连接器检测不良及原因
连接器十大不良PPT培训课件

绝缘不良
总结词
绝缘不良是指连接器在正常工作状态 下,其绝缘材料或绝缘层存在缺陷, 导致电气性能下降。
详细描述
绝缘不良可能是由于连接器绝缘材料 老化、破损或制造工艺不良等原因引 起的。它可能导致电路短路、漏电或 电击等安全问题。
短路
总结词
短路是指连接器的电路被意外短路,导致电流不经过负载直 接流过。
详细描述
极性反接可能是由于操作失误或连接器标识不清等原因引起的。它会导致电路功能异常、设备损坏或 安全问题等后果。
0错位
总结词
0错位是指连接器的插针或插孔在装配过程 中出现错位,导致无法正常插入或拔出。
详细描述
0错位可能是由于制造工艺控制不当、插针 或插孔的设计不合理或使用不当等原因引起 的。它会影响连接器的正常使用和可靠性, 严重时会导致设备损坏或安全问题。
人为操作注意事项
总结词
提高操作人员素质和意识
详细描述
加强操作人员的培训和教育,提高其专业素质和安全意 识。规范操作流程,强调安全操作注意事项,避免因人 为操作失误导致连接器损坏或事故发生。
05 连接器不良现象案例分析
案例一:某品牌手机充电口接触不良问题
总结词
充电口接触不良是手机连接器常见问题之一,可能导 致充电速度慢、无法充电或充电过程中断等问题。
VS
详细描述
压接不良可能是由于线缆插入的深度不够 、插头的端子松动或压接工具使用不当等 原因引起的。它会影响信号传输的质量和 稳定性,严重时会导致线缆脱落或电路断 路。
焊接不良
总结词
焊接不良是指连接器的焊接点存在虚焊、脱焊、焊点粗糙等问题,导致电气性能下降。
详细描述
焊接不良可能是由于焊接工艺控制不当、焊接材料质量差或焊接操作不规范等原因引起的。它会导致电路电阻增 大、接触不良或短路等安全问题。
连接器检测不良及原因

连接器检测不良及原因1 引言不论是高频电连接器,还是低频电连接器,绝缘电阻、介质耐压(又称抗电强度)和接触电阻都是保证电连接器能正常可靠地工作的最基本的电气参数。
通常在电连接器产品技术条件的质量一致性检验A、B组常规交收检验项目中都列有明确的技术指标要求和试验方法。
这三个检验项目也是用户判别电连接器质量和可靠性优劣的重要依据。
但根据笔者多年来从事电连接器检验的实践发现,目前各生产厂之间以及生产厂和使用厂之间,在具体执行有关技术条件时尚存在许多不一致和差异,往往由于采用的仪器、测试工装、操作方法、样品处理和环境条件等因素不同,直接影响到检验准确和一致。
为此,笔者认为,针对目前这三个常规电性能检验项目和实际操作中存在的问题进行一些专题研讨,对提高电连接器检验可靠性是十分有益的。
另外,随着电子信息技术的迅猛发展,新一代的多功能自动检测仪正在逐步替代原有的单参数测试仪。
这些新型测试仪器的应用必将大大提高电性能的检测速度、效率和准确可靠性。
2 绝缘电阻检验2.1作用原理绝缘电阻是指在连接器的绝缘部分施加电压,从而使绝缘部分的表面或内部产生漏电流而呈现出的电阻值。
即绝缘电阴(MΩ)=加在绝缘体上的电压(V)/泄漏电流(μA)。
通过绝缘电阻检验,确定连接器的绝缘性能能否符合电路设计的要求,或在经受高温、潮湿等环境应力时,其绝缘电阻是否符合有关技术条件的规定。
绝缘电阻是设计高阻抗电路的限制因素。
绝缘电阻低,意味着漏电流大,这将破坏电路和正常工作。
如形成反馈回路,过大的漏电流所产生的热和直流电解,将使绝缘破坏或使连接器的电性能变劣。
2.2影响因素主要受绝缘材料、温度、湿度、污损、试验电压及连续施加测试电压的持续时间等因素影响。
2.2.1绝缘材料设计电连接器时选用何种绝缘材料非常重要,它往往影响产品的绝缘电阻能否稳定合格。
如某厂原使用酚醛玻纤塑料和增强尼龙等材料制作绝缘体,这些材料内含极性基因,吸湿性大,在常温下绝缘性能可满足产品要求,而在高温潮湿下则绝缘性能不合格。
连接器十大不良
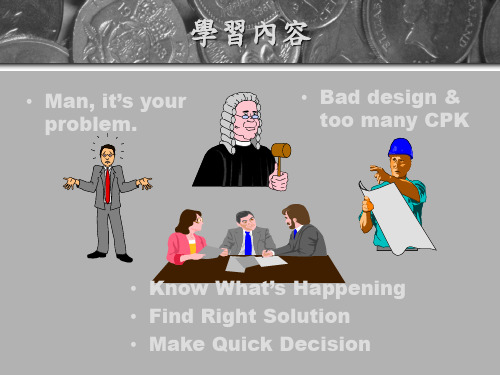
• 主因(二)
– 方向性玻纖排 列造成MD與 TD方向收縮不 均。
• 解決方案
– 採樑結購方式 設計
– 局部逃料玻亂 方向
翹曲變形(Warpage)
• 主因(三)
– 產品肉厚太薄 或流動長度過 長導致流動困 難及殘留應力 過大。
• 解決方案
– 設計考慮成型 性(如L/T比)
• 主因(四)
– 模溫冷卻系統設計 不當,公母模溫差 大。兩面收縮不同 造成翹曲。
• 解決方案
– 加肉厚降射壓 – Gate加頂針
• 主因(二)
– 頂出系統不平 衡,導致頂穿 而黏模。
• 解決方案
– 考量整體配置 – 料深區需於兩
側加裝頂針
脫模不順
• 主因(三)
– 分模線設計不 當黏母模,無 法脫模。。
• 主因(四)
– 模仁損傷或組 配不量,造成 毛頭產生影響 脫模。
• 解決方案
– 頂出平衡 – Gate與夾持面積大
之區域加裝頂針
翹曲變形(Warpage)
• 主因(七)
– 模具冷卻不足, 產品強度尚不足。 頂出時產品發生 變形。
• 解決方案
– 冷卻時間加長 – 冷卻局部熱集中
區(加冷卻機構)
短射(Short Shot)
• 現象
– 融膠射入模穴 中,產品某區 域無法完全充 填,因而產生 填料不足之現 象。
