(常用刀柄结构)SHK-KM-CAPTO
加工中心刀柄规格

加工中心刀柄规格加工中心的主轴锥孔通常分为两大类,即锥度为7:24 的通用系统和1:10 的HSK 真空系统。
7:24 锥度的通用刀柄锥度为7:24 的通用刀柄通常有五种标准和规格,即NT(传统型)、DIN 69871(德国标准)、IS07388/1 (国际标准)、MAS BT(日本标准)以及ANSI/ASME(美国标准)。
NT 型刀柄德国标准为DIN 2080,是在传统型机床上通过拉杆将刀柄拉紧,国内也称为ST;其它四种刀柄均是在加工中心上通过刀柄尾部的拉钉将刀柄拉紧。
目前国内使用最多的是DIN 69871 型(即JT)和MAS BT 型两种刀柄。
DIN 69871 型的刀柄可以安装在DIN 69871 型和ANSI/ASME 主轴锥孔的机床上,IS0 7388/1 型的刀柄可以安装在DIN69871 型、IS0 7388/1 和ANSI/ASME 主轴锥孔的机床上,所以就通用性而言,IS0 7388/1 型的刀柄是最好的。
(1)DIN 2080 型(简称NT 或ST)DIN 2080 是德国标准,即国际标准ISO 2583 ,是我们通常所说NT 型刀柄,不能用机床的机械手装刀而用手动装刀。
(2)DIN 69871 型(简称JT、DIN、DAT 或DV)DIN 69871 型分两种,即DIN 69871 A/AD 型和DIN 69871 B 型,前者是中心内冷,后者是法兰盘内冷,其它尺寸相同。
(3)ISO 7388/1 型(简称IV 或IT)其刀柄安装尺寸与DIN 69871 型没有区别,但由于ISO 7388/1 型刀柄的D4 值小于DIN 69871型刀柄的D4 值,所以将ISO 7388/1 型刀柄安装在DIN 69871 型锥孔的机床上是没有问题的,但将DIN 69871 型刀柄安装在ISO 7388/1 型机床上则有可能会发生干涉。
(4)MAS BT 型(简称BT)BT 型是日本标准,安装尺寸与DIN 69871、IS0 7388/1 及ANSI 完全不同,不能换用。
BT刀柄和HSK刀柄的特点和用途

BT刀柄和HSK刀柄的特点和用途SK系列(7:24锥度)a:BT 系列,日本标准b:JT 系列(DIN 69871) 德标c:CAT 系列dIN 2080 系列,用于手动换到HSK 系列主要有A,B,C,D,E 五类HSK柄是高速柄,特别是E系列无键槽是目前最高动平衡标准主柄SK系列转速不能太高,一般一万左右就到极限了(受限与拉钉拉紧方式)不过HSK 由于制造复杂,属于过定位内涨式类型价格比较高另外还有肯那专门为马扎克制作的类似于HSK 柄的多用于车铣中心具体自己看看资料了我是天天做刀柄的,前面有个朋友说NT不是型号,那你就说错了,NT就是德国DIN2080,普通机床上用的, 天天做刀柄,如果有对刀柄研究的请加我QQ:774384667 备注 :abc现在主要市场有7/24 和1/10的锥柄的刀柄,其中7/24有数控用和普通用,数控有国际标准,德国,日本,美国,普通用的,是公制和英制区分,在中国市场日本的BT型用的最多,还有就是德国的DIN69871(SK或NC),1/10锥柄因为他的造价和制造技术问题,国内企业还没有几个能做,它的型号用HSK 机台的主轴要求比较高,国内厂家还没有普遍使用,在刀柄的制造公司中,日本的BIG公司的BBT,可以替代hsk,因为HSK是空心柄,结构强度有一点问题,但是BBT就不同了,......................刀柄的定位精度有自定位(如BT等)和过定位(HSK和BIG等),静态精度都不错,主要的区别在于动态精度. 传说HSK等在高速时仍能保持与主轴接触的紧密性,动态精度好,因广泛应用于高速加工中.BT和HSK等大都是通过键来传递扭矩,还有一些刀柄是通过自身形状传递扭矩的(如Capto接口). 一般通过自身形状传递扭矩的刀柄都号称传递扭矩较大且更稳定,尤其是高速状态时.加工中心的主轴锥孔通常分为两大类,即锥度为7:24的通用系统和1:10的HSK真空系统。
数控刀柄规格型号大全
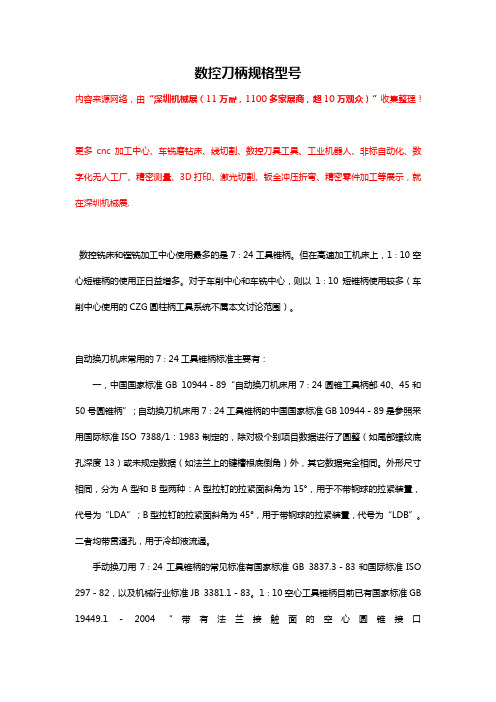
数控刀柄规格型号内容来源网络,由“深圳机械展(11万㎡,1100多家展商,超10万观众)”收集整理!更多cnc加工中心、车铣磨钻床、线切割、数控刀具工具、工业机器人、非标自动化、数字化无人工厂、精密测量、3D打印、激光切割、钣金冲压折弯、精密零件加工等展示,就在深圳机械展.数控铣床和镗铣加工中心使用最多的是7∶24工具锥柄。
但在高速加工机床上,1∶10空心短锥柄的使用正日益增多。
对于车削中心和车铣中心,则以1∶10短锥柄使用较多(车削中心使用的CZG圆柱柄工具系统不属本文讨论范围)。
