900万吨年减压蒸馏装置设计开题报告
【开题报告】年产100万吨中东含硫原油常减压装置设计(常压系统)

开题报告化学工程与工艺年产100万吨中东含硫原油常减压装置设计(常压系统)一、综述本课题国内外研究动态,说明选题的依据和意义石油是现代工业的血液,我国的工业生产和经济运行都离不开石油,但是又不能直接作为产品使用,必须经过加工炼制过程,连制成多种在质量上符合使用要求的石油产品,才能投入使用。
中国炼油工业迅速发展,据美国《油气杂志》世界炼油特别报告统计,2005年中国原油年加工能力达3.12亿吨,超过俄罗斯和日本,成为仅次于美国的世界炼油大国。
根据统计,2005年中国共有51座炼厂,炼厂数和炼油能力均位居世界第二。
但是,中国石油产品质量还相对较低,汽车排气污染控制愈显重要。
中国融入世界清洁燃料进程,不断提高炼油技术水平,尽快与国际接轨,任务紧迫而重大。
国民经济和国防部门众多的各种应用场合对石油产品提出了许多不同的使用要求。
随着我国社会经济情况的变化、科学技术水平以及工业生产水平的大幅度提高,对石油产品质量指标的要求不断严格,所要求的石油产品的品种和数量也不断增加。
目前,我国原油的年加工量约为2亿吨。
而国内所能提供原油量仅为1.3亿吨,为了满足原油的需求量,则需要每年从国外二十多个国家和地区进口约6940万吨原油。
为了更好的提高石油资源的利用率,增加企业的经济效益,对从国外进口的原油炼制构成进行开发研究也是十分必要的。
为课题的研究提供了国情依据。
原油精馏装置是炼油企业的“龙头”,是炼油工业的第一道工序,为二次加工装置提供原料,是原油加工的基础,其能量的综合利用程度和拔出率高低体现在石化企业的效益上,因此,开展常压精馏装置的研究很有意义[1--3]。
原油常减压蒸馏作为原油的一次加工工艺,在原油加工总流程中占有重要作用,近年来常减压蒸馏技术和管理经验不断创新,装置节能消耗显著,产品质量提高。
但与国外先进水平相比,仍存在较大的差距,装置能耗仍然偏高,分馏精度和减压拔出深度偏低,对含硫原油的适应性差等。
进一步提高常减压装置的操作水平和运行水平,显著日益重要,对提高炼油企业的经济效益也具有重要意义。
500万吨年炼油减压蒸馏装置设计书

500万吨/年炼油减压蒸馏装置设计书第一章文献综述1.1石油工业简介石油又称原油,是从地下深处开采的棕黑色可燃粘稠液体。
由碳和氢化合形成的烃类构成石油的主要组成部分,约占95%~99%,含硫、氧、氮的化合物对石油产品有害,在石油加工中应尽量除去。
不同产地的石油中,各种烃类的结构和所占比例相差很大,但主要属于烷烃、环烷烃、芳香烃三类。
通常以烷烃为主的石油称为石蜡基石油;以环烷烃、芳香烃为主的称环烃基石油;介于二者之间的称中间基石油。
我国主要原油的特点是含蜡较多,凝固点高,硫含量低,镍、氮含量中等,钒含量极少。
除个别油田外,原油中汽油馏分较少,渣油占1/3。
组成不同类的石油,加工方法有差别,产品的性能也不同,应当物尽其用。
石油炼制工业是国民经济最重要的支柱产业之一,是提供能源,尤其是交通运输燃料和有机化工原料的最重要的工业。
据统计,全世界总能源需求的40%依赖于石油产品,汽车,飞机,轮船等交通运输器械使用的燃料几乎全部是石油产品,有机化工原料主要也是来源于石油炼制工业,世界石油总产量的10%用于生产有机化工原料。
石油是十分复杂的烃类非烃类化合物的混合物。
石油产品种类繁多,市场上各种牌号的石油产品达1000种以上,大体上可分为以下几类:⑴燃料:如各种牌号的汽油、航空煤油、柴油、重质燃料油等;⑵润滑油:如各种牌号的燃机油、机械油等;⑶有机化工原料:如生产乙烯的裂解原料、各种芳烃和烯烃等;⑷工艺用油:如变压器油、电缆油、液压油等;⑸沥青:如各种牌号的铺路沥青、建筑沥青、防腐沥青、特殊用途沥青等;⑹蜡:如各种食用、药用化妆品用,包装用的石蜡和地蜡;⑺石油焦炭:如电极用焦、冶炼用焦、燃料焦等。
从上述石油产品品种之多和用途之广也可以看到石油炼制工业在国民经济和国防中的重要地位。
石油作为一种能流密度高,便于储存、运输、使用的清洁能源已广泛应用于国民经济的方方面面。
按2001年中国各行业石油消费构成看,交通运输业占30%以上,是消费石油最多的行业。
常减压蒸馏装置过程模拟与生产计划优化系统的集成的开题报告
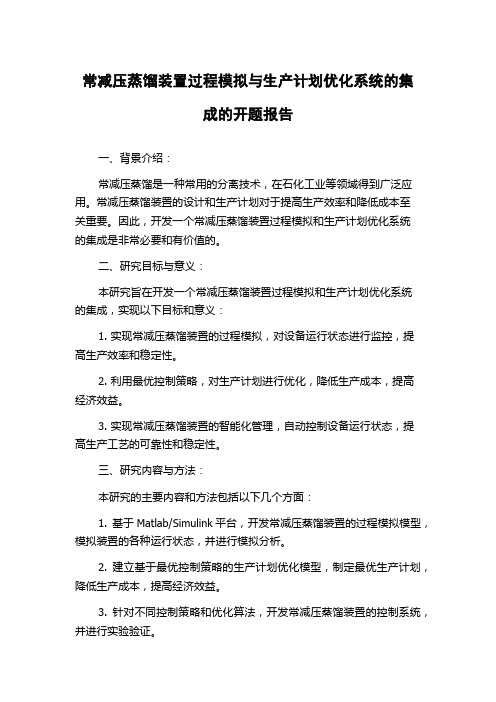
常减压蒸馏装置过程模拟与生产计划优化系统的集成的开题报告一、背景介绍:常减压蒸馏是一种常用的分离技术,在石化工业等领域得到广泛应用。
常减压蒸馏装置的设计和生产计划对于提高生产效率和降低成本至关重要。
因此,开发一个常减压蒸馏装置过程模拟和生产计划优化系统的集成是非常必要和有价值的。
