钢板弹簧制造工艺
汽车钢板弹簧
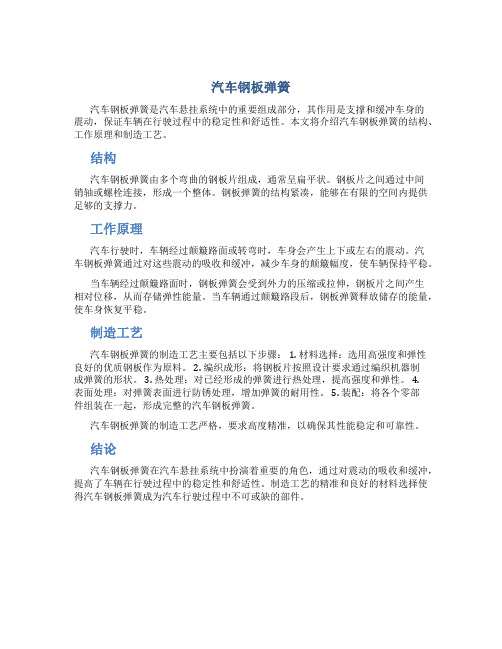
汽车钢板弹簧
汽车钢板弹簧是汽车悬挂系统中的重要组成部分,其作用是支撑和缓冲车身的
震动,保证车辆在行驶过程中的稳定性和舒适性。
本文将介绍汽车钢板弹簧的结构、工作原理和制造工艺。
结构
汽车钢板弹簧由多个弯曲的钢板片组成,通常呈扁平状。
钢板片之间通过中间
销轴或螺栓连接,形成一个整体。
钢板弹簧的结构紧凑,能够在有限的空间内提供足够的支撑力。
工作原理
汽车行驶时,车辆经过颠簸路面或转弯时,车身会产生上下或左右的震动。
汽
车钢板弹簧通过对这些震动的吸收和缓冲,减少车身的颠簸幅度,使车辆保持平稳。
当车辆经过颠簸路面时,钢板弹簧会受到外力的压缩或拉伸,钢板片之间产生
相对位移,从而存储弹性能量。
当车辆通过颠簸路段后,钢板弹簧释放储存的能量,使车身恢复平稳。
制造工艺
汽车钢板弹簧的制造工艺主要包括以下步骤: 1. 材料选择:选用高强度和弹性
良好的优质钢板作为原料。
2. 编织成形:将钢板片按照设计要求通过编织机器制
成弹簧的形状。
3. 热处理:对已经形成的弹簧进行热处理,提高强度和弹性。
4.
表面处理:对弹簧表面进行防锈处理,增加弹簧的耐用性。
5. 装配:将各个零部
件组装在一起,形成完整的汽车钢板弹簧。
汽车钢板弹簧的制造工艺严格,要求高度精准,以确保其性能稳定和可靠性。
结论
汽车钢板弹簧在汽车悬挂系统中扮演着重要的角色,通过对震动的吸收和缓冲,提高了车辆在行驶过程中的稳定性和舒适性。
制造工艺的精准和良好的材料选择使得汽车钢板弹簧成为汽车行驶过程中不可或缺的部件。
机械制造技术课程设计-前钢板弹簧吊耳加工工艺及钻2-10.5孔夹具设计(全套图纸)
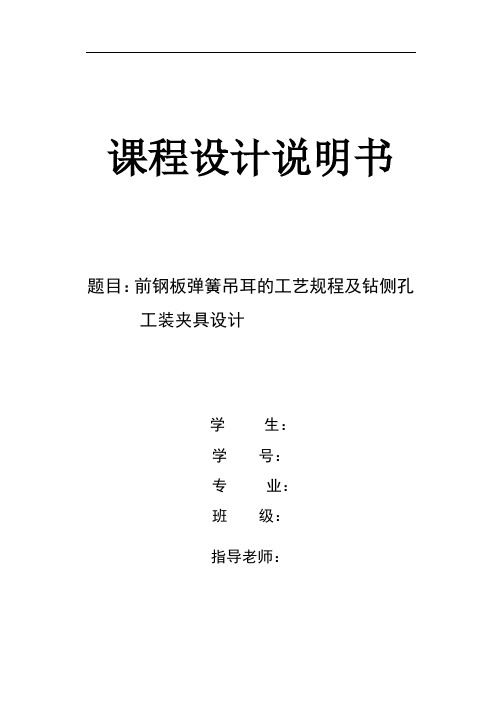
课程设计说明书题目:前钢板弹簧吊耳的工艺规程及钻侧孔工装夹具设计学生:学号:专业:班级:指导老师:摘要本次设计内容涉及了机械制造工艺及机床夹具设计、金属切削机床、公差配合与测量等多方面的知识。
吊耳前钢板弹簧加工工艺规程及其钻侧孔的夹具设计是包括零件加工的工艺设计、工序设计以及专用夹具的设计三部分。
在工艺设计中要首先对零件进行分析,了解零件的工艺再设计出毛坯的结构,并选择好零件的加工基准,设计出零件的工艺路线;接着对零件各个工步的工序进行尺寸计算,关键是决定出各个工序的工艺装备及切削用量;然后进行专用夹具的设计,选择设计出夹具的各个组成部件,如定位元件、夹紧元件、引导元件、夹具体与机床的连接部件以及其它部件;计算出夹具定位时产生的定位误差,分析夹具结构的合理性与不足之处,并在以后设计中注意改进。
关键词:工艺、工序、切削用量、夹紧、定位、误差。
全套图纸加153893706ABSTRCTThis design content has involved the machine manufacture craft and the engine bed jig design, the metal-cutting machine tool, the common difference coordination and the survey and so on the various knowledge.The reduction gear box body components technological process and its the processing hole jig design is includes the components processing the technological design, the working procedure design as well as the unit clamp design three parts. Must first carry on the analysis in the technological design to the components, understood the components the craft redesigns the semi finished materials the structure, and chooses the good components the processing datum, designs the components the craft route; After that is carrying on the size computation to a components each labor step of working procedure, the key is decides each working procedure the craft equipment and the cutting specifications; Then carries on the unit clamp the design, the choice designs the jig each composition part, like locates the part, clamps the part, guides the part, to clamp concrete and theengine bed connection part as well as other parts; Position error which calculates the jig locates when produces, analyzes the jig structure the rationality and the deficiency, and will design in later pays attention to the improvement.Keywords:The craft, the working procedure, the cutting specifications, clamp, the localization, the error目录序言 (1)一. 零件分析 (2)1.1 零件作用 (2)1.2零件的工艺分析 (3)二. 工艺规程设计 (4)2.1确定毛坯的制造形式 (4)2.2基面的选择传 (5)2.3制定工艺路线 (8)2.4机械加工余量、工序尺寸及毛坯尺寸的确定 (6)2.5确定切削用量及基本工时 (6)三夹具设计 (8)3.1问题的提出 (8)3.2定位基准的选择 (8)3.3切削力及夹紧力计算 (9)3.4定位误差分析 (11)3.5夹具设计及操作简要说明 (15)总结 (17)致谢 (18)参考文献 (19)序言机械制造业是制造具有一定形状位置和尺寸的零件和产品,并把它们装备成机械装备的行业。
钢板弹簧生产工艺

钢板弹簧生产工艺钢板弹簧是一种弹性元件,广泛应用于工业制造和机械设备中。
