镀铝转移常见原因分析
镀铝板带的表面处理技术及其影响因素分析
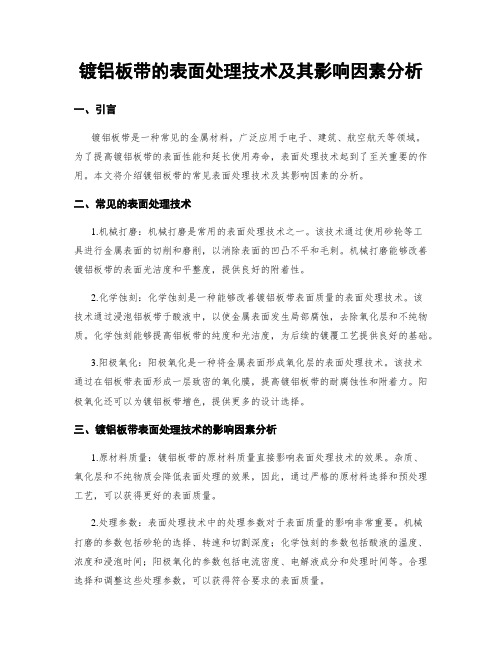
镀铝板带的表面处理技术及其影响因素分析一、引言镀铝板带是一种常见的金属材料,广泛应用于电子、建筑、航空航天等领域。
为了提高镀铝板带的表面性能和延长使用寿命,表面处理技术起到了至关重要的作用。
本文将介绍镀铝板带的常见表面处理技术及其影响因素的分析。
二、常见的表面处理技术1.机械打磨:机械打磨是常用的表面处理技术之一。
该技术通过使用砂轮等工具进行金属表面的切削和磨削,以消除表面的凹凸不平和毛刺。
机械打磨能够改善镀铝板带的表面光洁度和平整度,提供良好的附着性。
2.化学蚀刻:化学蚀刻是一种能够改善镀铝板带表面质量的表面处理技术。
该技术通过浸泡铝板带于酸液中,以使金属表面发生局部腐蚀,去除氧化层和不纯物质。
化学蚀刻能够提高铝板带的纯度和光洁度,为后续的镀覆工艺提供良好的基础。
3.阳极氧化:阳极氧化是一种将金属表面形成氧化层的表面处理技术。
该技术通过在铝板带表面形成一层致密的氧化膜,提高镀铝板带的耐腐蚀性和附着力。
阳极氧化还可以为镀铝板带增色,提供更多的设计选择。
三、镀铝板带表面处理技术的影响因素分析1.原材料质量:镀铝板带的原材料质量直接影响表面处理技术的效果。
杂质、氧化层和不纯物质会降低表面处理的效果,因此,通过严格的原材料选择和预处理工艺,可以获得更好的表面质量。
2.处理参数:表面处理技术中的处理参数对于表面质量的影响非常重要。
机械打磨的参数包括砂轮的选择、转速和切割深度;化学蚀刻的参数包括酸液的温度、浓度和浸泡时间;阳极氧化的参数包括电流密度、电解液成分和处理时间等。
合理选择和调整这些处理参数,可以获得符合要求的表面质量。
3.设备状况:设备的状态直接影响对金属表面的处理效果。
设备的精度、稳定性和附加功能,如过滤系统和搅拌系统等,都会对表面处理结果产生影响。
因此,定期检查、维护和升级设备,保持其良好的工作状态,对于获得高质量的表面处理效果至关重要。
4.操作工艺:操作工艺是表面处理技术中不可忽视的因素。
防止镀铝膜转移的方法和策略
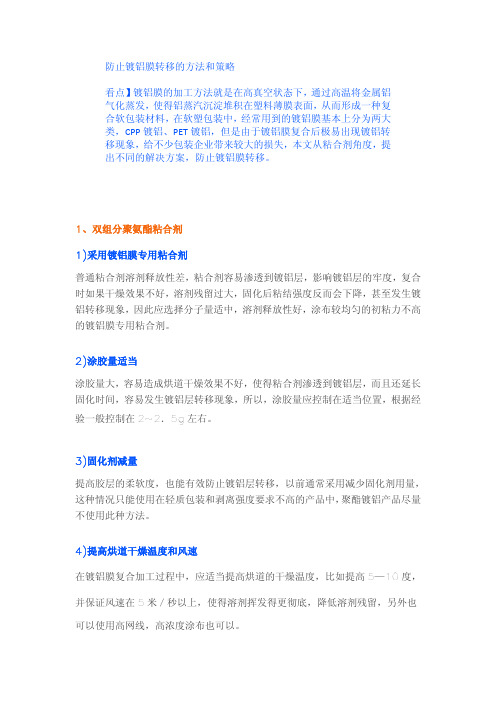
防止镀铝膜转移的方法和策略看点】镀铝膜的加工方法就是在高真空状态下,通过高温将金属铝气化蒸发,使得铝蒸汽沉淀堆积在塑料薄膜表面,从而形成一种复合软包装材料,在软塑包装中,经常用到的镀铝膜基本上分为两大类,CPP镀铝、PET镀铝,但是由于镀铝膜复合后极易出现镀铝转移现象,给不少包装企业带来较大的损失,本文从粘合剂角度,提出不同的解决方案,防止镀铝膜转移。
1、双组分聚氨酯粘合剂1)采用镀铝膜专用粘合剂普通粘合剂溶剂释放性差,粘合剂容易渗透到镀铝层,影响镀铝层的牢度,复合时如果干燥效果不好,溶剂残留过大,固化后粘结强度反而会下降,甚至发生镀铝转移现象,因此应选择分子量适中,溶剂释放性好,涂布较均匀的初粘力不高的镀铝膜专用粘合剂。
2)涂胶量适当涂胶量大,容易造成烘道干燥效果不好,使得粘合剂渗透到镀铝层,而且还延长固化时间,容易发生镀铝层转移现象,所以,涂胶量应控制在适当位置,根据经验一般控制在2~2.5g左右。
3)固化剂减量提高胶层的柔软度,也能有效防止镀铝层转移,以前通常采用减少固化剂用量,这种情况只能使用在轻质包装和剥离强度要求不高的产品中,聚酯镀铝产品尽量不使用此种方法。
4)提高烘道干燥温度和风速在镀铝膜复合加工过程中,应适当提高烘道的干燥温度,比如提高5—10度,并保证风速在5米/秒以上,使得溶剂挥发得更彻底,降低溶剂残留,另外也可以使用高网线,高浓度涂布也可以。
5)提高固化温度,缩短熟化时间镀铝膜复合产品在固化过程中应适当提高固化温度,缩短熟化时间,使得粘合剂减少对镀铝层的渗透破坏作用,有效防止镀铝层转移,一般控制温度50—60度,时间在24小时左右,切忌长时间固化。
6)使用质量好的镀铝膜如成本允许,应采购高质量的镀铝膜,如带底涂胶的。
邯郸达南科机械科技,西科弧形辊维修,达科弧形辊!2、水性粘合剂1)对轻质产品的包装,如膨化食品,方便面等的生产,基本上使用的材料为CPP 镀铝,为了控制生产成本,大部分使用的为单组分水性粘合剂,在多年的生产过程中,只出现过油墨转移的问题,而镀铝未转移,同时经实际检测,复合后剥离强度都能在1.ON/15mm以上,能满足此种包装产品的标准要求。
镀铝膜使用中的常见问题

镀铝薄膜使用中的常见问题真空镀铝薄膜由于既具有塑料薄膜的特性,又具有金属的特性,是一种价廉美观、性能优良、实用性强的包装材料,因此,镀铝膜已经被广泛地应用于食品、医药、化工等产品的包装,比如快餐食品、茶叶、咖啡和化妆品的包装。
镀铝薄膜干式复合应用中的常见问题及解决方法:1、复合后镀铝膜的镀铝层发生迁移现象产生原因:(1)、镀铝层与基膜之间的结合牢度比较差;(2)、所选用的胶粘剂不合适;(3)、复合膜的固化时间过长;(4)、涂胶量过大,胶粘剂干燥不充分,残留的溶剂逐步渗透到镀铝层,造成镀铝层的迁移;(5)、张力控制不当,镀铝膜的基膜在较大张力下发生弹性形变,从而影响到镀铝层的附着力,这也是促进镀铝膜的镀铝层发生迁移的因素之一。
改善措施:(1)、更换质量较好的镀铝膜;(2)、更换合适的胶粘剂,最好是镀铝膜专用胶粘剂;(3)、适当提高固化温度并缩短固化时间,加快胶粘剂的固化反应速度,防止胶粘剂逐渐渗透到镀铝膜的镀铝层,并消弱镀铝膜基膜与镀铝层之间的附着力。
(4)、控制涂胶量,或者调整干式复合工艺的干燥温度、通风量及复合线速度等,保证胶粘剂充分干燥,将残留溶剂量控制在最低限度之内,减少对镀铝层的影响;(5)、调整张力设置,注意张力适当小一些,防止镀铝膜发生较大的弹性形变。
