聚丙烯合成工艺的研究
聚丙烯本体法—气相法组合工艺

聚丙烯本体法—气相法组合工艺聚丙烯是一种重要的塑料材料,广泛应用于包装、电子、汽车等领域。
而聚丙烯的制备过程中,聚丙烯本体法和气相法是两种常用的组合工艺。
聚丙烯本体法是指通过聚合反应直接合成聚丙烯的方法。
首先,将丙烯单体在合适的溶剂中溶解,然后加入催化剂进行聚合反应。
聚合反应中,丙烯单体的双键被打开,形成聚合物链。
随着反应的进行,聚丙烯链不断增长,最终形成高分子量的聚合物。
最后,通过蒸发溶剂和除去残余的催化剂等步骤,得到纯净的聚丙烯产品。
聚丙烯本体法具有反应条件温和、操作简单、产物纯度高等优点。
然而,该方法也存在一些问题。
首先,由于聚丙烯的分子量较大,反应时间较长,反应速率较慢。
其次,聚合反应中产生的热量不易散发,容易导致反应温度过高,影响产物质量。
因此,为了提高反应速率和控制反应温度,可以采用气相法进行辅助。
气相法是指通过将丙烯单体在高温下转化为气体,然后在催化剂的作用下进行聚合反应。
首先,将丙烯单体加热至一定温度,使其转化为气体。
然后,将气体丙烯引入反应器中,与催化剂接触进行聚合反应。
聚合完成后,通过冷却和减压等操作,将产物聚丙烯收集。
气相法的优点是反应速率快、产物纯度高。
由于丙烯单体转化为气体后,分子间的碰撞频率增加,有利于反应的进行。
同时,气相法的反应温度可通过控制供气量和冷却方式等参数进行调节,使得反应温度更易控制。
聚丙烯本体法和气相法的组合工艺是将两种方法有机地结合起来,充分发挥各自的优点。
首先,利用聚丙烯本体法合成聚丙烯的基础,通过反应条件的优化,得到分子量较高的聚丙烯初产物。
然后,将初产物转化为气体,采用气相法进行进一步的聚合反应。
这样做的好处是既可以利用聚丙烯本体法合成高分子量的聚丙烯,又可以利用气相法提高反应速率和产物质量。
使用聚丙烯本体法—气相法组合工艺制备聚丙烯的过程中,需要注意一些关键问题。
首先,需要选择适合的催化剂和溶剂,以提高聚合反应的效率和产物纯度。
其次,需要合理控制反应温度和反应时间,以避免产物质量的下降。
聚丙烯纤维的制备工艺研究
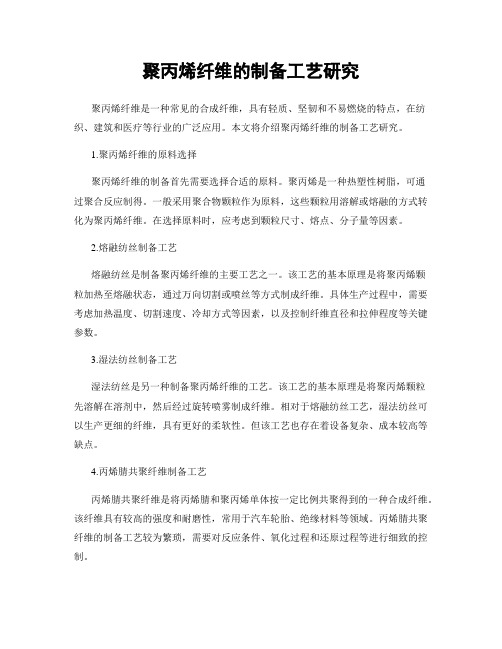
聚丙烯纤维的制备工艺研究聚丙烯纤维是一种常见的合成纤维,具有轻质、坚韧和不易燃烧的特点,在纺织、建筑和医疗等行业的广泛应用。
本文将介绍聚丙烯纤维的制备工艺研究。
1.聚丙烯纤维的原料选择聚丙烯纤维的制备首先需要选择合适的原料。
聚丙烯是一种热塑性树脂,可通过聚合反应制得。
一般采用聚合物颗粒作为原料,这些颗粒用溶解或熔融的方式转化为聚丙烯纤维。
在选择原料时,应考虑到颗粒尺寸、熔点、分子量等因素。
2.熔融纺丝制备工艺熔融纺丝是制备聚丙烯纤维的主要工艺之一。
该工艺的基本原理是将聚丙烯颗粒加热至熔融状态,通过万向切割或喷丝等方式制成纤维。
具体生产过程中,需要考虑加热温度、切割速度、冷却方式等因素,以及控制纤维直径和拉伸程度等关键参数。
3.湿法纺丝制备工艺湿法纺丝是另一种制备聚丙烯纤维的工艺。
该工艺的基本原理是将聚丙烯颗粒先溶解在溶剂中,然后经过旋转喷雾制成纤维。
相对于熔融纺丝工艺,湿法纺丝可以生产更细的纤维,具有更好的柔软性。
但该工艺也存在着设备复杂、成本较高等缺点。
4.丙烯腈共聚纤维制备工艺丙烯腈共聚纤维是将丙烯腈和聚丙烯单体按一定比例共聚得到的一种合成纤维。
该纤维具有较高的强度和耐磨性,常用于汽车轮胎、绝缘材料等领域。
丙烯腈共聚纤维的制备工艺较为繁琐,需要对反应条件、氧化过程和还原过程等进行细致的控制。
5.聚丙烯纤维在实际应用中的问题和解决方法聚丙烯纤维在实际应用中会遇到一些问题,如热收缩、毛羽较多等。
为了解决这些问题,可采取措施如改变纺丝温度、纤维互锁等。
此外,聚丙烯纤维的染色和印刷也需要根据其化学性质和纤维结构特征进行相应的处理和修饰。
总之,聚丙烯纤维在现代工业和日常生活中的应用非常广泛,其制备工艺的研究和掌握对于提高纤维品质和开发新产品都具有重要意义。
虽然聚丙烯纤维的制备工艺存在一定的技术难度,但随着技术的不断进步和创新,相信在未来会有更多的突破和提高。
聚丙烯合成工艺流程
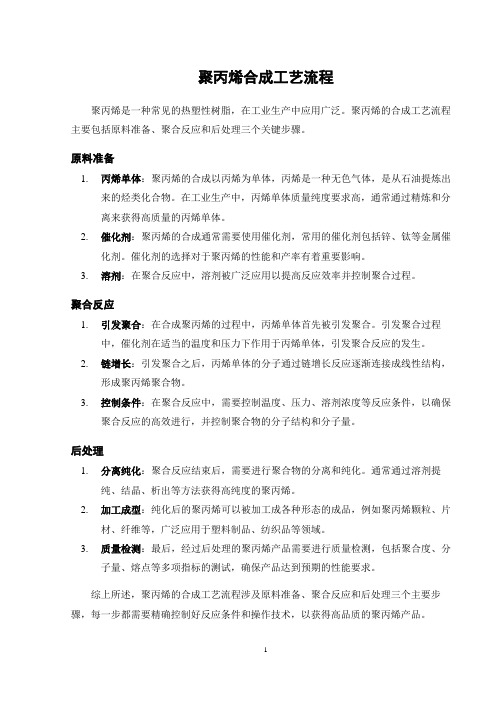
聚丙烯合成工艺流程聚丙烯是一种常见的热塑性树脂,在工业生产中应用广泛。
聚丙烯的合成工艺流程主要包括原料准备、聚合反应和后处理三个关键步骤。
