无损检测概论1
《无损检测概论》课件

无损检测的工作原理和方法
无损检测的工作原理基于材料对不同类型能量的反射、散射、透射和吸收的 特性。常用的无损检测方法包括:发射、接收和分析能量信号。
常用无损检测技术介绍
超声波检测
通过发送超声波脉冲来探测 物体内部的缺陷,并根据接 收到的反射信号推断缺陷的 位置和性质。
磁粉检测
利用磁场和铁粉颗粒的磁性 相互作用,检测材料中的缺 陷和裂纹。
从高层次来看,无损检测是一种用于识别、评估和监测材料、结构和系统中 缺陷和性能问题的技术。它可以在不破坏原材料或构件的情况下,提供准确 的结果。
无损检测的分类及应用领域
• 无损检测根据检测方法的不同可以分为:视觉检测、渗透检测、超声波检测、磁性颗粒检测等。 • 无损检测在多个领域中都有广泛应用,包括:航空航天、汽车制造、核能行业等。
渗透检测
通过涂覆可渗透液体的表面, 然后观察渗透液是否被材料 中的缺陷吸收,来检测缺陷 的存在。来自无损检测的优势和局限性
1 优势
无损检测无需破坏材料,能够快速、准确地检测缺陷,提高生产效率和安全性。
2 局限性
无损检测技术对操作符要求高,并且在某些情况下可能无法探测到微小的或深埋的缺陷。
无损检测在工业中的应用案例
航空航天
无损检测在航空航天行业中广泛 应用,用于检测飞机结构、发动 机零件等的缺陷和疲劳损伤。
汽车制造
无损检测可用于检测汽车零部件 的质量和完整性,确保汽车在生 产过程中没有任何缺陷。
核能行业
无损检测可以帮助检测核能设施 内部的缺陷,确保其安全性和性 能。
总结及未来发展趋势
无损检测是一个重要的技术领域,为许多行业提供了关键的质量控制和安全 保障。随着科学技术的不断发展,无损检测技术将进一步提高准确性、效率 和实用性。
无损检测概论

射线检测 (Radiography Testing )简称RT
超声波检测(Ultrasonic Testing)简称UT 磁粉检测(Magnetic Testing)简称MT
渗透检测(Penetrant Testing)简称)简称PT
四、无损检测方法的选择
1.经济方面的考虑
首先要考虑的是进行必要的资本投入,并应详细评估 资金的回收情况。对于一个好的企业,在检测方法和 可靠性方面的投资,会收到相当的经济效益。
一般:
射线检测对体积型缺陷比较敏感;
超声波检测对面缺陷比较敏感; 磁粉检测只能用于铁磁性材料的检测; 渗透检测则用于表面开口缺陷的检测; 涡流检测对开口或近表面缺陷、磁性和非磁性的 导电材料都具有很好的适用性。
因此,无损检测技术广泛应于各种设备、压力容器、机械零部 件等的检测诊断,受到工业界的普遍重视。
二、无损检测技术的发展阶段
(一)无损检测技术发展的三个阶段
无损检查( Nondestructive Inspection, NDI)、 无损检测(Nondestructive Testing,NDT)、
2. 在役检测 使用无损检测技术对装臵在运行过程中进行监测,或者在检修 期进行检测,能及时发现影响其安全运行的隐患,防止事故。 这对于大型设备,如核反应堆、桥梁建筑、铁路车辆、压力容 器、输送管道、飞机、火箭等,具有重要的意义。 在役检测不仅可以及时发现隐患,更重要的是可以根据所发 现的早期缺陷及其发展程度(如疲劳裂纹的萌生与发展),在 确定其方位、形状、尺寸和性质等的基础上,对装臵能否继续 使用及其安全运行寿命进行评价。
(三)无损检测技术的特点
1.无损检测不会对构件造成任何损伤 无损检测是在不破坏构件的前提下,利用材料物理性质的变 化来判断构件内部和表面是否存在缺陷,不会对材料、工件和 设备造成任何损伤。
无损检测基础

5.再热裂纹
名称
特征
产生机理
防止措施
冷裂纹
a.成生于较低温度,且产生于焊后一段时间以后,故又称为延迟裂纹。 b.主要产生于热影响区,也有发生在焊缝区的。 c.冷裂纹可能是沿晶开裂,穿晶开裂或两者混合出现。 d.冷裂纹引起的构件破坏是典型的脆断。
1.坡口尺寸不合理; 2.坡口有污物; 3.多层焊时,层间清渣不彻底; 4.焊接线能量小; 5.焊缝散热太快,液态金属凝固过快; 6.焊条药皮,焊剂化学成分不合理,熔点过高,冶金反应不完全,脱渣性不好; 7.钨极惰性气体保护焊时,电源极性不当,电流密度大,钨极熔化脱落于熔池中。 8.手工焊时,焊条摆动不良,不利于熔渣上浮。
a.合金元素合杂质的影响碳元素以及硫、磷等杂质元素的增加,会扩大敏感温度区。使结晶裂纹的产生机会增多。 b.冷去速度的影响 冷却速度增大,一是使结晶偏析加重,二是使结晶温度区间增大,两者都会增加结晶裂纹的出现机会。 c.结晶应力与拘束力的影响 在脆性温度区内,金属的强度极低,焊接应力又使这部分金属受拉,当拉应力达到一定程度时,就会出现结晶裂纹。