2、复合膜出现斑点:产生原因:(1)、胶粘剂选用不当,普通胶粘剂对镀铝层亲和力较差,涂布性能差,如果徒步不均匀,就会出现斑点现象;(2)、胶液中的残留溶剂较多,印刷膜复合后,墨层被胶液中的残留溶剂所浸润,从而可能产生斑点现象;(3)、油墨的遮盖力不足,尤其是浅色油墨,光线穿过油墨层而被铝层反射回来,产生斑点。
(4)、涂胶量不足或者涂胶不均匀,复合膜中夹杂有气泡。
改善措施:(1)、选择适当的胶粘剂,如镀铝膜专用胶粘剂;(2)、适当提高烘道的干燥温度,或者适当降低复合线速度,保证胶粘剂能够充分干燥;(3)、选择遮盖力强的油墨或加厚油墨墨层;(4)、适当提高胶粘剂涂胶量,并检查橡胶压辊的状态,以保证涂胶均匀。
镀铝膜复合后有镀铝转移、白斑、隧道现象,一网扫尽

镀铝膜复合后有镀铝转移、白斑、隧道现象,一网扫尽一、防止镀铝转移1、采用镀铝膜专用胶黏剂普通胶黏溶剂剂释放性差,胶液容易渗透到镀铝层,影响镀铝层的牢度。
复合时如果干燥效果不好,残留溶剂过多,固化后粘结强度反而会下降。
因此,应选择分子量适中、溶剂释放性好、涂布比较均匀、初黏力不太高的镀铝膜专用胶黏剂。
2、涂胶量要适当涂胶量太大,容易造成烘道干燥效果不好,使胶液渗透到镀铝层,而且还延长了固化时间,容易发生镀铝层的迁移现象。
所以涂胶量应当控制在合适的范围内。
根据经验,一般控制在 2g/m 2 -2.5g/m 2 比较适宜。
3、固化剂减量提高胶层的柔软性,也能有效防止镀铝转移现象。
以前通常采用减少固化剂用量的方法,若选择镀铝专用胶则按正常配比即可。
4、提高烘道的干燥温度和风速在镀铝膜复合加工过程中,应适当地提高烘道的干燥温度,比如提高 5 0 C-10 0 C ,并保证风速在 5m/s 以上(如果设备条件具备),使溶剂挥发得更彻底一些,降低溶剂的残留量,防止镀铝层发生转移。
另外采用高网线辊、高浓度涂布也有一定的效果。
5、提高固化温度,缩短固化时间镀铝膜复合产品在固化过程中应当适当地提高固化温度、缩短固化时间,使粘合剂减少其对镀铝层的渗透破坏作用,有利于防止镀铝层转移。
一般控制在50 0 C-60 0 C 之间熟化 24 小时 -36 小时,切忌低温长时间的固化。
6、使用质量好的镀铝膜如成本允许,一些要求较高的产品最好选用带有底涂胶的镀铝,目前国内已经有厂家生产。
7、防止复合膜出现白斑选用质量较好的油墨,保证粘合剂涂布均匀,且墨层能被残留溶剂均匀浸润选用对所用油墨和镀铝膜涂布性能都好的粘合剂。
浅颜色尤其是白色面积较大时要适当加大涂胶量。
采用镀铝膜涂胶的复合方式,但会加剧镀铝的转移。
二、防止隧道现象1、协调控制好主、副放卷及烘道的张力,使复合膜的各层在冷却后和固化时同步回缩。
2、提高烘道的干燥温度和风速来提高初黏力。
关于镀铝CPP质量问题的分析
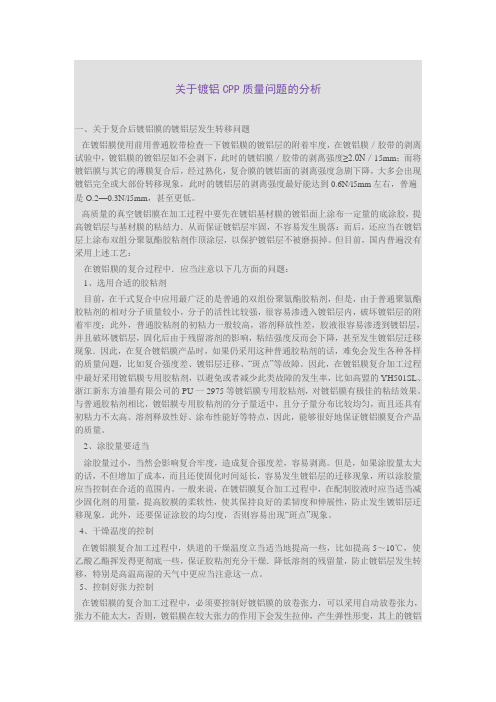
关于镀铝CPP质量问题的分析一、关于复合后镀铝膜的镀铝层发生转移问题在镀铝膜使用前用普通胶带检查一下镀铝膜的镀铝层的附着牢度,在镀铝膜/胶带的剥离试验中,镀铝膜的镀铝层如不会剥下,此时的镀铝膜/胶带的剥离强度≥2.0N/15mm;而将镀铝膜与其它的薄膜复合后,经过熟化,复合膜的镀铝面的剥离强度急剧下降,大多会出现镀铝完全或大部份转移现象,此时的镀铝层的剥离强度最好能达到0.6N/l5mm左右,普遍是O.2—0.3N/l5mm,甚至更低。
高质量的真空镀铝膜在加工过程中要先在镀铝基材膜的镀铝面上涂布一定量的底涂胶,提高镀铝层与基材膜的粘结力.从而保证镀铝层牢固,不容易发生脱落:而后,还应当在镀铝层上涂布双组分聚氨酯胶粘剂作顶涂层,以保护镀铝层不被磨损掉。
但目前,国内普遍没有采用上述工艺:在镀铝膜的复合过程中.应当注意以下几方面的问题:1、选用合适的胶粘剂目前,在干式复合中应用最广泛的是普通的双组份聚氨酯胶粘剂,但是,由于普通聚氨酯胶粘剂的相对分子质量较小,分子的活性比较强,很容易渗透入镀铝层内,破坏镀铝层的附着牢度;此外,普通胶粘剂的初粘力一般较高,溶剂释放性差,胶液很容易渗透到镀铝层,并且破坏镀铝层,固化后由于残留溶剂的影响,粘结强度反而会下降,甚至发生镀铝层迁移现象.因此,在复合镀铝膜产品时,如果仍采用这种普通胶粘剂的话,难免会发生各种各样的质量问题,比如复合强度差、镀铝层迁移、“斑点”等故障。
因此,在镀铝膜复合加工过程中最好采用镀铝膜专用胶粘剂,以避免或者减少此类故障的发生率,比如高盟的YH501SL、浙江新东方油墨有限公司的PU一2975等镀铝膜专用胶粘剂,对镀铝膜有极佳的粘结效果。
与普通胶粘剂相比,镀铝膜专用胶粘剂的分子量适中,且分子量分布比较均匀,而且还具有初粘力不太高、溶剂释放性好、涂布性能好等特点,因此,能够很好地保证镀铝膜复合产品的质量。
2、涂胶量要适当涂胶量过小,当然会影响复合牢度,造成复合强度差,容易剥离。
镀铝膜转移机理探讨

镀铝膜转移机理探讨在实际应用中,不少包装膜使用厂家对镀铝膜符合产品提出镀铝层不可转移或时对剥离强度(如剥离试验机)提出较高的要求。
理论上讲,镀铝层与镀铝基材间不是密不可分的,剥离时,如镀铝层与其他基材间的黏接轻度大于镀铝层的附着力时,就会发生镀铝层转移现象。
某知名基材厂采用EAA热封的方法检测镀铝层的附着力数据,其结果为:增强型VMPET,4.83N/15mm(Max);普通型VMPET,1.71N/15mm(Max)。
而在实际生产当中,没有一家软包装材料加工企业所加工的镀铝膜符合薄膜能够达到上述结果。
当使用普通型镀铝膜和普通型聚氨酯胶黏剂生产时,镀铝层容易发生转移。
下面在这种使用情况下,探讨镀铝层转移的相关问题。
镀铝膜的影响虽然都是普通镀铝膜,因各镀铝厂家的镀铝设备、基材、工艺等的不同,生产的镀铝膜附着力不同,所以要加强对镀铝膜的进厂检验和选择。
镀铝层的厚度也影响符合强度。
“镀铝层越厚,脆性增大,铝层与镀铝基膜的膨胀系数差值越大,与其它基材复合后复合强度月底,越容易造成铝层转移。
