零件检验方法
零部件的检验方法

零部件的检验方法一、经历法经历法是通过观察、敲击和感觉来检验和判断零件技术状况的方法。
这种方法虽然简单易行,但它要求技术人员有对各种尺寸、间隙、紧度、转矩和声向的感觉经历,它的准确性和可靠性是有限的。
1.目测法对于零件外表有毛糙、沟槽、刮伤、剥落〔脱皮〕,明显裂纹和折断、缺口、破洞以及零件严重变形、磨损和橡胶零件材料的变质等,都可以通过眼看、手摸或借助放大镜观察检查确定出来。
对于齿轮中心键槽或轴孔的磨损,可以与相配合的零件配合检验,以判定其磨损程度。
2.敲击法汽车上局部壳体、盘形零件有无裂纹,用铆钉连接的零件有无松动,轴承合金与底板结合是否严密,都可用敲击听音的方法进展检验。
用小锺轻击零件,发出清脆的金属响声,说明技术状况是好的;如发出的声音沙哑,那么可判定零件有裂纹、松动或结合不严密。
3.比拟法用新的标准零件与被检验零件相比,从中鉴别被检验零件的技术状况。
用此法可检验弹簧的自由长度和负荷下的长度、滚动轴承的质量等。
如将新旧弹簧一同夹在虎钳上,用此法可判定其弹力大小。
用比拟法检验弹簧弹力二、测量法零件因磨损或变形引起尺寸和几何形状的变化,或因长期使用引起技术性能〔如弹性〕的下降等。
这些改变,通常是采用各种量具和仪器测量来确定的。
如轴承孔和轴孔的磨损,一般用相配合的零件进展配合检验,较松旷时,可插入厚薄规检查,判定其磨损程度,确定是否可继续使用;要求较高的气缸损坏时,应用量缸表或内径测微器进展测量,确定其失圆和锥形程度。
轴类零件一般用千分尺来检查。
对于磨损较均匀的轴,只检查其外径大小,但对某些磨损不均匀的轴,还需检查其椭圆度及锥度的大小。
测量曲轴连杆轴颈时,先在轴颈油孔两侧测量,然后转90°再测量。
轴颈同一横断面上差数最大值为椭圆度,轴颈同一纵断面上差数最大值为锥度。
滚珠轴承〔球轴承〕的磨损情况,可以通过测量它的径向和轴向间隙加以判定。
将轴承放在平板上,使百分表的触针抵住轴承外圈,然后一手压紧轴承内圈,另一手往复推动轴承外圈,表针所变动的数字,即为轴承的径向间隙。
热处理零件检查方法及性能要求
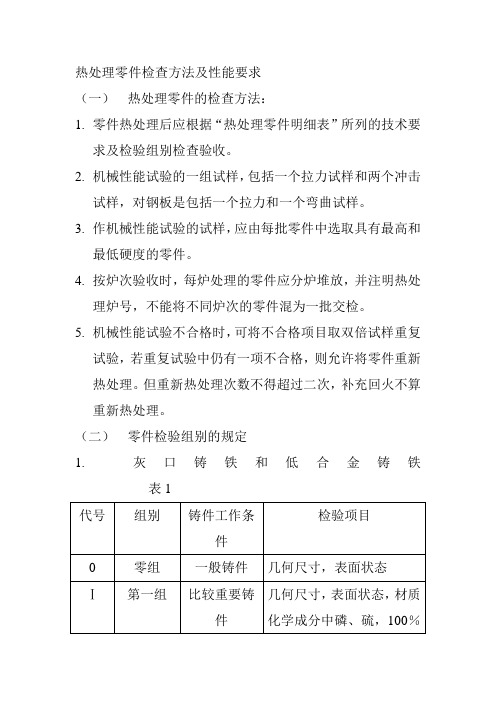
表1
代号 组别 铸件工作条
检验项目
件
0
零组
一般铸件 几何尺寸,表面状态
Ⅰ 第一组 比较重要铸 几何尺寸,表面状态,材质
件
化学成分中磷、硫,100%
检查硬度 Ⅱ 第二组 重要铸件 几何尺寸,表面状态,材质
化学成分中磷、硫、抗弯σ w,挠度 Y(或抗拉),按 图纸规定作水压试验。
2. 锻件及型钢
表2
代号 组别 检验项目
件
炉号检验材质σb、δ、HB。
Ⅱ 第二组 重要铸件 几何尺寸,表面状态,按同
炉号检验材质σb、δ、HB
和化学成分,按图纸规定作
水压试验和无损探伤。
4. 按炉次验收时,每炉处理的零件应分炉堆放,并注明热处
理炉号,不能将不同炉次的零件混为一批交检。
5. 机械性能试验不合格时,可将不合格项目取双倍试样重复
试验,若重复试验中仍有一项不合格,则允许将零件重新
热处理。但重新热处理次数不得超过二次,补充回火不算
重新热处理。
(二) 零件检验组别的规定
1.
灰口铸铁和低合金铸铁
热处理零件检查方法及性能要求
(一) 热处理零件的检查方法:
1. 零件热处理后应根据“热处理零件明细表”所列的技术要
求及检验组别检查验收。
2. 机械性能试ห้องสมุดไป่ตู้的一组试样,包括一个拉力试样和两个冲击
试样,对钢板是包括一个拉力和一个弯曲试样。
3. 作机械性能试验的试样,应由每批零件中选取具有最高和
最低硬度的零件。
组
铸件 热处理炉号检验σs、σb、δ、Ψ
和化学成分。
Ⅱ 第二 重要铸件 几何尺寸,表面状态,按同一熔炼,
组
常用零件质量检验方法

常用零件质量检验方法常用零件质量检验方法1. 引言本旨在介绍常用零件质量检验方法,包括质量检验的基本原理、常见的零件质量检验方法及其步骤、工具和设备的使用等。
通过本的学习,读者将了解零件质量检验的基本概念和方法,掌握实施零件质量检验的技巧,提高零件质量的水平和准确度。
2. 零件质量检验的基本原理零件质量检验是通过对零件的外观、尺寸、材料和性能等方面进行测试和评估,以确保零件符合设计要求和质量标准的过程。
零件质量检验的基本原理包括如下几个方面:2.1 外观检验原理外观检验主要通过对零件的外观形状、表面光洁度、涂层质量等进行检查,以判断零件的表面是否有缺陷、腐蚀、裂纹、变形等问题。
2.2 尺寸检验原理尺寸检验主要通过对零件的几何尺寸进行测量和评估,以确定零件的尺寸是否符合设计要求和制造标准。
2.3 材料检验原理材料检验主要通过对零件的材料组织、成分、硬度等进行分析和测试,以确定零件的材料是否满足要求。
2.4 性能检验原理性能检验主要通过对零件的静态和动态性能进行测试和评估,以确定零件的可靠性、耐久性和工作性能是否满足要求。
3. 常见的零件质量检验方法及其步骤3.1 外观检验方法及步骤3.1.1 外观检验方法:(1)目测法:对零件进行直接目测,观察其表面有无明显缺陷、腐蚀、裂纹等。
(2)放大镜检验法:使用放大镜对零件表面进行放大观察,以检测微小缺陷和表面处理效果。
(3)影像检测法:利用影像检测设备对零件表面进行拍照或录像,通过图像处理系统对图像进行分析和评估。
3.1.2 外观检验步骤:(1)准备检验设备和工具:包括放大镜、影像检测设备、检验划线工具等。
(2)检查零件的整体外观:观察零件的表面是否有变形、缺陷、腐蚀等。
(3)检查零件的特定区域:对关键部位进行仔细检查,如螺纹孔、切割边缘等。
(4)记录检验结果:按照规定的记录表格进行记录,包括零件编号、检验日期、检验结果等。
3.2 尺寸检验方法及步骤3.2.1 尺寸检验方法:(1)直接测量法:使用卡尺、游标卡尺等直接测量零件的尺寸。
零部件检验标准及方法

零部件检验标准及方法零部件检验标准及方法1. 背景介绍在制造工业中,零部件的质量检验是确保产品品质的关键环节之一。
通过对零部件进行科学、严谨的检验,可以提高产品的可靠性和安全性。
本文将介绍常用的零部件检验标准及方法。
2. 外观检验•目的:检查零部件外观是否符合要求,包括表面光洁度、几何形状、尺寸精度等方面。
•方法:–直接目视检查:通过直接观察零部件外观,判断是否存在缺陷、损伤等问题。