原料准备1.丙烯单体:聚丙烯的合成以丙烯为单体,丙烯是一种无色气体,是从石油提炼出来的烃类化合物。
在工业生产中,丙烯单体质量纯度要求高,通常通过精炼和分离来获得高质量的丙烯单体。
2.催化剂:聚丙烯的合成通常需要使用催化剂,常用的催化剂包括锌、钛等金属催化剂。
催化剂的选择对于聚丙烯的性能和产率有着重要影响。
3.溶剂:在聚合反应中,溶剂被广泛应用以提高反应效率并控制聚合过程。
聚合反应1.引发聚合:在合成聚丙烯的过程中,丙烯单体首先被引发聚合。
引发聚合过程中,催化剂在适当的温度和压力下作用于丙烯单体,引发聚合反应的发生。
2.链增长:引发聚合之后,丙烯单体的分子通过链增长反应逐渐连接成线性结构,形成聚丙烯聚合物。
3.控制条件:在聚合反应中,需要控制温度、压力、溶剂浓度等反应条件,以确保聚合反应的高效进行,并控制聚合物的分子结构和分子量。
后处理1.分离纯化:聚合反应结束后,需要进行聚合物的分离和纯化。
通常通过溶剂提纯、结晶、析出等方法获得高纯度的聚丙烯。
2.加工成型:纯化后的聚丙烯可以被加工成各种形态的成品,例如聚丙烯颗粒、片材、纤维等,广泛应用于塑料制品、纺织品等领域。
3.质量检测:最后,经过后处理的聚丙烯产品需要进行质量检测,包括聚合度、分子量、熔点等多项指标的测试,确保产品达到预期的性能要求。
综上所述,聚丙烯的合成工艺流程涉及原料准备、聚合反应和后处理三个主要步骤,每一步都需要精确控制好反应条件和操作技术,以获得高品质的聚丙烯产品。
1。
气相法聚丙烯生产工艺技术进展研究
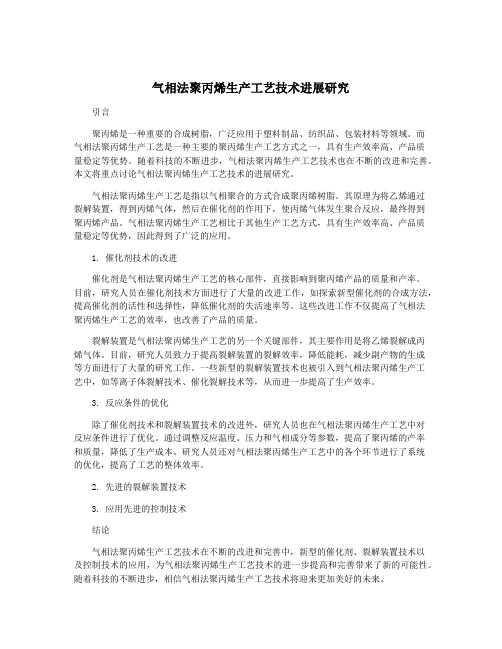
气相法聚丙烯生产工艺技术进展研究引言聚丙烯是一种重要的合成树脂,广泛应用于塑料制品、纺织品、包装材料等领域。
而气相法聚丙烯生产工艺是一种主要的聚丙烯生产工艺方式之一,具有生产效率高、产品质量稳定等优势。
随着科技的不断进步,气相法聚丙烯生产工艺技术也在不断的改进和完善。
本文将重点讨论气相法聚丙烯生产工艺技术的进展研究。
气相法聚丙烯生产工艺是指以气相聚合的方式合成聚丙烯树脂。
其原理为将乙烯通过裂解装置,得到丙烯气体,然后在催化剂的作用下,使丙烯气体发生聚合反应,最终得到聚丙烯产品。
气相法聚丙烯生产工艺相比于其他生产工艺方式,具有生产效率高、产品质量稳定等优势,因此得到了广泛的应用。
1. 催化剂技术的改进催化剂是气相法聚丙烯生产工艺的核心部件,直接影响到聚丙烯产品的质量和产率。
目前,研究人员在催化剂技术方面进行了大量的改进工作,如探索新型催化剂的合成方法,提高催化剂的活性和选择性,降低催化剂的失活速率等。
这些改进工作不仅提高了气相法聚丙烯生产工艺的效率,也改善了产品的质量。
裂解装置是气相法聚丙烯生产工艺的另一个关键部件,其主要作用是将乙烯裂解成丙烯气体。
目前,研究人员致力于提高裂解装置的裂解效率,降低能耗,减少副产物的生成等方面进行了大量的研究工作。
一些新型的裂解装置技术也被引入到气相法聚丙烯生产工艺中,如等离子体裂解技术、催化裂解技术等,从而进一步提高了生产效率。
3. 反应条件的优化除了催化剂技术和裂解装置技术的改进外,研究人员也在气相法聚丙烯生产工艺中对反应条件进行了优化。
通过调整反应温度、压力和气相成分等参数,提高了聚丙烯的产率和质量,降低了生产成本。
研究人员还对气相法聚丙烯生产工艺中的各个环节进行了系统的优化,提高了工艺的整体效率。
2. 先进的裂解装置技术3. 应用先进的控制技术结论气相法聚丙烯生产工艺技术在不断的改进和完善中,新型的催化剂、裂解装置技术以及控制技术的应用,为气相法聚丙烯生产工艺技术的进一步提高和完善带来了新的可能性。
世界主要聚丙烯生产工艺

世界主要聚丙烯生产工艺
聚丙烯是一种热塑性的合成树脂,广泛应用于塑料制品、纤维和薄膜等领域。
世界上主要的聚丙烯生产工艺包括以下几种:
1. 偏聚工艺(Isotactic Polymerization):通过催化剂催化聚合
丙烯单体,使其形成偏聚结构的聚丙烯。
该工艺广泛应用于商业聚丙烯的生产,具有成本低廉、生产效率高等优点。
2. 股聚工艺(Syndiotactic Polymerization):通过特殊催化剂
催化聚合丙烯单体,使其形成股聚结构的聚丙烯。
这种聚丙烯具有较高的结晶度和熔融温度,适用于一些特殊领域的应用。
3. 合金工艺(Alloying):将聚丙烯和其他材料进行混合,形
成聚丙烯合金。
这种工艺可以改善聚丙烯的性能,使其具有更多的应用领域。