胶黏剂的影响粘合的作用:可靠粘结、抵抗破坏、传递应力。
粘合的目的是使机械功从一个物体传递到另一个物体。
由于胶黏剂的引入,并且由于胶黏剂本身形成了一个薄的本体相层,这就使得机械功变成从一个物体传递到胶黏剂层,然后再从胶黏剂层传递到另一个物体,整个粘合体系包括了三个本体相和两个界面(注:以两层的复合薄膜为例)。
刚下机的镀铝膜复合产品初期剥离强度较好,但是熟化后剥离强度下降,镀铝层也转移了。
初期剥离时,还没形成可靠的粘结(胶层未完全固化),剥离时一般是胶层的本体破坏,胶层不能完成机械功的传递,所以镀铝层不会转移。
聚氨酯粘合剂固化后,如果胶层与镀铝层间的结合力大于镀铝层与基材间的吸附力,就会在用剥离实验机时出现镀铝层转移的现象。
熟化温度的影响复合软包装材料加工中所用的各种塑料薄膜在一定的温度条件下都会发生某种程度的收缩,在一般情况下,熟化温度越高、时间越长,薄膜产生的收缩就越大,而且,不同的薄膜在同一温度条件下的收缩率是不一样的,因此,高温熟化易造成复合薄膜层间较大的应力。
镀铝膜干式复合应用中常见的问题及解决办法

镀铝膜干式复合应用中常见的问题及解决办法1.复合后镀铝膜的镀铝层发生迁移现象问题原因:(1)镀铝膜本身的质量比较差,镀铝层与基膜之间结合牢固度比较差。
进口的镀铝膜在基膜的真空镀铝面上有一层底图胶,用来提高镀铝膜的附着力,然后在底涂胶上真空镀铝,再在吕层上涂覆双组分聚氨酯胶做顶涂层,用来保护镀铝层不脱落,这种镀铝膜的镀铝层牢固度好,不容易脱落。
而国内一般的镀铝膜,由于没有使用底涂胶,镀铝附着力底,不太牢固,所以很容易脱落下来。
(2)所选用的胶粘就剂不合适。
(3)复合膜的固话时间过长。
(4)涂胶量过大,胶粘剂干燥不充分,残留的溶剂逐步渗透到镀铝层,造成镀铝层的迁移。
(5)张力控制不当,镀铝层的基膜在较大张力下发生弹性形变,从而影响镀铝层的附着力,这也是促使镀铝膜的镀铝层发生迁移的因素之一。
解决办法:(1)更换质量较好的镀铝膜。
(2)更换合适的胶粘剂,最好是镀铝膜专用胶粘剂。
(3)适当提高固化温度并缩短固话时间,加快胶粘剂的固化反映速率,防止胶粘剂逐渐渗透到镀铝膜的镀铝层,并削弱镀铝膜基膜与镀铝层之间的附着力。
(4)控制涂胶量,或者调整干式复合工艺的干燥温度、通风量级复合线速度等,保证胶粘剂充分干燥,将残留溶剂量控制在最低限度内,减少其对镀铝层的影响。
(5)调整张力设置,注意张力适当调小一些,防止镀铝膜发生较大的弹性形变。
(6)邯郸达南科机械科技有限公司专注镀铝机弧形辊的研发,可维修西科弧形辊kickert spreader roll日本KSK等国际品牌弧形辊。
2.复合膜出现斑点问题原因:(1)胶粘剂选用不当,普通胶粘剂对镀铝层亲和较差,涂布性能差,如果涂布不均匀,就会出现斑点现象。
(2)胶液中残留的溶剂较多,印刷复合膜后,墨层被胶液中的残留溶剂所浸润,从而有可能产生斑点现象。
(3)油墨的遮盖率不足,尤其是浅色油墨,光线穿过油墨层而被吕层反射回来,产生斑点。
(4)涂胶量不足或者涂胶不均匀,复合膜中夹有气泡。
无溶剂胶复合工艺三大异常现象的处理对策,简单实用!

无溶剂胶复合工艺三大异常现象的处理对策,简单实用!本文详细分析了无溶剂复合工艺中常见的纸塑脱离、镀铝转移、气泡等质量问题出现的原因,并介绍了相应的解决方法,希望能为使用无溶剂复合工艺的生产企业带来一些技术借鉴。
一、纸塑脱离现象纸塑脱离现象主要表现为复合膜剥离强度不足,胶不干,纸张印刷品与塑料薄膜上面的胶粘层脱离。
此现象容易在印刷面积比较大及大实地产品中出现。
因表面油墨层较厚,胶水难以润湿、扩散、渗透。
1、主要原因影响纸塑脱离的因素有许多,纸张的平滑度、匀度、含水量、塑料薄膜的各项性能、印品墨层的厚薄度、辅助材料用量、纸塑复合时的温度与压力、生产环境卫生状况以及温度、相对湿度等都会对纸塑复合的最终结果产生一定影响。
2、处理方法(1)油墨的墨层太厚,造成胶粘剂的渗透和扩散,使得纸塑脱离。
处理方法是增加胶粘剂的涂布量以及增加压力。
(2)墨层未干或未干透时,墨层中残留溶剂的成分使粘合力减弱形成纸塑脱离。
处理方法是等产品油墨干透后,再进行复合。
(3)印刷品表面残留的喷粉也会阻碍纸张与塑料薄膜的粘合形成纸塑脱离。
处理方法是利用机械和人工方式擦除印刷品表面的粉质后再复合。
4)操作工艺不规范、压力偏小,机速较快,导致纸塑脱离。
处理方法是严格按工艺规范操作,适当增加覆膜的压力、降低机速。
(5)胶粘剂被纸张及印刷油墨吸收,涂布量不足引起的纸塑脱离。
应对胶粘剂重新配方和按厂家要求确定上胶量。
(6)塑料薄膜表面电晕处理不够或超过使用期,使处理面失效引起的纸塑脱离。
应按薄膜覆膜的电晕标准对塑料基材电晕或更新塑料薄膜。
(7)在使用单组分胶粘剂时,因空气湿度不足引起的纸塑脱离,则应根据单组分胶粘剂加工工艺的湿度要求,进行人工加湿。
(8)确保胶粘剂在保质期内,并按生产厂家要求保管和使用,如双组分自动混胶机处于良好状态,保证配比的准确、均匀、充分。
二、镀铝转移现象镀铝膜既有塑料薄膜的特性,又在某种程度上替代了铝箔,起到提高产品档次的作用,而且相对成本较低。
软包装常见问题分析与解决方法

软包装常见问题分析与解决方法一、镭射膜的转移大家应该在市场上见过一些含有镭射的包装,只有几个字有镭射而其它的地方没有,这种包装是怎么做出来的呢?大家第一反应肯定是复合复进去的。
但它并不是复合上去的。
如果把这个包装撕开,仔细观看并且用手摸那几个字,可以测出有镭射字和没有镭射字的地方厚度是一样的,这就肯定了不是复合上的。
而且镭射一旦经过热辊的温度,几乎很难拉下来,这样就造成了损耗,当然或许有的客户是需要复上去,但一般常见的包装并不是复合上去的。
镭射是在印刷上面转移的,在印刷的最后一色,做根版,加个小放料架,把膜的位置对上需要镭射的那几个字就行了。
