公司库存管理及库存控制模型
精选库存控制模型
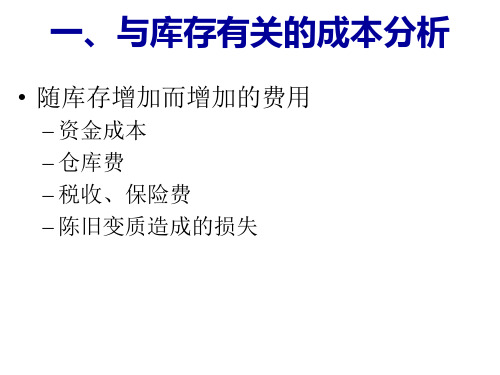
5、有关S的灵敏性分析
说明:减少订货成本对企业总是有好处的。
在EOQ模型中,认为库存的补充是瞬时交货的,而实际生产中往往存在边消耗边补充的情况。这样就会出现以下情况:当生产能力大于需求时,库存是逐渐增加的,因而生产过程是间断的;当生产能力小于或等于需求时,生产过程是连续的,不存在成品库存;当生产能力大于需求时,就要解决多大的生产批量最经济的问题。
3、重订货点
4、有关D的灵敏性分析改变年总需要量,观察经济订货批量的变化
说明:库存的增长速度不应当与销售的增长一样快!
库存系统的规模经济:随着企业销售的增长,需要支持这些销售的库存应当以较慢的速度增长。例如:若销售量翻了一番,则所需的库存量不应当翻一番(应是1.414倍)。规定保持库存以满足特定时期内的供应量,这种库存管理方式并没有发挥库存系统规模经济的作用。
三、经济生产批量
基本参数C—单位生产成本;D—年总需求量;S—每次生产的生产准备费; Q—一次生产的批量;H—单位货物每年的存储成本;p—生产率(单位时间的产量);r—需求率(单位时间的出库量,r<p);TC—年总成本; RL—订货点; LT—生产提前期
年总费用TC =
求得最优解:Q* =
最大库存:Q1= tp(p-r)=Q(p-r)/ p平均库存= Q1 / 2=Q(p-r)/ (2p)年总成本:TC=CD+(D/Q)S+[ Q(p-r)/ (2p)]H年生产次数:n=D / EPQ订货点:RL=rLT
2、经济订货批量模型基本参数C—购买的单位货物的成本;D—年总需求量;S—每次订货发生的费用(与供应商的联系费、采购人员旅差费等);H—单位货物每年的存储成本(H=Ch,h为资金费用率,元/件.年);Q—订货批量;TC—年总成本;
供应链库存控制模型
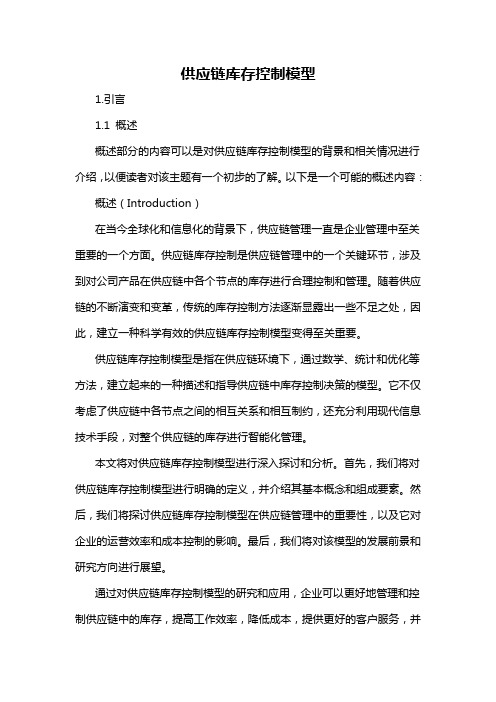
供应链库存控制模型1.引言1.1 概述概述部分的内容可以是对供应链库存控制模型的背景和相关情况进行介绍,以便读者对该主题有一个初步的了解。
以下是一个可能的概述内容:概述(Introduction)在当今全球化和信息化的背景下,供应链管理一直是企业管理中至关重要的一个方面。
供应链库存控制是供应链管理中的一个关键环节,涉及到对公司产品在供应链中各个节点的库存进行合理控制和管理。
随着供应链的不断演变和变革,传统的库存控制方法逐渐显露出一些不足之处,因此,建立一种科学有效的供应链库存控制模型变得至关重要。
供应链库存控制模型是指在供应链环境下,通过数学、统计和优化等方法,建立起来的一种描述和指导供应链中库存控制决策的模型。
它不仅考虑了供应链中各节点之间的相互关系和相互制约,还充分利用现代信息技术手段,对整个供应链的库存进行智能化管理。
本文将对供应链库存控制模型进行深入探讨和分析。
首先,我们将对供应链库存控制模型进行明确的定义,并介绍其基本概念和组成要素。
然后,我们将探讨供应链库存控制模型在供应链管理中的重要性,以及它对企业的运营效率和成本控制的影响。
最后,我们将对该模型的发展前景和研究方向进行展望。
通过对供应链库存控制模型的研究和应用,企业可以更好地管理和控制供应链中的库存,提高工作效率,降低成本,提供更好的客户服务,并在激烈的市场竞争中保持竞争优势。
因此,对供应链库存控制模型的深入理解和运用具有重要的理论和实践意义。
在接下来的内容中,我们将系统地介绍供应链库存控制模型的定义和重要性,以期为读者提供一个全面了解并应用该模型的基础。
1.2文章结构文章结构是指文章的框架和组织方式,它决定了文章的逻辑性和信息传递的清晰性。
文章结构的合理安排可以帮助读者更好地理解和吸收文章的内容。
本文将按照以下结构展开讨论供应链库存控制模型的相关内容:引言:本章将介绍供应链库存控制模型的概述、文章的结构以及研究目的。
首先,我们会简要介绍供应链库存控制模型的背景和基本概念,并引出本文的研究重点。
库存的基本概念与基本模型
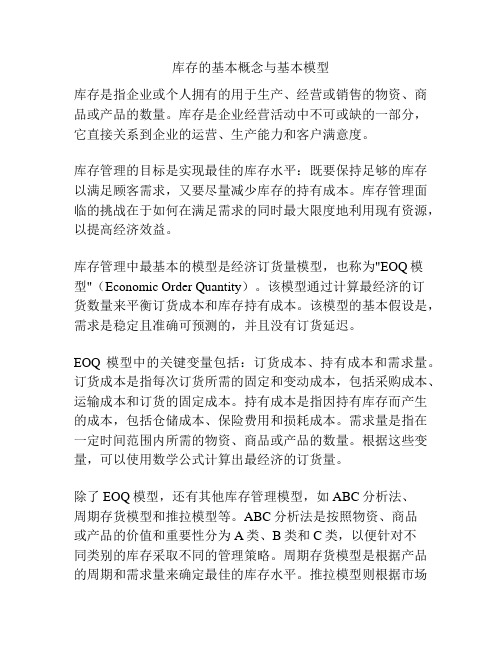
库存的基本概念与基本模型库存是指企业或个人拥有的用于生产、经营或销售的物资、商品或产品的数量。
库存是企业经营活动中不可或缺的一部分,它直接关系到企业的运营、生产能力和客户满意度。
库存管理的目标是实现最佳的库存水平:既要保持足够的库存以满足顾客需求,又要尽量减少库存的持有成本。
库存管理面临的挑战在于如何在满足需求的同时最大限度地利用现有资源,以提高经济效益。
库存管理中最基本的模型是经济订货量模型,也称为"EOQ模型"(Economic Order Quantity)。
该模型通过计算最经济的订货数量来平衡订货成本和库存持有成本。
该模型的基本假设是,需求是稳定且准确可预测的,并且没有订货延迟。
EOQ模型中的关键变量包括:订货成本、持有成本和需求量。
订货成本是指每次订货所需的固定和变动成本,包括采购成本、运输成本和订货的固定成本。