–使用显微镜或放大镜进行检查:通过放大镜或显微镜观察细微的表面问题,如划痕、气孔等。
–使用测量工具进行尺寸检验:使用卡尺、量规等测量工具,对零部件的尺寸进行检查,确保其符合要求。
3. 功能性检验•目的:检查零部件的功能是否符合设计要求。
•方法:–运行测试:将零部件安装到相应的设备或系统中,进行正常工作状态下的运行测试,观察其功能是否正常。
–性能测试:使用专门的性能测试设备,对零部件进行负载测试、耐压测试、抗振动测试等,验证其性能是否达标。
4. 材料检验•目的:检查零部件所使用的材料是否符合要求,包括化学成分、物理性能等。
•方法:–化学分析:使用化学分析仪器,对材料进行成分分析,确保其成分符合要求。
–物理性能测试:使用拉力机、硬度计等测试材料的物理性能,如强度、硬度等。
5. 寿命检验•目的:检查零部件的使用寿命是否符合要求。
•方法:–疲劳测试:通过对零部件进行循环加载、循环使用等方式,检测其在长期使用过程中的寿命情况。
–加速老化测试:使用特定的老化设备,对零部件进行加速老化测试,模拟长期使用环境,检查其在短时间内的寿命表现。
6. 环境适应性检验•目的:检查零部件在特定环境条件下的适应性。
•方法:–温度适应性测试:将零部件暴露在不同温度条件下,观察其在不同温度下的性能变化。
–湿度适应性测试:将零部件暴露在高湿度或低湿度条件下,观察其在不同湿度条件下的性能表现。
–耐腐蚀性测试:将零部件暴露在化学腐蚀性环境中,观察其对腐蚀的抵抗能力。
零件常用的检验方法有

零件常用的检验方法有
以下是一些常用的零件检验方法:
1. 外观检查:通过目视检查,检查零件的表面是否有磨损、划痕、氧化、变形、裂纹等问题。
2. 尺寸检测:使用测量工具(如卡尺、量规、显微镜)测量零件的尺寸,与设计图纸或规格要求进行比较,以确定零件的尺寸是否符合要求。
3. 检测密封性:使用压力测试装置或浸漏法检测零件的密封性能,以确保没有泄漏。
4. 材料检验:通过使用化学分析、显微镜观察、拉伸试验等方法来检查材料的成分、晶体结构和机械性能,以验证材料的质量。
5. 功能性能检测:将零件安装到相应的设备或系统中,并测试其在实际运行条件下的功能性能,以确保零件能够正常工作。
6. 环境试验:将零件暴露在不同的环境条件下(如温度、湿度、振动等)进行测试,以评估零件的适应性和耐久性。
7. 可靠性试验:通过在特定条件下进行长时间的运行测试或边界条件测试来评估零件的可靠性和寿命。
8. 破坏性测试:将零件暴露在极限条件下,如超载、过温等,
以测试零件的最大承载能力和抗破坏性能。
这些方法可以组合使用,以确保零件的质量和可靠性。
具体的检验方法应根据零件的特点和要求进行选择。
金属零件类检验规范

金属零件类检验规范1. 引言金属零件在许多行业中都扮演着重要的角色,如制造业、汽车行业、航空航天等。
为了保证金属零件的质量和性能,需要进行严格的检验。
本文档旨在提供金属零件类检验的规范和流程,确保零件的质量符合标准要求。
2. 检验准备在开始金属零件的检验之前,需要进行必要的准备工作。
这些准备工作包括:•准备检验工具和设备,如千分尺、卡尺、金属磨光机等。
•根据零件图纸和要求,了解零件的关键尺寸和要求。
•清理和准备检验场所,确保无尘和干净。
3. 检验流程3.1 外观检验外观检验是金属零件检验的第一步,主要是对零件的表面进行检查。
具体步骤包括:1.用肉眼检查零件外观是否有明显的缺陷,如划痕、凹陷等。
2.使用放大镜或显微镜检查零件表面是否有微小的瑕疵,如气泡、裂纹等。
3.使用表面粗糙度测量仪测量零件的表面粗糙度是否符合标准要求。
3.2 尺寸检验尺寸检验是金属零件检验的核心内容,准确的尺寸是保证零件质量的关键。
具体步骤包括:1.使用千分尺、卡尺等测量工具测量零件的关键尺寸,如长度、直径等。
2.将测量结果与零件图纸上的要求进行比对,判断零件的尺寸是否符合要求。
3.对于复杂的零件,可以使用三坐标测量机进行精确的尺寸测量。
3.3 材质检验材质检验是判断金属零件材质是否符合要求的重要步骤。
具体步骤包括:1.使用金属成分分析仪测量零件中金属元素的含量,确保其符合要求。
2.对于特殊要求的零件,可以进行硬度测试、拉伸试验等,验证其材质的性能。
3.4 其他检验除了上述的外观、尺寸和材质检验外,根据零件的具体要求,还可以进行以下检验:1.表面处理检验:检查零件的表面处理是否符合要求,如镀层、喷漆等。
2.磁粉检验:对于需要进行磁粉探伤的零件,进行磁粉检验,发现和评估零件中的裂纹和缺陷。
3.超声波检验:对于需要进行超声波探伤的零件,进行超声波检验,检测零件内部的缺陷和瑕疵。
4. 检验记录和报告在完成金属零件的检验后,需要做好检验记录和报告,以备将来参考和追溯。
光学零件检验方法

光学零件检验方法光学零件的检验方法是确保光学零件质量和性能的重要步骤。
以下是常见的光学零件检验方法:1.外观检验:外观检验是最简单和最常见的检验方法之一、它涉及对光学零件表面的检查,以确保没有明显的缺陷、瑕疵或污染。
常用的外观检查仪器有放大镜、显微镜和光谱仪等。
2.尺寸检验:尺寸检验是测量光学零件尺寸和形状的方法。
常用的尺寸测量仪器有投影仪、坐标测量机和光学分光计等。
这些仪器可以精确测量光学零件的长度、宽度、直径、圆度和平面度等。
3.表面粗糙度检验:表面粗糙度是表面微小不规则性的度量标准,对光学零件的性能具有重要影响。
常用的表面粗糙度检测仪器有光学轮廓仪、表面粗糙度仪和压电表面粗糙度仪等。
4.平整度检验:平整度是表面平坦性的度量标准,对光学零件的质量和性能有着重要影响。
常用的平整度测量仪器有检测平台和激光干涉仪等。
5.光学性能检验:光学性能检验涉及到对光学零件传输、透射、反射、折射、散射等光学性能的测量和评估。
常用的光学性能测量仪器有光谱仪、干涉仪、激光测距仪和分光光度计等。
6.工作环境检验:在一些特殊应用中,光学零件需要在特定的环境条件下工作,比如高温、低温、高湿度或低湿度等。
在这种情况下,光学零件的工作环境稳定性也需要进行检验。
7.强度检验:一些光学零件可能会经受较大的外力作用,因此需要进行强度检验。
常用的强度检验方法包括拉伸测试、弯曲测试、冲击测试和疲劳测试等。
总之,光学零件的检验方法是多样的,根据具体需要选择合适的检验方法进行检验,以确保光学器件的质量和性能符合要求。
