烧结脱硫烟气流量量程的修正算法
宣钢烧结机烟气脱硫技术要求

宣化钢铁集团有限责任公司360m2烧结机烟气脱硫技术要求一、项目总体要求采用石灰石-石膏(湿)法烧结烟气脱硫技术,该技术应能很好地适应烧结烟气量、烟气温度、二氧化硫浓度的大幅度波动,系统运行稳定、可靠;脱硫(达到95%的脱硫率)、除尘效率高,功耗小,钙硫比低,并能有效地去除烧结机烟气中的氟化氢、氯化氢、重金属、碱金属等,且副产物石膏结晶好,颗粒大、品质高,符合综合利用要求。
二、原始工艺条件及设计参数要求脱硫入口烟气参数三、设计要求1、脱硫工艺系统设计要求脱硫工艺系统主要由石灰石浆液制备系统、烟气系统、SO2吸收系统、排空及事故浆液系统、石膏脱水系统、工艺水系统、水处理系统、杂用和仪用压缩空气系统等组成。
包括:(1)脱硫工艺采用石灰石—石膏法。
(2)脱硫装置的烟气处理能力为一台烧结机最大工况时的烟气量。
脱硫效率按大于95%设计。
(3)脱硫系统设置100%烟气旁路,以保证脱硫装置在任何情况下不影响烧结机的安全运行。
(4)吸收剂制浆方式采用外购成品石灰石粉,在吸收剂浆液制备区加水制成浆液。
(5)脱硫副产品—石膏脱水后含游离水含量小于10%,CaSO4·2H2O含量高于90%;CaCO3低于3%(以无游离水分的石膏作基准);达到综合利用条件。
(6)脱硫系统经烟囱排放烟气。
(7)重要设备考虑冗余配置,保证系统可靠运行;(8)为减少运行人员劳动强度,采用DCS系统对脱硫系统进行监控。
(9)脱硫系统工艺水循环使用,节约用水。
(10)脱硫设备年利用小时按7920小时(330天)考虑。
(11)装置可用率不小于95%。
(12)装置服务寿命为30年。
2、总包范围:该工程为总包工程(EPC方式),除能源介质由甲方供应至红线外一米处,电由甲方供至高压进线柜,地基处理甲方负责外,其余全部工程的设计、制造、供货、安装、调试等均由总包方负责。
化工生产烟气脱硫工艺参数优化与脱硫效果评价指南
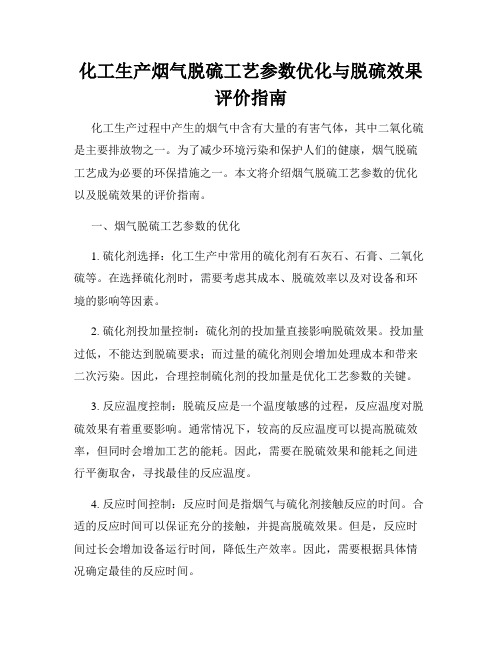
化工生产烟气脱硫工艺参数优化与脱硫效果评价指南化工生产过程中产生的烟气中含有大量的有害气体,其中二氧化硫是主要排放物之一。
为了减少环境污染和保护人们的健康,烟气脱硫工艺成为必要的环保措施之一。
本文将介绍烟气脱硫工艺参数的优化以及脱硫效果的评价指南。
一、烟气脱硫工艺参数的优化1. 硫化剂选择:化工生产中常用的硫化剂有石灰石、石膏、二氧化硫等。
在选择硫化剂时,需要考虑其成本、脱硫效率以及对设备和环境的影响等因素。
2. 硫化剂投加量控制:硫化剂的投加量直接影响脱硫效果。
投加量过低,不能达到脱硫要求;而过量的硫化剂则会增加处理成本和带来二次污染。
因此,合理控制硫化剂的投加量是优化工艺参数的关键。
3. 反应温度控制:脱硫反应是一个温度敏感的过程,反应温度对脱硫效果有着重要影响。
通常情况下,较高的反应温度可以提高脱硫效率,但同时会增加工艺的能耗。
因此,需要在脱硫效果和能耗之间进行平衡取舍,寻找最佳的反应温度。
4. 反应时间控制:反应时间是指烟气与硫化剂接触反应的时间。
合适的反应时间可以保证充分的接触,并提高脱硫效果。
但是,反应时间过长会增加设备运行时间,降低生产效率。
因此,需要根据具体情况确定最佳的反应时间。
二、脱硫效果评价指南1. 脱硫效率:脱硫效率是评价工艺脱硫效果的重要指标之一。
通常使用脱硫率或去除率来表示,计算公式为:脱硫率(%)=(进口SO2浓度-出口SO2浓度)/进口SO2浓度×100%。
脱硫率越高,脱硫效果越好。
2. 副产物生成量:在烟气脱硫过程中,会生成一些副产物,如石膏、含钙废液等。
评价脱硫效果时,需要考虑这些副产物的生成量。
副产物生成量越低,说明工艺对环境的影响越小。
3. 设备压降:脱硫设备内部流动引起的压降是影响工艺经济性和设备运行稳定性的因素之一。
良好的脱硫工艺应该具有较低的压降,以提高设备的运行效率。
4. 附着物生成:脱硫设备内部易产生附着物,如石膏结壳等。
附着物的生成会导致设备堵塞、运行不稳定等问题。
CEMS烟气流量所需公式
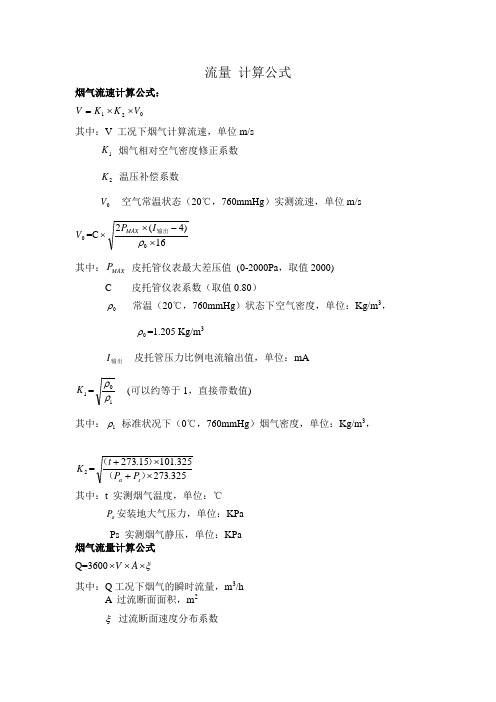
流量 计算公式
烟气流速计算公式:
1K V =2K ⨯0V ⨯
其中:V 工况下烟气计算流速,单位m/s 1K 烟气相对空气密度修正系数 2K 温压补偿系数
0V 空气常温状态(20℃,760mmHg )实测流速,单位m/s 0V =C ⨯16)
4(20⨯-⨯ρ输出I P MAX
其中:MAX P 皮托管仪表最大差压值 (0-2000Pa ,取值2000)
C 皮托管仪表系数(取值0.80) 0ρ 常温(20℃,760mmHg )状态下空气密度,单位:Kg/m 3,
0ρ=1.205 Kg/m 3
输出I 皮托管压力比例电流输出值,单位:mA
1K =1
0ρρ (可以约等于1,直接带数值) 其中:1ρ 标准状况下(0℃,760mmHg )烟气密度,单位:Kg/m 3,
2K =325
.273325.10115.273⨯+⨯+)()(s a P P t 其中:t 实测烟气温度,单位:℃ a P 安装地大气压力,单位:KPa Ps 实测烟气静压,单位:KPa 烟气流量计算公式
Q=3600ξ⨯⨯⨯A V
其中:Q 工况下烟气的瞬时流量,m 3/h
A 过流断面面积,m 2 ξ 过流断面速度分布系数。
脱硫计算公式比较全

湿法脱硫系统物料平衡计算基础数据(1)待处理烟气烟气量:1234496Nm3/h(wet)、1176998 Nm3/h(dry)烟气温度:114C烟气中SO2浓度:3600mg/Nm3烟气组成:石灰石浓度:96.05%平衡计算(1)原烟气组成计算(2)烟气量计算1、①-②(增压风机出口 T GGH 出口):取GGH 的泄漏率为0.5%,则GGH 出口总烟气量为1234496 Nm 3/h (1-0.5%)=1228324Nm 3/h=1629634kg/h泄漏后烟气组分不变,但其质量分别减少了 0.5%,见下表。
温度为70 C 。
2、⑥-⑦(氧化空气):假设脱硫塔设计脱硫率为95.7%,即脱硫塔出口二氧化硫流量为 3778 X(1-95.7%) =163 kg/h ,二氧化硫脱除量=(3778-163) /64.06=56.43kmol/ho取 O/S=4需空气量=56.43 4/2/0.21=537.14kmol/h 28.36 (空气分子量)=15499.60kg/h,约 12000Nm 3/ho其中氧气量为 537.14 kmol/h 0.21=112.80 kmol/h 32=3609.58kg/h 氮气量为 537.14 kmol/h 0.79=424.34 kmol/h 28.02=11890.02kg/h= 氧化空气进口温度为20r ,进塔温度为80^03、②-③(GGH 出口-脱硫塔出口):烟气蒸发水量计算:(40C)=0.2520 kcal/kg.r 。
Cp 烟气=(0.2536+0.2520) /2=0.2528 kcal/kg.C氧化空气进口温度为 80r ,其比热约为 0.2452 1)假设烟气进塔温度为70C ,在塔内得到充分换热, 由物性数据及烟气中的组分,可计算出进口烟气的比热约为出口温度为40^00.2536kcal/kg.r, Cpkcal/kg.r, Cp ( 40r)=0.2430kcal/kg.C 。
脱硫系统常用计算公式

1) 由于烟气设计资料,常常会以不同的基准重复出现多次,(如:干基湿基,标态实际态,实际O2 等),开始计算前一定要核算统一,如出现矛盾,必须找出正确的一组数据,避免原始数据代错。
