注塑件生产通用标准
通用塑料注塑工艺标准参数表

常用塑料注塑工艺参数表:常用塑料注塑工艺参数(2)2010-06-16 20:02:13| 分类:个人日记| 标签:|字号大中小订阅聚甲醛加工参数聚甲醛的成型收缩率聚甲醛的后收缩九、PC注塑工艺特性与工艺参数的设定1、聚集态特性属于无定型塑料,Tg为149~150℃;Tf为215~225℃;成型温度为250~310℃; 2、热稳定性较好,并随分子量的增大而提高。
但PC高温下遇水易降解,成型时要求水分含量在0.02%以下。
高温下水分对PC特别有害。
在成型前,PC树脂必须进行充分干燥(并且应当充分注意防止干燥过的物料再吸湿)。
干燥效果的快速检验法,是在注塑机上采用“对空注射”。
3、熔体粘度高,流动性较差,其流动特性接近于牛顿流体,熔体粘度受剪切速率影响较小,而对温度的变化十分敏感,在适宜的成型加工温度范围内调节加工温度,能有效地控制PC的粘度。
4、由于粘度高,注射压力较高,一般控制在80~120MPa。
对于薄壁长流程、形状复杂、浇口尺寸较小的制品,为使熔体顺利、及时充模,注射压力要适当提高至120~150MPa。
保压压力为80~100MPa。
5、成型时,冷却固化快,为延迟物料冷凝,需控制模温为80~120℃。
6、PC分子主链中有大量苯环,分子链的刚性大,注塑中易产生较大的内应力,使制品开裂或影响制品的尺寸稳定性;(在100℃以上作长时间热处理,它的刚硬性增加,内应力降低)。
PC的典型干燥曲线台湾奇美典型牌号加工参数:十、PA及玻纤增强PA注塑工艺特性与工艺参数设定 1、常用品种及其熔点:q 品种:尼龙-66;尼龙-610;尼龙-1010;尼龙-1212;尼龙-46尼龙-6;尼龙-7;尼龙-9;尼龙-11;尼龙-12;尼龙-66/6、尼龙-66/610;尼龙-6∕66∕1010;尼龙-66/6/610q 熔点:尼龙n系列:尼龙-6 215~220℃;尼龙-12为178℃;尼龙m,n系列:尼龙-46 295 ℃;尼龙-66 255~265℃;尼龙-610 215~223℃;尼龙-1010 200℃;共缩聚尼龙:由于分子链的规整性较差,结晶性和熔点一般较低,如尼龙-6∕66∕1010的熔点仅为155~175℃,但其有较好的透明性和弹性。
注塑件生产通用标准
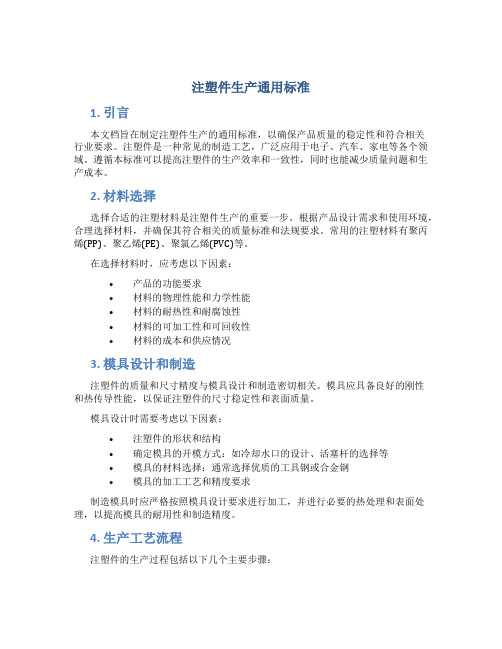
注塑件生产通用标准1. 引言本文档旨在制定注塑件生产的通用标准,以确保产品质量的稳定性和符合相关行业要求。
注塑件是一种常见的制造工艺,广泛应用于电子、汽车、家电等各个领域。
遵循本标准可以提高注塑件的生产效率和一致性,同时也能减少质量问题和生产成本。
2. 材料选择选择合适的注塑材料是注塑件生产的重要一步。
根据产品设计需求和使用环境,合理选择材料,并确保其符合相关的质量标准和法规要求。
常用的注塑材料有聚丙烯(PP)、聚乙烯(PE)、聚氯乙烯(PVC)等。
在选择材料时,应考虑以下因素:•产品的功能要求•材料的物理性能和力学性能•材料的耐热性和耐腐蚀性•材料的可加工性和可回收性•材料的成本和供应情况3. 模具设计和制造注塑件的质量和尺寸精度与模具设计和制造密切相关。
模具应具备良好的刚性和热传导性能,以保证注塑件的尺寸稳定性和表面质量。
模具设计时需要考虑以下因素:•注塑件的形状和结构•确定模具的开模方式:如冷却水口的设计、活塞杆的选择等•模具的材料选择:通常选择优质的工具钢或合金钢•模具的加工工艺和精度要求制造模具时应严格按照模具设计要求进行加工,并进行必要的热处理和表面处理,以提高模具的耐用性和制造精度。
4. 生产工艺流程注塑件的生产过程包括以下几个主要步骤:4.1 材料预处理材料预处理是为了消除材料中的湿气和气泡,以提高注塑件的密实性和表面质量。
常见的材料预处理方法包括干燥、烘烤和真空处理等。
4.2 注塑注塑是将预处理的材料通过注塑机加热熔化后,通过模具的喷嘴注入模腔中,使其冷却凝固并形成注塑件的过程。
在注塑过程中,应注意控制以下几个关键因素:•注塑温度:根据材料的熔点和热性能确定合适的注塑温度范围•注塑压力:根据产品的尺寸和形状确定合适的注塑压力•注塑速度:控制注塑速度,以避免产生气泡、毛刺等缺陷•冷却时间:保证注塑件充分冷却,以避免变形和缩水等问题4.3 产品去毛刺处理在注塑过程中,可能会产生一些毛刺或射出物,需要进行去毛刺处理。
注塑件检验标准

注塑:注塑是一种工业产品生产造型的方法。
产品通常使用橡胶注塑和塑料注塑。
注塑还可分注塑成型模压法和压铸法。
注射成型机(简称注射机或注塑机)是将热塑性塑料或热固性料利用塑料成型模具制成各种形状的塑料制品的主要成型设备,注射成型是通过注塑机和模具来实现的。
注塑件检验标准:闭合度为0.65即可。
检验标准:1、MIL-STD-105E II表,正常检验、单次抽样计划,AQL订定为CRI=0、MAJ=0.65、MIN=1.5。
2、相关抽样标准或判定标准,可视品质状况或客户要求等做修正。
质量要求:一、基本尺寸1、胶件的几何形状,尺寸大小精度应符合正式有效的开模图纸(或3D文件)要求。
2、通用结构尺寸标准。
a、胶件一般要求做到平均胶厚,非平均胶厚应符合图纸要求。
b、螺柱根部直径:M3螺丝为φ6.0+0.2mm,火山口直径φ10.0mm;M2.6螺丝为φ5.0+0.2mm,火山口直径φ9.0mm。
c、叉骨、围骨根部厚度:1.2+0.2mm。
d、按钮的顶RUBBER十字骨顶部厚度:0.9+0.1mm。
e、司筒柱顶部壁厚:1.2±0.1mm。
f、电池箱后模勾针位胶厚小于2.0mm。
g、胶件同PL面处前后模出胶位时其错位小于0.05 mm。
h、面底壳配合。
3、二级或三级止口配合要求PL面错位小于0.1 mm,没有刮手现象;4、包止口配合单边间隙为0.1~0.3 mm,外形复杂取大值。
a、电池门与电池箱间水平方向单边间隙为0.2~0.3 mm。
b、钮与孔配合。
一般几何形状钮与孔单边间隙为0.15~0.25 mm。
