织疵的产生原因及消除方法
喷气织机主要织疵形成原因及解决办法
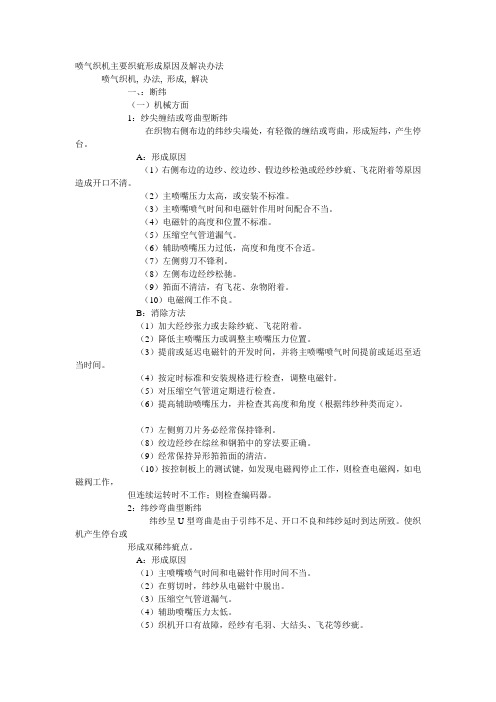
喷气织机主要织疵形成原因及解决办法喷气织机, 办法, 形成, 解决一、:断纬(一)机械方面1:纱尖缠结或弯曲型断纬在织物右侧布边的纬纱尖端处,有轻微的缠结或弯曲,形成短纬,产生停台。
A:形成原因(1)右侧布边的边纱、绞边纱、假边纱松弛或经纱纱疵、飞花附着等原因造成开口不清。
(2)主喷嘴压力太高,或安装不标准。
(3)主喷嘴喷气时间和电磁针作用时间配合不当。
(4)电磁针的高度和位置不标准。
(5)压缩空气管道漏气。
(6)辅助喷嘴压力过低,高度和角度不合适。
(7)左侧剪刀不锋利。
(8)左侧布边经纱松驰。
(9)筘面不清洁,有飞花、杂物附着。
(10)电磁阀工作不良。
B:消除方法(1)加大经纱张力或去除纱疵、飞花附着。
(2)降低主喷嘴压力或调整主喷嘴压力位置。
(3)提前或延迟电磁针的开发时间,并将主喷嘴喷气时间提前或延迟至适当时间。
(4)按定时标准和安装规格进行检查,调整电磁针。
(5)对压缩空气管道定期进行检查。
(6)提高辅助喷嘴压力,并检查其高度和角度(根据纬纱种类而定)。
(7)左侧剪刀片务必经常保持锋利。
(8)绞边经纱在综丝和钢筘中的穿法要正确。
(9)经常保持异形筘筘面的清洁。
(10)按控制板上的测试键,如发现电磁阀停止工作,则检查电磁阀,如电磁阀工作,但连续运转时不工作;则检查编码器。
2:纬纱弯曲型断纬纬纱呈U型弯曲是由于引纬不足、开口不良和纬纱延时到达所致。
使织机产生停台或形成双稀纬疵点。
A:形成原因(1)主喷嘴喷气时间和电磁针作用时间不当。
(2)在剪切时,纬纱从电磁针中脱出。
(3)压缩空气管道漏气。
(4)辅助喷嘴压力太低。
(5)织机开口有故障,经纱有毛羽、大结头、飞花等纱疵。
(6)开口量太小或开口时间不标准。
(7)经纱碰到辅助喷嘴尖端。
(8)经纱张力太小。
(9)主喷嘴位置不对。
B:消除方法(1)提前或延迟电磁针的开起时间,并将主喷嘴的喷气时间提前或延迟。
(2)调整左剪刀、导纱器作用时间,以减小切断阻力;或适当提高剪切吹气压力。
梭织特有织疵
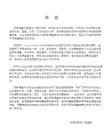
B:消除方法
1:厂区周围空气中含油较多时,要加强空调洗涤室进风窗的管理,尽量少用室外空气。
2:织机停车在5个班及以上时,经纱上应喷射滑石粉。织机停车前,空调洗涤室应提前40min停止给湿,使车间湿度降低,以防止产生黑白面布。
3:织机停车3个班及以上时,可采取人工轮流开车,并制织约2mm布后停车,也有一定收效。
梭织特有织疵
一:纬缝。
梭织特有织疵
一:纬缝
(一)形成原因
1:经纱上机张力不良。
(1)后梁位置过高或过低,使经纱上机张力不匀。
(2)送经装置不良,使经纱上机张力不匀,忽紧忽松,产生纬缝。
(3)卷取装置不良。
2:边撑伸幅作用不良。
(1)边撑刺环回转不灵活。
(2)边撑铜环尖顶与边撑盖板间得距离不合要求,两侧边撑高低、前后位置不一致,均会导致布幅两边得伸幅作用用力发生差异。
四:布辊皱。
四:布辊皱
A:形成原因
涤纶纤维表面光滑,单纱较高,受外力易伸长消除外力后回缩。
B:消除方法
1:改用橄榄形固定导布辊。
2:选用锣旋形导布辊。
3:加装弧形杆(板)。
4:加大卷布辊与刺毛辊之间的压力。
五:黑白面布。
五:黑白面布
A:形成原因
涤棉或其他化纤织物在织造过程中,由于开口、打纬等运动,经纱磨擦大而产生较强的静电。当织机停车后,静电不易导出,从而吸附空气中混有湿度较大的煤灰微粒。经纱磨擦愈厉害,静电产生愈强,而吸附的煤灰微粒也愈多,所以织口处形成的黑白布面就更明显。
6:纬纱捻度差异。
B:消除方法:
1:涤纶原料变更前,首先要掌握沸水收缩率,如前后批差值较大,应做到“先做先出、先进先用”,严格分开使用,防止产生裙子疵点。
云织织疵的成因和检修措施
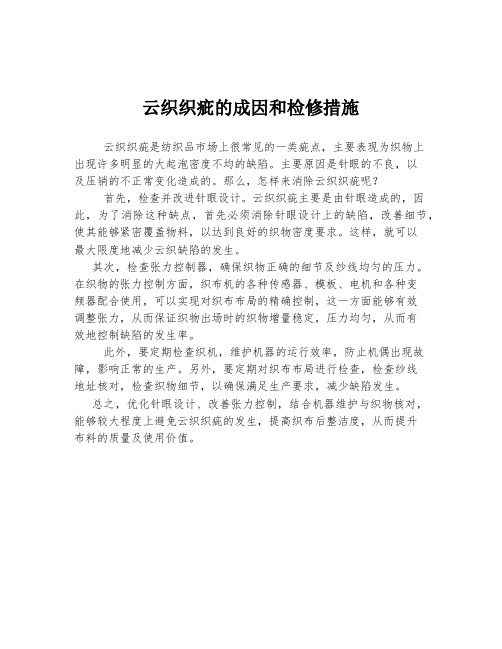
云织织疵的成因和检修措施
云织织疵是纺织品市场上很常见的一类疵点,主要表现为织物上
出现许多明显的大起泡密度不均的缺陷。
主要原因是针眼的不良,以
及压销的不正常变化造成的。
那么,怎样来消除云织织疵呢?
