氢脆的避免消除措施
去氢脆处理原因与措施

文章主要说明氢脆产生的原因,并以液压主控阀阀芯为例讲述发生氢脆的薄弱点,最后阐明了去氢脆处理的主要措施。
一、氢脆的定义氢脆是溶于钢中的氢聚合为氢分子,造成应力集中,超过钢的强度极限,在钢内部形成细小的裂纹,又称白点。
氢脆主要发生在低合金高强度钢、不锈钢及弹性零件上,造成氢脆的主要原因是表面处理,如电镀、氮化等零件的处理过程中产生的氢渗入到金属内部导致晶格排列混乱,产生扭曲,造成内应力增加,使金属或镀层产生脆性,从而引起零件的断裂或镀层的脱落。
在过程中氢脆的发生需要满足两个条件:金属有较高的含氢量;有一定的外力作用。
由于氢脆所导致的滞后开裂的特性,严重影响零部件的使用性能,存在较大的安全隐患。
因此在零件的设计加工时,尤其是液压元件工作在高压下,更需要严格控制。
二、去氢脆处理适用的范围及工序并不是所有金属在表面处理过程中都会产生氢脆现象,通过研究数据及实践来看,在零件表面处理后氢脆主要产生于以下材料中。
(1)抗拉强度在981N/mm2(或硬度在38HRC)以上的经过热处理的碳素钢及合金钢零件。
(2)硬度为370HV以上的弹簧钢(包含琴钢丝、油回火钢丝、高碳钢丝)的零件。
(3)在抗拉强度1236N/mm2以上(或36HRC以上)实施热处理的马氏体的不锈钢产品。
现在的加工中,可导致氢脆的工序主要有酸洗、电镀、氮化、电解,以上工序在处理零件表面时,会产生氢且渗入到零件中,从而导致氢脆。
三、氢脆的案例分析液压产品一般需在高压下工作,部分零件承受的力较大,当零件吸氢后,在其薄弱地方会发生断裂,如图1所示的阀芯。
阀芯内部为中空,由于功能要求,中空处需要与单向阀配合密封,阀芯处于高压工作,这就需要与单向阀的配合处具有较强的抗冲击性及韧性,同时为了达到一定的耐磨要求,许多厂家选择该种阀芯表面镀铬处理,而且要求的镀层较厚,但由于镀铬工艺本身电流效率低,因此需要电镀的时间较长,渗氢严重。
图1 主控阀阀芯示意该阀芯材质为42CrMo,调质处理后硬度为32~36HRC,装配后要求镀铬层厚度0.04~0.06mm。
氢脆的避免消除措施

避免和消除的措施.1 减少金属中渗氢的数量在除锈和氧化皮时,尽量采用吹砂除锈,若采用酸洗,需在酸洗液中添加若丁等缓蚀剂;在除油时,采用化学除油、清洗剂或溶剂除油,渗氢量较少,若采用电化学除油,先阴极后阳极;在电镀时,碱性镀液或高电流效率的镀液渗氢量较少。
2 采用低氢扩散性和低氢溶解度的镀涂层一般认为,在电镀Cr、Zn、Cd、Ni、Sn、Pb时,渗入钢件的氢容易残留下来,而Cu、Mo、Al、Ag、Au、W等金属镀层具有低氢扩散性和低氢溶解度,渗氢较少。
在满足产品技术条件要求的情况下,可采用不会造成渗氢的涂层,如机械镀锌可以,不会发生氢脆,耐蚀性高,附着力好,厚5~100μm,成本低。
3 镀前去应力和镀后去氢以消除氢脆隐患若零件经淬火、焊接等工序后内部残留应力较大,镀前应进行回火处理,减少发生严重渗氢的隐患。
对电镀过程中渗氢较多的零件原则上应尽快去氢,因为镀层中的氢和表层基体金属中的氢在向钢基体内部扩散,其数量随时间的延长而增加。
新的国际标准草案规定“最好在镀后1h内,但不迟于3h,进行去氢处理”。
国内也有相应的标准,对电镀锌前、后的去氢处理作了规定。
电镀后去氢处理工艺广泛采用加热烘烤,常用的烘烤温度为150~300°C,保温2~24h。
具体的处理温度和时间应根据零件大小、强度、镀层性质和电镀时间的长短而定。
去氢处理常在烘箱内进行。
镀锌零件的去氢处理温度为110~220°C,温度控制的高低应根椐基体材料而定。
对于弹性材料、0.5mm以下的薄壁件及机械强度要求较高的钢铁零件,镀锌后必须进行去氢处理。
为了防止“镉脆”,镀镉零件的去氢处理温度不能太高,通常为180~200°C。
弹性紧固件电镀锌氢脆分析及预防为有效地提高弹性紧固件(弹簧垫圈、锥形垫圈、鞍形垫圈、波形垫圈等)抗蚀防护性能和装饰性,多半要进行表面处理,如发黑、磷化、电镀锌等处理。
其中电解镀锌及钝化处理应用更为广泛。
金属氢脆原因及解决方法

一■氢脆1氢脆现象氢脆通常表现为应力作用下的延迟断裂现象。
曾经出现过汽车弹簧、垫圈、螺钉、片簧等镀锌件,在装配之后数小时内陆续发生断裂,断裂比例达40%~50%。
某特种产品镀镉件在使用过程中曾出现过批量裂纹断裂,曾组织过全国性攻关,制订严格的去氢工艺。
另外,有一些氢脆并不表现为延迟断裂现象,例如:电镀挂具(钢丝、铜丝)由于经多次电镀和酸洗退镀,渗氢较严重,在使用中经常出现一折便发生脆断的现象;猎枪精锻用的芯棒,经多次镀铭之后,堕地断裂;有的淬火零件(内应力大)在酸洗时便产生裂纹。
这些零件渗氢严重,无需外加应力就产生裂纹,再也无法用去氢来恢复原有的韧性。
2氢脆机理延迟断裂现象的产生是由于零件内部的氢向应力集中的部位扩散聚集,应力集中部位的金属缺陷多(原子点阵错位、空穴等)。
氢扩散到这些缺陷处,氢原子变成氢分子,产生巨大的压力,这个压力与材料内部的残留应力及材料受的外加应力,组成一个合力,当这合力超过材料的屈服强度,就会导致断裂发生。
氢脆既然与氢原子的扩散有关,扩散是需要时间的,扩散的速度与浓差梯度、温度和材料种类有关。
因此,氢脆通常表现为延迟断裂。
氢原子具有最小的原子半径,容易在钢、铜等金属中扩散,而在镉、锡、锌及其合金中氢的扩散比较困难。
镀镉层是最难扩散的,镀镉时产生的氢,最初停留在镀层中和镀层下的金属表层,很难向外扩散,去氢特别困难。
经过一段时间后,氢扩散到金属内部,特别是进入金属内部缺陷处的氢,就很难扩散出来。
常温下氢的扩散速度相当缓慢,所以需要即时加热去氢。
温度升高,增加氢在钢中的溶解度,过高的温度会降低材料的硬度,所以镀前去应力和镀后去氢的温度选择,必须考虑不致于降低材料硬度,不得处于某些钢材的脆性回火温度,不破坏镀层本身的性能。
二.避免和消除的措施1 .减少金属中渗氢的数量在除锈和氧化皮时,尽量采用吹砂除锈,若采用酸洗,需在酸洗液中添加若丁等缓蚀剂;在除油时,采用化学除油、清洗剂或溶剂除油,渗氢量较少,若采用电化学除油,先阴极后阳极;在电镀时,碱性镀液或高电流效率的镀液渗氢量较少。