这个版不需要雕得太深,里面放的不是油墨,是放的白色乳液胶,放不干胶也可以,就只过镭射的膜就可以,过了这道版之后再与印刷膜结合一起收卷,但所需镭射的地方必须对齐,收卷不用太紧,一般就好。
镭射膜不需要张力,靠收卷和版辊的转动就可以。
在收卷完毕之后,马上卸下来放进烘箱,烘半个小时到一个小时,然后取出来在分切机上倒卷拉开,把镭射膜和印刷膜分开收卷,再看效果如何,是否需要再烘(注意张力的控制)。
倒卷好了之后就去复合,这样就完成了,不仅可以减少成本,也达到镭射的效果。
二、镀铝转移这个问题我相信一直困挠着一些软包装企业,不管企业大小都有。
常见的镀铝有镀铝CPP和镀铝PET,镀铝转移通常都出现在镀铝PET上,因为它经常被应用在中层复合。
镀铝PET,个人了解到分两种:一是镀上去的铝,二是转移上去的铝,两种镀铝的效果和附着力是不一样的。
镀上去的要好些,而转移上去的产品很多是企业买差的PET再加工转移上去,附着能力较差。
这是因为薄膜本身的剥离强度太低,镀铝层与基膜之间结合牢固度比较差。
正常的镀铝膜是在基材的真空镀铝面上有一层底涂胶,用来提高镀铝层的附着力,然后在底涂胶上真空镀铝,再在铝层上涂覆双组分聚氨酯胶作项涂层,用来保护镀铝层不脱落,这种镀铝膜的镀铝层牢固度好,不容易脱落。
而有的镀铝膜厂家为了节省生产成本,在生产镀铝膜时,没有使用底涂胶,镀铝附着力低,不太牢固,所以很容易脱落下来。
软包装干式复合镀铝膜常见故障及排除

软包装干式复合镀铝膜常见故障及排除镀铝膜由于具有塑料薄膜和金属的双重特性,不仅具有较好的光泽,而且具有较好的阻隔性,在干燥、膨化食品的包装上已得到广泛应用,在其他方面也逐步受到青睐,例如:医药的外包装等。
镀铝膜的种类有多种,常见的有PET 镀铝膜,缩写为VMPET;CPP镀铝膜,缩写为VMCPP;OPP镀铝膜,缩写为VMOPP。
但镀铝膜在复合过程中,常会出现一些困扰人的质量问题,诸如:产生细小斑点及发白、光泽度降低、印品复合后发生变色、剥离强度降低、固化后铝层发生迁移等。
在长期的实践中,我们对镀铝膜复合出现的故障作了一下总结,并对不同的故障提出了相应的解决方法,且取得初步成效。
在此刊出,供同仁们参考、交流。
一、发白及细小斑点镀铝膜在干式复合过程中表面易出现细小斑点及发白,特别是采用普通胶粘剂对BOPP/VMOPP、OPP/VMCPP、BOPP/VMPET/VMCPP几种结构进行复合时更是如此。
我们注意到,在采用单组份热塑性胶粘剂时,产生发白、斑点现象的几率要比采用双组份二液反应型胶粘剂时高得多。
另外,以单组份热塑性胶粘剂复合的成品产生的斑点是不会消失的,且这种斑点常在复合BOPP/VMOPP、BOPP/VMCPP 时发生,这是为什么呢?1.与镀铝膜本身的质量有关如果镀铝膜铝层不均匀、紧密性不好,通过检测可发现镀铝膜本身有微小的针孔,而且分布不均衡,铝层光泽度不够好,透过弱光即可发现铝层很薄,那么就导致发白、斑点现象。
这也是复合成品色调变暗的一个原因。
所以在复合前必须进行检测,以保证镀铝膜的质量符合要求。
具体做法是:取一段镀铝膜,先观察其正反两面,好的镀铝膜光泽度好、铝层均匀;再用千分尺测定其厚度,符合要求方可使用。
另外,发白、斑点现象的产生与镀铝膜的表面张力值也有关系。
表面张力值达不到要求,将影响其剥离强度。
在实际生产过程中,BOPP/VMOPP复合时,镀铝膜铝层镀得粗细不均,镀层容易剥离,油墨与粘结剂在其表面产生的粘结力高低不一,在斑点产生的地方油墨层与镀层的粘结力较低,层间的紧密度也较差,而没有斑点的地方,粘结力较高。
无溶剂复合常见故障分析与解决

无溶剂复合常见故障分析与解决(总5页)--本页仅作为文档封面,使用时请直接删除即可----内页可以根据需求调整合适字体及大小--无溶剂复合常见故障分析与解决近年来,无溶剂复合工艺在软包装生产过程中逐步得到推广,尽管该工艺较为简单和稳定,但在应用过程中还是凸显出了一些共性问题。
本文中,笔者总结了几类无溶剂复合常见故障,并给出了原因及解决方案,供业内人士参考。
固化不充分原因分析:双组分胶黏剂混合不均匀;双组分胶黏剂混配比有误,如-OH组分偏少;固化时间不够或固化温度偏低;胶黏剂已变质。
解决方案:提高双组分胶黏剂混合均匀性,检查相关混配设置是否正常工作,如检查静态混合管,一旦发现问题,应立即对其进行更换;检查双组分胶黏剂混配比,并按照说明书要求调整至正确的混配比;适当延长固化时间,提高固化温度;如果胶黏剂已变质,应立即更换。
复合膜上产生纵向或横向皱纹原因分析:横向皱纹产生的主要原因是两种复合基材张力不匹配;收卷压力不稳定,复合基材两侧收卷压力不平衡、自身横向松紧度严重不一致、接头不平整。
纵向皱纹产生的主要原因是收卷张力过大;复合基材两侧收卷压力不平衡、接头不平整。
解决方案:调节通道、第二放卷单元的收卷张力;更换质量更好的复合基材;仔细黏结新旧料带;调节收卷张力大小及两侧收卷压力的平衡。
芯皱(里皱)芯皱(里皱)是指复合料卷内部靠近芯管的区域出现皱褶。
在无溶剂复合生产中,芯皱发生的概率和造成的影响都要比干式复合生产大一些。
芯皱产生的主要原因是胶黏剂初黏力较低,其他影响因素如下。
(1)芯管的直径和质量。
通常我们使用的芯管直径为3英寸和6英寸,一般情况下,芯管直径越大,产生芯皱的概率就越少。
此外,芯管不圆、表面不平整或存在其他质量缺陷也都会直接影响芯皱数量。
(2)料头和胶带状况。
在单工位无溶剂复合设备中,我们经常采用手工操作方式黏结新旧料带,而接头和胶带粘贴是否平整会直接影响芯皱问题的发生。
(3)两种复合基材的张力匹配状况。
镀铝转移分析
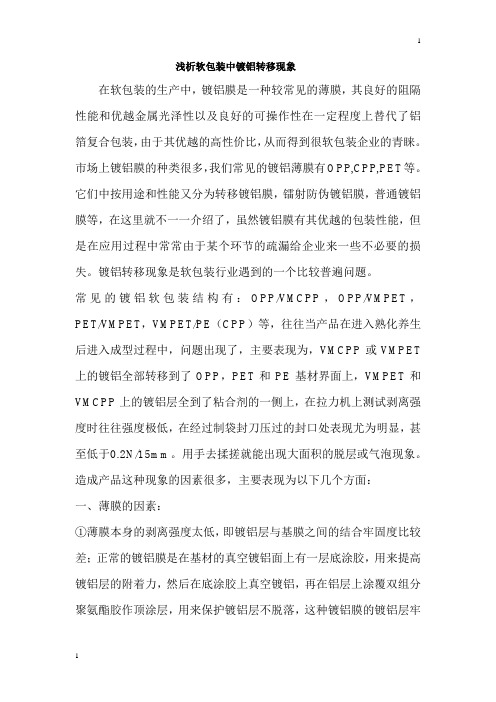
浅析软包装中镀铝转移现象在软包装的生产中,镀铝膜是一种较常见的薄膜,其良好的阻隔性能和优越金属光泽性以及良好的可操作性在一定程度上替代了铝箔复合包装,由于其优越的高性价比,从而得到很软包装企业的青睐。