其主要特点是可以储存和释放能量,具有较高的弹性和耐久性。
下面介绍钢板弹簧的生产工艺。
第一步:原材料准备钢板弹簧的原材料主要是优质碳素钢板。
在生产过程中,需要根据弹簧的用途和要求选择适合的钢板。
钢板会经过切割、裁剪和修整等工艺,确保其大小和形状符合要求。
第二步:弯曲加工接下来,钢板将会经过弯曲加工。
弯曲加工是钢板弹簧生产中最重要的一步,它决定了弹簧的形状和性能。
弯曲加工可以通过机械加工方法或者热加工方法进行。
机械加工方法包括弯折、滚轧和冷弯等,而热加工方法主要是指热处理。
在弯曲加工过程中,需要根据设计要求将钢板进行弯曲、压缩和拉伸等操作,以形成所需形状和弹性。
第三步:热处理完成弯曲加工后,弹簧会经过热处理,以提高其强度和弹性。
热处理是通过加热和冷却来改变钢板的组织和性能的方法。
具体来说,弹簧会先被加热到一定温度,然后进行保温,最后快速冷却。
这样可以使钢板获得更均匀的组织结构和更好的弹性性能。
第四步:表面处理表面处理是为了提高弹簧的耐蚀性和表面光洁度。
常见的表面处理方法包括镀锌、镀镍、喷涂等。
这些方法可以有效地增加弹簧的寿命和耐候性,提高其在不同环境下的使用性能。
第五步:组装和检测最后,弹簧会经过组装和检测。
组装包括将弹簧和其他零部件进行装配,确保其稳定性和可靠性。
检测是为了确保弹簧达到设计要求和产品质量标准。
常见的检测方法包括外观检查、尺寸测量和性能测试等。
综上所述,钢板弹簧的生产工艺包括原材料准备、弯曲加工、热处理、表面处理、组装和检测等环节。
每个环节都非常重要,直接影响到弹簧的性能和质量。
只有在严格遵循工艺流程的情况下,才能生产出高质量的钢板弹簧。
50CrVA钢的工艺优化及其在钢板弹簧产品中的应用
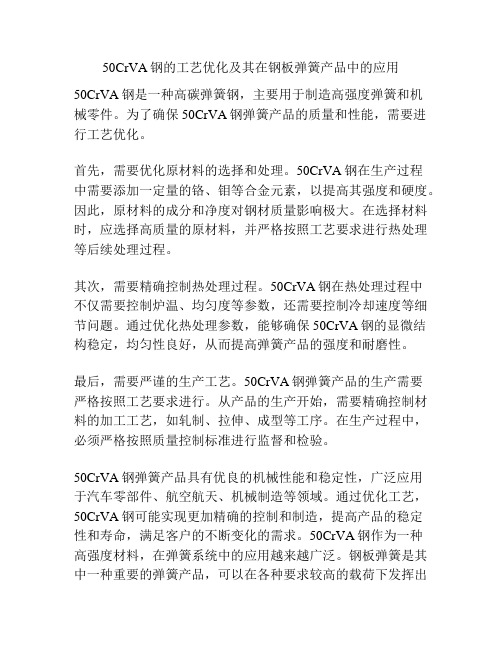
50CrVA钢的工艺优化及其在钢板弹簧产品中的应用50CrVA钢是一种高碳弹簧钢,主要用于制造高强度弹簧和机械零件。
为了确保50CrVA钢弹簧产品的质量和性能,需要进行工艺优化。
首先,需要优化原材料的选择和处理。
50CrVA钢在生产过程中需要添加一定量的铬、钼等合金元素,以提高其强度和硬度。
因此,原材料的成分和净度对钢材质量影响极大。
在选择材料时,应选择高质量的原材料,并严格按照工艺要求进行热处理等后续处理过程。
其次,需要精确控制热处理过程。
50CrVA钢在热处理过程中不仅需要控制炉温、均匀度等参数,还需要控制冷却速度等细节问题。
通过优化热处理参数,能够确保50CrVA钢的显微结构稳定,均匀性良好,从而提高弹簧产品的强度和耐磨性。
最后,需要严谨的生产工艺。
50CrVA钢弹簧产品的生产需要严格按照工艺要求进行。
从产品的生产开始,需要精确控制材料的加工工艺,如轧制、拉伸、成型等工序。
在生产过程中,必须严格按照质量控制标准进行监督和检验。
50CrVA钢弹簧产品具有优良的机械性能和稳定性,广泛应用于汽车零部件、航空航天、机械制造等领域。
通过优化工艺,50CrVA钢可能实现更加精确的控制和制造,提高产品的稳定性和寿命,满足客户的不断变化的需求。
50CrVA钢作为一种高强度材料,在弹簧系统中的应用越来越广泛。
钢板弹簧是其中一种重要的弹簧产品,可以在各种要求较高的载荷下发挥出其良好的性能表现。
在钢板弹簧的制造过程中,需要选用优质的50CrVA钢材料,同时进行热处理,以达到所需的机械性能。
此外,还需要考虑钢板弹簧的设计、加工和装配等多个因素,以确保最终产品的质量和性能。
首先,钢板弹簧的设计需要满足弹簧材料的性能要求及其所受力的需求,同时还需要考虑到弹簧的使用环境和稳定性问题。
在钢板弹簧的设计时,需要对产品的结构、尺寸、弯曲半径、回弹等多个因素进行综合考虑,以确保弹簧的稳定性和机械性能。
其次,钢板弹簧的加工需要精确掌握。
后钢板弹簧吊耳加工工艺及夹具设计
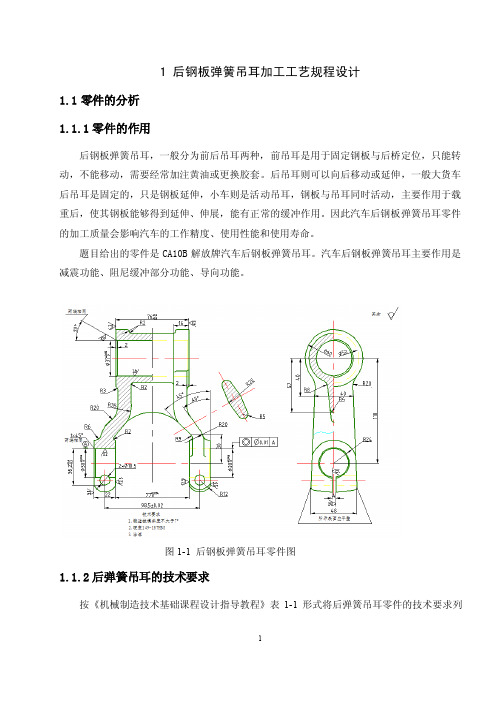
1 后钢板弹簧吊耳加工工艺规程设计1.1零件的分析1.1.1零件的作用后钢板弹簧吊耳,一般分为前后吊耳两种,前吊耳是用于固定钢板与后桥定位,只能转动,不能移动,需要经常加注黄油或更换胶套。
后吊耳则可以向后移动或延伸,一般大货车后吊耳是固定的,只是钢板延伸,小车则是活动吊耳,钢板与吊耳同时活动,主要作用于载重后,使其钢板能够得到延伸、伸展,能有正常的缓冲作用。
因此汽车后钢板弹簧吊耳零件的加工质量会影响汽车的工作精度、使用性能和使用寿命。
题目给出的零件是CA10B解放牌汽车后钢板弹簧吊耳。
汽车后钢板弹簧吊耳主要作用是减震功能、阻尼缓冲部分功能、导向功能。
图1-1 后钢板弹簧吊耳零件图1.1.2后弹簧吊耳的技术要求按《机械制造技术基础课程设计指导教程》表1-1形式将后弹簧吊耳零件的技术要求列于下表2-1中:表1-1 后弹簧吊耳零件的技术要求表加工表面 尺寸及技术要求 公差及精度等级表面粗糙度Ra/m μ 形位公差/mmmm 60φ两外圆端面mm2.06.076-- IT12 6.3mm 05.0037+φ孔mm 05.0030+IT8 1.6 R24内侧面 54mm IT12 12.5 R24外侧面54mmIT13 50mm 045.0030+φ孔mm 045.0030+IT8 1.6 ◎ φ0.01 Amm 5.10φ孔 mm 5.10IT12 12.5 开口槽4mmIT13501.1.3后钢板弹簧吊耳的工艺分析由后钢板弹簧吊耳零件图知可将其分为两组加工表面。
它们相互间有一定的位置要求。
现分析如下:(1)以60mm φ两外圆端面为主要加工表面的加工面。
这一组加工表面包括:。
60mm φ两外圆端面的铣削,加工mm 05.0037φ的孔,其中60mm φ两外圆端面表面粗糙度要求为 6.3Ra m μ,mm 05.0037φ的孔表面粗糙度要求为 1.6Ra m μ(2)以mm 045.0030φ孔为主要加工表面的加工面。
汽车钢板弹簧制造工艺

汽车钢板弹簧制造工艺引言:汽车钢板弹簧是汽车悬挂系统中重要的零部件之一,它承受着车身与路面之间的冲击力,保证了行驶的平稳性和舒适性。
本文将介绍汽车钢板弹簧的制造工艺,包括材料选择、弹簧制作、热处理和表面处理等方面。
一、材料选择汽车钢板弹簧的制造材料通常选择高强度低合金钢,具有良好的弹性和耐久性。
常用的材料包括SUP9、SUP9A、55CrMnA等。
在选择材料时,需要考虑到弹簧的设计要求,如负荷、变形量和工作环境等因素。
二、弹簧制作1. 板材切割:根据设计要求,将选定的钢板切割成合适尺寸的片材。
2. 弯曲成型:将切割好的片材放入弯曲机中,通过压力和模具的作用,使其呈现出弯曲的形状。
这一步骤需要根据弹簧的设计要求和图纸进行精确的操作。
3. 热处理:将形成的弯曲片材进行热处理,以提高其强度和弹性。
常用的热处理方法包括淬火和回火。
4. 整形修整:经过热处理后的弹簧可能会存在一定的变形,需要进行整形修整,使其恢复到设计要求的形状。
