齿轮变位系数
斜齿轮变位系数xn和xt

斜齿轮变位系数xn和xt
首先,我们来谈谈斜齿轮的法向变位系数xn。
法向变位系数xn 是描述斜齿轮齿廓曲线的参数,它表示了齿轮齿面在法向上的变形程度。
斜齿轮的啮合传动中,由于齿轮的啮合不是理想的点接触,齿轮齿面会有一定程度的变形,法向变位系数xn就是用来描述这种变形程度的。
xn的计算涉及到齿轮的模数、齿数、齿轮啮合角等参数,它对于斜齿轮的设计和分析具有重要的意义。
其次,切向变位系数xt也是斜齿轮传动中的重要参数。
切向变位系数xt描述了斜齿轮齿廓曲线在切向上的变形程度。
在斜齿轮传动中,由于齿轮的旋转运动和啮合,齿面也会有一定程度的切向变形,xt就是用来描述这种变形程度的。
xt的计算也涉及到齿轮的几何参数和啮合角等,它对于斜齿轮传动的性能分析和设计具有重要的作用。
综上所述,斜齿轮变位系数xn和xt是描述斜齿轮传动中齿轮齿面变形程度的重要参数,它们的计算和分析对于斜齿轮传动的设计和性能评估具有重要的意义。
在工程实践中,工程师们需要根据具体的传动要求和参数来计算和分析xn和xt,以确保斜齿轮传动的可靠性和性能。
直齿圆柱齿轮变位系数、公法线长度、齿厚、最小法向侧隙的计算

外啮合直齿圆柱齿轮变位系数、公法线长度、齿厚、最小法向侧隙的计算1,直齿圆柱齿轮变位系数计算:Case1:a,此处例子仅计算用齿条型刀具加工时的情况(插齿刀加工见相关手册公式):小结:由此可知本例选取的齿数在不变位的情况也不会产生根切现象。
b,根据下图选择大小齿轮的变位系数和x∑。
本例在P6-P7区间取值。
即齿根及齿面承载能力较高区,进行选择。
因大小齿轮的齿数和为18+19=37。
所以本例选择的变位系数和x∑=0.8。
本例我们的两个齿轮在工作时属于减速运动,所以按减速运动的变位系数分配线图,进行2个齿轮的变位系数的选择。
先按(z1+z1)/2=18.5,作为横坐标,做一条垂线(图中蓝色的线),再按x∑/2=0.4,作为纵坐标,做一条水平线(图中橙色的线),接着沿着L线的趋势,穿过上面2条线的交点做一条射线(图中红色的线)最后按大小齿轮的齿数做相应的垂线(图中紫色的线),即得到需要的各自变位系数。
最后我们选择的变位系数即为:小齿轮x1=0.42,大齿轮x2=0.38。
【基本保障其和与之前x ∑一致,即可】。
c,验算变位后的齿顶厚度:注:一般要求齿顶厚Sa≥0.25m;对于表面淬火的齿轮要求Sa≥0.4m下表中的da的计算见后面的计算表格中的计算公式(因为当齿轮变位后,齿顶圆的计算和未变位齿轮的计算稍有差别-涉及到变位系数和中心距变位系数。
)。
分度圆直径db mm 73.8 77.9齿轮的齿顶圆直径da mm 83.027 86.799齿轮的齿顶压力角αa °27.27 26.17中间值invα0.0215 0.0215中间值invαa 0.0587 0.0347齿顶厚Sα 5.77 7.47判断值0.25m 1.025 1.025判断值0.4m 1.64 1.64小结:计算发现变位后的齿轮齿顶厚满足设计需求。
根据上面确定的变位系数,计算齿轮的中心距变位系数和节圆直径、齿根圆直径、齿顶圆直径。
kisssoft齿轮变位系数_解释说明
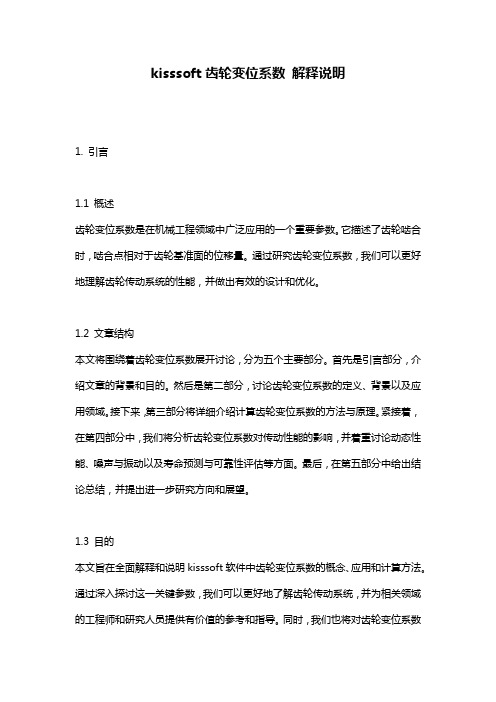
kisssoft齿轮变位系数解释说明1. 引言1.1 概述齿轮变位系数是在机械工程领域中广泛应用的一个重要参数。
它描述了齿轮啮合时,啮合点相对于齿轮基准面的位移量。
通过研究齿轮变位系数,我们可以更好地理解齿轮传动系统的性能,并做出有效的设计和优化。
1.2 文章结构本文将围绕着齿轮变位系数展开讨论,分为五个主要部分。
首先是引言部分,介绍文章的背景和目的。
然后是第二部分,讨论齿轮变位系数的定义、背景以及应用领域。
接下来,第三部分将详细介绍计算齿轮变位系数的方法与原理。
紧接着,在第四部分中,我们将分析齿轮变位系数对传动性能的影响,并着重讨论动态性能、噪声与振动以及寿命预测与可靠性评估等方面。
最后,在第五部分中给出结论总结,并提出进一步研究方向和展望。
1.3 目的本文旨在全面解释和说明kisssoft软件中齿轮变位系数的概念、应用和计算方法。
通过深入探讨这一关键参数,我们可以更好地了解齿轮传动系统,并为相关领域的工程师和研究人员提供有价值的参考和指导。
同时,我们也将对齿轮变位系数对传动性能的影响进行分析,以期对齿轮设计与优化提供实用的建议。
2. 齿轮变位系数的定义与背景:2.1 齿轮变位系数的概念:齿轮变位系数是用来描述齿轮传动中两个啮合齿轮相对于理想位置的偏移程度的参数。
在齿轮传动中,由于制造和安装误差、载荷等因素的影响,实际上啮合的两个齿轮可能存在一定程度的相对位置偏移。