首先,检查并改进针眼设计。
云织织疵主要是由针眼造成的,因此,为了消除这种缺点,首先必须消除针眼设计上的缺陷,改善细节,使其能够紧密覆盖物料,以达到良好的织物密度要求。
这样,就可以
最大限度地减少云织缺陷的发生。
其次,检查张力控制器,确保织物正确的细节及纱线均匀的压力。
在织物的张力控制方面,织布机的各种传感器、模板、电机和各种变
频器配合使用,可以实现对织布布局的精确控制,这一方面能够有效
调整张力,从而保证织物出场时的织物增量稳定,压力均匀,从而有
效地控制缺陷的发生率。
此外,要定期检查织机,维护机器的运行效率,防止机偶出现故障,影响正常的生产。
另外,要定期对织布布局进行检查,检查纱线
地址核对,检查织物细节,以确保满足生产要求,减少缺陷发生。
总之,优化针眼设计、改善张力控制,结合机器维护与织物核对,能够较大程度上避免云织织疵的发生,提高织布后整洁度,从而提升
布料的质量及使用价值。
常见针织面料疵点及其产生原因

常见针织疵点及其产生原因1.漏针:在编织过程中,织针没有勾到毛纱或勾到毛纱后又脱出针钩而形成线圈脱散,在布面出现垂直的条痕及小孔的现象。
原因及处理方法:(1) 针的原因,针钩或针舌坏、针舌长短不一、针头大小不一等。
(换针)(2) 纱咀位置不好,离针舌太高或太低、过里或过外。
(调纱咀)(3) 针槽不干净或有异物,针槽太松或太紧导致织针不能正常工作。
(清洁、修理针槽)(4) 沉降片三角与三角相对位置不正确,退圈时,发生织针穿过旧线圈的现象。
(调整沉降三角与织针三角的相对位置)(5) 给纱张力过小或纱过硬张力大。
(调整输线量或弯纱深度,纱线重新过蜡)卷布张力不均匀或太松。
(调整卷布张力)双面织物还存分里漏针、外漏针,针盘上织针的漏针为里漏针,针筒上织针的漏针为外漏针。
2.断针:一条垂直的坑或较连续的孔。
原因:(1)织针的原因,针太旧,针钩、针舌坏,或是用错针。
(换针)(2)个别针槽紧,织针运动困难。
(修理针槽)(3)纱只问题,粗纱、大纱结或乱纱卡住针钩等。
(4)布架太紧,卷布张力过大。
(调整卷布张力)(5)纱咀位置不好。
(调纱咀位置)3.撞针:在编织过程中针踵与三角组之间相互碰撞的现象,会损伤针筒(针盘)、织针等,撞针损失巨大,所以在生产中应小心避免。
原因:(1) 缺油、车速太高。
(2) 上下针槽末对准,针门关不严,螺丝松动等。
(3) 针槽坏,棱角起毛,或针槽内有断针脚;(4) 纱咀位置错误,或探布针伸入针槽且失灵;(5) 纱线张力突然增大;(6) 棱角之间接缝过大,过道太窄或上下棱角位置对位不好,上下织针相碰;(7) 脱布末能自停,布上浮造成撞针;4.花针:成圈过程中,新旧线圈重叠在一起形成一个线圈,在布面上出现连续或不连续小坑,纱乱等,花针主要是个别织针在编织成圈过程中退圈不足或脱圈不足(包头)造成; (1)针的原因:针舌歪,长短不一,针发毛等;(2)棱角位置不好,压针不足等设备原因;(3)针叶太松,缺损等(增加槽壁压力)(4)织物牵拉力过小,退圈不足等;(5)纱线不均匀,粗纱脱不出;另:织针损坏而形成的花针称直花针,无规则的花针称为散花针。
织布疵点原因及预防措施

11:落布操作时,由于木辊直径较大,容易与卷布刺辊上的刺毛铁皮相摩擦而产生类似边撑疵坏布。
12:边撑盒盖上螺栓头部碰撞筘帽前夹木或碰撞飞梭装置铁杆。
13:平车或拆坏布后,用手将布边拉入边撑盒的操作不当。
B:消除方法1:边撑、刺辊配套良好,安装正确。
2:使织机有关部件处于正常状态。
3:加强各工种的操作管理。
4:加强温湿度调节工作。
5:几项技术改进。
(1):采用单只刺辊。
(2):采用颗粒橡胶刺辊或乳胶管辊与铁刺辊混用。
(3):采用十片铜刺辊,比木刺辊或铁刺辊伸幅作用大1~1.5CM。
既可消除因伸幅不良造成的断边,也可减少边撑疵点。
(4):检查木刺辊、铁刺辊、铜刺辊是否达到技术要求。
(5):织机卷布刺辊两端包布,防止落布后将布头卷紧时,布边和刺毛辊表面摩擦而产生边撑疵。
(6):织机卷布辊托脚木轴承厚度,可有原来的19.2MM减为9.6MM,防止落布时布辊直径过大与卷布刺毛辊相擦而造成类似的边撑疵布。
(三):烂边第一类大烂边A:形成原因1:纬纱上的棉结杂质,特别是中、细特纱上的大杂质,以及细纱纺制时的飞花、回丝附入而产生的细节,与纬纱退绕气圈相碰,造成意外阻力。
2:纬管腔内积有回丝,因梭子冲击而从纬管头部小眼内脱出,阻塞梭子骑马钢丝或瓷眼通道,致使纬纱引伸受阻,张力增加。
3:织机揩扫时飞花落入梭子瓷眼,使纬纱引伸不畅,增加意外张力。
4:梭管配合不良,两者中心不一,梭芯高低位置不正,梭芯忽高忽低,纬管内孔磨损等,均会使纬纱退绕时的张力严重不匀。
B:消除方法1:提高纬纱质量,根据织造品种不同,提出原纱棉结杂质的具体要求,一般棉杂要小而少。
2:纬管内孔回丝,纺部要设法解决,织造车间应结合纬管定期检修,加以消除。
3:清扫织机时,落梭箱需用盖布遮住,防止飞花落入,阻塞梭子瓷眼。
4:做好梭、管配套工作。
第二类小烂边A:形成原因1:边撑伸幅作用不够,边撑刺辊第握持力不足,边纱控制不牢。
特别在纬纱由满纱逐渐退绕至小纱时更为突出。
常见织疵造成原因

常见织疵造成原因织疵是指纺织品上出现的缺陷或瑕疵。
这些缺陷或瑕疵可以是织物表面的瑕疵,也可以是织物结构上的缺陷。
对于一个完美的织物,没有任何缺陷是理想的,但由于各种原因,织疵在生产过程中总是会出现。
下面将介绍一些常见的织疵造成原因。
第一,织机故障是一个常见的织疵造成原因。
织机在运作过程中可能会出现各种问题,比如织机的各个部件的磨损,不正常的振动或运动,机器的故障等。
这些故障可能导致织物上出现缺陷,比如断纬、断经、错纱等。
第二,纱线质量问题也是织疵造成原因之一。
