使用废钢合成球墨铸铁的生产工艺研究和实践
合成铸铁的生产及应用
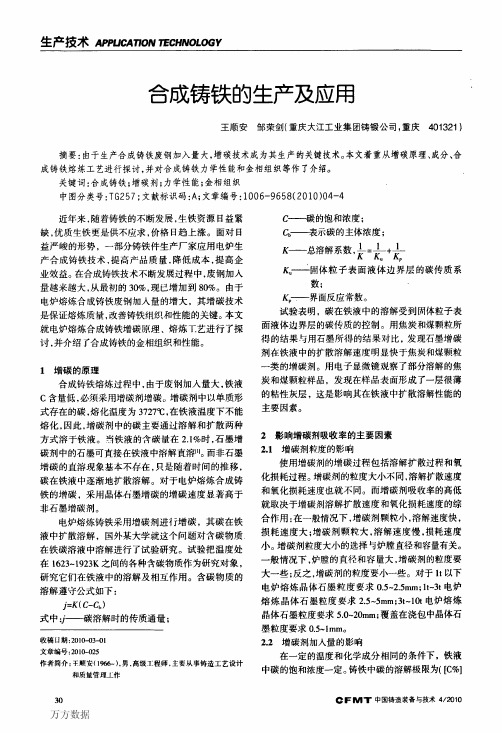
99.9
O.20
0.0lO
0.099
白|墨粉压粒
97.5
030
0.07
2.20
电煅煤增碳剂
98.4
0.22
0.85
O.05
沥青焦增碳剂
99.7
0.04
O.01
O.22
水份
1.5
O.25
表2炉料配比
项目
废钢
传统铸铁配比 30~50
合成铸铁配比 40-80
配比(%,
回炉料
30-40
生铁
lO~40
增碳剂 其余合金
1增碳的原理 合成铸铁熔炼过程中,由于废钢加入量大,铁液
C含量低,必须采用增碳剂增碳。增碳剂中以单质形 式存在的碳,熔化温度为37270C,在铁液温度下不能 熔化,因此,增碳剂中的碳主要通过溶解和扩散两种 方式溶于铁液。当铁液的含碳量在2.1%时,石墨增 碳剂中的石墨可直接在铁液中溶解直溶IlI。而非石墨 增碳的直溶现象基本不存在,只是随着时间的推移, 碳在铁液中逐渐地扩散溶解。对于电炉熔炼合成铸 铁的增碳,采用晶体石墨增碳的增碳速度显著高于 非石墨增碳剂。
生产技术APPLICATION TECHNOLOGY
合成铸铁的生产及应用
王顺安邹荣剑(重庆大江工业集团铸锻公司,重庆401321)
摘要:由于生产合成铸铁废钢加入量大,增碳技术成为其生产的关键技术。本文着重从增碳原理、成分、合 成铸铁熔炼工艺进行探讨,并对合成铸铁力学性能和金相组织等作了介绍。
关键词:合成铸铁;增碳剂;力学性能;金相组织 中图分类号:TG257:文献标识码:A;文章编号:1 006-9658(2010)04—4
感应电炉熔炼合成铸铁的炉料配比主要是回炉 料+工业碳素废钢+增碳剂,再配以适量的合金(常见 配比见表2)。回炉料配量以本单位回炉料多少而定,
合成球墨铸铁生产工艺
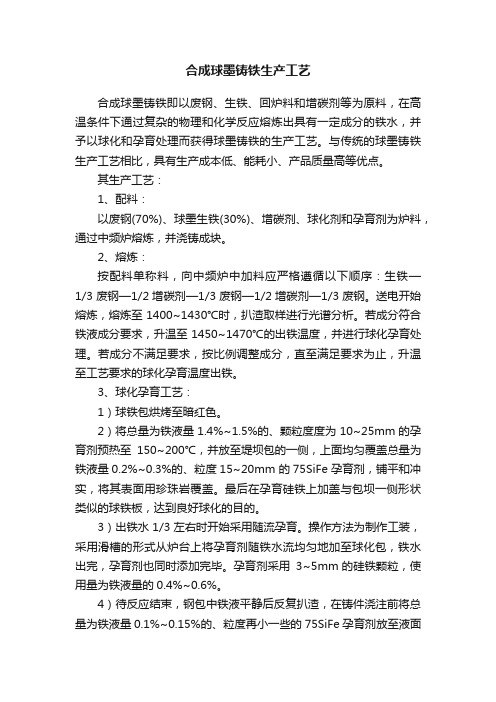
合成球墨铸铁生产工艺合成球墨铸铁即以废钢、生铁、回炉料和增碳剂等为原料,在高温条件下通过复杂的物理和化学反应熔炼出具有一定成分的铁水,并予以球化和孕育处理而获得球墨铸铁的生产工艺。
与传统的球墨铸铁生产工艺相比,具有生产成本低、能耗小、产品质量高等优点。
其生产工艺:1、配料:以废钢(70%)、球墨生铁(30%)、增碳剂、球化剂和孕育剂为炉料,通过中频炉熔炼,并浇铸成块。
2、熔炼:按配料单称料,向中频炉中加料应严格遵循以下顺序:生铁—1/3 废钢—1/2增碳剂—1/3废钢—1/2增碳剂—1/3 废钢。
送电开始熔炼,熔炼至1400~1430℃时,扒渣取样进行光谱分析。
若成分符合铁液成分要求,升温至1450~1470℃的出铁温度,并进行球化孕育处理。
若成分不满足要求,按比例调整成分,直至满足要求为止,升温至工艺要求的球化孕育温度出铁。
3、球化孕育工艺:1)球铁包烘烤至暗红色。
