生产现场管理创新
工地现场创新管理制度
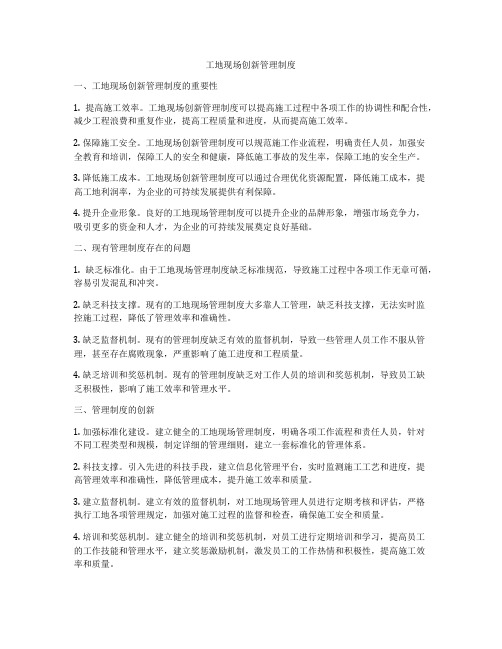
工地现场创新管理制度一、工地现场创新管理制度的重要性1. 提高施工效率。
工地现场创新管理制度可以提高施工过程中各项工作的协调性和配合性,减少工程浪费和重复作业,提高工程质量和进度,从而提高施工效率。
2. 保障施工安全。
工地现场创新管理制度可以规范施工作业流程,明确责任人员,加强安全教育和培训,保障工人的安全和健康,降低施工事故的发生率,保障工地的安全生产。
3. 降低施工成本。
工地现场创新管理制度可以通过合理优化资源配置,降低施工成本,提高工地利润率,为企业的可持续发展提供有利保障。
4. 提升企业形象。
良好的工地现场管理制度可以提升企业的品牌形象,增强市场竞争力,吸引更多的资金和人才,为企业的可持续发展奠定良好基础。
二、现有管理制度存在的问题1. 缺乏标准化。
由于工地现场管理制度缺乏标准规范,导致施工过程中各项工作无章可循,容易引发混乱和冲突。
2. 缺乏科技支撑。
现有的工地现场管理制度大多靠人工管理,缺乏科技支撑,无法实时监控施工过程,降低了管理效率和准确性。
3. 缺乏监督机制。
现有的管理制度缺乏有效的监督机制,导致一些管理人员工作不服从管理,甚至存在腐败现象,严重影响了施工进度和工程质量。
4. 缺乏培训和奖惩机制。
现有的管理制度缺乏对工作人员的培训和奖惩机制,导致员工缺乏积极性,影响了施工效率和管理水平。
三、管理制度的创新1. 加强标准化建设。
建立健全的工地现场管理制度,明确各项工作流程和责任人员,针对不同工程类型和规模,制定详细的管理细则,建立一套标准化的管理体系。
2. 科技支撑。
引入先进的科技手段,建立信息化管理平台,实时监测施工工艺和进度,提高管理效率和准确性,降低管理成本,提升施工效率和质量。
3. 建立监督机制。
建立有效的监督机制,对工地现场管理人员进行定期考核和评估,严格执行工地各项管理规定,加强对施工过程的监督和检查,确保施工安全和质量。
4. 培训和奖惩机制。
建立健全的培训和奖惩机制,对员工进行定期培训和学习,提高员工的工作技能和管理水平,建立奖惩激励机制,激发员工的工作热情和积极性,提高施工效率和质量。
安全生产管理中的创新实践案例有哪些

安全生产管理中的创新实践案例有哪些在当今复杂多变的生产环境中,安全生产管理至关重要。
为了保障员工的生命安全和企业的可持续发展,各行业不断探索和实践创新的安全生产管理方法。
以下为您介绍一些具有代表性的创新实践案例。
一、智能化安全监控系统的应用某大型制造企业引入了智能化的安全监控系统。
该系统通过在生产现场安装高清摄像头、传感器等设备,实时采集图像、声音、温度、湿度等数据。
这些数据被传输到中央处理平台,利用人工智能和大数据分析技术进行处理和分析。
一旦系统检测到异常情况,如火灾隐患、设备故障、人员违规操作等,会立即发出警报,并将相关信息推送给安全管理人员和现场负责人。
这使得安全问题能够被及时发现和处理,大大降低了事故发生的可能性。
例如,在一次设备运行过程中,系统监测到温度异常升高,迅速发出警报。
维修人员及时赶到,发现是一个关键部件的润滑不足导致摩擦过热。
由于发现及时,避免了设备损坏和可能引发的生产事故。
二、虚拟现实(VR)安全培训一家建筑公司采用了虚拟现实技术进行安全培训。
员工们戴上 VR头盔,身临其境地体验各种危险场景,如高处坠落、物体打击、触电等。
这种培训方式相比传统的课堂讲解和视频演示更加直观和生动。
员工能够亲身体验危险的后果,从而深刻理解安全操作规程的重要性,增强自我保护意识。
在一次新员工培训中,一名员工通过 VR 体验了高处坠落的场景,事后他表示:“那种失重和恐惧的感觉太真实了,让我明白了在高处作业时必须严格遵守安全规定。
”三、移动安全管理应用程序某化工企业开发了一款移动安全管理应用程序。
员工可以通过手机随时随地访问安全相关的信息,如安全制度、操作规程、应急预案等。
同时,员工还可以利用该应用程序进行日常的安全检查和隐患上报。
发现问题后,只需拍照并填写相关信息,即可提交给管理部门。
管理部门能够快速做出响应和处理,提高了隐患排查和整改的效率。
有一次,一名巡检工人在车间发现了一处管道泄漏,他立即通过应用程序上报。
施工现场安全管理创新做法
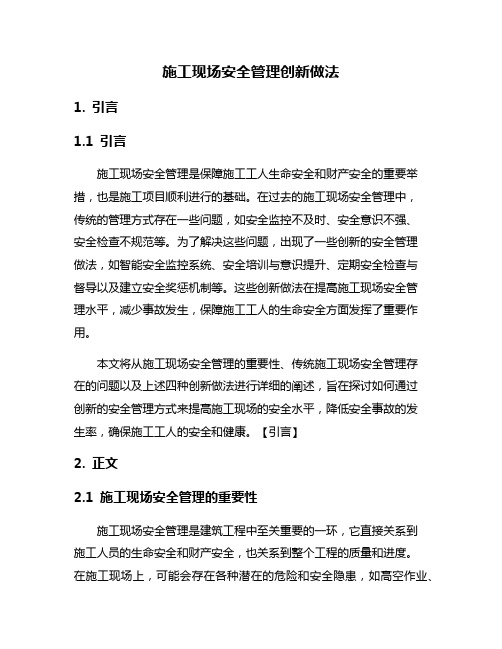
施工现场安全管理创新做法1. 引言1.1 引言施工现场安全管理是保障施工工人生命安全和财产安全的重要举措,也是施工项目顺利进行的基础。
在过去的施工现场安全管理中,传统的管理方式存在一些问题,如安全监控不及时、安全意识不强、安全检查不规范等。
为了解决这些问题,出现了一些创新的安全管理做法,如智能安全监控系统、安全培训与意识提升、定期安全检查与督导以及建立安全奖惩机制等。
这些创新做法在提高施工现场安全管理水平,减少事故发生,保障施工工人的生命安全方面发挥了重要作用。
本文将从施工现场安全管理的重要性、传统施工现场安全管理存在的问题以及上述四种创新做法进行详细的阐述,旨在探讨如何通过创新的安全管理方式来提高施工现场的安全水平,降低安全事故的发生率,确保施工工人的安全和健康。
【引言】2. 正文2.1 施工现场安全管理的重要性施工现场安全管理是建筑工程中至关重要的一环,它直接关系到施工人员的生命安全和财产安全,也关系到整个工程的质量和进度。
在施工现场上,可能会存在各种潜在的危险和安全隐患,如高空作业、机械设备操作、电气作业等,如果没有科学合理的安全管理措施,就会极大地增加事故发生的风险。