銀線(Silver Streak)
塑料除濕 乾燥完全
塑料的水份或揮 發物於射出時汽 化所致,螺桿捲 入空氣亦是原因
結論
•成型品質不是用機台調的 •產品/模具設計主宰品質 •品質是大家的問題
短射(Short Shot)
• 主因(一)
连接器三大致命故障

连接器三大致命故障
美昊电子:/news/
我们在使用连接器接线端子的过程中,或多或少都会遇到一些问题:如腐蚀、划伤、飞边、破裂,又或者是接触部位的做工粗糙、变形等各种各样的原因造成的外观不良,亦或者是配合尺寸不合等故障;JST一级代理商的美昊电子电气工程师分析接线端子常见的致命故障,归纳总结为以下3点:
1.接触不良:
导致原因:接触件设计不合理,材料选用错误,尺寸不合标准,或电镀层处理不当。
造成后果:影响电源、信号等传递,严重的可能导致无法传递。
2.固定不良:
导致原因:由于设计不可靠,选材错误,成型工艺选择不当,热处理,模具,装配,熔接等工艺质量差,装配不到位等;
也或是有时粗心大意安装不完善,或者产品耐久度有限如插拔次数太多。
造成后果:轻者影响接触可靠造成瞬间断电,严重的就是产品解体。
3.绝缘不良:
导致原因:主要的原因是由于连接器在制造的时候选材不当;也有可能是由于绝缘体表面或内部存在金属多余物,表面尘埃,焊剂等污染受潮,有机材料析出物及有害气体吸附膜与表面水膜融合形成离子性导电通道,吸潮,长霉,绝缘材料老化等原因,都会造成短路,漏电,击穿,绝缘电阻低等原因造成。
造成后果:绝缘体的作用是使接触件保持正确的位置排列,并使接触件与接触件之间,接触件与壳体之间相互绝缘。
手机连接器概述及失效分析方法
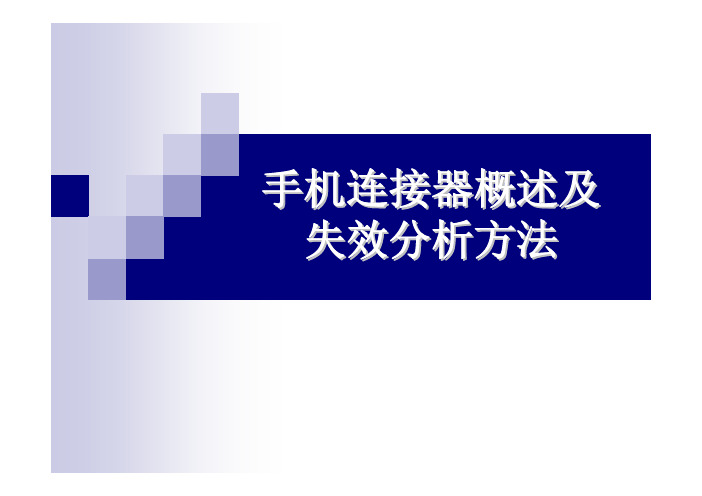
3)接触类型 接触类型有单触点和双触点两种。双接触可靠性更高,推荐使用
双接触点类型的BTB。
单接触
双接触
4)平面度 平面度直接影响焊接效果,要求控制在0.08mm以内。
5)防爬锡设计 一般端子采用露Ni电镀方式来满足要求。锡爬到端子接触区和弹片
位置会影响使用寿命及接触可靠性。
插座
插头
4.2、FPC插座:
Mini usb
micro usb
五 手机连接器生产流程简介
连接器的生产主要包括以下几方面: 1. 五金件冲压,电镀。 2. 塑胶件注塑成型 3. 成品组装(以USB为例说明)
电镀 五金件冲压成型 塑胶件注塑成型
入庫 成品组装
出货
5.1 五金件冲压
冲压是一种先进的金属加工方法,是建立在金属塑性变形的基础上,利用
2)侦测开关结构
用于侦测耳机是否插入,常见有两种结构,一种用两跟端子直接 作用,插入插头后实现闭合或者断开,从而侦测出耳机已经插入。另 一种用两跟端子通过插头实现闭合,从而实现功能,这种方式可以减 少耳机模式问题。
一
二
4.7、USB插座
用于数据传输和充电,由信号端子,塑胶,铁壳组成。有 mini,micro两种形式。按焊板方式可分为贴板式,插板式,沉 板式等几种。
2. 端子加工制造
切料,將端子切成預定 PIN數小片
通过折弯治具把端子折成要求 的形状
折弯前(左图) 折弯后(右)
3. 端子和塑胶组装 通过手工和相应治具把端子装进塑胶槽内
插针
压针
压针后 半成品
4. solder pin的成型
通过相应的治具把端子脚加工成SMT,DIP类型,并切成规格长度。
切针前
关于连接器之接线端子常见故障的分析

关于连接器之接线端子常见故障的分析接线端子的塑料绝缘材料和导电部件直接关系到端子的质量,它们分别决定了端子的绝缘性能和导电性能。
任何一个接线端子失效都将导致整个系统工程的失败。
都说预防是目的,分析是基础。
所以仪器仪表世界网指出从某个使用角度讲,接线端子应该达到的功能是:接触部位该导通的地方必须导通,接触可靠。
绝缘部位不该导通的地方必须绝缘可靠。
接线端子常见的故障形式有以下三种:1.接触不良接线端子内部的金属导体是端子的核心零件,它将来自外部电线或电缆的电压,电流或信号传递到与其相配的连接器对应的接触件上。
故接触件必须具备优良的结构,稳定可靠的接触保持力和良好的导电性能。
由于接触件结构设计不合理,材料选用错误,模具不稳定,加工尺寸超差,表面粗糙,热处理电镀等表面处理工艺不合理,组装不当,贮存使用环境恶劣和操作使用不当,都会在接触件的接触部位和配合部位造成接触不良。
2.绝缘不良绝缘体的作用是使接触件保持正确的位置排列,并使接触件与接触件之间,接触件与壳体之间相互绝缘。
故绝缘件必须具备优良的电气性能,机械性能和工艺成型性能。
特别是随着高密度,小型化接线端子的广泛使用,绝缘体的有效壁厚越来越薄。
这对绝缘材料,注塑模具精度和成型工艺等提出了更苛严的要求。
由于绝缘体表面或内部存在金属多余物,表面尘埃,焊剂等污染受潮,有机材料析出物及有害气体吸附膜与表面水膜融合形成离子性导电通道,吸潮,长霉,绝缘材料老化等原因,都会造成短路,漏电,击穿,绝缘电阻低等绝缘不良现象。
3.固定不良绝缘体不仅起绝缘作用,通常也为伸出的接触件提供精确的对中和保护,同时还具有安装定位,锁紧固定在设备上的功能。
固定不良,轻者影响接触可靠造成瞬间断电,严重的就是产品解体。