自动换刀机床常用的7∶24工具锥柄标准主要有:一,中国国家标准GB 10944-89“自动换刀机床用7∶24圆锥工具柄部40、45和50号圆锥柄”;自动换刀机床用7∶24工具锥柄的中国国家标准GB 10944-89是参照采用国际标准ISO 7388/1:1983制定的,除对极个别项目数据进行了圆整(如尾部螺纹底孔深度13)或未规定数据(如法兰上的键槽根底倒角)外,其它数据完全相同。
外形尺寸相同,分为A型和B型两种:A型拉钉的拉紧面斜角为15°,用于不带钢球的拉紧装置,代号为“LDA”;B型拉钉的拉紧面斜角为45°,用于带钢球的拉紧装置,代号为“LDB”。
二者均带贯通孔,用于冷却液流通。
手动换刀用7∶24工具锥柄的常见标准有国家标准GB 3837.3-83和国际标准ISO 297-82,以及机械行业标准JB 3381.1-83。
1∶10空心工具锥柄目前已有国家标准GB 19449.1-2004“带有法兰接触面的空心圆锥接口二,国际标准ISO 7388/1:1983(40、45和50号工具锥柄)和ISO 7388/3:1986(30号工具锥柄);国际标准ISO 7388/1:1983又是参照德国标准DIN 69871-1的A型工具锥柄制定的,所以这三个标准的外形尺寸相同。
在国内,其工具锥柄的代号为“JT”。
(常用刀柄结构)SHK-KM-CAPTO

摘要:高速切削技术是近十多年来发展最为迅速的先进制造技术之一。
文章在论述高速切削技术发展历程和特点的基础上,着重研究了高速切削技术中的刀柄结构,包括HSK、KM及CAPTO,并比较了常用的BT刀柄与HKS、KM刀柄的拉紧特性。
对高速旋转所带来的特殊的动平衡问题及其执行标准也作了叙述。
1、概述高速切削是一个相对概念,并且随着时代的进步而不断变化。
一般认为高速切削或超高速切削的速度为普通切削加工的5~10倍。
可以从不同的角度对切削速度进行划分,如从加工工艺的角度看,高速切削加工范围为:车削700~7000m/min;铣削300~6000m/min;钻削200~1100m/min;磨削150~360m/min。
也可以根据被加工材料来确定高速切削的范围,如加工钢材达到380m/min以上、铸铁700m/min以上、铜材1000m/min以上、铝材1100m/min以上。
也可以根据主轴转速、功率、锥孔大小、和平衡标准来划分,如按主轴的Dn值划分,高速主轴的Dn值一般为500000~2000000;对于加工中心,可按主轴锥孔的大小来划分:50号锥——10000~20000r/min;40号锥——20000~40000r/min;30号锥——25000~40000r/min;HSK 锥——20000~40000r/min;KM锥——35000r/min以上。
而根据ISO—1940,高速主轴的转速至少要超过8000r/min。
1978年CIRP切削委员会将高速切削定为500~7500 m/min[1][2][3]。
研究表明:随着切削速度的提高,切削力会降低15~30%以上,切削热量大多被切屑带走,加工表面质量可提高1~2级,生产效率的提高,可降低制造成本20%~40%。
所以高速切削意义不仅仅是得到较高的表面切削质量[2]。
国外对高速切削技术的研究比较早,可以追溯到20世纪60年代。
目前已应用于航空、航天、汽车、模具等多种工业中的钢、铸铁及其合金、铝、镁合金、超级合金(镍基、铬基、铁基和钛基合金)及碳素纤维增强塑料等复合材料的加工,其中以加工铸铁和铝合金最为普遍。
新型CAPTO夹刀结构

瑞典Coromant Capto®界面专用 最新拉刀机构组件(适合高速强力主轴)1背景说明瑞典Sandvik Coromant 公司于1998 年开发出适用于 Coromant Capto 模块化刀把及刀具系统之专用主轴拉刀机构组件。
由于Coromant Capto 系统在车削、铣削、钻削的各式各样刀把及刀具上的优越模块化速换性能,拉刀机构性能及整体刚性,使得该系统特别适合应用于多功能的车铣复合机上。
1.1现行拉刀机构设计现行拉刀机构的设计,一般由拉刀夹爪,倍力器,碟型弹簧或螺旋弹簧组合而成 (见下图)。
由于近年来,市场对工具机除了要求性能的提升外,对机台外型尺寸也要求精巧,以适应日趋饱和的厂房面积及摆设问题。
在主轴设计上,也相对的要求在提升转速及扭力输出之外,主轴外径及长度也应予以适度的缩减。
2最新拉刀机构设计针对上述的对工具机要求瑞典Sandvik Coromant 公司特别推出全新的拉刀机构。
该设计中包含Coromant Capto 拉刀爪 (简称 : CC 拉刀爪),全新设计的倍力器机构来配合独步全球的氮气弹簧及。
CC 拉刀爪及全新的倍力器机构的组合也可以配合现有的碟型或螺旋弹簧使用。
