刀柄系统
(整理)刀柄系统种类规格培训

加工中心的主轴锥孔通常分为两大类,即锥度为7:24的通用系统和1:10的HSK真空系统。
7:24锥度的通用刀柄锥度为7:24的通用刀柄通常有五种标准和规格,即NT(传统型)、DIN 69871(德国标准)、IS0 7388/1 (国际标准)、MAS BT(日本标准)以及ANSI/ASME(美国标准)。
NT型刀柄德国标准为DIN 2080,是在传统型机床上通过拉杆将刀柄拉紧,国内也称为ST;其它四种刀柄均是在加工中心上通过刀柄尾部的拉钉将刀柄拉紧。
目前国内使用最多的是DIN 69871型(即JT)和MAS BT 型两种刀柄。
DIN 69871型的刀柄可以安装在DIN 69871型和ANSI/ASME主轴锥孔的机床上,IS0 7388/1型的刀柄可以安装在DIN 69871型、IS0 7388/1 和ANSI/ASME主轴锥孔的机床上,所以就通用性而言,IS0 7388/1型的刀柄是最好的。
(1)DIN 2080型(简称NT或ST)DIN 2080是德国标准,即国际标准ISO 2583 ,是我们通常所说NT型刀柄,不能用机床的机械手装刀而用手动装刀。
(2)DIN 69871 型(简称JT、DIN、DAT或DV)DIN 69871 型分两种,即DIN 69871 A/AD型和DIN 69871 B型,前者是中心内冷,后者是法兰盘内冷,其它尺寸相同。
(3)ISO 7388/1 型(简称IV或IT)其刀柄安装尺寸与DIN 69871 型没有区别,但由于ISO 7388/1 型刀柄的D4值小于DIN 69871 型刀柄的D4值,所以将ISO 7388/1型刀柄安装在DIN 69871型锥孔的机床上是没有问题的,但将DIN 69871 型刀柄安装在ISO 7388/1型机床上则有可能会发生干涉。
(4)MAS BT 型(简称BT)BT型是日本标准,安装尺寸与DIN 69871、IS0 7388/1 及ANSI 完全不同,不能换用。
刀柄培训讲义课件

HSK 其他专用
• 莫氏锥孔 • 其他形式
DIN 2080
ISO 标准锥度刀柄
无机械手卡槽 无防错功能 带圆柱形尾部 带拉紧螺栓孔
NT 柄主要尺寸
MAS 403 - BT
JIS标准锥度刀柄
带机械手卡槽 无防错功能 带拉钉螺栓孔 内冷却孔方式可选
BT 柄主要尺寸
DIN 69871
运 动 范 围
第二讲 镗刀杆
镗孔加工
•镗孔精度与机床精度 •镗孔深度与系统刚性 •前道工序的影响 •镗孔加工适用情况
粗镗
单刃镗刀 双刃镗刀
平衡性能 等高、等径 错齿
各种精镗刀杆
精镗
微调单元
精镗刀杆
锥度标准
带机械手卡槽 带防错功能 带拉钉螺栓孔 内冷却孔方式可选
SK 柄主要尺寸
CAT 柄主要尺寸
DIN 69893 HSK
短锥标准
HSK 主要尺寸
刀柄的装卸
•换刀自动化 •刀库 •机械手
加工中心刀库
加工中心自动换刀
课间休息
二. 刀具连接部分形式
• 外圆柱形
光滑、平削边、斜削边
• 外圆锥形
精度
5μm
侧固式铣刀柄
夹持力大 适用 粗铣
粗镗
削边柄
DIN 1835 斜削边
二段平削边
平削边
液压刀柄
热装刀柄
莫氏锥柄刀具的连接
带扁尾 无扁尾
带扁尾 莫氏锥柄标准尺寸
无扁尾 莫氏锥柄标准尺寸
面铣刀柄
面铣刀和套式面铣刀 公(米)制和英制 定心圆柱和传力键
其他形式刀柄
▪ 攻丝刀柄 ▪ 延长杆 ▪ 快换接柄 ▪ 模块式刀柄 ▪ 专机主轴结构 ▪ 专利连接结构 ▪ ……
刀柄知识——精选推荐
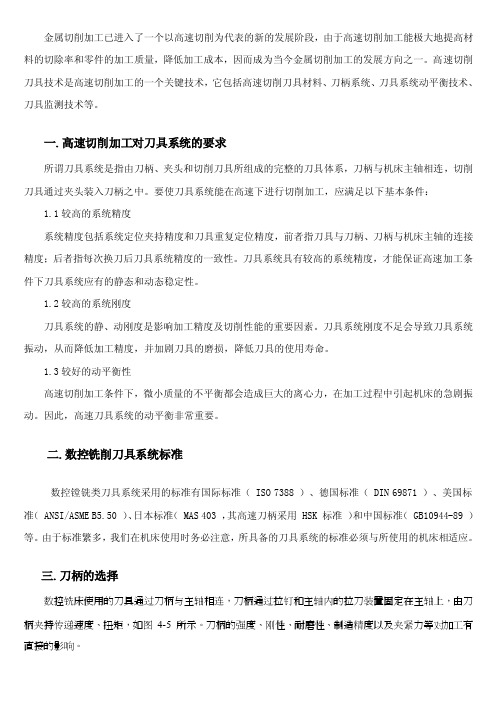
金属切削加工已进入了一个以高速切削为代表的新的发展阶段,由于高速切削加工能极大地提高材料的切除率和零件的加工质量,降低加工成本,因而成为当今金属切削加工的发展方向之一。
高速切削刀具技术是高速切削加工的一个关键技术,它包括高速切削刀具材料、刀柄系统、刀具系统动平衡技术、刀具监测技术等。
一.高速切削加工对刀具系统的要求所谓刀具系统是指由刀柄、夹头和切削刀具所组成的完整的刀具体系,刀柄与机床主轴相连,切削刀具通过夹头装入刀柄之中。
要使刀具系统能在高速下进行切削加工,应满足以下基本条件:1.1较高的系统精度系统精度包括系统定位夹持精度和刀具重复定位精度,前者指刀具与刀柄、刀柄与机床主轴的连接精度;后者指每次换刀后刀具系统精度的一致性。
刀具系统具有较高的系统精度,才能保证高速加工条件下刀具系统应有的静态和动态稳定性。
1.2较高的系统刚度刀具系统的静、动刚度是影响加工精度及切削性能的重要因素。
刀具系统刚度不足会导致刀具系统振动,从而降低加工精度,并加剧刀具的磨损,降低刀具的使用寿命。
1.3较好的动平衡性高速切削加工条件下,微小质量的不平衡都会造成巨大的离心力,在加工过程中引起机床的急剧振动。
因此,高速刀具系统的动平衡非常重要。
二.数控铣削刀具系统标准数控镗铣类刀具系统采用的标准有国际标准( ISO 7388 )、德国标准( DIN 69871 )、美国标准( ANSI/ASME B5.50 )、日本标准( MAS 403 ,其高速刀柄采用 HSK 标准)和中国标准( GB10944-89 )等。
由于标准繁多,我们在机床使用时务必注意,所具备的刀具系统的标准必须与所使用的机床相适应。
三.刀柄的选择数控铣床使用的刀具通过刀柄与主轴相连,刀柄通过拉钉和主轴内的拉刀装置固定在主轴上,由刀柄夹持传递速度、扭矩,如图4-5 所示。
刀柄的强度、刚性、耐磨性、制造精度以及夹紧力等对加工有直接的影响。
常见刀柄如下图:1.传统刀柄标准7/24锥联结目前,在数控铣床、数控镗床和加工中心上使用的传统刀柄是标准7:24锥度实心长刀柄。
山特维克-刀柄系统 共41页

刀柄系统 – 刀具夹持
弹簧夹头
/April 20, 2006
29
刀柄系统 – 刀具夹持
三爪夹头
/April 20, 2006