纱线在织物生产过程中充当了重要的角色,它们是织物的基础。
如果纱线的质量不好,比如存在断丝、返纺、破编等问题,那么织物上就会出现相应的缺陷。
第三,操作人员的错误也是织疵造成原因之一。
在织物生产过程中,操作人员的技术水平和经验直接影响着织物的质量。
如果操作人员不熟悉织机的操作,或者在织物检查过程中出现疏忽,就容易导致织物上出现各种缺陷,比如错编、错纬、错织、粗织等。
第四,原料的质量问题也是织疵造成原因之一。
织物的质量受到原料质量的直接影响。
如果原料的质量不好,比如存在杂质、纤维断裂、扭曲等问题,那么织物上就会出现相应的缺陷。
第五,生产环境和工艺问题也会导致织疵的产生。
在织物生产过程中,生产环境和工艺的合理性对织物的质量有着重要的影响。
比如,如果生产环境的温度、湿度等参数不合适,或者采用了不恰当的工艺流程,都可能导致织物上出现各种缺陷。
第六,外部因素也可能导致织疵的产生。
比如运输过程中的振动、摩擦,还有织物在使用过程中的洗涤、摩擦等都可能导致织物上出现疵点。
织疵的产生是一个复杂的过程,涉及到织机、纱线、操作人员、原料、生产环境和工艺等多个方面的因素。
为了减少织疵的产生,可以采取一些有效的措施,比如密切关注织机的运行状态,定期维护和保养织机,严格控制纱线的质量,提高操作人员的技术水平和责任心,加强对原料的质量监控,优化生产环境和工艺流程等。
只有在综合考虑和解决以上因素的基础上,才能够减少织疵的产生,提高织物的质量。
喷气织机主要织疵形成原因及解决办法
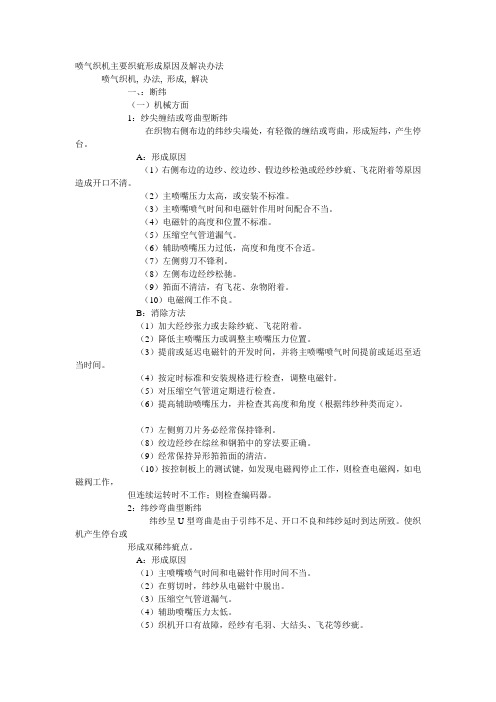
喷气织机主要织疵形成原因及解决办法喷气织机, 办法, 形成, 解决一、:断纬(一)机械方面1:纱尖缠结或弯曲型断纬在织物右侧布边的纬纱尖端处,有轻微的缠结或弯曲,形成短纬,产生停台。
A:形成原因(1)右侧布边的边纱、绞边纱、假边纱松弛或经纱纱疵、飞花附着等原因造成开口不清。
(2)主喷嘴压力太高,或安装不标准。
(3)主喷嘴喷气时间和电磁针作用时间配合不当。
(4)电磁针的高度和位置不标准。
(5)压缩空气管道漏气。
(6)辅助喷嘴压力过低,高度和角度不合适。
(7)左侧剪刀不锋利。
(8)左侧布边经纱松驰。
(9)筘面不清洁,有飞花、杂物附着。
(10)电磁阀工作不良。
B:消除方法(1)加大经纱张力或去除纱疵、飞花附着。
(2)降低主喷嘴压力或调整主喷嘴压力位置。
(3)提前或延迟电磁针的开发时间,并将主喷嘴喷气时间提前或延迟至适当时间。
(4)按定时标准和安装规格进行检查,调整电磁针。
(5)对压缩空气管道定期进行检查。
(6)提高辅助喷嘴压力,并检查其高度和角度(根据纬纱种类而定)。
(7)左侧剪刀片务必经常保持锋利。
(8)绞边经纱在综丝和钢筘中的穿法要正确。
(9)经常保持异形筘筘面的清洁。
(10)按控制板上的测试键,如发现电磁阀停止工作,则检查电磁阀,如电磁阀工作,但连续运转时不工作;则检查编码器。
2:纬纱弯曲型断纬纬纱呈U型弯曲是由于引纬不足、开口不良和纬纱延时到达所致。
使织机产生停台或形成双稀纬疵点。
A:形成原因(1)主喷嘴喷气时间和电磁针作用时间不当。
(2)在剪切时,纬纱从电磁针中脱出。
(3)压缩空气管道漏气。
(4)辅助喷嘴压力太低。
(5)织机开口有故障,经纱有毛羽、大结头、飞花等纱疵。
(6)开口量太小或开口时间不标准。
(7)经纱碰到辅助喷嘴尖端。
(8)经纱张力太小。
(9)主喷嘴位置不对。
B:消除方法(1)提前或延迟电磁针的开起时间,并将主喷嘴的喷气时间提前或延迟。
(2)调整左剪刀、导纱器作用时间,以减小切断阻力;或适当提高剪切吹气压力。
喷气织机常见织疵的成因及解决措施
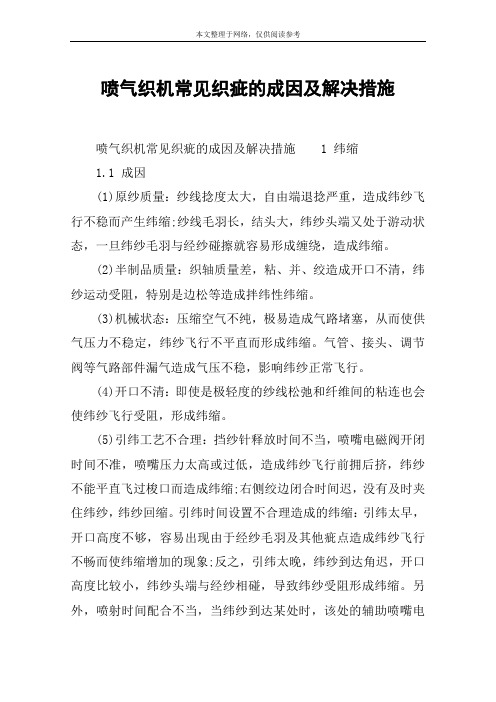
喷气织机常见织疵的成因及解决措施喷气织机常见织疵的成因及解决措施 1 纬缩1.1 成因(1)原纱质量:纱线捻度太大,自由端退捻严重,造成纬纱飞行不稳而产生纬缩;纱线毛羽长,结头大,纬纱头端又处于游动状态,一旦纬纱毛羽与经纱碰擦就容易形成缠绕,造成纬缩。
(2)半制品质量:织轴质量差,粘、并、绞造成开口不清,纬纱运动受阻,特别是边松等造成拌纬性纬缩。
(3)机械状态:压缩空气不纯,极易造成气路堵塞,从而使供气压力不稳定,纬纱飞行不平直而形成纬缩。
气管、接头、调节阀等气路部件漏气造成气压不稳,影响纬纱正常飞行。
(4)开口不清:即使是极轻度的纱线松弛和纤维间的粘连也会使纬纱飞行受阻,形成纬缩。
(5)引纬工艺不合理:挡纱针释放时间不当,喷嘴电磁阀开闭时间不准,喷嘴压力太高或过低,造成纬纱飞行前拥后挤,纬纱不能平直飞过梭口而造成纬缩;右侧绞边闭合时间迟,没有及时夹住纬纱,纬纱回缩。
引纬时间设置不合理造成的纬缩:引纬太早,开口高度不够,容易出现由于经纱毛羽及其他疵点造成纬纱飞行不畅而使纬缩增加的现象;反之,引纬太晚,纬纱到达角迟,开口高度比较小,纬纱头端与经纱相碰,导致纬纱受阻形成纬缩。
另外,喷射时间配合不当,当纬纱到达某处时,该处的辅助喷嘴电磁阀没有及时开启,造成纬纱在松弛状态下飞行,形成纬缩。
(6)车间温湿度偏低,纤维间的弹性相对增强,摩擦力减小,促使反捻回扭力增加。
1.2 解决措施(1)一般应在纬纱强力符合织造要求的情况下,尽可能选择较小的捻系数,涤棉织物更要提高定捻效果;设计最佳捻度,降低捻不匀;采用无结头纱;在紧度不大时适当推迟开口。
(2)整经的边纱张力应为2 ~3 g,严格控制浆纱边纱排头,校正盘板开档的距离,确保盘板开档与筘幅匹配。
(3)压缩空气不纯可以在进气口处加装双层过滤网,过滤网定期清洗和保养;布面出现水分应检查干燥系统运行是否正常;在日常维修中,要仔细用超声波振动仪清洗电磁阀。
