硬质合金的烧结工艺
硬质合金的烧结工艺

硬质合金的烧结工艺 Revised by Chen Zhen in 2021硬质合金烧结工艺硬质合金是由各种碳化物和铁族元素组成,例如WC-Co、WC-TiC-TaC-NbC-Co或是TiC-MoC-Ni。
这些材料的典型特点就是,通过液相烧结可以达到几乎100%理论密度,烧结后,低的残余孔隙度是成功应用硬质合金于金属切削、石油开采钻头或者金属成形模具等高应力使用工况的关键。
此外,必须仔细控制烧结工艺,以获得希望的显微组织和化学成分。
在很多应用场合,硬质合金都是以烧结态应用的。
烧结态合金表面经常承受条件苛刻的摩擦和应力,在大多数的切削金属应用中,刀头表面的磨耗深度只要超过0.2~0.4mm,工具就被判定报废,所以,提高硬质合金的表面性能是相当重要的。
烧结硬质合金的两种基本方法:一种是氢气烧结——在氢气中与常压下通过相反应动学来控制零件成分,另一种是真空烧结——采用真空环境或降低环境气体压强,通过减缓反应动力学来控制硬质合金成分。
真空烧结有着更为广泛的工业应用。
有时,还采用烧结热等静压和热等静压,这些技术都对硬质合金的生产有着重要的影响。
氢气烧结:氢气是还原性的气氛,但当氢气与烧结炉壁或承载装置发生反应时会改变其他成分,提供合适的碳化势以维持与硬质合金的热力学平衡。
在传统的硬质合金烧结中,要将混合料中的碳化物的含碳量调节到理论值,并在整个氢气烧结过程中维持这个值不变。
例如,烧结94WC-6CO硬质合金时,入炉时,碳含量为5.70~5.80%(质量分数),出炉时,则要维持在5.76+0.4%氢气烧结工艺的气氛控制能力对于钨钴类硬质合金来说是足够的,但是对于切钢工具用含碳化钛碳化钽或碳化铌的合金来说,气氛的氧化势太高,导致合金的成分变化,通常用真空烧结来减低这些,合金氧化物的含量,氢气烧结一般用机械推舟的方式,通过连续烧结来完成,可用一个单独的预烧炉除去润滑剂防止挥发物污染后的高烧结过程。
预烧结还可以调高生胚强度,使能对其进行粗切削加工,例如,进行车削和钻孔,预烧结温度在500~800摄氏度间,这主要取决于润滑剂除去的是否彻底及所需生胚强度。
硬质合金烧结工艺
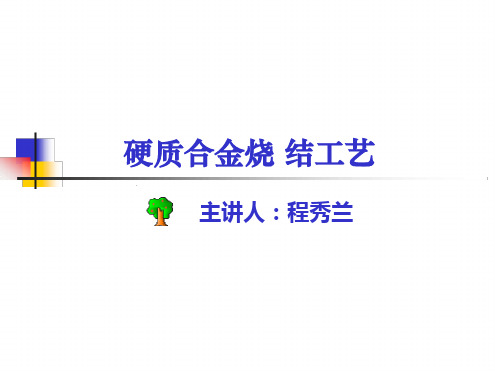
图1W-C-C O系状态图在凝固温度下的等温切面
1. 1 烧结过程四阶段及相应的组织转变
1.1.1. 脱蜡预烧阶段(<800℃) 1) 成形剂的脱除 2) 粉末表面氧化物还原 3) 粉末颗粒相互之间的状态发生变化 1.1.2. 固相烧结阶段(800℃~共晶温度) ? 共晶温度是指缓慢升温时,烧结体中开始出现共晶液相的温度,对
③重结晶阻力 a. 阻止WC 晶粒长大; b. 降低对烧结温度的敏感性; c. 降低WC 晶粒长大倾向对碳的敏感性; d. 降低WC 晶粒长大倾向对湿磨时间的敏感性。 (2 )WC -TiC -CO合金 1 ) TiC-WC +γ两相合金 固溶体的晶粒长大具有如下特点: ①与碳化钨不同,长大的结果没有那样明显的不均一性。 ②对工业合金而言,固溶体的晶粒长大与烧结体的液相数量无关。 ③这种合金的固溶体晶粒长大主要决定于烧结温度和烧结时间。 ④合金的晶粒大小与碳化钛在混合料中存在的形式有关。
相;碳量过剩,则为WC+C+ 液相;碳适量,则为WC+ 液相。
? 1.1.4. 冷却阶段(烧结温度~室温)
? 冷却速度只影响γ 相成分,不影响组织,最终组织为 WC+ γ。 ? WC-TiC- CO合金的烧结:与WC – CO 合金的烧结基本类似 。其主要区别表现 在液相的成分,出现液相的温度和所得 合金组织的不同。
? 就几何参数的影响而言,所有相( WC、CO和抑制剂碳化物)在粉末压块中的分布 状况决定着后续烧结时的初始几何位置。抑制剂碳化物是以细散碳化物颗粒形式 存在于 WC、CO粉末基体中。在后续烧结过程中,决定抑制剂利用率的参数如下 (见图5-52)。
热压烧结的操作步骤及应用
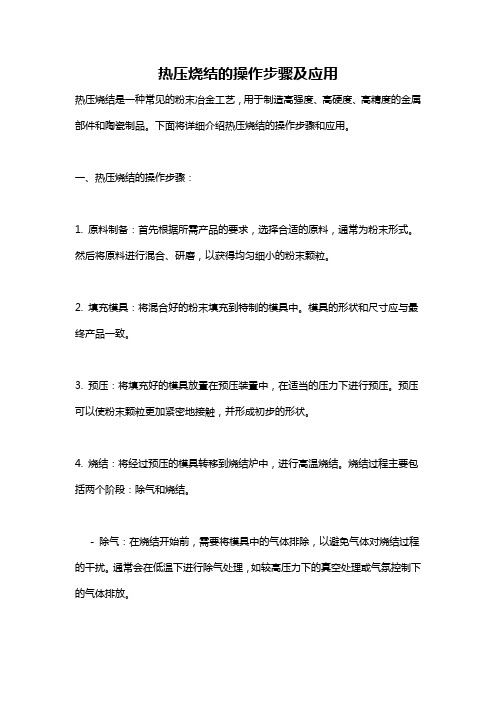
热压烧结的操作步骤及应用热压烧结是一种常见的粉末冶金工艺,用于制造高强度、高硬度、高精度的金属部件和陶瓷制品。
下面将详细介绍热压烧结的操作步骤和应用。
一、热压烧结的操作步骤:1. 原料制备:首先根据所需产品的要求,选择合适的原料,通常为粉末形式。
然后将原料进行混合、研磨,以获得均匀细小的粉末颗粒。
2. 填充模具:将混合好的粉末填充到特制的模具中。
模具的形状和尺寸应与最终产品一致。
3. 预压:将填充好的模具放置在预压装置中,在适当的压力下进行预压。
预压可以使粉末颗粒更加紧密地接触,并形成初步的形状。
4. 烧结:将经过预压的模具转移到烧结炉中,进行高温烧结。
烧结过程主要包括两个阶段:除气和烧结。
- 除气:在烧结开始前,需要将模具中的气体排除,以避免气体对烧结过程的干扰。
通常会在低温下进行除气处理,如较高压力下的真空处理或气氛控制下的气体排放。
- 烧结:将除气后的模具加热到适当的温度,使粉末颗粒发生相互结合和扩散,形成致密的固体。