常用折算公式如下:烟气量(dry)=烟气量(wet) >(1-烟气含水量%)实际态烟气量=标态烟气量>气压修正系数x温度修正系数烟气量(6%02) = ( 21-烟气含氧量)/ ( 21 -6%)S02 浓度(6%02 ) = ( 21 - 6%) / (21 -烟气含氧量)S02 浓度( mg/Nm3 ) =S02 浓度( ppm) x2.857物料平衡计算1 )吸收塔出口烟气量G2G2= (G1 x (1 - mw1) X(P2/(P2-Pw2)) (X —mw2 )+ G3X (1- 0.21/K) ) >(P2/(P2-Pw2))G1: 吸收塔入口烟气流量mw1: 入口烟气含湿率P2:烟气压力Pw2 :饱和烟气的水蒸气分压说明: Pw2 为绝热饱和温度下的水蒸气分压,该值是根据热平衡计算的反应温度,由烟气湿度表查得。
(计算步骤见热平衡计算)2) 氧化空气量的计算根据经验,当烟气中含氧量为6%以上时,在吸收塔喷淋区域的氧化率为50 - 60 %。
采用氧枪式氧化分布技术,在浆池中氧化空气利用率n 02=25-30%,因此,浆池内的需要的理论氧气量为:S=(G1 x q1-G2 x q2) x(1-0.6)/2/22.41所需空气流量QreqQreq=S x22.4/(0.21 0.x3)G3= Qreq >KG3:实际空气供应量K :根据浆液溶解盐的多少根据经验来确定,一般在 2.0-3左右。
3) 石灰石消耗量计算W1=100x qs xnsW1: 石灰石消耗量qs: :入口S02 流量n S兑硫效率4) 吸收塔排出的石膏浆液量计算W2=172xx qs xn s/SsW2:石膏浆液量Ss石膏浆液固含量5) 脱水石膏产量的计算W3=172xx qs xn s/SgW3: 石膏浆液量Sg:脱水石膏固含量(1-石膏含水量)6) 滤液水量的计算W4=W3-W2W3: 滤液水量7) 工艺水消耗量的计算W5=18x (G4-G1-G3 x(1-0.21/K))+W3 (1x-Sg)+36x qs x n+W s WT蒸发水量石膏表面水石膏结晶水排放废水。
烟气流量计算公式
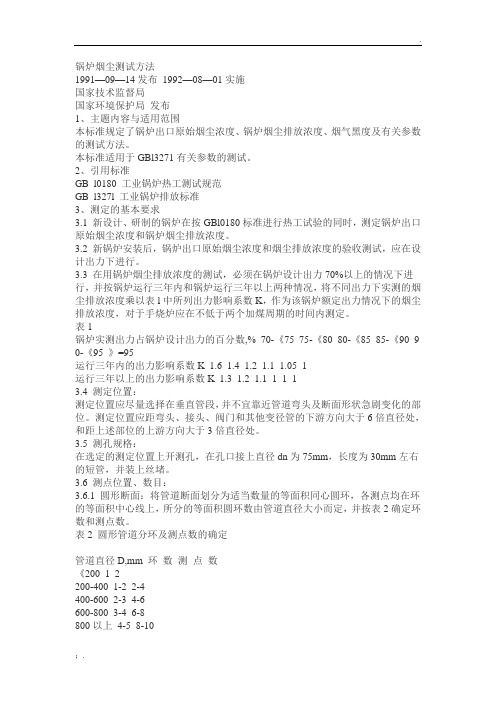
锅炉烟尘测试方法1991—09—14发布1992—08—01实施国家技术监督局国家环境保护局发布1、主题内容与适用范围本标准规定了锅炉出口原始烟尘浓度、锅炉烟尘排放浓度、烟气黑度及有关参数的测试方法。
本标准适用于GBl3271有关参数的测试。
2、引用标准GB l0180 工业锅炉热工测试规范GB l327l 工业锅炉排放标准3、测定的基本要求3.1 新设计、研制的锅炉在按GBl0180标准进行热工试验的同时,测定锅炉出口原始烟尘浓度和锅炉烟尘排放浓度。
3.2 新锅炉安装后,锅炉出口原始烟尘浓度和烟尘排放浓度的验收测试,应在设计出力下进行。
3.3 在用锅炉烟尘排放浓度的测试,必须在锅炉设计出力70%以上的情况下进行,并按锅炉运行三年内和锅炉运行三年以上两种情况,将不同出力下实测的烟尘排放浓度乘以表l中所列出力影响系数K,作为该锅炉额定出力情况下的烟尘排放浓度,对于手烧炉应在不低于两个加煤周期的时间内测定。
表1锅炉实测出力占锅炉设计出力的百分数,% 70-《75 75-《80 80-《85 85-《90 9 0-《95 》=95运行三年内的出力影响系数K 1.6 1.4 1.2 1.1 1.05 1运行三年以上的出力影响系数K 1.3 1.2 1.1 1 1 13.4 测定位置:测定位置应尽量选择在垂直管段,并不宜靠近管道弯头及断面形状急剧变化的部位。
测定位置应距弯头、接头、阀门和其他变径管的下游方向大于6倍直径处,和距上述部位的上游方向大于3倍直径处。
3.5 测孔规格:在选定的测定位置上开测孔,在孔口接上直径dn为75mm,长度为30mm左右的短管,并装上丝堵。
3.6 测点位置、数目:3.6.1 圆形断面:将管道断面划分为适当数量的等面积同心圆环,各测点均在环的等面积中心线上,所分的等面积圆环数由管道直径大小而定,并按表2确定环数和测点数。
表2 圆形管道分环及测点数的确定管道直径D,mm 环数测点数《200 1 2200-400 1-2 2-4400-600 2-3 4-6600-800 3-4 6-8800以上4-5 8-10当测定现场不能满足3.4条所述要求时,对圆形管道应增加与第一测量直径成9 0°夹角的第二测量直径,总测点数增加一倍。
cems流量计算公式每平米烧结风量

cems流量计算公式每平米烧结风量
1、烟气流速m/
V= K XSqr20P/p
AP=Pd-s=p (Ts).V2/2ρ=ρ1X(p+Ba)/Ba X273/(Ts+273)V=pX Sqrt2Xρ1X(7s+273)1273X10325/(s+Ba)p其中v=1.414。
ρ1-1.34kg/m3--m/s,测定断面的气平均流速:v,速度场系数:p-皮托管系数:Pd --P烟气动压:Ba--Pa.当地大气压:p_km',湿排气密度:s-_Pa.烟气静压:Ts_c,烟气温度AP:压差。
2、过量空气系数
21-o--%,烟气中氧的体积百分比:3、折算浓度mg/m3C=x。
22-mg/m',折算成过量空气系数为a时的排放浓度:Ci--mg/m',
标准状态F干烟气的排放浓度:a-在测点实测的过量空气系数:Cs-有关排放标准中规定的过量空气系数:实测锅炉烟尘、二氧化硫、氮氧化物排放浓度按下表规定的系数折算。
锅炉类型折算项目过量空气系数烟尘初始排放浓度a=1.7燃煤锅炉烟尘、二氧化硫排放浓度0=1.8 燃油、燃气锅炉烟尘、二氧化硫、氮氧化物排放浓度a=1.24、烟气流量Q=AXVX Ba+Pg273-(1-m)101325273+TX%排气中水分含量体积百分比。
脱硫净烟气环保计算公式

脱硫净烟气环保计算公式随着工业化进程的加速,大量的燃煤、燃油等化石燃料的燃烧释放出大量的二氧化硫等有害气体,对环境造成了严重的污染。
为了减少这些有害气体对环境的影响,脱硫净烟气技术应运而生。
脱硫净烟气技术是通过化学或物理方法将烟气中的二氧化硫等有害气体去除,从而达到净化烟气的目的。
本文将介绍脱硫净烟气环保计算公式,以帮助人们更好地了解脱硫净烟气技术的环保效果。
脱硫净烟气环保计算公式主要包括两个方面,脱硫效率和净化效果。
脱硫效率是指脱硫设备去除烟气中二氧化硫的能力,通常用百分比表示。
净化效果是指脱硫后烟气中二氧化硫浓度的降低程度,通常用浓度比值表示。
下面将详细介绍脱硫净烟气环保计算公式的具体内容。
脱硫效率的计算公式如下:脱硫效率 = (进口二氧化硫浓度出口二氧化硫浓度)/ 进口二氧化硫浓度×100%。
其中,进口二氧化硫浓度是指进入脱硫设备前烟气中二氧化硫的浓度,出口二氧化硫浓度是指经过脱硫设备后烟气中二氧化硫的浓度。
脱硫效率的计算公式可以直观地反映出脱硫设备去除二氧化硫的能力,是评价脱硫设备性能的重要指标之一。
净化效果的计算公式如下:净化效果 = 出口二氧化硫浓度 / 进口二氧化硫浓度。
净化效果是指脱硫后烟气中二氧化硫浓度与进口二氧化硫浓度的比值。
净化效果越大,说明脱硫设备去除二氧化硫的效果越好,对环境的保护作用也越显著。
通过净化效果的计算,可以更直观地了解脱硫设备对烟气中有害气体的净化效果,为环保工作提供科学依据。
除了脱硫效率和净化效果外,脱硫净烟气环保计算公式还可以包括其他指标,如脱硫能耗、脱硫成本等。