保障施工现场的安全管理,不仅可以有效预防事故的发生,减少人员伤亡和财产损失,还可以提高施工效率和工程质量。
一个安全管理良好的施工现场,能够让工人们更加专注地投入到工作中,减少因为安全问题而造成的工作中断,从而提高整体的工作效率。
做好施工现场的安全管理工作,也是公司形象的体现。
一个安全管理良好,没有事故发生的工地,会给客户和社会一个良好的印象,提升公司的信誉和竞争力。
施工现场安全管理的重要性不言而喻,只有加强安全管理意识,做好各项安全管理工作,才能有效地保障施工现场的安全。
2.2 传统施工现场安全管理存在的问题1. 安全意识不强:在传统的施工现场中,很多工人和管理人员对安全意识的重视程度不够高。
他们往往认为安全管理是一种形式主义,只是为了符合规定而已,缺乏真正的安全意识。
生产管理创新思路(3篇)
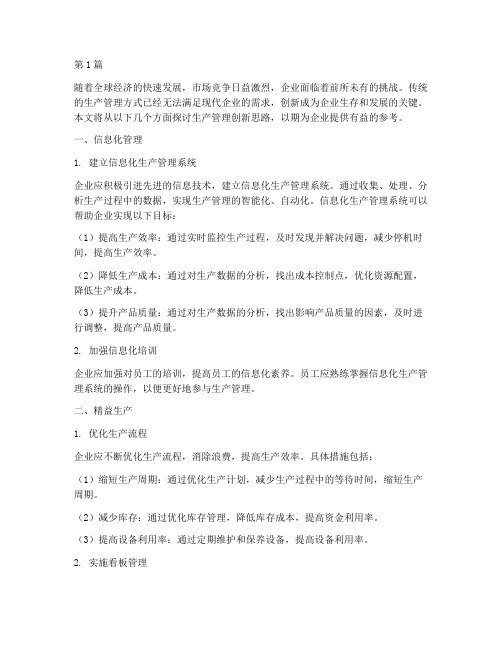
第1篇随着全球经济的快速发展,市场竞争日益激烈,企业面临着前所未有的挑战。
传统的生产管理方式已经无法满足现代企业的需求,创新成为企业生存和发展的关键。
本文将从以下几个方面探讨生产管理创新思路,以期为企业提供有益的参考。
一、信息化管理1. 建立信息化生产管理系统企业应积极引进先进的信息技术,建立信息化生产管理系统。
通过收集、处理、分析生产过程中的数据,实现生产管理的智能化、自动化。
信息化生产管理系统可以帮助企业实现以下目标:(1)提高生产效率:通过实时监控生产过程,及时发现并解决问题,减少停机时间,提高生产效率。
(2)降低生产成本:通过对生产数据的分析,找出成本控制点,优化资源配置,降低生产成本。
(3)提升产品质量:通过对生产数据的分析,找出影响产品质量的因素,及时进行调整,提高产品质量。
2. 加强信息化培训企业应加强对员工的培训,提高员工的信息化素养。
员工应熟练掌握信息化生产管理系统的操作,以便更好地参与生产管理。
二、精益生产1. 优化生产流程企业应不断优化生产流程,消除浪费,提高生产效率。
具体措施包括:(1)缩短生产周期:通过优化生产计划,减少生产过程中的等待时间,缩短生产周期。
(2)减少库存:通过优化库存管理,降低库存成本,提高资金利用率。
(3)提高设备利用率:通过定期维护和保养设备,提高设备利用率。
2. 实施看板管理看板管理是一种以视觉信号为主要手段的生产管理方法。
企业应实施看板管理,使生产现场一目了然,及时发现并解决问题。
三、绿色生产1. 节能减排企业应注重节能减排,降低生产过程中的能源消耗和污染物排放。
具体措施包括:(1)采用节能设备:选用节能、环保的生产设备,降低能源消耗。
(2)优化生产工艺:改进生产工艺,降低污染物排放。
(3)加强环保管理:建立健全环保管理制度,加强环保设施建设。
2. 循环经济企业应积极发展循环经济,实现资源的循环利用。
具体措施包括:(1)回收利用废弃物:对生产过程中的废弃物进行回收利用,降低资源浪费。
创新现场管理的六大平台文档

创新现场管理的六大平台企业生产作业现场,是产品的诞生地,是三个文明建设的结合点,是企业文化建设的一项基础性工作,也是一项永久性“52程”。
如何经营企业生产作业现场,全过程管理到位,进而创造一方和谐环境?福建省三钢(集团)有限责任公司(以下简称三钢)按照科学发展观的要求,针对冶金企业环境条件差,生产作业现场“老面孔”,不断完善作业现场管理,以创新为抓手,营造和谐、安全、文明、有序、洁净、美化的生产作业环境。
一、以完善物流管理和强化保洁为平台,改善生产作业环境在生产作业场,物品的日常流动方向、流动数量、流动时间,既有规律性,也有不确定性;为了改善现场作业环境,必须对日常流动物品实施定置管理。
三钢作为大型钢铁联合企业,生产过程物流量大,且多数原料呈粉状和小块状;废渣、粉尘等伴生物多,导致环境治理工作量大,现场管理难度也大。
三钢占地面积仅2.72平方千米,为有效利用生产作业现场资源,将完善物流管理和日常保洁作为现场管理的平台,有效地促进了生产作业环境建设。
首先,制定物流管理规则,对生产现场定置图绘制、区域划分、通道设置、标志牌设计、区域界线标识、物品存放数量和方式等作详细规定。
同时,各二级单位以改善作业环境、促进安全生产、提高生产效率为目的,从理顺物流、完善设施、优化空间利用、改进人机关系、加快生产节奏、实现均衡生产、提高工作效率等多角度、多层面的要求统筹规划和优化物流管理方案。
各单位根据各自情况,在生产现场因地制宜、因物制宜地制作可供大型备件存放的货架、可移动的小件物品货架、多层立体式货架等,要求各类物品按物料的形状、大小、轻重、使用频度、防护标准合理存放,方便物料的存放和取用,提高空间利用率和工作效率。
其次,通过明确生产作业卫生责任区、完善日常清扫保洁制度、交接班制度等措施,提高各类场所的洁净度,对各类场所实行分层次差异化管理,对不同的场所提出不同的管理、考核要求。
加强技改竣工项目、公共场所、交叉交界场所、公厕等区域的文明卫生协调与管理,促进这些场所清洁状况的有效改善。
工程施工管理创新举措
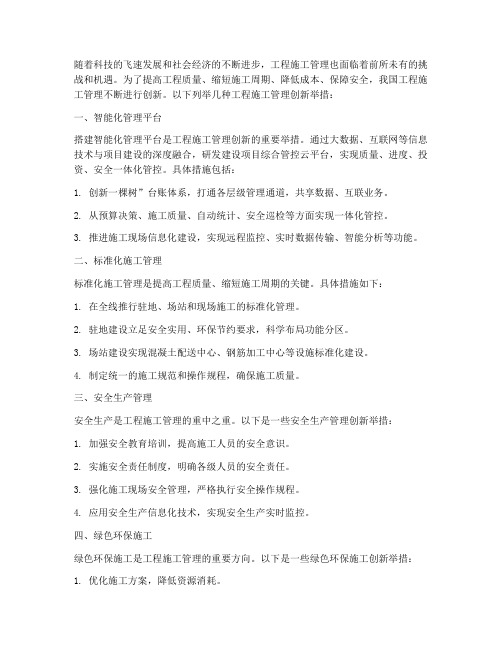
随着科技的飞速发展和社会经济的不断进步,工程施工管理也面临着前所未有的挑战和机遇。
为了提高工程质量、缩短施工周期、降低成本、保障安全,我国工程施工管理不断进行创新。
以下列举几种工程施工管理创新举措:一、智能化管理平台搭建智能化管理平台是工程施工管理创新的重要举措。