2)将总量为铁液量1.4%~1.5%的、颗粒度度为10~25mm的孕育剂预热至150~200℃,并放至堤坝包的一侧,上面均匀覆盖总量为铁液量0.2%~0.3%的、粒度15~20mm 的75SiFe 孕育剂,铺平和冲实,将其表面用珍珠岩覆盖。
最后在孕育硅铁上加盖与包坝一侧形状类似的球铁板,达到良好球化的目的。
3)出铁水1/3左右时开始采用随流孕育。
操作方法为制作工装,采用滑槽的形式从炉台上将孕育剂随铁水流均匀地加至球化包,铁水出完,孕育剂也同时添加完毕。
孕育剂采用3~5mm 的硅铁颗粒,使用量为铁液量的0.4%~0.6%。
4)待反应结束,钢包中铁液平静后反复扒渣,在铸件浇注前将总量为铁液量0.1%~0.15%的、粒度再小一些的75SiFe孕育剂放至液面上,并反复搅拌,进行瞬时孕育。
4、浇注:按要求将铁液浇注成块。
5、热处理工艺:为避免采用了连续退火工艺对球墨铸铁件进行热处理,出现了产品质量不稳定等问题。
采用更合适的分段退火热处理工艺,即高温石墨化和低温组织转变两阶段退火,以消除白口、降低硬度、改善切削性能。
球墨铸铁铸造工艺流程
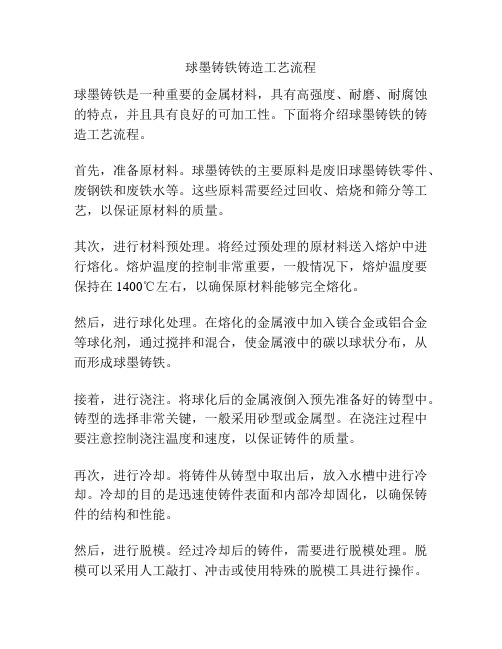
球墨铸铁铸造工艺流程球墨铸铁是一种重要的金属材料,具有高强度、耐磨、耐腐蚀的特点,并且具有良好的可加工性。
下面将介绍球墨铸铁的铸造工艺流程。
首先,准备原材料。
球墨铸铁的主要原料是废旧球墨铸铁零件、废钢铁和废铁水等。
这些原料需要经过回收、焙烧和筛分等工艺,以保证原材料的质量。
其次,进行材料预处理。
将经过预处理的原材料送入熔炉中进行熔化。
熔炉温度的控制非常重要,一般情况下,熔炉温度要保持在1400℃左右,以确保原材料能够完全熔化。
然后,进行球化处理。
在熔化的金属液中加入镁合金或铝合金等球化剂,通过搅拌和混合,使金属液中的碳以球状分布,从而形成球墨铸铁。
接着,进行浇注。
将球化后的金属液倒入预先准备好的铸型中。
铸型的选择非常关键,一般采用砂型或金属型。
在浇注过程中要注意控制浇注温度和速度,以保证铸件的质量。
再次,进行冷却。
将铸件从铸型中取出后,放入水槽中进行冷却。
冷却的目的是迅速使铸件表面和内部冷却固化,以确保铸件的结构和性能。
然后,进行脱模。
经过冷却后的铸件,需要进行脱模处理。
脱模可以采用人工敲打、冲击或使用特殊的脱模工具进行操作。
最后,进行后处理。
包括切割、磨削、修整、喷漆等工艺。
切割是将铸件切割成所需的形状和尺寸,磨削是为了提高表面光洁度和精度,修整是为了去除铸件上的缺陷,喷漆是为了保护铸件表面并提高外观质量。
综上所述,球墨铸铁的铸造工艺流程包括原材料准备、材料预处理、球化处理、浇注、冷却、脱模和后处理等环节。
每一个环节都需要经过严格的控制和操作,以确保最终得到优质的球墨铸铁铸件。
用废钢生产球墨铸铁方法,谈谈生产实践经验!