二、研究目标与意义:本研究旨在开发一个常减压蒸馏装置过程模拟和生产计划优化系统的集成,实现以下目标和意义:1. 实现常减压蒸馏装置的过程模拟,对设备运行状态进行监控,提高生产效率和稳定性。
2. 利用最优控制策略,对生产计划进行优化,降低生产成本,提高经济效益。
3. 实现常减压蒸馏装置的智能化管理,自动控制设备运行状态,提高生产工艺的可靠性和稳定性。
三、研究内容与方法:本研究的主要内容和方法包括以下几个方面:1. 基于Matlab/Simulink平台,开发常减压蒸馏装置的过程模拟模型,模拟装置的各种运行状态,并进行模拟分析。
2. 建立基于最优控制策略的生产计划优化模型,制定最优生产计划,降低生产成本,提高经济效益。
3. 针对不同控制策略和优化算法,开发常减压蒸馏装置的控制系统,并进行实验验证。
4. 开发常减压蒸馏装置的智能化管理系统,实现自动控制装置的运行状态,提高生产工艺的可靠性和稳定性。
四、预期研究成果:本研究预计实现以下研究成果:1. 建立常减压蒸馏装置的过程模拟模型,对装置的各种运行状态进行分析和优化。
2. 建立基于最优控制策略的生产计划优化模型,制定最优生产计划,降低生产成本,提高经济效益。
3. 开发常减压蒸馏装置的控制系统,并进行实验验证。
4. 开发常减压蒸馏装置的智能化管理系统,实现自动控制装置的运行状态,提高生产工艺的可靠性和稳定性。
五、研究进度及计划:本研究的进度计划如下:1. 第一阶段:文献综述和方案制定。
预计完成时间:1个月。
2. 第二阶段:常减压蒸馏装置的过程模拟和实验验证。
预计完成时间:2个月。
石油化工生产技术专业毕业设计开题报告_毕业设计_
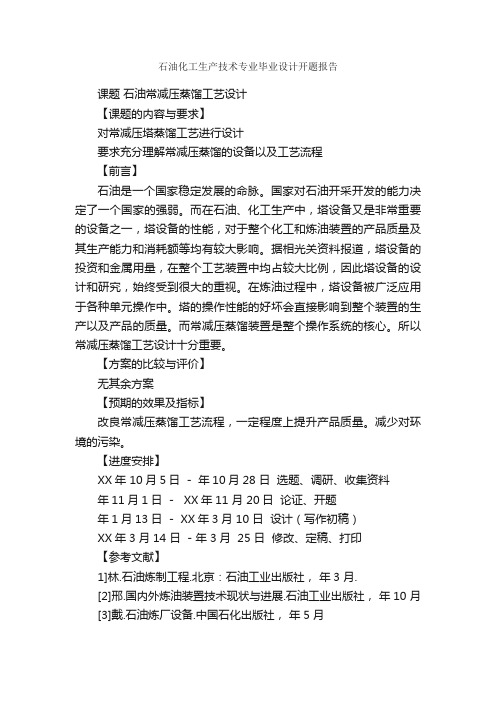
石油化工生产技术专业毕业设计开题报告课题石油常减压蒸馏工艺设计【课题的内容与要求】对常减压塔蒸馏工艺进行设计要求充分理解常减压蒸馏的设备以及工艺流程【前言】石油是一个国家稳定发展的命脉。
国家对石油开采开发的能力决定了一个国家的强弱。
而在石油、化工生产中,塔设备又是非常重要的设备之一,塔设备的性能,对于整个化工和炼油装置的产品质量及其生产能力和消耗额等均有较大影响。
据相光关资料报道,塔设备的投资和金属用量,在整个工艺装置中均占较大比例,因此塔设备的设计和研究,始终受到很大的重视。
在炼油过程中,塔设备被广泛应用于各种单元操作中。
塔的操作性能的好坏会直接影响到整个装置的生产以及产品的质量。
而常减压蒸馏装置是整个操作系统的核心。
所以常减压蒸馏工艺设计十分重要。
【方案的比较与评价】无其余方案【预期的效果及指标】改良常减压蒸馏工艺流程,一定程度上提升产品质量。
减少对环境的污染。
【进度安排】XX年 10月5日 - 年10月28 日选题、调研、收集资料年11月1日 - XX年11 月 20日论证、开题年1月13日 - XX年3月 10 日设计(写作初稿)XX年3 月14 日 - 年 3月 25 日修改、定稿、打印【参考文献】1]林.石油炼制工程.北京:石油工业出版社,年3 月.[2]邢.国内外炼油装置技术现状与进展.石油工业出版社,年10 月[3]戴.石油炼厂设备.中国石化出版社,年5 月【指导教师意见】(有针对性地说明选题意义及工作安排是否恰当等)□同意提交开题论证□修改后提交□不同意提交(请说明理由)指导教师签章:年月日【系部意见】□同意指导教师意见□不同意指导教师意见(请说明理由)□其它(请说明)系(部)主任签章:年月日。
450万吨年原油常减压蒸馏装置工艺设计

1 课题的目的与意义原油是极其复杂的混合物,通过原油的蒸馏可以按所制定的产品方案将其分割成直馏汽油、煤油、轻柴油或重柴油馏分及各种润滑油馏分和渣油等[1]。
原油蒸馏是石油加工中第一道不可少的工序,故通常称原油蒸馏为一次加工,其他加工工序则称为二次加工[2]。
原油的一次加工能力即原油蒸馏装置的处理能力,常被视为一个国家炼油工业发展水平的标志。
截至2008年年底,我国原油加工能力为4.2亿t/a,占世界炼油总能力42.8亿t的10%;我国原油加工量3.42亿t,占世界炼油加工量的7%,居世界第二位(仅次于美国);我国炼厂总数(大中型)为53座,占世界总数655座的8%,其中,镇海炼厂位居世界排名第十七位[3]。
原油常压蒸馏在炼化企业加工过程中占有很重要的地位,其加工的好坏直接关系到后续产品质量和经济效益。
因此,原油常压蒸馏被称为石油加工的“龙头”。
基于以上原因,几乎在所有的炼油厂中,原油的第一个加工装置就是常压蒸馏装置。
尽管近年来常减压蒸馏技术和管理经验不断创新,装置节能降耗和产品质量得到了显著的提高,但与国外先进水平相比,仍存在较大的差距,如装置耗能较大,分馏和减压拔出深度偏低,对含硫原油的适应性较差等。