通过大数据、互联网等信息技术与项目建设的深度融合,研发建设项目综合管控云平台,实现质量、进度、投资、安全一体化管控。
具体措施包括:1. 创新一棵树”台账体系,打通各层级管理通道,共享数据、互联业务。
2. 从预算决策、施工质量、自动统计、安全巡检等方面实现一体化管控。
3. 推进施工现场信息化建设,实现远程监控、实时数据传输、智能分析等功能。
二、标准化施工管理标准化施工管理是提高工程质量、缩短施工周期的关键。
具体措施如下:1. 在全线推行驻地、场站和现场施工的标准化管理。
2. 驻地建设立足安全实用、环保节约要求,科学布局功能分区。
3. 场站建设实现混凝土配送中心、钢筋加工中心等设施标准化建设。
4. 制定统一的施工规范和操作规程,确保施工质量。
三、安全生产管理安全生产是工程施工管理的重中之重。
以下是一些安全生产管理创新举措:1. 加强安全教育培训,提高施工人员的安全意识。
2. 实施安全责任制度,明确各级人员的安全责任。
3. 强化施工现场安全管理,严格执行安全操作规程。
4. 应用安全生产信息化技术,实现安全生产实时监控。
四、绿色环保施工绿色环保施工是工程施工管理的重要方向。
以下是一些绿色环保施工创新举措:1. 优化施工方案,降低资源消耗。
2. 应用绿色施工技术,减少施工过程中的污染。
3. 加强施工现场环境保护,确保施工过程符合环保要求。
4. 推广绿色施工设备,提高施工效率。
五、项目管理团队建设项目管理团队建设是工程施工管理创新的基础。
以下是一些团队建设创新举措:1. 选拔具备丰富经验和专业素质的项目经理。
2. 建立健全项目管理制度,明确团队职责。
现场管理的技术应用与创新
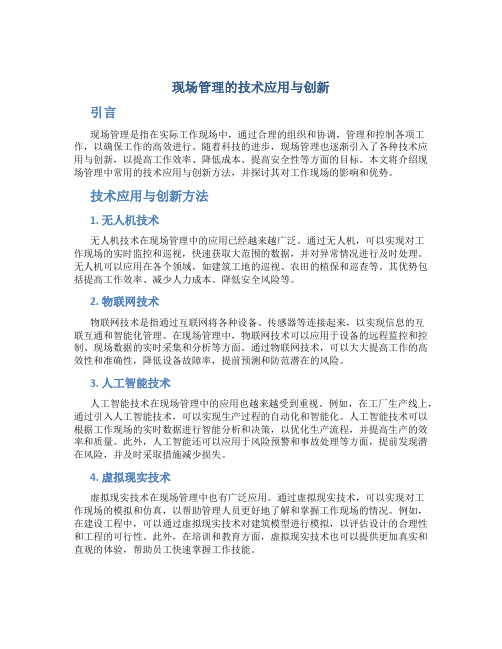
现场管理的技术应用与创新引言现场管理是指在实际工作现场中,通过合理的组织和协调,管理和控制各项工作,以确保工作的高效进行。
随着科技的进步,现场管理也逐渐引入了各种技术应用与创新,以提高工作效率、降低成本、提高安全性等方面的目标。
本文将介绍现场管理中常用的技术应用与创新方法,并探讨其对工作现场的影响和优势。
技术应用与创新方法1. 无人机技术无人机技术在现场管理中的应用已经越来越广泛。
通过无人机,可以实现对工作现场的实时监控和巡视,快速获取大范围的数据,并对异常情况进行及时处理。
无人机可以应用在各个领域,如建筑工地的巡视、农田的植保和巡查等。
其优势包括提高工作效率、减少人力成本、降低安全风险等。
2. 物联网技术物联网技术是指通过互联网将各种设备、传感器等连接起来,以实现信息的互联互通和智能化管理。
在现场管理中,物联网技术可以应用于设备的远程监控和控制、现场数据的实时采集和分析等方面。
通过物联网技术,可以大大提高工作的高效性和准确性,降低设备故障率,提前预测和防范潜在的风险。
3. 人工智能技术人工智能技术在现场管理中的应用也越来越受到重视。
例如,在工厂生产线上,通过引入人工智能技术,可以实现生产过程的自动化和智能化。
人工智能技术可以根据工作现场的实时数据进行智能分析和决策,以优化生产流程,并提高生产的效率和质量。
此外,人工智能还可以应用于风险预警和事故处理等方面,提前发现潜在风险,并及时采取措施减少损失。
4. 虚拟现实技术虚拟现实技术在现场管理中也有广泛应用。
通过虚拟现实技术,可以实现对工作现场的模拟和仿真,以帮助管理人员更好地了解和掌握工作现场的情况。
例如,在建设工程中,可以通过虚拟现实技术对建筑模型进行模拟,以评估设计的合理性和工程的可行性。
此外,在培训和教育方面,虚拟现实技术也可以提供更加真实和直观的体验,帮助员工快速掌握工作技能。
5. 数据分析与可视化数据分析与可视化是现场管理中不可或缺的一部分。
施工现场安全管理亮点与创新
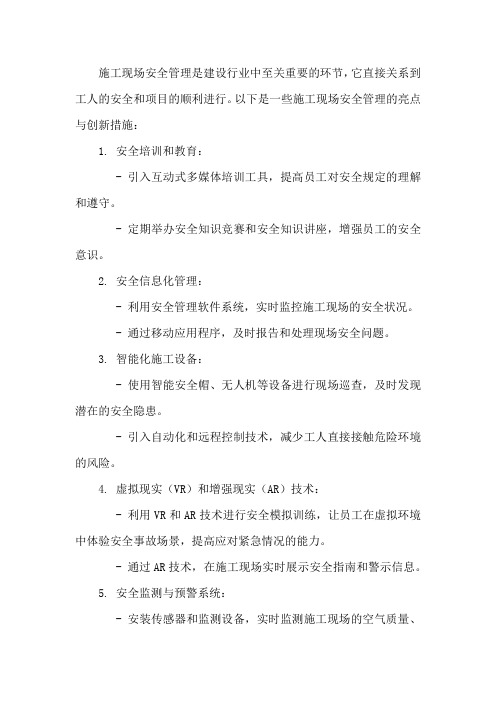
施工现场安全管理是建设行业中至关重要的环节,它直接关系到工人的安全和项目的顺利进行。
以下是一些施工现场安全管理的亮点与创新措施:1. 安全培训和教育:- 引入互动式多媒体培训工具,提高员工对安全规定的理解和遵守。
- 定期举办安全知识竞赛和安全知识讲座,增强员工的安全意识。
2. 安全信息化管理:- 利用安全管理软件系统,实时监控施工现场的安全状况。
- 通过移动应用程序,及时报告和处理现场安全问题。
3. 智能化施工设备:- 使用智能安全帽、无人机等设备进行现场巡查,及时发现潜在的安全隐患。
- 引入自动化和远程控制技术,减少工人直接接触危险环境的风险。
4. 虚拟现实(VR)和增强现实(AR)技术:- 利用VR和AR技术进行安全模拟训练,让员工在虚拟环境中体验安全事故场景,提高应对紧急情况的能力。
- 通过AR技术,在施工现场实时展示安全指南和警示信息。
5. 安全监测与预警系统:- 安装传感器和监测设备,实时监测施工现场的空气质量、噪声水平、振动等,超标时自动报警。
- 利用大数据分析,预测和预防潜在的安全风险。
6. 应急预案与救援演练:- 制定详细的应急预案,包括火灾、地震、中毒等各种可能的安全事故。
- 定期进行救援演练,确保员工熟悉应急程序和逃生路线。
7. 安全文化建设:- 建立安全文化,鼓励员工主动参与安全管理,积极提出安全建议。
- 设立安全奖励机制,对表现突出的个人或团队给予奖励。
8. 环境友好型施工:- 采用绿色施工方法,减少对环境的影响,如使用可持续材料、减少废物产生等。
- 实施噪音和粉尘控制措施,减少对周围社区的影响。
9. 持续改进与反馈:- 建立持续改进机制,定期审查和更新安全管理制度和程序。