解体是指接线端子在插合状态下,由于材料,设计,工艺等原因导致结构不可靠造成的插头与插座之间,插针与插孔之间的不正常分离,将造成控制系统电能传输和信号控制中断的严重后果。
由于设计不可靠,选材错误,成型工艺选择不当,热处理,模具,装配,熔接等工艺质量差,装配不到位等都会造成固定不良。
连接器通用检验标准
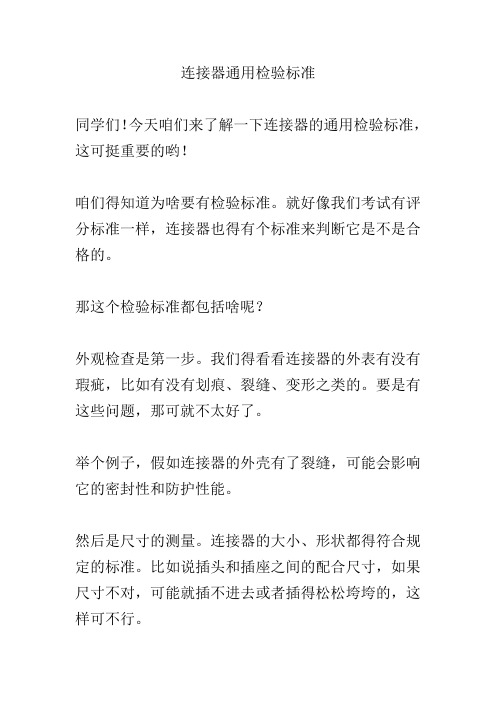
连接器通用检验标准同学们!今天咱们来了解一下连接器的通用检验标准,这可挺重要的哟!咱们得知道为啥要有检验标准。
就好像我们考试有评分标准一样,连接器也得有个标准来判断它是不是合格的。
那这个检验标准都包括啥呢?外观检查是第一步。
我们得看看连接器的外表有没有瑕疵,比如有没有划痕、裂缝、变形之类的。
要是有这些问题,那可就不太好了。
举个例子,假如连接器的外壳有了裂缝,可能会影响它的密封性和防护性能。
然后是尺寸的测量。
连接器的大小、形状都得符合规定的标准。
比如说插头和插座之间的配合尺寸,如果尺寸不对,可能就插不进去或者插得松松垮垮的,这样可不行。
再说说电气性能的检验。
这就像是检查连接器能不能好好“导电”。
我们要测测它的电阻、电容、绝缘电阻这些参数。
如果电阻太大,电流通过就会有损耗;如果绝缘电阻不够,可能会漏电,这都是很危险的。
比如说,在一些精密的电子设备中,连接器的电气性能不好,可能会导致设备故障甚至损坏。
还有插拔力的测试。
就是看看插头插进插座和拔出来的时候,需要用多大的力气。
插拔力太大或者太小都不行。
太大了插拔困难,太小了又容易松动。
手机充电线的连接器,如果插拔力不合适,用着用着可能就接触不良了。
接着是耐腐蚀性的检验。
因为连接器可能会在各种环境中使用,如果不耐腐蚀,很快就会坏掉。
在潮湿或者有化学物质的环境中,不耐腐蚀的连接器会生锈或者被腐蚀掉。
还有可靠性和稳定性的测试。
要模拟连接器在长期使用中的情况,看看它能不能一直保持良好的性能。
不断地插拔连接器,看它经过多次使用后会不会出现问题。
连接器的通用检验标准就像是给连接器做了一个全面的“体检”,从外观到性能,各个方面都要检查到位,只有都合格了,才能算是一个好的连接器。
同学们,现在是不是对连接器的检验标准有了更清楚的了解啦?。
JACK连接器8D报告(变形缺损)案例

版次:B/3有 限 公 司异 常 通 知 单□内部检查、审核 ■QC □其它□环境检查、审核 □预防措施 NO.130426-3■急件 □一般件 □厂内 ■厂外(供方) 问题发生部门提出部门品保提出时间2020年04月26日1 异 常 说 明进贵司TP6152T 开关,经敝司生产1000PCS ,检测发现有3PCS 开关按键压伤变形、缺损(见不良图片)请贵司分析上述不良原因,提出有效改善措施,以确保后续交货品质,并回复,谢谢!审核: 提出者:2 原因分析成员负责人 完成日期2020.04.27 3 不良紧急遏制计划1. 装配部立即停止生产(暂无生产) 2.暂停出货,库存品重检。
2020.04.274 根本原因分析1.此为按键套入底座时挤压变形。
2.缺损此为注塑机在长时间运作中,注塑参数发生波动,压力偏小所致。
2020.04.275 长 期 对 策1.组装时按键应单边套入底座中不可强行挤入;2.后续生产时,注塑部每小时对注塑参数进行确认一次,发现异常及时调整,并将不良品区分处理。
3.全检QC 作100%外观检查;2020.04.276 对策有效性验证暂无库存2020.04.277 再现性预防1.装配部生产时按键与底座组立须放正,组立时,先将单边扣位按入上盖到位以后再进行另一边扣位按入。
2. IPQC 巡检/QA 抽检时对产品外观有无异常作重点确认。
2020.04.278 批准: 审核: 报告人: 以上2~8项由问题发生单位填写,急件24小时内回复。
□实际完成日期及验证情况验证者:按键压伤变形 按键缺损。
JACK连接器8D报告(凸点缺失 缺料)
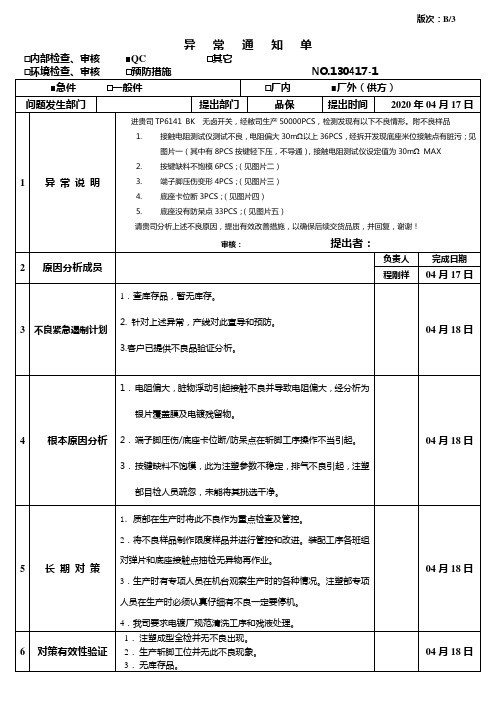
6
对策有效性验证
1.注塑成型全检并无不良出现。
2.生产斩脚工位并无此不良现象。
3.无库存品。
04月18日
7
再现性预防
1.IPQC对斩脚和注塑工位加严此不良的检查力度。
2.制不良限度样品教育全检/生产员工的品质意识。
04月18日
8
批准:审核:报告人:
以上2~8项由问题发生单位填写,急件24小时内回复。
1.查库存品,暂无库存。
2. 针对上述异常,产线对此宣导和预防。
3.客户已提供不良品验证分析。
04月18日
4
根本原因分析
1.电阻偏大,脏物浮动引起接触不良并导致电阻偏大,经分析为银片覆盖膜及电镀残留物。
2.端子脚压伤/底座卡位断/防呆点在斩脚工序操作不当引起。
3.按键缺料不饱模,此为注塑参数不稳定,排气不良引起,注塑部目检人员疏忽,未能将其挑选干净。
□实际完成日期及验证情况
验证者:
2.按键缺料不饱模6PCS;(见图片二)
3.端子脚压伤变形4PCS;(见图片三)
4.底座卡位断3PCS;(见图片四)
5.底座没有防呆点33PCS;(见图片五)
请贵司分析上述不良原因,提出有效改善措施,以确保后续交货品质,并回复,谢谢!