这种位置偏移会导致传动性能下降、噪声和振动增加以及寿命缩短。
2.2 齿轮变位系数的应用领域:齿轮变位系数是齿轮设计和分析中一个重要的参数,广泛应用于机械工程领域。
特别是在高速、精密、大功率传动系统中,更加重视减小齿轮变位系数以提高传动效率和可靠性。
2.3 齿轮变位系数的重要性:齿轮变位系数对于确定有效载荷分布、计算接触应力、考虑弹性变形等都具有重要作用。
通过准确计算和控制齿轮变位系数,可以优化设计方案并提高传动系统的性能。
减小齿轮变位系数可以降低齿轮传动中产生的噪声和振动,提高系统的工作平稳性和舒适性。
proe5.0齿轮变位系数

proe5.0齿轮变位系数齿轮变位系数是齿轮传动中的一个重要参数,它表示齿轮齿数与模数之间的比值。
在Pro/E 5.0中,我们可以使用Gear模块来创建和分析齿轮传动系统。
本文将详细介绍如何在Pro/E 5.0中设置齿轮变位系数。
1. 打开Pro/E 5.0软件,点击“文件”菜单,选择“新建”,然后选择“组件”类型,点击“确定”。
2. 在弹出的“新文件选项”对话框中,选择“mmns_asm_design”模板,点击“确定”。
3. 在左侧的模型树中,右键点击“组件.1”,选择“插入模式”,然后选择“元件”类型。
4. 在弹出的“元件创建”对话框中,选择“gear”类型,输入齿轮的名称,点击“确定”。
5. 在弹出的“齿轮建模”对话框中,设置齿轮的基本参数,如齿数、模数、压力角等。
这些参数将影响齿轮的变位系数。
6. 在齿轮建模对话框中,点击“齿轮设置”选项卡,进入齿轮设置界面。
7. 在齿轮设置界面中,我们可以看到一个名为“变位系数”的选项。
这个选项用于设置齿轮的变位系数。
8. 在变位系数选项中,我们可以选择预设的变位系数,也可以手动输入自定义的变位系数。
预设的变位系数包括正常变位、短齿变位、长齿变位等。
9. 在选择或输入变位系数后,我们需要设置另一个参数“中心距”。
中心距是指两个齿轮之间的间距,它也是影响齿轮传动性能的一个重要参数。
10. 在设置好变位系数和中心距后,我们可以点击齿轮建模对话框中的“预览”按钮,查看齿轮的三维模型。
如果模型不符合要求,我们可以返回齿轮设置界面,调整变位系数和中心距,直到满意为止。
11. 在确认齿轮模型无误后,我们可以点击齿轮建模对话框中的“确定”按钮,完成齿轮的创建。
此时,我们在左侧的模型树中可以看到刚刚创建的齿轮元件。
12. 接下来,我们需要将创建好的齿轮元件装配到主组件中。
在模型树中,右键点击主组件(即“组件.1”),选择“组装”,然后选择刚刚创建的齿轮元件。
13. 在弹出的“组装”对话框中,我们可以设置齿轮元件的位置和方向。
齿轮变位系数公式

齿轮变位系数公式
齿轮是机械传动中常用的元件,齿轮传动的稳定性和可靠性是机械传动的关键之一。
在齿轮传动中,齿轮的变位系数是一个重要的参数,它可以反映齿轮传动的稳定性和可靠性等性能指标。
齿轮变位系数是指齿轮轴线之间的垂直距离与模数的比值,通常用符号ε表示。
齿轮变位系数的计算公式如下:
ε = (y1 + y2) / (2m)
其中,y1和y2分别表示相邻两个齿轮齿数之差的绝对值,m为模数。
该公式适用于所有齿轮传动类型,包括直齿轮、斜齿轮、圆弧齿轮等。
齿轮变位系数的计算可以通过手算和计算机辅助设计软件进行。
在手算时,需要准确测量齿轮的齿数和模数,并应用齿轮变位系数公式进行计算。
在计算机辅助设计软件中,可以直接输入齿轮参数,软件会自动计算齿轮变位系数。
齿轮变位系数的大小对齿轮传动的稳定性和可靠性有着重要的影响。
当齿轮变位系数太大时,齿轮传动会出现过载、振动等问题,影响传动系统的性能;当齿轮变位系数太小时,齿轮传动会出现接触不良、噪声等问题,同样会影响传动系统的性能。
因此,在齿轮设计
和选择时,需要合理地选取齿轮变位系数,以保证传动系统的稳定性和可靠性。
齿轮变位系数是齿轮传动中一个重要的性能指标,它的大小对传动系统的稳定性和可靠性有着重要的影响。
齿轮变位系数的计算公式简单易用,可以帮助工程师准确地计算齿轮的变位系数,从而保证传动系统的性能。
齿轮变位系数

齿轮变位系数、侧隙选择
z1=10z2=60m=0.35
安装中心距12.3
材料为pa66
那么变位系数选择
侧隙的控制方法
侧隙根据经验选取
如果中心距为12.3
那么需要0.145的总变位系数
建议你小齿轮采用0.2变位
大齿轮采用-0.055变位
此时小齿轮齿顶稍有变尖
但可以满足0.1齿顶园角(线切割单变偏置)
1>按照常规,总变位0.145027。
按DIN 3992合理分配小齿x1≈0.28 x2 = 0.145027-x1= -0.134473 .
