热芯盒覆膜砂制芯技改过程综述
热交换器铝铸件热芯盒覆膜砂制芯工艺的应用(1)

69120
11060 38870
1500 & 580
22~ 25
12270 1600 & 660
18~ 20
1500 & 450
20~ 22
40210 860 & 650
19~ 21
1120 & 400
19~ 21
12270 860 & 650
22~ 25
1200 & 450
22~ 25
1500 & 1000 & 3041 1900& 1110& 3305 1600 & 710& 2950 1000 & 900 & 3300 1105& 1470& 2105 1700 & 900& 3220 1200 & 990& 2565
压缩弹簧的作用, 处于顶
出状态; 合模后, 顶芯板
在复位杆的作用下处于原
始位置; 当砂芯固化结束
图 3 弹簧顶芯机构
开模时,
压缩弹簧推动顶 1
5
芯盒 2 限位块 3 顶芯板 4 轴套 连接板 6 顶芯杆 7 弹簧 8 复位杆
芯板和顶芯杆保证砂芯留
在有顶芯的一面。压缩弹簧由耐热的弹簧钢制成, 压
缩后的最大工作负荷略大于砂芯在定模处的包容力和
540 & 325 & 320 570 & 430 & 460 505 & 280 & 580 640 & 410 & 360 320 & 300 & 260 385 & 300 & 440 420 & 170 & 200
缸盖水腔芯的热芯盒覆膜砂制芯

关键词 : 盖 , 芯 ,热芯 盒制 芯 ,覆膜 砂 缸 砂 中图分 类号 : G 4 7: 献标 识码 : 文 章编 号 : 0 — 6 8 2 0 ) 1 2 T 1 2. 文 A; 1 6 9 5 (0 80 — 0
柴 ( ) 发 动 机缸 盖 水 腔 砂 芯结 构 复 杂 , 汽 油 尺寸 精 度高 , 壁厚 薄 , 清理 困难 。 据其特 点 , 内大 部 分 根 国
吸湿 性很 小 , 长期存 放 。 可
④在高温铁液的作用下 , 树脂烧损 , 砂芯溃散性
特别 好 , 方便 于除 芯 。
1 缸盖 水腔 芯热 芯盒工 艺 的使用情 况
图 2 插入式射砂嘴 I I
象l 则可根据试模时的 实际情况 , 在该射砂嘴 与射砂板 的连接面处 垫相应厚度 紫铜 皮垫
2 8
维普资讯
材 料 工 艺 M TR L E H O O Y A E I &TC N L G A
大 减 小开模 时 射砂 棒所 受 的包 容 阻力 ,保 证 射砂 棒 能从上芯 盒 内顺 利脱 出 。
为 了增 大操 作 空 间并 降低 设备 造 价 ,垂 直分 型
封效果 , 调整结束后再打上骑缝螺钉 。 2 图 结构的射 砂 嘴相 对 图 1 构而 言 ,在射 砂嘴 A 平 面处设 置一 结 耐热 密封 圈 ,射 砂 时密 封 圈压 紧 B平 面来 保证 密封
效果 。 2结构 的射砂 嘴工 作时 , 芯形 状 的要求 将 其分 为 上下
为 了解 决无 上 顶芯情 况 下水 平分 型 射砂 棒 易 于 折 断的 问题 , 以采 用 图 1 图 2两 种 结构 的插 入 式 可 、
覆膜砂工艺流程

覆膜砂生产工艺流程及应用覆膜砂铸造在造型、制芯时大多数铸件都是用湿型和干型铸造的,90%以上的砂芯用烘干炉干燥的砂芯油作粘结剂,是由德国人J.Croning开发了以酚醛树脂作粘结剂的壳型造型,使合成树脂粘结剂及合成树脂砂进入铸造工业。
以合成树脂作粘结剂的制型(芯)的方法主要有:1、热法:砂型(芯)的成型和硬化直接在模板上或芯盒内靠已加热的模板(芯盒)或通热热气流完成。
主要有壳法(壳型、壳芯的制造法)、热芯盒法、温芯盒法。
2、冷法:砂型(芯)的成型、硬化在室温下完成。
主要有自硬法、气硬冷芯盒法(三乙胺法、SO2法、无毒、低毒气体促硬法)。
上述新型制芯、造型技术的开发和应用,给铸造生产工艺带来了一场重大变革,其提高了砂型(芯)的尺寸精度,简化了制芯工艺,减少了能耗,降低了对熟练工人的需求,提高了生产效率,同时提高了铸件质量(铸件尺寸、表面粗糙度),使砂型铸造朝着近无余量铸件的铸造工艺迈出了一大步。