异形钮与孔单边间隙为0.3~0.4 mm,喷油钮间隙应取大值。
钮与花仔配合时其配合情况能达到安全测试标准。
c、插卡位配合。
插卡门与面底壳的配合单边间隙为0.2~0.3 mm。
插口与插盒单边间隙为0.5mm。
d、四大件转轴位轴向单边最小间隙0.1~0.2 mm。
e、LOCK与其配合枕位孔单边间隙为0.2 mm。
注塑件通用检验标准及表格

1. 装配时不能出现组装困难、胶件破裂或装配后影响功能的情 况; 2. 装配的成品做安全测试时不能有安全问题发生产。
紧配管位钉位在开合三次以上,钉子不能断裂失去功能。
螺丝柱打螺丝测试,在达到如下扭力情况下,不能出现螺丝打 不进、螺丝打滑、螺丝柱爆裂、螺丝头孔柱爆裂的情况: M2.0自攻螺丝 , 扭力≥ 2.0kgf.cm ; M2.3自攻螺丝 , 扭力≥ 2.5kgf.cm ; M2.6自攻螺丝 , 扭力≥ 3.0kgf.cm ; M3.0自攻螺丝 , 扭力≥ 4.0kgf.cm ; 紧配轴孔在打入相配铁轴时不能撑爆,另外,打入轮轴的车轮 必须能承受 90N拉力不脱开。 拆装力度 0.8 ~1.5KG,500次后仍能达 0.5KG以上
1. 不能影响装配和功能。 2. 组装后产品外露部分,对比签办,不可高出或凹陷大于 0.3mm 。 组装成品后外露部分,缺陷 5.9E不可明显可视。
组装成品后外露部分,缺陷 5.9E不可明显可视。
组装成品后外露部分,缺陷 5.9E不可明显可视。
目测、试装、量具
目测、试装、量具 试装、目测 试装、目测 试装、目测
试装、目测
试装、目测
试装、目测
扭力计
试装、目测、拉力计 试装,拉力计 试验、目测 试验、试装 试验、试装
第 2页 共3页 版本 :1
标准说明: 1. 以上标准规定的是检验要求,而缺陷分类和抽样标准由品管部制定。 2. 具体产品如无特别规定,则按通用标准执行。 3. 以上标准执行出现异议时,可向工程部寻求确认和极限签办。
喷印电镀后,注塑件上的注塑缺陷, 5.9E不可明显可视。
说明:凡是后工序需电镀或喷印注塑件,均不能使用可影响喷印电镀效果的脱模剂和清洁剂。
QMZ-J54.006-2018_注塑件及装配通用技术条件(含AM1)
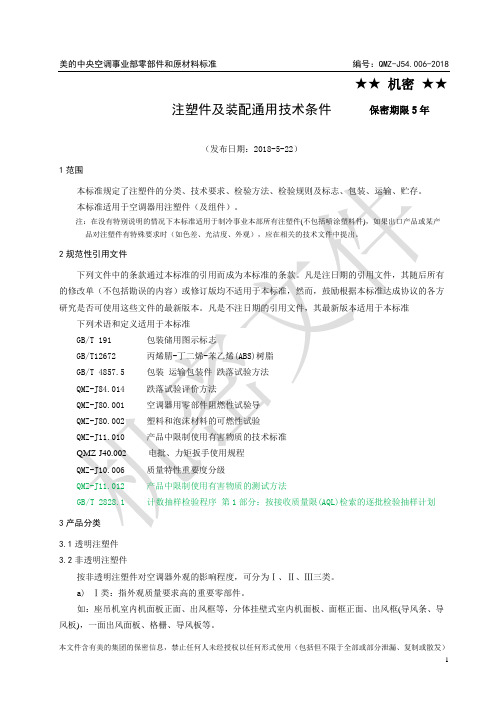
注塑件及装配通用技术条件(发布日期:2018-5-22)1 范围本标准规定了注塑件的分类、技术要求、检验方法、检验规则及标志、包装、运输、贮存。
本标准适用于空调器用注塑件(及组件)。
注:在没有特别说明的情况下本标准适用于制冷事业本部所有注塑件(不包括喷涂塑料件),如果出口产品或某产品对注塑件有特殊要求时(如色差、光洁度、外观),应在相关的技术文件中提出。
2 规范性引用文件下列文件中的条款通过本标准的引用而成为本标准的条款。
凡是注日期的引用文件,其随后所有的修改单(不包括勘误的内容)或修订版均不适用于本标准,然而,鼓励根据本标准达成协议的各方研究是否可使用这些文件的最新版本。
凡是不注日期的引用文件,其最新版本适用于本标准下列术语和定义适用于本标准 GB/T 191 包装储用图示标志GB/T12672 丙烯腈-丁二烯-苯乙烯(ABS)树脂 GB/T 4857.5 包装 运输包装件 跌落试验方法 QMZ-J84.014 跌落试验评价方法QMZ-J80.001 空调器用零部件阻燃性试验导 QMZ-J80.002 塑料和泡沫材料的可燃性试验 QMZ-J11.010 产品中限制使用有害物质的技术标准 QMZ-J40.002 电批、力矩扳手使用规程 QMZ-J10.006 质量特性重要度分级QMZ-J11.012 产品中限制使用有害物质的测试方法GB/T 2828.1 计数抽样检验程序 第1部分:按接收质量限(AQL)检索的逐批检验抽样计划 3 产品分类 3.1 透明注塑件 3.2 非透明注塑件按非透明注塑件对空调器外观的影响程度,可分为Ⅰ、Ⅱ、Ⅲ三类。
a) Ⅰ类:指外观质量要求高的重要零部件。
如:座吊机室内机面板正面、出风框等,分体挂壁式室内机面板、面框正面、出风框(导风条、导风板),一面出风面板、格栅、导风板等。
★★ 机密 ★★保密期限5年b)Ⅱ类:指外观质量要求高的次要零部件。
如:分体挂壁式室内机底盘、面框两側面等。
ts16949注塑件形位标准_解释说明以及概述

ts16949注塑件形位标准解释说明以及概述1. 引言1.1 概述TS16949注塑件形位标准是指在汽车零部件制造过程中,针对注塑件的形位测量和要求而制定的一系列标准规范。
这些标准规定了注塑件在尺寸和位置上的公差范围,以确保注塑件能够正确安装和与其他零部件精确配合。
1.2 文章结构本文主要围绕TS16949注塑件形位标准展开详细说明和解释,并探讨其在质量管理中的应用。
文章分为五个部分:引言、TS16949注塑件形位标准解释说明、形位标准的具体要点解析与示例说明、注塑件形位标准在质量管理中的应用、结论与展望。
1.3 目的本文旨在向读者介绍和解释TS16949注塑件形位标准,包括其定义和背景,作用和重要性,以及分类和要求方面的内容。
同时,我们将对形位标准的具体要点进行深入解析,并提供示例说明。
此外,文章还将探讨注塑件形位标准在质量管理中的应用,并分析其对生产过程、质量检验和评估的影响与控制措施。
最后,我们将总结文章主要观点和研究成果,并展望注塑件形位标准研究的不足之处和未来发展方向。
2. TS16949注塑件形位标准解释说明:2.1 定义和背景:TS16949是汽车行业质量管理体系标准,也是ISO/TS 16949:2009技术规范的简称。
注塑件形位标准是该标准中的一个重要部分,用于规范和约束汽车注塑件在尺寸、位置以及相关要求方面的质量控制。
2.2 形位标准的作用和重要性:注塑件形位标准在汽车零部件制造过程中起着至关重要的作用。
通过明确注塑件尺寸公差、位置公差等要求,可以保证零部件在装配过程中的一致性和互换性。
形位标准可以有效地指导产品设计与制造,并为供应商提供参考,从而提高整个供应链上各环节的生产效率和产品质量。