持有成本是指因持有库存而产生的成本,包括仓储成本、保险费用和损耗成本。
需求量是指在一定时间范围内所需的物资、商品或产品的数量。
根据这些变量,可以使用数学公式计算出最经济的订货量。
除了EOQ模型,还有其他库存管理模型,如ABC分析法、周期存货模型和推拉模型等。
ABC分析法是按照物资、商品或产品的价值和重要性分为A类、B类和C类,以便针对不同类别的库存采取不同的管理策略。
周期存货模型是根据产品的周期和需求量来确定最佳的库存水平。
推拉模型则根据市场需求进行预测,决定是否推动生产或以预测订购的方式进行库存管理。
综上所述,库存是企业经营活动中不可或缺的一部分,库存管理的目标是实现最佳的库存水平。
EOQ模型是库存管理中最基本的模型,通过计算最经济的订货量来平衡订货成本和库存持有成本。
此外,还有其他库存管理模型可供选择,以适应不同的需求和情况。
库存管理是企业中非常重要的一环,直接关系到企业的运营效率和经济效益。
合理管理库存不仅可以满足客户需求,提高客户满意度,还可以减少库存成本,优化企业的资金运营。
库存管理的基本原理和方法,基本的库存控制方法

〔二〕、库存问题的分类
• 单周期库存与多周期库存
• 根据对物品需求是否重复可将物品分为单周期 需求与多周期需求。
• 单周期需求:是指对物品在一段特定时间内的 需求。
• 报纸、新年贺卡、圣诞树等属于这种物品; • 易腐食品(如海鲜、活鱼、新鲜水果)属于这种
物品;
• 机器设备的备件也属于这种物品
• 多周期需求:那么指在足够长的时间里对某种 物品的重复的、连续的需求。
• 库存的功用
快速满足用户期望;消除需求波动在 生产-分销间的影响;防止发生缺货; 防止价格上涨, 争取数量折扣
2、库存控制的定义:以控制库存为目的的方法、手 段、技术以及操作过程的集合,是对企业的库存进 行方案、协调和控制的工作。
库存控制的目标: 1、降低库存本钱 2、提高客户效劳水平 寻求二者平衡,到达最正确结合点
• 独立需求库存与相关需求库存 • 独立需求:来自用户的对企业产品和效劳
的需求称为独立需求。独立需求最明显的 特征是需求的对象和数量不确定,只能通 过预测方法粗略地估计
• 相关需求:企业内部物料转化各环节之间 所发生的需求称为相关需求。相关需求也 称为非独立需求,它可以按对最终产品的独 立需求精确地计算出来
0
LT
订货提前期LT
时间
典型库存控制系统之二:固定间隔期系统
订货间隔期固定,每次的订货量为随机变量。
库
最高库存
存 量
S-L2
量S
S-L1
L2
L1 0 订货间隔期t
LT t
LT t
L3 时间
典型库存控制系统之三:最大最小系统
固定间隔期系统的变种,设置一个低限订货点。
库
S
存 量
供应链库存管理模型

通过对VMI和JMI两种模式的分析可得出:VMI就是以系统的、集成的管理思想进行库存管理,使供应链系统能够获得同步化的优化运行。
通过几年的实施,VMI和JMI被证明是比较先进的库存管理办法,但VMI和JMI也有以下缺点:①VMI是单行的过程,决策过程中缺乏协商,难免造成失误;②决策数据不准确,决策失误较多;③财务计划在销售和生产预测之前完成,风险较大;④供应链没有实现真正的集成,使得库存水平较高,订单落实速度慢;⑤促销和库存补给项目没有协调起来;⑥当发现供应出现问题(如产品短缺)时,留给供应商进行解决的时间非常有限;VMI过度地以客户为中心,使得供应链的建立和维护费用都很高。
随着现代科学技术和管理技术的不断提升,VMI和JMI中出现的种种弊端也得到改进,提出了新的供应链库存管理技术,CPFR(共同预测、计划与补给)。
CPFR有效地解决了VMI和JMI的不足,成为现代库存管理新技术。
协同规划、预测和补给(Collaborative Planning ForecastingReplenishment,简称CPFR)是一种协同式的供应链库存管理技术,它能同时降低销售商的存货量,增加供应商的销售量。
CPFR最大的优势是能及时准确地预测由各项促销措施或异常变化带来的销售高峰和波动,从而使销售商和供应商都能做好充分的准备,赢得主动。
同时CPFR采取了一种"双赢'的原则,始终从全局的观点出发,制定统一的管理目标以及方案实施办法,以库存管理为核心,兼顾供应链上的其它方面的管理。
因此,CPFR能实现伙伴间更广泛深入的合作,它主要体现了以下思想。
1)合作伙伴构成的框架及其运行规则主要基于消费者的需求和整个价值链的增值。
2)供应链上企业的生产计划基于同一销售预测报告。
销售商和制造商对市场有不同的认识,在不泄露各自商业机密的前提下,销售商和制造商可交换他们的信息和数据,来改善他们的市场预测能力,使最终的预测报告更为准确、可信。
库存成本、库存控制决策、控制模型及控制决策的定量分析

6
一. 库存控制的基本决策(2-1)
订货量变化对平均库存水平有影响 7
一. 库存控制的基本决策(2-2)
推论:
平均库存量与需求速度和进货速度有关 需求速度一定时,可通过对进货速度的控制,将库存
水平维持在合适的水平上。
库存控制的基本决策主要内容