5. 表面处理:为了提高弹簧的耐腐蚀性和外观质量,常常对其进行表面处理,如镀锌、喷涂等。
三、热处理热处理是汽车钢板弹簧制造中不可或缺的步骤,它可以改善钢材的性能和组织结构。
常用的热处理方法有淬火和回火。
1. 淬火:将弹簧加热到临界温度,然后迅速冷却,使钢材的组织结构发生变化,从而提高其硬度和强度。
淬火后的弹簧通常具有较高的弹性模量和疲劳寿命。
2. 回火:淬火后的弹簧虽然硬度高,但脆性也增加,为了提高其韧性和塑性,需要进行回火处理。
回火是将淬火后的弹簧加热到一定温度,然后缓慢冷却,使其组织结构得到调整,达到一定的硬度和韧性平衡。
四、表面处理为了提高汽车钢板弹簧的耐腐蚀性和外观质量,常常对其进行表面处理。
1. 镀锌:镀锌是将弹簧浸入含锌溶液中,通过电化学反应在钢材表面形成一层锌层。
锌层可以有效防止钢材腐蚀,延长弹簧的使用寿命。
2. 喷涂:喷涂是将特殊的涂料喷洒在弹簧表面,形成一层保护膜,防止钢材与外界环境接触,起到防腐和美观的作用。
机械制造技术课程设计-前钢板弹簧吊耳加工工艺及铣平面夹具设计(全套图纸)

前钢板弹簧吊耳加工工艺设计和铣平面夹具设计学生姓名:学生学号:院(系):年级专业:指导教师:摘要本次设计是对前钢板弹簧吊耳零件的加工工艺设计。
前钢板弹簧吊零件的主要加工表面是平面及孔。
由加工工艺原则可知,保证平面的加工精度要比保证孔的加工精度容易。
所以本设计遵循先面前孔的原则。
并将孔与平面的加工明确划分成粗加工和精加工阶段以保证加工精度。
基准选择以前钢板弹簧吊耳大外圆端面作为粗基准,以前钢板弹簧吊耳大外圆端面与两个工艺孔作为精基准。
主要加工工序安排是先以前钢板弹簧吊耳大外圆端面互为基准加工出端面,再以端面定位加工出工艺孔。
在前续工序中除个别工序外均用端面和工艺孔定位加工其他孔与平面。
整个加工过程均选用专用机床。
关键词前钢板弹簧吊耳,加工工艺全套图纸,加153893706ABSTRACTThe design of the plate after spring lug parts of the processing order of the processes and some special fixture design. Spring plate after hanging parts of the main plane of the surface and pore. By the principle known Processing, the plane guarantee precision machining holes than guarantee the machining precision easy. So the design follows the surface after the first hole principle. Plane with holes and the processing clearly divided into roughing and finishing stages of processing to ensure accuracy. After selecting base plate spring lug large cylindrical face as a rough benchmark, After the leaf spring lug large cylindrical end with two holes as a precision technology benchmarks. main processes arrangements after the first spring plate lug large cylindrical face each other benchmarks machined face, End position to further processing out of holes. In addition to the follow-up processes are individual processes with end-positioning technology and other processing Kong and plane. The entire process of processing machine combinations were selected.Key words The empress steel plate spring coil mourns the ear,Process the craft,Appropriation tongs目录摘要 (I)ABSTRACT ................................................................................................................. I I1 绪论 (1)2 前钢板弹簧吊耳加工工艺规程设计 (2)2.1零件的分析 (2)2.1.1零件的作用 (2)2.1.2零件的工艺分析 (2)2.2工艺过程设计所应采取的相应措施 (3)2.3前钢板弹簧吊耳加工定位基准的选择 (3)2.3.1 确定毛坯的制造形式 (3)2.3.2粗基准的选择 (3)2.3.3精基准的选择 (4)2.4工艺路线的制定 (4)2.4.1 工艺方案一 (4)2.4.2 工艺方案二 (5)2.4.3 工艺方案的比较与分析 (5)2.5机械加工余量、工序尺寸及毛坯尺寸的确定 (6)2.6确定切削用量及基本工时(机动时间) (6)2.7时间定额计算及生产安排 (13)2.8本章小结 (14)3 铣平面夹具设计 (15)3.1设计要求 (15)3.2夹具设计 (15)3.2.1 定位基准的选择 (15)3.2.2 切削力及夹紧力的计算 (15)3.3定位误差的分析 (17)3.4零、部件的设计与选用 (18)3.5夹具设计及操作的简要说明 (19)总结 (21)参考文献 (22)致谢 (23)1 绪论机械的加工工艺及夹具设计是在完成了大学的全部课程之前,进行的一次理论联系实际的综合运用,使我对专业知识、技能有了进一步的提高,为以前从事专业技术的工作打下基础。
汽车钢板弹簧国家标准
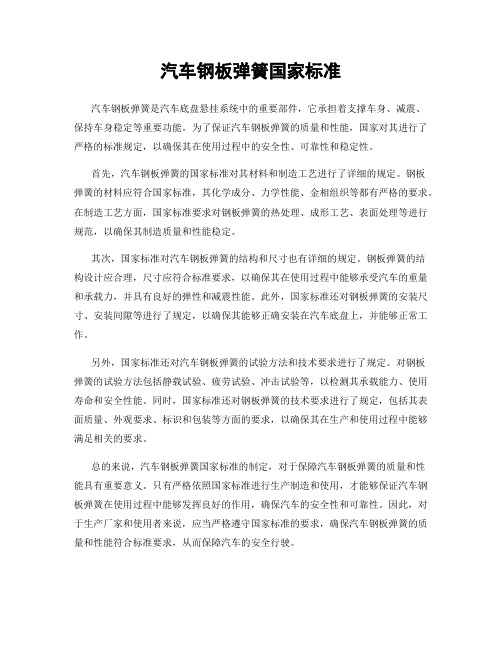
汽车钢板弹簧国家标准汽车钢板弹簧是汽车底盘悬挂系统中的重要部件,它承担着支撑车身、减震、保持车身稳定等重要功能。
为了保证汽车钢板弹簧的质量和性能,国家对其进行了严格的标准规定,以确保其在使用过程中的安全性、可靠性和稳定性。
首先,汽车钢板弹簧的国家标准对其材料和制造工艺进行了详细的规定。
钢板弹簧的材料应符合国家标准,其化学成分、力学性能、金相组织等都有严格的要求。