- 鼓励员工提供反馈,不断优化安全管理措施。
通过这些亮点和创新措施,可以有效提升施工现场的安全管理水平,减少事故发生的风险,保护工人健康和生命财产安全。
施工现场安全管理创新
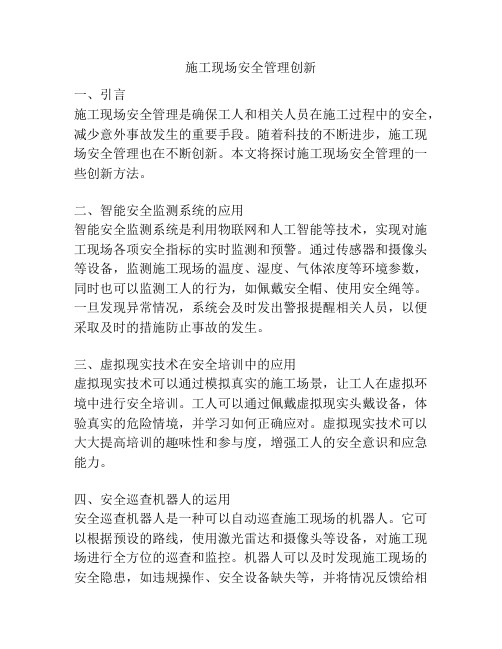
施工现场安全管理创新一、引言施工现场安全管理是确保工人和相关人员在施工过程中的安全,减少意外事故发生的重要手段。
随着科技的不断进步,施工现场安全管理也在不断创新。
本文将探讨施工现场安全管理的一些创新方法。
二、智能安全监测系统的应用智能安全监测系统是利用物联网和人工智能等技术,实现对施工现场各项安全指标的实时监测和预警。
通过传感器和摄像头等设备,监测施工现场的温度、湿度、气体浓度等环境参数,同时也可以监测工人的行为,如佩戴安全帽、使用安全绳等。
一旦发现异常情况,系统会及时发出警报提醒相关人员,以便采取及时的措施防止事故的发生。
三、虚拟现实技术在安全培训中的应用虚拟现实技术可以通过模拟真实的施工场景,让工人在虚拟环境中进行安全培训。
工人可以通过佩戴虚拟现实头戴设备,体验真实的危险情境,并学习如何正确应对。
虚拟现实技术可以大大提高培训的趣味性和参与度,增强工人的安全意识和应急能力。
四、安全巡查机器人的运用安全巡查机器人是一种可以自动巡查施工现场的机器人。
它可以根据预设的路线,使用激光雷达和摄像头等设备,对施工现场进行全方位的巡查和监控。
机器人可以及时发现施工现场的安全隐患,如违规操作、安全设备缺失等,并将情况反馈给相关人员,以便及时处理,降低事故发生的风险。
五、移动应用程序的发展移动应用程序的发展,为施工现场安全管理带来了许多便利。
通过手机和平板电脑等移动设备,工人可以随时随地查看施工现场的安全操作指南、安全手册和应急预案等信息。
同时,移动应用程序还可以用于工人的签到、培训记录和任务指派等,提高工作的规范性和安全性。
六、结论随着科技的不断进步,施工现场安全管理也在不断创新。
智能安全监测系统、虚拟现实技术、安全巡查机器人和移动应用程序等都为施工现场安全管理提供了许多新的思路和方法。
然而,创新只是手段,关键在于管理者和工人的重视和执行。
只有将创新技术与实际操作相结合,不断提高安全管理水平,才能真正做到施工现场的安全可控。
生产车间现场管理方法生产车间现场管理方法
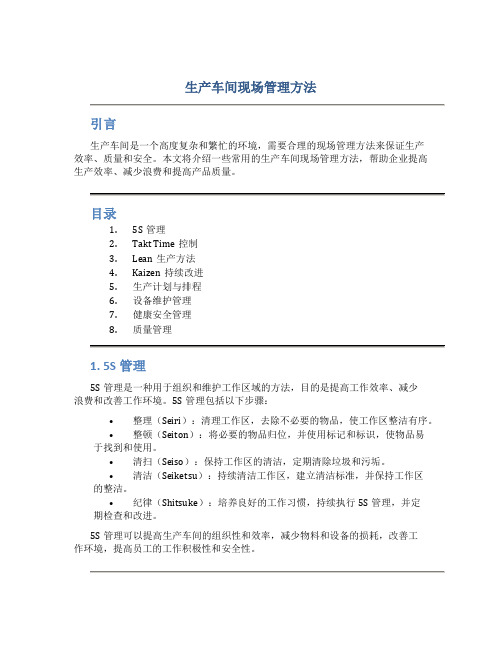
生产车间现场管理方法引言生产车间是一个高度复杂和繁忙的环境,需要合理的现场管理方法来保证生产效率、质量和安全。
本文将介绍一些常用的生产车间现场管理方法,帮助企业提高生产效率、减少浪费和提高产品质量。
目录1.5S管理2.Takt Time控制3.Lean生产方法4.Kaizen持续改进5.生产计划与排程6.设备维护管理7.健康安全管理8.质量管理1. 5S管理5S管理是一种用于组织和维护工作区域的方法,目的是提高工作效率、减少浪费和改善工作环境。
5S管理包括以下步骤:•整理(Seiri):清理工作区,去除不必要的物品,使工作区整洁有序。
•整顿(Seiton):将必要的物品归位,并使用标记和标识,使物品易于找到和使用。
•清扫(Seiso):保持工作区的清洁,定期清除垃圾和污垢。
•清洁(Seiketsu):持续清洁工作区,建立清洁标准,并保持工作区的整洁。
•纪律(Shitsuke):培养良好的工作习惯,持续执行5S管理,并定期检查和改进。
5S管理可以提高生产车间的组织性和效率,减少物料和设备的损耗,改善工作环境,提高员工的工作积极性和安全性。
2. Takt Time控制Takt Time是指生产一个产品所需的时间,是根据客户需求和生产能力来确定的。
Takt Time控制是指在生产过程中,根据Takt Time来安排和控制生产节奏,使生产线产出与需求匹配。
Takt Time控制可以帮助企业确定最佳的生产节奏,避免过度生产或产能不足,保证生产线的平衡和流畅。
通过Takt Time控制,企业可以提高生产效率,减少生产周期,减少浪费和降低库存。
3. Lean生产方法Lean生产方法是一种以减少浪费为目标的生产方法。
它通过识别和消除生产过程中的各种浪费,如过度生产、库存、等待、运输、处理、运动和缺陷,来提高生产效率和质量。
Lean生产方法包括以下主要原则:•价值流分析:识别和分析产品从原料到交付给客户的全过程,找出非价值增加的环节和活动。
车间创新100个小点子
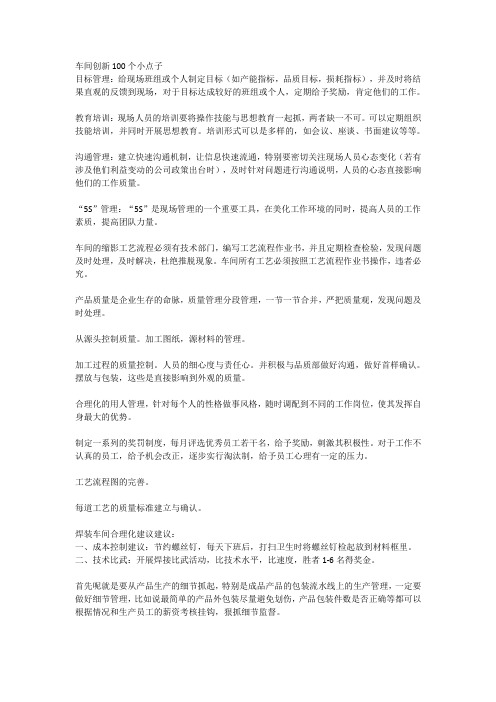
车间创新100个小点子目标管理:给现场班组或个人制定目标(如产能指标,品质目标,损耗指标),并及时将结果直观的反馈到现场,对于目标达成较好的班组或个人,定期给予奖励,肯定他们的工作。
教育培训:现场人员的培训要将操作技能与思想教育一起抓,两者缺一不可。
可以定期组织技能培训,并同时开展思想教育。
培训形式可以是多样的,如会议、座谈、书面建议等等。
沟通管理:建立快速沟通机制,让信息快速流通,特别要密切关注现场人员心态变化(若有涉及他们利益变动的公司政策出台时),及时针对问题进行沟通说明,人员的心态直接影响他们的工作质量。
“5S”管理:“5S”是现场管理的一个重要工具,在美化工作环境的同时,提高人员的工作素质,提高团队力量。
车间的缩影工艺流程必须有技术部门,编写工艺流程作业书,并且定期检查检验,发现问题及时处理,及时解决,杜绝推脱现象。
车间所有工艺必须按照工艺流程作业书操作,违者必究。
