杭州中瑞思创科技股份有限公司 精益推行年度总结报告
杭州中瑞思创科技股份有限公司 精益推行年度总结报告【用心整理精品资料】
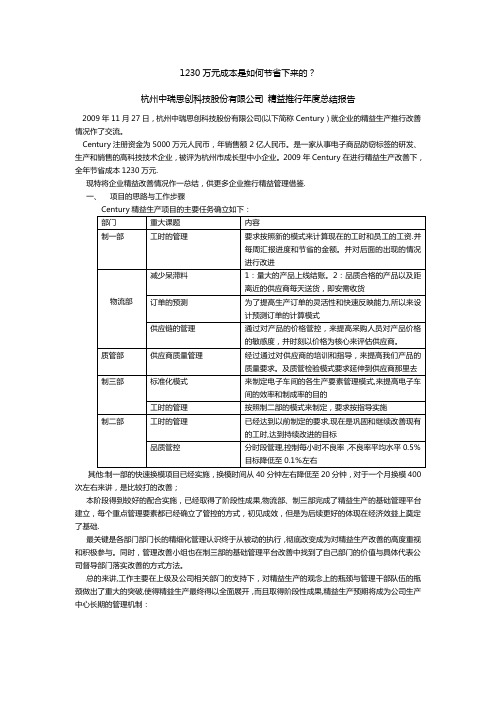
1230万元成本是如何节省下来的?杭州中瑞思创科技股份有限公司精益推行年度总结报告2009年11月27日,杭州中瑞思创科技股份有限公司(以下简称Century)就企业的精益生产推行改善情况作了交流。
Century注册资金为5000万元人民币,年销售额2亿人民币。
是一家从事电子商品防窃标签的研发、生产和销售的高科技技术企业,被评为杭州市成长型中小企业。
2009年Century在进行精益生产改善下,全年节省成本1230万元.现特将企业精益改善情况作一总结,供更多企业推行精益管理借鉴.一、项目的思路与工作步骤次左右来讲,是比较打的改善;本阶段得到较好的配合实施,已经取得了阶段性成果,物流部、制三部完成了精益生产的基础管理平台建立,每个重点管理要素都已经确立了管控的方式,初见成效,但是为后续更好的体现在经济效益上奠定了基础.最关键是各部门部门长的精细化管理认识终于从被动的执行,彻底改变成为对精益生产改善的高度重视和积极参与。
同时,管理改善小组也在制三部的基础管理平台改善中找到了自己部门的价值与具体代表公司督导部门落实改善的方式方法。
总的来讲,工作主要在上级及公司相关部门的支持下,对精益生产的观念上的瓶颈与管理干部队伍的瓶颈做出了重大的突破,使得精益生产最终得以全面展开,而且取得阶段性成果,精益生产预期将成为公司生产中心长期的管理机制:从全年的精益生产推进的角度看,一些改善数据可以说明生产管理发生了彻底的改变,这种变化有以下几个分类:(一)现场管理提升◎例:制造三部的标准化管理改善。
核心问题:制造三部精益生产推进开始几个月一直受阻,且实际的管理存在严重的问题,也就是说,制造三部并没有形成一个电子制品部基本的生产与管理平台,很多必须具备的生产作业环境与作业条件不具备,比如ESD失控,所以不良率达18%,品质与交货期处于失控状态,更不用成本挖潜.对策措施:全面辅导各管理要素改善,现在制造三部已经具备基本生产作业环境与作业条件,并且已经形成对过程管理的几个重要控制机制:工时管理(针对效率达成)、动线管理(针对多品种流水线人员管理)、分时段管理(针对设备、工艺及品控人员的过程控制实施)数据现状对比:稽核数据:改善前的稽核结果:不合格项253项,合格率46.28%,远低于合格线60%。
企业年度创新总结报告(优秀8篇)

企业年度创新总结报告(优秀8篇)企业年度创新总结报告(优秀8篇)企业年度创新总结报告要怎么写,才更标准规范?根据多年的文秘写作经验,参考优秀的企业年度创新总结报告样本能让你事半功倍,下面分享,供你选择借鉴。
企业年度创新总结报告篇1回望20_年的工作生活,感受到公司及身边的人这一年来发生的巨大变化,公司的项目发展得越来越多,身边的同事也都在不断进步着,朝着同一个目标奋斗。
新的一年到来了,也带来了新的挑战,在我们准备以全新的面貌来迎接新年的到来时,也不忘回顾和总结过去一年来所做的工作,现对我今年的工作做如下总结。
一、考勤管理每日对员工考勤单及请假单的处理。
出差人员根据公司传回的考勤数据对报销费用进行审核。
根据考勤数据审核工作人员的车费及餐费补贴。
每月根据考勤明细,认真做好考勤的统计,为造发工资带给依据,根据考勤统计状况,公布考勤通报。
根据每月考勤状况进行统计并作为转正考评、年终评优和年终奖的计算带给依据。
二、人事档案管理新员工入职时,告知准备所需的人事资料,根据员工带给的人事档案,建立人事档案。
建立员工花名册和人事台帐,做到电子版台帐和纸质档案相符。
负责管理和保管集团公司及下属公司所有员工的人事档案。
建立人事档案借阅登记表。
将集团公司及下属公司的离职档案进行整理,归入档案室。
完成了人事台帐汇总表的更新,根据领导指标及要求增加了人员编制及增减比率等栏目,集团公司及下属公司员工花名册上也相应增加了人员编制栏目,为人员招聘核编带给了便利。
三、招聘及储备工作了解各部门新增岗位的管理及各部门人员需求状况。
根据各部门人员的实际需求,有针对性、合理性招聘员工已配备各岗位。
透过采取一系列切实措施:广发招聘信息、网上招聘、内部员工推荐、现场招聘、贴招聘广告等各种途径招聘人才。
为更好地适应集团公司快速发展的需要,有效地推进公司人才储备工作,满足公司战略目标及业务发展对人才的需求,作好公司人才梯队建设,为员工带给发展晋升的平台。
精益年度工作总结汇报

THANKS
感谢观看
3
降低浪费和成本
通过消除生产过程中的浪费,降低运营成本,提 高资源利用效率。
精益团队建设规划
组建专业团队
成立专门的精益团队,负责推进精益改善项目,提供技术支持和指 导。
培养内部人才
通过内部培训和选拔,培养一批具备精益理念和技能的骨干员工, 形成精益改善的中坚力量。
加强团队协作
强化跨部门、跨岗位的协作与沟通,形成协同推进精益改善的良好局 面。
培训方式与内容创新
在培训过程中,采用了多种培训方式和手段,如课堂讲授、案例分析、小组讨论、实践操 作等,使培训内容更加生动有趣、易于理解和接受。同时,不断引入新的精益理念和方法 ,保持培训内容的更新和升级。
培训效果评估与反馈
对每场培训课程和活动都进行了效果评估和反馈收集,及时发现问题和不足,并采取相应 的措施进行改进和完善,确保培训效果的持续提升。