烧结温度、时间和气氛的选择取决于所用材料和所需产品的特性。
5. 冷却:在烧结结束后,将模具从炉中取出,进行自然冷却或采用其他冷却方式。
冷却过程中,要注意避免产品出现热应力导致的开裂。
6. 除模:将烧结后的成品从模具中取出。
通常需要经过机械加工或其他后续处理步骤,以满足最终产品的要求。
二、热压烧结的应用:1. 金属制品:热压烧结可以用于制造各种金属制品,如钢制品、铝合金制品等。
由于热压烧结可以使金属颗粒充分结合,因此制造的金属制品具有高强度、高硬度和良好的耐磨性。
常见的应用包括汽车零部件、工具和模具、航空航天部件等。
2. 陶瓷制品:热压烧结是制造陶瓷制品的常用工艺之一。
热压烧结可以使陶瓷颗粒结合更紧密,从而获得高强度、高硬度和高密度的陶瓷制品。
常见的应用包括陶瓷刀具、陶瓷瓷砖、陶瓷合成材料等。
3. 硬质合金:热压烧结是制造硬质合金的主要工艺之一。
硬质合金通常由金属粉末和碳化物等非金属粉末混合而成。
硬质合金烧结实验

硬质合金的烧结一、实验目的了解硬质合金烧结的基本知识及烧结特点二、实验原理烧结是指在高温作用下,坯体发生一系列物理化学变化,由松散状态逐渐致密化,且机械强度大大提高的过程。
在烧结过程中包括有机物的挥发、坯体内应力的消除、气孔率的减少;在烧结气氛作用下,粉末颗粒表面氧化物的还原、原子的扩散、粘性流动和塑性流动;烧结后期还可能出现二次再结晶过程和晶粒长大过程。
三、烧结方式及特点真空烧结与低压烧结真空烧结:在低于大气压力条件下进行的粉末烧结。
主要用于烧结活性金属和难熔金属铍、钍、钛、锆、钽、铌等;烧结硬质合金、磁性合金、工具钢和不锈钢;以及烧结那些易于与氢、氮、一氧化碳等气体发生反应的化合物。
优点是:(1)减少了气氛中有害成分(水、氧、氮)对产品的不良影响。
(2)对于不宜用还原性或惰性气体作保护气氛(如活性金属的烧结),或容易出现脱碳、渗碳的材料均可用真空烧结。
(3)真空可改善液相对固相的润湿性,有利于收缩和改善合金的组织。
(4)真空烧结有助于硅、铝、镁、钙等杂质或其氧化物的排除,起到净化材料的作用。
(5)真空有利于排除吸附气体、孔隙中的残留气体以及反应气体产物,对促进烧结后期的收缩有明显作用。
如真空烧结的硬质合金的孔隙度要明显低于在氢气中烧结的硬质合金。
(6)真空烧结温度比气体保护烧结的温度要低一些,如烧结硬质合金时烧结温度可降低100~150℃。
这有利于降低能耗和防止晶粒长大。
不足是:(1)真空烧结时,常发生金属的挥发损失。
如烧结硬质合金时出现钴的挥发损失。
通过严格控制真空度,即使炉内压力不低于烧结金属组分的蒸气压,也可大大减少或避免金属的挥发损失。
(2)真空烧结的另一个问题是含碳材料的脱碳。
这主要发生在升温阶段,炉内残留气体中的氧、水分以及粉末内的氧化物等均可与碳化物中的化合碳或材料中的游离碳发生反应,生成一氧化碳随炉气抽出。
含碳材料的脱碳可用增加粉末料中的含碳量以及控制真空度来解决。
低压烧结:低压烧结的“低压”是相对…热等静压‟的压力来说的,二者都是在等静压力下烧结,前者的压力约为5Mpa 左右,后者的压力高达70~100MPa 。
硬质合金的制备方法

硬质合金的制备方法硬质合金是一种高性能、高强度材料,广泛应用于机床、航空、航天、石油、化工等领域。
本文将介绍硬质合金的制备方法。
硬质合金的制备方法主要分为粉末冶金法和熔融冶金法两种。
1. 粉末冶金法粉末冶金法是制备硬质合金的主要方法之一。
其主要原理是将金属粉末和非金属粉末按一定比例混合,再经过压制、烧结等工艺制成。
具体步骤如下:(1)原料制备。
将金属粉末和非金属粉末按一定比例混合,经过筛选、干燥等处理。
(2)压制成型。
将经过处理的原料粉末放入模具中,经过压制成型。
(3)烧结处理。
将成型后的粉末坯体放入高温炉中,进行烧结处理。
烧结温度一般在1300℃~1500℃之间,时间约为1~4小时。
烧结后的坯体具有一定的强度和韧性。
(4)后续加工。
经过烧结后的坯体,需要进行后续的加工,如切割、磨削、抛光等工艺处理,制成成品。
2. 熔融冶金法熔融冶金法是另一种制备硬质合金的主要方法。
其主要原理是将金属和非金属原料按一定比例熔融后,冷却成坯,再进行后续加工制成硬质合金。
具体步骤如下:(1)原料制备。
将金属和非金属原料按一定比例混合,经过筛选、干燥等处理。
(2)熔融处理。
将经过处理的原料放入电炉中,进行熔融处理。
熔融温度一般在1600℃~2000℃之间。
熔融后的合金液体需要进行除渣、保温等处理。
(3)坯体铸造。
将熔融后的合金液体倒入铸造模具中,冷却成坯体。
(4)热处理。
将坯体进行热处理,使其具有一定的强度和韧性。
(5)后续加工。
经过热处理后的坯体,需要进行后续的加工,如切割、磨削、抛光等工艺处理,制成成品。
粉末冶金法和熔融冶金法是制备硬质合金的主要方法。
两种方法各有优缺点,具体应根据实际情况选择。
无论采用哪种方法,都需要严格控制各项工艺参数,以保证制得的硬质合金具有优良的性能和质量。
硬质合金密封环 工艺
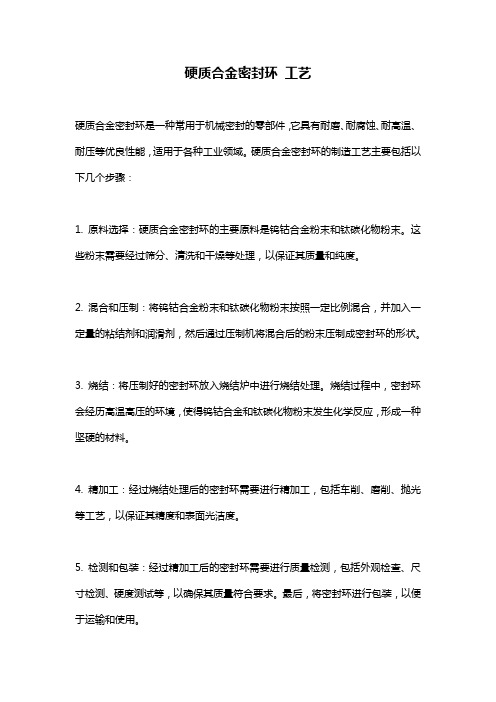