2.1应用范围Coromant Capto 刀具接口系统配合此一全新设计的拉刀机构可以全方位应用在各型低转速或高转速的工具机上。
Coromant Capto 三角短锥界面 (简称 : CC 接口)的特性与平衡对称设计的拉刀机构,可以使得此一组合应用在高速加工机时,大幅减轻高速主轴组立时的动平衡的调整工作。
2.2拉刀机构组件2.3 组合种类清单C 4-SP-CS-11 C 5-SP-CS-11C 6-SP-CS-11 C 8-SP-CS-11CC 拉刀爪 + 倍力器 + 氮气弹簧C 4-SP-CS-12 C 5-SP-CS-12 C 6-SP-CS-12 C 8-SP-CS-12CC 界面套环CC 拉刀爪 + 倍力器 + 氮气弹簧C 4-SP-CS-01 C 5-SP-CS-01 C 6-SP-CS-01 C 8-SP-CS-01CC 拉刀爪 + 倍力器 ( + 自配弹簧)C 4-SP-CS-02 C 5-SP-CS-02 C 6-SP-CS-02 C 8-SP-CS-02CC 界面套环CC 拉刀爪 + 倍力器 ( + 自配弹簧)倍力器53 技术数据Coromant Capto ® 拉刀机构主要尺寸及拉刀力/退刀力*) 主轴端面至尾端联打刀结处。
高速刀柄及其工具系统的结构与性能

图 3 KM 刀柄的结构
KM 工具系统具有高刚度、高精度、快速装夹和 维护简 单等优点。试验证 实 KM 刀柄的动 刚度比 HSK 系统更高, 不过由于 KM 刀柄锥面上开有对称 的两个供夹紧用的圆弧凹槽, 通常需要较大的夹紧 力才能使其正常工作。
3. 4 NC5 刀柄及其工具系统 NC5 工具系统是日本株式会社日研工作所开发 的( 如图 4 所示) , 该刀柄采用 1: 10 锥度的实心短锥 结构, 锥柄外部套装有开轴向槽的锥套, 锥套和法兰 端面之间装有碟形弹簧。锥套在碟形弹簧的作用下 轴向移动, 实现和主轴锥面的配合, 同时也实现了端 面定位。
1 tan2b
接传递) cos( q+ 2 6385)
3. 5 ( 详 见 参考文献 [ 3] )
拉钉
后靠 传递
拉 锥
紧 套
1(拉 钉 接传递)
直
tana
冷却 形式
外部冷却 可以内冷
可以内冷 可以内冷 可以内冷
锥体 形式
实心锥体 空心薄壁
实 心 锥 体 实心 锥 体
空心薄壁 ( 带冷却孔 ( 带内部冷
* 十五 国家科技攻关项目( 项目编号: 2001BA205) 江苏省自然科学基金资助项目( 项目编号: BK2004027)
收稿日期: 2008 年 1 月
图 1 高速加工时 BT 刀柄工作示意图
3 高速刀柄及其工具系统
3. 1 高速加工对工具系统的基本要求 高速加工工具系统的基本功能是保证刀具在机 床中的准确定位, 同时传递加工所需的运动和动力。 为了实现其基本功能, 工具系统要具有高动平衡精
2008 年第 42 卷 10
31
高速刀柄及其工具系统的结构与性能*
薛宏丽1 王贵成1 刘 钢2
Capto C5刀柄关键尺寸的确定
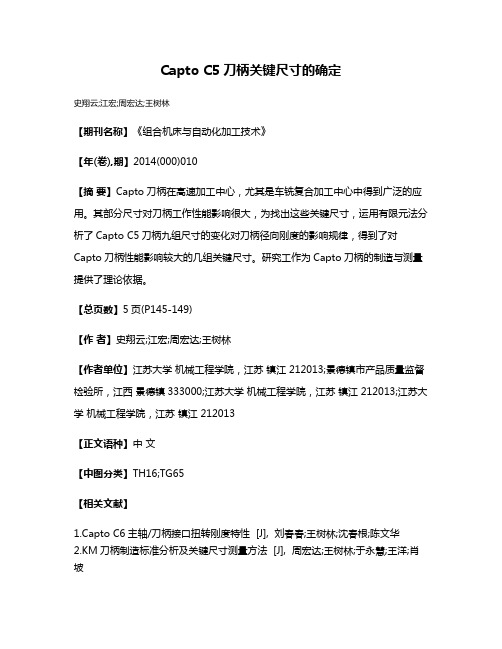
Capto C5刀柄关键尺寸的确定
史翔云;江宏;周宏达;王树林
【期刊名称】《组合机床与自动化加工技术》
【年(卷),期】2014(000)010
【摘要】Capto刀柄在高速加工中心,尤其是车铣复合加工中心中得到广泛的应用。
其部分尺寸对刀柄工作性能影响很大,为找出这些关键尺寸,运用有限元法分析了Capto C5刀柄九组尺寸的变化对刀柄径向刚度的影响规律,得到了对Capto刀柄性能影响较大的几组关键尺寸。
研究工作为Capto刀柄的制造与测量提供了理论依据。
【总页数】5页(P145-149)
【作者】史翔云;江宏;周宏达;王树林
【作者单位】江苏大学机械工程学院,江苏镇江 212013;景德镇市产品质量监督检验所,江西景德镇333000;江苏大学机械工程学院,江苏镇江 212013;江苏大学机械工程学院,江苏镇江 212013
【正文语种】中文
【中图分类】TH16;TG65
【相关文献】
1.Capto C6主轴/刀柄接口扭转刚度特性 [J], 刘春春;王树林;沈春根;陈文华
2.KM刀柄制造标准分析及关键尺寸测量方法 [J], 周宏达;王树林;于永慧;王洋;肖坡
3.WALTER 瓦尔特推出带有Walter Capto^TM刀柄系统的Xtra·tec Insert Drill 可转位刀片钻头 [J],
4.液压式微量位移驱动器关键尺寸的确定 [J], 张兵
5.高速加工用Capto刀柄关键尺寸测量技术研究 [J], 张劲;王树林;史翔云;周益军因版权原因,仅展示原文概要,查看原文内容请购买。
新型CAPTO夹刀结构