精益工作存在的问题
浪费现象严重
生产现场存在大量浪费现象,如过度生产、等待、 运输等,导致成本增加、效率低下。
流程不顺畅
部分流程存在瓶颈和不必要的环节,导致流程不 顺畅,影响工作效率和客户满意度。
员工参与度不高
员工对精益工作的参与度和积极性不高,缺乏持 续改进的动力。
原因分析
培训不足
公司对员工的精益培训不足,导致员工对精益理念和工具的认识 和掌握程度不够。
分析精益项目带来的成果和效益,包 括效率提升、成本降低、质量改善等 方面。
02
精益工作成果总览
精益项目数量及分布
项目数量
本年度共实施精益项目XX个,较 去年增长XX%。
项目分布
项目涵盖生产、销售、研发等多 个领域,其中生产领域项目占比 最大,达到XX%。
精益求精汽车行业年终总结

精益求精汽车行业年终总结一、引言精益求精是一种追求卓越的理念,让汽车行业充满活力和竞争力。
今年,我们公司在精益求精的指导下,取得了显著的成绩。
本文将对我们汽车行业在这一年所取得的成就和经验进行总结和分析。
二、市场情况分析1.全球汽车市场回顾今年全球汽车市场受到经济不确定性和贸易摩擦的影响,市场需求出现了波动。
不过,我们公司凭借出色的市场洞察和灵活的战略调整,成功应对了市场挑战。
2.国内汽车市场发展国内汽车市场在政府政策的支持下继续保持增长。
我们公司通过加强产品研发和提升品质,稳定了市场份额,并扩大了消费群体。
三、核心竞争力分析1.产品技术创新技术创新是精益求精的核心要素之一。
我们公司在这一年持续加大研发投入,推出了一系列具有竞争力的新产品。
这些产品不仅在节能环保、安全性能上有所突破,还融入了人工智能和互联网技术,提升了用户体验,并获得了市场的认可和好评。
2.生产流程优化精益求精的理念体现在生产流程的优化上。
我们公司通过引进先进的生产设备和制度管理的改进,大幅提高了生产效率和产品质量。
同时,我们也注重员工培训,提升团队协作能力,从而实现了生产流程的精益化。
3.营销策略创新市场竞争激烈,营销策略的创新至关重要。
我们公司通过整合线上线下资源,加强品牌推广和市场宣传,有效提升了品牌知名度和市场份额。
同时,我们也加大了与经销商和合作伙伴的合作,拓展销售渠道,加深品牌与消费者之间的连接。
四、面临的挑战与机遇1.挑战:新能源汽车市场竞争新能源汽车市场竞争激烈,技术更新换代快。
我们公司将加大在新能源领域的研发投入,提升产品技术和市场竞争力。
2.机遇:智能出行时代智能出行时代的到来给汽车行业带来了巨大机遇。
我们公司将加大对智能化技术的研发和应用,推出更多智能化产品,以满足用户对便捷出行的需求。
五、未来发展策略1.继续推进技术创新技术是精益求精的核心,我们将继续加大研发投入,不断推出具有竞争力的新产品。
同时,我们还将积极与科研院校和合作伙伴合作,加强技术交流和创新合作。
中瑞思创:2010年第三季度报告全文 2010-10-22

杭州中瑞思创科技股份有限公司2010年第三季度季度报告全文§1 重要提示1.1 本公司董事会、监事会及董事、监事、高级管理人员保证本报告所载资料不存在任何虚假记载、误导性陈述或者重大遗漏,并对其内容的真实性、准确性和完整性承担个别及连带责任。
1.2 公司第三季度财务报告未经会计师事务所审计。
1.3 公司负责人路楠、主管会计工作负责人蓝宗烛及会计机构负责人(会计主管人员)蓝宗烛声明:保证季度报告中财务报告的真实、完整。
§2 公司基本情况2.1 主要会计数据及财务指标单位:元本报告期末上年度期末本报告期末比上年度期末增减(%)总资产1,181,652,366.46 199,547,581.22 492.17%归属于公司普通股股东的所有者权益(或股东权益)1,139,402,157.42 140,180,594.01 712.81% 归属于公司普通股股东的每股净资产(元/股)17.01 2.80 507.50%年初至报告期期末比上年同期增减(%)经营活动产生的现金流量净额43,272,338.61 8.24% 每股经营活动产生的现金流量净额(元/股)0.65 -18.75%报告期比上年同期增减(%)年初至报告期期末比上年同期增减(%)营业收入88,052,616.63 50.31% 229,401,955.08 55.29% 归属于公司普通股股东的净利润25,270,331.38 18.51% 65,138,563.41 59.88% 基本每股收益(元/股)0.38 -11.63% 1.10 35.80% 稀释每股收益(元/股)0.38 -11.63% 1.10 35.80% 净资产收益率(%) 2.24% -17.06% 9.42% -31.00% 扣除非经常性损益后的净资产收益率(%) 2.22% -13.38% 9.24% -25.89%非经常性损益项目年初至报告期期末金额非流动资产处置损益34,336.80计入当期损益的政府补助,但与公司正常经营业务密切相关,符合国家政策规定、按照一定标准定额或定量持续享受的政府补助除外1,428,764.00 除上述各项之外的其他营业外收入和支出-25,000.00 减:企业所得税影响数(所得税减少以“-”表示)215,715.12合计1,222,385.682.2 报告期末股东总人数及前十名无限售条件股东持股情况表单位:股报告期末股东总数(户)7,764前十名无限售条件流通股股东持股情况股东名称(全称)期末持有无限售条件流通股的数量种类全国社保基金六零二组合349,719 