这些指标的计算可以帮助企业更全面地评估脱硫净烟气技术的环保效果和经济效益,为环保工作提供更多的参考依据。
总之,脱硫净烟气环保计算公式是评价脱硫净烟气技术环保效果的重要工具,通过对脱硫效率、净化效果等指标的计算,可以更科学地评估脱硫设备的性能,为环保工作提供科学依据。
希望本文介绍的脱硫净烟气环保计算公式能够帮助人们更好地了解脱硫净烟气技术的环保效果,推动环保工作取得更大的成效。
脱硫烟气量计算

项目名称符号单位公式及计算设计煤种校对煤种一炉内石灰石脱硫收到基硫份St,ar%已知 1.91 1.94燃煤中的含硫量燃烧后氧化成SO2的份额(3)P4Ks脱硫除尘表11炉内脱硫效率η1%脱硫除尘表80.0080.00 Ca/S(钙硫比)β脱硫除尘表 1.3 1.3炉膛出口过剩空气系统αl烟风量表 1.18 1.18空气的绝对湿度(含湿量)(2)P327d g水/kg空气烟风量表 4.12 4.12反应方程式 S + O2= SO2分子量 32 64St,ar*Ks △m SO21除去的SO2量(质量流量)△m SO2kg/kg煤2*Ks*St,ar0.0380.039除去的SO2量(体积流量)(1)P129△VSo2Nm3/kg煤2*Ks*St,ar*22.4/64=0.7*Ks*St,ar=△m SO2*22.4/640.01340.0136反应方程式CaCO3 + SO2 + 0.5*O2 = CaSO4 + CO2摩尔量 1 0.5 1△Vso2 △Vo2 △Vco22脱硫消耗的O2量(体积流量)(1)P129△Vo2Nm3/kg煤0.5*△VSo2=0.35*Ks*St,ar*0.00670.0068脱硫消耗的O2量(质量流量)△m O2kg/kg煤64/22.4*△Vo20.019100.01940 3脱硫消耗的理论干空气量(体积流量)(1)P128△V0CFB Nm3/kg煤△Vo2 /0.21=1.66*Ks*St,ar0.031830.03233脱硫消耗的实际湿空气量(体积流量)(1)P128△VCFB Nm3/kg煤α(1+0.0016d)*△V0CFB0.037810.03840 CaCO3煅烧增加的CO2排放(体积流量)(1)P128△V'Co2Nm3/kg煤β*△VSo2=β*Ks*St,ar*η10.01740.0177石灰石中MgCO3的含量(1)P127G MgCO3kg/kg煤K MgCO3/K CaCO3*100/32*St,ar*Ks*β脱硫除尘表0.00500.0051MgCO3煅烧增加的CO2排放(质量流量)△m''cO2kg/kg煤44/84*G MgCO30.00260.0027MgCO3煅烧增加的CO2排放(体积流量)(1)P128△V''Co2Nm3/kg煤22.4/44*△m''cO20.00130.0014 4脱硫增加的CO2排放(体积流量)△V cO2Nm3/kg煤△V'Co2+△V''Co20.01870.0190脱硫增加的CO2排放(质量流量)△m cO2kg/kg煤44/22.4*△Vco20.03680.0374石灰石含水率K H2O0.010.01石灰石中CaCO3的含量K CaCO3脱硫除尘表0.8810.881纯石灰石消耗量(1)P127G CaCO3kg/kg煤100/32*St,ar*Ks*β 脱硫除尘表0.0775940.078813石灰石中水蒸汽的含量(质量流量)△m H2O kg/kg煤K H2O/K CaCO3*100/32*St,ar*Ks*β0.0008800.000894石灰石中水蒸汽的含量(体积流量)(1)P129△V'HO2kg/kg煤22.4/18*K H2O/K CaCO3*100/32*St,ar*Ks*β0.0010960.001113脱硫消耗的理论干空气量中的水蒸汽量(体积流量)(1)P129△V''HO2kg/kg煤0.0016d△V0CFB0.0002100.000213 5脱硫增加的H2O排放(体积流量)△VHO2kg/kg煤0.0013050.001326 6脱硫后增加的理论干烟气量(1)P128△Vdg kg/kg煤△V0CFB+△V cO2-△Vo2-△VSo20.030500.03098脱硫后增加的理论湿烟气量△Vwg kg/kg煤△V0CFB+△V cO2+△VHO2-△Vo2-△VSo20.031810.03231汇总:脱硫消耗的理论干空气量(体积流量)(1)P128△V0CFB Nm3/kg煤△Vo2 /0.21=1.66*Ks*St,ar0.031830.03233脱硫后增加的理论干烟气量(1)P128△Vdg kg/kg煤△V0CFB+△V cO2-△Vo2-△VSo20.030500.03098。
脱硫各项计算公式
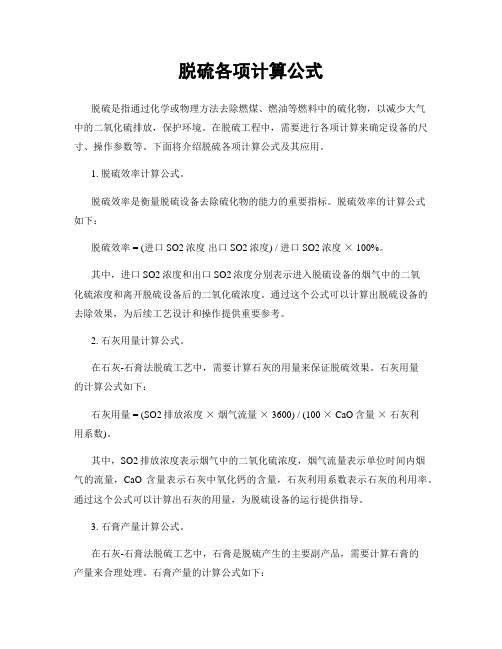
脱硫各项计算公式脱硫是指通过化学或物理方法去除燃煤、燃油等燃料中的硫化物,以减少大气中的二氧化硫排放,保护环境。
在脱硫工程中,需要进行各项计算来确定设备的尺寸、操作参数等。
下面将介绍脱硫各项计算公式及其应用。
1. 脱硫效率计算公式。
脱硫效率是衡量脱硫设备去除硫化物的能力的重要指标。
脱硫效率的计算公式如下:脱硫效率 = (进口SO2浓度出口SO2浓度) / 进口SO2浓度× 100%。
其中,进口SO2浓度和出口SO2浓度分别表示进入脱硫设备的烟气中的二氧化硫浓度和离开脱硫设备后的二氧化硫浓度。
通过这个公式可以计算出脱硫设备的去除效果,为后续工艺设计和操作提供重要参考。
2. 石灰用量计算公式。
在石灰-石膏法脱硫工艺中,需要计算石灰的用量来保证脱硫效果。
石灰用量的计算公式如下:石灰用量 = (SO2排放浓度×烟气流量× 3600) / (100 × CaO含量×石灰利用系数)。
其中,SO2排放浓度表示烟气中的二氧化硫浓度,烟气流量表示单位时间内烟气的流量,CaO含量表示石灰中氧化钙的含量,石灰利用系数表示石灰的利用率。
通过这个公式可以计算出石灰的用量,为脱硫设备的运行提供指导。
3. 石膏产量计算公式。
在石灰-石膏法脱硫工艺中,石膏是脱硫产生的主要副产品,需要计算石膏的产量来合理处理。
石膏产量的计算公式如下:石膏产量 = SO2排放浓度×烟气流量× 3600 / 100。
通过这个公式可以计算出单位时间内产生的石膏量,为后续的石膏处理提供依据。
4. 脱硫塔液气比计算公式。
在湿法脱硫工艺中,需要计算脱硫塔的液气比来保证脱硫效果。
脱硫塔液气比的计算公式如下:液气比 = (进口SO2浓度×烟气流量) / (脱硫液循环速率× 3600)。
其中,进口SO2浓度和烟气流量表示进入脱硫塔的烟气中的二氧化硫浓度和烟气流量,脱硫液循环速率表示单位时间内脱硫液的循环速率。
朝阳公司烟气脱硫设计计算(师弟)

