Electro-Hydraulic Actuators
调速器英文说明书

第三章调速器Chapter Three Governor1 调速器设计原则 Design principle of governorIEEE标准IEC61362-1998标准IEC308《水轮机调速系统试验国际规程》GB/T 9652.1-1997 《水轮机调速器与油压装置技术条件》GB/T 9652.2-1997《水轮机调速器与油压装置试验验收规程》IEEE standardIEC61362-1998 standardIEC308 “International regulations of turbine governing system test”GB/T 9652.1-1997 “Technical specifications of turbine governor and oil pressure device”GB/T 9652.2-1997 “Acceptance regulations of turbine governor and oil pressure device test”DL/T563-95《水轮机电液调节系统及装置技术规程》DL/T496-2001《水轮机电液调节系统及装置调整试验导则》JB/T 56079-2000《大型水轮机调速器与油压装置产品质量分等》其他相关水轮机、调速器标准DL/T563-95 “Turbine electrohydraulic control system and device technical specification”DL/T496-2001 “Turbine electrohydraulic control system and device a djustment test guideline”JB/T 56079-2000 “Large turbine governor and oil pressure product quality grading”Other relevant turbine, governor specifications2 调速器主要技术参数调速器型号: BWST-PLC-80/4.0调速器型式:并联PID调节电液转换型式:无油步进式电液转换器测速方式:残压或齿盘测频误差:≤0.00034%2. Major technical parameter of governorGovernor model number: BWST-PLC-80/4.0Governor type: parallel connection PID adjustmentElectro-hydraulic conversion type: No oil stepping type electro-hydraulic converterSpeed measurement method: residual voltage or fluted discFrequency measurement error: ≤0.00034%扫描周期: 5ms电源: AC 220V±15%和DC 220V±15%(同时供电)永态转差系数: bp=0~10%(调整分辨率为1%)比例增益KP: 0.5~20 s积分增益Ki: 0.05~1.01/s微分增益Kd: 0~10 s暂态转差系数: bt=1~200%(调整分辨率为1%)积分时间常数: Td=1~20 s(调整分辨率为1s)加速度时间常数: Tn=0~5 s(调整分辨率为0.1s)频率给定范围: FG=45~55 Hz(调整分辨率为0.01Hz)频率死区范围: E=0~0.5 Hz(调整分辨率为0.01Hz)Scanning period: 5msPower supply: AC 220V±15% and DC 220V±15%(power supply at the same time)Eternity deviation coefficient: bp=0~10%(Adjustment resolution is 1%)Proportional gain KP: 0.5~20 sIntegral gain Ki: 0.05~1.01/sDifferential gain Kd: 0~10 sTransient deviation coefficient:bt=1~200%(Adjustment resolution is 1%)Integral time constant: Td=1~20 s(Adjustment resolution is 1s)Acceleration time constant: Tn=0~5 s(Adjustment resolution is 0.1s)Frequency given range: FG=45~55 Hz(Adjustment resolution is 0.01Hz)Frequency dead zone range: E=0~0.5 Hz(Adjustment resolution is 0.01Hz)功率死区范围: i=0~5%电气开度限制范围: L=0~100%(调整分辨率≤1%)功率给定范围: P=0~120%(调整分辨率≤1%)Power dead zone range: i=0~5%Electrical opening limit range: L=0~100%(Adjustment resolution≤1%)Power given range: P=0~120%(Adjustment resolution≤1%)人工失灵区:±1.0% (调整分辨率为0.01Hz)转速调节范围±10%;导叶主配置径: 80mm桨叶主配置径: 80mm导叶接力器全开行程时间调整范围为2~15s导叶接力器全关闭行程时间调整范围为2~15s桨叶接力器关闭时间调整范围为12-60S桨叶接力器开启时间调速范围为12-60SArtificial failure zone: ±1.0% (Adjustment resolution is 0.01Hz)Rotating speed governing range: ±10%;Guide vane lord configuration diameter: 80mmPaddle lord configuration diameter: 80mmGuide vane servomotor full open trip time adjustment range: 2~15sGuide vane servomotor full closed trip time adjustment range: 2~15sPaddle servomotor closed time adjustment range: 12~60sPaddle servomotor open time adjustment range: 12~60s3 调速器性能保证调速器所有性能指标均能达到或超过国标GB/T9652-1997大型调速器的技术要求。
电液执行机构演示
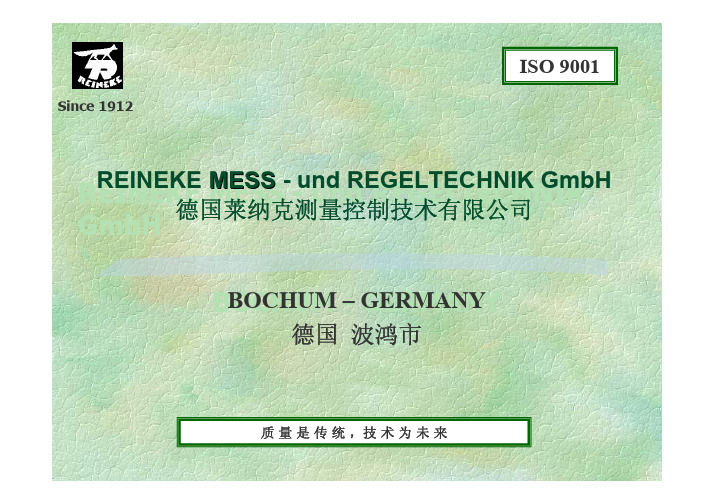
ISO 9001
Since 1912
REINEKE MESS - und REGELTECHNIK GmbH 德国莱纳克测量与控制技术有限公司
Von Ebner-Eschenbach-Str. 5 D-44807 Bochum, Germany Phone:+ 49 234 95 95 0 Fax: + 49 234 95 95 200 E-Mail: reinekefuchs@t-online.de Internet:
应用举例
高炉煤气 清洗系统
Since 1912
应用举例
高炉煤气 清洗系统
Since 1912
应用举例
高炉煤气 清洗系统
Since 1912
高炉煤气 清洗系统 环缝洗涤 器AGE
Since 1912
高炉煤气 清洗系统
水位调节 Water Element
Since 1912
高炉煤气 清洗系统 液压缸
Since 1912
液压 流程图
ISO 9001
Since 1912
电液直行程 执行机构
Since 1912
伺服阀
Since 1912
电液角行程 执行机构 (RKAD)
带伺服阀、连 杆、充氮囊式 蓄能器和手泵
Since 1912
ROTARY ACTUATOR 角行程执行机构
调节控制功能 力矩:100 - 5,000 牛顿米 角度:70° 速度: 3 - 30 秒
Since 1912
EHA 3 SSV 调节阀执行机构
Since 1912
电子压力安全 控制装置 DESY-3
Since 1912
电子压力安全 控制装置 DESY-3
阀门英语术语
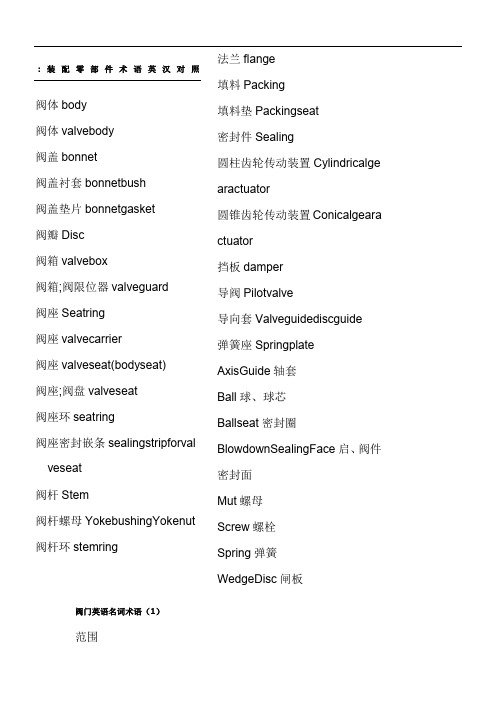
:装配零部件术语英汉对照阀体body阀体valvebody阀盖bonnet阀盖衬套bonnetbush阀盖垫片bonnetgasket阀瓣Disc阀箱valvebox阀箱;阀限位器valveguard阀座Seatring阀座valvecarrier阀座valveseat(bodyseat)阀座;阀盘valveseat阀座环seatring阀座密封嵌条sealingstripforval veseat阀杆Stem阀杆螺母YokebushingYokenut 阀杆环stemring 法兰flange填料Packing填料垫Packingseat密封件Sealing圆柱齿轮传动装置Cylindricalge aractuator圆锥齿轮传动装置Conicalgeara ctuator挡板damper导阀Pilotvalve导向套Valveguidediscguide弹簧座SpringplateAxisGuide轴套Ball球、球芯Ballseat密封圈BlowdownSealingFace启、阀件密封面Mut螺母Screw螺栓Spring弹簧WedgeDisc闸板阀门英语名词术语(1)范围??本标准适用于工业管道(或机器、设备)的通用阀门。
??阀门分类??阀门valve??用来控制管道内介质流动的,具有可动机构的机械产品的总体。
??闸阀gatevalve,slidevalve??启闭件(闸板)由阀杆带动,沿阀座(密封面)作升降运动的阀门。
??截止阀globevalve,stopvalve??启闭式(阀瓣)由阀杆带动,沿阀座(密封面)轴线作升降运动的阀门??节流阀throttlevalve??通过启闭件(阀瓣)改变通路截面积,以调节流量、压力的阀门。
??球阀ballvalve??启闭式(球体)绕垂直于通路的曲线旋转的阀门。
??蝶阀butterflyvalve??启闭式(蝶板)绕固定轴旋转的阀门。
??隔膜阀diaphragmvalve??启闭式(隔膜)由阀杆带动,沿阀杆轴线作升降运动,并将动作机构与介质隔开的阀门。
EHA 电液作动器介绍
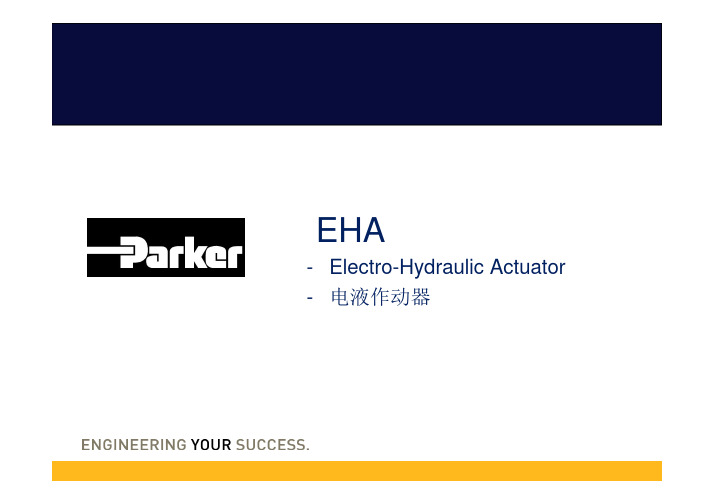
有产品的元件,都是非常简单的事情。
9
Micro-Hydraulic System
Integrated EHA
Seals 密封
Hydraulic Motor 液压马达
Motor type Gear Motor, Cycloid Motor 马达类型 齿轮马达、摆线马达
Stroke length Max. 2000mm, Depending on Torque
-20°C to +150°C
基于磷酸酯的难燃液,及适应
氟橡胶、聚四氟乙烯
于高温环境下的液压油。
10 Micro-Hydraulic System
Integrated EHA
Performance 性能
Actuator 执行器
Cylinder 液压缸
Bore sizes 缸径规格
From 20mm to 125mm 从20mm至125mm
Medical/patient handling 医疗/病人设备
• Stretchers & beds 担架和医疗床 • Ambulance cots 救护床 • Wheelchair access ramps 轮椅进入坡道 • Kneeling handicap vans 下跪式残疾车
Micro-Hydraulic System
Integrated EHA
Features and Benefits 功能和优点
1. Motor 电机 2. Pump 泵 3. Cylinder 缸 4. sensor传感器 5. Mounting type 安装方式6. Valves assembly阀组 7. Reservoir 油箱
飞行模拟机缩写大全

ABCU〔Alternative Breaking Control Unit〕备用刹车掌握组件ACARS〔Aircraft Communication Addressing and Report System〕飞机通信寻址与报告系统ACCU〔Accumulator〕蓄压器AIB〔Audio Interface Box〕音频接口盒ALARM ACKNOWLEDGED 警告确认按钮ADF〔Automatic Direction Finder〕自动方位搜寻器/自动定向机ADIRS〔Air Data Inertial Reference System〕大气数据惯性基准系统ADIRU〔Air Data Inertial Reference Unit〕大气数据惯性基准组件ADR〔Air Data Reference〕大气数据基准AFDS〔Autopilot Flight Director System〕自动驾驶飞行指引系统AFM〔Aircraft Flight Manual〕飞机飞行手册AMPS〔Ampere,AMPS 是复数形式〕安培〔电流单位〕A/P〔Automatic Pilot〕自动驾驶APL〔Airplane〕飞机APO〔Auto Power Off Device〕自动电源关断装置APU〔Auxiliary Power Unit〕关心动力装置ARPT〔Airport〕机场Ashtray /ˈæʃˌtre/烟灰缸ASIC〔Application Specific Integrated Circuit〕专用集成电路A/SKID&N/W STRG 防滞与前轮转弯掌握电门A/T〔Auto Throttle〕自动油门ATD〔ActualTime Departure〕实际离港时间A/W〔AccessWay〕通道AWG〔American Wire Gauge〕美国线规BARO〔Barometric〕大气压力BAT DISCHARGE电瓶放电BC〔Battery Chargers〕电瓶充电器BFEBSCU〔Breaking and Swerve Control Unit〕刹车和转弯掌握组件Captain 机长〔Pilot In Command〕CAN〔Controller Area Network〕掌握器局域网络CB〔Contact Block〕接触块,接点排CB〔CircuitBreaker〕电路跳开关CCD〔Cursor Control Device〕光标掌握装置CDB〔Common Database〕公用数据库CDU〔Control Display Unit〕掌握显示组件CE〔Symbol for European Compliance〕CH〔Channel〕C/L〔Check List〕检查单CMB〔Control Monitor Board〕监视掌握板CPDSP〔Compact PCI Digital Signal Processor〕外设部件的数字信号处理器CPMONCPPDM〔〕CSV〔Comma Separated Values〕逗号分隔值〔文件格式〕CPICPS〔Cycles Per Second〕~次/秒〔频率单位〕CPSIO〔Compact PCI Sound & Audio Input / Output〕外设部件音频/音响输入/输出CPTMCTS〔Commercial Training Solutions〕Current Rating 额定电流CVR〔Cockpit Voice Recorder〕驾驶舱话音记录器C/W〔Control Wheel〕驾驶盘DB〔Daughter Board〕子板DBU〔Digital Buffer Unit〕数字式缓冲装置DECEL〔Decelerate〕减速DEU〔Display Electric Unit〕显示电子装置DFCS〔Digital Flight Control System〕数字式飞行操纵系统DiGIT〔Distributed Graphical Interface Tool〕-a Graphical User Interface (GUI) tool that providesa touch-screen orientated Human MachineInterface (HMI).DMC〔Datapath Micro Computer〕数据通道微处理器DMC〔Digital Motor Controllers〕数字式发动机掌握器DOF〔Degree Of Freedom〕自由度DOME WHITE 顶部白光DPS〔Distributed Power Supply〕分布式供电源Drawbridge 开合桥,活动吊桥DS〔Downstream〕下游DSP〔Display Select Panel〕显示选择面板D-sub〔D-subminiature[adj.超小型的,微型的]〕即VGADual Lock 联动拉手,双锁扣DVI〔Digital Visual Interface〕数字视频接口DU〔Display Unit〕显示组件ECAM〔Electronic Centralized Aircraft Monitoring〕电子集成飞机监控系统〔AIRBUS〕ECB〔Electronic Control Box〕电子掌握盒ECL〔Electric Control Loading〕EEPROM〔Electrically Erasable Programmable Read-Only Memory〕电可擦可编程只读存储器EFB〔Electronic Flight Bag〕电子飞行包EFIS〔Electronic Flight Instrument System〕电子飞行仪表系统EGT〔Exhaust Gas Temperature〕排气温度EDB〔Electronic Load Unit Dynamic Brake〕电子式负荷装置动态制动器EICAS〔Engine Indication and Crew Alerting System〕发动机指示机组警告系统〔Boeing〕EID〔Electronic Load Unit Identification〕电子式负荷装置识别ELAC〔Elevator Aileron Computer〕升降舵副翼计算机EMA〔Electro-Mechanical Actuators〕电动机械作动筒EMC〔Electro-Magnetic Compatibility〕电磁兼容性EMI〔Electro Magnetic Interference〕电磁干扰EMM〔Electro-Mechanical Motion〕电动机械运动EMO〔Emergency Motion Off〕紧急运动关断EMS〔Electro-Mechanical Susceptibility〕电磁敏感性EPO〔Emergency Power Off〕紧急电源关断回路EPR 〔Engine Pressure Ratio〕发动机压力比ETA〔Estimated Time of Arrival〕估量到达时间E/WD〔Engine/Warning Display〕发动机/警告显示FAIL〔Failed/Failure〕失效FBW〔Fly By Wire〕电传操纵FC〔Flight Compartment〕驾驶舱FCC〔Flight Control Computer〕飞行掌握计算机FCOM 〔Flight Crew Operation Manual〕飞行机组操作手册FCU 〔Flight Control Unit〕飞行掌握组件F/D〔Flight Director〕飞行指引仪FDAU〔Flight Data Acquisition Unit〕飞行数据采集组件FEA〔Finite Element Analysis〕有限元分析FFS〔Full Flight Simulator〕全动模拟机Feed Valve进给阀,进水阀,给气阀Flash Light=Torch 手电筒FLSCU〔Fuel Level S Control Unit〕燃油面探测掌握装置Fly-by-wire 电传操纵F/O〔First Officer〕副驾驶FOB〔Fuel Oil Board〕机载燃油量FPGA〔Field Programmable Gate Array〕现场可编程门阵列FPV〔Flight Path Vector〕飞行航迹向量FREQ〔Frequent〕频率FTA〔Fault Tree Analysis〕故障树分析Full Face Mask 全罩式面罩GPIM〔General Purpose Interface Module〕通用接口模块GPM〔Gallon Per Minute〕~加仑/分钟〔流量单位〕GPS 〔Global Positioning System〕〔全球定位系统〕GPU 〔Ground Power Unit〕地面电源装置GPWS〔Ground Proximity Warning System〕地面迫近警告系统GUI〔Graphical User Interface〕图形用户界面Hand Microphone 手持话筒Handset Stowage 手持听筒Hat Holder 帽夹Hat Stowage 帽子存放处Headset〔尤指带麦克风的〕头戴式受话器,耳机HDAC〔Hydraulic Accumulator〕HOST〔Host Computer〕HPU〔Hydraulic Power Unit〕液压工作站Hz〔Hertz〕赫兹IBUTTON〔Information Button〕信息纽扣IDG〔Integral Drive Generator〕整体驱动发电机IDLE 慢车IFB〔Interface Board〕接口板IG〔Image Generator〕图像发生器IGBT〔Insulated Gate Bipolar Transistor〕绝缘栅双极晶体管IN/SEC〔Inches Second〕英寸/秒IOM〔Input / Output Module〕IOS〔Instructor’s Operator〕S t教a t员i o操n纵台IPT〔Integrated Procedures Trainer〕综合程序训练器IR〔Inertial Reference〕惯性基准ITMS〔Integrated Terminal Management System〕终端综合治理系统JAA〔Joint Air Agency〕联合航空当局Jack Panel 插座面板Jet Pump 喷射泵Knots ~海里/小时〔~节〕KRST-复位继电器KSRA-安全继电器LBS 磅LE〔Leading Edge〕〔机翼〕前缘LED〔Light Emitting Diode〕发光二极管LGCIU〔Landing Gear Control and Interface Unit〕起落架掌握接口组件Line Maintenance 日常维护LPM〔Liter Per Minute〕~升/分钟〔流量单位〕LPS〔Lesson Plan Studio〕课程打算工作室LRU〔Line Replaceable Unit〕—An item that is replaced either on the simulator or if not possibleas a shop or bench procedure to an assembly 现场可更换部件LTK Pumps〔Left Tank Pumps〕左油箱燃油泵MCC〔Motion Control Card〕运动掌握卡MCL〔MotionControl Logic〕运动规律掌握MCL〔Motion andControl Loading〕运动和操纵负荷MCDU〔Multipurpose Control & Display Unit〕多功能掌握显示组件MDA〔Motion Drive Algorithm〕运动驱动算法Medical Kit 医药用品MENGD〔Motion Engaged Signal〕运动信号MPIC〔Multi Purpose Interface Card〕多功能接口卡MSB〔Most Significant Bit〕最高有效位MTRS〔备用工作电门,以米和英尺显示高度和MCP 选择高度〕计量电门N/A〔Not Applicable〕不适用Navigation Light 航行灯NDB〔Non Direction Beacon〕无方向信标台NDT〔Navigation Data Tool〕NSA〔Non Simulated Area〕OEM〔Original Equipment Manufacturer〕原始设备制造商PBE〔Protective Breathing Equipment〕防护呼吸面罩PCI〔Peripheral Component Interconnect〕外设部件互连标准PCM〔Power Conditioning Module〕功率调整模块PCU〔Power Control Unit〕动力掌握组件PDU〔Power Distribution Unit〕电力安排单元PEDALS 脚蹬PFC〔Power Factor Correction〕功率因数补偿PLUG-AND-PLAY即插即用Port Wing 左翼Portable OXY Bottle 手提式氧气瓶P/S〔Power Supply〕供电源PSI〔Pounds per Square Inch〕~磅/平方英尺〔压力单位〕〔1BAR=14.5PSI=0.1MPa〕PTC〔Positive Temperature Coefficient〕正温度系数QRH〔Quick Reference Handbook〕快速检查单QTG〔Qualification Test Guide〕品质测试指南RainRepellent Bottle 拨水剂瓶Restraint Kit 座椅安全带设备RTP〔Radio Turning Panel〕RIBBON CABLE 扁平电缆RJ〔Registered Jack〕注册的插座RLS〔Remote Light Sensor〕远距光传感器RM〔Relay Module〕继电器模块RMI〔Rotary Magnetic Indicator〕无线电磁指示器RMS〔Root Mean Square〕均方根R&R〔Removaland Replacement〕拆卸与更换RTH〔Return toHome〕RTP〔Radio Turning Panel〕RTX〔Real-time Extension〕实时系统扩展SAT〔Static Air Temperature〕静温SBC〔Single Board Computer〕单板计算机SD〔System Display〕系统显示Secondary Circuit Breakers 关心电路跳开关SERCOS(Serial real time Communication System)串行实时通信系统SERCOS(Serial real time Communication Specification)串行实时通信协议Signaling Kit 信号盒Smoke Hood 防烟面罩SOV〔Shut Off Valve〕关断活门STA (Scheduled Time Arrival) 打算到达时间Stowage〔船或飞机上〕存放物品处TAT〔Total Air Temperature〕机外温度=〔SAT+动温〕TAXI〔Taxiway〕滑行道TB〔Terminal Block〕接线端子TCAS〔Traffic Collision Avoidance System〕空中防撞系统TE〔Trailing Edge〕后缘TERR〔Terrain〕地形TFC〔Traffic〕交通Thermistor/θɜ:”mɪst / 热敏电阻UL〔Underwriters Laboratory〕美国一家进展安全认证的企业UNLK〔Unlock〕UPS〔Uninterruptible Power Supply〕不连续电源UTC〔Universal Time Coordinated〕国际协调时VAC〔Volts Alternating Current〕沟通电压VDC〔volts Direct Current〕直流电压VGA〔Video Graphics Array/Adapter〕视频图像阵列/适配器VOR〔VHF Omnidirectional Range〕甚高频全向信标WPT 〔Waypoint〕航路点WXR〔Weather Radar〕气象雷达X-Bleed 交输活门XPDR〔Transponder〕应答机YAWDAMPER偏航阻尼器。
压电叠堆执行器迟滞非线性建模与分析

第39卷第4期2017年8月压电与声光PIEZOELECTRICS & 八COUSTOOPTICSVol. 39 No.4Aug.2017文章编号:1004-2474(2017)04-0520-05压电叠堆执行器迟滞非线性建模与分析郭亚子,朱玉川(南京航空航天大学机电学院,江苏南京210016)摘要:压电叠堆执行器输出位移具有迟滞非线性特性,在高精度控制和电静液作动器等应用领域,为实现进一步研究和控制,需要针对该特性进行建模。
该文首先针对压电叠堆执行器的静态特性,采用改进的非对称Bouc- W e n模型建立压电叠堆执行器的准静态模型;其次,为描述其动态位移输出特性,将执行器输出力分为线性模块和滞后模块,根据系统动力学方程建立压电叠堆执行器迟滞非线性动态模型,进行参数辨识、模型仿真与实验研究。