30
刀柄系统 – 刀具夹持
侧压夹头
/April 20, 2006
31
几种夹持方式测量径跳比
——长径比为3的验棒头部径跳
CoroGrip液压夹头 Runout 0.003-0.006mm
山特维克可乐满 大中华区效率中心
金属切削基础及刀具应用
---刀柄系统
/1
1
刀柄系统
/April 20, 2006
刀柄系统组成 机床主轴接口形式 刀具接口形式 夹紧形式 中间接杆 模块化刀具 刀具夹持 组装工具 常见的配刀限制
2
刀柄系统 – 组成
机床主轴
7:24定位锥面
9
刀柄系统 – 机床主轴的接口形式
HSK接口
使用者可以按如下方面进行选择: HSK A和C 型 :适度中等的扭矩,中等或 高速的主轴转速; HSK B和D 型 :扭矩刚性最大,中等或高 速的主轴转速; HSK E和F 型 :低的扭矩刚性,但主轴转 速允许极高。 HSK刀柄最关键的不在于制造精度,而在于严 格的钢材质和热处理标准
Hydro-Grip 精密夹头 Runout 0.003 - 0.008mm
Weldon/Whistle Notch 夹柄 Runout 0.01 - 0.03mm
弹簧夹套 Runout 0.03-0.06mm
/April 20, 2006
32
刀柄系统 – 刀具夹持
丝锥夹头
/April 20, 2006
HSK刀柄工作原理及常见问题分析

作就可以解决问题,这个问题就不展开说明。但
是,液压装置漏油绝大部分都是非常缓慢,不能够
很直观地发现问题所在,影响问题查找,造成长时
间的停机。建议通过以下方法来对设备进行验证:
首先,手动按动卸刀按钮,如果无法顺利拆
卸,请不要急于放弃,反复按动设备拆刀按钮,待
刀杆可以顺利拆下来。再一次把刀杆安装到设备上
油不会有明显的缺少,所以刀杆在第一次可以拆卸
之后,短时间内不会再出现抱死现象。传动装置如
图6所示。
图6 传动装置
3. 结语 通过HSK特点及原理的了解,更直观分析刀柄 使用中出现问题,提高分析能力,缩短问题处理时 间,为车间争取更多生产机会。
(收稿日期:20121207)
冷加工
47 2013年 第7期
L=l(1+at) V=v(1+bt) 式中,a为线膨胀系数;b为体膨胀系数;l与v是固 体在0℃时的长度与体积;t为温度。 出现这种现象,请不要急于拆刀,在设备停止 加工的状态下,等待一段时间,刀具自然冷却或人 为冷却后,刀杆就能够顺利的拆卸。 (2)刀柄与设备联接系统 刀柄和主轴的状 态对设备的加工影响非常大,刀杆和主轴的状态不 好不仅会引起无法精确定位,更会导致刀杆“抱 死”在设备主轴上面。例如,在刀杆定位面上有划 痕或者磕碰的高点、主轴孔上面有毛刺等现象,刀 具夹紧系统装夹过程中会出现刀杆定位面的局部高 点提前和设备主轴接触,定位装置受力不均匀,很 容易造成卡爪失效,严重时造成刀柄与主轴“抱 死”,无法拆卸。 所以,在实际生产中,一定做好刀柄和主轴孔 的保养和维护。刀具运送过程中,不能与工作台和 运送小车直接接触,要有完好的橡胶或者泡沫垫垫 在刀具放置的位置,保证刀具在发生磕碰的时候, 被碰物体的硬度要远远小于刀杆硬度;在刀具安装 到设备之前,要做好清洁和修整工作,用干净的无 纺布擦拭刀具和设备主轴的定位面,然后用油石打 磨刀杆和主轴有异常的位置,并辅助使用压缩空气 枪清洗干净。卡爪系统内部结构如图5所示。 (3)设备控制系统 液压装置也是直接影响 刀具难拆的重要因素之一,但检查比较复杂,需要
刀柄系统和拉钉

刀柄系统和拉钉刀柄系统和拉钉加工中心的主轴锥孔通常分为两大类:即锥度为7:24的通用系统和1:10的锥柄系统。
一. 1:10的锥柄系统。
1:10的锥柄系统有几种,比较有影响的有德国的HSK真空刀柄(标准DIN69873)和一些大的公司的企业标准与日本的NC5实心刀柄。
HSK真空刀柄靠刀柄的弹性变形,不但刀柄的1:10锥面与机床主轴孔的1:10锥面接触,而且使刀柄的法兰盘面与主轴面也紧密接触,1∶10空心工具锥柄目前已有国家标准GB19449.1-2004(带有法兰接触面的空心圆锥接口第1部分:柄部—尺寸)。
它等同采用了国际标准ISO12164-1:2001的内容。
原德国标准DIN69893-1:1996已被新的标准DIN69873-1:2003代替,新的德国标准也等同采用了国际标准ISO12164-1:2001的内容。
其它常见结构的1∶10工具锥柄基本采用企业标准,具有垄断性,如美国肯纳公司的KM型系列、瑞典山特维克公司的Capto 系列、德国瓦尔特公司的NOVEX系列等。
这种双面接触系统在高速加工、连接刚性和重合精度上均优于7:24的通用刀柄系统,但也有其缺点,如加工困难、刀具悬伸大而影响刀具刚性、刀柄重磨困难等。
日本的NC5刀柄采用的是实心结构。
二.7:24的通用系统。
锥度为7:24的通用刀柄通常有四种国际标准和规格:IS0 7388/1-1983(E)(等同于DIN69871.A和GB/T10944-1989);DIN 69871(德国标准);ANSIB5.50CAT(美国标准);MAS403BT(日本标准)。
1).IS0 7388/1-1983(E)(等同于DIN69871.A和GB/T10944-1989):该标准的刀柄的国内代号是JT,如JT30、JT40、JT50等。
中国国家标准GB10944-89是参照采用国际标准ISO88/1:1983制定的,除对极个别项目数据进行了圆整(如尾部螺纹底孔深度13)或未规定数据(如法兰上的键槽根底倒角)外,其它数据完全相同。
数控刀柄知识
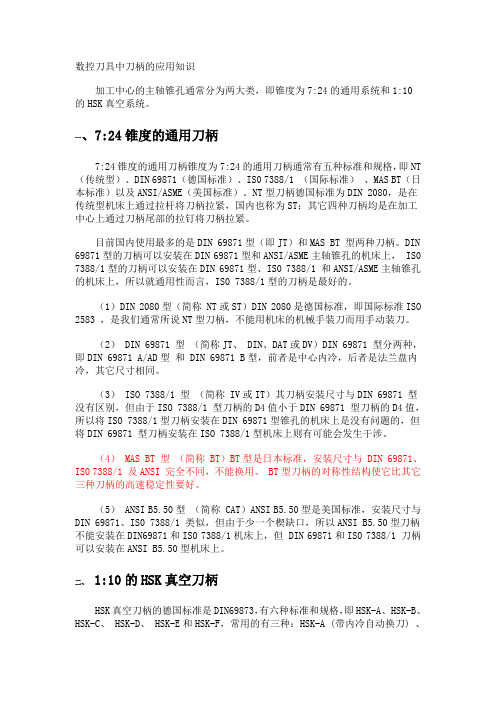
数控刀具中刀柄的应用知识加工中心的主轴锥孔通常分为两大类,即锥度为7:24的通用系统和1:10的HSK真空系统。
