模具设计要求
模具设计规范及要点

模具设计规范及要点模具设计是制造业中非常重要的环节,它直接影响到产品的质量和生产效率。
为了确保模具设计的准确性和合理性,制定一系列的规范是非常必要的。
本文将介绍模具设计的规范及其要点。
一、模具设计规范的目的模具设计规范的目的是确保模具具备高质量和高效率的生产能力,并最大限度地减少模具使用过程中的故障和损耗。
通过遵守规范,可以提高模具的使用寿命,减少维修和更换成本,提高生产效率,降低生产成本,提升产品的质量。
二、模具设计规范的要点1.模具设计应符合产品的要求:模具设计必须根据产品的尺寸、形状、材料和数量要求来进行,确保模具可以完美地制造出符合产品要求的零件。
2.模具设计应考虑材料的选择和加工工艺:模具所选材料应具有足够的强度和硬度,以承受生产过程中的高负荷和磨损。
同时,模具的加工工艺应考虑到成本、时间和质量的平衡,确保成型过程的高效和精确。
3.模具设计应遵循安全和可靠性的原则:模具的设计应确保操作过程中的安全性,尽量减少操作人员的伤害和事故发生。
同时,模具的设计要保证其可靠性,能够稳定地工作,并且容易进行维护和修复。
4.模具设计应考虑到工装和夹具的需要:在模具设计过程中,应充分考虑到工装和夹具的配套需求,确保模具能够与其完美配合,提高生产效率和产品质量。
5.模具设计应简化结构:模具的设计应尽量简洁,避免复杂的结构,以减少制造成本和使用成本。
同时,简化结构也有利于操作和维护。
6.模具设计应具备可拆卸性:模具的设计应尽量满足零部件的可拆卸性,使得维护和更换变得容易。
这样可以减少停机时间,提高生产效率。
7.模具设计应合理确定尺寸公差:模具的设计应根据产品的尺寸要求合理确定公差,以确保模具制造出来的零件尺寸准确且符合要求。
8.模具设计应注意冷却系统的布置:模具的冷却系统设计应合理布置,以确保零件的快速冷却和缩短生产周期。
冷却系统的设计也要考虑到冷却介质的供应和排放。
9.模具设计应充分考虑排气和出渣:模具的设计应考虑到充分的排气和出渣,以防止铸件中产生气孔和杂质。
模具行位设计标准要求规范

模具行位设计标准要求规范模具行位设计标准要求规范主要包括以下几个方面:一、尺寸要求:模具行位的尺寸应符合国家标准或相关行业标准的要求。
包括行位的长度、宽度、高度、孔径等尺寸参数。
行位的尺寸应与相邻模具零件的尺寸保持一致,确保模具在装配的过程中能够正常配合、连接。
二、垂直度要求:模具行位的垂直度是指行位与模具的垂直度,也是指行位上下两个面的平行度。
行位的垂直度要求符合国家标准或相关行业标准的要求。
垂直度的要求主要是为了保证模具的精度和稳定性,使其在使用过程中不产生变形、偏斜等问题。
三、表面质量要求:行位的表面质量要求符合国家标准或相关行业标准的要求。
行位的表面应光滑、平整,不得有明显的裂纹、气孔、划痕等缺陷。
表面质量的要求主要是为了保证模具的精度和使用寿命,使其能够正常运行。
四、材料要求:模具行位的材料要求应符合国家标准或相关行业标准的要求。
行位的材料应具有一定的强度和耐磨性,能够承受模具在使用过程中的压力、冲击等力量。
材料的选择要根据具体的模具使用环境和工作条件来确定,确保模具的使用效果和寿命。
五、加工精度要求:模具行位的加工精度要求应符合国家标准或相关行业标准的要求。
行位的加工精度主要包括尺寸精度、形位公差、表面粗糙度等指标。
加工精度的要求主要是为了保证模具的精度和稳定性,使其能够满足产品的要求。
六、安装要求:模具行位的安装要求应符合国家标准或相关行业标准的要求。
行位的安装应牢固可靠,保证模具在使用过程中不会因为行位的松动而产生误差。
安装的过程中要注意行位与相邻模具零件的配合和对齐,确保模具的装配精度和稳定性。
以上是模具行位设计标准要求规范的一些主要内容,具体的标准要求还需要根据具体的模具类型、使用环境和产品要求来确定。
模具行位的设计标准要求规范能够保证模具的质量和性能,提高模具的使用效果和寿命。
同时,对于模具生产厂家和用户来说,严格按照标准进行设计和生产,有助于提高产品的竞争力和市场占有率。
汽车模具设计标准与要求
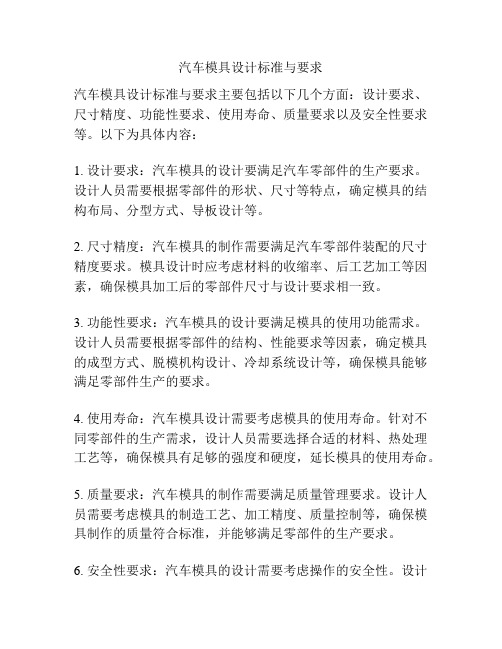
汽车模具设计标准与要求
汽车模具设计标准与要求主要包括以下几个方面:设计要求、尺寸精度、功能性要求、使用寿命、质量要求以及安全性要求等。
以下为具体内容:
1. 设计要求:汽车模具的设计要满足汽车零部件的生产要求。
设计人员需要根据零部件的形状、尺寸等特点,确定模具的结构布局、分型方式、导板设计等。
2. 尺寸精度:汽车模具的制作需要满足汽车零部件装配的尺寸精度要求。
模具设计时应考虑材料的收缩率、后工艺加工等因素,确保模具加工后的零部件尺寸与设计要求相一致。
3. 功能性要求:汽车模具的设计要满足模具的使用功能需求。
设计人员需要根据零部件的结构、性能要求等因素,确定模具的成型方式、脱模机构设计、冷却系统设计等,确保模具能够满足零部件生产的要求。
4. 使用寿命:汽车模具设计需要考虑模具的使用寿命。
针对不同零部件的生产需求,设计人员需要选择合适的材料、热处理工艺等,确保模具有足够的强度和硬度,延长模具的使用寿命。
5. 质量要求:汽车模具的制作需要满足质量管理要求。
设计人员需要考虑模具的制造工艺、加工精度、质量控制等,确保模具制作的质量符合标准,并能够满足零部件的生产要求。