a.再热裂纹的产生机理有多种解释,其中楔型开裂理论的解释如下:近缝区金属在高温热循环作用下,强化相碳化物(如碳化钛、碳化钒、碳化铌、碳化铬等)沉积在晶内的位错上,使晶内强化迁都大大高于晶界强化,尤其是当强化相弥散分别在晶粒内时,会阻碍晶粒内部的局部调整,又会阻碍晶粒的整体变形,这样由于应力松弛而带来的塑性变形就主要由晶界金属来承担,于是,晶界区金属会产生滑移,且在三晶粒交界处产生应力集中,就会产生裂纹,即所谓的楔型开裂。图2-30是楔型开裂的示意图。
朱明zhubob-无损检测概论

检测方法和检测对象的适应性(表一)
无 损 检 测培 训
主讲:朱明 高级工程师、高级技师、国家经济师 高级国家职业技能鉴历经兵农工商学。 历经:兵团开车,地方修车,企业管理:技术、运营、 物流、安全、保卫, 职任:客运站长、 公司经理, 集团技术总监, 总经理 及法人代表。 ((本人教学资料搜索:朱明zhubob(需要资料内容) 学历:本科、MBA, 专业:汽车维修与使用、企业管理、经济管理。 职业资格与职称:高级工程师、高级技师、国家经济师、 高级技能专业教师、高级国家职业资格考评员。 管理科 学研究院特约讲师、 管理顾问有限公司高级讲师。 客座任教:大学、 技师学院、国家职业资格培训与考评 及企业内部职业培训。Q号657555589
在产品工艺试验中,对工艺试样进行无损检 验,并根据检测结果改进制造工艺,确定理 想的制造工艺。
4)降低生产成本
在产品制造过程中的适当环节正确地进行无 损检测,防止以后的工序浪费,减少返工, 降低废品率,从而降低制造成本。
3.无损检测的应用特点
1)要与破坏性检测相结合
由于无损检测具有的局限性,不是所有的需 要测试的项目和性能都能进行无损检测,这 种局限性可能来自方法本身,也可能来自被 测试对象的形状、位置等客观条件的不允许, 所以某些试验只能采用破坏性检验。
2).铸件中常见宏观缺陷及其产生原因
夹砂(冲砂)和夹渣:浇口设计不当容易出现,主要是 铸件表面的砂粒和高温溶液接触,剥离后混入钢中;钢 溶液中混入熔渣后又将钢水注入铸型中。超声波检测 缩孔和疏松:凝固过程中溶液供给不足时产生,此外与 铸件的材质也有关系,收缩率越大材料越容易出现缩孔, 射线和超声波共同使用效果最好 铸造裂纹:铸件各部分冷却速度不同,产生内应力,当 内应力超过该温度下的承受能力时,便会造成铸件撕裂 而形成裂纹。热裂纹 (1300℃) :晶间夹杂物是脆性的, 在晶间拉伸应力的作用下产生热裂纹;缩孔性裂纹:不 能完全承受其它部位的收缩力产生;冷裂纹( 260℃ ): 由奥氏体向马氏体转变温度范围内,组织应力造成穿晶 断裂。超声波检测,大型铸件射线透照加高能加速器 冷隔:同一铸件中一次浇铸或两次浇铸时,由于温度偏 低,金属液体未能充分融合在一起,边界形成带有氧化 层的隔层。超声波探伤。
无损检测概论.

无损检测概论一.无损检测基础知识1.无损检测的定义与分类(1)定义:在不损坏试件的前提下,以物理或化学方法为手段,借助先进的技术和设备器材,对试件的内部及表面的结构、性质、状态进行检查和测试的方法,以“NDT”英文缩写表示。
而用人的肉眼为手段称之为宏观检查,以英文“VT”表示。
1无损探伤:是无损检测早期阶段的名称,其涵义是探测和发现缺陷;2无损检测:是当前阶段的名称,其内涵不仅仅是探测缺陷,还包括探测试件的一些其他信息,例如结构、性质、状态等,并试图通过测试,掌握更多的信息;3无损评价:是将进入或目前正在进入的新阶段的名称,其内涵不仅仅是探测缺陷、探测试件的结构、性质、状态,还要求获取更全面、更深刻的、更准确的综合信息,例如缺陷的形状、尺寸、位置、取向、内含物、缺陷部位的金相组织、残余应力等,结合成像技术、自动化技术、计算机数据分析和处理等技术,与材料力学、断裂力学等知识综合应用,对试件或产品的质量和性能给出全面、准确的评价。
(2)分类:目前无损检测方法可分为射线检测(RT)、超声波检测(UT)、磁粉检测(MT)、渗透检测(PT)、涡流检测(ET)、声发射检测(AE)。
1、常用的无损检测方法:RT、UT、MT、PT是应用最广泛的探测缺陷的四大常规方法2、 RT、UT是用于探测试件内部缺陷的,RT是检测内部的体积壮缺陷,UT是检测内部的平面形缺陷。
3、 MT和PT、ET主要用于探测试件表面和近表面缺陷。
4、声发射主要用于探测试件在承载状态下的缺陷张口位移(活动)情况。
5、其他如激光、红外、微波、液晶等技术应用于无损检测。
2.无损检测的目的(1)保证产品质量:通过无损检测可以将原材料中的冶炼、轧制缺陷和制造中的工艺缺陷,如焊接缺陷等一些不允许存在的缺陷发现并予以消除而保证产品质量。
(2)保障使用安全:通过无损检测可以发现设备试件在使用中产生的缺陷,并予以消除而提高了设备在规定的使用条件下工作时的可靠性。
无损检测概论

A型脉冲反射式模拟超声波检测仪的主要组成部分是:同步电路、扫描电 路、发射电路、接受放大器电路、显示器和电源电路等。