选择较大侧隙,例如GB2363-90 的 d , 也可以按照材料特性自己定义。
2>不需要拉大中心距。
3>小齿轮虽然存在一些根切,对啮合没有太大影响。
进啮点处0.0059 没有渐开线。
齿厚按照-0.03 考虑,用0.15 线丝切割模具型腔,还可以走丝不干涉。
4>PA66 按照 1.35% 考虑收缩,也可以按实际修改。
【本文来源】皇家小铺(/)【原文地址】/post/20090412434.html。
圆柱齿轮啮合变位系数分配

变位系数变位系数x是径向变位系数,加工标准齿轮时,齿条形刀具中线与齿轮分度圆相切。
加工变位齿轮时齿条形刀具中线与齿轮分度圆相切位置偏移距离xm,外移x为正,内移x为负。
除了圆锥齿轮有时采用切向变位xt外,圆柱齿轮一般只采用径向变位。
变位系数x的选择不仅仅是为了凑中心距,而主要是为了提高强度和改善传动质量。
变位齿轮的主要功用如下:(1)减小齿轮传动的结构尺寸,减轻重量 在传动比一定的条件下,可使小齿轮齿数zl<zmin,从而使传动的结构尺寸减小,减轻机构重量。
(2)避免根切,提高齿根的弯曲强度 当小齿轮齿数z1<zmin时,可以利用正变位避免根切,提高齿根的弯曲强度。
x≥xmin=(Z-Zmin)/Zmin,对α=20o时,Zmin=17。
(3)提高齿面的接触强度 采用啮合角α’>α的正传动时,由于齿廓曲率半径增大,故可以提高齿面的接触强度。
(4)提高齿面的抗胶合耐磨损能力 采用啮合角α’>α的正传动,并适当分配变位系数xl、x2,使两齿轮的最大滑动率相等时,既可降低齿面接触应力,又可降低齿面间的滑动率以提高齿轮的抗胶合和耐磨损能力。
(5)配凑中心距 当齿数z1、z2不变的情况下,啮合角α’不同,可以得到不同的中心距,以达到配凑中心距的目的。
(6)修复被磨损的旧齿轮 齿轮传动中,小齿轮磨损较重,大齿轮磨损较轻,可以利用负变位把大齿轮齿面磨损部分切去再使用,重配一个正变位小齿轮,这就节约了修配时需要的材料与加工费用。
选择变位系数的基本原则(1)润滑条件良好的闭式齿轮传动 当齿轮表面的硬度不高时(HBS<350),即对于齿面未经渗碳、渗氮、表面淬火等硬化处理的齿轮,齿面疲劳点蚀或剥伤为其主要的失效形式,这时应选择尽可能大的总变位系数x,即尽量增大啮合角,以便增大啮合节点处齿廓的综合曲率半径,减少接触应力,提高接触强度与疲劳寿命。
当轮齿表面硬度较高时(HBS>350),常因齿根疲劳裂纹的扩展造成轮齿折断而使传动失效,这时,选择变位系数应使齿轮的齿根弯曲强度尽量增大,并尽量使相啮合的两齿轮具有相近的弯曲强度。
齿轮的变位系数

齿轮的变位系数变位系数x是径向变位系数,加工标准齿轮时,齿条形刀具中线与齿轮分度圆相切。
加工变位齿轮时齿条形刀具中线与齿轮分度圆相切位置偏移距离xm,外移x为正,内移x为负。
除了圆锥齿轮有时采用切向变位xt外,圆柱齿轮一般只采用径向变位。
变位系数x的选择不仅仅是为了凑中心距,而主要是为了提高强度和改善传动质量。
变位齿轮的主要功用如下:(1)减小齿轮传动的结构尺寸,减轻重量 在传动比一定的条件下,可使小齿轮齿数zl<zmin,从而使传动的结构尺寸减小,减轻机构重量。
(2)避免根切,提高齿根的弯曲强度 当小齿轮齿数z1<zmin时,可以利用正变位避免根切,提高齿根的弯曲强度。
x≥xmin=(Z-Zmin)/Zmin,对α=20o时,Zmin=17。
(3)提高齿面的接触强度 采用啮合角α’>α的正传动时,由于齿廓曲率半径增大,故可以提高齿面的接触强度。
(4)提高齿面的抗胶合耐磨损能力 采用啮合角α’>α的正传动,并适当分配变位系数xl、x2,使两齿轮的最大滑动率相等时,既可降低齿面接触应力,又可降低齿面间的滑动率以提高齿轮的抗胶合和耐磨损能力。
(5)配凑中心距 当齿数z1、z2不变的情况下,啮合角α’不同,可以得到不同的中心距,以达到配凑中心距的目的。
(6)修复被磨损的旧齿轮 齿轮传动中,小齿轮磨损较重,大齿轮磨损较轻,可以利用负变位把大齿轮齿面磨损部分切去再使用,重配一个正变位小齿轮,这就节约了修配时需要的材料与加工费用。
选择变位系数的基本原则(1)润滑条件良好的闭式齿轮传动 当齿轮表面的硬度不高时(HBS<350),即对于齿面未经渗碳、渗氮、表面淬火等硬化处理的齿轮,齿面疲劳点蚀或剥伤为其主要的失效形式,这时应选择尽可能大的总变位系数x,即尽量增大啮合角,以便增大啮合节点处齿廓的综合曲率半径,减少接触应力,提高接触强度与疲劳寿命。