用废钢生产球墨铸铁方法,谈谈生产实践经验!如今合成铸铁并不是什么新鲜东西,在中频电炉中大量利用废钢、钢铁屑、机杂铁、回炉料和增碳剂等低值炉料通过电炉熔炼,配合直读光谱仪在线检测技术确定其化学成分来生产合成铸铁,这一铸铁生产方法对铸造企业来说确实是不错的选择,而且由于废钢、钢铁屑等的大量使用,铸造生产成本也相应降低,新生铁等原材料价格一路疯涨的势头得到了有效遏制,极大地缓解了企业的生存压力。
本文就利用中频电炉合成高强度球墨铸铁方法结合本企业近几年来的生产实践谈谈认识。
一、生产合成铸铁的主要原材料概况1、废钢:相对来说就是废旧的钢铁结构件、边角余料,A3、45#、40Cr等普通的含CW≤1%、SiW≤1%、MnW≤1%、低S、低P的材料;废旧的压力容器要通过解体,薄小的废钢料要打包,零散的或者是通过打包成块的,要能直接加入到熔炉内,不能卡炉影响布料更不能残存汽、液体引起爆炸;最好是不要生锈,能清除油污,国外介绍甚至要清除掉油漆和镀层的。
它可以在炉料中占比到50%以上,做到少用甚至不用新生铁。
2、钢铁屑:在机加工过程中钢铁件因加工去掉的屑,其中,钢屑的化学成分与废钢相同,铁屑因铸铁的材质是普通灰铸铁还是球墨铸铁而有所不同,其主要化学成分在CW2.5~4.0%之间,SiW1.5~3.5%之间,MnW0.3~2.0%之间;钢铁屑碎小零散,要装袋或做成屑饼以方便司炉和节省能源,同样要清除油污和切削液,最好不生锈;若散装料将会在熔炉内占较大空间,一炉铁水要多次在不同的状态、不同的温度下加料,特别是在炉料已融化、铁水已生成时再加入的铁屑料极易氧化发渣,影响熔炼过程正常进行,而即使是氧化严重的铁屑,在熔炉内没有铁水出现的早期加入,也能正常熔炼;一般情况下铸件的切削余量也即铁屑量占比不过20%左右;3、机杂铁:拆卸的报废的机器设备钢铁零部件、机身、底座等,化学成分相对复杂,可能含有少量合金元素或非金属杂质,一般情况下可清除其中的铝、锌、铅、锡等轻质低熔点金属和铜等有色金属以及油污坭后再使用;生产时根据产品的要求其用量可以控制到20%左右,生产球墨铸铁时尽量少用或不用;4.回炉料:就是铸造生产时产生的浇冒系统、飞边、毛刺、铁豆、锅巴铁以及废品等,其化学成分可以方便掌握,但要除掉其表面的粘砂以及除锈后才能使用。
球墨铸铁生产工艺流程

球墨铸铁生产工艺流程球墨铸铁是一种由球状石墨组织环绕的铁素体组织,具有优异的机械性能和良好的耐蚀性能。
下面是球墨铸铁的生产工艺流程。
1. 原料准备:将生铁、废钢、废铁等原料按照一定比例混合,以保证合金成分的准确性和均匀度。
2. 原料熔炼:将混合好的原料放入高炉中进行熔炼。
炉温一般为1500-1600℃,炉内的铁液要达到足够的液态度和连续重量。
3. 处理渣出炉:熔炼后,对炉内生成的渣进行处理。
通常会采用机械捞渣或氧气在渣中切割等方式进行处理,以确保铁液的质量。
4. 球化处理:对铁液进行球化处理以生成球状石墨。
一般球化剂为球墨化剂或球化包,在一定温度和时间下进行球化处理,使铁液中原本形成的石墨变成球状。
5. 调质处理:球化处理后,对球化铁液进行冷却,并加入适量的纯铁或调质剂以调整合金成分和控制结晶过程,以提高球墨铸铁的性能。
6. 铸造处理:将调质处理后的球墨铸铁液倒进模具中进行铸造。
模具一般采用砂型或金属型。
铸造过程中要注意温度控制、液态铁的流动和凝固,确保铸件的质量。
7. 淬火处理:对铸件进行淬火处理,以控制铸件的组织和性能。
通常通过加热到适当温度再迅速冷却的方式进行淬火处理。