2.3 注塑件形位标准的分类和要求:注塑件形位标准可以分为两大类:尺寸公差和位置公差。
尺寸公差是指允许零部件实际尺寸与理论尺寸之间的偏差范围;而位置公差则主要描述了零部件之间或其它基准面之间的相对位置关系要求。
塑料注塑工艺标准

塑料注塑工艺标准1、PP塑料制品:1.1概述:聚丙烯,英文简称PP,为一种白色蜡状材料,密度0.90g/cm3。
PP具有良好的电性能和化学稳定性,其机械性能、耐热性均高于PE,经过增强的PP可用做工程材料。
PP成纤性好,耐疲劳性好,用其制成的铰链几十万次不断;PP低温冲击性不好,成型收缩率大,产品精度不高。
1.2加工:1.2.1成型特性:1.2.1.1结晶性料,吸湿性小,可能发生熔融破裂,长期与热金属接触易发生分解。
1.2.1.2流动性极好,溢边值0.03mm左右。
1.2.1.3冷动速度快,浇注系统及冷却系统应散热缓慢。
1.2.1.4成型收缩范围大,收缩率大,易发生缩孔、凹痕、变形、方向性强。
1.2.1.5注意控制成型温度,料温低方向性明显,尤其是低温高压时更明显,模温低于50℃以下塑件不光泽,易发生熔接不良、流痕;90℃以上时易发生翘曲、变形。
1.2.1.6塑件应壁厚均匀,避免缺口、尖角,以避免应力集中。
1.2.1.7注塑模及注塑制品:A、最小脱模斜度30’---1°。
B、最小壁厚0.85mm。
C、流程与壁厚的关系: ,其中t为壁厚(mm),l为流程(mm)。
D、塑件转接处均应有不小于0.5---1mm的圆角。
E、塑件壁厚应尽可能均匀一致,以防制品结构缩水和翘曲、变形。
1. 3注塑工艺条件:1.2.3.1干燥温度和时间:封袋PP无须干燥即可注塑,预热温度和时间:80---100℃/1---2h。
1.2.3.2料筒温度:200---230℃。
1.2.3.3射嘴温度:180---190℃。
1.2.3.4模温:20---60℃。
1.2.3.5注射压力:≤69---98Mpa1.2.3.6注射时间(包括保压时间):≤20---60S。
1.2.3.7冷却时间:≤20---90S。
1.2.3.8螺杆转速:≤80rpm。
2、PE塑料制品:2.1概述:聚乙烯,英文简称PE,有低密度聚乙烯(LDPE)、高密度聚乙烯(HDPE)及线性低密度聚乙烯(LLDPE)三种。
注塑件生产通用标准
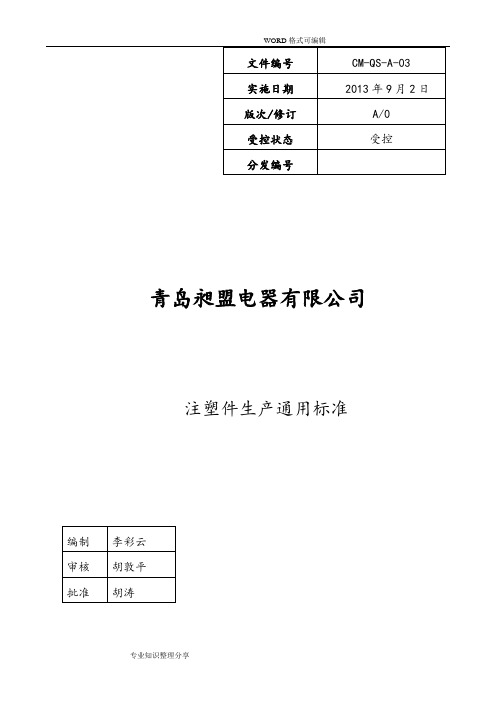
青岛昶盟电器有限公司注塑件生产通用标准注塑件生产通用标准一、范围本标准规定了注塑件的分类、技术要求、检验方法、检验规则及标志、包装、运输、贮存。
本标准适用于汽车配件用注塑件。
二、引用标准1.1 客户图纸及技术要求。
1.2 GB2828-2003GⅡ抽样及加严抽样标准。
1.3 具体见附表。
1.4 作业指导书。
三、产品分类1.5 透明注塑件1.6 非透明注塑件按非透明注塑件对外观的影响程度,可分为Ⅰ、Ⅱ、Ⅲ三类。
Ⅰ类:指外观质量要求高的重要制件。
通称为“A面”,如塑件的出面。
Ⅱ类:指外观质量要求高的次要制件。
通称为“B面”,如塑件的侧面,背面,内饰件。
Ⅲ类:指外观质量要求一般的制件。
通称为“C面”,如组装在一起的制件底面,不可见面。
四、技术要求1.7 一般要求1.7.1 清晰、正确,图案及字体符合图纸要求。
不得有花、刮花等缺陷。
1.7.2 熔接痕各类注塑件允许存在不明显的由模具结构决定、工艺无法解决的熔接痕,但不得影响整机外观。
具体按封样状态执行。
1.7.3 飞边各类注塑件不得存在影响装配、结构、外观存在质量隐患的飞边;外观的划伤等现象。
1.7.4 注塑组装件装配质量,严格按作业指导书执行。
1.8 注塑件外观质量1.8.1 清洁度要求:表面干净,无脏迹、油污。
1.8.2 表面分型面连接圆滑,表面光洁,无磕碰划、雪花纹,装配可视面无杂质、白印。
1.8.3 汽车配件用注塑件修边整齐,无锯齿状,修边宽度≤0.5mm,注料口修边整齐。
1.8.4 装配可视面各处不允许有毛刺。
1.8.5汽车配件用注塑件平整度≤1.5/500mm,离40cm侧光目视筋痕收缩不明显,注料口部位无缩痕。
1.8.6与封样件颜色相同,没有封样件的符合图纸所标色标颜色,成套零件中,目测无明显色差;整体色泽均匀,线形部分粗细均匀;无明显影响外观的皱纹、气泡。
1.8.7 直接外露表面与喷漆颜色不一致的杂质,每点的直径应小于等于0.3mm。
1.8.8 单个塑料喷涂件正面可视面上直径小于等于0.3mm的杂质不得超过5点。
注塑件检验标准

封闭度为0.65。
检验标准:1. MIL-STD-105E(国家标准gb2828-87通用检验级别II)的表II,常规检验和单个抽样计划的AQL为CRI = 0,maj = 0.65,min = 1.5。
2.有关抽样标准或判断标准可根据质量状况或客户要求进行修改。
扩展数据:质量要求:1,基本尺寸1.橡胶零件的几何形状,尺寸和精度应符合正式有效的开模图纸(或3D文件)的要求。
2.一般结构尺寸标准。
一种。
橡胶零件一般要求平均胶厚,非平均胶厚应符合图纸要求。
b。
螺栓根直径:m3螺钉为φ6.0 + 0.2mm,弹坑直径为φ10.0mm; m2.6螺丝为φ5.0 + 0.2mm,弹坑直径为φ9.0mm。
C。
叉骨和骨膜根的厚度:1.2±0.2mm。
d。
按钮顶部橡胶十字的厚度:0.9 + 0.1mm。
e。
插头的顶壁厚度为1.2±0.1毫米。
F。
电池盒后模具中的胶水厚度小于2.0毫米。
G。
前后模具在同一PL表面的错位小于0.05 mm。
H。
正面和底部饰身。
3.对于第二或第三类接头,PL表面的错位应小于0.1mm,且不得刮擦;4.端部接头的单边间隙为0.1-0.3 mm,对于复杂形状,取较大的值。
一种。
电池盖和电池盒之间的水平单边间隙为0.2-0.3毫米。
b。
按钮适合孔。
通常,按钮和孔之间的间隙为0.15-0.25毫米。
异形按钮与孔之间的间隙为0.3-0.4毫米,燃油喷射按钮之间的间隙应更大。