4. 吹膜工艺(Blow Molding):将熔融的聚丙烯注入吹膜机中,通过气流的作用将其吹膨成薄膜。
吹膜工艺可以生产出各种厚度和用途的聚丙烯薄膜。
5. 压力挤出工艺(Compression Molding):将熔融的聚丙烯注入模具中进行压力挤出,使其形成所需的形状。
压力挤出工艺常用于生产聚丙烯制品,如瓶子、管道等。
6. 注塑工艺(Injection Molding):将熔融的聚丙烯注入注塑
机中,通过模具的作用使其凝固成所需的形状。
注塑工艺广泛应用于聚丙烯制品的生产,如塑料零件、容器等。
以上是世界主要的聚丙烯生产工艺,不同工艺在应用领域、成本效益等方面具有差异,选择适合的生产工艺能够提高生产效率和产品质量。
聚丙烯缝线合成方法
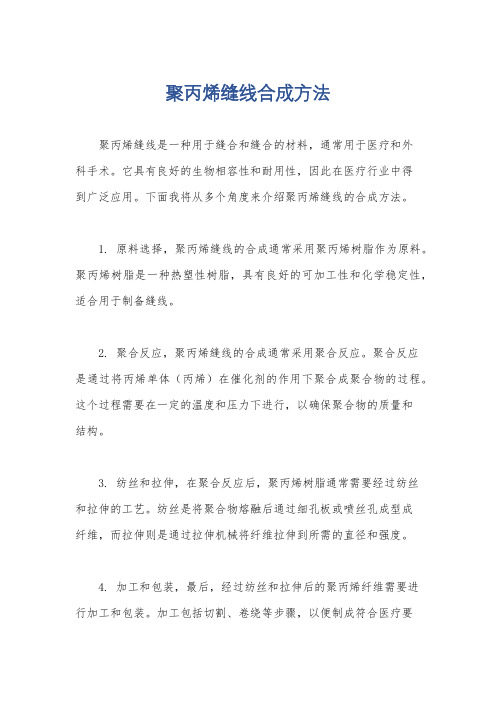
聚丙烯缝线合成方法
聚丙烯缝线是一种用于缝合和缝合的材料,通常用于医疗和外
科手术。
它具有良好的生物相容性和耐用性,因此在医疗行业中得
到广泛应用。
下面我将从多个角度来介绍聚丙烯缝线的合成方法。
1. 原料选择,聚丙烯缝线的合成通常采用聚丙烯树脂作为原料。
聚丙烯树脂是一种热塑性树脂,具有良好的可加工性和化学稳定性,适合用于制备缝线。
2. 聚合反应,聚丙烯缝线的合成通常采用聚合反应。
聚合反应
是通过将丙烯单体(丙烯)在催化剂的作用下聚合成聚合物的过程。
这个过程需要在一定的温度和压力下进行,以确保聚合物的质量和
结构。
3. 纺丝和拉伸,在聚合反应后,聚丙烯树脂通常需要经过纺丝
和拉伸的工艺。
纺丝是将聚合物熔融后通过细孔板或喷丝孔成型成
纤维,而拉伸则是通过拉伸机械将纤维拉伸到所需的直径和强度。
4. 加工和包装,最后,经过纺丝和拉伸后的聚丙烯纤维需要进
行加工和包装。
加工包括切割、卷绕等步骤,以便制成符合医疗要
求的规格。
而包装则是为了保护聚丙烯缝线,确保其在运输和使用
过程中不受到污染和损坏。
总的来说,聚丙烯缝线的合成方法涉及到原料选择、聚合反应、纺丝和拉伸、加工和包装等多个环节。
这些环节需要严格控制和操作,以确保最终产品符合医疗器械的要求。
同时,合成过程中还需
要考虑到环境友好和生产成本等因素,以实现可持续发展和经济效益。
气相法聚丙烯生产工艺技术进展研究

气相法聚丙烯生产工艺技术进展研究气相法聚丙烯生产是目前工业上生产聚丙烯的主要方法之一。
该方法的主要优点是易于控制反应的温度、压力、气体成分和流速等参数,生产出的聚丙烯具有优异的物理化学性能。
本文将介绍目前气相法聚丙烯生产的技术进展及相关问题研究。
首先,关于催化剂的研究。
气相法聚丙烯生产是通过催化剂引发反应,使丙烯分子聚合形成聚合物。
提高催化剂的活性和选择性是提高聚合物产率和质量的关键因素。
目前研究表明,具有良好活性和选择性的Ziegler-Natta催化剂和Phillps催化剂是目前工业上使用最多的两种催化剂。
最近,研究人员也开始研究利用单质铬催化剂进行气相聚丙烯合成,其优点是可以在低压下进行聚合反应,大大减少了能耗和污染排放。
其次,关于反应器的研究。
反应器是气相聚丙烯生产中的关键设备,保证反应器的稳定运行是生产高质量聚合物的基础。
目前研究表明,采用多级反应器或者循环流化床反应器,可以有效地提高聚合物的产率和降低副产物的生成。
同时,也研究出了一种新型的反应器——催化剂牵引床,其在保证反应器稳定的前提下,实现了催化剂循环利用,大大缩短了反应时间。
第三,关于共聚反应的研究。
除了聚丙烯单体外,还可以使用其他共聚单体进行反应,使得聚合物具有更好的特性和应用价值。
例如,采用环氧丙烷作为共聚单体可以制备出具有优异热稳定性和耐磨性的聚丙烯复合材料。
同时,也有研究表明采用硅氧烷接枝共聚可以大大提高聚合物的附着性和表面耐磨性。
第四,关于催化剂毒化和废催化剂利用的研究。
催化剂毒化是气相聚丙烯生产中的常见问题,其原因可能是反应物中杂质的存在或者催化剂的老化。
因此,提高催化剂的稳定性和循环使用率是解决催化剂毒化问题的关键。
同时,废催化剂的处理也是一个比较严峻的问题,传统方法是将其直接处理为废物,这既浪费资源也增加了环境负担。
现在人们开始研究如何将废催化剂进行再利用,例如利用钴或铬等元素从废催化剂中提取出来,制备成新型催化剂或是应用于其他业务领域。
PP材料的合成工艺

PP材料的合成工艺
PP材料是一种广泛应用于塑料制品中的材料,它具有优异的物理性能和化学稳定性,因此在各种领域都有着广泛的应用。
那么,PP 材料是如何合成的呢?