结果表明,在400 H z频率范围内,所建立的模型能够准确描述与预测压电叠堆执行器输出位移的迟滞非线性。
关键词:压电材料;Bouc-W en模型;非对称;迟滞非线性;动态模型中图分类号:T H137 文献标识码:八Modeling and Analysis on Hysteresis Nonlinear Characteristicsof the Piezoelectric Stack ActuatorsGUO Yazi,ZHU Yuchuan(College of Mechanical and Electrical Engineering»Nanjing University of Aeronautics and Astronautics»Nanjing 210016 »China) Abstract:T he output displacem ent of the piezoelectric stack actuator(PSA) exhibits hysteresis nonlinear characteristics. To achieve further research and control,a modeling of the reliable hysteresis nonlinearity is essential,especially in the fields of precision control and electro-hydraulic actuator and etc. Firstly, a quasi-static model is established by using the modified asym m etric Bouc-W en model according to the static characteristic of PSA in this paper. T hen, the output force is divided into the linear portion and the lag portion to descript the dynamic displacem ent output features,and a hysteresis nonlinear dynamic model of the PSA is established according to the system kinetic equation. F inally,the param eter identification,m odel sim ulation and experim ental study have been carried out. T he results show that the model can accurately descript and predict the dynamic characteristics of the PSA at the frequency range of 400 Hz.Key words:piezoelectric m aterial;Bouc-W en m odel; asym m etric;hysteresis nonlinearity;dynamic modelo引百压电叠堆执行器以压电叠堆为驱动元件,具有 结构简单,响应快,输出力大等特点,在航空航天、精 密运动控制等领域获得了长足的发展。
液化烃(球罐)根部防火阀国产化解决方案

液化烃(球罐)根部防火阀国产化解决方案作者:高丽华来源:《今日自动化》2021年第08期[摘要]中石化石家庄炼化分公司新区建设期间,首次遇到国家对液化烃(球罐)根部阀做防火要求,当时设计为进口阀门,费用高,采购周期长,不满足采购需求,为降低采购费用,缩短采购周期,达到液化烃(球罐)根部防火阀设计要求,依据设计技术参数,针对大口径阀门采用国产一体式电液执行机构及阀门,经过自动复位设计,使执行机构具有故障安全性能,并且执行机构采用进口防火罩保护,阀门经过整体防火设计达到了安全完整性等级要求。
当火灾发生时,阀门可以自动快速切断介质,保证罐区安全。
[关键词]罐根阀;球阀;防火罩;电液执行机构[中图分类号]TE65 [文献标志码]A [文章编号]2095–6487(2021)08–0–02[Abstract]During the construction of the new area of our company, we encountered the national fire protection requirements for the root valve of liquefied hydrocarbon (spherical tank) for the first time. At that time, it was designed as an imported valve. The cost was high and the procurement cycle was long. It did not meet the procurement requirements. In order to reduce procurement costs and shorten procurement Cycle, meet the design requirements of the fire damper at the root of liquefied hydrocarbon (spherical tank). Based on the design technical parameters, this article adopts domestic integrated electro-hydraulic actuators and valves for large-diameter valves. After automatic reset design, the actuators have fail-safe performance, and The actuator adopts imported fire protection cover, and the valve meets the requirements of safety integrity level through the overall fire protection design. When a fire occurs, the valve can automatically and quickly cut off the medium to ensure the safety of the tank area.[Keywords]tank root valve;ball valve;fire shield;electro-hydraulic actuator球罐作為一种特殊的压力容器,被广泛用于存储液化石油气、液化天然气、液态丙烯、液态丁烯、液氧、液氮等介质。
Q_KTZ002-2019电动液压执行器试验方法

Q 江苏今创自控科技有限公司企业标准Q/KTZ002-2019电动液压执行器的试验方法 Testing method for Electro-hydraulicactuators2019-10-10 发布 2019-10-14实施江苏今创自控科技有限公司发布目次1范围 (4)2规范性引用文件 (4)3术语与定义 (4)4试验方法 (5)4.1试验条件 (5)4.1.1一般大气条件 (5)4.1.2动力条件 (5)4.2试验的一般规定 (5)4.3试验方法 (6)4.3.1与准确度有关的试验 (6)4.3.2与影响量有关的试验 (7)4.3.3与安全性能相关的试验 (11)4.3.4其它性能项目的试验 (11)4.3.5功能检查 (15)5检验规则 (16)5.1型式试验 (16)5.2例行试验 (16)5.3检验项目 (16)前言为了规范电动液压执行器的生产和管理,保证电动液压执行器的质量,特制订本标准。
本标准主要依据GB/T 1.1-2009《标准化工作导则第1部分:标准的结构和编写》进行编制。
本标准由江苏今创自控科技有限公司提出。
本标准由江苏今创自控科技有限公司起草。
本标准主要起草人:张帅审核:刘进批准:杨维国本标准于2019年10月10日首次发布。
1范围本标准规定了电动液压执行器的型式试验、例行试验方法及判定依据。
本标准适用于各行程的电动液压执行器(以下简称执行器)。
2规范性引用文件下列文件中的条款通过本标准的引用而成为本标准的条款。
凡是注日期的引用文件,其随后所有的修改单(不包括勘误的内容)或修订版均不适用与本标准,仅所注日期的版本适用于本标准。
凡是不注日期的引用文件,其最新版本(包括所有的修改单)适用于本标准。
GB 4208 外壳防护等级(IP代码)(GB 4208-2008,IEC 60529:2001,IDT)GB 4793.1 测量、控制盒实验室用电气设备的安全要求第1部分:通用要求GB/T 15479 工业自动化仪表绝缘电阻绝缘强度技术要求和试验方法GB/T 16511 电气和电子测量设备随机文件(GB/T 16511-1996,idt IEC 61187:1993)GB/T 16842 外壳对人和设备的防护检验用试具(GB/T 16842-2008,IEC 61032:1997,IDT)GB/T 17626.2 电磁兼容试验和测量技术静电放电抗扰度试验GB/T 17626.3 电磁兼容试验和测量技术射频电磁场辐射抗扰度试验GB/T 17626.4 电磁兼容试验和测量技术电快速瞬变脉冲群抗扰度试验GB/T 17626.5 电磁兼容试验和测量技术浪涌(冲击)抗扰度试验GB/T17626.6 电磁兼容试验和测量技术射频场感应的传导骚扰抗扰度GB/T17626.8 电磁兼容试验和测量技术工频磁场抗扰度试验GB/T4824 工业、科学和医疗(ISM)射频设备骚扰特性限值和测量方法JB/T 9329 仪器仪表运输、运输储存基本环境条件及试验方法GB/T 17212 工业过程测量和控制术语和定义3术语与定义GB/T 17212确立的术语与定义适用于本标准。
西门子电液执行器SKB62... SKC62... SKB60 SKC60 说明书

4566Electro-hydraulic actuators for valves with a 20 mm or 40 mm stroke SKB62...SKC62... SKB60SKC60•SK...62...:Operating voltage AC 24 V, control signal DC 0…10 V,4… 20 mA or 0 ... 1000 Ω , with spring-return function•SK...60:as SK...62, but without spring-return function•SK...62U:as SK...62, but UL-approved•SK...62UA:as SK...62U, but with enhanced functions (stroke limit control,sequence control with adjustable start point and operating range,and choice of direction of operation)•Choice of linear or equal-percentage flow characteristic•Position feedback•Stroke calibration•LED status indication•Override control•Manual adjuster and position indicator•Positioning force 2800 N•For direct mounting on valves; no adjustments required•Additional functions with auxiliary switch, stem heater andmechanical stroke inverter (SKB... only)•SK...62U and SK...62UA are UL-approvedCM1N4566ESiemens Building Technologies2/14ApplicationFor the operation of Siemens two-port and three-port valves, types VVF... and VXF...with a 20 mm or 40 mm stroke.• Field of application in accordance with IEC 721-3-3 Class 3K5• Ambient temperatures: −15 ... +55 °C• Temperature of medium in the connected valve: −25 ... +220 °C >220 ... 350 °C: use special extension on valve < 0 °C: type ASZ6.5 stem heater requiredFunctions• Electro-hydraulic actuators; no maintenance required • Pump, pressure cylinder and piston to open valve • Return spring and bypass valve to close valve • Manual adjuster and position indication• SK...62... with spring-return function to DIN 32730•Standard electronics:– Choice of control signal (DC 0 ... 10 V / 4 ... 20 mA / 0 ... 1000 Ω)– Choice of flow characteristic (equal-percentage / linear)– Position feedback – Stroke calibration – LED status indication– Override control via terminal Z •SK...62UA enhanced functions:– Stroke limit control– Sequence control with adjustable starting position and operating range – Choice of direction of operation (direct acting / reverse acting)• Mounting space for auxiliary switch • Stem heater can be fitted if required• Mechanical stroke inverter can be installed if required (SKB... only)•SK...62U and SK...62UA actuators are UL-approvedTypesType Operating Control Spring-return Running time Enhanced function voltage (Control signal)Function Time Opening Closing SKB62SKB62U *Yes15 sSKB60AC 24 VDC 0 ... 10 V,4 ... 20 mAor0 ... 1000 ΩNo --120 s15 sNoSKB62UA *AC 24 V DC 0 ... 10 V,4 ... 20 mAor0 ... 1000 ΩYes15 s120 s15 sStroke limit control Sequence control Signal inversionType Operating Control Spring-return Running time Enhanced function voltage (Control signal)Function Time Opening Closing SKC62SKC62U *Yes20 sSKC60AC 24 VDC 0 ... 10 V,4 ... 20 mAor0 ... 1000 ΩNo --120 s20 sNoSKC62UA *AC 24 VDC 0 ... 10 V,4 ... 20 mAor0 ... 1000 ΩYes20 s120 s20 sStroke limit control Sequence control Signal inversion* UL-approved versionsSKB... with 20 mm stroke Versions withstandard electronics Version withenhanced electronicsSKC... with 40 mm stroke Versions withstandard electronics Version withenhanced electronics3/14Type Description ASC1.6Auxiliary switch ASZ6.5Stem heater AC 24 VASK51Mechanical stroke inverter (SKB... only)OrderingWhen ordering please specify the quantity, product name and type code.Example:1 actuator, type SKC62 and1 auxiliary switch ASC1.6The actuator, valve and accessories are supplied in separate packaging and not assembled prior to delivery.Compatibility The actuators can be driven by all control systems which have an AC 24 V SELV/PELV supply and operate with DC 0 ... 10 V or 4 ... 20 mA signals.The actuators are suitable for operation of the following Siemens two-port and three-port valves with a 20 mm or 40 mm stroke:ValveDN PN Data sheet Two-port valves VV… (control valves or safety shut-off valves):VVF21... (Flange)25 ... 100 mm 6 bar 4310VVF31... (Flange)25 ... 150 mm 10 bar 4320VVF40... (Flange)15 ... 150 mm 16 bar 4330VVF41... (Flange)50 ... 150 mm 16 bar 4340VVF45... (Flange)50 ... 150 mm 16 bar 4345VVF52... (Flange)15 ... 40 mm 25 bar 4373VVF61... (Flange)15 ... 150 mm 40 bar 4382Three-port valves VX... (control valves for mixing and distribution)VXF21... (Flange)25 ... 100 mm 6 bar 4410VXF31... (Flange)25 ... 150 mm 10 bar 4420VXF40... (Flange)15 ... 150 mm 16 bar 4430VXF41... (Flange)15 ... 150 mm 16 bar 4440VXF61... (Flange)15 und 25 mm40 bar4482For admissible differential pressures ∆p max and closing pressures ∆p s , refer to the relevant valve data sheets.Third-party valves with strokes between 6 and 20 mm (SKB...) and 12 ... 40 mm(SKC...) can be motorized, provided they are «closed with the de-energized» fail-safe mechanism and provided that the necessary mechanical coupling is available.We recommend that you contact local Siemens office for the necessary information.AccessoriesDeliveryControllersMounting on linear valvesNoteTechnology4/145/14The override control input (Z) has three modes of operation:The Z-modes shown assume the factory-setting «direct-acting».To determine the stroke positions 0 and 100% in the valve, calibration is required when the valve/actuator are commissioned for the first time. For this purpose, the actuator must be mechanically connected to a Siemens valve (see «Compatibility») and must have a supply voltage of AC 24 V. The calibration procedure can be repeated as often as necessary.Before starting calibration, ensure that the manual adjuster is set to «Automatic»in order to register the actual values.There is a slot on the printed circuit boards of the actuators. To initiate the calibration procedure, the contacts inside this slot must be short-circuited (e.g. with a screwdriver).Automatic calibration proceeds as follows:• Actuator runs to the «0 stroke» position (1), valve closes, green LED flashes.• Actuator then runs to the «100 stroke» position(2), valve opens, green LED flashes.• Measured values are stored.The calibration procedure is finish, and the green LED now glows steadily (normal operation).• The actuator now moves to the position defined by control signal Y or Z (3).0%t100%Stroke123• Throughout this procedure, output U is inactive, i.e. the values only represent actual positions when the green LED stops flashing and remains on continuously.LED Display FunctionActionGreenOn • Normal operationAutomatic operation, no problems Flashing• Stroke calibration in progress Wait until calibration is complete (LED stops flashing)RedOn• Faulty stroke calibration• Internal error Check mountingRe-start stroke calibration(by short-circuiting calibration slot)Replace electronics Flashing • Inner valve jammed Check the valve Off• No power supply •Faulty electronicsCheck mains Replace electronicsOverride control NoteStroke calibrationLED status indicationConnectionterminals Stroke calibrationLED status indicationDIL switchesFunctions see below ONOFFDIL switches Selection ofcontrol signal Selection offlow characteristicON DC 4 ... 20 mA Linear* OFF DC 0 ...10 V Equal percentageConnectionterminalsStroke calibrationRotary switches LOand UPLEDstatus indication6/147/14• With normally-closed valves, «direct-acting» means that with a signal input of 0 V,the valve closes (applies to all Siemens valves listed under «Compatibility» on page 3)• With normally-open valves, «direct-acting» means that with a signal input of 0 V, the valve is open.4 mA 0 Ω20 mA 1000 ΩThe mechanical spring-return function is not affected by the direction of operation selected.