进一步的提高常减压装置的操作水平和运行水平显得日益重要,对提高炼油企业的经济效益也具有非常重要的意义。
本设计主要是依据国家成品油有关标准和市场供需情况,确定原油加工方案,进行原油常压蒸馏的工艺设计。
它的意义在于,通过常压蒸馏对原油的处理,可以按所指定的产品方案将原油分割得到汽油、煤油、轻柴油、重柴油馏分以重油馏分等。
可以减少渣油量,提高原油总拔出率。
不仅能获得更多的轻质油品,也可为二次加工、三次加工提供更多的原料油。
2 国内外研究现状原油蒸馏作为一次加工在石油加工中占有重要地位。
通常炼厂是依次使用常压和减压的方法,将原油按照沸程切割成不同的馏分。
人们将既采用了常压蒸馏又采用了减压蒸馏的原油蒸馏装置通常称为常减压蒸馏[4]。
万吨年常减压蒸馏装置工艺设计

万吨年常减压蒸馏装置工艺设计一、引言常减压蒸馏是一种重要的分离工艺,广泛应用于石油化工行业。
本文基于万吨年常减压蒸馏装置的设计要求,对工艺进行详细设计,旨在满足设备的高效运行和产品质量的要求。
二、装置工艺流程常减压蒸馏装置的主要工艺流程包括进料、预热、加热、分馏、冷却和产品收集等步骤。
2.1 进料进料是装置的起始步骤,原料从储罐经过输送管道进入装置。
进料过程需要考虑流量和温度的控制,以确保装置的正常运行。
2.2 预热进料经过加热器进行预热,提高进料的温度至蒸发温度。
预热过程需要控制加热温度和时间,以确保进料在进入分离塔前达到合适的温度。
2.3 加热预热后的进料进入分离塔,在分离塔内进行加热。
加热过程中需要控制加热温度和压力,使得进料能够充分蒸发并分离成不同的组分。
2.4 分馏在分馏塔中进行分离,通过不同组分的沸点差异,实现轻质组分和重质组分的分离。
分馏过程中需要控制塔底的温度和塔顶的压力,以确保合理的分离效果。
2.5 冷却分馏后的产品经过冷却器进行冷却,降低温度至合适的收集温度。
冷却过程中需要控制冷却温度和冷却时间,避免产品的过热或过冷。
2.6 产品收集冷却后的产品通过收集器进行收集,分离出所需的产物。
产品收集过程需要注意收集器的遮挡和密封,以防止产品的污染或泄露。
三、工艺参数设计为了保证装置的高效运行和产品质量的要求,需要对装置的工艺参数进行设计。
3.1 进料流量根据设备的设计要求和生产需求,确定进料的流量范围。
进料流量的选择需要考虑装置的生产能力和运行稳定性。
3.2 加热温度和压力根据进料组分的性质和分离要求,确定加热的温度和压力范围。
加热温度和压力的选择需要兼顾分离效果和能耗的平衡。
3.3 分馏塔底温度和塔顶压力根据产品要求和分离塔的结构特点,确定分馏塔底温度和塔顶压力的要求。
分馏塔底温度和塔顶压力的选择需要满足产品质量和工艺要求。
3.4 冷却温度和冷却时间根据产品的蒸发温度和收集温度,确定冷却的温度和时间范围。
蒸馏开题报告工艺

山东轻工业学院毕业设计(论文)开题报告1)粗馏塔温度控制调节阀的计算选型阀前绝对压力:P1=0.301MPa阀后绝对压力:P2=0.151MPa蒸汽流量:Gs=3440kgf/h2)粗馏塔液位控制调节阀的计算选型阀前绝对压力:P1=0.151MPa阀后绝对压力:P2=0.101MPa酒槽重度:ϒ=1.07kg/m3Q max=27m3/h Q min=1/3 Q max=9m3/h 3)蒸汽包压力控制调节阀的计算选型阀前绝对压力:P1=12.01*100KPa阀后绝对压力:P2=3.01*100KPa 蒸汽流量:Gs=9000kgf/h4)精馏塔顶温度控制调节阀的计算选型阀前绝对压力:P1=0.301MPa阀后绝对压力:P2=0.151MPa蒸汽流量:Gs=3440kgf/h5)酒精采出点温度控制调节阀的计算选型阀前绝对压力:P1=0.151MPa阀后绝对压力:P2=0.101MPa酒槽重度:ϒ=790kg/m3Q max=1.758m3/h Q min=1/3 Q max=0.586m3/h 92C︒时酒精饱和蒸汽压:Pv=1.0*100KPa6)精馏塔液位控制调节阀的计算选型阀前绝对压力:P1=0.151MPa阀后绝对压力:P2=0.101MPaϒ=1000kg/m3Q max=6.7m3/h7)回流罐内液位控制调节阀的计算选型阀前绝对压力:P1=0.151MPa阀后绝对压力:P2=0.101MPaϒ=790kg/m3Q max=7m3/h19C︒时,酒精饱和蒸汽Pv=0.053*100kPa8)第一、三号冷凝器温度控制调节阀的计算选型阀前绝对压力:P1=0.281MPa阀后绝对压力:P2=0.151MPaϒ=1000kg/m3Q max=15m3/h50C︒时水压Pv=0.123*100KPa 30C︒时水压Pv=0.123*100KPa工艺控制指标:粗塔顶温度要达到98℃粗塔液位稳定在0.8m左右蒸汽包压力控制在0.2MPa精塔顶温控制在79℃酒精采出点温度为92℃精馏塔内液位维持在0.8m,回流罐液位稳定在1.2 m1#冷凝器要求酒精蒸汽降温至50o C,3#冷凝器要求酒精蒸汽降温至30o C,。