瑞典Coromant Capto®界面专用 最新拉刀机构组件(适合高速强力主轴)1背景说明瑞典Sandvik Coromant 公司于1998 年开发出适用于 Coromant Capto 模块化刀把及刀具系统之专用主轴拉刀机构组件。
由于Coromant Capto 系统在车削、铣削、钻削的各式各样刀把及刀具上的优越模块化速换性能,拉刀机构性能及整体刚性,使得该系统特别适合应用于多功能的车铣复合机上。
1.1现行拉刀机构设计现行拉刀机构的设计,一般由拉刀夹爪,倍力器,碟型弹簧或螺旋弹簧组合而成 (见下图)。
由于近年来,市场对工具机除了要求性能的提升外,对机台外型尺寸也要求精巧,以适应日趋饱和的厂房面积及摆设问题。
在主轴设计上,也相对的要求在提升转速及扭力输出之外,主轴外径及长度也应予以适度的缩减。
2最新拉刀机构设计针对上述的对工具机要求瑞典Sandvik Coromant 公司特别推出全新的拉刀机构。
该设计中包含Coromant Capto 拉刀爪 (简称 : CC 拉刀爪),全新设计的倍力器机构来配合独步全球的氮气弹簧及。
CC 拉刀爪及全新的倍力器机构的组合也可以配合现有的碟型或螺旋弹簧使用。
2.1应用范围Coromant Capto 刀具接口系统配合此一全新设计的拉刀机构可以全方位应用在各型低转速或高转速的工具机上。
Coromant Capto 三角短锥界面 (简称 : CC 接口)的特性与平衡对称设计的拉刀机构,可以使得此一组合应用在高速加工机时,大幅减轻高速主轴组立时的动平衡的调整工作。
2.2拉刀机构组件2.3 组合种类清单C 4-SP-CS-11 C 5-SP-CS-11C 6-SP-CS-11 C 8-SP-CS-11CC 拉刀爪 + 倍力器 + 氮气弹簧C 4-SP-CS-12 C 5-SP-CS-12 C 6-SP-CS-12 C 8-SP-CS-12CC 界面套环CC 拉刀爪 + 倍力器 + 氮气弹簧C 4-SP-CS-01 C 5-SP-CS-01 C 6-SP-CS-01 C 8-SP-CS-01CC 拉刀爪 + 倍力器 ( + 自配弹簧)C 4-SP-CS-02 C 5-SP-CS-02 C 6-SP-CS-02 C 8-SP-CS-02CC 界面套环CC 拉刀爪 + 倍力器 ( + 自配弹簧)倍力器53 技术数据Coromant Capto ® 拉刀机构主要尺寸及拉刀力/退刀力*) 主轴端面至尾端联打刀结处。
刀柄种类规格

加工中心的主轴锥孔通常分为两大类,即锥度为7:24的通用系统和1:10的HSK真空系统。
7:24锥度的通用刀柄锥度为7:24的通用刀柄通常有五种标准和规格,即NT(传统型)、DIN 69871(德国标准)、IS0 7388/1 (国际标准)、MAS BT(日本标准)以及ANSI/ASME(美国标准)。
NT型刀柄德国标准为DIN 2080,是在传统型机床上通过拉杆将刀柄拉紧,国内也称为ST;其它四种刀柄均是在加工中心上通过刀柄尾部的拉钉将刀柄拉紧。
目前国内使用最多的是DIN 69871型(即JT)和MAS BT 型两种刀柄。
DIN 69871型的刀柄可以安装在DIN 69871型和ANSI/ASME主轴锥孔的机床上, IS0 7388/1型的刀柄可以安装在DIN 69871型、IS0 7388/1 和ANSI/ASME主轴锥孔的机床上,所以就通用性而言,IS0 7388/1型的刀柄是最好的。
(1)DIN 2080型(简称 NT或ST)DIN 2080是德国标准,即国际标准ISO 2583 ,是我们通常所说NT型刀柄,不能用机床的机械手装刀而用手动装刀。
(2) DIN 69871 型(简称JT、 DIN、DAT或DV)DIN 69871 型分两种,即DIN 69871 A/AD型和 DIN 69871 B型,前者是中心内冷,后者是法兰盘内冷,其它尺寸相同。
(3) ISO 7388/1 型(简称 IV或IT)其刀柄安装尺寸与DIN 69871 型没有区别,但由于ISO 7388/1 型刀柄的D4值小于DIN 69871 型刀柄的D4值,所以将ISO 7388/1型刀柄安装在DIN 69871型锥孔的机床上是没有问题的,但将DIN 69871 型刀柄安装在ISO 7388/1型机床上则有可能会发生干涉。
(4) MAS BT 型(简称 BT)BT型是日本标准,安装尺寸与 DIN 69871、IS0 7388/1 及ANSI 完全不同,不能换用。
刀柄部分的结构图例PPT课件

14
/April 20, 2006
第14页/共18页
刀柄系统 – 刀具夹持
液压夹头CoroGrip
F
15
/April 20, 2006
第15页/共18页
刀柄系统 – 刀具夹持
可调式刀柄
16
/April 20, 2006