螺丝电镀后氢脆问题及解决方案

螺丝电镀后氢脆问题及解决方案直接说结论:以合金钢作原料生产的10。
9级、12.9级、14。
9级高强度螺栓电镀后(或仅酸洗后),必须在第一时间除氢脆处理,除氢脆处理的方法是:200度烘箱加热3—4小时析出氢原子。
以下内容是唠叨:第二次世界大战初期,英国皇家空军一架Spitpie战斗机由于引擎主轴断裂而坠落,机毁人亡,此事曾震惊英国朝野。
1975年美国芝加哥一家炼油厂,因一根15cm 的不锈钢管突然破裂,引起爆炸和火灾,造成长期停产。
法国在开采克拉克气田时,由于管道破裂,造成持续一个月的大火。
我国在开发某大油田时,也曾因管道破裂发生过井喷,损失惨重。
在军事方面还有:美国“北极星”导弹因固体燃料发动机机壳破裂而不能发射,美空军F—11战斗机在空中突然坠毁等.途中行驶的汽车因传动轴突然断裂而翻车,正在机床上切削的刀具突然断裂等事故枚不胜举。
这些灾难性的恶性事故,瞬时发生,事先毫无征兆,断裂无商量,严重地威胁着人们生产财产安全.起初科学工作者们对出事原因,众说纷纭,一筹莫展.后来经过长期观察和研究,终于探明这一系列的恶性事故的罪魁祸首-—氢脆。
1、氢脆的原因氢脆通常表现为钢材的塑性显著下降,脆性急剧增加,并在静载荷下(往往低于材料的σb)经过一段时间后发生破裂破坏的趋势.众所周知,氢在钢中有一定的溶解度.炼钢过程中,钢液凝固后,微量的氢还会留在钢中。
通常生产的钢,其含氢量在一个很小的范围内。
氢在钢中的溶解度随温度下降而迅速降低,过饱和的氢将要析出。
氢是在钢铁中扩散速度最快的元素,其原子半径最小,在低温区仍有很强的扩散能力。
如果冷却时有足够的时间使钢中的氢逸出表面或钢中的氢含量较低时,则氢脆就不易发生。
如果冷却速度快,钢件断面尺寸比较大或钢中氢含量较高时,位于钢件中心部分的氢来不及逸出,过剩的氢将进入钢的一些缺陷中去,如枝晶间隙、气孔内。
若缺陷附近由于氢的聚集会产生强大的内压而导致微裂纹的萌生与扩展.这是由于缺陷吸附了氢原子之后,使表面能大大降低,从而导致钢材破坏所需的临界应力也急剧降低。
热处理如何防止氢脆
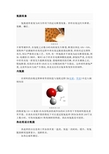
氢脆通常表现为应力作用下的延迟断裂现象。
曾经出现过汽车弹簧、垫圈、螺钉、氢脆现象片簧等镀锌件,在装配之后数小时内陆续发生断裂,断裂比例达40%~50%。
某特种产品镀镉件在使用过程中曾出现过批量裂纹断裂,曾组织过全国性攻关,制订严格的去氢工艺。
另外,有一些氢脆并不表现为延迟断裂现象,例如:电镀挂具(钢丝、铜丝)由于经多次电镀和酸洗退镀,渗氢较严重,在使用中经常出现一折便发生脆断的现象;猎枪精锻用的芯棒,经多次镀铬之后,堕地断裂;有的淬火零件(内应力大)在酸洗时便产生裂纹。
这些零件渗氢严重,无需外加应力就产生裂纹,再也无法用去氢来恢复原有的韧性。
内氢脆在材料的冶炼过程和零件的制造与装配过程(如电镀、焊接)中进入钢材内部氢脆现象元素的微量氢(10—6量级)在内部残余的或外加的应力作用下导致材料脆化甚至开裂。
在尚未出现开裂的情况下可以通过脱氢处理(例如加热到200℃以上数小时,可使内氢减少)恢复钢材的性能。
因此内氢脆是可逆的。
热处理适合氢脆热处理的方法是将工件加热至某一温度,保温一段时间,缓冷,使氢随溶解度逐渐变小,逐渐析出。
加热会破坏镀层。
主要是将酸洗控制好。
首先,尽量缩短酸洗时间;其次加缓蚀剂,减少产氢量。
防氢脆现象用品压力容器的氢脆(或称氢损伤)是指它的器壁受到氢的侵蚀,造成材料塑性和强度降低,并因此而导致的开裂或延迟性的脆性破坏。
高温高压的氢对钢的损伤主要是因为氢以原子状态渗入金属内,并在金属内部再结合成分子,产生很高的压力,严重时会导致表面鼓包或皱折;氢与钢中的碳结合,使钢脱碳,或使钢中的硫化物与氧化物还原。
造成压力容器氢脆破坏的氢,可以是设备中原来就存在的,例如,炼钢、焊接过程中的湿气在高温下被还原而生成氢,并溶解在液体金属中。
或设备在电镀或酸洗时,钢表面被吸附的氢原子过饱和,使氢渗入钢中;也可以是使用后由介质中吸收进入的,例如在石油、化工容器中,就有许多介质中含氢或含混有硫化氢的杂质。
钢发生氢脆的特征主要表现在微观组织上。
氢脆的概念、机理及应对措施详解
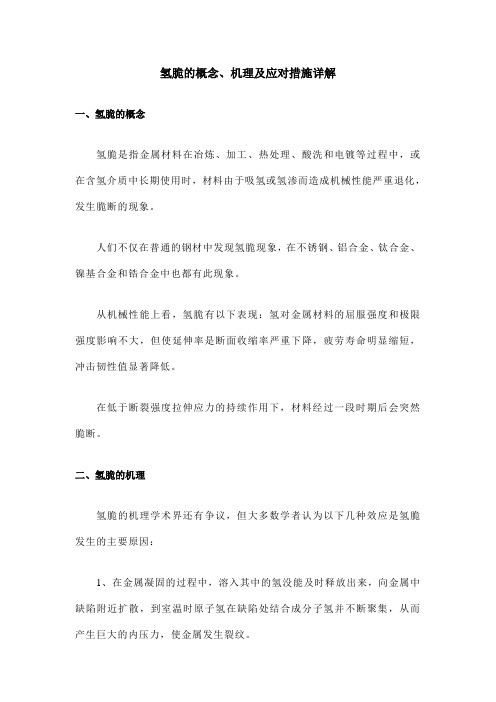
氢脆的概念、机理及应对措施详解一、氢脆的概念氢脆是指金属材料在冶炼、加工、热处理、酸洗和电镀等过程中,或在含氢介质中长期使用时,材料由于吸氢或氢渗而造成机械性能严重退化,发生脆断的现象。
人们不仅在普通的钢材中发现氢脆现象,在不锈钢、铝合金、钛合金、镍基合金和锆合金中也都有此现象。
从机械性能上看,氢脆有以下表现:氢对金属材料的屈服强度和极限强度影响不大,但使延伸率是断面收缩率严重下降,疲劳寿命明显缩短,冲击韧性值显著降低。
在低于断裂强度拉伸应力的持续作用下,材料经过一段时期后会突然脆断。
二、氢脆的机理氢脆的机理学术界还有争议,但大多数学者认为以下几种效应是氢脆发生的主要原因:1、在金属凝固的过程中,溶入其中的氢没能及时释放出来,向金属中缺陷附近扩散,到室温时原子氢在缺陷处结合成分子氢并不断聚集,从而产生巨大的内压力,使金属发生裂纹。
2、在石油工业的加氢裂解炉里,工作温度为300-500度,氢气压力高达几十个到上百个大气压力,这时氢可渗入钢中与碳发生化学反应生成甲烷。
甲烷气泡可在钢中夹杂物或晶界等场所成核,长大,并产生高压导致钢材损伤。
3、在应力作用下,固溶在金属中的氢也可能引起氢脆。
金属中的原子是按一定的规则周期性地排列起来的,称为晶格。
氢原子一般处于金属原子之间的空隙中,晶格中发生原子错排的局部地方称为位错,氢原子易于聚集在位错附近。
金属材料所外力作用时,材料内部的应力分布是不均匀的,在材料外形迅速过渡区域或在材料内部缺陷和微裂纹处会发生应力集中。