仪器工作原理:同步电路产生触发脉冲同时加至扫描电路和发射电路, 扫描电路受触发开始工作,产生锯齿波扫描电压,加至示波管水平偏转 板,使电子束发生水平偏转,在荧光屏上产生一条水平扫描线。与此同 时,发射电路受触发产生高频脉冲,施加至探头,激励压电晶片振动, 在工件中产生超声波,超声波在工件中以一定方式和速度向前传播,遇 到缺陷或底面产生反射,返回探头时,又被压电晶片转变为电信号,经 接收放大和检波,加至示波管垂直偏转板上,使电子束发生垂直偏转, 在水平扫描线的相应位置上产生缺陷回波和底波。
无损检测概论
武进
无损检测(NDT):就是利用声、光、磁和电等特
性,在不损坏或不影响被检对象使用性能的前提下, 检测被检对象中是否存在缺陷或不均匀性,给出缺 陷大小、位置、性质和数量等信息,进而判定被检 对象所处技术状态(如合格与否、使用寿命等)的 所有技术手段的总称。无损检测方法很多(目视检 测、声发射、超声波衍射时差法等),并且随着科 学技术的不断发展,出现了红外等新的检测技术手 段,但根据美国国家宇航局调研分析,其认为可分 为六大类约70余种。但在实际应用中比较常用的, 也就是我们说的常规无损检测方法仍指为涡流检测、 磁粉(漏磁)检测、射线检测、渗透检测和超声检 测五种。
缺点:不适用于形状复杂的工件,而且只能检测导 电材料表面和近表面缺陷,缺陷深度一般不大于 5mm,涡流检测必须有高频信号存在,给信号处理带 来一定困难,容易引起信号相互干涉。检测结果也 易受到材料本身及检测仪器功能和检测条件等其它 因素干扰。
漏磁(磁粉)检测(MT)(MFT)法的简介
漏磁(磁粉)检测
第一章 无损检测概论 第三节 渗透检测

第三节渗透检测一、概述由于毛细管作用,涂覆在洁净、干燥零件表面上的荧光(或着色)渗透液会渗入到表面开口缺陷中;去除零件表面的多余渗透液,并施加薄层显像剂后,缺陷中的渗透液回渗到零件表面,并被显像剂吸附,形成放大的缺陷显示;在黑光(或白光)下观察显示,可确定零件缺陷的分布、形状、尺寸和性质等。
渗透检测的基本步骤包括:预处理、渗透、去除、干燥、显像、检验和后处理共七个步骤。
渗透检测主要用于检测各种非多孔性固体材料制件的表面开口缺陷,适用于原材料、在制零件、成品零件和在用零件的表面质量检验。
渗透检测的主要功能是检测零件的表面质量。
渗透检测的优点是:缺陷显示直观;检测灵敏度高;可检测的材料与缺陷范围广;一次操作可检测多个零件,可检测多方位的缺陷;操作简单等。
渗透检测的缺点是:只能检测零件的表面开口缺陷;一般只能检测非多孔性材料;对零件和环境有污染等。
渗透检测与磁粉、涡流检测的比较渗透探伤的分类1. 方法分类的依据:渗透液种类、清洗方式、显象方式、灵敏度2. 分类①根据渗透液种类(染料)和清洗方法的分类:水洗型荧光法(FA)水洗型着色法(V A)后乳化型荧光法(FB)后乳化型着色法(VB)溶剂清洗型荧光法(FC)溶剂清洗型着色法(VC) F:荧光法V:着色法A:水洗型B:后乳化型C:溶剂清洗型②根据显像剂类型的方类:干式显像法:(用于荧光法) D水基湿显像法:水溶液显像:A;水悬浮液显像:W非水基湿显像法:(溶剂悬浮、速干式)S特殊显象法: E自显象法:N③根据渗透探伤灵敏度的分类:很低级、低级、中级、高级、超高级各种方法的优缺点(一)各种方法的优缺点(二)二、物理基础(一)毛细管作用如图1-6所示,将细管插入液体中时,由于表面张力和附着力的作用,管内的液体可能呈凹面而上升(当液体润湿管子时),也可能呈凸面而下降(当液体不润湿管子时),这种现象称为毛细管现象,或称毛细管作用。
图1-6 毛细管作用润湿液体在毛细管中上升的高度,可用下列公式计算:2cos h r g σθρ=式中 h ——液体在毛细管中上升的高度,单位是m ;σ——液体的表面张力系数,单位是N /m ;θ——液体对固体表面的接触角,单位是°;r ——毛细管的内半径,单位是m ;ρ——液体的密度,单位是kg /m ;g ——重力加速度,单位是m /s 。
《无损检测概述》课件
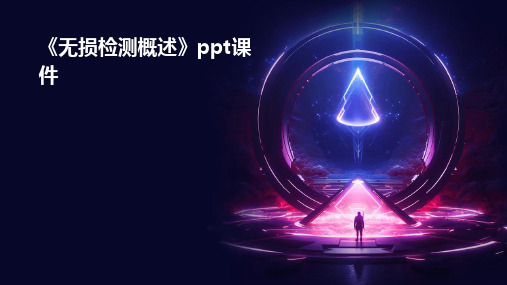
检测标准与规范
无损检测技术的标准与规范需要不断 完善,以确保检测结果的准确性和可 靠性。
检测人员素质
无损检测技术需要高素质的检测人员 ,以确保检测结果的准确性和可靠性 。
无损检测技术的未来发展方向
智能化
无损检测技术将向智能化方 向发展,通过引入人工智能 、机器学习等技术,提高检 测效率和准确性。
数字化
无损检测技术将向数字化方 向发展,通过引入数字化技 术,实现无损检测数据的数 字化存储、处理和传输。
集成化
无损检测技术将向集成化方 向发展,通过将多种无损检 测技术进行集成,实现更全 面、更准确的检测。
绿色环保
无损检测技术将向绿色环保 方向发展,通过采用环保材 料和绿色技术,降低对环境 的负面影响。
优点
对表面缺陷检测灵敏度高,可实现快 速在线检测。
缺点
仅适用于导电材料,对非导电材料不 适用。
渗透检测
原理
应用
利用渗透剂渗透到物体的表面裂纹中,通 过显像剂显示缺陷。