当按钮与花朵匹配时,配合即可达到安全测试标准。
C。
插入卡使其适合。
浇口与表面和底壳之间的配合单边间隙为0.2〜0.3 mm。
插座与插头盒之间的间隙为0.5mm。
d。
四个大型旋转轴的最小轴向单边间隙为0.1-0.2 mm。
e。
锁和与其匹配的枕孔之间的单边间隙为0.2毫米。
F。
支架与其匹配孔之间的单边间隙为0.1-0.2 mm,如果长度大于150 mm,则取较大值。
G。
盖子与其配合孔之间的单边间隙为0.1毫米。
注塑产品通用外观检查标准

文件控制印章副本发放部门☐营业部☑品证部☑装配☐项管☐行政部☐财务报关☑采购部☑注塑部☑清洁胶☑货仓☐厂机部□SMD☑PMC ☑工程部☑喷油丝印☐工模部☐电脑课☑IMDPATH:G:\DOCCON\TS16949工作指引\KS-QMD-002.DOC如此印章并非蓝色,代表此文件并非合法之版本,并不会受到控制及更新,请使用受控制之文件。
一、目的:明确注塑品一般外判定基准,使作业及检验有据可依。
二、范围:适用于公司所有注塑品的外观判定(若客户有要求时按客户特别要求执行)。
三、内容3.1注塑品常见的外观缺陷:混色、白化、黑点、缺胶、溢胶、缩水、夹水纹、银纹、气纹、伤、油污、表面积灰等;3.2金属部件一般外观判定标准;3.3喷油、丝印、移印、烫印一般外观判定标准;3.4组装件一般外观判定要求及标准;3.5其它类产品一般外观判定要求及标准。
3.6手柄类(BOSCH)外观判定标准3.7工具箱类(BOSCH)外观判定标准3.8 汽车内饰件外观检验标准四、定义:无五、程序内容:常见缺陷及一般外观判定基准5.1注塑产品通用检查标准见附表(1)5.2 金属部件的一般判定基准:5.2.1 金属表面不能有油污,不可有异物附着,用手、目、白抹布及胶纸确认。
5.2.2 金属件生锈断面一般只要少于全周的三分之一可以接受,对螺纹孔生锈只要内径、外径、有效径三项合格可以接收.但部品表面生锈,涂层及表面处理层脱落均不可。
5.2.3 金属部品变形不可,加工中遗漏不可,断裂不可,螺纹倾斜1°内可接受.5.2.4 金属部品如客户有特别要求,则必须按客户要求执行。
5.2.5 关于五金件和处理保管有其特殊要求,具体可参考祥工016:五金件处理标准。
5.2.6 金属表面若有酒精无法抹去之异色,对内装件可接受。
5.3 喷油、丝印、移印、烫印的一般具体测试及要求可参考<祥品003>的“3A”5.3.1 质检员检查,喷油、丝印、移印、烫印后易显现注塑缺陷。
注塑件通用技术条件

注塑件通用技术条件(总10页)-CAL-FENGHAI.-(YICAI)-Company One1-CAL-本页仅作为文档封面,使用请直接删除Q/LX注塑件通用技术条件隆鑫通用动力股份有限公司发布前言本标准是对Q/LX C2—2006的修订,与Q/LX C2—2006相比主要差异如下:——将GB/T 1843-2008代替作废标准GB/T 1843-1996 、GB/T 1040.1-2006~GB/T 1040.4-2006代替GB/T 1040-1992、GB/T 1039-1992 等;——新增加引用标准GB/T1031-2009《产品几何技术规范(GPS) 表面结构轮廓法表面粗糙度度参数及其数值》及GB/T8807-1988《塑料镜面光泽试验方法》;——将“重庆润通工业有限技术开发部”修订为“重庆隆鑫机车有限公司塑胶分部品质技术部”;——补充第7.2.2的检查抽样规则;——增加纹路、顶白的术语和定义;——纠正标准中的错别字如“第7.3.3 ……也可同时随即多抽改为随机多抽”;——删除未使用的材料标准如“聚氯乙烯(PVC)产品”;——删除标准内光亮度要求,因白坯制件的光泽度都是烤漆后作要求;——删除制件应具有光泽,同批产品色泽应一致不允许有色差,因为喷砂、皮纹处理的目的是用亚光或隐去光泽,该条要求是矛盾的。
本标准实施的过渡要求:对于本标准实施前已经做完实验的注塑产品,对照本标准相应规定如有不符,给予6个月的过渡期。
本标准由隆鑫通用动力股份有限公司提出。
本标准由隆鑫通用动力股份有限公司技术中心管理部规格管理室归口。
本标准由重庆隆鑫机车有限公司塑胶分部品质技术部起草。
本标准主要起草人:刘琼本标准审核人:程光敏本标准批准人:何军本标准所代替标准版本的历次发布情况为:——Q/LX C2—2006注塑件通用技术条件1 范围本标准规定了摩托车注塑产品的术语和定义、要求、试验方法、检验规则、标志、包装、运输、贮存等。
注塑类内外饰模具通用技术规范

3.26.2 其余零件按照双方协商制定,并满足模具寿命和使用要求。 3.27 注塑成型模具表面有皮纹时,皮纹样式必需符合长安公司提供的皮纹样板 (CTF 样板)及皮纹深度、范围要求。
第 7 页 共 23 页
3.28 内饰件(外饰件)有皮纹要求时,为了具有同一风格装饰效果纹理,模具 型腔的选材必须保持一致。 3.29 模具零件品牌及材料要求。 严禁私自变更和长安达成一致的模具制造过程中所选用的钢材、热流道、关 重标准件等,(如有异议,请提交申请,经长安同意后方可使用)。 3.29.1 模具供应商必须提供相关材料必须证明所备材料符合本要求。若对模具 材料选择若有异议,需书面提出建议,双方商议确认最终材料要求。 3.29.2 模具主要部件材料明细参考下表:
第 2 页 共 23 页
目
录
1.范围 2.规范性引用文件 3.基本要求 4.流道系统 5.液压机构、抽芯及复位机构 6.冷却系统 7.滑块、斜顶机构 8.导向、锁紧及镶拼 9.顶出系统 10.模具安装、起吊 11.品质要求 12.检查 13.项目管理 14.设计变更 15.提交资料 16.其他要求