在应力梯度作用下氢原子在晶格内扩散或跟随位错运动向应力集中区域。
由于氢和金属原子之间的交互作用使金属原子间的结合力变弱,这样在高氢区会萌生出裂纹并扩展,导致了脆断。
另外,由于氢在应力集中区富集促进了该区域塑性变形,从而产生裂纹并扩展。
还有,在晶体中存在着很多的微裂纹,氢向裂纹聚集时有吸附在裂纹表面,使表面能降低,因此裂纹容易扩展。
4、某些金属与氢有较大的亲和力,过饱和氢与这种金属原子易结合生成氢化物,或在外力作用下应力集中区聚集的高浓度的氢与该种金属原子结合生成氢化物。
去氢处理
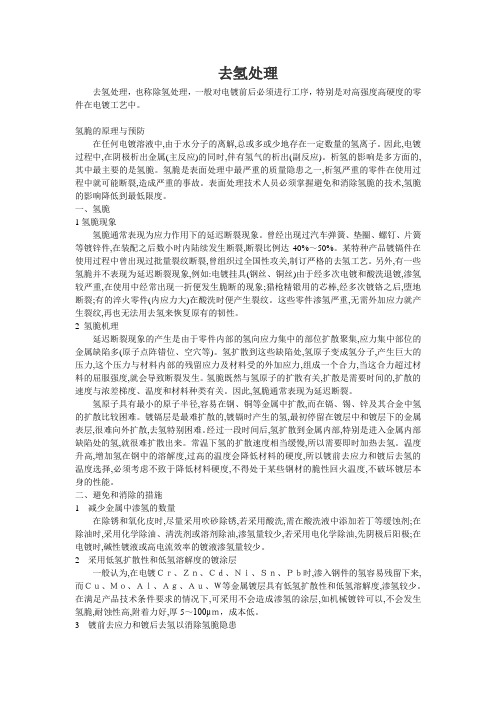
去氢处理去氢处理,也称除氢处理,一般对电镀前后必须进行工序,特别是对高强度高硬度的零件在电镀工艺中。
氢脆的原理与预防在任何电镀溶液中,由于水分子的离解,总或多或少地存在一定数量的氢离子。
因此,电镀过程中,在阴极析出金属(主反应)的同时,伴有氢气的析出(副反应)。
析氢的影响是多方面的,其中最主要的是氢脆。
氢脆是表面处理中最严重的质量隐患之一,析氢严重的零件在使用过程中就可能断裂,造成严重的事故。
表面处理技术人员必须掌握避免和消除氢脆的技术,氢脆的影响降低到最低限度。
一、氢脆1氢脆现象氢脆通常表现为应力作用下的延迟断裂现象。
曾经出现过汽车弹簧、垫圈、螺钉、片簧等镀锌件,在装配之后数小时内陆续发生断裂,断裂比例达40%~50%。
某特种产品镀镉件在使用过程中曾出现过批量裂纹断裂,曾组织过全国性攻关,制订严格的去氢工艺。
另外,有一些氢脆并不表现为延迟断裂现象,例如:电镀挂具(钢丝、铜丝)由于经多次电镀和酸洗退镀,渗氢较严重,在使用中经常出现一折便发生脆断的现象;猎枪精锻用的芯棒,经多次镀铬之后,堕地断裂;有的淬火零件(内应力大)在酸洗时便产生裂纹。
这些零件渗氢严重,无需外加应力就产生裂纹,再也无法用去氢来恢复原有的韧性。
2 氢脆机理延迟断裂现象的产生是由于零件内部的氢向应力集中的部位扩散聚集,应力集中部位的金属缺陷多(原子点阵错位、空穴等)。
氢扩散到这些缺陷处,氢原子变成氢分子,产生巨大的压力,这个压力与材料内部的残留应力及材料受的外加应力,组成一个合力,当这合力超过材料的屈服强度,就会导致断裂发生。
氢脆既然与氢原子的扩散有关,扩散是需要时间的,扩散的速度与浓差梯度、温度和材料种类有关。
因此,氢脆通常表现为延迟断裂。
氢原子具有最小的原子半径,容易在钢、铜等金属中扩散,而在镉、锡、锌及其合金中氢的扩散比较困难。
镀镉层是最难扩散的,镀镉时产生的氢,最初停留在镀层中和镀层下的金属表层,很难向外扩散,去氢特别困难。
金属材料氢脆研究及防护措施

金属材料氢脆研究及防护措施氢脆是指金属在使用过程中与氢气发生反应,导致其脆性增加,易于发生裂纹和断裂。
这是金属材料出现的一个严重问题,对于工业生产和使用中的金属材料有很大的不利影响。
氢脆的原因是金属与氢气发生反应,导致氢分子渗透到金属内部,并与金属原子结合成为氢化物,在细小的缺陷处形成高应力区,导致金属发生塑性变形,产生微裂纹,最终导致金属材料的断裂。
为了解决氢脆问题,工业生产中采取了多种措施。
其中最常用的方法是在生产中控制氢气的来源和含量,尽可能降低金属与氢气发生反应的可能性。
此外,在金属材料的加工和使用过程中,需要特别注意减少金属表面裂纹和缺陷的产生,避免强化材料上的应力和变形。
通过这些措施可以有效地预防金属材料的氢脆现象。
除了采取预防措施,科学家们还在积极研究氢脆的成因和防护方法。
他们发现,氢分子与金属原子发生反应时,需要一定的能量才能形成氢化物。
因此,如果能够控制金属表面的能量状态,就有可能避免氢分子与金属原子发生反应,从而防止氢脆现象的产生。
为了实现这一点,研究人员提出了各种抗氢脆防护措施。
其中最常用的方法就是采用钼、铬等金属元素将金属材料的表面覆盖,从而防止氢分子与金属原子直接接触。
另外,还可以采用涂层、膜、纳米材料等方法来包裹金属,形成保护层,隔绝金属与氢分子的接触,从而减少氢脆的发生。
此外,科学家们还在研究新型抗氢脆材料和涂层,以及新的氢脆防护体系。
他们采用分子层析、光学、表面分析等各种技术手段,探索金属和氢气之间的反应机制,开发高效的抗氢脆材料。
同时,他们也在研究氢脆防护系统的优化和改进,以提高其防护性能和可靠性。
总之,氢脆是金属材料在使用过程中面临的一个重要问题。
为了解决这个问题,工业生产研究中采取了多种预防措施,同时科学家们也在积极研究新的抗氢脆材料和防护系统。
这将有助于提高工业生产效率和质量,推动金属材料产业进一步的发展。
消除氢脆的方法

消除氢脆的方法以消除氢脆的方法为标题,写一篇文章:消除氢脆是一项重要的工作,它可以防止金属材料在加工过程中发生脆性断裂,保障产品的质量和安全。
下面将介绍几种常用的消除氢脆的方法。
合理控制金属材料的含氢量是消除氢脆的关键。
在金属材料的生产和加工过程中,要注意避免材料吸附过多的氢气。
可以通过采用高纯度的原材料、提高生产工艺的稳定性、控制加工环境的湿度和气氛等措施来降低金属材料中的氢含量。
另外,材料在加工过程中也要注意避免和含氢物质的接触,以减少氢的吸附。
适当提高金属材料的加工温度可以降低氢脆的程度。
在加工过程中,加热金属材料可以促使吸附在金属结构中的氢气释放出来,从而减少氢脆的风险。
但是要注意控制加热温度,避免过高的温度造成金属材料的热变形或其他负面影响。
采用热处理工艺也是消除氢脆的有效方法之一。
热处理可以通过改变金属材料的晶体结构,降低氢的扩散速率,从而减少氢脆的发生。
常用的热处理方法包括退火、正火、淬火等。
不同的金属材料和具体情况下,选择合适的热处理方法可以有效地消除氢脆。
选择合适的材料也是消除氢脆的重要措施。
一些金属材料本身就具有较高的抗氢脆能力,因此在需要抗氢脆性能的场合下,应选择这些具有抗氢脆性能的材料。
例如,一些特殊合金材料、不锈钢等都具有较好的抗氢脆性能,可以在一定程度上消除氢脆的风险。
加强金属材料的表面保护也是消除氢脆的有效方法之一。