机械零部件检验规范

机械零部件检验规范机械零部件是机械设备的组成部分,它们直接关系到机械设备的整体性能和使用寿命。
因此,对机械零部件进行检验是非常必要的。
机械零部件的检验需要遵循一定的规范,下面将介绍机械零部件检验的规范。
一、机械零部件的检查方法机械零部件的检查方法主要包括外观质量检查、尺寸检查、物理性能检查和化学成分检查。
1. 外观质量检查外观质量检查是对机械零部件表面的缺陷、划痕、气泡、裂纹等进行检查,在机械零部件加工完成后应进行外观合格鉴定。
对于表面有缺陷的机械零部件,应予以拒收。
2. 尺寸检查尺寸检查是对机械零部件的尺寸、形位公差、形状和位置等进行检查。
尺寸检查应使用专业的测量仪器,在采用传统测量方法无法得到很高的精度时,应采用三坐标测量机、光学投影仪等高精度测量设备。
3. 物理性能检查物理性能检查主要对机械零部件的强度、硬度、韧性、耐磨性、耐热性、防腐性等进行检查。
这种检查主要通过对机械零部件进行试验来完成,如拉伸试验、冲击试验、压缩试验和硬度试验等。
4. 化学成分检查化学成分检查是对机械零部件的成分及成分中所含的有害元素进行检查。
机械零部件中所含的有害元素可能会影响机械零部件的性能和使用寿命,因此化学成分检查是必不可少的。
二、机械零部件的检验标准机械零部件的检验标准是机械零部件检验的依据。
机械零部件的检验标准应根据行业的标准、国家标准和地方标准等进行确定。
机械零部件的检验标准应包括以下内容:1. 外观质量要求外观质量应包括机械零部件表面的缺陷、划痕、气泡和裂纹等。
2. 尺寸公差要求尺寸公差应根据机械零部件的用途和要求确定,应符合行业的标准、国家标准和地方标准等规定。
3. 检验方法检验方法应包括机械零部件的外观质量检查、尺寸检查、物理性能检查和化学成分检查等。
4. 数据统计要求数据统计应包括机械零部件的尺寸公差、物理性能指标和化学成分指标的统计。
5. 合格标准合格标准应根据机械零部件的用途和要求确定,应符合行业的标准、国家标准和地方标准等规定。
汽车零部件的质量标准及检验方法
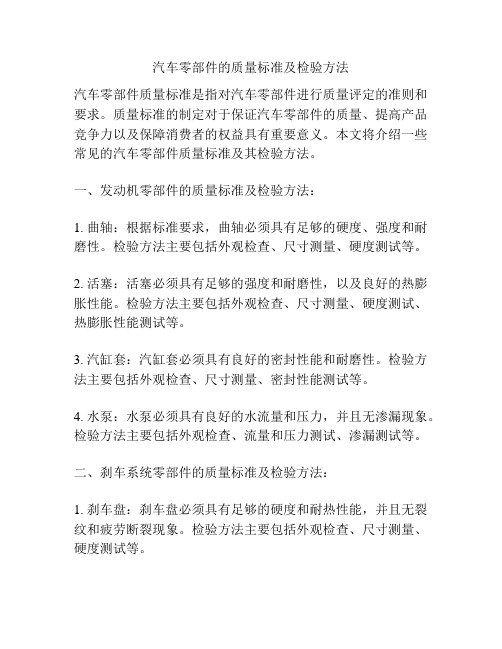
汽车零部件的质量标准及检验方法汽车零部件质量标准是指对汽车零部件进行质量评定的准则和要求。
质量标准的制定对于保证汽车零部件的质量、提高产品竞争力以及保障消费者的权益具有重要意义。
本文将介绍一些常见的汽车零部件质量标准及其检验方法。
一、发动机零部件的质量标准及检验方法:1. 曲轴:根据标准要求,曲轴必须具有足够的硬度、强度和耐磨性。
检验方法主要包括外观检查、尺寸测量、硬度测试等。
2. 活塞:活塞必须具有足够的强度和耐磨性,以及良好的热膨胀性能。
检验方法主要包括外观检查、尺寸测量、硬度测试、热膨胀性能测试等。
3. 汽缸套:汽缸套必须具有良好的密封性能和耐磨性。
检验方法主要包括外观检查、尺寸测量、密封性能测试等。
4. 水泵:水泵必须具有良好的水流量和压力,并且无渗漏现象。
检验方法主要包括外观检查、流量和压力测试、渗漏测试等。
二、刹车系统零部件的质量标准及检验方法:1. 刹车盘:刹车盘必须具有足够的硬度和耐热性能,并且无裂纹和疲劳断裂现象。
检验方法主要包括外观检查、尺寸测量、硬度测试等。
2. 刹车片:刹车片必须具有良好的摩擦性能和耐磨性,并且无过度磨损和断裂现象。
检验方法主要包括外观检查、尺寸测量、摩擦性能测试等。
3. 刹车管:刹车管必须具有足够的压力和耐腐蚀性能,并且无渗漏现象。
检验方法主要包括外观检查、压力测试、渗漏测试等。
三、底盘系统零部件的质量标准及检验方法:1. 前后悬挂系统:悬挂系统必须具有良好的弹性和稳定性,并且无脱落现象。
检验方法主要包括外观检查、弹性测试等。
2. 轮胎:轮胎必须具有良好的抗磨性和抗刺穿性,并且无脱胎现象。
检验方法主要包括外观检查、压力测试、刺穿测试等。
3. 车轮:车轮必须具有足够的刚度和强度,并且无裂纹和疲劳断裂现象。
检验方法主要包括外观检查、尺寸测量、强度测试等。
以上是一些常见的汽车零部件质量标准及其检验方法,只是列举了部分内容,并不能覆盖全部零部件。
汽车零部件的质量标准和检验方法应根据不同的零部件类型和用途进行制定,以确保汽车零部件具有良好的质量和性能。
常用零件的检验方法及特点
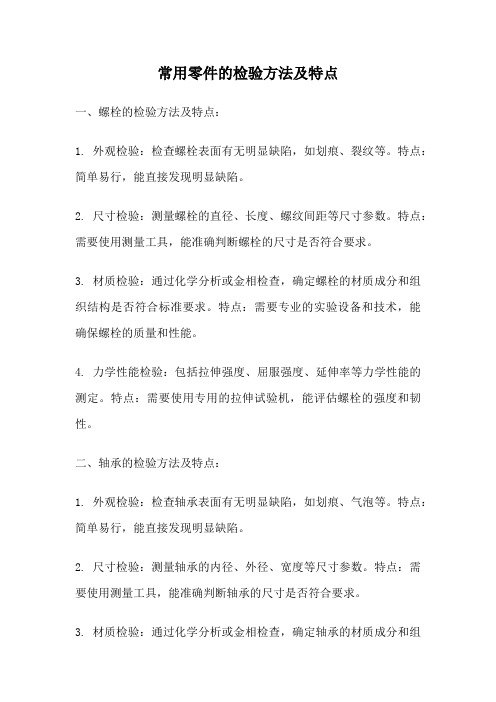
常用零件的检验方法及特点一、螺栓的检验方法及特点:1. 外观检验:检查螺栓表面有无明显缺陷,如划痕、裂纹等。
特点:简单易行,能直接发现明显缺陷。
2. 尺寸检验:测量螺栓的直径、长度、螺纹间距等尺寸参数。
特点:需要使用测量工具,能准确判断螺栓的尺寸是否符合要求。
3. 材质检验:通过化学分析或金相检查,确定螺栓的材质成分和组织结构是否符合标准要求。
特点:需要专业的实验设备和技术,能确保螺栓的质量和性能。
4. 力学性能检验:包括拉伸强度、屈服强度、延伸率等力学性能的测定。
特点:需要使用专用的拉伸试验机,能评估螺栓的强度和韧性。
二、轴承的检验方法及特点:1. 外观检验:检查轴承表面有无明显缺陷,如划痕、气泡等。
特点:简单易行,能直接发现明显缺陷。
2. 尺寸检验:测量轴承的内径、外径、宽度等尺寸参数。
特点:需要使用测量工具,能准确判断轴承的尺寸是否符合要求。
3. 材质检验:通过化学分析或金相检查,确定轴承的材质成分和组织结构是否符合标准要求。
特点:需要专业的实验设备和技术,能确保轴承的质量和性能。
4. 润滑状态检验:观察轴承的润滑状态,检查有无干涩、过热等现象。
特点:需要经验丰富的操作人员,能判断轴承的润滑是否良好。
5. 运动性能检验:通过转动轴承,观察其转动是否平稳、无噪音等。
特点:需要专用的测试设备,能评估轴承的运动性能。
三、齿轮的检验方法及特点:1. 外观检验:检查齿轮表面有无明显缺陷,如划痕、气泡等。
特点:简单易行,能直接发现明显缺陷。
2. 尺寸检验:测量齿轮的模数、齿宽、齿数等尺寸参数。
特点:需要使用测量工具,能准确判断齿轮的尺寸是否符合要求。
3. 材质检验:通过化学分析或金相检查,确定齿轮的材质成分和组织结构是否符合标准要求。
特点:需要专业的实验设备和技术,能确保齿轮的质量和性能。