在制造工艺方面,国家标准要求对钢板弹簧的热处理、成形工艺、表面处理等进行规范,以确保其制造质量和性能稳定。
其次,国家标准对汽车钢板弹簧的结构和尺寸也有详细的规定。
钢板弹簧的结构设计应合理,尺寸应符合标准要求,以确保其在使用过程中能够承受汽车的重量和承载力,并具有良好的弹性和减震性能。
此外,国家标准还对钢板弹簧的安装尺寸、安装间隙等进行了规定,以确保其能够正确安装在汽车底盘上,并能够正常工作。
另外,国家标准还对汽车钢板弹簧的试验方法和技术要求进行了规定。
对钢板弹簧的试验方法包括静载试验、疲劳试验、冲击试验等,以检测其承载能力、使用寿命和安全性能。
同时,国家标准还对钢板弹簧的技术要求进行了规定,包括其表面质量、外观要求、标识和包装等方面的要求,以确保其在生产和使用过程中能够满足相关的要求。
总的来说,汽车钢板弹簧国家标准的制定,对于保障汽车钢板弹簧的质量和性能具有重要意义。
只有严格依照国家标准进行生产制造和使用,才能够保证汽车钢板弹簧在使用过程中能够发挥良好的作用,确保汽车的安全性和可靠性。
因此,对于生产厂家和使用者来说,应当严格遵守国家标准的要求,确保汽车钢板弹簧的质量和性能符合标准要求,从而保障汽车的安全行驶。
钢板弹簧的组成
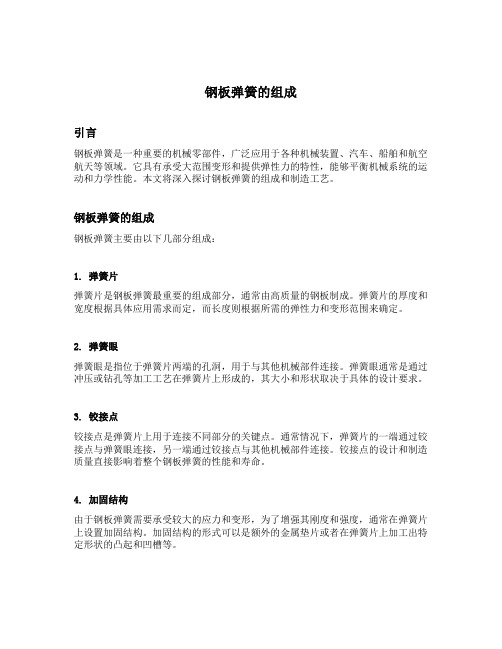
钢板弹簧的组成引言钢板弹簧是一种重要的机械零部件,广泛应用于各种机械装置、汽车、船舶和航空航天等领域。
它具有承受大范围变形和提供弹性力的特性,能够平衡机械系统的运动和力学性能。
本文将深入探讨钢板弹簧的组成和制造工艺。
钢板弹簧的组成钢板弹簧主要由以下几部分组成:1. 弹簧片弹簧片是钢板弹簧最重要的组成部分,通常由高质量的钢板制成。
弹簧片的厚度和宽度根据具体应用需求而定,而长度则根据所需的弹性力和变形范围来确定。
2. 弹簧眼弹簧眼是指位于弹簧片两端的孔洞,用于与其他机械部件连接。
弹簧眼通常是通过冲压或钻孔等加工工艺在弹簧片上形成的,其大小和形状取决于具体的设计要求。
3. 铰接点铰接点是弹簧片上用于连接不同部分的关键点。
通常情况下,弹簧片的一端通过铰接点与弹簧眼连接,另一端通过铰接点与其他机械部件连接。
铰接点的设计和制造质量直接影响着整个钢板弹簧的性能和寿命。
4. 加固结构由于钢板弹簧需要承受较大的应力和变形,为了增强其刚度和强度,通常在弹簧片上设置加固结构。
加固结构的形式可以是额外的金属垫片或者在弹簧片上加工出特定形状的凸起和凹槽等。
钢板弹簧的制造工艺钢板弹簧的制造工艺可以分为以下几个步骤:1. 材料选择制造钢板弹簧的首要步骤是选择合适的材料。
一般来说,高强度和高韧性的合金钢常用于制造钢板弹簧,因为它们可以承受大变形而不易疲劳。
2. 切割根据设计要求,将选定的钢板切割成相应尺寸的弹簧片。
切割可以采用机械切割或激光切割等工艺进行。
3. 成型将切割好的钢板弹簧片进行成型。
成型可以采用冷却弯曲、冲压和机械滚压等方法。
其中,机械滚压是一种常用的成型工艺,通过将弹簧片放置在滚轮间进行滚压,使其成型为弹簧形状。
4. 热处理经过成型的钢板弹簧需要进行热处理以改变其组织和性能。
热处理通常包括回火和淬火两个步骤。
回火可以提高钢板弹簧的韧性和塑性,而淬火可以增加其硬度和强度。
5. 表面处理经过热处理的钢板弹簧需要进行表面处理以提高其耐腐蚀性能。
后钢板弹簧吊耳加工工艺及其夹具设计-加工工艺设计-毕业论文

目录1 摘要---------------------------------------------------------------------------------------------------12后钢板弹簧吊耳加工工艺流程设计-----------------------------------22.1 零件分析----------------------------------------------------------------------------------22.2定位基准的选择-----------------------------------------------------------------32.3制定工艺路线----------------------------------------------------------------42.4确定工序尺寸及加工余量--------------------------------------------52.5确定切削用量及基本工时-----------------------------------------73铣削后钢板弹簧吊耳内侧面的夹具设计----------------------------------14 3.1粗铣后钢板弹簧吊耳内侧面的夹具设计--------------------------------------14 3.2定位基准的选择以及定位方案的分析--------------------------------------14 3.3夹紧力和铣削力的计算-------------------------------------------------------143.4对刀装置的设计---------------------------------------------------------------154加工φ30mm孔的夹具设计-----------------------------------------------164.1加工φ30mm孔的夹具设计--------------------------------------------164.2定位基准的选择以及定位方案的分析--------------------------------174.3夹紧力和铣削力的计算------------------------------------------------194.4夹具的精度分析---------------------------------------------------------224.5夹具装置的简要说明------------------------------------------------------225加工φ10.5mm孔的夹具设计-----------------------------------------------235.1加工φ10.5mm孔的夹具设计------------------------------234.2定位基准的选择以及定位方案的分析--------------------------------174.3夹紧力和铣削力的计算------------------------------------------------194.4夹具的精度分析---------------------------------------------------------224.5夹具装置的简要说明------------------------------------------------------22摘要在夹具的设计过程中,最重要的主要是被加工零件的定位、夹紧等问题。