一、7:24锥度的通用刀柄7:24锥度的通用刀柄锥度为7:24的通用刀柄通常有五种标准和规格,即NT (传统型)、DIN 69871(德国标准)、IS0 7388/1 (国际标准)、MAS BT(日本标准)以及ANSI/ASME(美国标准)。
NT型刀柄德国标准为DIN 2080,是在传统型机床上通过拉杆将刀柄拉紧,国内也称为ST;其它四种刀柄均是在加工中心上通过刀柄尾部的拉钉将刀柄拉紧。
目前国内使用最多的是DIN 69871型(即JT)和MAS BT 型两种刀柄。
DIN 69871型的刀柄可以安装在DIN 69871型和ANSI/ASME主轴锥孔的机床上, IS0 7388/1型的刀柄可以安装在DIN 69871型、IS0 7388/1 和ANSI/ASME主轴锥孔的机床上,所以就通用性而言,IS0 7388/1型的刀柄是最好的。
(1)DIN 2080型(简称 NT或ST)DIN 2080是德国标准,即国际标准ISO 2583 ,是我们通常所说NT型刀柄,不能用机床的机械手装刀而用手动装刀。
(2) DIN 69871 型(简称JT、 DIN、DAT或DV)DIN 69871 型分两种,即DIN 69871 A/AD型和 DIN 69871 B型,前者是中心内冷,后者是法兰盘内冷,其它尺寸相同。
(3) ISO 7388/1 型(简称 IV或IT)其刀柄安装尺寸与DIN 69871 型没有区别,但由于ISO 7388/1 型刀柄的D4值小于DIN 69871 型刀柄的D4值,所以将ISO 7388/1型刀柄安装在DIN 69871型锥孔的机床上是没有问题的,但将DIN 69871 型刀柄安装在ISO 7388/1型机床上则有可能会发生干涉。
(4) MAS BT 型(简称 BT)BT型是日本标准,安装尺寸与 DIN 69871、IS0 7388/1 及ANSI 完全不同,不能换用。
加工中心刀柄结构说明
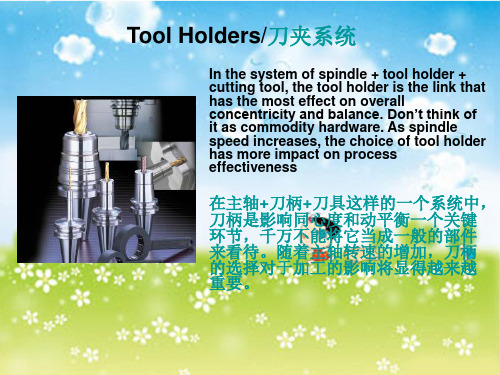
Balance & Concentricity/动平衡和同心度
It is also possible for a tool / tool holder system to be concentric but not balanced. A tool holder with a set screw is an example of this. Even if the tool holder holds the tool perfectly concentric, the weight of the screw itself would not be balanced. This tool holder will cause vibration when spun.
在主轴+刀柄+刀具这样的一个系统中, 刀柄是影响同心度和动平衡一个关键 环节,刀柄 的选择对于加工的影响将显得越来越 重要。
Two Face Contact & HSK holders/两面接触HSK刀柄
•Centrifugal force from fast spindle speeds can cause the tool holder to retract when the spindle and holder touch only along the taper.
动平衡的测量需要将刀具和刀柄整体进行。在主轴旋转时 好的动平衡刀柄和刀具结合不会产生任何的离心力。但是实际 上完全的动平衡是不存在的。在主轴旋转时动不平衡将产生周 期性的震动。如果动不平衡量很小,那么这种震动也会很微弱。
刀柄

标准目前主要标准有BT、SK、CAPTO、BBT、HSK等几种规格的主轴型号。
BT,BBT,均为日本标准,现也是普遍使用的一种标准。
SK(DIN6987)德国标准传统刀柄,有ER型,强力型,侧固型,平面铣刀型,钻夹头,莫氏锥柄现代有液压刀柄,热胀刀柄,PG(冷压)型。
HSK刀柄简介在高速切削加工已成为机械加工制造技术重要的环节。
传统的BT刀具系统的加工性能已难以满足高速切削的要求。
目前高速切削应用较广泛的有德国的HSK (德文Hohl Shaft Kegel缩写)刀具系统、美国的KM 刀具系统、日本的NC5、BIG-PLUS刀具系统等以上皆属于两面拘束刀柄。
而刀具系统能在高速下进行切削加工,应满足以下基本条件:1. 较高的系统精度系统精度包括系统定位夹持精度和刀具重复定位精度,前者指刀具与刀柄、刀柄与机床主轴的连接精度;后者指每次换刀后刀具系统精度的一致性。
刀具系统具有较高的系统精度,才能保证高速加工条件下刀具系统应有的静态和动态稳定性。
2. 较高的系统刚度刀具系统的静、动刚度是影响加工精度及切削性能的重要因素。
刀具系统刚度不足会导致刀具系统振动,从而降低加工精度,并加剧刀具的磨损,降低刀具的使用寿命。
3. 较好的动平衡性高速切削加工条件下,微小质量的不平衡都会造成巨大的离心力,在加工过程中引起机床的急剧振动。
因此,高速刀具系统的动平衡非常重要。
二、HSK工具系统标准的制订从1987年开始,由德国阿亨工业大学机床实验室以及一些工具制造厂、机床制造厂、用户企业等30多个单位成立了专题工作组,在M.Weck 教授领导下开始了新型工具系统的研究开发工作。
经过第一轮研究,工作组于1990年7月向德国工业标准组织提交了「自动换刀空心柄」标准建议。
德国于1991年7月公布了HSK刀具系统的DIN标准草案,并向国际标准化组织建议制定相关ISO标准。
1992年5月,国际标准化组织ISOT/TC29(工具技术委员会)决定暂不制订自动换刀空心柄的ISO标准。
金属切削刀具基本知识

金属切削刀具基本知识 Last updated on the afternoon of January 3, 2021秦皇岛技师学院机械安装与维修系金属切削刀具基本知识郝赫(编)金属切削刀具基本知识1 金属切削的基本要素机械制造过程概述机器是由零件、组件、部件等组成的,一台机器的制造过程包含了从零件、部件加工到整机装配的全过程,这一过程可以用图1所示的系统图来表示。