审核:提出者:
2
原因分析成员
负责人
完成日期
程刚祥
04月17日
3
不良紧急遏制计划
04月18日
5
长期对策
1.质部在生产时将此不良作为重点检查及管控。
2.将不良样品制作限度样品并进行管控和改进。装配工序各班组对弹片和底座接触点抽检无异物再作业。
3.生产时有专项人员在机台观察生产时的各种情况。注塑部专项人员在生产时必须认真仔细有不良一定要停机。
连接器焊接不良失效分析

连接器焊接不良失效分析黄爱珍,陆玉凤(深圳长城开发科技股份有限公司,广东深圳518000)摘要:连接器焊接不良失效时有发生,针对连接器引脚空焊不良进行了深入的分析,详细地介绍了分析的过程和手段。
通过外观检查、wetting balance 、切片、SEM+EDS 、DSC 等分析手段,发现连接器引脚空焊不良的主要原因是FPC 软板变形。
同时,提出了有效的改善对策,以降低或避免此空焊不良的发生。
关键词:连接器;柔性电路板;空焊;润湿性;变形中图分类号:TM 503+.5文献标志码:A 文章编号:1672-5468(2019)S1-0063-07doi:10.3969/j.issn.1672-5468.2019.S1.012Failure Analysis of Connector Soldering DefectsHUANG Aizhen ,LU Yufeng(Shenzhen Kaifa Technology Co.,Ltd.,Shenzhen 518000,China )Abstract :Poor welding failure of connector occurs from time to time.The poor air-welding ofconnector pin is analyzed deeply ,and the process and means of analysis are introduced in detail.Through the analysis means of appearance inspection ,wetting balance ,slice ,SEM and DSC ,it is found that the main reason for the poor welding of connector pin is the deformation of FPC .At the same time ,some effective countermeasures are put forward so as to reduce or avoid the occurrence of poor air welding .Key words :connector ;FPC ;welding opening ;wettability ;deformation收稿日期:2019-04-16作者简介:黄爱珍(1986-),女,广东深圳人,深圳长城开发科技股份有限公司项目管理工程师,从事PCB&PCBA 焊接可靠性方面的研究工作。
电池连接器改善报告

报告人:邓锋 日期:2017.2.6
一、不良描述
客户料号:SPH-650R 新龙料号:BT-0042-L1G 客诉日期:2017/1/22 不良率:2PCS 不良现象:产品BT-0042-L1G 在做整机测试過程中,發現与电池有接触不良导致手机不能 正常开机的現象.
问题样机分析:
判定结果:问题样机是由于电池连 接器导致接触不良,不能正常开机 第一步:将金 手指涂黑
第二步: 正常装配电池
第三步:验证结果 电池连接器不良 金手指没有接触痕迹
电池连接器 良品 金手指没有明显接触痕迹
二、改善团队
工程部:邓锋/ 王松/刘文东
品管部:杨谦惠/柯望春
贸易部:孙逸致/庞媚芳
生产部:孙艳/杨冬桃
3.4 既然弹片变形量正常,为什么会出现接触不良的现象呢?让我们再进一步分析 电池接触模拟图
电池金手指与弹片接触安全距离仅有0.2, 而电池斜插会对弹片产生向下变形的分 解力,弹片一旦向下变形就会接触在塑 胶隔栏上而不是金手指上,最终产生与 电池接触不良的隐患。
制程检验
成品增加弹片形状孔规全检
为有效管控制程弹 片组装导致的变形 不良,成品增加孔 规全检,能顺利放 入孔规为OK,反之 NG.
三、原因分析
3.1 将客户提供的不良品进行分析测量发现,良品与不良品弹片位置尺寸存在如下差异。 良品 不良品
标准尺寸:2.30+/-0.25 良品测量数据2.362 不良品测量数据2.029 变形量:0.333mm;
三、原因分析
3.2 电池连接器弹片变形分析:
因为电池在装配时,有一定的插入角度,虽然连 接器弹片能在电池金手指表面往上滑动,但因每 次斜插的角度不同导致弹片受力分解的方向力度 都不一样,因而如右图所示的弹片变形量是正常 的。
连接器产品制程不良原因分析及改善课件(PPT55张)

Confidential
Page:16
三 .
翹
曲
•主因(三)
–產品肉厚太薄 或流動長度過 長導致流動困 難及殘留應力 過大。
•主因(二)
–方向性玻纖排 列造成MD與TD 方向收縮不均。
•解決方案
–採樑結購方式 設計 –局部逃料玻亂 方向
Confidential
•解決方案
–設計考慮成型 性(如L/T比)
Confidential
Page:11
二 .
氣 泡
(5)料管溫度過低,造成熔膠不良,溫度過高,則 會導致原料的裂解。 (6)螺桿的清洗若不徹底,時間過久,則會導致滯 留物的裂解,產生瓦斯氣。 (7)成型加工前,塑粒乾燥程度不夠,致使水份一 直保留在塑粒之內,於成 型後之產品則容易產生 氣泡。
Confidential
• 解決方案
– 設計時儘量將 肉厚均勻化
Confidential
Page:5
一. 不
飽
模
3.模具不良原因/对策:
原因:模具温度低.---塑胶凝固过早,无法到达模 穴所有位置.
对策:适当增加模温. 原因:浇口或流道太小.---塑胶流动不畅,凝固过早, 无法到达模穴所有位置. 对策:适当加大浇口或流道.
原因:顶出不平衡---塑胶品受力不均产生变形.
改善后 原浇口 改善后
Confidential
图1
Page:7
图2
二. 1.图示:
氣 泡
中間突起
Confidential
Page:8
二 .