人民币普通股中国工商银行-汇添富均衡增长股票型证券投资基金338,224 人民币普通股中国工商银行-建信优选成长股票型证券投资基金242,718 人民币普通股建信基金公司-建行-建信灵动精选资产管理计划200,000 人民币普通股吕剑锋179,950 人民币普通股姚文莉130,000 人民币普通股王斐126,084 人民币普通股宋建124,400 人民币普通股张颖112,600 人民币普通股建信基金公司-建行-建信灵动精选2号资产管理计划112,200 人民币普通股2.3 限售股份变动情况表单位:股股东名称期初限售股数本期解除限售股数本期增加限售股数期末限售股数限售原因解除限售日期路楠22,500,000 0 0 22,500,000 首发承诺2013年4月30日俞国骅21,100,000 0 0 21,100,000 首发承诺2011年4月30日杭州博泰投资管理有限公司3,000,000 0 0 3,000,000 首发承诺2013年4月30日张佶1,000,000 0 0 1,000,000 首发承诺2011年4月30日商巍750,000 0 0 750,000 首发承诺2011年4月30日陈武军500,000 0 0 500,000 首发承诺2011年4月30日蒋士平500,000 0 0 500,000 首发承诺2011年4月30日蓝宗烛400,000 0 0 400,000 首发承诺2011年4月30日王勇250,000 0 0 250,000 首发承诺2011年4月30日网下配售3,400,000 3,400,000 0 0 网下配售规定2010年7月30日合计53,400,000 3,400,000 0 50,000,000 --§3 管理层讨论与分析3.1 公司主要财务报表项目公司主要财务报表项目、、财务指标大幅度变动的情况及原因√适用□不适用(1) 截至2010年9月30日,公司货币资金为102,309.06万元,较年初增加95,865.71 万元,增长1487.83%。
精益求精提升运营效率年度运营管理年终总结
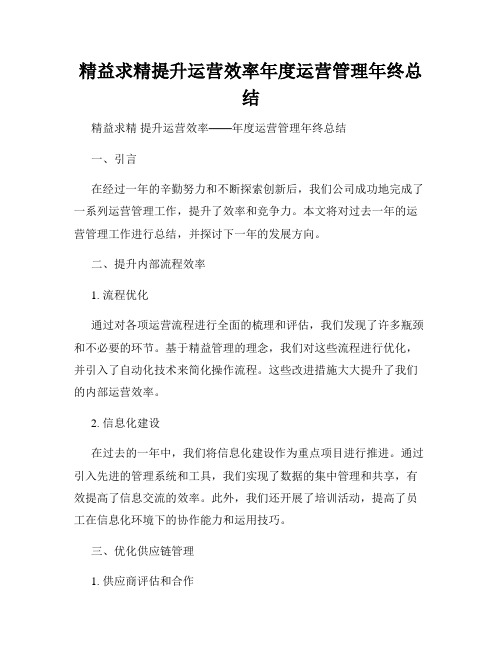
精益求精提升运营效率年度运营管理年终总结精益求精提升运营效率——年度运营管理年终总结一、引言在经过一年的辛勤努力和不断探索创新后,我们公司成功地完成了一系列运营管理工作,提升了效率和竞争力。
本文将对过去一年的运营管理工作进行总结,并探讨下一年的发展方向。
二、提升内部流程效率1. 流程优化通过对各项运营流程进行全面的梳理和评估,我们发现了许多瓶颈和不必要的环节。
基于精益管理的理念,我们对这些流程进行优化,并引入了自动化技术来简化操作流程。
这些改进措施大大提升了我们的内部运营效率。
2. 信息化建设在过去的一年中,我们将信息化建设作为重点项目进行推进。
通过引入先进的管理系统和工具,我们实现了数据的集中管理和共享,有效提高了信息交流的效率。
此外,我们还开展了培训活动,提高了员工在信息化环境下的协作能力和运用技巧。
三、优化供应链管理1. 供应商评估和合作我们成立了供应商评估团队,对现有供应商进行综合评估,并与高质量供应商建立了长期稳定的合作关系。
这样一来,我们不仅保证了原材料的质量和供应的及时性,还降低了采购成本,提高了供应链的稳定性。
2. 库存管理优化通过建立库存管理系统,我们能够实时跟踪和控制库存水平。
基于市场需求和销售数据,我们优化了库存的存储和调拨,以避免过量投资和库存积压。
这项改进大大提高了我们的运营效率,减少了库存风险。
四、加强人力资源管理1. 员工培训与发展我们注重员工的培训与发展,通过组织内外部培训、轮岗和参与项目等方式,不断提高员工的专业能力和综合素质。
同时,我们鼓励员工分享经验和知识,促进团队合作,激发员工的创造力和工作热情。
2. 激励机制优化我们对激励机制进行了全面评估,并结合公司战略目标进行了调整。
通过合理的薪酬制度、福利待遇和晋升机制,我们增强了员工的工作动力和归属感。
这项改进不仅有助于留住人才,还提升了员工的工作效率和质量。
五、加强与合作伙伴的沟通和协作1. 外部合作加强我们积极与合作伙伴进行沟通和交流,共同解决运营中的问题和挑战。
年末公司创新工作总结写法7篇
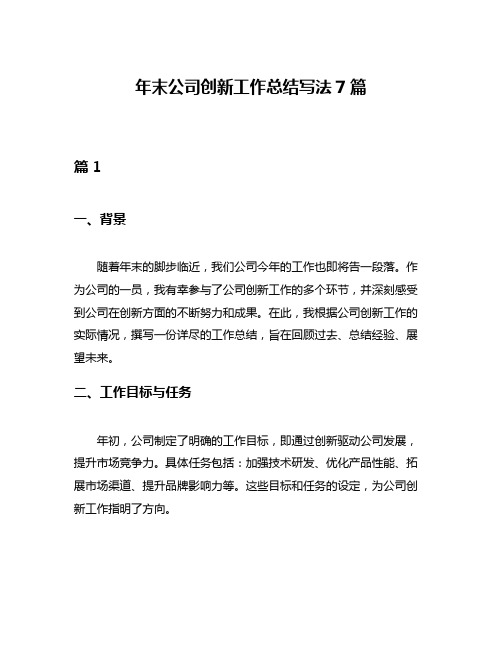
年末公司创新工作总结写法7篇篇1一、背景随着年末的脚步临近,我们公司今年的工作也即将告一段落。
作为公司的一员,我有幸参与了公司创新工作的多个环节,并深刻感受到公司在创新方面的不断努力和成果。
在此,我根据公司创新工作的实际情况,撰写一份详尽的工作总结,旨在回顾过去、总结经验、展望未来。
二、工作目标与任务年初,公司制定了明确的工作目标,即通过创新驱动公司发展,提升市场竞争力。
具体任务包括:加强技术研发、优化产品性能、拓展市场渠道、提升品牌影响力等。
这些目标和任务的设定,为公司创新工作指明了方向。
三、工作进展与成果1. 技术研发:公司在技术研发方面取得了显著进展。
通过加大投入和引进先进技术,公司在多个关键技术领域实现了突破。
例如,在人工智能算法、大数据分析等方面取得了重要成果,为后续产品优化和市场拓展提供了有力支持。
2. 产品性能优化:针对公司产品性能的提升,我们进行了持续的技术攻关和创新实践。
通过对产品进行不断优化和改进,公司产品性能得到了显著提升,用户满意度也随之提高。