但应当指出,上述的制芯、制型法目前均在一定的范围内适用。
生产实际应用上具体选用哪一种工艺往往受多种因素的影响,除了考虑生产纲领、材质、尺寸的大小以及质量要求外,还需考虑投资大小、能源供应、人员素质、管理水平、以及公害、污染等因素。
我国在50年代末就开展了这方面的试验研究工作。
由于当时我国壳型用酚醛树脂的性能不过关和供应难以保证,价格也较高,而且当时我国还没有专用的覆膜砂生产设备,特别是汽车工业十分落后,对铸件也没有很高的质量要求等多方面的原因,壳型工艺在我国没有得到推广和应用。
80年代以后,随着我国汽车工业的迅速发展,对铸件的质量也提出了很高的要求,于是一汽从英国引进了一套热法树脂覆膜砂设备,并通过技术消化开发出了国产SZ7215型热法覆膜砂混砂装置。
随后济南铸锻机械研究所等一些科研单位和院校一方面改进覆膜砂混砂设备,提高它的牵引动力和搅拌速度,从而改善了酚醛树脂在硅砂表面的覆膜效果,另一方面,在方面过程中添加各种附加物,以提高覆膜砂的强度、耐热性和溃散性,于是树脂覆膜砂在我国的汽车、拖拉机、柴油机工厂中得到了广泛的应用。
2024年覆膜砂壳型制造工艺

覆膜砂壳型制造工艺是一种把砂、砂芯或砂芯和非金属复合物焊接在
外壳上的技术。
它通常用于制造海洋电力装置、电缆接头,以及船舶的电
气部件、滤波器等。
覆膜砂壳型工艺的基本步骤如下:
一、准备外壳
首先需要准备外壳,将根据实际应用需要选择铝合金或者不锈钢材料,然后冲孔处理,获得满足要求的外壳结构,以及与砂芯相匹配的尺寸孔径,确保将来填充砂、砂芯或砂芯和非金属复合物时能够完美的结合在一起。
二、砂填充
接下来就要填充砂,将砂分别摆放到外壳内,分别使用不同种类的砂,可以根据实际应用的情况灵活选择合适的砂,经过完美填充,再将填充完
的砂块紧实固定。
三、砂芯安装
在填充完砂后,接下来就是安装砂芯。
根据实际应用的情况,安装砂
芯的材料可以是铝合金、不锈钢或其他材料,要求砂芯的外形结构和尺寸
要与外壳内的空隙完全匹配,同时要把砂芯紧紧固定在外壳内。
四、砂芯复合
紧接着,就是进行砂芯复合,将砂芯和非金属复合物(如膨胀螺栓或
涂胶)进行复合,保证复合后的结构紧密,并做到抗拉力、抗扭力以及抗
振动能力。
热芯盒覆膜砂制芯技改过程
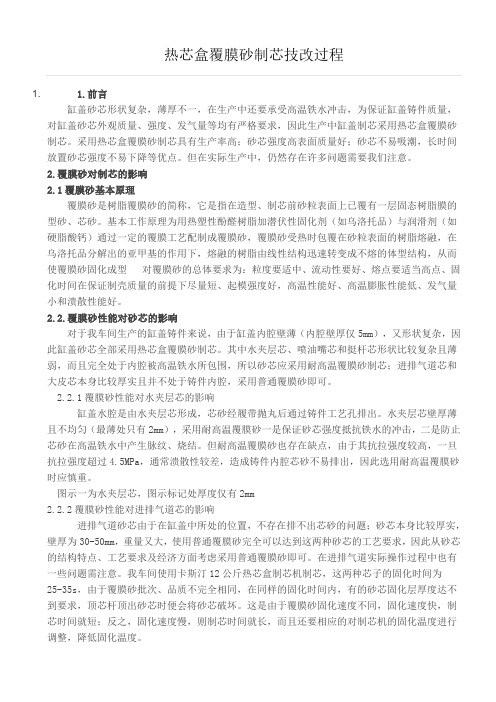
热芯盒覆膜砂制芯技改过程1. 1.前言缸盖砂芯形状复杂,薄厚不一,在生产中还要承受高温铁水冲击,为保证缸盖铸件质量,对缸盖砂芯外观质量、强度、发气量等均有严格要求,因此生产中缸盖制芯采用热芯盒覆膜砂制芯。
采用热芯盒覆膜砂制芯具有生产率高;砂芯强度高表面质量好;砂芯不易吸潮,长时间放置砂芯强度不易下降等优点。
但在实际生产中,仍然存在许多问题需要我们注意。
2.覆膜砂对制芯的影响2.1覆膜砂基本原理覆膜砂是树脂覆膜砂的简称,它是指在造型、制芯前砂粒表面上已覆有一层固态树脂膜的型砂、芯砂。
基本工作原理为用热塑性酚醛树脂加潜伏性固化剂(如乌洛托品)与润滑剂(如硬脂酸钙)通过一定的覆膜工艺配制成覆膜砂,覆膜砂受热时包覆在砂粒表面的树脂熔融,在乌洛托品分解出的亚甲基的作用下,熔融的树脂由线性结构迅速转变成不熔的体型结构,从而使覆膜砂固化成型对覆膜砂的总体要求为:粒度要适中、流动性要好、熔点要适当高点、固化时间在保证制壳质量的前提下尽量短、起模强度好,高温性能好、高温膨胀性能低、发气量小和溃散性能好。
2.2.覆膜砂性能对砂芯的影响对于我车间生产的缸盖铸件来说,由于缸盖内腔壁薄(内腔壁厚仅5mm),又形状复杂,因此缸盖砂芯全部采用热芯盒覆膜砂制芯。
其中水夹层芯、喷油嘴芯和挺杆芯形状比较复杂且薄弱,而且完全处于内腔被高温铁水所包围,所以砂芯应采用耐高温覆膜砂制芯;进排气道芯和大皮芯本身比较厚实且并不处于铸件内腔,采用普通覆膜砂即可。
2.2.1覆膜砂性能对水夹层芯的影响缸盖水腔是由水夹层芯形成,芯砂经履带抛丸后通过铸件工艺孔排出。
水夹层芯壁厚薄且不均匀(最薄处只有2mm),采用耐高温覆膜砂一是保证砂芯强度抵抗铁水的冲击,二是防止芯砂在高温铁水中产生脉纹、烧结。