PP材料的合成工艺主要分为以下几个步骤:
1. 原料准备
PP材料的主要原料是丙烯,因此在合成之前需要对丙烯进行准备。
通常情况下,丙烯是从石油或天然气中提取出来的,然后通过蒸馏、裂解等工艺进行精制,得到高纯度的丙烯。
2. 聚合反应
将准备好的丙烯加入反应釜中,加入催化剂和其他助剂,进行聚合反应。
在反应过程中,丙烯分子会不断地连接起来,形成长链状的聚丙烯分子。
这个过程需要控制反应温度、压力、催化剂种类和用量等因素,以确保聚合反应的顺利进行。
3. 精炼和加工
聚合反应完成后,得到的聚丙烯物料需要进行精炼和加工。
这个过程包括熔融、挤出、拉伸、压制等工艺,以将聚丙烯物料加工成各种形状和尺寸的制品。
在这个过程中,需要控制加工温度、压力、
速度等因素,以确保制品的质量和性能。
4. 检测和质量控制
需要对制品进行检测和质量控制。
这个过程包括物理性能测试、化学性能测试、外观检查等,以确保制品符合相关的标准和要求。
如果发现制品存在质量问题,需要及时进行调整和改进。
PP材料的合成工艺是一个复杂的过程,需要掌握一定的化学和工程知识。
只有通过科学的工艺流程和严格的质量控制,才能生产出高质量的PP制品,满足市场的需求。
气相法聚丙烯生产工艺技术进展研究
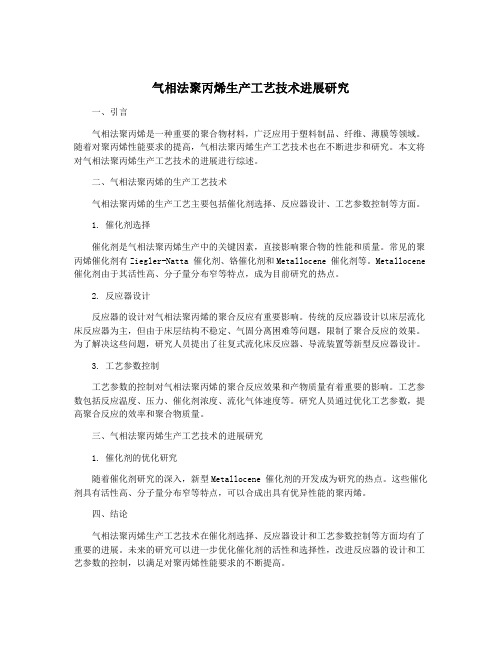
气相法聚丙烯生产工艺技术进展研究一、引言气相法聚丙烯是一种重要的聚合物材料,广泛应用于塑料制品、纤维、薄膜等领域。
随着对聚丙烯性能要求的提高,气相法聚丙烯生产工艺技术也在不断进步和研究。
本文将对气相法聚丙烯生产工艺技术的进展进行综述。
二、气相法聚丙烯的生产工艺技术气相法聚丙烯的生产工艺主要包括催化剂选择、反应器设计、工艺参数控制等方面。
1. 催化剂选择催化剂是气相法聚丙烯生产中的关键因素,直接影响聚合物的性能和质量。
常见的聚丙烯催化剂有Ziegler-Natta 催化剂、铬催化剂和Metallocene 催化剂等。
Metallocene 催化剂由于其活性高、分子量分布窄等特点,成为目前研究的热点。
2. 反应器设计反应器的设计对气相法聚丙烯的聚合反应有重要影响。
传统的反应器设计以床层流化床反应器为主,但由于床层结构不稳定、气固分离困难等问题,限制了聚合反应的效果。
为了解决这些问题,研究人员提出了往复式流化床反应器、导流装置等新型反应器设计。
3. 工艺参数控制工艺参数的控制对气相法聚丙烯的聚合反应效果和产物质量有着重要的影响。
工艺参数包括反应温度、压力、催化剂浓度、流化气体速度等。
研究人员通过优化工艺参数,提高聚合反应的效率和聚合物质量。
三、气相法聚丙烯生产工艺技术的进展研究1. 催化剂的优化研究随着催化剂研究的深入,新型Metallocene 催化剂的开发成为研究的热点。
这些催化剂具有活性高、分子量分布窄等特点,可以合成出具有优异性能的聚丙烯。
四、结论气相法聚丙烯生产工艺技术在催化剂选择、反应器设计和工艺参数控制等方面均有了重要的进展。
未来的研究可以进一步优化催化剂的活性和选择性,改进反应器的设计和工艺参数的控制,以满足对聚丙烯性能要求的不断提高。
聚丙烯材料的制备和改性研究
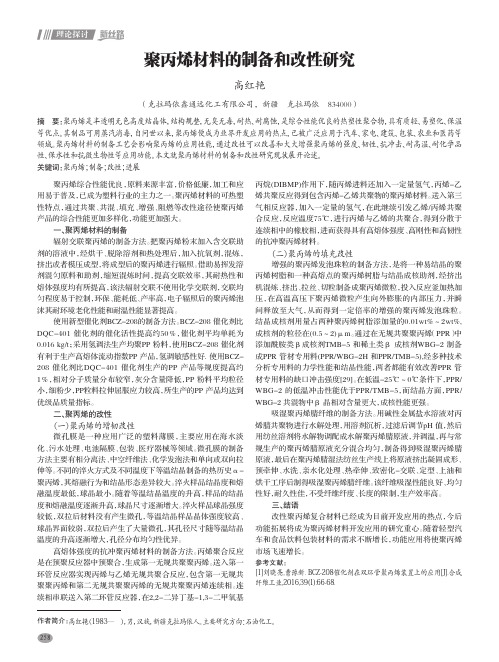
258作者简介:高红艳(1983— ),男,汉族,新疆克拉玛依人。
主要研究方向:石油化工。
聚丙烯综合性能优良,原料来源丰富,价格低廉,加工和应用易于普及,已成为塑料行业的主力之一。
聚丙烯材料的可热塑性特点,通过共聚、共混、填充、增强、阻燃等改性途径使聚丙烯产品的综合性能更加多样化,功能更加强大。
一、聚丙烯材料的制备辐射交联聚丙烯的制备方法。
把聚丙烯粉末加入含交联助剂的溶液中,经烘干、脱除溶剂和热处理后,加入抗氧剂,混炼,挤出或者模压成型,将成型后的聚丙烯进行辐照。
借助易挥发溶剂混匀原料和助剂,缩短混炼时间,提高交联效率,其耐热性和熔体强度均有所提高,该法辐射交联不使用化学交联剂,交联均匀程度易于控制,环保、能耗低、产率高,电子辐照后的聚丙烯泡沫其耐环境老化性能和耐温性能显著提高。
使用新型催化剂BCZ-208的制备方法。
BCZ-208 催化剂比DQC-401 催化剂的催化活性提高约50%,催化剂平均单耗为0.016 kg/t;采用氢调法生产均聚PP 粉料,使用BCZ-208 催化剂有利于生产高熔体流动指数PP 产品,氢调敏感性好. 使用BCZ-208 催化剂比DQC-401 催化剂生产的PP 产品等规度提高约1%,相对分子质量分布较窄,灰分含量降低,PP 粉料平均粒径小,细粉少,PP粒料拉伸屈服应力较高,所生产的PP 产品均达到优级品质量指标。
二、聚丙烯的改性(一)聚丙烯的增韧改性微孔膜是一种应用广泛的塑料薄膜,主要应用在海水淡化、污水处理、电池隔膜、包装、医疗器械等领域。
微孔膜的制备方法主要有相分离法、中空纤维法、化学发泡法和单向或双向拉伸等。
不同的淬火方式及不同温度下等温结晶制备的热历史α-聚丙烯,其熔融行为和结晶形态差异较大。
淬火样品结晶度和熔融温度最低,球晶最小。
随着等温结晶温度的升高,样品的结晶度和熔融温度逐渐升高,球晶尺寸逐渐增大。
淬火样品球晶强度较低,双拉后材料没有产生微孔,等温结晶样品晶体强度较高、球晶界面较弱,双拉后产生了大量微孔,其孔径尺寸随等温结晶温度的升高逐渐增大,孔径分布均匀性优异。
气相法聚丙烯生产工艺技术进展研究

气相法聚丙烯生产工艺技术进展研究一、气相法聚丙烯生产工艺技术原理气相法聚丙烯生产工艺是将乙烯和丙烯等原料与催化剂一起送入反应器中,经过聚合反应后形成聚丙烯。
其原理主要包括以下几个方面:1. 催化剂选择:气相法聚丙烯生产工艺中常用的催化剂有Ziegler-Natta催化剂、Phillips催化剂等。
这些催化剂在聚合反应中能够高效催化乙烯和丙烯的共聚反应,生成高分子量的聚丙烯。
2. 反应条件控制:聚丙烯的生产过程需要严格控制反应温度、压力等条件,以保证聚合反应的高效进行和聚合物合成的良好质量。
3. 聚合反应过程:乙烯和丙烯等原料通过催化剂的作用,进行聚合反应生成聚丙烯。