硬质合金密封环工艺
硬质合金密封环是一种常用于机械密封的零部件,它具有耐磨、耐腐蚀、耐高温、耐压等优良性能,适用于各种工业领域。
硬质合金密封环的制造工艺主要包括以下几个步骤:
1. 原料选择:硬质合金密封环的主要原料是钨钴合金粉末和钛碳化物粉末。
这些粉末需要经过筛分、清洗和干燥等处理,以保证其质量和纯度。
2. 混合和压制:将钨钴合金粉末和钛碳化物粉末按照一定比例混合,并加入一定量的粘结剂和润滑剂,然后通过压制机将混合后的粉末压制成密封环的形状。
3. 烧结:将压制好的密封环放入烧结炉中进行烧结处理。
烧结过程中,密封环会经历高温高压的环境,使得钨钴合金和钛碳化物粉末发生化学反应,形成一种坚硬的材料。
4. 精加工:经过烧结处理后的密封环需要进行精加工,包括车削、磨削、抛光等工艺,以保证其精度和表面光洁度。
5. 检测和包装:经过精加工后的密封环需要进行质量检测,包括外观检查、尺寸检测、硬度测试等,以确保其质量符合要求。
最后,将密封环进行包装,以便于运输和使用。
总的来说,硬质合金密封环的制造工艺需要经过多个环节的处理,包括原料选择、混合和压制、烧结、精加工、检测和包装等。
这些步骤需要严格控制,以保证密封环的质量和性能。
硬质合金的烧结
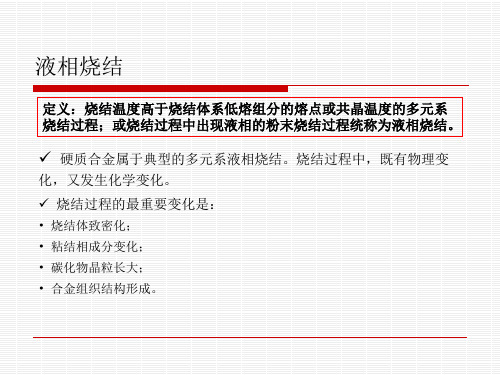
实际的烧结过程
WC+Co+W2C+C混合料的烧结特点:生产中常见的混合料组成,
尤其是在采用人造橡胶作成形剂时。
• 烧结过程伴随着一些固相化学反应而使过程复杂化。 • 在低温时先形成η相。 • 当碳量足够时, η相会因渗碳而消失。W2C亦可补充碳化化成WC。生 成的γ+η+C三元共晶(1250~1270℃)也可能消失。 • 获得的合金为WC+两相组织。 • 当碳量过剩时,可看成是WC+Co+C的烧结。而当缺碳时,则可看成是
典型的真空烧结工艺
真空烧结的4个阶段:
成形剂脱除阶段 预烧结阶段 高温烧结阶段 冷却阶段
真空烧结工艺
真空烧结的工艺过程为:脱蜡(胶)、预烧→烧结冷却出炉 • 脱蜡(胶)一般在350~400℃下进行3~4小时,它即可在真空下进 行,也可在氢气中进行。
• 预烧一般在700℃左右进行1小时。
硬质合金烧结的几个阶段
脱除成形剂及预烧阶段(<800℃):成形剂的脱除(挥发、裂解); 粉末表面氧化物还原 ;粘结金属粉末开始回复和再结晶,颗粒开始表面扩 敢,压块强度有所提高。 固相烧结阶段(800℃~共晶温度):共晶温度是指缓慢升温时出现共 晶液相的温度。WC-Co合金在平衡烧结时的共晶温度为1340℃。此时,扩 散速度增加,颗粒塑性流动加强,烧结体出现明显收缩。
溶解-再析出阶段
固相在液相中具有一定溶解度的体系; 化学位差异,化学位高的部位将发生优先溶解并在附近的液相中 形成浓度梯度; 发生固相原子等在液相中的扩散和宏观的马孪哥尼流动(溶质浓 度变化导致液体表面张力梯度,产生液相流动),在化学位低的 部位析出。
化学位高的区域 颗粒突起或尖角处,细颗粒; 发生细颗粒和颗粒尖角处的优先溶解。 化学位较低的部位 颗粒的凹陷处和大颗粒表面; 溶解在液相中固相组分的原子在这些部位析出。
硬质合金烧结工艺控制要点

硬质合金烧结工艺控制要点嘿,朋友们!今天咱们就像聊美食一样聊聊硬质合金烧结工艺的控制要点。
这硬质合金烧结啊,就像是一场神秘又刺激的魔法烹饪。
首先呢,温度那可是这个魔法烹饪的火候。
这温度控制得不好,就像你烤蛋糕的时候把烤箱温度调得乱七八糟一样。
温度过高,硬质合金可能就像个气球一样鼓起来,然后各种性能就全乱套了,它可不会乖乖听话变成我们想要的坚韧家伙。
而温度过低呢,就好比你想把肉炖烂却用小火慢慢悠悠的,结果硬质合金就达不到应有的硬度和密度,软趴趴的,像个没骨气的小面团。
接着是烧结时间。
这时间啊,就像是给这个“菜”烹饪的时长。
时间太长,硬质合金可能就像在锅里煮过头的面条,变得又干又脆,还容易断裂,完全没有了那种恰到好处的韧性。
要是时间太短,就像你急急忙忙炒个菜,菜还是生的,硬质合金的内部结构还没来得及好好组合,性能就大打折扣,就像一个没经过训练的新兵,毫无战斗力。
再说说气氛控制。
这气氛就像是烹饪时的调味料。
如果气氛不对,比如氧含量没控制好,那硬质合金就像放在空气里太久的苹果,开始氧化生锈。
原本应该光鲜亮丽、坚不可摧的它,可能变得坑坑洼洼,像个长满麻子的脸。
粉末的粒度也是个关键因素。
粉末粒度就像食材的颗粒大小。
要是粉末粒度不均匀,那就好比你做米饭的时候米有大有小,煮出来的饭肯定有的生有的熟。
硬质合金的质量也会参差不齐,有的地方硬得像石头,有的地方又松松垮垮。
烧结过程中的压力也很有趣。
压力就像你在做煎饼的时候用的那把铲子压着的力度。
压力过大,硬质合金可能就被压得扁扁的,像被踩扁的易拉罐。
压力过小呢,它又不能紧密地结合在一起,就像一盘散沙,风一吹就散了。
还有加热速率,这就像是你开着车加速的过程。
加热太快,就像你开车突然猛踩油门,硬质合金可能会因为“晕车”而内部结构紊乱。
加热太慢,就像乌龟爬一样,生产效率低下,大家都等得心急火燎的。
添加剂的使用呢,就像是给菜加调料。