4. 齿形检验:通过齿形测量仪或齿形图,检查齿轮的齿形是否符合标准要求。
特点:需要专用的测试设备,能准确评估齿轮的齿形质量。
汽车零件检验方法
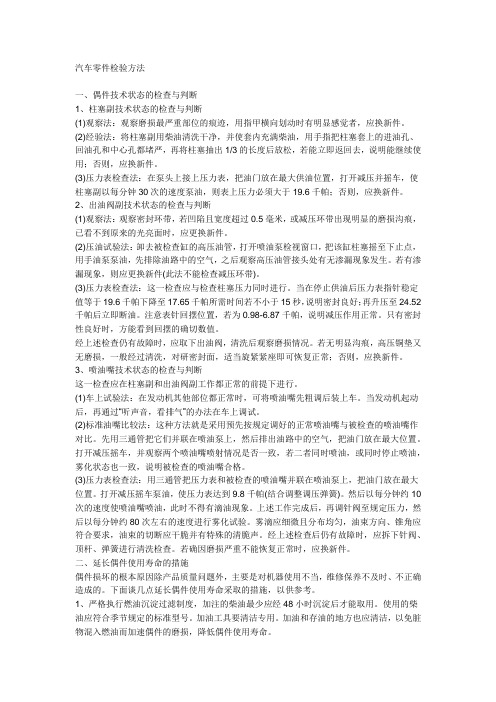
汽车零件检验方法一、偶件技术状态的检查与判断1、柱塞副技术状态的检查与判断(1)观察法:观察磨损最严重部位的痕迹,用指甲横向划动时有明显感觉者,应换新件。
(2)经验法:将柱塞副用柴油清洗干净,并使套内充满柴油,用手指把柱塞套上的进油孔、回油孔和中心孔都堵严,再将柱塞抽出1/3的长度后放松,若能立即返回去,说明能继续使用;否则,应换新件。
(3)压力表检查法:在泵头上接上压力表,把油门放在最大供油位置,打开减压并摇车,使柱塞副以每分钟30次的速度泵油,则表上压力必须大于19.6千帕;否则,应换新件。
2、出油阀副技术状态的检查与判断(1)观察法:观察密封环带,若凹陷且宽度超过0.5毫米,或减压环带出现明显的磨损沟痕,已看不到原来的光亮面时,应更换新件。
(2)压油试验法:卸去被检查缸的高压油管,打开喷油泵检视窗口,把该缸柱塞摇至下止点,用手油泵泵油,先排除油路中的空气,之后观察高压油管接头处有无渗漏现象发生。
若有渗漏现象,则应更换新件(此法不能检查减压环带)。
(3)压力表检查法:这一检查应与检查柱塞压力同时进行。
当在停止供油后压力表指针稳定值等于19.6千帕下降至17.65千帕所需时间若不小于15秒,说明密封良好;再升压至24.52千帕后立即断油。
注意表针回摆位置,若为0.98-6.87千帕,说明减压作用正常。
只有密封性良好时,方能看到回摆的确切数值。
经上述检查仍有故障时,应取下出油阀,清洗后观察磨损情况。
若无明显沟痕,高压铜垫又无磨损,一般经过清洗,对研密封面,适当旋紧紧座即可恢复正常;否则,应换新件。
3、喷油嘴技术状态的检查与判断这一检查应在柱塞副和出油阀副工作都正常的前提下进行。
(1)车上试验法:在发动机其他部位都正常时,可将喷油嘴先粗调后装上车。
当发动机起动后,再通过“听声音,看排气”的办法在车上调试。
(2)标准油嘴比较法:这种方法就是采用预先按规定调好的正常喷油嘴与被检查的喷油嘴作对比。
先用三通管把它们并联在喷油泵上,然后排出油路中的空气,把油门放在最大位置。
零件检验的方法
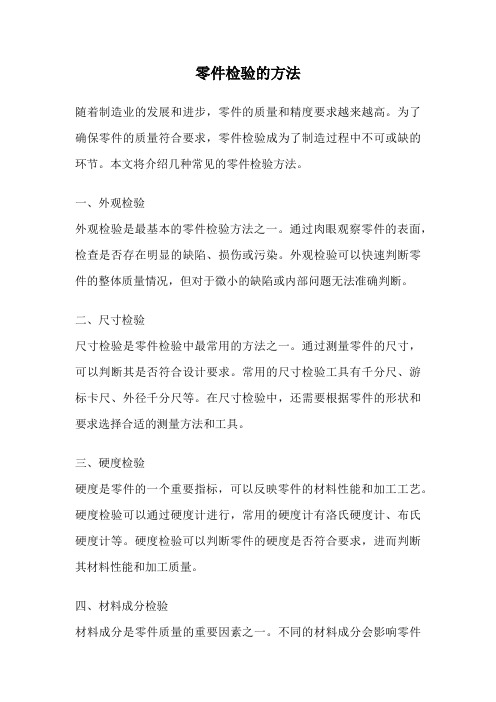
零件检验的方法随着制造业的发展和进步,零件的质量和精度要求越来越高。
为了确保零件的质量符合要求,零件检验成为了制造过程中不可或缺的环节。
本文将介绍几种常见的零件检验方法。
一、外观检验外观检验是最基本的零件检验方法之一。
通过肉眼观察零件的表面,检查是否存在明显的缺陷、损伤或污染。
外观检验可以快速判断零件的整体质量情况,但对于微小的缺陷或内部问题无法准确判断。
二、尺寸检验尺寸检验是零件检验中最常用的方法之一。
通过测量零件的尺寸,可以判断其是否符合设计要求。
常用的尺寸检验工具有千分尺、游标卡尺、外径千分尺等。
在尺寸检验中,还需要根据零件的形状和要求选择合适的测量方法和工具。
三、硬度检验硬度是零件的一个重要指标,可以反映零件的材料性能和加工工艺。
硬度检验可以通过硬度计进行,常用的硬度计有洛氏硬度计、布氏硬度计等。
硬度检验可以判断零件的硬度是否符合要求,进而判断其材料性能和加工质量。
四、材料成分检验材料成分是零件质量的重要因素之一。
不同的材料成分会影响零件的性能和使用寿命。
材料成分检验可以通过光谱仪、化学分析等方法进行。
通过检测零件中的元素含量,可以判断其材料成分是否符合要求。
五、功能性能检验功能性能是零件的关键指标之一。
功能性能检验是通过模拟零件的使用环境和工作条件,对零件进行各种功能测试。
例如,对于一个传动零件,可以进行负载测试、耐磨测试等。
功能性能检验可以判断零件在实际使用中是否能够正常工作。
六、可靠性检验可靠性是零件的一个重要指标,可以反映零件的工作寿命和故障率。
可靠性检验是通过加速寿命试验、可靠性试验等方法进行。
通过模拟零件在长时间使用中的各种工况和环境条件,可以评估零件的可靠性。
零件检验是确保零件质量的重要环节。
通过外观检验、尺寸检验、硬度检验、材料成分检验、功能性能检验和可靠性检验等方法,可以全面评估零件的质量和性能。
不同的零件需要选择不同的检验方法,以确保零件的质量符合要求。
只有通过科学、准确的零件检验,才能保证制造出高质量的产品。
零件加工质量及检验方法
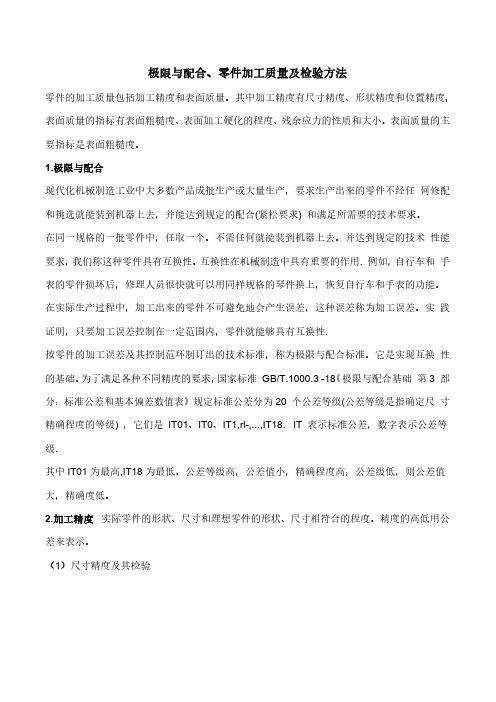
极限与配合、零件加工质量及检验方法零件的加工质量包括加工精度和表面质量。
其中加工精度有尺寸精度、形状精度和位置精度,表面质量的指标有表面粗糙度、表面加工硬化的程度、残余应力的性质和大小。
表面质量的主要指标是表面粗糙度。
1.极限与配合现代化机械制造工业中大多数产品成批生产或大量生产,要求生产出来的零件不经任何修配和挑选就能装到机器上去,并能达到规定的配合(紧松要求) 和满足所需要的技术要求。
在同一规格的一批零件中,任取一个。
不需任何就能装到机器上去。
并达到规定的技术性能要求,我们称这种零件具有互换性。
互换性在机械制造中具有重要的作用. 例如,自行车和手表的零件损坏后,修理人员很快就可以用同样规格的琴件换上,恢复自行车和手表的功能。
在实际生产过程中,加工出来的零件不可避免地会产生误差,这种误差称为加工误差。
实践证明,只要加工误差控制在一定范围内,零件就能够具有互换性.按零件的加工误差及其控制范环制订出的技术标准,称为极限与配合标准。
它是实现互换性的基础。
为了满足各种不同精度的要求,国家标准GB/T.1000.3 -18《极限与配合基础第3 部分:标准公差和基本偏差数值表》规定标准公差分为20 个公差等级(公差等级是指确定尺寸精确程度的等级) ,它们是IT01、IT0、IT1,rl-,...,IT18. IT 表示标准公差,数字表示公差等级.其中IT01为最高,IT18为最低。
公差等级高,公差值小,精确程度高;公差级低,则公差值大,精确度低。
2.加工精度实际零件的形状、尺寸和理想零件的形状、尺寸相符合的程度。
精度的高低用公差来表示。
(1)尺寸精度及其检验1)尺寸精度尺寸精度是指实际零件的尺寸和理想零件的尺寸相符合的程度,即尺寸准确的程度,尺寸精度是由尺寸公差(简称公差)控制的。