6. 安全性要求:汽车模具的设计需要考虑操作的安全性。
设计
人员需要合理设置模具的安全装置、警示标识等,确保操作人员的人身安全。
总之,汽车模具设计标准与要求是为了保证模具能够满足汽车生产的需求,并达到高质量、高效率的生产目标。
模具设计人员应严格按照标准要求进行设计,确保模具的质量和安全性。
模具的设计与制作要求

模具的设计与制作要求1.准确的产品尺寸和形状:模具的设计要根据产品的准确尺寸和形状进行,这是保证产品质量和一致性的基础。
同时,也要考虑到产品的形状复杂性,进行合理布局和结构设计。
2.合理的材料选择:模具的工作环境要考虑到温度、压力、磨损等因素,所以在材料的选择上需要具有良好的耐磨性、耐腐蚀性和热稳定性。
一般常用的模具材料有铸钢、工具钢、硬质合金等。
3.可靠的结构设计:模具的结构设计要考虑到产品的工艺要求和承受的力,以确保模具在工作过程中不变形、不破裂,并有足够的刚度和强度。
另外,还要考虑到模具的分解性、装配性和可维修性,方便模具的更换和维护。
4.高效的冷却系统设计:模具的制作过程中会产生大量的热量,如果不能有效地散热,会导致模具温度过高,进而影响产品质量和模具寿命。
因此,模具的设计中要充分考虑冷却系统的设置,合理布置冷却通道和出水口,以提高散热效果。
5.精密的加工工艺:模具的制作一般采用数控机床进行精密加工,要求加工精度高,尺寸精确,表面光洁度好。
加工工艺包括铣削、钻孔、褶皱、车削、车削、划线等,要保证模具的加工质量和尺寸精度。
6.严格的质量控制:模具的设计与制作过程中,要进行严格的质量控制,包括原材料的采购、模具制作过程中的检测和验收,以及最终的模具出厂检验。
尤其对于关键部件和加工工艺要进行特别的把关。
7.合理的模具使用和维护:模具的使用和维护也非常重要,要按照操作规范进行使用,定期保养和维修,并且要妥善保管模具,以延长模具的使用寿命。
总之,模具的设计与制作是一个相对复杂和繁琐的工作,需要综合考虑产品的需求、材料的特性、工艺的要求以及工装设备的配合等多个因素,以实现高效、精确、持久的生产制造目的。
模具设计之基本要求

模具设计之基本要求顶针类:1.顶针大小要跟成品尺寸成合理比例:不能大成品小顶针¸小成品大顶针.2. 顶针位置落点应在骨位边、呵位边,尽量避免在大平面处落顶针,因成品受力点不在大平面,如硬在平面落针容易顶白。
3. 如太高骨位例超出高度12mm,应考虑在骨底加扁顶针。
4. 水口钩针大小要视啤机顿数或产品大小定尺寸,例成品小于60mm,钩针只须Ø4mm¸小于200 mm,钩针只须6 mm大于200 mm以上方可8 mm钩针。
5. 顶针排放要有规律不能东一支西一支因顶针排放没有规律会影响放运水位置,便不能有效地冷却成品。
6. 顶针的要求格式先要了解客户要公制或英制。
7. 顶潜水之顶针不能太接近潜水位,最佳顶针与潜水的距离15 mm至20 mm,避免潜水口容易折断在水位内。
8. 斜顶的斜度一定要超过10度最多20度。
(如有低过或过标准就要先问"主任"可行否)9. 无特别要求,一般选用大同标准。
如要求用HASCO的顶针,则选用Z40。
(特别模具用Z41)水口类:1.水口粗幼要按成品大小决定,例成品在50 mm以下水口只须做Ø4 mm以下,50 mm至100 mm水口约做Ø5 mm,100 mm至150 mm成品水口做Ø6 mm,如有难走水口工程塑料水口就相应加大约20%。
2.唧咀位的支头尽量缩短,因太长会影响走水速度,影响啤作。
3.钩针藏冷胶位要有10至15 mm高度视成品大小决定。
4.水口对转角前一定要多约6 mm至8 mm冷胶位,避免冷胶堵塞走水或入水,影响啤塑。
运水类:1.一般运水Ø8 mm,如特大产品才Ø10 mm至Ø12 mm,又或因各种因素影响才可改细运水,但先要通知主任2.内模的运水与运水之间的中心距离如无特别影响,中心距应在60 mm至80 mm,因太阔及太知短都会影响模具冷却、影响生产。
模具设计的几个要求

模具设计的几个要求第一篇:模具设计的几个要求青岛海培德模具加工厂模具设计的几个要求1.冲压工艺性分析冲压工艺性是指零件冲压加工的难易程度。
在技术方面,主要分析该零件的形状特点、尺寸大小(最小孔边距、孔径、材料厚度、最大外形)、精度要求和材料性能等因素是否符合冲压工艺的要求。
如果发现冲压工艺性差,则需要对冲压件产品提出修改意见,经产品设计者同意后方可修改。
.搜集必要的资料设计冷冲模时,需搜集的资料包括产品图、样品、设计任务书和参考图等,并相应了解如下问题:)了解最大限度采用标准件的可能性,以缩短模具制造周期。
)了解制件的生产性质是试制还是批量或大量生产,以确定模具的结构性质。
)了解适用的压力机情况和有关技术规格,根据所选用的设备确定与之相适应的模具及有关参数,如模架大小、模柄尺寸、模具闭合高度和送料机构等。
)了解提供的产品视图是否完备,技术要求是否明确,有无特殊要求的地方。
5)了解模具制造的技术力量、设备条件和加工技巧,为确定模具结构提供依据。
)了解制件的材料性质(软、硬还是半硬)、尺寸和供应方式(如条料、卷料还是废料利用等),以便确定冲裁的合理间隙及冲压的送料方法。
