<15%的合金球化剂二、盖包法处理工艺特点:(1)在冲人法处理包上安装盖式中间包接受铁液,通过中间包底部浇口直径控制注入处理包中的铁液流量(2)减少镁在反应过程中的闪光与烟雾以及大气对流过程带来的镁烧损。
适用球化剂类型:镁含量<15%的合金球化剂三、转包法处理工艺特点(1)反应室用石墨粘土制成(2)镁利用率高。
可处理硫为0.3%的原铁液(3)处理温度1400-1500℃适用球化剂类型:纯镁、43%镁含量镁焦球化剂四、压力加镁法处理工艺特点:(1)球化剂放置在钟罩内,铁叶流入专门的压力加镁包内,紧固包盖,压下钟罩(2)处理温度≥1400℃(3)原铁液尽量含硫量低(4)适用于处理大量铁液,一般每次处理铁液量>3t适用球化剂类型:纯镁球化剂五、型内球化剂处理工艺特点:(1)浇注系统设有反应室,球化剂放入其中(2)原铁液含硫量≤0.04%。
球化剂加入量0.8%左右(3)球化剂颗粒度3-6mm(4)浇注温度≥1450℃适用球化剂类型:含镁量为5%-8%的稀土硅铁镁合金和稀土硅铁镁钙合金六、密封流动法处理工艺特点:1)将反应器置于出铁槽和铁液包之间,在反应器内加入球化剂后,铁液在密封条件下流过反应室吸收球化元素2)球化剂加入量为1.0%~1.1%3)处理温度为1500℃适用球化剂类型:稀土镁合金球化剂七、喂丝线球化法处理工艺特点:1)用自动喂线机把包芯线(含球化剂)均匀地送入铁液中2)包芯线是厚0.2~0.4mm的薄铁管,内装球化剂3)球化1t铁液需包芯线25~30m,Mg吸收率40% ~50%4)二次渣少,无镁光、烟雾适用球化剂类型:镁为20%-45%,稀土为0-6%,钙为1.0%-3.0%,硅为40%-70%,余铁。
球化退火

图9-5 快速球化退火工艺曲线
4、球化退火工艺
①缓慢冷却球化退火 适于共析及过 共析钢,球化 较充分,周期 长。
T Ac3 Ac1
Ac1+10-20℃
10~20℃/h
550℃
缓慢冷却球化退火
t
② 等温球化
适于过共析钢,合 金工具钢,球化充
T AC3 Ac1+20~30℃ AC1 Ar1-(20~30℃)
分,易控制,周期 短,适于大件。
等温球化退火
t
③循环球化退火
Ac1+20℃ Ar1- 20℃
循环 球化 退火
循环周期:要求球化颗粒越细,循环周期越长 适于过共析 C 钢及合金工具钢,周期较短,球化较充分,
但控制麻烦,不宜大件
图9-3 不均匀奥氏体中碳的聚集球化退火 a)缓慢冷却球化退火 b)等温球化退火 c)周期(循环)球化退火 球化退火
d)感应加热快速
(3) 形变球化退火
形变球化退火 将工件在一定温度下施行一定的形变加工后, 再于低于A1温度下进行长时间保温,这种工艺叫做形变球化 退火,低温形变球化,高温形变球化。
球化退火
3、应用:
球化退火主要适用于含C>0.6%的各种高C工具钢、模
具钢、轴承钢的预备热处理。
当中C及中C合金钢要求硬度极低而韧性极高(如用于
冷冲压坯料)时。
低 C 钢球化退火后,不适于切削前处理(太软,发
ห้องสมุดไป่ตู้
粘),但可以改善冷变形的加工性能
时间保温,然后缓慢冷却到450~500℃出炉空冷的 球化退火工艺,如图9-2所示。 主要适合高合金结
构钢及冷变形钢的 球化,不适合原组 织粗大及过共析钢
(1) 低温球化退火 低温球化退火是把钢加热到Ac1以下10~30℃长