1. 确定相邻两次订货间隔时间。 2. 确定每次订货订货批量。 3. 确定每次订货提前期。 4. 确定库存满足供货服务率。
60~65
5~10
控制策略:
对A类库存,重点管理,进行连续观察,尽量减少库 存
对C类库存,不再精确管理,可采用定期观察 对B类库存,介于两者之间。
21
3.进行ABC分类的具体步骤
进行ABC分类的具体步骤如下:
(1)首先根据企业的库存物资信息,将各 库存物资占用资金的情况进行汇总,计 算出各种物资占用库存资金比例
例2仍以例1的数据为背景, 若物资的单价随每 次订货量的增加而略有下降。
当订货批量不超过40件时,单价为22元; 订货批量在41至80件时的单价为20元; 订货批量超过80件时的单价为18元; 试求此种条件下的经济订货批量是多少。
Q=0~40,P=22
EOQ1=48 TC=22213
Q=41~80,P=20
库存成本及控制
• 第一 库存管理 • 第二 库存成本与库存控制决策 • 第三 库存控制模型 • 第四 库存控制决策的定量分析
库存管理的基本目标就是防止超储和缺货,在企业现有资源约束下,以合理的成 本为用户提供所期望水平的服务,即在达到顾客期望的服务水平的前提下,尽量 将库存成本减少到可以接受的水平。
经济订货批量 EOQ = 50(件)
精选库存管理的基本模型介绍
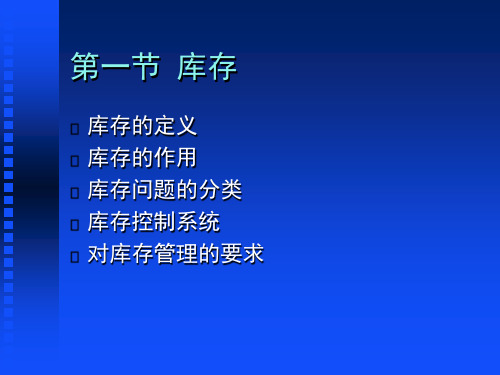
p—生产率(单位时间产量);D—需求率(单位时间出库 量),D<p;Tp一生产的时间;Imax—最大库存量;Q—生产批量;ROP—订货点;LT—生产提前期。
经济生产批量模型(续)
CT = CH + CR + CP =H(Imax/2) + S(D/Q) + pD.问题现在归结为求Imax。由上图可以看出: Imax = tp(p-D).由Q=ptp,可以得出 tp=(Q/p)。 所以,CT=H(1-D/p)Q/2 + S(D/Q) + pD 将式(8-6)与式(8-2)比较,可以得出:
ABC分类
ABC分类的基本思想:20%-80% 物资ABC分类法的实施 列出所有产品及其全年使用量(预测值),将年使用量乘以单价求得其价值,按价值的高低标明各种物资的大小序号;按序号大小将物资重新排序,并计算累积年使用金额和累积百分比;进行整理,即可得到ABC分类汇总表。
ABC分类(续)
ABC分类的运用 A类物资:应施以尽可能紧的控制,包括最完整、精确的记录,最高的作业优先权,高层管理人员经常检查,小心精确地确定订货量和订货点,紧密的跟踪措施以使库存时间最短。B类物资:正常的控制,包括做记录和固定时间的检查; 只有在紧急情况下,才赋予较高的优先权;可按经济批量定货。C类物资:简单的控制,如设立简单的记录或不设立记录,可通过半年或一年一次的盘存来补充大量的库存,给予最低的优先作业次序等。
经济订货批量模型(续)
CT = CH + CR + CP =H(Q/2) + S(D/Q) + pD
S—一次订货费或调整准备费; H —单位维持库存费,H=p·h, p为单价,h为资金效果系数。 D—年需求量; Qo—最佳订货批量或称经济订货批量。
库存控制管理的方法

库存控制管理的方法库存控制管理是指企业为了减少库存成本、降低库存风险、提高库存周转率,对库存进行综合管理的过程。
库存控制管理是企业供应链管理中的重要环节,能够帮助企业实现高效的物流和供应链运作。
下面将在以下几个方面详细介绍库存控制管理的方法。
一、库存分类与管理1.按照性质分类根据物料的性质分类,如原材料、半成品、成品等,分别制定不同的库存管理策略。
比如对于原材料,可以采取定期订购、按需生产等方式,以避免原材料过期或过量等问题;对于成品,可以采取多品种小批量生产的方式,以减少库存损失。
2.按照价值分类按照物料的价值进行分类,将高价值的物料与低价值的物料进行分割管理。
对于高价值的物料,可以采取严格的库存管理策略,如定期盘点、安全库存控制等;而对于低价值的物料,可以采取SLR(低库存再订单)策略,即根据订单量及供应时间进行库存补充。
3.按照需求分类根据产品的需求情况进行分类,将畅销产品和滞销产品分别管理。
对于畅销产品,可以适当增加库存量,以满足市场需求;而对于滞销产品,可以采取库存转移、清仓处理等方式,以减少滞销产品的库存风险。
二、库存量的控制1.确定安全库存量安全库存量是指为了应对不可预测需求和供应延迟等风险所设置的库存。
确定安全库存量可以采用多种方法,如历史数据法、模拟法等。
通过合理设置安全库存量,能够确保及时满足客户需求,并减少因供应不可靠而导致的库存风险。
2.优化订货周期订货周期是指从下达订货到库存到货的时间。
通过优化订货周期,可以减少订单处理时间,提高物流效率。
可以采取多种方式来缩短订货周期,如采购自动化、供应商合作等。
3.建立有效的预测模型建立有效的预测模型是准确预测需求的关键。
可以采用历史数据法、趋势分析法等来建立预测模型,通过对需求进行精确的预测,能够减少库存量、提高库存周转率。