.确定合理的冲压工艺方案确定方法如下:)最后从产品质量、生产效率、设备占用情况、模具制造的难易程度、模具寿命、工艺成本、操作方便和安全程度等方面进行综合分析、比较,在满足冲件质量要求的前提下,确定适合具体生产条件的最经济合理的冲压工艺方案,并填写冲压工艺过程卡片(内容包括工序名称、工序数目、工序草图(半成品形状和尺寸)、所用模具、所选设备、工序检验要求、板料规格和性能、毛坯形状和尺寸等):;)根据工艺计算,确定工序数目,如拉深次数等。
)根据各工序的变形特点、尺寸要求确定工序排列的顺序,例如,是先冲孔后弯曲还是先4)根据生产批量和条件,确定工序的组合,如复合冲压工序、连续冲压工序等。
)根据工件的形状、尺寸精度、表面质量要求进行工艺分析,确定基本工序的性质,即落料、冲孔、弯曲等基本工序。
模具设计总体要求
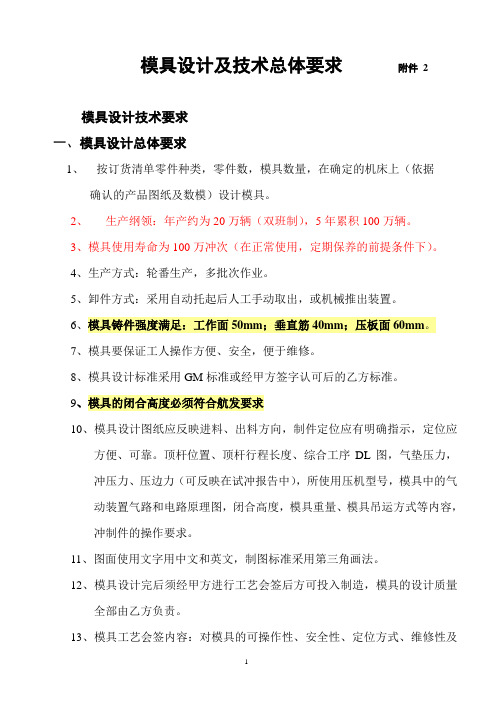
模具设计及技术总体要求附件 2模具设计技术要求一、模具设计总体要求1、按订货清单零件种类,零件数,模具数量,在确定的机床上(依据确认的产品图纸及数模)设计模具。
2、生产纲领:年产约为20万辆(双班制),5年累积100万辆。
3、模具使用寿命为100万冲次(在正常使用,定期保养的前提条件下)。
4、生产方式:轮番生产,多批次作业。
5、卸件方式:采用自动托起后人工手动取出,或机械推出装置。
6、模具铸件强度满足:工作面50mm;垂直筋40mm;压板面60mm。
7、模具要保证工人操作方便、安全,便于维修。
8、模具设计标准采用GM标准或经甲方签字认可后的乙方标准。
9、模具的闭合高度必须符合航发要求10、模具设计图纸应反映进料、出料方向,制件定位应有明确指示,定位应方便、可靠。
顶杆位置、顶杆行程长度、综合工序DL图,气垫压力,冲压力、压边力(可反映在试冲报告中),所使用压机型号,模具中的气动装置气路和电路原理图,闭合高度,模具重量、模具吊运方式等内容,冲制件的操作要求。
11、图面使用文字用中文和英文,制图标准采用第三角画法。
12、模具设计完后须经甲方进行工艺会签后方可投入制造,模具的设计质量全部由乙方负责。
13、模具工艺会签内容:对模具的可操作性、安全性、定位方式、维修性及模具对甲方压机规格的适应性等进行检查。
14、订货模具的图纸设计必须采用公制ISO标准。
15、模具的总体结构应便于直接安装、拆卸、使用,并有足够刚性。
16、修边、冲孔、翻边、整形等模具的侧面,上平面开观察检验窗口。
修边刃口与制件夹角小于75°时要充分考虑避免毛刺产生的措施。
17、冲孔凹模尽量采用镶件结构,并符合快卸式易更换原则。
18、导向润滑采用自润滑结构。
19、交付验收时的模具必须与模具设计图、冲压工序工程图保持一致,要求实物和图纸相符。
20、乙方所选用的试冲压机,必须是机械压力机,其压力机的性能及吨位应考虑与甲方选用的压力机相对应(拉深模必须在机械压力机上试压)。
薄壁模具设计标准规范
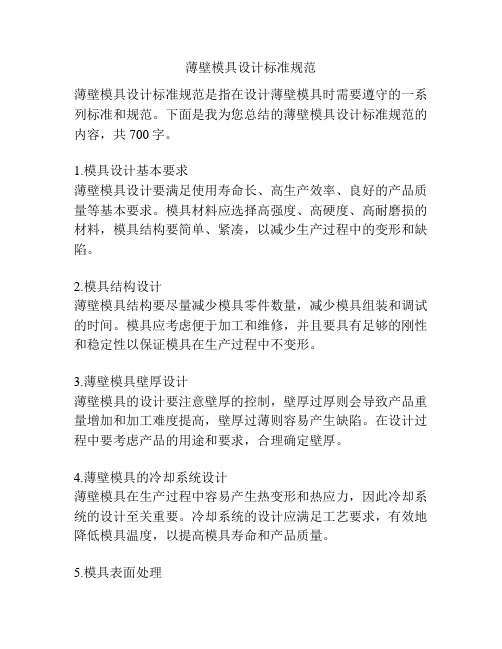
薄壁模具设计标准规范薄壁模具设计标准规范是指在设计薄壁模具时需要遵守的一系列标准和规范。
下面是我为您总结的薄壁模具设计标准规范的内容,共700字。
1.模具设计基本要求薄壁模具设计要满足使用寿命长、高生产效率、良好的产品质量等基本要求。
模具材料应选择高强度、高硬度、高耐磨损的材料,模具结构要简单、紧凑,以减少生产过程中的变形和缺陷。
2.模具结构设计薄壁模具结构要尽量减少模具零件数量,减少模具组装和调试的时间。
模具应考虑便于加工和维修,并且要具有足够的刚性和稳定性以保证模具在生产过程中不变形。
3.薄壁模具壁厚设计薄壁模具的设计要注意壁厚的控制,壁厚过厚则会导致产品重量增加和加工难度提高,壁厚过薄则容易产生缺陷。
在设计过程中要考虑产品的用途和要求,合理确定壁厚。
4.薄壁模具的冷却系统设计薄壁模具在生产过程中容易产生热变形和热应力,因此冷却系统的设计至关重要。
冷却系统的设计应满足工艺要求,有效地降低模具温度,以提高模具寿命和产品质量。
5.模具表面处理为了减少产品的摩擦阻力和磨损,模具表面需要进行适当的处理。
常用的表面处理方法有热处理、电火花抛光、镜面抛光等,根据实际需要选择合适的方法进行处理。
6.薄壁模具的自动化设计薄壁模具的自动化设计可以提高生产效率,降低成本。
可以考虑引入自动送料装置、自动脱模装置、自动清理装置等,提高生产线的自动化程度。
7.薄壁模具的检测与质量控制薄壁模具制造完成后,需要进行一系列的检测与质量控制,以保证模具的质量。
常用的方法有三坐标测量、硬度测量、裂纹检测等,合格的模具才能进入生产环节。
总结起来,薄壁模具设计标准规范是在设计薄壁模具时需要遵循的一系列准则和规范。
它涵盖了模具基本要求、结构设计、壁厚设计、冷却系统设计、模具表面处理、自动化设计和质量控制等方面的内容,旨在保证薄壁模具的质量和性能,提高生产效率,减少生产成本,满足市场需求。
模具设计技术要求
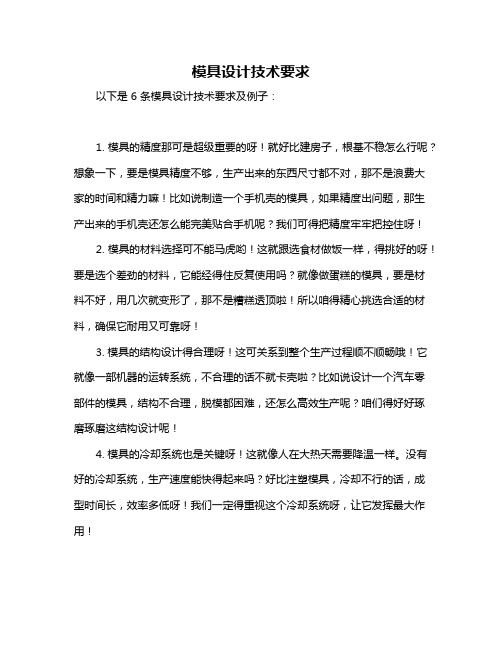
模具设计技术要求
以下是 6 条模具设计技术要求及例子:
1. 模具的精度那可是超级重要的呀!就好比建房子,根基不稳怎么行呢?想象一下,要是模具精度不够,生产出来的东西尺寸都不对,那不是浪费大家的时间和精力嘛!比如说制造一个手机壳的模具,如果精度出问题,那生产出来的手机壳还怎么能完美贴合手机呢?我们可得把精度牢牢把控住呀!