首先,从图中可以看出机器中的组成单元是一个个的零件,它们都是由毛坯经过相应的机械加工工艺过程变为合格零件的,在这一过程中要根据零件的设计信息制订每一个零件的适当加工方法,加工成在形状、尺寸、表面质量等各方面都符合加工使用要求的合格零件。
其次,要根据机器的结构和技术要求,把某些零件装配成部件,部件是由若干组件、套件和零件在一个基准零件上装配而成的,部件在整个机器中能完成一定的、完整的功能,这种把零件和组件、套件装配成部件的过程称为部装过程。
部装过程是依据部件装配工艺,应用相应的装配工具和技术完成的,部件装配的质量直接影响整个机器的性能和质量。
最后,在一个基准零部件上把各个部件、零件装配成一个完整的机器,我们把零件和部件装配成最终机械产品的过程称为总装过程,总装过程是依据总装工艺文件进行的,在产品总装后,还要经过检测、试车、喷漆、包装等一系列辅助过程最终形成合格的产品,如一辆汽车就是经过这样的机械制造过程而生产出来的。
图1 机械制造过程的构成机械加工工艺系统从机械制造的整个过程来看,机器的最基本组成单元为零件,也就是首先要制造出合格的零件,然后组装成部件,再由零、部件装配成机器,因此,制造出符合要求的各种零件是机械加工的主要目的,而机械加工中绝大部分材料是金属材料,故机械加工主要是对各种金属进行切削加工。
零件的表面通常是几种简单表面如平面、圆柱面、圆锥面、球面、成形表面等的组合,而零件的表面是通过各种切削加工方法得到的,其中在金属切削机床上利用工件和刀具彼此间协调的相对运动切除被加工零件多余的材料,获得在形状、尺寸和表面质量都符合要求的这种加工方法称为金属切削加工。
KM刀具系统

KM刀具系统KM Tooling SystemsKM刀具系统QuickKMQuickKMKM 模块式刀具系统 HSK 刀柄Erickson 刀柄和夹头加工中心刀具机械附件综合产品在车床和加工中心上使用的产品Lathe and Machining Center ProductsQuick KM KM Manufacturing Locations Kingswinford, England Nabburg, GermanyDetroit, MI +改革者+刀具制造商+供应商+提高生产力的合作伙伴Kennametal 公司QuickKM材料材料的使用是肯纳公司工艺技术的核心通过“全球性”材料规范认证材料通过热处理(不是表面硬化) SAE 4340H13Hardness 48 -52 HRcQuick KMQuickKMé 3 个面接触é灵活和通用地夹持设计é高刚性和高精度é宽的尺寸范围和多种形式é针对车/镗/钻/铣设计é有经受高切削负载的能力KM 和其它产品比较The KM 锥面BESTQuickKM三个有效地接触面通过机械放大产生3倍到7倍地锁紧力密封结合(橡胶O型环) 以防止内部零件受污染The KM 结合方式QuickKM0,25 mm (.010“)KM -锁紧过程1) 未锁紧没有接触2) 未锁紧3) 锁紧QuickKM面和锥面上2点接触换刀V 型槽定位孔标准直径1:10锥度球型锁紧孔(锥部两侧)中心内冷孔高性能和自动平衡夹头KM Taper径向驱动槽(两侧相等的宽和深)QuickKM旋转刀具9铣削(circular)9钻削9镗孔,双头镗9精镗9铰9浮动夹头9攻丝旋转工件9车削9切槽9切断9镗孔9钻头机床配件:9带KM 形式的主轴KM -通用型的应用QuickKM端面-锥面接触系统硬度和刚性主要依靠:1) 标准直径的过盈量2) 后拉力后拉力Interference between gage diameters实际QuickKMTest conducted by Kennametal in Latrobe, PA在切向受力下的偏移量13在切向受力下的偏移量QuickKMQuickKMTest conducted by Kennametal in Latrobe, PA在切向受力下的偏移量和屈服扭矩在切向受力下的偏移量和屈服扭矩QuickKMQuickKMTest conducted by Kennametal -Hertel in Furth, Germany在切向受力下的偏移量QuickKMTest conducted by Kennametal -Hertel in Furth, Germany在切向受力下的偏移量QuickKMKM 3240506380100Maximum Tangential Load at std. F & C 7,1 KN (1,600 LBF)12,0 KN (2,700 LBF)22,2 KN (5,000 LBF)35,6 KN (8,000 LBF)53,4 KN (12,000 LBF)66,7 KN (15,000 LBF)System Torque Capacity 155 Nm (115 ft lbs)325 Nm (240 ft lbs)780 Nm (575 ft lbs)1530 Nm (1,130 ft lbs)2,800 Nm (2,100 ft lbs)4,200 Nm (3,100 ft lbs)Capto C5C6C817 KN (3,800 LBF)32 KN (7,200 LBF)54 KN (12,200 LBF)Quick KM。
刀柄系统的分类与选择
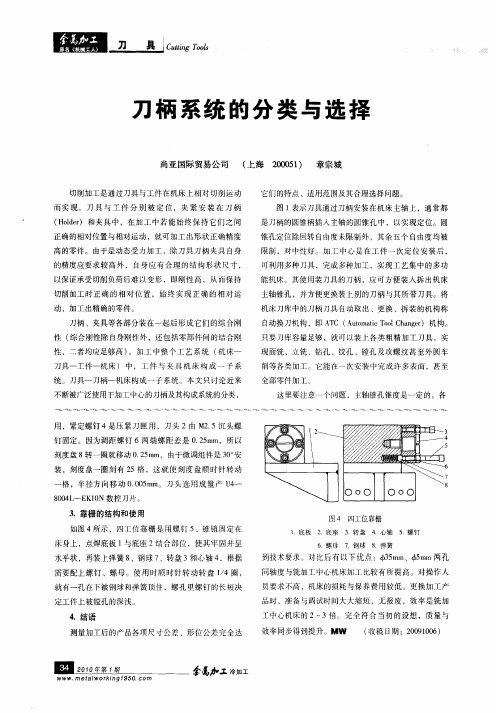
’
80 L E 1N数 控 刀 片 。 04 - K 0
o o o
1r
\
o o o
3 .靠栅的结构和使用
如图 4所示 ,四工位靠 栅是用 螺钉 5、锥销 固定 在
1 .底板
图4 四工位靠栅
2 .底座 3 .转盘 4 .心轴 5 螺 钉 .