当轮齿表面硬度较高时(HBS>350),常因齿根疲劳裂纹的扩展造成轮齿折断而使传动失效,这时,选择变位系数应使齿轮的齿根弯曲强度尽量增大,并尽量使相啮合的两齿轮具有相近的弯曲强度。
变位系数

变位系数变位系数,是用于减小齿轮传动的结构尺寸。
限制条件保证加工时不根切等选择原则润滑条件良好的闭式齿轮传动等主要功用减小齿轮传动的结构尺寸等目录1. 1 名称由来2. 2 概念3. 3 主要功用4. 4 选择原则5. 5 限制条件变位系数名称由来标准齿轮传动存在着一些局限性:(1)受根切限制,齿数不得少于Zmin,使传动结构不够紧凑;(2)不适合于安装中心距a'不等于标准中心距a的场合。
当a'<a时无法安装,当a'>a时,虽然可以安装,但会产生过大的侧隙而引起冲击振动,影响传动的平稳性;(3)一对标准齿轮传动时,小齿轮的齿根厚度小而啮合次数又较多,故小齿轮的强度较低,齿根部分磨损也较严重,因此小齿轮容易损坏,同时也限制了大齿轮的承载能力。
齿轮传动示意图为了改善齿轮传动的性能,出现了变位齿轮。
如图所示,当齿条插刀齿顶线超过极限啮合点N1,切出来的齿轮发生根切。
若将齿条插刀远离轮心O1一段距离(xm),齿顶线不再超过极限点N1,则切出来的齿轮不会发生根切,但此时齿条的分度线与齿轮的分度圆不再相切。
这种改变刀具与齿坯相对位置后切制出来的齿轮称为变位齿轮,刀具移动的距离xm称为变位量,x称为变位系数。
刀具远离轮心的变位称为正变位,此时x>0;刀具移近轮心的变位称为负变位,此时x<0。
标准齿轮就是变位系数x=0的齿轮。
变位系数概念齿轮的变位系数变位系数x 是径向变位系数,加工标准齿轮时,齿条形刀具中线与齿轮分度圆相切。
加工变位齿轮时齿条形刀具中线与齿轮分度圆相切位置偏移距离xm,外移x 为正,内移x 为负。
除了圆锥齿轮有时采用切向变位xt 外,圆柱齿轮一般只采用径向变位。
变位系数x 的选择不仅仅是为了凑中心距,而主要是为了提高强度和改善传动质量。
变位系数主要功用(1)减小齿轮传动的结构尺寸,减轻重量在传动比一定的条件下,可使小齿轮齿数zl< zmin,从而使传动的结构尺寸减小,减轻机构重量。
齿轮变位系数计算公式
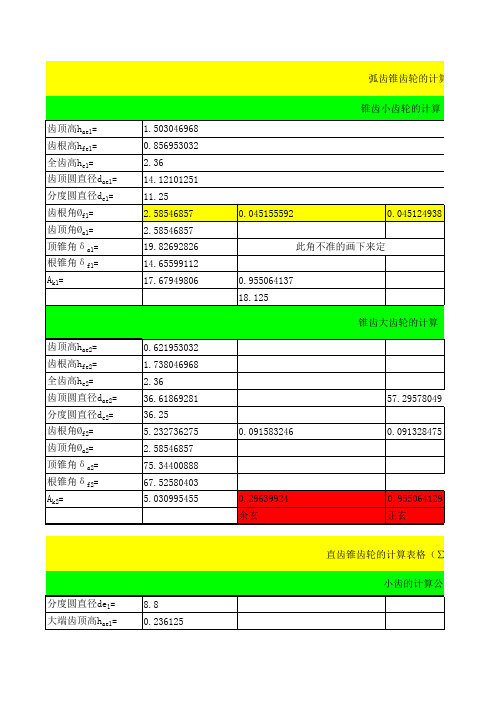
端面基圆齿距pbt=
基圆螺旋角βb=
21.46902352
法向齿厚sn=
2.35619449
端面齿厚st=
2.599772973
端面基圆齿厚sbt= 2.474242055
法向基圆齿厚sbn= 2.3025682
端面齿顶圆压力角α
at=
27.87834641
端面重合度εa=
14.89560191 根据传动要求和齿数和由图2-1a 选得 0.040564012 13.65404495
1.743355127
1.622393438
27.87834641 0.295868875
直齿外齿轮 斜齿外齿轮
公法线长度 跨测齿数 公法线长度 跨测齿厚
公法线长度的计算
Wk= k= Wkn= k=
标准齿轮 9.70116265 5.055555556
直齿外齿轮
公法线长度 跨测齿数
Wk= k=
9.700915
1.570796327 1.616117505 #NUM! 1.299732823
0 0.337197611
0 60 0.582 62.5 28.58 -25 -26.75205269
8.995894626 8 9.396926208 3.141592654 2.952131434 1.570796327 1.336013929 #NUM! 1.217405061
齿顶高hae1= 齿根高hfe1= 全齿高he1= 齿顶圆直径dae1= 分度圆直径de1= 齿根角Øf1= 齿顶角Øa1= 顶锥角δa1= 根锥角δf1= Ak1=
1.503046968 0.856953032 2.36 14.12101251 11.25 2.58546857 2.58546857 19.82692826 14.65599112 17.67949806
直齿圆柱齿轮变位系数的优化选择
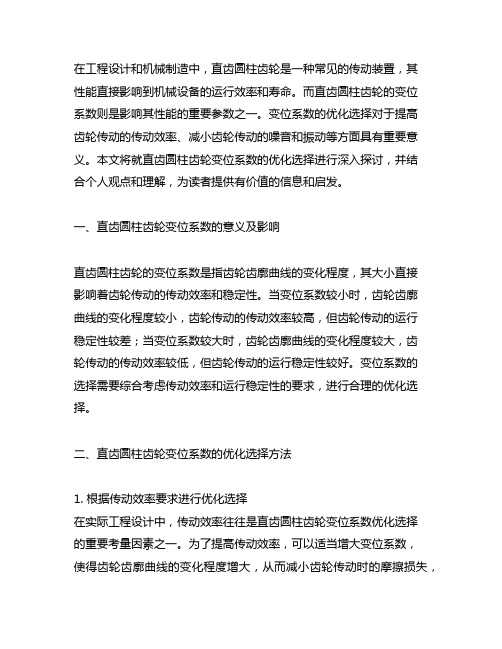