整个过程主要包括聚合反应、卸载和再生等步骤。
二、气相法聚丙烯生产工艺技术模型建立为了更好地研究和优化气相法聚丙烯生产工艺,研究者们通常会建立相应的数学模型来模拟和预测聚合反应的情况,并基于模型结果进行工艺参数的优化。
目前,已经有许多关于气相法聚丙烯生产工艺技术模型的研究,其中主要包括以下几个方面:1. 反应器动力学模型:研究者们利用反应器动力学模型来描述聚丙烯的聚合反应过程,分析反应器中的乙烯和丙烯浓度、催化剂浓度等对聚合反应速率的影响,从而优化反应条件。
2. 热力学模型:利用热力学模型来分析聚丙烯聚合反应的热力学行为,包括热量的生成和传递等,以确保反应器的温度控制在合适范围内。
3. 流体力学模型:通过建立流体力学模型,研究者们可以模拟和分析气相法聚丙烯生产工艺中气流和反应器内流体的运动状态,以优化反应器结构和气流分布等参数。
三、气相法聚丙烯生产工艺技术的改进随着科学技术的不断发展,气相法聚丙烯生产工艺技术也在不断改进和完善中,以提高生产效率和产品质量。
一些改进方向包括以下几个方面:1. 催化剂的研究和改进:研究者们通过改进催化剂的配方和制备工艺,使得其在聚合反应中的催化效率更高、寿命更长,从而提高聚丙烯的生产效率和产品质量。
2. 反应器结构的优化:对气相法聚丙烯生产工艺中的反应器结构进行改进,以提高反应器的稳定性和催化剂的利用率,从而减少生产成本和环境污染。
聚丙烯生产工艺技术

聚丙烯生产工艺技术1. 简介聚丙烯(Polypropylene,简称PP)是一种重要的合成聚合物。
由于其优异的物理性能和化学稳定性,聚丙烯被广泛应用于塑料制品、纺织品和包装材料等领域。
聚丙烯的生产工艺技术对产品的质量和性能有着重要影响。
2. 聚丙烯生产工艺流程聚丙烯的生产工艺主要包括以下几个步骤:2.1 原料准备聚丙烯的主要原料是丙烯(propylene)。
在生产过程中需要对丙烯进行预处理,包括脱色和脱气等操作,以确保原料的质量。
2.2 聚合反应在聚合反应中,丙烯通过聚合反应生成线性或分支聚合物链。
该过程通常在高压或高温条件下进行,配合催化剂和稳定剂等添加剂以控制聚合反应的速率和产物的质量。
2.3 精炼和分离精炼和分离步骤主要用来净化和分离聚合物链。
这一步骤通常包括过滤、洗涤、溶剂抽出和熔融分离等操作,以去除杂质和分离不同分子量的聚合物。
2.4 加工成型加工成型是将聚丙烯通过加工设备加工成所需的形态,常见的加工方式包括挤出、注塑和吹塑等。
在加工成型过程中,需要控制温度、压力和速度等参数,以确保产品的质量和性能。
2.5 产品后处理产品后处理是指对加工成型后的聚丙烯进行后续处理,以提高产品的性能和外观。
常见的后处理方式包括退火、表面处理和添加剂添加等。
3. 聚丙烯生产工艺技术的控制为了确保聚丙烯产品的质量和性能稳定,生产过程中需要进行严格的工艺控制。
3.1 温度控制温度是聚合反应和加工成型过程中的关键参数之一。
在聚合反应中,需要控制反应温度以控制聚合反应的速率和产物的分子量。
在加工成型过程中,温度的控制可以影响产品的流动性和形态。
3.2 压力控制压力是聚合反应和加工成型过程中的另一个重要参数。
在聚合反应中,需要控制反应压力以控制聚合反应的速率和产物的分子量。
在加工成型过程中,压力的控制可以影响产品的强度和形态。
3.3 添加剂控制在聚丙烯的生产过程中,通常需要添加催化剂、稳定剂和其他添加剂等。
添加剂的种类和用量对产品的性能和质量有重要影响,因此需要进行精确的添加剂控制。
聚丙烯生产—聚丙烯生产工艺

高聚物 PMMA
PS PVC LDPE
工艺过程要点
预聚阶段转化率控制在10%左右,制备黏稠浆液,然后 浇模分段升温聚合,最后脱模成材。
在80~85℃下预聚至转化率为33%~35%的聚合物,流 入聚合塔,温度从100℃递增至220℃,最后熔体挤出造粒。
制备转化率为7%~11%的预聚物,形成颗粒骨架,继续 进行沉淀聚合,最后以粉状出料。(少数企业)
选用管式或釜式反应器,连续聚合,控制单程转化率约 为15% ~20%,最后熔体挤出造粒。
高聚物生产技术 2.溶液聚合
将单体和引发剂溶解于溶剂中进行聚合反应的方法。
体系 组成
单体
引发剂
溶剂
聚丙烯的生产 助剂
高聚物生产技术
优点
均相反应、降 低体系粘度、 易导出反应热、 对涂料、粘合 剂等产品可直 接使用
高聚物生产技术
三、聚合工艺路线特点
聚丙烯的生产
1 反应器型式(立式搅拌床反应器) 2 聚合温度控制(60-70℃) 3 高产率的聚合循环(传热能力强)
自由基聚合
产物特点与用途
纺丝液 配制纺丝液 制备聚乙烯醇、维纶的原 料
涂料、粘合剂
配位聚合 阴离子聚合
顺丁橡胶 低顺式聚丁二烯
高聚物生产技术
聚丙烯的生产
实施方法 本体聚合
溶液聚合
连锁聚合反应工业实施方法比较
反应前组成 单体、引发剂
特点
简单、反应热难排除, 产品纯度高
控制条件 反应热,产物出料
单体、引发剂 溶 剂
单体
引发剂
助剂
高聚物生产技术
优点
均相反应体系 简单;工艺简 单、易于连续 化聚合;生产 能力大、成本 低;产物纯度 高、透明性好
聚丙烯的生产工艺

聚丙烯的生产工艺摘要:聚丙烯(简称PP)是一种热望性合成树脂,用途十分广泛,市场需求一直呈快速增长态势。
在聚烯烃树脂中,己成为仅次于聚氯乙烯、聚乙烯的第三大塑料,在合成树脂中占有越来越重要的地位。
聚丙烯生产工艺主要有4 种;溶液聚合法、浆液法、液相本体聚合法、气相聚合法。
而液相本体法聚丙烯工艺自1978年工业化以来,由于具有工艺流程短、操作简单、生产成本低、装置投资小、经济效益好等特点,被广泛用于国内许多炼油厂中的聚丙烯生产。
关键字:聚丙烯间歇式液相本体法1.聚丙烯的简介1.1聚丙烯产品性质聚丙烯(PP)分为等规、无规和间规三种,是一种热塑性合成树脂塑料,分子式(c3H6)n,分子量2545万,为白色固体粉状,表观密度低(约为0.4-0.489/cm3),透明性及表面光泽好,机械性能良好,化学稳定性好,制品耐热性好(熔点高达167℃,可在沸水中使用或蒸汽消毒),无毒性,也是一种最轻的塑料树脂。