同一基本尺寸的零件,公差值的大小就决定了零件的精确程度,公差值小的,精度高,公差值大的,精度低。
2)尺寸精度的检验尺寸精度常用游标卡尺、百分尺等来检验。
汽车零件检验的基本方法

汽车零件检验的基本方法一、汽车零件检验的基本方法1.检视法检视法是在汽车维修作业中常用的零件检查方法;汽车上多数零件都可以使用该法进行检查;1用目测的方法检查零件;对于表面损伤的零件,如表面粗糙、沟槽、明显的裂纹、刮伤、剥落、折断等损伤,以及零件的重大变形、严重磨损、表面退火或烧蚀、橡胶零件等材料的变质或其他现象,都可以通过眼看手模的方式,检验和确定是否需要修理或更换;2用敲击的方法检查零件;汽车上部分壳体及盘形零件有无裂纹,通过铆钉连接的零件有无松动,可用敲击听音的方法进行检查;用小锤轻击被检测的零件,如果发出清脆的金属敲击声,说明其技术状况是好的;如果发出嘶哑的声音,可以判定被检验的零件有裂纹、松动或结合不紧密,需要进行修理或更换;3用比较的方法检验零件;用新的标准零件与被检验的零件进行比较,从对比中鉴定被检验零件的技术状态;用这种方法可以检验弹簧的自由长度和负荷下的长度,滚动轴承的质量等;2.量具仪器测量法零件因磨损或变形引起尺寸和几何形状的变化,或因长期使用引起其技术性能如弹簧的弹性下降等现象;一般可通过量具和仪器测量其现有的尺寸和数据,对照允许使用的技术标准,来确定零件是否需要修理或更换还是继续使用;常用于检验的量具有:千分尺、外径千分尺、游标卡尺、厚薄规和其他专用量具等;常用于检验的仪器有:弹簧检验器、轴承检测仪、前束尺等;使用量具和仪器检验零件,一般都能获得比较精确的数据;但要操作正确,同时在测量前必须认真检查量具本身的精确度,测量部位的选择以及仪表和量具的读数等都要正确;3.无损探伤法对于零件隐蔽缺陷的检验,特别是对汽车上的曲轴、转向节等重要零件细微裂纹的检验,对于保证汽车维修质量和行车安全有十分重要的意义,必须认真进行;常用的探测法有:磁力探伤、X光探伤、超声波探伤等;由于无损探伤需要专用设备,并需要一定的操作技能,这里就不一一介绍,请读者参阅有关资料;二、典型零件的检验汽车上的零件总类繁多,如果按照它的结构和作用,可以分为壳体、轴、齿轮、轴承、弹簧等五种基本类型;各类零件具体的结构形状虽然有许多不同,但其损坏特点和检验方法却大体上相似,只要掌握了各类零件一般的检验方法,就能指导我们对具体零件的检验方和分类;1.壳体类零件的检验壳体类零件是指气缸体、飞轮壳、变速器壳、主减速器壳等,它是各总成装配的基础;壳体类零件使用中通常产生的损伤有:裂纹、破损、穿孔、螺纹损伤、孔壁磨损、结合平面翘曲变形等;对于此类零件的检验,一般可采用检视法并配合必要的量具进行,其检验的主要项目和方法是:1裂纹;检验裂纹一般从直接观察配合敲击听音即可发现;有的零件,如变速器壳的轴承座孔与轴孔的连接处容易发生裂纹,或壳体断面急剧变化的地方,由于应力集中而往往引起裂纹,这些部位应仔细地进行检查,或用放大镜检查;气缸体的隐蔽裂纹还应进行水压实验才能被发现;2螺纹损伤;螺纹损伤一般发生在螺纹口处较多,从外部检视即可发现,如螺纹损伤在两圈以内的,可以不需修理;对于螺栓孔内螺纹的检查,可用与它相配合的螺栓旋入实验,螺栓应能顺利旋到底,并无松动现象为好;3孔壁磨损;孔壁磨损一般用眼看手模即可初步判断其磨损程度;对于要求较高的气缸等孔壁部位,应使用量缸表进行测量,以确定其圆度合圆柱度;4轴承座孔合轴孔的磨损;确定座孔磨损一般用相配合的零件进行配合检验,如果比较松旷时,可插入厚薄规检查,以判定磨损程度,确定是否可继续使用或修理;5结合平面的翘曲;检测时可将两相互结合的零件如气缸体与气缸盖扣合在一起,或将零件放在平台上,用厚薄规从四周测量检查,以确定其翘曲程度;6形位尺寸失准;对壳体零件的检验时,还应对壳体轴孔的同心度合轴孔轴线的平行度合垂直度进行检验;2.轴类零件的检测汽车上轴类零件很多,如曲轴、凸轮轴、变速器轴、传动轴等;轴类零件在使用中常见的损伤有:弯曲、磨损圆度、圆柱度及断裂等,其检验方法如下:1弯曲;将轴两端用V型铁水平支撑,使百分表触针抵在中间轴颈上,然后慢慢转动轴一周,观察并记录表针的摆动情况,表针摆差的最大值即反映了轴的弯曲程度摆差的一半就是轴的实际弯曲程度;汽车上许多轴弯曲的允许量是很微小的,因此在检查时必须认真细致;对于某些形状简单的轴,如变速滑轨等,可直接放在平板上滚动,滚动时观察轴与平台间漏光度的变化,因此来判断轴是否弯曲;2磨损;对轴类的磨损一般用外径千分尺来检查;对于磨损较为均匀的轴,只检查其外径大小,但某些磨损不均匀的轴,还需检查其圆度和圆柱度的大小;测量时,先在轴颈油孔两侧测量,然后转90°再测量;轴颈同一断面上差数最大值的1/2为圆度值;轴颈不同纵断面上差数最大值的1/2为圆柱度值;3断裂;可用检视法、无损伤探伤等方法检查;3.齿轮的检验汽车上的齿轮,虽然工作条件不同,但其磨损与损坏情况基本相同,主要表现有:齿的长度和厚度的磨损,齿面的锈蚀斑点、疲劳剥落、沟槽和阶梯形磨损,个别轮齿裂纹或折断,以及与轴配合的键槽和轴孔的磨损等等;对于齿轮的检验,可直接观察齿的外表,以发现磨损与损坏的情况;一般齿面的锈蚀斑点和疲劳剥落不超过一个齿面的20%,齿长磨损在齿高三分之二处测量不超过原齿长的25%套齿不超过原齿长的20%;齿厚磨损在节圆处测量,一般不超过0.30mm套齿不应超过0.20mm,以及轻微阶梯形磨损等可以继续使用;对于齿轮中心键槽或轴孔的磨损,可与相配合的零件进行配合检验,以判定其磨损程度;4.