适用于检测非疏孔性材料的表面裂纹、气 孔等缺陷。
优点
对表面缺陷检测灵敏度高,操作简便。
缺点
需要使用化学试剂,对环境有一定影响。
CHAPTER
原理
利用磁粉的磁性,检测铁磁性 材料的表面和近表面缺陷。
应用
适用于检测钢铁、不锈钢等材 料的表面裂纹、折叠等缺陷。
优点
对表面缺陷检测灵敏度高。
缺点
仅适用于铁磁性材料,对非磁 性材料不适用。
涡流检测
原理
利用电磁感应原理,检测导电材料的 表面和近表面缺陷。
应用
适用于检测金属材料的表面裂纹、折 叠等缺陷。
02
磁粉检测技术细节
第一章 无损检测概论

6)加强检查标准和判废标准的研究和建立, 大力开展人员培训和等级资格认证考核工 作。
7)开展无损检测与评价的“技术经济”研 究。无损检测与评价
在生产中是需要一定的投资的,在一个 产品的各个生产环节中,如何分配投入无损 检测的力量,使其产品质量得到最佳保证, 而且投资最少,在生产过程中因避免浪费而 获得的直接经济效益最大。
2)发展新材料和特异形构件新的无损检 测与评定方法和技术
随着材料科学和工程技术的发展,不断 涌现出一些新材料和异型结构件。对它们 的无损检测与评价,用原有的技术和方法 常常难以进行或达不到要求。
比如各种复合材料,某些工程陶瓷材料、 特殊的高分子材料、粗大晶粒材料、混凝 土及一些异型工件特殊部位的检测等。对 于这些材料和工件的检测,必须研究一些 新的方法和技术。
常见的有:超声波探伤(UT)、射线 照相探伤(RT)、磁粉探伤(MT)、渗 透探伤(PT)和涡流检测(ET)等等。
各类无损检测人员的技术资格分为三 个等级。III级为最高级,I为最低级。
各级人员的职责要求如下:
I 级无损检测人员: 根据技术说明书进行无损检测操作的
能力;
II级无损检测人员: 根据确定的检测工艺,实施和管理无
1.7 NDT人员要求
1)必须掌握不同制造方法可能产生的缺陷, 并能选择最适于发现这种缺陷的无损检测方 法。
例如,要发现锻造及冲压加工所产生的 缺陷,不宜采用射线探伤。对于表面淬火裂 纹,则宜采用磁粉探伤。
2)必须具备关于缺陷对材料性能影响方面的 丰富知识,根据无损检测的结果来判定材料 及构件是否满足性能要求。
盐田港二期工程
深圳市重点工程,检测内容包括螺旋焊管桩(1.6万吨)、出口大门、冷藏箱钢走 道、灯塔、焊接钢轨道(上图左侧为焊接钢轨道的r射线拍片,上图右侧为螺旋焊管的 X射线拍片)。
探伤培训资料

第一章无损检测概论1.1无损检测的定义与分类所谓无损检测,从字面上理解就是指在不损坏试件的前提下,对试件进行检查和测试的方法。
射线检测(RT)、超声波检测(UT)、磁粉检测(MT)和渗透检测(PT)是开发较早,应用较广泛的探测缺陷的方法,被称为四大常规检测方法。
其中RT 和UT主要用于探测试件内部缺陷,MT和PT主要用于探测试件表面缺陷。
1.2无损检测的目的应用无损检测技术,通常是为了达到以下目的:1.保证产品质量应用无损检测技术,可以探测到肉眼无法看到的试件内部和表面的缺陷。
应用无损检测技术的另一个优点是可以进行百分百检验。
采用破坏性检测,在检测完的同时也破坏了试件,因此破坏性检测只能进行抽样检验。
许多重要的材料,结构或产品,必须保证万无一失,只有采用无损检测手段,才能为质量提供有效保证。
2.保障使用安全即使是设计和制造质量完全符合规范要求的设备或零部件,在经过一段时间使用后也可能发生破坏事故。
为了保障使用安全,对有特殊要求的在用设备,必须定期进行检验,及时发现缺陷,避免事故发生,无损检测就是在用设备定期检验的主要内容和发现缺陷的最有效手段。
3.改进制造工艺在产品生产过程中,为了了解制造工艺是否适宜,必须事先进行工艺试验。
在工艺试验中,经常对工艺试样进行无损检测,并根据检测结果改进制造工艺,最终确定理想的制造工艺。
4.降低生产成本在产品制造过程中进行无损检测,往往被认为要增加检查费用,从而使制造成本增加。
如果在制造过程中的适当环节正确地进行无损检测,就是防止以后工序的浪费,减少返工,降低废品率,从而降低制造成本。
如对铸造件进行机械加工,有时不允许机加后表面出现气孔、裂纹等缺陷,选择在机加工前对要进行加工部位实施无损检测,对发现缺陷的部位就不再加工,从而降低废品率,节省加工工时。
1.3无损检测的应用特点1.无损检测要与破坏性检测相结合无损检测最大的特点就是能在不损伤材料、工件和结构的前提下进行检测,但不是所有需要检测的项目和指标都能进行无损检测,无损检测技术本身还有局限性。
《无损检测概论》课件

04
无损检测在工业领域的应用案例
航空工业的无损检测应用
飞机制造过程中,无损检测技术 用于检测复合材料、金属材料等 的质量,确保飞机结构的完整性
和安全性。
在航空发动机制造中,无损检测 技术用于检测发动机叶片、涡轮 盘等关键部件的内部缺陷和表面
损伤。
在飞机维修和检查中,无损检测 技术用于检测飞机各个部件的损 伤和疲劳裂纹,确保飞机的安全
