电石生产工艺图示解
电石生产工艺流程简介
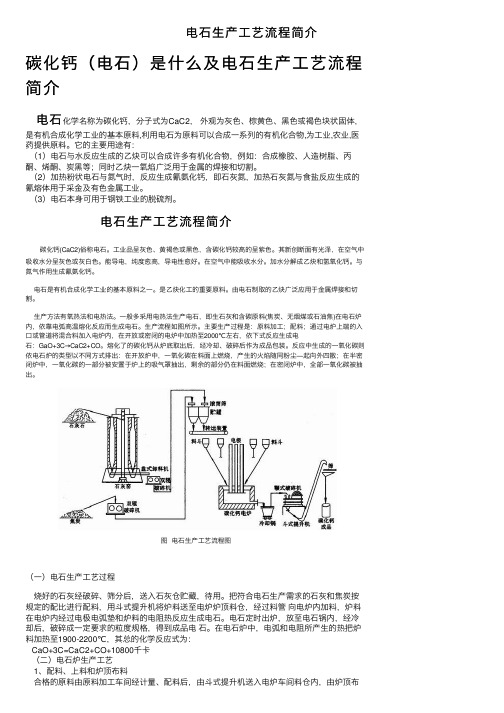
电⽯⽣产⼯艺流程简介碳化钙(电⽯)是什么及电⽯⽣产⼯艺流程简介电⽯化学名称为碳化钙,分⼦式为CaC2,外观为灰⾊、棕黄⾊、⿊⾊或褐⾊块状固体,是有机合成化学⼯业的基本原料,利⽤电⽯为原料可以合成⼀系列的有机化合物,为⼯业,农业,医药提供原料。
它的主要⽤途有:(1)电⽯与⽔反应⽣成的⼄炔可以合成许多有机化合物,例如:合成橡胶、⼈造树脂、丙酮、烯酮、炭⿊等;同时⼄炔⼀氧焰⼴泛⽤于⾦属的焊接和切割。
(2)加热粉状电⽯与氮⽓时,反应⽣成氰氨化钙,即⽯灰氮,加热⽯灰氮与⾷盐反应⽣成的氰熔体⽤于采⾦及有⾊⾦属⼯业。
(3)电⽯本⾝可⽤于钢铁⼯业的脱硫剂。
电⽯⽣产⼯艺流程简介碳化钙(CaC2)俗称电⽯。
⼯业品呈灰⾊、黄褐⾊或⿊⾊,含碳化钙较⾼的呈紫⾊。
其新创断⾯有光泽,在空⽓中吸收⽔分呈灰⾊或灰⽩⾊。
能导电,纯度愈⾼,导电性愈好。
在空⽓中能吸收⽔分。
加⽔分解成⼄炔和氢氧化钙。
与氮⽓作⽤⽣成氰氨化钙。
电⽯是有机合成化学⼯业的基本原料之⼀。
是⼄炔化⼯的重要原料。
由电⽯制取的⼄炔⼴泛应⽤于⾦属焊接和切割。
⽣产⽅法有氧热法和电热法。
⼀般多采⽤电热法⽣产电⽯,即⽣⽯灰和含碳原料(焦炭、⽆烟煤或⽯油焦)在电⽯炉内,依靠电弧⾼温熔化反应⽽⽣成电⽯。
⽣产流程如图所⽰。
主要⽣产过程是:原料加⼯;配料;通过电炉上端的⼊⼝或管道将混合料加⼊电炉内,在开放或密闭的电炉中加热⾄2000℃左右,依下式反应⽣成电⽯:GaO+3C→CaC2+CO。
熔化了的碳化钙从炉底取出后,经冷却、破碎后作为成品包装。
反应中⽣成的⼀氧化碳则依电⽯炉的类型以不同⽅式排出:在开放炉中,⼀氧化碳在料⾯上燃烧,产⽣的⽕焰随同粉尘—起向外四散;在半密闭炉中,⼀氧化碳的⼀部分被安置于炉上的吸⽓罩抽出,剩余的部分仍在料⾯燃烧;在密闭炉中,全部⼀氧化碳被抽出。
图电⽯⽣产⼯艺流程图(⼀)电⽯⽣产⼯艺过程烧好的⽯灰经破碎、筛分后,送⼊⽯灰仓贮藏,待⽤。
把符合电⽯⽣产需求的⽯灰和焦炭按规定的配⽐进⾏配料,⽤⽃式提升机将炉料送⾄电炉炉顶料仓,经过料管向电炉内加料,炉料在电炉内经过电极电弧垫和炉料的电阻热反应⽣成电⽯。
电石生产培训资料 ppt课件
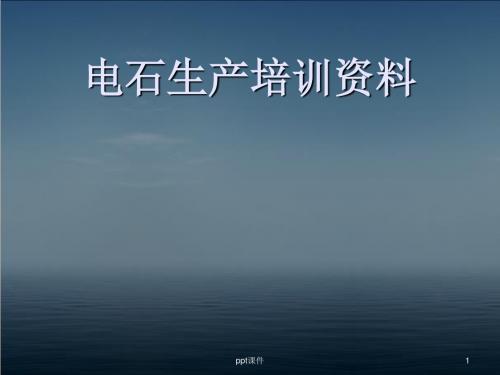
理的抽气系统以及其他技术改进,可使电炉的 维护管理费用降低20%,电能单耗降低20%,焦 炭单耗降低8%,电极糊降低20%该公司在克纳 普沙克还改建了两座有功功率为27000千瓦的半 密闭炉和两座有功功率为22000千瓦的开放炉。 据该公司断定,生产能力的提高以及容量为 47000千伏安(有功功率为42000千瓦)的两座 新型电石炉在生产中积累的经验,可作出如下
ppt课件
18
三、我国电石生产情况
我国在解放前几乎没有电石工业,只是在某些采矿场建有几度小型电 石炉,容量为300千伏安左右,生产的电石主要用于点灯。与国外电 石工业相比,相差约半个世纪。
解放后,1948年在吉林建成了第一座容量为1750千伏安的开放炉,年生 产能力为3000吨。抗美援朝战争爆发后,1951年在吉林建成第二座电石 炉,容量与第一座相同。两年后,为适应国家经济建设的需要,又将 这两座电石炉由1750千伏安改成3000千伏安和6000千安。1956年河北 省下花园建成一座容量为3000千伏安的电石炉,1957年又从苏联引进 一座容40000千伏安的长方形三相半密闭炉,在吉林建成投产。这时 候全国电石总产量接近10万吨。
(4)通过电子计算机监控所有冷却水的变化。
(5)通过电子计算机监视和预测电极糊软化烧结 情况。
(6)通过电子计算机可以测量,控制电极工作长 度,并保持电石炉在恒定功率运行。
电石生产工艺
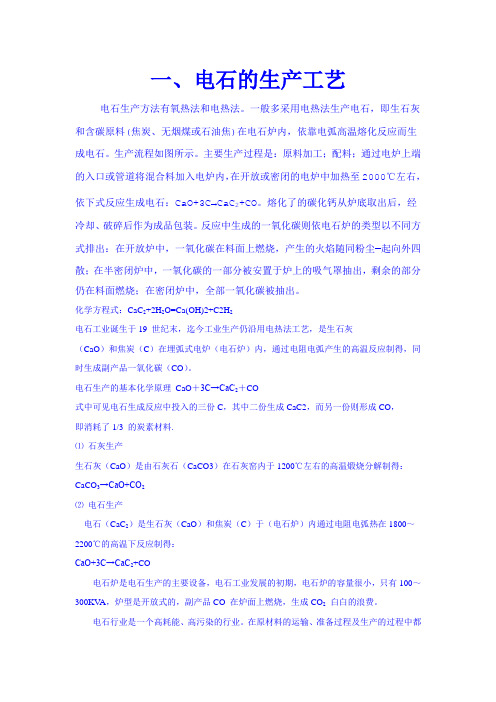
一、电石的生产工艺电石生产方法有氧热法和电热法。
一般多采用电热法生产电石,即生石灰和含碳原料(焦炭、无烟煤或石油焦)在电石炉内,依靠电弧高温熔化反应而生成电石。