3. 市场渠道拓展:公司在市场渠道拓展方面取得了显著成效。
通过线上线下多渠道营销策略,公司成功开拓了多个新市场领域,产品销量和市场份额均有所增长。
同时,公司还加强了与合作伙伴的合作关系,为后续发展奠定了坚实基础。
4. 品牌影响力提升:公司在品牌建设方面取得了显著成果。
通过加强品牌宣传和推广,公司品牌知名度和美誉度均有所提升。
同时,公司还获得了多项行业荣誉和奖项,进一步提升了品牌影响力。
四、面临的挑战与问题在取得成绩的同时,我们也清醒地认识到公司在创新工作中面临的一些挑战与问题。
例如,技术研发过程中的人才短缺和技术更新迅速问题;产品性能优化过程中的质量控制和稳定性问题;市场渠道拓展过程中的竞争激烈和渠道成本问题;品牌影响力提升过程中的品牌维护和推广策略问题等。
这些挑战与问题的存在,对我们公司的创新工作提出更高的要求和期待。
五、解决方案与建议针对上述挑战与问题,我们提出以下解决方案与建议:1. 加强人才培养和引进:通过加大人才培养力度和引进优秀技术人才,解决人才短缺问题;同时,建立完善的人才培养机制和激励机制,激发员工的创新活力和创造力。
创新年终总结文稿范文(3篇)

第1篇尊敬的各位领导、亲爱的同事们:随着2021年的落幕,我们站在了新的起点上。
在过去的一年里,创新公司在全体员工的共同努力下,取得了令人瞩目的成绩。
在此,我代表公司对大家表示衷心的感谢,并对2021年的工作进行总结,对2022年的工作进行展望。
一、2021年工作回顾1. 业绩成果2021年,创新公司在市场竞争激烈的环境中,实现了业绩的稳步增长。
以下是部分关键业绩指标:(1)营业额同比增长15%,达到XX亿元。
(2)净利润同比增长20%,达到XX亿元。
(3)研发投入占比达到XX%,研发成果丰硕。
2. 产品创新(1)成功研发并上市了XX款新产品,满足了市场多样化需求。
(2)对现有产品进行升级,提升了产品竞争力。
(3)积极参与行业标准制定,推动行业发展。
3. 市场拓展(1)拓展了XX个新市场,实现了业务的多元化。
(2)与XX家国内外知名企业建立了合作关系。
(3)品牌知名度进一步提升,市场份额不断扩大。
4. 团队建设(1)优化了人才引进机制,引进了一批高素质人才。
(2)开展了各类培训活动,提升了员工的专业技能和综合素质。
(3)完善了绩效考核体系,激发了员工的工作积极性。
5. 社会责任(1)积极参与公益事业,捐赠物资价值XX万元。
(2)推动绿色生产,降低能耗,减少污染物排放。
(3)关注员工身心健康,举办各类文体活动。
二、2021年工作亮点1. 创新驱动创新公司始终坚持以创新为核心驱动力,不断推动技术、产品、管理等方面的创新,为公司发展注入源源不断的活力。
2. 市场导向紧密关注市场需求,及时调整战略方向,确保公司产品始终处于市场前沿。
3. 团队协作全体员工团结一心,齐心协力,共同为实现公司目标而努力。
4. 可持续发展坚持可持续发展理念,关注环境保护,推动公司可持续发展。
三、2022年工作展望1. 业绩目标(1)营业额同比增长XX%,达到XX亿元。
(2)净利润同比增长XX%,达到XX亿元。
2. 产品研发(1)投入XX亿元用于研发,确保产品创新。
标杆精益qcc年终总结
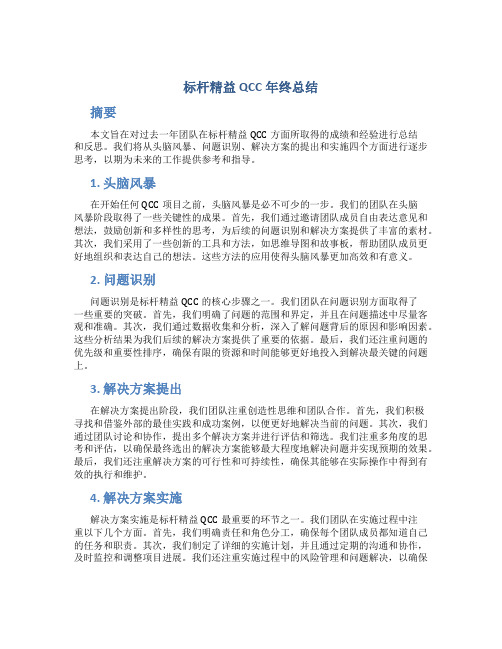
标杆精益QCC年终总结摘要本文旨在对过去一年团队在标杆精益QCC方面所取得的成绩和经验进行总结和反思。
我们将从头脑风暴、问题识别、解决方案的提出和实施四个方面进行逐步思考,以期为未来的工作提供参考和指导。
1. 头脑风暴在开始任何QCC项目之前,头脑风暴是必不可少的一步。
我们的团队在头脑风暴阶段取得了一些关键性的成果。
首先,我们通过邀请团队成员自由表达意见和想法,鼓励创新和多样性的思考,为后续的问题识别和解决方案提供了丰富的素材。
其次,我们采用了一些创新的工具和方法,如思维导图和故事板,帮助团队成员更好地组织和表达自己的想法。
这些方法的应用使得头脑风暴更加高效和有意义。
2. 问题识别问题识别是标杆精益QCC的核心步骤之一。
我们团队在问题识别方面取得了一些重要的突破。
首先,我们明确了问题的范围和界定,并且在问题描述中尽量客观和准确。
其次,我们通过数据收集和分析,深入了解问题背后的原因和影响因素。
这些分析结果为我们后续的解决方案提供了重要的依据。
最后,我们还注重问题的优先级和重要性排序,确保有限的资源和时间能够更好地投入到解决最关键的问题上。
3. 解决方案提出在解决方案提出阶段,我们团队注重创造性思维和团队合作。
首先,我们积极寻找和借鉴外部的最佳实践和成功案例,以便更好地解决当前的问题。
其次,我们通过团队讨论和协作,提出多个解决方案并进行评估和筛选。
我们注重多角度的思考和评估,以确保最终选出的解决方案能够最大程度地解决问题并实现预期的效果。
最后,我们还注重解决方案的可行性和可持续性,确保其能够在实际操作中得到有效的执行和维护。
4. 解决方案实施解决方案实施是标杆精益QCC最重要的环节之一。
我们团队在实施过程中注重以下几个方面。
首先,我们明确责任和角色分工,确保每个团队成员都知道自己的任务和职责。
其次,我们制定了详细的实施计划,并且通过定期的沟通和协作,及时监控和调整项目进展。
我们还注重实施过程中的风险管理和问题解决,以确保项目能够按时和高质量地完成。
公司研发年终总结范文(3篇)

第1篇一、前言时光荏苒,岁月如梭。