滚动轴承的磨损汽车上的滚动轴承包括球轴承、滚子轴承、圆锥轴承及滚针轴承;它们经常处于在高速、重载的条件下工作,承受着相当大的交变载荷;因此,滚动体与滚道往往会产生严重磨损、疲劳剥落、破裂、烧蚀即高温退火,严重时,颜色承紫黑,类似发蓝色等现象;滚动轴承时一个组合件,一般不用分解检查每个零件的损坏情况;检验时,先把轴承清洗并擦净,通过外表检视,空转实验和必要时检测内部间隙,即可鉴定其质量;1外表检查;在检查中,如果发现下列损坏现象时,一般应及更换:在滚动体钢球、圆柱滚子、圆锥滚子、滚针和内外滚道打上因烧蚀而变色;在轴承内外滚道上,发生撞击痕迹、伤印和擦伤;在轴承内外滚道、滚动体钢球、圆柱滚子、圆锥滚子、滚针上发生裂纹、金属脱层、鳞状剥落及大量一般在面积的三分之一以上黑斑点;在保持装滚子的槽口磨损过甚,滚子能自行掉出;由于圆锥滚子磨损,其小端的工作面凸出于轴承外座圈端面;圆锥滚子轴承内环大端内端面缺口和金属剥落;在滚动轴承的检验中,如仅发现轴承上有细微腐蚀性黑斑点,保持架轻微缺陷,而不影响轴承转动,一般可以继续使用;2空转检查;该项实验主要看轴承旋转是否灵活,有无噪音,有无卡住等现象;轴承旋转的不均匀性,可从手上的感觉来判断旧轴承允许有轻微响声;3内部间隙检查;内部间隙的测量,球轴承的磨损情况,可以测量它的径向和轴向间隙加以判定,方法如下:轴向间隙检验:是将轴承外座圈放置在两垫块上,并使内座圈悬空,再在内座圈上放一块小平板,将百分表触针抵在平板的中央,轴向间隙的最大允许值为~0.25mm;径向间隙检验:将轴承放在平板上,使百分表的触针抵住轴承外座圈,然后一手压紧轴承内圈,另一手往复推动轴承外圈,表针所摆动的数字即为轴承的径向间隙;径向间隙的最大允许值为~0.15mm;5.螺旋弹簧检验螺旋弹簧按受力情况可分为:压缩弹簧、拉伸弹簧和扭转弹簧三种;汽车上应用的压缩弹簧有:气门弹簧、离合器弹簧、制动主缸和轮缸弹簧等;这类弹簧在使用中,由于受热退火或疲劳损坏,弹性减弱,结果产生残余变形,使长度缩短或歪扭变形,有时还可能产生疲劳断裂等故障;弹簧的自由长度可用钢板尺测量,看其是否合乎规定,或与新弹簧比较其长短;弹簧弹力的大小,可用弹簧实验器检测;将弹簧装到实验器上,按规定压缩至一定长度,观察其弹力是否合乎规定;弹簧歪斜可用直角尺检查,歪斜超过2°时,必须更换;拉伸弹簧如制动蹄片回位弹簧由于经常受拉伸作用,可能产生弹簧伸长、折断等损坏现象,其技术状态从外表检视和测量长度即可判定;。
批量零件检验报告
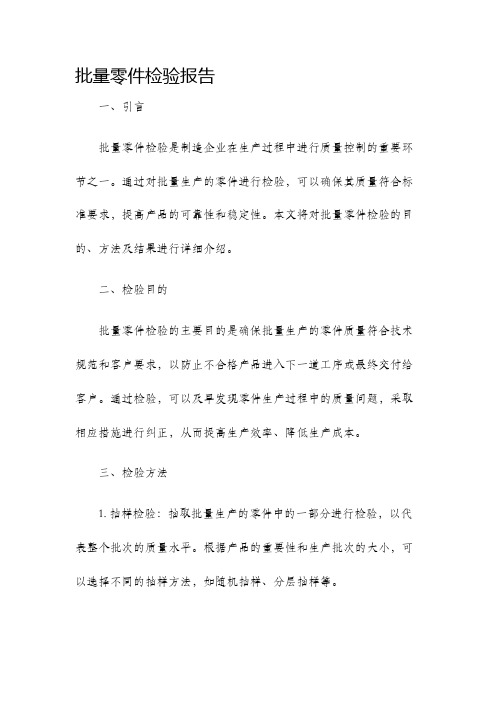
批量零件检验报告一、引言批量零件检验是制造企业在生产过程中进行质量控制的重要环节之一。
通过对批量生产的零件进行检验,可以确保其质量符合标准要求,提高产品的可靠性和稳定性。
本文将对批量零件检验的目的、方法及结果进行详细介绍。
二、检验目的批量零件检验的主要目的是确保批量生产的零件质量符合技术规范和客户要求,以防止不合格产品进入下一道工序或最终交付给客户。
通过检验,可以及早发现零件生产过程中的质量问题,采取相应措施进行纠正,从而提高生产效率、降低生产成本。
三、检验方法1. 抽样检验:抽取批量生产的零件中的一部分进行检验,以代表整个批次的质量水平。
根据产品的重要性和生产批次的大小,可以选择不同的抽样方法,如随机抽样、分层抽样等。
2. 外观检验:对零件的外观质量进行检查,包括表面光洁度、形状尺寸、色泽等。
通过目测和测量工具对外观进行评估,判断零件是否存在缺陷、变形等问题。
3. 功能性检验:对零件的功能进行测试,验证其是否满足产品设计和技术要求。
可以采用各种测试方法,如静态测试、动态测试、负载测试等,以确保零件在实际使用中的性能符合要求。
4. 材料成分检验:对批量零件的材料成分进行检测,以确认是否符合设计要求。
可以使用化学测试方法、光谱分析等技术手段来鉴定材料的成分和含量,防止因材料问题导致的质量风险。
5. 可靠性检验:通过对部分批量零件进行可靠性试验,验证其使用寿命和稳定性。
可以采用加速寿命测试、环境适应性测试等方法,模拟零件在实际使用过程中的工作环境,评估其可靠性水平。
四、检验结果根据批量零件的检验结果,可以进行以下处理:1. 合格品放行:如果零件完全符合技术规范和客户要求,可以将其放行,继续进行下一道工序或交付给客户。
这需要确保零件在运输、存储和使用过程中不会发生质量问题。
2. 重新加工或修改:如果部分批量零件存在一些小的缺陷或问题,可以进行重新加工或修改。
这需要及时采取相应纠正措施,确保批量零件的质量能够达到要求。
零部件检验标准及方法

零部件检验标准及方法前言:零部件的质量对产品的性能和可靠性具有重要影响。
为确保零部件质量符合要求,必须建立适用的检验标准和方法。
本文将详细介绍零部件检验标准及方法,以提高零部件的质量控制水平。
一、零部件检验标准的制定零部件检验标准的制定必须遵循以下原则:(1)符合国家法律法规和相关标准的要求;(2)根据零部件的特性和用途,明确技术指标和检验方案;(3)符合经济适用的原则,既要保证质量,又要提高效率;(4)灵活性,可以根据需要进行补充和修改。
1.2 制定步骤制定零部件检验标准的步骤如下:(1)明确标准的适用范围和目的,包括产品类别、性能要求等;(2)调查研究,分析现有标准和方法的适用性,了解先进技术和国际标准的最新发展;(3)制定技术要求,包括尺寸、几何形状、物理性能、化学成分等;(4)确定检验方法,根据技术要求选择合适的检验方法,如目测、测量、检验仪器等;(5)编制标准文件,包括标准名称、编号、适用范围、技术要求、检验方法等;(6)审批和发布标准文件,并进行宣贯,确保执行。
二、常用的零部件检验方法2.1 目测检验目测检验是一种简单直观的检验方法,通过肉眼观察零部件的外观、颜色、表面缺陷等,判断其是否符合标准要求。
如存在划痕、变形、变色等情况,则被视为不合格。
2.2 尺寸测量尺寸测量是常用的零部件检验方法之一,通过使用测量工具如卡尺、游标卡尺、外径测量仪等,对零部件的长度、宽度、高度、直径等尺寸进行准确测量,并与标准要求进行比对。
超过允许偏差范围的被判定为不合格。
2.3 物理性能测试物理性能测试是指对零部件的机械性能、热性能、耐腐蚀性等进行测试。
常用的测试方法包括拉伸试验、冲击试验、硬度测试、高低温试验、盐雾试验等。
根据零部件的特性和使用环境,选择合适的物理性能测试项目进行验证,确保零部件的耐久性和稳定性。
2.4 化学成分分析对于需要考虑化学成分的零部件,进行化学成分分析是必要的。
常用的分析方法有光谱分析、质谱分析、色谱分析等。
机械零件检验与鉴定的基本方法
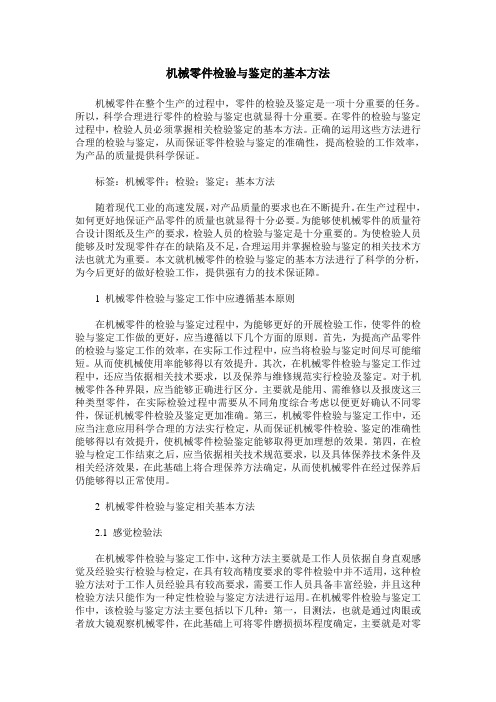
机械零件检验与鉴定的基本方法机械零件在整个生产的过程中,零件的检验及鉴定是一项十分重要的任务。
所以,科学合理进行零件的检验与鉴定也就显得十分重要。
在零件的检验与鉴定过程中,检验人员必须掌握相关检验鉴定的基本方法。