三、库存流转和盘点管理1.制定物料流转流程建立合理的物料流转流程,加强对物料流转过程的管理,能够减少因物料流转不畅而导致的库存积压和损失。
库存ABC分类与库存控制模型
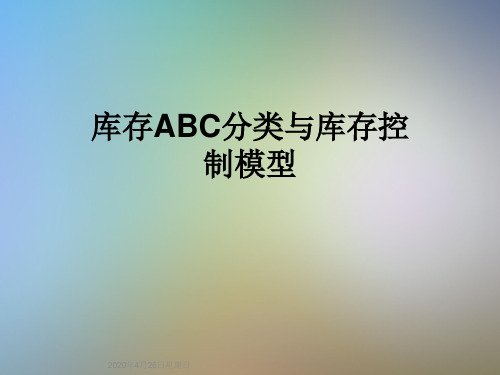
本、搬运费、保险费、过时损失、折旧费等。若存储成本
高,则应保持低库存量并经常补充库存。
•
2、订购成本(Setup Cost/Trade Cost)
•
采购每批物料时通常须耗费的成本。如准备购买订
单或生产订单所引起的管理和办公费用,一般为固定成本
。
•
3、短缺成本
•
停工待料或无法立即满足需求所发生的各种损失。
• 以库存金额计算:
•
ITR=一定期间的出货金额/同期间的库存金额
• 以库存数量计算:
•
ITR=一定期间的出货数量/同期间的平均库存数量
第二节 库存的ABC分析
一、基本思想:
源自帕累托(Pareto)图,最早用于解释经济学中的现象:少数人掌握着大 多数财富。美国GE公司首先应用于库存管理,创造库存的ABC3级分析法。 对库存进行分类的目的:按利用价值对存货单元加以区别对待,采用不同 的库存控制策略分别进行控制。 将存货单元累计20%,但是成本却占总成本的80%的物料划分为A类 库存 将存货单元在20%—50%,成本占总成本15%的物料划分为B类库存 将存货单元在50%—100%,成本占总成本5%的物料划分为C类库存
按下限(30%)计算,该公司将可以节约300多万美圆。
减少库存节约的成本可看作是利润的增加。
企业库存量大的好处之一就是企业不会因缺货造成损失,但库存量 大容易使许多问题被掩盖起来,这不利于发现问题,解决问题,不 符合精益思想的原则。
库存是一把“双刃剑”。
库存分析和控制的重要性:
•所有的公司(包括JIT方式下的公司)都要保持一定的库存因为 :
•
处于运输过程中的物料(成品、半成品、原材料
)及两地之间的库存。运输库存取决于运输的时间。
第5章库存经济分析之库存概述及库存模型

1-2
库存的作用和类型
库存的作用:
为预期的用户需求提供存货 将生产与销售过程分开 可以从数量折扣中得到好处
可以套购保值
防止存货告罄
使生产过程得以顺利进行
1-3
库存的作用和类型
订 单
供 应 厂 家 采购 原材料 库存 备件库存 成品 库存 顾 客 发运 半成品 库存
收货
供应过程
1-13
准时制库存
是维持系统完整运行所需的最少库存。
库存水平
库存水平
资源不平衡
生产停 工时间 质量不一致
资源不平衡
人员绩效差
生产停 工时间 质量不一致
准备时间 送货延误 人员绩效差 准备时间 送货延误 计划有误 (A) 计划有误
(A)减少库存就能找到问题
(B)解决这些问题,然后再减少库 存。最后物料就能顺利地流通
1-9
库存管理 2)ABC分类结果的运用
A类物品:应集中力量进行分析与控制以减少库存,要较准确地 确定定货点和定货量; B类物品:进行正常地控制,可按经济批量定货; C类物品:尽可能简单地控制,可保持较大的库存;
3)库存记录精确度要求(美国生产与库存控制协会(APICS))
A类:±0.2% B类:±1% C类:±5%
1-14
库存管理
库存管理的二个衡量指标
库存周转率:
第5章 库存经济分析之库存概述及 库存模型
库存的作用和类型
库存管理 准时制库存 库存模型 库存控制系统 边际分析
1-1
库存的作用和类型
制造系统中的库存可分为以下四类:
原材料库存 指从工厂外部购买的,在工厂内 的制作/装配过程中使用的零部件、组件或材料 在制品库存(WIP) 正在生产线中的所有未完 工的部件或产品 成品库存(FGI) 完工而尚未售出的产品 备件库存 用以维修或维护生产设备的部件
库存控制模型

随机型存储控制模型
缺货情况与安全库存量:
在定量订货方式中,每当库存量降至存货点s是,即按一定批量
Q(Q=S-s)
订货补充。如图所示:
Q(t)
S
Q
s S
ss
S:最高库存量 s:订货点 ss:安全库存
0 T
时间(t)
随机型存储控制模型
如果订货后交货并在交货期间无过量使用,并不动用安全库存量ss,如果订货 后不按时交货,出现延误时间,将要动用安全库存量,以应对延误时间内的用 量;如果在订货到交货期间,出现过量使用,库存量下降速率增加,则也要动 用安全库存量,以应付缺货情况。
第二节 ABC库存控制法
ABC库存控制法
ABC库存控制法
三、ABC分析法的应用
A类商品的管理方法 (1)采取定期订货方式,定期调整库存; (2)增加盘点次数,以提高对库存量的精确掌握; (3)尽量减小货物出库量的波动,使仓库的安全储备量降低; (4)A类商品必须保证不拖延交货期; (5)A类商品是价值分析的对象; (6)货物放置于便于进出的地方; (7)货物包装尽可能标准化,以提高库场利用率。
3、订货点的确定
需求量和提前订货时间随机波动,订货点的库存量就需要根据历史的 波动数据求得平均和平均提前订货时间,或者根据最大提前时间来计算。
库存管理与库存控制

实时调整策略要求企业具备快速响应的能力,及时调整生产和采购计划。
03
02
01