生产流程如图所示。
主要生产过程是:原料加工;配料;通过电炉上端的入口或管道将混合料加入电炉内,在开放或密闭的电炉中加热至2000℃左右,依下式反应生成电石:CaO+3C→CaC2+CO。
熔化了的碳化钙从炉底取出后,经冷却、破碎后作为成品包装。
反应中生成的一氧化碳则依电石炉的类型以不同方式排出:在开放炉中,一氧化碳在料面上燃烧,产生的火焰随同粉尘—起向外四散;在半密闭炉中,一氧化碳的一部分被安置于炉上的吸气罩抽出,剩余的部分仍在料面燃烧;在密闭炉中,全部一氧化碳被抽出。
化学方程式:CaC2+2H2O=Ca(OH)2+C2H2电石工业诞生于19 世纪末,迄今工业生产仍沿用电热法工艺,是生石灰(CaO)和焦炭(C)在埋弧式电炉(电石炉)内,通过电阻电弧产生的高温反应制得,同时生成副产品一氧化碳(CO)。
电石生产的基本化学原理CaO+3C→CaC2+CO式中可见电石生成反应中投入的三份C,其中二份生成CaC2,而另一份则形成CO,即消耗了1/3 的炭素材料.⑴石灰生产生石灰(CaO)是由石灰石(CaCO3)在石灰窑内于1200℃左右的高温煅烧分解制得:CaCO3→CaO+CO2⑵电石生产电石(CaC2)是生石灰(CaO)和焦炭(C)于(电石炉)内通过电阻电弧热在1800~2200℃的高温下反应制得:CaO+3C→CaC2+CO电石炉是电石生产的主要设备,电石工业发展的初期,电石炉的容量很小,只有100~300KV A,炉型是开放式的,副产品CO 在炉面上燃烧,生成CO2白白的浪费。
电石行业是一个高耗能、高污染的行业。
在原材料的运输、准备过程及生产的过程中都有污染物生成。
现在这个行业国家规定比较严格,另外一氧化碳的回收也取得了很好的效果.电石生产方法主要有氧热法和电热法。
工艺流程图及工艺流程叙述
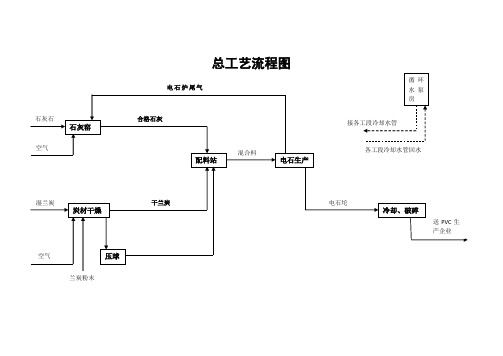
总工艺流程图碳材干燥工艺流程石灰生产工艺流程电石生产工艺流程图工艺流程经过炭材干燥工序后的兰炭与通过石灰窑石灰石烧制产生的氧化钙在电石炉内反应生成碳化钙,此过程发生的主要化学方程式为:具体工艺流程如下:(1)600t/d套筒窑工艺流程简述:①石灰石筛分系统主要是将合格粒度的石灰石进行筛分,去除5mm以下的。
将筛上物输送至窑前料仓。
②窑前料仓内装有雷达测位计用来探测仓内料位。
底部通向石灰窑的计量斗。
③上料系统当窑顶料位计指示窑内料时,仓下电振自动向计量斗内加料,达到设定值后,电振停止加料。
计量斗向小车内加料,到一定时间卷扬机自动启动,牵引小车沿斜桥到达窑顶后,通过窑顶受料装置将石灰石加入窑内。
套筒窑的装料由称量料斗、闸门、单斗提升机、密封闸板、旋转布料器、料钟及料位检测装置组成,窑顶旋转布料器、密封闸板、料钟由液压驱动。
④套筒窑主体物料经过窑内的预热带、上部逆流煅烧带、中部逆流煅烧带、下部并流煅烧带和冷却带,通过窑下出灰机进入窑底料仓,最后由振动出灰机排出窑外。
套筒窑主要由窑体、上料装置、出料装置、燃烧系统、换热器、喷射器(耐热铸钢)以及风机系统组成。
窑体由内外筒组成,内筒分上下两个独立部分,上部为上内筒,下部为下内筒。
上下内筒由双层结构形成圆柱形钢板箱,钢板箱内通入冷空气对内筒进行连续冷却防止其高温变形,预热的空气作为燃烧室的一次空气。
内筒与外筒同心布置,形成一个环形空间,石灰石就在环形区域内煅烧。
燃料的燃烧过程是通过烧嘴在燃烧室内进行的,燃烧室在窑体的中部并分上下两层,同一层均匀布置,上下两层错开布置。
燃烧产生的高温烟气通过拱下的空间进入石灰石料层。
石灰石在套筒窑内煅烧的一个显著特点是逆流煅烧与并流煅烧同时进行。
套筒窑外壳上分布的两层燃烧室将窑体分成两个逆流操作的煅烧带和一个并流操作的煅煅烧带。
上层燃烧室至下内套筒上端,以及上层燃烧室至下层燃烧室之间为两个逆流煅烧带,下层燃烧室至下内筒底部为顺流煅烧带。
电石生产工艺介绍
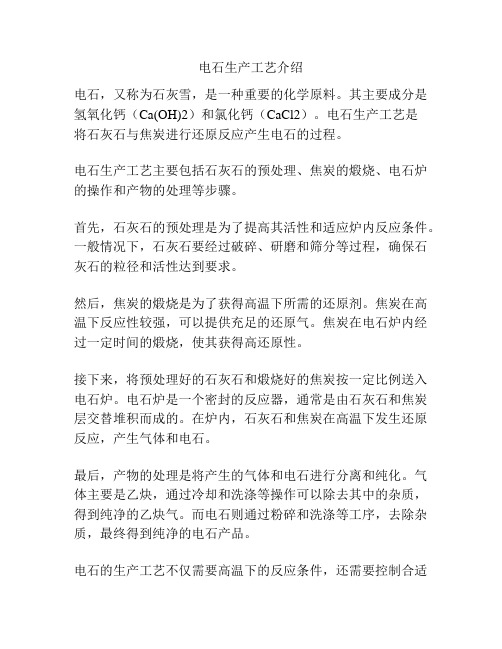
电石生产工艺介绍
电石,又称为石灰雪,是一种重要的化学原料。
其主要成分是氢氧化钙(Ca(OH)2)和氯化钙(CaCl2)。