床身上 ,点焊底板 1 与底座 2 结合部位 ,使其牢 固并 呈 水平状 ,再装上弹簧 8 、钢球 7 、转盘 3 和心轴 4 ,根据
■ I 。I I
刀 具 l tg t Ci un
 ̄ I
刀 柄 系统 的分 类 与 选 择
尚亚 国际贸易公司 ( 上海 20 5 ) 章宗城 0 0 1
切削加工是通过刀具与工件在机床上相对切 削运 动
它们 的特点 、适用范围及其合理选择问题 。 图 1表示刀具通过刀柄安装 在机床主轴上 ,通常都
现面铣 、立铣 、钻孑 、铰孔 、镗孔 及攻螺纹甚 至外 圆车 L
削等各类加工 。它能在一次安装 中完成许 多表面 ,甚 至
全 部 零件 加 工 。
不断被广泛使用于加工中心的刀柄及其构成系统的分类 ,
‘ … l 。
这里要注意一个问题 ,主紧刀 匣用 ,刀头 2由 M25沉头螺 . 钉 固定。因为调距 螺钉 6两端螺 距差 是 02 rm,所 以 .5 a
需要配上螺 钉 、螺母。使用 时顺时 针转动转 盘 14圈 , / 就有一孔在下被钢球 和弹簧顶住 ,螺孔里螺钉 的长短决
定工 件 上 被 镗孔 的深 浅 。
6 .螺母
7 .钢球
8 .弹簧
到技术要求。对比后有 以下 优点 :西 5 m bm 3 m 、( m两孔 5
机床结构和部件介绍
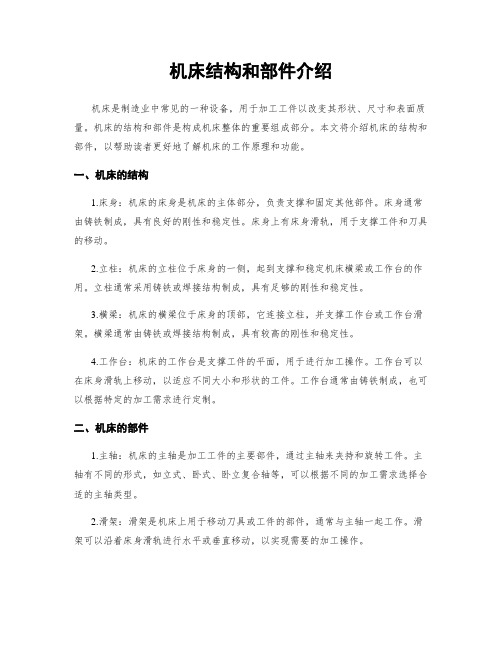
机床结构和部件介绍机床是制造业中常见的一种设备,用于加工工件以改变其形状、尺寸和表面质量。
机床的结构和部件是构成机床整体的重要组成部分。
本文将介绍机床的结构和部件,以帮助读者更好地了解机床的工作原理和功能。
一、机床的结构1.床身:机床的床身是机床的主体部分,负责支撑和固定其他部件。
床身通常由铸铁制成,具有良好的刚性和稳定性。
床身上有床身滑轨,用于支撑工件和刀具的移动。
2.立柱:机床的立柱位于床身的一侧,起到支撑和稳定机床横梁或工作台的作用。
立柱通常采用铸铁或焊接结构制成,具有足够的刚性和稳定性。
3.横梁:机床的横梁位于床身的顶部,它连接立柱,并支撑工作台或工作台滑架。
横梁通常由铸铁或焊接结构制成,具有较高的刚性和稳定性。
4.工作台:机床的工作台是支撑工件的平面,用于进行加工操作。
工作台可以在床身滑轨上移动,以适应不同大小和形状的工件。
工作台通常由铸铁制成,也可以根据特定的加工需求进行定制。
二、机床的部件1.主轴:机床的主轴是加工工件的主要部件,通过主轴来夹持和旋转工件。
主轴有不同的形式,如立式、卧式、卧立复合轴等,可以根据不同的加工需求选择合适的主轴类型。
2.滑架:滑架是机床上用于移动刀具或工件的部件,通常与主轴一起工作。
滑架可以沿着床身滑轨进行水平或垂直移动,以实现需要的加工操作。
3.进给系统:进给系统用于控制机床上刀具或工件的进给速度和方向。
进给系统包括进给电机、进给轴和进给装置等。
通过调整进给系统,可以实现工件的不同加工要求,如进给速度、切削深度和进给方向等。
4.刀具系统:刀具系统包括刀柄、刀片和刀座等部件,用于安装和固定刀具。
刀具系统具有较高的刚性和稳定性,以实现精确的切削加工。
5.润滑系统:润滑系统用于对机床运动部件和轴承等进行润滑,以减少磨损和摩擦。
润滑系统包括润滑油箱、润滑泵和润滑管路等部件,通过循环输送润滑油,保持机床的正常运行。
6.控制系统:控制系统是机床的重要组成部分,用于控制机床的加工过程。
山特维克可乐满 液压刀柄铣刀 刀柄介绍

0.01 -50% T,每增加0.01mm跳动刀具寿命减小50%
/25
表面质量
跳动对表面精度的影响
Profile depth
红色 = 差的 TIR 蓝色 = 好的 TIR
Surface - with and without run-out
TIR(径跳动)直接影响表面质量. TIR(径跳动)直接影响刀具寿命.
– 如果需要提供冷却液通过刀具中心请使用密封型夹套
CoroPak 09.2 - Internal information material - Hydro-Grip HD 19
Hydro-Grip® HD
技术特点/益处
低跳动 高夹持力
– 由于液压系统提供均匀的对称夹持刀具,从而确保了低的跳动量 (最大. 6 µm 在 3 x D处测得).
刀柄投资费用低于热涨式刀柄. 径跳动< 0.006 mm TIR, 从夹头端面3倍刀具直径悬伸处测得. 支持夹持任何形式的圆柱柄。例如,削平柄,惠氏等 圆柱柄为达到最佳的性能
/4
CoroGrip®笔形夹套
为型腔加工提高可达性
提高稳定性延长刀具寿命 – 可达4倍寿命提 高
/9
CoroGrip® 圆柱夹套
两种设计适用于铣削和钻削
狭窄型 393.CG
狭缝型 393.CG
密封型 393.CGS
密封型 393.CGS
/11
CoroGrip® HMS 型
为重载铣削减小刀具悬伸 有效抵抗径向力和振动 可夹持圆柱柄, 削平柄或惠氏削平柄刀
具 特别适用密齿整体硬质合金铣刀加工淬
硬材料(HRC42 以上)
– 提高工件表面质量 – 为了达到最低的跳动精度推荐使用圆柱直柄刀具,h6和h7级柄部精度 – 每增加 10 µm 刀具跳动, 刀具寿命减少50%.