联合管理
联合库存管理是一种合作性的库存管理方式,通过供应商和零售商之间的合作,共同管理库存。
共享信息
联合库存管理需要共享需求信息和库存信息,以便供应商和零售商能够协同决策。
降低库存成本
通过联合库存管理,可以降低双方各自的库存成本,提高整个供应链的效率。
总结词
实时库存更新系统是一种利用信息技术实时更新库存数据的管理系统,可以提高库存数据的准确性和及时性。
详细描述
实时库存更新系统通过与仓库管理系统(WMS)或企业资源规划(ERP)系统的集成,实现库存数据的实时更新。这种系统可以减少人为错误和延迟,提高库存数据的准确性和及时性,帮助企业更好地掌握库存情况并做出相应的决策。
库存管理可以帮助企业应对市场风险、供应风险等不确定性因素,降低企业的经营风险。
02
库存控制方法
总结词
ABC分类法是一种有效的库存管理方法,根据物品的重要性和消耗量对库存进行分类,以便更好地分配资源和管理库存。
详细描述
ABC分类法将库存物品分为A、B、C三类,其中A类物品数量少但价值高,B类物品数量较多但价值较低,C类物品数量最多但价值最低。通过对不同类别的物品采用不同的管理策略,可以更有效地控制库存,降低库存成本并提高库存周转率。
经济订货量模型是一种通过计算最优订货量和订货时间来降低库存持有成本和缺货成本的模型。
总结词
经济订货量模型(EOQ)考虑了订货成本、库存持有成本和缺货成本等因素,通过数学模型计算出最优的订货量(EOQ)和订货时间。该模型可以帮助企业确定最佳的采购计划,降低库存成本并保持足够的库存水平以避免缺货。
某公司库存管理与库存控制模型

库存管理第一节库存管理过程一、库存管理过程1.库存的经济分析库存管理的任务是用最少的费用在适宜的时间和适宜的地点获取适当数量的原材料、消耗品或最终产品。
库存是包含经济价值的物质资产,购置和储存都会产生费用。
库存成本是建立库存系统时或采取经营措施所造成的结果。
库存系统的成本主要有购入成本、订货费、保管(储存)费用及缺货成本。
⑴购入成本某种物品的购入成本有两种含义:当物品从外部购买时,购入成本指单位购入价格;当由企业部制造时,指单位生产成本。
单位成本始终要以进入库存时的成本来计算。
对购物品来说,单位成本应包括购价加上运费。
对于自制物品来说,单位成本则包括直接费、直接材料费和企业管理费用等。
⑵订货费用(或称订购成本)定货费用是从需求的确认到最终的到货,通过采购或其他途径获得物品或原材料的时候发生的费用。
订购成本包括提出订货申请单、分析货源、填写采购订货单、来料验收、跟踪定货等各项费用。
主要包括以下因素:①部各部人员的费用,如采购、财务、原材料控制与储存人员的工资等。
②管理费用,如办公用品、、计算机系统的应用。
订货费用的主要特征是与采购次数直接有关 ,而与订货量的大小几乎无关。
因为这个原采购必须制定政策与战略,以便从市场上以最有效的订货批量来进行采购,而不仅仅根根据生产与需求。
⑶保管(储存)费用保管费用包括:收货、存储和搬运费用。
最重要的保管费用是机会成本,就是资金投资在库存上比投资在其他领域的收益哪个更大。
保管费用包括:①存储费用取暖、照明以及仓储建筑物的折旧。
②人员费用库存运行的人力资源。
③库存记录的保存费用管理和系统费用,包括盘点和检查库存。
④安全与保险⑤库存损坏与废弃⑥折旧这些都是可以控制的费用,用来衡量库存过程的管理效率。
⑷缺货成本缺货成本是由于外部或部中断供应所产生的。
当企业的用户得不到他们的全部订货时,外部缺货;而当企业部某一个班组或一个部门得不到它的全部订货时,叫做部缺货。
2.库存控制政策与职能库存控制就是决定和调节库存物品的种类和数量,使之既不过剩又不缺货。
运营管理第8章 库存管理

68为可行的订货量
订货量大于68的数量折扣点只有一个,即75单位。 分别计算订货量为68单位和75单位时的总成本CT(68)和CT(75)。 CT(68)=(68/2)×4.20+(1200/68)×8+1200=42283.98元 CT(75)=(75/2)×3.90+(1200/75)×8+1200×32.50=39274.25(元)
DL为提前期内需求的期望值
总库存费用
CT S D Q H Q 2 RL DL C S D Q y RL p y y RL
最佳订货点RL*
HQ p y p DL RL 1 p DL RL C D y RL S
3.价格折扣模型
有数量折扣的价格曲线
采购批量小于Q1时,单价为p1 采购批量大于或等于Q1而小于Q2时,单价为p2 采购批量大于或等于Q2时,单价为p3。
p3<p2<p1
有两个折扣点的价格折扣模型的费用
总费用曲线也是一条不连续的曲线 最经济的订货批量仍然是总费用曲线CT上最低点所对应的数量
成本最低点
3)
E (ROP) (y 55)p(y)
S y 56
58
(56 55) 0.06 (57 55) 0.03 (58 55) 0.02 0.18 再代入: Q 2D[S C SE S (ROP)] H 2 1800 [30 8 0.18] 61.4 200 0.15