球墨铸铁中石墨的球化率及球化级别
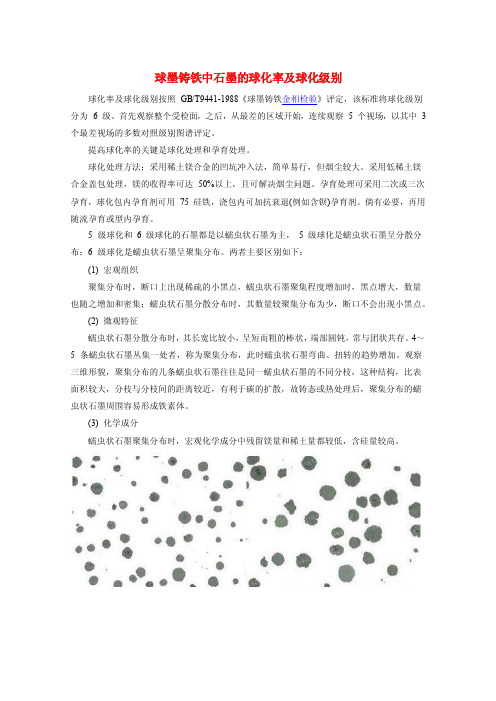
球墨铸铁中石墨的球化率及球化级别球化率及球化级别按照GB/T9441-1988《球墨铸铁金相检验》评定,该标准将球化级别分为 6 级。
首先观察整个受检面,之后,从最差的区域开始,连续观察 5 个视场,以其中3 个最差视场的多数对照级别图谱评定。
提高球化率的关键是球化处理和孕育处理。
球化处理方法:采用稀土镁合金的凹坑冲入法,简单易行,但烟尘较大。
采用低稀土镁合金盖包处理,镁的收得率可达50%以上,且可解决烟尘问题。
孕育处理可采用二次或三次孕育,球化包内孕育剂可用75 硅铁,浇包内可加抗衰退(例如含钡)孕育剂。
倘有必要,再用随流孕育或型内孕育。
5 级球化和6 级球化的石墨都是以蠕虫状石墨为主,5 级球化是蠕虫状石墨呈分散分布;6 级球化是蠕虫状石墨呈聚集分布。
两者主要区别如下:(1) 宏观组织聚集分布时,断口上出现稀疏的小黑点,蠕虫状石墨聚集程度增加时,黑点增大,数量也随之增加和密集;蠕虫状石墨分散分布时,其数量较聚集分布为少,断口不会出现小黑点。
(2) 微观特征蠕虫状石墨分散分布时,其长宽比较小,呈短而粗的棒状,端部圆钝,常与团状共存。
4~5 条蠕虫状石墨丛集一处者,称为聚集分布,此时蠕虫状石墨弯曲、扭转的趋势增加。
观察三维形貌,聚集分布的几条蠕虫状石墨往往是同一蠕虫状石墨的不同分枝,这种结构,比表面积较大,分枝与分枝间的距离较近,有利于碳的扩散,故铸态或热处理后,聚集分布的蠕虫状石墨周围容易形成铁素体。
(3) 化学成分蠕虫状石墨聚集分布时,宏观化学成分中残留镁量和稀土量都较低,含硅量较高。
图号:图号:光学放大倍数:100×光学放大倍数:100×浸蚀剂:未侵蚀浸蚀剂:未侵蚀材料及状态:球墨铸铁材料及状态:球墨铸铁处理:铸态处理:铸态组织及说明:图中石墨呈球状,少数团状,球化率为≥95%,球化级别为1 级。
组织及说明:图中石墨大部分呈球状,余为团状和极少量团絮状,球化率为90%~<95%,球化级别为 2 级。
钢材球化率和球化级别

钢材球化率和球化级别1.引言1.1 概述概述部分的内容可以侧重介绍钢材球化率和球化级别的概念以及其在钢材领域的重要性。
以下是一个示例:钢材球化率和球化级别是钢材领域中一个重要的指标和评价体系。
钢材的球化率是指在特定工艺条件下,在钢材中形成球状组织的程度。
而球化级别是对钢材球化程度的分类和评价。
钢材球化率和球化级别的概念来源于对钢材组织结构的研究和分析。
在钢材制备过程中,钢材的组织结构对其性能和用途有着重要的影响。
通过球化处理,可以改善钢材的韧性、强度、耐磨性等性能,提高其适用性和使用寿命。
影响钢材球化率的因素很多,包括钢材的成分、冷却速度、球化处理温度和时间等。
其中,钢材的成分是影响球化率和球化级别的关键因素之一。
不同成分的钢材在球化处理过程中会出现不同的相变机制和组织结构,从而导致球化率和球化级别的差异。
钢材的球化级别是对球化率的分类和评价。
常见的球化级别包括完全球化、部分球化和未球化等。
完全球化表示钢材中几乎全部组织都呈现球状,球化程度非常高;部分球化则表示只有部分组织呈现球状,球化程度较低;而未球化则表示几乎没有球状组织形成。
准确评价钢材的球化率和球化级别对于钢材的应用和质量控制非常重要。