加少了没效果,就像炒菜没放盐,平淡无奇。
加多了又会破坏整体的平衡,就像糖放多了把菜变成了甜品,那可就完全不是我们想要的硬质合金了。
硬质合金生产工艺
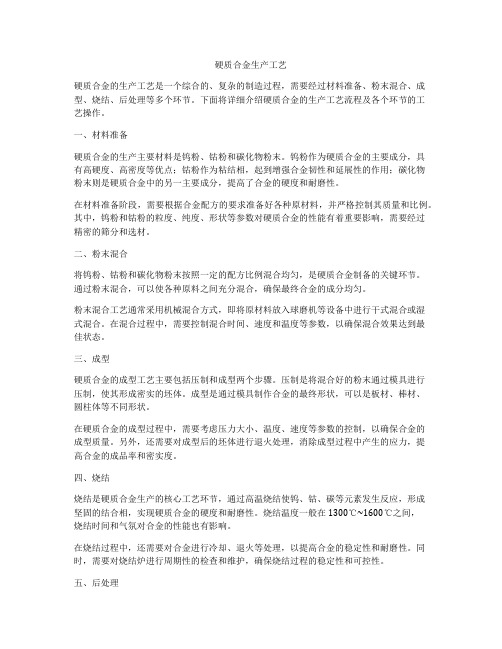
硬质合金生产工艺硬质合金的生产工艺是一个综合的、复杂的制造过程,需要经过材料准备、粉末混合、成型、烧结、后处理等多个环节。
下面将详细介绍硬质合金的生产工艺流程及各个环节的工艺操作。
一、材料准备硬质合金的生产主要材料是钨粉、钴粉和碳化物粉末。
钨粉作为硬质合金的主要成分,具有高硬度、高密度等优点;钴粉作为粘结相,起到增强合金韧性和延展性的作用;碳化物粉末则是硬质合金中的另一主要成分,提高了合金的硬度和耐磨性。
在材料准备阶段,需要根据合金配方的要求准备好各种原材料,并严格控制其质量和比例。
其中,钨粉和钴粉的粒度、纯度、形状等参数对硬质合金的性能有着重要影响,需要经过精密的筛分和选材。
二、粉末混合将钨粉、钴粉和碳化物粉末按照一定的配方比例混合均匀,是硬质合金制备的关键环节。
通过粉末混合,可以使各种原料之间充分混合,确保最终合金的成分均匀。
粉末混合工艺通常采用机械混合方式,即将原材料放入球磨机等设备中进行干式混合或湿式混合。
在混合过程中,需要控制混合时间、速度和温度等参数,以确保混合效果达到最佳状态。
三、成型硬质合金的成型工艺主要包括压制和成型两个步骤。
压制是将混合好的粉末通过模具进行压制,使其形成密实的坯体。
成型是通过模具制作合金的最终形状,可以是板材、棒材、圆柱体等不同形状。
在硬质合金的成型过程中,需要考虑压力大小、温度、速度等参数的控制,以确保合金的成型质量。
另外,还需要对成型后的坯体进行退火处理,消除成型过程中产生的应力,提高合金的成品率和密实度。
四、烧结烧结是硬质合金生产的核心工艺环节,通过高温烧结使钨、钴、碳等元素发生反应,形成坚固的结合相,实现硬质合金的硬度和耐磨性。
烧结温度一般在1300℃~1600℃之间,烧结时间和气氛对合金的性能也有影响。
在烧结过程中,还需要对合金进行冷却、退火等处理,以提高合金的稳定性和耐磨性。
同时,需要对烧结炉进行周期性的检查和维护,确保烧结过程的稳定性和可控性。
五、后处理硬质合金生产完成后,还需要进行后处理工艺,包括抛光、清洗、检测等环节。
硬质合金低压热等静压烧结工艺
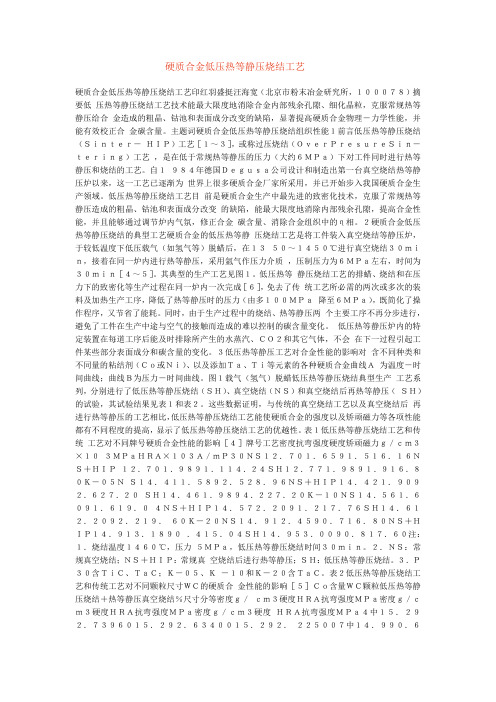
硬质合金低压热等静压烧结工艺硬质合金低压热等静压烧结工艺印红羽盛挺汪海宽(北京市粉末冶金研究所,100078)摘要低压热等静压烧结工艺技术能最大限度地消除合金内部残余孔隙、细化晶粒,克服常规热等静压给合金造成的粗晶、钴池和表面成分改变的缺陷,显著提高硬质合金物理-力学性能,并能有效校正合金碳含量。
主题词硬质合金低压热等静压烧结组织性能1前言低压热等静压烧结(Sinter-HIP)工艺[1~3],或称过压烧结(OverPresureSin-tering)工艺,是在低于常规热等静压的压力(大约6MPa)下对工件同时进行热等静压和烧结的工艺。
自1984年德国Degusa公司设计和制造出第一台真空烧结热等静压炉以来,这一工艺已逐渐为世界上很多硬质合金厂家所采用,并已开始步入我国硬质合金生产领域。
低压热等静压烧结工艺目前是硬质合金生产中最先进的致密化技术,克服了常规热等静压造成的粗晶、钴池和表面成分改变的缺陷,能最大限度地消除内部残余孔隙,提高合金性能,并且能够通过调节炉内气氛,修正合金碳含量、消除合金组织中的η相。
2硬质合金低压热等静压烧结的典型工艺硬质合金的低压热等静压烧结工艺是将工件装入真空烧结等静压炉,于较低温度下低压载气(如氢气等)脱蜡后,在1350~1450℃进行真空烧结30min,接着在同一炉内进行热等静压,采用氩气作压力介质,压制压力为6MPa左右,时间为30min[4~5]。
其典型的生产工艺见图1。
低压热等静压烧结工艺的排蜡、烧结和在压力下的致密化等生产过程在同一炉内一次完成[6],免去了传统工艺所必需的两次或多次的装料及加热生产工序,降低了热等静压时的压力(由多100MPa降至6MPa),既简化了操作程序,又节省了能耗。
同时,由于生产过程中的烧结、热等静压两个主要工序不再分步进行,避免了工件在生产中途与空气的接触而造成的难以控制的碳含量变化。
低压热等静压炉内的特定装置在每道工序后能及时排除所产生的水蒸汽、CO2和其它气体,不会在下一过程引起工件某些部分表面成分和碳含量的变化。
硬质合金真空烧结

硬质合金真空烧结硬质合金的烧结为液相烧结,即再黏结相呈液相的条件下进行。
将压坯在真空炉中加热到1350℃—1600℃。
烧结时压坯的线收缩率约为18%,体积收缩在50%左右,收缩量的准确值取决于粉末的粒度和合金的成分。
硬质合金的烧结是一个复杂的物理化学过程,株洲三鑫硬质合金生产有限公司友情出品。
这一过程包括增塑剂脱除、脱气、固相烧结、液相烧结、合金化、致密化、溶解析出等过程。
压坯在特定烧结条件下形成具有一定化学成分、组织结构、性能和形状尺寸的制品。