(4)在上机初始时必须按照工艺要求调整好综框及开口动程,并且在调整综框时要注意综框两侧工艺的一致性。
干货喷气织造知识——常见织疵的产生原因及消除方法
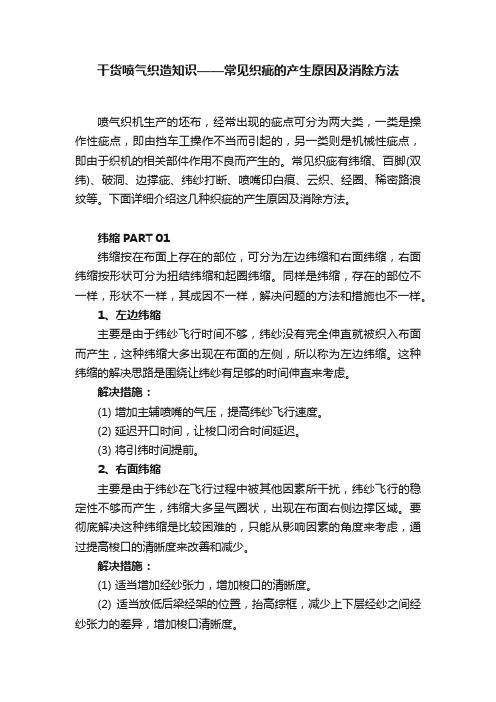
干货喷气织造知识——常见织疵的产生原因及消除方法喷气织机生产的坯布,经常出现的疵点可分为两大类,一类是操作性疵点,即由挡车工操作不当而引起的,另一类则是机械性疵点,即由于织机的相关部件作用不良而产生的。
常见织疵有纬缩、百脚(双纬)、破洞、边撑疵、纬纱打断、喷嘴印白痕、云织、经圈、稀密路浪纹等。
下面详细介绍这几种织疵的产生原因及消除方法。
纬缩PART 01纬缩按在布面上存在的部位,可分为左边纬缩和右面纬缩,右面纬缩按形状可分为扭结纬缩和起圈纬缩。
同样是纬缩,存在的部位不一样,形状不一样,其成因不一样,解决问题的方法和措施也不一样。
1、左边纬缩主要是由于纬纱飞行时间不够,纬纱没有完全伸直就被织入布面而产生,这种纬缩大多出现在布面的左侧,所以称为左边纬缩。
这种纬缩的解决思路是围绕让纬纱有足够的时间伸直来考虑。
解决措施:(1) 增加主辅喷嘴的气压,提高纬纱飞行速度。
(2) 延迟开口时间,让梭口闭合时间延迟。
(3) 将引纬时间提前。
2、右面纬缩主要是由于纬纱在飞行过程中被其他因素所干扰,纬纱飞行的稳定性不够而产生,纬缩大多呈气圈状,出现在布面右侧边撑区域。
要彻底解决这种纬缩是比较困难的,只能从影响因素的角度来考虑,通过提高梭口的清晰度来改善和减少。
解决措施:(1) 适当增加经纱张力,增加梭口的清晰度。
(2) 适当放低后梁经架的位置,抬高综框,减少上下层经纱之间经纱张力的差异,增加梭口清晰度。
(3) 提高原纱和浆纱质量,减少棉结杂质和毛羽,减少开口时上、下层经纱相互粘连的现象。
(4) 检查左右绞边器的绞边时间。
(5) 钢筘的使用上尽量使用较大一点筘号,原来4/筘可改3/筘,3/筘可改2/筘,会收到较好的效果,筘号大,每筘穿人数减少,经纱之间粘连的现象会大为改观。
(6) 扭结纬缩的产生多半是由于纬纱捻度过高或钢筘弯曲造成纬纱头端扭结而无法伸直。
(7) 优化引纬工艺,最佳配置引纬时间、主、辅喷嘴作用时间以及主、辅喷嘴的气压。
纺织品瑕疵原因分析及处理方法

服装材料纺织品瑕疵纤维原料到最后制造成成品织物,需经过纺纱、织造、印染等工程,且每种工程中,又需经过一连续多个加工过程(Process)始能完成。
在各层次的加工中,设定条件之不当,人员操作之疏忽,机械之故障等,均可能致使产品发生外观上之缺点。
就理论上言之,加工之层次愈多,则发生缺点之机率亦愈高。
在织物外观所能见到之此种缺点,称谓织物瑕疵(Fabric Defect)。
但亦有在胚布状态无异状,若经漂、染加工后则显著出现,此种一般多称之谓潜隐瑕疵(Latent Defect)或隐性瑕疵。
我国有一句俗语:「多作多错,少作少错,不作不错。
」,此语虽在现代工作精神上不合时宜,但用在纺织多层次加工所产生之瑕疵上却甚为切合实际。
世界上少有完美之事物,纺纱工程会使原纱产生瑕疵,例如棉粒(Nep)、粗结(Slub)等;织造工程会使胚布产生瑕疵,例如并纬(Mispicks)、断经(Broken Ends)等;印染工程会使成品布产生瑕疵,例如染料点(Dye Spot)、结尾色差(Tailing or Ending)等。
品质优良之成品织物,其瑕疵应为极少。
如某种成品织物之瑕疵甚多,无论是用作制衣、被服、或其它日用品及装饰品,均会影响其美观,而降低其价值。
二、织物瑕疵之外观特征与成因由纤维至成品织物,加工之阶段可分为纺纱(Spinning),织造(Weaving),练漂、染色、印花(Scouring & Bleaching,Dyeing,Printing)与整理加工(Finishing)四大阶段。
现以在各阶段中可能发生之瑕疵,用工厂一般通用之名称,就其外观特征与生成之原因分述于下:1.属于纤维原料、纱支原因者2.属于织造原因者3.属于印染整理原因者4.生成原因难以归属及专业加工者1.属于纤维原料、纱支原因者(1)棉粒(Nep)外观:布面呈现类似接头大小之棉纤维团,且系纺入纱中者。
如将之拔下,则纱呈断裂或将至断裂之状态。
干货纺织品62种瑕疵及成因汇总,如何帮客户解决?
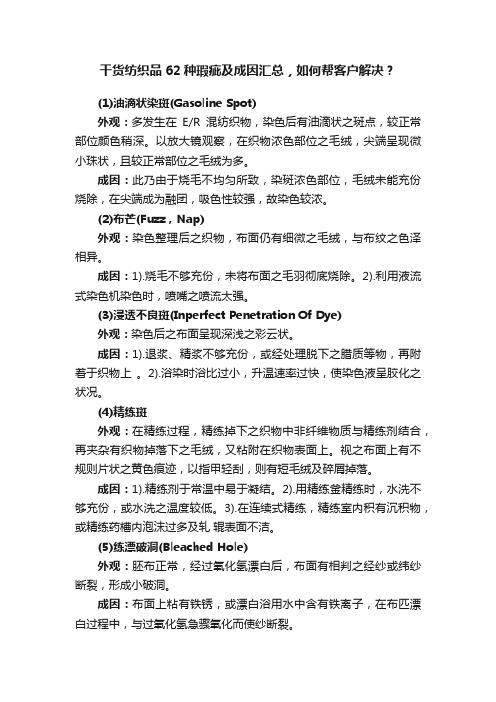
干货纺织品62种瑕疵及成因汇总,如何帮客户解决?(1)油滴状染斑(Gasoline Spot)外观:多发生在E/R混纺织物,染色后有油滴状之斑点,较正常部位颜色稍深。
以放大镜观察,在织物浓色部位之毛绒,尖端呈现微小珠状,且较正常部位之毛绒为多。
成因:此乃由于烧毛不均匀所致,染斑浓色部位,毛绒未能充份烧除,在尖端成为融团,吸色性较强,故染色较浓。
(2)布芒(Fuzz,Nap)外观:染色整理后之织物,布面仍有细微之毛绒,与布纹之色泽相异。
成因:1).烧毛不够充份,未将布面之毛羽彻底烧除。
2).利用液流式染色机染色时,喷嘴之喷流太强。
(3)浸透不良斑(Inperfect Penetration Of Dye)外观:染色后之布面呈现深浅之彩云状。
成因:1).退浆、精浆不够充份,或经处理脱下之腊质等物,再附着于织物上。
2).浴染时浴比过小,升温速率过快,使染色液呈胶化之状况。
(4)精练斑外观:在精练过程,精练掉下之织物中非纤维物质与精练剂结合,再夹杂有织物掉落下之毛绒,又粘附在织物表面上。
视之布面上有不规则片状之黄色痕迹,以指甲轻刮,则有短毛绒及碎屑掉落。
成因:1).精练剂于常温中易于凝结。
2).用精练釜精练时,水洗不够充份,或水洗之温度较低。
3).在连续式精练,精练室内积有沉积物,或精练药槽内泡沫过多及轧辊表面不洁。