氣 泡
2.现象/形成原因: 由於靠近樣品表層有氣體或水汽,因PV/T為 一恆量,現溫度(T)升高,氣體的壓力(P) 及體積(V)必定要隨之增加,而材料的剛性又 不足以壓制,因而會突出表層,形成氣泡。 部分气体包在塑胶内部,过高温(IR) 后才显现出来. 内部凹陷
连接器失效机理及其对策

连接要求及其影响因素
Encnn enables connection!
连接器的失效机制/机理介绍
连接器界面的失效形式 连接器设计决定连接器内在的潜在失效机制/机理(e.g.锡镀层/微动腐
考虑尺寸公差,应用等因素,提高端子弹性工作范围 增加端子过应力保护特征:导向柱/pin/槽/机构,倒角,限位结构
正向力丧失的抵御
抵御应力松弛:
选择适当的电镀规格以保证合理的正向力要求 选择适当的端子材料控制应力释放的速度和程度 各种常见连接器端子材料在各种工作温度和电镀规格的正向力要求.
Encnn enables connection!
膜的作用方式
与收缩电阻串联 与收缩电阻并联 界面不存在膜.
Encnn enables connection!
氧化
Encnn enables connection!
Encnn enables connection!
连接器镀层抵御腐蚀的措施
贵重金属系统:
增加厚度-降低孔隙性,提高耐磨性; 施敷润滑涂层-降低裸露底层和基材的腐蚀,减少磨损,预防薄金 动腐蚀; 封孔剂-降低接触腐蚀; 施镀漂金层-降低表面腐蚀,降低孔隙性,提高耐磨性(砧板效应) 加强对环境的隔离 保证足够的正向力(整个产品寿命期) 平衡赫兹应力-较高赫兹应力增加渗透能力,也同时增加磨损率 施敷润滑涂层-预防微动腐蚀 改善设计-提高端子柔韧性 增加正向力,提高界面机械和电气稳定性 降低基材裸露的可能性和提高对腐蚀的抵御能力 减缓腐蚀攀爬 提高耐磨损性能,降低基材裸露的可能性 阻碍基材元素向表层电镀的扩散
连接器引脚上锡不良失效分析

连接器引脚上锡不良失效分析(作者:美信检测失效分析实验室)1. 案例背景送检样品为某款PCBA板,该PCBA板上一连接器在经过SMT后发现个别引脚上锡不良,失效不稳定;该连接器引脚每侧共50个引脚,材质为铜表面镀镍镀锡,PCB焊盘表面为OSP 工艺,锡膏成分为Sn-Ag-Cu(95%-3%-0.5%)。
2. 分析方法简述2.1 样品外观观察通过将失效样品和正常样品分别放在体式显微镜下观察,发现失效样品的某些引脚确实存在引脚上锡不良现象,失效引脚位置在连接器上分布不规律,但失效样品主要集中在连接器中间区域,且两端引脚上锡相对较好,典型照片见图1。
正常样品表现为两端上锡饱满,中间区域引脚上锡不饱满,典型照片见图2,该现象说明失效可能与位置相关。
上锡不良上锡不饱满上锡饱满上锡饱满上锡饱满上锡不饱满如图3~4所示,分别对NG焊点表面和未使用引脚表面进行表面SEM观察和EDS成分分析,成分测试结果见表1~2,均未发现明显污染元素,说明造成该引脚上锡不良与污染相关性不大。
表2 未使用连接器引脚表面EDS测试结果(Wt%)将NG焊点分别按照横向和纵向制作切片,观察焊点内部连接情况:如图5和表3所示,通过纵向切片可知,焊锡与焊盘间形成良好IMC层,而引脚与焊锡之间出现分离,分层中间存在异物,通过对异物进行成分分析,主要元素为C、O、Sn、Br,怀疑其可能为助焊剂;如图6和表4所示,通过横向切片可知,NG焊点引脚与焊盘存在偏位现象,表现为两侧不上锡,焊锡与焊盘形成均匀连续的IMC层,引脚底部与焊锡之间亦存在分层,中间也存在异物。
通过对分层处进行放大观察,发现引脚底部存在一层锡层,锡层成分为纯锡(如图6中位置1和2所示);而焊点焊锡成分中含少量Ag(位置4和5),与锡膏(Sn-Ag-Cu:95%-3%-0.5%)中成分相对应。
由此可推出,NG焊点引脚底部锡层为引脚表面镀锡层,因此可侧面说明NG焊点在SMT过炉过程中,引脚底部与焊锡没有良好接触。
造成连接器接触不良的4个常见原因你知道有哪些吗?
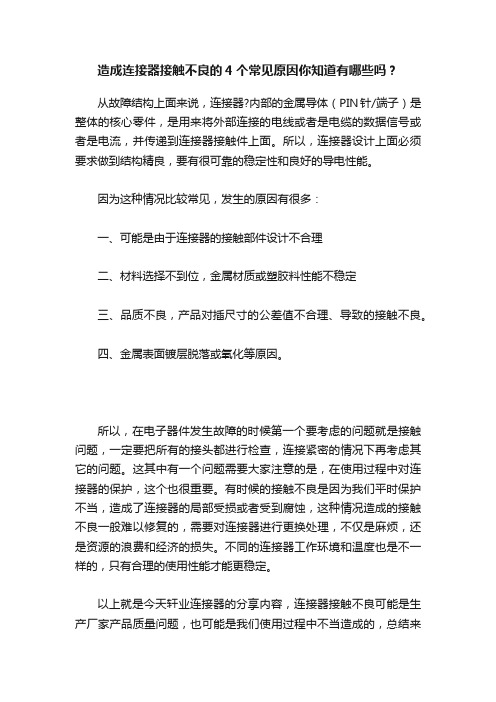
造成连接器接触不良的4个常见原因你知道有哪些吗?