根据不同的使用要求和工艺需求,合理选择和控制球化率和球化级别可以提高钢材的性能、延长其使用寿命,并减少因材料缺陷而引起的事故风险。
在本文接下来的部分,将分别详细介绍钢材球化率和球化级别的定义、影响因素以及评价标准,同时探讨钢材球化率和球化级别之间的关系以及其在钢材领域中的应用和意义。
1.2 文章结构本篇长文将从引言、正文和结论三个部分展开讨论钢材球化率和球化级别的相关内容。
引言部分将对钢材球化率和球化级别的背景和意义进行概述,以及介绍文章的目的。
通过引入这一研究主题,读者可以对钢材球化率和球化级别的重要性有一个初步了解。
正文部分将分为两个主要章节,分别是钢材球化率和球化级别。
在钢材球化率章节中,我们将对其定义和意义进行阐述,并探讨影响钢材球化率的因素。
几种球化处理比较介绍

几种球化处理比较介绍
球化处理是图形学中经常用到的一种技术,它可以将一个不规则的三维模型转化为一个球形模型,以便于后续处理,在游戏开发和数字艺术领域都有广泛应用。
下面介绍几种球化处理方法及其优缺点。
1. 点云球化
点云球化是一种简单但常用的球化处理方法,它的原理是将三维模型中的所有顶点看作是球心,然后根据球心与周围顶点距离的平均值来计算球半径,最终得到一个球形模型。
该方法不需要复杂的数学计算,处理速度快,但是球体表面的曲率会受到影响,存在局限性。
2. 最小二乘球化
最小二乘球化是一种以最小化重心到球面上的距离平方和为目标的方法。
该方法可以处理非常复杂的三维模型,得到的球形模型曲率比较光滑。
但是需要对三维模型进行预处理,需要先从三角形面片抽取出球心和半径等信息,然后再进行最小二乘计算,因此时间复杂度是比较高的。
3. 基于贝叶斯理论的球化
基于贝叶斯理论的球化是一种新型的球化处理方法,它将球形模型的生成看作是一个概率推断问题,从而利用贝叶斯理论进行求解。
该方法可以由一组观测数据推断出球形模型的分布概率,并进一步优化模型的精度。
相比于其他方法,该方法的精度和稳定性更高,但是计算时间较长,需要使用高性能计算机。
总的来说,不同的球化处理方法适用于不同的场景,开发者需要根据具体的需求选择适用的方法。
如果需要快速生成球形模型并且曲率不需要过分精细,则可以使用点云球化方法。
如果需要处理非常复杂的三维模型并且要求球形模型曲率比较光滑,则可以选择最小二乘球化方法。
如果需要确保模型精度和稳定性,则可以使用基于贝叶斯理论的球化方法。
- 1、下载文档前请自行甄别文档内容的完整性,平台不提供额外的编辑、内容补充、找答案等附加服务。
- 2、"仅部分预览"的文档,不可在线预览部分如存在完整性等问题,可反馈申请退款(可完整预览的文档不适用该条件!)。
- 3、如文档侵犯您的权益,请联系客服反馈,我们会尽快为您处理(人工客服工作时间:9:00-18:30)。
各种球化处理方法述评发布时间:2012-06-26 07:01:42 浏览次数:217来源:张忠仇,李克锐( 郑州机械研究所,河南,郑州,450052 )摘要:球化处理是生产高质量球铁件的重要环节之一。
通过对国内外球化处理方法的介绍和分析,提出应按照球化剂种类、铸件大小,产量规模、生产方法和环保等条件选择最合适的球化处理方法,逐步改变我国大多数工厂只采用冲入法球化处理的状况。
关键词:球墨铸铁;球化处理方法球化处理是生产高质量球铁件的重要环节之一,我国大多数工厂只采用敞口包冲入法球化处理工艺。