2.聚丙烯的生产2.1聚合配方及工艺参数丙烯纯度:>99.2% 催化剂:Ticl3-异戊醚-TiCI4-AIEt2CI AI/Ti 2-6mol催化剂效率:70000g聚丙烯/g钛丙烯转化率60% 聚合物浓度:35%调节剂:H2 聚合温度: 50-60℃聚合压力:1.1-1.2mpa聚合等规度:95-96% 无规物:4-5%2.2原料丙烯来源聚丙烯主要原料是丙烯,目前它主要由石油炼制裂化所得的液化气以及石油烃裂解气,进行馏分分离、提纯而制得。
另外,丙烷脱氢也可制得丙烯。
下面对两种主要方法作简要介绍:2.2.1石油烃裂解石油烃裂解是指在隔绝空气的高温条件下,大分子烃发生分解而生成小分子烷烃和烯烃的过程。
裂解产生的裂解气一般通过深冷分离过程进行分离,其中丙烯约为裂解气的11~16%(W)。
2.2.1炼厂气回收:炼厂气是石油炼制过程中产生的气体总称,主要有热裂化气、催化裂化气、焦化气、重整气和加氢裂化气等。
催化裂化的裂化气中液化气量较多,为原料的8~15%(W),其中丙烯含量较高,占原料的4.0~5.0%(W),特别是新开发的催化裂解工艺,丙烯可达原料的18%(W)左右,因此,催化裂化、催化裂解释炼厂气丙烯的主要来源。
年产万吨聚丙烯合成工艺设计

一、工艺原理
聚丙烯合成工艺分为气相法和熔相法两种。
本次设计采用的是气相法,它的工艺原理主要是将甲烷与乙炔按一定比例在20-25MPa、650-750℃的
条件下在反应器内反应,产物主要为聚丙烯(PP)。
气相反应有利于形成
更高分子量的分子,具有较高的装置投资效率和更高的催化杂质释放特性。
二、反应材料与反应剂
聚丙烯合成反应采用的材料主要有:甲烷(CH4)、乙炔(C2H4),
反应剂可选择的催化剂有:活性炭(AC)、硫酸钆(GAS)等,活性炭是
最常用的反应剂。
三、反应器
本次设计采用的反应器主要有气液混合器、反应器本体,气液混合器
可选择的有螺旋管式混合器、旋转式混合器、流失式混合器等,本次采用
的是螺旋管式混合器,反应器本体主要为不锈钢管,采用热交换的方式加热;反应器采用正常压力反应,压力范围15-20MPa,温度范围620-750℃,反应时间2小时,反应完成后,料温降至室温。
四、分离蒸馏设备。
聚丙烯 毕业论文

聚丙烯毕业论文聚丙烯是一种重要的合成塑料,广泛应用于包装、纺织、建筑等领域。
本文将从聚丙烯的性质、制备工艺、应用以及环境影响等方面进行探讨。
一、聚丙烯的性质聚丙烯是由丙烯单体聚合而成的高分子化合物,具有优良的物理性质和化学稳定性。
它具有较高的熔点和熔融粘度,可以通过调整聚合条件得到不同分子量的聚丙烯。
此外,聚丙烯还具有良好的耐腐蚀性、耐热性和耐候性,是一种重要的工程塑料。
二、聚丙烯的制备工艺聚丙烯的制备主要通过聚合反应完成。
常见的聚合方法有催化剂聚合和无催化剂聚合两种。
催化剂聚合是指在聚合反应中引入催化剂,加速聚合反应的进行。
无催化剂聚合则是直接通过高温条件下的热聚合反应进行。
此外,还可以通过改变聚合条件和添加其他助剂来调控聚丙烯的分子量和性能。
三、聚丙烯的应用由于聚丙烯具有良好的物理性质和化学稳定性,被广泛应用于各个领域。
在包装行业,聚丙烯可以制成薄膜、瓶盖、容器等,用于食品、药品等产品的包装。
在纺织行业,聚丙烯纤维可以制成绳索、织物等,用于制作袋子、地毯等产品。
此外,聚丙烯还可以制成管道、板材等用于建筑和工程领域。
四、聚丙烯的环境影响虽然聚丙烯在各个领域得到广泛应用,但其对环境的影响也不容忽视。
首先,聚丙烯是一种不可降解的塑料,长时间存在于自然环境中,对土壤和水体造成污染。
其次,聚丙烯的制备过程中会产生大量的废气和废水,对大气和水体环境造成污染。
因此,在聚丙烯的生产和使用过程中,需要加强环境保护措施,减少对环境的影响。
综上所述,聚丙烯是一种重要的合成塑料,具有良好的物理性质和化学稳定性,被广泛应用于包装、纺织、建筑等领域。
然而,聚丙烯的制备和使用过程中也会对环境造成一定的影响,因此需要加强环境保护工作。
未来,随着科技的发展,我们有望研发出更环保的替代品,以减少对聚丙烯的依赖,实现可持续发展。
PP材料的合成工艺
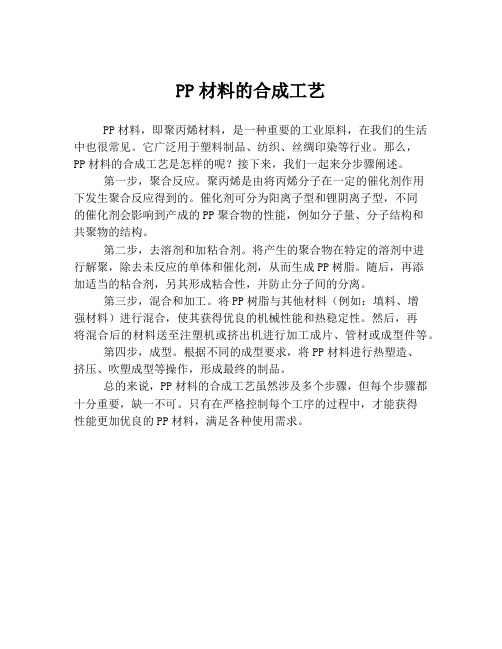
PP材料的合成工艺
PP材料,即聚丙烯材料,是一种重要的工业原料,在我们的生活中也很常见。
它广泛用于塑料制品、纺织、丝绸印染等行业。
那么,
PP材料的合成工艺是怎样的呢?接下来,我们一起来分步骤阐述。
第一步,聚合反应。
聚丙烯是由将丙烯分子在一定的催化剂作用
下发生聚合反应得到的。
催化剂可分为阳离子型和锂阴离子型,不同
的催化剂会影响到产成的PP聚合物的性能,例如分子量、分子结构和
共聚物的结构。
第二步,去溶剂和加粘合剂。
将产生的聚合物在特定的溶剂中进
行解聚,除去未反应的单体和催化剂,从而生成PP树脂。
随后,再添
加适当的粘合剂,另其形成粘合性,并防止分子间的分离。
第三步,混合和加工。
将PP树脂与其他材料(例如:填料、增
强材料)进行混合,使其获得优良的机械性能和热稳定性。
然后,再
将混合后的材料送至注塑机或挤出机进行加工成片、管材或成型件等。
第四步,成型。
根据不同的成型要求,将PP材料进行热塑造、
挤压、吹塑成型等操作,形成最终的制品。
总的来说,PP材料的合成工艺虽然涉及多个步骤,但每个步骤都十分重要,缺一不可。
只有在严格控制每个工序的过程中,才能获得
性能更加优良的PP材料,满足各种使用需求。
聚丙烯工艺技术总结与感悟

聚丙烯工艺技术总结与感悟聚丙烯是一种广泛应用于塑料制品、纺织品、包装材料等领域的合成树脂。
在工艺技术方面,聚丙烯的制备过程是关键,下面我对聚丙烯工艺技术进行总结与感悟。
首先,聚丙烯的制备过程包括聚合、加工和成型三个基本步骤。
聚合是将丙烯单体加热到一定温度下,添加催化剂和引发剂,使其发生聚合反应。
这一步骤的关键是确保温度和催化剂的配比,以及控制反应时间,从而得到预期的聚合度。
加工是将聚合后的聚丙烯块料进行熔融,使其具有一定的流动性,便于后续的成型操作。