8. 精加工和检测:对淬火后的铸件进行切削、铣削、磨削等精加工工艺,以获得所需的形状和尺寸。
同时进行外观检验、尺寸测量和力学性能测试等质量检测。
9. 表面处理和涂装:对精加工后的铸件表面进行研磨、喷砂、打磨等处理,以改善表面光洁度和质感。
然后进行涂装,以提高铸件的耐蚀性能和装饰性能。
10. 包装运输:将经过表面处理和涂装的球墨铸铁件进行包装和装箱,以便安全运输和储存。
综上所述,球墨铸铁的生产工艺流程包括原料准备、原料熔炼、处理渣出炉、球化处理、调质处理、铸造处理、淬火处理、精加工和检测、表面处理和涂装以及包装运输等环节。
这些环节相互关联,每个环节都对最终的球墨铸铁产品的质量起着重要的作用。
球墨铸铁500—7的铸造生产工艺

球墨铸铁500—7的铸造生产工艺作者:张燕明针对铸件结构、尺寸特点,选择适当的化学成分,使用球铁专用浇包,加强球化处理过程控制,稳定生产出符合技术要求的铸态QT500-7薄壁小型球墨铸铁件铸态高强度球墨铸铁的生产可以通过合金化强化基体组织等措施而获得,但是铸态综合性能良好的QT500-7球墨铸铁的生产,由于生铁、废钢和合金等原材料含有许多强化基体组织的微量合金元素导致球墨铸铁的性能下降,其生产难度较大。
现将我公司小型(重量1~10Kg)、薄壁球墨铸铁件(壁厚5~20mm)多年生产实践总结如下。
1性能及金相组织的要求抗拉强度≥500N/mm2,屈服强度≥320N/mm2,延伸率≥7,布氏硬度170~230,球化等级≤3,珠光体15?~45?,渗碳体≤1,石墨大小≥6级。
2化学成分的选择化学成分对集基体组织和铸造生铁机械性能起着重要作用,根据铸件结构特点、大小及要求化学成分选择如下:3.6?~3.9?C,原铁液含Si量选择为1.2?~1.6?,终Si量控制在2.6?~2.9?,碳当量(CE):4.5?~4.7?,0.2?~0.3?Mn,<0.05?P,<0.03?S,<0.03?RE残,0.035?~0.06?Mg同时应保证RE残/Mg残≤2/3。
3球化处理工艺笔者所在的企业采用0.5T中频炉熔化铁液,出铁温度在1520℃以上。
采用0.5T球铁专用凹坑式浇包冲入法进行球化处理。
球化剂为GB4138-88的FeSiMg8RE5,孕育剂为硅钡复合孕育剂,炉前检验合格后,快速浇注。
控制浇注时间在15min内,防止球化孕育衰退。
3.1球化剂处理铁液量0.5吨,球化剂的粒度应为10~20mm,球化剂粒度小于10mm的质量分数不大于10?,球化剂应烘干并预热,预热温度最好在150~200℃,如无条件也可制作专用料斗在炉口烘烤。
生产球铁希望铁液温度高,气体含量小不氧化,化学成分稳定。
现国内多采用各种冲天炉熔炼铁液,由于各种炉型都有自己的特点,应从实际出发,选择更利于生产球铁的炉型。
球墨铸铁生产工艺流程

球墨铸铁生产工艺流程
《球墨铸铁生产工艺流程》
球墨铸铁是一种优秀的铸铁材料,具有高强度、高韧性和优异的耐腐蚀性能。
其生产工艺流程主要包括原料准备、熔化、浇注、除渣、清理、热处理和检验等步骤。
首先是原料准备。
球墨铸铁的主要原料是生铁、废钢、石墨、球化剂和脱硫剂。
这些原料需要按照一定的配比进行混合,并且进行熔化前的预处理,以确保最终产品的质量。
接下来是熔化。
原料经过混合后,被送入高炉或电弧炉进行熔化,熔化温度通常在1500-1600摄氏度之间。
在熔化的过程中,需要不断搅拌并且加入球化剂和脱硫剂,以确保合金的成分和结构符合要求。