设计参数耗煤量:27t/d,全硫含量:0.8%-1%,烟气温度:150℃煤气硫含量:450mg/ m3, 发生炉煤气产量:4000 m3/t转化成二氧化硫的硫含量:847 mg/ m3设计计算1.烟气量计算单日产气总量=27x4000=108000m3则所选煤气的分子量M=2x13.33%+28x27.40%+16x1.5%+44x3.8%+28x49.6%+18x4.17%+32x0.2%=24.553则所选煤气24.553kg/kmol÷22.4Nm3/kmol=1.096kg/ m3低位发热值Qd=10805x13.33%+12650x27.40%=4906.4kJ/Nm3=4906.4/4.1868=1171.88kcal/N m3=4906.4/1.3053=3758.83kcal/kg设1立方米发生炉煤气完全燃烧,空气系数ɑ=1.5经计算,理论空气需要量Qv=1.11 m3实际空气量=1.11x1.5=1.67 m3理论需氧量=0.234 m3烟气中过剩氧气量=(a-1)x理论需氧量=0.5x0.234=0.117 m3过剩氮气量=过剩氧气量x78/21=0.117X78/21=0.435 m3理论烟气量=1.03 m3实际烟气量=理论生成物总量+过剩氧气量+过剩氮气量=1.03+0.117+0.435=1.582 m3则烟气量Q=108000x1.582/24=7119 m3/h(150度)进行温度修正后的烟气量Q’=7119*(273.15+20)/(273.15+150)=4908.7 m3/h(20度)锅炉烟尘最高允许排放浓度及黑度限值锅炉二氧化硫和氮氧化物最高允许排放浓度限值本设计中燃气锅炉属于二时段(2001年1月1日),即烟尘最高允许排放浓度为50mg/m3,二氧化硫最高允许排放浓度为100mg/ m3。
2.工艺流程见设计方案3.二氧化硫排放量Qs=847/1000/1000x7119=6.03kg/h;烟气脱硫主要设备设计计算1.喷淋塔设计计算烟道烟气流速取18m/s。
烟气脱硫物料平衡计算

烟气脱硫物料平衡计算输入数据脱硫计算书原始输入数据列表序名称符号单位计算公式或数值来源计算结果号1 煤质分析收到基碳 % 51.38 C ar收到基氢 % 0.56 H ar收到基氧 % 3.35 O ar收到基氮 % 0.22 N ar收到基硫 % 1.36 S ar收到基灰分 % 37.35 A ar收到基全水分 % 5.78 M ar空气干燥基水分 % M ad干燥无灰基挥发份 % V daf收到基低位发热量 kcal/kg 4106.94 Q net.ar2 耗煤量锅炉实际耗煤量(B-MCR) B t/h 44.00机械未完全燃烧热损失 % 3.00 q 4计算耗煤量(B-MCR) Bj t/h 42.6800 3 引风机出口烟气参数3(1) 引风机出口实际烟量 /h 384084.72 mV jpy3 Nm/h 280000.00引风机出口排烟温度 t ? 132.00 yin3 引风机出口飞灰浓度 m mg/Nm 70.00 h引风机出口过剩空气系数 a' 1.36 lfa3(2) 引风机出口干烟气量(6,O) Vs Nm/h 2gy3 引风机出口SO浓度 m mg/Nm 干烟气,含氧量6, 2600.00 2so24 年运行小时数 H h 6500.005 多年平均气压 P mbar 936.906 脱硫及吸收塔相关参数要求脱硫率η % 96.50吸收塔进口烟温 t ? 132.00 py吸收塔出口烟温 t ? 45.50 ck浓缩段出口烟气温度 ? 603 吸收塔出口要求含尘浓度 m mg/Nm 50.00 ck3 吸收塔出口要求含SO浓度 m mg/Nm 91.00 2ck7 摩尔分子量(NH4)2SO4分子量 g/mol 132SO分子质量 g/mol 64 2NH3分子量 g/mol 17O2分子量 32CO2分子量 44N2分子量 28H2O分子量 18烟气参数计算烟气参数计算序号名称符号单位计算公式或数值来源计算结果一烟气量计算031 理论空气量 V Nm/kg 0.0889(C+0.375S)+0.265H-0.0333O 4.65 arararar 300002 燃烧产物理论体积 V Nm/kg V+V+V 4.85 yN2RO2H2O3001) 氮气 V Nm/kg 0.79V+0.008N 3.68 N2ar302) 二氧化物 V Nm/kg 0.01866(C+0.375S) 0.97 arRO2ar3003) 水蒸汽 V Nm/kg 0.111H+0.0124M+0.0161V 0.21 arH2Oar30003 燃烧产物实际体积 V' Nm/kg V+0.0161(a'-1)V+(a'-1)V 6.53yylfalfa30004 干烟气量 V' Nm/kg V+V+(a'-1)V 6.30 gyRO2N2lfa5 烟气含氧量和含湿量计算3001) 烟气中的水分 V' Nm/kg V+0.0161(a'-1)V 0.24 H2OH2Olfa302) 烟气中的氧量 V' Nm/kg 0.21(a'-1)V 0.35 lfaO23) 干烟气中含氧量 n' % V'/V' 5.51 go2O2gy4) 湿烟气中含氧量 n' % V'/V' 5.31 sho2O2y5) 湿烟气中含湿量 n' % V'/V' 4.00 H2OH20y6) 湿烟气中CO含量 n' % 0.01866Car/V' 14.68 shCO22y7) 干烟气中CO含量 n' % 0.01866Car/V' 15.23 gCO22gy8) 湿烟气中SO含量 n' % 0.01866*0.375Sar/V' 0.15 shSO22y9) 干烟气中SO含量 n' % 0.01866*0.375Sar/V' 0.15 gSO22gy010) 湿烟气中N含量 n' % (0.79a'V+0.008N)/V' 76.26 shN2lfa2ary011) 干烟气中N含量 n' % (0.79a'V+0.008N)/V' 79.11 gN2lfa2argy36 总燃烧产物实际湿体积 Vt Nm/h V'*B*1000 279930 shyyj37 总燃烧产物实际干体积Vt Nm/h V'*B*1000 268732 ggyyj3'8 总燃烧产物6%O干体积 Vt Nm/h V*(21-n)/(21-6) 277454 g2y-O2tgygo29 烟气量计算误差 % <1 -0.025二烟气组分计算SO2 kmol/h 18.208O2 kmol/h 664.156N2 kmol/h 9529.965CO2 kmol/h 1834.326H2O kmol/h 499.87三各组分定压比热60?时SO2 J /mol K 41.82660?时O2 J /mol K 29.44860?时N2 J /mol K 28.52860?时CO2 J /mol K 38.56220?时SO2 J /mol K 41.33220?时O2 J /mol K 29.39620?时N2 J /mol K 28.37620?时CO2 J /mol K 38.974 45.500 ?时SO2 J /mol K 41.647 45.500 ?时O2 J /mol K 29.429 45.500 ?时N2 J /mol K 28.473 45.500 ?时CO2 J /mol K 38.711 132.000 ?时SO2 J /mol K 42.715 132.000 ?时O2 J /mol K 29.542 132.000 ?时N2 J /mol K 28.802 132.000 ?时CO2 J /mol K 37.820 四进口水质量 kg/h 8997.738假设烟气出口温度 45.500热平衡计算序号名称符号单位计算公式或数值来源计算结果一进口烟气热量计算1 SO2带入热量 KJ/h 100524.722 O2带入热量 KJ/h 2589870.643 N2带入热量 KJ/h 36231129.064 CO2带入热量 KJ/h 9157492.662723.14为132?下水蒸5 水带入热量 KJ/h 24502100.04 气焓值(KJ/KG) 带入总热量 Q1 KJ/h 72581117.12二出口烟气热量计算SO2带出热量 KJ/h 1207.58O2带出热量 KJ/h 889322.43N2带出热量 KJ/h 12346231.66CO2带出热量 KJ/h 3230920.29带出总热量 Q2 KJ/h 16467681.96三进口出口热量差值 KJ/H 56113435.16四出口水蒸气含量计算?