市场上镀铝膜的种类很多,我们常见的镀铝薄膜有OPP,CPP,PET等。
它们中按用途和性能又分为转移镀铝膜,镭射防伪镀铝膜,普通镀铝膜等,在这里就不一一介绍了,虽然镀铝膜有其优越的包装性能,但是在应用过程中常常由于某个环节的疏漏给企业来一些不必要的损失。
镀铝转移现象是软包装行业遇到的一个比较普遍问题。
常见的镀铝软包装结构有:OPP/VMCPP,OPP/VMPET,PET/VMPET,VMPET/PE(CPP)等,往往当产品在进入熟化养生后进入成型过程中,问题出现了,主要表现为,VMCPP或VMPET 上的镀铝全部转移到了OPP,PET和PE基材界面上,VMPET和VMCPP上的镀铝层全到了粘合剂的一侧上,在拉力机上测试剥离强度时往往强度极低,在经过制袋封刀压过的封口处表现尤为明显,甚至低于0.2N/15mm。
用手去揉搓就能出现大面积的脱层或气泡现象。
造成产品这种现象的因素很多,主要表现为以下几个方面:一、薄膜的因素:①薄膜本身的剥离强度太低,即镀铝层与基膜之间的结合牢固度比较差;正常的镀铝膜是在基材的真空镀铝面上有一层底涂胶,用来提高镀铝层的附着力,然后在底涂胶上真空镀铝,再在铝层上涂覆双组分聚氨酯胶作顶涂层,用来保护镀铝层不脱落,这种镀铝膜的镀铝层牢固度好,不容易脱落。
而有的镀铝膜厂家为了节省生产成本,在生产镀铝膜时,没有使用底涂胶,镀铝附着力低,不太牢固,所以很容易脱落下来。
BB/T0030-2004中6.12项就有对BOPET镀铝附着力有这样的规定;将剥离强度为(2.0±0.2)N/cm的透明BOPP压敏胶带粘到镀铝膜的镀铝面上,而后裁15mm宽的试样,要求镀铝膜与压敏胶带间粘贴紧密;不得有气泡;皱褶等缺陷。
镀铝层
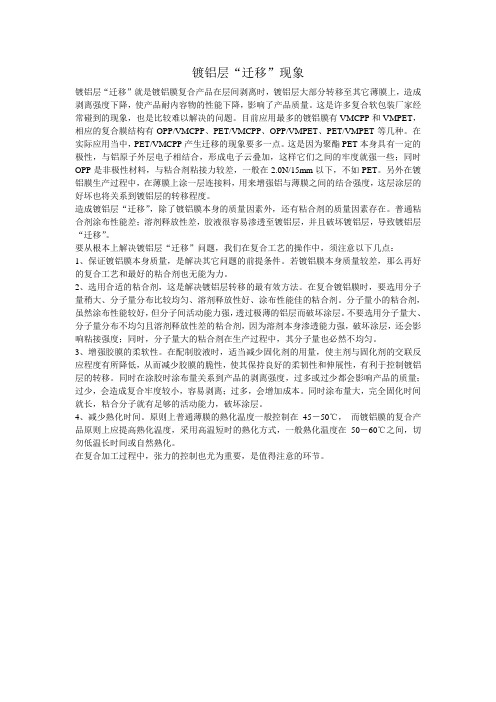
镀铝层“迁移”现象镀铝层“迁移”就是镀铝膜复合产品在层间剥离时,镀铝层大部分转移至其它薄膜上,造成剥离强度下降,使产品耐内容物的性能下降,影响了产品质量。
这是许多复合软包装厂家经常碰到的现象,也是比较难以解决的问题。
目前应用最多的镀铝膜有VMCPP和VMPET,相应的复合膜结构有OPP/VMCPP、PET/VMCPP、OPP/VMPET、PET/VMPET等几种。
在实际应用当中,PET/VMCPP产生迁移的现象要多一点。
这是因为聚酯PET本身具有一定的极性,与铝原子外层电子相结合,形成电子云叠加,这样它们之间的牢度就强一些;同时OPP是非极性材料,与粘合剂粘接力较差,一般在2.0N/15mm以下,不如PET。
另外在镀铝膜生产过程中,在薄膜上涂一层连接料,用来增强铝与薄膜之间的结合强度,这层涂层的好坏也将关系到镀铝层的转移程度。
造成镀铝层“迁移”,除了镀铝膜本身的质量因素外,还有粘合剂的质量因素存在。
普通粘合剂涂布性能差;溶剂释放性差,胶液很容易渗透至镀铝层,并且破坏镀铝层,导致镀铝层“迁移”。
要从根本上解决镀铝层“迁移”问题,我们在复合工艺的操作中,须注意以下几点:1、保证镀铝膜本身质量,是解决其它问题的前提条件。
若镀铝膜本身质量较差,那么再好的复合工艺和最好的粘合剂也无能为力。
2、选用合适的粘合剂,这是解决镀铝层转移的最有效方法。
在复合镀铝膜时,要选用分子量稍大、分子量分布比较均匀、溶剂释放性好、涂布性能佳的粘合剂。
分子量小的粘合剂,虽然涂布性能较好,但分子间活动能力强,透过极薄的铝层而破坏涂层。
不要选用分子量大、分子量分布不均匀且溶剂释放性差的粘合剂,因为溶剂本身渗透能力强,破坏涂层,还会影响粘接强度;同时,分子量大的粘合剂在生产过程中,其分子量也必然不均匀。
3、增强胶膜的柔软性。
在配制胶液时,适当减少固化剂的用量,使主剂与固化剂的交联反应程度有所降低,从而减少胶膜的脆性,使其保持良好的柔韧性和伸展性,有利于控制镀铝层的转移。
塑料薄膜脱铝、开层现象产生的原因

一些镀铝的复合薄膜包装,我们有时候会发现有时用力撕包装袋时,里面的那层银色的铝层会脱落;用手揉搓,还会开层,这是为什么呢?林州顺天人包装探讨一下镀铝复合薄膜包装的脱铝和开层现象形成的原因。
镀铝复合薄膜包装的脱铝现象有两种:1、镀铝面上出现片状黑色的斑点。
这是由于真空镀铝层很薄,容易遇湿氧化,从而在薄膜的镀铝面上出现片状黑色斑点。
2、镀铝层消失。
特别是PET镀铝薄膜和PE薄膜的包装,以及PET镀铝薄膜和PE薄膜复合包装袋的封口边缘。
这是因为受潮或中间被胶黏剂溶剂侵蚀,便出现了铝消失,其实也是一种脱铝的现象。
镀铝薄膜的镀铝层受潮或被胶黏剂溶剂的侵蚀脱落,也会导致复合膜开层,当吹胀PE薄膜的内应力收缩回弹时,铝便向里层薄膜转移,那么铝失去薄膜镜平面的依托,也就像消失一样不见了。
如果仔细查看,实际上微量的金属铝还浓缩在内层薄膜上。
所以镀铝复合包装袋的封口边缘一定要压封好,注意镀铝面不要和PE膜粘合,应该将镀铝面与面膜复合,然后将镀铝的薄膜面再和内层的PE薄膜复合。
再就是要注意镀铝薄膜的复合包装袋,不宜作为水煮和蒸煮包装袋。
镀铝复合薄膜包装开层的原因:我国南方生产的BOPP薄膜和CPP真空镀铝薄膜的小食品、瓜子、雪糕等复合包装,受热或揉搓冲击,复合面膜和内层薄膜便开层,而且手还能感到有些黏,同时嗅到股油漆和松香味。
实际嗅到的是BOPP薄膜上印刷的聚酰胺表印油墨和复合使用的BS单组分复合胶的气味。
塑料表印聚酰胺凹版油墨气味较大,色膜光泽性好、爽滑耐磨、不利于复合,因而在复合包装的制作上应减少使用。
另外,BS(人造橡胶)单组分胶粘性的气味较大,自然胶连不易固化,上胶量过大会呈不干胶状,耐温度低、黏结牢度也差,因此受热或揉搓冲击就会起皱、开层,表印油墨和BS单组分胶黏剂制作成的复合包装不宜用于食品包装。
关于镀铝CPP质量问题的分析