钢板弹簧工艺知识

钢板弹簧工艺知识钢板弹簧工艺知识是在钢板加工行业中非常重要的一部分。
钢板弹簧广泛应用于汽车、家电、建筑及机械制造等领域。
这些弹簧可以用于支撑、缓冲和控制运动,其性能与制造工艺密切相关。
以下将介绍钢板弹簧的工艺知识,包括材料选择、设计原则和加工过程。
材料选择:材料的选择对于钢板弹簧的性能至关重要。
常用的弹簧材料包括普通碳素钢、合金钢和不锈钢。
选择合适的材料可以确保弹簧的强度、韧性和耐腐蚀性。
对于高温或特殊环境下的应用,还可以选择耐高温合金钢或高强度不锈钢等特殊材料。
设计原则:钢板弹簧的设计需要考虑弹性模量、应力和变形等因素。
为了获得理想的弹簧特性,弹簧的设计应遵循以下原则:1.合适的线径选择:线径越大,弹簧的刚度越大;线径越小,弹簧的刚度越小。
2.合适的弹簧绕制方式:弹簧可以采用单绕或多绕的方式制作。
单绕弹簧更容易设计和制造,但多绕弹簧可以提供更高的负荷能力。
3.合适的活动区域:设计时需考虑弹簧的活动区域,以确保弹簧在工作时没有塑性变形。
4.合适的弹簧常数:弹簧常数与材料的弹性模量和几何形状有关。
通过调整弹簧的直径、线径和绕制方式等参数来控制弹簧常数。
加工过程:钢板弹簧的加工过程包括原料准备、切割、成型和热处理等步骤。
1.原料准备:选取合适的钢板材料,根据设计要求切割成所需长度。
2.切割:使用剪切机、钢板刀或激光切割机等工具将钢板按要求切割成片状。
3.成型:使用弹簧机械设备将切割好的钢板进行弯曲、扭转等操作,使其成为所需形状和尺寸的弹簧。
4.热处理:通过热处理过程,如淬火和回火,来改善弹簧的强度和弹性。
5.表面处理:对成品弹簧表面进行防锈处理,如镀锌或喷涂。
钢板弹簧工艺知识的掌握对于生产高质量的钢板弹簧至关重要。
通过选择合适的材料、遵循设计原则和掌握合适的加工过程,可以制造出符合要求的弹簧产品。
此外,技术人员还应了解关于弹簧的相关标准和测试方法,以确保产品的合格性和可靠性。
后钢板弹簧吊耳加工工艺及夹具设计
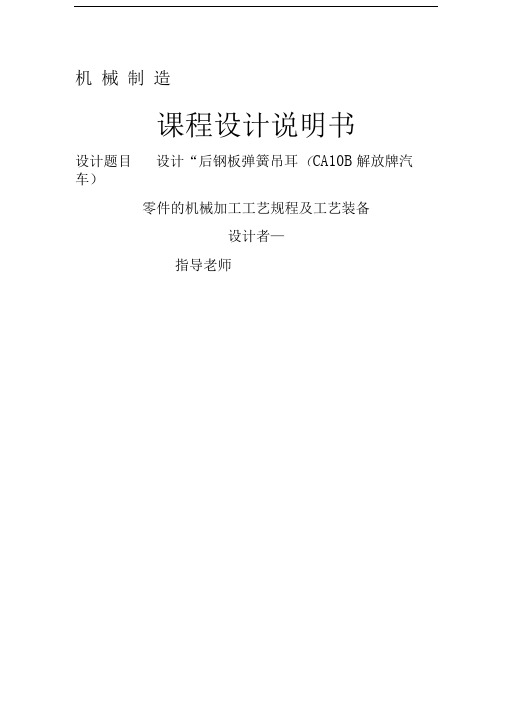
机械制造课程设计说明书设计题目设计“后钢板弹簧吊耳(CA10B解放牌汽车)零件的机械加工工艺规程及工艺装备设计者—指导老师目录目录 (1)搞要.............................................................. ..... . (3)1绪论. (4)2 后钢板弹簧吊耳加工工艺规程设计 (6)零件的分析 (6)零件的作用 (6)零件的工艺分析 (6)工艺过程设计所应采取的相应措施 (7)后钢板弹簧吊耳加工定位基准的选择 (7)确定毛坯的制造形式 (7)粗基准的选择 (7)精基准的选择 (8)工艺路线的制定 (8)工艺方案一 (8)工艺方案二 (8)工艺方案的比较与分析 (9)机械加工余量、工序尺寸及毛坯尺寸的确定. (9)确定切削用量及基本工时(机动时间) (10)时间定额计算及生产安排 (19)本章小结 (21)3 粗铣后钢板弹簧吊耳内侧端面夹具设计 (22)粗铣后钢板弹簧吊耳内侧端面夹具设计 (22)定位方案的分析和定位基准的选择 (22)定位误差分析 (22)铣削力与夹紧力计算 (23)定向键与对刀装置设计 (24)夹紧装置及夹具体设计 (26)夹具设计及操作的简要说明 (27)本章小结 (27)4 加工30mm 工艺孔夹具设计 (28)加工30mm 工艺孔夹具设计. (28)定位方案的分析和定位基准的选择 (28)定位误差分析................................................................ ..28 切削力的计算与夹紧力分析 .. (29)钻套、衬套、钻模板及夹具体设计 (29)夹具精度分析 (31)夹具设计及操作的简要说明 (31)本章小结 (32)5 加工10.5mm 工艺孔夹具设计 (33)加工10.5mm 工艺孔夹具设计 (33)定位方案的分析和定位基准的选择 (33)定位元件的设计 (33)定位误差分析 (35)切削力的计算与夹紧力分析 (35)钻套、衬套、钻模板及夹具体设计 (36)夹具精度分析 (37)夹具设计及操作的简要说明 (38)本章小结 (38)结论 (39)参考文献 (40)致谢 (40)摘要本次设计是对后钢板弹簧吊耳零件的加工工艺规程及一些工序的专用夹具设计。
钢板弹簧设计手册技术手册指导书
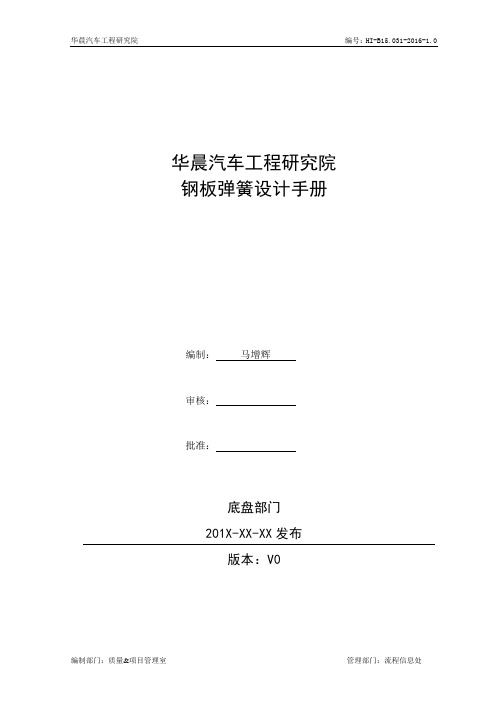
华晨汽车工程研究院钢板弹簧设计手册编制:马增辉审核:批准:底盘部门201X-XX-XX发布版本:V0前言本设计手册规定的XXXX产品的要求,和国家有关标准规定而制定。
本设计手册由汽车工程研究院XXXX负责起草;本设计手册由汽车工程研究院XXXX进行管理和解释;本设计手册主要起草人员:变更记录目录1.概述 (1)1.1定义 (1)1.2基本功能和原理 (1)1.3钢板弹簧的布置方案 (3)2.钢板弹簧材质 (4)3.钢板弹簧生产工艺 (4)4.钢板弹簧的参数设计 (4)4.1满载弧高fa (4)4.2钢板弹簧长度L的确定 (5)4.3钢板弹簧断面尺寸及片数的确定 (6)4.4钢板弹簧片数n (8)4.5钢板弹簧各片长度的确定 (8)4.6钢板弹簧刚度的验算 (9)4.7钢板弹簧总成在自由状态下的弧高及曲率半径计算 (10)4.8钢板弹簧总成弧高的核算 (11)4.9钢板弹簧的强度验算 (12)5.钢板弹簧设计阶段潜在失效模式 (13)6钢板弹簧台架试验 (13)华晨汽车工程研究院钢板弹簧设计手册1.概述1.1定义钢板弹簧是汽车悬架中应用最广泛的一种弹性元件,它是由若干片等宽但不等长(厚度可以相等,也可以不相等)的合金弹簧片组合而成的一根近似等强度的弹性梁,作用是支撑车体,缓和由路面传来的振动和冲击载荷。
图1 钢板弹簧1.2基本功能和原理当钢板弹簧安装在汽车悬架中,所承受的垂直载荷为正向时,各弹簧片都受力变形,有向上拱弯的趋势。
这时,车桥和车架便相互靠近。
当车桥与车架互相远离时,钢板弹簧所受的正向垂直载荷和变形便逐渐减小,有时甚至会反向。
图2 钢板弹簧与车桥简图钢板弹簧第一片称为主片,其两端弯成卷耳,内装青铜或塑料、橡胶、粉末冶金制成的衬套,以便使用弹簧销与固定在车架上的支架或吊耳作销链连接。
钢板弹簧中部一般用U形螺栓固定在车桥上。
中心螺栓用以连接各弹簧片,并保证装配时各片的相对位置。
中心螺栓距两端卷耳的距离可以相等,(称为对称式钢板弹簧);也可以不相等(称为非对称式钢板弹簧)。
钢板弹簧的制造工艺流程
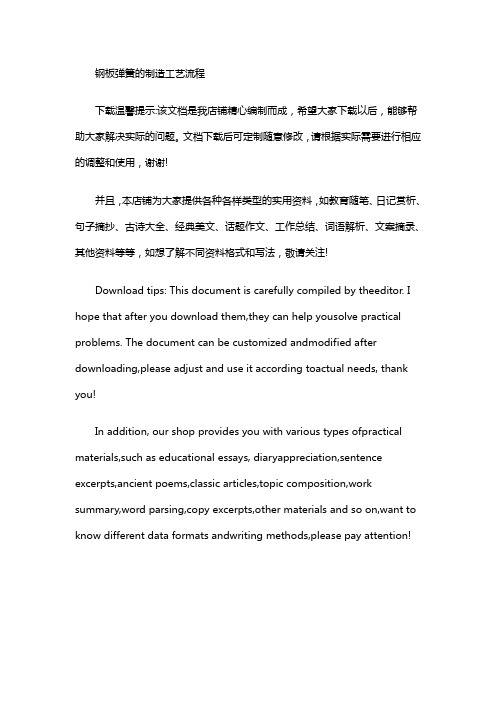