3.30 在成型部位中,产品和模具均要做断差,采取天包地方式,中小型模具 0.05mm, 大型模具 0.1mm,保险杠等 0.15mm,对于影响内外饰精致工艺 的部位须另单独提出。 4、流道系统 4.1 热流道要求: 4.1.1 供应商模具数据流道系统信息须符合长安汽车股份有限公司 《模流分析报 告》中关于模具流道信息的要求,其主要包含:流道的分类(模具中采用热 流道还是冷流道),流道的截面形状(圆形、梯形、椭圆形等)、流道的尺 寸大小、浇口的形式(点浇口、侧浇口、潜伏式浇口等)、浇口的尺寸大小、 浇口的位置以及浇口的数量等。 4.1.2 浇口套与注塑机喷嘴的配合要求良好,无漏胶。 4.1.3 升温时间要求:热流道 200℃/30min;热喷嘴 200℃/20min;并且能够有 热电偶等加热控制装置对热流道进行精确控制。 4.1.4 热流道总成要耐受在 100-300℃的工作温度所产生的热变形以及需能耐
塑料零部件的通用技术规范和要求详解

塑料零部件的通用技术规范和要求详解General Technical Requirements for Plastic PartsPlastic parts play a vital role in various industries, ranging from automotive to electronics. To ensure the quality and functionality of plastic parts, there are several general technical requirements that need to be met.1. Material Selection: The choice of plastic material is crucial in determining the performance and durability of plastic parts. Factors such as mechanical properties, chemical resistance, and temperature resistance should be considered when selecting the appropriate material.2. Dimensional Accuracy: Plastic parts should meet specific dimensional tolerances to ensure proper fit and function. This requires precise design and manufacturing processes, including injection molding or 3D printing.3. Surface Finish: The surface finish of plastic parts affects not only their appearance but also their performance. Smoothsurfaces are desirable to prevent friction and improve aesthetics.4. Strength and Durability: Plastic parts should possess sufficient strength and durability to withstand the intended application. This involves considering factors such as load-bearing capacity, impact resistance, and fatigue life.5. Environmental Compatibility: Plastic parts should be designed to be environmentally friendly, considering factors such as recyclability, biodegradability, and the use of eco-friendly materials.6. Assembly and Integration: Plastic parts often need to be assembled or integrated with other components. Compatibility, ease of assembly, and proper integration should be considered to ensure seamless operation.7. Regulatory Compliance: Plastic parts should adhere to applicable regulations and standards, such as safety requirements and material restrictions.中文回答:塑料件通用技术要求塑料件在各个行业中起着重要的作用,从汽车到电子产品都有使用。
注塑件通用技术要求
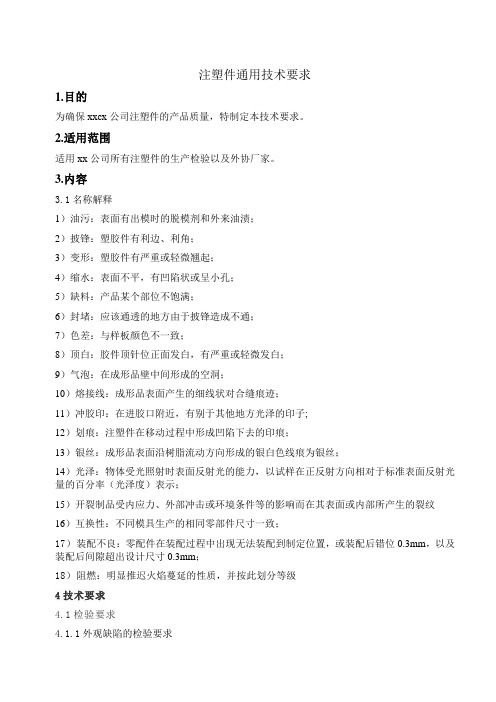
注塑件通用技术要求1.目的为确保xxcx公司注塑件的产品质量,特制定本技术要求。
2.适用范围适用xx公司所有注塑件的生产检验以及外协厂家。
3.内容3.1名称解释1)油污:表面有出模时的脱模剂和外来油渍;2)披锋:塑胶件有利边、利角;3)变形:塑胶件有严重或轻微翘起;4)缩水:表面不平,有凹陷状或呈小孔;5)缺料:产品某个部位不饱满;6)封堵:应该通透的地方由于披锋造成不通;7)色差:与样板颜色不一致;8)顶白:胶件顶针位正面发白,有严重或轻微发白;9)气泡:在成形品壁中间形成的空洞;10)熔接线:成形品表面产生的细线状对合缝痕迹;11)冲胶印:在进胶口附近,有别于其他地方光泽的印子;12)划痕:注塑件在移动过程中形成凹陷下去的印痕;13)银丝:成形品表面沿树脂流动方向形成的银白色线痕为银丝;14)光泽:物体受光照射时表面反射光的能力,以试样在正反射方向相对于标准表面反射光量的百分率(光泽度)表示;15)开裂制品受内应力、外部冲击或环境条件等的影响而在其表面或内部所产生的裂纹16)互换性:不同模具生产的相同零部件尺寸一致;17)装配不良:零配件在装配过程中出现无法装配到制定位置,或装配后错位0.3mm,以及装配后间隙超出设计尺寸0.3mm;18)阻燃:明显推迟火焰蔓延的性质,并按此划分等级4技术要求4.1检验要求4.1.1外观缺陷的检验要求表面光洁,无油污、色泽均匀、无变色,同批产品色调一致。