在金属材料的表面形成一层保护膜,可以防止氢气的渗透和吸附,减少氢脆的发生。
常用的表面保护方法包括电镀、喷涂、镀膜等。
选择合适的表面保护方法,可以提高金属材料的抗氢脆性能,降低氢脆的风险。
消除氢脆是保障产品质量和安全的重要工作。
控制金属材料的含氢量、提高加工温度、采用热处理工艺、选择合适的材料和加强表面保护等方法都可以有效地消除氢脆。
在实际应用中,根据具体的材料和工艺要求,选择合适的消除氢脆方法是至关重要的。
通过合理的措施,我们可以有效地消除氢脆,提高产品的质量和可靠性。
金属氢脆原因及去氢脆方法
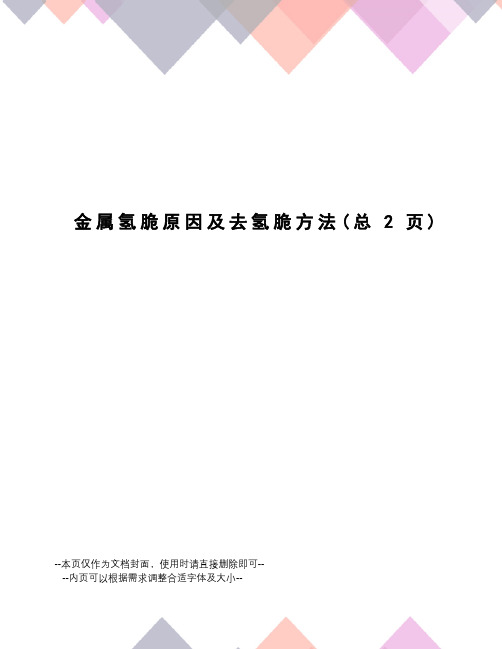
金属氢脆原因及去氢脆方法(总2页)--本页仅作为文档封面,使用时请直接删除即可----内页可以根据需求调整合适字体及大小--金属氢脆原因及去氢脆方法?在任何电镀溶液中,由于水分子的离解,总或多或少地存在一定数量的氢离子。
因此,电镀过程中,在阴极析出金属(主反应)的同时,伴有氢气的析出(副反应)。
析氢的影响是多方面的,其中最主要的是氢脆。
氢脆是表面处理中最严重的质量隐患之一,析氢严重的零件在使用过程中就可能断裂,造成严重的事故。
表面处理技术人员必须掌握避免和消除氢脆的技术,以使氢脆的影响降低到最低限度。
一、氢脆1氢脆现象氢脆通常表现为应力作用下的延迟断裂现象。
曾经出现过汽车弹簧、垫圈、螺钉、片簧等镀锌件,在装配之后数小时内陆续发生断裂,断裂比例达40%~50%。
某特种产品镀镉件在使用过程中曾出现过批量裂纹断裂,曾组织过全国性攻关,制订严格的去氢工艺。
另外,有一些氢脆并不表现为延迟断裂现象,例如:电镀挂具(钢丝、铜丝)由于经多次电镀和酸洗退镀,渗氢较严重,在使用中经常出现一折便发生脆断的现象;猎枪精锻用的芯棒,经多次镀铬之后,堕地断裂;有的淬火零件(内应力大)在酸洗时便产生裂纹。
这些零件渗氢严重,无需外加应力就产生裂纹,再也无法用去氢来恢复原有的韧性。
2?氢脆机理延迟断裂现象的产生是由于零件内部的氢向应力集中的部位扩散聚集,应力集中部位的金属缺陷多(原子点阵错位、空穴等)。
氢扩散到这些缺陷处,氢原子变成氢分子,产生巨大的压力,这个压力与材料内部的残留应力及材料受的外加应力,组成一个合力,当这合力超过材料的屈服强度,就会导致断裂发生。
氢脆既然与氢原子的扩散有关,扩散是需要时间的,扩散的速度与浓差梯度、温度和材料种类有关。
因此,氢脆通常表现为延迟断裂。
氢原子具有最小的原子半径,容易在钢、铜等金属中扩散,而在镉、锡、锌及其合金中氢的扩散比较困难。
镀镉层是最难扩散的,镀镉时产生的氢,最初停留在镀层中和镀层下的金属表层,很难向外扩散,去氢特别困难。
金属表面处理及电镀质量隐患之金属氢脆的原因分析及解决方案

金属表面处理及电镀质量隐患之金属氢脆的原因分析及解决方案在任何电镀溶液中,由于水分子的离解,总或多或少地存在一定数量的氢离子。
因此,电镀过程中,在阴极析出金属(主反应)的同时,伴有氢气的析出(副反应)。
析氢的影响是多方面的,其中最主要的是氢脆。
氢脆是表面处理中最严重的质量隐患之一,析氢严重的零件在使用过程中就可能断裂,造成严重的事故。
表面处理技术人员必须掌握避免和消除氢脆的技术,以使氢脆的影响降低到最低限度。
一、氢脆1氢脆现象氢脆通常表现为应力作用下的延迟断裂现象。
曾经出现过汽车弹簧、垫圈、螺钉、片簧等镀锌件,在装配之后数小时内陆续发生断裂,断裂比例达40%〜50%。
某特种产品镀镉件在使用过程中曾出现过批量裂纹断裂,曾组织过全国性攻关,制订严格的去氢工艺。
另外,有一些氢脆并不表现为延迟断裂现象,例如:电镀挂具(钢丝、铜丝)由于经多次电镀和酸洗退镀,渗氢较严重,在使用中经常出现一折便发生脆断的现象;猎枪精锻用的芯棒,经多次镀铭之后,堕地断裂;有的淬火零件(内应力大)在酸洗时便产生裂纹。
这些零件渗氢严重,无需外加应力就产生裂纹,再也无法用去氢来恢复原有的韧性。
2氢脆机理原因分析延迟断裂现象的产生是由于零件内部的氢向应力集中的部位扩散聚集,应力集中部位的金属缺陷多(原子点阵错位、空穴等)。
氢扩散到这些缺陷处,氢原子变成氢分子,产生巨大的压力,这个压力与材料内部的残留应力及材料受的外加应力,组成一个合力,当这合力超过材料的屈服强度, 就会导致断裂发生。
氢脆既然与氢原子的扩散有关,扩散是需要时间的,扩散的速度与浓差梯度、温度和材料种类有关。
因此,氢脆通常表现为延迟断裂。
氢原子具有最小的原子半径,容易在钢、铜等金属中扩散,而在镉、锡、锌及其合金中氢的扩散比较困难。
镀镉层是最难扩散的,镀镉时产生的氢,最初停留在镀层中和镀层下的金属表层,很难向外扩散,去氢特别困难。
经过一段时间后,氢扩散到金属内部,特别是进入金属内部缺陷处的氢, 就很难扩散出来。
氢脆的控制及去氢工艺
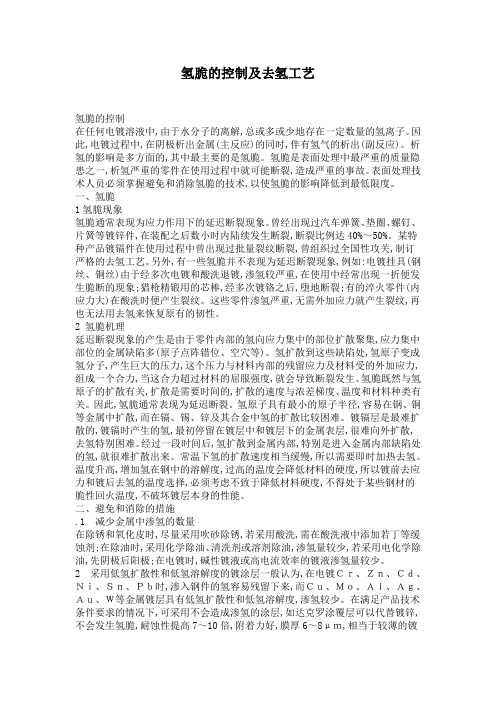
氢脆的控制及去氢工艺氢脆的控制在任何电镀溶液中,由于水分子的离解,总或多或少地存在一定数量的氢离子。
因此,电镀过程中,在阴极析出金属(主反应)的同时,伴有氢气的析出(副反应)。
析氢的影响是多方面的,其中最主要的是氢脆。
氢脆是表面处理中最严重的质量隐患之一,析氢严重的零件在使用过程中就可能断裂,造成严重的事故。
表面处理技术人员必须掌握避免和消除氢脆的技术,以使氢脆的影响降低到最低限度。
一、氢脆1氢脆现象氢脆通常表现为应力作用下的延迟断裂现象。
曾经出现过汽车弹簧、垫圈、螺钉、片簧等镀锌件,在装配之后数小时内陆续发生断裂,断裂比例达40%~50%。
某特种产品镀镉件在使用过程中曾出现过批量裂纹断裂,曾组织过全国性攻关,制订严格的去氢工艺。
另外,有一些氢脆并不表现为延迟断裂现象,例如:电镀挂具(钢丝、铜丝)由于经多次电镀和酸洗退镀,渗氢较严重,在使用中经常出现一折便发生脆断的现象;猎枪精锻用的芯棒,经多次镀铬之后,堕地断裂;有的淬火零件(内应力大)在酸洗时便产生裂纹。