这些工艺条件依不同的烧结装置具有较大的差异。
硬质合金真空烧结是在低于1atm(1atm=101325Pa)下进行烧结的工艺过程。
在真空条件下烧结,大大降低了粉末表面吸附气体和封闭孔隙内气体对致密化的阻碍作用,有利于扩散过程和致密化的进行,避免了烧结过程中金属与气氛中某些元素的反应,可显著改善液体黏结相与硬质相的湿润性,但真空烧结要注意防止钴的蒸发损失。
真空烧结一般可以分为四个阶段,即增塑剂脱除阶段、预烧阶段、高温烧结阶段、冷却阶段。
增塑剂脱除阶段是从室温开始升温到200℃左右,压坯中粉末颗粒表面吸附的气体在热的作用下脱离颗粒表面,不断从压坯中逃逸出来。
压坯中的增塑剂受热化逸出压坯。
保持较高的真空度有利于气体的解除和逸出。
不同种类增塑剂受热变化的性能不尽相同,制定增塑剂脱除工艺要根据具体情况进行试验确定。
一般增塑剂的气化温度在550℃以下。
预烧阶段是指高温烧结前进行预烧结,使粉末颗粒中的化合氧与碳发生还原反应,生成一氧化碳气体离开压坯,如果这种气体在液相出现时不能排除,将成为封闭孔隙残留在合金中,即使加压烧结,也难以消除。
另一方面,氧化存在会严重影响液相对硬质相的湿润性,最终影响硬质合金的致密化过程。
在液相出现前,应充分得脱气,并采用尽可能高得真空度。
高温烧结阶段是硬质合金压坯发生致密化得关键阶段,而烧结温度及烧结时间是压坯实现致密化、形成均匀得组织结构、获得所要求性能的重要工艺参数。
硬质合金烧结方法的新进展

硬质合金烧结方法的新进展1前言烧结是硬质合金生产过程的最后一道工序,也是最基本、最关键的一道工序,烧结前工序中的某些缺陷在一定范围内可以通过调整烧结工艺加以纠正,而由烧结造成的废品一般无法通过以后的工序来挽救,因此烧结工艺和装备选择是否恰当,对烧结产品的质量有着决定性的影响。
长久以来,在实际生产中逐渐形成了多种烧结方法,较为传统的包括氢气烧结、真空烧结、热等静压烧结、真空后续热等静压、烧结热等静压等。
80年代纳米结构问世之后,又逐渐形成了新型烧结方法,如微波烧结、放电等离子烧结等。
下面就这几种烧结技术特别是纳米硬质合金烧结技术做一综合介绍。
2氢气烧结将压坯装在石墨舟中,再充填一定含碳量的氧化铝填料或石墨颗粒填料,通常是装入连续推进式的钼丝炉内,在氢气保护下进行烧结,这个过程就是氢气烧结<1 > 。
氢气烧结的特点是:能够提供还原性气氛;需要预烧结来清除压制时添加的成形剂。
氢气烧结虽然曾在较长时期内被广泛采用,甚至目前还有少数厂家采用它,但经过长期实践,人们发现它存在许多不足。
钼丝刚玉管炉的优点是结构简单、炉子功率小、炉管寿命长,但是炉温控制不准、炉内气氛变化大、产品容易渗碳、脱碳。
另外,其烧结过程是在正压下进行的,产品内部的孔隙不能充分得到消除,留有残余孔隙,一些氧化物杂质也不能较好地挥发排除掉<2 > 。
3真空烧结硬质合金的真空烧结始于上世纪三十年代,而到六十年代才获得较大的发展。
所谓真空烧结,就是在负压的气(汽)体介质中烧结压制的过程。
真空烧结与氢气烧结相比,可以提高炉气纯度,同时负压改善了粘结相对硬质相的润湿性。
真空烧结具有如下优点:(1 )能够更好地排除烧结体中Si、Mg、Ca等微量氧化物杂质,从而提高硬质合金的纯度;(2 )真空下气相的渗碳、脱碳作用大大减少,易于保证最终合金的碳含量,控制合金的组织结构;(3)可以降低烧结温度或保温时间,防止碳化物晶粒的不均匀长大;(4)烧结品残留孔隙比氢气烧结少,可提高合金的密度和机械性能;(5 )烧结时产品不用填料隔开和保护,操作简单,而且产品表面无粘附物和白亮的金属铝沉积物。
硬质合金的热处理

硬质合金的热处理
硬质合金是由钨、钴、钛等元素组成,具有具有高硬度、高韧性、耐磨、耐腐蚀等特性,广泛应用于刀具、模具、矿山机械、石油钻头等领域。
为了提高硬质合金的性能,常常需要进行热处理。
硬质合金的热处理主要包括烧结前处理和烧结后处理两个过程。
烧结前处理主要是对粉末进行烘干、脱脂和预热等处理,以保证粉末的燃烧和烧结质量。
烧结后处理,则是在烧结后对硬质合金进行正火、退火、淬火和回火等工艺,以改善其组织和性能。
正火是指对铸造、锻造后的硬质合金进行加热、保温和冷却的过程,以调节其组织和性能。
硬质合金的正火温度通常在1150℃~1250℃之间,保温时间为1~4小时,冷却方式为空气冷却或水冷却。
正火处理可以改善硬质合金的结晶度、均匀性和韧性,同时提高其硬度和耐磨性。
总之,硬质合金的热处理是优化其性能和应用的必要技术之一。
在进行热处理时,应根据具体情况选择合适的工艺和参数,以达到所需的性能要求。
硬质合金生产工艺流程

石蜡工艺硬质合金生产工艺1 生产工艺原理1.1 原理概述硬质合金是一种由难熔金属硬质化合物与粘结金属组成,采用粉末冶金方法生产,具有很高耐磨性和一定韧性的硬质材料。
由于所具有的优异性能,硬质合金被广泛应用于切削加工、耐磨零件、矿山采掘、地质钻探、石油开采、机械附件等各个领域。