转眼间,我们又迎来了新的一年。
在这辞旧迎新的时刻,我谨代表公司研发部门,对过去一年的工作进行总结,对全体研发团队的辛勤付出表示衷心的感谢。
以下是对公司研发部门过去一年的工作回顾和总结。
二、工作回顾(一)项目进展与成果1. 重点项目完成情况在过去的一年里,我部门承担了多个重点项目,包括产品研发、技术升级、系统集成等。
经过全体研发人员的共同努力,以下项目取得了显著成果:- 新产品研发:成功研发了XX型号产品,该产品在性能、稳定性、用户体验等方面均达到行业领先水平。
- 技术升级:完成了XX系统升级,提高了系统运行效率,降低了故障率。
- 系统集成:完成了XX项目的系统集成,确保了项目按时交付。
2. 专利申请与授权在过去的一年里,我部门共申请专利XX项,其中发明专利XX项,实用新型专利XX项。
截止目前,已有XX项专利获得授权。
(二)团队建设与人才培养1. 团队建设为了提升团队整体实力,我们加强了团队建设,开展了以下工作:- 定期组织技术分享会,提升团队成员技术水平。
- 加强团队沟通与协作,提高工作效率。
- 建立健全绩效考核制度,激发员工积极性。
2. 人才培养在人才培养方面,我们采取了以下措施:- 开展新员工入职培训,帮助新员工快速融入团队。
- 组织内部技术竞赛,激发员工学习热情。
- 鼓励员工参加外部培训,提升个人能力。
(三)质量管理与风险控制1. 质量管理体系我部门始终坚持“质量第一”的原则,不断完善质量管理体系,确保产品和服务质量。
主要措施如下:- 建立健全质量管理制度,明确各部门职责。
- 加强过程控制,确保产品和服务质量。
- 定期进行质量审核,及时发现和解决质量问题。
2. 风险控制针对研发过程中可能出现的风险,我们采取了以下措施:- 制定风险管理计划,明确风险识别、评估和控制措施。
- 加强项目风险管理,确保项目顺利进行。
- 建立应急响应机制,及时应对突发事件。
三、工作总结与反思(一)工作亮点1. 研发成果丰硕:过去一年,我部门在项目研发、技术升级、系统集成等方面取得了显著成果,为公司创造了良好的经济效益。
精密科技年度总结汇报(3篇)
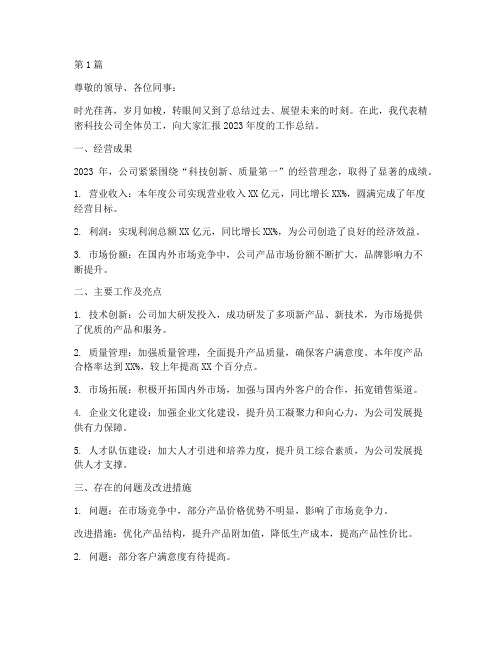
第1篇尊敬的领导、各位同事:时光荏苒,岁月如梭,转眼间又到了总结过去、展望未来的时刻。
在此,我代表精密科技公司全体员工,向大家汇报2023年度的工作总结。
一、经营成果2023年,公司紧紧围绕“科技创新、质量第一”的经营理念,取得了显著的成绩。
1. 营业收入:本年度公司实现营业收入XX亿元,同比增长XX%,圆满完成了年度经营目标。
2. 利润:实现利润总额XX亿元,同比增长XX%,为公司创造了良好的经济效益。
3. 市场份额:在国内外市场竞争中,公司产品市场份额不断扩大,品牌影响力不断提升。
二、主要工作及亮点1. 技术创新:公司加大研发投入,成功研发了多项新产品、新技术,为市场提供了优质的产品和服务。
2. 质量管理:加强质量管理,全面提升产品质量,确保客户满意度。
本年度产品合格率达到XX%,较上年提高XX个百分点。
3. 市场拓展:积极开拓国内外市场,加强与国内外客户的合作,拓宽销售渠道。
4. 企业文化建设:加强企业文化建设,提升员工凝聚力和向心力,为公司发展提供有力保障。
5. 人才队伍建设:加大人才引进和培养力度,提升员工综合素质,为公司发展提供人才支撑。
三、存在的问题及改进措施1. 问题:在市场竞争中,部分产品价格优势不明显,影响了市场竞争力。
改进措施:优化产品结构,提升产品附加值,降低生产成本,提高产品性价比。
2. 问题:部分客户满意度有待提高。
改进措施:加强客户服务体系建设,提高服务质量,关注客户需求,提升客户满意度。
四、2024年工作展望1. 深化科技创新,提升产品竞争力。
2. 加强市场拓展,扩大市场份额。
3. 优化内部管理,提高运营效率。
4. 持续加强人才队伍建设,为公司发展提供人才保障。
5. 深入推进企业文化建设,提升员工凝聚力和向心力。
总之,2023年精密科技公司取得了丰硕的成果,但我们深知,成绩属于过去,未来仍需努力。
在新的一年里,我们将继续发扬拼搏精神,为实现公司高质量发展而努力奋斗!谢谢第2篇尊敬的领导,各位同事:时光荏苒,转眼间又到了年终总结的时刻。
中瑞思创:国信证券股份有限公司关于公司持续督导期间跟踪报告 2011-03-18

国信证券股份有限公司关于杭州中瑞思创科技股份有限公司持续督导期间跟踪报告国信证券股份有限公司(以下简称“国信证券”)作为杭州中瑞思创科技股份有限公司(以下简称“中瑞思创”、“公司”)的保荐人,根据《证券发行上市保荐业务管理办法》、《深圳证券交易所创业板股票上市规则》等有关规定,对中瑞思创2010年度规范运作的情况进行了跟踪,具体情况如下:一、中瑞思创执行并完善防止控股股东、实际控制人及其他关联方违规占用公司资源制度的情况(一)中瑞思创控股股东、实际控制人中瑞思创的控股股东和实际控制人为公司董事长路楠。
截至本报告出具之日,路楠直接持有公司2,250万股股份,占总股本的33.58%,同时还通过控股杭州博泰投资管理有限公司间接持有公司172.07万股股份,占总股本的2.57%。
路楠直接和间接合计持有公司36.15%的股份,是公司的实际控制人。