KM刀具系统
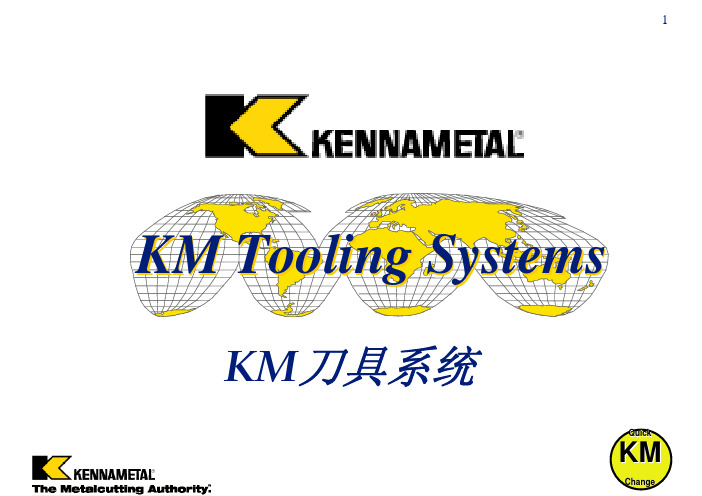
KM Tooling SystemsKM刀具系统QuickKMQuickKMKM 模块式刀具系统 HSK 刀柄Erickson 刀柄和夹头 加工中心刀具 机械附件 综合产品在车床和加工中心上使用的产品Lathe and Machining Center ProductsQuick KM KM Manufacturing LocationsKingswinford, England Nabburg, GermanyDetroit, MI +改革者+刀具制造商+供应商+提高生产力的合作伙伴Kennametal 公司QuickKM材料材料的使用是肯纳公司工艺技术的核心通过“全球性”材料规范认证材料通过热处理(不是表面硬化)SAE 4340H13Hardness 48 -52 HRcQuick KMQuickKMÉ 3 个面接触É灵活和通用地夹持设计É高刚性和高精度É宽的尺寸范围和多种形式É针对车/镗/钻/铣设计É有经受高切削负载的能力KM 和其它产品比较The KM 锥面BESTQuickKM三个有效地接触面通过机械放大产生3倍到7倍地锁紧力 密封结合(橡胶O型环) 以防止内部零件受污染The KM 结合方式QuickKM0,25 mm (.010“)KM -锁紧过程1) 未锁紧没有接触2) 未锁紧3) 锁紧QuickKM面和锥面上2点接触换刀V 型槽定位孔标准直径1:10锥度球型锁紧孔(锥部两侧)中心内冷孔高性能和自动平衡夹头KM Taper径向驱动槽(两侧相等的宽和深)QuickKM旋转刀具9铣削(circular)9钻削9镗孔,双头镗9精镗9铰9浮动夹头9攻丝旋转工件9车削9切槽9切断9镗孔9钻头机床配件:9带KM 形式的主轴KM -通用型的应用QuickKM端面-锥面接触系统硬度和刚性主要依靠:1) 标准直径的过盈量2) 后拉力后拉力Interference between gage diameters实际QuickKMTest conducted by Kennametal in Latrobe, PA在切向受力下的偏移量13在切向受力下的偏移量QuickKMQuickKMTest conducted by Kennametal in Latrobe, PA在切向受力下的偏移量和屈服扭矩在切向受力下的偏移量和屈服扭矩QuickKMQuickKMTest conducted by Kennametal -Hertel in Furth, Germany在切向受力下的偏移量QuickKMTest conducted by Kennametal -Hertel in Furth, Germany在切向受力下的偏移量QuickKMKM 3240506380100Maximum Tangential Load at std. F & C 7,1 KN (1,600 LBF)12,0 KN (2,700 LBF)22,2 KN (5,000 LBF)35,6 KN (8,000 LBF)53,4 KN (12,000 LBF)66,7 KN (15,000 LBF)System Torque Capacity 155 Nm (115 ft lbs)325 Nm (240 ft lbs)780 Nm (575 ft lbs)1530 Nm (1,130 ft lbs)2,800 Nm (2,100 ft lbs)4,200 Nm (3,100 ft lbs)Capto C5C6C817 KN (3,800 LBF)32 KN (7,200 LBF)54 KN (12,200 LBF)Quick KMQuickKM2.3.2 1/2 圈旋转从侧面或顶端来锁紧KM-LOC ™140 度手动锁紧使用蝶形弹簧自动或半自动夹持QuickKMKM 针对车床的夹持系统•手动和自动系统•KM-LOC 140º锁紧•VDI 柄•法兰装夹•方柄•圆柄KM针对车床的夹持系统手动方式2 1/2 圈旋转锁紧需要扭距设定QuickKMQuickKMKM-LOC™KM -LOC ™车床刀具 仅仅140º旋转就能锁紧和放松 专利设计提供了简易的安装 实际上不用维护QuickKM140°夹持Defined start & end-position:ÖUnclamped ÖClamped5°140°ClampUser friendly, NO torque wrench required Wrench force required:•KM32 = 25 Nm •KM40 = 35 Nm •KM50 = 50 Nm •KM63 = 50 NmClamped刀具中心超精调整通过一个特殊的螺钉来调整刀具中心高度.(这个特殊螺钉必须特别订购)QuickKMQuickKMOnly the disc springsare pre-loaded, NOT components.锁紧位置The spring force works in addition to the self-locking cam feature of the KM-LOC.KM-LOC™KM -LOC ™技术特征QuickKM维护涂脂于夹持零部件:•12个月维护一次(3200 次装夹)•维护无需将刀具拆开•降低摩擦力•增加零部件寿命•在标准包装内已配备了所有必需品•Gleitmo 805K 润滑油KM-LOC™KM -LOC ™技术特征KM 针对车床的夹持系统A自动和半自动系统A夹持其实就是利用蝶形弹簧或液压力QuickKMKM 针对加工中心的刀具一套完整的刀柄系统有CV, BT & DIN标准柄KM 刀具允许在车床和加工中心之间进行灵活地互换QuickKMQuickKMKM 夹持系统•dual position blocks •extended reach •increased setback •designs for custom turrets•industry’s best tooling application engineersQuick KMQuickKMKM32= 25 Nm KM40= 35 Nm KM50= 50 Nm KM63= 50 NmC3=35NmC4=50Nm C5=70Nm C6=90NmKM Vs CaptoSandvik CaptoKennametal KMQuickKM球型半自动锁紧 Internal machining-cutting units or boring bars 低的锁紧力Bolt or wedge type clamping Internal machining-only with dedicated boring bars 高的锁紧力-稳固性有问题KM™CaptoKM vsKM vs CaptoQuickKMKM Vs CaptoKM-LOC quick clamp with interlock Central coolant supply sealed with o-rings Multiple clamping unit designs-flange mounts, VDI, machine specific, automatic, square shank, extensions & reducers, specials… Reversed spindle rotation-position cutting unit 180ºQuick clamp-NO interlock