第16页/共18页
刀柄系统 – 组装工具
•用于装配和拆卸主刀 柄的装卸台391.200 •模块化刀具的组装工 具
第11页/共18页
刀柄系统 – 模块化刀具
Modular
Solid
/April 20, 2006
Total: 4+2+30+10 = 46 items
12
第12页/共18页
Total 480 items
刀柄系统 – 刀具夹持
液压夹头CoroGrip
13
/April 20, 2006
第13页/共18页
刀柄系统 – 机床主轴的接口形式
HSK接口
Taper:1/10 Angle: 2°51 47
3
/April 20, 2006
第3页/共18页
刀柄系统 – 机床主轴的接口形式
Capto®接口
20000-40000转/分钟 的高速度
车刀和回转刀具共 用的主轴接口形式
4
/April 20, 2006
第4页/共18页
刀柄系统 – 机床主轴的接口形式
Capto®接口
+/- 0.002mm
5
/April 20, 2006
第5页/共18页
刀柄系统 – 夹紧方式
• 利用差动螺钉和一对 锯齿形夹爪将刀柄/刀 具夹紧。
刀柄

标准目前主要标准有BT、SK、CAPTO、BBT、HSK等几种规格的主轴型号。
BT,BBT,均为日本标准,现也是普遍使用的一种标准。
SK(DIN6987)德国标准传统刀柄,有ER型,强力型,侧固型,平面铣刀型,钻夹头,莫氏锥柄现代有液压刀柄,热胀刀柄,PG(冷压)型。
HSK刀柄简介在高速切削加工已成为机械加工制造技术重要的环节。
传统的BT刀具系统的加工性能已难以满足高速切削的要求。
目前高速切削应用较广泛的有德国的HSK (德文Hohl Shaft Kegel缩写)刀具系统、美国的KM 刀具系统、日本的NC5、BIG-PLUS刀具系统等以上皆属于两面拘束刀柄。
而刀具系统能在高速下进行切削加工,应满足以下基本条件:1. 较高的系统精度系统精度包括系统定位夹持精度和刀具重复定位精度,前者指刀具与刀柄、刀柄与机床主轴的连接精度;后者指每次换刀后刀具系统精度的一致性。
刀具系统具有较高的系统精度,才能保证高速加工条件下刀具系统应有的静态和动态稳定性。
2. 较高的系统刚度刀具系统的静、动刚度是影响加工精度及切削性能的重要因素。
刀具系统刚度不足会导致刀具系统振动,从而降低加工精度,并加剧刀具的磨损,降低刀具的使用寿命。
3. 较好的动平衡性高速切削加工条件下,微小质量的不平衡都会造成巨大的离心力,在加工过程中引起机床的急剧振动。
因此,高速刀具系统的动平衡非常重要。
二、HSK工具系统标准的制订从1987年开始,由德国阿亨工业大学机床实验室以及一些工具制造厂、机床制造厂、用户企业等30多个单位成立了专题工作组,在M.Weck 教授领导下开始了新型工具系统的研究开发工作。
经过第一轮研究,工作组于1990年7月向德国工业标准组织提交了「自动换刀空心柄」标准建议。
德国于1991年7月公布了HSK刀具系统的DIN标准草案,并向国际标准化组织建议制定相关ISO标准。
1992年5月,国际标准化组织ISOT/TC29(工具技术委员会)决定暂不制订自动换刀空心柄的ISO标准。
KM刀具系统

KM刀具系统KM Tooling SystemsKM刀具系统QuickKMQuickKMKM 模块式刀具系统 HSK 刀柄Erickson 刀柄和夹头加工中心刀具机械附件综合产品在车床和加工中心上使用的产品Lathe and Machining Center ProductsQuick KM KM Manufacturing Locations Kingswinford, England Nabburg, GermanyDetroit, MI +改革者+刀具制造商+供应商+提高生产力的合作伙伴Kennametal 公司QuickKM材料材料的使用是肯纳公司工艺技术的核心通过“全球性”材料规范认证材料通过热处理(不是表面硬化) SAE 4340H13Hardness 48 -52 HRcQuick KMQuickKMé 3 个面接触é灵活和通用地夹持设计é高刚性和高精度é宽的尺寸范围和多种形式é针对车/镗/钻/铣设计é有经受高切削负载的能力KM 和其它产品比较The KM 锥面BESTQuickKM三个有效地接触面通过机械放大产生3倍到7倍地锁紧力密封结合(橡胶O型环) 以防止内部零件受污染The KM 结合方式QuickKM0,25 mm (.010“)KM -锁紧过程1) 未锁紧没有接触2) 未锁紧3) 锁紧QuickKM面和锥面上2点接触换刀V 型槽定位孔标准直径1:10锥度球型锁紧孔(锥部两侧)中心内冷孔高性能和自动平衡夹头KM