(5)练漂破洞(Bleached Hole)外观:胚布正常,经过氧化氢漂白后,布面有相判之经纱或纬纱断裂,形成小破洞。
成因:布面上粘有铁锈,或漂白浴用水中含有铁离子,在布匹漂白过程中,与过氧化氢急骤氧化而使纱断裂。
(6)色花(Skilteriness)外观:布面有不规则片状之颜色深浅。
成因:前处理工程之退浆,精练未能彻底作好。
(7)雾斑(Mist)外观:片状之染斑,有深有浅,轮廓不明显,形状大小不一,发生之位置不集中,亦无一定之规则。
成因:1).待染之织物,被溅到污水或其它药品。
2).练漂后未立即烘干,长时间堆积在布车上,部份织物发生风干之水印。
毛织服装在编结过程中疵点的形成及消除方法
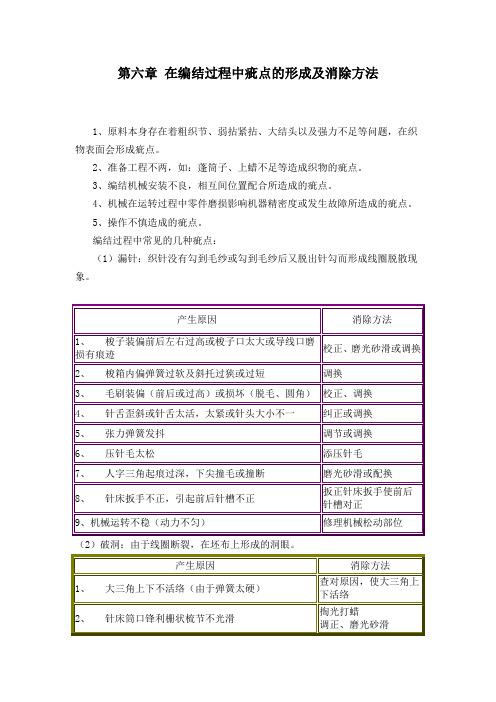
第六章在编结过程中疵点的形成及消除方法1、原料本身存在着粗织节、弱拈紧拈、大结头以及强力不足等问题,在织物表面会形成疵点。
2、准备工程不两,如:蓬筒子、上蜡不足等造成织物的疵点。
3、编结机械安装不良,相互间位置配合所造成的疵点。
4、机械在运转过程中零件磨损影响机器精密度或发生故障所造成的疵点。
5、操作不慎造成的疵点。
编结过程中常见的几种疵点:(1)漏针:织针没有勾到毛纱或勾到毛纱后又脱出针勾而形成线圈脱散现象。
(2)破洞:由于线圈断裂,在坯布上形成的洞眼。
(3)豁嘴:坯布在同一个横列内有较多织针同时产生脱圈而造成的豁口(4)密度松紧不匀:有横列与横列间线圈大小不匀,和同一横列内线圈大小不匀及不规则线圈大小等几种。
①密度松紧不匀②斜角松紧:③布面发花:2(5)花针:成圈过程中,新旧线圈重迭在一起形成羊羔线圈叫花针。
产生主要是个别织针在编结线圈过程中退圈不足或脱圈不足(包头)造成。
3(6)撞针:在编结过程中,针锤与三角之间互相碰撞叫撞针。
(7)稀路针:在织物上某几个织针所形成的线圈过大,在纵行方向出现的明显条纹。
产生原因消除方法1、针槽宽狭大小和深浅或有龌龊调换清除垃圾2、个别筒口过高或过低调换或修平筒口3、个别栅状梳节凹凸,厚薄不等或碰歪锉成相等,锉薄或校正4、针杆弯曲、粗、细针踵弯或发翘,针舌发硬,歪斜调换发毛,针舌过长,针尖大小不一5、大三角吃线快慢应取快慢相等(8)油针、油污:加油不慎、操作不慎等造成。
(9)夹档、横条:由毛纱的颜色差异和粗细不匀或其他原因,在坯布上形成显著的档子叫夹档,形成横向条痕的称横条。
喷气织机常见织疵的成因及解决措施
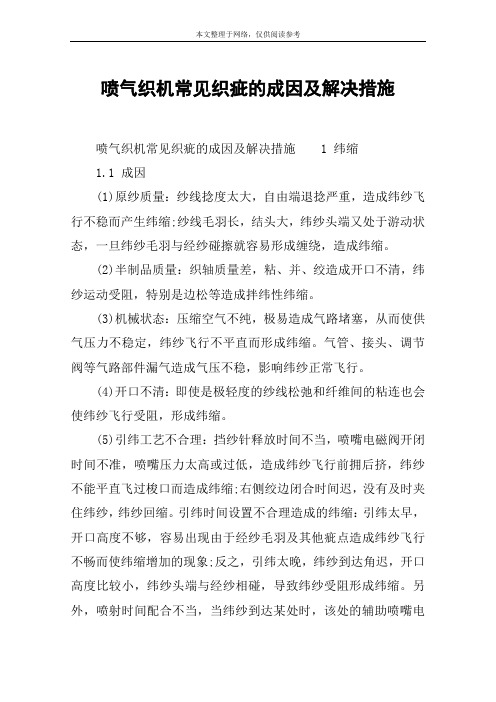
喷气织机常见织疵的成因及解决措施喷气织机常见织疵的成因及解决措施 1 纬缩1.1 成因(1)原纱质量:纱线捻度太大,自由端退捻严重,造成纬纱飞行不稳而产生纬缩;纱线毛羽长,结头大,纬纱头端又处于游动状态,一旦纬纱毛羽与经纱碰擦就容易形成缠绕,造成纬缩。
(2)半制品质量:织轴质量差,粘、并、绞造成开口不清,纬纱运动受阻,特别是边松等造成拌纬性纬缩。
(3)机械状态:压缩空气不纯,极易造成气路堵塞,从而使供气压力不稳定,纬纱飞行不平直而形成纬缩。
气管、接头、调节阀等气路部件漏气造成气压不稳,影响纬纱正常飞行。
(4)开口不清:即使是极轻度的纱线松弛和纤维间的粘连也会使纬纱飞行受阻,形成纬缩。
(5)引纬工艺不合理:挡纱针释放时间不当,喷嘴电磁阀开闭时间不准,喷嘴压力太高或过低,造成纬纱飞行前拥后挤,纬纱不能平直飞过梭口而造成纬缩;右侧绞边闭合时间迟,没有及时夹住纬纱,纬纱回缩。
引纬时间设置不合理造成的纬缩:引纬太早,开口高度不够,容易出现由于经纱毛羽及其他疵点造成纬纱飞行不畅而使纬缩增加的现象;反之,引纬太晚,纬纱到达角迟,开口高度比较小,纬纱头端与经纱相碰,导致纬纱受阻形成纬缩。
另外,喷射时间配合不当,当纬纱到达某处时,该处的辅助喷嘴电磁阀没有及时开启,造成纬纱在松弛状态下飞行,形成纬缩。
(6)车间温湿度偏低,纤维间的弹性相对增强,摩擦力减小,促使反捻回扭力增加。
1.2 解决措施(1)一般应在纬纱强力符合织造要求的情况下,尽可能选择较小的捻系数,涤棉织物更要提高定捻效果;设计最佳捻度,降低捻不匀;采用无结头纱;在紧度不大时适当推迟开口。
(2)整经的边纱张力应为2 ~3 g,严格控制浆纱边纱排头,校正盘板开档的距离,确保盘板开档与筘幅匹配。
(3)压缩空气不纯可以在进气口处加装双层过滤网,过滤网定期清洗和保养;布面出现水分应检查干燥系统运行是否正常;在日常维修中,要仔细用超声波振动仪清洗电磁阀。
(4)在上机初始时必须按照工艺要求调整好综框及开口动程,并且在调整综框时要注意综框两侧工艺的一致性。
真丝面料疵病及处理方法
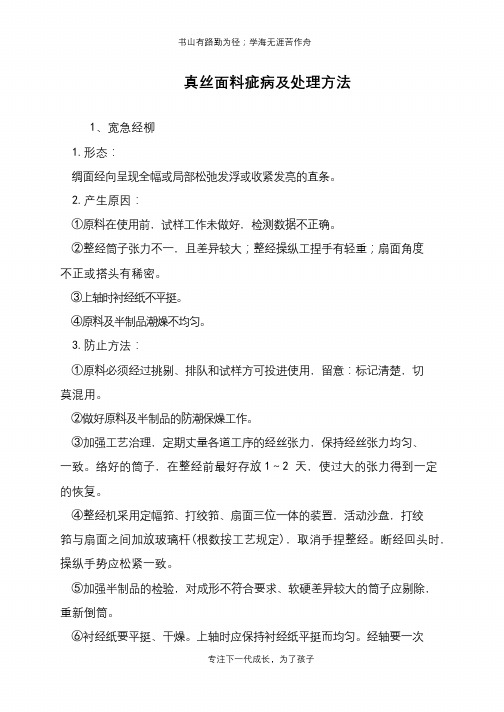
书山有路勤为径;学海无涯苦作舟
真丝面料疵病及处理方法
1、宽急经柳
1.形态:
绸面经向呈现全幅或局部松弛发浮或收紧发亮的直条。
2.产生原因:
①原料在使用前,试样工作未做好,检测数据不正确。
②整经筒子张力不一,且差异较大;整经操纵工捏手有轻重;扇面角度
不正或搭头有稀密。
③上轴时衬经纸不平挺。
④原料及半制品潮燥不均匀。
3.防止方法:
①原料必须经过挑剔、排队和试样方可投进使用,留意:标记清楚,切
莫混用。
②做好原料及半制品的防潮保燥工作。
③加强工艺治理,定期丈量各道工序的经丝张力,保持经丝张力均匀、
一致。
络好的筒子,在整经前最好存放1~2天,使过大的张力得到一定
的恢复。
④整经机采用定幅筘、打绞筘、扇面三位一体的装置,活动沙盘,打绞
筘与扇面之间加放玻璃杆(根数按工艺规定),取消手捏整经。
断经回头时,操纵手势应松紧一致。
⑤加强半制品的检验,对成形不符合要求、软硬差异较大的筒子应剔除,
重新倒筒。
⑥衬经纸要平挺、干燥。
上轴时应保持衬经纸平挺而均匀。