这些零件渗氢严重,无需外加应力就产生裂纹,再也无法用去氢来恢复原有的韧性。
2 氢脆机理延迟断裂现象的产生是由于零件内部的氢向应力集中的部位扩散聚集,应力集中部位的金属缺陷多(原子点阵错位、空穴等)。
氢扩散到这些缺陷处,氢原子变成氢分子,产生巨大的压力,这个压力与材料内部的残留应力及材料受的外加应力,组成一个合力,当这合力超过材料的屈服强度,就会导致断裂发生。
氢脆既然与氢原子的扩散有关,扩散是需要时间的,扩散的速度与浓差梯度、温度和材料种类有关。
因此,氢脆通常表现为延迟断裂。
氢原子具有最小的原子半径,容易在钢、铜等金属中扩散,而在镉、锡、锌及其合金中氢的扩散比较困难。
镀镉层是最难扩散的,镀镉时产生的氢,最初停留在镀层中和镀层下的金属表层,很难向外扩散,去氢特别困难。
经过一段时间后,氢扩散到金属内部,特别是进入金属内部缺陷处的氢,就很难扩散出来。
螺丝氢脆的控制及去氢工艺
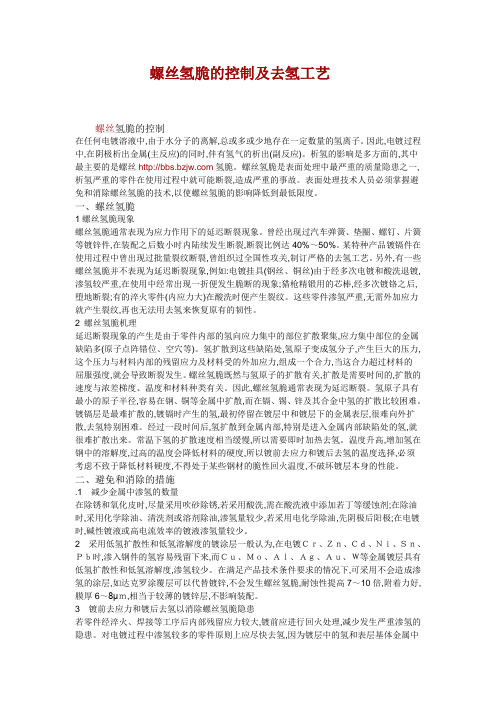
螺丝氢脆的控制及去氢工艺螺丝氢脆的控制在任何电镀溶液中,由于水分子的离解,总或多或少地存在一定数量的氢离子。
因此,电镀过程中,在阴极析出金属(主反应)的同时,伴有氢气的析出(副反应)。
析氢的影响是多方面的,其中最主要的是螺丝氢脆。
螺丝氢脆是表面处理中最严重的质量隐患之一,析氢严重的零件在使用过程中就可能断裂,造成严重的事故。
表面处理技术人员必须掌握避免和消除螺丝氢脆的技术,以使螺丝氢脆的影响降低到最低限度。
一、螺丝氢脆1螺丝氢脆现象螺丝氢脆通常表现为应力作用下的延迟断裂现象。
曾经出现过汽车弹簧、垫圈、螺钉、片簧等镀锌件,在装配之后数小时内陆续发生断裂,断裂比例达40%~50%。
某特种产品镀镉件在使用过程中曾出现过批量裂纹断裂,曾组织过全国性攻关,制订严格的去氢工艺。
另外,有一些螺丝氢脆并不表现为延迟断裂现象,例如:电镀挂具(钢丝、铜丝)由于经多次电镀和酸洗退镀,渗氢较严重,在使用中经常出现一折便发生脆断的现象;猎枪精锻用的芯棒,经多次镀铬之后,堕地断裂;有的淬火零件(内应力大)在酸洗时便产生裂纹。
这些零件渗氢严重,无需外加应力就产生裂纹,再也无法用去氢来恢复原有的韧性。
2 螺丝氢脆机理延迟断裂现象的产生是由于零件内部的氢向应力集中的部位扩散聚集,应力集中部位的金属缺陷多(原子点阵错位、空穴等)。
氢扩散到这些缺陷处,氢原子变成氢分子,产生巨大的压力,这个压力与材料内部的残留应力及材料受的外加应力,组成一个合力,当这合力超过材料的屈服强度,就会导致断裂发生。
螺丝氢脆既然与氢原子的扩散有关,扩散是需要时间的,扩散的速度与浓差梯度、温度和材料种类有关。
因此,螺丝氢脆通常表现为延迟断裂。
氢原子具有最小的原子半径,容易在钢、铜等金属中扩散,而在镉、锡、锌及其合金中氢的扩散比较困难。
镀镉层是最难扩散的,镀镉时产生的氢,最初停留在镀层中和镀层下的金属表层,很难向外扩散,去氢特别困难。
经过一段时间后,氢扩散到金属内部,特别是进入金属内部缺陷处的氢,就很难扩散出来。
金属氢脆原因及去氢脆方法
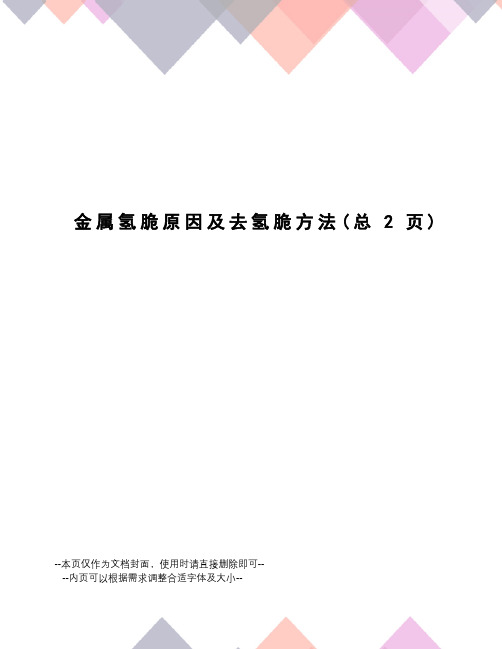
金属氢脆原因及去氢脆方法(总2页)--本页仅作为文档封面,使用时请直接删除即可----内页可以根据需求调整合适字体及大小--金属氢脆原因及去氢脆方法?在任何电镀溶液中,由于水分子的离解,总或多或少地存在一定数量的氢离子。
因此,电镀过程中,在阴极析出金属(主反应)的同时,伴有氢气的析出(副反应)。
析氢的影响是多方面的,其中最主要的是氢脆。
氢脆是表面处理中最严重的质量隐患之一,析氢严重的零件在使用过程中就可能断裂,造成严重的事故。
表面处理技术人员必须掌握避免和消除氢脆的技术,以使氢脆的影响降低到最低限度。
一、氢脆1氢脆现象氢脆通常表现为应力作用下的延迟断裂现象。
曾经出现过汽车弹簧、垫圈、螺钉、片簧等镀锌件,在装配之后数小时内陆续发生断裂,断裂比例达40%~50%。
某特种产品镀镉件在使用过程中曾出现过批量裂纹断裂,曾组织过全国性攻关,制订严格的去氢工艺。
另外,有一些氢脆并不表现为延迟断裂现象,例如:电镀挂具(钢丝、铜丝)由于经多次电镀和酸洗退镀,渗氢较严重,在使用中经常出现一折便发生脆断的现象;猎枪精锻用的芯棒,经多次镀铬之后,堕地断裂;有的淬火零件(内应力大)在酸洗时便产生裂纹。
这些零件渗氢严重,无需外加应力就产生裂纹,再也无法用去氢来恢复原有的韧性。
2?氢脆机理延迟断裂现象的产生是由于零件内部的氢向应力集中的部位扩散聚集,应力集中部位的金属缺陷多(原子点阵错位、空穴等)。
氢扩散到这些缺陷处,氢原子变成氢分子,产生巨大的压力,这个压力与材料内部的残留应力及材料受的外加应力,组成一个合力,当这合力超过材料的屈服强度,就会导致断裂发生。
氢脆既然与氢原子的扩散有关,扩散是需要时间的,扩散的速度与浓差梯度、温度和材料种类有关。
因此,氢脆通常表现为延迟断裂。
氢原子具有最小的原子半径,容易在钢、铜等金属中扩散,而在镉、锡、锌及其合金中氢的扩散比较困难。
镀镉层是最难扩散的,镀镉时产生的氢,最初停留在镀层中和镀层下的金属表层,很难向外扩散,去氢特别困难。
螺丝氢脆的控制及去氢工艺
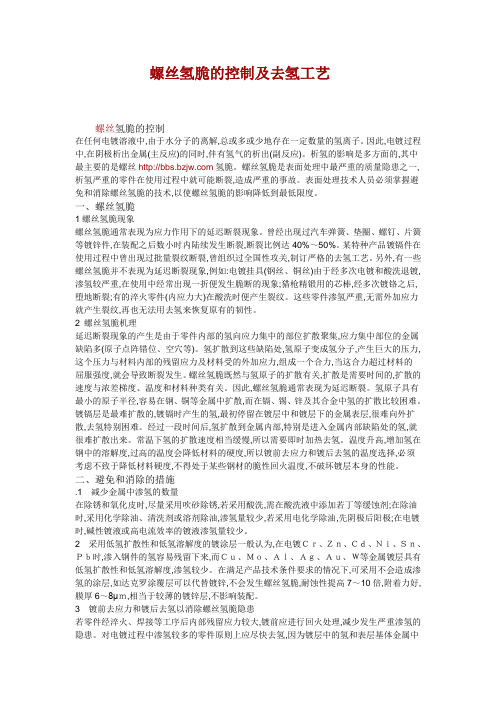
螺丝氢脆的控制及去氢工艺螺丝氢脆的控制在任何电镀溶液中,由于水分子的离解,总或多或少地存在一定数量的氢离子。
因此,电镀过程中,在阴极析出金属(主反应)的同时,伴有氢气的析出(副反应)。
析氢的影响是多方面的,其中最主要的是螺丝氢脆。
螺丝氢脆是表面处理中最严重的质量隐患之一,析氢严重的零件在使用过程中就可能断裂,造成严重的事故。
表面处理技术人员必须掌握避免和消除螺丝氢脆的技术,以使螺丝氢脆的影响降低到最低限度。
一、螺丝氢脆1螺丝氢脆现象螺丝氢脆通常表现为应力作用下的延迟断裂现象。
曾经出现过汽车弹簧、垫圈、螺钉、片簧等镀锌件,在装配之后数小时内陆续发生断裂,断裂比例达40%~50%。