Radial coolantsupply-NO sealing from contamination Limited standard clamping designs Reversed spindle rotation-only throughdisassembly of clamping unit.KM™CaptoQuickKMKMTMKM Vs CaptoPage 24CaptoQuickKMAssemblyTools RequiredC3=45Nm C4=55Nm C5=95Nm C6=170Nm C8=170NmKM Vs CaptoCaptoQuickKM•多边形锥度= 1:20•通过楔形块在内部中心夹紧•快速夹紧90°, 扭距设定•Rear clamp with central bolt•柱面锥度= 1:10•内部中心通过2个球来提供夹紧力•KM-LOC 140°度锁紧和放松•手动2 1/2圈锁紧KMTMCaptoQuickKM冷却液地供给冷却液放射状地通过锥部冷却液放射状地通过锥部冷却液地供给通过O 型环密封冷却液地供给通过O 型环密封KM Vs CaptoKMTMCaptoQuickKM内圆加工System ØKM32(44)KM4054KM5070KM6386KM80105System Ø D min KMTMInternal machining is only possibleby using EnlongationsorIntegral Boring BarsCaptoKM Vs CaptoQuick KMQuickKMKM 标准产品切削刀具Comprehensive range of cutting units in various KM sizes,lead angles, geometries, and insert clamping-Kenloc Pin M -Leverlock P -Wedgelock W -Screw-on S -Top Notch N -Thread & Groove N -LT Threading L -Deep Grooving GQuickKM60604343KM63KM6335355050KM50KM5040402727KM40KM4022223535KM32一套完整的车削刀具尺寸KM 标准产品刀具尺寸F dimensionl 1 d i m e n s i o nQuickKMKM 标准产品完整的镗刀杆一系列镗刀杆包括:•钢柄•硬质合金柄•长径比达14:1的镗刀(TUNED )镗刀形式有:•镗孔•螺纹•槽Quick KM! NEW !A range of DV and BT inlong design!KM 标准产品加工中心主刀柄ÉTaper shank 40, 45 and 50ÉDIN 69871, Form A and B ÉMAS BT Japanese taper shank ÉDIN 2080 taper 40 and 50ÉCAT 40 and 50Quick KM 接柄和接杆•Collet chucks•Collets-TG, ER & DA •Drill chucks •Tap chucks -rigid-tension/compression •Adapters -end mills -whistle notch -face mills -Morse taper-combi-type•hydraulic chucksKM 标准产品QuickKMDrill -Fix 钻头Indexable Drills •KM 32, 40 and 502 x d •KM 503 x d 直径范围:16 to 50 mmKM KM 标准产品标准产品QuickKMDriven Tools for:Okuma Mori Seiki Mazak HardingeNakamura Boehringer Gildemeister etc.KM 标准产品QuickKMSpecial Tools for:multiple proccessesdual pockets cartidgesextended reach etc.KM 特殊产品Designed and manufactured inQuick KMQuickKMKM63 KM LOCÎ7:1 机械效益Î刀夹允许使用者Cartridge design allows user to manufacture tool block at his option Î冷却液压力可达100 bar, 1500 psi Î最少的零部件新KM 产品。
- 1、下载文档前请自行甄别文档内容的完整性,平台不提供额外的编辑、内容补充、找答案等附加服务。
- 2、"仅部分预览"的文档,不可在线预览部分如存在完整性等问题,可反馈申请退款(可完整预览的文档不适用该条件!)。
- 3、如文档侵犯您的权益,请联系客服反馈,我们会尽快为您处理(人工客服工作时间:9:00-18:30)。
AP型直角高速铣刀
直径从¢10-¢50. 1刃到4刃 高刚性,高进给。 耐崩,耐磨。
采用高钢性工具钢,整体预硬后加工。
AP型直角高速铣刀
RD圆刃端铣刀
采用高钢性工具钢, 整体预硬后加工。
直径从¢12-¢50. 高刚性,高进给。 耐崩,耐磨。
RD圆刃端铣刀
粗,精加工用球刀
仿形加工。
模具的粗及半精加工用。
刀
镗
刀
小径精镗刀是通过更换前部刀杆和调整刀杆偏心获得调整直径目的的。 由于调整范围广,且可加工小径孔,所以在工、模具和产品的单件、小批 量生产中得以广泛的应用。 选择方法: a.确认机床接口 (选配刀柄形式例 BT40) b.确认工件结构、孔径、深度及材料等 c.选配镗刀调整头 d.选配刀头、刀杆(根据孔径、结构和孔深等) e.选配钨钢刀杆套筒(可选项,根据刀杆柄径) f. 选配刀柄 (注接口型号一致) g.选配刀片 (根据刀片座,工件材料) 特点: (1)通过更换不同的刀杆,可以加工φ2~φ50mm的 孔,可调范围大,所以成本较低; (2)对于长径比较大的孔,可采用钨钢防震刀杆进 行加工; (3)对于φ20以上的孔,其刚性和稳定性不如模块式 镗刀。
加热刀柄
优点:动平衡好,适合于高速 加工。重复定位精度高,一般 在0.002mm以内。夹紧力大, 支承好。径向跳动小,可达到 0.002mm-0.005mm.抗污能力 好。在加工中防干涉能力好。 缺点:可换性差,每种规格刀 柄只适安装一种柄径的刀具。 注意事项:需配置一套加热设 备。
电磁诱导加热器
HSK空心短圆锥工具系统
• 能够提高系统的刚性和稳定性以及在高速加工时的 产品精度,并缩短刀具更换的时间;
• 支持高速机械加工的运用;
• 刀柄供应商正在不断地改进HSK工具系统,使其适应 机床主轴转速达到60,000转/分;
• HSK工具系统正在被广泛用于航空航天、汽车、精 密模具等制造工业之中。
刀柄系统-锥柄形式
7:24工具锥柄的刀柄系统占所有加工中心 刀柄的80%以上; HSK工具系统能够提高系统的刚性和稳定 性以及在高速加工时的产品精度,并缩短刀 具更换的时间,在高速加工中发挥很重要 的作用。
刀柄系统-锥柄形式
7:24工具系统
HSK空心短圆锥工具系统
大锥度7:24 DIN 69871
7:24刀柄系统优缺点