经轴要一次
专注下一代成长,为了孩子。
面料织疵分析概述

面料织疵分析概述面料作为衣物的重要组成部分,一直是人们十分关注的一个方面。
而在面料生产中,织疵是必不可少的一个环节,不同类型的织疵会对布面造成不同影响,因此对织疵的分析就显得尤为关键。
本文将对面料织疵的分析进行概述。
一、织疵的定义织疵是指织物表面出现的各种瑕疵,是由于纱线的不均匀性所导致的缺陷。
织疵可以分为诸如梳毛、洞洛、错花、错织等多种类型,其中每一种类型都会在一定程度上影响织物的美观度和使用寿命。
二、织疵的分类1. 梳毛梳毛是指织物表面上出现的绒毛状缺陷,这种缺陷多出现在毛料、革面绸等面料上,会影响织物的美观度和触感。
2. 洞洛洞洛是指织物表面出现的孔洞型缺陷,这种缺陷多由于纱线的质量问题造成,会直接影响到织物的使用寿命和防风等功能。
3. 错花错花是指织物表面出现的花纹不规则、错位的缺陷,这种缺陷多由于织机的质量问题或者织机操作不当造成,会直接影响到织物的美观度和风格。
4. 错织错织是指织物表面出现的纱线交错的不正常现象,这种缺陷会对织物的质量和结构造成直接影响,会导致织物易于破裂或者使用寿命短。
三、织疵的分析针对不同类型的织疵,需要进行不同的分析方法和处理措施。
1. 梳毛针对梳毛的分析,需要首先确定梳毛的程度以及毛细度大小,接着可以使用剪刀或者电吹风等工具进行处理。
具体处理方法包括毛绒部分的剪除或者吹风,根据织物的类型和梳毛的情况,可以选择不同的处理方式。
2. 洞洛针对洞洛的分析,需要首先确定洞洛的位置和大小,接着可以使用补补织等工具进行处理。
如果洞洛比较大或者出现在织物表面比较显著的位置,可以使用针线对洞洛进行修补。
3. 错花针对错花的分析,需要首先确定错花的范围和类型,接着可以采取重新编织等方式进行处理。
如果错花较小,可以使用调整织机的力度或者修改编织程序的方式进行调整;如果错花的范围较大,需要进行重新编织。
4. 错织针对错织的分析,需要首先确定错织的位置和类型,接着可以使用重新编织等方法进行处理。
织疵的产生原因及消除方法
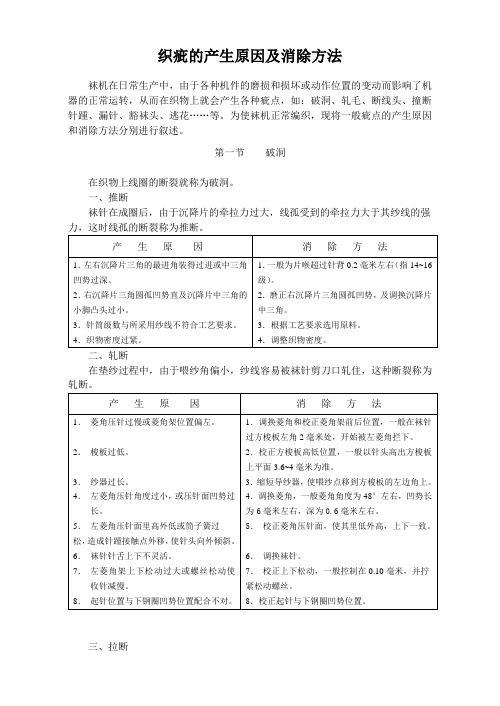
织疵的产生原因及消除方法袜机在日常生产中,由于各种机件的磨损和损坏或动作位置的变动而影响了机器的正常运转,从而在织物上就会产生各种疵点,如:破洞、轧毛、断线头、撞断针踵、漏针、豁袜头、逃花……等。
为使袜机正常编织,现将一般疵点的产生原因和消除方法分别进行叙述。
第一节破洞在织物上线圈的断裂就称为破洞。
一、推断袜针在成圈后,由于沉降片的牵拉力过大,线孤受到的牵拉力大于其纱线的强二、轧断在垫纱过程中,由于喂纱角偏小,纱线容易被袜针剪刀口轧住,这种断裂称为三、拉断在成圈过程中,由于线弧受到的张力超过其纱线的强力,这时线弧的断裂称为拉断。
四、顶断袜针成圈后,由于沉降片牵拉滞后或牵拉不足,使袜针上升时,其针头顶住旧线圈而造成纱线断裂,称为顶断。
袜针沿起针镶板上升,使针钩内的线圈移到针杆较粗的位置,由于线圈长度小六、缝合圈的轧碎(俗称缝头眼子轧碎)袜头编织结束,开始编织缝合圈时,由于机件配合不良,使个别缝合圈线弧被拉断,这种疵点称为缝合圈轧碎。
其他产生原因参看前面《拉断》的内容。
第二节合罗纹后编织平针时的疵点一、罗纹口虚环以及轧碎当罗纹口合好后,由于喂线过早,造成针钩内余线过长,在部分袜针上形成不规则的虚环,称为罗纹口虚环;这段虚环在第二转成圈时容易产生拉断,这一部位二、罗纹口漏针以及豁口当罗纹合好后,开始喂纱时,由于成圈机件配合不当,使第一只长踵袜针没有三、罗纹口花针(吊针)当罗纹合好后,在第一转成圈时,由于某些成圈机件配合不当,使部分袜针上的老线圈没有退圈,针钩内同时存在两根线弧,在第二转中脱圈,这种疵点,称为罗纹口花针。
第三节撞针在袜子编织过程中,由于某些机件的磨损或机件间相对尺寸配合不好,造成袜针、提花片、底脚片及沉降片与机件撞击的现象,称为撞针。
一、在编织袜统时袜针针踵的撞断二、在编织袜头跟时撞断长踵袜针。
三、在编织袜头跟时撞断短踵袜针。
四、菱角架进出时撞断长踵袜针。
六、提花片片踵及提花片齿撞断。
七、沉降片踵撞断第四节袜身疵点一、纵向条纹又称稀紧路。
面料织疵分析
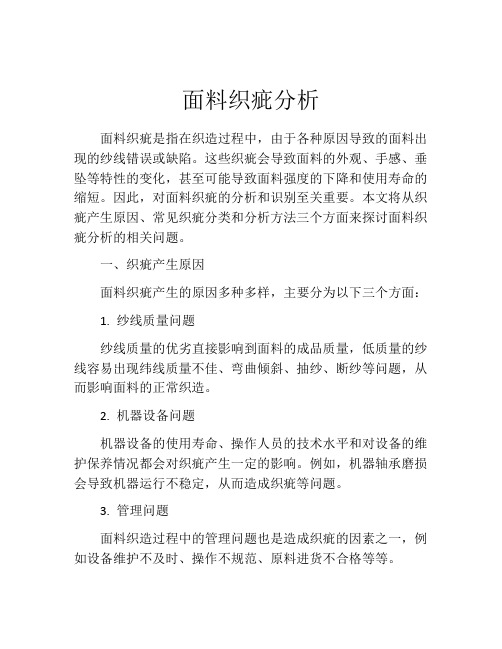
面料织疵分析面料织疵是指在织造过程中,由于各种原因导致的面料出现的纱线错误或缺陷。
这些织疵会导致面料的外观、手感、垂坠等特性的变化,甚至可能导致面料强度的下降和使用寿命的缩短。
因此,对面料织疵的分析和识别至关重要。
本文将从织疵产生原因、常见织疵分类和分析方法三个方面来探讨面料织疵分析的相关问题。
一、织疵产生原因面料织疵产生的原因多种多样,主要分为以下三个方面:1. 纱线质量问题纱线质量的优劣直接影响到面料的成品质量,低质量的纱线容易出现纬线质量不佳、弯曲倾斜、抽纱、断纱等问题,从而影响面料的正常织造。
2. 机器设备问题机器设备的使用寿命、操作人员的技术水平和对设备的维护保养情况都会对织疵产生一定的影响。
例如,机器轴承磨损会导致机器运行不稳定,从而造成织疵等问题。
3. 管理问题面料织造过程中的管理问题也是造成织疵的因素之一,例如设备维护不及时、操作不规范、原料进货不合格等等。
二、常见面料织疵分类1. 结构性疵点结构性疵点指的是面料上出现的结构性变化,例如缺纬、漏纬、抽纱等。
这些疵点会影响面料的垂坠度、外观和手感等特性,甚至会导致面料的运用寿命降低。
2. 色线疵点色线疵点主要包括色差、错花、织花等问题,这些疵点对面料的颜色、图案、质感也有一定的影响。
3. 尺寸性疵点尺寸性疵点指的是面料大小、厚度、密度等方面的织疵。
这些疵点如果严重则会导致面料失去应有的使用功能,例如不适合制作衣物等。