曲线斜率为零的点 曲线的中断点
有价格折扣最优订货批量的计算步骤
(1)取最低价格代入基本EOQ公式求出最佳订货批量 Q*,若Q*可行(即所求的点在曲线CT上),Q*即 为最优订货批量,停止。否则转步骤(2)。 (2)取次低价格代入基本EOQ公式求出Q*。如果Q*可 行,计算订货量为Q*时的总费用和所有大于Q*的 数量折扣点(曲线中断点)所对应的总费用,取其 中最小总费用所对应的数量即为最优订货批量,停 止。 (3)如果Q*不可行,重复步骤(2),直到找到一个可 行的EOQ为止。
库存管理和库存控制

一、库存管理和库存控制(一)库存管理是指优化物资的存储,以便使企业在合适的时间,以最低的成本,满足用户对特定数量和质量产品的需求的方法。
(二)库存管理的目标:1、削减库存2、库存风险的明细化3、降低生产销售计划的周期4、在保持客户服务水平的前提下实现成本的最优化。
(三)降低库存和库存控制要做到以下两点.1、需求变动原因的收集和分析,制定高精度的销售计划,同时通过缩短计划和周期,尤其是销售计划和生产的周期来达到削减库存的目的;通过基于客观指标的需求预测模型,依靠统计手法所得的需求预测,和反映销售意图的销售计划分离的机制来使库存风险的明细化;同时通过系统引入,预测、销售计划业务的效率化,各业务单位的生产销售计划标准化、共享化,来制定未来销售拓展计划,并进而达到生产销售计划周期的降低。
2、在完成了上述设计之后,更关键的是在组织和流程方面进行全面的重新确定。
在组织方面,重新设计和计划决策部门的职能,划分了需求预测和销售计划的职能;在业务流程设计方面,设计能实现每周计划的业务流程、建立了以统计的预测手段为前提的需求预测流程和独立的需求预测流程和销售计划流程.由于有了组织和流程的保证,使得整体的设计得以顺利实现。
二、配送中心(一)配送是在经济合理区域范围内,根据客户的要求,对物品进行拣选、加工、包装、分割、组配等作业,并按时送达指定地点的物流活动。
(二)配送中心是指按客户要求配备产品并发送到客户的一个中介组织,均衡、合理地分布在全国各地的多个配送中心就形成一个配送网络。
(三)重新整合公司的运输配送网络。
对于在北京、上海、广州、武汉、成都等五个中心城市,设立了自己的区域销售分公司的基本上建立配送中心,各配送中心是接受并处理末端用户的订单信息,对于由总公司运来的货物进行分拣,根据用户订货要求进行拣选、加工、组配,送货,以提高营运效率。
从原有的总部直接向末端用户配送变成了由中央分发中心至区域物流中心,再到直供商,形成了“中央仓-区域仓—客户”的配送网络体系,对原来的仓库重新整合.在地理上重新规划企业的供销厂家分布,以充分满足客户需要,并降低经营成本。
库存控制模型

式中,T为订货间隔期;m为每年订货或检查次数, m=1/T;D/(2m)为年平均库存量。
库存控制模型
要使TC最小,将式(5-7)对T求一阶导数,并令导 数为0,得到经济订货间隔期T的数学模型为:
库存控制模型
图5-2 订货量与库存有关成本之间的关系
库存控制模型
2. 订货点的确定
经济订货批量的确定,可以为管理者选择合适的订货批 量和作出正确的库存控制决策提供辅助决策信息。下一步 的工作是在确定订货批量的基础上,确定何时发出订货指 令,即确定订货点。定量订货法的库存变化情况如图5-3所 示。此图中假设单位时间内的需求量或供货不稳定,企业 需持有安全库存。
库存控制模型
图5-3 定量订货法的库存变化情况
库存控制模型
订货点=订货提前期需求量+安全库存=需求速度×订货提前期+安全库存 (5-4)
安全库存用数量表示,则订货点的计算公式为:
ROP=d×L+S
(5-5)
式中,ROP为订货点;d为需求或使用速度,常用日需求量;L为订货提前 期,常以日为单位;S为安全库存。
安全库存若用时间表示,则订货点的计算公式为:
ROP=d×(L+S) (5-6)
库存控制模型
(二) 经济订货间隔期模型
1. 经济订货间隔期问题
在定期订货系统中,经济订货间隔期就是在定期订货系 统中使库存总成本最低的订货间隔期,经济订货间隔期决定 某项或数项物品应在何时发出订单,即物品的订货都是按固 定的时间周期进行的。
库存控制模型
二、 库存控制基本模型
- 1、下载文档前请自行甄别文档内容的完整性,平台不提供额外的编辑、内容补充、找答案等附加服务。
- 2、"仅部分预览"的文档,不可在线预览部分如存在完整性等问题,可反馈申请退款(可完整预览的文档不适用该条件!)。
- 3、如文档侵犯您的权益,请联系客服反馈,我们会尽快为您处理(人工客服工作时间:9:00-18:30)。
库存管理第一节库存管理过程一、库存管理过程1.库存的经济分析库存管理的任务是用最少的费用在适宜的时间和适宜的地点获取适当数量的原材料、消耗品或最终产品。
库存是包含经济价值的物质资产,购置和储存都会产生费用。
库存成本是建立库存系统时或采取经营措施所造成的结果。
库存系统的成本主要有购入成本、订货费、保管(储存)费用及缺货成本。