浇注是下一个关键步骤。
熔化后的合金被倒入模具中,并且进行冷却凝固。
在这个过程中,需要控制浇注温度和速度,以确保最终产品具有均匀的组织结构和良好的密度。
除渣和清理是后续的步骤。
在浇注结束后,需要进行除渣和清理工作,以去除产生在浇注过程中的杂质和残渣。
热处理是为了提高产品的力学性能而进行的处理。
经过热处理后的球墨铸铁,可以获得更好的强度和韧性。
最后是检验。
经过以上步骤后的产品需要进行质量检验,以确
保其性能和外观符合标准要求。
检验的内容包括化学成分分析、金相组织分析、力学性能测试和尺寸检查等。
综上所述,《球墨铸铁生产工艺流程》包括原料准备、熔化、浇注、除渣、清理、热处理和检验等多个步骤。
每个步骤都对最终产品的质量产生重要影响,需要严格把控和管理。
球墨铸铁熔炼与铸造工艺

球墨铸铁是一种高强度、高韧性的铸铁材料,其熔炼与铸造工艺主要包括以下几个步骤。
原料准备:主要原料是铸铁和球化剂。
铸铁通常是废铁、废钢等回收材料,而球化剂则是一种能够使铸铁中的碳以球形形式存在的添加剂。
熔炼铸造:将原料放入高温熔炉中进行熔炼,熔炼温度通常在1400℃以上。
在熔炼过程中,加入球化剂,使铸铁中的碳以球形形式存在。
浇注铸造:将熔融的球墨铸铁液体倒入铸型中,待其冷却凝固后,取出铸件。
热处理:对铸件进行热处理,以提高其强度和韧性。
通常采用淬火和回火的方法进行热处理。
加工和表面处理:对铸件进行加工和表面处理,以达到所需的形状和表面质量。
在整个铸造过程中,还需要特别注意以下几点:
球墨铸铁铸造工艺比普通灰铁铸件造型更为严格,其缩量要大于普通灰铁铸件,因此在造型时要加大冒口尺寸,确保冒口内铁液能够完全补充需要的缩量。
造型用型砂不能使用水泥砂造型,而要选用树脂砂或水玻璃砂进行造型,且耐火涂料要选择高温耐火材料。
在熔炼过程中,要严格控制球墨铸铁的含量要求,如要求球墨铸件材质为QT450材质,就需要控制五大元素含量在特定范围内。
浇铸时要采用高温出炉低温浇铸的原则,开始浇铸后要保证每个冒口铁液都能浇满,并持续为冒口补充铁液直至冒口内铁液不再下沉减少为止。
怎样用废钢炼球墨铸铁,生产中又应该注意哪些问题呢?
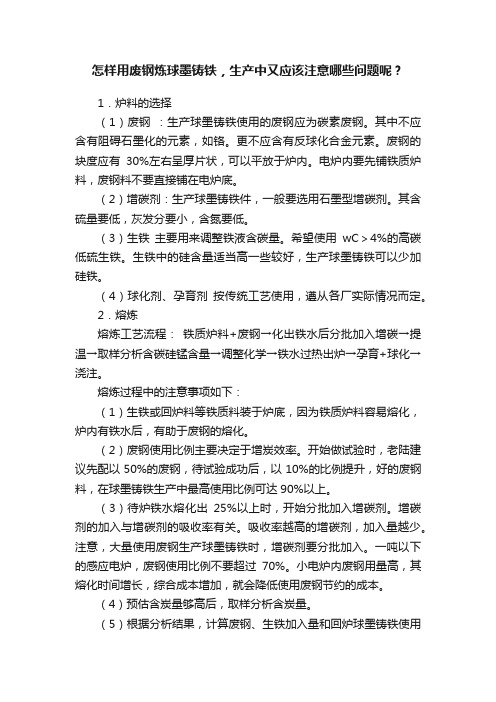
怎样用废钢炼球墨铸铁,生产中又应该注意哪些问题呢?1.炉料的选择(1)废钢:生产球墨铸铁使用的废钢应为碳素废钢。
其中不应含有阻碍石墨化的元素,如铬。
更不应含有反球化合金元素。
废钢的块度应有30%左右呈厚片状,可以平放于炉内。
电炉内要先铺铁质炉料,废钢料不要直接铺在电炉底。
(2)增碳剂:生产球墨铸铁件,一般要选用石墨型增碳剂。
其含硫量要低,灰发分要小,含氮要低。
(3)生铁主要用来调整铁液含碳量。
希望使用wC>4%的高碳低硫生铁。
生铁中的硅含量适当高一些较好,生产球墨铸铁可以少加硅铁。
(4)球化剂、孕育剂按传统工艺使用,遵从各厂实际情况而定。
2.熔炼熔炼工艺流程:铁质炉料+废钢→化出铁水后分批加入增碳→提温→取样分析含碳硅锰含量→调整化学→铁水过热出炉→孕育+球化→浇注。
熔炼过程中的注意事项如下:(1)生铁或回炉料等铁质料装于炉底,因为铁质炉料容易熔化,炉内有铁水后,有助于废钢的熔化。
(2)废钢使用比例主要决定于增炭效率。
开始做试验时,老陆建议先配以50%的废钢,待试验成功后,以10%的比例提升,好的废钢料,在球墨铸铁生产中最高使用比例可达90%以上。
(3)待炉铁水熔化出25%以上时,开始分批加入增碳剂。