Taper径向驱动槽(两侧相等的宽和深)QuickKM旋转刀具9铣削(circular)9钻削9镗孔,双头镗9精镗9铰9浮动夹头9攻丝旋转工件9车削9切槽9切断9镗孔9钻头机床配件:9带KM 形式的主轴KM -通用型的应用QuickKM端面-锥面接触系统硬度和刚性主要依靠:1) 标准直径的过盈量2) 后拉力后拉力Interference between gage diameters实际QuickKMTest conducted by Kennametal in Latrobe, PA在切向受力下的偏移量13在切向受力下的偏移量QuickKMQuickKMTest conducted by Kennametal in Latrobe, PA在切向受力下的偏移量和屈服扭矩在切向受力下的偏移量和屈服扭矩QuickKMQuickKMTest conducted by Kennametal -Hertel in Furth, Germany在切向受力下的偏移量QuickKMTest conducted by Kennametal -Hertel in Furth, Germany在切向受力下的偏移量QuickKMKM 3240506380100Maximum Tangential Load at std. F & C 7,1 KN (1,600 LBF)12,0 KN (2,700 LBF)22,2 KN (5,000 LBF)35,6 KN (8,000 LBF)53,4 KN (12,000 LBF)66,7 KN (15,000 LBF)System Torque Capacity 155 Nm (115 ft lbs)325 Nm (240 ft lbs)780 Nm (575 ft lbs)1530 Nm (1,130 ft lbs)2,800 Nm (2,100 ft lbs)4,200 Nm (3,100 ft lbs)Capto C5C6C817 KN (3,800 LBF)32 KN (7,200 LBF)54 KN (12,200 LBF)Quick KM。
比BT好在哪?HSK、BBT、C、KM的刀柄结构对比

比BT好在哪?HSK、BBT、C、KM的刀柄结构对比这是夹具侠(jiajoin)发布的第 1082 篇技术文章如今高速切削加工已成为机械加工制造技术重要的环节,传统BT 刀具系统的加工性能已难以满足高速切削的要求。
而现在我们常说的主轴两面定位系统,就是通过锥面和端面同时实现定位的主轴系统。
两面定位系统的比较早在40多年以前,大家就已经发现主轴的鼻端与刀具端面贴合时可以增加刚性,然而限于早期加工技术并无法做到刀具与主轴端面结合时的精度。
BIG-PLUS的主轴系统利用量规与其它设备,来控制主轴端面与刀具贴合面的尺寸,来达到两面拘束的目的。
BIG-PLUS的主轴与刀具是可以互换的,传统的主轴可以使用BIG-PLUS刀具,而BIG-PLUS的主轴可以使用传统刀具。
传统主轴、BIG-PLUS主轴与刀具的结合示意图如下,简单的说,传统刀把与主轴端面间是有间隙的,而BIG-PLUS则是利用量规等设备来将间隙消除,使刀把与主轴端面贴合,达到两面拘束的目的。
市面上的两面定位系统有大昭和的BBT系统,德国的HSK接口,山特的可乐满C接口以及美国的KM接口。
BBT和HSK接口主要用于加工中心设备,可乐满C接口主要用于车铣复合设备,而KM接口在国内主要用在某些专机上多一些。
BIG-PLUS的原理主轴与刀具的锥面与端面要做到两面拘束势必要将端面的间隙归零,然而以加工技术而言几乎是不可能。
因此,BIG-PLUS系统使用弹性变形的方式来达到两面拘束的目的。
如图所示,在拉刀前,主轴与刀具仅有锥面接触,在主轴与刀具端面留有一定的间隙;而在拉刀时,刀具受轴向力,主轴内孔受力扩张产生弹性变形,使主轴与刀具的端面间隙消除进而贴合,达到两面拘束目的。
由于BIG-PLUS系统是靠弹性变形达到两面拘束,因此刀具于拉刀时所产生的轴向位移量就显得非常重要。
选择BBT还是HSK刀柄?从下图可以看出受本身结构限制,与HSK刀柄相比BBT基础柄可以做的更短,刃具插入量更大,从而使刃具伸出量变短。
HSK和BT刀柄种类规格
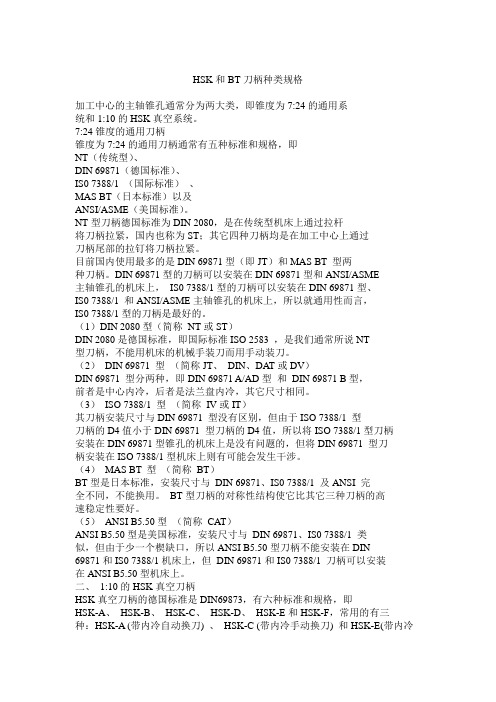
HSK和BT刀柄种类规格加工中心的主轴锥孔通常分为两大类,即锥度为7:24的通用系统和1:10的HSK真空系统。
7:24锥度的通用刀柄锥度为7:24的通用刀柄通常有五种标准和规格,即NT(传统型)、DIN 69871(德国标准)、IS0 7388/1 (国际标准)、MAS BT(日本标准)以及ANSI/ASME(美国标准)。
NT型刀柄德国标准为DIN 2080,是在传统型机床上通过拉杆将刀柄拉紧,国内也称为ST;其它四种刀柄均是在加工中心上通过刀柄尾部的拉钉将刀柄拉紧。