某特种产品镀镉件在使用过程中曾出现过批量裂纹断裂,曾组织过全国性攻关,制订严格的去氢工艺。
另外,有一些螺丝氢脆并不表现为延迟断裂现象,例如:电镀挂具(钢丝、铜丝)由于经多次电镀和酸洗退镀,渗氢较严重,在使用中经常出现一折便发生脆断的现象;猎枪精锻用的芯棒,经多次镀铬之后,堕地断裂;有的淬火零件(内应力大)在酸洗时便产生裂纹。
这些零件渗氢严重,无需外加应力就产生裂纹,再也无法用去氢来恢复原有的韧性。
2 螺丝氢脆机理延迟断裂现象的产生是由于零件内部的氢向应力集中的部位扩散聚集,应力集中部位的金属缺陷多(原子点阵错位、空穴等)。
氢扩散到这些缺陷处,氢原子变成氢分子,产生巨大的压力,这个压力与材料内部的残留应力及材料受的外加应力,组成一个合力,当这合力超过材料的屈服强度,就会导致断裂发生。
螺丝氢脆既然与氢原子的扩散有关,扩散是需要时间的,扩散的速度与浓差梯度、温度和材料种类有关。
因此,螺丝氢脆通常表现为延迟断裂。
氢原子具有最小的原子半径,容易在钢、铜等金属中扩散,而在镉、锡、锌及其合金中氢的扩散比较困难。
镀镉层是最难扩散的,镀镉时产生的氢,最初停留在镀层中和镀层下的金属表层,很难向外扩散,去氢特别困难。
经过一段时间后,氢扩散到金属内部,特别是进入金属内部缺陷处的氢,就很难扩散出来。
金属氢脆原因及去氢脆方法
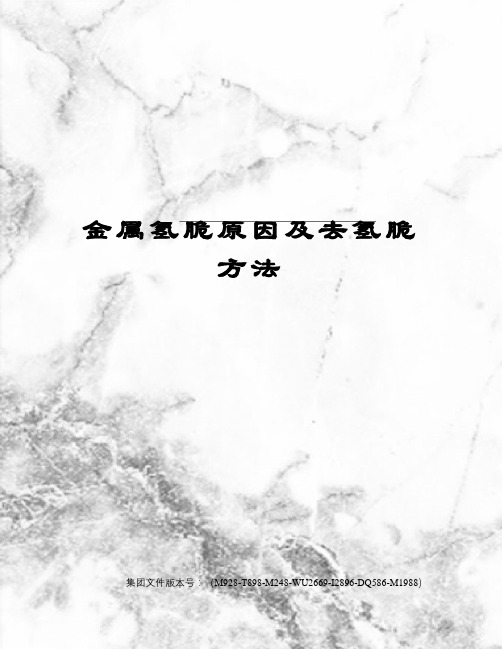
金属氢脆原因及去氢脆方法集团文件版本号:(M928-T898-M248-WU2669-I2896-DQ586-M1988)在任何电镀溶液中,由于水分子的离解,总或多或少地存在一定数量的氢离子。
因此,电镀过程中,在阴极析出金属(主反应)的同时,伴有氢气的析出(副反应)。
析氢的影响是多方面的,其中最主要的是氢脆。
氢脆是表面处理中最严重的质量隐患之一,析氢严重的零件在使用过程中就可能断裂,造成严重的事故。
表面处理技术人员必须掌握避免和消除氢脆的技术,以使氢脆的影响降低到最低限度。
一、氢脆1氢脆现象氢脆通常表现为应力作用下的延迟断裂现象。
曾经出现过汽车弹簧、垫圈、螺钉、片簧等镀锌件,在装配之后数小时内陆续发生断裂,断裂比例达40%~50%。
某特种产品镀镉件在使用过程中曾出现过批量裂纹断裂,曾组织过全国性攻关,制订严格的去氢工艺。
另外,有一些氢脆并不表现为延迟断裂现象,例如:电镀挂具(钢丝、铜丝)由于经多次电镀和酸洗退镀,渗氢较严重,在使用中经常出现一折便发生脆断的现象;猎枪精锻用的芯棒,经多次镀铬之后,堕地断裂;有的淬火零件(内应力大)在酸洗时便产生裂纹。
这些零件渗氢严重,无需外加应力就产生裂纹,再也无法用去氢来恢复原有的韧性。
2 氢脆机理延迟断裂现象的产生是由于零件内部的氢向应力集中的部位扩散聚集,应力集中部位的金属缺陷多(原子点阵错位、空穴等)。
氢扩散到这些缺陷处,氢原子变成氢分子,产生巨大的压力,这个压力与材料内部的残留应力及材料受的外加应力,组成一个合力,当这合力超过材料的屈服强度,就会导致断裂发生。
氢脆既然与氢原子的扩散有关,扩散是需要时间的,扩散的速度与浓差梯度、温度和材料种类有关。
因此,氢脆通常表现为延迟断裂。
氢原子具有最小的原子半径,容易在钢、铜等金属中扩散,而在镉、锡、锌及其合金中氢的扩散比较困难。
镀镉层是最难扩散的,镀镉时产生的氢,最初停留在镀层中和镀层下的金属表层,很难向外扩散,去氢特别困难。
关于氢脆问题

关于氢脆问题1、螺纹紧固件氢脆产生的原因及危害螺纹紧固件在制造的过程(如:调质(淬火+高温回火)、氰化、渗炭、化学清洗、磷化、电镀、滚压碾制和机加工(不适当的润滑而烧焦)等工序)和服役环境中,由于阴极保护的反作用或腐蚀的反作用,氢原子有可能进入钢或其他金属的基体,并滞留在基体内,在低于屈服强度(合金的公称强度)的应力状态下,它将可能导致延伸性或承载能力的降低或丧失、裂纹(通常是亚微观的),直致在服役过程或储存过程中发生突然断裂,造成严重的脆性失效。
螺纹紧固件,尤其是高强度紧固件经冷拔、冷成形、碾制螺纹、机加工、磨削后,再进行淬硬热处理、电镀处理,极易受氢脆的破坏。
导致紧固件氢脆的原因很多,但是电镀处理工序是关键的因素之一。
紧固件由于氢脆产生的脆性断裂,一般发生的很突然,是无法预料的,故这种失效的形式造成的后果是很严重的。
尤其是在有安全性能要求时,减少氢脆的产生是很有必要的,因此,电镀紧固件去除氢脆是一项很重要的工作工作。
2、紧固件易产生氢脆失效危险的情况及特征A、高抗拉强度或硬化或表面淬硬;B、吸附氢原子;C、在拉伸应力状态下。
随着零件硬度的提高、含碳量的增加、冷作硬化程度的强化,在酸洗和电镀过程中。
氢的溶解度和因此产生吸收氢的总量也将增加,也就是说零件的氢脆敏感性就越强。
直径较小的零件比直径较大的零件氢脆敏感性就强。
3、减少电镀紧固件氢脆的措施A、加工硬度大于或等于320HV的电镀紧固件,在清洗过程前,应增加应力释放过程;在清洗过程中,应使用防腐蚀酸、碱性或机械方法进行。
浸入到防腐酸的时间尽可能的设计为最小持续时间。
B、硬度超过320HV的紧固件在进行冷拔、冷成形、机械加工、磨削后进行热处理工序时,则应符合ISO9587D的规定;C、应尽可能避免有意引入残余应力办法。
如:螺栓、螺钉在热处理后碾制螺纹;D、经热处理或冷作硬化的硬度超过385HV或性能等级12.9级及其以上的紧固件不适宜采用酸洗处理,应使用无酸的特殊方法,如:碱性清洗、喷砂等方法。
电镀氢脆的原理与控制

100μm,成本低。
电镀氢脆的原理与控制
避免和消除的措施
3 镀前去应力和镀后去氢以消除氢脆隐患
若零件经淬火、焊接等工序后内部残留应力较大,镀前应
进行回火处理,减少发生严重渗氢的隐患。对电镀过程中渗氢 较多的零件原则上应尽快去氢,因为镀层中的氢和表层基体金 属中的氢在向钢基体内部扩散,其数量随时间的延长而增加。
表面处理技术人员必须掌握避免和消除氢脆的技术,以使氢脆 的影响降低到最低限度。
电镀氢脆的原理与控制
氢脆现象