减压蒸馏—微电解预处理HNS生产废水的开题报告
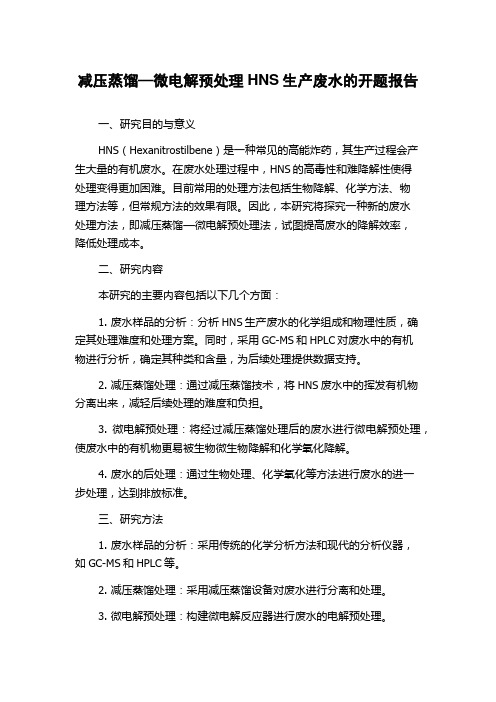
减压蒸馏—微电解预处理HNS生产废水的开题报告一、研究目的与意义HNS(Hexanitrostilbene)是一种常见的高能炸药,其生产过程会产生大量的有机废水。
在废水处理过程中,HNS的高毒性和难降解性使得处理变得更加困难。
目前常用的处理方法包括生物降解、化学方法、物理方法等,但常规方法的效果有限。
因此,本研究将探究一种新的废水处理方法,即减压蒸馏—微电解预处理法,试图提高废水的降解效率,降低处理成本。
二、研究内容本研究的主要内容包括以下几个方面:1. 废水样品的分析:分析HNS生产废水的化学组成和物理性质,确定其处理难度和处理方案。
同时,采用GC-MS和HPLC对废水中的有机物进行分析,确定其种类和含量,为后续处理提供数据支持。
2. 减压蒸馏处理:通过减压蒸馏技术,将HNS废水中的挥发有机物分离出来,减轻后续处理的难度和负担。
3. 微电解预处理:将经过减压蒸馏处理后的废水进行微电解预处理,使废水中的有机物更易被生物微生物降解和化学氧化降解。
4. 废水的后处理:通过生物处理、化学氧化等方法进行废水的进一步处理,达到排放标准。
三、研究方法1. 废水样品的分析:采用传统的化学分析方法和现代的分析仪器,如GC-MS和HPLC等。
2. 减压蒸馏处理:采用减压蒸馏设备对废水进行分离和处理。
3. 微电解预处理:构建微电解反应器进行废水的电解预处理。
4. 废水的后处理:采用生物处理和化学氧化等方法对废水进行进一步处理。
四、研究预期成果通过本研究,预计可以得到以下成果:1. 确定HNS生产废水的物理性质和化学成分。
2. 探究减压蒸馏—微电解预处理技术对HNS生产废水的降解效果,提高降解效率和废水处理效果。
3. 确定废水处理的最优方案,比较各种处理方法的优劣,从而为企业提供更加可行和经济的处理方法。
五、研究难点与解决途径1. HNS生产废水中含有大量的高毒性有机物,如何有效地实现其去除和降解是本研究的难点之一。
减压蒸馏装置安全运行风险评估与故障诊断系统的研究的开题报告
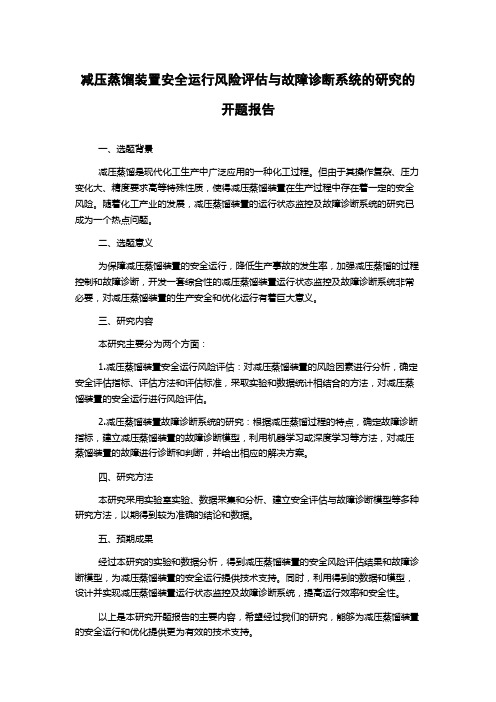
减压蒸馏装置安全运行风险评估与故障诊断系统的研究的
开题报告
一、选题背景
减压蒸馏是现代化工生产中广泛应用的一种化工过程。
但由于其操作复杂、压力变化大、精度要求高等特殊性质,使得减压蒸馏装置在生产过程中存在着一定的安全风险。
随着化工产业的发展,减压蒸馏装置的运行状态监控及故障诊断系统的研究已成为一个热点问题。
二、选题意义
为保障减压蒸馏装置的安全运行,降低生产事故的发生率,加强减压蒸馏的过程控制和故障诊断,开发一套综合性的减压蒸馏装置运行状态监控及故障诊断系统非常必要,对减压蒸馏装置的生产安全和优化运行有着巨大意义。
三、研究内容
本研究主要分为两个方面:
1.减压蒸馏装置安全运行风险评估:对减压蒸馏装置的风险因素进行分析,确定安全评估指标、评估方法和评估标准,采取实验和数据统计相结合的方法,对减压蒸馏装置的安全运行进行风险评估。
2.减压蒸馏装置故障诊断系统的研究:根据减压蒸馏过程的特点,确定故障诊断指标,建立减压蒸馏装置的故障诊断模型,利用机器学习或深度学习等方法,对减压蒸馏装置的故障进行诊断和判断,并给出相应的解决方案。
四、研究方法
本研究采用实验室实验、数据采集和分析、建立安全评估与故障诊断模型等多种研究方法,以期得到较为准确的结论和数据。
五、预期成果
经过本研究的实验和数据分析,得到减压蒸馏装置的安全风险评估结果和故障诊断模型,为减压蒸馏装置的安全运行提供技术支持。
同时,利用得到的数据和模型,设计并实现减压蒸馏装置运行状态监控及故障诊断系统,提高运行效率和安全性。
以上是本研究开题报告的主要内容,希望经过我们的研究,能够为减压蒸馏装置的安全运行和优化提供更为有效的技术支持。
常压蒸馏流程模拟与优化及换热网络综合的开题报告
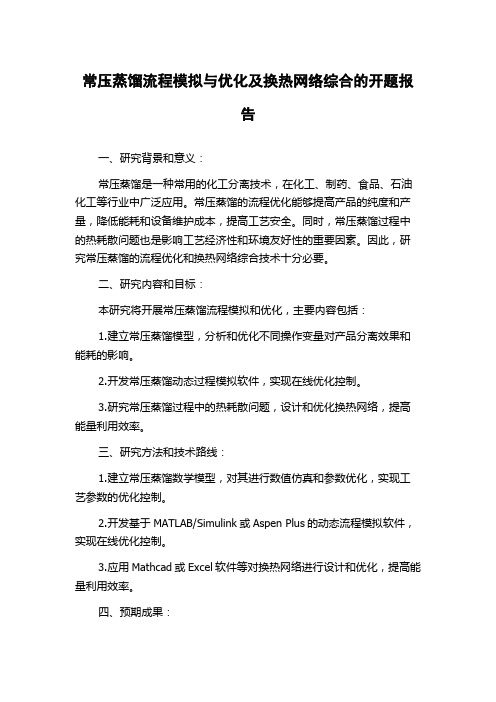
常压蒸馏流程模拟与优化及换热网络综合的开题报
告
一、研究背景和意义:
常压蒸馏是一种常用的化工分离技术,在化工、制药、食品、石油化工等行业中广泛应用。
常压蒸馏的流程优化能够提高产品的纯度和产量,降低能耗和设备维护成本,提高工艺安全。