从故障结构上面来说,连接器?内部的金属导体(PIN针/端子)是整体的核心零件,是用来将外部连接的电线或者是电缆的数据信号或者是电流,并传递到连接器接触件上面。
所以,连接器设计上面必须要求做到结构精良,要有很可靠的稳定性和良好的导电性能。
因为这种情况比较常见,发生的原因有很多:
一、可能是由于连接器的接触部件设计不合理
二、材料选择不到位,金属材质或塑胶料性能不稳定
三、品质不良,产品对插尺寸的公差值不合理、导致的接触不良。
四、金属表面镀层脱落或氧化等原因。
所以,在电子器件发生故障的时候第一个要考虑的问题就是接触问题,一定要把所有的接头都进行检查,连接紧密的情况下再考虑其它的问题。
这其中有一个问题需要大家注意的是,在使用过程中对连接器的保护,这个也很重要。
有时候的接触不良是因为我们平时保护不当,造成了连接器的局部受损或者受到腐蚀,这种情况造成的接触不良一般难以修复的,需要对连接器进行更换处理,不仅是麻烦,还是资源的浪费和经济的损失。
不同的连接器工作环境和温度也是不一样的,只有合理的使用性能才能更稳定。
以上就是今天轩业连接器的分享内容,连接器接触不良可能是生产厂家产品质量问题,也可能是我们使用过程中不当造成的,总结来
说既要选择好的连接器厂家,也要好好保护连接器,这样才能使用的更为长久,不易发生故障。
更多连接器厂家信息或连接器知识请关注轩业连接器。
低频连接器电缆组件的故障诊断和维修技术

低频连接器电缆组件的故障诊断和维修技术1. 引言低频连接器电缆组件在现代通信和电子设备中起到至关重要的作用。
然而,由于长期使用、恶劣环境和错误操作等原因,这些组件有时会出现故障。
本文将介绍低频连接器电缆组件常见的故障类型,并提供相应的诊断和维修技术。
2. 故障类型2.1 连接不良连接不良是低频连接器电缆组件最常见的故障类型之一。
连接不良可能导致信号传输中断或者信号质量下降。
常见的连接不良原因包括接触点腐蚀、接触力不足和插拔次数过多。
2.2 线路断开线路断开会导致信号无法传输。
线路断开的原因可能包括电缆损坏、导线断裂或焊点断裂。
线路断开通常需要通过替换电缆或修复焊点来解决。
2.3 短路短路是指电缆中的两个或多个导线之间发生不应有的短路。
短路可能导致设备损坏或者电路故障。
短路的常见原因包括导线绝缘损坏和导线之间的意外接触。
2.4 电缆损坏电缆损坏可能会导致信号传输中断或信号质量下降。
电缆损坏的原因包括外部机械损伤、压力过大、温度过高等。
电缆损坏通常需要替换整根电缆来解决。
3. 故障诊断技术3.1 目视检查目视检查是最常用的故障诊断技术之一。
通过仔细检查连接器和电缆组件,可以发现一些明显的故障,如腐蚀、断裂或损坏。
目视检查应该在清洁的工作区域进行,并使用适当的照明设备。
3.2 电压测试电压测试可以用来检测导线之间的连接状态和信号传输质量。
使用万用表或示波器测量不同连接点之间的电压,可以确定是否存在连接不良或线路断开的问题。
3.3 电阻测试电阻测试可以用来检测导线之间的连接状态和导线质量。
使用万用表或电阻测试仪测量不同连接点之间的电阻,可以判断是否存在连接不良、线路断开或短路等问题。
4. 维修技术4.1 清洁连接器当连接不良是故障的原因时,首先应该清洁连接器。
使用去脂剂或清洁液清洁连接器接触点,然后用干净的棉球或软布擦拭干净。
如果接触点出现腐蚀,可以使用细砂纸或针尖轻轻擦拭,恢复接触点的光洁度。
4.2 焊接修复对于焊点断裂或导线断裂的情况,可以使用焊接工具重新焊接。
连接器引脚上锡不良失效分析

连接器引脚上锡不良失效分析(作者:美信检测失效分析实验室)1. 案例背景送检样品为某款PCBA板,该PCBA板上一连接器在经过SMT后发现个别引脚上锡不良,失效不稳定;该连接器引脚每侧共50个引脚,材质为铜表面镀镍镀锡,PCB焊盘表面为OSP 工艺,锡膏成分为Sn-Ag-Cu(95%-3%-0.5%)。
2. 分析方法简述2.1 样品外观观察通过将失效样品和正常样品分别放在体式显微镜下观察,发现失效样品的某些引脚确实存在引脚上锡不良现象,失效引脚位置在连接器上分布不规律,但失效样品主要集中在连接器中间区域,且两端引脚上锡相对较好,典型照片见图1。
正常样品表现为两端上锡饱满,中间区域引脚上锡不饱满,典型照片见图2,该现象说明失效可能与位置相关。
上锡不良上锡不饱满上锡饱满上锡饱满上锡饱满上锡不饱满如图3~4所示,分别对NG焊点表面和未使用引脚表面进行表面SEM观察和EDS成分分析,成分测试结果见表1~2,均未发现明显污染元素,说明造成该引脚上锡不良与污染相关性不大。
表2 未使用连接器引脚表面EDS测试结果(Wt%)将NG焊点分别按照横向和纵向制作切片,观察焊点内部连接情况:如图5和表3所示,通过纵向切片可知,焊锡与焊盘间形成良好IMC层,而引脚与焊锡之间出现分离,分层中间存在异物,通过对异物进行成分分析,主要元素为C、O、Sn、Br,怀疑其可能为助焊剂;如图6和表4所示,通过横向切片可知,NG焊点引脚与焊盘存在偏位现象,表现为两侧不上锡,焊锡与焊盘形成均匀连续的IMC层,引脚底部与焊锡之间亦存在分层,中间也存在异物。
通过对分层处进行放大观察,发现引脚底部存在一层锡层,锡层成分为纯锡(如图6中位置1和2所示);而焊点焊锡成分中含少量Ag(位置4和5),与锡膏(Sn-Ag-Cu:95%-3%-0.5%)中成分相对应。
由此可推出,NG焊点引脚底部锡层为引脚表面镀锡层,因此可侧面说明NG焊点在SMT过炉过程中,引脚底部与焊锡没有良好接触。
导致连接器产品接触不良的具体原因分析介绍

导致连接器产品接触不良的具体原因分析介绍电子产品中,接触不良的故障的比例非常大,而且这种故障很麻烦,特别是连接器,而常用的连接器有金属连接器、防水连接器等等。
这些连接器因为会表现出来有时好有时坏,分析起来很麻烦。
而且,有时的接触不良体现出来的现象会令人迷惑不解。
有些元器件是因为自身内部的接触不良,也有元器件互连时的接触不良,也有虚焊(一般为组件与PCB)产生的不良。
下面以最常见的连接器(接插件)之间的接触为实例分析接触不良问题,之后大家可以触类旁通。
连接器一般是针接触件和孔接触件之间的连接。