氢脆通常表现为应力作用下的延迟断裂现象。曾经出现过 汽车弹簧、垫圈、螺钉、片簧等镀锌件,在装配之后数小时内 陆续发生断裂,断裂比例达40%~50%。某特种产品镀镉件在 使用过程中曾出现过批量裂纹断裂,曾组织过全国性攻关,制订 严格的去氢工艺。另外,有一些氢脆并不表现为延迟断裂现象, 例如:电镀挂具(钢丝、铜丝)由于经多次电镀和酸洗退镀,渗氢 较严重,在使用中经常出现一折便发生脆断的现象;猎枪精锻用 的芯棒,经多次镀铬之后,堕地断裂;有的淬火零件(内应力大)在 酸洗时便产生裂纹。这些零件渗氢严重,无需外加应力就产生 裂纹,再也无法用去氢来恢复原有的韧性。
电镀氢脆的原理与控制
避免和消除的措施
2 采用低氢扩散性和低氢溶解度的镀涂层
一般认为,在电镀Cr、Zn、Cd、Ni、Sn、Pb
时,渗入钢件的氢容易残留下来,而Cu、Mo、Al、Ag、 Au、W等金属镀层具有低氢扩散性和低氢溶解度,渗氢较少。 在满足产品技术条件要求的情况下,可采用不会造成渗氢的涂 层,如机械镀锌可以,不会发生氢脆,耐蚀性高,附着力好,厚5~
电镀氢脆的原理与控制
电镀氢脆的原理与控制
氢脆机理
延迟断裂现象的产生是由于零件内部的氢向应力集中的 部位扩散聚集,应力集中部位的金属缺陷多(原子点阵错位、空 穴等)。氢扩散到这些缺陷处,氢原子变成氢分子,产生巨大的压 力,这个压力与材料内部的残留应力及材料受的外加应力,组成
- 1、下载文档前请自行甄别文档内容的完整性,平台不提供额外的编辑、内容补充、找答案等附加服务。
- 2、"仅部分预览"的文档,不可在线预览部分如存在完整性等问题,可反馈申请退款(可完整预览的文档不适用该条件!)。
- 3、如文档侵犯您的权益,请联系客服反馈,我们会尽快为您处理(人工客服工作时间:9:00-18:30)。
金属材料的两种经常有关而又有别的被破坏(或断裂)的现象。
目前,由延迟断裂氢脆引发的弹性紧固件断裂自然是一个严重的产品质量问题,人们可以采取各种技术来减少和预防弹性紧固件的氢脆问题。
1.材料缺陷的影响
弹性紧固件材料表面缺陷对电镀锌的有害影响是不容忽视的,比如钢板表面轻微裂纹折叠、斑痕蚀坑夹杂和超过允许深度的脱碳层,都会对弹性紧固件镀锌产生十分有害的影响,压弯成型不当造成表面插划伤,局部应力集中等都会有不良影响。
⑶应选择氢脆性较小的镀锌电解液,一般而言,氯化物型镀锌电解液相对析氢较少,产生氢脆的可能性也小;而氰化物镀锌电解液析氢、渗氢较多,产生氢脆的机率也较大。
⑷采用有效的驱氢工序驱散渗氢,减少氢脆应力。驱氢温度一般为190-230℃,驱氢时间6-8h。在电镀锌后钝化前2h内进行,停留时间越短越好。
我要评论查看评论
2.热处理工艺的影响
热处理工艺对弹性紧固件电镀锌后的氢脆是有较大影响的,若硬度≥45HRc时,均会诱发或导致弹性紧固件断裂。
在确保热处理技术参数的前提下,选择适宜的加热温度,合理的加热时间,充分予以回火。以最大限度地消除组织应力和热应力,避免其有害影响。淬火加热时应严防氧化和脱碳,网带炉碳势控制在0.60%-0.70%,盐浴炉必须认真脱氧捞渣,进行硬度检测时,严格注意表面层造成硬度虚假现象,使硬度測试值失真。一般应控制在42-44HRc为佳,不要超过45HRc。
(1)
式中α为形状因子,可从断裂力学手册中查到。裂纹深度(a)的扩展速度(da/dt)随KI的变化,一般有图3所示的三阶段的关系,依据Ⅱ阶段的da/dt以及(1)式,可以估算寿命。
上述各种试验方法也适用于氢脆,这时,试样或预先充氢,或在致氢环境(气相或液相)中加载,一般也获得类似图2及图3的结果。此外,对于预先充氢的试样,也采用一般的抗拉试验,用断面收缩率(ψ)的变化来确定脆化系数I:
避免和消除的措施
.1 减少金属中渗氢的数量
在除锈和氧化皮时,尽量采用吹砂除锈,若采用酸洗,需在酸洗液中添加若丁等缓蚀剂;在除油时,采用化学除油、清洗剂或溶剂除油,渗氢量较少,若采用电化学除油,先阴极后阳极;在电镀时,碱性镀液或高电流效率的镀液渗氢量较少。
2 采用低氢扩散性和低氢溶解度的镀涂层
一般认为,在电镀Cr、Zn、Cd、Ni、Sn、Pb时,渗入钢件的氢容易残留下来,而Cu、Mo、Al、Ag、Au、W等金属镀层具有低氢扩散性和低氢溶解度,渗氢较少。在满足产品技术条件要求的情况下,可采用不会造成渗氢的涂层,如机械镀锌可以,不会发生氢脆,耐蚀性高,附着力好,厚5~100
对应力腐蚀断裂的抑制可根据已知的表象规律和机理基础从材料、应力和腐蚀三个方面选择抑制措施。
材料抑制在应力腐蚀体系中,材料的屈服强度(σs)愈高,则K愈低(图6)。图中虚线表明(1)式中裂纹深度ac与K及σs之间的关系:σs愈高,能容许的ac愈小,构件反而愈不安全。用于含H2S的油气田的钢管,为了抑制SCC,硬度一般控制在HRC22以下。在沸腾的42%MgCl2水溶液中,常用的Cr18%-Ni8%奥氏体不锈钢的应力腐蚀敏感性最大,增镍降铬,都可降低这种敏感性。此外,采用过时效处理(见脱溶),可以降低Zn-Mg-Cu系铝合金的应力腐蚀断裂敏感性。
曾经将阳极溶解机理叫作“活化途径机理”,认为这种活化途径是预先存在的。例如高强度铝合金、α黄铜、低碳钢的晶界区。但是,预先存在的活化途径并不是必要条件。例如,α黄铜在氧化性的含NH嬋的水溶液中,SCC是沿晶的;而在非氧化性的含NH嬋的水溶液中,SCC却是穿晶的。
氢致开裂机理或称氢脆机理,是应力腐蚀断裂的第二种机理。这种机理承认SCC必须首先有腐蚀,但是,纯粹的电化学溶解,在很多情况下,既不易说明SCC速度,也难于解释SCC的脆性断口形貌。氢脆机理认为,蚀坑或裂纹内形成闭塞电池,局部平衡使裂纹根部或蚀坑底部具备低的pH值,这是满足阴极反应放氢的必要条件。这种氢进入金属所引起的氢脆,是SCC的主要原因。这种机理取决于氢能否进入金属以及金属是否有高度的氢脆敏感性。高强度钢在水溶液中的SCC以及钛合金在海水中的SCC是氢脆引起的。