三、面料织疵分析方法1. 观察法通过目视观察,找出布面上的不规则点、掌纹、节每扭曲、疵片等。
不仅要看疵点的大小和形状,还要通过观察它的位置和分布规律等信息确定是何种织疵。
2. 毛细管吸气法毛细管吸气法可用于观察织疵扭曲、断裂及织结的位置等信息。
通过对织疵吸气时毛细管内的水的变化观察,得出织疵的位置与形状。
3. 线追踪法线追踪法是一种通过对织疵产生的图案特征进行描述,然后追踪相应的纬线或经线,以确定其在布面上的位置与形状的方法。
常见织疵形成的原因及预防措施
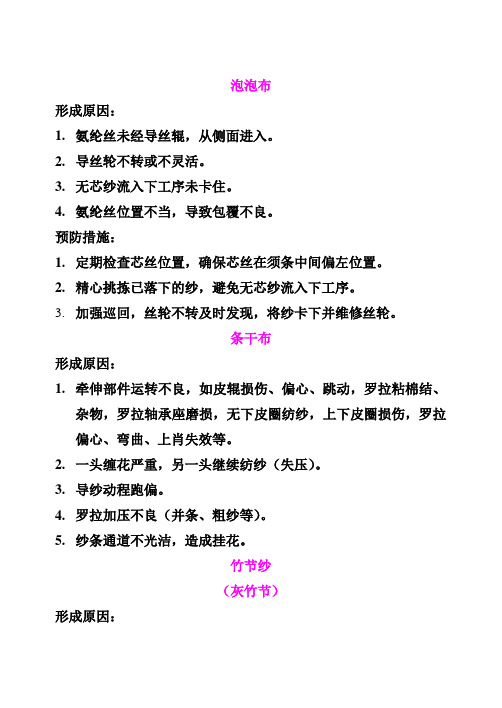
泡泡布形成原因:1.氨纶丝未经导丝辊,从侧面进入。
2.导丝轮不转或不灵活。
3.无芯纱流入下工序未卡住。
4.氨纶丝位置不当,导致包覆不良。
预防措施:1.定期检查芯丝位置,确保芯丝在须条中间偏左位置。
2.精心挑拣已落下的纱,避免无芯纱流入下工序。
3.加强巡回,丝轮不转及时发现,将纱卡下并维修丝轮。
条干布形成原因:1.牵伸部件运转不良,如皮辊损伤、偏心、跳动,罗拉粘棉结、杂物,罗拉轴承座磨损,无下皮圈纺纱,上下皮圈损伤,罗拉偏心、弯曲、上肖失效等。
2.一头缠花严重,另一头继续纺纱(失压)。
3.导纱动程跑偏。
4.罗拉加压不良(并条、粗纱等)。
5.纱条通道不光洁,造成挂花。
竹节纱(灰竹节)形成原因:1.清梳工序漏底花堆积太多,带入棉层。
2.各工序通道粘、缠、挂、堵带入(三角区、龙头,并粗、细纱牵伸通道)3.绒板、绒套、绒辊花带入(并条、粗纱、精梳、细纱)。
4.高空清洁积花掉入半成品或正在纺纱机内。
5.各工序清洁方法不当。
6.卡疵把关不严,疵点流入下工序。
7.清洁不彻底(例如粗纱斜坡、车面清洁不及时,巡回吹吸风吹入,打擦板时的飞花卷入纱条等)。
8.各工序揩车不良,油飞花粘附纱条,半成品棉条、粗纱掉地,造成污染。
三丝疵布形成原因:1.拣花间未拣净,后工序未卡住。
2.个别员工在工作场所梳头,清洁工具破损掉毛仍在使用。
应对措施:1.加强员工拣色杂责任心教育,后续工序严格执行卡疵把关制度。
2.加强管理,严格要求,杜绝在工作场所梳头现象;同时,车间定期对清洁工具检查,发现掉毛立即停止使用。
粗经、粗纬形成原因:1.粗纱断头、烂纱后未及时停车,飘入邻纱未处理干净。
2.条子粘连,机后换条子破条或机后双条喂入。
3.接头不符合操作法要求(并条、粗纱、细纱等工序)。
4.细纱断头飘入邻纱(主要是混纺纱)5.细纱续粗纱或粗纱纱尾飘入邻纱,细纱机车顶板的粗纱尾巴下垂,被卷入上排粗纱。
疵点条子形成原因:粗细条:生条:1、棉卷片段重量差异大或粘卷、破洞、头码过厚、双层卷。
喷气织机常见织疵成因分析及解决措施l纬缩成因解决对策经纱

(13)控制好温湿度,若车间温湿度偏低,使纬纱收缩性质变化,影响纬纱飞行。织布车间的最适合温度、相对湿度按照纱线种类有所差异。根据气候变化,推荐如下的条件:温度25—30℃,相对湿度65%.75%。
2烂边
成因
解决对策
(1)绞边纱选择不良。
(1)选择合适的绞边纱。
(2)绞边纱断头自停失灵。
(4)张力传感器灵敏度下降,零张力误差大。
(2)检查并重新调整零张力。
(5)卷取系统齿轮啮合太紧或太浅,或缺牙。
(2)检查并重新调整零张力。
(6)卷取离合器磨损。
(3)检查并保糟卷取、送经机构工作状态良好。
(7)筘座中支撑轴承磨损,影响打纬力稳定。
(2)加强设备维护保养,更换磨损机件。
(6)右侧引纬力不足。右侧的引纬气流应强于左侧和中部,否则不能保证纬纱到位和拉直纬纱。
(6)适当增加最后一组辅助喷嘴的压力和延长其喷射时间,以保证引纬结束后到综平前这段时间内纬纱处于伸直状态,防止纬纱弯曲而形成纬缩。
(7)引纬时间太早,纬纱头端扭结。
(7)合理设置引纬时间,防止因引纬时间过早而造成进梭口时的绊纬纬缩。
(2)稳定捻度是解决纬缩疵点的有效保障。对细特纱、强捻纱或棉锦等混纺纬纱,可采取热湿定捻来稳定纬纱的捻度,增加纤维问的抱合力,使纱层间附着力增大,减少纬缩。同时,相对湿度的增加使纱线的回潮率也随之增大,不易起圈。定捻最好采用热定捻锅,其热湿定捻效果好,同时在使用前储放至少24 h。
(3)空压机系统供气不足,压力不稳定,使引纬力波动;主喷嘴压力太高,纬纱飞行时“前拥后挤”。
(3)空压机供气要有压力、流量、压力稳定性等要求,才能保证织机气流的正常喷射、连续喷射以及流量相等,从而保证气流引纬力恒定。合理设置主辅喷嘴的压力,若主喷嘴压力过小,使纬纱到达右边时间过迟,纬纱还没完全伸直织机就已打纬,形成纬缩;压力过大,一方面纬纱上有细节、弱捻等疵点会在纬纱飞行中被吹断,另一方面,高速飞行的纬纱很容易产生纬小结。一般情况下辅喷压力要大于主喷压力。因主喷嘴供气压力高,纬纱飞行速度快时。辅助喷嘴的供气压力也必须相应提高,其喷射的高速气流才能对纬纱进行有效控制,否则纬纱会前拥后挤。
- 1、下载文档前请自行甄别文档内容的完整性,平台不提供额外的编辑、内容补充、找答案等附加服务。
- 2、"仅部分预览"的文档,不可在线预览部分如存在完整性等问题,可反馈申请退款(可完整预览的文档不适用该条件!)。
- 3、如文档侵犯您的权益,请联系客服反馈,我们会尽快为您处理(人工客服工作时间:9:00-18:30)。
织疵的产生原因及消除方法
袜机在日常生产中,由于各种机件的磨损和损坏或动作位置的变动而影响了机器的正常运转,从而在织物上就会产生各种疵点,如:破洞、轧毛、断线头、撞断针踵、漏针、豁袜头、逃花……等。
为使袜机正常编织,现将一般疵点的产生原因和消除方法分别进行叙述。
第一节破洞
在织物上线圈的断裂就称为破洞。
一、推断
袜针在成圈后,由于沉降片的牵拉力过大,线孤受到的牵拉力大于其纱线的强
二、轧断