电石生产工艺是
将石灰石与焦炭进行还原反应产生电石的过程。
电石生产工艺主要包括石灰石的预处理、焦炭的煅烧、电石炉的操作和产物的处理等步骤。
首先,石灰石的预处理是为了提高其活性和适应炉内反应条件。
一般情况下,石灰石要经过破碎、研磨和筛分等过程,确保石灰石的粒径和活性达到要求。
然后,焦炭的煅烧是为了获得高温下所需的还原剂。
焦炭在高温下反应性较强,可以提供充足的还原气。
焦炭在电石炉内经过一定时间的煅烧,使其获得高还原性。
接下来,将预处理好的石灰石和煅烧好的焦炭按一定比例送入电石炉。
电石炉是一个密封的反应器,通常是由石灰石和焦炭层交替堆积而成的。
在炉内,石灰石和焦炭在高温下发生还原反应,产生气体和电石。
最后,产物的处理是将产生的气体和电石进行分离和纯化。
气体主要是乙炔,通过冷却和洗涤等操作可以除去其中的杂质,得到纯净的乙炔气。
而电石则通过粉碎和洗涤等工序,去除杂质,最终得到纯净的电石产品。
电石的生产工艺不仅需要高温下的反应条件,还需要控制合适
的料层结构和反应时间等参数,以保证反应效果和产量。
同时,还需要对产生的气体和电石进行合理的处理,以达到环保要求和产品质量要求。
总体来说,电石生产工艺是一项复杂的过程,但其产生的乙炔气和电石等产物在化工、冶金、医药等领域具有重要的应用价值。
随着技术的发展,电石生产工艺也在不断改进和创新,以提高效率和产品质量,同时减少对环境的影响。
电石生产工艺图示解 ppt课件

3、工艺流程图
电石生产工艺图示解
17
② MgO:氧化镁对电石生产的危害较大,在熔融区内迅速还 原成金属镁。镁蒸汽上升过程中与CO和O2再次反应放出大量 的热量导致炉面发红、炉料结成壳阻碍炉气上升,严重时熔池
外壳被破坏,高温熔融液直接与耐火砖接触烧损耐火砖、电石 流道被堵塞。
反应式: MgO+C=Mg+电C石O生产↑-工艺1图1示6解千卡。
密闭电石炉生产工 (27000KVA)
电石生产工艺图示解
1
一、原料加工及输送流程
1、原料碳素
27000KVA密闭电石炉对焦炭的需求:
①颗粒度为5---25mm
②固定碳≥84%
③灰分≤15%
④ 挥发分≤1.9%
⑤水分≤1.0%
27000KVA密闭电石炉对兰炭的需求:
①颗粒度为5---25mm
③把电流通过电极导入炉内。
⑷出炉系统设备:
①炉嘴:用耐热铁或铸铁制成,安装在炉体的出炉口,炉 嘴最好能通水冷却,一则寿命长,再则方便于炉嘴堵住。
②烧穿装置:出炉时,必须用电弧去烧穿炉眼,利用电弧 烧穿炉眼的装置叫做烧穿装置。
三、炉气净化
1、炉气的性质及组成
电式石可生以成知反道应,:在电Ca石O炉+3内C=生C成aC电2+石CO的-同1时1.1,3千伴卡随。有从大反量应的 CO气体生成。在实际生产中,炉气的回收量约为400标准 米3/吨电石,炉气组成大致如下。
沉淀在炉底造成炉底升高。
※消化石灰的影响:
石灰生产过程中与空气接触一部分氧化钙生成氢氧化
钙,还有一部分与碳材中的水分结合形成氢氧化钙。氢氧
化钙输送当中容易裂碎,粉末氢氧化钙进入电石炉后分解
简叙电石生产工艺流程

电石生产工艺流程工艺流程简述电石生产将分为原料贮运、炭材干燥、电石生产、固态电石冷却、破碎、储存及电极壳制造几个工序。
(1)原料贮运电石生产主要原料焦炭、石灰、电极糊均由汽车运入厂区,经地中衡计量后贮存。
焦炭采用露天堆场和焦棚贮存,贮存周期按14天计,贮量为5000t;石灰采用地下料仓贮存,贮存周期按2天计,贮量为850t;电极糊贮存在电极糊厂房内,贮存量为8t。
焦炭干燥时由装载机送到受料斗中,经带式输送机及斗式提升机送到破碎筛分楼筛分,5-25mm通过带式输送机送至炭材干燥中间料仓。
0-5mm用小车送至电厂、空心电极或炭材干燥焦粉仓供热风炉使用;石灰需要时经带式输送机送至石灰破碎筛分楼进行破碎筛分。
破筛后8~45mm的石灰大倾角输送机送至配料站配料。
0~8mm的石灰送至石灰粉仓;电极糊经破碎机破碎后用专用小车运往电石厂房。
(2)炭材干燥合格粒度(≤25mm)焦炭由胶带输送机分别送入湿焦炭仓,再由电机振动给料机把焦炭送入回转干燥机进行烘干。