这种方法,球化剂烧损大、镁的回收率低,球化不稳定,特别是镁光烟雾,造成铸造车间环境污染。
人们也在寻求别的途径进行球化处理,如盖包、转包、喂线等等。
某些工厂经过摸索,积累了很好的经验,不断改进,取得很好效果,但也有相当一部分工厂,由于没有掌握要领,采用新方法出现了这样那样的问题,又重新采用冲入法处理。
全国铸铁及熔炼专委会在征求部分专家的意见后,认为有必要在第八届学术会议上展开重点研讨。
1、铸铁石墨球化有关问题自1948年英国莫勒Morrogh和美国INCO公司宣布往铸铁中加入稀土元素铈和镁获得球状石墨,并在1949年开始生产球墨铸铁以来,人们从实践中认识到,使铸铁石墨球化的元素,主要是镁,其它元素(稀土、钙、锂、锶等)在不同条件下虽也有一定的球化能力,但只是用于抑制干扰元素的影响,起辅助球化作用,过量反而会影响球墨的圆整度,影响球化,起不良作用。
郑州机械研究所早在上世纪70~80年代就开始进行稀土、镁元素对铸铁变质作用的研究。
试验表明,镁是最好的球化元素,单独用稀土处理,也能球化,但稀土元素球化效果不好、球形差,易出现各种变态石墨、白口倾向大。
球化剂中含少量稀土元素能降低保证球化的残余镁量,增加石墨球数,消除干扰元素的作用和减少氧化夹杂,因此球化剂应以镁为主,辅以少量稀土。
[1]国外研究工作者如Lalich[2]、Barton[3]也得出了同样的试验结果。
回顾我国球铁发展历程,过去提的“稀土镁球铁”,是在一定历史、物质和技术条件下的产物,现在更名为“镁球铁”或“镁稀土球铁”,或许更科学、更合理。
选择合适的球化处理方法实质就是研究如何提高镁的回收率,即加入最少量的镁(使球铁中含有保证球化的Mg 残),获得球化率高且质量稳定的球铁,同时球化处理过程还要安全、平稳、便捷和环境友好。
[4]镁元素的物理性能列于表1。
表1 镁的部分物理性能在元素周期表中的序数原子量晶格排列密度熔点沸点比热熔化潜热汽化潜热1 224.32紧密六方晶格1.73g/cm3651℃1107℃.25卡/克.℃86.3卡/克1254±61.8卡/克图1 敞口包一般冲入法,高径比=2:1将镁加入铁液中会产生以下问题:1)镁在固态铁中的溶解度非常小,在铁液中,随温度升高,碳硅含量增加,溶解度略为增加;2)镁的沸点为1107℃,而球化处理时铁液的温度约1500℃左右,如加入纯镁,不采取安全保护措施,将会迅速汽化,形成很高蒸汽压,引起激烈的沸腾喷溅;3)镁的密度仅为1.73g/cm2,比铁液的密度7.3g/cm3小得多,这将促使加入的镁漂浮至液面而沸腾和燃烧;4)镁和氧有很大的亲和力,两者很易生成白烟状的MgO,会污染铸造车间的空气;5)一部分Mg与S生成MgS;MgO往往与来自铁液和包衬耐火材料中的SiO2生成MgSiO3;这些氧化物/硅酸盐/硫化物混合在一起在铁液表面生成一层粘膜,或形成固体状的夹杂物。
这些夹杂物如未被彻底清除,有可能进入铸件形成夹渣缺陷,成为球铁件报废的主要原因之一。
生产中,以镁回收率(Mg回收率,%)来表示球化处理的效果:Mg回收率很大程度上取决于球化方法;一般随处理温度提高而下降;受处理包的设计和维护以及球化剂(镁合金)的选择影响较大。