目前国内使用最多的是DIN 69871型(即JT)和MAS BT 型两种刀柄。
DIN 69871型的刀柄可以安装在DIN 69871型和ANSI/ASME主轴锥孔的机床上,IS0 7388/1型的刀柄可以安装在DIN 69871型、IS0 7388/1 和ANSI/ASME主轴锥孔的机床上,所以就通用性而言,IS0 7388/1型的刀柄是最好的。
(1)DIN 2080型(简称NT或ST)DIN 2080是德国标准,即国际标准ISO 2583 ,是我们通常所说NT型刀柄,不能用机床的机械手装刀而用手动装刀。
(2)DIN 69871 型(简称JT、DIN、DAT或DV)DIN 69871 型分两种,即DIN 69871 A/AD型和DIN 69871 B型,前者是中心内冷,后者是法兰盘内冷,其它尺寸相同。
(3)ISO 7388/1 型(简称IV或IT)其刀柄安装尺寸与DIN 69871 型没有区别,但由于ISO 7388/1 型刀柄的D4值小于DIN 69871 型刀柄的D4值,所以将ISO 7388/1型刀柄安装在DIN 69871型锥孔的机床上是没有问题的,但将DIN 69871 型刀柄安装在ISO 7388/1型机床上则有可能会发生干涉。
(4)MAS BT 型(简称BT)BT型是日本标准,安装尺寸与DIN 69871、IS0 7388/1 及ANSI 完全不同,不能换用。
刀柄尺寸

CNC刀柄标准加工中心的主轴锥孔通常分为两大类,即锥度为7:24的通用系统和1:10的HSK真空系统。
7:24锥度的通用刀柄锥度为7:24的通用刀柄通常有五种标准和规格,即NT(传统型)、DIN 69871(德国标准)、IS0 7388/1 (国际标准)、MAS BT(日本标准)以及ANSI/ASME(美国标准)。
NT型刀柄德国标准为DIN 2080,是在传统型机床上通过拉杆将刀柄拉紧,国内也称为ST;其它四种刀柄均是在加工中心上通过刀柄尾部的拉钉将刀柄拉紧。
目前国内使用最多的是DIN 69871型(即JT)和MAS BT 型两种刀柄。
DIN 69871型的刀柄可以安装在DIN 69871型和ANSI/ASME主轴锥孔的机床上, IS0 7388/1型的刀柄可以安装在DIN 69871型、IS0 7388/1 和ANSI/ASME主轴锥孔的机床上,所以就通用性而言,IS0 7388/1型的刀柄是最好的。
(1)DIN 2080型(简称 NT或ST)DIN 2080是德国标准,即国际标准ISO 2583 ,是我们通常所说NT型刀柄,不能用机床的机械手装刀而用手动装刀。
(2) DIN 69871 型(简称JT、 DIN、DAT或DV)DIN 69871 型分两种,即DIN 69871 A/AD型和DIN 69871 B型,前者是中心内冷,后者是法兰盘内冷,其它尺寸相同。
(3) ISO 7388/1 型(简称 IV或IT)其刀柄安装尺寸与DIN 69871 型没有区别,但由于ISO 7388/1 型刀柄的D4值小于DIN 69871 型刀柄的D4值,所以将ISO 7388/1型刀柄安装在DIN 69871型锥孔的机床上是没有问题的,但将DIN 69871 型刀柄安装在ISO 7388/1型机床上则有可能会发生干涉。
(4) MAS BT 型(简称 BT)BT型是日本标准,安装尺寸与 DIN 69871、IS0 7388/1 及ANSI 完全不同,不能换用。
- 1、下载文档前请自行甄别文档内容的完整性,平台不提供额外的编辑、内容补充、找答案等附加服务。
- 2、"仅部分预览"的文档,不可在线预览部分如存在完整性等问题,可反馈申请退款(可完整预览的文档不适用该条件!)。
- 3、如文档侵犯您的权益,请联系客服反馈,我们会尽快为您处理(人工客服工作时间:9:00-18:30)。
摘要:高速切削技术是近十多年来发展最为迅速的先进制造技术之一。
文章在论述高速切削技术发展历程和特点的基础上,着重研究了高速切削技术中的刀柄结构,包括HSK、KM及CAPTO,并比较了常用的BT刀柄与HKS、KM刀柄的拉紧特性。
对高速旋转所带来的特殊的动平衡问题及其执行标准也作了叙述。
1、概述
高速切削是一个相对概念,并且随着时代的进步而不断变化。
一般认为高速切削或超高速切削的速度为普通切削加工的5~10倍。
可以从不同的角度对切削速度进行划分,如从加工工艺的角度看,高速切削加工范围为:车削700~7000m/min;铣削300~6000m/min;钻削200~1100m/min;磨削150~360m/min。
也可以根据被加工材料来确定高速切削的范围,如加工钢材达到380m/min以上、铸铁700m/min以上、铜材1000m/min以上、铝材1100m/min以上。