但耐高温覆膜砂也存在缺点,由于其抗拉强度较高,一旦抗拉强度超过4.5MPa,通常溃散性较差,造成铸件内腔芯砂不易排出,因此选用耐高温覆膜砂时应慎重。
图示一为水夹层芯,图示标记处厚度仅有2mm2.2.2覆膜砂性能对进排气道芯的影响进排气道砂芯由于在缸盖中所处的位置,不存在排不出芯砂的问题;砂芯本身比较厚实,壁厚为30-50mm,重量又大,使用普通覆膜砂完全可以达到这两种砂芯的工艺要求,因此从砂芯的结构特点、工艺要求及经济方面考虑采用普通覆膜砂即可。
热芯盒射芯机使用覆膜砂的方法

热芯盒射芯机使用覆膜砂的方法
洪热生
【期刊名称】《铸造技术》
【年(卷),期】1991()4
【摘要】热芯盒射芯机一般使用尿醛树脂砂、尿酚醛树脂砂、呋喃Ⅰ、Ⅱ型树脂砂等热芯盒用砂。
这些砂流动性能较差,存放时间短、制做壁薄、形状复杂的砂芯,质量难以保证,在一些厂家射芯机利用率较低。
而热固性酚醛树脂砂(即覆膜砂),具有和干砂一样的流动性,混制好后存放时间可达半年以上,砂芯强度高,因此适合制做壁薄复杂的芯(型)。
我厂就使用Z8525A射芯机(已改为热模)生产S195曲轴覆模砂薄壳砂型(背为热铁型)。
热芯盒射芯机使用覆膜砂,只需对原工装中的射砂板进行简单的改造,以解决覆膜砂在不射砂时的自动下落问题。
【总页数】2页(P34-35)
【关键词】热芯盒射芯机;覆膜砂
【作者】洪热生
【作者单位】永安内燃机配件厂
【正文语种】中文
【中图分类】TG231.66
【相关文献】
1.缸盖水腔芯的热芯盒覆膜砂制芯 [J], 陈剑敏
2.ZHTO750射芯机一盒两芯制作气缸体水套砂芯热芯盒的优化设计 [J], 彭显平
3.覆膜砂热芯盒法在柴油机缸盖水套砂芯上的应用 [J], 赵军;黄占有
4.射砂棒对覆膜砂热芯盒制芯的影响及解决方法 [J], 陈剑敏
5.用热芯盒射芯机射制酚醛树脂覆膜砂芯 [J], 车传阳;白凤阳
因版权原因,仅展示原文概要,查看原文内容请购买。
热芯盒制芯的关键工艺环节综述
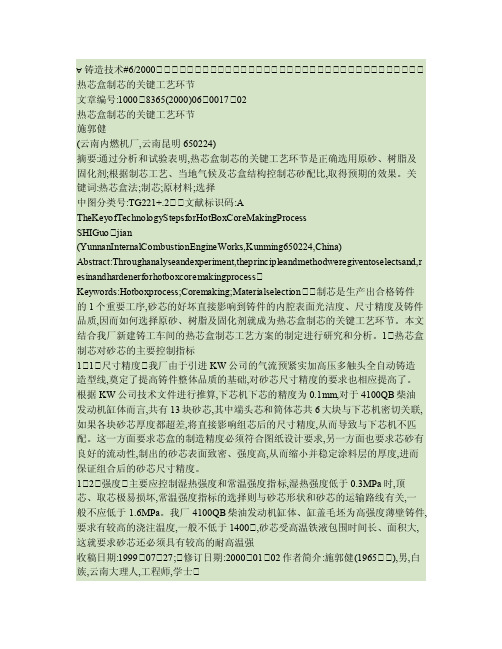
∀铸造技术#6/2000热芯盒制芯的关键工艺环节文章编号:10008365(2000)06001702热芯盒制芯的关键工艺环节施郭健(云南内燃机厂,云南昆明650224)摘要:通过分析和试验表明,热芯盒制芯的关键工艺环节是正确选用原砂、树脂及固化剂;根据制芯工艺、当地气候及芯盒结构控制芯砂配比,取得预期的效果。
关键词:热芯盒法;制芯;原材料;选择中图分类号:TG221+.2文献标识码:A TheKeyofTechnologyStepsforHotBoxCoreMakingProcessSHIGuo jian(YunnanInternalCombustionEngineWorks,Kunming650224,China)Abstract:Throughanalyseandexperiment,theprincipleandmethodweregiventoselectsand,r esinandhardenerforhotboxcoremakingprocessKeywords:Hotboxprocess;Coremaking;Materialselection制芯是生产出合格铸件的1个重要工序,砂芯的好坏直接影响到铸件的内腔表面光洁度、尺寸精度及铸件品质,因而如何选择原砂、树脂及固化剂就成为热芯盒制芯的关键工艺环节。
本文结合我厂新建铸工车间的热芯盒制芯工艺方案的制定进行研究和分析。
1热芯盒制芯对砂芯的主要控制指标11尺寸精度我厂由于引进KW公司的气流预紧实加高压多触头全自动铸造造型线,奠定了提高铸件整体品质的基础,对砂芯尺寸精度的要求也相应提高了。
根据KW公司技术文件进行推算,下芯机下芯的精度为0.1mm,对于4100QB柴油发动机缸体而言,共有13块砂芯,其中端头芯和筒体芯共6大块与下芯机密切关联,如果各块砂芯厚度都超差,将直接影响组芯后的尺寸精度,从而导致与下芯机不匹配。
这一方面要求芯盒的制造精度必须符合图纸设计要求,另一方面也要求芯砂有良好的流动性,制出的砂芯表面致密、强度高,从而缩小并稳定涂料层的厚度,进而保证组合后的砂芯尺寸精度。