钢板弹簧的制造工艺流程下载温馨提示:该文档是我店铺精心编制而成,希望大家下载以后,能够帮助大家解决实际的问题。
文档下载后可定制随意修改,请根据实际需要进行相应的调整和使用,谢谢!并且,本店铺为大家提供各种各样类型的实用资料,如教育随笔、日记赏析、句子摘抄、古诗大全、经典美文、话题作文、工作总结、词语解析、文案摘录、其他资料等等,如想了解不同资料格式和写法,敬请关注!Download tips: This document is carefully compiled by theeditor. I hope that after you download them,they can help yousolve practical problems. The document can be customized andmodified after downloading,please adjust and use it according toactual needs, thank you!In addition, our shop provides you with various types ofpractical materials,such as educational essays, diaryappreciation,sentence excerpts,ancient poems,classic articles,topic composition,work summary,word parsing,copy excerpts,other materials and so on,want to know different data formats andwriting methods,please pay attention!钢板弹簧作为汽车悬挂系统的重要组成部分,承担着缓冲和支撑车身重量的功能。
后钢板弹簧吊耳加工工艺及夹具设计

汇报人:
01
03
05
02
04
切割:将钢板弹簧吊耳材料 切割成所需的形状和尺寸
焊接:将弯曲好的钢板弹 簧吊耳材料进行焊接处理
检验:对加工好的钢板弹 簧吊耳进行质量检验
材料准备:选择合适的 钢板弹簧吊耳材料
弯曲:将切割好的钢板弹 簧吊耳材料进行弯曲处理
准确定位和夹紧工件
设计夹具检测:根据夹具 结构和加工工艺设计夹具 检测方案,确保夹具能够
准确定位和夹紧工件
设计夹具维护:根据夹具 结构和加工工艺设计夹具 维护方案,确保夹具能够
长期稳定工作
夹具类型:根据加工需求选择合适的夹具 类型,如固定式、移动式、旋转式等。
夹紧机构:设计合理的夹紧机构,保证工 件的稳定和精确定位。
打磨:对焊接好的钢板 弹簧吊耳进行打磨处理
包装:将检验合格的钢板 弹簧吊耳进行包装处理
材料选择:选用高强度、耐磨 损、耐腐蚀的材料
加工精度:保证加工精度,确 保吊耳与钢板弹簧的配合精度
表面处理:进行适当的表面处 理,提高耐磨性和耐腐蚀性
夹具设计:设计合理的夹具, 保证加工过程中的稳定性和准 确性
材料:高强度钢 加工方法:冲压、弯曲、焊接 尺寸精度:±0.1mm 表面处理:电镀、喷漆 质量控制:检验、测试 生产效率:每小时生产100个
提高安全性:减少 操作风险,提高生 产安全性
优化加工工艺,提高生产效率 改进夹具设计,提高产品质量 加强员工培训,提高操作技能 引入新技术,提高生产自动化程度
技术发展趋势:智 能化、自动化、高 效化
应用领域拓展:汽 车、机械、建筑等 行业
效果提升:提高生 产效率,降低成本 ,提高产品质量
弹簧钢简介与应用

弹簧是应用很广泛的各种机械和仪表中重要零件,其外形可分成板簧和螺旋弹簧两大类。
弹簧的主要功能是消震及储能。
弹簧工作时产生很大的弹性变形、吸收冲击能量、缓和冲击,例如汽车等车辆上的缓冲弹簧;弹簧还可以通过释放所吸收的能量,使其它零件完成某种动作,例如发动机上的气阀弹簧、仪表弹簧等。
1、弹簧钢的特点弹簧钢首先,必须应具备高的弹性极限和高的屈强比,以避免弹簧在高载荷下产生永久变形;其次,应具备高的疲劳极限和高的抗拉强度,以免弹簧在长期震动和交变载荷应力的作用下产生疲劳破坏;再次,有一定冲击韧度和足够的塑性;同时还要求有良好的淬透性和低的脱碳敏感性,使弹性极限大幅度降低;以及良好的表面质量,在冷热状态下容易加工成形和良好的热处理工艺性。
弹簧钢一般均在弹性极限范围内服役,承受载荷时不允许产生塑性变形,因此要求弹簧钢经淬火、中温回火后具有尽可能高的弹性极限和屈强比值(≥0.90)。
为了获得弹簧所要求的性能,弹簧钢采用较高的含碳量,碳素弹簧钢通常在0.60%~0.85%范围。
如65、70钢等的淬透性较差,其截面尺寸超过12mm时在油中就不能淬透,若用水淬火就容易开裂。
对于截面尺寸较大、承受较重负荷的弹簧都是用合金钢制造。
合金弹簧钢的合碳量一般在0.50%~0.70%之间,所含合金元素有Si、Mn、Cr、V等,它们的主要作用是提高钢的淬透性和回火稳定性,强化铁素体和细化晶粒,从而有效地改善弹簧钢的力学性能。
Si和Mn主要提高淬透性,同时也提高屈强比,且以Si的作用最突出,但它在热处理时促进表面脱碳,Mn则使钢易过热,造成晶粒粗大。
重要用途的弹簧钢必须加入Cr、V、W等元素,Si--Cr弹簧钢表面不易脱碳;Cr--V弹簧钢不易过热,晶粒细,不易长大粗化,耐冲击性能好,高温强度也高,其中Cr、V、W还有利于提高弹簧钢的高温强度。
弹簧钢的牌号请见《888弹性地带》第85期“弹簧钢的技术发展与生产使用”一文。
2、弹簧制造过程的特征弹簧热处理后质量的判别主要是弹簧的寿命,从性能的角度考虑时需要调整弹性参数与韧性参数的平衡;性能与弹簧钢的淬透性有密切关系。
后钢板弹簧吊耳零件工艺及加工Φ30两孔夹具设计

后钢板弹簧吊耳零件工艺及加工Φ30两孔夹具设计一、后钢板弹簧吊耳零件工艺1.材料准备:选择适用于后钢板弹簧吊耳的优质钢板,根据设计要求订购相应的材料。
2.切割加工:根据图纸尺寸,使用剪板机或激光切割机将钢板切割成相应尺寸大小的矩形坯料。
3.表面处理:使用砂轮或砂纸进行表面打磨,去除锈蚀、氧化层和毛刺等表面缺陷,提高表面质量。
4.弯曲成型:根据图纸要求,使用弯曲机将钢板进行弯曲成型,形成弯折角度和弯曲半径。
5.冲压加工:使用冲床或冲裁机对钢板进行冲孔或压下形成指定形状。
6.焊接:根据零件的要求,采用电弧焊接或气体保护焊将零件进行焊接,确保焊缝牢固可靠。
7.表面处理:对焊接好的零件进行再次表面处理,如去除焊缝的烟灰和氧化层,进行除锈处理。
8.清洗和检验:对零件进行清洗和检验,确保表面没有杂质和缺陷。
9.表面涂装:根据设计要求,进行表面涂装,常见涂层有镀锌、烤漆等,提高零件的表面保护和美观度。
10.组装:按照图纸要求将各个零部件进行组装,使用螺栓、螺母等连接件将零件固定组合。
11.质量检验:对组装完成的零件进行整体质量检验,确保符合设计要求和标准。