正确的运用这些方法进行合理的检验与鉴定,从而保证零件检验与鉴定的准确性,提高检验的工作效率,为产品的质量提供科学保证。
标签:机械零件;检验;鉴定;基本方法随着现代工业的高速发展,对产品质量的要求也在不断提升。
在生产过程中,如何更好地保证产品零件的质量也就显得十分必要。
为能够使机械零件的质量符合设计图纸及生产的要求,检验人员的检验与鉴定是十分重要的。
为使检验人员能够及时发现零件存在的缺陷及不足,合理运用并掌握检验与鉴定的相关技术方法也就尤为重要。
本文就机械零件的检验与鉴定的基本方法进行了科学的分析,为今后更好的做好检验工作,提供强有力的技术保证障。
1 机械零件检验与鉴定工作中应遵循基本原则在机械零件的检验与鉴定过程中,为能够更好的开展检验工作,使零件的检验与鉴定工作做的更好,应当遵循以下几个方面的原则。
首先,为提高产品零件的检验与鉴定工作的效率,在实际工作过程中,应当将检验与鉴定时间尽可能缩短。
从而使机械使用率能够得以有效提升。
其次,在机械零件检验与鉴定工作过程中,还应当依据相关技术要求,以及保养与维修规范实行检验及鉴定。
对于机械零件各种界限,应当能够正确进行区分。
主要就是能用、需维修以及报废这三种类型零件,在实际检验过程中需要从不同角度综合考虑以便更好确认不同零件,保证机械零件检验及鉴定更加准确。
第三,机械零件检验与鉴定工作中,还应当注意应用科学合理的方法实行检定,从而保证机械零件检验、鉴定的准确性能够得以有效提升,使机械零件检验鉴定能够取得更加理想的效果。
第四,在检验与检定工作结束之后,应当依据相关技术规范要求,以及具体保养技术条件及相关经济效果,在此基础上将合理保养方法确定,从而使机械零件在经过保养后仍能够得以正常使用。
精密机械车间零件检验
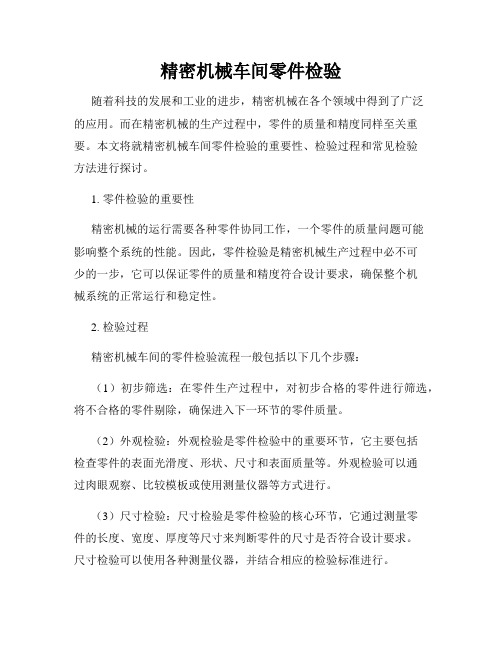
精密机械车间零件检验随着科技的发展和工业的进步,精密机械在各个领域中得到了广泛的应用。
而在精密机械的生产过程中,零件的质量和精度同样至关重要。
本文将就精密机械车间零件检验的重要性、检验过程和常见检验方法进行探讨。
1. 零件检验的重要性精密机械的运行需要各种零件协同工作,一个零件的质量问题可能影响整个系统的性能。
因此,零件检验是精密机械生产过程中必不可少的一步,它可以保证零件的质量和精度符合设计要求,确保整个机械系统的正常运行和稳定性。
2. 检验过程精密机械车间的零件检验流程一般包括以下几个步骤:(1)初步筛选:在零件生产过程中,对初步合格的零件进行筛选,将不合格的零件剔除,确保进入下一环节的零件质量。
(2)外观检验:外观检验是零件检验中的重要环节,它主要包括检查零件的表面光滑度、形状、尺寸和表面质量等。
外观检验可以通过肉眼观察、比较模板或使用测量仪器等方式进行。
(3)尺寸检验:尺寸检验是零件检验的核心环节,它通过测量零件的长度、宽度、厚度等尺寸来判断零件的尺寸是否符合设计要求。
尺寸检验可以使用各种测量仪器,并结合相应的检验标准进行。
(4)功能性检验:功能性检验是对零件进行实际工作能力验证的环节。
这包括对零件进行拧紧、运动测试、负载测试等,以确保零件能够正常运行并具有所需的性能。
3. 常见检验方法在精密机械车间中,常见的零件检验方法主要包括以下几种:(1)视觉检测:通过使用显微镜、放大镜等视觉工具对零件进行细致观察,以检测零件的外观缺陷和表面品质。
(2)影像检测:利用高精度相机和图像处理软件对零件进行图像采集和分析,以达到检测零件表面缺陷和尺寸精度的目的。
(3)全息干涉检测:利用全息干涉原理对零件进行检测,可实现对零件内部缺陷、尺寸精度和表面形貌的检测。
(4)超声波检测:通过超声波的传播和反射来检测零件的内部缺陷,如裂纹、杂质等。
总之,精密机械车间的零件检验在确保机械系统正常运行和产品质量的过程中起着重要作用。
- 1、下载文档前请自行甄别文档内容的完整性,平台不提供额外的编辑、内容补充、找答案等附加服务。
- 2、"仅部分预览"的文档,不可在线预览部分如存在完整性等问题,可反馈申请退款(可完整预览的文档不适用该条件!)。
- 3、如文档侵犯您的权益,请联系客服反馈,我们会尽快为您处理(人工客服工作时间:9:00-18:30)。
零件檢驗方法一﹑電容1﹑分類﹕●陶瓷電容●鋁質電解電容●鉭質電解電容●晶片積層電容及材質Y5V/X7R/NPO2﹑外觀檢驗﹕目視電容外觀無殘缺﹑裂痕等不良現象。
3﹑外形尺寸﹕用游標卡尺根據廠商承認書規格進行測量﹐測量值應在規定范圍內。
4﹑電容值﹕在廠商規定的測試條件下﹐用3260B(電橋)進行測量﹐將儀器調至電容“C”檔位﹐測得到值為標准值加上公差﹐應在規定范圍內。
5﹑耐壓性﹕在廠商規定的測試條件下﹐用GPI-735&GPR-7510HD(直流高壓機&電源供給器)進行測量﹐測試條件根據材料的額定電壓﹐正向連接﹐測試結果應不會被擊穿。
6﹑耐熱性﹕●將電容浸入260±5℃(業界)錫爐中﹐經10秒后取出來﹐在常溫下靜置1小時以上﹐2小時以下﹔●將電容過Air Reflow【260+0/-5℃﹐時間為10~30秒(業界)】﹐總程6分鐘後取出﹐在常溫下靜置1小時以上﹐2小時以下再測量其值﹕A.測試結果應在標准值加上公差范圍內﹔B.表面應該無異常變化。
C.此為材料必檢項目。
7﹑焊錫性﹕浸助焊劑后﹐將電容浸入235±5℃(業界)錫溶液中﹐經2±0.5秒取出﹐電容兩端95%以上附著新錫﹐此為材料必檢項。
二﹑電阻1﹑分類﹕●以插件加工分類﹕DIP( 色環電阻)﹐SMD(晶片電阻)●按功率分類﹕1/20,1/10,1/8,1/4,1/2等。
●常見材質﹕碳膜電阻(常用電阻680Ω±5%﹐1/8W)﹐金屬氧化皮膜﹐繞線有/無感。
●測偵用途﹕光敏電阻﹐壓敏電阻﹐熱敏電阻等。
2●●3●阻值﹕用3260B(電橋)進行測量﹐測得到值為標准值加上公差﹐應在規定范圍內。
●通過色環來辨認﹐具體為﹕●計數方法﹕D D D * 10n±TA.通常最后一環表示精度T( 公差)。
B.其次為倍率n。
C. 前面為有效數位(十進制)。
●晶片電阻常用代碼表示﹕“473”表示“47KΩ” ﹔“1542”表示“15.4KΩ”●晶片電阻外觀尺寸及阻值﹐例如﹐470Ω/±5%/1/8w/1206,1KΩ±5% 1/10W 1206,470Ω±5% 1/4W 1206, 1.2 KΩ±5% 1/10W 0805等。