在工程设计和机械制造中,直齿圆柱齿轮是一种常见的传动装置,其性能直接影响到机械设备的运行效率和寿命。
而直齿圆柱齿轮的变位系数则是影响其性能的重要参数之一。
变位系数的优化选择对于提高齿轮传动的传动效率、减小齿轮传动的噪音和振动等方面具有重要意义。
本文将就直齿圆柱齿轮变位系数的优化选择进行深入探讨,并结合个人观点和理解,为读者提供有价值的信息和启发。
一、直齿圆柱齿轮变位系数的意义及影响直齿圆柱齿轮的变位系数是指齿轮齿廓曲线的变化程度,其大小直接影响着齿轮传动的传动效率和稳定性。
当变位系数较小时,齿轮齿廓曲线的变化程度较小,齿轮传动的传动效率较高,但齿轮传动的运行稳定性较差;当变位系数较大时,齿轮齿廓曲线的变化程度较大,齿轮传动的传动效率较低,但齿轮传动的运行稳定性较好。
变位系数的选择需要综合考虑传动效率和运行稳定性的要求,进行合理的优化选择。
二、直齿圆柱齿轮变位系数的优化选择方法1. 根据传动效率要求进行优化选择在实际工程设计中,传动效率往往是直齿圆柱齿轮变位系数优化选择的重要考量因素之一。
为了提高传动效率,可以适当增大变位系数,使得齿轮齿廓曲线的变化程度增大,从而减小齿轮传动时的摩擦损失,提高传动效率。
但值得注意的是,过大的变位系数会导致齿轮传动的运行稳定性下降,因此需要根据具体情况进行合理的选择。
2. 根据运行稳定性要求进行优化选择在一些对齿轮传动的运行稳定性要求较高的应用场合,如精密机床、航空航天等领域,通常需要选取较小的变位系数,以保证齿轮传动在运行过程中的稳定性。
较小的变位系数可以减小齿轮齿廓曲线的变化程度,降低齿轮传动的动态载荷,从而提高齿轮传动的运行稳定性。
但传动效率可能会有所降低,因此需要在传动效率与运行稳定性之间进行权衡,选择合适的变位系数。
3. 结合实际应用需求进行优化选择除了传动效率和运行稳定性外,直齿圆柱齿轮变位系数的优化选择还需要考虑到具体的应用需求。
在某些特殊工况下需要对传动进行精密调控,就需要更加严格地选择变位系数,以确保传动的精度和稳定性。
齿轮变位系数计算公式
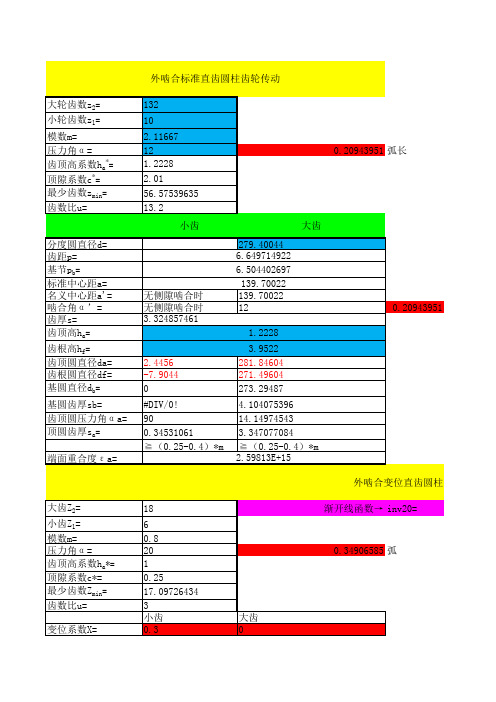
1.743355127
1.622393438
27.87834641
0.295868875
直齿外齿轮
公法线长度
公法线长度的计算 Wk=
标准齿轮 9.70116265
直齿外齿轮 斜齿外齿轮
跨测齿数 公法线长度 跨测齿厚
k= Wkn= k=
5.055555556
直齿外齿轮
公法线长度 跨测齿数
齿顶高hae1= 齿根高hfe1= 全齿高he1= 齿顶圆直径dae1= 分度圆直径de1= 齿根角Øf1= 齿顶角Øa1= 顶锥角δa1= 根锥角δf1= Ak1=
14.212488
齿根圆直径df=
11.14560191
基圆直径db=
12.5630209
法向齿距pn=
端面齿距pt=
5.199545947
法向基圆齿距pbn=
端面基圆齿距pbt=
基圆螺旋角βb=
21.46902352
法向齿厚sn=
2.35619449
端面齿厚st=
2.599772973
端面基圆齿厚sbt= 2.474242055
0.003117051
0.019 要查出,我没查,用时一定要
0.01
查
弧长
αa1
αa2
1.570796327 0.246959646
位直齿圆柱齿轮传动 0.014904
给定x∑求a' 0.320442451
αa1 0.743891086
αa2 0.479274389
inv20= invαa1= invαa2=
变位系数X=
18
6 0.8 20 1 0.25 17.09726434 3 小齿 0.3
变位系数

变位系数变位系数x是径向变位系数,加工标准齿轮时,齿条形刀具中线与齿轮分度圆相切。
加工变位齿轮时齿条形刀具中线与齿轮分度圆相切位置偏移距离xm,外移x为正,内移x为负。
除了圆锥齿轮有时采用切向变位xt外,圆柱齿轮一般只采用径向变位。
变位系数x的选择不仅仅是为了凑中心距,而主要是为了提高强度和改善传动质量。
变位齿轮的主要功用如下:(1)减小齿轮传动的结构尺寸,减轻重量在传动比一定的条件下,可使小齿轮齿数zl<zmin,从而使传动的结构尺寸减小,减轻机构重量。
(2)避免根切,提高齿根的弯曲强度当小齿轮齿数z1<zmin时,可以利用正变位避免根切,提高齿根的弯曲强度。