我们知道,元器件的引脚或端子,一般是有一层镀层,比如镀铅锡合金、镀纯锡、镀镍、镀银、镀银钯合金、镀金、等等。
所以组件之间的接触,其实就是这些镀层金属之间的接触。
当然,不同的镀层金属的导电率是不同的,对应产生的接触电阻也有所不同。
一般金的导电率比较好,银次之。
在焊接工艺时,由于焊接实际上是形成合金的过程,这个合金本身就是良导体,所以焊接本身的可靠性是比较高的,除非是焊接不良。
但是,连接器之间的连接,靠的是表面之间的接触,所以容易导致接触不良,更具体的原因分析如下。
两个金属表面之间的接触是否良好,主要取决于材料(不同金属导电率不同)、接触压力、实际接触面结。
关于材料种类,上面已经提到了,一般器件的镀层材料,基本上都是由良导体做的,对接触不良的影响不大,顶多影响接触电阻(当然更进一步来说还影响到了是否容易被氧化),所以不再更详细地讨论。
关于连接器的接触压力,连接器靠的是孔接触件的弹力来给针接触件一定的压力的。
一般压力越大接触得也越好。
当然,一般小而又薄的孔接触件是不太可能提供特大的压力的。
而且如果这个孔接触件本身的弹性不好,这个压力就小,接触也就没那么好。
同时,如果孔接触件或针接触件有变形,也会导致实际接触面积小,从而有可能导致接触不良。
同时,连接器的孔接触件或针接触件当然一般是连接在塑料上的,如果脚数多了,有可能导致某一个或数个接触件装在塑料件上的位置有偏差,于是,两个连接器插入时,那些偏位了的接触件就有可能接触不好。
- 1、下载文档前请自行甄别文档内容的完整性,平台不提供额外的编辑、内容补充、找答案等附加服务。
- 2、"仅部分预览"的文档,不可在线预览部分如存在完整性等问题,可反馈申请退款(可完整预览的文档不适用该条件!)。
- 3、如文档侵犯您的权益,请联系客服反馈,我们会尽快为您处理(人工客服工作时间:9:00-18:30)。
连接器检测不良及原因1引言不论是高频电连接器,还是低频电连接器,绝缘电阻、介质耐压(又称抗电强度)和接触电阻都是保证电连接器能正常可靠地工作的最基本的电气参数。
通常在电连接器产品技术条件的质量一致性检验A、B组常规交收检验项目中都列有明确的技术指标要求和试验方法。
这三个检验项目也是用户判别电连接器质量和可靠性优劣的重要依据。
但根据笔者多年来从事电连接器检验的实践发现,目前各生产厂之间以及生产厂和使用厂之间,在具体执行有关技术条件时尚存在许多不一致和差异,往往由于采用的仪器、测试工装、操作方法、样品处理和环境条件等因素不同,直接影响到检验准确和一致。
为此,笔者认为,针对目前这三个常规电性能检验项目和实际操作中存在的问题进行一些专题研讨,对提高电连接器检验可靠性是十分有益的。
另外,随着电子信息技术的迅猛发展,新一代的多功能自动检测仪正在逐步替代原有的单参数测试仪。
这些新型测试仪器的应用必将大大提高电性能的检测速度、效率和准确可靠性。
2绝缘电阻检验2.1作用原理绝缘电阻是指在连接器的绝缘部分施加电压,从而使绝缘部分的表面或内部产生漏电流而呈现出的电阻值。
即绝缘电阴(MΩ)=加在绝缘体上的电压(V)/泄漏电流(μA)。
通过绝缘电阻检验,确定连接器的绝缘性能能否符合电路设计的要求,或在经受高温、潮湿等环境应力时,其绝缘电阻是否符合有关技术条件的规定。
绝缘电阻是设计高阻抗电路的限制因素。
绝缘电阻低,意味着漏电流大,这将破坏电路和正常工作。
如形成反馈回路,过大的漏电流所产生的热和直流电解,将使绝缘破坏或使连接器的电性能变劣。
2.2影响因素主要受绝缘材料、温度、湿度、污损、试验电压及连续施加测试电压的持续时间等因素影响。
2.2.1绝缘材料设计电连接器时选用何种绝缘材料非常重要,它往往影响产品的绝缘电阻能否稳定合格。
如某厂原使用酚醛玻纤塑料和增强尼龙等材料制作绝缘体,这些材料内含极性基因,吸湿性大,在常温下绝缘性能可满足产品要求,而在高温潮湿下则绝缘性能不合格。
后采用特种工程塑料PES(聚苯醚砜)材料,产品经200℃、1000h和240h潮湿试验,绝缘电阻变化较小,仍在105MΩ以上,无异常变化。
2.2.2温度高温会破坏绝缘材料,引起绝缘电阻和耐压性能降低。
对金属壳体,高温可使接触件失去弹性、加速氧化和发生镀层变质。
如按GJB598生产的耐环境快速分离电连接器系列II产品,绝缘电阻规定25℃时应不小于5000MΩ,而200℃时,则降低至不小于500MΩ。
2.2.3温度潮湿环境引起水蒸气在绝缘体表面的吸引和扩散,容易使绝缘电阻降低到MΩ级以下。
长期处于高温环境下会引起绝缘体物理变形、分解、逸出生成物,产生呼吸效应及电解腐蚀及裂纹。
如按GJB2281生产的带状电缆电连接器,标准大气条件下的绝缘电阻值应不小于5000MΩ,而经相对湿度90%~95%、温度40±2℃、96h湿热试验后的绝缘电阻降至不小于1000MΩ。
2.2.4污损绝缘体内部和表面的洁净度对绝缘电阻影响很大,由于注塑绝缘体用的粉料或胶接上、下绝缘安装板的胶料中混有杂质,或由于多次插拔磨损残留的金属屑及锡焊端接时残留的焊剂渗入绝缘体表面,都会明显降低绝缘电阻。
如某厂生产的圆形电连接器在成品交收试验时发现有一个产品接触件之间的绝缘电阻很低,仅20MΩ,不合格。
后经解剖分析发现,这是因注塑绝缘体用的粉料中混有杂质而造成的。
后只得将该批产品全部报废。
2.2.5试验电压绝缘电阻检验时施加的试验电压对测试结果有很大关系。
因为试验电压升高时,漏电流的增加不成线性关系,电流增加的速率大于电压增加的速率,故试验电压升高时测得的绝缘电阻值将会下降。
电连接器产品技术条件引用的试验方法中,对试验电压都有明确的规定,通常规定为500V。
因此不能用一般欧姆表、直流电桥等电阻测量仪器来测量绝缘电阻。
2.2.6持续时间(读数时间)由于被测电连接器在测量极之间存在着一定的电容,测量初期电源先要对电容充电,因此在测试时往往会出现绝缘电阻测试仪上指示的电阻值有逐渐上升的趋势,这是正常现象。
不少电连接器试验方法中明确规定,读取绝缘电阻测试仪上的读数必须在电压施加1min后进行。
2.3问题研讨2.3.1检验环境温、湿度的影响电连接器技术条件通常都规定了产品的使用环境温度和湿度,如温度为-55~125℃,湿度为40±2℃、95%±3%。