经过烘干后的物料由胶带输送机斗式提升机送往配料站,储存备用。
烘干炭材的热量由热风炉供给,达到400~600℃,炭材物料流入烘干机内,由回转干燥机转动,其内部栅格式扬板使物料均匀扬起,使热风与物料充分接触,热风把物料中水份带走,起到干燥物料作用。
热风炉以煤为燃料。
用过的热风低于160℃进入旋风除尘器、布袋除尘器净化排空,收集的炭材粉被送入炭材粉仓,再由汽车送至厂外。
除尘后的废气达标经烟囱排空。
在炭材干燥设备选用φ2.2×15m,能力为12t/h台的回转干燥机两台,每台每天生产1-2班,全年工作日为330天。
(3)电石生产合格粒度的石灰、焦炭由仓口分别经配料站块料仓下的振动给料机又经称重斗,按合适的重量配比,由振动给料机分三层经长胶带式输送机送至电石生产厂房,经短胶带式输送机分别送到电石炉的环形加料机进入炉料贮斗。
电炉炉料共有12个贮仓,贮仓中的混合物料经过向下延伸的料管及炉盖上的进料口靠重力连续进入炉中;装在电极糊盛斗内的破碎好的电极糊(100mm以下),经单轨吊从地面提升到各电极筒顶部倒入电极筒内。
电石车间工艺流程

电石车间工艺流程那咱就开始聊聊电石车间的工艺流程吧。
电石车间啊,那可是个很有趣的地方呢。
这电石的生产,得从原料说起。
原料主要就是石灰和焦炭啦。
石灰呢,它是那种白白的东西,在这个流程里可重要着呢。
焦炭呢,黑不溜秋的,看着不起眼,但是缺了它可不行。
再说说焦炭,焦炭得保证有足够的纯度和合适的粒度。
要是粒度太大了,混合的时候就不均匀;要是太小了呢,又可能会有其他的问题。
把石灰和焦炭混合均匀后,就会被送进电炉里面。
这电炉啊,就像是一个超级大的魔法炉。
一进去,就开始发生奇妙的反应啦。
在电炉里,通过电极通电,产生高温。
这个温度高得吓人呢,能让石灰和焦炭发生化学反应。
这时候,就开始生成电石啦。
在反应的过程中,还会有一些其他的情况发生。
比如说,会产生一些气体。
这些气体可不能随便放着不管,得把它们收集起来处理好。
要是不管这些气体,那可就对环境不友好啦。
生成的电石呢,它是块状的。
从电炉里出来之后,还要经过冷却这个环节。
就像刚出炉的热馒头得晾凉了才能吃一样,电石也得冷却好了才能进行下一步的操作。
冷却之后,就会对电石进行筛选,把那些不符合要求的杂质去掉。
这整个电石车间的工艺流程啊,就像是一场精心编排的舞蹈。
每个环节都得配合好,哪一个环节出了问题,都可能影响到最后的结果。
工人们在这个车间里就像指挥家一样,要时刻关注着每个步骤的进行情况。
要是发现哪里不对劲,就得赶紧调整。
你知道吗,这个电石的生产啊,还和好多其他的产业有关系呢。
比如说,它是一些化工产品的重要原料。
所以啊,电石车间的工艺流程顺利进行,对整个产业链都有着非常重要的意义。
在电石车间里,大家每天都忙忙碌碌的。
虽然工作有时候会有点累,但是看到那些合格的电石生产出来,就会觉得特别有成就感。
这就像是自己精心培育的小树苗,慢慢长大了一样,心里可高兴啦。
而且大家在车间里还会互相开玩笑,互相帮忙。
要是有新的工人来了,老工人就会像大哥大姐一样,耐心地给他们讲解工艺流程,告诉他们哪里要小心,哪里容易出问题。
电石生产工艺学

电石生产工艺学电石,又称重质碳酸钙,是工业中重要的化学原料之一。
电石可以通过焦炉焦炭和石灰石的高温反应得到,这个过程就是电石生产工艺。
电石生产工艺的步骤电石生产工艺可以分为以下5个步骤:1. 原料准备电石生产的原料是焦炉焦炭和石灰石。
焦炭一般是指经过高温热解后的煤炭,这个过程中煤炭中的杂质被除去,留下的是纯净的碳。
石灰石是一种由碳酸钙组成的矿物,常见于地下矿床中。
2. 炉料配制将焦炭和石灰石按一定比例混合成为炉料。
通常情况下,焦炭的质量占到炉料总质量的80%以上,而石灰石的质量则占到20%以下。
3. 反应加热将经过配制的炉料投入电石炉中,进行加热反应。
电石炉的工作原理是利用电极将电能转化为热能,然后传递到炉料中,使其达到高温。
这个过程中,炉料中的石灰石和焦炭会反应,产生出电石和二氧化碳。
4. 操作分离将反应后的炉料通过操作分离,得到电石、炉渣和废气。
炉渣是指反应后的石灰石和焦炭的残留物,废气则是指在反应过程中产生的二氧化碳和氮气等气体。