同时,常压蒸馏过程中的热耗散问题也是影响工艺经济性和环境友好性的重要因素。
因此,研究常压蒸馏的流程优化和换热网络综合技术十分必要。
二、研究内容和目标:
本研究将开展常压蒸馏流程模拟和优化,主要内容包括:
1.建立常压蒸馏模型,分析和优化不同操作变量对产品分离效果和能耗的影响。
2.开发常压蒸馏动态过程模拟软件,实现在线优化控制。
3.研究常压蒸馏过程中的热耗散问题,设计和优化换热网络,提高能量利用效率。
三、研究方法和技术路线:
1.建立常压蒸馏数学模型,对其进行数值仿真和参数优化,实现工艺参数的优化控制。
2.开发基于MATLAB/Simulink或Aspen Plus的动态流程模拟软件,实现在线优化控制。
3.应用Mathcad或Excel软件等对换热网络进行设计和优化,提高能量利用效率。
四、预期成果:
1.建立常压蒸馏流程模型和换热网络模型,实现流程优化和能耗降低。
2.开发常压蒸馏动态过程模拟软件,实现在线优化控制。
3.撰写并发表1-2篇相关研究论文。
总之,本研究将为常压蒸馏行业的技术进步和性能优化提供一定的指导和支持。
常减压蒸馏装置改造设计的开题报告

常减压蒸馏装置改造设计的开题报告一、选题背景及意义常减压蒸馏是一种适用于石油化工、精细化工、医药等行业的蒸馏技术,具有节能、加工效率高、产品品质优良等特点。
然而,传统的常减压蒸馏装置存在很多问题,如能效低、设备体积大、占地面积大、操作复杂等。
因此,对常减压蒸馏装置进行改造设计,提高其性能和效率,对于推进相关行业的发展具有重要的意义和价值。
二、研究内容和目标本次常减压蒸馏装置改造设计的研究内容主要包括以下方面:1. 设计一种能够有效提高装置能效的供料系统和回流系统。
2. 设计一种合理的控制系统,能够实现装置的自动化运行和监控。
3. 设计一种较小体积的常减压蒸馏装置,以降低设备成本和占地面积。
4. 通过实验测试,验证装置改造后的性能和效率是否得到提升。
本次研究的目标是通过装置的改造和优化设计,提高其能效和效率,降低设备成本和占地面积,实现常减压蒸馏装置的自动化控制和运行。
三、研究方法和技术路线本次研究将采取多种方法和技术手段进行,包括理论分析、数值模拟、实验研究、数据分析等。
具体技术路线如下:1. 分析传统常减压蒸馏装置的运行特点和存在的问题,确定改造设计的目标和方案。
2. 采用数值模拟技术,对装置的供料系统、回流系统以及分离塔进行优化设计。
3. 设计一种合理的自动控制系统,实现装置的自动化控制和监控。
4. 进行实验验证装置改造后的性能和效率是否有所提升,通过数据分析和对比来验证改造效果。
四、预期成果通过本次常减压蒸馏装置改造设计,预期可以获得以下成果:1. 设计出一种能够有效提高装置能效和效率的常减压蒸馏装置。
2. 开发出一种操作方便、自动化程度较高的控制系统。
3. 实现装置较小体积化,降低设备成本和占地面积。
4. 提高装置的分馏效率和产品品质,使其在相关领域得到广泛应用。
五、进度计划1. 研究背景和文献调研:1个月。
2. 设计装置改造的方案:2个月。
3. 进行数值模拟和实验研究:4个月。
4. 改造装置并实现自动化控制:3个月。
200万吨原油减压蒸馏装置的初步设计_本科毕业论文

200万吨原油减压蒸馏装置的初步设计_本科毕业论文摘要减压塔根据生产任务的不同可以分为润滑油型和燃料油型两种。
本次设计参考川中原油的基本性质,川中原油属于低硫石蜡基原油,其特点是高含蜡,高凝点,沥青质含量不高,胶质高,直馏汽油辛烷值低,柴油十六烷值高,是制润滑油的好原料。
根据市场对产品的需求、经济效益等方面的因素,川中原油的加工采用了润滑油型加工方案。
本次设计根据任务书的要求,参照川中原油的常减压蒸馏的部分操作数据,设计完成一座年处理量为200万吨的减压蒸馏装置,设计的主要内容包括:工艺设计;塔体设计;接管、抽真空系统及加热炉负荷的计算。
关键词:原油;减压塔;抽真空系统;加热炉负荷ABSTRACTAccording to different production tasks, vacuum tower can be divided into two kinds of type: Lubricant type and Fuel type. The design references the basic nature of Chuanzhong crude oil. It belongs to sweet paraffinic crude oil, which is characterized by high wax, high pour point, lower asphaltene content, high resin content, low