矿用合金分厂石蜡工艺硬质合金的生产过程一般为:a) 将难熔金属硬质化合物(碳化钨、碳化钽等)、粘结金属(钴粉或镍粉)及少量添加剂(硬脂酸或依索敏)经过配料,在己烷研磨介质中进行混合和研磨,添加石蜡的料浆,再经真空干燥(或喷雾干燥)、过筛、制粒,制成掺蜡混合料;b) 掺蜡混合料经鉴定合格,经过精密压制,制成高精度压坯;c) 压坯经真空脱蜡烧结或低压烧结,制成硬质合金。
1.2 各工艺过程原理1.2.1 混合料制备原理称取所需的各组份原料及少量添加剂,装入滚动球磨机或搅拌球磨机,在球磨机中合金球研磨体的冲击、研磨作用下,各组份原料在己烷研磨介质中得到细化和均匀分布,在喷雾干燥前(或湿磨后期)加入一定量液态石蜡,卸料后经喷雾干燥、振动过筛(或真空干燥、均匀化破碎过筛),制成有一定成分和粒度要求的掺蜡混合料,以满足压制成型和真空烧结的需要。
1.2.2 压制原理将混合料装入定型模腔内,在压力机冲头或其它传压介质施予的压力的作用下,压力传向模腔内的粉末,粉末发生位移和变形,随压力的增加,粉末颗粒之间的距离变小,粉末颗粒之间发生机械啮合,孔隙度大大降低,同时在成型剂的作用下,混合料被密实成具有一定形状、尺寸、密度、强度的压坯。
在保证压力机、模具及混合料满足压制要求的基础上,利用有效手段控制过程中的各种影响因素,最终得到高精度尺寸的压坯。
由于粉末颗粒与模具壁之间的摩擦作用,使压力在压坯高度方向产生衰减,引起压坯单位高度上的重量变化,即反映了压坯密度的变化。
道斯特机械自动(或C35-160、C35-500、TPA45.2、TPA50/2、TPA20/3等)双向压力机,是靠机械凸轮在动力带动下完成压制动作,一旦动作的上下死点限定,压制动作就不会改变,故能保证压坯的高度不变,这时,装料量的变化会引起压制力的变化,从而引起压坯尺寸的变化,故应控制单重的波动范围,即通过控制压制工艺参数来实现等密度压制。
硬质合金低压烧结工艺的探索

硬质合金低压烧结工艺的探索背景介绍硬质合金是一种具有优异性能的材料,广泛应用于切削工具、磨料工具、钻头等领域。
然而,传统的硬质合金烧结工艺存在一些问题,如高温烧结过程中易产生裂纹、粉末不易压实等。
为了解决这些问题,近年来,低压烧结工艺被引入硬质合金的生产中,取得了良好的效果。
本文将对硬质合金低压烧结工艺进行探索。
低压烧结工艺的原理低压烧结工艺是在传统的高温烧结工艺基础上进行的改进。
该工艺是在相对较低的温度和压力下进行的,能够有效降低硬质合金烧结过程中的应力,减少裂纹的产生。
具体工艺流程如下:1.硬质合金粉末的制备:首先,根据所需的产品要求,将合适的金属粉末混合,并加入适量的粘结剂和稳定剂,经过混合、湿法粉碎、干燥等工序得到合适的硬质合金粉末。
2.模具填充与压实:将制备好的硬质合金粉末填充至模具中,然后施加一定的压力进行初步压实。
这一步骤旨在保证硬质合金粉末的均匀分布和初步的固结。
3.低压烧结过程:将填充好硬质合金粉末的模具放入低压烧结炉中,根据设计要求,控制合适的温度和压力进行烧结过程。
相对于传统高温烧结工艺,低压烧结的温度和压力要求更低,从而减少了产生裂纹的可能性。
4.冷却与脱模:低压烧结过程结束后,将烧结好的硬质合金模具从炉中取出,进行冷却。
待冷却后,使用合适的方法将硬质合金产品从模具中取出,完成脱模操作。
优势与挑战低压烧结工艺相比传统高温烧结工艺具有以下优势:1.减少裂纹的产生:传统高温烧结工艺中,由于温度和压力较高,易导致硬质合金产生内应力,从而产生裂纹。
低压烧结工艺通过降低温度和压力,减小了硬质合金内应力的产生,有效减少了裂纹的发生。
2.增加硬质合金的致密度:低压烧结工艺在初步压实的基础上,通过烧结过程进一步压实硬质合金粉末,提高了硬质合金的致密度,从而提高了其力学性能和耐磨性。
3.环保节能:相对于高温烧结工艺,低压烧结工艺不需要经过高温环境,减少了能源的消耗,同时也减少了对环境的污染。
硬质合金烧结变形及控制方法
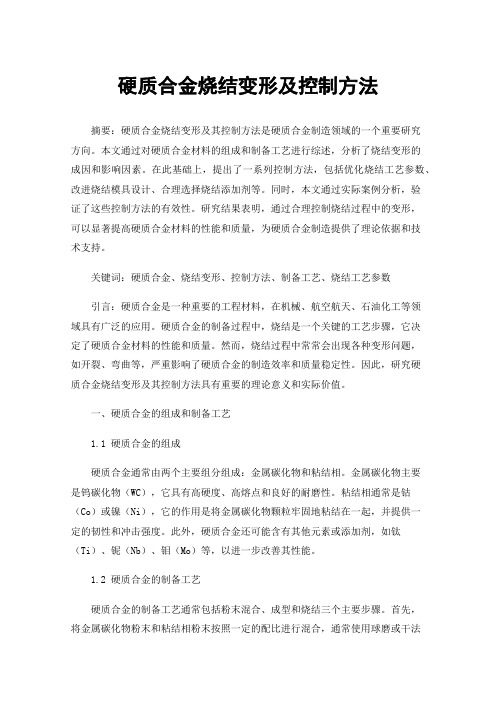
硬质合金烧结变形及控制方法摘要:硬质合金烧结变形及其控制方法是硬质合金制造领域的一个重要研究方向。
本文通过对硬质合金材料的组成和制备工艺进行综述,分析了烧结变形的成因和影响因素。
在此基础上,提出了一系列控制方法,包括优化烧结工艺参数、改进烧结模具设计、合理选择烧结添加剂等。
同时,本文通过实际案例分析,验证了这些控制方法的有效性。
研究结果表明,通过合理控制烧结过程中的变形,可以显著提高硬质合金材料的性能和质量,为硬质合金制造提供了理论依据和技术支持。
关键词:硬质合金、烧结变形、控制方法、制备工艺、烧结工艺参数引言:硬质合金是一种重要的工程材料,在机械、航空航天、石油化工等领域具有广泛的应用。
硬质合金的制备过程中,烧结是一个关键的工艺步骤,它决定了硬质合金材料的性能和质量。
然而,烧结过程中常常会出现各种变形问题,如开裂、弯曲等,严重影响了硬质合金的制造效率和质量稳定性。
因此,研究硬质合金烧结变形及其控制方法具有重要的理论意义和实际价值。
一、硬质合金的组成和制备工艺1.1 硬质合金的组成硬质合金通常由两个主要组分组成:金属碳化物和粘结相。
金属碳化物主要是钨碳化物(WC),它具有高硬度、高熔点和良好的耐磨性。