5. 成品包装将生产出来的电石进行包装和储存。
电石的形态大多为固体或块状,需要进行包装以便运输和储存。
电石生产工艺的优缺点电石生产工艺的优点是可以大规模生产,并且生产出的产品纯度高、品质稳定。
同时,电石还可以作为制造乙炔的重要原料,应用广泛。
但是电石生产工艺也有一些缺点。
首先,电石炉的能耗大,需要大量的电力供应。
其次,生产过程中需要使用大量的焦炭和石灰石等原材料,这对环境造成了一定程度的压力。
此外,电石生产过程中产生的废气还会对大气环境造成污染。
电石生产工艺的应用领域电石是一种重要的化工原料,可以广泛应用于以下领域:•生产乙炔:电石是乙炔的重要原料,可以通过化学反应制成乙炔气体,用于气焊、气割等工业领域;•生产氯化物:电石可以被用来制造氯化钙、氯化铁等氯化物,这些化合物被广泛应用于医药、制冷、硬化剂等领域;•生产其他化学品:除乙炔和氯化物外,电石还可以被用来生产氧化钙、钙基汽油清洁剂、染料和颜料等其他化学品。
电石生产工艺流程

电石生产工艺流程1.配料工艺流程图1.1方框流程图日料仓内的原料石灰和炭材按配比称量后按设定的下料时间落入皮运机混合均匀,由皮运机输送至环形加料机,然后再送入电石炉各料仓。
皮带起步开始的由1#、2#炉操作室配料工负责;B皮带起步开始的由3#、4#炉操作室配料工负责。
1A 2A 3A 4A 5A 1#炉(全长203.95m,皮带速度1.35m/s,从卸料到环型加料机时间为2分32秒)1A 2A 3A 5B 2#炉(全长193.75m,皮带速度1.35m/s,从卸料到环型加料机时间为2分24秒)1B 2B 6B 8A 3#炉(全长201.65m,皮带速度1.35m/s,从卸料到环型加料机时间为2分30秒)1B 2B 6B 7B 8B 4#炉(全长211.85m,皮带速度1.35m/s,从卸料到环型加料机时间为2分37秒)3B、4B、6A、7A备用1.3带控制点的流程图2.电石炉工艺流程图2.1方框流程图2.2流程简述石灰与炭材通过环形加料机进入电石炉各料仓,然后自然下落至电石炉内凭借电流通过电极产生的电弧热和电阻热在1800~2200℃的高温下反应而生成碳化钙,最后出炉。
2.3带控制点的流程图3.净化系统工艺流程图3.1方框流程图3.2流程简述电石炉产生的尾气在600℃~850℃,经过两级旋风空冷除尘器冷却,将气体冷却至200℃~260℃之间,同时将气体中大颗粒的粉尘捕集下来,温度控制在200℃~250℃之间主要原因是:一、防止焦油在低于200℃时析出并堵塞管路;二、防止温度过高,损坏过滤器及风机设备等,经过滤器除尘过的气体经风机增压送至气烧石灰窑使用。
电石炉尾气经旋风冷却器冷却后进入布袋过滤器过滤,过滤后的气体经净气风机输送至增压站,再经增压风机将气体增压至气烧石灰窑所需压力后进入气烧石灰窑燃烧,过剩气体可通过泄放烟囟排出。
经旋风空冷除尘器滤下的粉尘和布袋过滤器同滤下的粉尘由密封式链板机输送至粉尘总仓。
电石生产工艺PPT学习教案

R2O3(三氧化物) ≤2
P
≤0.01
S
≤0.04
生、过烧总量(%) <5%
粒度(mm):
10-50
第14页/共55页
粒 度 : 3~ 25mm; 粒 度合 格率≥ 90%
灰分
≤14.0%
挥发分
≤2.0%
水
≤1.0
硫
≤0.5%
磷
≤0.04%
焦 末 含 量 ≤5%
冶金焦
第15页/共55页
兰碳
成 份 ( 重 量 %)
的密度与其碳化钙的含量关系如下表。(品 级越低,质量越大)
CaC2含量% 90
密度g/cm3 2.24
80
70
60
50
40
30
2.32 2.40 2.50 2.58 2.66 2.74
第4页/共55页
c、熔点 电石的熔点随电石中碳化钙含量的改变而改变,纯碳化
钙的熔点为2300℃。碳化钙的含量在69%的混合物的熔 点最低,为1750℃。碳化钙的含量继续减少时,熔点反 而升高,后降到1800℃,此时混合物中碳化钙含量为35.6 %。在此二个最低熔点(1750~1800℃)之间有一个最 大值1980℃,它相当于含碳化钙52.5%的混合物。随着碳 化钙含量继续减少(即低于35.6%)混合物的熔点又升高。 见下图。