2、国内外球化处理方法介绍[5]、[6]、[7]2.1 包内冲入法2.1.1 敞口包一般冲入法这种方法在早期应用比较广泛,国外较多使用Ni-Mg合金,密度比纯镁大得多,如含Mg 10%的Ni-Mg合金密度约可达8.1g/cm3。
将这种合金置于包底凹坑内,迅速冲入铁液,合金不会上漂。
适用生产高镍奥氏体球铁(如排气管、增压器等铸件)。
国内处理包高径比H:D一般较小,约为1.2,现逐渐要求≥1.5,但也比国外小。
此外,国内球化剂大多为镁稀土硅铁,密度较小,所以这种不加覆盖剂的方法基本不用。
2.1.2 夹层覆盖冲入法(Sardwich, 三明治法)在包底凹坑装入球化剂上再覆盖一定数量的球铁、废钢、铁屑、硅铁(有时还加入碳化钙)压实,最上面再盖一块预先浇铸的铁板,覆盖一夹层,所谓的Sandwich,三明治法(见图2),可以延缓镁合金的反应(几秒~十几秒),使冲入的铁液有一定高度,建立一个压头后才起反应,使镁蒸气上升过程中尽量被铁液吸收,减小反应激烈程度,提高镁的回收率。
球化剂密度增大,处理温度适当降低,均可以提高镁的回收率,国外的试验结果见图3。
这种方法在国内被广泛应用,由于国内的球化剂多采用镁稀土硅铁,密度较小,一些工厂要求球化处理包撇渣后直接浇注,铁水包高径比也较小(<1.5),镁反应比较激烈,镁的回收率较低,且不稳定,镁光烟雾大,劳动条件差。
不少企业寻求新的处理方法。
2.2 盖包法这是上世纪70~80年代,随着球铁生产工业应用的迅速扩大,不断改进发展起来的。
在有合金覆盖夹层的铁液包上端放上一个带浇口杯或中间包的包盖,并使进铁液口错开装合金的凹坑180°。
盖包的好处:1)由于盖上包盖后,包中来自空气的有氧空间容积得到有效限制,减少了Mg的氧化烧损,使镁回收率显著提高。
2)球化剂加入量减少,节省铸造成本。
图4是国外用含Mg 5%的MgFeSi合金在同样试验条件下,盖包法处理与其它方法(敞口包冲入法、敞口包+凹坑、Sandwich法)处理时Mg 合金加入量的比较。
3)MgO白烟量减少和被限制在包中,显著地改善铸造车间和周围的大气环境(在国外许多环保管理部门建议和主张铸造厂采用这种方法)。
4)使用包盖能改善保温条件,减少处理过程中铁液温度下降。
但盖包法处理出铁时因看不到液面变化,需有铁液称量装置。
2.2.1 带活动盖的盖包图5是带活动盖的盖包,处理前需打开包盖,加球化剂,合盖,冲入铁液球化处理,处理完毕,又需打开包盖,扒渣、出铁、浇注。
操作比较麻烦,但如配有合适的机械或起吊装置,经过一段时间的磨合,也能熟练掌握。
图6是焦作固德公司带活动包盖的盖包的一种形式。
2.2.2 带固定盖的盖包图7是包盖固定的形式,要求用于原铁液含S较低,处理温度较高,处理后渣量极少的条件,河南欧迪艾铸造公司采用这种工艺。
图8是盖包球化处理烟雾减轻的情况。
图9是河南欧迪艾铸造公司采用的盖包法与一般冲入法球化处理比较,烟雾大大减轻。
2.2.3 包底双凹坑活动盖盖包这是一种改进形式(图10)。
双凹坑轮流使用球化剂室,可以防止合金粘底、粘渣、保持凹坑清洁,适合连续作业。
2.2.4 茶壶嘴盖包这是撤渣能力好的盖包形式(图11),但包子制造维修麻烦。
单嘴茶壶盖包的壶嘴,兼作注入原铁液和倾出处理后的铁液两用,双嘴茶壶盖包(图12),装合金的门设在包盖中间,包底装合金的凹坑也在中间,原铁液从一个嘴流入,处理完的铁液从另一个嘴流出。