成型是将熔化的聚丙烯通过挤出、注塑、吹塑等方式,使其成为所需的制品。
在聚丙烯的制备过程中,我深刻体会到了技术的重要性。
合理的催化剂配比和温度控制,可以确保聚合反应的进行,从而获得具有理想性能的聚丙烯。
同时,加工过程中的温度和压力控制也是影响最终产品质量的关键因素。
只有通过合理的工艺参数,才能保证成品的外观、尺寸和力学性能符合要求。
另外,聚丙烯工艺技术的发展也需要持续的创新和改进。
随着社会的发展和人们对质量要求的提高,对聚丙烯制品性能的要求也越来越高。
因此,在工艺技术的研究和应用中,我们需要不断地引入新的材料和工艺方法,以提高聚丙烯制品的性能和质量。
例如,近年来随着生物技术的发展,聚丙烯的生物降解性材料已经成为一个研究热点。
通过将可降解材料引入聚丙烯制备过程中,可以减少塑料垃圾对环境的污染,具有良好的社会和环境效益。
总的来说,聚丙烯工艺技术在塑料制品行业中起到了重要的作用。
通过掌握和应用合理的工艺技术,可以获得高质量的聚丙烯制品。
同时,聚丙烯工艺技术的研究也需要不断创新和改进,以满足社会对高性能、低环境影响的聚丙烯制品的需求。
这对于推动塑料制品行业的可持续发展具有重要意义。
- 1、下载文档前请自行甄别文档内容的完整性,平台不提供额外的编辑、内容补充、找答案等附加服务。
- 2、"仅部分预览"的文档,不可在线预览部分如存在完整性等问题,可反馈申请退款(可完整预览的文档不适用该条件!)。
- 3、如文档侵犯您的权益,请联系客服反馈,我们会尽快为您处理(人工客服工作时间:9:00-18:30)。
聚丙烯合成工艺的研究摘要中国聚丙烯的工业生产始于20世纪70年代,经过30多年的发展,已经基本上形成了溶剂法、液相本体-气相法、间歇式液相本体法、气相法等多种生产工艺并举,大中小型生产规模共存的生产格局,本文主要介绍了世界5大类聚丙烯生产工艺,着重介绍了液相本体法聚丙烯工艺流程及控制条件。
Abstract Industrial production of polypropylene in China began in the 20th century, 70's, after 30 years of development, has been basically formed a solvent, liquid bulk - Gas Law, intermittent liquid bulk, gas phase, and other production processes simultaneously,the coexistence of large and small scale production patterns, the paper introduces the world's five major categories of polypropylene production process, focusing on the liquid flow Polypropylene and control conditions中国聚丙烯的工业生产始于20世纪70年代,经过30多年的发展,已经基本上形成了溶剂法、液相本体-气相法、间歇式液相本体法、气相法等多种生产工艺并举,大中小型生产规模共存的生产格局。
现在中国的大型聚丙烯生产装置以引进技术为主,中型和小型聚丙烯生产装置以国产化技术为主。
聚丙烯,英文名称:Polypropylene,日文名称:ポリプロピレン分子式:C3H6nCAS 简称:PP由丙烯聚合而制得的一种热塑性树脂。
按甲基排列位置分为等规聚丙烯(isotaeticPolyProlene)、无规聚丙烯(atacticPolyPropylene)和间规聚丙烯(syndiotatic PolyPropylene)三种。
目前,聚丙烯的生产工艺按聚合类型可分为溶液法、淤浆法、本体法和气相法和本体法-气相法组合工艺5大类。
具体工艺主要有BP公司的气相Innovene工艺、Chisso公司的气相法工艺、Dow公司的Unipol工艺、Novolene气相工艺、Sumitomo气相工艺、Basell公司的本体法工艺、三井公司开发的Hypol 工艺以及Borealis公司的Borstar工艺等。
世界5大类聚丙烯生产工艺概述1 淤浆法工艺淤浆法工艺(Slurry Process)又称浆液法或溶剂法工艺,是世界上最早用于生产聚丙烯的工艺技术。
从1957年第一套工业化装置一直到20世纪80年代中后期,淤浆法工艺在长达30年的时间里一直是最主要的聚丙烯生产工艺。
典型工艺主要包括意大利的Montedison 工艺、美国Hercules工艺、日本三井东压化学工艺、美国Amoco工艺、日本三井油化工艺以及索维尔工艺等。
这些工艺的开发都基于当时的第一代催化剂,采用立式搅拌釜反应器,需要脱灰和脱无规物,因采用的溶剂不同,工艺流程和操作条件有所不同。
近年来,传统的淤浆法工艺在生产中的比例明显减少,保留的淤浆产品主要用于一些高价值领域,如特种BOPP薄膜、高相对分子质量吹塑膜以及高强度管材等。
近年来,人们对该方法进行了改进,改进后的淤浆法生产工艺使用高活性的第二代催化剂,可删除催化剂脱灰步骤,能减少无规聚合物的产生,可用于生产均聚物、无规共聚物和抗冲共聚物产品等。
目前世界淤浆法PP的生产能力约占全球PP 总生产能力的13%。
2 溶液法工艺溶液法生产工艺是早期用于生产结晶聚丙烯的工艺路线,由Eastman公司所独有。
该工艺采用一种特殊改进的催化剂体系-锂化合物(如氢化锂铝)来适应高的溶液聚合温度。
催化剂组分、单体和溶剂连续加入聚合反应器,未反应的单体通过对溶剂减压而分离循环。
额外补充溶剂来降低溶液的粘度,并过滤除去残留催化剂。
溶剂通过多个蒸发器而浓缩,再通过一台能够除去挥发物的挤压机而形成固体聚合物。
固体聚合物用庚烷或类似的烃萃取进一步提纯,同时也除去了无定形聚丙烯,取消了使用乙醇和多步蒸馏的过程,主要用于生产一些与浆液法产品相比模量更低、韧性更高的特殊牌号产品。