工艺流程简图:
电 电石炉尾气进行石灰生产 机
壳 制 造
石灰石 石料 炭 材 烘干后炭材 干燥
空冷 分却 空循 压环
水
第12页/共55页
冷却 车间 成品电石
第三节:电石生产所需原料
第13页/共55页
1.石灰
成份(重量%)
CaO
≥92
电石的生产工艺
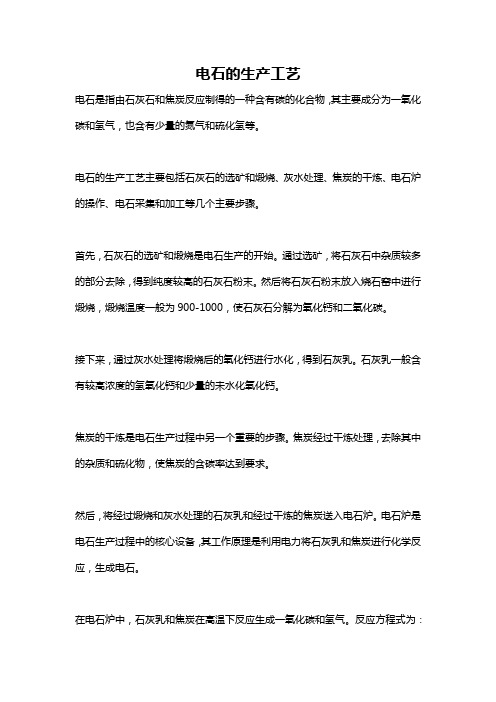
电石的生产工艺电石是指由石灰石和焦炭反应制得的一种含有碳的化合物,其主要成分为一氧化碳和氢气,也含有少量的氮气和硫化氢等。
电石的生产工艺主要包括石灰石的选矿和煅烧、灰水处理、焦炭的干炼、电石炉的操作、电石采集和加工等几个主要步骤。
首先,石灰石的选矿和煅烧是电石生产的开始。
通过选矿,将石灰石中杂质较多的部分去除,得到纯度较高的石灰石粉末。
然后将石灰石粉末放入烧石窑中进行煅烧,煅烧温度一般为900-1000,使石灰石分解为氧化钙和二氧化碳。
接下来,通过灰水处理将煅烧后的氧化钙进行水化,得到石灰乳。
石灰乳一般含有较高浓度的氢氧化钙和少量的未水化氧化钙。
焦炭的干炼是电石生产过程中另一个重要的步骤。
焦炭经过干炼处理,去除其中的杂质和硫化物,使焦炭的含碳率达到要求。
然后,将经过煅烧和灰水处理的石灰乳和经过干炼的焦炭送入电石炉。
电石炉是电石生产过程中的核心设备,其工作原理是利用电力将石灰乳和焦炭进行化学反应,生成电石。
在电石炉中,石灰乳和焦炭在高温下反应生成一氧化碳和氢气。
反应方程式为:CaO + 3C →CaC2 + CO。
其中,CaC2即为电石。
最后,将电石从电石炉中取出,并进行加工处理。
电石采集一般采用东窑法或新窑法。
在电石采集过程中,电石需要保持湿润状态,以减少反应产物的飞散和爆炸的危险。
通过上述工艺,可以实现电石的生产。
电石广泛用于合成乙炔、聚氯乙烯树脂、合成橡胶和合成农药等领域,是化工行业中重要的原料之一。
电石的生产工艺中,煅烧和干炼的过程中会产生大量的二氧化碳和二氧化硫等废气,这对环境造成了一定的污染。
为减少对环境的影响,现代电石生产工艺中,通常采取了废气的收集和处理措施,以减少废气的排放量。
同时,提高电石破碎设备和研磨设备的效率,减少粉尘的飞散,也是减少污染的重要手段。
总之,电石的生产工艺主要包括石灰石的选矿和煅烧、灰水处理、焦炭的干炼、电石炉的操作、电石采集和加工等几个主要步骤。
通过这些步骤,可以实现电石的高效生产,为化工行业提供重要的原料。
- 1、下载文档前请自行甄别文档内容的完整性,平台不提供额外的编辑、内容补充、找答案等附加服务。
- 2、"仅部分预览"的文档,不可在线预览部分如存在完整性等问题,可反馈申请退款(可完整预览的文档不适用该条件!)。
- 3、如文档侵犯您的权益,请联系客服反馈,我们会尽快为您处理(人工客服工作时间:9:00-18:30)。
如电极套内送热风,可以促进电极焙烧;固定移动导电环 和承担导电鄂板、锥形环的重量;固定了传动锥形环等设 备的重量 ③把电流通过电极导入炉内。 ⑷出炉系统设备: ①炉嘴:用耐热铁或铸铁制成,安装在炉体的出炉口,炉 嘴最好能通水冷却,一则寿命长,再则方便于炉嘴堵住。 ②烧穿装置:出炉时,必须用电弧去烧穿炉眼,利用电弧 烧穿炉眼的装置叫做烧穿装置。 三、炉气净化 1、炉气的性质及组成 电石生成反应: CaO+3C= CaC2+CO-11.13千卡。从反应 式可以知道,在电石炉内生成电石的同时,伴随有大量的 CO气体生成。在实际生产中,炉气的回收量约为400标准 米3/吨电石,炉气组成大致如下。 一氧化碳CO 70-90% 氢气H2 2—6% 二氧化碳CO2 1----3%
配料站筛子
干焦仓
干焦仓
干焦仓
除尘
除尘
除尘 源自
2、原料石灰 27000KVA密闭电石炉对生石灰的需求: ①GaO ≥90% ② MaO ≤ 1.8% ③SiO2≤1.1% ④ 生过烧≤6% ⑤颗粒度10---50mm 电石原料氧化钙是煅烧石灰石生产的,外购的石灰石 经过筛分后输送到双梁式气烧窑中进行煅烧,炉温控制在 1150℃左右,煅烧温度过高或出炉时间过长会产生过 烧现象,影响石灰在电石炉中的反应速度,煅烧温度过低 或出炉时间较短会出现生烧现象,生烧部分进入电石炉中 分解成氧化钙后参加反应导致电耗增加。烧好的氧化钙经 过输送和筛分至配料站的混料仓中。 ※石灰加工和输送流程 :