粘结相通常是钴(Co)或镍(Ni),它的作用是将金属碳化物颗粒牢固地粘结在一起,并提供一定的韧性和冲击强度。
此外,硬质合金还可能含有其他元素或添加剂,如钛(Ti)、铌(Nb)、钼(Mo)等,以进一步改善其性能。
1.2 硬质合金的制备工艺硬质合金的制备工艺通常包括粉末混合、成型和烧结三个主要步骤。
首先,将金属碳化物粉末和粘结相粉末按照一定的配比进行混合,通常使用球磨或干法混合的方法,以确保两种粉末均匀混合。
然后,将混合粉末通过成型工艺,如压制、注射成型等,制备成所需的形状,如板材、棒材、刀片等。
最后,成型体经过烧结工艺,即在高温下进行加热处理,以使金属碳化物颗粒结合成整体。
烧结过程中,首先进行预烧结,将成型体加热至金属碳化物颗粒开始颗粒间结合的温度。
硬质合金制备过程中的基本原理、烧结工艺及应用培训
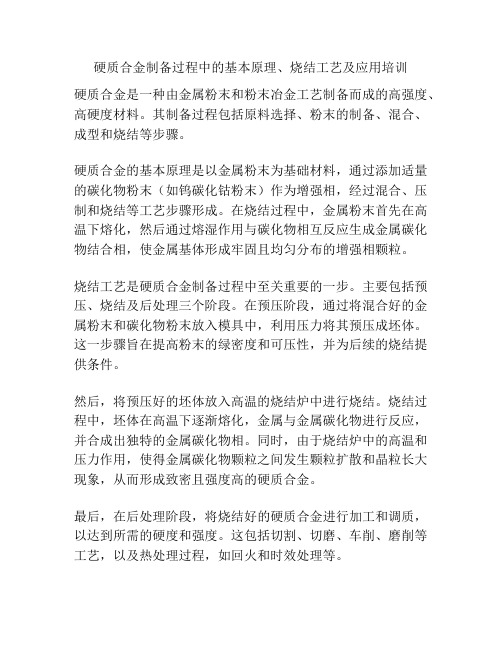
硬质合金制备过程中的基本原理、烧结工艺及应用培训硬质合金是一种由金属粉末和粉末冶金工艺制备而成的高强度、高硬度材料。
其制备过程包括原料选择、粉末的制备、混合、成型和烧结等步骤。
硬质合金的基本原理是以金属粉末为基础材料,通过添加适量的碳化物粉末(如钨碳化钴粉末)作为增强相,经过混合、压制和烧结等工艺步骤形成。
在烧结过程中,金属粉末首先在高温下熔化,然后通过熔湿作用与碳化物相互反应生成金属碳化物结合相,使金属基体形成牢固且均匀分布的增强相颗粒。
烧结工艺是硬质合金制备过程中至关重要的一步。
主要包括预压、烧结及后处理三个阶段。
在预压阶段,通过将混合好的金属粉末和碳化物粉末放入模具中,利用压力将其预压成坯体。
这一步骤旨在提高粉末的绿密度和可压性,并为后续的烧结提供条件。
然后,将预压好的坯体放入高温的烧结炉中进行烧结。
烧结过程中,坯体在高温下逐渐熔化,金属与金属碳化物进行反应,并合成出独特的金属碳化物相。
同时,由于烧结炉中的高温和压力作用,使得金属碳化物颗粒之间发生颗粒扩散和晶粒长大现象,从而形成致密且强度高的硬质合金。
最后,在后处理阶段,将烧结好的硬质合金进行加工和调质,以达到所需的硬度和强度。
这包括切割、切磨、车削、磨削等工艺,以及热处理过程,如回火和时效处理等。
硬质合金的应用非常广泛,常见的应用包括切削工具、矿业工具、电子元件等领域。
由于硬质合金具有极高的硬度、耐磨性和耐腐蚀性,因此在切削加工领域被广泛应用于车削、钻孔、铣削和切割等工艺中。
同时,在矿业工具领域,硬质合金可以用作凿岩钻头、矿山钻头等,因为它的耐磨性和强度能够满足严苛的工况要求。
在电子元件领域,由于硬质合金具有优异的导热性和耐腐蚀性能,因此常用于制造散热器、金属工具接触点等。
总之,硬质合金的制备是一个复杂的过程,包括原料选择、混合、成型和烧结等多个步骤。
通过控制工艺参数和多次迭代优化,可以获得具有优异性能的硬质合金材料,满足不同领域的应用需求。
硬质合金生产技术之压制和烧结

硬质合金生产技术之压制和烧结Company number:【0089WT-8898YT-W8CCB-BUUT-202108】第三章压制第一节压制机理一,压制过程:粉末压制成型是粉末冶金生产的基本成型方法;在压摸中填装粉末,然后在压力机下加压,脱模后得到所需形状和尺寸的压坯制品,,粗略分三阶段:1,压块密度随压力增加而迅速增大;孔隙急剧减少。
2,压块密度增加缓慢,因孔隙在1阶段中大量消除,继续加压只是让颗粒发生弹性屈服变形。
3,压力的增大可能达到粉末材料的屈服极限和强度极限,粉末颗粒在此压力下产生塑性变形或脆性断裂。
因颗粒的脆性断裂形成碎块填入孔隙,压块密度随之增大。
二,压制压力:压制压力分二部分;一是没有摩擦的条件下,使粉末压实到一定程度所需的压力为“静压力”(P1);二是克服粉末颗粒和压模之间摩擦的压力为“侧压力”(P2)。
压制压力P=P1+P2侧压系数=侧压力P2÷压制压力P=粉末的泊松系数u÷(1-u)=tg2(45o-自然坡度角Φ÷2)侧压力越大,脱模压力就越大,硬质合金粉末的泊松系数一般为之间。
三,压制过程中的压力分布:引起压力分布不匀的主要原因是粉末颗粒之间以及粉末与模壁之间的摩擦力。
压块高度越高,压力分布越不均匀。
实行双向加压或增大压坯直径,能减少压力分布的不均匀性。
四,压块密度分布:越是复杂的压块,密度分布越不均匀;除压力分布的不均匀(压力降)外,装粉方式不正确,使压块不同部位压缩程度不一致,也会造成压块密度不均匀。
1,填充系数:是指压块密度Y压与料粒的松装密度Y松的比值;压缩比:是指粉末料粒填装高度h粉与压块高度h压之比;在数值上填充系数和压缩比是相等的。
K=Y压÷Y松=h粉÷h压2,为了减少压块密度分布的不均匀性:(1)提高模具的表面光洁度;(2)减少摩擦阻力;(3)提高料粒的流动性;(4)采用合理的压制方式;3,粉末粒度对压制的影响;(1)粉末分散度越大(松装越小),压力越大。
- 1、下载文档前请自行甄别文档内容的完整性,平台不提供额外的编辑、内容补充、找答案等附加服务。
- 2、"仅部分预览"的文档,不可在线预览部分如存在完整性等问题,可反馈申请退款(可完整预览的文档不适用该条件!)。