覆膜砂芯子烘烤工艺流程
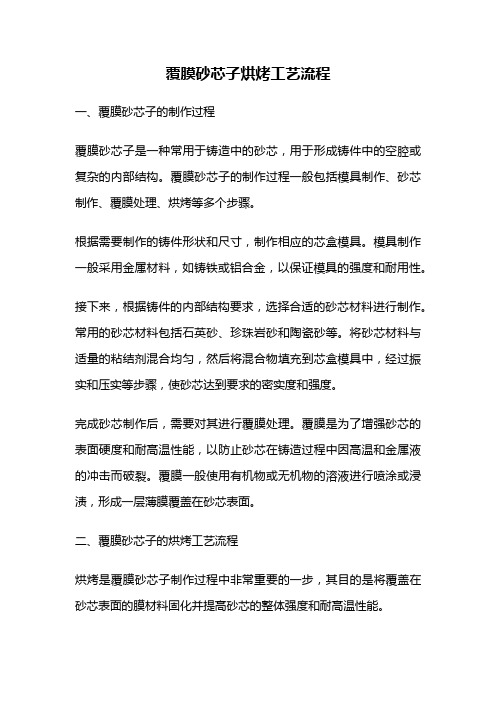
覆膜砂芯子烘烤工艺流程一、覆膜砂芯子的制作过程覆膜砂芯子是一种常用于铸造中的砂芯,用于形成铸件中的空腔或复杂的内部结构。
覆膜砂芯子的制作过程一般包括模具制作、砂芯制作、覆膜处理、烘烤等多个步骤。
根据需要制作的铸件形状和尺寸,制作相应的芯盒模具。
模具制作一般采用金属材料,如铸铁或铝合金,以保证模具的强度和耐用性。
接下来,根据铸件的内部结构要求,选择合适的砂芯材料进行制作。
常用的砂芯材料包括石英砂、珍珠岩砂和陶瓷砂等。
将砂芯材料与适量的粘结剂混合均匀,然后将混合物填充到芯盒模具中,经过振实和压实等步骤,使砂芯达到要求的密实度和强度。
完成砂芯制作后,需要对其进行覆膜处理。
覆膜是为了增强砂芯的表面硬度和耐高温性能,以防止砂芯在铸造过程中因高温和金属液的冲击而破裂。
覆膜一般使用有机物或无机物的溶液进行喷涂或浸渍,形成一层薄膜覆盖在砂芯表面。
二、覆膜砂芯子的烘烤工艺流程烘烤是覆膜砂芯子制作过程中非常重要的一步,其目的是将覆盖在砂芯表面的膜材料固化并提高砂芯的整体强度和耐高温性能。
1. 温度升降过程烘烤过程一般分为升温和降温两个阶段。
在升温阶段,砂芯放入烘炉中,温度逐渐升高至所需的烘烤温度。
升温速度应适中,以避免砂芯因温度过快变化而产生开裂或爆炸等问题。
在升温过程中,砂芯表面的膜材料会逐渐固化。
2. 稳温保温过程当烘炉温度达到所需的烘烤温度后,进入稳温保温过程。
此时,烘炉内部的温度要保持在一定范围内,以保证砂芯的整体性能得到充分发挥。
保温时间一般根据砂芯的尺寸和要求的强度来确定,通常为几小时至几十小时。
3. 降温过程烘烤结束后,需要将烘炉温度逐渐降低至室温。
降温过程一般比升温过程更为缓慢,以避免砂芯因温度变化过快而产生开裂或变形等问题。
降温完成后,砂芯即可取出进行后续的操作和使用。
总结:覆膜砂芯子的烘烤工艺流程是砂芯制作过程中的关键环节,通过适当的温度升降和稳温保温控制,可以使覆盖在砂芯表面的膜材料固化并提高砂芯的整体强度和耐高温性能。
简述制芯工艺
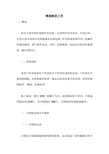
简述制芯工艺一、概述砂芯主要用来形成铸件的内腔、孔洞和凹坑等部分,在浇注时,它的大部分或部分表面被液态金属包围,经受铁液的热作用、机械作用都较强烈,排气条件也差,出砂、清理困难,因此对芯砂的性能要求一般比型砂高。
二、植物油砂采用干性油和靠近干性油的半干性油作油砂粘结剂。
干性油含不饱和脂肪酸,其加热硬化机理一般认为是氧化聚合的结果。
常用的植物油有,桐油、亚麻油等。
烘干温度一般以200~220℃为宜。
如需缩短烘干时间,可将温度提高到250℃,但不能超过300℃,否则粘结性能将被破坏。
三、合脂粘结剂及合脂砂(一)合脂粘结剂合脂是合成脂肪酸蒸馏残渣的简称,是从炼油厂原料脱蜡过程中得到的石蜡,制皂工业再将石蜡制取合成脂肪酸时所得的副产品。
合脂砂的烘干湿度范围比油砂宽些,但是最适宜范围仍是200~220℃之间。
合脂粘结剂的加入量一般为砂质量的2.5~4.5%,过多,强度增加不显著,而发气量明显增大,粘膜加重,蠕变加大,出砂性变差。
存在的问题:1.湿强度低合脂砂的湿压强度只有2.0~2.5kPa。
比植物油砂还要低。
加入膨润土或者含泥量高的天然粘土砂可以提高湿强度。
2.砂芯蠕变合脂砂湿强度低,合脂本身在常温下粘度大,芯砂流动性差,造芯时不易紧实;因此合脂砂芯在湿态和烘干过程中易发生蠕变,即逐渐往下沉。
在冬天,合脂变得更加粘稠,蠕变现象就更为严重。
可采用加入膨润土和高温入炉烘干硬化的方法来减少蠕变的缺陷。
四、壳芯(型)(一)壳芯(型)的制造1940年,Johannes Croning发明用热法制造壳型,称为“C”法或“壳法”,此法不仅可用于造型,更主要的是用于制造壳芯。
该法用酚醛树脂作粘结剂,配制的型(芯)砂叫做覆膜砂像干砂一样松散。
其制壳的方法有两种:翻斗法和吹砂法。