产品质量是企业生存的命脉,质量管理分段管理,一节一节合并,严把质量观,发现问题及时处理。
从源头控制质量。
加工图纸,源材料的管理。
加工过程的质量控制。
人员的细心度与责任心。
并积极与品质部做好沟通,做好首样确认。
摆放与包装,这些是直接影响到外观的质量。
合理化的用人管理,针对每个人的性格做事风格,随时调配到不同的工作岗位,使其发挥自身最大的优势。
制定一系列的奖罚制度,每月评选优秀员工若干名,给予奖励,刺激其积极性。
对于工作不认真的员工,给予机会改正,逐步实行淘汰制,给予员工心理有一定的压力。
工艺流程图的完善。
每道工艺的质量标准建立与确认。
焊装车间合理化建议建议:一、成本控制建议:节约螺丝钉,每天下班后,打扫卫生时将螺丝钉检起放到材料框里。
二、技术比武:开展焊接比武活动,比技术水平,比速度,胜者1-6名得奖金。
首先呢就是要从产品生产的细节抓起,特别是成品产品的包装流水线上的生产管理,一定要做好细节管理,比如说最简单的产品外包装尽量避免划伤,产品包装件数是否正确等都可以根据情况和生产员工的薪资考核挂钩,狠抓细节监督。
生产管理工作创新(范文)

生产管理工作创新生产管理工作创新篇一:车间生产管理创新车间生产管理创新 201X-02-20 清华领导力培训瞧这网实现产能超越需要先进的生产管理创新理念,高素质的职工队伍和强有力的团队战斗力。
结合车间的生产特点,我们积极引进“精益生产”理念,整合车间软、硬环境,努力追求产能的最大化。
车间生产管理创新一、实施精益生产管理,实现资源有效配置。
实现产能超越需要先进的生产管理创新理念,高素质的职工队伍和强有力的团队战斗力。
结合车间的生产特点,我们积极引进“精益生产”理念,整合车间软、硬环境,努力追求产能的最大化。
在生产组织过程中,贯彻精益生产管理创新理念。
组织车间全员学习讨论《中型厂精益生产教材》,从思想上戒除自满心理,以进取的心态主动工作迎接挑战,在全车间形成追求快节奏、高效率的氛围。
在此基础上强化车间基础管理,进一步细化车间员工手册,按照计划、布置、落实、监督、检查、考评的闭环管理持续改进车间基础管理。
达到车间生产管理t hldl.rg.cn制度与先进理念的有效融合,为高产稳产搭建坚实的管理平台。
系统优化,破除瓶颈,最大限度的释放产能。
在科学系统的分析测算各工序产能、工序间的衔接和设备能力的基础上,我们进行了系列短板补平的工艺改造工作,实现流程再造。
一是加大坯料断面,提高BD轧机产能;二是增加轧件倍尺数量,提高了轧机的小时作业率,从而进一步推进了产能的提高;三是减少BD轧机的轧制道次,提高BD轧机轧制速度。
就目前实际生产来看,BD轧机的生产节奏是中型生产线绝大多数规格产能发挥的瓶颈环节。
经过对轧机工艺设备的精心测算,通过提高BD轧机的轧制速度和减少轧制道次提高了产能。
精益生产管理创新模式的核心理念是“只做有价值的工作”,根本目的是集中消灭无效生产时间,压减作业切换时间,较少“浪费”。
安全生产管理创新实践的典型案例有哪些

安全生产管理创新实践的典型案例有哪些在当今的工业生产和社会发展中,安全生产管理至关重要。
随着科技的进步和管理理念的更新,许多企业和组织在安全生产管理方面进行了创新实践,取得了显著的成效。
以下为您介绍一些典型的案例。
案例一:某化工企业的智能化安全监控系统这家化工企业面临着复杂的生产工艺和高风险的化学物质处理,为了确保生产过程的安全,他们引入了一套智能化的安全监控系统。
该系统通过在生产现场安装大量的传感器,实时监测温度、压力、浓度等关键参数。
这些传感器将数据传输到中央控制系统,系统利用先进的算法和数据分析技术,对数据进行实时处理和分析。
一旦发现参数异常,系统会立即自动发出警报,并采取相应的紧急措施,如停止生产流程、启动通风设备等。
此外,该系统还具备预测功能。
通过对历史数据的分析和学习,它能够预测可能出现的安全隐患,并提前通知管理人员进行预防和维护工作。
通过这一智能化的安全监控系统,该化工企业大大提高了对生产过程中潜在安全风险的感知和响应能力,有效地减少了事故的发生。
案例二:某建筑公司的安全文化建设某建筑公司深知,仅仅依靠制度和技术手段无法完全保障安全生产,于是他们大力开展安全文化建设。
公司定期组织全体员工参加安全培训,不仅包括安全操作规程和法律法规的学习,还注重培养员工的安全意识和责任感。
培训采用多样化的形式,如现场演示、案例分析、小组讨论等,让员工更加深入地理解安全的重要性。
同时,公司设立了安全奖励制度,对遵守安全规定、提出有效安全建议的员工进行表彰和奖励。
这激发了员工积极参与安全管理的积极性,形成了人人关心安全的良好氛围。
在施工现场,公司设置了明显的安全标识和警示标语,提醒员工时刻保持警惕。
此外,他们还组织了安全文化活动,如安全知识竞赛、安全文艺表演等,让安全理念深入人心。
通过这些举措,该建筑公司的员工从“要我安全”转变为“我要安全”,安全事故率显著下降。
案例三:某制造企业的精益安全管理一家制造企业引入了精益安全管理的理念和方法。
创新“7S”管理方式 改善现场环境

督 查 组 成 员 主 要 是 由公 司 各 生 产 经 营单 位 、 后 勤 部 门负 责“ 7 S ” 管 理 的 兼 职人 员 组 成 , 原来 组织“ 7 S ” 检查 . 督 导 组 成 员 针对 “ 7 S ” 的七个 方 面进行 检查 . 结 果 发 现 检 查 的 过 程 泛 泛、 不仔细 , 不能准确定性 , 检 查 效 率 也 低 。经 分 析 、 研究, 将 督查组成员按检查项细分成三个小组 。 即“ 整 理、 整顿组 ” “ 清 扫、 清洁、 素养组” “ 安全 、 节约组” . 由各 小 组 分 头 负 责 所 检 查 项 经 改 进 的检 查 方 式 , 不易产生漏项 , 问题 不 重 复计 分 , 查 出 的 问题 更 有 针 对 性 . 也 更 专 业