表面无裂纹、开裂、划伤、飞边及毛刺。
外表面无缩水、变形、顶白、银丝、欠注、留痕、波纹、亮点、麻点、起泡(凸起的)等可视缺陷。
注塑件无缺料、封堵、无明显熔接线印子、无明显冲胶印。
视力:具有正常视力1.0---1.2视力和色感照度:正常日光灯,室内无日光时用40W日光灯或60W普通灯泡的照度为标准。
目测距离:眼睛距离产品40-----50CM直视为准观察时间:<10秒(每个可见平面需要3秒)4.1.2 外观尺寸及尺寸的配合的检验方法使用普通长度测量仪或各种量规进行测量.试装产品能顺利装配4.2 不合格类别划分:B类: 单位产品的重要质量特性不符合规定C类:单位产品的一般质量特性不符合规定4.3检验项目及标准4.3.1塑件的检验标准(表1)A、B、C面示意图注:A面:在正常的产品操作中可见的表面。
注塑件通用检验标准
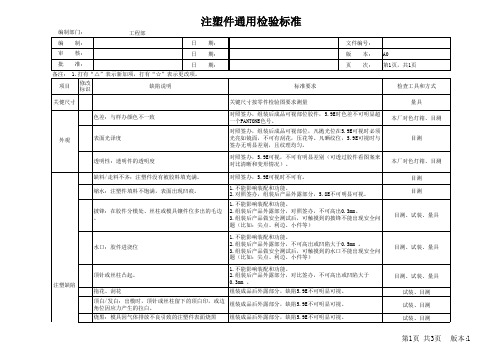
第1页 共3页 版本:1
相配件颜 色一致性 喷印、电
镀
装配
储存和包 装保护 使用寿命
水纹、气纹:因原料未烘干或模具排气不好导致的 组装成品后外露部分,缺陷5.9E不可明显可视。
裂纹、龟裂
组装成品后外露部分,缺陷5.9E不可明显可视。
混色/阴阳色:注塑时混进了不正确的颜色或色粉拌和 不均匀
组ቤተ መጻሕፍቲ ባይዱ成品后外露部分,缺陷5.9E不可明显可视。
拖花、刮花
组装成品后外露部分,缺陷5.9E不可明显可视。
顶白/发白:出模时,顶针或丝柱留下的顶白印,或边 角位因应力产生的拉白。
组装成品后外露部分,缺陷5.9E不可明显可视。
烧黑:模具因气体排放不良引致的注塑件表面烧黑 组装成品后外露部分,缺陷5.9E不可明显可视。
目测、试装、量具
目测、试装、量具 试装、目测 试装、目测 试装、目测
变形
1.不能影响装配和功能。 2.对照签办,5.9E变形不能明显可视。
污点、黑点、杂色点、压花点 隔水线或夹水纹:注塑时熔胶的接合线
同颜色相配合胶件颜色一致性 与存仓胶货以及存仓相配件颜色一致性 上油性能测试 电镀性能测试 与喷油模配合度
缺陷5.9E不可明显可视。
1.不能影响装配和功能需要的强度。 2.组装后产品外露部分,缺陷5.9E不可明显可视。 在本厂的对色灯箱里,5.9E不可有超过一个PANTONE色号的色 差 在。 本厂的对色灯箱里,5.9E不可有超过一个PANTONE色号的色 差。 需喷印胶件,必须进行试喷油测试,不允许有脱油现象
外观光滑的胶件(在成品中外露可视),必须用胶袋保护,整 齐排放,不能出现5.9E可视的花痕。
需配合有运动功能的胶件,和表面易变色胶件或喷印件,需做 老化测试,确认其仓储不会因变形、变色等而不能使用。 需运动部件,要组装成品,按要求进行寿命测试合格。
注塑产品通用外观检查标准

文件控制印章副本发放部门☐营业部☑品证部☑装配☐项管☐行政部☐财务报关☑采购部☑注塑部☑清洁胶☑货仓☐厂机部□SMD☑PMC ☑工程部☑喷油丝印☐工模部☐电脑课☑IMDPATH:G:\DOCCON\TS16949工作指引\KS-QMD-002.DOC如此印章并非蓝色,代表此文件并非合法之版本,并不会受到控制及更新,请使用受控制之文件。
一、目的:明确注塑品一般外判定基准,使作业及检验有据可依。
二、范围:适用于公司所有注塑品的外观判定(若客户有要求时按客户特别要求执行)。
三、内容3.1注塑品常见的外观缺陷:混色、白化、黑点、缺胶、溢胶、缩水、夹水纹、银纹、气纹、伤、油污、表面积灰等;3.2金属部件一般外观判定标准;3.3喷油、丝印、移印、烫印一般外观判定标准;3.4组装件一般外观判定要求及标准;3.5其它类产品一般外观判定要求及标准。
3.6手柄类(BOSCH)外观判定标准3.7工具箱类(BOSCH)外观判定标准3.8 汽车内饰件外观检验标准四、定义:无五、程序内容:常见缺陷及一般外观判定基准5.1注塑产品通用检查标准见附表(1)5.2 金属部件的一般判定基准:5.2.1 金属表面不能有油污,不可有异物附着,用手、目、白抹布及胶纸确认。
5.2.2 金属件生锈断面一般只要少于全周的三分之一可以接受,对螺纹孔生锈只要内径、外径、有效径三项合格可以接收.但部品表面生锈,涂层及表面处理层脱落均不可。
5.2.3 金属部品变形不可,加工中遗漏不可,断裂不可,螺纹倾斜1°内可接受.5.2.4 金属部品如客户有特别要求,则必须按客户要求执行。
5.2.5 关于五金件和处理保管有其特殊要求,具体可参考祥工016:五金件处理标准。
5.2.6 金属表面若有酒精无法抹去之异色,对内装件可接受。
5.3 喷油、丝印、移印、烫印的一般具体测试及要求可参考<祥品003>的“3A”5.3.1 质检员检查,喷油、丝印、移印、烫印后易显现注塑缺陷。
注塑厂塑胶件外观通用检验标准

注塑厂塑胶件外观通用检验标准1.目的:明确注塑厂生产或外购的塑胶产品外观质量标准,规范塑胶产品的外观检验与判定标准。
2.范围:适用于注塑厂生产或外购的塑胶产品。
3.职责:品质:负责按照本标准对塑胶产品进行检验及结果判定。
生产:作业人员需按照本标准进行自检、互检。
4.定义:4.1质量缺陷等级4.1.1超严重缺陷:(Critical)不符合相关安全法规标准,有安全隐患。
可能危及消费者的生命财产安全。
如原料性能达不到安全要求。
4.1.2严重缺陷:(Major)显着降低或丧失实用性能,不能达到使用效果。
可能造成消费者退货、投诉。
如缺胶、堵孔及A面、B面严重料花、缩水、异色、烧焦等缺陷。