笔者认为,检验环境条件和使用环境条件是有区别的。
技术条件规定产品可以在上述温湿度使用环境下工作,并不意味着生产厂在上述使用环境条件下测试绝缘电阻都应满足正常大气压下的考核指标。
如有使用温度上限125℃和40±2℃、93%±3%湿热环境条件下测绝缘电阻,则应按技术条件规定的高温和湿热环境试验的考核指标进行考核,而不应按正常大气压下的考核指标进行考核。
笔者在实际检验时多次发现,同一批产品在北方气候较干燥的条件下(湿度<50%)出厂检验绝缘电阻大于1000MΩ,是合格的;但产品发运至南方使用厂,在较潮湿的环境下(湿度>80%)复验,绝缘电阻仅为100MΩ~200MΩ,属不合格。
遇此情况,有时用酒精清洗烘干后,刚取出检验是合格的,但放置到次日再复测又不合格。
为此,建议生产厂在产品交收试验时,应将绝缘电阻控制在规定值以上一个恰当水平,保持有一定的裕度;不要将在干燥环境下勉强达到规定值的产品判为合格出厂,以免供需双方因检验气候环境条件不同造成检验结果不一致而引起争议。
为明确检验环境温湿度要求,现在有部分试验方法既规定了测试的环境温湿度(相对较宽的范围),又规定了出现分歧仲裁时的温湿度要求(相对取中限较窄的范围)。
如GJB1217-91《电连接器试验方法》规定:试验的标准大气条件,温度15~35℃,湿度20%~80%,气压73~103kPa。
仲裁试验的标准大气条件,温度25±1℃,湿度50%±2%,气压86~106kPa。
2.3.2检验工装的影响电连接器技术条件规定,电连接器所有接触件之间和所有接触件与壳体之间的绝缘电阻都应符合规定值;又规定其施加电压的持续时间要大于1min。
故许多电连接器生产厂对其所生产的每一型号规格产品都备有相应的2~3个不同编排连接方式的检验工装(头孔配座针工装或头针配座孔工装),通过对其接触件点与点之间、排与排之间和所有接点与壳体之间并联施加试验电压,检验其绝缘电阻是否合格。
这种用检验工装并联施加电压比单个接点间施加电压条件苛刻。
故若用检验工装测试发现绝缘电阻不合格时,允许不用工装直接用表棒在单点间施加电压进行复测。
但现有部分生产厂和绝大多数使用单位都不用检验工装,而是直接采用与绝缘电阻测试仪相连的两根测试表棒,在每个接触件之间或接触件与壳体之间搭接,检验其绝缘电阻是否合格。
这种不同检验工装的方法有以下缺点:一是随机性很大,极有可能产生漏检;二是每个接点不可能像有检验工装那样,可以停留1min后再读数,故有可能造成误判,检验的可靠性较差。
当然,即使使用检验工装,在检验前必须首先保证工装合格,要保证工装洁净和干燥,其本身绝缘电阻必须合格,且留有充分余量。
3介质耐压检验3.1作用原理介质耐压检验又称抗电强度检验。
它是在连接器接触件与接触件之间、接触件与壳体之间,在规定时间内施加规定的电压,以此来确定连接器额定电压下能否安全工作,能否耐受由于开关浪涌及其它类似现象所导致的过电位的能力,从而评定电连接器绝缘材料或绝缘间隙是否合格。
如果绝缘体内有缺陷,在施加试验电压后,则必然产生击穿放电或损坏。
击穿放电表现为飞弧(表面放电)、火花放电(空气放电)或击穿(击穿放电)现象。
过大漏电流可能引起电参数或物理性能的改变。
由于过电位,即使是在低于击穿电压时也可能有损于绝缘或降低其安全系数,所以应当慎重地进行介质耐压检验。
在例行试验中,如果需要连续施加试验电压时,最好在进行随后的试验时降低电位。
3.2影响因素主要受绝缘材料、洁净度、湿度、大气压力、接触件间距、爬电距离和耐压持续时间等因素影响。
3.2.1绝缘材料设计必须选用恰当的工程塑料制作绝缘体,才能满足预定的耐压性能指标要求。
如选用击穿电压为16kV/mm的PES(聚苯醚砜)特种工程塑料,能满足GJB598《耐环境快速分离圆形电连接器》YB系列II产品标准大气压下耐压为1500V的要求。
氟塑料(F4)具有比其它材料更高的介质耐压和绝缘电阻,广泛用于制作射频同轴电连接器绝缘体。
3.2.2洁净度绝缘体内部和表面洁净度对介质耐压影响很大。
笔者在某圆形连接器补充筛选时发现有一产品要求耐压1500V,实际测试施加电压至400V,即在两个接触件之间产生击穿现象。
经与生产厂共同进行解剖分析后认为:击穿发生于绝缘体上、下两个绝缘安装板的胶接界面,是由于胶粘剂中混有杂质所致。
3.2.3湿度增加湿度会降低介质耐压。
如J36A矩形电连接器技术条件规定:正常条件下耐压为1000V;而经40±2℃、93%±2℃、48h湿热试验后耐压降为500V。
3.2.4低气压在空气稀薄的高空,绝缘体材料会放出气体污染接触件,并使电晕产生的趋势增加,耐压性能下降,使电路产生短路故障。
故高空使用的非密封电连接器都必须降额使用,如Y27A圆形电连接器技术条件规定:正常条件下耐压为1300V,而在1.33Pa低气压条件下耐压降为200V。
3.2.5接触件间距连接器的小型化和高密度的发展,具体体现在矩形电连接器和印制电路电连接器上,要求间距能达到0.635mm,甚至0.3mm,外形尺寸中最关键的高度尺寸已减小到1~1.5mm。
表面贴装技术(SMT)与小型化的发展有着密切的关系。
这就要求我们选用耐压性能更高的绝缘材料,以满足设计尺寸小型化的要求。
3.2.6爬电距离它是指接触件与接触件之间,或接触件与壳体之间沿绝缘体表面量得的最短距离。
爬电路离短容易引起表面放电(飞弧)。
故有部分连接器的绝缘安装板表面插针(孔)安装孔设计成凹凸台阶形状,以增加爬电距离,提高抵抗表面放电的能力。
3.2.7耐压持续时间一般电连接器技术条件均规定为电压施加到规定值后持续1min应无击穿、飞弧、放电现象。
但许多电连接器生产厂在做成品交收试验时,为提高检测速度,往往采用提高试验电压20%、缩短耐压持续时间为5s或10s的方法。
笔者认为,它们之间不存在某种函数关系。
从交流耐压击穿机理来分析,击穿主要是由泄漏引起的,即泄漏电流大于规定值就认为击穿。
另一种是热击穿,提高试验电压强加泄漏,热击穿与时间长短没有关系。
如国军标GJ1217-91《电连接器试验方法》规定,试验电压加至规定值后应持续1min。
当有规定时,厂内质量一致性试验时的保持时间可降至最少5s。