也可以根据主轴转速、功率、锥孔大小、和平衡标准来划分,如按主轴的Dn值划分,高速主轴的Dn值一般为500000~2000000;对于加工中心,可按主轴锥孔的大小来划分:50号锥——10000~20000r/min;40号锥——20000~40000r/min;30号锥——25000~40000r/min;HSK 锥——20000~40000r/min;KM锥——35000r/min以上。
而根据ISO—1940,高速主轴的转速至少要超过8000r/min。
1978年CIRP切削委员会将高速切削定为500~7500 m/min[1][2][3]。
研究表明:随着切削速度的提高,切削力会降低15~30%以上,切削热量大多被切屑带走,加工表面质量可提高1~2级,生产效率的提高,可降低制造成本20%~40%。
所以高速切削意义不仅仅是得到较高的表面切削质量[2]。
国外对高速切削技术的研究比较早,可以追溯到20世纪60年代。
目前已应用于航空、航天、汽车、模具等多种工业中的钢、铸铁及其合金、铝、镁合金、超级合金(镍基、铬基、铁基和钛基合金)及碳素纤维增强塑料等复合材料的加工,其中以加工铸铁和铝合金最为普遍。
加工钢和铸铁及其合金可达到500~1500 m/min,加工铝及其合金可达到3000~4000 m/min[3]。
国家自然科学基金项目(50575150)、北京市教委项目(05001011200401)
我国在高速切削领域方面的研究起步较晚,20世纪80年代才开始研究高速硬切削。
刀具以高速钢、硬质合金为主,切削速度大多在100~200 m/min,高速钢在40 m/min以内。
切削水平和加工效率都比较低。
近年来,虽然对高速切削技术已有比较深的认识,进口的部分数控机床和加工中心中也能达到高速切削加工的要求,但由于刀具等原因,高速切削技术应用也较少。
目前主要在模具、汽车、航空、航天工业应用高速切削技术稍多,一般采用进口刀具,以加工铸铁和铝合金为主[3]。
高速切削技术主要分为两方面,一方面是高速切削刀具技术,包括刀具材料、刀柄和刀夹系统、刀具动平衡技术、高速切削数据库技术、检测与监控系统等;另一方面是高速数控机床技术,包括机床整机结构的静动热态特性、电主轴、直线电机进给系统、数控与伺服系统的高速及高加速度性能、轴承润滑系统、刀具冷却系统等。
本文重点谈谈高速切削技术中的刀柄结构。
2、典型的刀柄结构及其特性
一般切削最常用的是BT刀柄,而高速切削用得比较多的是HSK刀柄。
BT刀柄
BT刀柄的锥度为7:24,转速在10,000r/min左右时,刀柄-主轴系统还不会出现明显的变形,但当主轴从10,000 r/min升高到40,000 r/min时,由于离心力的作用,主轴系统的端部将出现较大变形,其径跳由0.2 m左右增加到2.8 m左右。
刀柄与主轴锥孔间将出现明显的间隙(见图1),严重影响刀具的切削特性,因此BT刀柄一般不能用于高速切削[3]。
图1 高速下离心力造成BT刀柄-主轴系统变形
HSK刀柄
HSK刀柄锥的结构形式与常用的BT刀柄不同,它是一种新型的高速锥型刀柄,采用锥面与端面双重定位的方式(见图2),在足够大的拉紧力作用下,HSK 1:10空心工具锥柄和主轴1:10锥孔之间在整个锥面和支承平面上产生摩擦,提供封闭结构的径向定位。
平面夹紧定位防止刀柄的轴向窜动。
HSK短锥柄部长度短(约为标准BT锥柄长度的1/2)、重量轻,因此换刀时间短。
在整个速度范围内,HSK锥柄比BT(7:24)具有更大的动、静径向刚度和良好的切削性能。
分为A、B、C、D、E、F型(见图3)。
国内采用DIN6989b-1中的A型和C型标准,如HSK50A、HSK63A、HSK100A等。
HSK50和HSK63刀柄的主轴转速可达25,000 r/min,HSK100刀柄可达12,000r/min,精密平衡后的HSK刀柄可达40,000r/min。
随着转速增加,径向刚度将有所降低,见图4。
图2 HSK的双重定位结构
图3 HSK结构形式
图4 HSK与BT锥柄主轴转速与径向刚度关系比较
KM刀柄
KM刀柄是1987年美国Kennametal公司与德国Widia公司联合研制的1:10短锥空心刀柄(见图5),其长度仅为标准7:24锥柄长度的1/3。
由于配合锥度比较短,且刀柄设计成中空结构,在拉杆轴向拉力
作用下,短锥可径向收缩,所以有效地解决了端面与锥面同时定位而产生的干涉问题。
图5 KM刀柄的结构
研究表明:与BT刀柄相比,HSK刀柄与KM刀柄具有更加优越的静刚度和动刚度,其中由于KM刀柄的拉紧力与锁紧力明显大于HSK刀柄,所以KM刀柄的性能最优。
它们的结构及性能比较见表1。
结构及性能比较见表1。