octane of straight-run gasoline, high diesel cetane number, is good raw materials for Lubricating oil. According to market demand for products, economic and other factors, the processing of Chuanzhong crude oil adopt Lubricant type processing program.The design according to the requirements of the mission statement, reference to similar atmospheric and vacuum distillation of crude oil part of the operating data, design an annual handling capacity of 200 thousand tons of vacuum distillation unit, main contents of design include: process design; tower design; calculation of connector pipe; calculation of vacuum system; furnace loadKey words: crude oil; vacuum tower calculations; vacuum systems; heating load.目录1 绪论 (1)1.1设计背景 (1)1.2技术应用与发展现状 (1)1.3 装置设备的考虑因素 (2)1.4 润滑油型减压塔的工艺特征 (3)2 减压塔的工艺计算 (4)2.1设计数据 (4)2.2 减压塔工艺计算 (5)2.2.1 汽提蒸汽用量 (6)2.2.2 塔板形式和塔板数 (6)2.3 全塔气液负荷的计算 (7)2.3.1 全塔热量平衡计算 (7)2.3.2减压五线塔板上的气液负荷 (9)2.3.3减压四线塔板上的气液负荷 (10)2.3.4减压三线塔板上的气液负荷 (11)2.3.5 减压二线塔板上的气液负荷 (13)2.3.6减压一线塔板上的气液负荷 (14)2.3.7二中抽出板上的气液负荷 (16)2.3.8二中回流板上的气液负荷 (17)2.3.9一中抽出板上的气液负荷 (19)2.3.10一中回流板上的气液荷 (20)2.4 中段循环回流量 (22)2.5全塔气液负荷性能图 (22)2.6 结构计算的相关参数 (22)2.7 塔径计算 (23)2.8 溢流装置的确定 (24)2.9 塔板形式、浮阀数目及排列 (24)2.10 流体力学验算 (26)2.11 塔板负荷性能图 (29)2.12 减压塔上下两段缩径的确定 (31)2.13 塔体设计 (32)2.14 接管计算 (32)3 抽真空系统 (36)3.1 蒸汽喷射器的工作原理 (36)3.2 蒸汽喷射器结构参数的确定 (36)3.2.1级数的确定 (36)3.2.2各级压缩比的确定 (37)3.2.4漏入空气量G2 (37)3.2.5油气量G3 (38)3.2.6带入水汽量G4 (38)3.2.7工作蒸汽用量G S (38)3.3 喷射泵的结构尺寸计算 (39)4 加热炉负荷计算 (42)4.1 进加热炉的热量Q1 (42)4.2 出加热炉的热量Q2 (42)4.3 加热炉负荷Q (42)5设计结果总结 (43)致谢 (45)参考文献 (46)1 绪论1.1设计背景石油又称原油,是从地下深处开采的棕黑色可燃粘稠液体。
过程模拟技术在蒸馏装置上的应用的开题报告

过程模拟技术在蒸馏装置上的应用的开题报告一、研究背景及意义蒸馏装置是化工生产中常见的一种设备,广泛应用于石油、化工、医药等领域中。
蒸馏过程是将混合物中不同的组分按照沸点差异进行分离的过程,具有重要的经济效益和社会价值。
但是,蒸馏过程具有复杂性和不确定性,其过程参数的变化和优化对产品质量和能源消耗有着重要的影响。
因此,如何提高蒸馏装置的操作效率和降低能源消耗,成为化工行业亟待解决的问题。
随着计算机技术和数值模拟技术的不断发展,过程模拟技术成为化工生产优化和过程控制的重要手段。
通过数值模拟和优化,可预测和控制化工生产中的复杂过程,提高生产效率和产品质量,降低能源消耗和生产成本。
因此,研究过程模拟技术在蒸馏装置上的应用,对提高化工生产效率和降低能源消耗有着重要的意义。
二、研究内容和方法本研究的主要内容是通过过程模拟技术,建立蒸馏装置的数学模型,研究蒸馏过程中的温度、压力、流量等过程参数随时间的变化规律,以及各组分的分离效率和产品质量的影响因素。