关于镀铝CPP质量问题的分析一、关于复合后镀铝膜的镀铝层发生转移问题在镀铝膜使用前用普通胶带检查一下镀铝膜的镀铝层的附着牢度,在镀铝膜/胶带的剥离试验中,镀铝膜的镀铝层如不会剥下,此时的镀铝膜/胶带的剥离强度≥2.0N/15mm;而将镀铝膜与其它的薄膜复合后,经过熟化,复合膜的镀铝面的剥离强度急剧下降,大多会出现镀铝完全或大部份转移现象,此时的镀铝层的剥离强度最好能达到0.6N/l5mm左右,普遍是O.2—0.3N/l5mm,甚至更低。
高质量的真空镀铝膜在加工过程中要先在镀铝基材膜的镀铝面上涂布一定量的底涂胶,提高镀铝层与基材膜的粘结力.从而保证镀铝层牢固,不容易发生脱落:而后,还应当在镀铝层上涂布双组分聚氨酯胶粘剂作顶涂层,以保护镀铝层不被磨损掉。
但目前,国内普遍没有采用上述工艺:在镀铝膜的复合过程中.应当注意以下几方面的问题:1、选用合适的胶粘剂目前,在干式复合中应用最广泛的是普通的双组份聚氨酯胶粘剂,但是,由于普通聚氨酯胶粘剂的相对分子质量较小,分子的活性比较强,很容易渗透入镀铝层内,破坏镀铝层的附着牢度;此外,普通胶粘剂的初粘力一般较高,溶剂释放性差,胶液很容易渗透到镀铝层,并且破坏镀铝层,固化后由于残留溶剂的影响,粘结强度反而会下降,甚至发生镀铝层迁移现象.因此,在复合镀铝膜产品时,如果仍采用这种普通胶粘剂的话,难免会发生各种各样的质量问题,比如复合强度差、镀铝层迁移、“斑点”等故障。
因此,在镀铝膜复合加工过程中最好采用镀铝膜专用胶粘剂,以避免或者减少此类故障的发生率,比如高盟的YH501SL、浙江新东方油墨有限公司的PU一2975等镀铝膜专用胶粘剂,对镀铝膜有极佳的粘结效果。
与普通胶粘剂相比,镀铝膜专用胶粘剂的分子量适中,且分子量分布比较均匀,而且还具有初粘力不太高、溶剂释放性好、涂布性能好等特点,因此,能够很好地保证镀铝膜复合产品的质量。
2、涂胶量要适当涂胶量过小,当然会影响复合牢度,造成复合强度差,容易剥离。
镀铝复合膜的离层现象及解决办法

镀铝复合膜的离层现象及解决办法不同于其它复合膜,采购镀铝膜时应特别注意镀铝复合膜分层现象,镀铝复合膜分层一直以来困扰着包装企业,其中之一是油墨层大部分脱层,这是因为复合产品经过熟化后,油墨层大部分转移道镀铝面,导致剥离强度差。
该现象大多出现在PET印刷膜上,OPP印刷膜上出现的机率相对不多。
深圳镀铝袋、镀铝膜厂家-洁迪,以多年的生产经验汇总影响镀铝复合膜分层的因素如下:1、OPP印刷膜出现这种情况大多与使用的聚酰胺类型的油墨有关,只要改用氯化聚丙烯类的油墨,该现象就会解决;另外OPP表面处理度差也会导致此镀铝膜分层现象。
2、PET印刷膜出现种种情况有三种因素影响:a、与使用的氯化聚丙烯类油墨有一定关系。
解决办法是将上墨量大的油墨改用聚酯、尼龙专用的油墨,上墨量少的可继续使用氯化聚丙烯类油墨就可以解决。
b、与残留溶剂影响有关。
只要降低溶剂残留量,转移现象就会减轻。
c、与PET膜产品质量有关。
有些PET膜,表面处理度都很好,一面能达到45达因,印刷面能达到50达因,表面上看质量很好,如果选用聚酯、尼龙专用的油墨,在实际印刷时,印刷表面印刷的牢度反倒不如印刷在45达因这面。
经过复合后印刷在印刷面的反而转移,而印刷在反面的反而不转移。
其主要原因在于膜的生产厂家过于追求薄膜的表面处理度,在生产处理薄膜时,将薄膜电晕处理过头,对薄膜表面产生了破坏作用。
另外是镀铝膜复合产品剥离强度较差,存在的现象以OPP/VMCPP及OPP/VMPET为多。
刚复合好的产品初剥离较好,但是熟化后剥离强度反而下降了,无法达到标准要求,这种现象在制袋时就能直接检测出来。
具体表现在镀铝层没有“迁移”,印刷油墨也未被拉下。
产生这一种现象,有二种因素影响:1、油墨的影响主要使用了表印改性的聚酰胺类型的油墨,该类型的油墨与聚氨酯胶水相溶性差(结合牢度差)。
2、与镀铝膜本身的质量有关,镀铝膜质量差很容易出现该类质量问题。
而另一种离层现象出现比较少,也是往往不被注意的镀铝膜复合分层现象,一旦出现,往往损失较大。
镀铝膜复合中的转移问题

镀铝膜复合中的转移问题从出现镀铝膜的时候起,镀铝膜复合就一直存在着两个问题:一是外观问题,俗话说的白点;一个是镀铝转移问题。
当然还有其它问题,如起皱、又叫起隧道等。
当然这些问题在一些技术力量较强的大厂,通过材料的正确选择和复合工艺的改进,已经不是问题了。
但仍然有很多中小企业在反反复复出这些问题,究其原因,还是没有真正了解产生这些问题的因素,没能从根源上解决。
下面主要分析镀铝膜转移的主要原因:1、胶水内应力的原因镀铝转移的其中一个原因是双组份粘合剂在高温熟化过程中,主剂与固化剂快速相互交联产生的内应力造成的。
这个原因可以用一个简单的实验证明:如果将复合好的镀铝膜不进熟化室,在常温下熟化(需要数天的时间才能完全固化,没有实际生产意义,仅仅是实验),或在常温下熟化数小时后再进熟化室熟化,镀铝转移现象都会大幅度缓解或消除。
同时,我们能发现,用50%固含量的粘合剂,即低固含量的粘合剂去复合镀铝膜,转移现象也会好很多。
这正是因为低固含量的粘合剂在交联过程中,形成的网状结构没有高固含粘合剂形成的网状结构致密,产生的内应力不那么均匀,不足以密集地均匀作用在镀铝层上,从而缓解或消除了镀铝转移现象。
一般的镀铝专用胶除去主剂与普通粘合剂的主剂略有不同外,固化剂一般也比普通粘合剂要少,这里也有减少或缓解固化过程中粘合剂交联产生内应力的目的,以减少镀铝层的转移。
所以我个人认为“采取高温快速固化的方式来解决镀铝层转移”这个方法是不可行的,反而会适得其反。
现在很多厂家在复合镀铝膜时都采用了水性粘合剂,从水胶的结构特性来看,应该也可以佐证此观点。
2、薄膜拉伸变形的原因镀铝转移的另一种比较明显的现象,一般出在三层复合上,尤其是PET//VMPET//PE这种结构。
一般我们是先复合PET//VMPET。
在这层复合时,镀铝层一般是不转移的。