- 3、如文档侵犯您的权益,请联系客服反馈,我们会尽快为您处理(人工客服工作时间:9:00-18:30)。
硬质合金烧结工艺
硬质合金是由各种碳化物和铁族元素组成,例如WC-Co、WC-TiC-TaC-NbC-Co或是TiC-Mo?C-Ni。
这些材料的典型特点就是,通过液相烧结可以达到几乎100%理论密度,烧结后,低的残余孔隙度是成功应用硬质合金于金属切削、石油开采钻头或者金属成形模具等高应力使用工况的关键。
此外,必须仔细控制烧结工艺,以获得希望的显微组织和化学成分。
在很多应用场合,硬质合金都是以烧结态应用的。
烧结态合金表面经常承受条件苛刻的摩擦和应力,在大多数的切削金属应用中,刀头表面的磨耗深度只要超过~,工具就被判定报废,所以,提高硬质合金的表面性能是相当重要的。
烧结硬质合金的两种基本方法:一种是氢气烧结——在氢气中与常压下通过相反应动学来控制零件成分,另一种是真空烧结——采用真空环境或降低环境气体压强,通过减缓反应动力学来控制硬质合金成分。
真空烧结有着更为广泛的工业应用。
有时,还采用烧结热等静压和热等静压,这些技术都对硬质合金的生产有着重要的影响。
氢气烧结:氢气是还原性的气氛,但当氢气与烧结炉壁或承载装置发生反应时会改变其他成分,提供合适的碳化势以维持与硬质合金的热力学平衡。
在传统的硬质合金烧结中,要将混合料中的碳化物的含碳量调节到理论值,并在整个氢气烧结过程中维持这个值不变。
例如,烧结94WC-6CO硬质合金时,入炉时,碳含量为~%(质量分数),出炉时,则要维持在+%
氢气烧结工艺的气氛控制能力对于钨钴类硬质合金来说是足够的,但是对于切钢工具用含碳化钛碳化钽或碳化铌的合金来说,气氛的氧化势太高,导致合金的成分变化,通常用真空烧结来减低这些,合金氧化物的含量,氢气烧结一般用机械推舟的方式,通过连续烧结来完成,可用一个单独的预烧炉除去润滑剂防止挥发物污染后的高烧结过程。
预烧结
还可以调高生胚强度,使能对其进行粗切削加工,例如,进行车削和钻孔,预烧结温度在500~800摄氏度间,这主要取决于润滑剂除去的是否彻底及所需生胚强度。
真空烧结:与氢气烧结相比,真空烧结主要要几个优点,首先真空烧结能极好的控制产品成分,在~133pa压强下,碳和氧气在气氛与合金之间的交换速率非常低。
影响成分变化的主要因素是碳化物颗粒中的氧含量,而不是碳与真空中稀薄气体的反应速率,因而在烧结硬质合金的工业生产中,真空烧结占有优势。
氢气烧结时,由于氢气的渗入以及氢与陶瓷炉部件的反应,使得炉内的气氛气体的氧化势增高。
真空烧结不存在这些问题,炉内氧化势比氢气烧结时低,因此,含有对氧化很敏感的碳化钛,碳化钽和碳化铌的合金,真空烧结工艺,更为合适。
其次,真空烧结可灵活的控制烧结制度,特别是加热升温阶段的升温速率,以满足生产的需要,例如,当烧结含有碳化钛、碳化钽、碳化铌的合金时,必须缓慢的升温,还要有一个在中间的温度保温的阶段才能得到高质量的产品。
真空烧结是间歇式操作,可灵活调节所需要的烧结制度,而氢气烧结大多是连续烧结工艺,很能实现对各烧结阶段的温度进行准确的控制。
如果能实现,较慢的升温速率就有足够的时间使碳——氧充分反应:形成的CO气体也来的及从连通孔隙逸出,如果升温速率太快,气体就会滞留下来,形成孔隙。
在真空炉中,很容易调节加热过程的升温速率,而对于机械推舟式氢气烧结炉来说,各烧结区的温度和达到最高烧结时的时间,都受限制很难调整。
现在工业真空烧结的操作成本较低,以前的真空烧结设备,是小的感应加热炉,这种炉子能量消耗大、冷却时间长,而且在烧结前需要单独清除润滑剂,现在应用的真空烧结炉至少在以下几方面比氢气烧结成本低:装炉量大、电阻加热、用强制气体冷却以及可在炉内清除润滑剂。
烧结热等静压:烧结热等静压有时也称之为过压烧结和加压烧结。
烧结炉实际上是一个可以充压的真空烧结炉,为了减少或消除残留空隙在烧结温度下当零件内形成封闭孔隙后,往炉内充以惰性气体对其施加等静压力,氩气压力在~10Mpa,远低于通常意义的热等静压压力。
一个具体的烧结过程,包括润滑剂清除、氧化物还原和碳化物合金烧结。
当碳化物烧结出现闭孔时,才将炉内的低压热的静压力升到较高的水平。
有报道指出对于含Co3%~6%的WC-Co牌号的硬质合金,烧结热等静压压力大约为温度在1420~1460摄氏度范围内出现闭孔;而对于含有立方碳化钨的硬质合金,在1430~1480摄氏度时出现闭孔。
就作业成本而言同等生产能力的烧结热等静压设备操作成本比真空烧结炉的操作成本要高的多。
热等静压是在一个专门设计的高压容器中进行的,利用氩气加压到100Mpa,温度和传统的烧结温度大体一样。
通常是先烧结,在作等静压后续处理,以消除少量用正常烧结工艺消除不了的残留空隙。
当然也可以用热等静压来固结只预烧过的压胚。
热等静压机是主要的关键投资,作为烧结的后处理工序,它增加了作业成本、能量和气体的消耗和生产周期。
热等静压生产的硬质合金具有晶粒细小,含量低的特点,因而强度更高但无论采用烧结热等静压还是后热等静压,只有建立了时间、温度和压力之间的合适关系,才能得到比氢气的烧结和真空烧结产品高的强度。