⑴购入成本某种物品的购入成本有两种含义:当物品从外部购买时,购入成本指单位购入价格;当由企业内部制造时,指单位生产成本。
单位成本始终要以进入库存时的成本来计算。
对购物品来说,单位成本应包括购价加上运费。
对于自制物品来说,单位成本则包括直接费、直接材料费和企业管理费用等。
⑵订货费用(或称订购成本)定货费用是从需求的确认到最终的到货,通过采购或其他途径获得物品或原材料的时候发生的费用。
订购成本包括提出订货申请单、分析货源、填写采购订货单、来料验收、跟踪定货等各项费用。
主要包括以下因素:①内部各部人员的费用,如采购、财务、原材料控制与储存人员的工资等。
②管理费用,如办公用品、电话、计算机系统的应用。
订货费用的主要特征是与采购次数直接有关,而与订货量的大小几乎无关。
因为这个原采购必须制定政策与战略,以便从市场上以最有效的订货批量来进行采购,而不仅仅根根据生产与需求。
⑶保管(储存)费用保管费用包括:收货、存储和搬运费用。
最重要的保管费用是机会成本,就是资金投资在库存上比投资在其他领域的收益哪个更大。
保管费用包括:①存储费用取暖、照明以及仓储建筑物的折旧。
②人员费用库存运行的人力资源。
③库存记录的保存费用管理和系统费用,包括盘点和检查库存。
④安全与保险⑤库存损坏与废弃⑥折旧这些都是可以控制的费用,用来衡量库存过程的管理效率。
⑷缺货成本缺货成本是由于外部或内部中断供应所产生的。
当企业的用户得不到他们的全部订货时,外部缺货;而当企业内部某一个班组或一个部门得不到它的全部订货时,叫做内部缺货。
2.库存控制政策与职能库存控制就是决定和调节库存物品的种类和数量,使之既不过剩又不缺货。
目标是在库存过多和库存过少之间获得平衡。
维持较高的库存水平是一个简单地减少缺货风险的方法。
进一步说,可以减少订货次数以降低订货费用。
但是,保管费用提高了。
另一方面,只维持较低的库存水平是一个困难的决策。
这不仅是因为依赖供应商的准时送货,而且提高了订货次数,反过来提高了库存的管理时间与费用。
但是管理费用降低了。
库存的范围和深度取决于库存物品的属性(数量、时间、频率、范围、可预测性)、缺货的承受程度、采购费用、库存费用以及采购提前期。
库存管理过程包括:确定需求、存货识别与编码、存货分类以及采购提前期管理等过程。
3.库存管理过程⑴确定需求——需求识别与需求预测对库存进行管理,首先要进行需求识别与需求预测。
⑵存货识别与编码要使库存管理更为有效,必须对存货进行识别和编码。
①存货识别与合理化库存中的存货包括很多不同种类的物品, 最容易的识别方法是用起名字或描述性文字。
②存货编码当数量很多种类很广时,只使用名字和描述性文字是不合适的,容易混淆,所以这时候通常采用编码。
采用编码就要开发一个编码系统,制定编码规则。
目前,有很多不同的编码体系和编码方式。
常见的一种编码方式是对要描述的物品属性,如物品自然属性、物品最终用途、库存地点、供应源以及最终用户进行分组,然后按照一定的规则进行编码。
编码方法如组码和条形码⑶服务水平与安全库存的定义①服务水平服务水平是指顾客提出订货要求时,企业能够满足用户需求的可能性。
如果整个生产系统在任何时候均能满足全部用户的订货需求,则其服务水平为100%,如果能满足95%的需求,则其订货服务水平为95%,也可以称此时的生产系统的缺货概率为5%。
②安全库存安全库存可以预防预测与实际消耗之间的差异,以及期望运输时间与实际之间的差异所造成的损失,在补充周转库存时预防缺货。
它也是在库存水平上增加一部分以满足不可预见的需求,如不稳定的需求、供应困难以及其他紧急情况。
计算安全库存要以需求因素(包括需求变化、预测不准确和缺货)、供应因素(包括采购提前期变化、采购提前期估计不准确、供应的安全性等因素)、库存策略(包括缺货的危害、物品费用、报废损失、损耗率和空间需求)以及客观条件(包括理货、质量检验、机器工厂布置、零件、工具、检验设备、叉车的流动、工厂和仓库的布置)等因素为基础。
安全库存一般可以用提前期需求比例法、某一个特定时间的值以及均差法三种不同的方法来确定。
1)提前期需求比例法将安全库存表示为一设定的时间段,用该时间乘以该段时间内平均需求量。
对大多数物品来说,50%提前期的需要量一般就可以作为一个合适的库存数量。
例如:每日需求=(450/30)=15单位提前期=10天提前期的需求=10×15=150单位安全库存=150×50%=75单位每天15单位的需求与10天提前期的乘积150就是这段时间的总需求。
安全库存是这个数的一半即750这实际是5天的库存量。
这种方法对许多物品来说会导致过多或过少的安全库存,如对于那些有很长的可靠的提前期而且需求相当稳定的物品。
用这种方法,如果一个进口产品有12周的提前期,6周的需求量为安全库存,但是如果运输是及时的而且消耗是逐月稳定的,那么安全库存就太大了,这意味着太多的资金占用在非生产性的库存上。
对于有很短的提前期而且需求变动非常大的物品,如果有一周的提前期,则安全库存有3到4天的需求量;如果需求变化非常大,安全库存已经不能满足用户的需要了,存在着很高的缺货风险。