*The smallest adjustment is 3 V;control with 0…30 V is only possible via Y.Selecting the direction of operationNoteStroke limit control and sequence control8/14ASC1.6 auxiliary switch –Switching point 0 … 5 % stroke5434561Z 08ASZ6.5 stem heater − For media below 0°C − Mount between valve and actuatorEngineering notesThe actuators must be electrically connected in accordance with local wiring regulations and with the wiring diagram on page 12.Regulations and requirements designed to ensure the safety of people and property must be observed at all times.The ASZ6.5 stem heater has a heat output of 30 VA and is required to keep the valve stem free of ice in the cooling range 0 °C ... −25 °C. In this case, in order to ensure adequate air circulation, the actuator bracket and the valve stem must not be insulated. Physical contact with unprotected hot components can cause burns.Failure to observe the above advice can result in accidents or fire.The admissible temperatures (see «Application» and «Technical data») must be observed.Mounting instructionsPermissible Not permissibleInstructions for fitting the actuator to the valve are bypacked in the actuator packaging.The instructions for accessories are enclosed with the accessories themselves.Accessories Orientation9/14Commissioning notesWhen commissioning the system, check the wiring and functions, and set any auxiliary switches, potentiometers and stroke limit devices as necessary, or check the existing settings.Cylinder with valve stem connector fully retracted → stroke = 0 %Cylinder with valve stem connector fully extended → stroke = 100 %The manual adjuster must be rotated counterclockwise to the end stop.This causes the Siemens valves, types VVF... and VXF... to close (stroke = 0%).For automatic operation, the crank (2) on the manual adjustment knob (1) must be engaged. If not engaged, turn the crank counter-clockwise until the display window (3)neither shows the scale (4) nor the crank engagement bar.124564Z 144564Z 16Engaged crank (2) on the manual adjustment knob (1)Display window with invisible scale dial and crank engagement barFor manual operation, swing out the crank (2) so that the display window (3) becomes visible. By rotating the crank or the manual adjustment knob (1), the display window shows the engagement bar and/or the scale dial with stroke indication.34564Z 154Swung-out crank,display window (3)Display window with scale dial (4)and stroke indicationAutomatic operationManual operation10/14MaintenanceWhen servicing the valve:• Switch OFF the pump and power supply, close the main shut-off valves in the pipework, release pressure in the pipes and allow them to cool down completely. If necessary, disconnect electrical connections from terminals.• The valve must be re-commissioned only with the actuator correctly assembled.DisposalThe actuator includes electrical and electronic components and must not be disposed of as domestic waste.Current local legislation must be observed .WarrantyThe application-related technical data (∆ p max , ∆ p s , leakage, noise levels and service life) is valid for the Siemens actuators only in conjunction with the Siemens valves listed in the section on «Compatibility».Before using these actuators with third-party valves, written approval must be obtained from Siemens Building Technologies. A failure to obtain this approval invalidates any guarantee.Technical data Power supplyOperating voltage (SELV, PELV)AC 24 V –20 % / +30 %Frequency50 or 60 Hz Power consumption SKB62... SKB60 SKC62... SKC6017 VA / 12 W 13 VA / 10 W 28 VA / 20 W 24 VA / 18 WExternal supply cable fuse SKB... SKC...Min. 1 A slow blow,max. 10 A slow blow Min. 1,6 A slow blow,max. 10 A slow blowOperating dataType of control (proportional)DC 0 ... 10 V, DC 4 ... 20 mA or 0 ... 1000 ΩRunning time at 50 Hz SKB... SKC...Opening 120 s 120 s Closing 15 s 20 s Spring-return time (closing) SKB... SKC...15 s20 sNominal stroke SKB... SKC...20 mm40 mm Positioning force 2800 NFlow characteristicLinear / equal percentage can be selected ** in conjunction with valves listed under «Compatibility» on page 3Signal inputs Terminal YVoltageInput impedance CurrentInput impedance Signal resolution Hysteresis DC 0 ... 10 V 100 kΩDC 4 ... 20 mA 240 Ω<1 %1 %Terminal ZResistance0 ... 1000 ΩOverride control functionsZ not connectedZ connected directly to GZ connected directly to G0Z connected to M via 0 ... 1000 ΩNo function (priority at Terminal Y) Max. stroke 100 %Min. stroke 0 %Linear / equal percentageSignal outputs Terminal UVoltageLoad impedance CurrentLoad impedance DC 0 ... 9.8 V ±2 %>500 ΩDC 4 ... 19.6 mA ±2 % <500 ΩGeneralambient conditions Maximum admissible temperature ofmedium in the connected valve:≤220 °C OperationEnvironmental conditionsTemperatureHumidityTo IEC 721-3-3Class 3K5–15 ... +50 °C5 ... 95 % rh TransportEnvironmental conditionsTemperatureHumidityTo IEC 721-3-2Class 2K3–30 ... +65 °C<95 % rh StorageEnvironmental conditionsTemperatureHumidityTo IEC 721-3-1Class 1K3–15 ... +50 °C5 ... 95 % rhIndustry standards Meets the requirements for CE marking inEMC DirectiveLow Voltage Directive 89/336/EEC 73/23/EECElectromagnetic compatibilityEmitted interference Interference immunity EN 61000-6-3 Residential EN 61000-6-2 IndustrialProduct standards for automaticelectric controls EN 60 730-2-14C-tick N474Protection standard IP54 to EN 60529Protection class III to EN 60730UL approval UL 873 Dimensions See «Dimensions»Weight SKB...SKC...ASK51 stroke inverter8,60 kg(including packaging) 10,00 kg(including packaging) 1,10 kg(including packaging)Materials Actuator housing and bracketHousing box and manual adjuster Die-cast aluminum PlasticCable glands SK...62, SK (60)SK...62U, SK...62UA Pg 11 (4 x)Pg 16 (4 x)11/1412/14SK...62UA enhanced functions Direction of operationDirect acting / reverse actingDC 0 ... 10 V / DC 10 ... 0 V DC 4 ... 20 mA / DC 20 ... 4 mA 0 ... 1000 Ω / 1000 ... 0 ΩStroke limit control Range of lower limit Range of upper limit 0 ... 45 % adjustable 100 ... 55 % adjustable Sequence controlTerminal YStarting point of sequence Operating range of sequence0 ... 15 V adjustable 3 ... 15 V adjustableAccessoriesASC1.6 auxiliary switch Switching capacity of auxiliary switch AC 24 V, 10 mA ... 4 (2) A ASZ6.5 stem heaterOperating voltagePower consumption (heat output)AC 24 V ±20 %30 VAConnection diagramA C 24 VB1SensorF1Temperature limiter N1Controller Y1ActuatorU ZG0G Y M Operating voltage AC 24 V System neutral (SN)Operating voltage AC 24 V System potential (SP)Control signal DC 0 ... 10 (30) V or DC 4 ... 20 mA Measuring neutral (= G0)Position indication DC 0 ... 10 V or DC 4 ... 20 mA Override input (functions see page 5)c134501804Connection terminalsASC1.6auxiliary switch13/14DimensionsAll dimensions in mm*Height of actuator from valve plate without stroke inverter ASK51 = 300 mm Height of actuator from valve plate with stroke inverter ASK51 = 357 mm **The hole diameter on the SK...62U... actuators corresponds to the Pg16 gland.s =>100 mm Minimum clearance from ceiling or wall for mounting,ss =>200 mm connection, operation, maintenance etc.20*109,535444456,5108∅∅4561M 02* Maximum stroke = 20 mmASK51 stroke inverter14/14© 2002 Siemens Building Technologies Ltd.Subject to alteration。
Rotork Skilmatic电动弹簧回弹执行器说明书

GENERAL DESCRIPTIONRotork Skilmatic quarter turn actuators are compact and robust electrically operated spring return devices,providing a 90degree travel,for two position applications,on all types of Ball,Butterfly,Plug Valves and Dampers.The Model SB301/302Actuators are the general purpose two position versions of the Skilmatic range,with torque outputs of 29Nm (256in lbs)to 65Nm (575in lbs)for the Model SB301and 140Nm (1239in lbs)to 480Nm (4248in lbs)for the Model SB302.The Model SB301/2have been specifically designed for Fail Safe valve isolation and damper control.The actuators combine the simplicity of electrical operation with the power of hydraulics and the reliability of spring-powered fail safe action.The integral fully sealed Skilmatic Electro-hydraulic pump system provides the power to operate the scotch yoke spring return drive.Offering the most reliable means of positioning the valve or damper in a safe condition.Available with spring return clockwise or anti-clockwise for fail-safe to close or open on power failure.The Model SB301is supplied as a compact single oscillating Electro-hydraulic pump system.The Model SB302provides a dual redundant internal oscillating pump system.All models are supplied with two volt free end of stroke limit switch.Manual gearbox overrides are also available and the option of biodegradable oil for food and water applications.The actuators are available with thermal jackets to meet high temperature applications such as smoke and fire damper in tunnel.Weatherproof to IP67.For modulating control applications see product specification sheet Model SB406.For Hazardous area Zone 1/Division 1application see product specification sheet Model SB-1Q and SB-2Q.PRODUCT SPECIFICATIONSkilmaticGENERAL PURPOSE ¼TURN FAIL-SAFE ELECTRIC ACTUATOR ON /OFF CONTROL MODEL SB301/302FEATURES▪Electrically operated,spring return –fail-safe.▪Compact and robust.▪Minimal moving parts no motors or gears.▪Model SB301compact,single internal Oscillating pump.▪Model SB302Dual redundant internal Oscillating pumps.▪Operates from a 230or 110/120V.ac 50/60Hz Supply.▪Minimal power consumption.Issue 04/14ROTORK FLUID SYSTEMS REGINA HOUSERING ROAD,BRAMLEY LEEDS LS134ET UNITED KINGDOMTelephone:+44(0)1132057278Fax:+44(0)1132363310ROTORK FLUID SYSTEMS 04/14SPECIFICATIONEnclosure:Splash and dust proof to IP67Power unit:Aluminium Al Si 12,DIN1725Actuator Body:-Anodised Aluminium Piston:AluminiumDrive shaft:Zinc-plated stainless steelSprings:Corrosion protected springs steel Paint Finish:2-pack epoxy red.Weight:See dimensional tableOperating Temperature:-250C to 750C (-13to 1670F),Optional -Thermal jacket for Low -400C,and High 2500C /4000C (for over two hours )applications.Mounting:Vertical or horizontal (See Instruction Manual)Stroke:-00to 900adjustment +/-30Action:Spring return clockwise or anti-clockwise.Failure Mode:Fail-safe in the direction of the spring orFail in last position.Maximum internal working pressure:-12Bar Torque/Stroke Speed:See order information.Hydraulic Fluid:10cSt hydraulic fluid ,15cSt biodegradable fluidor silicon fluid for low temperatures.Electrical Supply:230V a.c.110V/120V a.c,50/60Hz ±10%Power Consumption:Model SB301@230Vac 207VA(106watts)nominal,@110Vac -264VA(135watts)nominal reducing to 15VA(6watts)in balanced state.Model SB302-374VA(190watts),reducing to 15VA(6watts)in balanced state.When quick closure valve part number ESD1is required add 23VA to assembly.Cable Entries:-Two treaded M20optional ½”NPT adaptor Duty Rating:80%rated Optional:Limit Switches:Two spare volt free switch rated at 5Aat 230VacManual override:Manual override gearbox.For modulating control applications see product specification SB406.ORDERING INFORMATION AND MODEL CODEKEY MODEL CODE SB302-A6-D1-MOTable 1-Supply Voltage Table 2-Actuator Torque Table 3-AccessoriesKEY MODEL CODE Code DescriptionSB3011/4Turn Fail –safe electro-hydraulic.actuator with torque output type A,B or C Table 2SB3021/4Turn Fail –safe electro-hydraulic actuator with torque output type D,E,F or G Table 2TABLE 1-SUPPLY VOLTAGECode Description A6230V a.c ±10%50Hz B6110/120V a.c ±10%50/60HzTABLE 3-ACCESSORIES Code Description MO TJ NPTBIO SI ESD1BRGeared manual overrideHigh temperatureThermalJacket1/2“NPT cable entryBio-degradable oil (for waterand food industries)20cSt Silicone oil.For low temperature applications -400C Quick closure Manifold solenoid (see stroke speeds in table 2)Valve mounting kittosuitspecific valveTABLE 2-ACTUATOR TORQUECodeTorque NmStroke speed (see table3)Spring ReturnHydraulic strokeSpring returnHydSpring DirectionClockwiseanti-clockwisestartmidfinishstartmidfinishStdESD301B1BA16930374321291631C1CA195426093406530 5.5 1.5302C1CA195426093406515 5.5 1.5D1DA11909512018010014030102E1EA129014017032517024050154F1FA172036050050026038095296G1GA162030035063034048095296NOTES1.All torques are in Nm.For torque in lbs in x 8.85.2.Stroke speeds are typical for actuators with no load at 20o C Tolerance ±10%.Rotork SKILmatic reserve the right to change the specifications without prior notice.。
液压控制系统(常同立编著,清华大学出版社)PPT课件

12
应用案例 5——机器动物
高功率体积比和结构紧凑
13
应用案例 5——机器动物
14
应用案例 5——机器动物
15
应用案例 6——两足机器人
高功率体积比和结构紧凑
16
应用案例 6 —— 两足机器人
17
小结
液压控制技术是一门机电液一体化新技术,它是自动控制技术的 一个重要分支。液压控制技术包括开环控制和闭环控制两类,其中液 压闭环控制较为复杂。
29
第2章 参考文献
[1] Katsuhiko Ogata. System dynamics. 北京:机械工业出版社. 2004.3 [2] 吴重光. 仿真技术. 北京:化学工业出版社. 2000.5. [3] Katsuhiko Ogata. Modern control engineering. Prentice Hall, 2010 [4] John J. D’Azzo and Constantine H. Houpis, Stuart N. Sheldon. Linear Control System Analysis and Design with Matlab. New York: Marceld Dekker, Inc. 2003 [5] 王广雄,何朕. 控制系统设计. 北京:清华大学出版社, 2008.3. [6] 高钟毓等. 机电控制工程. 北京:清华大学出版社, 2011.8. [7] www. [8] Roland S. Burns. Advanced Control Enginineering. Oxord: Butterworth-Heinemann. 2001. [9] J.R. Leigh. Control theory. London: The institution of engineering and technology. 2004. [10] Isaac Horowitz. Some ideas for QFT research. International Journal of Robust and Nonlinear Control, 2003, 13: 599-605. [11] 刘兵,冯纯伯. 基于双重准则的二自由度预测控制——连续情况. 自动化学报. 1998,24(6):721-726. [12] 冯勇等. 现代计算机控制系统. 哈尔滨:哈尔滨工业大学出版社, 1998.7. [13] D. M. Auslander, J. R. Ridgely, J. D. Ringgenberg. Control software for mechanical systems: object-oriented design in a real-time world. Pearson Education, Inc. 2002.