壳法造型、造芯的优点是混制好的覆膜砂可以较长期贮存(三个月以上);无需捣砂,能获得尺寸精确的型、芯;型、芯强度高,质量轻,易搬运;透气性好,可用细的原砂得到光洁的铸件表面;无需砂箱;覆膜砂消耗量小;型、芯可以长期贮放。
铸造模具热芯盒覆膜砂模具的铸造技术解答
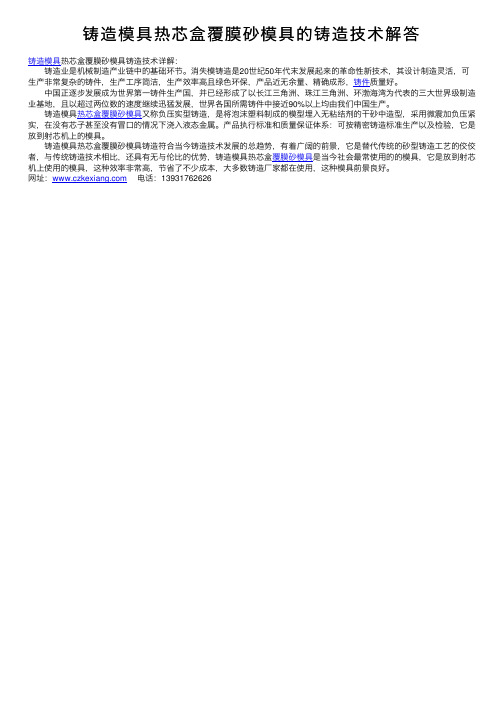
铸造模具热芯盒覆膜砂模具的铸造技术解答
铸造模具热芯盒覆膜砂模具铸造技术详解:
铸造业是机械制造产业链中的基础环节。
消失模铸造是20世纪50年代末发展起来的⾰命性新技术,其设计制造灵活,可⽣产⾮常复杂的铸件,⽣产⼯序简洁,⽣产效率⾼且绿⾊环保,产品近⽆余量、精确成形,铸件质量好。
中国正逐步发展成为世界第⼀铸件⽣产国,并已经形成了以长江三⾓洲、珠江三⾓洲、环渤海湾为代表的三⼤世界级制造业基地,且以超过两位数的速度继续迅猛发展,世界各国所需铸件中接近90%以上均由我们中国⽣产。
铸造模具热芯盒覆膜砂模具⼜称负压实型铸造,是将泡沫塑料制成的模型埋⼊⽆粘结剂的⼲砂中造型,采⽤微震加负压紧实,在没有芯⼦甚⾄没有冒⼝的情况下浇⼊液态⾦属。
产品执⾏标准和质量保证体系:可按精密铸造标准⽣产以及检验,它是放到射芯机上的模具。
铸造模具热芯盒覆膜砂模具铸造符合当今铸造技术发展的总趋势,有着⼴阔的前景,它是替代传统的砂型铸造⼯艺的佼佼者,与传统铸造技术相⽐,还具有⽆与伦⽐的优势,铸造模具热芯盒覆膜砂模具是当今社会最常使⽤的的模具,它是放到射芯机上使⽤的模具,这种效率⾮常⾼,节省了不少成本,⼤多数铸造⼚家都在使⽤,这种模具前景良好。
⽹址:电话:139****2626。
热芯盒覆膜砂制芯技改过程综述
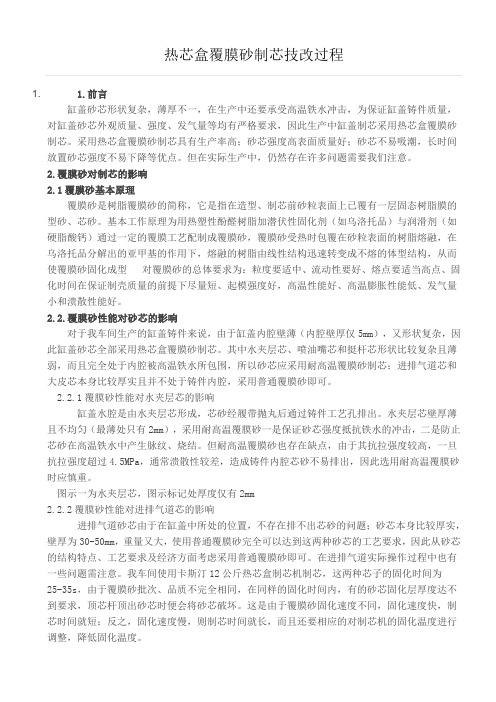
热芯盒覆膜砂制芯技改过程1. 1.前言缸盖砂芯形状复杂,薄厚不一,在生产中还要承受高温铁水冲击,为保证缸盖铸件质量,对缸盖砂芯外观质量、强度、发气量等均有严格要求,因此生产中缸盖制芯采用热芯盒覆膜砂制芯。
采用热芯盒覆膜砂制芯具有生产率高;砂芯强度高表面质量好;砂芯不易吸潮,长时间放置砂芯强度不易下降等优点。
但在实际生产中,仍然存在许多问题需要我们注意。
2.覆膜砂对制芯的影响2.1覆膜砂基本原理覆膜砂是树脂覆膜砂的简称,它是指在造型、制芯前砂粒表面上已覆有一层固态树脂膜的型砂、芯砂。
基本工作原理为用热塑性酚醛树脂加潜伏性固化剂(如乌洛托品)与润滑剂(如硬脂酸钙)通过一定的覆膜工艺配制成覆膜砂,覆膜砂受热时包覆在砂粒表面的树脂熔融,在乌洛托品分解出的亚甲基的作用下,熔融的树脂由线性结构迅速转变成不熔的体型结构,从而使覆膜砂固化成型对覆膜砂的总体要求为:粒度要适中、流动性要好、熔点要适当高点、固化时间在保证制壳质量的前提下尽量短、起模强度好,高温性能好、高温膨胀性能低、发气量小和溃散性能好。
2.2.覆膜砂性能对砂芯的影响对于我车间生产的缸盖铸件来说,由于缸盖内腔壁薄(内腔壁厚仅5mm),又形状复杂,因此缸盖砂芯全部采用热芯盒覆膜砂制芯。
其中水夹层芯、喷油嘴芯和挺杆芯形状比较复杂且薄弱,而且完全处于内腔被高温铁水所包围,所以砂芯应采用耐高温覆膜砂制芯;进排气道芯和大皮芯本身比较厚实且并不处于铸件内腔,采用普通覆膜砂即可。
2.2.1覆膜砂性能对水夹层芯的影响缸盖水腔是由水夹层芯形成,芯砂经履带抛丸后通过铸件工艺孔排出。
水夹层芯壁厚薄且不均匀(最薄处只有2mm),采用耐高温覆膜砂一是保证砂芯强度抵抗铁水的冲击,二是防止芯砂在高温铁水中产生脉纹、烧结。
但耐高温覆膜砂也存在缺点,由于其抗拉强度较高,一旦抗拉强度超过4.5MPa,通常溃散性较差,造成铸件内腔芯砂不易排出,因此选用耐高温覆膜砂时应慎重。
图示一为水夹层芯,图示标记处厚度仅有2mm2.2.2覆膜砂性能对进排气道芯的影响进排气道砂芯由于在缸盖中所处的位置,不存在排不出芯砂的问题;砂芯本身比较厚实,壁厚为30-50mm,重量又大,使用普通覆膜砂完全可以达到这两种砂芯的工艺要求,因此从砂芯的结构特点、工艺要求及经济方面考虑采用普通覆膜砂即可。
覆膜砂热芯盒芯头部分的综合改进
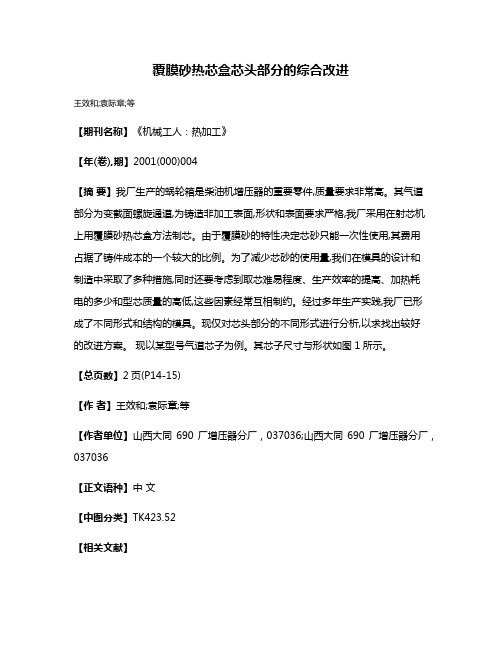
覆膜砂热芯盒芯头部分的综合改进