2. 模具的材料选择可不能马虎哟!这就跟选食材做饭一样,得挑好的呀!要是选个差劲的材料,它能经得住反复使用吗?就像做蛋糕的模具,要是材料不好,用几次就变形了,那不是糟糕透顶啦!所以咱得精心挑选合适的材料,确保它耐用又可靠呀!
3. 模具的结构设计得合理呀!这可关系到整个生产过程顺不顺畅哦!它就像一部机器的运转系统,不合理的话不就卡壳啦?比如说设计一个汽车零部件的模具,结构不合理,脱模都困难,还怎么高效生产呢?咱们得好好琢磨琢磨这结构设计呢!
4. 模具的冷却系统也是关键呀!这就像人在大热天需要降温一样。
没有好的冷却系统,生产速度能快得起来吗?好比注塑模具,冷却不行的话,成型时间长,效率多低呀!我们一定得重视这个冷却系统呀,让它发挥最大作用!
5. 模具的维护保养可不能忘啊!这就像爱护自己的宝贝一样。
不保养它,它能一直好用吗?你想啊,一个长期不保养的模具,各种问题都会冒出来,那不是给自己找麻烦嘛!所以呀,要定期给模具做个检查、保养护理啥的,让它一直健健康康的呀!
6. 模具的设计创新多重要呀!这就像给自己的生活加点新花样一样。
一直守着老一套,能有进步吗?看看人家那些厉害的模具设计,多么有创意呀!咱也不能落后呀,要大胆去尝试新的设计思路,说不定就能做出让人惊艳的模具呢!
总之,模具设计技术要求可多了去了,每一条都得认真对待,这样才能做出好的模具,生产出高质量的产品呀!。
冲压模具设计的安全要求

冲压模具设计的安全要求1.环境安全要求:冲压模具设计需要在安全、整洁、通风良好的环境中进行。
工作区域应清晰、明亮,避免过于拥挤。
2.机械设备安全要求:冲压模具设计需要使用符合安全标准的机械设备。
设备应定期维护和保养,确保其正常运行,并配备相应的安全保护装置。
3.材料安全要求:冲压模具设计需要使用质量稳定、符合相关标准的材料。
材料的强度、韧性、耐磨性等性能要满足设计的要求,以确保模具的安全性和稳定性。
4.操作安全要求:冲压模具设计需要经过专业的培训和资格认证后方可操作。
操作人员需要穿戴个人防护装备,如安全帽、护目镜、防护手套等。
操作时需严格遵循操作规程,禁止在不安全的状态下工作,及时发现并及时解决安全隐患。
5.模具设计安全要求:冲压模具设计应遵循设计规范和标准,保证模具结构安全可靠,使用寿命长。
模具设计时需要考虑模具的强度、刚度、稳定性等因素,避免出现断裂、疲劳等失效现象,防止意外事故的发生。
6.模具维护安全要求:冲压模具设计后需要定期进行维护和保养,及时排除模具上的损坏、松动和变形等现象,以确保模具的正常使用。
维修和保养时需要遵守相关程序,确保人员和设备的安全。
7.废料处理安全要求:冲压模具设计会产生废料和废气,在废料和废气处理过程中要符合环保要求,避免对环境造成污染。
8.紧急救援安全要求:冲压模具设计应设立相应的紧急救援机制,如设置紧急停工按钮、紧急疏散通道、消防器材等,以应对突发事件并及时采取果断行动。
总结起来,冲压模具设计的安全要求包括环境安全、机械设备安全、材料安全、操作安全、模具设计安全、模具维护安全、废料处理安全以及紧急救援安全等多个方面。
只有在满足这些要求的前提下,冲压模具设计才能确保工作人员的安全,保障生产的顺利进行。
模具设计制作规范
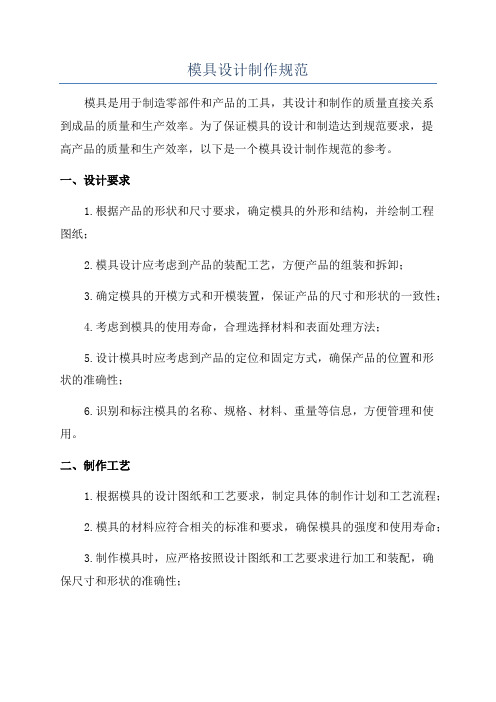
模具设计制作规范模具是用于制造零部件和产品的工具,其设计和制作的质量直接关系到成品的质量和生产效率。
为了保证模具的设计和制造达到规范要求,提高产品的质量和生产效率,以下是一个模具设计制作规范的参考。
一、设计要求1.根据产品的形状和尺寸要求,确定模具的外形和结构,并绘制工程图纸;2.模具设计应考虑到产品的装配工艺,方便产品的组装和拆卸;3.确定模具的开模方式和开模装置,保证产品的尺寸和形状的一致性;4.考虑到模具的使用寿命,合理选择材料和表面处理方法;5.设计模具时应考虑到产品的定位和固定方式,确保产品的位置和形状的准确性;6.识别和标注模具的名称、规格、材料、重量等信息,方便管理和使用。
二、制作工艺1.根据模具的设计图纸和工艺要求,制定具体的制作计划和工艺流程;2.模具的材料应符合相关的标准和要求,确保模具的强度和使用寿命;3.制作模具时,应严格按照设计图纸和工艺要求进行加工和装配,确保尺寸和形状的准确性;4.在模具加工和装配过程中,应进行必要的测量和校验,确保模具的质量和尺寸的准确性;5.模具的表面处理应根据需要选择合适的方法,如镀铬、表面喷涂等,提高模具的耐磨性和耐腐蚀性;6.制作完成后,对模具进行全面的检查和试模,确保模具的使用功能和使用寿命。
三、质量控制1.模具的质量控制应按照相关的标准和要求进行,确保模具的精度和强度;2.在模具制作的每个环节,都应有专人进行工艺指导和质量检查,及时发现和解决问题;3.对模具的加工和装配过程中发现的问题以及不合格品,应及时返修或重新制作;4.对模具的质量控制应建立完善的档案和记录,方便追溯和改进;5.在使用模具前,应进行必要的试模和样品检验,确保模具的质量和性能符合要求;6.对模具的维护保养和修理应按照规定进行,延长模具的使用寿命。
四、安全保障1.模具制作过程中,应严格遵守相关的安全操作规程,保障工作人员的安全;2.在模具制作现场,应配备必要的安全设施和个人防护用品,防止事故的发生;3.模具制作过程中,需保持工作区域的整洁和通风,防止火灾和有害气体的产生;4.模具制作现场应定期进行安全检查和隐患排查,及时消除安全隐患;5.定期对模具制作人员进行安全教育和培训,提高安全意识和处理突发事故的能力。
推板模具设计标准最新

推板模具设计标准最新为了推动模具设计领域的发展和促进模具产品质量的提升,各国在制定模具设计标准方面进行了不断的研究和改进。
下面是目前模具设计标准的最新综合版本的主要内容,以供参考。