Remote Control RC200 Pneumatic Actuator说明书
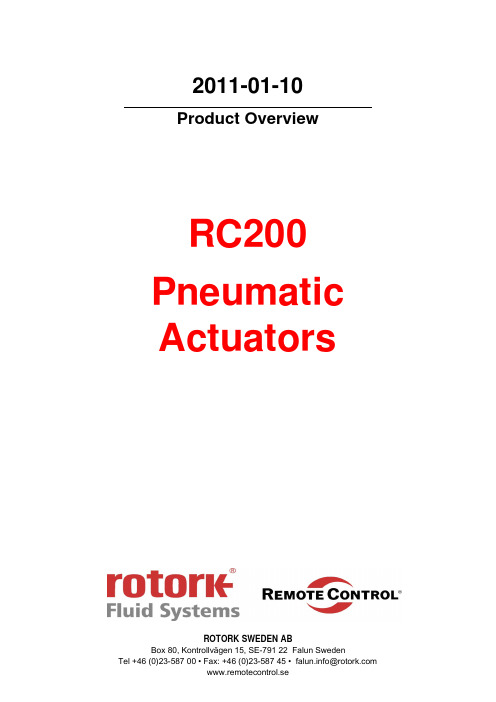
Product Overviewwww.remotecontrol.se2011-01-10Pneumatic RC200ActuatorsROTORK SWEDEN ABBox 80, Kontrollvägen 15, SE-791 22 Falun SwedenTel+46(0)23-58700•Fax:+46(0)23-58745•*********************Example:RC210-SRBMF050HESURFACE TREATMENTBL=BlueE=EpoxyR=Red (Standard, not marked)SPECIAL DESIGNH=HydraulicsHT=High tempAC=Fully adjustable in closed positionAO=Fully adjustable in open positionLT=Low tempPD=Piston in ductile ironQ=Quick operatingS=Stainless shaft + screw + ciclipWH=Water hydraulicsSPRING PRESSURE020-100=20psi - 100psiSPRING FUNCTIONF=Spring opens (Fail open)MANUAL OVERRIDEM=M1M2=M2SHAFT TYPEA=A-shaft (Standard, not marked)B=B-shaftC=Key grooveFUNCTIONDA=Double actingSR=Spring returnSIZE10 - 100MODELRC=Terminated model RC05-80RC2=RC200 seriesRCA=Stainless steel actuatorRCC=Steel actuatorRCD=DIN actuatorRCE=Electro-hydraulic actuatorRCI=RCI actuatorRCT=Actuator with reinforced corrosion protectionRCR=180 - Degree actuatorRCG=Cast steel actuator2Product OverviewConversion TableFor RC Actuators2011-01-10 RC210 -SR B M F050H EPageConversion Table 2 Contents 3 Torque figures4 RC200 Actuator acc to DIN/ISO standard5 RC200 Actuators according to DIN/ISO standard with manual override M16 RCT200 Actuator Reinforced corrosion protection with stainless outer parts7 RCT200 Actuators Reinforced corrosion protection and manual override unit M18 RC 88 / RCT88 Actuators9 Spare Parts10 Limit switches RCE4L 11 Limit switches IND12 Limit switches Explosion proof design 13 Positioners 14 RCC-Firesafe15 Solenoid valves Namur 16 Solenoid valves Accessories 17 Mounting kits Stainless steel18 Mounting kits / Reducers Painted carbon steel19 Mounting kits for 3-piece ball valves without mounting flange 20 Telephone E-mail213Product OverviewContents2011-01-10Double acting actuators DA210-DA220-DA 230-DA 240-DA 250-DA 260-DA 265-DA 270-DA 280-DA 88-DA90-DA100-DA0° = Closed positionConversion table Torque1 Nm = 0,102 kpm = 8,85 Ib.in.1 kpm = 9,81 Nm = 86,8 Ib.in.1 Ib.in = 0,113 Nm = 0,0115 kpm Pressure1 Mpa = 10 bar = 10,2 kp/cm² = 145 psi47400357054001525072001135038001900274076003800548012966099211890940136045022532091046065014572105290145210381927763854Product OverviewTorque figuresSizeTorque in Nm at valve position Air pressure 0,6 Mpa (6 bar / 87 psi)0°50°90°2011-01-10CE marking according to ATEX Directive 94/9/EC (class II 2GD)RC270-RC88 CE marking according to PED 97/23/EG module A RC200-DA ModelOrder No Torque (Nm)RC210-DA F05-1411325238RC220-DA F05-1412310176RC230-DA F07-17133095145RC240-DA F10-22143096290RC250-DA F10-22153316450RC260-DA F12-27163245910RC265-DA F12-271650071231RC270-DA F14-361732141890RC280-DA F16-461832553800RC200-SR (spring pressure 6 bar = 87 psi)Model Order No Torque (Nm)RC210-SR087 F05-1411325720/12RC220-SR087 F05-1412310641/25RC230-SR087 F07-17 13309878/47RC240-SR087 F10-22 143099158/96RC250-SR087 F10-22 153319245/150RC260-SR087 F12-27 163248500/305RC265-SR087 F12-27165008673/412RC270-SR087 F14-361732181030/620RC280-SR087 F16-461832592080/1260RC210-SRF087 F05-1411325822/15RC220-SRF087 F05-1412310844/30RC230-SRF087 F07-17 13310283/57RC240-SRF087 F10-22 143104170/115RC250-SRF087 F10-22 153323260/180RC260-SRF087 F12-27 163252530/360RC265-SRF087 F12-27 165020696/416RC270-SRF087 F14-361732221090/750RC280-SRF087 F16-461832632230/1510SR = Spring closes SRF = Spring opensOther spring combinations (4 bar = 60 psi and 7 bar = 100 psi) on request.Torque is given at 0° opening / 0° closing.5Product OverviewRC200 Actuatoracc to DIN/ISO standard2011-01-10RC200-DAM with manual override M1ModelArticle No Torque (Nm)RC210-DAM F05-1411325438RC220-DAM F05-1412310276RC230-DAM F07-17133112145RC240-DAM F10-22 143108290RC250-DAM F10-22153333450RC260-DAM F12-27 163247910RC265-DAM F12-271650181231RC270-DAM F14-361732161890RC280-DAM F16-461832583800RC200-SRM with manual override M1 (spring pressure 6 bar = 87 psi)Model Article No Torque (Nm)RC210-SRM087 F05-1411326420/12RC220-SRM087 F05-1412311341/25RC230-SRM087 F07-1713310478/47RC240-SRM087 F10-22 143106158/96RC250-SRM087 F10-22 153325245/150RC260-SRM087 F12-27 163254500/305RC265-SRM087 F12-27165012673/412RC270-SRM087 F14-361732241030/620RC280-SRM087 F16-461832662080/1260RC210-SRMF087 F05-1411328622/15RC220-SRMF087 F05-1412315044/30RC230-SRMF087 F07-17 13310583/57RC240-SRMF087 F10-22 143107170/115RC250-SRMF087 F10-22 153326260/180RC260-SRMF087 F12-27 163256530/360RC265-SRMF087 F12-27165021696/416RC270-SRMF087 F14-361732251090/750RC280-SRMF087 F16-461832672230/1510Bracket for locking the handwheel with padlock Model Article No Bracket for locking RC210-220259226Bracket for locking RC230-240259227Bracket for locking RC250-260259228Bracket for locking RC265259350Bracket for locking RC270-280259327SRM = Spring closes SRMF = Spring opensOther spring combinations (4 bar = 60 psi and 7 bar = 100 psi) on request.Torque is given at 0° opening / 0° closing.6Product OverviewRC200 Actuatorsaccording to DIN/ISO standard with manual override M1RC270-RC88 CE marking according to PED 97/23/EG module ACE marking according to ATEX Directive 94/9/EC (class II 2GD)2011-01-10RCT200-DA. Reinforced corrosion protection Model Order No Torque (Nm)RCT210-DA F05-1411325638RCT220-DA F05-1412310476RCT230-DA F07-17 133111145RCT240-DA F10-22 143114290RCT250-DA F10-22 153332450RCT260-DA F12-27 163258910RCT265-DA F12-27 1652301231RCT270-DA F14-361732261890RCT280-DA F16-461832683800RCT200-SR. Reinforced corrosion protection (spring pressure 6 bar = 87 psi)Model Order No Torque (Nm)RCT210-SR087 F05-1411326020/12RCT220-SR087 F05-1412310941/25RCT230-SR087 F07-17 13310778/47RCT240-SR087 F10-22 143110158/96RCT250-SR087 F10-22 153328245/150RCT260-SR087 F12-27 163261500/305RCT265-SR087 F12-27 165232673/412RCT270-SR087 F14-361732291030/620RCT280-SR087 F16-461832712080/1260RCT210-SRF087 F05-1411328422/15RCT220-SRF087 F05-1412311044/30RCT230-SRF087 F07-17 13310883/57RCT240-SRF087 F10-22 143111170/115RCT250-SRF087 F10-22 153329260/180RCT260-SRF087 F12-27 163274530/360RCT265-SRF087 F12-27 165265696/416RCT270-SRF087 F14-361732441090/750RCT280-SRF087 F16-461832862230/1510SR = Spring closes SRF = Spring opensOther spring combinations (4 bar = 60 psi and 7 bar = 100 psi) on request.Torque is given at 0° opening / 0° closing.7Product OverviewRCT200 ActuatorReinforced corrosion protectionwith stainless outer partsCE marking according to ATEX Directive 94/9/EC (class II 2GD)RC270-RC88 CE marking according to PED 97/23/EG module A 2011-01-10RCT200-DAM. Reinforced corrosion protection. With manual override M1.Model Article No Torque (Nm)RCT210-DAM F05-1411325538RCT220-DAM F05-1412310376RCT230-DAM F07-17133113145RCT240-DAM F10-22143115290RCT250-DAM F10-22153334450RCT260-DAM F12-27163259910RCT265-DAM F12-271652311231RCT270-DAM F14-361732271890RCT280-DAM F16-461832693800RCT200-SRM. Reinforced corrosion protection. With manual override M1 (spring pressure 6 bar = 87 psi).Model Article No Torque (Nm)RCT210-SRM087F05-1411326320/12RCT220-SRM087F05-1412311241/25RCT230-SRM087 F07-1713310978/47RCT240-SRM087 F10-22143112158/96RCT250-SRM087 F10-22153330245/150RCT260-SRM087 F12-27163262500/305RCT265-SRM087 F12-27165233673/412RCT270-SRM087F14-361732301030/620RCT280-SRM087F16-461832722080/1260RCT210-SRMF087F05-1411328322/15RCT220-SRMF087F05-1412311744/30RCT230-SRMF087 F07-1713311083/57RCT240-SRMF087 F10-22143113170/115RCT250-SRMF087 F10-22153331260/180RCT260-SRMF087 F12-27163263530/360RCT265-SRMF087 F12-27165266696/416RCT270-SRMF087F14-361732311090/750RCT280-SRMF087F16-461832742230/1510SRM = Spring closes SRMF = Spring opensOther spring combinations (4 bar = 60 psi and 7 bar = 100 psi) on request.Torque is given at 0° opening / 0° closing.8Product OverviewRCT200 ActuatorsReinforced corrosion protection and manual override unit M1Prices for RCT200 actuators with alternative shaftsCE marking according to ATEX Directive 94/9/EC (class II 2GD)RC270-RC88 CE marking according to PED 97/23/EG module A2011-01-10CE marking according to ATEX Directive 94/9/EC (class II 2GD) RC270-RC88 CE marking according to PED 97/23/EG module ARC88-DAModel Order No Torque (Nm) RC88-DA 1837167600RC88-SR (spring pressure 6 bar = 87 psi)Model Order No Torque (Nm) RC88-SR087 1837224160/2520RC88-SRF0871837234470/3020RCT88-DA Actuator with reinforced corrosion protectionModelOrder No Torque (Nm)RCT88-DA1837307600RCT88-SR Actuator with reinforced corrosion protection (6 bar = 87 psi)Model Order No Torque (Nm)RCT88-SR087 1837314160/2520RCT88-SRF087 1837324470/3020Manual override Gearbox complete MountedModel Order NoGearbox Complete181742SR= Spring closesSRF= Spring opensOther spring combinations (4 bar = 60 psi and 7 bar = 100 psi) on request.Torque is given at 0° opening / 0° closing.9Product OverviewRC 88 / RCT88Actuators2011-01-10Repair kit for RC200ModelArticle No Seal kit for RC210-220123200Seal kit for RC230-240143190Seal kit for RC250-260163126Seal kit for RC265165006Seal kit for RC270-280183099Seal kit for RC88183087Seal kit for RC88-Single Shaft 183817Seal kit for RCG90193014Seal kit for RCG100203014Complete piston ModelArticle No PI1020 for RC210-220122343PI3040 for RC230-240142370PI5060 for RC250-260162342PI265 for RC265165115PI7088 for RC270-280, RC88182108PI90100 for RCG90-100202027Complete spring pack 87 psi (standard)Model Article No SP21020-087 for RC210-220122320SP23040-087 for RC230-240142341SP25060-087 for RC250-260162352SP265-087 for RC265165056SP27080-087 for RC270-280182313SP88-087 for RC88182041SPG90100-080 for RCG90-100202025Other combinations on plete Endcaps (standard)ModelArticle No EP2 10/BLACK for RC210121157EP2 1020-W/BLACK for RC210-220121154EP2 30/BLACK for RC230132128EP2 3040-W/BLACK for RC230-240142387EP2 50/BLACK for RC250152294EP2 5060-W/BLACK for RC250-260162407EP2 65/BLACK for RC265162378EP2 70/BLACK for RC270172017EP2 7080-W/BLACK for RC270-280,88182016EPG 90/BLACK for RCG90192003EPG 90100/BLACK for RCG90-100202019Note! 2 pistons are required for sizes 20, 40, 60, 80 and 100; 4 pistons are required for size 88!10Product OverviewSpare Parts2011-01-10RCE4L excluding mounting details and mounting Switch box IP67Order NoE4L-MEK 258240E4L-MEKTU Reinforced corrosion protection258237E4LS-MEKAISI 316 Stainless steel 258277Mounting kit RCE4L For actuator Order No RC210Namur stainless 257837RC220-265Namur stainless 257838RC270-280, RC88Namur stainless257806RCG90-100Namur stainless257863For mounting kits E4L for RC30-60 manufactured before December 31, 1996,please contact factory.Mounting RCE4L ActuatorsOrder No RC210-280, RC88, RCG90-100257950ArticleOrder No Wiring E4/solenoid valve 261791RCE4L (258240) mounted on actuator For actuator Order No E4L- on RC210258241E4L- on RC220-265258242E4L- on RC270-280, RC88258243E4L- on RCG90-100258244Mounting kit RCE4L for hand-operated valves ArticleOrder NoFor hand-operated valve 257705Rigging costper valve size and order occasion549900Mounting RCE4L on hand-operated valve ActuatorsOrder No Mounting cost RCE4L on valve25795211Product OverviewLimit switchesRCE4LOther will be offered on request.2011-01-10RC200-IND inductive sensors ModelArticle No IN5224,2-wire PNP/NPN with socket25763610-36VDC, IP67 (add PNP/NPN conn. cable)IN5290,2-wire PNP/NPN with sealed cable 25772710-36VDC, IP67IN5225,3-wire PNP with socket25759610-36VDC, IP67 (add PNP/NPN conn. cable)IN5251,3-wire PNP with sealed cable25763710-36VDC, IP67NN5008,2-wire NAMUR with socket25763910-36VDC, IP67 (add connection cable Namur)NN5009,2-wire NAMUR with sealed cable257638IP67NN5013,2-wire NAMUR with BS-200-K socket257658IP65 (add connection socket)IN0108,2-wire universal sensor with BS-200-K socket 25772620-250VAC/DC, IP65 (add connection socket)IN0109,2-wire universal sensor with shielded RTF-cable 25772520-250VAC/DC, IP67IN0110,2-wire universal sensor with PVC-cable 25772420-250VAC/DC, IP67Connecting cable, connecting socket ArticleArticle No Connecting cable PNP/NPN ( 2 meter cable angular E10900 )257904Connecting cable NAMUR ( 2 meter cable E10355 )257645Connecting socket E17014, angular, PTB/PG9 for BS-200-K socket257660Mounting kits IND Article Article No INDMS210-265257601INDMS270-280. RC88257641INDMS90-100257693For mounting kits IND for RC 30-60 manufactured before December 31, 1996, please contact factory.MountingArticleArticle No MOUNTING IND/DON 257951Mounting kits IND for hand valves ArticleArticle No MKIND/ FOR VALVE 257700Rigging costper valve size and order occasion 549900Mounting cost IND on valve25795312Product OverviewLimit switchesIND2011-01-101990 Explosion proof switch box excluding mounting and mounting kit Switch box Order No 1990 EExdIICT6 IP66258063Mounting kit 1990 Box TypeOrder No MK1990RC210257729MK1990RC220-265257730MK1990RC270-280, 88257731MK1990RCG90-100257719Mounting 1990 Box ActuatorOrder No RC210-280, RC88, RCG90-100257732Mounting kits RC1990 for hand valves ArticleArticle No MK1990/ FOR VALVE 258807Rigging costper valve size and order occasion 549900Mounting cost RC1990 on valve 257953Cable glands M20 EExd Cable diameterOrder No M20 6,1 -11,6 mm EExd 257755M20 6,5 -13,9 mm EExd 257756M20 Stopping plugg EExd257757Nemko 03 ATEX 1435 0470 II 2 G D EExd IIC T4, T5 or T6For use in potentially explosive atmospheres.Directive conformity: 94/9/ECStandard conformity: CENELEC EN 50014:1997+A1: 1999+A2 CENELEC EN 50018:2000CENELEC EN 50281-1-1:1998NOTE:For a valid Ex classification, it is necessary to supply the 1990 box with Exd classified cable gland or plug.13Product OverviewLimit switchesExplosion proof designOther voltages will be offered on request.2011-01-10PMV Positioners pneumatic, 3-15 psi Model Order No P5S23-NAMUR 259014PMV Positioners electro-pneumatic, 4-20 mA input signal Model Order No EP5 S23-NAMUR 259013D3 D23-NAMUR 259053D3 D23-NAMURMechanical switches + output signal 4-20mA 259057Other will be offered on request.F5 limit switchModelOrder No F5-MEK S00 2 pcs mechanical switches259026F5-420 S00Mechanical switches + output signal 4-20mA259028PMV Digital Positioners , 4-20 mA input signal for Actuators type SR Model Order No D20IMU S23-NAMUR Utsignal 4-20 mA ATEX/Brytare 2xSPDT 259525D20IMU S23-NAMUR ATEX 259526D20IMU S23-NAMUR HART ATEX / Brytare 2 x SPDT 259527D20IMU S23-NAMUR HART ATEX 259528259529Other will be offered on request.Mounting of positioner including mounting kit Model / ActuatorOrder No MOUNTING POSITIONER RC210259148MOUNTING POSITIONER RC220-240259149MOUNTING POSITIONER RC250-265259150MOUNTING POSITIONER RC270-280, RC88259151MOUNTING POSITIONER RCG90-10025914714Product OverviewPositionersD20IMU S23-NAMUR Utsignal 4-20 mA ATEX/ Utan indikator 2011-01-10RCC-Firesafe TypeOrder NoRCC30-SR080 Firesafe F07-14133260RCC50-SR080 Firesafe F10-19153193Note: Switches and junction boxes offer on demand.For Steel, Electric and Multiturn see special pricelist15Product OverviewRCC-Firesafe2011-01-10For double acting actuators and single acting type DA / SRLucifer complete Namur solenoid valve with manual override 5/2-way with manual override Ambient temp C°Order No 600 Nl/min341N01-8980220/50 2W IP65-25 - +50261153341N01-898024VDC 2,5W IP65-25 - +50261154341N01-2606EExmII T5 220/50 2W IP65-25 - +50261155341N01-2606EExmII T5 24VDC 2,5W IP65-25 - +50261156600 Nl/min 341N31-1865220/50 8W IP65-25 - +50261165341N31-186524VDC 9W IP65-25 - +50261166341N31-5905EExdm lIC T4 220/50 8W IP67-25 - +65/40261683341N31-5905EExdm lIC T4 24VDC 9W IP67-25 - +65/40261682Joucomatic / Asco complete Namur solenoid valve with manual override 5/2-way with manual override Ambient temp C°Order No 700 Nl/min551 220/50 2,5W IP65-25 - +60261332551 24VDC 2,5W IP65-25 - +60261333551 220/504W IP65 EExmIIT4-25 - +55261335551 24VDC 4W IP65 EExmIIT4-25 - +55261334Mounting and trimming of Namur solenoid valves on RC200-series, silencers included Type Order No NAMUR mounting on RC210-280, RC88, RCG90-100261262Price for wiring solenoid valve to RC-E4 and RC-E4L ArticleOrder No Wiring E4/ solenoid valve