氧气O2 0.2---1.0% 氮气N2 5------20% 一氧化碳气体的用途很广,可以用作工业上的燃料。 本装置生产石灰时燃烧一氧化碳,煅烧石灰石,即可充分 利用能源,又可改善环境污染。炉气中粉尘含量的多少, 取决于原料中的粉末含量和电极插入炉内的深度。一般含 尘量在100g/m3左右,炉气为高温度气体,一般温度在400--600℃,瞬间温度可以达到1100℃,所以,在净化的同时, 还必须降温。炉气中的粉尘组成较复杂,从净化后污泥分 析结果如下。 碳C 10—20% 氧化钙 28---30% 酸不溶物 8----10% 三氧化物 9---10% 氧化镁 13----18%
反应式: MgO+C=Mg+CO ↑-116千卡。
Mg+CO=MgO+C+ 117千卡 2 Mg+O2=2MgO+293.2千卡 ③Fe2O3:氧化铁被还原成金属铁后与硅作用,前面已讲 反应式: Fe2O3+3C=2Fe+3CO↑-108千卡 AI2O3:氧化铝在电石炉内不能完全还原成金属铝,一部 分混在电石里降低电石质量。大部分成为粘度很大的炉渣, 沉淀在炉底造成炉底升高。 ※消化石灰的影响: 石灰生产过程中与空气接触一部分氧化钙生成氢氧化 钙,还有一部分与碳材中的水分结合形成氢氧化钙。氢氧 化钙输送当中容易裂碎,粉末氢氧化钙进入电石炉后分解 成氧化钙粉末和水。 反应式:Ca(OH)2 = CaO+H2O-26千卡 H2O+C = CO↑+H2↑ -39.6千卡 从以上反应可以看出石灰吸潮不单是电能和碳材的消 耗增加,重要的是阻碍炉气的上升导致炉压升高。 ※石灰颗粒度的影响
除尘
石灰石
筛分楼
窑前仓
窑气除尘 煅烧窑 风机
CO增压风机
炉气气柜
罗茨风机 煤粉制备机 除尘
除尘
氧化钙筛分楼
电石工序
混料仓 除尘
配料站筛子 除尘
燃煤
热风炉
3、原料电极糊 27000KVA密闭电石炉对生石灰的需求: 固定碳≥80%; 灰分≤4.0%; 软化点90---120℃ 挥发分:12—14% 4、原料指标的影响 ※石灰中的有害杂质: ①SiO2:二氧化硅在电石炉中被焦炭还原成硅。一部分在炉内 生成碳化硅,沉于炉底造成炉底升高。一部分继续与铁作用成 硅铁,硅铁是个耐高温物质对炉壁铁壳烧损严重并且出炉时烧 损炉嘴。 反应式: SiO2+2C=Si+2CO↑-137千卡 ② MgO:氧化镁对电石生产的危害较大,在熔融区内迅速还 原成金属镁。镁蒸汽上升过程中与CO和O2再次反应放出大量 的热量导致炉面发红、炉料结成壳阻碍炉气上升,严重时熔池 外壳被破坏,高温熔融液直接与耐火砖接触烧损耐火砖、电石 流道被堵塞。
密闭电石炉生产工 (27000KVA)
编写:甘孝文
一、原料加工及输送流程
1、原料碳素 27000KVA密闭电石炉对焦炭的需求: ①颗粒度为5---25mm ②固定碳≥84% ③灰分≤15% ④ 挥发分≤1.9% ⑤水分≤1.0% 27000KVA密闭电石炉对兰炭的需求: ①颗粒度为5---25mm ②固定碳≥84% ③灰分≤9% ④ 挥发分≤7% ⑤水分≤1.0%
磷 硫
0.1% 0.18----0.19% 一氧化碳是无色、无味、无臭、有毒气体,与空气混 合到一定浓度时会引起燃烧和爆炸。在18—19℃时,一氧 化碳在空气中的浓度达到12.5—74.2%的范围内时即爆炸。 一氧化碳在650℃时与空气接触会自燃, 2、炉气净化工艺 本装置采用的炉气净化方式为水洗法。从电石炉出来 的粗一氧化碳进入一级空气旋风冷却器,再进入夹套式水 冷却器,将温度降到过滤器的要求后进入除尘过滤器。除 掉的粉尘进入除灰装置,过滤后的一氧化碳进入水洗塔。 在水洗塔中一氧化碳和水进行逆向接触除掉剩余的粉尘和 水溶气体。从水洗塔出来的水进入沉降池进行沉降后重新 使用;一氧化碳进入气柜储存。气柜中的一氧化经过增压 风机输送到石灰窑中作为燃料。 3、工艺流程图