在垫纱过程中,由于喂纱角偏小,纱线容易被袜针剪刀口轧住,这种断裂称为
三、拉断
在成圈过程中,由于线弧受到的张力超过其纱线的强力,这时线弧的断裂称为
四、顶断
袜针成圈后,由于沉降片牵拉滞后或牵拉不足,使袜针上升时,其针头顶住旧
袜针沿起针镶板上升,使针钩内的线圈移到针杆较粗的位置,由于线圈长度小或纱线延伸小,而造成线圈断裂称为胀断。
六、缝合圈的轧碎(俗称缝头眼子轧碎)
袜头编织结束,开始编织缝合圈时,由于机件配合不良,使个别缝合圈线弧被
第二节合罗纹后编织平针时的疵点
一、罗纹口虚环以及轧碎
当罗纹口合好后,由于喂线过早,造成针钩内余线过长,在部分袜针上形成不规则的虚环,称为罗纹口虚环;这段虚环在第二转成圈时容易产生拉断,这一部位
其他的产生原因可参阅本章第一节的内容。
二、罗纹口漏针以及豁口
当罗纹合好后,开始喂纱时,由于成圈机件配合不当,使第一只长踵袜针没有及时钩到纱线而造成漏针,严重时就形成豁口,这种织疵称为罗纹口漏针以及豁口。
续表
三、罗纹口花针(吊针)
当罗纹合好后,在第一转成圈时,由于某些成圈机件配合不当,使部分袜针上的老线圈没有退圈,针钩内同时存在两根线弧,在第二转中脱圈,这种疵点,称为罗纹口花针。
第三节撞针
在袜子编织过程中,由于某些机件的磨损或机件间相对尺寸配合不好,造成袜针、提花片、底脚片及沉降片与机件撞击的现象,称为撞针。
一、在编织袜统时袜针针踵的撞断
二、在编织袜头跟时撞断长踵袜针。
三、在编织袜头跟时撞断短踵袜针。
继表
四、菱角架进出时撞断长踵袜针。
五、底脚片片踵撞断。
六、提花片片踵及提花片齿撞断。
第四节袜身疵点
一、纵向条纹又称稀紧路。
在编织过程中,由于成圈机件磨损或配合不良在袜子正面有部分的线圈纵行,有宽于或狭于正常纵行,宽者称稀路,狭者称紧路,总称为袜子的纵向条纹或稀紧
二、织物密度不匀
在编织过程中,由于某些对密度有关的机件相互配合不当,而产生织物上密度松紧不匀现象,影响了袜子的长短。
三、织物上线圈大小不匀。
在编织过程中,由于成圈机件配合不良,在织物上出现部分线圈大小不匀的现象。
四、袜子正反面起毛
在编织过程中,由于袜针、沉降片或其他机件擦伤纱线,使织物的正反面出现
第五节袜头跟疵点
一、袜头跟密度不匀
在袜头跟编织时,由于成圈机件磨损不一或相互差异过大,而产生袜头跟织物一转松、一转紧,形成袜头跟密度松紧不匀。
这种织疵又称头跟松紧花。
二、袜头跟歪角
在编织袜头跟时,两边的挑针数不等或揿针数不一造成袜头跟两边的提针线长
续表
三、提针线轧毛
在编头跟时,由于机件配合不当或工艺不当,使提针处的线圈轧毛,生产上又称辫子轧毛。
四、提针线孔眼(俗称包针眼)
在编织袜头跟时,由于成圈机件配合不良,在袜机倒顺转的最后一针,出现老线圈重套,使此针在下转被挑起时,针杆上只有一只线圈。
这样在提针线上就形成
第六节漏针
在编织过程中由于成圈机件相对位置配合不良,使部分或个别袜针勾不到纱线,在织物上形成纵行间线圈脱散。
第七节豁袜头
在倒顺转编织袜头跟时,由于某些机件发毛或互相配合不当,产生余线回退不足或影响垫纱位置,使针钩没有勾取进线,造成袜头跟的并列的漏针,称为豁袜头。
续表
第八节坏针舌和针头
一、削针头
由于成圈机件的作用面磨痕过深或走针运动方向的变化,在正常运转的条件下,发生针头断裂,俗称为削针头。
在运转过程中,由于成圈机件的作用面磨痕过深,或走针运动方向的变化,引起针舌发毛,歪斜和断裂,称为坏针舌。
第九节夹底闪色疵点
一、夹底不齐和跳浜。
在编织夹底部段时,由于添纱机件配合不衣或添纱张力过松,使夹底位置不固
二、夹底密度过紧
在编织夹底部段时,由于夹底打松部分机件配合不良,使夹底织物密度比袜面紧。
三、闪色露底
在编织添纱组织时,由于成圈机件配合不良,使地纱与添纱相对位置不稳定,在织物上形成不规则的露底现象,这种不规则的露底称闪色露底或夹底反花。
第十节编织横条织物时的疵点
一、横条调线不齐及调线位置偏歪
在编织横条织物时,由于调线机件磨损或相互配合不当,使导纱器在交替进入工作时有快有慢,产生调线处位置不齐,或调线位置偏左偏右,前者称为调线不齐,
续表
二、横条花纹错乱
在编织横条织物时,由于反链条架、反高节链条及其有关的机件,磨损过多或
第十一节缺花及多花
在编织绣花织物时,由于机件的磨损或相对位置配合不良,使花型的完全组织出现残缺或多余的花。
这些织疵前者称缺花或逃花,后者称多花。
产生这种疵点原因很多,一般可以按织疵情况来判定。
如织疵是产生在纵条上的,一般可检查针筒、提花片、袜针、底脚片或沉降片;如产生在一个横列上,可检查选针机构;如分散
续表
第十二节断吊线和绣花露底
一、断吊线
在绣花过程中,由于机件的磨损,起毛或位置配合不良,而造成吊线断裂。
这种现象称为断吊线。
二、绣花露底
在绣花过程中,由于吊线(添纱)的张力波动或某些机件安装不良,使部分绣
其他可参阅“断吊线的产生原因”。
第十三节花针
在编织过程中,由于成圈机件的配合不良,使个别袜针上除套有一个封闭的旧线圈外,还有一个未封闭的悬孤,在织物上形成不规则的集圈。
这种织疵称为花针或吊针。
在使用弹力锦纶丝时,有几根丝被针舌带住,在织物上也会形成小的花针(俗称芝麻点)。
第十四节少网眼和多网眼
在编织网眼织物时,由于成圈机件配合不良,使个别针多勾取添纱形成少网眼
第十五节平口袜袜口处
漏针和扎口轧碎
在编织平口袜袜口时,由于垫纱位置不良或部分袜针没有勾取纱线,造成漏针或纱线垫在袜针的剪刀口处,使纱线断裂,造成轧碎等疵点。
其他原因可参阅第十章第六节。
其他原因可参阅第十章第一节。
第十六节平口袜袜口处撞针
在编织平口袜袜口时,由于机件配合不良,使部分袜针针踵和底脚片片踵发生
第十七节平口袜袜口处
浮起和吊线
在编织平口袜袜口时,由于机件安装不良,使织物浮起或吊扎口现象。