压力容器行业的无损检测应用
在压力容器、锅炉等设备的制 造中,无损检测技术用于检测 焊接缝、热影响区等部位的缺 陷和损伤。
在压力容器的定期检验中,无 损检测技术用于评估容器的安 全性能和剩余寿命。
在压力容器行业的维修和改造 中,无损检测技术用于检测设 备的内部缺陷和表面损伤,确 保设备的安全运行。
THANKS
1 2
多元化和个性化
随着工业制造的多样化发展,无损检测技术需要 不断适应各种不同的检测需求,向多元化和个性 化方向发展。
智能化和自动化
未来无损检测技术将更加依赖于人工智能、机器 学习等先进技术,实现智能化和自动化检测。
3
绿色环保
随着环保意识的提高,无损检测技术需要更加注 重环保和节能,如减少有害物质的使用、降低能 耗等。
对于一些关键部件和设备,无损检测可以及时发现其内部损伤和缺 陷,避免因设备故障导致天
飞机和航天器的制造过程中需 要进行大量的无损检测,以确
保其安全性和可靠性。
石油化工
管道、压力容器等设备的无损 检测是石油化工领域的重要应 用。
轨道交通
高铁、地铁等轨道交通设备的 无损检测对于保障乘客的安全 至关重要。
无损检测技术的发展趋势
技术创新
随着科技的不断进步,无损检测 技术也在不断创新,如超声、射 线、涡流等检测技术都在逐步提
无损检测概论
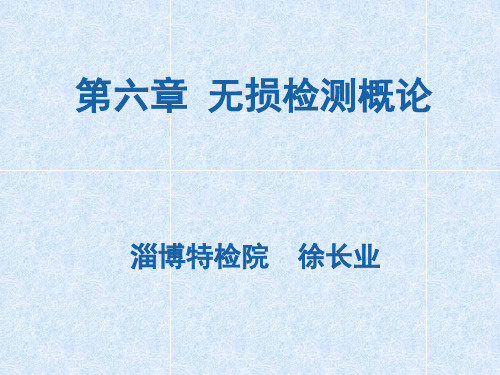
无损检测概论
无损检测技术的发展过程出现过三个名称,即:无损 探伤,无损检测,无损评价。无损探伤是早期的阶段的名 称,其含义是探测和发现缺陷。无损检测是目前的名称, 其含义不仅仅是探测缺陷,还包括探测工件的其它信息, 例如结构,性质,状态等。无损评价是我们即将进入或正 在进入的新的发展阶段,它在无损检测基础上还要求获得 更全面,更准确的内容。 目前,无损检测(Non—distructive Testing)有6大常 规方法:射线检测(Radiography Testing即RT),超声波 检测(Ultrasonic Testing即UT),磁粉检测(Magnetic Testing即MT),渗透检测(Penetrant Testing即PT), 涡流检测(Eddy current Testing即ET),声发射检测( Acoustic Emission即AT)
射线检测基础知识
2 射线照相的原理 是指用X射线或γ射线穿透工件,以胶片作为记录信息 的器材的无损检测方法。射线到达胶片时,能使胶片 乳剂层中的卤化银产生潜影,经过显影和定影后就黑 化,接受射线多的部位黑化程度就高,把底片放在观 片灯上观察,就可以发现缺陷,大小,位置。 射线照相法是最基本,应用最广泛的一种射线检测方 法 射线照相目的:检测工件内部的宏观缺陷。
无损检测概论
3.无损检测的应用特点 (2)正确选用实施无损检测的时机 在进行无损检测时,必须根据无损检测的目的,正确 选择无损检测实施的时机。例如,有冷裂纹倾向的材料, 就应该安排在焊接完成24小时以后进行无损检测。只有正 确的选用实施无损检测的时机,才能顺利的完成检测。正 确评价产品质量。
无损检测概论
射线检测基础知识
射线检测示意图
图7.2-5 x射线照相原理
无损检测概论(第一)

未焊透: 焊接接头根部未完全熔透, 未焊透 : 焊接接头根部未完全熔透 , 原因是焊接电流
过小、运条速度过快、坡口角度太小、 过小、运条速度过快、坡口角度太小、根部间隙过小等
形状缺陷:咬边( 形状缺陷 : 咬边 ( 焊接参数选择不当或操作工艺不正
确 ) 、 焊瘤、 烧穿或下塌( 下垂, 焊接电流过大) 、 错 焊瘤 、 烧穿或下塌 ( 下垂 , 焊接电流过大) 边和角变形、 焊缝尺寸及形状不符合要求( 余高过高、 边和角变形 、 焊缝尺寸及形状不符合要求 ( 余高过高 、 焊脚尺寸不足等) 焊脚尺寸不足等)
其它几种常用无损探伤方法 涡流检测(Eddy current Testing )简称ET 声发射检测(Acoustic Emission)简称AE 目视检测(Visual and Optical Testing) 简称 VT 泄漏检测(Leak Testing)简称LT
其它无损检测技术 随着现代科学技术的发展,激光、红外、微 波、液晶等技术都被应用于无损检测领域, 而传统的常规无损检测技术也因为现代科技 的发展,大大丰富了应用方法,如射线照相 就可细分为X射线、γ射线、中子射线、高能 X射线、射线实时照相、层析照相……等多种 方法。
无损评价:( 无损评价:(Non- distructiv Evaluation) :( ) 简称NDE 简称 新的发展阶段的名称 不仅要求发现缺陷,探测试件的结构、状态 、性质,还要求获取更全面、准确和综合的 信息,辅以成象技术、自动化技术、计算机 数据分析和处理技术等,与材料力学、断裂 力学等学科综合应用,以期对试件和产品的 质量和性能作出全面、准确的评价。
无损检测概论
1.无损检测的定义和分类 .