行冷却,产物CO进入炉气净化装置进行净化;电石出炉时 产生的烟气进入出炉除尘装置进行净化。电石炉运行当中 通过底部空气冷却装置来降低炉壳温度并且利用冷却水降 低炉盖及电极把持装置的温度。
冷却空气 混料仓 环形料仓 小料仓 电石炉
冷却水 电石锅
除尘
炉气净化
出炉除尘
3、电石炉设备 ⑴炉体:目前国内炉体有两种形式,圆柱形壳和圆锥形壳。 圆柱形的应用比较广泛。炉壳用20mm钢板制成的并且内 衬一层耐火粘土和一层耐火砖,三个出炉口用更耐高温的 刚玉砖来砌筑的;炉体底部是先铺一层耐火粘土、再铺六 层耐火砖(缝隙错开),耐火砖层上再铺四层碳砖并且把 缝隙全部用电极糊粉末来填充。 ⑵变压器:变压器是电石炉的心脏设备。将把高电压改变 成电石炉操作适应的工作电压。电石炉使用的一次电压为 35KV、一次电流为257A,二次电压为185V—241V、二次 电流为37000A---48000A。 ⑶电极装置:电极上设备作用基本有三个①电极上油压使 电极动作保证操作条件的要求。如电极升降是利用油压系 统的升降油缸来动作;摩擦带松紧由摩擦系统的松紧油缸 来完成;摩擦带上下移动靠压放油缸来完成。为了保证电 极升降两侧油缸和摩擦带上下移动的两侧放压油缸动作平 衡,还要有平衡装置。②保证电极的焙烧和固定导电设备 以及固定传动设备。
石灰的颗粒度对电石生产是十分重要的。如颗粒度较 小时阻碍炉气的升上导致炉压升高、喷料等现象发生。如 颗粒较大时石灰的接触面积减小导致反应速度减慢。所以 电石生产中对石灰的颗粒度严格要求。 ※碳素原料灰分的影响: 碳素原料中的杂质主要是灰分,全部由氧化物组成。 在电石炉中被还原,既要消耗电能也要消耗碳材而且还原 后的杂质沉于炉底或混在电石中影响电石的纯度。 ※碳素原料挥发分的影响: 碳材中的挥发分会增加电石炉的热损失、并且靠近反 应区形成半融粘结状,影响炉料的正常下降和炉气的正常 上升。 ※碳材水分的影响 碳材中的水分与氧化钙接触后导致石灰的消化。
电石炉
一级 空冷
二级 水冷
过滤器
除灰
除灰 石灰窑 气柜 水洗塔 沉降池
四、故障处理 1、石灰窑 ①煅烧去向上移:
因外购的碳材水分较高、颗粒大小不一致,兰炭水分≤ 17%、焦炭水 分≤ 8--15%。所以进炉之前对碳材进行筛分和烘干,水分降至为小于等 于1%、颗粒控制在5—25mm。 ※碳材加工和输送流程
除尘 除尘 除尘
碳材
筛分楼
湿焦仓
锻煤
沸腾炉
回转干燥筒(600度)
90度皮带仓 移动皮带
电石工序
混合料仓
钙混在电石中,在乙炔发生工序中产生磷化氢和硫化氢导 致乙炔的自然点下降、对乙炔设备和管道造成腐蚀。 ※电极糊灰分和挥发分的影响 电极糊的挥发分必须控制在指定范围内,挥发分过大, 电极不易烧结、容易分层、强度差、容易软断;挥发分过 小,电极过早烧结发生硬断。 灰分含量越低越好,过高影响电石质量并且导致电极强度 下降,发生电极硬断。 二、电石生产 1、电石生成理论 炉料凭借电弧热和电阻热在1800℃----2200 ℃ 的高温下反应而制得碳化钙。本反应是吸热反应 反应式为: CaO+3C= CaC2+CO-11.13千卡。 2、电石的生产工艺流程 从配料站出来的混合料经过皮带机输送到环形加料器 中,混料再从环形加料器进入电石炉小料仓,再流入到电 石炉中进行反应。产出物电石从出炉嘴流入到电石锅中进
※碳材颗粒度的影响:
碳素原料在颗粒度不一致时它的电阻也不一样。颗粒 度愈大电阻愈小,支流电流增加,电石炉操作时电极容易 上台,热量利用较低,炉温降低。反之颗粒度愈小,电阻 愈大,电石炉操作时电极容易深入炉内,减小电极与炉底 的距离,增加电流密度,增加炉温、提高热量利用率。但 是过小的颗粒会阻碍炉气的上升。 ※碳素原料粉末的影响: ①粉末多后炉料透气性较差,CO不能顺利排出导致电石生 成反应速度减慢,有利于反应向反方向进行。 ②炉料透气性差会导致发生电石炉喷料现象。 ③粉料多时,许多粉料被炉气带走影响炉料配比的准确性。 粉末在炉料层中容易结成硬壳,电极附近形成支流电路导 致电极上台。 ※磷和硫的影响: 磷和硫进入电石炉后与氧化钙反应生成磷化钙和硫化