应力腐蚀断裂(SCC) 是应力与腐蚀介质协同作用下引起的金属断裂现象(见金属腐蚀)。它有三个主要特征:①应力腐蚀断裂是时间的函数。拉伸应力越大,则断裂所需时间越短;断裂所需应力一般都低于材料的屈服强度。这种应力包括外加载荷产生的应力、残余应力、腐蚀产物的楔形应力等。②腐蚀介质是特定的,只有某些金属-介质的组合(见表)情况下,才会发生应力腐蚀断裂。若无应力,金属在其特定腐蚀介质中的腐蚀速度是微小的。③断裂速度在纯腐蚀及纯力学破坏之间,断口一般为脆断型。
氢脆(HE) 又称氢致开裂或氢损伤,是一种由于金属材料中氢引起的材料塑性下降、开裂或损伤的现象。所谓“损伤”,是指材料的力学性能下降。在氢脆情况下会发生“滞后破坏”,因为这种破坏需要经历一定时间才发生。氢的来源有“内含”的及“外来”的两种:前者指材料在冶炼及随后的机械制造(如焊接、酸洗、电镀等)过程中所吸收的氢;而后者是指材料在致氢环境的使用过程中所吸收的氢(见金属中氢)。致氢环境既包括含有氢的气体,如H2、H2S;也包括金属在水溶液中腐蚀时阴极过程所放出的氢。
金属的应力腐蚀断裂和氢脆是两种既经常相关而又不同的现象。在高温高压氢气中结构件的开裂,既是HE,又是SCC;水溶液中应力腐蚀时,若阴极过程析出的氢对断裂起了决定性作用,则这种破坏既是SCC,也是HE;这两个实例便位于图1所示的重叠区内。
试验方法和工程参量应力腐蚀试验一般采用光滑或缺口试样,固定环境条件(即腐蚀介质和温度),采用断裂为临界点、测定固定应力下的断裂时间(tf)或固定tf下的断裂应力(σf),用tf的长短或σf的高低,来衡量材料抗应力腐蚀断裂能力的大小。70年代以来,人们广泛地运用了断裂力学研究应力腐蚀断裂;用预制裂纹的试样进行应力腐蚀试验,如图2所示。断裂时间tf是随着应力场强度因子(KI)的降低而增加的;随着tf的增加,KI下降并趋近于一稳定值K (曲线a),或采用给定的tf来确定K(曲线b)。K叫作应力腐蚀断裂的临界应力场强度因子,也称应力腐蚀临界应力强度因子。根据断裂力学公式,可以计算它与断裂应力σf及临界裂纹深度ac之间的关系:
应力抑制降低拉伸应力,可降低应力腐蚀断裂敏感性。例如,冷加工后的黄铜件、奥氏体不锈钢的焊件,通过消除残余应力的退火处理,也可以避免上表所示的应力腐蚀断裂,喷丸、滚压及其他使表面处于残余压应力状态的机械加工工艺对抑制应力腐蚀断裂也是有效的。缺口半径(ρ)影响应力集中系数,从而也是影响K(图7Байду номын сангаас的重要因素。因此,增加构件的ρ,可以有效地提高抗应力腐蚀断裂的能力。
弹性紧固件电镀锌氢脆分析及预防
为有效地提高弹性紧固件(弹簧垫圈、锥形垫圈、鞍形垫圈、波形垫圈等)抗蚀防护性能和装饰性,多半要进行表面处理,如发黑、磷化、电镀锌等处理。其中电解镀锌及钝化处理应用更为广泛。
加上弹性紧固件的硬度一般在42-50HRc之间,由于材料及表面处理的原因,它对氢比较敏感,在电镀后,除氢处理未达到驱氢目的,其残存的氢会造成弹性紧固件的延迟断裂。
阳极溶解机理说明了应力腐蚀断裂的主要特征──腐蚀介质是特定的。因为只有在活化-钝化或钝化-再活化的很窄电位范围(图5)内,才能产生应力腐蚀断裂;而给定的金属介质组合,具有固定的开路电位,若这个电位落在图5所示的金属的应力腐蚀断裂电位区内,便会发生应力腐蚀断裂。这个机理还可说明许多新的实验现象。例如,Cr17~25%-Mo5%-Cu0.37%(或Ni1%)铁素体不锈钢的阳极极化曲线与Cr18%-Ni8%奥氏体不锈钢的相近,在热浓的MgCl2水溶液中,这两种不锈钢尽管组织不同,同样都发生应力腐蚀断裂。又例如α黄铜在含NH嬋的碱性水溶液中发生应力腐蚀断裂(见前表),但是,通过阳极极化,α黄铜在含No婣及SO娹的酸性水溶液中,也能发生应力腐蚀断裂。
4.氢脆的预防
⑴电镀锌前必须严格控制阴极电解除油。对弹性紧固件(尤其是厚度≤1mm),不宜采用阴极电解除油,而是采用阳极电解除油、化学除油或超声波除油,也可以选用金属清洗剂除油(效果较好)。
⑵对弹性紧固件不宜采用强酸腐蚀,而是采用喷砂或喷丸等处理方法达到净化、活化表面目的。必须进行酸洗活化处理时,选用盐酸较硫酸为好。注意掌握酸洗时间不宜过长(每次控制30-60s),以多次短时间比长时间酸洗效果好。
3.电镀过程的影响
弹性紧固件由于氢的侵袭往往发生氢脆断裂,造成重大损失。析氢渗氢在整个电解镀锌中是不可避免的,析出的氢能够渗入镀锌层,甚至渗入基体金属内。锌的吸氢大约在0.001%-0.100%,而铁碳合金吸氢在0.1%左右。氢在金属内使晶格扭曲,产生很大的内应力,致使其机械性能降低,析氢不仅对镀层性能产生不利影响,如产生针孔、麻点、气泡等缺陷,而且会渗透至基体金属中,使金属韧性大大降低,导致零件脆断。析氢的原因除在热处理外,较高的加热温度,氢很容易渗入零件应力集中的区域,酸洗和电镀都会发生析氢。
腐蚀抑制改进设计,防止腐蚀介质的富集,是一项有效的措施。例如,奥氏体不锈钢管在含Cl-气氛中易于吸收Cl-并逐渐富集,曾用硅胶油先涂在管的外壁,然后再包绝热层,成功地解决了这个问题。介质的预处理,也是一项重要措施。例如,汽轮机发电机组用水应预先处理,降低NaOH含量;核反应设备的不锈钢热交换器中,需将水中含有的Cl-及O2降低到PPm级以下。缓蚀剂、涂层及电化学保护都可用于抑制腐蚀。但应指出,以氢脆为断裂机理的应力腐蚀体系中,阴极极化及阳极极化都可促进局部区域氢的析出,都使裂断纹扩展加速。
氢致开裂机理又可从三方面考虑:①推动力理论。化学反应所形成的气体(CH4)、H2O与沉淀反应所析出的氢气团和H2气的内在应力以及氢致马氏体相变应力,都可与外加的或残余应力叠加,引起开裂。②阻力理论。氢引起的相变产物如马氏体或氢化物,固溶氢引起的金属结合能及表面能下降,都可降低氢致开裂阻力,促进开裂。③过程理论。氢在裂纹尖端区多方向应力梯度下的扩散和富集,表面膜对氢渗入和渗出的影响,氢在金属内部缺陷的陷入和跃出,氢对裂纹尖端塑性区的影响等,都是氢致开裂或氢脆的过程理论。上述的三种机理不是相互矛盾对立的,而是相辅相成的。对于具体的体系,应从氢所造成的变化去确定起决定作用的机理。