4.1.3轻微缺陷:(Minor)一般属于外观问题,不影响正常使用。
可能造成消费者对产品产生消极看法。
如轻微料花、缩水、异色等缺陷。
4.2表面等级划分根据国际通用外观检验标准及使用习惯,通常将外观面按接触的频度分为其A、B、C面,重要性依次降低,具体如下:1)A面:正常放置,除底部外所有能够看到的表面。
(产品的正面、侧面和背面)。
2)B面:产品的底部。
3)C面:通过拆卸螺钉或破坏才能看到的面。
4.3常见塑胶缺陷名称及释义1)异色:胶件表面由不同于本体颜色可见杂质或烧焦的碎片形成。
2)碰划伤:产品受外力作用在表面出现的各种凹线或无深度线性伤痕,用手指甲感觉会有层次感。
3)披锋:在塑料零件的边缘或结合线处线性凸起的胶料及产品边缘处因人工修边而产生缺口等不规则形状(通常为成型不良所致)。
4)色差:胶料着色时色粉混搅不均匀,水口料使用比例不当,注塑温度变化等原因造成与色板颜色形成的偏差(指:实际部品颜色与承认样品颜色或与标准色板比对超出允收值)。
5)缩水:注塑成型后,塑料冷却时由于受到各种影响,产品体积内收缩在表面形成的凹陷的痕迹6)缺胶:注射量不足和模具损坏而造成产品形体的缺损、缺料情形。
7)变形:注塑时,温度太高,冷却时间不够,出模后收缩,本身残留应力变化导致弯曲或由于出模不顺,顶针强行顶出变形。
- 1、下载文档前请自行甄别文档内容的完整性,平台不提供额外的编辑、内容补充、找答案等附加服务。
- 2、"仅部分预览"的文档,不可在线预览部分如存在完整性等问题,可反馈申请退款(可完整预览的文档不适用该条件!)。
- 3、如文档侵犯您的权益,请联系客服反馈,我们会尽快为您处理(人工客服工作时间:9:00-18:30)。
文件编号CM-QS-A-03实施日期2013年9月2日版次/修订A/0受控状态受控分发编号青岛昶盟电器有限公司注塑件生产通用标准编制李彩云审核胡敦平批准胡涛注塑件生产通用标准一、范围本标准规定了注塑件的分类、技术要求、检验方法、检验规则及标志、包装、运输、贮存。
本标准适用于汽车配件用注塑件。
二、引用标准1.1 客户图纸及技术要求。
1.2 GB2828-2003GⅡ抽样及加严抽样标准。
1.3 具体见附表。
1.4 作业指导书。
三、产品分类1.5 透明注塑件1.6 非透明注塑件按非透明注塑件对外观的影响程度,可分为Ⅰ、Ⅱ、Ⅲ三类。
Ⅰ类:指外观质量要求高的重要制件。
通称为“A面”,如塑件的出面。
Ⅱ类:指外观质量要求高的次要制件。
通称为“B面”,如塑件的侧面,背面,内饰件。
Ⅲ类:指外观质量要求一般的制件。
通称为“C面”,如组装在一起的制件底面,不可见面。
四、技术要求1.7 一般要求1.7.1 清晰、正确,图案及字体符合图纸要求。
不得有花、刮花等缺陷。
1.7.2 熔接痕 各类注塑件允许存在不明显的由模具结构决定、工艺无法解决的熔接痕,但不得影响整机外观。
具体按封样状态执行。
1.7.3 飞边 各类注塑件不得存在影响装配、结构、外观存在质量隐患的飞边;外观的划伤等现象。
1.7.4 注塑组装件装配质量,严格按作业指导书执行。
1.8 注塑件外观质量1.8.1 清洁度要求:表面干净,无脏迹、油污。
1.8.2 表面分型面连接圆滑,表面光洁,无磕碰划、雪花纹,装配可视面无杂质、白印。
1.8.3 汽车配件用注塑件修边整齐,无锯齿状,修边宽度≤0.5mm,注料口修边整齐。
1.8.4 装配可视面各处不允许有毛刺。
1.8.5汽车配件用注塑件平整度≤1.5/500mm,离40cm侧光目视筋痕收缩不明显,注料口部位无缩痕。
1.8.6与封样件颜色相同,没有封样件的符合图纸所标色标颜色,成套零件中,目测无明显色差;整体色泽均 匀,线形部分粗细均匀;无明显影响外观的皱纹、气泡。
1.8.7 直接外露表面与喷漆颜色不一致的杂质,每点的直径应小于等于0.3mm。
1.8.8 单个塑料喷涂件正面可视面上直径小于等于0.3mm的杂质不得超过5点。
1.8.9 自然光下(非太阳光直射),塑料喷涂件表面无露白,拉手内及四直角处无明显露白。
1.8.10表面不得出现划伤,碰毛现象。
1.8.11表面及边部不能出现堆漆、桔皮、淋挂现象。
1.8.12断面不允许出现针孔状空洞,杂质等。
1.8.13颜色:表面色泽均匀,应与标准色板或封样件保持一致(∆E≤2.0)1.9透明注塑件外观质量1.9.1颜色 以标准色板或样板为标准进行检验。
色差符合标准色板上下限范围要求。
1.9.2表面光洁度 应达到图纸所规定的表面光洁度的要求。
1.9.3透明度 不低于样板透明度,并且满足零部件设计要求。
1.9.4外观缺陷 除另有规定(标准)或双方约定外,透明注塑件允许存在以下的外观缺陷。
a) 流痕:轻微,正视不明显,且不在零件主要位置。
b) 凹痕:轻微,正视不明显,且不在零件正面位置。
c) 黑点:微小(≤0.5mm),正视不明显,且不在零件正面位置。
d) 杂点:杂点(≤0.5mm),正视不明显,且不在零件正面位置。
e) 机械损伤:每件(部件)允许出现轻微划痕二条,划痕长度≤3mm,且不在零件的正面位置。
f) 顶白:允许在零件次要位置由正视不可见面明显的应力,允许应力长度 ≤10mm 。
g) 长条状缺陷:轻微,正视不明显,且不在零件正面位置。
1.10 非透明注塑件的外观质量1.10.1 零部件颜色要求 所有注塑件颜色应符合标准色板,与标准色板比较,允许色差值ΔE≤1.2。
1.10.2 光洁度 光洁面、磨砂面、亚光面的表面光洁度应符合样板或封样件要求。
1.10.3 外观缺陷划分及判定: 外观缺陷划分及判定要求按表1的规定。
表1 非透明注塑件外观缺陷划分及判定零件类别Ⅰ类Ⅱ类Ⅲ类缺陷项目第一类:长条状缺陷 (包括:长条收缩痕、气纹、色纹、银纹、顶白等。
)不允许存在明显可见的该类缺陷。
各卡扣、螺钉柱等连接部位和四周转角处不允许存在顶白(发白)。
1. 允许存在不明显的 熔接痕,其长度不超过20mm;2. 不得有长度超过 25mm的气纹和明显的长条状收缩痕、色纹、顶白等。