增碳剂的加入与增碳剂的吸收率有关。
吸收率越高的增碳剂,加入量越少。
注意,大量使用废钢生产球墨铸铁时,增碳剂要分批加入。
一吨以下的感应电炉,废钢使用比例不要超过70%。
小电炉内废钢用量高,其熔化时间增长,综合成本增加,就会降低使用废钢节约的成本。
(4)预估含炭量够高后,取样分析含炭量。
(5)根据分析结果,计算废钢、生铁加入量和回炉球墨铸铁使用量。
(6)根据含硅量估算,决定是否可用回炉料补足铁液总量。
(7)适当提高铁液温度,按照分析结果补足合金元素,达到出炉温后出炉前加入硅铁。
(8)硅铁熔至熔融状态,立即出炉。
(9)球化、孕育、浇注照常规进行。
3.成分调整计算众所周知球墨铸铁的力学性能取决于化学成分、冷却速度(铸态球墨铸铁)和热处理工艺。
利用废钢生产铸态QT450_10
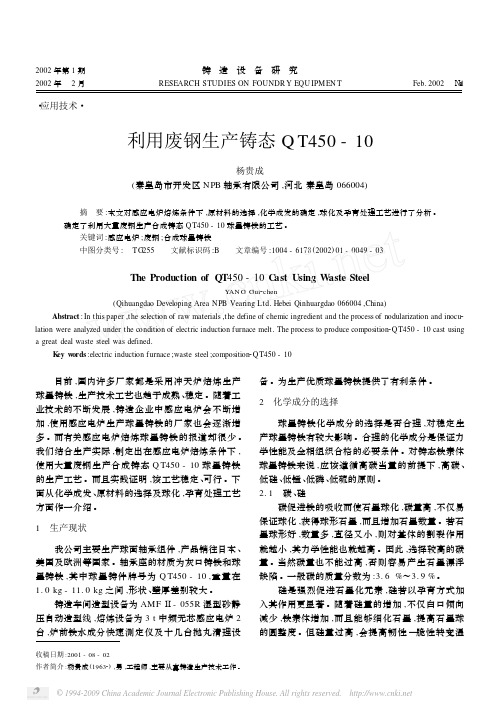
2002年第1期铸造设备研究2002年 2月RESEARCH STUDIES ON FOUNDR Y EQU IPMEN TFeb.2002 №1收稿日期:2001-08-02作者简介:杨贵成(19632),男,工程师,主要从事铸造生产技术工作。
・应用技术・利用废钢生产铸态Q T450-10杨贵成(秦皇岛市开发区NPB 轴承有限公司,河北秦皇岛066004) 摘 要:本文对感应电炉熔炼条件下,原材料的选择,化学成发的确定,球化及孕育处理工艺进行了分析。
确定了利用大量废钢生产合成铸态Q T450-10球墨铸铁的工艺。
关键词:感应电炉;废钢;合成球墨铸铁 中图分类号: TG 255 文献标识码:B 文章编号:1004-6178(2002)01-0049-03The Production of QT 450-10C ast Using W aste SteelYAN G Gui 2chen(Qihuangdao Developing Area NPB Vearing Ltd.Hebei Qinhuargdao 066004,China ) Abstract :In this paper ,the selection of raw materials ,the define of chemic ingredient and the process of nodularization and inocu 2lation were analyzed under the condition of electric induction furnace melt.The process to produce composition 2Q T450-10cast using a great deal waste steel was defined. K ey w ords :electric induction furnace ;waste steel ;composition 2Q T450-10 目前,国内许多厂家都是采用冲天炉焙炼生产球墨铸铁,生产技术工艺也趋于成熟、稳定。
使用废钢合成球墨铸铁的生产工艺研究和实践
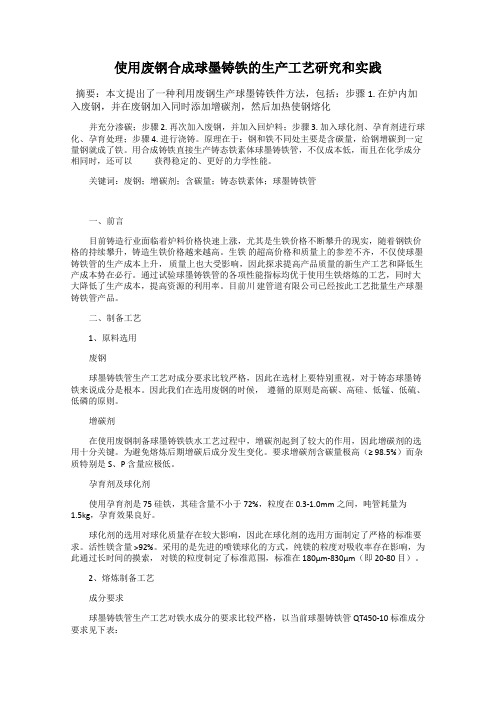
使用废钢合成球墨铸铁的生产工艺研究和实践摘要:本文提出了一种利用废钢生产球墨铸铁件方法,包括:步骤 1. 在炉内加入废钢,并在废钢加入同时添加增碳剂,然后加热使钢熔化并充分渗碳;步骤 2. 再次加入废钢,并加入回炉料;步骤 3. 加入球化剂、孕育剂进行球化、孕育处理;步骤 4. 进行浇铸。