定义: 定义: 通俗的定义: 通俗的定义:无损检测指在不损坏试件的前 提下,对试件进行检查和测试的方法。 提下,对试件进行检查和测试的方法。 亦称非破坏性检验。 亦称非破坏性检验。
无损检测概论

无损检测方法分类
五大常规方法 (1)射线探伤法----RT (2)超声探伤法----UT (3)磁粉探伤法----MT (4)渗透探伤法----PT (5)涡流探伤法----ET 另外还有许多非常规方法,如声发射、红外检 测、目视检测、泄漏检测等。
磁粉探伤
• 只适于铁磁材料中非铁磁性缺陷的检测,包括锻 件、焊缝、铸件等。 • 由于趋肤效应,磁探法只能探测表面或近表面缺 陷。 • 一般能确定缺陷的位置、大小和形状,但难以确 定缺陷的深度,有时难以确定缺陷的性质。 • 不适用对象:非铁磁性材料,如奥氏体不锈钢、 铜、铝等。
涡 流 工 作 原 理 示 意 图
涡流检测的特点
1 适合各种导电材料的试件探伤; 2 可以检出表面和近表面缺陷; 3 探测结果以电信号给出,容易实现自动化; 4 由于采用非接触接触,所以检测速度很快; 5 对形状复杂的试件很难应用;一般用于管材、 棒材、板材等; 6 不能显示缺陷图形,因此无法从显示信号判断 出缺陷性质; 7 检测干扰因素多,容易引起杂乱信号; 8 由于趋肤效应,埋藏较深的缺陷无法检出; 9 不能用于非导电的材料。
超声波探伤
• 超声法适用于锻件、板材、管材、焊缝等工件或 材料的探伤。 • 主要用于内部缺陷的探测,也可用于表面缺陷的 探测。 • 缺陷显示不够直观。 • 超声探伤能测定缺陷位置和相对尺寸,缺陷的种 类一般较难判定。 • 不适合粗晶材料和形状复杂或表面粗糙的工件。
射线检测
• 基于被检测件对透入射线的不同吸收来检 测零件内部及表面缺陷的无损检测方法。 • 目前主要有X射线照相技术、γ射线照相技 术、射线实时成像技术、计算机射线照相 技术、CT检测技术等。
无损检测的应用
• 应用时机:设计阶段;制造过程;成品检验; 在役检查。 • 应用对象: • 各类材料:金属、非金属等; • 各种工件:焊接件、锻件、铸件等; • 各种工程:机械设备、道路建设、水坝建设、 桥梁建设、机场建设等。 • 各个行业:特种设备、航空航天、机械电子、 核工业、船舶、铁道、建筑等。
无损检测概论

• • • • • • • • • • • • • • • •
无损检测工艺规程包括通用工艺规程和工艺卡。 A. 无损检测通用工艺规程 无损检测通用工艺规程应根据相关法规、产品标并针对检测机构的特点和检测能力进行编制。无 损检测通用工艺规程应涵盖本单位(制造、安装或检测单位)产品的检测范围。 无损检测通用工艺规程至少应包括以下内容: a) 验适用范围; b) 引用标准、法规; c) 检测人员资格; d) 检测设备、器材和材料; e) 检测表面制备; f) 检测时机; g) 检测工艺和检测技术; h) 检测结果的评定和质量等级分类; i) 检测记录、报告和资料存档; j) 编制(级别)、审核(级别)和批准人; k) 制定日期。 无损检测通用工艺规程的编制、审核及批准应符合相关法规或标准的规定。
1.2.3 无损检测人员
• 1.2.3 无损检测人员 • 从事承压设备的原材料、零部件和焊接接 头无损检测的人员,应按照《特种设备无损检 测人员考核与监督管理规则》的要求取得相应 无损检测资格。 • 无损检测人员分为Ⅲ(高)级、Ⅱ(中)级和 I(初)级。取得不同无损检测方法各资格级别的 人员,只能从事与该方法和该资格级别相应的 无损检测工作,并负相应的技术责任。
8
底片的图像
9
射线检测特点1
①.检测结果有直接记录——底片。由于底片上记录的信息十分丰富,且可以 长期保存,从而使射线照相法成为各种无损检测方法中记录最真实、最直观、 最全面、可追踪性最好的检测方法。 ②可以获得缺陷的投影图像,缺陷定性定量准确各种无损检测方法中,射线照 相对缺陷定性是最准的。在定量方面,对体积型缺陷(气孔、夹渣类)的长 度、宽度尺寸的确定也很准。 ③体积型缺陷检出率很高。而面积型缺陷检出率受到多种因素影响。体积型缺 陷是指气孔、夹渣类缺陷。射线照相大致可以检出直径在试件厚度 1%以上的 体积型缺陷。面积型缺陷是指裂纹、未熔合类缺陷,其检出率的影响因素包 括缺陷形态尺寸、透照厚度、透照角度、透照几何条件、源和胶片种类、像 质计灵敏度等,所以裂纹检出率相对较低。 ④.适宜检测较薄的工件而不适宜较厚的工件。检测厚工件需要高能量的射线 探伤设备。300 kV便携式X射线机透照厚度一般小于40 mm,420 kV移动式X 射线机和Irl92γ射线机透照厚度均小于100 mm,对厚度大于100 mm的工件 照相需使用加速器或C060,因此是比较困难的。此外,板厚增大,射线照相 绝对灵敏度是下降的,也就是说对厚工件采用射线照相,小尺寸缺陷以及一 些面积型缺陷漏检的可能性增大。