具体研究内容包括:1.建立蒸馏装置的数学模型通过分析和建立蒸馏装置的物料平衡和能量平衡等基本方程,建立蒸馏装置的数学模型。
通过本研究的数学模型,可以计算蒸馏过程中各组分的浓度、温度、压力等参数随时间的变化规律。
2.模拟蒸馏过程中各组分的分离效率通过模拟蒸馏过程中各组分的分离效率,分析和评价蒸馏装置的分离效果。
通过改变操作参数,如加热温度、回流比等,探究其对分离效果的影响。
3.优化蒸馏过程中的操作参数通过优化蒸馏过程中的操作参数,如回流比、加热温度等,探究其对产品质量和能源消耗的影响。
通过模拟和优化,可实现蒸馏装置的生产优化,提高其经济效益和社会价值。
本研究采用过程模拟技术,建立数学模型,并利用数值模拟软件进行模拟和优化,最终得到蒸馏装置的优化操作策略。
三、研究进度安排初步安排研究进度如下:第一年1.调研和综述相关研究文献2.建立蒸馏装置的数学模型3.利用数值模拟软件进行模拟分析第二年1.改进和优化数学模型2.进行蒸馏过程中的操作参数优化3.分析和评价优化效果第三年1.撰写毕业论文并进行答辩2.完成论文修改和提交四、预期成果和意义本研究的预期成果包括:1.建立蒸馏装置的数学模型,实现蒸馏过程的定量分析和优化控制;2.对蒸馏过程中的流程参数、操作策略、组分分离等关键问题进行探究,提高生产效率和产品质量;3.为化工行业中蒸馏过程的生产优化和能源节约提供技术支持和参考。
- 1、下载文档前请自行甄别文档内容的完整性,平台不提供额外的编辑、内容补充、找答案等附加服务。
- 2、"仅部分预览"的文档,不可在线预览部分如存在完整性等问题,可反馈申请退款(可完整预览的文档不适用该条件!)。
- 3、如文档侵犯您的权益,请联系客服反馈,我们会尽快为您处理(人工客服工作时间:9:00-18:30)。
本科毕业论文开题报告
题目900万吨/年原油减压蒸馏装置
初步设计
学生姓名蒋川学号0904040429 教学院系化学化工学院
专业年级2009级化学工程与工艺
指导教师段蜀波职称讲师
单位西南石油大学化学化工学院
辅导教师邹长军职称教授
单位西南石油大学
完成日期2012 年 3 月18 日
900万吨/年原油减压蒸馏装置初步设计(开题报告)
1选题目的、意义
随着社会的发展,我国经济的发展越来越依赖化石燃料的供应。
而这些燃料中,石油被誉为“工业的血液”,其对我国经济发展的重要性是不言而喻的。
石油是一种及其复杂的混合物。
要从原油中提炼出多种多样的燃料、润滑油和其他产品,基本途径就是:将原油分割为不同沸程的馏分,然后按照油品的使用要求,除去这些馏分中的非理想组分,或者是经由化学转化形成所需要的组成,进而获得合格的石油产品。
在这个过程中蒸馏就是一种合适的手段,而且也是最经济、最容易实现的手段。
因此,蒸馏装置是炼油厂中一个很重要的装置。
原油蒸馏是石油加工中第一道不可少的工序,故通常称原油蒸馏为一次加工,其他加工工序则称为二次加工[2]。
原油的一次加工能力即原油蒸馏装置的处理能力,常被视为一个国家炼油工业发展水平的标志。
原油常减压蒸馏在炼化企业加工过程中占有很重要的地位,其加工的好坏直接关系到后续产品质量和经济效益。
因此,原油常减压蒸馏被称为石油加工的“龙头”。
基于以上原因,几乎在所有的炼油厂中,原油的第一个加工装置就是常减压蒸馏装置。
尽管近年来常减压蒸馏技术和管理经验不断创新,装置节能降耗和产品质量得到了显著的提高,但与国外先进水平相比,仍存在较大的差距,如装置耗能较大,分馏和减压拔出深度偏低,对含硫原油的适应性较差等。
进一步的提高常减压装置的操作水平和运行水平显得日益重要,对提高炼油企业的经济效益也具有非常重要的意义。
本设计主要是依据《大庆原油评价报告》确定原油加工方案,进行原油常减压蒸馏的工艺设计。
它的意义在于,通过常减压蒸馏对原油的处理,可以按所指定的产品方案将原油分割得到汽油、煤油、轻柴油、重柴油馏分以重油馏分等。
可以减少渣油量,提高原油总拔出率。
不仅能获得更多的轻质油品,也可为二次加工、三次加工提供更多的原料油。
2国内外研究现状
2.1国内现状
国内常减压蒸馏技术近年来有很大发展,在改进加工流程,提高设备效率,降低能耗,提高产品质量方面做了大量的开发性工作,常减压蒸馏装置的平均
能耗已达到世界先进水平,近年来国内主要工艺进展表现在以下几个方面:
(1)采用原油预闪蒸技术或设置初馏塔
采用原油预闪蒸技术或设置初馏塔,以适应不同原油及不同炼厂的要求并可以降低能耗。
(2)多产柴油技术
多产柴油技术主要包括强化减压塔底汽提技术。
强化减压塔底汽提主要包括合理确定汽提塔段的塔板数、汽提蒸汽量、汽提段结构等参数,使汽提段的效果最佳,减压侧线产品质量提高,柴油收率增加。