x≥xmin=(Z-Zmin)/Zmin,对α=20o时,Zmin=17。
(3)提高齿面的接触强度采用啮合角α’>α的正传动时,由于齿廓曲率半径增大,故可以提高齿面的接触强度。
(4)提高齿面的抗胶合耐磨损能力采用啮合角α’>α的正传动,并适当分配变位系数xl、x2,使两齿轮的最大滑动率相等时,既可降低齿面接触应力,又可降低齿面间的滑动率以提高齿轮的抗胶合和耐磨损能力。
(5)配凑中心距当齿数z1、z2不变的情况下,啮合角α’不同,可以得到不同的中心距,以达到配凑中心距的目的。
(6)修复被磨损的旧齿轮齿轮传动中,小齿轮磨损较重,大齿轮磨损较轻,可以利用负变位把大齿轮齿面磨损部分切去再使用,重配一个正变位小齿轮,这就节约了修配时需要的材料与加工费用。
选择变位系数的基本原则(1)润滑条件良好的闭式齿轮传动当齿轮表面的硬度不高时(HBS<350),即对于齿面未经渗碳、渗氮、表面淬火等硬化处理的齿轮,齿面疲劳点蚀或剥伤为其主要的失效形式,这时应选择尽可能大的总变位系数x,即尽量增大啮合角,以便增大啮合节点处齿廓的综合曲率半径,减少接触应力,提高接触强度与疲劳寿命。
当轮齿表面硬度较高时(HBS>350),常因齿根疲劳裂纹的扩展造成轮齿折断而使传动失效,这时,选择变位系数应使齿轮的齿根弯曲强度尽量增大,并尽量使相啮合的两齿轮具有相近的弯曲强度。
减速机圆柱斜齿轮变位系数

减速机圆柱斜齿轮变位系数引言减速机是一种常见的机械传动装置,广泛应用于各个领域。
而圆柱斜齿轮作为减速机的重要组成部分之一,其变位系数是评价其性能的重要指标。
本文将对减速机圆柱斜齿轮变位系数进行全面、详细、完整且深入地探讨。
什么是变位系数变位系数是指圆柱斜齿轮在运动过程中齿轮齿廓的变形程度。
由于齿轮在传动过程中承受着较大的载荷,其齿廓会发生变形,进而影响传动的精度和寿命。
变位系数可以用来描述这种变形程度,是评价圆柱斜齿轮传动性能的重要指标之一。
变位系数的计算方法计算圆柱斜齿轮的变位系数需要考虑多个因素,包括齿轮的材料、齿轮的几何参数、载荷等。
下面将介绍一种常见的计算方法。
步骤一:确定齿轮的几何参数首先需要确定齿轮的几何参数,包括模数、齿数、压力角等。
这些参数决定了齿轮的形状和尺寸,进而影响变位系数的计算结果。
步骤二:计算齿轮的载荷齿轮的载荷是指在传动过程中齿轮所承受的力。
可以通过分析传动系统的工作条件和传递的功率来计算齿轮的载荷。
载荷的大小对于变位系数的计算至关重要。
步骤三:计算齿轮的变位系数根据齿轮的几何参数和载荷,可以利用相应的计算公式来计算齿轮的变位系数。
常见的计算公式包括ISO 6336标准中的公式和AGMA标准中的公式。
选择适合的计算公式可以得到较为准确的结果。
影响变位系数的因素圆柱斜齿轮的变位系数受多个因素的影响,下面将介绍其中几个重要的因素。
材料齿轮的材料对于变位系数的大小有重要影响。
不同材料的弹性模量和热膨胀系数不同,会导致齿轮的变形程度不同。
选择合适的材料可以降低变位系数,提高传动的精度和寿命。
几何参数齿轮的几何参数也是影响变位系数的重要因素之一。
例如,增大模数可以减小变位系数,提高传动的精度。
而减小齿数会增大变位系数,降低传动的精度。
润滑良好的润滑可以减小齿轮的摩擦和磨损,进而降低变位系数。
选择适当的润滑剂和润滑方式可以改善传动的性能。
加工精度齿轮的加工精度也会对变位系数产生影响。
齿轮的变位系数与中心距的关系

齿轮的变位系数与中心距的关系
齿轮的变位系数与中心距之间存在着一定的关系。
在制造一个齿轮驱动系统中,中心距是一个很重要的参数,这测定着齿轮运转时碰撞是否会出现振动,从而确定了运动片的变位系数。
首先,齿轮变位系数依赖于齿轮的中心距。
它的定义为,在相对的极面上,齿
轮的直接接触点相对于齿轮的圆心形成的边界的水平和垂直的偏移距离的倒数。
当中心距小于正确的值时,会引起齿轮的周期性摆动,这会影响变位系数。
另外,当中心距为正确值时,变位系数最大,此时齿轮处于连接状态,齿轮之间产生稳定的、均匀的作用,有助于一个顺畅的传动。
其次,不同尺寸的齿轮中心距的值不一样,但是通用的原理是,若中心距大于
最大值时,齿轮之间不能有效连接,变位系数会迅速降低,并且它也会导致齿轮在运转时产生振动。