饱和气压 Kpa 9.786水的汽化潜热+显热 KJ/Kg 2406.50饱和水蒸气压力修正系数 0.90进口烟气压力 Kpa 93.69引风机出口压力 Kpa 1.30吸收塔阻力 Kpa 1.10出口烟气压力 Kpa 93.89出口烟气湿含量 kg/m3 0.0831798出口烟气水蒸气质量 kg/h 23284.49水进口温度 ? 假设环境温度为20? 20.00五出口水蒸气热量 Q3 KJ/H 56034136.66六误差 % <1 0.14七烟气出口带走水量 kg/h 14286.76八浓缩段出口热量 1 SO2带入热量 KJ/h 45693.05 2 O2带入热量 KJ/h 1173484.03 3 N2带入热量 KJ/h 16312251.12 4 CO2带入热量 KJ/h 4244116.845 带走总热量 KJ/h 21775545.036 浓缩段与入口热量差值 KJ/h 50805572.097 浓缩段出口水蒸气汽焓值KJ/kg 查水蒸气性质表 2608.79 8 浓缩段出口带水 kg/h 19474.76 9 浓缩段带走水量 kg/h 10477.03物料平衡计算名称单位计算公式数值脱硫效率 0.965烟气量 Nm3/h 280000O2 0.0573SO2 mg/Nm3 2600SO2脱除率 g/h 702520烟气温度 ? 132年运行小时 6000SO2质量 g/h 728000SO2分子量 64NH3分子量 17(NH4)2SO4分子量 132O2分子量 32液氨浓度 0.996液氨使用效率 0.97液氨消耗量 t/h 0.3863016硫铵生成量 t/h 1.4489475理论O2消耗量 kmol/h 5.4884375实际O2消耗量 kmol/h 16.465313 空气耗量 Nm3/min 29.271667 塔内气速m/s 2.83 设计塔径 m 7.206857 液气比 L/Nm3 3 循环浆液量 m3/H 840 吨硫酸氨的消耗液量 t 0.2666085氧化风机计算名称数值单位 1 理论流量 29.27166667 Nm3/min设计流量 32.19883333 Nm3/min设计温度 20估计阻力 0.034168475设计工况流量 0.734797748 m3/s设计流速 6~8 7 m/s设计管径 365.6790332 mm选择管径 DN 350 2 压力1m水柱压力 9560.204082 Pa塔内密度 1.3538 t/m3氧化塔内阻力 0.130396738 Mpa浓缩段阻力 0.028473729 MPa管道内阻力计算体积流量V, 200 m3/h管道长度l, 12 m弯头数 5 个弯头当量长度 40 m总的沿程长度 52 m流速u, 7 m/s绝对粗糙度 0.0000001 mλ, 0.0049411690.397261991 m 水头损失H,沿程阻力损失 0.005141605 Mpa理论总的阻力损失 0.164012072 Mpa设计压力系数 1.2设计选型压力 0.196814487 Mpa循环泵计算名称数值单位总的循环流量 840 m3/h 1 一级循环泵流量 560 m3/h 流速选择 1.5~2.5 2.2 m/s计算管径 300.12114 mm选择管径 DN 300 mm实际流速u 2.2017771 m/s2 一级循环泵压力1m水柱压力 9560.2041 Pa 2.1 管道内阻力计算体积流量V, 560 m3/h管道长度l, 16.272 m弯头数 6 个弯头当量长度 48 m三通数 2 个三通当量长度 13.6 m阀门数量 3 个阀门当量长度 240 m大小头数量 2 个大小头当量长度 60 m总的沿程长度 377.872 m实际流速 2.2017771 m/s绝对粗糙度 0.0003 mλ 0.0196275.9923117 m 水头总损失H吸收塔进口高度 20.35 m 2.2 理论管道总的阻力 26.342312 m 2.3 喷嘴进口压力 14 m 2.4 循环泵进口扬程 11 m设计压力系数 1.2 2.5 设计选型压力 35.210774 Mpa3 二级循环泵流量 280 m3/h流速选择 1.5~2.5 1.6 m/s计算管径 248.84731 mm选择管径 DN 250 mm实际流速u 1.5852795 m/s4 二级循环泵压力1m水柱压力 9560.2041 Pa 4.1 管道内阻力计算体积流量V, 280 m3/h管道长度l, 20.556 m弯头数 10 个弯头当量长度 80 m三通数 4 个三通当量长度 27.2 m阀门数量 5 个阀门当量长度 400 m大小头数量 2 个大小头当量长度 60 m总的沿程长度 587.756 m实际流速 1.5852795 m/s绝对粗糙度 0.0003 mλ 0.02052786.0642977 m 水头总损失H吸收塔进口高度 22.15 m 4.2 理论管道总的阻力 28.214298 m 4.3 喷嘴进口压力 14 m 4.4 循环泵进口扬程 11 m设计压力系数 1.2 4.5 设计选型 37.457157 Mpa塔内阻力计算名称单位数值塔阻力 Pa 797.87485填料层阻力 Pa 107.50702多孔阻力 Pa 36.158675总阻力 941.540541035.6946其中300?烟气粘度 0.0000282400?烟气粘度 0.000031744?烟气粘度 1.924E-05烟气密度 kg/m3 1.32烟气流速 m/s 2.83Re 1059043.7摩擦系数λ 0.2548265 填料层阻力 107.50702。
冶金企业气体介质流量补正方法
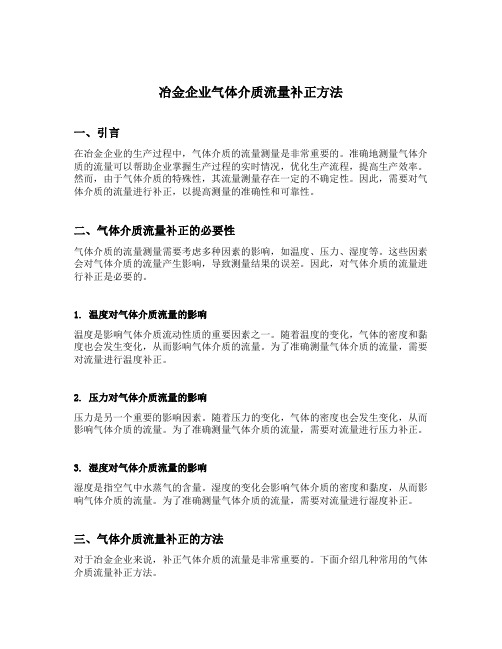
冶金企业气体介质流量补正方法一、引言在冶金企业的生产过程中,气体介质的流量测量是非常重要的。
准确地测量气体介质的流量可以帮助企业掌握生产过程的实时情况,优化生产流程,提高生产效率。
然而,由于气体介质的特殊性,其流量测量存在一定的不确定性。
因此,需要对气体介质的流量进行补正,以提高测量的准确性和可靠性。
二、气体介质流量补正的必要性气体介质的流量测量需要考虑多种因素的影响,如温度、压力、湿度等。
这些因素会对气体介质的流量产生影响,导致测量结果的误差。
因此,对气体介质的流量进行补正是必要的。
1. 温度对气体介质流量的影响温度是影响气体介质流动性质的重要因素之一。
随着温度的变化,气体的密度和黏度也会发生变化,从而影响气体介质的流量。
为了准确测量气体介质的流量,需要对流量进行温度补正。
2. 压力对气体介质流量的影响压力是另一个重要的影响因素。
随着压力的变化,气体的密度也会发生变化,从而影响气体介质的流量。
为了准确测量气体介质的流量,需要对流量进行压力补正。
3. 湿度对气体介质流量的影响湿度是指空气中水蒸气的含量。
湿度的变化会影响气体介质的密度和黏度,从而影响气体介质的流量。
为了准确测量气体介质的流量,需要对流量进行湿度补正。
三、气体介质流量补正的方法对于冶金企业来说,补正气体介质的流量是非常重要的。
下面介绍几种常用的气体介质流量补正方法。
1. 温度补正方法温度补正是根据气体介质的温度对流量进行修正。
常用的温度补正方法有:•等温法:假设气体介质的温度不变,即认为气体介质的密度和黏度不随温度变化而变化。