- 1、下载文档前请自行甄别文档内容的完整性,平台不提供额外的编辑、内容补充、找答案等附加服务。
- 2、"仅部分预览"的文档,不可在线预览部分如存在完整性等问题,可反馈申请退款(可完整预览的文档不适用该条件!)。
- 3、如文档侵犯您的权益,请联系客服反馈,我们会尽快为您处理(人工客服工作时间:9:00-18:30)。
检测结果的可靠性,必须在检测前正确选定最 适当的无损检测方法。在选择中,既要考虑被 检工件、设备的材质、结构、形状、尺寸,预 计可能产生的什么种类、形状的缺陷,在什么 部位,什么方向产生。又要依以上种种情况考 虑无损检测方法各自的特点。例如,钢板的分 层缺陷因其延伸方向与钢板平行,就不适合射 线检测而应选择超声波检测。检查工件、设备 表面细小的裂纹,就不应选择射线和超声波检
这三个名称体现了无损检测技术发展的三个阶 段。无损探伤是早期阶段的名称,其含义是检测 和发现缺陷;无损检测是当前阶段的名称,其内 涵不仅仅是检测缺陷,还包含检测试件的一些其 他信息,例如结构、性质、状态等,并试图通过 检测,掌握更多的信息。无损评价则是即将进入 或正在进入的新的发展阶段。无损评价涵盖更广 泛、更深刻的内容,它不仅要求发现缺陷,检测 试件的结构、性质、状态,还要求获取更全面积、 更准确的综合信息,例如缺陷的形状、尺寸、位 置、取向、内含物、缺陷部位的组织、残余应力
取长补短,坐而取得更多的信息。例如,超声 波检测对裂纹缺陷检测灵敏度较高,但定性不 准,而射线检测的优点是对缺陷定性比较准确, 两者配合使用,就能保证检测结果即可靠又准 确。
承压类特种设备无损检测标准
目前国内无损检测各种相关标准很多,有一 百五十多个。例,GB/T9445—2008无损检测 人员资格鉴定与认证、 GB/T14693—2008焊
(接上页)
是如果在制造过程中间的适当环节正确地进 行无损检测,就是防止以后的工序浪费,减 少返工,降低废品率,从而降低成本。例如, 厚板焊接时,如果在焊接全部完成后再进行 无损检测,发现超标缺陷需要返修,要花费 许多工时或者很难返修。因此可以在焊至一 半时先进行一次无损检测,确认没有超标缺 陷再继续焊接,这样虽然无损检测费用有所 增加,但总的制造成本降低了。
二、保障使用安全 即使是设计和制造质量完全符合规范标准要 求的设备,在经过一段时间使用后,也有可能导致 破坏事故。这是由于苛刻的运行条件使设备状态 发生变化,例如由于高温和应力的作用导致材料蠕 变;由于温度、压力的波动产生交变应力,使设备 的应力集中部位产生疲劳;由于腐蚀作用使壁厚 减薄或材质劣化;等等。上述因素有可能使设备 中原来存在的制造规范标准允许的小缺陷扩展开 裂,或使设备中原来没有缺陷的地方产生这样或那 样的缺陷,最终导致设备失效。为了保障设备使用
等信息。它要结合成像技术、自动化技术、计 算机数据分析和处理技术,与材料力学等领域 知识,对试件或产品的质量和性能给出全面、准 确的评价。
射线检测(RT)、超声波检测(UT)、磁粉 检测(MT)和渗透检测(PT)是开发较早,应 用较广泛的检测缺陷的方法,称为四大常规检测 方法。到目前为止,这四种方法仍是承压类特种 设备、非承压类设备制造质量检测和在用设备检 测最常用的无损检测方法。其中RT和UT主要用
于检测试件内部缺陷,MT主要用于检测试件表面 及近表面缺陷,PT主要用于检测试件表面开口型缺 陷。其他无损检测方法有涡流检测(ET)、 声 发射检测(AT)等。 为满足生产的需要,并伴随着现代科学技术的 进展,无损检测的方法和种类日益繁多,除了上面提 到的几种方法外,激光、红外、微波、液晶等技术 都被应用于无损检测。仅利用射线的无损检测方 法就可细分为X射线照相、γ射线照相、中子射线 照相、高能X射线照相、射线实时成像、层析照 等十几种。
无损检测的应用特点
一、无损检测要与破坏性检测相结合 无损检测的最大特点是能在不损伤材料、工 件和结构的前提下来进行检测,所以实施无损 检测后,产品的检查率可以达100%。但是并 不是所有需要测试的项目和指标都能进行无损 检测,无损检测技术自身还有局限性。某些试 验只能采用破坏性检测,因此,在目前无损检 测还不能完全代替破坏性检测。也就是说,要 对工件、材料、设备作出准确的评价,必须把
安全,对在用设备进行定期检验,及时发现缺陷, 避免事故发生,而无损检测就是设备定期检验的 主要内容和发现缺陷最有效的手段。 三、改进制造工艺 在产品生产中为了了解工艺是否适宜,必须事 先进行工艺试验。在工艺试验中经常对工艺试 样进行无损检测,最终确定理想的是制造工艺。 四、降低生产成本 在产品制造过程中进行无损检测,往往被认 为要增加检查费用,从而使制造成本增加。可