RC210261791Other voltages will be offered on request.16Product OverviewSolenoid valvesNamur2011-01-10Accessories for solenoid valves Type / For actuatorsOrder No RESTRICTOR-SILENCER R1/8" RSW 261294RESTRICTOR-SILENCER R1/4" RSW261295Accessories for solenoid valves Type / For actuators Order No SILENCER M5 264004SILENCER R1/8"264003SILENCER R1/4"264002SILENCER R1/2"264067Accessories for solenoid valvesType / For actuatorsOrder No SPEED RESTRICTOR FOR NAMUR VALVES 261309SPEED RESTRICTOR NAMUR TUFRAM261361Accessories for solenoid valves Type / For actuatorsOrder No QUICK EXHAUST VALVE R1/2"264005QUICK EXHAUST VALVE R1/4"264006Accessories for solenoid valves TypeOrder No DIN PLUG rectangular 261047DIN PLUG square261046DIN PLUG rectangular 110V with sensors 261134DIN PLUG rectangular 220V with sensors 261048DIN PLUG rectangular 24V with sensors 261049DIN PLUG square 220V with sensors 261291DIN PLUG square 24V with sensors26113717Product OverviewSolenoid valvesAccessories2011-01-10Only adaptable for valves with mounting flange according to ISO 5211Mounting kits (Price group A)TypeSize Order No Mounting kit DIN F05* / F03** 210-220549850Mounting kit DIN F05* / F04** 210-220549851Mounting kit DIN F05* / F05** 210-220549852Mounting kit DIN F05* / F07** 210-220549853Mounting kit DIN F05* / F10**210-220549869Mounting kit DIN F07* / F04** 230549848Mounting kit DIN F07* / F05** 230549849Mounting kit DIN F07* / F07** 230549854Mounting kit DIN F07* / F10** 230549855Mounting kit DIN F10* / F07** 240-250549856Mounting kit DIN F10* / F05** 240-250549857Mounting kit DIN F10* / F10** 240-250549858Mounting kit DIN F10* / F12** 240-250549859Mounting kit DIN F12* / F12** 260-265549860Mounting kit DIN F12* / F10**260-265549861*= The mounting kit F-size refers to the actuator bottom side** = The mounting kit F-size refers to the valve mounting flange Materail in Bushing AISI 303, Console AISI 304, screws A2Prices for packing each mounting kit individiualy TypeOrder No Packing Individually549919Heavy duty Mountingkits for Regulating Type Size Order No Mount.kit DIN F05 / Modulating 210-220549862Mount.kit DIN F07 / Modulating 230549863Mount.kit DIN F10 / Modulating 240549864Mount.kit DIN F10 / Modulating 250549868Mount.kit DIN F12 / Modulating 260-265549865Mount.kit DIN F14 / Modulating 270549866Mount.kit DIN F16 / Modulating 280549867Material RC270-280 Console SS1312Prices for mounting (actuator on valve) and test in our workshop Type Order No RC210-240549703RC250-265549704RC270549705RC280549706The prices above are only indicative and can be altered for valves which are unusually easy or unusually difficult to mount.Mounting or mounting details can also be offered for other types of valves on request.18Product OverviewMounting kitsStainless steelNOTE!When ordering mounting kits, please always advise valvemanufacture, valve type and size !NOTE:When adding the number of assemblages, the valves must be fully identical and the same actuator size must be used.2011-01-10Mounting kits for valves without ISO flange Type Size Order No Mounting kit DIN F05*210-220549588 Mounting kit DIN F07*230549589 Mounting kit DIN F10*240-250549590 Mounting kit DIN F12*260-265549591 Mounting kit DIN F14*270549592Mounting kit DIN F16*280549593Mounting kit RC88549738* = The mounting kit F-size refers to the actuator bottom sideMaterial in Bushing stainless AISI 303, Console AISI , screws stainless typ A2Prices for packing each mounting kit invidiualyType Order NoPacking Individually549919Prices for mounting (actuator on valve) and test in our workshopType Order NoRC210-240549703RC250-265549704RC270549705RC280549706RC88549740Epoxy painted mounting kitsModel Order NoRHE1109500765RHE1411500766RHE1711500767RHE1714500768RHE2217500769RHE2722500770RHE3627500771The prices above are only indicative and can be altered for valves which areunusually easy or unusually difficult to mount.Mounting or mounting details can also be offered for other types of valves on request.19Above prices +30%NOTE!When ordering mounting kits, please always advisevalve manufacture, valve type and size !Mounting kits / ReducersPainted carbon steelNOTE:When adding the number of assemblages, the valves mustbe fully identical and the same actuator size must be used.Prices for reducers to RC actuatorsProduct Overview2011-01-10Mounting kits contain: mounting brackets in stainless steel, painted or zinc plated driving bushes and zinc plated screw kits for the actuator size.Mounting kits (Price group B)Type Size Order No Mounting kit DIN F05*210-220549746Mounting kit DIN F07*230549747Mounting kit DIN F10*240-250549748Rigging costper valve size and order occasion549900Extended valve screws for 3-piece ball valvesFor valveOrder No DN8-15 549510DN20 549504DN25 549505DN32 549506DN40 549507DN50549508DN65549509DN80549511Prices for mounting (actuator on valve) in our workshop TypeOrder No RC210-240549703RC250-265549704RC270549705RC280549706The prices above are only indicative and can be altered for valves which are unusually easy or unusually difficult to mount.Mounting or mounting details can also be offered for other types of valves on request.20* = The mounting kit F-size refers to the actuator bottom sideProduct OverviewMounting kitsfor 3-piece ball valveswithout mounting flangeNOTE!When ordering mounting kits, please always advise valve manufacture, valve type and size !NOTE:When adding the number of assemblages, the valves must be fully identical and the same actuator size must be used.2011-01-10Reception Telefax SalesEriksson Micael Ersson Lars Groth Villy Jacobs Arjan Johansson BjörnLjungbergh HansLjungberg Karl Park CarlSpange Maria Westin Håkan Wiklund Håkan Service Groth Sten-Olof21*************************************************+46 23-587 41+46 70-366 9741+46 23-587 34+46 70-594 0174+46 70-594 0551************************+46 70-593 4567+46 70-593 4567***********************************************************************+46 70-536 2898Product Overview+46 70-594 0411+46 70-594 0411Telephone Mobile E-mail+46 23-587 56***********************+46 23-587 42Telephone E-mailTelephone MobileE-mail+46 23-587 00+46 23-587 45+46 23-587 55+46 70-594 9858+46 23-587 35+46 70-381 7735**************************+46 23-587 16**********************+46 70-592 4355**********************+46 70-331 3034+46 23-587 57+46 70-594 9107***********************+46 23-587 11+46 23-587 28+46 70-594 3536**************************Telephone: +46 23-587 00 • Telefax: +46 23-587 45http://www.remotecontrol.se•*********************Rotork Sweden AB, Box 80, Kontrollvägen 15, SE-791 22 FALUN, SWEDEN2011-01-10。
电液执行器在转辙机中的应用分析
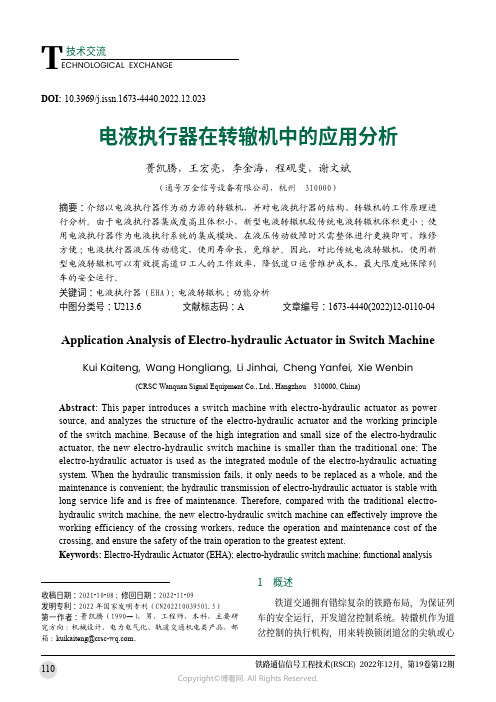
电液执行器在转辙机中的应用分析蒉凯腾,王宏亮,李金海,程砚斐,谢文斌(通号万全信号设备有限公司,杭州 310000)摘要:介绍以电液执行器作为动力源的转辙机,并对电液执行器的结构、转辙机的工作原理进行分析。
由于电液执行器集成度高且体积小,新型电液转辙机较传统电液转辙机体积更小;使用电液执行器作为电液执行系统的集成模块,在液压传动故障时只需整体进行更换即可,维修方便;电液执行器液压传动稳定,使用寿命长,免维护。
因此,对比传统电液转辙机,使用新型电液转辙机可以有效提高道口工人的工作效率,降低道口运营维护成本,最大限度地保障列车的安全运行。
关键词:电液执行器(EHA);电液转辙机;功能分析中图分类号:U213.6 文献标志码:A 文章编号:1673-4440(2022)12-0110-04 Application Analysis of Electro-hydraulic Actuator in Switch Machine Kui Kaiteng, Wang Hongliang, Li Jinhai, Cheng Yanfei, Xie Wenbin(CRSC Wanquan Signal Equipment Co., Ltd., Hangzhou 310000, China) Abstract: This paper introduces a switch machine with electro-hydraulic actuator as power source, and analyzes the structure of the electro-hydraulic actuator and the working principle of the switch machine. Because of the high integration and small size of the electro-hydraulic actuator, the new electro-hydraulic switch machine is smaller than the traditional one; The electro-hydraulic actuator is used as the integrated module of the electro-hydraulic actuating system. When the hydraulic transmission fails, it only needs to be replaced as a whole, and the maintenance is convenient; the hydraulic transmission of electro-hydraulic actuator is stable with long service life and is free of maintenance. Therefore, compared with the traditional electro-hydraulic switch machine, the new electro-hydraulic switch machine can effectively improve the working efficiency of the crossing workers, reduce the operation and maintenance cost of the crossing, and ensure the safety of the train operation to the greatest extent.Keywords: Electro-Hydraulic Actuator (EHA); electro-hydraulic switch machine; functional analysis DOI: 10.3969/j.issn.1673-4440.2022.12.023收稿日期:2021-10-08;修回日期:2022-11-09发明专利:2022年国家发明专利(CN202210039501.5)第一作者:蒉凯腾(1990—),男,工程师,本科,主要研究方向:机械设计、电力电气化、轨道交通机电类产品,邮箱:**********************。
基于EEMD的重燃压气机液压IGV系统内泄漏诊断

基于EEMD的重燃压气机液压IGV系统内泄漏诊断武鑫;陈雄伟;芮晓明【摘要】重型燃气轮机中轴流压气机的进口导叶(IGV)系统中,液压油缸在变化的运动位移和负载条件下工作.液压油缸的内泄漏故障会导致IGV系统累积偏差超过限度,引发燃气发电机组跳闸.针对此故障,根据液压油缸一侧油腔的压力信号,提出了一种基于集合经验模态分解(EEMD)和希尔伯特变换(HT)的诊断方法.该方法先将压力信号通过EEMD方法分解成一系列固有模态函数(IMF)分量,然后应用HT方法对第一个IMF分量进行变换,获得瞬时幅值,最后得到瞬时幅值的绝对均值.通过IGV模拟实验台的实验证明,提出的诊断方法能够有效地检测液压油缸有无内泄漏发生,以及泄漏的程度.【期刊名称】《风机技术》【年(卷),期】2018(060)004【总页数】6页(P69-74)【关键词】重型燃气轮机压气机;进口导叶系统;内泄漏;EEMD方法【作者】武鑫;陈雄伟;芮晓明【作者单位】华北电力大学能源动力与机械工程学院;华北电力大学能源动力与机械工程学院;华北电力大学能源动力与机械工程学院【正文语种】中文【中图分类】TH4530 引言对于重型燃气轮机,进口导叶(Inlet Guide Vane,IGV)系统,起着保护机组安全运行、提高运行效率的重要作用。
目前,IGV系统主要为电液伺服调节方式。
在液压系统的几类故障中,液压油缸的泄漏是最普遍的一种故障形式,泄漏产生原因一般有制造缺陷、安装误差以及磨损等。
液压油缸的泄漏有内泄漏和外泄漏两种,外泄漏一般可以通过观察的方法发现,而内泄漏极其隐蔽,难以察觉。
对于IGV 系统,一旦发生液压油缸的内泄漏故障,最直接的影响就是系统的响应时间变长,位置控制精度降低,进而影响温度限制模块、压比限制模块的功能[1],导致温度控制不佳,致使机组运行效率下降。
此外,还可能导致压气机喘振的发生,对机组的安全运行造成严重影响。
内泄漏故障亦会导致IGV系统无法达到指定的开度,当实际开度和指令开度的累积偏差超过限度,将引发燃气发电机组跳闸。
汤姆森线性电机H-Track电液一体化直线执行器说明书

H-TrackH-Track – A Compact Hybrid of Superior PerformanceMore Power in Less SpaceH-Track electro-hydraulic actuators feature the smallest mounting envelope in their class with a patented valve and reservoir design that provides significant space savings compared to competitive models. H-Track is a robust linear actuator providing force up to 4800 lbf (21350 N) and travel speeds near 4 in (100 mm) per second. With stroke lengths up to 16 in (406 mm), end switch options and multiple configurations available, the H-Track offers a unique set of options for machine designers.Made for Tough ConditionsH-Track actuators are weatherproof, dust tight, corrosion resistant, and IP67 static (temporary submersion) and IP69K (high-pressure washdown) tested. The H-Track offers an optional operation temperature as low as -40°F (-40°C) to as high as 180°F (82°C), making it an ideal option for use in demanding conditions.H-Track electro-hydraulic actuators provide the high-load performance of hydraulics without the expansive space requirements nor the prohibitive cost of full-sized, fluid-based systems.H-Track Completely Self-ContainedThe motor, pump and valves are contained in one mini power pack mounted directly to the combined cylinder/fluid tank. This means that the inner workings are completely sealed from the outside, allowing this unique arrangement to minimize parts and improve performance. Unlike hydraulic cylinders, there is no need for external hoses, valves, reservoirs or hydraulic connectors that can break or leak. The operation is as simple as with a traditional electric actuator - just turn the supply voltage onto move and change polarity to reverse direction.If necessary, the actuator extension tube can be manually overridden, allowing the tube to float for operating in emergency situations.Electro-Hydraulic AdvantagesThe best features from the electric and hydraulic actuator worlds have been chosen to power the H-Track linear actuator, giving it a unique set of capabilities that allow it to be used in applications that otherwise might be too difficult for other solutions to take on.Compact DesignH-Track actuators have a mounting length that is shorter than any other electromechanical actuator on the market. It can fit into applications with a pin-to-pin length as small as 4.8 in (122 mm) plus its stroke, and still provide up to 4800 lbf (21350 N) of force.Superb Load Holding PowerH-Track actuators operate in both tension and compression and will hold a load stationary without power in either direction. Static load holding capability will always exceed the dynamic load moving capability.Vibration and Shock Load ResistantH-Track actuators are immune to vibrational drifting, hydraulically self lock and safely absorb shocks. Energy EfficientElectric control provides clean, smooth linear motion without hydraulic plumbing or other expensive componentry. The H-Track’s power demands are significantly less than those of a full hydraulic system as the actuators require power only when in motion. Solid Extension TubeSince the extension tube is solid, it allows for increased resistance to buckling compared to a hollowextension tube of the same size.H-TrackHydraulics Isolated from the AtmosphereThe fluid reservoir is vented and isolated from the atmosphere with a flexible lid, allowing actuator and pump operation in any orientation without entraining or cavitation.Maintenance-FreeH-Track actuators require no lubrication, hydraulic fluid fillup, or any other type of maintenance or adjustments for their entire lifecycle. Contamination-FreeThe H-Track pump is burnished, cleaned, flushed and vacuum filled with degassed hydraulic fluid. The system is completely sealed with no hosesto leak. This ensures you enjoy contaminant-free performance for the life of the actuator.Thoroughly TestedThroughout their entire development process,H-Track actuators are rigorously tested to ensure they meet all relevant standards and performance specifications prior to leaving the factory. Please contact Thomson customer support to learn more about which standards H-Track meets and how our testing is carried out.CustomizationAs with most Thomson products, H-Track actuators can be customized. Our engineers will work with you to determine the modifications needed – from a simple color change to a complete overhaul of the design. Thomson is a global leader in custom actuator production and takes pride in supplying the optimal solution to each customer.Built to PerformH-Track is one of the strongest actuators for its size without compromising life expectancy or the ability to withstand the elements.1Compact and strong power pack unit, containing pump, valve and motor 2Fluid tank integrated into the cover tube3Solid small-diameter, buckling-resistant extension tube312Get the best from the electric and hydraulic worlds in one package. H-Track is powerful, tough, and vibration and shock load resistant.Yet it only needs a battery and a switch to run, requires no maintenance, and minimizes the risks and hazards associated with hydraulic fluid leaks.4Power pack unit completely sealed from the outsideTwo-wire operation6Large number of power pack and cylinder configurations allow for great design flexibility4 585H-Track is built from the outside in to excel in situations where many otheractuators are forced to bow out. The unique electro-hydraulic design combines the best features from two distinct systems and opens up new application possibilities for linear actuators.H-Track410H-Track is designed and tested to operate under the harshest conditions without failure or the need for maintenance.10IP69K/IP67 protection class 13Large operating temperature range 11Chrome finished steel extension tube 14High shock load and vibration resistance 12Salt spray tested for 200 hoursAnodized aluminum alloy housing1912101178211976Built for the Toughest ApplicationsWith a self-contained electro-hydraulic system, H-Track actuators meet the growing demand for power-dense performance used in a variety of industrial applications, including agricultural sprayer booms, snow plow blades and mower deck lifts.Designed to Withstand Life on the FieldsWith agricultural sprayers becoming larger and boom lengths reaching up to 177 ft (54 m), strain on the actuators has increased exponentially. Actuators are used to fold the long sprayer booms from an extended position to a stowed position for transport. The folding and unfolding of these booms apply very high loads on the actuators. The strain on the units is dramatically increased when the sprayeris in motion and the bouncing of the booms causes even more extreme loads. These combined loads create tremendous impact force that can easily destroy most other electric actuators. The H-Track is designed to handle this type of loading with ease.H-Track Ideal for Demanding Outdoor ApplicationsWhere the often harsh outdoor environmentcreates conditions that can be fatal for mostactuators, the H-Track thrives. A snow plowbattling icy roads and striking a stationary, concreteobject is an example that would quickly destroymost linear actuators. The H- T rack’s unique valveand reservoir design gives it the ability to cushionthese blows and continue operating without issue.The optional ability to operate in temperatures aslow as -40°F (-40°C) makes it a perfect fit for eventhe coldest climates. Mower deck lifts are typicallywhere electric actuators shine, but with increasingdeck sizes and ground speeds, the limits of thesetraditional actuators are being exceeded. Withits reliable, load-holding capabilities, enhanceddurability for higher transport speeds, and ability towithstand high-pressure washdowns, the H-Trackis a perfect choice for the next generation of larger,faster mowers.Technical FeaturesH-Track Electro-Hydraulic Linear Actuator • Combines the best from the hydraulic and electric worlds.