(3)电脱盐技术
吸收引进电脱盐成套技术,提高了脱盐脱水效果,同时降低了电耗。
对于低速电脱盐技术,国内通过吸收引进的技术已完全掌握,并开发出了高效交、直流电脱盐成套技术,已在国内普遍应用。
目前国内电脱盐技术应用比较多的交直流低速电脱盐,电脱盐罐尺寸大、占地大。
对于大处理量减压装置来说,交、直流低速电脱盐由于占地过大是不合适使用的。
(4)塔内件
国内有许多塔内件供应商,不断推出塔盘新技术,已逐步取代传统的浮阀塔盘,减压塔采用高通量、高弹性塔盘作为内件。
几种比较有代表性的塔盘有清华大学开发的ADV微分浮阀塔盘、华东理工大学开发的导向浮阀塔盘、石油大学开发的Super系列浮阀塔盘等。
我国减压蒸馏装置发展趋势是逐渐呈现规模大型化,原油加工品种多样化,生产操作智能化等趋势,技术水平有了较大的提高。
但与国际先进水平相比,我国减压蒸馏装置仍然存在较大的差距,主要是装置规模小,运行负荷低,运行周期短,关键工艺技术落后,能耗依然偏高等。
2.2国外现状
减压蒸馏装置是一个工艺成熟的装置,技术进步大多是在工艺加工流程、设备结构及优化操作等方面,在满足生产方案、产品质量的前提下获得较高拔出率及较低的能耗,主要的技术进展有以下几个方面:
(1)设备革新
近十年来,各种汽液传质内件的开发与应用有了快速的发展,各种高效散装填料、规整填料及相应的汽、液分布系统和各种高通量、高弹性的塔板相继问世并且很快得到了广泛应用。
近年来减压蒸馏装置的主要技术进步在于塔器内部构件的开发,塔内件供应商相继推出了一系列新型填料和新型塔板。
(2)窄点技术的应用
自七十年代英国学者B.Linnhoff等人提出窄点技术以来,这一技术被迅速应用于炼油厂及石油化工厂的能量回收系统,特别是应用于减压蒸馏装置的换热网络优化设计,取得了很大的成效。
(3)电脱盐技术
电脱盐是原油蒸馏装置的重要设施,可减轻装置设备的腐蚀、节能并同时降低下游装置原料中金属离子等有害物料的含量。
八十年代以前,主要是低速脱盐技术。
九十年代,Petrolite公司在低速脱盐的基础上开发出了高速电脱盐,其主要特点是:
-进料位置与低速电脱盐不同;
-进料管不用管式或倒槽式而采用特殊喷头型式;
-电脱盐罐处理能力取决于喷头的能力;
-采用交流电,水平电极板。
该技术与低速电脱盐相比具有脱盐效率高、处理能力大、电耗低、占地面积小等优点。
据有关资料介绍,高速电脱盐的处理能力是低速电脱盐的1.75倍至2.0倍。
目前世界上已有100多套电脱盐装置采用了该技术,近几年,国内镇海炼化、上海石化、大连西太平洋和齐鲁石化等常减压装置的电脱盐均采用了引进的Petrolite公司高速电脱盐技术。
国外炼油厂蒸馏装置的大型化提高了劳动生产率和经济效益,降低了能耗和物耗。
3毕业设计(论文)的主要内容
(1)依据《大庆原油评价报告》、国家成品油有关标准和市场供需情况,确定原油加工方案。
(2) 根据原油加工方案制定减压蒸馏装置的生产工艺流程;
(3) 根据基础数据完成减压蒸馏装置的设计计算。
确定出包括塔顶温度、汽化段温度、汽化段压力等工艺参数;确定主体设备(减压塔)的主要工艺尺寸:
塔高、塔径、塔板数等,并对数据进行汇总。
(4) 用A2图纸绘制减压蒸馏装置工艺流程图;
4所采用的方法、手段及步骤等
(1) 认真阅读《石油炼制工程》教材,为设计工作做好准备;
(2) 分析处理《大庆原油评价报告》相关数据,绘制图表,为后续设计
计算做好必要准备;
(3) 通过文献检索,查阅相关中外文献并进行必要的整理,做好笔记;
(4)通过网络搜索获取最新的基础资料,如国家成品油有关标准和市场供需情况;
(5)查阅各种相关图表集、手册、经验数据及同类型装置的生产数据等,进行初馏塔、常压塔的工艺设计;塔板结构设计及水力学验算;
5设计(论文)的进程安排
3月11日~3月15日:在图书馆获取并查阅本课题的参考文献;
3月16日~3月20日:撰写开题报告;
3月21日~3月23日:准备开题报告答辩;
3月24日~4月15日:完成原油常压蒸馏装置设计的步骤及内容;
4月16日~5月15日:进行原油常压蒸馏装置的设计计算;
5月16日~5月27日:完成原油常压蒸馏工艺流程图;
5月28日~6月10日:论文写作;
6月11日~6月24日:答辩准备;
参考文献
[1].林世雄.石油炼制工程.北京:石油工业出版社,2000
[2].石油化学工业部石油化工规划设计院.塔的工艺计算.石油化学工业出版社,1976
[3].陆良福.炼油过程及设备.北京:中国石化出版社,1993
[4].汤景凝.化工原理课程设计参考资料.北京:石油大学化工原理教研室,1987
[5].匡国柱.史启才.化工单元工程及设备课程设计.化学工业出版社,2001。