一、模具设计基本原则1. 简化结构:尽可能减少模具的零件数和工序,简化模具结构,提高生产效率和降低生产成本。
2. 保证质量:要求模具设计符合产品的质量要求和生产工艺要求,确保模具产品的质量可靠。
3. 提高效率:优化模具设计,提高生产效率,降低生产成本,提高生产效益。
4. 安全可靠:模具设计要考虑到操作人员和生产设备的安全性,确保模具操作和生产过程的安全可靠。
二、模具设计基本要求1. 尺寸精度:模具设计要求模具尺寸精度满足产品的设计要求,并能够保证模具产品的精度稳定。
2. 运动精度:模具设计要求模具零件之间的运动精度满足产品装配要求和使用要求。
3. 寿命要求:模具设计要求模具使用寿命达到预定的要求,并能够保持较长时间的使用性能。
4. 维修和保养:模具设计要求模具具有方便维修和保养的设计,以确保模具的正常运行。
三、模具设计基本规范1. 材料选择:模具设计要求根据产品的要求和模具使用环境选择合适的材料,并进行材料的热处理和表面处理。
2. 结构设计:模具设计要求结构设计合理,满足产品的功能和使用要求,并能够方便模具的加工和装配。
3. 标准件选用:模具设计要求选用符合国际标准的标准件,以确保模具的通用性和互换性。
4. 工艺选择:模具设计要求选择合理的加工工艺和装调工艺,以提高模具的生产效率和生产质量。
四、模具设计确认和验收1. 客户确认:模具设计完成后,要求客户对模具设计进行确认,确保符合客户的需求和要求。
2. 检验验收:模具设计完成后,要求进行模具的检验验收,确保模具符合设计要求和标准规范。
总结:推板模具设计标准的最新版本主要包括模具设计基本原则、基本要求、基本规范以及设计确认和验收等内容,旨在提高模具设计的质量和效率,推动模具设计领域的发展。
模具设计标准

Subject :一、(一).排位1.根据产品大小、结构等因素确定模穴,如1X1、1X2、1X3、1X4、1X8、1X16 等。
2.当几个产品出在同一套模具中时,考虑进胶的均匀性。
应将大的产品排在中间位置,小的产品置于两边。
3.当几个分型面不规则的产品在同一模具中时,排位必须充分考虑其分型面连接的顺畅。
4.一模多穴模具中,当有镶拼、行位等结构时,不得使其发生干涉。
5.排位时应综合模具每一方面,对流道,是否镶拼、行位、顶出、运水等结构要有一个全局性思考。
6.排位时以产品零线为定位基准。
当一模出一件时,可以考虑以产品对称方向外形分中。
(二)、模具系统设计【模具系统设计程序】浇注系统内模结构行位系统顶出系统冷却系统导向定位系统排气系统模胚结构件。
说明﹕在具体的模具设计过程中﹐不一定会严格遵守此程序﹐通常我们要返回上一步甚至上几步﹐修改部分数值﹐直至最后确认。
1﹑浇注系统浇注系统由主流道﹑分流道﹑冷料井和浇口等部分组成。
在设计浇注系统时,要考虑: 制品最主要的要求是什么?外观还是强度或是尺寸精度,找出最主要的矛盾,设计时,立足主要矛盾,同时,在不与主要矛盾发生冲突的前提下,改善其它次要矛盾,要做到进浇的均匀与顺畅。
1.1.主流道主流道一般为圆锥形,角度2~4o1.2.分流道1.2.1 .分流道的形状有圆形﹑梯形等几种,从减少压力和热量损失的角度来看, 圆形流道是最优越的流道形状。
当分型面是平面或者曲面时,一般采用圆形流道;细水口模,选用梯形流道,当流道只开在前模或者后模时,则选用梯形流道。
1.2.2.布置一模多腔的流道时,应充分考虑进浇的均匀性,尽可能做到平衡进浇。
1.2.3.设计分流道大小时,应充分考虑制品大小,、壁厚、材料流动性等因素,流动性不好的材料如PC料其流道应相应加大,并且分流道的截面尺寸一定要大于制品壁厚,同时应选适合成形品形状的流道长度。
流道长则温度降低明显,流道过短则剩余应力大,容易产生“喷池”,顶出也较困难。
模具上下模座设计标准要求

模具上下模座设计标准要求
模具上下模座设计是模具设计中的重要一环,对于模具的性能和使用寿命有着很大的影响。
下面是模具上下模座设计的一些标准要求:
1. 尺寸精度要求:模具上下模座的尺寸精度要达到工艺要求的精度,一般要求在0.1mm以内。
精度要求高,可以采用数控机床进行加工,确保模具上下模座的尺寸精确。
2. 材料选择:模具上下模座的材料要选择高强度、高硬度、高耐磨性的材料,如合金工具钢、合金硬质合金等,以提高模具的使用寿命和耐磨性。
3. 设计结构合理:模具上下模座的设计结构要合理,要确保模具在使用过程中不易变形和失配,能够稳定地固定上下模具。
4. 油腔、排气孔设计:模具上下模座中需设置油腔和排气孔,以保证模具的润滑和顺畅排气,并防止模具在使用过程中产生过热和粘连的现象。
5. 安装便捷:模具上下模座的安装要方便、快捷,可采用螺纹连接或快速换模结构,以提高模具的换模效率。
6. 导向结构设计:模具上下模座的导向结构要设计合理、刚性好,以确保模具在工作过程中运动平稳,提高模具的定位精度和加工精度。
7. 冷却系统设计:模具上下模座中需设置冷却系统,以及时、均匀地冷却模具,提高模具的使用寿命和加工效率。
8. 防撞设计:模具上下模座要设计防撞结构,以保护模具的工作表面不受损伤,降低模具的维修成本。
总之,模具上下模座设计的标准要求涉及尺寸精度、材料选择、结构合理性、油腔和排气孔设计、安装便捷性、导向结构设计、冷却系统设计、防撞设计等多个方面,只有满足这些要求,才能保证模具的正常使用和长期稳定性能。
注塑模具设计准则
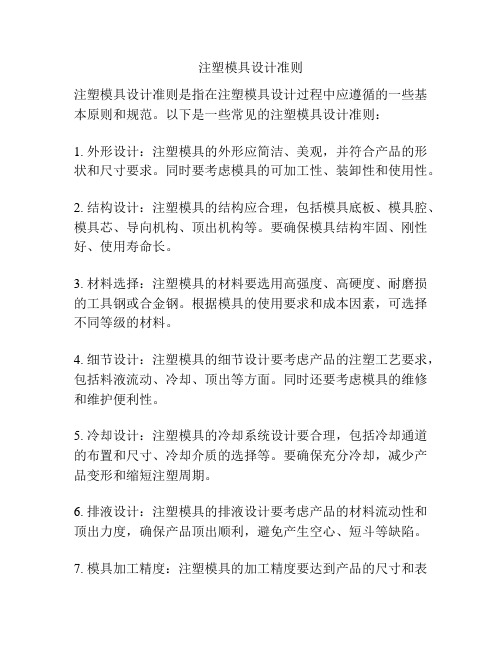
注塑模具设计准则
注塑模具设计准则是指在注塑模具设计过程中应遵循的一些基本原则和规范。
以下是一些常见的注塑模具设计准则:
1. 外形设计:注塑模具的外形应简洁、美观,并符合产品的形状和尺寸要求。
同时要考虑模具的可加工性、装卸性和使用性。
2. 结构设计:注塑模具的结构应合理,包括模具底板、模具腔、模具芯、导向机构、顶出机构等。