●耐壓﹕(廠商提供標准值)﹐可根據U=√PR 來計算。
4﹑耐熱性﹕●將電容浸入260±5℃(業界)錫爐中﹐經10秒后取出來﹐在常溫下靜置1小時以上﹐2小時以下﹔●將電容過Air Reflow【260+0/-5℃﹐時間為10~30秒(業界)】﹐總程6分鐘後取出﹐在常溫下靜置1小時以上﹐2小時以下再測量其值﹕A.測試結果應在標准值加上公差范圍內﹔B.表面應該無異常變化。
C.此為材料必檢項目。
5﹑焊錫性﹕浸助焊劑后﹐將電容浸入235±5℃(業界)錫溶液中﹐經2±0.5秒取出﹐電容兩端95%以上附著新錫﹐此為材料必檢項。
三﹑電感1﹑外觀﹕目視電感﹐有無外觀破損﹑腳斷之現象﹐標記是否正確﹐PIN腳有無變形變色狀況發生。
2﹑外形尺寸﹕基本測試尺寸為電感本體長度﹑寬度﹐帶PIN之電感基本測試尺寸還包括PIN腳之腳長度﹑腳間距﹑相對二腳間之距離﹑腳厚度﹐其它測試要點如材料規格書所示。
2﹑電感量﹕也稱電自感系數表示電感元件自感應能力的一種物理量(電磁慣性大小)﹐常通過一個線圈的磁通(通過某一面積的磁力線數目)來發生變化﹐產生的電勢為感生電動勢﹐它正比于磁通變化的速度和線圈匝數。
注意﹕電感即表示一個單位符號量綱﹐同時又表示一個物件。
3﹑感抗X L與電感L﹐品質因數Q頻率f有關﹐一般未列在規格書上。
計算公式﹕X L= jωL4﹑品質因數﹕(可用WK3260B測試)在額定頻率下的交流電壓下工作時﹐感抗和等效損耗電阻之比即為Q值﹐其公式為﹕線圈的感抗越大﹐損耗電阻越小﹐其Q值越高。
當f較高時﹐鐵芯線圈及浸漬物的介質損耗﹐導線高頻趨膚效應損耗等影響較為明顯。
Q值越高﹐電路的損耗越小﹐效率越高。
5﹑直流電阻﹕用萬用表之歐姆檔測試。
6﹑額定電流指允許長時間通過電感元件的直流電流值。
選用時應該注意電流不得高于規格。
四﹑二極體1﹑外觀﹕目視二極體﹐有無外觀破損﹑腳斷之現象﹐標記是否正確﹐PIN腳有無變形變色狀況發生。
2﹑外形尺寸﹕基本測試尺寸如﹕二極體本體長度﹑寬度﹑腳長度﹑腳間距﹑相對二腳間之距離﹑腳厚度﹐其它測試要點如材料規格書所示。
2﹑正向導通電阻﹕用萬用表測試﹐紅表筆接正極﹐黑表筆接負極﹐測量值應在0.5~~0.65KΩ范圍內。
表筆反接﹐阻值接近無窮大﹐帶黑色標記的一端為負極。
若兩方向之讀數均高﹐則二極管斷路。
反之為短路。
硅管正向電阻為數百至數千歐﹐反向1M歐以上。
鍺管正向電阻為數10Ω~~1000Ω。
3﹑逆向耐壓值﹕逆向耐壓值例如100V﹑用高壓機進行測試﹐反接于電路中﹐即紅表筆接負極﹐黑表筆接正極﹐經過10秒后﹐二極管不被擊穿。
4﹑耐熱性﹕將二極管浸入260±5℃錫爐中10秒取出來﹐表面應該無異常變化﹐此為必檢項目。
5﹑焊錫性﹕將二極管浸入235±5℃錫溶液中﹐經3秒取出﹐二極管兩端75%以上附著新錫﹐此為必檢項目。
6﹑最高工作頻率f M﹕(用晶體管特性圖示儀測試)超過f M值﹐則單向導電性不佳。
五﹑電晶體1﹑外觀﹕目視電晶體﹐有無外觀破損﹑腳斷之現象﹐標記是否正確﹐PIN腳有無變形變色狀況發生。
2﹑外形尺寸﹕基本測試尺寸如﹕電晶體本體長度﹑寬度﹑腳長度﹑腳間距﹑相對二腳間之距離﹑腳厚度﹐其它測試要點如材料規格書所示。
** b,c,e極判斷﹕a)﹑將印字面正對自己﹐從左到右依次為e,c,b。
b)﹑用數字萬用表如下測試﹕(1K檔測試)先假設一電極為b極﹐用黑表筆接b極﹐紅表筆分別接其它兩電極﹐若電阻都很小﹐則可判斷出為NPN型﹐再判斷c,e極﹐黑表筆接b極﹐紅表筆分別接其它剩下的兩極﹐測得電阻小的為e極﹐剩下的為c極。
PNP型類似﹐先假設一電極為b極﹐用紅表筆接b極﹐黑表筆分別接其它兩電極﹐若電阻都很小﹐則可判斷出為PNP型﹐再判斷c,e極﹐紅表筆接b極﹐黑表筆分別接其它剩下的兩極﹐測得電阻小的為c極﹐剩下的為e極。
2﹑放大倍數hFE利用三用表hFE檔來測量﹐將三極管按NPN或PNP的腳位插好﹐讀取數據。
DIP 直接測量﹐SMD需連線﹐一般在300左右。
3﹑耐壓﹕假若V CE耐壓為60V左右﹐V CBO耐壓為120V左右﹐用電源供給器或高壓機設定為60V﹐紅表筆接c極﹐黑表筆接e極﹐經10秒后﹐三極管不被擊穿。
同樣方法測試V CBO,電壓設定為120V﹐紅表筆接c極﹐黑表筆接b極﹐經10秒后﹐三極管不被擊穿。
4﹑耐熱性﹕將電晶體浸入260±5℃錫爐中10秒取出來﹐測量hFE值在測試前±5%范圍以內﹐表面無異常變化﹐此為材料必檢項目。
5﹑焊錫性﹕將電晶體浸入235±5℃錫溶液中﹐經2±0.5秒取出﹐電晶體PIN腳75%以上附著新錫﹐此為材料必檢項。
6﹑f T特征頻率:根據廠商提供之規格﹐可用晶體管特性圖示儀測試﹐若f T值過高﹐晶體管可能截止不工作。
六﹑穩壓管1﹑外觀及尺寸﹕目視光電耦合器﹐觀察無肉眼可視的不良﹐并根據材料規格書測試其尺寸﹐應在公差范圍內。
2﹑特性檢驗﹕用兩個萬用表1K檔。
分別接1﹑2﹑3﹑4腳位(正向連接)﹐在回路中串上發光管用以顯示﹐可在萬用表上讀數0.6K左右﹐即OK。
(此時發光管發光。
) 3﹑耐熱性﹕將光電耦合器浸入260±5℃錫爐中10秒取出來﹐測量值在測試前±5%范圍以內﹐表面應該無異常變化﹐此為材料必檢項目。
4﹑焊錫性﹕將光電耦合器浸入235±5℃錫溶液中﹐經4±1秒取出﹐90%以上附著新錫﹐此為材料必檢項目。
八﹑IC1﹑外觀﹕外觀包裝有無破損﹑本體表面標記的正確性﹑PIN 1的指示標點是否正確﹑PIN腳有無變色變形情形。
2﹑外形尺寸﹕基本測試尺寸如﹕腳長度﹑腳間距﹑相對二腳間之距離﹑腳厚度﹐其它測試要點如材料規格書所示。
3﹑電氣測試﹕限於儀器設備的問題﹐采用制成產品之方式對其電氣特性作檢驗﹐并詳細記錄測試數據。
4﹑焊錫性﹕將IC浸入235±5℃錫溶液中﹐經4±1秒取出﹐90%以上附著新錫﹐此為材料必檢項目。
5﹑標記的附著性﹕用手指輕刮IC本體表面的標記﹐標記不得有脫落現象。
九﹑PCB板1﹑外觀﹕觀察有無外觀損傷﹐銅箔是否鍍錫良好﹐線路的位置、圓度、准度﹑螺絲洞孔位置、圓度、准度﹑PCB板整體的平整度。
2﹑尺寸測量﹕螺絲洞孔徑大小﹑外形尺寸﹑PCB厚度。
3﹑電氣測試﹕對照PCB板線路圖﹐測試PCB板的open – short點。
4﹑焊錫性﹕將PCB板浸入235±5℃錫溶液中﹐經4±1秒取出﹐90%以上附著新錫﹐此為材料必檢項目。