原理在于:钢和铁不同处主要是含碳量,给钢增碳到一定量钢就成了铁。
用合成铸铁直接生产铸态铁素体球墨铸铁管,不仅成本低,而且在化学成分相同时,还可以获得稳定的、更好的力学性能。
关键词:废钢;增碳剂;含碳量;铸态铁素体;球墨铸铁管一、前言目前铸造行业面临着炉料价格快速上涨,尤其是生铁价格不断攀升的现实,随着钢铁价格的持续攀升,铸造生铁价格越来越高。
生铁的超高价格和质量上的参差不齐,不仅使球墨铸铁管的生产成本上升,质量上也大受影响,因此探求提高产品质量的新生产工艺和降低生产成本势在必行。
通过试验球墨铸铁管的各项性能指标均优于使用生铁熔炼的工艺,同时大大降低了生产成本,提高资源的利用率。
目前川建管道有限公司已经按此工艺批量生产球墨铸铁管产品。
二、制备工艺1、原料选用废钢球墨铸铁管生产工艺对成分要求比较严格,因此在选材上要特别重视,对于铸态球墨铸铁来说成分是根本。
因此我们在选用废钢的时候,遵循的原则是高碳、高硅、低锰、低硫、低磷的原则。
增碳剂在使用废钢制备球墨铸铁铁水工艺过程中,增碳剂起到了较大的作用,因此增碳剂的选用十分关键。
为避免熔炼后期增碳后成分发生变化。
要求增碳剂含碳量极高(≥ 98.5%)而杂质特别是 S、P 含量应极低。
孕育剂及球化剂使用孕育剂是 75 硅铁,其硅含量不小于 72%,粒度在 0.3-1.0mm之间,吨管耗量为1.5kg,孕育效果良好。
球化剂的选用对球化质量存在较大影响,因此在球化剂的选用方面制定了严格的标准要求。
活性镁含量 >92%。
采用的是先进的喷镁球化的方式,纯镁的粒度对吸收率存在影响,为此通过长时间的摸索,对镁的粒度制定了标准范围,标准在180μm-830μm(即 20-80 目)。
- 1、下载文档前请自行甄别文档内容的完整性,平台不提供额外的编辑、内容补充、找答案等附加服务。
- 2、"仅部分预览"的文档,不可在线预览部分如存在完整性等问题,可反馈申请退款(可完整预览的文档不适用该条件!)。
- 3、如文档侵犯您的权益,请联系客服反馈,我们会尽快为您处理(人工客服工作时间:9:00-18:30)。
使用废钢合成球墨铸铁的生产工艺研究和实践
发表时间:2020-03-19T02:52:51.750Z 来源:《建设者》2019年23期作者:曹二兵[导读] 用合成铸铁直接生产铸态铁素体球墨铸铁管,不仅成本低,而且在化学成分相同时,还可以获得稳定的、更好的力学性能。
芜湖新兴铸管有限责任公司安徽芜湖 241000摘要:本文提出了一种利用废钢生产球墨铸铁件方法,包括:步骤 1. 在炉内加入废钢,并在废钢加入同时添加增碳剂,然后加热使钢熔化
并充分渗碳;步骤 2. 再次加入废钢,并加入回炉料;步骤 3. 加入球化剂、孕育剂进行球化、孕育处理;步骤 4. 进行浇铸。
原理在于:钢和铁不同处主要是含碳量,给钢增碳到一定量钢就成了铁。
用合成铸铁直接生产铸态铁素体球墨铸铁管,不仅成本低,而且在化学成分相同时,还可以获得稳定的、更好的力学性能。
关键词:废钢;增碳剂;含碳量;铸态铁素体;球墨铸铁管一、前言
目前铸造行业面临着炉料价格快速上涨,尤其是生铁价格不断攀升的现实,随着钢铁价格的持续攀升,铸造生铁价格越来越高。
生铁的超高价格和质量上的参差不齐,不仅使球墨铸铁管的生产成本上升,质量上也大受影响,因此探求提高产品质量的新生产工艺和降低生产成本势在必行。
通过试验球墨铸铁管的各项性能指标均优于使用生铁熔炼的工艺,同时大大降低了生产成本,提高资源的利用率。