要确保模具结构牢固、刚性好、使用寿命长。
3. 材料选择:注塑模具的材料要选用高强度、高硬度、耐磨损的工具钢或合金钢。
根据模具的使用要求和成本因素,可选择不同等级的材料。
4. 细节设计:注塑模具的细节设计要考虑产品的注塑工艺要求,包括料液流动、冷却、顶出等方面。
同时还要考虑模具的维修和维护便利性。
5. 冷却设计:注塑模具的冷却系统设计要合理,包括冷却通道的布置和尺寸、冷却介质的选择等。
要确保充分冷却,减少产品变形和缩短注塑周期。
6. 排液设计:注塑模具的排液设计要考虑产品的材料流动性和顶出力度,确保产品顶出顺利,避免产生空心、短斗等缺陷。
7. 模具加工精度:注塑模具的加工精度要达到产品的尺寸和表
面质量要求,确保产品的工艺性能和外观质量。
8. 模具标准化:注塑模具的设计要符合国际、行业和企业的标准要求,提高模具的互换性和通用性。
总之,注塑模具设计准则是按照工艺要求、产品要求和生产要求来合理设计模具的过程,以确保模具的质量、性能和寿命,提高生产效率和产品质量。
模具设计原则范文

模具设计原则范文1.简化设计:模具设计应尽量简化,减少不必要的部件和加工步骤,降低制造成本。
通过优化和简化设计,可以提高生产效率,缩短生产周期,降低生产成本。
2.标准化设计:模具设计应尽量遵循标准化原则,采用通用标准件和零部件,减少定制化和个性化设计,降低模具制造成本,提高模具的交换性和维修性。
3.可靠性设计:模具设计应具有良好的可靠性和稳定性,能够在长期运行和高负载工况下保持正常工作。
在设计时应考虑材料的可靠性和疲劳性能,合理设置结构形式和承载能力,预防模具的破损和失效。
4.确保精度:模具设计应确保产品和工件的精度要求,在设计过程中考虑到工艺装备的限制和影响,合理控制尺寸和几何形状的公差。
采用合适的材料和热处理工艺,提高模具的精度和稳定性。
5.高效利用材料:模具设计应尽量减少材料的消耗,提高材料的利用率。
通过合理的布局和结构设计,减少碎片材料和废料的产生,降低模具的成本和制造周期。
6.方便维护与修理:模具设计应考虑到维护和修理的便利性,方便对模具进行检修和更换磨损部件。
合理设置零部件的安装和拆卸方式,减少维护和维修的时间和成本。
7.降低生产周期:模具设计应注重提高生产效率和缩短生产周期,通过合理的布局和工艺设计,减少模具装夹和调试的时间,提高模具的生产能力和效率。
8.考虑安全性:模具设计应考虑到操作人员的安全和生产过程的安全性,避免设计上的缺陷和隐患。
合理设置防护装置和警示标识,提供安全操作和维护指导,降低事故的风险。
9.环保设计:模具设计应符合环保要求,避免污染和浪费。
合理选择材料和润滑方式,减少对环境的影响。
优化生产工艺和工艺装备,降低能耗和资源消耗。
10.创新设计:模具设计应注重创新和技术进步,引入新材料和新技术,提高模具的制造精度和效率。
通过创新设计,可以开拓新的市场和产品领域,提高企业的竞争力和市场份额。
总之,模具设计原则是为了提高模具的质量、效益和可靠性,降低制造成本和生产周期,保障操作人员的安全和环境的保护,实现模具设计和制造的可持续发展。
模具行位设计标准要求有哪些

模具行位设计标准要求有哪些
模具行位设计标准要求主要有以下几个方面:
1. 尺寸和形状要求:模具行位应符合产品设计要求的尺寸和形状。
对于三维形状复杂的产品,行位设计可能需要考虑更多的因素,比如模具分离、气门冷却和产品外观等。
2. 位置和方向要求:行位的位置和方向应能满足产品的组装要求。
行位通常用来定位产品的连接件或组件,要求能使产品的各个组成部分精确地对位并稳定地连接。
3. 接口和配合要求:行位需要与其他零部件或设备的接口配合,以确保整个系统的正常运转。
接口和配合要求可能包括形状、尺寸、材料、表面粗糙度、摩擦系数等方面的要求。
4. 加工和制造要求:行位需要容易加工和制造,以提高生产效率和降低成本。
行位的加工和制造要求可能包括材料可加工性、制造精度、加工工艺和设备要求等。
5. 强度和刚度要求:行位需要具备足够的强度和刚度,以承受和传递产品的力和扭矩。
行位的强度和刚度要求可能涉及材料的选择、截面形状、支撑结构等。
6. 表面处理和润滑要求:行位需要进行适当的表面处理和润滑,以防止磨损、腐蚀和卡滞等问题。
表面处理和润滑要求可能包括表面硬度、表面光洁度、涂层材料和润滑剂的选择等。
7. 可靠性和耐久性要求:行位需要具备足够的可靠性和耐久性,以确保模具的长期使用和产品的质量稳定。
可靠性和耐久性要求可能包括应力分布、疲劳寿命、使用寿命等。
综上所述,模具行位设计标准要求涉及到尺寸和形状要求、位置和方向要求、接口和配合要求、加工和制造要求、强度和刚度要求、表面处理和润滑要求,以及可靠性和耐久性要求等方面。
这些要求旨在保证行位的功能和性能,提高模具的生产效率和产品的质量稳定性。
模具行位设计标准要求是什么
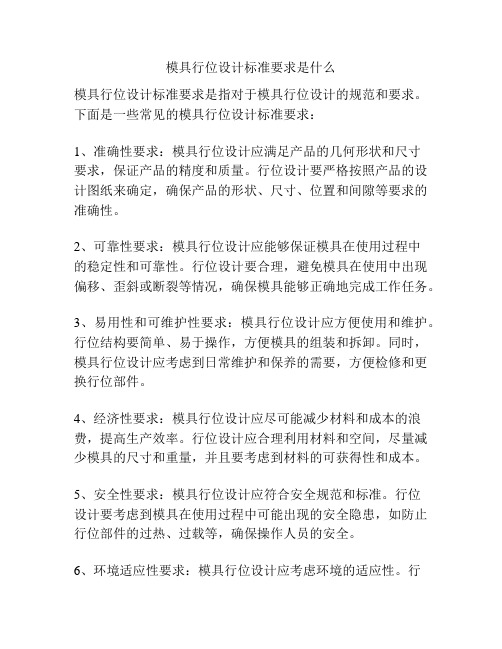
模具行位设计标准要求是什么模具行位设计标准要求是指对于模具行位设计的规范和要求。
下面是一些常见的模具行位设计标准要求:1、准确性要求:模具行位设计应满足产品的几何形状和尺寸要求,保证产品的精度和质量。
行位设计要严格按照产品的设计图纸来确定,确保产品的形状、尺寸、位置和间隙等要求的准确性。
2、可靠性要求:模具行位设计应能够保证模具在使用过程中的稳定性和可靠性。
行位设计要合理,避免模具在使用中出现偏移、歪斜或断裂等情况,确保模具能够正确地完成工作任务。
3、易用性和可维护性要求:模具行位设计应方便使用和维护。
行位结构要简单、易于操作,方便模具的组装和拆卸。
同时,模具行位设计应考虑到日常维护和保养的需要,方便检修和更换行位部件。
4、经济性要求:模具行位设计应尽可能减少材料和成本的浪费,提高生产效率。