(二)中瑞思创执行并完善防止控股股东、实际控制人及其他关联方违规占用公司资源制度的情况中瑞思创按照《公司法》、《上市公司章程指引》等有关法律法规及相关规定,制定了《公司章程》、《股东大会议事规则》、《董事会议事规则》、《关联交易管理办法》等规章制度,建立了规范健全的法人治理结构,公司及控股子公司均按照有关法律法规的要求规范运作,防止控股股东、实际控制人及其他关联方违规占用公司资源。
保荐人通过访谈相关人员、查阅公司财务报告及股东大会、董事会、监事会相关文件及其他资料后认为:公司较好地执行并完善了防止控股股东、实际控制人及其他关联方违规占用公司资源的制度,不存在控股股东、实际控制人及其他关联方违规占用公司资源的情况。
二、中瑞思创执行并完善防止其董事、监事、高级管理人员利用职务之便损害公司利益的内控制度情况(一)中瑞思创具有健全的组织机构公司根据《公司法》、《公司章程》的相关规定,建立了股东大会、董事会、监事会、经理层等组织机构,在董事会下设置了战略决策委员会、提名委员会、薪酬与考核委员会、审计委员会等四个专门委员会,并建立了独立董事制度和董事会秘书制度。
精密科技年度总结报告(3篇)

第1篇一、前言随着科技的不断发展,精密科技在我国产业升级中扮演着越来越重要的角色。
在过去的一年里,我公司紧密围绕市场需求,不断提升产品研发能力,优化生产流程,强化质量管理,取得了显著的成果。
现将本年度工作总结如下:一、研发成果丰硕1. 新产品研发:本年度,我公司成功研发了XX系列精密产品,该产品具有高性能、高精度、环保节能等特点,填补了国内空白,赢得了市场的广泛认可。
2. 技术创新:针对现有产品,我们持续进行技术改进,提高产品性能,降低成本。
本年度,共申请专利XX项,授权XX项。
二、生产流程优化1. 生产线改造:为了提高生产效率,降低能耗,我们对现有生产线进行了全面升级改造,实现了自动化、智能化生产。
2. 原材料采购:加强原材料采购管理,严格控制采购成本,确保原材料质量。
三、质量管理提升1. 质量体系完善:本年度,我们进一步完善了质量管理体系,严格执行ISO9001质量管理体系标准,确保产品质量。
2. 员工培训:加强员工质量意识培训,提高员工操作技能,降低不良品率。
四、市场营销拓展1. 市场调研:针对市场需求,开展市场调研,了解客户需求,为产品研发和市场推广提供依据。
2. 市场推广:加大市场推广力度,积极参加国内外展会,提升公司品牌知名度。
五、总结与展望1. 总结:过去的一年,我公司取得了丰硕的成果,在研发、生产、质量、市场等方面取得了显著进步。
2. 展望:在新的一年里,我们将继续加大研发投入,提升产品竞争力;优化生产流程,降低生产成本;加强质量管理,提高产品质量;拓展市场,提升品牌知名度,为实现公司持续发展奠定坚实基础。
总之,本年度我公司取得了可喜的成绩,但同时也面临着诸多挑战。
在新的一年里,我们将继续努力,为实现公司战略目标而不懈奋斗。
第2篇一、前言2021年,我国精密科技行业在国内外市场需求的推动下,取得了显著的成果。
在全体员工的共同努力下,本公司在技术创新、市场拓展、管理优化等方面取得了丰硕的成果。
精益研发工作情况汇报

精益研发工作情况汇报一、前言近年来,我部门一直致力于精益研发工作,以提高研发效率、降低成本、缩短产品开发周期为目标,不断推进全面质量管理,全面实施精益生产。
在上级领导的关心支持和各部门的通力合作下,我部门在精益研发工作中取得了一些成绩和经验。
现就我部门的精益研发工作情况向领导汇报如下:二、工作基本情况(一)在精益研发工作方面,我部门对研发流程进行了分析与优化。
通过分析研发流程,明确了研发工作中的关键节点和痛点,找出了流程中的弊端和隐患。
在此基础上,我部门通过优化流程、改造设备、提高人员素质等措施,取得了明显的效果。
比如,我们对研发流程进行重新设计,优化了研发步骤,缩短了开发周期;对设备进行改造和更新,提高了生产效率;对人员进行培训和激励,提高了工作质量。
所有这些举措都为精益研发工作的顺利进行打下了良好基础。
(二)在精益研发工作中,我部门重视精益生产管理。
我们通过引进先进的生产管理理念和方法,不断提高生产效率,优化生产资源配置,降低生产成本。
比如,我们采用了精益生产中的7大浪本,即延迟决策、多变生产、过度生产、物料运输、物料处理、等待、库存。
根据这些浪本,我们优化了生产流程,并建立了精益生产与管理的体系,有效降低了生产成本和浪费。
(三)在精益研发工作中,我部门还重点关注了产品质量。
我们提高了员工的质量意识,加强了全员质量教育,建立了完善的品质管理体系,不断提高产品质量和市场竞争力。
比如,我们建立了产品质量信息反馈系统,及时发现和解决产品质量问题;采取了精益研发工具,不断改进产品设计和生产工艺,确保产品质量符合客户要求。
通过这些举措,我们明显提高了产品质量,获得了客户的信赖和好评。
三、存在的问题在精益研发工作中,我们也遇到了一些问题。
比如,生产线上存在不稳定性、效率低下等问题;产品质量管理不到位,存在着成本偏高的情况;员工的培训意识不强,影响了顺利进行精益研发工作等。
为了解决这些问题,我们下一步的工作计划是……四、未来工作计划(一)继续优化研发流程。
质量管理精髓与推行

泰勒制案例:产线平衡案例剖析
工位
总装1:李 武军
总1
总装2:刘 家才
总2
序号
1
2 3 4 5 6 7 8 9 10 11 12 13 14 15 16
17 18 19 20 21 22 23 24 25 26 27 28 29 30
车同轨,书同 文,质量才能
做好!