•线性法:假设气体介质的密度和黏度与温度成线性关系,通过线性插值计算补正系数。
•实测法:通过实测温度和气体介质的密度、黏度建立温度补正模型,根据实测数据进行补正。
2. 压力补正方法压力补正是根据气体介质的压力对流量进行修正。
常用的压力补正方法有:•等压法:假设气体介质的压力不变,即认为气体介质的密度不随压力变化而变化。
CEMS污染物、颗粒物、流量的计算和折算公式
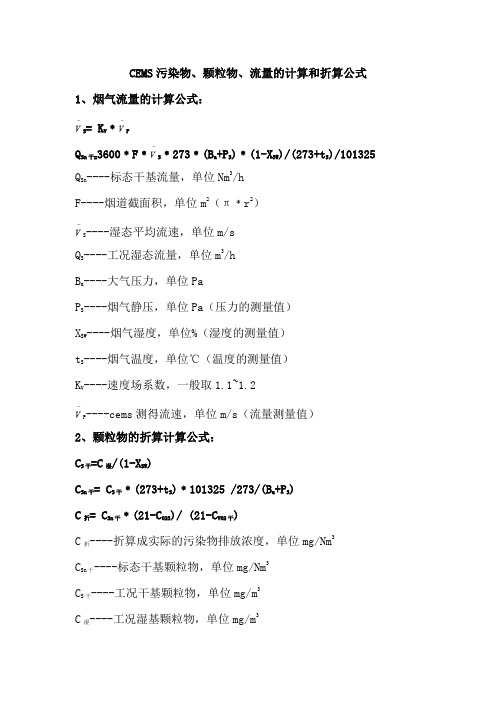
CEMS污染物、颗粒物、流量的计算和折算公式1、烟气流量的计算公式:-V S= K V﹡-V PQ Sn干=3600﹡F﹡-V S﹡273﹡(B a+P S)﹡(1-X SW)/(273+t S)/101325 Q Sn----标态干基流量,单位Nm3/hF----烟道截面积,单位m2(π﹡r2)-V S----湿态平均流速,单位m/sQ S----工况湿态流量,单位m3/hB a----大气压力,单位PaP S----烟气静压,单位Pa(压力的测量值)X SW----烟气湿度,单位%(湿度的测量值)t S----烟气温度,单位℃(温度的测量值)K V----速度场系数,一般取1.1~1.2-V P----cems测得流速,单位m/s(流量测量值)2、颗粒物的折算计算公式:C S干=C湿/(1-X SW)C Sn干= C S干﹡(273+t S)﹡101325 /273/(B a+P S)C折= C Sn干﹡(21-C O2S)/ (21-C VO2干)C折----折算成实际的污染物排放浓度,单位mg/Nm3C Sn干----标态干基颗粒物,单位mg/Nm3C S干----工况干基颗粒物,单位mg/m3C湿----工况湿基颗粒物,单位mg/m3X SW----烟气湿度,单位%(湿度的测量值)B a----大气压力,单位PaP S----烟气静压,单位Pa(压力的测量值)t S----烟气温度,单位℃(温度的测量值)C O2S----行业内氧气基准值,单位%(火电厂6%,垃圾焚烧11%,钢铁烧结机16%)C VO2干----烟气中含氧量干基体积浓度,单位%(氧气的测量值)3、气态污染物的折算计算公式:(SO2、HCL、HF、NO﹡、CO、)C S干=C湿/(1-X SW)C Sn干= C S干﹡(273+t S)﹡101325 /273/(B a+P S)C折= C Sn干﹡(21-C O2S)/ (21-C VO2干)C折----折算成实际的污染物排放浓度,单位mg/Nm3C Sn干----标态干基污染物,单位mg/Nm3C S干----工况干基污染物,单位mg/m3C湿----工况湿基污染物,单位mg/m3X SW----烟气湿度,单位%(湿度的测量值)B a----大气压力,单位PaP S----烟气静压,单位Pa(压力的测量值)t S----烟气温度,单位℃(温度的测量值)C O2S----行业内氧气基准值,单位%(火电厂6%,垃圾焚烧11%,钢铁烧结机16%)C VO2干----烟气中含氧量干基体积浓度,单位%(氧气的测量值)。
脱硫算法

脱硫算法1.入口流速:公式:Vsi=K1×K p×Pdi/ρs其中K1=流动系数(需要环保测定,后修改);K p=皮托管系数(取0.83);Pdi=差压(工程值,0-400Pa.公式中差压是要开方的,项目中是在变送器中开方的);ρs=管道内湿气密度(密度取0.6025,开方后为0.7762).在我的算法中:1×1×0.83×value /100/0.7762K1=1;第2个1是留给你现场修改的系数;0.83=皮托管系数;value/100=In差压/100=Pdi;0.7762=ρs2.工况流量:公式:Q工=3600×Vsi×F=3600×K1×K p×Pdi/ρs×F=0.36×K1×K p×Pdi/ρs×F(万方)在我的算法中:1×0.8×0.83×19.56×0.36×value/100/0.7762K1=流动系数(需要环保测定,后修改);第2个0.8是留给你现场修改的系数;0.83=皮托管系数;F=19.56(是入口烟道的截面积);value/100=In_差压/100=Pdi;0.7762=ρs;3.标况流量:公式:Q标=3600×Vsi×F×{(B a+P s)×[1-(17/100)]}/101325×273/(t s+273)/10000Q标=3600×273/101325×Vsi×F×{(B a+P s)×[1-(17/100)]} /(t s+273)/100003600×273/101325=9.7;Ba=In_压力,烟道中的压力;Ps=测定断面烟气静压,取的是攀枝花当地的大气压=89790Pa;[1-(17/100)]=干烟气;t s=烟道中的温度;/10000是换算万方。
烟气流量的换算
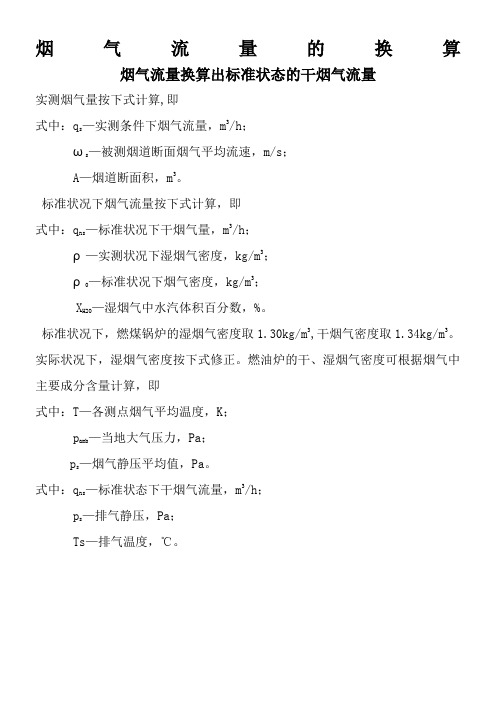
烟气流量的换算烟气流量换算出标准状态的干烟气流量
实测烟气量按下式计算,即
式中:q s—实测条件下烟气流量,m3/h;
ωs—被测烟道断面烟气平均流速,m/s;
A—烟道断面积,m3。
标准状况下烟气流量按下式计算,即
式中:q ns—标准状况下干烟气量,m3/h;
ρ—实测状况下湿烟气密度,kg/m3;
ρ0—标准状况下烟气密度,kg/m3;
X H2O—湿烟气中水汽体积百分数,%。
标准状况下,燃煤锅炉的湿烟气密度取1.30kg/m3,干烟气密度取1.34kg/m3。
实际状况下,湿烟气密度按下式修正。
燃油炉的干、湿烟气密度可根据烟气中主要成分含量计算,即
式中:T—各测点烟气平均温度,K;
p amb—当地大气压力,Pa;
p s—烟气静压平均值,Pa。
式中:q ns—标准状态下干烟气流量,m3/h;
p s—排气静压,Pa;
Ts—排气温度,℃。
烟气脱硫计算公式汇总(烟气量、脱硫量、空气量、产物量等)

干烟气中SO2含量
ngSO2'
%
0.01866*0.375Sar/Vgy'
10)
湿烟气中N2含量
nshN2'
%
(0.79alfa'V0+0.008Nar)/Vy'
11)
干烟气中N2含量
ngN2'
%
(0.79alfa'V0+0.008Nar)/Vgy'
6
总燃烧产物实际湿体积
Vtshy
Nm3/h
Vy'*Bj*1000
Nm3/kg
0.79V0+0.008Nar
2)
二氧化物
VRO20
Nm3/kg
0.01866(Car+0.375Sar)
3)
水蒸汽
VH2O0
Nm3/kg
0.111Har+0.0124Mar+0.0161V0
3
燃烧产物实际体积
Vy'
Nm3/kg
Vy0+0.0161(alfa'-1)V0+(alfa'-1)V0
Cso2
mg/Nm3
M/Vtshy(标态,干基,6%O2)
ppm
Cso2*22.41/64
3
要求脱硫量
Ms
kg/h
M*η*n/100
kmol/h
Ms/64
4、吸收剂消耗量计算
1
石灰石(CaCO3)理论消耗量
M3
kmol/h
Ms/64*(Ca/S)
kg/h
M3*M1
2
石灰石(CaCO3)实际消耗量
M3'
脱硫计算公式大全

t/h
M3/(ca/s)*((ca/s)-1))
5
CaCO3带入的杂质
M7
t/h
M3'*(1-P/100)
6
脱硫产物总量
M8
t/h
M4+M5+M6+M7
7
皮带机出口石膏产量
M9
t/h
M8/
8
石膏纯度
n1
%
M4/M8
9
总的脱硫产物量
M8'
t/h
M8