• High power density.• Very compact and short pin-to-pin versus stroke length relationship.• Solid extension tube allows for increased resistance to buckling.• Immune to vibrational drifting and hydraulically self locks.• High shock load and vibration resistance.• Fluid reservoir is vented and isolated from the atmosphere with a flexible lid, allowing actuator and pump operation in any orientation withoutentraining or cavitation.• Standard strokes up to 16 in (406 mm).• Designed for harsh outdoor conditions.•Reliable and maintenance free.H-TrackTechnical SpecificationsElectrical ConnectionsF FuseS1 Double pole double throw switchTo extend the actuator, apply +Vdc to black (white) and -Vdc to grey (green/white). To retract, apply-Vdc to black (white) and +Vdc to grey (green/white). Colors in between brackets are valid for the 560 W motor. Avoid running the actuator in to the ends.DimensionsH-Track DimensionsWeightbut at temperatures below 40°F (4°C), force and current begin to increase, while speed decreases. At temperatures above 120°F (50°C), speed will decrease slightly. The exact amount of performance change is difficult to calculate. Also, when it comes to the lower temperature span, the performance will move towards what is stated above as the temperature rises in the actuator due to the heat generated by its work. Please consult Thomson customer service for more information.Performance MatrixH-Track Ordering KeySizing and SelectionIn order to choose the optimal H-Track actuator for your application, please follow the sizing and selection process as described below. Do not hesitate to contact Thomson customer support if you need assistance.Step 1. Determining Load ConfigurationDetermine which load configuration (C, H, N or B) is valid for your application. Also see page 18.Example: Assuming that the load needs to be pushed horizontally, and the extenson tube will not be affected by gravity when pushing or pulling, then the application corresponds to load configuration N.Step 2. Bore and Extension Tube SizingDetermine which bore size is needed for your load and stroke. Also see page 19.Example: Assuming the application requires 16-in stroke, and that load is 2500 lbf at extension (red dot) and 500 lbf at retraction (yellow dot), then the Stroke vs. Load and Bore Size diagram below shows, that only the blue curve is above both points. Therefore, bore size H3 is the only possible choice in this case.Stroke vs. Load and Bore SizeStroke [in]Bore SizeH1H2H3L o a d [l b f (N )]0 2 4 6 8 10 12 14 16 18 20 22 245500 (24464)5000 (22240)4500 (20016)4000 (17792)3500 (13344)3000 (13344)2000 (8896)1500 (6672)1000 (4448)500 (2224)H-TrackStep 3. Sizing of Motor, Pump and Power Supply Determine the size of the actuator motorand pump for your application, as wellas the current draw by referring to the diagrams on pages 20 - 22.Example: Since the load configuration in step 1 was determined to be of type N, refer to the diagrams on page 22.In the Load vs. Speed diagrams for load configuration N, the maximum extension and retraction loads that were assumed in step 2 are shown by the vertical lines. In this example, we also assume that a travel speed of 0.25 in/s is required when extending and 1 in/s when retracting. The only H3 bore size of the four that can deliver that speed when extending at 2500 lbf and retracting at 500 lbf is model H3N-xx-2B23.In order to size the power supply, you must decide which voltage to use and themaximum load currect draw at extensionand retraction. To do that, first determine the percentage of the maximum permissible load that is used in each direction.According to the Load vs. Speed diagram, H3N-xx-2B23 has a maximum load of about 2700 lbf at extension and 2000 lbf at retraction (the exact max. load values can be found in the Performance Matrix on page 14). The assumed maximum loads needed in the application, which requires 2500 lbf at extension and 500 lbf at retraction, are about 92% (red line) and 25% (yellow line) of the maximum permissible loads. The current forH3N-xx-2B23 equipped with a 24 Vdc motor (model H3N-24-2B2) would, in this case, follow the dotted red line and be about 20 A at extension and 40 A at retraction. Be sure to size your power supply with some margin.Step 4. Finishing the Ordering CodeAt this point, the ordering code is H3N-24-2B23-xxxx. In order to complete it, the type of extension tube front adapter, the stroke length and the rear adapter orientation need to be determined. Also see page 15.Example: In step 2, it was assumed the application required a 16-in stroke, which means the code becomes H3N-24-2B23-x16x. If we assume a standard front adapter and a 90° rear adapter orientation are required, the complete ordering code would be H3N-24-2B23-A16R.Load vs. Speed @ Extension Load vs. Speed @ RetractionC u r r e n t [A ]S p e e d [i n /s (m m /s )]Load [lbf (N)]12 Vdc Actuators Bore Size H124 Vdc Actuators Bore Size H248 Vdc ActuatorsBore Size H3Percent of Maximum Permissible Load [%]H1N-xx-1B11 H1N-xx-1B41H1N-xx-2B11H1N-xx-2B41HxN-12-1xxx HxN-12-2xxx HxN-24-1xxx HxN-24-2xxx HxN-48-1xxxHxN-48-2xxx H2N-xx-1A12 H2N-xx-1B42H2N-xx-2A22H2N-xx-2B32H3N-xx-1A13 H3N-xx-1B23H3N-xx-2A13H3N-xx-2B23Load vs. CurrentDetermining Load ConfigurationThere are four main types of load and gravity configurations, which will determine the performance of the actuator. Please refer to the configurations below and choose the one that best corresponds to your application. Contact Thomson customer support if you are unable to determine a valid configuration for your application.Configuration CThe gravity resists the load being moved when the actuator extends and helps it when retracting. Configuration NThe gravity does not affect the load in any direction.Configuration HThe gravity helps the load being moved when the actuator extends and resists it when retracting.Configuration BThe gravity both helps and resists the load being moved in both directions except at one point where the load is not affected by the gravity at all. If this is your configuration, try to re-design the mechanical linkage so that the result is a C, H or N configuration. Please contact Thomson customer support if that is not possible.H-TrackSizing of Bore and Extension TubeStroke vs. Load and Bore SizeStroke [in]Bore SizeH1H2H3L o a d [l b f (N )]0 2 4 6 8 10 12 14 16 18 20 22 245500 (24464)5000 (22240)4500 (20016)4000 (17792)3500 (13344)3000 (13344)2500 (11120) 2000 (8896)1500 (6672)1000 (4448)500 (2224)The maximum load in each direction and the required stroke length determine the minimum bore and extension tube size needed for the actuator. Refer to the diagram below todetermine which bore size your application requires. If no solution exists, the stroke and/or load must be reduced. Contact Thomson customer support if you are unable to determine a valid combination for your application.Sizing of Motor, Pump and Power SupplyLoad vs. Speed @ ExtensionLoad vs. Speed @ RetractionC u r r e n t [A ]S p e e d [i n /s (m m /s )]Load [lbf (N)]12 Vdc ActuatorsBore Size H124 Vdc ActuatorsBore Size H248 Vdc ActuatorsBore Size H3Percent of Maximum Permissible Load [%]H1C-xx-1B11 H1C-xx-1B41H1C-xx-2B11H1C-xx-2B41HxC-12-1xxx HxC-12-2xxxHxC-24-1xxx HxC-24-2xxxHxC-48-1xxx HxC-48-2xxxH2C-xx-1A12 H2C-xx-1B32H2C-xx-2A22H2C-xx-2B32H3C-xx-1A13 H3C-xx-1B23H3C-xx-2A13H3C-xx-2B23Load vs. CurrentH-TrackSizing of Motor, Pump and Power SupplyLoad vs. Speed @ ExtensionLoad vs. Speed @ RetractionC u r r e n t [A ]S p e e d [i n /s (m m /s )]Load [lbf (N)]12 Vdc ActuatorsBore Size H124 Vdc ActuatorsBore Size H248 Vdc ActuatorsBore Size H3Percent of Maximum Permissible Load [%]H1H-xx-1B11 H1H-xx-1B41H1H-xx-2B11H1H-xx-2B41HxH-12-1xxx HxH-12-2xxxHxH-24-1xxx HxH-24-2xxxHxH-48-1xxx HxH-48-2xxxH2H-xx-1A12 H2H-xx-1B32H2H-xx-2A22H2H-xx-2B32H3H-xx-1A13 H3H-xx-1B23H3H-xx-2A13H3H-xx-2B23Load vs. CurrentSizing of Motor, Pump and Power SupplyLoad vs. Speed @ ExtensionLoad vs. Speed @ RetractionC u r r e n t [A ]S p e e d [i n /s (m m /s )]Load [lbf (N)]12 Vdc ActuatorsBore Size H124 Vdc ActuatorsBore Size H248 Vdc ActuatorsBore Size H3Percent of Maximum Permissible Load [%]H1N-xx-1B11 H1N-xx-1B41H1N-xx-2B11H1N-xx-2B41HxN-12-1xxx HxN-12-2xxxHxN-24-1xxx HxN-24-2xxxHxN-48-1xxx HxN-48-2xxxH2N-xx-1A12 H2N-xx-1B32H2N-xx-2A22H2N-xx-2B32H3N-xx-1A13 H3N-xx-1B23H3N-xx-2A13H3N-xx-2B23Load vs. CurrentH-TrackThomson offers a wide variety of online tools to help you in the sizing and selection process. An experienced team of engineers is also available to help size and select an H-Track model to best fit your application needs. To explore additional technical resources and options, contact customer support at /cs.Online ResourcesInteractive 3D CAD ModelsDownload free interactive 3D CAD models in the most common CAD formats./H-Track-cadH-Track on the WebGet additional information and learn more about H-Track on this content-rich web page. /h-trackH-Track Overview VideoLearn about this electro-hydraulic actuator with this brief, informative video./H-Track-videoIs H-Track suitable for tough environments such as washdown or extreme temperatures? Yes. H-Track actuators are designed for washdown and have passed 200 hours of salt spray tests. They can operate in temperatures ranging from -20 to +65°C (-20 to +150°F).How is the duty cycle determined?The duty cycle = on time / on time + off time. For example, if H-Track is powered for 15 seconds and then off for 45 seconds, the duty cycle for that minute would be 25%. All models are rated to 25% at full load, and an ambient temperature of 25°C (77°F). If load and/or ambient temperature are lower, then the duty cycle can exceed 25%. At higher temperatures, the duty cycle will be lower. Can H-Track be side loaded?No. A proper design of the application should eliminate any side loads.Frequently Asked QuestionsWhat is the typical life of an actuator?Life is a function of load and stroke length. Please contact customer support for more information.What are the most common reasons for premature actuator failure?Side load due to incorrect mounting, shock loading, exceeding the duty cycle and incorrect wiring are the most prominent causes of premature failure.Is H-Track maintenance free?Yes, it never requires lubrication, maintenance or adjustment for wear.What are IP ratings?Ingress Protection (IP) ratings are commonly referenced standards that classify electrical equipment using standard tests to determineresistance to ingress of solid objects (first digit) and liquids (second digit). See the IP Ratings table below.H-TrackIs it possible for a load to back-drive the extension tube?H-Track is self locking up to at least the maximum static load. Higher static load may result in damage and back driving.What is the difference between a tension and a compression load?A tension load tries to stretch the actuator,while a compression load tries to compress it. With bi-directional loads, the end play of the actuator extension tube may need to be takeninto consideration when using the actuator for positioning tasks.What is the range of input voltage an H-Track can operate with?A 12 Vdc version will accept 9 – 16 Vdc, a 24 Vdc18 – 32 Vdc and a 48 Vdc 36 – 64 Vdc. Outsideof these limits, operation may be erratic and the actuator permanently damaged.Is H-Track protected against overheating? Yes, the motor incorporates a thermal switch in the windings to shut off the actuator motor in case of overheating or high overcurrent.Can the speed of an H-Track be adjusted by changing the input voltage?Yes, as long as the voltage is within the acceptable input voltage limits.What is the inrush current?The inrush current is a short current peak that appears at the start of an actuator as the motor tries to get the load moving. Typically, the inrush current will last between 75 – 150 milliseconds and can be up to three times higher than the current for the actuator and load. Batteries have no problem delivering the inrush current, but if using an AC power supply, it is important to size it to handle the inrush current.What special mounting considerations does the H-Track require?There is no restraining torque that needs to be considered as H-Track is internally restrained. However, the actuator must be mounted so that there are no side loads acting on the extension tube. What is the maximum travel speed?The travel speed of an H-Track actuator is a linear function of the load. To determine the speed at a certain load and direction, consult the load vs. speed diagrams on pages 18 - 20. If a higher linear travel speed is required, a simple mechanical linkage canbe employed. Tension CompressionH-TrackEUROPEUnited Kingdom ThomsonOffice 9, The BarnsCaddsdown Business Park Bideford, Devon, EX39 3BT Phone: +44 1271 334 500E-mail:******************************Germany ThomsonNürtinger Straße 7072649 Wolfschlugen Phone: +49 7022 504 403Fax: +49 7022 504 405E-mail:******************************France ThomsonPhone: +33 243 50 03 30E-mail:******************************Italy ThomsonVia per Cinisello 95/9720834 Nova Milanese (MB)Phone: +39 0362 366406Fax: +39 0362 276790E-mail:*****************************Sweden Thomson Estridsväg 1029109 Kristianstad Phone: +46 44 590 2400Fax: +46 44 590 2585E-mail:******************************SOUTH AMERICA Brazil ThomsonAv. João Paulo Ablas, 2970Jardim da Glória - Cotia SP - CEP: 06711-250 Phone: +55 11 4615 6300E-mail:******************************USA, CANADA and MEXICO Thomson203A West Rock Road Radford, VA 24141, USA Phone: 1-540-633-3549Fax: 1-540-633-0294E-mail:*************************Literature: ASIAAsia Pacific ThomsonE-mail:****************************China ThomsonRm 805, Scitech Tower 22 Jianguomen Wai Street Beijing 100004Phone: +86 400 606 1805Fax: +86 10 6515 0263E-mail:*****************************IndiaKollmorgen – Div. of Altra Industrial Motion India Private LimitedUnit no. 304, Pride Gateway,Opp. D-Mart,Baner Road, Pune, 411045MaharashtraPhone: +91 20 67349500E-mail:**************************South Korea Thomson3033 ASEM Tower (Samsung-dong) 517 Yeongdong-daeroGangnam-gu, Seoul, South Korea (06164)Phone: + 82 2 6001 3223 & 3244E-mail:*****************************。
电液联动执行机构操作流程
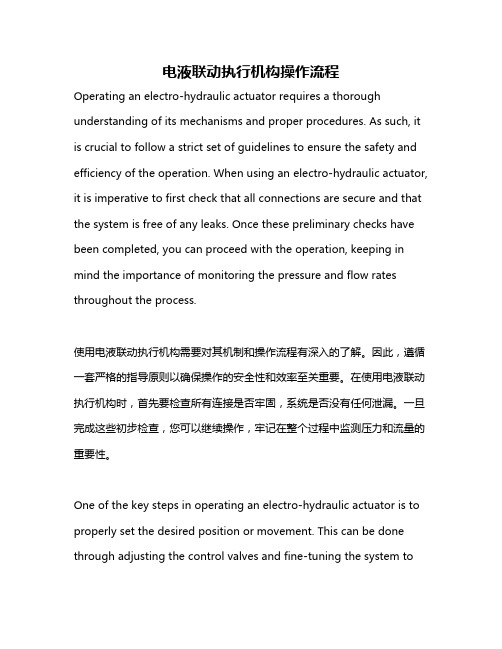