质量及其管理的概念
•
ISO8402-1994【质量管理和
质量保证术语】中对质量的定义
:质量是反映实体(产品,过程
或者服务等)满足明确或隐含所
需要的能力的特征总和。
•
质量包括产品质量,过程质
量和服务质量。质量的形成过程
成为工程,过程质量即工程质量
,是产品质量的保证。服务可统
• 中国古代的质量观与成就 • 理解质量与管理概念 • 西方工业革命的质量管理的萌芽 • 理解质量与标准化
2.质量检验时期
• 泰勒制案例 • QC的组织与分类 • IPQC分时段管理案例分析 • SOP的案例 • 海尔的案例视频
目录(精髓,人物与推行技术)
3.统计质量控制时期
– 休哈特的SPC – QC七大手法收集与处理数据 – 戴明14法
称为工作,工作质量是工程质量
的保证。
质量 手册
程序文件
质量计划/作业指导书/操 作规程/检验标准
表格/记录/分析报告/档案等
质量萌芽阶段(质量的史前文明---1875年 前)西方
工业革命以前质量管理经过了漫长 的“蒙昧时期”
•这个阶段生产方式主要是手工作坊 ,质量控制依靠工匠或艺人自己来 控制。
•从手工作坊到工业革命,不可避免 地产生了管理实践和管理科学,质 量管理也就应运而生了。
SMT年终总结

SMT年终总结SMT年终总结一、引言在过去一年的工作中,SMT团队取得了非常显著的成绩。
本文档将对我们的工作进行总结和回顾,包括项目进展、团队合作、技术创新、市场表现等方面。
同时,我们还会分析当前的问题和挑战,并提出改进和发展的建议和计划。
二、项目进展2.1 项目1在项目1中,我们成功完成了新产品的研发和上市,取得了极高的市场反应。
我们投入了大量的研究和开发资源,设计出了具有创新性和竞争力的产品,并进行了精确的生产和品质控制。
通过有效的市场推广和销售策略,我们取得了出色的销售业绩。
2.2 项目2在项目2中,我们面临了一些挑战,包括市场需求的变化和竞争的加剧。
我们采取了灵活的策略和行动,及时调整了产品定位和市场定位,积极寻找新的合作伙伴和渠道。
虽然我们还存在一些问题,但我们相信我们可以通过持续努力和创新来克服这些挑战。
三、团队合作3.1 内部合作我们团队内部的合作非常紧密和高效。
每个成员都充分发挥了自己的专业能力和经验,相互支持和合作。
我们通过定期的会议和沟通,及时解决了工作中的问题,并确保项目按时完成。
3.2 外部合作我们与外部合作伙伴的合作也非常成功。
我们与供应商和客户保持密切的联系和沟通,共同解决了一系列的问题和挑战。
我们建立了良好的合作关系,并互相支持和信任。
四、技术创新4.1 新技术应用我们团队在技术创新方面取得了显著的进展。
我们成功应用了一系列新的技术,提高了产品的性能和质量。
我们还不断推动技术的研发和改进,保持在市场上的竞争优势。
4.2 知识分享和学习我们注重团队成员的知识分享和学习,定期组织技术培训和研讨会,推动团队的整体素质提升。
我们还鼓励团队成员积极参与行业会议和交流活动,扩大视野和增加经验。
五、市场表现我们在市场上取得了良好的表现。
我们成功进军了新的市场,扩大了市场份额。
我们与客户建立了长期稳定的合作关系,并得到了客户的高度认可和赞赏。
六、问题与挑战在工作中,我们也遇到了一些问题和挑战。
企业技术创新年度工作总结汇报

企业技术创新年度工作总结汇报尊敬的领导、各位同事:大家好!在过去的一年里,我们企业在技术创新方面取得了一系列的成绩和进展。
在这里,我将对我们企业技术创新年度工作进行总结汇报,希望能够得到大家的认可和支持。
首先,我们在技术研发方面取得了一定的突破。
我们不断加大对技术研发的投入,引进了一批高水平的技术人才,加强了研发团队的建设。
通过不懈努力,我们成功研发出了一系列具有自主知识产权的产品和技术,为企业的发展壮大提供了有力的支撑。
其次,我们在技术创新管理方面也取得了一些成果。
我们建立了完善的技术创新管理体系,加强了对技术创新项目的规划和管理,提高了技术创新项目的成功率和效益。
同时,我们还加强了对技术创新成果的保护和运用,确保了企业技术创新成果的最大化利用。
最后,我们在技术创新应用方面也取得了一定的成绩。
我们积极推进技术创新成果的应用和推广,为企业的生产经营提供了更多的技术支持。
我们还加强了对技术创新成果的市场开发和营销,为企业的产品和服务赢得了更多的市场份额和竞争优势。
总的来说,我们在过去的一年里在技术创新方面取得了一系列的成绩和进展,为企业的发展壮大做出了积极的贡献。
但是,我们也清醒地认识到,在技术创新的道路上,还有很多困难和挑战需要我们克服和应对。
我们将继续加大对技术创新的投入,加强对技术创新项目的管理,不断提升技术创新的能力和水平,为企业的可持续发展做出更大的贡献。
最后,我谨代表技术创新团队,向全体员工表示诚挚的感谢和衷心的祝福!让我们携手并进,共同开创企业技术创新的美好未来!谢谢大家!。
技术年中总结范文

您好!转眼间,2022年上半年已经过去,我在公司技术部门度过了充实而忙碌的半年。
现将我在上半年的工作总结如下:一、工作回顾1. 技术研发在上半年,我积极参与了公司多项技术项目的研发工作。
针对公司产品在市场上存在的问题,我主动与研发团队沟通,提出改进建议,为产品优化升级提供了有力支持。
在项目实施过程中,我严格按照研发流程,确保项目进度和质量。
2. 技术培训为了提高公司员工的技术水平,我组织了多场技术培训,内容包括新工艺、新技术、新设备的操作与维护等。
通过培训,员工们对新技术有了更深入的了解,为公司的技术创新奠定了基础。
3. 技术支持在日常工作中,我积极为各部门提供技术支持,解决生产过程中遇到的技术难题。
通过与各部门的密切合作,确保了生产线的稳定运行。
4. 技术交流为了拓宽视野,提高自己的技术水平,我积极参加各类技术交流活动,与同行分享经验,学习先进技术。
同时,我还主动与公司内部其他部门沟通,促进跨部门的技术交流与合作。
二、工作亮点1. 成功研发新型工艺,提高生产效率20%。
2. 优化生产流程,降低生产成本10%。
3. 通过技术培训,提高员工技能水平,为公司的技术创新和人才培养做出贡献。
4. 积极参与技术交流活动,为公司带来新的技术信息。
三、工作不足1. 在技术研发方面,对部分新技术的掌握还不够深入,需要加强学习。
2. 在技术培训方面,培训内容有待进一步丰富,以满足不同部门的需求。
3. 在技术支持方面,对部分疑难问题的解决速度还有待提高。
四、下半年工作计划1. 深入学习新技术,提高自己的技术水平。
2. 优化技术培训体系,提高培训效果。
3. 加强与各部门的沟通与协作,提高技术支持质量。
4. 积极参与公司技术项目的研发,为公司的技术创新贡献力量。
5. 深入了解市场动态,为公司产品研发提供有力支持。
总结,2022年上半年我在工作中取得了一定的成绩,但同时也暴露出一些不足。
在接下来的时间里,我将继续努力,不断提升自己的综合素质,为公司的发展贡献自己的力量。
- 1、下载文档前请自行甄别文档内容的完整性,平台不提供额外的编辑、内容补充、找答案等附加服务。
- 2、"仅部分预览"的文档,不可在线预览部分如存在完整性等问题,可反馈申请退款(可完整预览的文档不适用该条件!)。
- 3、如文档侵犯您的权益,请联系客服反馈,我们会尽快为您处理(人工客服工作时间:9:00-18:30)。
1230万元成本是如何节省下来的?