目前川建管道有限公司已经按此工艺批量生产球墨铸铁管产品。
二、制备工艺
1、原料选用
废钢
球墨铸铁管生产工艺对成分要求比较严格,因此在选材上要特别重视,对于铸态球墨铸铁来说成分是根本。
因此我们在选用废钢的时候,遵循的原则是高碳、高硅、低锰、低硫、低磷的原则。
增碳剂
在使用废钢制备球墨铸铁铁水工艺过程中,增碳剂起到了较大的作用,因此增碳剂的选用十分关键。
为避免熔炼后期增碳后成分发生变化。
要求增碳剂含碳量极高(≥ 98.5%)而杂质特别是 S、P 含量应极低。
孕育剂及球化剂使用孕育剂是 75 硅铁,其硅含量不小于 72%,粒度在 0.3-1.0mm之间,吨管耗量为 1.5kg,孕育效果良好。
球化剂的选用对球化质量存在较大影响,因此在球化剂的选用方面制定了严格的标准要求。
活性镁含量 >92%。
采用的是先进的喷镁球化的方式,纯镁的粒度对吸收率存在影响,为此通过长时间的摸索,对镁的粒度制定了标准范围,标准在 180μm-830μm(即 20-80 目)。
2、熔炼制备工艺成分要求
球墨铸铁管生产工艺对铁水成分的要求比较严格,以当前球墨铸铁管 QT450-10 标准成分要求见下表:
在实际生产过程中根据球墨铸铁管的管径可以适当的进行调整碳含量,调整原则为管径越小,碳含量可调整到上限,反之调整到下限。
炉料的温度控制
球墨铸铁金属液是 Fe-C-Si-O 合金液。
其内部存在化学反应及化学反应平衡问题。
平衡温度在 1390-1420 之间,故推荐球化处理温度为1450±20 为最佳温度。
当炉内铁水温度达到 1320℃左右时,清除铁水表面熔渣取样进行光谱分析,根据分析结果进行 C,Si 的调整,通过调整达到标准后将温度升至 1450 左右即可出铁进行球化,铁水制备程序完成,进入到球化喷镁进行球化处理。
熔炼工艺对材质的影响
对材质质量的影响。
首先,感应电炉熔炼时铁液温度可以提升到1550 度以上,并可以在高温状态下长时间保温,使原材料带入的夹杂物,以及在熔炼过程中形成的渣及夹杂物上浮至铁液表面。
对于废钢加增碳剂,尤其是粒子钢 + 废钢 + 增碳剂 + 回炉料,这些炉料无论是废钢、粒子钢,大都是白口组织,其具有较强的遗传性。
而消除遗传性就需要适当的提高熔化温度,增加保温时间,才能较好的净化铁液,减少铸件缺陷。
其次合金元素烧损量低,铁液中锰、硅的烧损较其他熔化方式低,便于各元素的调控,能够稳定化学成分。
第三,
用废钢加增碳剂生产合成铸铁时,由于废钢的夹杂物含量低,成分稳定,加增碳剂经高温熔炼之后消除了炉料的遗传性,铁液的纯净度得到提高,同时增碳剂具有孕育作用,使石墨化效果更加稳定突出,铸件的基体组织晶粒会更加均匀、细化,因此铸件材质的韧性和强度均得到提高。
三、产品质量检测
使用合成球墨铸铁生产的球墨铸铁管产品,经检测金相球化等级为2级( 最低不得低于3级 ), 石墨大小为7~8级( 最低不得低于6级 ), 石墨球数≥ 700 个每平方毫米,布氏硬度≤ 230。
铸管实体切割做力学性能试验,抗拉强度≥ 420,延伸率≥ 12%,完全符合产品要求。
(见图1、图 2)
废钢价格每吨在 2000 元左右,加上增碳、增硅成本,远低于生铁价格。
参考文献
范英俊杨彬球墨铸铁管生产工艺及装备;
宋协春王东废钢发展情况综述,中国装备 2009.3;
杨群收王志明废钢合成铸铁的发展前景,废钢加增碳剂冶炼球墨铸铁的研究;洪利兵阳家丽合成铸铁生产铸态铁素体铸件的工艺控制点。