王效和;袁际章;等
【期刊名称】《机械工人:热加工》
【年(卷),期】2001(000)004
【摘要】我厂生产的蜗轮箱是柴油机增压器的重要零件,质量要求非常高。
其气道部分为变截面螺旋通道,为铸造非加工表面,形状和表面要求严格,我厂采用在射芯机上用覆膜砂热芯盒方法制芯。
由于覆膜砂的特性决定芯砂只能一次性使用,其费用
占据了铸件成本的一个较大的比例。
为了减少芯砂的使用量,我们在模具的设计和
制造中采取了多种措施,同时还要考虑到取芯难易程度、生产效率的提高、加热耗
电的多少和型芯质量的高低,这些因素经常互相制约。
经过多年生产实践,我厂已形
成了不同形式和结构的模具。
现仅对芯头部分的不同形式进行分析,以求找出较好
的改进方案。
现以某型号气道芯子为例。
其芯子尺寸与形状如图1所示。
【总页数】2页(P14-15)
【作者】王效和;袁际章;等
【作者单位】山西大同690厂增压器分厂,037036;山西大同690厂增压器分厂,037036
【正文语种】中文
【中图分类】TK423.52
【相关文献】
1.缸盖水腔芯的热芯盒覆膜砂制芯 [J], 陈剑敏
2.0.5kg热芯盒射芯机的再次改进设计 [J], 张笑山
3.GSR2型两工位热芯盒射芯机的改进与应用 [J], 李德林
4.用热芯盒射芯机射制酚醛树脂覆膜砂芯 [J], 车传阳;白凤阳
5.热芯盒射芯机使用覆膜砂的方法 [J], 洪热生
因版权原因,仅展示原文概要,查看原文内容请购买。
- 1、下载文档前请自行甄别文档内容的完整性,平台不提供额外的编辑、内容补充、找答案等附加服务。
- 2、"仅部分预览"的文档,不可在线预览部分如存在完整性等问题,可反馈申请退款(可完整预览的文档不适用该条件!)。
- 3、如文档侵犯您的权益,请联系客服反馈,我们会尽快为您处理(人工客服工作时间:9:00-18:30)。
热芯盒覆膜砂制芯技改过程1. 1.前言缸盖砂芯形状复杂,薄厚不一,在生产中还要承受高温铁水冲击,为保证缸盖铸件质量,对缸盖砂芯外观质量、强度、发气量等均有严格要求,因此生产中缸盖制芯采用热芯盒覆膜砂制芯。
采用热芯盒覆膜砂制芯具有生产率高;砂芯强度高表面质量好;砂芯不易吸潮,长时间放置砂芯强度不易下降等优点。
但在实际生产中,仍然存在许多问题需要我们注意。
2.覆膜砂对制芯的影响2.1覆膜砂基本原理覆膜砂是树脂覆膜砂的简称,它是指在造型、制芯前砂粒表面上已覆有一层固态树脂膜的型砂、芯砂。
基本工作原理为用热塑性酚醛树脂加潜伏性固化剂(如乌洛托品)与润滑剂(如硬脂酸钙)通过一定的覆膜工艺配制成覆膜砂,覆膜砂受热时包覆在砂粒表面的树脂熔融,在乌洛托品分解出的亚甲基的作用下,熔融的树脂由线性结构迅速转变成不熔的体型结构,从而使覆膜砂固化成型对覆膜砂的总体要求为:粒度要适中、流动性要好、熔点要适当高点、固化时间在保证制壳质量的前提下尽量短、起模强度好,高温性能好、高温膨胀性能低、发气量小和溃散性能好。
2.2.覆膜砂性能对砂芯的影响对于我车间生产的缸盖铸件来说,由于缸盖内腔壁薄(内腔壁厚仅5mm),又形状复杂,因此缸盖砂芯全部采用热芯盒覆膜砂制芯。
其中水夹层芯、喷油嘴芯和挺杆芯形状比较复杂且薄弱,而且完全处于内腔被高温铁水所包围,所以砂芯应采用耐高温覆膜砂制芯;进排气道芯和大皮芯本身比较厚实且并不处于铸件内腔,采用普通覆膜砂即可。
2.2.1覆膜砂性能对水夹层芯的影响缸盖水腔是由水夹层芯形成,芯砂经履带抛丸后通过铸件工艺孔排出。
水夹层芯壁厚薄且不均匀(最薄处只有2mm),采用耐高温覆膜砂一是保证砂芯强度抵抗铁水的冲击,二是防止芯砂在高温铁水中产生脉纹、烧结。
但耐高温覆膜砂也存在缺点,由于其抗拉强度较高,一旦抗拉强度超过4.5MPa,通常溃散性较差,造成铸件内腔芯砂不易排出,因此选用耐高温覆膜砂时应慎重。
图示一为水夹层芯,图示标记处厚度仅有2mm2.2.2覆膜砂性能对进排气道芯的影响进排气道砂芯由于在缸盖中所处的位置,不存在排不出芯砂的问题;砂芯本身比较厚实,壁厚为30-50mm,重量又大,使用普通覆膜砂完全可以达到这两种砂芯的工艺要求,因此从砂芯的结构特点、工艺要求及经济方面考虑采用普通覆膜砂即可。