杭州中瑞思创科技股份有限公司精益推行年度总结报告 2009年11月27日,杭州中瑞思创科技股份有限公司(以下简称Century)就企业的精益生产推行改善情况作了交流。
Century注册资金为5000万元人民币,年销售额2亿人民币。
是一家从事电子商品防窃标签的研发、生产和销售的高科技技术企业,被评为杭州市成长型中小企业。
2009年Century在进行精益生产改善下,全年节省成本1230万元。
现特将企业精益改善情况作一总结,供更多企业推行精益管理借鉴。
一、项目的思路与工作步骤
Century精益生产项目的主要任务确立如下:
其他:制一部的快速换模项目已经实施,换模时间从40分钟左右降低至20分钟,对于一个月换模400次左右来讲,是比较打的改善;
本阶段得到较好的配合实施,已经取得了阶段性成果,物流部、制三部完成了精益生产的基础管理平台建立,每个重点管理要素都已经确立了管控的方式,初见成效,但是为后续更好的体现在经济效益上奠定了基础。
最关键是各部门部门长的精细化管理认识终于从被动的执行,彻底改变成为对精益生产改善的高度重视和积极参与。
同时,管理改善小组也在制三部的基础管理平台改善中找到了自己部门的价值与具体代表公司督导部门落实改善的方式方法。
总的来讲,工作主要在上级及公司相关部门的支持下,对精益生产的观念上的瓶颈与管理干部队伍的瓶颈做出了重大的突破,使得精益生产最终得以全面展开,而且取得阶段性成果,精益生产预期将成为公司生产中心长期的管理机制:
阶段成果
签订供应商品质协议书,建立供应商质量风险金制度
检查督导每个供应商的质量检验标准与方法
已与6个供应商建立数据管控,并且取得明显供应商品质改善成果供应商供货合格率已经从90%提升至96%
已与三个制造部建立类似数据管控,强化分时段品质控制力度
阶段成果
可确定制一、制二、制三立即都可形成10%-15%的效率提升空间,后续细化管理还可继续挖掘潜力。
制一部快速换模,已经全面实施,平均降低换模时间20分钟。
制三部快速换线的机制已经建立(动线管理机制)
阶段进展及目标:
实施目标是至6月底实现节约库存资金60万目标(目前20万)
销售预测准确录从低于50%稳固于70-80%以上,(目前建立基本数据模型)
建立跟催机制及相关信息共享规范(目前建立基本规范)
提案项目:129项预期金额:
945万
实际完成金额:1156.25万按计划达成率:75.25%
要求把目前基础工作完善的过程中,有成效的工作上报成为项目
5.实施工作5:其他配合制造中心管理工作
制造中心专业化发展的沟通与建议
配合工作,辅导管理改善小组承担督导责任
从全年的精益生产推进的角度看,一些改善数据可以说明生产管理发生了彻底的改变,这种变化有以下几个分类:
(一)现场管理提升◎例:制造三部的标准化管理改善。
核心问题:制造三部精益生产推进开始几个月一直受阻,且实际的管理存在严重的问题,也就是说,制造三部并没有形成一个电子制品部基本的生产与管理平台,很多必须具备的生产作业环境与作业条件不具备,比如ESD失控,所以不良率达18%,品质与交货期处于失控状态,更不用成本挖潜。
对策措施:全面辅导各管理要素改善,现在制造三部已经具备基本生产作业环境与作业条件,并且已经形成对过程管理的几个重要控制机制:工时管理(针对效率达成)、动线管理(针对多品种流水线人员管理)、分时段管理(针对设备、工艺及品控人员的过程控制实施)
数据现状对比:
稽核数据:改善前的稽核结果:不合格项253项,合格率46.28%,远低于合格线60%。
改善至09年5月的稽核结果:
不合格项减少为119项,合格率73.38%。
从不良率的角度也可以看到从18%降低至1-2%的水平,但是和制造二部<0.5%的水平比还有较大差距。
(二)工效管理提升◎例:制造一部、制造二部的工时管理。
(1)制造二部最快接受精益生产改善的理念与方法,实施了新的瓶颈工位标准,重新制定每个产品的标准工时。
09年3月前,由生计部门负责标准工时工作,根据统计从08年6月至5月,标准定额根据实际产品产量提升了:8.95%
09年3月16日制造二部接受标准工时工作,在生计部门的基础上,又完成第一次产品定额全面整理,全系产品标准定额提升了:10.23%
形成具体的工时管控分析机制,建立欠产员工管理提升效率机制,员工欠产,非计件人员得到控制:
(2)制一部最终接受了工时的改善思路,建立了新的执行标准,结论是:定额提升10%左右。
(3)制三部开始实行新的产线平衡并且实施从计时改为计件,初步实施9个产品的新工时,定额提升为5.9%
(4)结论:目前三个制造部门都已经形成工时管理规范,以及持续改善的机制。
(三)供应链管理提升◎例:供应商管理小组的供应商品质辅导及内部制造部品质分时段管控。
制程品质管理辅导
品质管量辅导是从《分时段管理计划》开始
《质量奖惩办法》
定期的品质例会制度推行
形成定期的品质报表分析制度
供应链管理
供应链管理小组管理办法的起稿及运行;
质量协议的起稿,以及与供应商签订《质量协议》;
日常供应商品质问题的沟通流程以及表单改善;
与供应商统一质量标准,并让供应商盖章确认并作为《质量协议》的补充的内容;
帮助供应商建立质量控制点,要求供应商提供相关检验记录;并派人员到供应
商现场进行确认相关检验的执行情况,针对存在的问题进行现场辅导;
将我司的IQC前移至供应商,即把供应商的FQC当作我司的IQC;形成IQC与FQC相对应的检出率的报表,实时监控供应商现场的品质状况,做到提前预防,及时发现问题及时去现场查核与辅导。
结论:品质部已经把制造三个部门纳入统一的供应商管理体系,并且意识到下一步是加快扩大到其他供应商,完成全部供应商的品质协议技术附件的确认。
(四)库存管理提升◎例:物流部实施上线结算,以及重视计划跟催预警流程建立、预测机制建立。
实施目标是至6月底实现节约库存资金60万目标(目前20万)
销售预测准确率从低于50%稳固于70-80%以上,(目前建立基本数据模型)建立跟催机制及相关信息共享规范(目前建立基本规范)
物流部目前进展相对落后,只是开始明确改善的思路并启动改善措施,后续还要强化辅导,争取取得深化成果。