Φ30两孔夹具是一种用于夹持Φ30直径零件的夹具,以保证零件在加工和装配过程中的固定和稳定。
1.夹具结构设计:根据Φ30直径零件的形状和尺寸,设计夹具的结构和形式,可以采用框架式或夹爪式结构。
2.材料选择:选择具有足够强度和刚度的材料,如优质钢材或铝合金材料。
3.夹具夹持方式设计:根据Φ30直径零件的特点,选取合适的夹持方式,如夹爪式、夹板式、吸盘式等。
4.夹具定位设计:夹具需要能够准确定位Φ30直径零件,确保零件在夹具内的位置和角度正确。
5.夹具固定设计:夹具需要能够固定在加工设备或工作台上,以保证夹具的稳定和工作精度。
6.加工工艺设计:夹具的制造需要考虑到加工工艺和加工工装的设计,以确保夹具的加工精度和质量。
7.安全设计:夹具在使用过程中需要保证操作人员的安全,设计时需考虑到夹具的安全性和可靠性。
塔形弹簧的类别

塔形弹簧的类别一、引言弹簧是一种能够储存和释放能量的机械零件,广泛应用于各种机械设备中。
其中,塔形弹簧作为一种特殊的弹簧形式,具有独特的性能和应用场合。
本文将详细介绍塔形弹簧的类别。
二、塔形弹簧简介1. 定义塔形弹簧是一种由扁平钢带或圆钢经过冷却工艺加工而成的长条形弹簧。
它具有高度可控的刚度和载荷能力,并且可以在非常小的空间内提供大量的储存能量。
2. 制造工艺制造塔形弹簧需要经过以下几个步骤:(1)选材:选择适合制作塔形弹簧的钢材;(2)卷制:将钢带或圆钢卷成螺旋形;(3)冷却:在加工过程中进行冷却处理,以增加材料硬度和刚度;(4)裁剪:根据需要裁剪成所需长度。
3. 应用领域由于其高度可控的刚度和载荷能力,塔形弹簧广泛应用于以下领域:(1)汽车制造:用于悬挂系统和减震器;(2)工业机械:用于振动控制和冲击吸收;(3)建筑工程:用于支撑结构和减震。
三、塔形弹簧的类别1. 单层塔形弹簧单层塔形弹簧由一层扁平钢带或圆钢卷成螺旋形而成。
它具有高度可控的刚度和载荷能力,适合于需要大量储存能量的场合。
单层塔形弹簧的优点是结构简单、制造成本低廉,但其缺点是容易产生侧向位移,需要配合导向装置使用。
2. 多层塔形弹簧多层塔形弹簧由多个扁平钢带或圆钢卷成螺旋形而组成,每个扁平钢带或圆钢之间通过特殊的接头连接。
多层塔形弹簧具有更高的刚度和载荷能力,并且可以更好地控制侧向位移。
但其缺点是制造难度大、成本较高。
3. 双塔形弹簧双塔形弹簧由两个相同的塔形弹簧组成,通过特殊的连接件连接在一起。
双塔形弹簧具有更高的刚度和载荷能力,并且可以更好地控制侧向位移。
它适用于需要大量储存能量和对空间要求较小的场合。
4. 钢板弹簧钢板弹簧是一种由多个薄钢板组成的塔形弹簧。
它具有更高的刚度和载荷能力,并且可以更好地控制侧向位移。
但其缺点是制造难度大、成本较高。
四、结论总之,塔形弹簧作为一种特殊的弹簧形式,具有高度可控的刚度和载荷能力,并且可以在非常小的空间内提供大量的储存能量。
- 1、下载文档前请自行甄别文档内容的完整性,平台不提供额外的编辑、内容补充、找答案等附加服务。
- 2、"仅部分预览"的文档,不可在线预览部分如存在完整性等问题,可反馈申请退款(可完整预览的文档不适用该条件!)。
- 3、如文档侵犯您的权益,请联系客服反馈,我们会尽快为您处理(人工客服工作时间:9:00-18:30)。
钢板弹簧制造工艺第一节:断料1、 剪切力的计算:①平口剪切力: P 1= bh σb (kgf) ( 或者 P = Kbh τb K 是系数取1.3 ) 式中: b 扁钢宽度(mm ); h 扁钢厚度(mm) ; σb 抗拉强度(Kg/mm 2)结合板簧片的交货状态,这里的抗拉强度是指热轧状态下的,不是热处理状态下的。
之所以没有选抗剪强度τb ,是考虑到扁钢有厚度公差,还有剪刃变钝,剪刃间隙大小的变化等因素。
②斜口剪切力: P 2 = φσtg h b 25.0(kgf ) 式中φ为斜刃倾斜角。
③斜口剪切力与平口剪切力的比较:bbbh tg h p p σφσ2125.0= = φbtg h 5.0 设上式中 b tg φ=A ,也就是斜口高度,则上式变为h A Ah p p 5.05.012== 即: 125.0p hA p = 从此式可以看出,当A>0.5h 时(也就是半个片厚时),斜口剪切的剪切力就可以小于平口剪切的剪切力,这就是当设备或模具所受力过大时,可以选择斜口剪切的工艺方法之理论依据。
2、 常见的断料缺陷和产生原因:①剪切裂纹:原因是剪刃刀片不锋利;剪刃刀片间隙调整不当。
正确安装剪刃刀片并及时更换修理变钝的剪刃刀片,就可避免产生缺陷。
②剪切毛刺:使用变钝的剪刃刀片,间隙过大,是造成剪切毛刺的重要原因。
毛刺经淬火后硬度高,装配后对其相邻的片会形成损害(加剧摩擦和产生噪音),严重影响使用寿命。
③切口拉伸:在热剪切时由于加热温度过高所致。
温度越高端头切口拉伸现象越严重。
④切口厚度切斜:即单片切口沿厚度方向呈斜坡形状,是由于剪刃刀片间隙过大或剪切时扁钢前后方向串动所致。
⑤切口切斜:即斜头,是沿着单片宽度方向呈倾斜角。
原因是剪切时扁钢侧边没有靠近档板或持料不稳所致;扁钢侧弯太大也会造成斜头。
剪切长片时应尽量利用侧弯较小的扁钢材料。
⑥切口不齐:是指切口波浪弯,是由于剪刃刀片钝损或刀片间隙过大所致。
及时更换或修理钝损的剪刃刀片和正确调整剪刃刀片间隙。
第二节 中心孔和铆钉孔加工钻孔:要普通钻床上加工中心孔和端孔是一种生产效率很低的工艺方法,适用于小批量生产,但是定位和质量情况比冲孔要好一些。
尤其是当簧片比较厚而相对于孔径又比较小时,冲孔没法解决只能用钻孔。
冲孔:适用于大批量生产,特别适用于端孔,因为冲孔落料一端直径较大,因此只要码放有规则就可以省去划卡子孔的工序(大孔端淬火在凹面正好铆钉)。
冲孔和钻孔常见的缺陷一是毛刺,应及时清理;二是孔边尖角处容易造成淬火裂纹所以现在要求比较高的板簧,中心孔边缘要求进行挤压或倒角处理.第三节片端加工1、端头切角:一般采用冷切工艺,在厚度大于16mm时可考虑采用热切角工艺。
切角时与钢板圆边的交汇处极易产生毛刺,要及时进行清理。
2、端部压扁:对簧片单片进行端部压扁加工,可以减轻重量,使应力分布均匀并能改善汽车乘坐的舒适性。
①端部短轧扁:端部压扁长度一般不切入下一片的长度内,轿车和越野车上长用。
随着科技进步,人们对乘坐的舒适性要求越来越高,因此越来越多的车型也在采用这种加工形式。
②长轧扁:即全长锥形或抛物线形轧制。
这种轧制出来的板簧,可以应用在高级轿车上。
但是这种板簧在轧制时对轧机的要求非常高,一般是采用计算机控制线型的全自动轧机,其机电一体化的程度和计算机的控制水平都是非常高的。
第四节冲制定位凸包1、单纯中心定位凸包:板簧片采用中心定位凸包结构,可减少中心孔结构的钢板弹簧由于骑马螺栓松动而易在中心孔处损坏现象的发生。
但中心定位凸包由于加工复杂和运输过程中易散片等缺点而在多片式板簧中逐渐减少而改用中心孔结构。
中心定位凸包在小批量生产工厂都是在热处理前,用热冲成型工艺加工的。