在进排气道实际操作过程中也有一些问题需注意。
我车间使用卡斯汀12公斤热芯盒制芯机制芯,这两种芯子的固化时间为25-35s,由于覆膜砂批次、品质不完全相同,在同样的固化时间内,有的砂芯固化层厚度达不到要求,顶芯杆顶出砂芯时便会将砂芯破坏。
这是由于覆膜砂固化速度不同,固化速度快,制芯时间就短;反之,固化速度慢,则制芯时间就长,而且还要相应的对制芯机的固化温度进行调整,降低固化温度。
图示二标记处为砂芯固化强度不足,顶芯杆将砂芯顶伤图示三为正常砂芯1. 3.热芯盒工艺工装对砂芯的影响四缸连体缸盖水夹层芯热芯盒采用水平分型时,由于水平分型砂芯表面积大,必须有较多的射砂嘴才能将芯盒内腔射满,这样就会有比较多的射嘴棒被浪费掉了;现在改为垂直分型,射砂嘴减少,被浪费的射嘴棒就减少了,从而减少了覆膜砂的浪费。
图示四垂直分型射嘴为10个图示五水平分型射嘴为33个四缸连体缸盖和六缸连体缸盖的水夹层芯在我车间同一台热芯盒制芯机上生产,使用同样的耐高温覆膜砂,可是砂芯的质量确完全不同。
四缸连体缸盖水夹层射砂饱满,表面坚固,无缺陷;六缸连体缸盖水夹层芯在图示位置却存在起皮现象,即此部位稍微施加外力便会塌陷。
经跟踪观察及相互对比发现,六缸连体缸盖水夹层芯射砂嘴数量多,尺寸大,超出正常范围,射砂时带入大量的空气最终集中在此部位无法及时排出,导致这一现象。
现将射砂嘴尺寸减小,便可解决这一问题。
图示六标记位置为砂芯起皮位置4.结论4.1覆膜砂性能不仅仅局限于强度、粒度、发气量这些特性,一些微性能同样对砂芯质量有重大的影响,包括本文没有提到的覆膜砂发气速率对铸件气孔缺陷的影响等等。
4.2工艺工装的设计总会受生产条件、设备等一些因素的影响,要在生产中发现问题,解决问题;不断完善,不断提高。
5.结束语无论多成熟的生产工艺,在生产中总会因设备、操作者、环境、原材料等原因出现新的问题,面对这些问题,要善于发现,善于总结,用数据说话,找出问题根源,让工艺为生产服务,使我们的生产更加顺畅。
覆膜砂铸造工艺过程要点覆膜砂铸造在铸造领域已有相当长的历史,铸件的产量也相当大;但采用覆膜砂铸造生产精密铸钢件时面临很多难题:粘砂(结疤)、冷隔、气孔。
如何解决这些问题有待于我们去进一步探讨。
一、对覆膜砂的认识与了解(覆膜砂属于有机粘结剂型、芯砂)(1)覆膜砂的特点:具有适宜的强度性能;流动性好,制出的砂型、砂芯轮廓清晰,组织致密,能够制造出复杂的砂芯;砂型(芯)表面质量好,表面粗糙度可达Ra=6.3~12.5μm,尺寸精度可达CT7~CT9级;溃散性好,铸件容易清理。
(2)适用范围:覆膜砂既可制作铸型又可制作砂芯,覆膜砂的型或芯既可互相配合使用又可与其它砂型(芯)配合使用;不仅可以用于金属型重力铸造或低压铸造,也可以用于铁型覆砂铸造,还可以用于热法离心铸造;不仅可以用于铸铁、非铁合金铸件的生产,还可以用于铸钢件的生产。
二、覆膜砂的制备1.覆膜砂组成一般由耐火材料、粘结剂、固化剂、润滑剂及特殊添加剂组成。
(1)耐火材料是构成覆膜砂的主体。
对耐火材料的要求是:耐火度高、挥发物少、颗粒较圆整、坚实等。
一般选用天然擦洗硅砂。
对硅砂的要求是:SiO2含量高(铸铁及非铁合金铸件要求大于90%,铸钢件要求大于97%);含泥量不大于0.3%(为擦洗砂)--[水洗砂含泥量规定小于;粒度①分布在相邻3~5个筛号上;粒形圆整,角形因素应不大于1.3;酸耗值不小于5ml。
(2)粘结剂普遍采用酚醛树脂。
(3)固化剂通常采用乌洛托品;润滑剂一般采用硬脂酸钙,其作用是防止覆膜砂结块,增加流动性。
添加剂的主要作用是改善覆膜砂的性能。
(4)覆膜砂的基本配比成分配比(质量分数,%)说明:原砂100 擦洗砂,酚醛树脂1.0~3.0 占原砂重,乌洛托品(水溶液2)10~15 占树脂重,硬脂酸钙5~7 占树脂重,添加剂0.1~0.5 占原砂重。
1:2)10~15 占树脂重,硬脂酸钙5~7 占树脂重,添加剂0.1~0.5 占原砂重。
2.覆膜砂的生产工艺覆膜砂的制备工艺主要有冷法覆膜、温法覆膜、热法覆膜三种,目前覆膜砂的生产几乎都是采用热覆膜法。