10
皮带机出口的石膏总产量
M9'
t/h
M9
11
年石膏生成量
湿烟气中N2含量
nshN2'
%
'V0+/Vy'
11)
干烟气中N2含量
ngN2'
%
'V0+/Vgy'
6
总燃烧产物实际湿体积
Vtshy
Nm3/h
Vy'*Bj*1000
7
总燃烧产物实际干体积
Vtgy
Nm3/h
Vgy'*Bj*1000
8
总燃烧产物6%O2干体积
Vtgy-O2
Nm3/h
Vtgy*(21-ngo2')/(21-6)
%
VO2'/Vgy'
4)
湿烟气中含氧量
nsho2'
%
VO2'/Vy'
5)
湿烟气中含湿量
nH2O'
%
VH20'/Vy'
6)
湿烟气中CO2含量
nshCO2'
脱硫计算公式大全.docx

序名称符单位计算公式或数值来源号号一烟气量计算1理论空气量03(C ar ++ V Nm/kg燃烧产物理论体积V030+V00Nm/kg V+Vy N2RO2H2O 1)氮气V03+Nm/kgN22)二氧化物03(C ar + V RO2Nm/kg3)水蒸汽03++ V H2O Nm/kg3燃烧产物实际体积V y'30'-1)V+(a lfa '-1)V0 Nm/kg V y +(a lfa4干烟气量V gy'300'-1)V0 Nm/kg V RO2+V N2+(a lfa烟气含氧量和含湿量计算1)烟气中的水分V 'H2O 2)烟气中的氧量V 'O23)干烟气中含氧量n go2'4)湿烟气中含氧量n sho2'5)湿烟气中含湿量n H2O'6)湿烟气中 CO2含量 n shCO2'7)干烟气中 CO2含量 n gCO2'8)湿烟气中 SO2含量 n shSO2'9)干烟气中 SO2含量 n gSO2'10)湿烟气中 N 含量n '2shN2 11)干烟气中 N2含量n gN2'6总燃烧产物实际湿Vt shy 体积7总燃烧产物实际干Vt gy30'-1)V0Nm/kg V +(alfaH2O3(a lfa'-1)V0 Nm/kg%V O2'/V gy'%V O2'/V y'%V H20'/V y'%V y'%V gy'%*V y'%*V gy'%'V 0+/V y'%'V 0+/V gy'3V y'*B j *1000 Nm/h3V gy'*B j *1000 Nm/h总燃烧产物6%O2干3')/(21-6)8Vt gy-O2 Nm/h V tgy *(21-n go2体积烟气含硫量及脱硫量计算1脱硫进口 SO2量M kg/h Bj*1000*Sy/100**64/kmol/h M/642脱硫进口 SO2实际C3M/Vt(标态,干基, 6%O)mg/Nmshyso22浓度ppm C so2*643要求脱硫量M kg/h M*η*n/100skmol/h M s/64吸收剂消耗量计算石灰石 (CaCO3) 理论1M kmol/h M/64*(Ca/S)3s消耗量kg/h M*M31石灰石 (CaCO3)实际2M3'kg/h M3*M1/(P/100)消耗量t/h脱硫产物计算1生成量M4t/h M s/64*M 10/10003脱硫产物中飞灰含M5t/h m2*2/3引风机出口飞灰总量m2t/h V tgy-o2 *m h4未反应的 CaCO M t/h M/(ca/s)*((ca/s)-1))3635CaCO带入的杂质M t/h M'*(1-P/100)3736脱硫产物总量M t/h M+M+M+M845677皮带机出口石膏产M9t/h M8/量8石膏纯度n1%M/M849总的脱硫产物量M8't/h M810皮带机出口的石膏M't/h M99总产量11年石膏生成量t/ 年M'*H91kg 水蒸发需要热1)m sh kj/kg(50-10)*+2510量:脱硫反应热蒸发水量 (CaCO3+SO2+1/2O2++339kJ/mol)m t/h Ms/64*339/mshsh12)烟气降温蒸发水量 ( 未计放热损失 )热交换器放热端 : 126------t吸热端 : 50----85kcal/Nm 3.烟气比热100℃℃kcal/Nm 3.200℃℃i 1kcal/Nm 3. 插值法 : tpyi 2ti 3塔内烟气放热量Q1塔内烟气放热蒸发m sh2水量3)单塔蒸发水量M we单塔蒸发水汽体积V we 2脱硫耗水量1)脱硫结晶水M gyc2)石膏表面水M gys3)FGD废水M ww ℃插值法求 85℃比热℃t=126-i 2*(85-50)/i1kcal/Nm 3.插值法 : t℃kJ/h V ' * i3**(t-50)t/h Q1/m sht/h m sh1+m sh236Nm/h M we/18*10 *1000t/h M4/M10*(2*18)t/h M9*t/h(B j *%*1000+(M gyc +M gys+M we)*1000****1000*%)/10004)脱硫蒸发水量M t/hwe5)清洁冲洗水M t/h估计gyw6)泵与风机冷却用水M t/h估计wq7)单套脱硫装置耗水M w t/h M gyc +M gys+M ww+M we+M gyw+M wq 量8)总的脱硫装置耗水M't/h n*Mw w 量氧化空气量计算1需氧量V o2kg/h SO2---1/2O 2kmol/h Vo2/322需空气量3V k Nm/hV o2/32*七主要参数汇总四台炉的数据1吸收塔进口烟气量V'3 Nm/h2吸收塔出口烟气量V"3Vt+V -V+V -VNm/hshy o2so2k we3脱水机出口石膏M t/h含水 10%94旋流站出口石膏浆M11t/h M8/( 含水 50%)液量5石膏旋流站出口回M12t/h M13-M11-Mww(不包括废水 )流量6吸收塔排出浆液量M13t/h M8/( 含水 85%)7石灰石粉耗量M3't/h8工艺水量M t/h包括冷却水等w9FGD废水M t/hww八主要设备选择1吸收塔烟气流速νm/s取值烟气量Q3/h V"*(273+50)/273 m计算直径D m(4*Q/ ν/3600)液气接触时间S s取值吸收塔高度H mν*S液气比L/G取值浆液循环量Qc3(L/G)*V"/1000 m/h浆液停留时间T min取值吸收塔浆池容积3Qc*T/60 V1m2石灰石粉仓容积3按 7天储量: M3' ×7×24/ m3石灰石浆池容积3按 4小时储量: M' ×4/m3。
脱硫有关计算公式

脱硫有关计算公式一、锅炉每小时产生的SO2量:锅炉产生的SO2量(mg/Nm3)= 耗煤量(t/h)×含硫量(%)×2×燃烧率×109100×干烟气体积(N m3/h)我厂锅炉设计的干烟气体积为277920Nm3/h,如锅炉每小时耗煤量为35吨,煤的含硫量为1%,锅炉的燃烧率为95%,那么每台锅炉每小时产生的SO2量则为2393mg/Nm3。
二、每台吸收塔每小时脱除的SO2量:脱除的SO2量(t)=耗煤量(t/h)×含硫量(%)×2×燃烧率×脱硫率如锅炉每小时耗煤量为35吨,煤的含硫量为1%,锅炉的燃烧率为95%,设计脱硫率量则为0.6吨。
为90%,那么一台塔脱除的SO2三、脱硫系统每小时消耗的电石渣量:量(t)×56 脱硫系统消耗的电石渣(t/塔)= 脱除的SO264×0.65如锅炉每小时耗煤量为35吨,煤的含硫量为1%,那么一台吸收塔运行,每小时消耗的电石渣为0.8吨。
可以用下式对电石渣耗量进行估算:脱硫系统消耗的电石渣量(t/h)=80×锅炉(脱硫塔)运行台数×含硫量(%)四、脱硫系统每小时补充的钠碱量:脱硫系统补充的钠碱量(kg/塔)= 脱除的SO2量(t)×1000×0.05×4064×0.3如锅炉每小时耗煤量为35吨,煤的含硫量为1%,那么一台吸收塔运行,每小时补充的钠碱为62. 34kg。