4.适宜检测较薄的工件而不适宜较厚工件。 5.适宜检测对接焊缝,检测角焊缝效果较 差,不适宜检测板材、棒材、锻件。 6.有些试件结构和现场条件不适合射线照 相检测。 7.对缺陷在工件中厚度方向的位置、尺寸 (高度)确定比较困难。 8.检测成本高 9.射线照相检测速度慢。 10.射线对人体有伤害
Байду номын сангаас
超声波检测 超声波检测是用仪器来检测产品或试件 的内部缺陷。 超声波检测的优点和局限性: 1.面积型缺陷检出率高,而体积型缺陷检 出率较低。 2.适合检测厚度较大的工件。 3.适用范围广,可用于各种试件。 4.检测成本低,速度快,仪器体积小,现 场使用方便。 5.无法得到缺陷直观图像,定性困难,定 量精度不高。
缝无损检测符号、GB/T3323—2005金属熔化 焊焊接接头射线照相。 承压类特种设备无损检测标准主要有 JB/T 4730—2005承压设备无损检测、 SY/T4109--- 2005石油天然气钢质管道无 损检测、GB/T 12605—2008金属管道熔化焊 环向对接接头射 线照相方法等。
射线检测 射线检测用来检测工件或材料内部 缺陷。 射线检测的优点和局限性: 1.检测结果直接记录---底片。 2.可以获得缺陷的投影图像,缺陷定 性定量准确。 3.体积型缺陷检出率高,而面积型缺 陷的检出率受到多种因素影响。
3.检测灵敏度很高,可以发现极细小的裂纹 以及其它缺陷。 4.检测成本很低,速度快。 5.工件的形状和尺寸对检测有影响,有时因其 难以磁化而无法检测。 渗透检测 渗透检测用来检测工件表面开口型缺陷 渗透检测的优点和局限性: 1.渗透检测可以用于除了疏松多孔材料外任何 类的材料。 2.形状复杂的部件也可以用渗透检测,并一次 操作就可大致做到全面检测。
无损检测的目的
一、保证产品质量
应用无损检测技术,可以检测到人的肉眼无法 看到的试件内部缺陷;在对试件表面质量进行业 检验时,通过无损检测方法可以检测出许多人的肉 眼很难看见的细小缺陷。由于无损检测技术对缺 陷检测的应用范围广,灵敏度高,检测可靠性好,因 此产品制造过程检验和最终质量检验中普遍地采 用。
3.同时存在几个方向的缺陷,一次检测操作就 可完成检测。 4.不需大型设备,可不用水、电。 5. 试件表面粗糙度影响大,检测结果往往容易 受操作人员水平影响大。 6.可以检测表面开口型缺陷。 7.检测工序多,速度慢。 8.检测灵敏度比磁粉检测低。 9.材料较贵,成本较高。 10.检测所用材料大多数易燃有毒。 (不到之处请指正 )
无损检测概论
盐城智超检测技术有限公司 2010年06
无损检测的定义与分类
什么叫无损检测?从字面上理解,无损检测 就是指在不损坏试件的前提下,对试件进行检查 和测试的方法。 现代无损检测的定义是:在不损坏试件的前
提下,以物理或化学方法为手段,借助先进的技 术和设备器材,对试件的内部及表面结构、性质、 状态进行检查和测试的方法。
6.检测结果无直接见证记录。 7.对缺陷在工件厚度方向上的定位较准 8.材质、晶粒度对检测有影响。 9.工件不规则的外形和一些结构会影响检测。 10.不平或粗糙的表面会影响耦合和扫查,从而影 响检测精度和可靠性。 磁粉检测 磁粉检测用来检铁磁性材料工件或试件焊缝表 面、近表面缺陷。 磁粉检测的优点和局限性: 1.适宜铁磁性材料检测。 2.可以检出表面和近表面缺陷。
测,而应选择磁粉或渗透检测。只有这样,无 损检测方法的选择和应用才会是正确的、合理 的。 四、综合应用各种无损检测方法 在无损检测应用中,必须认识到任何一种无 损检测方法都不是万能的,每种无损检测方法 都有优缺点。因此,在无损检测的应用中,如 果可能,不要只采用一种无损检测方法,而尽 可能同时采用几种方法,以保证各种检测方法
无损检测的结果与破坏性检测的结果结合起 来加以考虑。 二、正确选用实施无损检测的时机 根据无损检测的目的来正确选择无损检测 实施的时机是非常重要的。例如,检查低合 金钢(15CrMo)焊缝有无延迟裂纹,无损 检测就应安排在焊后24小时以后进行。 三、选用最适当的无损检测方法 每种检测方法本身都有局限性,不可能适 用于所有工件、设备和所有缺陷。为了提高
无损检测是以现代科学技术的发展为基础的。 例如,用于检测工业产品缺陷的X射线照相法, 是在德国物理学家伦琴发现X射线后发展起来; 超声波检测是在两次世界大战中迅速发展的声纳 技术和雷达技术的基础上开发出来的;磁粉检测 建立在电磁学理论基础上;渗透检测则得益于物 理化学的进展。
在无损检测技术发展过程中出现过三个名称, 即无损探伤(NDI)、无损检测(NDT)、无损 评价(NDE)。