热法覆膜工艺是先将原砂加热到一定温度,然后分别与树脂、乌洛托品水溶液和硬脂酸钙混合搅拌,经冷却破碎和筛分而成。
由于配方的差异,混制工艺有所不同。
目前国内覆膜砂生产线的种类很多,手工加料的半自动生产线约有2000~2300条,电脑控制的全自动生产线也已经有将近50条,有效提高了生产效率和产品稳定性。
例如xx铸造有限公司的自动化可视生产线,其加料时间控制精确到0.1秒,加热温度控制精确到1/10℃,并且可以通过视频时时观察混砂状态,生产效率达到6吨/小时。
3.覆膜砂的主要产品类型(1)普通类覆膜砂普通覆膜砂即传统覆膜砂,其组成通常由石英砂,热塑性酚醛树脂,乌洛托品和硬脂酸钙构成,不加有关添加剂,其树脂加入量通常在一定强度要求下相对较高,不具备耐高温,低膨胀、低发气等特性,适用于要求不高的铸件生产。
(2)高强度低发气类覆膜砂特点:高强度、低膨胀、低发气、慢发气、抗氧化简介:高强度低发气覆膜砂是普通覆膜砂的更新换代产品,通过加入有关特性的“添加剂”和采用新的配制工艺,使树脂用量大幅度下降,其强度比普通覆膜砂高30%以上,发气量显著降低,并能延缓发气速度,能更好地适应铸件生产的需要。
该类覆膜砂主要适用于铸铁件中,中小铸钢、合金铸钢件的生产。
目前该类覆膜砂有三个系列:GD-1高强度低发气覆膜砂;GD-2高强度低膨胀低发气覆膜砂;GD-3高强度低膨胀低发气抗氧化覆膜。
(3)耐高温(类)覆膜砂(ND型)特点:耐高温、高强度、低膨胀、低发气、慢发气、易溃散、抗氧化简介:耐高温覆膜砂是通过特殊工艺配方技术生产出的具有优异高温性能(高温下强度高、耐热时间长、热膨胀量小、发气量低)和综合铸造性能的新型覆膜砂。
该类覆膜砂特别适用于复杂薄壁精密的铸铁件(如汽车发动机缸体、缸盖等)以及高要求的铸钢件(如集装箱角和火车刹车缓;中器壳件等)的生产,可有效消除粘砂、变形、热裂和气孔等铸造缺陷。
目前该覆膜砂有四个系列:VND-1耐高温覆膜砂. ND-2耐高温低膨胀低发气覆膜砂ND-3耐高温低膨胀低发气抗氧化覆膜砂ND-4耐高温高强底低膨胀低发气覆膜(4)易溃散类覆膜砂具有较好的强度,同时具有优异的低温溃散性能,适用于生产有色金属铸件。
(5)其它特殊要求覆膜砂为适应不同产品的需要,开发出了系列特种覆膜砂如:离心铸造用覆膜砂、激冷覆膜砂、湿态覆膜砂、防粘砂、防脉纹、防橘皮覆膜砂等。
三、覆膜砂制芯主要工艺过程加热温度200-300℃、固化时间30-150s、射砂压力0.15-0.60MPa。
形状简单的砂芯、流动性好的覆膜砂可选用较低的射砂压力,细薄砂芯选择较低的加热温度,加热温度低时可适当延长固化时间等。
覆膜砂所使用的树脂是酚醛类树脂。
制芯工艺的优点:具有适宜的强度性能;流动性好;砂芯表面质量好(Ra=6.3-12.5μm);砂芯抗吸湿性强;溃散性好,铸件容易清理。
1、铸型(模具)温度铸型温度是影响壳层厚度及强度的主要因素之一,一般控制在220~260℃,并根据下列原则选定: (1)保证覆膜砂上的树脂软化及固化所需的足够热量;(2)保证形成需要的壳厚且壳型(芯)表面不焦化;(3)尽量缩短结壳及硬化时间,以提高生产率。
2、射砂压力及时间射砂时间一般控制在3~10s,时间过短则砂型(芯)不能成型。
射砂压力一般为0.6MPa 左右;压力过低时,易造成射不足或疏松现象。
3、硬化时间:硬化时间的长短主要取决于砂型(芯)的厚度与铸型的温度,一般在60~120s左右。
时间过短,壳层未完全固化则强度低;时间过长,砂型(芯)表面层易烧焦影响铸件质量。
覆膜砂造型(芯)工艺参数实例:序号图号壳厚(㎜)重量(㎏)铸型温度(℃)射砂时间(s)硬化时间(s)1 (导向套)DN80-05 8~10 2.5~2.6220~240 2~3 60~80 2 (阀体)DN05-01 10~123.75~3.8 240~260 3~5 80~100四、覆膜砂应用中存在的问题及解决对策制芯的方法种类很多,总的可以划分为热固性方法和冷固性方法两大类,覆膜砂制芯属于热固性方法类。
任何一种制芯方法都有其自身的优点和缺点,这主要取决于产品的质量要求、复杂程度、生产批量、生产成本、产品价格等综合因素来决定采用何种制芯方法。