可以用下式对钠碱量的补充量进行估算:脱硫系统补充的钠碱时(kg/h)=6234×锅炉(脱硫塔)运行台数×含硫量(%)烟气密度=标准状态下烟气密度(压力101325Pa,温度0摄氏度)*测点绝对压力/标准压力(101325pa)*(273+测点温度)/273。
- 1、下载文档前请自行甄别文档内容的完整性,平台不提供额外的编辑、内容补充、找答案等附加服务。
- 2、"仅部分预览"的文档,不可在线预览部分如存在完整性等问题,可反馈申请退款(可完整预览的文档不适用该条件!)。
- 3、如文档侵犯您的权益,请联系客服反馈,我们会尽快为您处理(人工客服工作时间:9:00-18:30)。
烧结脱硫烟气流量量程的修正算法
摘要:烧结脱硫烟气流量计的量程是基于一定温度、压力条件下的标况量程,对于监
控的工况流量,需要根据实际工况重新计算差压和对应的量程,详细介绍了量程修正计算
的方法和过程。
关键词:流量计,标况,工况,量程
The Conversion Method for the Flowmeter Span of the Sintering
Waste Gas Desulfuration
Han Jun
(Bao Steel, Shanghai, 201900)
Abstract: The flowmeter span of the sintering waste gas desulfuration is the standard conditions span based on the given temperature and pressure. For the working conditions flow, it is necessary to calculate the differential pressure and span based on the real conditions. The arithmetic and process for Conversion span have been discussed detailedly.
Key words: flowmeter, standard conditions, working conditions, span
1、概述
宝钢三烧结机头脱硫装置根据工艺和环保要求,共装有4套巍缔巴均速管流量计分别对
原烟气入口风量、除雾器出口风量、旁路烟道A风量和旁路烟道B风量进行测量,4个测点
均不满足直管段要求,为提高测量精度全部选用满管插入的探头。
其中原烟气入口和除雾器
出口风量测量更采用2支巍缔巴均速管水平垂直交叉安装,并将2支流量计正压侧出口并联、负压侧出口
并联,组成横截面风量测量装置。
系统投运后发现监测的风量与烧结工艺明显不匹配:烧结正常生产时主抽风机入口测量风量为1900~2100 Km3/h(压力-16kpa左右,温度110℃左右),而原烟气入口风量只有1200 Km3/h,存在明显的差异。
经仔细检查分析,流量计厂家基于设计院提供的条件计算出的差压对应的流量是标况的量程,HMI监控中的量程与现场一致,这样就造成了偏差。
环保局要求上传的流量是工况下的流量,因此需要将现有的流量折算成工况流量,一种方法是对实测的标况流量进行温压补正,但由于进行温压补正的检测参数不全,因此决定对二次仪表的量程按工况进行修正计算。
2、工艺参数与计算条件
通过查看流量计厂家的计算书和设计院提供的原始工艺参数,4套流量计的详细数据如表1所示。
其中旁路烟气流量的量程为0~900 Km3/h,是基于压力为-100Pa、温度为110℃条件下计算的标况量程;增压风机入口流量的量程为0~1600 Km3/h,是基于压力为-400Pa、温度为200℃条件下计算的标况量程;除雾器出口流量的量程为0~1600 Km3/h,是基于压力为300Pa、温度为100℃条件下计算的标况量程。
设计院提供的设计温度与现场实际相差较大,其中增压风机入口、除雾器出口的设计温度是极限温度,不宜用来作为工况温度计算差压、量程。
旁路烟道A、B一个是脱硫系,一个是非脱硫系,两者之间的温度有一定差异,计算时全按110℃也不合适。
表1 流量计的设计数据
3对应工况量程的重新计算 3.1体积流量计算
任何一种差压式流量计都是遵循伯努利方程的,即可简单的表述为:
∆P ⨯=ρK M (1)
其中M :质量流量
K :流量常数
ρ:介质密度
∆P :差压
由式1可得体积流量计算公式
ρ/M Qv = (2)
无温压补偿时工况流量的计算模型如式3所示:
工
工工工
ρρρ∆P ⨯=
=K M Qv ……………………………………………(3) 如需要计算标况流量,可参照公式4:
标
工标标
ρρρ∆P ⨯=
=K M Qv ……………………………………………(4) 只要从差压变送器里接收到差压∆P ,就可以运算出瞬时流量和累积流量。
3.2理想气体状态方程
根据理想气体状态方程,由于温度压力变化引起的工况密度变化可用下式表示
标标工ρρρ⨯+⨯+⨯=⨯⋅⋅=
I )
T (T P )P (P T T P T P 000I 0工标标工…………………………(5)
其中:0T =273.15K
0P =101.33KPa
I P :工况下表压力 I T :工况下摄氏温度
3.3工况量程的计算
由式3和式4可得:
)P (P T )T (T P Q Q 000v v I +⨯+⨯===0I 工
标标
工标工ρρρρM M
所以标况流量量程转换工况流量量程的计算公式如式6所示:
标工v 000v Q )
P (P T )
T (T P Q ⨯+⨯+⨯=
I 0I (6)
四套流量计工况下的表压力基本在0kpa 附近,设计计算所依据的压力与现场是吻合的,而现场工况实际温度与设计依据温度偏差太大,而且两个旁路烟道无温度检测,无法进行温压补正,所以所取的参考温度与实际工况温度越接近越好。
增压风机入口和除雾器出口通过在脱硫控制系统收集近半年的温度数据进行计算,入口温度基本在125℃~135℃,取其平均温度130℃为计算所需的工况温度。
除雾器出口温度一般为55℃~60℃,取其最高温度60℃作为计算所需的工况温度。
两个旁路烟道由于无温度检测,就以各自烟道主轴风机前的烟道检测温度为基准,再加上15℃的风机升温作为实际工况温度,通过在三烧结主控制系统收集半年多的数据,对烧结正常工作时主抽风机前进口烟气温度进行平均,A 、B 烟道的温度为114℃和103℃,所以旁路烟道A 、B 的实际工况参考温度为129℃和118℃。
各流量计实际工况参数如表2所示,根据表中的数据,应用公式6计算各工况流量流程也如表2中所示。
表2流量计的修正数据
根据计算结果,修改二次仪表和PLC 中对应的量程,并与独立测量的数据进行了比对,
实际压力与计算所依据的工况压力非常接近,由于烧结工艺的变化,烟气实际温度
是波动的,但其平均值与修正后的参考温度非常接近,实测流量也基本一致。
4 结束语
在充分调查现场工况的基础上,应用理论分析与实测数据,较好地解决了流量计的工况转换,使其给出的测量数据达到了系统要求。
参考文献:
[1] 薛福连,流量测量中温度、压力补偿数学模型的建立,电气传动自动化,2008,
Vol.30(1),61-62
[2] 芦满涛,气体体积流量测量中温度和压力修正的必要性,冶金自动化,2008,
Vol.32(4),43-45
[3] 董萍等,威力巴流量计的特点及应用,石油化工自动化,2004,(5),90-91
.。