是“ S ” 故称 为 “ 7 S ” “ 7 S ” 是在“ 5 S ” 的 基础 上增 加 了 “ 安全” “ 节
( 二) 采 用 以点 带 面式的 管理 , 创 造 了公平 、 公 正
的 考 评 方 式
宝 石 公 司推 行 “ 7 S ” 活动 . 每 月组织检查并 考评 . 检 查 的 范围为公司东 、 西厂 区的 1 2个 生 产 经 营 单 位 ( 含后勤 部 门) 及2 1 个职能部室。 每个单位都有三两处车间 . 库 房 也 分 原 材 料库、 配件库 、 销售库等几处 , 若 全面检查 , 马不 停 蹄 三 天 才 能检查一个轮 回 . 检 查 效 果 也 不 理 想 为 此 我 们 将 检查 内容 细分 为 “ 生产车间 、 库房 、 办公区 、 更 衣室 、 卫生 间” 五项 , 每月 随机抽查各单位 五项参加考 评 , 以点带 面、 随 机 抽 查 的 管 理
决策 : 一是抓跑项 目、 跑 资金 、 跑重组 ; 二 是 抓 企 业 的 基 础 管 理, 强 炼 内功 。针 对 抓企 业 基 础 管 理 , 公 司提 出 “ 加 强 管 理 是 企业 永恒 的主题 ” “ 加强 企业 基础 管理提 升现 场管 理水平 ” “ 推行 ‘ 7 S ’ 管 理 是 提 高 现 场 管 理 水 平 的 重要 步骤 ” 等 决 策 向 管理要 效益 . 公 司及 时导入 了“ 7 S ” 管理模式 , 为 广 大 员 工 指 明 了方 向和 目标 . 为 企 业 扭 亏 增 盈 奠 定 了基 础 。
安全生产管理创新实践的典型案例有哪些

安全生产管理创新实践的典型案例有哪些在当今的工业生产和企业运营中,安全生产管理始终是至关重要的一环。
为了保障员工的生命安全、减少事故损失、提高生产效率,许多企业和组织都在不断探索和实践创新的安全生产管理模式。
以下是一些具有代表性的典型案例。
一、某大型制造业企业的智能化安全监控系统某大型制造业企业投入大量资金,研发并应用了一套智能化安全监控系统。
这套系统通过在生产现场安装大量的传感器和高清摄像头,实时采集温度、湿度、压力、设备运行状态等数据,并将这些数据传输到中央控制中心进行分析和处理。
当系统检测到异常情况时,如温度过高、压力过大、设备故障等,会立即自动发出警报,并通知相关人员进行处理。
同时,该系统还具备智能分析功能,能够对历史数据进行挖掘和分析,预测可能出现的安全隐患,并提前采取预防措施。
通过这套智能化安全监控系统的应用,该企业大大提高了安全监控的效率和准确性,及时发现并处理了许多潜在的安全隐患,有效避免了事故的发生。
二、某建筑施工企业的“行为安全之星”活动某建筑施工企业为了提高员工的安全意识和行为规范,开展了“行为安全之星”活动。
该活动的核心是通过奖励和表彰那些在工作中遵守安全规定、积极参与安全管理的员工,来激励更多的员工关注安全。
在施工现场,安全管理人员会随时观察员工的行为,对于那些正确佩戴安全帽、系好安全带、遵守操作规程等的员工,当场发放“行为安全之星”卡。
员工积累一定数量的卡片后,可以兑换相应的奖品。
此外,该企业还定期公布“行为安全之星”名单,并在内部宣传栏进行宣传,让这些员工成为大家学习的榜样。
通过这个活动,员工的安全意识得到了显著提高,施工现场的安全状况也得到了明显改善。
三、某化工企业的安全文化建设某化工企业深知安全文化对于安全生产的重要性,因此大力开展安全文化建设。
首先,企业制定了明确的安全价值观和安全目标,并将其传达给每一位员工。
同时,通过开展安全培训、安全知识竞赛、安全演讲等活动,让员工深入理解和认同企业的安全文化。
精益生产现场管理和改善

精益生产现场管理和改善精益生产现场管理和改善是一种管理方法,旨在通过减少浪费和提高效率,实现生产过程的优化。
它注重通过不断改进和创新来提高产品质量和客户满意度,以最小的成本和资源投入,实现最大的产出。
精益生产现场管理和改善的核心理念是追求价值流和流程的可视化、标准化和优化。
它强调对现场各项指标和生产过程进行细致的测量和分析,在实践中发现和解决问题的根本原因,以避免再次出现类似的问题。
这种管理方法还注重员工的参与和团队合作,鼓励员工提出改进建议,并通过培训和沟通与员工合作,培养他们的技能和意识,从而进一步提高生产效率和质量。
在精益生产现场管理和改善中,可以采用一系列工具和技术来帮助实现目标。
例如,价值流映射工具可以帮助团队识别和分析生产过程中的浪费,从而制定改进措施。
班组化管理可以将责任和决策权下放到基层员工,促进他们的主动性和责任感。
而持续改进则是一个持续的过程,通过不断追求卓越,将现场变得更加高效和灵活。
精益生产现场管理和改善的成功需要领导层的支持和承诺,以及全员的参与和共识。
它要求管理者和员工之间的密切合作和沟通,共同推动并落实改进措施。
同时,精益生产现场管理和改善也需要一个良好的改善文化,鼓励员工不断学习和创新,从而不断提升生产效率和质量。
总之,精益生产现场管理和改善是一种管理方法,通过减少浪费和提高效率,实现生产过程的优化。
它注重对现场各项指标和生产过程的细致测量和分析,鼓励员工参与和团队合作,通过培训和沟通提高员工的技能和意识。
只有在领导层的支持和全员的参与下,才能取得持续的改善和提高。