2.3 多孔塞(通气搅拌)法多孔塞法是铁液流入包子,处理合金经过放在包子上方的漏斗加入包内,在包底安装耐火砖多孔塞,通入N2气或其它惰性气体,产生搅拌和对流的处理方法(见图13)。
这方法较多用于酸性冲天炉熔炼,原铁液含S较高,需要脱S的场合。
先加入CaC2脱S,扒渣后,再加入FeSiMg或其它Mg合金球化处理。
该方法需要通入冷的N2气约1~几分钟,铁液温降较大;并增加多孔塞维护和更换成本。
通过气体搅拌,镁的回收率一般。
因此目前应用逐渐减少。
但对于用低Mg、高RE合金处理蠕墨铸铁,通过不断搅动铁液,增加稀土和镁的吸收,应该说还是一种较好的方法。
2.4 钟罩法钟罩法球化处理(见图14,图15),适用于纯镁(切成小块)作为球化剂。
它需要有一个耐火材料制成的钟罩和相当重量的包盖,以便承受内装镁块的钟罩由压杆压入铁液液面下时快速和激烈的镁反应过程产生上浮的压力。
为了减缓纯镁的反应激烈程度,有时将镁块外涂一层耐火涂料或采用含Mg 40%的镁合金,或采用浸镁的焦碳(镁焦),目的是为了提高镁的回收率。
钟罩法处理要求车间采取必要的安全防护措施,一般需要在车间设一个有防喷溅防护墙的专门的处理室内进行。
钟罩法适用于酸性冲天炉熔化含S较高的铁液;脱S和球化同时进行的场合,早期一些大量生产球铁管的工厂采用较多。
2.5 压力加镁法此法为对钟罩压入法的改进。
处理时采用能承受10个大气压左右的密封包,由镁金属沸腾产生的镁蒸气自建压力,或是由外部通入惰性气体建立压力。
此法适合纯镁处理,工艺稳定,镁吸收率高,但密封包结构复杂,操作要求高,稍有不慎就会出安全事故。
图16是一种压力加镁包的示意图。
[8]2.5 转包法1967年,GF公司设计和应用镁转包法球化处理。
将一定数量的镁块放入带耐火隔板砖的反应室,同时可附带一些稀土和合金元素,往转包中注入一定量的铁液后盖上盖子,转包转动90°,使铁液与镁块作用约30秒,转包中已处理的铁液倾注入浇包,同进进行孕育。
与其它纯镁处理法一样,转包法可以处理高硫的原铁液,无需预脱硫,伴随迅速脱氧脱硫并球化,Mg回收率可高达50%。
转包法处理生产效率很高,一般3~4次/h。
据了解,目前国内芜湖新兴铸管公司和昆山某外资企业等单位采用转包法球化处理。
图17是转包法球化处理的示意图。
2.6 喂线法喂线法多年来被广泛用于钢铁工业加B、V、Nb等合金元素,以后逐渐在铸铁行业被用于球化处理。
国内外有专门标准规格的球化芯线商品供应,一般芯线Ф9~13mm,将球化剂(颗粒状镁粒或镁合金混合物)用带钢包裹制成芯线成卷供应,每卷长达几千米,重约1吨。
根据需要,芯线中可以包含孕育剂和其它合金元素。
芯线绕在盘上,由喂线机喂入包底铁液不断反应球化,图18是喂线法球化处理工艺示意图。
众所周知,球化剂加入量多少与需处理的铁液重量、温度和原硫有关,而喂线法的优点是它可以根据上述因素,精确地控制芯线的长度和供线速度,烟气通过包盖上的抽烟装置排出室外。
这种方法适用于小至300公斤、大至上百吨的球铁件,无论大或小的铸造厂都可用。
缺点是要求带控制系统的能精确调节的喂线机,一次投资略大,而铠装芯线的价格比一般球化剂贵,所以生产成本较高。
然而,芯线处理的精确控制性、灵活机动的适应性和球化工艺的稳定可靠性、球化和孕育可同时进行以及环境友好性综合评价起来,被认为是一种很有发展前途的方法。
正因为它能精确控制合金的加入量,所以也适合蠕墨铸铁的生产。