2)供应天数法 这种方法是人为指定一段时间的供应量作为安全库存。
因为每个月没有足够的时间去检查每种物品的安全库存指标,这种按一定天数供应量计算的安全库存往往需要足够大的安全库存,结果是导致库存量大大增加。
例如,某种物品的每天的使用量为1Okg,按5天的供应量作为安全库存时,该物品的安全库存为5Okg(5×10=50)。
3)均差法 因为安全库存是为了保证用户在采购提前期和在接收补充库存的延迟期内的无规律的需求得到满足,因此,安全库存的数量取决于需求和提前期的变化。
需求和提前期变化越大,则这种物品的安全库存越大。
这种方法将安全库存表示为一个用某常数计算得来的数字,该常数反映期望服务水平与提前期用量以及提前期的标准偏差(或绝对方差)。
⑷存货分类存货有很多种分类,其中的一些如下:原材料一在成为产成品的一部分之前需要处理;零件一组装到产成品中;配件一安装到产成品上;包装一提供必要的保护;产成品一准备销售给最终消费者的物品;多余物品一废弃物、垃圾、生产过程中的废物等。
⑸采购提前期管理①采购提前期的定义无论订货数量多少,从订单发出到接收物品总有一个延迟的时间,这就是采购提前期(或称为采购前置时间)即从采购订单发出到收到货物的时间间隔。
采购前置时间可以是不变的,也可以是可变的。
当采购前置时间可变时,可以用某种概率分布来描述它。
采购前置时间一般可有以下几部分组成,其表达式为:54321T T T T T L ++++= (3-1)式中:L 一一补充库存的采购前置时间;1T 一一企业内部的订货准备时间;2T 一一订单传送时间;3T 一一供应厂家准备物品的时间;4T 一一运输的时间;5T 一一入库前对物品进行验收等活动所占用的时间。
可以看出除1T 和5T 可控外,其他变量都是不可控的。
②采购提前期的计算在计算订货数量时要考虑订货提前期。
订货提前期要考虑安全库存费用与缺货费用之间的平衡。
通常假设采购提前期是固定的,但实际上随着产品处于生命周期的不同阶段这个数字变化很大。
在计算机系统中常根据第一次购买或制造的时间设定采购提前期,这比处于生命周期中间阶段的时间要长。
计算采购提前期可以用许多不同的方法,常见的方法有:①根据最后一次订货的提前来确定采购提前期;②利用某一个固定的期间(如12个月)的平均值作为采购提前期;③利用所有采购提前期的平均时间作为采购提前期。
例3-1 某一种物品的采购提前期的历史数据见表3-1所示,表中记录了该物品10次的采购提前期,分别利用上述三种不同的方法计算其采购提前期。
解:①按最后一次订货的提前期来确定采购提前期。
A物品的采购提前期=9次②利用固定时间的期间(如表中的6次和10次)的平均值作为采购提前期。
A物品的采购提前期=(9+11+10+9+9)÷5=10天③利用所有采购提前期的平均时间作为采购提前期。
这时A物品的采购提前期=(10+8+7+5+8+9+11+10+9+9)÷10=8.6=9天⑹库存出库库存出库政策取决定物品消耗的顺序,确保物品货架寿命比储存的时间长。
先进先出(First In First Out, FIFO)这种政策按照进库的顺序进行处理,最先进库的物品最先使用,避免存储时间超过货架寿命。
物品被排成一列就可这样处理。
此原则一般适用于寿命周期短的商品,如感光纸、胶卷、食品等。
后进先出(Last In First Out, LIFO)指最后进库的物品最先出库。
堆成一堆的物品就可这样处理。
随机政策就是物品出库没有规则。
在零售时,标识日期的库存要经常检查和出库。
没有标识日期的库存要保持清洁和新鲜的外观。
将新的库存放在货架的后面以保证货架清洁,整齐。
二、支持新设备1.新设备备件库存的特点设备是企业物质系统的重要组成部分,是企业生产和再生产的重要物质与技术保证。
设备技术状态的好坏,直接影响企业产品的数量和质量,决定企业的服务水平。
因此,为保证设备能良好运行,需要对设备进行维护、保养和维修,需要储备一定数量的备件库存。
采购和使用新设备时,其部件和整体的损耗是未知的。
在确定使用新设备之前,必须确定能维持其维护和修理的初始供应量。
设备的初始供应量一般是根据制造商的建议来确定的。
制造商给出试验和模拟测试新设备的结果报告,它指明了新设备中部件的使用以及整件替换的期限。
2.新设备备件库存数量的确定确定新设备的备件库存数量,必须掌握设备的故障发生规律,根据故障发生规律来确定其备件的库存数量。
其备件的库存数量。
通过研究发现,在设备使用的不同时间阶段,设备的故障发生率是不同的。
故障发生率是指单位时间内故障发生的比率。
所引入的新设备或产品有一个重要的特征,即其使用备件和元件的“浴缸曲线”效应。
如图3-1所示,它将设备使用维修期间内的设备故障状态分为3个时期:故障发生率12 使用时间图3-1 浴缸故障发生曲线第1个时期称为初期故障期(10T t ≤),这一时期的特点是故障率由高到低发生变化。
当新设备的有些操作问题在试运行中没有被发现时,这些新设备在最初的使用阶段会经常出现故障。
这样导致了备件和元件的使用数量很高。
随时间的延续,设备逐渐进入第2个时期,是偶发故障期。