行位设计应合理利用材料和空间,尽量减少模具的尺寸和重量,并且要考虑到材料的可获得性和成本。
5、安全性要求:模具行位设计应符合安全规范和标准。
行位设计要考虑到模具在使用过程中可能出现的安全隐患,如防止行位部件的过热、过载等,确保操作人员的安全。
6、环境适应性要求:模具行位设计应考虑环境的适应性。
行位设计要能够适应不同的工作环境和工作条件,如温度、湿度和粉尘等,以保证模具的正常工作和寿命。
7、标准化要求:模具行位设计应遵循相关的国家和行业标准。
行位设计要符合国家关于模具行位设计的标准和要求,确保模具的质量和性能能够达到标准要求,并且便于与其他模具进行配套和交换。
总而言之,模具行位设计标准要求是为了保证模具的准确性、可靠性、易用性、可维护性、经济性、安全性、环境适应性和标准化,以提高模具的生产效率和质量。
模具设计岗位设计标准是什么

模具设计岗位设计标准是什么模具设计岗位设计标准是指在模具设计岗位上,员工需要具备的专业知识、技能和素质等要求。
以下是模具设计岗位设计标准的一般要求:1.专业知识:模具设计岗位的员工需要具备扎实的机械制图基础知识,熟悉CAD软件、UG等相关的模具设计软件的应用,了解模具设计的基本原理、流程和规范。
2.技能要求:模具设计员需要具备良好的三维建模技能,可以根据客户的需求和产品要求,设计出合理、高效的模具方案。
同时需要掌握出图、标注、尺寸控制等技能,能够制作完整、准确的模具设计图纸。
3.工作经验:对于模具设计岗位,通常要求有一定的工作经验。
在实践中积累模具设计的经验,能够独立解决常见的设计问题,并且能够根据项目的需求进行合理的设计方案。
4.沟通能力:模具设计员需要与项目经理、工程师、客户等各方面进行沟通和合作,因此需要具备良好的沟通能力和团队合作精神,能够理解和表达清晰的设计要求,并能够与团队成员进行良好的协调和配合。
5.创新意识:模具设计是一个创新性强的工作,在设计中需要不断地思考和提出创新的设计方案,以提高模具的性能和效率。
因此,模具设计员需要具备良好的创新意识和解决问题的能力。
6.工作质量:模具设计是一个要求精确和细致的工作,设计员需要具备高度的责任心和耐心,能够对自己的设计进行严格的质量控制和审核,并在设计中严格遵守相关的规范和标准。
7.学习能力:随着科技的不断发展和进步,模具设计技术也在不断更新和改进。
模具设计员需要具备良好的学习能力,能够不断学习和吸取新的知识和技术,以适应不断变化的模具设计需求。
综上所述,模具设计岗位需要员工具备扎实的专业知识和技能,良好的沟通能力和团队合作精神,创新意识和解决问题的能力,高度的责任心和耐心,以及良好的学习能力。
这些要求可以保证模具设计师在工作中能够胜任岗位,并不断提高和发展。
模具设计制作要求及特点

模具设计制作的要求是:尺寸精确、表面光洁;结构合理、生产效率高、易于自动化;制造容易、寿命高、成本低;设计符合工艺需要,经济合理。
模具结构设计和参数选择须考虑刚性、导向性、卸料机构、定位方法、间隙大小等因素。
模具上的易损件应容易更换。
对于塑料模和压铸模,还需要考虑合理的浇注系统、熔融塑料或金属流动状态、进入型腔的位置与方向。
为了提高生产率、减少流道浇注损失,可采用多型腔模具,在一模具内能同时完成多个相同或不同的制品。
在大批量生产中应采用高效率、高精度、高寿命的模具。
冲压模应采用多工位级进模,可采用硬质合金镶块级进模,以提高寿命。
在小批量生产和新产品试制中,应采用结构简单、制造快、成本低的简易模具,如组合冲模、薄板冲模、聚氨酯橡胶模、低熔点合金模、锌合金模、超塑性合金模等。
模具已开始采用计算机辅助设计(CAD),即通过以计算机为中心的一整套系统对模具进行最优化设计。
这是模具设计的发展方向。
模具制造按结构特点,分为平面的冲裁模和具有空间的型腔模。
冲裁模利用凸模与凹模的尺寸精确配合,有的甚至是无间隙配合。
其他锻模如冷挤压模、压铸模、粉末冶金模、塑料模、橡胶模等都属于型腔模,用于成形立体形状的工件。
型腔模在长、宽、高3个方向都有尺寸要求,形状复杂,制造困难。
模具生产一般为单件、小批生产,制造要求严格、精确,多采用精密的加工设备和测量装置。
平面冲裁模可用电火花加工初成形,再用成形磨削,坐标磨削等方法进一步提高精度。
成形磨削可用光学投影曲线磨床,或带有缩仿、修打砂轮机构的平面磨床,也可在精密平面磨床上采用专用成形磨削工具磨削。
立式深孔钻可用于模具的精密定位,以保证模具顶针孔孔壁光结、高精准、高效、高质量从而降低成本!。
- 1、下载文档前请自行甄别文档内容的完整性,平台不提供额外的编辑、内容补充、找答案等附加服务。
- 2、"仅部分预览"的文档,不可在线预览部分如存在完整性等问题,可反馈申请退款(可完整预览的文档不适用该条件!)。
- 3、如文档侵犯您的权益,请联系客服反馈,我们会尽快为您处理(人工客服工作时间:9:00-18:30)。
19.压毛边的位置一般为材料厚的 40%
(1) 上 下模座
★ 在模具比较在大的情况下,模座上有外导柱(小型模具可以不要外导柱,)导柱的单 边间隙在 0.01—0.02,这样才能起到良好的导正作用。
★ 模座与夹板联接起来需要樏栓,因此模座上也有螺栓沉头孔彧螺丝孔;有时模座和 夹板也需要合销来固定,因此,模座上也有合销孔,另外,下模座上一定要有漏料孔。有时 弹簧行程不够的情况下,在模座也会有钻弹簧孔。
9.下规条与下规条之间距离须考虑叉车臂宽,以利搬运. 10.有些需深入制品表面,且需要求深度之零件(如凸点 V 沟刻印等),因受力面积 小,易下沉,则垫板(SS41)需加埋金或(SK3)采局部热处理. 11.在切折或小部段曲时,因考虑加工材料,于此加工后,所产生的回弹现象, 取经验值于冲头或折块多加 1.5 度,以确保成品不出现段曲处往上斜. 12.V 沟的位置在内折线外侧,与折线距离(系数/2)处.材料系数为 40%.