电液联动执行机构操作流程Operating an electro-hydraulic actuator requires a thorough understanding of its mechanisms and proper procedures. As such, it is crucial to follow a strict set of guidelines to ensure the safety and efficiency of the operation. When using an electro-hydraulic actuator, it is imperative to first check that all connections are secure and that the system is free of any leaks. Once these preliminary checks have been completed, you can proceed with the operation, keeping in mind the importance of monitoring the pressure and flow rates throughout the process.使用电液联动执行机构需要对其机制和操作流程有深入的了解。
因此,遵循一套严格的指导原则以确保操作的安全性和效率至关重要。
在使用电液联动执行机构时,首先要检查所有连接是否牢固,系统是否没有任何泄漏。
一旦完成这些初步检查,您可以继续操作,牢记在整个过程中监测压力和流量的重要性。
One of the key steps in operating an electro-hydraulic actuator is to properly set the desired position or movement. This can be done through adjusting the control valves and fine-tuning the system toachieve the desired outcome. It is important to be patient and precise during this step, as any errors in positioning can lead to malfunctions or accidents. Additionally, it is crucial to follow the manufacturer's guidelines when setting the position to ensure the actuator functions correctly and efficiently.操作电液联动执行机构的关键步骤之一是正确设置所需的位置或运动。
西门子建筑技术有限公司 SKP 系列技术说明书文件号155-753 SKP55U.. 2014年7月

Siemens Building Technologies, Inc.SKP SeriesTechnical InstructionsDocument No. 155-753SKP55 U..July 9, 2014SKP55 U.. Air/Gas Ratio Controlling Actuators With Safety Shutoff FunctionFor Use with Gas Valves VGDescriptionSKP55 pressure regulating electro-hydraulic actuators combine with VG series gas valves to provide slow opening, fast closing safety shut-off and air/gas ratio control for industrial and commercial burner applications.The SKP55 actuator controls the pressure difference across a restriction in the gas supply line as a function of the pressure difference across a restriction in the air supply duct so that the air to gas ratio remains constant irrespective of air volume changes. There is no need for an upstream constant pressure regulator when using an SKP55 actuator within the applicable pressure range of the VG valve body.Since a single valve performs three functions: safety shut-off, constant pressure regulation, and air/gas ratio control, fewer components and fittings are required toassemble a gas train. This significantly reduces both the size and the weight of the gas train. The total pressure drop across the gas train arrangement is reduced, allowing for the use of smaller diameter gas trains in most applications.The modular design allows the SKP55 actuator to be used in combination with all VG series gas valves from 1/2-inch to 6-inch in size. The actuator is easily mounted on the square flange of any VG valve with four bolts. No gaskets or seals are required when mounting the actuator. A visible position indicator on the front of the actuator displays the entire stroke of the valve. A light indicates when the actuator is powered.Technical Instructions SKP55 U.. Air/Gas Ratio Controlling ActuatorsDocument No. 155-753 July 9, 2014Page 2 Siemens Building Technologies, Inc.Features • UL listed, FM approved, CSA certified for USA and Canada, and ISO 9001 certified; European, Australian and Japanese approved versions available.• Safety shut-off function, pressure regulating function and air/gas ratio control in one compact unit.• Proof Of Closure with Over Travel (POC) versions. •Simplifies commissioning and reduces start-up time for:o Recuperative burners with combustion air preheating.o Burners with continuously variable air or gas nozzle openings in the burnerhead. o Burners where either the air or gas pressure is not representative of the actualflow. o Burners with negative combustion air pressure levels.• Maintains air/gas ratio when the airflow is disrupted.• Automatic compensation for combustion chamber back pressure fluctuations. • No mechanical wear or play that causes drifting. • Visual stroke position indicator. • Light indicating "power on". • Optional auxiliary switch available.• Excellent tracking characteristic.•Low, 13.5 VA power consumption.ApplicationSKP55 series actuators may be combined with 1/2-inch to 6-inch VG series gas valvebodies. VG series gas valves are ordered as separate items (See VG U.. Technical Instructions P/N 155-512P25).Product NumbersTable 1.Product Number Operating Voltage Proof of ClosureSwitchAuxiliary SwitchType of SwitchSKP55.011U1 110 to 120 Vacx – SPDT SKP55.012U1 x x SPDT SPDTSKP55.013U1 – – SKP55.012U2 220 to 240 Vacx x SPDT SPDTSKP55.013U2––AccessoriesTable 2.Product Number DescriptionAGA66 Sealing gasket to provide NEMA 3, 3R, and 4 protection (for VGG/D valves)SKP55 U.. Air/Gas Ratio Controlling Actuators Technical Instructions Document No. 155-753July 9, 2014Siemens Building Technologies, Inc.Page 3SpecificationsAgency approvals As safety shut-off valve UL/429, FM/7400, ANSI Z21.21/CSA6.5 C/I in combination with VG U.. series gas valvesAs a pressure regulator ANSI Z21.18/CSA6.3 Power supplyOperating voltage 110 to 120 Vac + 10% to 15%220 to 240 Vac + 10% to 15%Operating frequency 50 to 60 Hz + 6% Power consumption 13.5 VA Duty cycle100%Operating environmentAmbient operating temperature 5°F to 140°F (-15°C to 60°C)Mounting position Optional, with diaphragms in verticalposition except upside down Maximum inlet gas pressure Same as VG valve PhysicalcharacteristicsWeight 4.2 lb (1.90 kg)Enclosure NEMA 1, 2, 5 and 12 for indoor use NEMA 3, 3R, and 4 with sealing gasketAGA66 (only for VGG/F/D valves) DimensionsSee Figure 4Specification for valves See gas valve Technical InstructionsP/N 155-512P25ConnectionsConduit connection Two 1/2-inch NPSM threaded knock-outs Electrical connectionSpring loaded terminals for 14 AWG wires Gas/air pressure connections 1/4” NPTOperatingcharacteristicsOutput force 100 lb (450 N) Maximum stroke1 inch (26 mm)Opening time for maximum stroke Varies with valve size, 14 seconds for max.strokeClosing time< 0.8 secondsControl signal Reference input signalCombustion air pressure difference Control characteristic Integral action Operation/installationDifferential pressure ratio1:1Permissible pressure differences during operation for accurate control Gas: Minimum 0.1" w.c. Gas: maximum 80" w.c. Air: minimum 0.1" w.c.Air: maximum 80" w.c. Minimum time required for high to low fire load changesApprox. 5 seconds Permissible leakage test pressure 20 psi Permissible leakage test vacuum 3 psiMinimum diameter of impulse pipe 1/4” inside diameter Low fire bias range -0.4 to 0.4" w.c. Minimum distance ofimpulse pipe connections 3 pipe diameters before and 5 pipediameters after any valve, damper, elbow,coupling, or flow disruption Auxiliary featuresProof of closure switch Non-adjustable Capacity of auxiliary switch6 (3) A, 250 VacSetting range of auxiliary switch40% to 100% of stroke)Technical Instructions SKP55 U.. Air/Gas Ratio Controlling ActuatorsDocument No. 155-753 July 9, 2014Page 4 Siemens Building Technologies, Inc.Operation(See Figure 1)Safety Shut-off FunctionThe electro-hydraulic actuator consists of a cylinder filled with oil, and a piston containing an electric oscillating pump and a relief system. When power is supplied to the actuator the relief system closes, and the pump moves oil from the reservoir into the pressure chamber. This action causes the piston to move downward in the cylinder, opening the gas valve. When power to the pump is interrupted, the relief system opens and the gas valve closes in less than 0.8 seconds.A pointer, visible through the transparent portion of the terminal box cover, indicates the entire stroke range of the actuator. A light, which is visible through the lower left transparent portion of the terminal box cover, indicates when the actuator receivespower. An optional, non-adjustable SPDT proof of closure over travel switch signals the closed position after the gas valve has closed. An optional SPDT auxiliary switch is adjustable between 40% and 100% of the stroke. The adjustment screw and scale are located on the right side of the terminal box, and are visible through the transparent portion of the terminal box cover.The sealing gasket, AGA66, can be installed between the actuator and the gas valve to provide NEMA 3, 3R, and 4 protection rating for VGG/D valves.Figure 1. SKP55)U.. Operation.Regulating FunctionDuring the burner pre-purge period, when the gas valve is closed, only the air pressure difference acts on the regulator causing the air diaphragm to move to the left and closes the regulating hydraulic bypass valve. When the actuator is powered the gas valvebegins to open. The downstream gas pressure difference immediately begins to increase until the gas pressure difference is in balance with the air pressure difference. Thebypass valve is now partially open so that the oil flow supplied by the pump is identical to the return flow.If, for example, heat demand increases, the air damper opens further increasing the differential air pressure. The SKP55 air diaphragm moves to the left, causing the bypass valve to close and the gas valve to open further. The opening of the gas valve increases the differential gas pressure moving the gas diaphragm to the right until balance is restored and the flow supplied by the pump is once again identical to thereturn flow through the regulator bypass. Unlike conventional direct acting regulators, the SKP55 servo operated regulating system displays virtually zero droop (offset) across the turndown range.SKP55 U.. Air/Gas Ratio Controlling Actuators Technical Instructions Document No. 155-753July 9, 2014Siemens Building Technologies, Inc. Page 5Operation, ContinuedNote: The SKP55 /VG is a 1:1 differential pressure air/gas ratio controller. Thismeans that the control adjusts the same pressure difference on the gas side as it senses on the air side. Any other gas to air ratio adjustment will require amodification to one of the restrictions or the installation of an adjustable orifice (this is normally an adjustable metering orifice in the gas line). For this purpose the VG gas valve with manual operation kit AGA61 may be used. See gas valve Technical Instructions 155-512P25. Many burner designs, because of reduced mixing energy at the low fire level, require somewhat more air at low fire in order to maintain optimum combustion parameters. To accommodate this requirement the SKP55 incorporates a bias adjustment, which allows the characteristic of the regulator to be displaced either towards excess air or reduced air. Pressure fluctuations in the combustion chamber do not influence the performance of the SKP55 air/gas ratio controller. There is no need for any compensation circuit. NOTES: 1. For optimal performance, both the air damper and SKP55 /VG gasvalve must be installed upstream of its pressure differential orifice. For other layouts please consult your authorized Siemens Building Technologies Combustion Products sales representative.2. To avoid oscillation, do not oversize the VG valves. (See TechnicalInstructions 155-512P25.)InstallationTechnical Instructions SKP55 U.. Air/Gas Ratio Controlling ActuatorsDocument No. 155-753 July 9, 2014Page 6 Siemens Building Technologies, Inc.Installation, ContinuedNOTES:1. Wiring must meet all local electrical codes.2. All pressure connection pipes must be at least 1/4-inch inside diameter.The pressure pick-up connections must be flush with the inner wall of the pipe or housing in order to sense turbulence-free pressures. The pressure pick-up connections should be located at least five pipe diameters downstream of the valve, damper, elbow, coupling, orifice, or other flow disturbing fitting. Do not use the taps on the valve body for gas connection to the regulator since these places may show turbulence. The pressure connection pipes should be as short as possible to allow the regulator to react to sudden changes.In cases where it is not possible to install an orifice in the air line, (e.g., lack of available air pressure) the SKP55 actuator may be connected to the air pressure upstream of the burner and the combustion chamber pressure, using the pressure differential across the burner orifice. This arrangement is not applicable to installations utilizing combustion air preheating systems.1 Adjustment of the bias2 Connection for the air pressure (+) sensing line3 Connection for the air pressure (-) sensing line4 Connection for the gas pressure (-) sensing line5 Connection for the gas pressure (+) sensing line6 Stroke indicationFigure 2. Connections and Adjustments.SKP55 U.. Air/Gas Ratio Controlling Actuators Technical Instructions Document No. 155-753July 9, 2014Siemens Building Technologies, Inc. Page 7Start-UpRegulator (See Figures 1, 2 and 3)1. The setting screw 1 on the SKP55 is factory-adjusted so that the gas to air ratiocurve intersects the zero point (no bias). If required, on-site adjustment may be achieved as follows:• Turn setting screw 1 counterclockwise until spring becomes completely loose. • Shut off gas supply upstream of the SKP55 actuator.• Make sure that there is no air pressure working on the SKP55 actuator. • Apply power to the SKP55 actuator.•Turn the setting screw clockwise until valve starts to open.2. Set the adjustable orifice to the pre-calculated value so that equal pressure differenceon both air and gas side results in approximate stoichiometric combustion. 3. Start the burner and run it at approximately 90% capacity by opening the air damper. 4. Measure the combustion values and correct the flow using the adjustable orifice untiloptimum values are obtained. 5. Return to low fire position by closing the air damper and check the combustion values.If necessary, correct the working characteristic until optimum values are obtained by rotating the setting screw 1. To obtain more gas: rotate clockwise. To obtain less gas: rotate counter-clockwise. 6. Limit the low fire air damper position. 7. If a substantial bias of the working characteristic was needed the adjustment of the90% position must be checked and corrected, if necessary, by adjusting the orifice. Repeat the procedure from Step 3. 8. Run the burner to the required high fire position and limit the air damper position. 9. Check flue gas values at several intermediate output levels. If corrections arenecessary, note:• At high fire, correct with the adjustable orifice•At low fire, correct with setting screw 1 on the SKP55 actuator.Figure 3. Adjustments.Technical Instructions SKP55 U.. Air/Gas Ratio Controlling ActuatorsDocument No. 155-753 July 9, 2014Page 8 Siemens Building Technologies, Inc.Start up,ContinuedSKP55 U Air/Gas Ratio Controlling Actuators Technical InstructionsDocument No. 155-753July 9, 2014 Information in this publication is based on current specifications. The company reserves the right to make changes in specifications and models as design improvements are introduced. Other product or company names mentioned herein may be the trademarks of their respective owners.© 2005 Siemens Building Technologies, Inc.SCC Inc.1250 Lunt AvenueElk Grove Village, IL 60007 U.S.A. Your feedback is important to us. If you havecomments about this document, please sendthem to *****************************Document No. 155-753Country of Origin: USPage 9Dimensions(Dimensions in inches;millimeters in parentheses.)GAFigure 4. SKP55)U.. Dimensions.。
AMESim 泵阀协调控制电动静液作动器方案分析

/tractate_show.asp?D_ID=248 (1 of 6)2008-11-16 18:17:47
该方案与典型的EHA 系统结构上的不同之处在于: ①用补油环节代替了蓄能器(增压油箱),补油泵的出口压 力设置为系统最高工作压力的一半; ②引入了TPCV, 使作动筒的两腔均为控制腔,提高了系统的频响. 同时由于 该方案本身是容积控制系统还具有较高的效率.
该方案对比前面两种方案来说, TPCV 为自动调节, 控制相对简单. 但该阀的加工制造是难点,而且其性能好 坏将直接影响该方案的响应性能. 2 各方案的仿真分析
摘 要: 针对典型的EHA (Electro-Hydrostatic Actuator)系统存在的频响较低的问题,为了兼顾作动系统的效率 和频响,将控制阀引入了EHA系统,提出了3种泵阀协调控制的EHA方案,分别是:采用EHSV (Electro-Hydraulic Servo Valve)的EHA 系统,采用DDV (Direct Drive Valve)的EHA 系统以及采用TPCV (Total Pressure Control Valve)的EHA 系统. 阐述了这3种方案的系统组成及工作原理,采用AMESim 对这3种方案及典型的 EHA 进行了仿真对比分析. 从仿真结果可以看出:泵阀协调控制的EHA 系统可以大大提高系统的频响,同时还 具有较高的效率. 作为3种过渡方案,将对目前机载电动静液作动系统的研制具有实际指导意义. 关 键 词: 功率电传; 电动静液作动器; 泵阀协调控制; 电液伺服阀; 直接驱动阀; 总压力控制阀 中图分类号: V 245. 1; TH 137 文献标识码:A 文章编号: 100125965 (2008) 02-0131-04 基金项目: 国家自然科学基金资助项目(50675009) 作者简介: 齐海涛(1981-),男,山东淄博人,博士生, haitao8642@163. com.