精益生产现场管理和改善是一项持续改进的管理方法,旨在优化生产流程,提高效率和产品质量。
它通过减少浪费、提升价值创造和增加客户价值来实现企业的长期竞争优势。
精益生产的核心概念是“价值流”,即从原材料到最终产品或服务交付给客户的整个过程。
通过细致的价值流分析,企业可以确定哪些步骤是产生价值的,哪些是浪费的,并提出改进措施来最大限度地减少或消除这些浪费。
施工现场管理创新报告

施工现场管理创新报告近年来,随着建筑行业的快速发展,施工现场管理的重要性日益凸显。
为了提高施工效率、确保施工质量和安全,各方面都在不断探索创新的管理方式。
本报告将介绍几种施工现场管理的创新方法,并分析其优势和挑战。
一、智能化管理系统随着信息技术的进步,智能化管理系统在施工现场管理中得到了广泛应用。
通过安装传感器和监控摄像头,可以实时监测施工进程和质量状况。
同时,利用人工智能技术,可以进行数据分析和预测,帮助管理人员及时发现问题并采取相应措施。
智能化管理系统的优势在于提高了信息的透明度和准确性,减少了人为错误和疏漏。
然而,这种系统的建设和运维成本较高,并且在一些复杂的施工环境中可能存在技术难题,需要进一步研发和优化。
二、BIM技术BIM(建筑信息模型)技术是近年来施工现场管理的又一重要创新。
通过建立三维模型,BIM可以提供施工过程中各方的协同设计和协作,减少设计和施工的碰撞和冲突。
同时,BIM技术还可以进行施工进度和资源的模拟和优化,帮助管理人员做出科学决策。
BIM技术的优势在于提高了施工的效率和质量,降低了成本和风险。
然而,BIM技术的应用还面临一些挑战,比如需要建立统一的标准和规范,以及培养专业人才的需求。
三、模块化施工传统的施工过程中,往往需要现场砌砖、浇筑混凝土等繁琐的操作。
而模块化施工则是将建筑模块化,通过工厂化生产,然后在现场进行组装。
这种方式可以大大缩短施工时间,减少对现场资源的依赖,提高工程的质量。
模块化施工的优势在于减少了人力劳动,降低了人力成本和工期风险。
然而,模块化施工的局限性在于需要提前进行精确的计划和设计,并且可能受到运输和组装的限制。
四、绿色施工随着环境保护意识的增强,绿色施工在施工现场管理中变得越来越重要。
绿色施工包括节能、环保和可持续发展等方面的要求,要求使用环保材料、采取节能措施并合理利用资源。
这种管理模式可以减少对环境的污染,提高施工的可持续性。
绿色施工的优势在于符合社会的期望和政策要求,而且可以提高企业的形象和竞争力。
创新现场管理工作模式
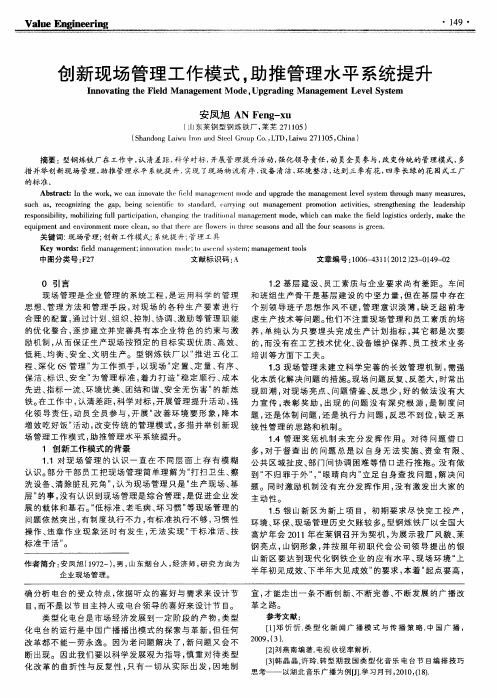
思 想 、 理 方 法 和 管 理 手 段 , 现 场 的 各 种 生 产 要 素 进 行 个 别 领 导 班 子 思 想 作 风 不硬 , 理 意 识 淡 薄 , 乏 超 前 考 管 对 管 缺 合理 的 配 置 , 过 计 划 、 织 、 制 、 调 、 励 等 管理 职 能 虑生 产 技术 等 问题 。 们 不 注 重 现 场 管理 和 员 工 素质 的培 通 组 控 协 激 他 的优 化 整合 , 步 建 立并 完 善具 有 本 企 业 特 色 的 约 束 与 激 养 , 纯 认 为只 要 埋 头 完 成 生 产 计 划 指 标 , 它 都 是 次 要 逐 单 其 励 机 制 , 而 保 证生 产 现 场 按 预 定 的 目标 实现 优 质 、 效 、 的 , 没 有在 工 艺技 术 优 化 、 备 维 护 保 养 、 工 技 术 业 务 从 高 而 设 员 低 耗 、 衡 、 全 、 明生 产 。 型 钢 炼 铁 厂 以 “ 进 五 化 工 培 训 等 方面 下 工 夫 。 均 安 文 推 程、 化 6 深 S管 理 ” 工 作 抓 手 , 现 场 “ 置 、 量 、 序 、 为 以 定 定 有 13现 场 管理 未 建 立 科 学 完 善 的长 效 管理 机 制 , 强 . 需
摘要 : 型钢炼铁厂在 .作 中, 清差距 , 学对标 , T - 认 科 开展管理提升活 动, 强化领 导责任 , 动员全 员参与 , 改变传统 的管理模 式 , 多
措 并举创 新现场管理 , 助推管理 水平 系统提升 , 实现 了现场 物流有序 、 设备 清 洁、 环境 整洁 , 达到三季有花 , 四季长绿 的花 园式 工厂
保 洁 、 识 、 全 ” 管 理 标 准 , 力 打 造 “ 定 顺 行 、 本 化 本 质 化 解 决 问题 的措 施 。 场 问题 反 复 、 差 大 , 常 出 标 安 为 着 稳 成 现 反 时 先进 、 指标 一 流 、 境 优 美、 环 团结 和 谐 、 全 无 伤 害 ” 新 炼 现 回 潮 , 现 场 亮 点 、 安 的 对 问题 借 鉴 、 思 少 , 的做 法 没 有 大 反 好 铁。 工作 中, 清差距 , 学对标 , 在 认 科 开展 管 理 提 升 活 动 , 强 力 宣 传 , 彰 奖 励 , 现 的 问题 没 有 深 究 根 源 , 制 度 问 表 出 是 化 领 导 责 任 , 员 全 员 参 与 , 展 “ 善 环 境 要 形 象 , 本 题 , 是 体 制 问题 , 是 执 行 力 问 题 , 思 不 到 位 , 乏 系 动 开 改 降 还 还 反 缺 增 效 吃 好饭 ” 活动 , 变传 统 的管 理 模 式 , 改 多措 并 举 创 新 现 统 性 管 理 的思 路 和 机 制 。 场 管 理 工 作 模 式 , 推 管 理 水 平 系统 提 升 。 助 14管 理 奖 惩 机 制 未 充 分 发 挥 作 用 。 