缺点 1、单独的锥面定位。 7:24锥度刀柄连接锥度较大,锥柄较长,锥体表 面同时要起两个重要作用,即刀柄相对于主轴的精确定位以 及实现刀柄夹紧。 2、在高速旋转时,由于离心力的作用,主轴前端锥孔会发 生膨胀,膨胀量的大小随着旋转半径与转速的增大而增大, 但是与之配合的7:24锥度刀柄由于是实心的所以膨胀量较 小,因此总的锥度连接刚度会降低,在拉杆拉力的作用下, 刀柄的轴向位移也会发生改变。每次换刀后刀柄的径向尺寸 都会发生改变,存在着重复定位精度不稳定的问题。
强力型刀柄
功能:用于铣刀,铰刀等直柄刀具及 工具的夹紧。 优缺点:夹紧力比较大,夹紧精度较 好,更换不同的筒夹来夹持不同柄径 的铣刀,铰刀等。在加工过程中,强 力型刀柄前端直径要比弹簧夹头刀柄 大,容易产生干涉。 精度:卡簧夹紧变形小,所夹持的刀具 柄径公差在h6 注意事项:1,使用时务必将刀柄内孔 及卡簧擦干净,切误将油渍留于刀柄 中。夹紧时不应使用加长棍,野蛮锁 紧,以免损坏刀柄。 2,在加工过程中不要用柴 油直接冲在刀柄 上,这样很容易损坏 刀柄。
侧固式刀柄
功能:适合装夹快速钻、铣 刀、粗镗刀等削平刀柄 刀具 的装夹。 优缺点:侧固式刀柄是夹持 力度大,其结构简单,相对 装夹原理也很简单。但通用 性不好,每一种刀柄只能装 同柄径的刀具。 安装方法:将刀具置入刀柄 内,将削平平面对准锁紧螺 钉。
平面铣刀柄
功能:主要用于套式平面铣 刀盘的装夹,采用中间心轴 和两边定位键定位,端面内 六角螺丝锁紧。 注意事项:1,平面铣刀柄分 为公制跟英制,选取时应了 解铣刀盘内孔孔径。 2,在加工条件允 许情况下,为提高刚性应尽 量选取短一点。
镗刀的分类和用途
镗刀用于加工各类不同直径的孔,特 别是位置精度要求较高的孔和孔系。 镗刀的类型按功能可分为粗镗刀、精 镗刀;按切削刃数量可分为单刃镗刀、双 刃镗刀和多刃镗刀;按照工件加工表面特 征可分为通孔镗刀、盲孔镗刀、阶梯孔镗 刀和端面镗刀;按刀具结构可分为整体式, 模块式等。
镗
刀
粗镗刀:
粗镗刀应用于孔的半精加工。常用的粗镗刀按结构可分为 单刃、双刃和三刃,根据不同的加工场合,也有通孔专用和盲 孔加工; 1.单刃粗镗刀的选配方法:
相对稳定性较低 (会晃动) 轴向精度低 有限的径向精度 不适合于高转速 重量较大,换刀较慢 应用广泛
空心短锥 DIN 69893
高的静态及动态稳定性 高的轴向及径向精度 非常适合在高转速下使用,定心准确 重量轻,易于换刀
7:24刀柄系统优缺点
优点 1、不自锁,可以实现快速装卸刀具; 2、刀柄的锥体在拉杆轴向拉力的作用下, 紧紧地与主轴的内锥面接触 3、7:24锥度的刀柄在制造时只要将锥角 加工到高精度即可保证连接的精度,所以 成本相应比较低,而且使用可靠。
镗
刀
镗
2.模块式精镗刀的选择方法 模块式精镗刀即是将镗刀分为:基础柄、延 长杆、变径杆、镗头、刀片座、等多个部分,然 后根据具体的加工内容(粗镗、精镗;孔的直径、 深度、形状;工件材料等)进行自由组合。 选择方法: a.确认机床接口 (选配刀柄形式例: BT40) b.确认工件结构、孔径、深度及材料等 c.选配镗刀头 (根据孔径、结构等) d.选配刀柄和接杆 (根据孔深、注接口型号一 致) e.选配刀片 (根据刀片座,工件材料)
油路刀柄
功能:在没有中心出 水的机床,通过刀柄 内部机构将外部冷却 转为中心内冷。(在 没有中心出水机床上 使用快速钻,为了能 使铁屑能出来,就要 将外冷转成内冷。) 注意事项:安装前要 确认刀柄中心到进油 孔的距离。
角度头
功能:为了能在三轴的加 工叫心实现第四轴的加工。 工作原理:是通过机床主 轴带动角度头内的齿轮运 转传递力矩,从而实现角 度转换。 注意事项:安装原理跟油 路刀柄一样。使用时应注 意当机床正转时,角度头 是反转的,机床反转时, 角度头是正转的。
a.确认机床接口 (选配刀柄形式) b.确认工件结构、孔径、深度及材料等 c.选配刀杆 (根据孔径、孔深等) d.选配镗刀头 (根据刀杆前端的方孔) e.选配刀片 (根据刀片座,工件材料)
镗
刀
单刃粗镗刀
2.可调式双刃粗镗刀
a.确认机床接口(选配刀柄形式例: BT40) b.确认工件结构、孔径、深度及材料等 c.选配镗刀头 (根据孔径、结构等) d.选配刀柄和接杆 (根据孔深、注接口型号一致) e.选配刀片 (根据刀片座,工件材料)
7:24刀柄系统特点
主轴锥孔的“喇叭口”状扩张,还会引起刀柄及夹紧机构质心的偏离, 从而影响主轴动平衡。 轴向定位精度较低 高速时产生径向膨胀 锥柄的质量和长度比较大
没有端面接触
支持外径比较小
1.弹簧夹头刀柄
功能:主要用于钻头、铣刀、丝锥等直柄 刀具及工具的装夹。
卡簧弹性变形量1mm 夹持范围: φ0.5~φ32
双刃粗镗刀
精镗刀的用途及分类
精镗刀应用于孔的精加工场合,能获得较高的直径和位置精度和光洁 度。为了在孔加工中能获得更高的精度,一般精镗刀采用的都是单刃形式, 刀头带有微调结构,以获得更高的调整精度和调整效率。根据其结构,精 镗刀可分为整体式精镗刀、模块式精镗刀和小径精镗刀,均广范的使用于 数控铣床,镗床和加工中心上。 1.整体式精镗刀 的选择方法 整体式精镗刀主要用在批量产品的生产 线近些年来,市场结构、市场需要日新月异, 产品周期日益缩短,这就要求加工机械以及 加工刀具具有更充分的柔性。所以在实际应 用中,尽管其价格比较低廉,我们并不是十 分推荐。 选择方法: a.确认机床接口 (选配刀柄形式) b.确认工件结构、孔径、深度及材料等 c.选配镗刀 (根据孔径、孔深等) d.选配刀片 (根据刀片座,工件材料)
旋转刀具及配套应用
刀柄系统-加工中心刀具配置图
刀柄系统-锥柄形式
用于连接机床和切削用刀具的数控工具系统,具 有卡具的功能和量具的精度,直接关系到刀具是 否得到正确使用,切削是否达到理想效果的关键 因素所在。包括: 加工中心用7:24锥柄刀柄系统:包括BT、SK、 CAT、DIN等各种标准;NT在早期数控铣床上用的 较多。 加工中心用1:10锥柄HSK空心短圆锥高速模块式 工具系统;
弹簧夹套的精度
在4D处跳动在20μm以内为A级(普通级); 在4D处跳动在10μm以内为AA级(精密 级); 在4D处跳动在5μm以内为超级精密级;
弹簧夹头的装夹
钻夹头刀柄
功能:主要用于夹紧直柄钻头, 也可用于直柄铣刀、铰刀、丝 锥的装夹。 优缺点:夹持范围广,单款可 夹持多种不同柄径的钻头,但 由于夹紧力较小,夹紧精度低, 所以常采用于直径在¢16以下 的普通钻头夹紧。 注意事项:夹紧时要用专用扳 手夹紧,在加工时如受力过大, 很容易造成三爪断裂。
模具仿形精加工用。
采用高钢性工具钢,整体预硬后加 工。
面铣刀
可用于坡走铣和螺旋插补铣粗加工凹穴 方肩铣、90度平面铣
直径从¢50-¢300.
45度大平面铣削
2008.10.12
丝攻刀柄
功能:用于加工螺纹时的装夹, 伸缩攻牙刀柄通过内部的保护机 构可使前后收缩5mm,在丝锥过 载停转时起到保护作用。 注意事项:1,使用ER刚性攻牙 筒夹。 2,选择ER刚性攻牙 筒夹时必须确认好丝锥柄径和方 头的心寸。也可以告知客户使用 丝锥是什么标准。 3,锁紧时要用开口 扳手夹住刀柄,使用另一只板手 锁紧螺帽。不能野蛮锁紧。
莫式刀柄
分类:1,莫氏铣刀刀柄(MTB) 2,莫式钻头刀柄 (MTA) 功能:MTA适合于安装莫氏有扁尾的钻 头,铰刀及非标刀具。 MTB适合天安装莫氏无扁尾的 铣刀各非标刀具。 为了满足模具深型腔加工,MTB刀柄有 加长型跟超长型。 注意事项: 使用前务必将锥孔内清洗干净,保证无 油脂否则会影响磨擦力,导致刀具的 “夹紧力”的下降. 刀具不使用时应当及时将刀具卸下来, 长时间处与拉紧状态可能会导致刀具无 法拆卸的结果.