反之,若中心距小于最小值时,也会降低变位系数,但由于偏移太小,变位系数降低的幅度不会很大,而且不会产生振动。
总而言之,齿轮的变位系数与中心距之间存在着一定关系:如果中心距大于最
大值或小于最小值,变位系数会降低,而且中心距为正确值时变位系数最大,达到最佳的传动性能。
克林贝格齿轮切向变位系数

克林贝格齿轮切向变位系数克林贝格齿轮切向变位系数(Helix Deviation Coefficient),是描述齿轮齿槽切向变位的一个重要参数。
它表征了齿轮齿槽斜面与与齿轮轴线垂直的平面之间的夹角变化程度,通常用字母ε表示。
克林贝格齿轮切向变位系数在齿轮传动中起着至关重要的作用。
首先,它影响着齿轮的工作精度和传动效率。
当切向变位系数较大时,齿轮的啮合效果较好,传动效率较高。
相反,如果切向变位系数较小,则齿轮之间的啮合效果较差,传动效率也相应降低。
其次,克林贝格齿轮切向变位系数还会影响齿轮的噪音和振动。
齿轮传动中的噪音和振动主要来自于齿轮齿面的非均匀接触与相对滑动,而切向变位系数的大小直接决定了齿面接触情况的好坏。
当切向变位系数合理时,齿轮之间的接触压力分布均匀,齿面接触面积较大,从而减小了噪音和振动的产生。
另外,克林贝格齿轮切向变位系数的大小还会对齿轮的自动稳定性和传动平稳性产生影响。
当切向变位系数较大时,齿轮之间的相对滑动较小,稳定性较好,传动过程更加平稳可靠。
但如果切向变位系数过大,反而会增加齿轮的摩擦和磨损,降低齿轮的寿命和可靠性。
为了保证齿轮传动的正常工作,我们需要在设计和制造过程中合理选择克林贝格齿轮切向变位系数。
具体来说,一方面,我们需要根据实际工况要求,选择适当的切向变位系数,以提高传动效率、降低噪音和振动。
另一方面,我们还需要结合齿轮的材料、热处理工艺和润滑方式等因素,综合考虑切向变位系数的大小,以确保齿轮传动的可靠性和稳定性。
总之,克林贝格齿轮切向变位系数是齿轮传动中的一个重要参数,它直接影响着齿轮的工作精度、传动效率、噪音振动、自动稳定性和传动平稳性等方面。
在设计和制造齿轮时,我们应该合理选择切向变位系数,并结合其他因素进行综合考虑,以确保齿轮传动的可靠性和性能。
斜齿轮变位系数xn和xt

斜齿轮变位系数xn和xt
斜齿轮是一种重要的传动元件,其结构具有许多特点,其中包括斜齿轮变位系数xn和xt。
斜齿轮变位系数xn和xt是指斜齿轮齿廓的特征参数,它们对于斜齿轮的传动性能和运行稳定性具有重要影响。
斜齿轮变位系数xn和xt能够影响斜齿轮的传动效率。
传动效率是指斜齿轮传动中输入功率与输出功率之比。
斜齿轮变位系数xn和xt的选择会直接影响斜齿轮的传动效率。
一般来说,当斜齿轮变位系数xn和xt适当时,斜齿轮的传动效率会比较高;而当斜齿轮变位系数xn和xt不合理时,斜齿轮的传动效率会降低。
斜齿轮变位系数xn和xt还能够影响斜齿轮的传动噪声。
传动噪声是指斜齿轮传动中产生的噪声。
斜齿轮变位系数xn和xt的选择会对斜齿轮的传动噪声产生一定的影响。
通常情况下,斜齿轮变位系数xn和xt越小,斜齿轮的传动噪声越小;而斜齿轮变位系数xn和xt越大,斜齿轮的传动噪声越大。
斜齿轮变位系数xn和xt还能够影响斜齿轮的传动精度。
传动精度是指斜齿轮传动中输出轴转动角度与输入轴转动角度之比。
斜齿轮变位系数xn和xt的选择会对斜齿轮的传动精度产生一定的影响。
一般来说,当斜齿轮变位系数xn和xt适当时,斜齿轮的传动精度会比较高;而当斜齿轮变位系数xn和xt不合理时,斜齿轮的传动精度会降低。
总的来说,斜齿轮变位系数xn和xt对斜齿轮的传动性能和运行稳定性具有重要影响,合理选择斜齿轮变位系数xn和xt可以提高斜齿轮的传动效率、降低传动噪声、提高传动精度。
因此,在设计和使用斜齿轮时,需要根据实际情况合理选择斜齿轮变位系数xn和xt,以保证斜齿轮的正常运行和长久使用。
- 1、下载文档前请自行甄别文档内容的完整性,平台不提供额外的编辑、内容补充、找答案等附加服务。
- 2、"仅部分预览"的文档,不可在线预览部分如存在完整性等问题,可反馈申请退款(可完整预览的文档不适用该条件!)。
- 3、如文档侵犯您的权益,请联系客服反馈,我们会尽快为您处理(人工客服工作时间:9:00-18:30)。
名称由来
标准齿轮传动存在着一些局限性:(1)受根切限制,齿数不得少于Zmin,使传动结构不够紧凑;(2)不适合于安装中心距a'不等于标准中心距a的场合。