只有在复合了第三层PE后,镀铝层才发生转移。
通过实验我们发现,在剥离三层复合好的样品时,如果给样品施加一定的张力(就是人为的把样品拉紧),镀铝层也不会转移,而一旦去掉张力,镀铝层就会马上转移。
镀铝转移常见原因分析
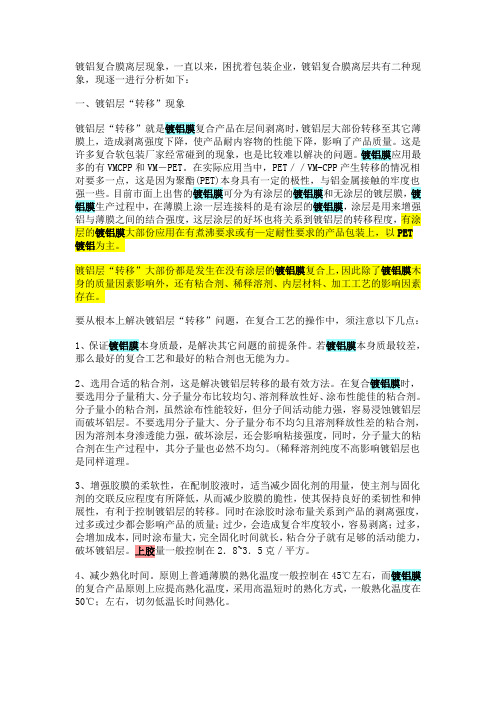
镀铝复合膜离层现象,一直以来,困扰着包装企业,镀铝复合膜离层共有二种现象,现逐一进行分析如下:一、镀铝层“转移”现象镀铝层“转移”就是镀铝膜复合产品在层间剥离时,镀铝层大部份转移至其它薄膜上,造成剥离强度下降,使产品耐内容物的性能下降,影响了产品质量。
这是许多复合软包装厂家经常碰到的现象,也是比较难以解决的问题。
镀铝膜应用最多的有VMCPP和VM-PET。
在实际应用当中,PET//VM-CPP产生转移的情况相对要多一点,这是因为聚酯(PET)本身具有一定的极性,与铝金属接触的牢度也强一些。
目前市面上出售的镀铝膜可分为有涂层的镀铝膜和无涂层的镀层膜,镀铝膜生产过程中,在薄膜上涂一层连接料的是有涂层的镀铝膜,涂层是用来增强铝与薄膜之间的结合强度,这层涂层的好坏也将关系到镀铝层的转移程度,有涂层的镀铝膜大部份应用在有煮沸要求或有—定耐性要求的产品包装上,以PET镀铝为主。
镀铝层“转移”大部份都是发生在没有涂层的镀铝膜复合上,因此除了镀铝膜木身的质量因素影响外,还有粘合剂、稀释溶剂、内层材料、加工工艺的影响因素存在。
要从根本上解决镀铝层“转移”问题,在复合工艺的操作中,须注意以下几点:1、保证镀铝膜本身质最,是解决其它问题的前提条件。
若镀铝膜本身质最较差,那么最好的复合工艺和最好的粘合剂也无能为力。
2、选用合适的粘合剂,这是解决镀铝层转移的最有效方法。
在复合镀铝膜时,要选用分子量稍大、分子量分布比较均匀、溶剂释放性好、涂布性能佳的粘合剂。
分子量小的粘合剂,虽然涂布性能较好,但分子间活动能力强,容易浸蚀镀铝层而破坏铝层。
不要选用分子量大、分子量分布不均匀且溶剂释放性差的粘合剂,因为溶剂本身渗透能力强,破坏涂层,还会影响粘接强度,同时,分子量大的粘合剂在生产过程中,其分子量也必然不均匀。
(稀释溶剂纯度不高影响镀铝层也是同样道理。
3、增强胶膜的柔软性,在配制胶液时,适当减少固化剂的用量,使主剂与固化剂的交联反应程度有所降低,从而减少胶膜的脆性,使其保持良好的柔韧性和伸展性,有利于控制镀铝层的转移。
镀铝工艺学习笔记

镀铝⼯艺学习笔记⼀、概述真空蒸镀⾦属薄膜是在⾼真空(10-4mba以上)条件下,以电阻、⾼频或电⼦束加热使⾦属熔融⽓化,在薄膜基材的表⾯附着⽽形成复合薄膜的⼀种⼯艺。
被镀⾦属材料可以是⾦、银、铜、锌、铬、铝等,其中⽤的最多的是铝。
在塑料薄膜或纸张表⾯镀上⼀层极薄的⾦属铝即成为镀铝薄膜或镀铝纸。
⽤于包装上的真空镀铝薄膜具有以下特点:(1)和铝箔相⽐⼤⼤减少了铝的⽤量,节省了能源和材料,降低了成本。
复合⽤铝箔厚度多为7~9um,⽽镀铝薄膜的铝层厚度约为400?(0.04um)左右,其耗铝量约为铝箔的1/200,且⽣产速度可⾼达700m /min。
(2)具有优良的耐折性和良好的韧性,很少出现针孔和裂⼝,⽆揉曲龟裂现象,对⽓体、⽔蒸汽、⽓味、光线等的阻隔性提⾼。
(3)具有极佳的⾦属光泽,光反射率可达97%;且可以通过涂料处理形成彩⾊膜,其装潢效果是铝箔所不及的。
(4)可采⽤屏蔽或洗脱进⾏部分镀铝,以获得任意图案或透明窗⼝,能看到包装的内容物。
(5)镀铝层导电性能好,能消除静电效应,尤其包装粉末状产品时,不会污染封⼝部分,保证了包装的密封性能。
(6)对印刷、复合等后加⼯具有良好的适应性。
由于以上特点,使镀铝薄膜成为⼀种性能优良、经济美观的新型复合薄膜,在许多⽅⾯已取代了铝箔复合材料。
主要⽤于风味⾷品、⽇⽤品、农产品、药品、化妆品以及⾹烟的包装。
⼆、真空蒸镀原理将卷筒状的待镀薄膜基材装在真空蒸镀机的放卷站上,将薄膜穿过冷却辊(蒸镀辊)卷绕在收卷站上,⽤真空泵抽真空,使蒸镀室中的真空度达到4×10-4mba以上,加热蒸发⾈使⾼纯度的铝丝在1300℃~1400℃的温度下融化并蒸发成⽓态铝。
启动薄膜卷绕系统,当薄膜运⾏速度达到⼀定数值后,打开挡板使⽓态铝微粒在移动的薄膜基材表⾯沉积、冷却即形成⼀层连续⽽光亮的⾦属铝层。
真空镀铝⽰意图见图1。
通过控制⾦属铝的蒸发速度、基材薄膜的移动速度以及蒸镀室内的真空度等来控制镀铝层的厚度,⼀般镀铝层厚度在250~500 ?。
- 1、下载文档前请自行甄别文档内容的完整性,平台不提供额外的编辑、内容补充、找答案等附加服务。
- 2、"仅部分预览"的文档,不可在线预览部分如存在完整性等问题,可反馈申请退款(可完整预览的文档不适用该条件!)。
- 3、如文档侵犯您的权益,请联系客服反馈,我们会尽快为您处理(人工客服工作时间:9:00-18:30)。
镀铝复合膜离层现象,一直以来,困扰着包装企业,镀铝复合膜离层共有二种现象,现逐一进行分析如下:
一、镀铝层“转移”现象
镀铝层“转移”就是镀铝膜复合产品在层间剥离时,镀铝层大部份转移至其它薄膜上,造成剥离强度下降,使产品耐内容物的性能下降,影响了产品质量。
这是许多复合软包装厂家经常碰到的现象,也是比较难以解决的问题。
镀铝膜应用最多的有VMCPP和VM-PET。
在实际应用当中,PET//VM-CPP产生转移的情况相对要多一点,这是因为聚酯(PET)本身具有一定的极性,与铝金属接触的牢度也强一些。
目前市面上出售的镀铝膜可分为有涂层的镀铝膜和无涂层的镀层膜,镀铝膜生产过程中,在薄膜上涂一层连接料的是有涂层的镀铝膜,涂层是用来增强铝与薄膜之间的结合强度,这层涂层的好坏也将关系到镀铝层的转移程度,有涂层的镀铝膜大部份应用在有煮沸要求或有—定耐性要求的产品包装上,以PET
镀铝为主。
镀铝层“转移”大部份都是发生在没有涂层的镀铝膜复合上,因此除了镀铝膜木身的质量因素影响外,还有粘合剂、稀释溶剂、内层材料、加工工艺的影响因素存在。