对 待 问题 借 口 . 1 创 新 工 作 模 式 的 背 景 多, 对于 督查 出的 问题 总是 以 自身无 法 实施、 资金有 限 、 11对 现 场 管 理 的 认 识 一 直 在 不 同 层 面 上 存 有 模 糊 公 共 区 域扯 皮 、 门 间 协 调 困难 等 借 口进 行 推 拖 。没 有 做 . 部 认 识 。 分干 部 员 工 把 现 场 管 理 简 单 理 解 为 “ 扫 卫 生 、 部 打 擦 到 “ 归 罪 于 外 ” “ 睛 向 内 ” 足 自身 查 找 问题 , 决 问 不 ,眼 立 解 洗 设备 、 除脏 乱 死 角 ”认 为现 场 管 理 只 是 “ 产 现 场 、 清 , 生 基 题 。同 时 激 励 机 制 没 有充 分 发挥 作 用 , 有 激 发 出大 家 的 没 层 ” 事 , 有 认 识 到 现 场 管 理 是 综 合 管 理 , 促 进 企 业 发 主 动 性 。 的 没 是 展 的载 体 和 基 石 。 低 标 准 、 毛 病 、 习惯 ” 现 场 管理 的 “ 老 坏 等 15银 山 新 区 为 新 上 项 目 ,初 期 要 求 尽 快 完 工 投 产 , . 问题 依 然突 出 , 制 度 执 行 不 力 , 标 准 执 行 不 够 , 有 有 习惯 性 环 境 、 保 、 场 管 理 历 史 欠 账 较 多 。 环 现 型钢 炼 铁 厂 以全 国大 操作 、 章作业 现象还 时有发生 , 法 实现 “ 标 准活 、 违 无 干 按 高炉年会 2 1 年在莱钢召开为契 机 , 01 为展 示我厂风貌、 莱 标 准 干 活 ” 。 钢 亮点 , 山钢 形 象 , 按 照 年 初 职 代 会 公 司 领 导 提 出 的银 并
- 1、下载文档前请自行甄别文档内容的完整性,平台不提供额外的编辑、内容补充、找答案等附加服务。
- 2、"仅部分预览"的文档,不可在线预览部分如存在完整性等问题,可反馈申请退款(可完整预览的文档不适用该条件!)。
- 3、如文档侵犯您的权益,请联系客服反馈,我们会尽快为您处理(人工客服工作时间:9:00-18:30)。
生产现场管理创新
构建“现场管理469保证屋”,以“公司文化”、“公司战略”、“公司制造”“公司工匠”为核心,确立“现场管理四大原则”、“六项质量活动”、九大精益管理(九大支柱),使柜架现场管理成为“公司制造2015战略”的组成部分。
一、现场管理四大原则
(一)开机前点检原则
(二)三分钟核对原则
(三)机长责任制原则
(四)质量剖析原则
二、六项质量活动:
(一)板料品质确认
(二)设备状态确认
(三)首检品质确认
(四)润滑三滤确认
(五)工序放行确认
(六)工具定位确认
三、九大精益管理:
(一)6S、目视化“全区域、全对象”管理
整合柜架生产、管理、生活三大区域,对设备、工装、工具、器材、场所和环境六大对象实施6S和目视化管理,以提高现场管理效率,减少浪费和设备故障、防止伤害,实现连续安全。
(二)现场作业人员“五项管理”
赋予作业人员“跑得快”、“跳得高”、“飞得远”的动能,培育有知识又有技术(跑),有意识又有素质(跳),敢担当又能担当(飞)的复合型员工。
五项管理:
1、掌握员工短板和需求,注重教育培训实效管理。
2、掌握培训重点和方法,抓好以“OPL单点课程、多点举措”为主流的培训管理。
3、激励员工传递隐性知识,做好全员知识共享管理。
4、培育“学习型”团队,实施卓越班组管理。
5、开展“三星一匠”管理,激励员工争当星匠。
(三)现场文件“五时管理”
整合现场文件管理与知识管理平台,激发文件管理的潜在作用,提高“管理有据可依,培训有据可循,贯标有据可找、考核有据可溯”的有效性。
确保“及时更新失效文件”、“及时组织宣贯培训”、“及时检查实施效果”、“及时修改作业规范”、“及时组织实训操作”的五时管理。
(四)设备管理“TPM管理”
建立“TPM”九大支柱,实施设备全员维护。
定期开展M-FMEA分析,做好预防性维护管理。
定时定人采集故障数据;实施周、月、季、
年设备维护计划、编制TPM看板。
建立机长责任制,管好用好设备提高设备利用率。
(五)过程质量“诚信卡”管理
建立“机长责任人”制度,推行《机长质量诚信卡》管理,明确过程质量监视测量“责、权、利”。
通过MES信息数据系统实施全过程产品质量管理。
定期开展P-FMEA分析,运用“因果图”剖析质量问题。
定期编制《A3报告》并报告,激励全员参与制定和实施纠正预防措施。
定期更新《QC工程表》技术参数、工艺路线和品质要求。
(六)原材料、在制品“零库存”管理
实施物料精益管理,确保原材料在制品库存量符合“订货点”要求。
根据柜架生产周期监控《在制品台账》数量,确保在制品“成套率”、减少“预投数”。
(七)生产计划“柔性”管理“刚性”执行
根据单件小批生产特点编制《生产作业计划》,保持节拍均衡满足最大产量。
强化过程精益化管理,定期开展价值流分析,消除七大浪费、缩短作业流程、提高增值活动时间。
(八)职业健康安全和环境保护的“风险预防责任清单”管理坚持“安全第一、预防为主”方针,定期开展危险源辨识和风险评价活动。
建立“风险预防责任清单”,激励人人参与风险预防。
抓好节能减排,人人参与生产性固废的源头控制,确保“减量化、无害化、资源化”。
(九)资源管理抓“源头”
通过MES生产信息系统对柜架板料消耗信息实时传输给设计部门,从计划设计源头控制大边料产生。
重视员工技能和多能培养,挖掘人力资源隐性能力,运用“双因素理论”激励员工提高效益和效率。