3. 各卡扣、螺钉柱等连接部位和四周转角处不允许存在明显顶白(发白)。
1. 不允许存在严重的熔接 痕(有明显手感); 2.气纹收缩痕的长度不超 过50mm。
3. 收缩痕的深度不影响其 性能与使用,允许轻微顶白(顶白≤4mm×4mm)。
4. 各卡扣、螺钉柱等连接部 位和四周转角处不允许存在明显顶白(发白)。
第二类:点状缺陷(黑点、亮点、气泡、点状收缩痕等。
) 1. 每两点点状缺陷间的距离≥100mm。
2. 点状收缩痕应不明显,且 不能在产品的可见表面出现。
3.黑点、亮点直线距离≤500mm;分散的直径≤0.5Ф≤0.9mm的点状缺陷,其数量不得超过二个。
4.黑点、亮点两点之间距离≤200mm的直径Φ≤0.5mm的点状缺陷,1. 黑点、亮点的直径Φ≤1.0mm,且每件点状缺陷总点数不得超过三点。
2.每两点间距≥120mm。
3.允许存在轻微点状 收缩(及手模有轻微手感)。
1. 黑点、亮点直径Φ≤ 2mm,且每件点状缺陷的总点数不得超过五点。
2. 不得存在严重点收缩(长 度≤50mm。
其数量不得超过三点。
5. 黑点、亮点两点之间距离 ≥200mm,分散的直径Φ≤0.5mm的点状缺陷,其数量不得超过五点。
第三类:机械损伤(划痕、擦伤、拉伤等。
) 不允许存在轻微的机械损伤。
每件产品上轻微的机械损伤不多于三条,其长度≤20mm,间距≥250mm。
每件产品上轻微的机械损伤不多于五条,其长度≤30mm,间距≥250mm。
第四类:弯曲变形 变形量以不影响装配、使用性能及外观为标准,500mm≤1.5mm。
第五类:应力微裂纹表面(拐角)应无明显的应力微裂纹(应在自然光(光源充足)的条件下目测)。
注1:不明显收缩痕:是指用手摸收缩处无明显凹凸感且在垂直于工件表面顺光目测时不明显。
注2:轻微机械损伤:是指目测时可以明显看见。
注4:对不易判定的外观缺陷(不影响使用性能)可采用封样件的形式进行判定。
1.11 结构尺寸 应符合图纸技术要求。
1.12 阻燃性要求 有阻燃要求的塑料零部件其阻燃性等级应符合相应技术条件要求。
六、检验方法说明色差值以色差仪的测量值为准。
(精度±0.1)。
各类注塑件的检验要求,主要针对产品的外观正面。
背面及其它表面的外观质量可适当降低,但应以不影响产品外观、装配及使用性能为原则。
1.13 透明注塑件 零件颜色要求在自然光下(不允许在阳光直射下及鲜艳颜色的背景下)与标准色板或样板进行比较;表面光洁度和透明度检验可在同一光源下与标准色板或样板比较;对允许存在的缺陷检验时,要求肉眼距离零件表面200mm处顺光进行。
1.14 非透明注塑件 外观质量目视检验时应光源充足,必须垂直于工件表面且顺光检测,产品与眼睛垂直距离为400mm。
1.15喷涂件,电镀件同非透明注塑件。
七、检验规则本规则的检验适用于注塑件成型入库、外协件入库抽检和成品出厂检验。
1.16 进货检验 每批进行检验。
检验项目、标准要求、检验方法、质量特性、不合格(缺陷)程度描述、不合格(缺陷)类别、编码、抽样方案、缺陷代号按表2规定,其中检验项目为表2中的序号1~18项。
1.17对新确认厂家首批物料使用时,需要按照检验标准进行进货检验型式试验和检验。
(全检)并出具首件样品报告单。
1.18 出厂检验 出厂检验的检验项目、标准要求、检验方法、质量特性、不合格(缺陷)程度描述、不合格(缺陷)类别、缺陷代号、编码、抽样方案按表2规定,其中检验项目为表2中的序号3、6、7、8、9、10、11、12、14、15、16、17、18项。
抽样判定按引用标准执行。
表2 成型检验、外协检验、出厂检验项目、要求、不合格(缺陷)分类及编码检验项目属性序号检验项目标准要 求的章条号检验方法质量特性不合格(缺陷)程度描述不合格(缺陷)类别不合格(缺陷)编码抽样方案代号类别1 标志1 标志7.1目测C标志欠缺或内容与实物不符B标志书写模糊或无法辨认B标志印刷模糊但可以辨认D2包装2包装7.2目测B无破损,实物相符,包括型号、规格、数量B内馐严格按作业指导书执行C3一般要求3印刷图案4.1.1目测 C内容不符或无法辨认,有B明显脱落现象4熔接痕4.1.2D有明显的熔接痕出现D5凹缺 4.1.3D对装配、结构及外观产生严重影响B对装配、结构及外观产生一般影响C对装配、结构及外观产生轻微影响D6飞边 4.1.4D对装配、结构及外观产生严重影响B对装配、结构及外观产生一般影响C对装配、结构及外观产生轻微影响D7装配质量4.1.5B注塑组装件装配错误或无法装配B注塑组装件配合部位有卡死、松脱C注塑组装件间隙不均匀D4透明注塑件外观8颜色 4.2.1 5.1C颜色与标准色板或样板严重不符合B颜色与标准色板或样板一般不符合C颜色与标准色板或样板轻微D不符合9表面光洁度4.2.2C表面光洁度与样板严重不符合B表面光洁度与样板一般不符合C表面光洁度与样板轻微不符合D10透明度4.2.3 5.1C与样板透明度比较偏差较大B与样板透明度比较偏差一般C与样板透明度比较偏差较小D11外观缺陷4.2.4C外观缺陷与规定要求严重不符B外观缺C陷与规定要求一般不符外观缺陷与规定要求轻微不符D5非透明注塑件外观12零部件颜色4.3.15.2C与标准色板相比色差偏差较大B与标准色板相比色差偏差一般C与标准色板相比色差偏差微小D13光洁度4.3.3C表面光洁度与要求严重不符合B表面光洁度与要求一般不符合C表面光洁度与要求轻微不符合D14外观缺陷长条状缺陷4.3.4C有明显可见长条收缩痕、气纹、色纹、银纹或顶白C有明显的长条状收缩痕、熔接痕、色纹、顶白或长度大于15mm的气纹C有严重的熔接痕、顶白或气纹收缩痕大于50mm,或收缩痕的深度影响性能与使用C点状缺陷C不符合规定要求C机械损伤C有明显的划伤、拉伤或擦伤等C不符合规定要求C划伤、擦伤或拉伤等严重C弯曲变形C严重变形,影响装配及使用C一般变形C6结构尺寸15结构尺寸4.4量测C结构尺寸严重超差B结构尺寸一般超差C结构尺寸轻微超差D7阻燃16阻燃性4.5阻燃试验B阻燃性不符合B性规定要求。