智能基础设施电液阀值电机4561说明书

4561Electrohydraulic actuators for valveswith a 20 mm stroke SKD32.. SKD82.. SKD62.. SKD60..•SKD32.. Operating voltage AC 230 V, 3-position control signal•SKD82.. Operating voltage AC 24 V, 3-position control signal•SKD6.. Operating voltage AC 24 V, control signal DC 0…10 V, 4…20 mA or0...1000 Ω•SKD6.. Choice of flow characteristic, position feedback, stroke calibration,LED status indication, override control•SKD62UA w ith functions choice of direction of operation, stroke limit control,sequence control with adjustable start point and operating range,operation of frost protection monitors QAF21.. and QAF61..•Positioning force 1000 N•Actuator versions with or without spring-return function•For direct mounting on valves; no adjustments required•Manual adjuster and position indicator•Optional functions with auxiliary switches, potentiometer, stem heater andmechanical stroke inverter•SKD..U are UL-approvedCM1N4561en2/20UseFor the operation of Siemens 2-port and 3-port valves, types VVF.., VVG.., VXF.. and VXG.. with a 20 mm stroke as control and safety shut-off valves in heating, ventilation and air conditioning systems.Types1) Approbation: CE 3)Direction of operation, stroke limit control, sequence control, signal addition2)Approbation: CE, ULWhen ordering please specify the quantity, product name and type code. Example: 1 actuator, type SKD32.50 and 1 potentiometer, type ASZ7.3 and 1 dual auxiliary switches ASC9.3The actuator, valve and accessories are supplied in separate packaging and not assembled prior to delivery.See overview, section «Replacement parts», page 19.AccessoriesOrderingDeliverySpare parts3/20Equipment combinationsFor admissible differential pressures ∆p max and closing pressures ∆p s , refer to the relevant valve data sheets. 1)Valves are phased-outThird-party valves with str okes between 6…20 mm can be motorized, provided they are «closed with the de-energized» fail-safe mechanism and provided that the necessary mechanical coupling is available. For SKD32.. and SKD82.. the Y1 signal must be routed via an additional freely-adjustable end switch (ASC9.3) to limit the stroke.We recommend that you contact your local Siemens office for the necessary information.Overview table, see page 20.Technology1 Manual adjuster2 Pressure cylinder3 Suction chamber4 Return spring5 Solenoid valve6 Hydraulic pump7 Piston8 Pressure chamber 9 Position indicator (0 to 1) 10 Coupling 11 Valve stem 12 Plug Valve closed Valve openNoteRev. no. Principle ofelectro-hydraulic actuators4/20The hydraulic pump (6) forces oil from the suction chamber (3) to the pressure chamber (8) and thereby moving the pressure cylinder (2) downwards. The valve stem (11) retracts and the valve opens. Simultaneously the return spring (4) is compressed. Activating the solenoid valve (5) allows the oil in the pressure chamber to flow back into the suction chamber. The compressed return spring moves the pressure cylinder upwards. The valve stem extends and the valve closesTurning the manual adjuster (1) clockwise moves the pressure cylinder downwards and opens the valve. Simultaneously the return spring is compressed.In the manual operation mode the control signals Y and Z can further open the valve but cannot move to the «0%» stroke position of the valve. To retain the manually set position, switch off the power supply or disconnect the control signals Y and Z. The red indicator marked «MAN» is visible.When setting the controller for a longer time period to manual operation, werecommend adjusting the actuator with the manual adjuster to the desired position. This guarantees that the actuator remains in this position for that time period. Attention: Do not forget to switch back to automatic operation after the controller is set back to automatic control.Turn the manual adjuster counterclockwise to the end stop. The pressure cylinder moves upward to the «0%» stroke position of the valve. The red indicator marked «MAN» is no longer visible.The actuator can manually be adjusted to a stroke position > 0 % allowing its use in applications requiring constantly a minimal volumetric flow.The SKD32.51, SKD32.21, SKD82.51.. and SKD62.. actuators, which feature a spring-return function, incorporate a solenoid valve which opens if the control signal or power fails. The return spring causes the actuator to move to the «0 %» stroke position and closes the valve.The actuator is controlled by a 3-position signal either via terminals Y1 or Y2 and generates the desired stroke by means of above described principle of operation. • Voltage on Y1 piston extends valve opens • Voltage on Y2 piston retracts valve closes • No voltage on Y1 and Y2 piston / valve stem remain in the respective positionThe valve is either controlled via terminal Y or override control Z. The positioning signal Y generates the desired stroke by means of above described principle of operation. • Signal Y increasing: piston extends valve opens • Signal Y decreasing: piston retracts valve closes • Signal Y constant: piston / valve stem remain in the respective position • Override control Z see description of override control input, page 8A frost protection thermostat can be connected to the SKD6.. actuator. The added signals from the QAF21.. and QAF61.. require the use of SKD62UA actuators. Notes on special programming of the electronics are described under «Enhanced electronics» on page 5.«Connection diagrams» for operation with frost protection thermostat or frost protection monitor refer to page 16.Opening the valveClosing the valveManual operation modeNote: Controller in manual operationAutomatic modeMinimal volumetric flow Spring-return facilitySKD32../SKD82..3-position control signalSKD62.., SKD60.. Y control signal DC 0...10 V and/orDC 4...20 mA, 0…1000 ΩFrost protection monitorFrost protectionthermostat5/201 Connection terminals2 Mode DIL switches3 LED status indication4 Slot for calibration0163811Connection terminals 2 DIL switches 3 LED status indication4 Stroke calibration 5Rotary switch Up (factory setting 0) 6Rotary switch Lo420 mAStandard electronics SKD62.., SKD60..DIL switches SKD62.., SKD60..Enhanced electronics SKD62UADIL switches SKD62UA6/20• With normally-closed valves, «direct-acting» means that with a signal input of 0 V, the valve closes (applies to all Siemens valves listed under «equipment combinations» on page 3)• With normally-open valves, «direct-acting» means that with a signal input of 0 V, the valve is open.100 %0 %4 mA 0 Ω20 mA 1000 ΩThe mechanical spring-return function is not affected by the direction of operation selected.Selection of direction of operation SKD62UANote7/20Prerequisites• • Actuator must be in «Automatic operation» enabling stroke calibration to capture the effective 0 % and 100 % values • AC 24 V power supply • Housing cover removed Calibration1. Short-circuit contacts in calibration slot (e.g. with a screwdriver)2. Actuator moves to «0 %» stroke position (1) (valve closed)3. Actuator moves to «100 %» stroke position (2) (valve open)4.Measured values are storedgreen LED flashes; position feedback U inactiveA lit red LED indicates a calibration error.The calibration can be repeated any number of times.Stroke limit control and sequence control SKD62UAStroke control withQAF21.. / QAF61.. signal addition SKD62UA onlyCalibrationSKD62.., SKD60..8/20The LED status indication indicates operational status with dual-colored LED and is visible with removed cover.LED Indication FunctionRemarks, troubleshootingGreen LitNormal operationAutomatic operation; everything o.k.FlashingCalibration in progressWait until calibration is finished (LED stops flashing, green or red LED will be lit) RedLitFaulty stroke calibration Check mountingRestart stroke calibration (by short-circuiting calibration slot)Internal errorReplace electronics FlashingInner valve jammed Check valveBothDarkNo power supply Electronics faultyCheck mains network, check wiring Replace electronicsAs a general rule, the LED can assume only the states shown above (continuously red or green, flashing red or green, or off).Override control input can be operated in following different modes of operationZ-modeno functionfully openclosedoverride with 0…1000 ΩSignal addition SKD62UA onlyC o n n e c t i o n sT r a n s f e r linear or equal-percentagelinear or equal-percentagelinear or equal-percentage• Z-contact not connected • Valve stroke follows Y-input• Z-contact connected directly to G • Y-input has no effect • Z-contact connected directly to G0 • Y-input has no effect • Z-contact connected to M via resistor R • Starting position at50 Ω / end position at 900 Ω• Y-input has no effect • Z-contact is connected to R ofthe frost protection monitor QAF21.. or QAF61.. • Valve stroke followssignals Y and R(Z)Shown operation modes are based on the factory setting «direct acting» Y-input has no effect in Z-mode.Indication of operating state SKD62.., SKD60..Override control input ZSKD62.., SKD60..Note9/20Accessories ASZ6.6 (S55845-Z108) stem heater• for media below 0 °C• mount between valve and actuatorASC9.3double auxiliary switchASZ7.3potentiometerASK50stroke inverter4561Z 05005154561Z 10adjustable switching points0…1000 Ω0 % actuator stroke corresponds to 100 % valve stroke; mount between valve and actuatorFor the combination SIMATIC S5/S7 and position feedback message, we recommend actuators with DC 0…9.8 V feedback signals.The signal peaks that occur in the potentiometer ASZ7.3 may result in error messages on Siemens SIMATIC.This is not the case when combined with Siemens HVAC controllers.The reason is that SIMATIC has a higher resolution and faster response time.ASC1.6auxiliary switchswitching point 0…5 % strokeSee section «Technical data» on page 13 for more information.SKD..SKD32.., SKD82..Note: ASZ7.3SKD62.., SKD60..10/20Engineering notesConduct the electrical connections in accordance with local regulations on electrical installations as well as the internal or connection diagrams.Safety regulations and restrictions designed to ensure the safety of people and property must be observed at all times!The plant operator must also ensure compliance with applicable guidelines on cable insulation when using a safety limiter. Failure to comply may cause the safety limiter function to fail.For media below 0 °C the ASZ6.6 stem heater is required to keep the valve from freezing. For safety reasons the stem heater is designed for an operating voltage of AC 24 V / 30 W.For this case, do not insulate the actuator bracket and the valve stem, as air circulation must be ensured. Do not touch the hot parts without prior protective measures to avoid burns.Non-observance of the above may result in accidentsand fires!Recommendation: Above 140 °C insulating the valves is strictly recommended.Observe admissible temperatures, refer to «Use» on page 2 and «Technical data» on page 13.If an auxiliary switch is required, its switching point should be indicated on the plant schematic.Every actuator must be driven by a dedicated controller (refer to«Connection diagrams», page 16).11/20Mounting instructionsMounting Instruction 74 319 0325 0 for fitting the actuator to the valve are by packed in the actuator packaging. The instructions for accessories are enclosed with the accessories themselves.Commissioning notesWhen commissioning the system, check the wiring and functions, and set any auxiliary switches and potentiometers as necessary, or check the existing settings. Coupling fully retracted→stroke = 0%Coupling fully extended→ stroke = 100 %The manual adjuster must be rotated counterclockwise to the end stop, i.e. until the red indicator marked «MAN» is no longer visible. This causes the Siemens valves, types VVF.., VVG.., VXF.. and VXG.. to close (stroke = 0%).Manual operation «M A N»Automatic operation« A U T O »Orientation12/20Maintenance notesThe SKD.. actuators are maintenance-free.When servicing the actuator:• Switch off pump of the hydronic loop• Interrupt the power supply to the actuator • Close the main shutoff valves in the system• Release pressure in the pipes and allow them to cool down completely • If necessary, disconnect electrical connections from the terminals• The actuator must be correctly fitted to the valve before recommissioning. Recommendation SKD6..: trigger stroke calibration.«Replacement parts», see page 19.A damaged housing or cover represents an injury risk• NEVER uninstall an actuator from the valve• Uninstall the valve-actuator combination (actuating device) as a complete device• Use only properly trained technicians to uninstall the unit• Send the actuating device together with an error report to your local Siemens representative for analysis and disposal• Properly mount the new actuating device (valve and actuator)Parts could fly ultimately resulting in injuries from uninstalling an actuator with a damaged valve housing due to the tensioned return spring.DisposalWarrantyTechnical data on specific applications are valid only together with Siemens products listed under "Equipment combinations", page 3. Siemens rejects any and all warranties in the event that third-party products are used.RepairTechnical dataPower supplySignal inputsPositionfeedbackElectricalconnectionsStandards,directives andapprovals13/2014/20Environmental compatibilityDimensions / weightMaterialsThe documents can be downloaded from /bt/download .Accessories ASC1.6 ASC9.3 double ASZ7.3 Potentiometer ASZ6.6 stem heaterSKD62UA enhanced functionsDirection of operationDirect-acting, reverse-actingDC 0...10 V / DC 10...0 V DC 4...20 mA / DC 20...4 mA 0...1000 Ω / 1000...0 Ω Stroke limit control Range of lower limit Range of upper limit 0...45 % adjustable 100...55 % adjustable Sequence controlTerminal YStarting point of sequence Operating range of sequence0...15 V adjustable 3...15 V adjustable Signal additionZ connected to R ofFrost protection monitor QAF21.. Frost protection monitor QAF61..0...1000 Ω, added to Y signal DC 1.6 V, added to Y signalAmbient conditions and protection dataClassification to IEC/EN 60730 Automatic action: Type 1AA / Type 1AC / Modulation Action Pollution degree: 2Housing protection as perIEC/EN 60529IP54 Environmental conditionsTransportation(in transport packaging) to IEC/EN 60721-3-2 Class 2K3Temperature -30...65 °CHumidity 5...95 % (no condensation)Operationto IEC/EN 60721-3-3 Class 3K5Temperature -15...50 °CHumidity 5...95 % (no condensation)Storageto IEC/EN 60721-3-1 Class 1K3Temperature -15...50 °CHumidity 5...95 % (no condensation)Internal diagramsSKD32.51, SKD32.21 AC 230 V, 3-PositionCm1end switchn solenoid valve for spring-returnc1, c2ASC9.3 double auxiliaryswitcha, b, c ASZ7.3 potentiometerY1Positioning signal «open»Y2Positioning signal «close» 21spring-return functionN neutral conductorSKD32.50AC 230 V, 3-PositionY2Positioning signal «close»21spring-return functionG System potentialSKD82.50AC 24 V, 3-PositionSKD60, SKD60U,SKD62,SKD62U, SKD62UAAC 24 V, DC 0…10 V,4…20 mA, 0…1000 ΩU position indicationZ override controlY positioning signalM measuring neutralG0operating voltage AC 24 V:system neutral (SN)G operating voltage AC 24 V:system potential (SP)Switching without power asa spring return function15/2016/20Connection terminals U ZG 0G Y M operating voltage AC 24 V: system neutral (SN) operating voltage AC 24 V: system potential (SP)Positioning signal DC 0...10 (30) V or DC 4...20 mA Measuring neutral (= G0)Position indication DC 0...10 V or DC 4...20 mAOverride control (functionality see page 8)Connection diagrams SKD32.21, SKD32.51SKD32.50F1 safety limiter (eg.temperature limiter) N1, N2 controller Y1, Y2actuatorsL Phase N neutralY1 Positioning signal «open» Y2 Positioning signal «close» 21Spring-return functionSKD6..Auxiliary switch ASC1.6SKD32.. AC 230 V 3-Position17/20SKD82.51, SKD82.51USKD82.50, SKD82.50USNSPSNSPSNSPSPAC 24 VF1 safety limiter (eg temperature limiter) N1, N2 controller Y1, Y2 actuators SP Systempotential AC 24 V SN System neutral (Y1), (Y2) controller contactsY1 Positioning signal «open» Y2 Positioning signal «close» 21 Spring-return functionSKD60SKD60USKD82.. AC 24 V 3-PositionSKD6..AC 24 VDC 0…10 V, 4…20 mA, 0…1000 Ω18/20SKD62 SKD62U SKD62UAY1 actuator N1 controllerF1 safety limiter (eg temperature limiter) F2frost protection thermostatterminals: 1 – 2 frost hazard / sensor is interrupted (thermostat closes with frost) 1 – 3 normal operation F3 Temperature detector F4 Frost protection monitor with 0…1000 Ω signal output, e.g. QAF21.. or QAF61.. (only SKC62UA) * G (SP) System potential AC 24 V G0 (SN) System neutral* Only with sequence control and the appropriate selector switch settings (see page 5ff)When using the safety limiter F1, ensure that no mistakes may occur on cableinsulation that may cancel out the temperature limiter function (applies to both 230 V as well as 24 V types).For SN earthing (e.g. PELV) comply under all circumstances with the note above.19/20DimensionsAll dimensions in mm*Height of actuator from valve plate without stroke inverter ASK50 = 300 mm Height of actuator from plate with stroke inverter ASK50 = 357 mm** SKD..U with knockouts for standard ½" conduit connectors (Ø 21.5 mm) ► = >100 mm ⎧ Minimum clearance from ceiling or wall for mounting, ►► = >200 mm ⎩ connection, operation, maintenance etc.20*109,535444456,5108181,580∅∅4561M 02* Maximum stroke = 20 mmReplacement partsOrder numbers for replacement partsCoverHand control 1)Control unitActuator typeSKD32.50 410456348 426855048 SKD32.51 410456348 426855048 SKD32.21 410456348 426855048 SKD82.50 410456348 426855048 SKD82.50U 410456348 426855048 SKD82.51 410456348 426855048 SKD82.51U 410456348 426855048SKD62 410456348 426855048 466857488 SKD62U 410456348 426855048 466857488 SKD60 410456348 426855048 466857598 SKD60U 410456348 426855048 466857598 SKD62UA4104563484268550484668575181)hand control, blue with mechanical partsASK50 stroke inverterRevision numbersPublished by:Siemens Switzerland Ltd. Building Technologies Division International Headquarters Gubelstrasse 226301 ZugSwitzerlandTel. +41 58-724 24 24/buildingtechnologies© Siemens Switzerland Ltd 1998 Delivery and technical specifications subject to change20/20。
- 1、下载文档前请自行甄别文档内容的完整性,平台不提供额外的编辑、内容补充、找答案等附加服务。
- 2、"仅部分预览"的文档,不可在线预览部分如存在完整性等问题,可反馈申请退款(可完整预览的文档不适用该条件!)。
- 3、如文档侵犯您的权益,请联系客服反馈,我们会尽快为您处理(人工客服工作时间:9:00-18:30)。
∗ JKU † Austrian
HOERBIGER Research Institute for Smart Actuators, Linz, Austria Center of Competence in Mechatronics (ACCM), Linz, Austria
978-1-4673-1301-8/12/$31.00 ©2012 IEEE 511
life cycle [1]. A brief literature review shows many different ways to calculate the temperature distribution of a machine. They can be classified in three main groups: The first possibility is the method of Finite Elements (FEM) [2]. It allows parameterized modeling but in general the effort to create and simulate the model is time consuming, especially if 3D models are used. On the other hand these models have the advantage to allow the coupling of thermal and electro-magnetical issues. The second group of models solve the thermal differential equations analytically. These analytical results directly show the dependency of the parameters and therefore give the maximum possible insight into the geometrical influences on the temperature distribution. Unfortunately the differential equations can be directly solved only for very simple geometries. This strongly limits the usability of such models. The third and biggest group is positioned between the previously described ones and uses an electrical network representation for modeling the thermal behavior. The challenge is here to define the parameters of the elements of the equivalent circuit (i.e. resistors, capacitors, ...). However the results for both transient and steady state analysis can easily be obtained. Now different kinds of models can be realized using electric networks which depict mathematically lumped parameter models because of their discretized spatially calculated properties. On the one hand there are geometrically distributed parameter models [3], [4] and on the other hand there are geometrically lumped descriptions [5], [6], [7], [8], [9]. Latter models outline a system by showing only parameters for summarized parts. For example to model an electrical motor parts like the stator, rotor, etc. are identified and represented by equivalent resistors and capacitors for each part. The major disadvantage of geometrically lumped models is that further assumptions have to be made because the system of equations is often under-determined. On the other hand an advantage is the use in combination with real time estimation of temperature for integration in feed-backward control strategies because of its fast speed [8]. Lumped parameter models with geometrically distributed elements are often found for calculation of thermal
Abstract—In highly exploited and integrated mechatronic systems the thermal design and management defines the maximum load case. The trend to move to higher power densities needs precise andห้องสมุดไป่ตู้reliable thermal models of electrical machines to determine the limits of new and thermally demanding use cases and/or gives design guidelines for future generations of the product. For the electro-hydraulic system investigated in this paper a mathematically lumped parameter model with geometrically distributed elements has been developed. The thermal properties of the elements are calculated with physical material properties according to their geometric sizes. This allows to implement a comfortable parameterized interface that facilitates an easy change of geometrical dimensions and material properties. Moreover sub-sections of the system can be grouped which allows modularized modeling - this possibility shows its strength when an electrical sub-system is combined with a hydraulic sub-system. Together with automated model generation the resulting SPICE model is well suited for parameterized optimization. The model applies to both transient and/or steady state temperature including the effects of heat radiation and air convection. Thus, fast and accurate calculation of the temperature distribution and heat flow is possible and has been validated by measurements on a test rig. Index Terms—electric network, electro-hydraulic actuator, geometrically distributed elements, lumped parameter model, thermal model.
I. I NTRODUCTION Along with advancing power density and optimization the temperature distribution in an electro-hydraulical system gains importance. However it is mainly not the overall thermal behavior of a system that limits the performance, but the temperature at specific points or in specific areas. These areas contain components or materials with a defined maximum operating temperature which limits the safe operational area of the system. In the demand to increase the operational area it is crucial to understand not only the thermal distribution but also the interconnections of the involved subsystems. The main focus rests here on the calculation of the temperature distribution in the electrical, mechanical or hydraulic sub-systems due to internal heat losses. Since the beginning of the developement of electrical machines it is recognized that an efficient cooling of a system/machine is absolutely necessary to maintain its