要从根本上解决镀铝层“转移”问题,在复合工艺的操作中,须注意以下几点:
1、保证镀铝膜本身质最,是解决其它问题的前提条件。
若镀铝膜本身质最较差,那么最好的复合工艺和最好的粘合剂也无能为力。
2、选用合适的粘合剂,这是解决镀铝层转移的最有效方法。
在复合镀铝膜时,要选用分子量稍大、分子量分布比较均匀、溶剂释放性好、涂布性能佳的粘合剂。
分子量小的粘合剂,虽然涂布性能较好,但分子间活动能力强,容易浸蚀镀铝层而破坏铝层。
不要选用分子量大、分子量分布不均匀且溶剂释放性差的粘合剂,因为溶剂本身渗透能力强,破坏涂层,还会影响粘接强度,同时,分子量大的粘合剂在生产过程中,其分子量也必然不均匀。
(稀释溶剂纯度不高影响镀铝层也是同样道理。
3、增强胶膜的柔软性,在配制胶液时,适当减少固化剂的用量,使主剂与固化剂的交联反应程度有所降低,从而减少胶膜的脆性,使其保持良好的柔韧性和伸展性,有利于控制镀铝层的转移。
同时在涂胶时涂布量关系到产品的剥离强度,过多或过少都会影响产品的质量;过少,会造成复合牢度较小,容易剥离;过多,会增加成本,同时涂布量大,完全固化时间就长,粘合分子就有足够的活动能力,破坏镀铝层。
上胶量一般控制在2.8~3.5克/平方。
4、减少熟化时间。
原则上普通薄膜的熟化温度一般控制在45℃左右,而镀铝膜的复合产品原则上应提高熟化温度,采用高温短时的熟化方式,一般熟化温度在50℃;左右,切勿低温长时间熟化。
5、内层薄膜的影响,有些厂家在复合PET//VM-PET//PE时,经常是PET与VM-PET 复合后经过熟化,然后复合PE,但是PET//VM-PET熟化后镀铝层不发生转移,继续复合PE后,镀铝层转移的现象就出现了。
有些厂家是PET与VM-PET复合后不经熟化直接复合PE,也会出现镀铝层转移的现象。
第一种现象的出现与各种薄膜、胶层及烘道温度、熟化时间等有直接关系,第二种现象的出现与内层膜厚薄、及复合加工过程中张力、温度的控制等有直接的关系。
一般三层镀铝复合膜复合时,最好是二层复合好后直接复第三层。
二、油墨层大部份脱层
复合产品经过熟化后,油墨层大部份转移到镀铝面,导致剥离强度差。
该现象大多出现在P ET印刷膜上,OPP印刷膜上出现的几率相对不多。
影响的因素有以下几个方面:
1、OPP印刷膜出现这种情况大多与使用的聚酰胺类型的油墨有关,只要改用氯化聚丙烯类
的油墨该现象就会解决;另外OPP表面处理度差也会导致此现象。
2、PET印刷膜出现这种情况有三种因素影响:
a、与使用的氯化聚丙烯类油墨有一定关系,解决办法是将上墨量大的油墨改用聚酯、尼龙
专用的油墨,上墨量少的可继续使用氯化聚丙烯类油墨就可以解决。
b、与残留溶剂影响有关,只要降低溶剂残留量,转移现象就会减轻。
c、与PET膜产品质量有关,有些PET膜,表面处理度都很好,一面能达到45达因,印刷面能达到50达因,表面上看质量很好,如果选用聚酯、尼龙专用的油墨,在实际印刷时,印刷面印刷的牢度反倒不如印刷在45达因这面,经过复合后印刷在印刷面的反而要转移,而印刷在反面的反而不转移。
其主要原因在于膜的生产厂家过于追求薄膜的表面处理度,在生产处理薄膜时,将薄膜电晕处理过头,对薄膜表面产生了破坏作用。
三、镀铝膜复合产品剥离强度较差
镀铝膜复合产品剥离强度较差,存在的现象以OPP//VMCPP及OPP//VMPET为多,刚复合好的产品初剥离较好,但是熟化后剥离强度反而下降了,无法达到标准要求,这种现象由于在制袋时就能直接检测出来。
具体表现在镀铝层没有“迁移”,印刷油墨也未被拉下。
产生这
一种现象,有二种因素影响:
1、油墨的影响主要使用了表印改性的聚酰胺类型的油墨,该类型的油墨与聚氨酯胶水相溶
性差(结合牢度差)。
2、与镀铝膜本身的质量有关,镀铝膜质量差很容易出现该类质量问题。
而另一种离层现象出现比较少,但往往不被注意的镀铝膜复合离层现象,一旦出现,往往损失较大。
主要表现在BOPP印刷//VM-PET,复合加工后两者初粘力相当好,熟化后剥离强度也较好,但是经过一个星期后或十几天后才能表现出来。
出现这种现象也是镀铝层没有“迁
移”,印刷油墨也未被拉下,但是出现后的损失也是比较严重,当包装袋包装物品后损失就更大了。
那么出现这种现象的主要原因是油墨层内的残留溶剂破坏了胶粘剂的粘接效果,具
体分析如下:
一、对离层产品进行表观分析,离层的现象出现在墨层较厚的部位,墨层薄的地方不太明显,
单白墨印刷处不离层;
二、厂家使用的油墨(色墨)稀释剂配方中,配有异丙醇和丁醇,而用该类溶剂配方的油墨,大多是聚酰胺改性复合油墨,醇类溶剂是真溶剂,这二类醇极易残留,醇类对胶粘剂起一定的破坏作用。
而白墨大多都是氯化聚丙稀复合油墨,不存在此现象;
三、浅色部位因印墨量少,残留溶剂相对较小,该现象也不太明显;
四、使用的粘合剂往往都是一些刚性较强的聚氨酯胶粘剂或快熟化聚氨酯胶粘剂,产品刚性较大,脆性也较大,当残留溶剂较多时对胶粘剂破坏效果最好。
而镀铝膜专用粘合剂熟化后还保留有一定的粘性,分子链较软,残留溶剂较多对它影响不是很大;
五、出现这种现象往往是当环境温度较高、湿度较大时,残留溶剂相对保留较多。
通过分析,出现这种现象往往跟油墨、粘合剂、环境因素有关,因此在油墨的选择上尽量采用氯化聚丙稀型复合油墨,而不建议用改性聚酰胺类复合油墨。
印刷时环境湿度较大时,尽量不要印刷。
选择粘合剂时尽量采用比较柔软的粘合剂或镀铝膜专用的粘合剂,另外也可以适当降低固化剂用量。
只要做到以上几点该现象就会避免。
在实际生产中,要解决剥离强度差的现象是多方面的,首先要保证所选用的复合基材质量,要保证稀释溶剂的质量,再一个就是要选用合适的粘合剂与选用合适的印刷油墨。
其次生产的工艺条件如烘道温度与风量、张力调节、复合辊温度与压力等等因素,也是必须予以关注和重视的。