2、中心孔+中心定位凸包:这种形式被越来越多的少片簧重载车使用,如美国三片簧系列板簧,特别是在最后一片上全部采用这种形式。
这一方面避免了运输过程中的散片,更重要的是,紧急刹车时,避免了冲击负荷对中心螺栓剪断的可能。
我们生产的建筑簧,现在全部采用这种结构形式,主要是为了防止板簧在支座内移动时把中心螺栓剪折。
这种工艺容易产生的缺陷是孔和圆包的同轴度不好,加工中要加以高度注意,否则,片与片之间在装配时会发生困难。
第五节卷耳和包耳1、上卷耳:上卷耳为我国大多数车型所采用。
同时为了加强第一片卷耳强度和在第一片断裂后起保护作用,第二片前端采用包耳结构。
第一片容易折的原因是力的的传递中心与第一片根部受力处有一个作用力臂(附加弯矩),根部附近受到剪切力和弯曲应力的双重作用。
上卷耳的前端长度一定要加工准确,否则车轴会装歪,车辆会跑偏。
2、下卷耳:一般是为了满足布置上和运动轨迹的要求而设计的,由于卷耳要承受垂直负荷,所以卷耳厚度要大些,否则容易张开产生塑变。
3、平卷耳:这种卷耳形式比上卷耳形式合理得多,但是在工艺上也困难得多。
一般这种卷耳形式,多用在越野车上。
它不存在上卷耳的弯曲力矩,耳根部只受拉力。
3、常见的卷耳缺陷有哪些?如何解决和预防?不同的卷耳设备,所产生的卷耳缺陷是不一样的。
有设备或模具本身带来的问题(称之为系统缺陷);也有操作不当带来的问题(称之为随机缺陷)。
①孔径大小不符:主要原因有加热温度过高,孔径偏小;加热温度过低不易卷圆,尺寸偏大。
模具用错或调整不当(如V型块选错或与芯轴配合关系不对);卷耳芯轴膨胀。
解决办法:严格按规程控制温度,学会看火色;正确调整模具;及时冷却芯轴或更换芯轴。
②吊耳宽度超差:主要原因有原材料宽度超差;半成品来料侧弯超差。
解决办法一是严把原材料关,二是对半成品来料不合格者退回上道工序。
③吊耳垂直度与平行度超差:主要原因有来料侧弯;模具与工装调整不当。
解决办法:将侧弯不合格的片挑出调直后再卷耳;调整侧定位靠板与卷耳模和芯轴垂直;V型顶头加工与安装要与卷耳芯轴平行。
④喇叭孔:主要原因是固定卷耳芯子的两端套口有磨损。
解决办法是哪端有磨损就更换哪端套口。
⑤过热、过烧、氧化严重:主要原因是加热温度过高或加热时间过长。
预防办法就是按工艺要求严格控制加热温度和加热时间,设备出故障时,要及时把片从高温区撤出。
第六节成型热处理钢板弹簧片的成型热处理由弯曲成形、淬火、回火三部份组成。
1、弯曲成形:由于设计上的需要,板簧各单片的曲率是不一样的,所以成形夹具分为两种:一种是固定某一曲率的成形夹具,即一套成形夹具只能生产一种曲率的弹簧片,俗称为死胎,适合于大批量生产。
另一种是曲率可调的成形夹具,即一套成形夹具可适用于多种曲率的弹簧片的成形,一般在多品种批量生产中采用,我厂基本上是这种型式。
2、淬火:弹簧钢全部都是亚共析钢,淬火是指把板簧片加热到Ac3以上30~50℃,并在该温度下保温足够的时间,使簧片整个断面的材料形成奥氏体组织,然后在淬火介质中迅速冷却,以得到不稳定的马氏体组织,从而提高簧片的硬度和强度,这一过程称为淬火。
弹簧片在淬火液中应保持足够的冷却时间,使奥氏体全部转变成马氏体,如果冷却不足或冷速过慢,就会发生非马氏体转变,影响弹簧的性能。
3、回火:钢板弹簧片淬火后得到的马氏体组织,硬度高而且很脆,另外由于在淬火过程中,由奥氏体转变为马氏体时发生体积膨胀而产生相当大的内应力,而且该组织极不稳定,所以必须进行回火后才能使用。
回火就是把淬火后的弹簧片加热到临界温度以下某一温度并在该温度下保温一定时间,然后冷却到室温,以得到回火屈氏体(低碳马氏体钢是得到回火板条马氏体),并消除内应力。
4、常见的板簧热处理缺陷有哪些?如何解决和预防?①硬度不足:一是加热温度不够或保温时间不足;二是操作速度过慢;三是冷却速度不够。
解决办法是保证有足够的加热温度和保温时间;操作动作要求迅速准确;保证淬火剂有足够的冷却速度,调整淬火剂的使用浓度,对我们来说是降低淬火液的浓度。
②硬度不均:一是加热不均匀;二是冷却不均匀。
解决办法就是保证加热均匀,冷却时不出温度不一致的片。
③过热与过烧:从金属学的角度讲:过热是晶粒明显长大(晶粒度评级图上大于等于4级的);过烧是晶界氧化或熔化。
原因是加热温度高或保温时间太长(本质细晶钢影响不大)。
预防的办法是严格控制加热温度。
④严重的氧化、脱碳:原因是加热温度高和保温时间较长。
预防办法是严格控制炉温和加热保温时间。
⑤淬火死弯:原因是淬火胎具调整不好。
解决办法是用样板重新调整。
⑥淬火裂纹:淬火时板簧内部的应力,超过材料本身的强度时就会产生裂纹。
解决办法一是降低淬火液的冷却速度,尤其是在Ms点以下的冷速要慢,对于我们来说,是提高淬火液浓度;二是淬火温度不要太高;三是不要反复淬火;四是淬火后立即回火;五是重量较大的簧片淬火后不要重叠放置;六要注意是否原材料本身的缺陷。
⑦回火硬度不合:A、回火硬度高:原因一是回火温度低,二是回火时间短,三是回火码料间隙过密;解决办法一是提高回火温度,二是延长回火时间,三是码料方式稀疏些。
B、回火硬度低:原因和上述情况相反,解决办法也和上述方法相反。
⑧淬火侧弯:(一)、侧弯产生的主要原因:误差理论告诉我们,系统的误差是由多个误差集合而成.解决的办法只有逐个地找出这些误差,视其轻重缓急程度加以解决。
我认为我厂的侧弯产生因素主要有以下几点:(1)、工艺因素:a、入水方式和簧片两侧面冷速不一样是工艺上造成侧弯的主要原因。
b、冷调直后的回复以及簧片从炉口高处掉下冲击造成的侧弯是次要原因。
(2)、设备因素:a、上下胎板之间对簧片横向有扭距造成的扭曲。
上下胎板之间滑块间隙偏大是造成扭曲的主要原因。
b、底胎板由于长期使用磨损不平,多次修复后胎板变薄因此刚性不足,是扭曲的次要原因。
(3)、操作因素a、操作上的不精心,红片着地或胎板时受力不合理是造成侧弯和扭曲的主要原因。
b、不认端进行操作,对认端装配的板簧总成侧弯加倍是总成侧弯的主要原因。
(二)、针对上述原因应采取的控制方案:(1)、工艺方面:设计和重新使用限制侧弯顶尖,作为一种保证,把它形成制度(尤其是对装入支架内的主片),定期进行检查。
(2)、设备方面:对胎板和胎板之间的滑块进行检修调整,并提出定期的检查制度。
(3)、对职工进行教育,强调不摔片和认端操作的重要性。
(4)、上述三方面均形成严格的考核制度。
第七节喷丸处理1、喷丸处理的定义及目的:喷丸处理是将高速钢丸打向弹簧片的凹面,使叶片表面引起塑性变形,形成一定厚度的硬化层的过程。
目的是使簧片受拉面产生足够大的残余压应力,降低由工作负荷引起的叶片表面的拉应力,从而提高弹簧的疲劳强度。
另外喷丸处理在弹簧片的喷丸表面产生大约0.25mm硬化层,因而能消除或改善或称钝化弹簧片的表面缺陷,从而也提高疲劳寿命。
钢板弹簧片喷丸后的断面应力状况图。
2、喷丸处理的分类:喷丸处理分为自由喷丸(簧片处于自由状况下的喷丸)和应力喷丸(簧片受拉面处于受拉应力状况的喷丸)两种。