当a'<a时无法安装,当a'>a时,虽然可以安装,但会产生过大的侧隙而引起冲击振动,影响传动的平稳性;(3)一对标准齿轮传动时,小齿轮的齿根厚度小而啮合次数又较多,故小齿轮的强度较低,齿根部分磨损也较严重,因此小齿轮容易损坏,同时也限制了大齿轮的承载能力
齿轮传动示意图
为了改善齿轮传动的性能,出现了变位齿
轮。
如图所示,当齿条插刀齿顶线超过极限啮合点N1,切出来的齿轮发生根切。
若将齿条插刀远离轮心O1一段距离(xm),齿顶线不再超过极限点N1,则切出来的齿轮不会发生根切,但此时齿条的分度线与齿轮的分度圆不再相切。
这种改变刀具与齿坯相对位置后切制出来的齿轮称为变位齿轮,刀具移动的距离xm称为变位量,x称为变位系数。
刀具远离轮心的变位称为正变位,此时x>0;刀具移近轮心的变位称为负变位,此时x<0。
标准齿轮就是变位系数x=0的齿轮。
2概念
齿轮的变位系数变位系数 x 是径向变位系数,加工标准齿轮时,齿条形刀具中线与齿轮分度圆相切。
加工变位齿轮时齿条形刀具中线与齿轮分度圆相切位置偏移距离 xm,外移 x 为正,内移 x 为负。
除了圆锥齿轮有时采用切向变位 xt 外,圆柱齿轮一般只采用径向变位。
变位系数 x 的选择不仅仅是为了凑中心距,而主要是为了提高强度和改善传动质量。
3主要功用
(1)减小齿轮传动的结构尺寸,减轻重量在传动比一定的条件下,可使小齿轮齿数 zl< zmin,从而使传动的结构尺寸减小,减轻机构重量。
(2)避免根切,提高齿根的弯曲强度当小齿轮齿数 z1<zmin 时,可以利用正变位避免根切,提高齿根的弯曲强度。
x≥xmin=(Z-Zmin)/Zmin,对α=20°时,Zmin=17。
(3)提高齿面的接触强度采用啮合角α’>α 的正传动时,由于齿廓曲率半径增大,故可以提高齿面的接触强度。
(4)提高齿面的抗胶合耐磨损能力采用啮合角α’>α 的正传动,并适当分配变位系数 xl、x2,使两齿轮的最大滑动率相等时,既可降低齿面接触应力,又可降低齿面间的滑动率以提高齿轮的抗胶合和耐磨损能力。
(5)配凑中心距当齿数 z1、z2 不变的情况下,啮合角α’不同,可以得到不同的中心距,以达到配凑中心距的目的。
(6)修复被磨损的旧齿轮齿轮传动中,小齿轮磨损较重,大齿轮磨损较轻,可以利用负变位把大齿轮齿面磨损部分切去再使用,重配一个正变位小齿轮,这就节约了修配时需要的材料与加工费用。
4选择原则
(1)润滑条件良好的闭式齿轮传动当齿轮表面的硬度不高时(HBS350),常因齿根疲劳裂纹的扩展造成轮齿折断而使传动失效,这时,选择变位系数应使齿轮的齿根弯曲强度尽量增大,并尽量使相啮合的两齿轮具有相近的弯曲强度。
(2)开式齿轮传动齿面研磨磨损或轮齿折断为其主要的失效形式。
故应选择总变位系数x∑ 尽可能大的正变位齿轮,并适当分配变位系数,使两轮齿根处的最大滑动率相等,这样不仅可以减小最大滑动率,提高其耐磨损能力,同时还可以增大齿根厚度,提高轮齿的弯曲强度。
(3)重载齿轮传动重载齿轮传动的齿面易产生胶合破坏,除了要选择合适的润滑油粘度,或采用含有添加剂的活性润滑油等措施外,应用变位齿轮时,应尽量增大传动的啮合角(即增大总变位系数x∑),并适当分配变位系数 xl 和x2,以使最大滑动率接近相等,这样不仅可以增大齿面的综合曲率半径,减小齿面接触应力,还可以减小最大滑动率以提高齿轮的抗胶合能力。
(4)高精度齿轮传动对于精度高于7 级的重载齿轮传动,为了减小节点处齿面上的压力,可以适当选择变位系数,使节点位于两对齿啮合区,以减少每一对啮合轮齿上的载荷,提高承载能力。
(5)斜齿圆柱齿轮传动斜齿圆柱齿轮传动可以采用高度变位或角度变位,而实际上多采用标准齿轮传动。
利用角度变位,可以增加齿面的综合曲率半径,有利于提高斜齿轮的接触强度,但变位系数较大时,又会使啮合轮齿的接触线过分地缩短,反而降低其承载能力。
故采用角度变位,对提高斜齿圆柱齿轮的承载能力的效果并不大。
有时,为了配凑中心距的需要,采用变位齿轮时,可以按其当量齿数zv(=z/cos3β),仍用直齿圆圆柱齿轮选择变位系数的方法确定其变位系数。
5限制条件
1保证加工时不根切;
2 保证加工时不顶切;
3 保证必要的齿顶厚;
4 保证必要的重合度;
5 保证啮合时不干涉;通常采用角度变位,大、小齿轮都用正变位,按等滑动比的原则选取。