该方法工艺流程复杂,且成本较高,聚合温度高,加上由于采用特殊的高温催化剂使产品应用范围有限,目前已经不再用于生产结晶聚丙烯。
3 本体法工艺本体法工艺的研究开发始于20世纪60年代,1964年美国Dart公司采用釜式反应器建成了世界上第一套工业化本体法聚丙烯生产装置。
1970年以后,日本住友、Phillips、美国EI Psao等公司都实现了液相本体聚丙烯工艺的工业化生产。
与采用溶剂的浆液法相比,采用液相丙烯本体法进行聚合具有不使用惰性溶剂,反应系统内单体浓度高,聚合速率快,催化剂活性高,聚合反应转化率高,反应器的时-空生产能力更大,能耗低,工艺流程简单,设备少,生产成本低,"三废"量少;容易除去聚合热,并使撤热控制简单化,可以提高单位反应器的聚合量;能除去对产品性质有不良影响的低分子量无规聚合物和催化剂残渣,可以得到高质量的产品等优点。
不足之处是反应气体需要气化、冷凝后才能循环回反应器。
反应器内的高压液态烃类物料容量大,有潜在的危险性。
此外,反应器中乙烯的浓度不能太高,否则在反应器中形成一个单独的气相,使得反应器难以操作,因而所得共聚产品中的乙烯含量不会太高。
本体法不同工艺路线的区别主要是反应器的不同。
反应器可分为釜式反应器和环管反应器两大类。
釜式反应器是利用液体蒸发的潜热来除去反应热,蒸发的大部分气体经循环冷凝后返回到反应器,未冷凝的气体经压缩机升压后循环回反应器。
而环管反应器则是利用轴流泵使浆液高速循环,通过夹套冷却撤热,由于传热面积大,撤热效果好,因此其单位反应器体积产率高,能耗低。
本体法生产工艺按聚合工艺流程,可以分为间歇式聚合工艺和连续式聚合工艺两种。
(1)间歇本体法工艺。
间歇本体法聚丙烯聚合技术是我国自行研制开发成功的生产技术。
它具有生产工艺技术可靠,对原料丙烯质量要求不是很高,所需催化剂国内有保证,流程简单,投资省、收效快,操作简单,产品牌号转换灵活、三废少,适合中国国情等优点,不足之处是生产规模小,难以产生规模效益;装置手工操作较多,间歇生产,自动化控制水平低,产品质量不稳定;原料的消耗定额较高;产品的品种牌号少,档次不高,用途较窄。
目前,我国采用该法生产的聚丙烯生产能力约占全国总生产能力的24.0%;(2)连续本体法工艺。
该工艺主要包括美国Rexall工艺、美国Phillips工艺以及日本Sumitimo工艺。
(a)Rexall工艺。
Rexall本体聚合工艺是介于溶剂法和本体法工艺之间的生产工艺,由美国Rexall公司开发成功,该工艺采用立式搅拌反应器,用丙烷含量为10%-30%(质量分数)的液态丙烯进行聚合。
在聚合物脱灰时采用己烷和异丙醇的恒沸混合物为溶剂,简化了精馏的步骤,将残余的催化剂和无规聚丙烯一同溶解于溶剂中,从溶剂精馏塔的底部排出。
以后,该公司与美国El Paso 公司组成的联合热塑性塑料公司,开发了被称为"液池工艺"的新生产工艺,采用Montedison -MPC公司的HY-HS高效催化剂,取消了脱灰步骤,进一步简化了工艺流程。
该工艺的特点是以高纯度的液相丙烯为原料,采用HY-HS高效催化剂,无脱灰和脱无规物工序。
采用连续搅拌反应器,聚合热用反应器夹套和顶部冷凝器撤出,浆液经闪蒸分离后,单体循环回反应;(b)Phillips工艺。
该工艺由美国Phillips石油公司于20世纪60年代开发成功。
其工艺特点是采用独特的环管式反应器,这种结构简单的环管反应器具有单位体积传热面积大,总传热系数高,单程转化率高、流速快、混合好、不会在聚合区形成塑化块、产品切换牌号的时间短等优点。
该工艺可以生产宽范围熔体流动速率的聚聚物和无规聚合物;(c)Sumitimo工艺。
该工艺由日本Sumitimo(住友)化学公司于1974年开发成功。
此工艺基本上与Rexene本体法相似,但Sumitimo本体法工艺包括除去无规物及催化剂残余物的一些措施。
通过这些措施可以制得超聚合物,用于某些电气和医学用途。
Sumitimo本体法工艺使用SCC络合催化剂(以一氯二乙基铝还原四氯化钛,并经过正丁醚处理),液相丙烯在50-80℃、3. 0MPa下进行聚合,反应速率高,聚合物等规指数也较高,还采用高效萃取器脱灰,产品等规指数为96%-97%,产品为球状颗粒,刚性高,热稳定性好,耐油及电气性能优越。
4 本体法-气相法组合工艺本体法-气相法组合工艺主要包括巴塞尔公司的Spheripol工艺、日本三井化学公司的Hypol工艺、北欧化工公司的Borstar工艺等。
(1)Spheripol工艺。
Spheripol工艺由巴塞尔(Basell)聚烯烃公司开发成功。
该技术自1982年首次工业化以来,是迄今为止最成功、应用最为广泛的聚丙烯生产工艺。
Spheripol工艺是一种液相预聚合同液相均聚和气相共聚相结合的聚合工艺,工艺采用高效催化剂,生成的PP粉料粒度其催化剂生产的粉料呈园球形,颗粒大而均匀,分布可以调节,既可宽又可窄。
可以生产全范围、多用途的各种产品。
其均聚和无规共聚产品的特点是净度高,光学性能好,无异味。
Spheripol工艺采用的液相环管反应器具有以下优点:(a)有很高的反应器时-空产率(可达400kgPP/h.m3),反应器的容积较小,投资少;(b)反应器结构简单,材质要求低,可用低温碳钢,设计制造简单,由于管径小(DN500或DN600),即使压力较高,管壁也较薄;(c)带夹套的反应器直腿部分可作为反应器框架的支柱,这种结构设计降低了投资;(d)由于反应器容积小,停留时间短,产品切换快,过渡料少;(e)聚合物颗粒悬浮于丙烯液体中,聚合物与丙烯之间有很好的热传递。
采用冷却夹套撤出反应热单位体积的传热面积大,传热系数大,环管反应器的总体传热系数高达1600W/(m2.℃);(f)环管反应器内的浆液用轴流泵高速循环,流体流速高达7m/s,因此可以使聚合物淤浆搅拌均匀,催化剂体系分布均匀,聚合反应条件容易控制而且可以控制得很精确,产品质量均一,不容易产生热点,不容易粘壁,轴流泵的能耗也较低;(g)反应器内聚合物浆液浓度高(质量分数大于50%),反应器的单程转化率高,均聚的丙烯单程转化率为50%-60%。