模具设计
1. 半成品之毛边向与模具的方向必须正确知(如切边.冲孔.毛边一定向
下)
2.模具高度及闭模高度须配记机台规格(下模 高:80T=180mm,110T=205mm,余为 235mm。)
东 莞 XX 五 金 电 子 厂
题
目 模具设计规笵第二章
版 本 第一节设计要求 共 8 页 第 2 页 编号
来决定
模具
機頭
機頭
模具
吊挂缺口
吊挂螺絲孔
5.如线割范围超宽 400 或长 750 以上则模板要分块.
6.如模板偏大,则需有基准孔(一般为 400mm 以上)以利修模时孔位能正确确认.
7.避位孔或避位槽需确实掌握,尤其是像凸点,补强,半剪断等小地方最易忽略.
8.辅助导柱孔.为辅助上模与下模合模时不可缺少之孔,一般固定于上夹板上, 上檔板与下模确保每次冲压时皆可于之轨迹上移动(夹板一般间隙单边 0.005-0.01 之间,下模档板一般间隙单边 0.01-0.015 滑配).
(2) 上 下夹板: 主要是用来固定, 夹持, 保护冲头的作用。夹板上冲头孔的单边间隙 取-0.03。
在有内导柱的情`下,夹板上有导柱或导柱孔;与模座联接固定合销孔 , 螺栓沉头孔 或螺丝孔;联接脱板的等高套筒过孔,限制脱板行程的弹簧孔或优力胶孔;固定冲头的螺 丝孔,固定销孔(比较在的冲头)。
(3)内 外脱板: 脱料板的作用主要是脱料和保护冲头。脱料板的单边间隙取+0.015,为紧 配合,因此在有脱料板的情况下,冲头可以不用合销。
制订部门
工程部
核准
日期
编撰者
日期
审查
日期
尚崇栋
030108
3.盲孔
3.1 全盲孔:即工件表面无任何钻孔,此种方式用于抽具上 3.2 导引工盲孔:即是工作表面容许有一小,孔此上孔可用来 导模具组立时定出螺丝位,以利冲头和夹板或垫板间之螺丝固定,此种方法
用于 PVC 制品或冲头备料。
全盲孔
導引式盲孔
2. 下模板与下垫板 除上述注意事项外,因有导型孔,基本上固定销孔也采有线,割避免免因组立 偏,差而造不良,再则选择对角孔(平衡位置)攻牙利拆模时模板之移动。 3.上脱板固定销孔逃孔一般应小于固定销以避免固定销掉落而损伤模具. 4.入子、冲头之组立应力求固定,使用各种防止方法勿必防止掉落而损伤模具..
面的交接处均须倒 R 角,以避免加工材料因拉料产生破裂.
A R角
A
PUNCH
15.SPOT 所用打凸冲头一律用 A 型 ø3-ø4 再加沉头,并且成品高 0.6-0.8 且不得有 直线部,冲头采用 ø2 时,模板割单+0.015,背面须钻 ø3-ø4 再加沉头,而对向模板 割单+0.1.
4/8
东 莞 XX 五 金 电 子 厂
东 莞 XX 五 金 电 子 厂
题
目 模具设计规笵第二章
版 本 第一节设计要求 共 8 页 第 1 页 编号
制订部门
工程部
核准
日期
编撰者
日期
审查
日期
尚崇栋
030108
模具设计要求
为了便于冲模设计者在设计模具时,全方位考虑问题,以减少不必要的修改
次数及时间,现特提出以下几点,希望设计时能参照以下内容进行思考,设计。
3/8
东 莞 XX 五 金 电 子 厂
版 本 第一节设计要求 共 8 页 第 4 页
题目Leabharlann 模具设计规笵第二章编号制订部门
工程部
核准
日期
编撰者
日期
审查
日期
尚崇栋
030108
系數/2
內
折
線
v 溝衝子
13.刻印冲无论在上模或在下模,均应用螺丝固定或背面锤大固定,基本上刻印印 凸出模面 0.3mm,特殊要求除外,若刻印或成型入子具有方向性,刻印入子或成 型入子须做防呆. 14.拱桥或切桥成型,于冲头或入块的制造过程中,无论哪一项,于两边斜度与平
1. 拿到产品图时,首先应了解产品所需毛边方向。
2. 了解产品材质类型及厚度,以决定间隙大小。
冲孔 下料时间隙的配置
冲孔冲子准,下料母模准。也就是讲,冲孔时间隙放在母模上,下料时间隙放
下冲子上。一般的情况下,剪断间隙为 5%T(單边间隙)。另外,间隙的配置,
还要依据产品的要求,依据各个尺寸的公差而定 。
17.定位: 材料于外形尺寸冲制完成后,若冲压件当中尚有其它须冲制之孔,于 其它工程加工时,即须用到此种孔为材料之位定用,其主要目的在于确认材 料在每一工程加工时相关位置,不致于偏差(间隙为单+0.01 滑配)
18.外导柱用于无法安置内导柱或连续模,使用外导柱必须确实注意闭模时导柱
是否过长,一般而言,闭模时不管何种导柱,导柱都低于座板 10mm 以上.
版 本 第一节设计要求 共 8 页 第 5 页
题
目 模具设计规笵第二章
编号
制订部门
工程部
核准
日期
编撰者
日期
审查
日期
尚崇栋
030108
16.新开模请购材料时,应采取档板与夹板全面闭合为考量,避免减少成本而采采
取局部使用等高块,虽然两种做法所产生的成品相同,但是于制模过程与模具
寿命之考量都应采用第一种.因为局部使用等高块,剥板容易爆裂.
2/8
东 莞 XX 五 金 电 子 厂
版 本 第一节设计要求 共 8 页
题
目 模具设计规笵第二章
编号
第3页
制订部门
工程部
核准
日期
编撰者
日期
审查
日期
尚崇栋
030108
4.上座板在冲床上机头涵盖范围内时,上座板可切割吊挂缺口.且切割口应倒角
(用于维护吊和人员安全).如超出上机头范围时, 关位置视冲床规格